高速铣削加工效率的一般计算与分析
高速铣加工切削参数研究

; m 母 i 蕊 . 翟《 ! l
跑 ”原则。图 2为刀具厂商提供 的几种 材料 的高速切削 通用范围。
O
损的主要原 因。
( )扩散磨损 在高温作用下 ,刀具与工件接触面 3 间的分子活动能量 大 ,会 产生合 金元 素相互 扩散置 换 ,
■一 图
f=  ̄ fz
t {7 : / , 式中 n ——转数 (/ n ; rmi)
— —
I
—
f
线速度 ( / n ; m mi)
{
图 1
D ——刀具直径 ( m) m ; v f ——进 给速度 ( m mn ; m / i) 卜 进给量 ( n ) m Vr ;
线速度 和每齿 进 给量 的选 择 ,理论 上 与刀具 、 工件 、机床等多个环节有关 ,一般情 况下 ,刀具 厂商在
的切削速度 ,适 当的进给量 ,6 % ~8 % 的刀具大小 的 0 0
径向切深 、小 的轴 向切深 ,也就是通常所 说的 “ 少吃快
e, i\! 三 0 — 、 ;\! . ,、 -, /_ 、3 . , ,、 ; 三 ,. , 、0 0一 ,、 .三
5 机构传动效率的确定 .
( 收稿 1 :2 10 0 ) 3期 0 0 7 1
( 一2) , H 11 = .7 ,叼 = 55 ,满足 了 1 i ] H 2= /3 006 9 m 4.%
参磊 工冷 工 加
WWW. e a| m t wor i k ng1 950 co . r n
21年 2期 0 第 0 0
性 ,此处我们仅计算刀架松开 、锁紧时机构的效率 。 综合上述 因素 ,取 吼 =09 ( 为转 化机构 的效率 ) . ,
高速切削技术研究
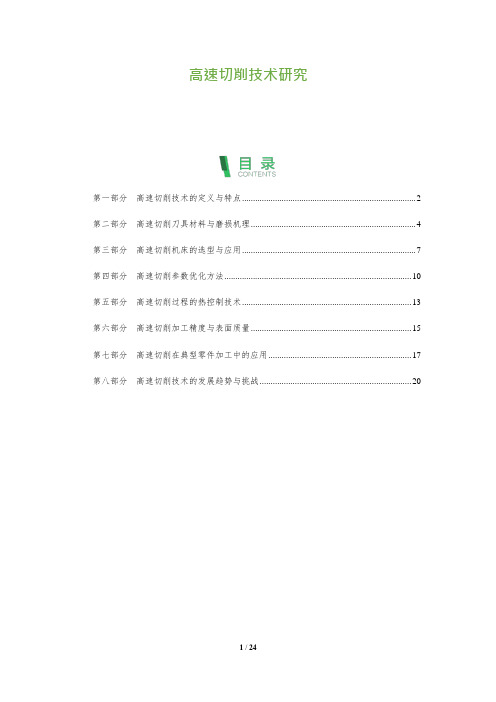
高速切削技术研究第一部分高速切削技术的定义与特点 (2)第二部分高速切削刀具材料与磨损机理 (4)第三部分高速切削机床的选型与应用 (7)第四部分高速切削参数优化方法 (10)第五部分高速切削过程的热控制技术 (13)第六部分高速切削加工精度与表面质量 (15)第七部分高速切削在典型零件加工中的应用 (17)第八部分高速切削技术的发展趋势与挑战 (20)第一部分高速切削技术的定义与特点高速切削技术是一种先进的制造工艺,它通过使用高转速的刀具和优化的切削参数来提高材料去除率、加工精度和表面质量。
该技术的核心在于实现高效率、高质量和高精度的加工过程。
在高速切削过程中,刀具以极高的速度旋转(通常超过每分钟数千转),同时进给速度也相应提高。
这种高速旋转产生的离心力有助于减小切削力和切削热,从而延长刀具寿命并减少工件的热变形。
此外,由于切削力的降低,高速切削还可以减少振动,进一步提高加工精度。
高速切削技术的优势主要体现在以下几个方面:1.高效率:与传统切削相比,高速切削可以显著提高材料去除率,缩短加工时间。
研究表明,高速切削可以提高生产效率达 30%至50%。
2.高精度:高速切削过程中的低切削力可以减少工件的振动,从而提高加工精度。
此外,由于切削热的影响较小,工件的热变形也得到了控制。
3.高质量表面:高速切削产生的切削热较低,这有助于减少工件的烧伤和裂纹,从而获得更好的表面质量。
4.刀具寿命延长:高速切削可以降低切削力,减少刀具磨损,从而延长刀具的使用寿命。
5.节能减排:高速切削技术可以实现更高的材料去除率,从而减少能源消耗和碳排放。
然而,高速切削技术也存在一些挑战,如刀具成本较高、对机床性能要求较高等。
因此,在实际应用中,需要根据具体加工需求和技术条件,合理选择切削参数和刀具,以确保高速切削技术的有效性和经济性。
总之,高速切削技术作为一种先进的制造工艺,具有高效率、高精度、高质量表面等优势,但在实际应用中需充分考虑其成本和设备要求。
高速加工技术

高速加工技术一.起源1931年,德国切削物理学家萨洛蒙(Carl.J.Salomon)博士提出了一个假设,即同年申请了德国专利的所罗门原理:被加工材料都有一个临界切削速度V0,在切削速度达到临界速度之前,切削温度和刀具磨损随着切削速度增大而增大,当切削速度达到普通切削速度的5~6倍时,切削刃口的温度开始随切削速度增大而降低,刀具磨损随切削速度增大而减小。
切削塑性材料时,传统的加工方式为“重切削”,每一刀切削的排屑量都很大,即吃刀大,但进给速度低,切削力大。
实践证明随着切削速度的提高,切屑形态从带状、片状到碎屑状演化,所需单位切削力在初期呈上升趋势,而后急剧下降,这说明高速切削比常规切削轻快,两者的机理也不同。
通过长期的研究,从上世纪90年代中期起,高速加工进入实用化阶段。
用户可以享受高速加工的高效率,高精度和成本优势。
德国OPS-INGERSOLL公司是目前世界上最好的高速加工中心制造商之一。
二.高速加工的定义高速加工是指转速在30,000RPM以上,实际加工切削进给保持8-12m/min的恒定进给。
我们从定义中看出,高速加工的一个关键要素是高速恒定进给。
由于高速加工时,转速上万转,特别在加工高硬度材料时,瞬间产生大量热量,所以必须保持高速进给,使产生的85%以上的热量被铁屑带走。
但在模具加工过程中,硬度通常在HRC50以上,且为复杂的曲面或拐角,所以高速机床必须做到在加工曲面或拐角时仍能高速进给。
另外实际加工中,刀具都有一个最佳切削参数,如能保持恒定进给,对刀具寿命,切削精度和加工表面质量都有提高。
由此看出,高速加工不仅是高速主轴,而且也是机床伺服系统的综合。
事实上,高速切削技术是一个非常庞大而复杂的系统工程,它涵盖了机床材料的研究及选用技术,机床结构设计和制造技术,高性能C NC控制系统、通讯系统,高速、高效冷却、高精度和大功率主轴系统,高精度快速进给系统,高性能刀具夹持系统,高性能刀具材料、刀具结构设计和制造技术,高效高精度测试测量技术,高速切削机理,高速切削工艺,适合高速加工的编程软件与编程策略等等诸多相关的硬件和软件技术。
铣削力计算公式详解

铣削力计算公式详解铣削力是指铣削过程中刀具对工件所施加的力,它是铣削加工过程中重要的参数之一。
铣削力大小的计算对于工件的加工质量、工具的寿命以及加工效率都有着重要的影响。
铣削力的计算公式通常是根据铣削的工艺参数以及材料的性质来推导,下面我们将详细解释铣削力的计算公式。
