高速铣削加工技术的主要优点及应用介绍
高速CNC加工的优点有哪些?

高速CNC加工的优点有哪些?高速CNC加工的优点有哪些?丰远五金制品厂可以制造五金模具和塑胶模具,在模具制造的过程中常用到高速CNC加工。
高速CNC加工有哪些特点和好处?一、高速CNC加工的优势:高速CNC加工(HSM或HSC)是二十世纪九十年代迅速发展应用的先进加工技术。
通常是指高的主轴转速(10,000-100,000r/min)、高的进给速度(40m-180m/min)下的铣削加工。
高速加工在实际应用中能解决新材料的加工问题,适应表面质量高、精度高、形状复杂的三维曲面加工,减少和避免效率低的电火花加工,解决薄壁零件的加工问题,数控高速复合加工还可以减少搬运与装夹次数,避免重复定位带来的加工误差等,既提高了加工质量,又提高了加工效率。
高速CNC加工一般采用高的铣削速度和快速多次走刀来提高效率,小直径刀具,适当的进给量,小的径向和轴向切削深度,即切削体积。
随着铣削速度的提高,加工时间大幅度缩短,并且切削力下降、振动小,尤其是径向切削力大幅度降低,零件变形小,由于在切削时大量的切削热被切屑带走,工件表面温度较低。
由于高速铣削的的上述特点,高速加工相对常规加工具有突出优点:高生产率、工作平稳、加工表面质量很高,无需再进行其它表面处理工序、有利于加工薄壁零件和高强度、高硬度脆性材料、可缩短交货期、减少设备台数及车间面积、减少工人数量。
二、高速CNC加工与塑胶模具制造目前塑料模具越来越精巧、结构越来越复杂,要求的合模次数接近和超过80万次,采用的模具钢材的硬度越来越高,有的甚至超过HRC 64以上,而模具的交货期却要求越来越短。
大多数塑胶模具材料都是高硬度、耐磨性能好,其加工难度大。
传统工艺广泛采用电火花(EDM)微切削加工成形,生产效率极低。
高速CNC 加工技术对塑胶模具加工工艺产生了巨大影响,它改变了传统模具加工所采用的“电火花→抛光”等复杂冗长的工艺流程,甚至可用高速切削加工替代原来的全部工序。
高速铣削的技术特点及在模具加工的应用

削力很小,这就有利于加工复杂模具型腔中一些细筋和薄壁 , 其壁厚甚至可以小于 l m。业内已应用到薄壁的壁厚分别为 m 0r . m、0 m 2 a . m和 0 m 3 . m,薄壁高度为 2 m 4 0 m的特殊零件加工。
已成为先进制造技术 的一个重要组成部分。
随着市场竞争的需要 , 产品更新换代速度加快 , 对模具的生产效率和制造质量提出了越来越高的要求, 许多原来被认为
优秀的加工方法就逐渐暴露出问题 , 不适应时代的要求, 如电火花加工是一种靠放电烧蚀的“ 微切削” 工艺, 对工件表面进行
局部高温放电烧蚀, 加工后的型腔类零件一般还要进行费力、 费时的研磨和抛光 , 生产效率低, 在某种程度上制约了新产品 开发速度。高速铣削加工技术的出现,为模具制造技术开辟了一条崭新的道路,它能在较短的时间提供给客户满意的模具。
1高速铣削技术特点及模具加工的优越性
1 高速铣削技术缩短了模具的制造周期 . 1
高速铣削加工相对于传统的切削加工 ,由于切削机理不同,单位时间的金属材料切除率提高了 3% 6%,切削力降低 0 一0
了 3%, 0 刀具的切削寿命提高了7 %, 0 加工效率提高了, 从而缩短了产品的制造周期。 在模具的高淬硬钢件(R 4一 R 6) H C 5H C 5
结果整个凹模加工工效提高 5 ,表面粗糙度达 R O 5 0 1 倍 a. ~ .a 2 4m,质量完全符合要求。
1 高速铣削技术能加工形状复杂的薄壁模具零件 . 3 由高速L削机理可知, 刃 高速切削时, 加工余量小 , 切削力大为减少, 切削过程变得比较轻松。 高速切削可以加工淬火钢 ,
机械制造中的机械加工高速切削技术

机械制造中的机械加工高速切削技术高速切削是机械加工领域中的一项重要技术,它在工件加工过程中使用高速切削工具,以较大的进给速度和转速进行切削,提高了加工效率和加工质量。
本文将介绍机械加工高速切削技术的原理、特点以及在机械制造中的应用。
一、高速切削技术的原理高速切削技术是基于高速运动的切削工具和工件之间的相对运动原理。
在高速切削过程中,切削工具以较高的转速和进给速度与工件接触,形成切屑并进行切削。
相比传统的慢速切削,高速切削具有以下特点:1. 切削速度较快:高速切削在保持刀具刃口整齐的情况下,增大刀具转速和进给速度,从而大幅提高了切削效率。
2. 切削温度较低:高速切削由于切削时间短,切削工具与工件接触时间减少,从而减少了热量在切削区域的积累,使得切削温度低于常规切削。
3. 切削力较小:高速切削采用较高的转速和进给速度,在单位时间内切削的材料量相对较大,切削力得到了有效分散,从而降低了切削力的大小。
二、高速切削技术的应用1. 提高生产效率:高速切削技术在机械制造中广泛应用,能够显著提高生产效率。
通过提高切削速度和进给速度,生产厂商可以在较短时间内完成更多的加工任务,提高了机械加工的效率。
2. 提高加工精度:高速切削技术具有切削温度低、切削力小等特点,能够减小热变形和机械振动对工件加工精度的影响,提高了加工精度和表面质量。
3. 增加工件材料种类:高速切削技术在闪光电火花加工、超硬材料和薄壁工件高速切削等领域应用广泛。
高速切削通过较高的转速和进给速度,能够更好地适应不同材料的加工需求。
4. 降低加工成本:高速切削技术通过提高加工效率和降低切削力,可以减少切削时间和刀具磨损,从而降低了加工成本。
三、机械加工高速切削技术的挑战与发展高速切削技术在机械制造中的应用受到了一些挑战,如切削热问题、切削润滑和冷却问题等。
同时,随着高速切削技术的发展,一些新的切削方式如超声波切削、激光切削等也受到了广泛关注。
为了进一步推动高速切削技术的发展,需要加强研究,探索新的切削理论和方法。
模具高速铣削加工的技术特点及应用

太 局 域 网 ( t r t 进 行 数 据 传 输 , 度 可 达 Eh n ) ee 速
2 0k 。 0 b
具, 提高转 速和每齿进 给量有利 于降低刀 具磨损 。
目前常用 的进给速度范围为(0~ 0 / i, 2 3 )m mn 如采
维普资讯
第7 卷
第1 期
20 年 1 07 月
科
学
技
术
与 工Biblioteka 程 Vo. No 1 Jn 0 7 17 . a .2 o
17 '8 9 20 ) - 120 6 1 11 (0 7 10 1 -5
S in eT c n lg n n ie r g ce c e h o o y a d E g n e i n
用大导程滚珠丝杠传动 , 进给速度 可达 6 / i; 0m m n
精度稳定 , 还可防止切 削时刀具振颤。采用模 态分
析和有限元结构计算等设计手段 , 优化机床支撑部 件结构。采用封 闭、 对称 的整体铸造床 身 , 配有 并
密布的加强筋 以确保机床稳定性 。
12 机床主轴 .
高速铣 削机 床 主轴 的转 速 范 围为 (000— 1 0 1000 / i, 0 0 )m mn 主轴功率大于 1 W。通过 主轴 5k
15 冷却润滑 . 高速加 工采 用 带涂 层 的硬 质合 金 刀具 , 高 在 速、 高温的情 况下 不用切 削液 , 削效率 更高。采 切 吹走切削区产生 的切 屑 , 走切削 热 , 带 经雾化 的润 滑油在刀具刃部 和工件表 面形成 一层极 薄 的微 观 保护膜 , 可延长刀具寿命并提高加工表面质量 。
高速铣削加工技术的主要优点及应用介绍

高速铣削加工技术的主要优点及应用介绍由于生产的发展和产品更新换代的速度加快,对模具的生产效率和制造质量提出了越来越高的要求,于是电火花加工存在的问题就暴露出来。
所谓高速铣削是指主轴转速可达10000?C80000转/分,快速进给速度可达30-40米/分,加速度可达1g,换刀时间可提高到1-2秒并可获得粗糙度Ra0.6mm以上,还可以加工硬度达60HRC的模块。
形成对电火花加工的挑战,它与传统铣削加工相比,具有温升低热变形小等优点。
从物理本质上来说,电火花加工是靠放电烧蚀的“微切削”工艺。
对加工过程非常之缓慢表面进行局部高温放电烧蚀过程中,工件表面的物理机械性能会受到一定程度的损伤,常在型腔表面形成微细裂纹,表面粗糙度也达不到模具的要求,因而还有进行费力,费时手工研磨和抛光。
因此,生产效率低,质量不稳定,模具已成为新产品开发速度的一关键因素,与电火花加工相比,高速铣削加工的主要优点:1、产品质量好。
高速铣削以高于常规切削速度10倍左右的切削速度对零件进行高速加工,毛坯材料的余量还来不及充分变形在瞬间被切离工件、工件表面的残余应力非常小;切削过程的绝大多数热量约95%被切削屑带走,工件热变形小;高速加工过程中,机床主轴高速运转,激振频率远离“机床—刀具—工件”系统的固有频率范围,加工过程平稳无冲击。
因此,零件的加工精度高,表面质量好,粗糙度可达0.6mm,型腔表面质量可达到磨削水平。
2、生产效率高。
用高速铣削加工的模具,可在一次装夹中完成粗、精加工和模具零件其他部位的机械加工,即所谓“一次过”技术,不需后续的手工研磨与抛光,又容易实现加工过程自动化。
它还能加工形状复杂的零件和薄壁零件。
由于高速切削时切削力大为减少,尤其是横向(Py)切削力很小,这就有利于加工复杂模具型腔中一些细筋和薄壁,其壁厚甚至小于1mm。
总之高速铣削完全符合现代制造技术“高效率、高精度和高自动化”的发展方向,有广阔的应用前景。
而电火花成型加工对一些尖角、窄槽、深小孔和过于复杂的型腔表面和精密加工还是有用的。
超高速加工技术在铣削加工中的应用