一、铣削力的基本概念为了更好地理解铣削力的计算公式,首先我们需要了解铣削力的基本概念。
在铣削加工过程中,刀具在与工件接触时会产生力的作用。
这些力包括主轴的进给力、切削力和阻力等。
其中,切削力是指刀具在切削过程中与工件发生力的作用,它是决定加工质量和加工效率的重要因素。
铣削力的大小与工件的材料性质、切削刀具的材料和几何形状、切削速度、进给速度、切削深度等因素密切相关。
因此,在进行铣削加工时,需要对铣削力进行精确地计算和控制,以保证加工质量和工具寿命。
二、铣削力的计算公式在铣削加工中,刀具施加在工件上的切削力可以用力学原理进行计算,一般来说,可以参考以下的铣削力计算公式:1.切削力Fc的计算公式切削力Fc是铣削中最常见的力。
在进行铣削加工时,切削力的大小直接影响着刀具的磨损情况和加工表面的加工质量。
切削力Fc的计算公式通常如下:Fc = kc * ae * ap * f //(1)其中,Fc为切削力,单位为牛顿(N);kc为切削力系数,其大小与材料性质、切削条件和刀具类型等有关;ae为轴向切削深度,单位为毫米(mm);ap为径向切削深度,单位为毫米(mm);f为给进量,单位为毫米/刀齿(mm/tooth)。
切削力Fc的大小与刀具材料、刀具的结构和铣削参数等因素有关。
在实际的工程中,我们需要根据具体的加工情况和工件材料来确定切削力系数kc的数值,然后通过公式(1)来计算切削力Fc的大小。
2.主轴的进给力Fr的计算公式除了切削力之外,铣削加工中还存在着主轴的进给力Fr。
主轴的进给力是指主轴在刀具与工件接触时所施加的力,它也是影响加工质量和加工效率的重要因素。
先进制造工艺--高速切削技术
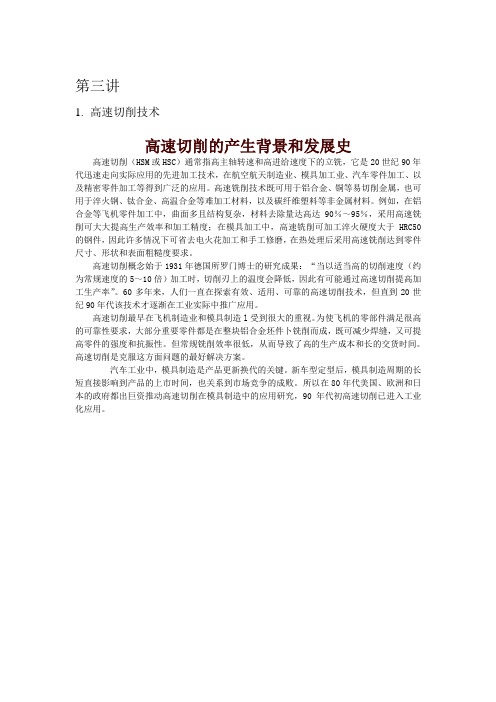
第三讲1.高速切削技术高速切削的产生背景和发展史高速切削(HSM或HSC)通常指高主轴转速和高进给速度下的立铣,它是20世纪90年代迅速走向实际应用的先进加工技术,在航空航天制造业、模具加工业、汽车零件加工、以及精密零件加工等得到广泛的应用。
高速铣削技术既可用于铝合金、铜等易切削金属,也可用于淬火钢、钛合金、高温合金等难加工材料,以及碳纤维塑料等非金属材料。
例如,在铝合金等飞机零件加工中,曲面多且结构复杂,材料去除量达高达90%~95%,采用高速铣削可大大提高生产效率和加工精度;在模具加工中,高速铣削可加工淬火硬度大于HRC50的钢件,因此许多情况下可省去电火花加工和手工修磨,在热处理后采用高速铣削达到零件尺寸、形状和表面粗糙度要求。
高速切削概念始于1931年德国所罗门博士的研究成果:“当以适当高的切削速度(约为常规速度的5~10倍)加工时,切削刃上的温度会降低,因此有可能通过高速切削提高加工生产率”。
60多年来,人们一直在探索有效、适用、可靠的高速切削技术,但直到20世纪90年代该技术才逐渐在工业实际中推广应用。
高速切削最早在飞机制造业和模具制造l受到很大的重视。
为使飞机的零部件满足很高的可靠性要求,大部分重要零件都是在整块铝合金坯件卜铣削而成,既可减少焊缝,又可提高零件的强度和抗振性。
但常规铣削效率很低,从而导致了高的生产成本和长的交货时间。
高速切削是克服这方面问题的最好解决方案。
汽车工业中,模具制造是产品更新换代的关键。
新车型定型后,模具制造周期的长短直接影响到产品的上市时间,也关系到市场竞争的成败。
所以在80年代美国、欧洲和日本的政府都出巨资推动高速切削在模具制造中的应用研究,90年代初高速切削已进入工业化应用。
图16 高速切削在生产应用中的发展历程图17 采用高速切削后产品质量提高的历程a一硬质合金切钢 b一硬质合金切铸铁c—CBN切铸铁图16是德国宝马公司(BMW)采用高速切削的历程。
铣削加工方法在高速加工中的应用探讨

圆弧 方 式 的 水 平 进 退 刀 运 动 ; 在 曲 面 轮 廓 铣 中 , 而 使 寿 命 提 高 了 7 , 于工 件 的 切 削 热 大 幅 度 降 低 , 削 振 动 运 动 、 O 留 切 用 切圆弧的进退刀 运动等 。 几 乎 消 失 ; 削 加 工 发 生 了本 质 性 的 飞 跃 。 在 常 规 切 削 加 切 刀具通常采用 球头铣刀 和平底 圆角铣 刀 , 用 1 采 2轴 加 工 中 备 受 困惑 的 一 系 列 问 题 亦 得 到 了 解 决 , 可 谓 是 集 高 真 加 效 、 质 、 耗 于 一 身 的 先 进 制 造 技 术 , 切 削 加 工 新 的 里 工 方 式 , 工 时 充 分 利 用 主 轴 的 加 工 功 率 。 优 低 是
料切除率提高 3 ~6倍 , 工 时 间 缩 短 5 ~ 7 。 当 加 工 加 O O 需 要 大 量 切 除 金 属 的 零 件 时 , 使 加 工 时 间 大 大 减 少 可
2 2 切 削 力 降 低 。 工 变 形 小 . 加
屑 槽 出 屑 以及 刀具 大 面 积 的 接 触 毛 坯 等 情 况 的 出 现 。 目的
高 速 铣 削 和 常 规 切 削 相 比 , 削 力 至 少 可 降 低 3 。 切 O 这 对 于 加 工 刚 性 较 差 的 零 件 来 说 可 减 少 加 工 变 形 , 一 些 使 薄壁类精细工 件的铣削加工成为可 能。 2 3 加 工 质 量 得 到 优 化 . 因 为 高 速 旋 转 时 刀 具 切 削 的 激 励 频 率 远 离 工 艺 系 统 的
程 碑 。在 切 削 速 度 上 , 合 金 9 0 5 0 / n 钛 合 金 铜 0 — 0 0 m mi ;
Mastercam动态高速铣削分析
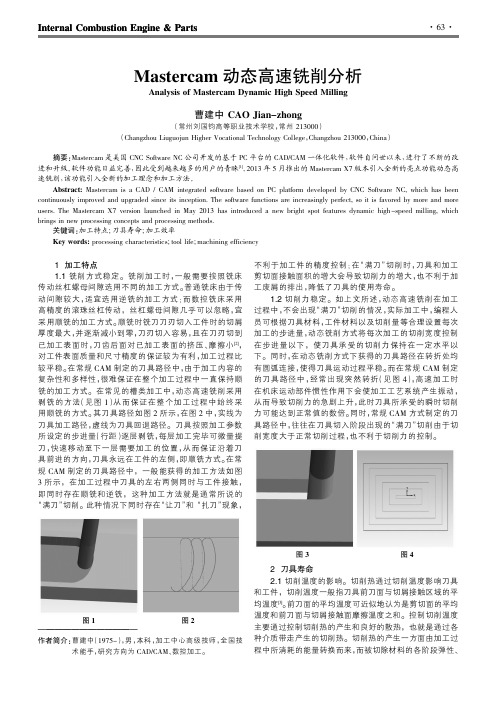
Internal Combustion Engine &Parts1加工特点1.1铣削方式稳定。
铣削加工时,一般需要按照铣床传动丝杠螺母间隙选用不同的加工方式。
普通铣床由于传动间隙较大,适宜选用逆铣的加工方式;而数控铣床采用高精度的滚珠丝杠传动,丝杠螺母间隙几乎可以忽略,宜采用顺铣的加工方式。
顺铣时铣刀刀刃切入工件时的切屑厚度最大,并逐渐减小到零,刀刃切入容易,且在刀刃切到已加工表面时,刀齿后面对已加工表面的挤压、摩擦小[2],对工件表面质量和尺寸精度的保证较为有利,加工过程比较平稳。