超高速加工技术在铣削加工中的应用近年来,随着科技的进步和制造业的发展,超高速加工技术逐渐应用于各个领域,其中之一就是铣削加工。
超高速加工技术以其独特的加工方式和高效的加工速度得到了广泛的关注和应用。
本文将探讨超高速加工技术在铣削加工中的应用,以及其带来的创新和改变。
首先,超高速加工技术在铣削加工中的应用使得加工效率大幅提升。
相较于传统的加工方法,超高速加工技术通过加快刀具的进给速度和转速,减小切削力和切削温度,从而有效地降低了加工时间。
这使得铣削加工变得更加快速和高效,大大提高了生产效率。
同时,超高速加工技术还可以在相同的加工时间内完成更多的切削量,进一步提高了加工效率。
其次,超高速加工技术在铣削加工中的应用还优化了产品的表面质量。
传统加工方法由于切削速度较慢,在加工过程中会产生较大的切削力和切削热量,容易引起刀具磨损和工件表面质量不良的问题。
而超高速加工技术通过高速的切削和冷却方式,有效地降低了切削力和切削温度,减少了刀具磨损和工件表面粗糙度的问题。
这使得产品的表面质量得到了极大的提升,满足了对高精度产品的需求。
此外,超高速加工技术在铣削加工中的应用还带来了新的设计理念和机制。
传统加工方法由于切削精度和加工速度的限制,对产品的设计和制造造成一定的限制。
而超高速加工技术以其快速的加工速度和高精度的切削精度,为设计师提供了更多的自由度和创造力。
设计师可以设计更为复杂和精细的产品结构,实现更多样化的产品需求。
另外,超高速加工技术还带来了新的机制,例如钻石刀具的应用和新型冷却系统的研发,进一步提高了加工效率和产品的质量。
最后,超高速加工技术在铣削加工中的应用也面临着一些挑战和问题。
一方面,超高速加工技术对刀具和冷却系统的要求较高,增加了设备投资和维护成本。
另一方面,超高速加工技术的应用范围有一定的限制,只适用于某些材料和形状的加工。
因此,在实际应用中需要根据具体情况进行技术选择和优化。
综上所述,超高速加工技术在铣削加工中的应用带来了诸多创新和改变。
先进制造工艺--高速切削技术
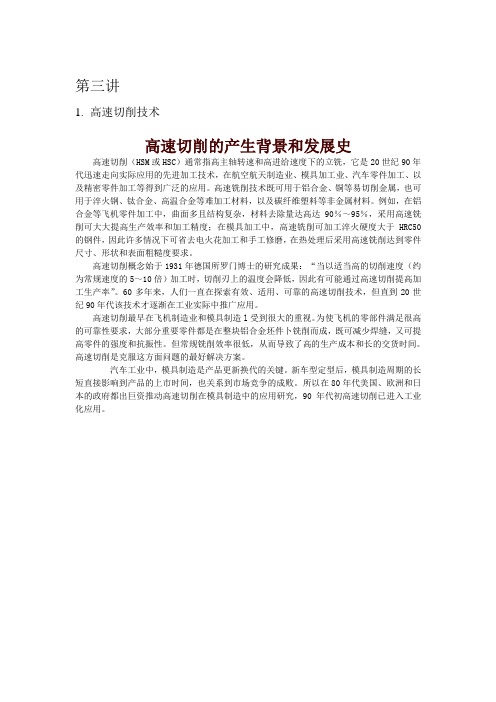
第三讲1.高速切削技术高速切削的产生背景和发展史高速切削(HSM或HSC)通常指高主轴转速和高进给速度下的立铣,它是20世纪90年代迅速走向实际应用的先进加工技术,在航空航天制造业、模具加工业、汽车零件加工、以及精密零件加工等得到广泛的应用。
高速铣削技术既可用于铝合金、铜等易切削金属,也可用于淬火钢、钛合金、高温合金等难加工材料,以及碳纤维塑料等非金属材料。
例如,在铝合金等飞机零件加工中,曲面多且结构复杂,材料去除量达高达90%~95%,采用高速铣削可大大提高生产效率和加工精度;在模具加工中,高速铣削可加工淬火硬度大于HRC50的钢件,因此许多情况下可省去电火花加工和手工修磨,在热处理后采用高速铣削达到零件尺寸、形状和表面粗糙度要求。
高速切削概念始于1931年德国所罗门博士的研究成果:“当以适当高的切削速度(约为常规速度的5~10倍)加工时,切削刃上的温度会降低,因此有可能通过高速切削提高加工生产率”。
60多年来,人们一直在探索有效、适用、可靠的高速切削技术,但直到20世纪90年代该技术才逐渐在工业实际中推广应用。
高速切削最早在飞机制造业和模具制造l受到很大的重视。
为使飞机的零部件满足很高的可靠性要求,大部分重要零件都是在整块铝合金坯件卜铣削而成,既可减少焊缝,又可提高零件的强度和抗振性。
但常规铣削效率很低,从而导致了高的生产成本和长的交货时间。
高速切削是克服这方面问题的最好解决方案。
汽车工业中,模具制造是产品更新换代的关键。
新车型定型后,模具制造周期的长短直接影响到产品的上市时间,也关系到市场竞争的成败。
所以在80年代美国、欧洲和日本的政府都出巨资推动高速切削在模具制造中的应用研究,90年代初高速切削已进入工业化应用。
图16 高速切削在生产应用中的发展历程图17 采用高速切削后产品质量提高的历程a一硬质合金切钢 b一硬质合金切铸铁c—CBN切铸铁图16是德国宝马公司(BMW)采用高速切削的历程。
高速铣削技术简介
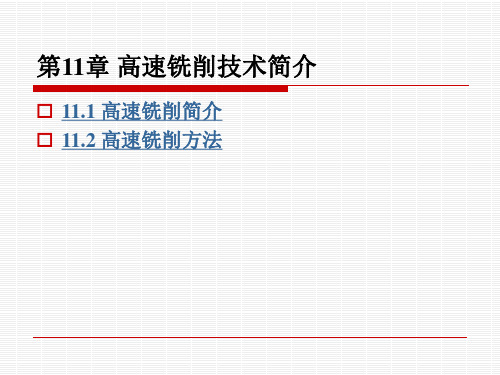
1)高速主轴单元 高速主轴大多采用内置式马达驱动,主轴机电 一体化,直接传动,转速达到每分钟几万转。其要求应用各种不同的 主轴轴承和主轴润滑和冷却来达到更高的载荷值。
11.1 高速铣削简介
1.粗加工的高速铣削要求: 1)刀具以5°倾角,采用螺旋或倾斜方式进入工件材料。 根据刀具材料、工件材料、机床和CNC系统的能力和条件,使其 进给率与主轴转速之比值应该达到最佳。 2)即使在减少进给量或刀具停止时也要避免急剧改变切削方向, 以防止刀具损坏。 3)为了平稳从容地加工硬化了的材料,径向进给量不得大于 6%~8%的刀具直径,深度进给量最大不超过5%的刀具直径。 2.半精加工的高速铣削要求: 1)避免急剧的铣削运动。 2)为了避免过切,刀具不采用螺旋或斜坡方式下刀,直接下沉到 下一个切削平面。 3)径向切削量小于6%~8%的刀具直径。 4)满足均匀切削条件
上一页 返回
11.2 高速铣削方法
1.进退刀控制 与常规铣削相比较,高速铣削在进退刀控制上要求更高,应尽量 采用斜线、圆弧或螺旋线方式及在轮廓、曲面切向进退刀,保证圆弧 过度,层间进退刀要减少进刀/退刀的相对高度,精加工时最好从工件 外部进刀。 2.移刀方法 在双向切削加工中,为避免行间过渡时方向急剧改变,可采用空 间内向圆弧走刀、空间外向圆弧走刀、“高尔夫”式走刀等方式加工。 如图11-1所示。
我们知道,在常规切削过程中,切削温度和刀具磨损限制了切削 线速度的提高,但远在60多年前,卡尔·索罗门博士(Salomon)发 现,当切削线速度进一步提高,超过某个临界值的时候,切削温度和 切削力反而变小,然后随着切削线速度的继续提高,温度和切削力又 急剧增加。这就使得高速加工(High Speed Machining)成为可能。
简述高速切削的优点

简述高速切削的优点
高速切削是一种在高速下进行金属切削的加工方法,具有许多优点,包括: 1. 高精度:高速切削可以实现高精度加工,因此在制造精密零部件和高速列车部件等领域中广泛应用。
2. 高效率:高速切削可以在较短的时间内完成加工,从而提高生产效率,降低生产成本。
3. 高硬度材料加工能力:高速切削适用于加工高硬度材料,如钛合金、硬质合金和不锈钢等。
4. 加工变形小:高速切削加工过程中变形小,能够保证零部件的精度和稳定性。
5. 可实现多道工序:高速切削可以实现多道工序,缩短生产周期,降低生产成本。
除了以上优点外,高速切削还具有一些其他特点,例如:
1. 可加工复杂形状:高速切削适用于加工复杂形状的零部件,如航空航天部件、汽车发动机部件等。
2. 不会产生热:高速切削不会产生热,因此加工过程中不会对零部件产生变形或损坏。
3. 适用于高温环境:高速切削适用于高温环境下的加工,如航空航天和能源领域。
4. 可加工的材料种类多:高速切削适用于加工多种材料,如金属、陶瓷和复合材料等。
综上所述,高速切削是一种高效、高精度、高硬度材料和复杂形状加工的理
想方法,具有广泛的应用前景和发展空间。
高速加工技术及应用
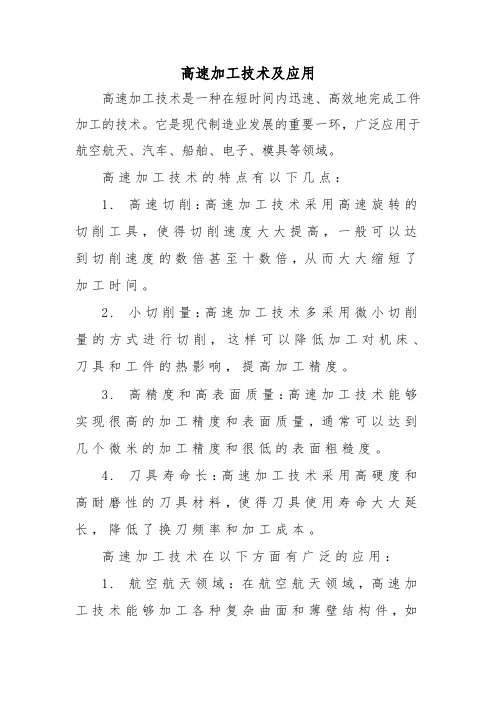
高速加工技术及应用高速加工技术是一种在短时间内迅速、高效地完成工件加工的技术。
它是现代制造业发展的重要一环,广泛应用于航空航天、汽车、船舶、电子、模具等领域。
高速加工技术的特点有以下几点:1.高速切削:高速加工技术采用高速旋转的切削工具,使得切削速度大大提高,一般可以达到切削速度的数倍甚至十数倍,从而大大缩短了加工时间。
2.小切削量:高速加工技术多采用微小切削量的方式进行切削,这样可以降低加工对机床、刀具和工件的热影响,提高加工精度。
3.高精度和高表面质量:高速加工技术能够实现很高的加工精度和表面质量,通常可以达到几个微米的加工精度和很低的表面粗糙度。
4.刀具寿命长:高速加工技术采用高硬度和高耐磨性的刀具材料,使得刀具使用寿命大大延长,降低了换刀频率和加工成本。
高速加工技术在以下方面有广泛的应用:1.航空航天领域:在航空航天领域,高速加工技术能够加工各种复杂曲面和薄壁结构件,如发动机叶片、航空航天零件等,提高了零件的精度和表面质量。
2.汽车领域:高速加工技术在汽车制造中主要用于零部件的加工,如发动机缸体、座椅滑块等,能够提高加工效率和产品质量。
3.船舶领域:高速加工技术在船舶制造中主要用于船体结构和轴承加工,如船体钢板切割、轴承的外圈和内圈加工等,提高了加工速度和质量。
4.电子领域:高速加工技术在电子领域主要用于半导体器件的切割和加工,如芯片切割、光纤连接器加工等,提高了加工精度和产品性能。
5.模具领域:高速加工技术在模具制造中主要用于模具的精细加工,如模具的深孔加工、细小结构的加工等,提高了模具的加工精度和寿命。
高速加工技术的发展对于提高制造业的竞争力和产品质量具有重要意义。
随着材料科学和机械加工技术的不断发展,高速加工技术将在更多领域得到应用,并不断推动制造业的发展。
高速铣削加工技术概述