在常规CAM 制定的刀具路径中,由于加工内容的复杂性和多样性,很难保证在整个加工过程中一直保持顺铣的加工方式。
在常见的槽类加工中,动态高速铣削采用剥铣的方法(见图1)从而保证在整个加工过程中始终采用顺铣的方式。
其刀具路径如图2所示,在图2中,实线为刀具加工路径,虚线为刀具回退路径。
刀具按照加工参数所设定的步进量(行距)逐层剥铣,每层加工完毕可微量提刀,快速移动至下一层需要加工的位置,从而保证沿着刀具前进的方向,刀具永远在工件的左侧,即顺铣方式。
在常规CAM 制定的刀具路径中,一般能获得的加工方法如图3所示,在加工过程中刀具的左右两侧同时与工件接触,即同时存在顺铣和逆铣,这种加工方法就是通常所说的“满刀”切削。
此种情况下同时存在“让刀”和“扎刀”现象,不利于加工件的精度控制;在“满刀”切削时,刀具和加工剪切面接触面积的增大会导致切削力的增大,也不利于加工废屑的排出,降低了刀具的使用寿命。
1.2切削力稳定。
如上文所述,动态高速铣削在加工过程中,不会出现“满刀”切削的情况,实际加工中,编程人员可根据刀具材料,工件材料以及切削量等合理设置每次加工的步进量,动态铣削方式将每次加工的切削宽度控制在步进量以下,使刀具承受的切削力保持在一定水平以下。
同时,在动态铣削方式下获得的刀具路径在转折处均有圆弧连接,使得刀具运动过程平稳。
铣削加工中的加工效率提高方法
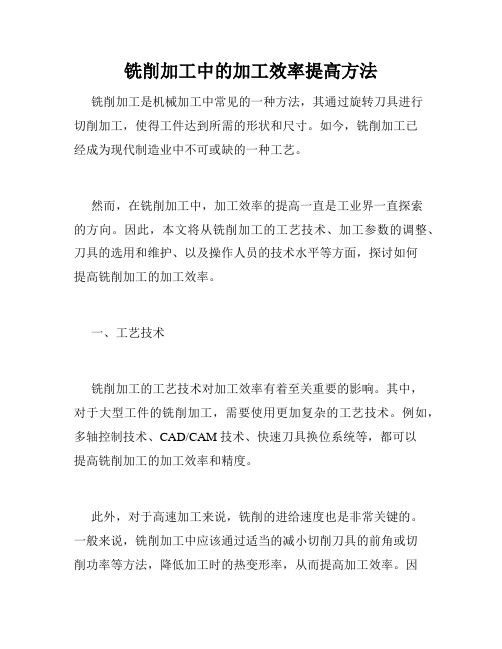
铣削加工中的加工效率提高方法铣削加工是机械加工中常见的一种方法,其通过旋转刀具进行切削加工,使得工件达到所需的形状和尺寸。
如今,铣削加工已经成为现代制造业中不可或缺的一种工艺。
然而,在铣削加工中,加工效率的提高一直是工业界一直探索的方向。
因此,本文将从铣削加工的工艺技术、加工参数的调整、刀具的选用和维护、以及操作人员的技术水平等方面,探讨如何提高铣削加工的加工效率。
一、工艺技术铣削加工的工艺技术对加工效率有着至关重要的影响。
其中,对于大型工件的铣削加工,需要使用更加复杂的工艺技术。
例如,多轴控制技术、CAD/CAM 技术、快速刀具换位系统等,都可以提高铣削加工的加工效率和精度。
此外,对于高速加工来说,铣削的进给速度也是非常关键的。
一般来说,铣削加工中应该通过适当的减小切削刀具的前角或切削功率等方法,降低加工时的热变形率,从而提高加工效率。
因此,在铣削加工过程中,需要根据不同的工件要求,来选择不同的切削参数。
二、加工参数的调整铣削加工中,不同加工参数的设置对加工效率也有着非常重要的影响。
例如,刀具进给速度、主轴转速、刀面康研度、加工深度等参数的变化,都会直接影响到加工效率和加工表面质量。
因此,在实际的铣削加工中,需要根据实际情况进行参数调整。
例如,对于工件直径相同但加工深度不同的情况,我们可以根据研究知识库中的数据,来调整切削参数。
对于精度要求高的工件,则应该根据加工要求,精益求精地调整切削参数,以保证加工效率和加工表面的质量。
三、刀具的选用和维护刀具的选用和维护也是影响铣削加工效率的重要因素。
不同的切削刀具在不同的加工条件下,都有着不同的优缺点,因此需要根据实际情况进行选择。
例如,对于需要大量切削金属的工件,我们可以选择高速钻头来提高铣削加工的效率。
除此之外,还要注意刀具的磨损情况。
在实际的加工过程中,切削刀具会因为磨损而导致加工效率下降。
因此,我们需要经常对刀具进行检查和维护,及时进行更换和磨削,以保证铣削加工中的加工效率。
高速铣削参数
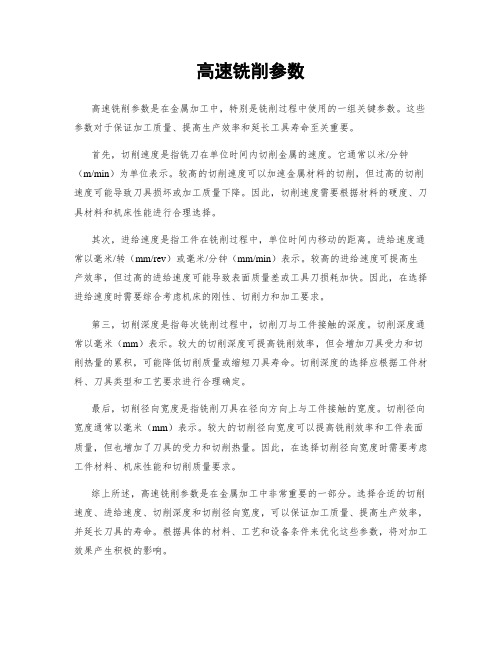
高速铣削参数高速铣削参数是在金属加工中,特别是铣削过程中使用的一组关键参数。
这些参数对于保证加工质量、提高生产效率和延长工具寿命至关重要。
首先,切削速度是指铣刀在单位时间内切削金属的速度。
它通常以米/分钟(m/min)为单位表示。
较高的切削速度可以加速金属材料的切削,但过高的切削速度可能导致刀具损坏或加工质量下降。
因此,切削速度需要根据材料的硬度、刀具材料和机床性能进行合理选择。
其次,进给速度是指工件在铣削过程中,单位时间内移动的距离。
进给速度通常以毫米/转(mm/rev)或毫米/分钟(mm/min)表示。
较高的进给速度可提高生产效率,但过高的进给速度可能导致表面质量差或工具刀损耗加快。
因此,在选择进给速度时需要综合考虑机床的刚性、切削力和加工要求。
第三,切削深度是指每次铣削过程中,切削刀与工件接触的深度。
切削深度通常以毫米(mm)表示。
较大的切削深度可提高铣削效率,但会增加刀具受力和切削热量的累积,可能降低切削质量或缩短刀具寿命。
切削深度的选择应根据工件材料、刀具类型和工艺要求进行合理确定。
最后,切削径向宽度是指铣削刀具在径向方向上与工件接触的宽度。
切削径向宽度通常以毫米(mm)表示。
较大的切削径向宽度可以提高铣削效率和工件表面质量,但也增加了刀具的受力和切削热量。
因此,在选择切削径向宽度时需要考虑工件材料、机床性能和切削质量要求。
综上所述,高速铣削参数是在金属加工中非常重要的一部分。
选择合适的切削速度、进给速度、切削深度和切削径向宽度,可以保证加工质量、提高生产效率,并延长刀具的寿命。
根据具体的材料、工艺和设备条件来优化这些参数,将对加工效果产生积极的影响。
数控铣削加工的效率因素的分析和实际应用中应注意的问题

目前 , 作为机床加工的核心是数控铣削机床加工 , 其中切削效率又是 (0 ~ 5 %)耐磨性好 , 5060 ; 比高速钢要高 1~ 0倍。由于这些特点, 52 使 机床加工生产成本控制的关键, 也是技术工作 的重要内容之一。现针 得硬质合金刀具 的切削速度比高速钢高 4 1 倍 。陶瓷刀具热硬度高 ~0 对如何提升数铣切削效率所涉及的主要因素进行分析 , 以指导改善铣 ( 可达 10 ℃)硬度高(0 C以上 ) 30 , 8 HR 。 C N适用 于切削高硬度淬硬钢和硬铸铁等 ,如加工高硬钢件 B 削加T的技术 、 生产与管理等方面的T作。 (0 6 H C 和冷硬铸铁时主要选用陶瓷刀具和 C N刀具 , 5~ 7 R ) B 其中加 1 数控 铣 削加工 注意 的 问题 T 硬度 6 ~ 5 C以下 的工 件 可用 陶瓷 刀具 ,而 6 H C以上 的1 0 6 HR 5R 二 1 切削速度。 . I 切削速度是影响数控刀具寿命的主要原 因之一。 在传 统 的切 削加 工 中 , 总是 先选 好 切削 深度 和进 给速 度 , 据 刀具 耐 用 件则用 C N刀具进行切削 ;C 再根 B P D适用于切削不含铁的金属 , 及合金 、 度选择合适切削速度,就是因为提高切削速度会使刀具寿命大大下 塑料和玻璃钢等 , 加工铝合金件时, 主要采用 P D和金刚石膜涂层刀 C 降。 在高速加工中 , 当切削速度的提高到一定值时 , 以使被加工部位 具 ; 可 碳素工具钢和合金工具钢现在只用作锉刀、 板牙和丝锥等工具 ; 硬 先“ 软化” 再切 除, 从而使切削力降低或使它的提升减缓 , 在一定程度 质合金涂层刀具 ( 如涂层 TN TC TC 、iI i 、i、iN TA N等 ) 虽然硬度较高 , 适 上改善了切削条件。 于加工的工件范围广 , 但其抗氧化温度一般不高 , 所以切削速度的提 1 进给速度。高速加工的进给速度对刀具寿命 、 T效率和加丁精 高也受到限制, . 2 加_ 一般可在 4 0 5 0 / n范围内加工钢铁件 。 0 0 mmi 度都 有着很 大 的影 响 。 很高 的切 削速度 下进 给 速度也 必须 达到 一定 在 此外 ,刀具切削部分的几何参数对切削效率的高低和加工质量 水平 , 不允许有明显的滞后 。 过低的进给速度不但切削效率低 , 甚至会 有 很大 影 响 , 速切 削时 的 刀具前 角 一般 比普 通切 削 时小 l。 , 角 高 0 后 使工件表面和刀具烧伤。 然而 , 当进给速度太高时, 加工表面质量会降 大 5 8 。 防止 刀尖处 的热 磨损 , 、 削刃 连接处 应采 用修 圆刀 ~。 为 主 副切 低, 切削力提高 , 刀具容易磨损甚至出现断刀现。 尖或倒角刀尖 , 以增大局部刀尖角, 增大刀尖附近切削刃的长度和刀 l 切削深度。切削深度是提高效率的重要 因素。对于提高切削效 具材料体积 , 3 以提高刀具刚性和减少刀具破损率。 率, 粗加丁和精加工的要求不同, 粗加工表现为单位时间 内去除切屑 另外 , 通常情况下 , 选择大直径的刀具 比直径小的刀具效率高 , 的体积, 而精加工为刀具在单位时间内切削面积。高速加工提倡 的是 如 同样加工一平面 ,如果机床功率许可 ,直径 2 r 0 m刀要 比直 径 a O m刀快—倍。同时, 尽量选择密齿刀( 在刀具每英寸直径上的刀齿 以较小的切削深度切削同时用很高的进给速度提高切削效率 , 这在精 lm > )增加每齿进给量 , 提高生产率及刀具寿命。有关试验研究表 加工时非常适用。 但是对粗加工, 有时从增大切削深度优 其是轴向切 数 13 , 削 深度 ) 提 高效 率 会更 加 明显 , 且增 加 切 削 深度 可 以减 少 进 刀 次 明:当线速度为 15 / n 来 而 6 mmi,每齿进 给为 0 4 m 时 ,进 给速度 为 .r 0a 3 1 m n刀具寿命为 3 件。 4 m/i, 0 如果将切削速度提高到 30 / n每齿 5 mmi, 进给为 0 8 m,进给速度则达到 2 8m/ i,是原来 加工 效率 的 .m 1 75 rn a 8 7 而刀 具寿 命增 加到 了 17 。 1%, 件 1 ’ 2 工件装夹的选择 。数铣机床( . 2 特别是加l T中心 ) 由于工序集 中的 在对零件进行定位 、 夹紧设计以及夹具 的选用和设计等问题上 具的使用寿命和提高加工效率。 余摆线式走刀和螺旋走刀是两种较优 原因, 应 由于通 用夹 具 的柔性 差 、 定 的高速铣走刀方法。余摆线式走刀主要用于加工沟槽类型腔 , 采用直 要全 面考 虑 。首先 , 尽量 采用 组合 夹具 , 径小于槽宽的铣刀沿余摆线走刀可避免刀具以全刀宽切入工件, 有效 位精度相对较低 , 当产品批量比较大 、 加工精度要求高时可以设计专 其 在选 避 地 减 小 了加工 淬 硬钢 的切 削力 及 刀具 与 工件 的接触 面 ,延 长 刀具 寿 用 夹具 。 次 , 择工 装时 应有 利于刀 具交 换 和在线 测量 , 免发生
高速铣削加工技术

模具高速铣削加工技术一、前言在现代模具生产中,随着对塑件的美观度及功能要求得越来越高,塑件内部结构设计得越来越复杂,模具的外形设计也日趋复杂,自由曲面所占比例不断增加,相应的模具结构也设计得越来越复杂。
这些都对模具加工技术提出了更高要求,不仅应保证高的制造精度和表面质量,而且要追求加工表面的美观。
随着对高速加工技术研究的不断深入,尤其在加工机床、数控系统、刀具系统、CAD/CAM软件等相关技术不断发展的推动下,高速加工技术已越来越多地应用于模具型腔的加工与制造中。
数控高速切削加工作为模具制造中最为重要的一项先进制造技术,是集高效、优质、低耗于一身的先进制造技术。
相对于传统的切削加工,其切削速度、进给速度有了很大的提高,而且切削机理也不相同。
高速切削使切削加工发生了本质性的飞跃,其单位功率的金属切除率提高了30%~40%,切削力降低了30%,刀具的切削寿命提高了70%,留于工件的切削热大幅度降低,低阶切削振动几乎消失。
随着切削速度的提高,单位时间毛坯材料的去除率增加了,切削时间减少了,加工效率提高了,从而缩短了产品的制造周期,提高了产品的市场竞争力。
同时,高速加工的小量快进使切削力减少了,切屑的高速排出减少了工件的切削力和热应力变形,提高了刚性差和薄壁零件切削加工的可能性。
由于切削力的降低,转速的提高使切削系统的工作频率远离机床的低阶固有频率,而工件的表面粗糙度对低阶频率最为敏感,由此降低了表面粗糙度。
在模具的高淬硬钢件(HRC45~HRC65)的加工过程中,采用高速切削可以取代电加工和磨削抛光的工序,从而避免了电极的制造和费时的电加工,大幅度减少了钳工的打磨与抛光量。
对于一些市场上越来越需要的薄壁模具工件,高速铣削也可顺利完成,而且在高速铣削CNC加工中心上,模具一次装夹可完成多工步加工。
高速加工技术对模具加工工艺产生了巨大影响,改变了传统模具加工采用的“退火→铣削加工→热处理→磨削”或“电火花加工→手工打磨、抛光”等复杂冗长的工艺流程,甚至可用高速切削加工替代原来的全部工序。