1 引言
高速铣削加工 不但具有加工 速度高 以及 良好 的加工精度
和表 面质量 , 而且与传统 的切削加 工相 比具有温 升低 ( ̄ / II J
降低 了 3 %,刀具 的切 削寿命提 高了 7 %。还 可加工淬硬零 0 0
件, 许多零件一次装夹可完成粗 、 半精和精加 工等全部 工序 , 对 复杂型面也 能达 到零件表面质量要求 , 进而提高 了加工生产率
20 0 8年 1 1月
广 西轻 工 业
G A G JI N Io IH D sR U N Ⅺ (瓜 A FLG TI u T Y ) N 机 械 与 电 气
第 1 期( 1 总第 1 0 ) 2 期
高 速铣 削 加 工技 术概 述
高发 伟
( 东 东阳 光铝业 股份有 限公 司, 东 韶 关 5 7 1 广 广 1 2) 2
21 可部分替代某些工艺 .
高 速切削时 的切 削力 小 , 有较高 的稳 定性 , 可加工高 质量
的薄壁零件 。 采用 分层铣削 的方法 , 可切削出壁厚 02 m, .r 壁高 a 2 rm的薄壁零件 。刀刃和工件的接触 时间非 常短 , 0 a 避免 了侧
壁 的变形 。
如 电火花加工、 磨削加工等高强度和高硬度 加工也是 高速
切 削的一大 特点 ,高速切削 已可 加工硬度 达 HR 6 C 0的零件。
3 高速 铣削加 工在 螺纹 加工 中的应用
用高速铣削刀盘加工螺纹 的方法又称旋风铣削法 , 加工 其 表面是刀齿旋转形成 的回转表 面在不同连续位置的包络面 , 它
一
采用带涂层的硬质合金刀具加工模具 , 直接将 淬硬工具钢一次
进制造技术领域重要 的研究方 向之一【3 1】 .。 长期以来 , 们对模具 的加工一 直采 用铣 削——磨削或者 人
高速铣削加工讲解

4)行切的端点采用圆弧连接,避免直线连接;
高 5)应尽量避免全力宽切削;
速 6)残余量加工或清根加工是提高加工效率的重要手段,一般应采用
铣 多次加工或采用系列刀具从大到小分次加工,直至达到所需尺寸,避
削
免用小刀一次加工完成;
加
7)刀具轨迹编辑优化功能非常重要,应避免多余空刀,可通过对刀 具轨迹的摄像、复制、旋转等操作来避免重复计算;
是二十世纪九十年代迅速走向实际应用的先进加
工技术 。
高 高速铣削可用于铝合金、铜等易切削家属和淬 速 火钢、钛合金、高温合金等难加工材料以及碳纤 铣 维塑料等非金属材料。 削 在模具加工中,高速铣削可加工淬火硬度大于 加 HRC50的钢件,因此许多情况下可省去电火花加 工 工和手工修磨,在热处理后采用高速铣削达到零
23
数 控
5.3 刀杆结构
加 工
技 高速铣削刀具,分为整体式和机夹式两类。
术
当机床最高转速达到15000 转/分时,通常
需要采用HSK 高速铣刀刀杆,或其他种类的
高 短柄刀杆。
速
铣
削
加
工
24
数 控
刀杆夹紧刀具的方式
加 工
技 有侧固式、弹性夹紧式(a)、液压夹紧式
术 (b)和热膨胀式(c)等。侧固式难以保证刀具
工 (5)每齿进给量为常数可达到最好的表面
加工质量。
18
数 控
高速铣削的工艺特点:
加
工
技
(1)很窄的公差带;
术
(2)浅切削;
(3)高的切削速度(达到机床极限);
高
(4)用斜坡和螺旋式进刀;
速
(5)大量采用分层切削;
高速铣削加工技术