高速铣削中的切削加工性研究

高速铣削中的切削加工性研究
高速铣削过程十分复杂,现有的科学研究仍然无法从本质上对高速铣削过程中存在的特殊现象给予全面的解释。
所以,我们需要细致地了解高速铣削过程中的切削加工性。
本文针对3Cr2Mo钢和45淬硬钢开展高速铣削研究,为进一步提高加工效率和质量提供理论依据。
本论文借助实验观测、理论分析、建模等手段对高速铣削中的切削加工性进行深入研究。
本论文中选取TiAlN涂层的整体圆柱立铣刀和TiAlN涂层硬质合金球形铣刀,在270~945m/min的范围内进行铣削试验。
本论文研究的主要内容和结果如下:(1)对3Cr2Mo钢和45淬硬钢进行高速铣削试验,并就铣削条件的改变对切屑形态及其变形的影响做出了分析。
试验得出:(1)随着铣削速度不断增加,切屑的形状由带状逐渐呈现为锯齿状,当铣削的速度达到临界值时,材料发生绝热剪切变形。
(2)对于硬度较高的工件材料,其切屑的锯齿化程度较高,而形成这类切屑所需的铣削速度却较低。
(2)综合分析了JC模型和幂指数模型的优缺点,利用ABAQUS软件针对
3Cr2Mo钢建立了新的适用于高速切削的材料动态力学模型。
模拟的结果与实际试验的结果基本相符。
(3)通过高速铣削试验,分析不同铣削速度对铣削力及其动态特性的影响。
得到结论:(1)初始阶段,铣削力随着铣削速度的增加而增大,但当铣削速度超过临界值后,铣削力就随铣削速度的增加而变小。
(2)高速铣削时,铣削力波形不同于常规铣削力波形,其在切削区和非切削区均有信号输出。
(3)频域内的铣削力信号仅出现在基频的整数倍处,当占有绝对优
势的峰值频率与刀齿切削频率相同时,产生谐波振动。
铣削力计算公式详解
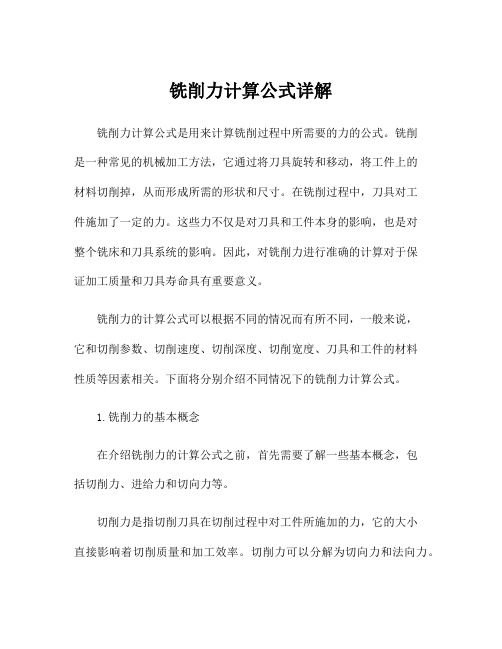
铣削力计算公式详解铣削力计算公式是用来计算铣削过程中所需要的力的公式。
铣削是一种常见的机械加工方法,它通过将刀具旋转和移动,将工件上的材料切削掉,从而形成所需的形状和尺寸。
在铣削过程中,刀具对工件施加了一定的力。
这些力不仅是对刀具和工件本身的影响,也是对整个铣床和刀具系统的影响。
因此,对铣削力进行准确的计算对于保证加工质量和刀具寿命具有重要意义。
铣削力的计算公式可以根据不同的情况而有所不同,一般来说,它和切削参数、切削速度、切削深度、切削宽度、刀具和工件的材料性质等因素相关。
下面将分别介绍不同情况下的铣削力计算公式。
1.铣削力的基本概念在介绍铣削力的计算公式之前,首先需要了解一些基本概念,包括切削力、进给力和切向力等。
切削力是指切削刀具在切削过程中对工件所施加的力,它的大小直接影响着切削质量和加工效率。
切削力可以分解为切向力和法向力。
切向力是指刀具在刀具进给方向上的力,它是刀具推进工件切削表面所产生的力,也是刀具的推进力。
切向力的大小决定了刀具的进给速度和切削深度。
法向力是指刀具对工件表面的垂直力,它是刀具沿着刀具旋转轴方向推压工件表面所产生的力,也是刀具的剪切力。
法向力的大小决定了刀具对工件的切削深度和切削精度。
进给力是指切削力在刀具进给方向上的分量,它是切向力在进给方向上的投影,也是切削负载。
进给力的大小直接影响着刀具的进给速度和切向力的大小。
切向力和法向力的计算公式可以根据不同情况而有所不同,一般来说,它们与切削参数、切削速度、切削深度、切削宽度、刀具和工件的材料性质等因素相关。
下面将分别介绍不同情况下的切向力和法向力的计算公式。
2.铣削力的计算公式铣削力的计算公式可以根据不同的情况而有所不同,下面将分别介绍不同情况下的铣削力的计算公式。
(1)标准铣削力的计算公式在标准铣削中,铣削力的大小可以通过下面的公式计算:Fc = kc * Ae * fFt = kc * Ae * f * tan(α)其中,Fc是切向力,Ft是法向力,kc是切削力系数,Ae是切削面积,f是进给量,α是刀具前角。
铣削加工方法、策略及铣削计算公式

铣削加工方法、策略及铣削计算公式1.铣削基本加工方法2.先进铣削加工方法先进铣削加工包括:- 斜坡铣- 螺纹插补- 摆线铣削- 推拉式仿形铣削- 插铣- 等高线铣削- 钻削3.铣削加工策略的定义:- 普通加工- 高速加工- 高性能加工- 高进给加工- 微加工1. 普通加工:是普通用途的加工策略。
切削宽度与切削深度比率可以各不相同,取决于工序的类型。
刀具特性:刀具拥有相对较长的切削刃和较小的芯部直径,在精度上没有很高要求。
机床要求:无特别要求。
应用领域:具有基本的CNC 技术,高难度的先进加工方法不可行;金属切除率只能达到一般的水平;应用领域通常包括小批量规模以及宽范围的材料。
2. 高速加工:是结合使用小的径向切削深度、高的切削速度与进给速度的加工策略;根据采用的方法、可达到很高的材料切除率和较低的Ra值。
这个策略的典型特征是切削力低、传递到刀具和工件上的热量少、毛刺的形成减少和工件的尺寸精度高;在高速加工下,使用比普通加工更快的切削速度,可以达到高金属切除率与好的表面粗糙度。
刀具特性:稳定(芯部直径较大和切削长度较短),清晰且成形良好的容屑空间,有利于良好的排屑,镀层。
机床要求:高速的CNC 控制、高转速、工作台进给速度快。
应用领域:模具工业的淬硬钢(48-62 HRC) 进行半精加工与精加工,交货时间短。
当使用正确刀具与先进的加工方法时,这项技术也可以应用在许多其他材料上。
3. 高性能加工:是一种能够达到非常高的金属切除率的加工策略。
这种策略的典型特征在于切削宽度是Dc的1倍,且切削深度是Dc的1~1.5倍,取决于工件材料;在高性能加工下,使用比普通加工切屑负载高得多的加工方式,能够达到极高的金属切除率。
刀具特性:刀具排屑槽上专门开发的容屑结构,刀尖用45°,小平面或刀尖圆弧进行保护,特别光滑的容屑空间,镀层,带或不带侧固柄。
机床要求:高稳定性、高功率要求、高刚性的夹紧系统。
应用领域:在大批量生产加工中,生产效率是关键的指标,或是要求高金属切除率的单件产品加工。
铣削原理及切削参数计算

A = 加工斜面的角度 (相对于水平面)
A:与X-Y的夹角
球刀有效直径的计算
球刀有效直径:球刀实际参与切削部分的直径. 在选择切削用量时以其有效直径来进行转速的计算.
刀具直径
Ad
有效直径
(ED)
直径Ø20mm,如Ad= 2 ⇒ ED=Ø12mm 直径Ø20mm,如Ad= 1 ⇒ ED=Ø8.7mm 直径Ø20mm,如Ad= 0.3 ⇒ ED=Ø4.86mm 直径Ø20mm,如Ad= 0.1 ⇒ ED=Ø2.82mm
热处理材料(SKD11) 52-60 HRC
推荐切削条件 (球刀直径x %)
Rd: 50% Ad: 10%
Rd: 45% Ad: 6~8%
Rd: 40% Ad: 5~6%
Rd: 35~40% Ad: 3~5%
注:刀具长径比 L/D = 5以内
表面残留高度与步距
• h-表面残留高度 预期的表面光洁度
高速切削理论是1931年4月德国物理学家Carl.J.Salomon提出的 在常规切削速度范围内,切削温度随着切削速度的提高而升高. 但切削速度提高到一定值后,切削温度不但不升高反会降低, 且该切削速度值与工件材料的种类有关 .
高速铣的优势
提高加工效率 提高加工精度 提高加工表面粗糙度
高速铣削是系统工程
滑动摩擦
☆ 顺铣 • 切入量由多变少 • 切削产生压应力 • 延长刀具寿命(切出点载荷
无突变) • 减少切削热量产生
高速铣削时推荐用顺铣加工
铣削加工切削参数
1.基本切削参数的确定(转速S、进给F) 2.切削深度 3.表面残留高度与步距 4.加工深度和与步距的经验公式
基本切削参数
基本的参数
(1) 切削速度
高速加工切削参数优化及实验分析

削深度这三个切削参 数为因素 , 每个 因素考 虑三个水 平, 采用正交实验设计方法进行实验设计。在高速五 轴联动加工中心上对 DE A IV R模具钢进行高速铣削实 验 。并采用 M t oos t t 0 表面粗糙度测定仪测 i t re 0 u y u s5 f 量工件的表面粗糙度。 1 1 高 速切 削 实验条 件 . 试件材料为 DE A IV R模具钢, 平面加工, 高压空气 冷 却。加 工机 床为 D C 5 L er 速五轴 加工 中 M 7V i a 高 n
a d v ra c nay i n a in e a l ss-t e ifue c so h s r me e so h ura e r u hn s a ebe n r s a c e h n l n e ft e epaa tr n t e s f c o g e sh v e e e r h d, t e sg iia c f t fe to s o h s a a tr n o r lto f t e o h u a e r ug ne s h in fc n e o he af ci n ft e e p r me es a d c re ain o h m n t e s r c o h s f h v e v lae a e be n e au td,a a tt p i lc ti g paa tr v e n fun tl s he o tma u tn r me e sha e b e o d. Ke ywo ds: g r Hih—s e d Cu tn p e ti g;Cu tn r mee s;S ra e Ro g n s ;Op i z t n ti g Pa a t r u c u h es f tmia i o
铣削力计算公式详解

铣削力计算公式详解铣削力是在铣削加工过程中切削刀具对工件所产生的力。
在进行铣削加工时,切削力的大小和刀工的功率直接关系到加工的效率和质量。
因此,对铣削力的计算和分析对于选用合适的切削参数和刀具具有很大的意义。
铣削力的计算是一个复杂的工程问题,涉及到材料力学、切削力学、热力学等多个领域的知识。
通常情况下,我们可以通过经验公式或者专业软件来计算和预测铣削力的大小。
下面将详细介绍铣削力的计算公式及其相关知识。
一、切削力的大小与刀具的进给量、转速、切削深度、切削速度等因素有关。
为了能够有针对性地确定切削参数,我们必须首先了解切削力的计算公式及其影响因素。
铣削力的计算公式通常可以通过以下几种方法进行估算:1.经验公式2.力矩平衡法3.数值模拟下面将分别对这三种方法进行详细介绍。
1.经验公式经验公式是根据大量的实验数据总结得出的,它可以简单、直观地估算切削力的大小。
通常情况下,经验公式需要根据不同的刀具和工件材料来选择不同的参数。
最常用的经验公式之一是菲利普公式,其计算公式为:F_c = K_c * D * d * f其中,F_c为切削力,K_c为切削力系数,D为刀具直径,d为切削深度,f为进给量。
菲利普公式是最简单、最常用的切削力计算公式之一。
但是,它只适用于一定范围内的切削参数和材料。
在实际应用中,由于不同的材料、刀具和加工条件的不同,菲利普公式可能会存在一定的误差。
因此,在进行铣削力计算时,还需要结合实际情况来选择合适的切削力计算公式。
2.力矩平衡法力矩平衡法是一种比较常见的精确计算切削力大小的方法。
它是基于切削力与切削热量之间的平衡关系来进行计算的。
通过分析刀具与工件之间的瞬时力平衡状态,可以得到切削力的大小。
这种方法对于复杂工件和刀具的铣削力计算特别有效。
力矩平衡法的基本思想是:对于切削过程中的每一小段切削刀具,刀具上的切削力与切屑推力之间存在一个平衡关系。
因此,我们可以通过对切屑推力的测量来间接测得切削力的大小。
高速加工技术

高速加工的一些定义
1. 高速铣削的切削速度比较传统铣削快5至10倍 2. 低切削力,进给速度高,主轴转速30,000转/分以上。 3. 高效能加工,切削量大,切削力稳定,刀具寿命长,高精 度,硬切削,不一定高转速。 4. 利用高主轴转速和高的轴向进给速度,以获得高的材料切 除率,而不降低零件的精度和表面质量。
高速加工的设备
高速加工机床 高速切削刀具
高速加工的应用
航空航天: 航空航天: ◎ 带有大量薄壁、细筋的大型轻合金整体构件加工,材料去 带有大量薄壁、细筋的大型轻合金整体构件加工, 除率达100-180cm /min。 除率达100-180cm3/min。 ◎ 镍合金、钛合金加工,切削速度达200-1000 m/min 镍合金、钛合金加工,切削速度达200汽车工业: 汽车工业: ◎ 采用高速数控机床和高速加工中心组成高速柔性生产线, 采用高速数控机床和高速加工中心组成高速柔性生产线, 实现多品种、 实现多品种、中小批量的高效生产 模具制造: 模具制造: ◎ 高速铣削代替传统的电火花成形加工,效率提高3-5倍 高速铣削代替传统的电火花成形加工,效率提高3 仪器仪表: 仪器仪表: ◎ 精密光学零件加工。
高速加工的意义
高速加工的真正意义?——改善加工生产流程!