高速铣削加工技术,具有许多优秀的特点,如可以获得很光滑的表面质量,容易实现零件的精细结构的加工而避免了大量电极制造和耗时的放电加工,可以有效地对高硬度材料进行加工,特别是可以实现脆性材料和薄壁零件的加工等。
同时简化了生产的工序,使绝大多数的工作都集中在高速加工中心上完成。
使用高速加工技术,不仅要有适合高速加工的设备-高速加工中心,还要选择适合进行高速加工的刀具。
另外采用适合高速加工的编程策略也至关重要。
一、高速加工编程时主要关心的问题采用高速铣削加工编程的原则主要与数控加工系统,加工材料,所用刀具等方面有关。
使用cam系统进行数控编程时,刀具选择、切削用量以及选择合适的加工参数可以根据具体情况设置外,加工方法的选择就成为高速加工数控编程的关键。
如何选择合适的加工方法来较为合理、有效地进行高速加工的数控编程,需要考虑的问题主要与以下几个方面相关:(1)由于高速加工中心具有前视或预览功能,在刀具需要进行急速转弯时加工中心会提前进行预减速,在完成转弯后再提高运动速度。
机床的这一功能主要是为了避免惯性冲击过大,从而导致惯性过切或损坏机床主轴而设置的。
有些高速加工中心尽管没有这一功能也能较好地承受惯性冲击,但该情况对于机床的主轴也是不利的,会影响主轴等零件的寿命。
在使用c am进行数控编程时,要尽一切可能保证刀具运动轨迹的光滑与平稳。
(2)由于高速加工中,刀具的运动速度很高,而高速加工中采用的刀具通常又很小,这就要求在加工过程中保持固定的刀具载荷,避免刀具过载。
因为刀具载荷的均匀与否会直接影响刀具的寿命、对机床主轴等,在刀具载荷过大的情况下还会导致断刀。
(3)采用更加安全和有效的加工方法与迅速进行安全检查校验与分析。
二、高速加工编程采用的编程策略1、采用光滑的进、退刀方式。
在cimatron系统中, 有多种多样的进、退刀方式,如在走轮廓时,有轮廓的法向进、退刀,轮廓的切向进、退刀和相邻轮廓的角分线进、退刀等。
铣削加工中的高速铣削技术

铣削加工中的高速铣削技术现代制造业中,铣削加工技术是十分重要的一部分。
如果能够用更高效的方式进行铣削工作,将会极大提高生产效率和降低成本。
因此,高速铣削技术被越来越多地应用到了现代生产中。
高速铣削技术与传统铣削相比,最显著的不同是其搭载了更先进的高速机床和工具系统。
这些机床和工具能够高效地运作,并在短时间内完成更大量的工作。
同时,高速铣削还使用了更高级的加工参数,例如更大的切削速度、进给速度和毛坯清理速度等。
高速铣削的最大特点是其高效率,其切削速度相比于传统铣削可以提高至10倍以上,而且对切削刃的磨损及其表面质量也大有好处。
大的切削速度需求对机床特性也提出更高的要求,对其刚度、动刚性等机床特性要求更加优良,这也是高速机床设计发展的必然要求。
高速铣削一般可以分为两类:一是高速加工中的tiny 中心铣削,二是高速刀具铣削。
前者是传统铣削工艺改进的产物,主要运用于硬质度较高的材料(如钢、铁、铜等)的加工中。
因为这些材料比较脆弱,且热膨胀系数较低,所以切削时也更容易产生比较严重的变形和加热问题。
高速加工中的 tiny 中心铣削的操作将更为精细,能够使切削过程更加平稳。
同时,由于加工参数的优化,也可以减轻机床的负担,增加刀具的使用寿命。
高速刀具铣削的主要应用是在可塑性工件的加工中,例如铝合金、塑料以及一些轻金属。
这些材料具有较高的可塑性,And 切削过程时变形也不如传统的金属材料严重。
而且,高速刀具铣削可以优化加工参数,大大减少加热和变形问题,提高加工效率。
在这种情况下,高速铣削技术可以极大地提高加工质量、减少浪费、降低成本。
不过,高速铣削技术还存在一些问题要注意。
首先是刀具寿命方面的问题。
由于刀具在高速切削过程中容易变形、断裂,因此需要提出更加精准的切削参数设计。
其次是机床质量方面的要求。
由于高速铣削需要更高的动刚性及刚度要求,因此机床设计以及部件的韧性定位,变形成为了一个需要非常注意的问题。
总的来说,高速铣削技术的应用将会极大地提高加工效率、降低成本。
模具高速铣削加工技术概述

模具高速铣削加工技术概述
随着现代制造业的迅速发展,越来越多的企业开始采用模具高速铣削加工技术来提高生产效率和产品质量。
模具高速铣削加工技术是一种利用高速旋转的切削刀具来对工件进行加工的技术,具有具有加工精度高、加工效率快、精度稳定等优点,成为许多企业的首选工艺之一。
模具高速铣削加工技术的特点在于高速旋转的刀具与工件之间的相对运动速度非常快,使得在相对运动时切削力非常大,对工件进行快速加工,减少加工过程中的切削阻力,从而加快加工速度,大大提高生产效率。
在模具高速铣削加工技术中,铣床是一种非常重要的工具,铣床使用旋转刀具将工件进行加工。
在高速铣削加工过程中,铣床的结构设计、加工精度和材料的选择都是非常重要的,尤其是材料的选择,过硬的材料可以更好地提高铣床的耐磨性和使用寿命,从而更好地满足企业的生产需求。
模具高速铣削加工技术的发展历程可以追溯到20世纪80
年代,当时日本企业就开始采用该技术来加工汽车配件、电子零件等行业产品。
在90年代,模具高速铣削加工技术开始逐
渐成熟,广泛应用于制造业中,使得中国等国家也开始投入研发模具高速铣削加工技术。
在模具高速铣削加工技术的应用中,数控技术也是非常重要的一部分。
数控技术可以让操作工人根据实际生产需求来控
制铣床的运行速度、刀具的旋转速度、调整加工精度等参数,从而可以更好地满足不同客户的定制需求。
总体来说,模具高速铣削加工技术是一种重要的制造工艺,是许多行业中的不可缺少的一部分。
在未来,模具高速铣削加工技术还将继续得到改进和完善,为各行各业的企业提供更加优质的加工服务。
高速铣削加工应用及技术研究