高速切削的原理- 高速切削的原理-高速切削中切屑的产生
高速切削不断增加的摩擦阻力导致切屑和刀 具的接触区域的温度升高。 接触区域的温度可能高达工件材料的熔点。 切屑在接近熔点的液体状态下起到了润滑效 果,因此,减低了摩擦系数。 区域摩擦力的降低,减小了对切屑流动的阻 碍,从而导致对切屑的压力减小和切削力降低。 流动切屑的一个重要特征就是切屑横截面积 减小和剪切角增大,切屑明显的扭曲。
高速铣削刀具及切削参数的选择

高速铣削刀具及切削参数的选择摘要:通过等效类比的方法研究了高速铣削刀具选择的一般原则。
推导了球头铣刀的有效直径和有效线速度的计算公式,以此进一步确定转速,通过试验的方法测定了径向铣削深度和每齿进给量对表面粗糙度的影响。
关键词:高速铣削刀具;有效直径;有效线速度;切削参数;表面粗糙度作者:宋志国,宋艳,常州信息职业技术学院0 引言传统意义上的高速切削是以切削速度的高低来进行分类的,而铣削机床则是以转速的高低进行分类。
如果从切削变形的机理来看高速切削,则前一种分类比较合适;但是若从切削工艺的角度出发,则后一种更恰当。
这是因为随着主轴转速的提高,机床的结构、刀具结构、刀具装夹和机床特性都有本质上的改变。
高转速意味着高离心力,传统的7∶24锥柄,弹簧夹头、液压夹头在离心力的作用下,难以提供足够的夹持力;同时为避免切削振动要求刀具系统具有更高的动平衡精度。
高速切削的最大优势并不在于速度、进给速度提高所导致的效率提高;而是由于采用了更高的切削速度和进给速度,允许采用较小的切削用量进行切削加工。
由于切削用量的降低,切削力和切削热随之下降,工艺系统变形减小,可以避免铣削颤振。
1 刀具的选择通常选用图1所示的3种立铣刀进行铣削加工,在高速铣削中一般不推荐使用平底立铣刀。
平底立铣刀在切削时刀尖部位由于流屑干涉,切屑变形大,同时有效切削刃长度最短,导致刀尖受力大、切削温度高,导致快速磨损。
在工艺允许的条件下,尽量采用刀尖圆弧半径较大的刀具进行高速铣削。
图1 立铣刀示意图随着立铣刀刀尖圆弧半径的增加,平均切削厚度和主偏角均下降,同时刀具轴向受力增加可以充分利用机床的轴向刚度,减小刀具变形和切削振动(图2)。
图2 立铣刀受力示意图图3为高速铣削铝合金时,等铣削面积时两种刀具的铣削力对比。
刀具为直径Φ10mm的2齿整体硬质合金立铣刀,螺旋角30度。
刀尖圆弧半径为1.5mm和无刀尖圆弧的两种刀具。
图3 刀尖圆弧半径对铣削力的影响铣削面积同定为a,a p·a e=2.Omm2。
切削效率公式
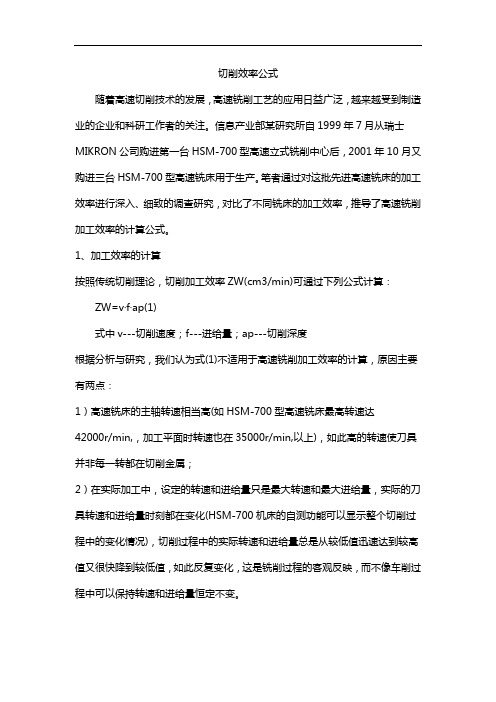
切削效率公式随着高速切削技术的发展,高速铣削工艺的应用日益广泛,越来越受到制造业的企业和科研工作者的关注。
信息产业部某研究所自1999年7月从瑞士MIKRON公司购进第一台HSM-700型高速立式铣削中心后,2001年10月又购进三台HSM-700型高速铣床用于生产。
笔者通过对这批先进高速铣床的加工效率进行深入、细致的调查研究,对比了不同铣床的加工效率,推导了高速铣削加工效率的计算公式。
1、加工效率的计算按照传统切削理论,切削加工效率ZW(cm3/min)可通过下列公式计算:ZW=v·f·ap(1)式中v---切削速度;f---进给量;ap---切削深度根据分析与研究,我们认为式(1)不适用于高速铣削加工效率的计算,原因主要有两点:1)高速铣床的主轴转速相当高(如HSM-700型高速铣床最高转速达42000r/min,,加工平面时转速也在35000r/min,以上),如此高的转速使刀具并非每一转都在切削金属;2)在实际加工中,设定的转速和进给量只是最大转速和最大进给量,实际的刀具转速和进给量时刻都在变化(HSM-700机床的自测功能可以显示整个切削过程中的变化情况),切削过程中的实际转速和进给量总是从较低值迅速达到较高值又很快降到较低值,如此反复变化,这是铣削过程的客观反映,而不像车削过程中可以保持转速和进给量恒定不变。
因此,我们提出用单位时间内的金属去除量Z(cm3/min)表示加工效率,即式中W---切削过程总的金属去除量(cm3)t---切削时间(<0,)式(2)更符合高速铣削的实际情况,用式(2)很容易实现对高速铣削加工效率的计算,同时也便于不同铣床加工效率的比较。
例如,原来在普通铣床上加工图1所示零件,为了缩短生产周期,一部分零件现采用高速铣床加工。
这样,可通过该零件的加工来比较两种加工设备的加工效率。
由于该零件的表面质量要求不高,高速铣削和普通铣削均能达到要求。
- 1、下载文档前请自行甄别文档内容的完整性,平台不提供额外的编辑、内容补充、找答案等附加服务。
- 2、"仅部分预览"的文档,不可在线预览部分如存在完整性等问题,可反馈申请退款(可完整预览的文档不适用该条件!)。
- 3、如文档侵犯您的权益,请联系客服反馈,我们会尽快为您处理(人工客服工作时间:9:00-18:30)。
高速铣削加工效率的一般计算与分析(转)
随着高速切削技术的发展,高速铣削工艺的应用日益广泛,越来越受到制造企业和科研工作者的关注。
信息产业部某研究所自1999年7月从瑞士MIKRON公司购进第一台HSM-700型高速立式铣削中心后,2001年10月又购进三台HSM-700型高速铣床用于生产。
笔者通过对这批先进高速铣床的加工效率进行深入、细致的调查研究,对比了不同铣床的加工效率,推导了高速铣削加工效率的计算公式。
1.加工效率的计算
按照传统切削理论,切削加工效率Zw(cm3/min)可通过下列公式计算:
Zw=v×f×ap (1)
式中:v——切削速度,f——进给量,ap——切削深度
根据分析与研究,我们认为式(1)不适用于高速铣削加工效率的计算,原因主要有两点:
①高速铣床的主轴转速相当高(如HSM-700型高速铣床最高转速达42000r/min,加工平面时转速也在35000r/min以上),如此高的转速使刀具并非每一转都在切削金属;
②在实际加工中,设定的转速和进给量只是最大转速和最大进给量,实际的刀具转速和进给量时刻都在变化(HSM-700机床的自测功能可以显示整个切削过程中的变化情况),切削过程中的实际转速和进给量总是从较低值迅速达到较高值又很快降到较低值,如此反复变化,这是铣削过程的客观反映,而不像车削过程中可以保持转速和进给量恒定不变。
因此,我们提出用单位时间内的金属去除量Z(cm3/min)表示加工效率,即:
Z=W/t (2)
式中:W——切削过程总的金属去除量(cm3),t——切削时间(min)(>0) 式(2)更符合高速铣削的实际情况,用式(2)很容易实现对高速铣削加工效率的计算,同时也便于不同铣床加工效率的比较。
例如,原来在普通铣床上加工某零件,为了缩短生产周期,一部分零件现采用高速铣床加工。
这样,可通过该零件的加工来比较两种加工设备的加工效率。
由于该零件的表面质量要求不高,高速铣削和普通铣削均能达到要求。
事实上,高速铣削加工出的零件表面粗糙度要比普通铣削加工低1~2个等级。
用单位时间内的金属去除量Z=W/t(cm3/min)表示加工效率。
试验中取铣削加工过程中的几个时间段,记录加工时间,测量在各个时间段零件加工前后的体积差,通过式(2)计算得到Z值。
通过多次测量计算取Z的平均值,该平均值即可视为较准确的Z值。
对于上述零件的高速铣削过程,由式(2)算得的Z值为:
Z(高速)=W/t=25.296cm3/min
按照传统切削理论即按式(1)计算得:
Zw=πDn/1000×100×vf/n×0.1×ap×0.1=376.8cm3/min
比较Z(高速)和Zw,显然Zw与该零件实际的高速铣削加工效率相差很大。
2.不同铣床加工效率的比较
某研究所目前用于生产的铣床除HSM-700型高速铣床外,还有国产的立式铣床和进口的铣削中心。
国产铣床是二十世纪九十年代初购进的北京第一机床厂生产的XK5040-1型立式升降台铣床(以下简称国产普通铣床),目前主要用于零件粗加工及少量铸铁件和钢件的加工;进口铣削中心是美国产VF-0 HAAS型铣削中心(以下简称进口普通铣床),可用于粗加工和精加工。
对于上述零件,在国产普通铣床上加工的切削效率为:
Z(国普)=W/t=3.073cm3/min
在进口普通铣床上加工的切削效率为:
Z(进普)=W/t=7.277cm3/min
将Z(高速)分别与Z(国普)和Z(进普)进行比较,有:
Z(高速)/Z(国普)=8.232
Z(高速)/Z(进普)=3.476
由上述计算和比较可以看出,在高速铣床上加工该零件的金属去除率相当高,与国产普通铣床相比其优势更为明显(据操作工人反映,甚至出现过高速铣床加工效率比国产普通铣床快10倍以上的情况)。
当然,对于不同材质、不同形状和不同加工要求的零件,不同铣床的加工效率并不相同。
对于加工面积较大的大型零件或形状特别复杂的零件,高速铣床具有更为显著的加工效率优势。
高速铣床的效率优势主要体现为高的刀具转速n和高的进给速度vf。
在实际加工中,进给速度vf对加工效率的影响往往更大。
3.考虑成本因素的加工效率比较
比较加工效率必须带有一定的约束条件,应结合企业的实际情况,考虑加工效率与生产成本的关系。
用式(2)求得的加工效率Z除以加工成本C来表示考虑了成本因素的加工效率E (cm3/min·万元),即:
E=Z/C (3)
式(3)中,为计算简便,设加工成本C主要为制造费用(包括设备成本、设备维护费用、刀具损耗费用等),并假设高速铣床、国产普通铣床、进口普通铣床的日常维护费用相等。
为了能客观地反映实际加工效率,对2001年1月到2002年5月这一较长时间段内的机床使用情况进行比较:
瑞士MIKRON HSM-700型高速铣床每台价值人民币C0(高速)=200万元;由于机床零部件价格昂贵,用于机床非日常维护的费用(包括故障检修、更换零部件等)为C2(高速)=9.5万元;在高速铣床上使用的刀具均为进口铣刀,价格较为昂贵,再加上缺少针对不同刀具和零件材料的切削用量规范,使得高速铣刀的使用成本较高,因此,从去年初至今,高速铣刀损耗费用为C3(高速)=14548.13元。
美国产VF-0 HAAS型铣削中心是1998年进口的普通铣削中心,当时价值人民币C0(进普)=80万元;机床使用性能较好,除日常维护外,至今没有出现需要维修的故障,C2(进普)=0.45万元;与高速铣床一样,所使用的刀具均为进口铣刀,除正常的刀具磨损外,很少出现刀具非正常损耗,铣刀损耗费用为C3(进普)=2195.26元。
1992年从北京第一机床厂购进的XK5040-1型立式升降台铣床,当时价值人民币C0(国普)=60万元;目前主要用于零件粗加工,虽然精度不高,但性能还比较稳定,除日常维护外,未出现大故障。
2000年对其操作系统进行了改造(换装了西门子操作系统),改造和检修的费用为C2(国普)=6.45万元;在此机床上既使用进口刀具也使用国产刀具,铣刀损耗费用为C3(国普)=1377.62元。
设机床的使用年限为20年,按照直线折旧法,机床每年折旧5%,则到2002年,三种铣床的当前成本分别为:
C1(高速)=(1/4)C0(高速)[(1-5%×3)+3(1-5%)]=185(万元)
C1(进普)=C0(进普)(1-5%×4)=64(万元)
C1(国普)=C0(国普)(1-5%×10)=30(万元)
由式(3)可求得考虑成本时三种不同铣床的加工效率分别为
E(高速)=Z(高速)/(C1(高速)+C2(高速)+C3(高速))=0.1291cm3/min·万元
E(进普)=Z(进普)/(C1(进普)+C2(进普)+C3(进普))=0.1125cm3/min·万元
E(国普)=Z(国普)/(C1(国普)+C2(国普)+C3(国普)=0.0840cm3/min·万元由计算结果可以看出,考虑成本因素后,高速铣削不再具有显著的效率优势(与进口普通铣削中心的加工效率接近)。
这一比较结果说明,目前高速铣削的使用成本还比较高(其设备成本、维护费用和刀具损耗费用都比普通机床高出很多)。
尽管目前采用高速铣削还达不到经济的切削效率,但并不说明高速铣削不具优势。
首先,上文对铣削效率经济性的分析仅考虑了生产成本,并没有考虑时间效益。
在技术飞速发展的今天,时间往往是更重要的经济因素。
高速铣削加工在缩短加工工时方面的优势是很明显的。
其次,上文所作加工效率比较是在高速铣床和普通铣床均能加工同一种零件的前提下进行的,事实上许多不适合(或不能)在普通铣床上加工的零件(如薄壁零件或对加工表面质量要求较高的零件)只能用高速铣床加工。
第三,高速铣削技术作为一种新的加工技术在我国正经历不断发展的过程,为了获得高速铣削的经济加工效率,必须深入研究高速铣削机理,加快进行高速铣削工艺的科研开发,同时加强生产管理,提高操作者素质。
相信随着对高速铣削
技术研究的不断深入,加工的经济性等问题将得到很好解决。
4.结论
(1)生产实践表明,高速铣床加工零件覆盖面广,特别适用于加工面积较大、形状复杂的精密零部件。
零件加工精度高,废品率低。
(2)传统的切削加工效率公式不适用于高速铣削,用单位时间内的金属去除量来表述高速铣削的加工效率更为准确。
(3)单从机床的切削效率来看,高速铣床要高出普通铣床好几倍,但目前高速铣床的使用成本较高。
在选择工艺方案时,可以考虑用普通铣床进行粗加工,用高速铣床进行半精加工和精加工。
(4)只有深入开展高速铣削技术的科研开发,才能充分发挥高速铣床的加工效率优势。