高速铣削加工应用及技术研究摘要:高速铣削工艺采用超硬材料刀具进行高速加工,充分利用技术应用的优势。
刀具和铣削参数的选择是测试高速铣削的两个主要区域,并向有关各方提供技术参考。
关键词:高速加工;铣削高速铣削是一种重要的材料加工技术,在生产过程中,使用超硬材料加工工具能更快地切削材料,获得优质加工产品适当尺寸和形状。
高速铣削比常规铣削更准确、更高效。
切削技术在高速铣削中是一种重要的形式,通常用于加工汽车、航天等领域的零件。
此技术的应用能够有效地与复杂曲面操作一起运行。
简而言之,高速铣削是一种高质量的加工技术,需要密集的研究工作才能对技术要素形成准确的理解。
一、高速铣削加工的原理第一个提出高速铣削理论的人是德国物理学家萨洛蒙,人们把铣削速度与温度的曲线命名为“萨洛蒙曲线”。
该曲线表明铣削温度与速度呈正相关。
但是,在峰值过后,铣削速度与温度成负相关。
峰值与材料有关,而对于所有材料,峰值均是存在的,峰值所在的区域就是刀具无法承受的温度范围,经过试验验证,高速钢、硬质合金、涂层和陶瓷刀具均在这种温度下不能正确切削,当时的理论体系因技术条件差而不完善。
但是,这种想法正朝着正确的方向发展,在这个范围之外,铣削效率可以进一步提高。
理论上说,科学家们在60年代开始进行高速加工试验,试验是用加农炮将待加工零件射向刀具的。
其结果是在超过高温区后,切屑的形成和低速区完全不同,当铣削速度从低速转向高速时,切屑从皮带状变为碎屑,铣削力逐渐增大和减小,表明高速铣削加工不同于低速铣削方法。
1977年进行了第一次高速铣削,检验出高速铣削中的铣削速度比传统铣削高出2~3倍,铣削强度提高了70%。
然后启动了高速铣削的系统研究,科学界开始了为轻质合金加工材料进行高速加工的先进加工研究项目,对高速铣削技术进行相关理论研究。
该研究表明,高温区域之外的铣削强度是由于铣削速度的负面影响。
用于制造的材料的导热系数决定了刀具的寿命。
铝合金处理速度1560-4500m/min,随后,40多家企业和机械工程研究所在几所大学进行了联合研究,验证了高速铣削所需的机床、工具和控制设备,并分析了相关技术,各种常用材料验证(钢、铸铁、专用、铝、铝镁铸造、铜合金等)的加工和应用数据,在高速铣削技术中的应用及在生产环境中的应用具有明显的经济效果。
模具高速铣削加工技术

模具高速铣削加工技术引言模具在现代制造业中起着重要的作用,它是生产各种零部件和产品的基础工具。
然而,传统的模具加工技术存在一些局限性,例如低效率、加工精度受限等问题。
为了克服这些问题,模具高速铣削加工技术应运而生。
本文将介绍模具高速铣削加工技术的基本原理、优势和应用,并提供一些实用的工艺技巧。
基本原理模具高速铣削加工技术是采用高转速切削工具和高速进给速度来加工模具的一种先进技术。
与传统的慢速加工相比,高速铣削具有更高的加工效率和更好的加工质量。
高速铣削的基本原理如下:1.高速切削工具:采用高硬度和高韧性的切削工具,如硬质合金铣刀或陶瓷铣刀。
这些切削工具能够承受高速切削的热和压力,同时具有较长的使用寿命。
2.高转速:利用高速切削工具的转速,通常在数千转/分以上,可以实现更快的切削速度和更高的切削力。
3.高速进给:采用高速进给速度,通常在数米/分钟以上,可以实现更快的进给速度和更高的切削深度。
优势模具高速铣削加工技术相比传统的慢速加工技术具有以下几个明显的优势:1.高效率:高速铣削能够以更快的速度完成加工任务,显著提高了生产效率。
在相同时间内,可以加工更多的模具零部件,提高了生产能力。
2.高精度:高速铣削由于切削速度和切削力较高,因此可以获得更高的加工精度和表面质量。
这对于一些对模具形状和尺寸要求较高的产品尤为重要。
3.粗加工和精加工一体化:高速铣削可以实现粗加工和精加工一体化,减少加工工序和装夹次数,提高了加工效率和加工精度。
4.节约成本:高速铣削由于加工效率高,可以减少加工时间和人力成本。
同时,由于切削工具的寿命较长,可以降低刀具消耗和更换成本。
应用模具高速铣削加工技术在各个领域都有广泛的应用,特别是在汽车制造、航空航天、电子通讯等高精度和复杂模具加工领域。
以下是一些常见的模具高速铣削应用:1.汽车模具:汽车模具具有较高的精度和复杂的形状要求,高速铣削可以高效地完成各种汽车模具的加工,如车身模具、发动机模具等。
铣削加工方法在高速加工中的应用探讨

铣削加工方法在高速加工中的应用探讨以提高加工效率,提高加工质量,降低成本,简化加工工艺流程为视角,在高速加工领域对铣削加工方法作了一定的探讨。
标签:高速加工;高速铣削技术;粗加工;精加工1 高速铣削技术高速切削技术,是以比常规高10倍左右对零件进行切削加工的一项先进制造技术。
实践证明,当切削速度提高10倍,进给速度提高20倍,远远超越传统的切削“禁区”后,切削机理发生了根本的变化。
其结果是:单位功率的金属切除率提高了30%-40%,切削力降低了30%,刀具的切削寿命提高了70%,留于工件的切削热大幅度降低,切削振动几乎消失;切削加工发生了本质性的飞跃。
在常规切削加工中备受困惑的一系列问题亦得到了解决,真可谓是集高效、优质、低耗于一身的先进制造技术,是切削加工新的里程碑。
在切削速度上,铜合金900-5000 m/min;钛合金100-1000 m/min;铝合金1000-7000 m/min;钢350-2000 m/min;铸铁400-2500m/min。
各种材料的高速切削进给速度范围为2-25 m/min。
2 高速铣削技术的优势2.1 机械加工效率大大提高高速铣削加工允许使用较大的进给率,单位时间的材料切除率提高3~6倍,加工时间缩短50%~70%。
当加工需要大量切除金属的零件时,可使加工时间大大减少。
2.2 切削力降低,加工变形小高速铣削和常规切削相比,切削力至少可降低30%。
这对于加工刚性较差的零件来说可减少加工变形,使一些薄壁类精细工件的铣削加工成为可能。
2.3 加工质量得到优化因为高速旋转时刀具切削的激励频率远离工艺系统的固有频率,不会造成工艺系统的受迫振动,保证了较好的加工状态。
由于切削深度、切削宽度和切削力都很小,使得刀具、工件变形小,保持了尺寸的精确性,另外也使得切削破坏层变薄,残余应力小,实现了高精度、低粗糙度加工。
2.4 加工工艺流程简洁化常规铣加工不能加工淬火后的材料,淬火变形必须进行人工修整或通过放电加工解决。
- 1、下载文档前请自行甄别文档内容的完整性,平台不提供额外的编辑、内容补充、找答案等附加服务。
- 2、"仅部分预览"的文档,不可在线预览部分如存在完整性等问题,可反馈申请退款(可完整预览的文档不适用该条件!)。
- 3、如文档侵犯您的权益,请联系客服反馈,我们会尽快为您处理(人工客服工作时间:9:00-18:30)。
高速铣削加工技术的主要优点及应用介绍由于生产的发展和产品更新换代的速度加快,对模具的生产效率和制造质量提出了越来越高的要求,于是电火花加工存在的问题就暴露出来。
所谓高速铣削是指主轴转速可达10000?C80000转/分,快速进给速度可达30-40米/分,加速度可达1g,换刀时间可提高到1-2秒并可获得粗糙度Ra0.6mm以上,还可以加工硬度达60HRC的模块。
形成对电火花加工的挑战,它与传统铣削加工相比,具有温升低热变形小等优点。
从物理本质上来说,电火花加工是靠放电烧蚀的“微切削”工艺。
对加工过程非常之缓慢表面进行局部高温放电烧蚀过程中,工件表面的物理机械性能会受到一定程度的损伤,常在型腔表面形成微细裂纹,表面粗糙度也达不到模具的要求,因而还有进行费力,费时手工研磨和抛光。
因此,生产效率低,质量不稳定,模具已成为新产品开发速度的一关键因素,与电火花加工相比,高速铣削加工的主要优点:1、产品质量好。
高速铣削以高于常规切削速度10倍左右的切削速度对零件进行高速加工,毛坯材料的余量还来不及充分变形在瞬间被切离工件、工件表面的残余应力非常小;切削过程的绝大多数热量约95%被切削屑带走,工件热变形小;高速加工过程中,机床主轴高速运转,激振频率远离“机床—刀具—工件”系统的固有频率范围,加工过程平稳无冲击。
因此,零件的加工精度高,表面质量好,粗糙度可达0.6mm,型腔表面质量可达到磨削水平。
2、生产效率高。
用高速铣削加工的模具,可在一次装夹中完成粗、精加工和模具零件其他部位的机械加工,即所谓“一次过”技术,不需后续的手工研磨与抛光,又容易实现加工过程自动化。
它还能加工形状复杂的零件和薄壁零件。
由于高速切削时切削力大为减少,尤其是横向(Py)切削力很小,这就有利于加工复杂模具型腔中一些细筋和薄壁,其壁厚甚至小于1mm。
总之高速铣削完全符合现代制造技术“高效率、高精度和高自动化”的发展方向,有广阔的应用前景。
而电火花成型加工对一些尖角、窄槽、深小孔和过于复杂的型腔表面和精密加工还是有用的。
两者应该扬长避短,相辅相成。
建议先在厦门、福州、泉州等地有实力的企业,引进高速铣削机床,然后全省逐渐推广。
台州亚古机床设备有限公司。