铣削加工的计算方法
UG铣削加工常用计算公式
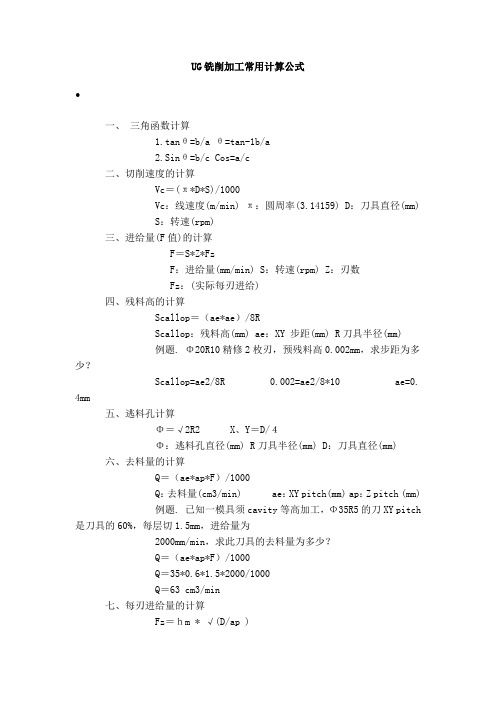
Fz=hm * √(D/ap )
Fz=0.2*√10/1.5
Fz=0.5mm
2000mm/min,求此刀具的去料量为多少?
Q=(ae*ap*F)/1000
Q=35*0.6*1.5*2000/1000
Q=63 cm3/min
七、每刃进给量的计算
Fz=hm * √(D/ap )
Fz:实施每刃进给量 hm:理论每刃进给量 ap:Z pitch (mm)
D:刀片直径(mm)
例题 (前提depo XY pitch是刀具的60%)depoΦ35R5的刀,切削NAK80材料hm为0.15mm,Z轴切深
五、逃料孔计算
Φ=√2R2 X、Y=D/4
Φ:逃料孔直径(mm) R刀具半径(mm) D:刀具直径(mm)
六、去料量的计算
Q=(ae*ap*F)/1000
Q:去料量(cm3/min) ae:XY pitch(mm) ap:Z pitch (mm)
例题. 已知一模具须cavity等高加工,Φ35R5的刀XY pitch是刀具的60%,每层切1.5mm,进给量为
UG铣削加工常用计算公式
一、 三角函数计算
1.tanθ=b/a θ=tan-1b/a
2.Sinθ=b/c Cos=a/c
二、切削速度的计算
Vc=(π*D*S)/1000
Vc:线速度(m/min) π:圆周率(3.14159) D:刀具直径(mm)
S:转速(rpm)
三、进给量(F值)的计算
F=S*Z*Fz
F:进给量(mm/min) S:转速(rpm) Z:刃数
Fz:(实际每刃进给)
四、残料高的计算
Scallop=(ae*ae)/8R
铣削用量进给量进给速度

铣削⽤量进给量进给速度铣削⽤量如何确定? 1. 铣削速度υ指铣⼑旋转的圆周线速度,单位为m/min 。
2.计算公式:1000dnπυ=3. 式中 d ——铣⼑直径,mm;n ——主轴(铣⼑)转速,r/min;从上公式可得到主轴(铣⼑)转速dn πυ1000=进给量在铣削过程中,⼯件相对于铣⼑的移动速度称为进给量。
有三种表⽰⽅法:(1)每齿进给量αf铣⼑每转过⼀个⼑齿,⼯件沿进给⽅向移动的距离,单位为mm/z 。
(2)每转进给量f 铣⼑每转过⼀转,⼯件沿进给⽅向移动的距离,单位为mm/r 。
(3)每分钟进给量νf 铣⼑每旋转1min ,⼯件沿进给⽅向移动的距离,单位为mm/min 。
三种进给量的关系为:νf=fn=αfzn 式中αf——每齿进给量,mm/z ;n ——铣⼑(主轴)转速,r/min ; z ——铣⼑齿数。
表⼆铣削⼑的每齿进给量f (mm/z )推荐值(1)铣削宽度αe铣⼑在⼀次进给中所切掉的⼯件表层的宽度,单位为mm 。
⼀般⽴铣⼑和端铣⼑的铣削宽度约为铣⼑的直径的50%~60%左右。
(2)背吃⼑量αp 铣⼑在⼀次进给中所切掉的⼯件表层的厚度,即⼯件已加⼯表⾯和待加⼯表⾯间的垂直距离,单位为mm 。
(3)⼀般⽴铣⼑粗铣时的背吃⼑量以不超过铣⼑半径为原则,⼀般不超过7mm,以防⽌背吃⼑量过⼤⽽造成⼑具损坏,精铣时约为0.05~0.3mm;端铣⼑粗铣时约为2~5mm , 精铣时约为0.1~0.50mm 。
加⼯内螺纹的切削速度与冷却润滑内螺纹攻丝的切削速度与加⼯的内螺纹件的材产、硬度、螺纹公差等级和丝锥的材质(如⾼速钢还是合⾦钢或⾼碳钢),以及使⽤的冷润滑油等均有关。
如果切削速度过快,将促使丝锥早期磨损、折断,导致内螺纹⽛侧粗糙,扩⼤内螺纹尺⼨;如果切削速度过慢,虽然可延长丝锥使⽤寿命,但降低⽣产率,内螺纹件的材料为中碳钢时,尽可能使⽤植物油(菜油、⾖油)进⾏润滑。
表3给出了⾼速钢丝锥加⼯各种材料的内螺纹件时,可参考使⽤切削速度。
铣削参数计算方法

Ks 数值
190 210 240 190 245 93 120 70
Ks × W × fZ × Z × N × d 6120000 ×
PHP =
6120 4500
× PKW
Ks : 比切削阻力值 [kgf/mm2] η : 机械效率 (0.7 ~ 0.8)
青铜、黄铜
● 切屑排出量
Q= W×F×d 1000
技术资料 计算式
● 切削速度
V=
× D × N
V : 切削速度 [m/min] D : 铣刀盘径 [mm] N : 主轴旋转数 [min-1]
d D
铣削加工
1000
● 工作台进给量与进刀量
fz = F Z ×N
fz : 进刀量 [mm/ 刃 ] F : 工作台进给量 [mm/min] Z : 铣刀盘刃数 N : 主轴旋转数 [min-1]
D L′ F L
549
技术资料 计算式
● 真斜角
tanT = tanR × cosC + tanA × sinC
C I T A (+)
铣削加工
● 刃斜角
tanI = tanA × cosC - tanR × sinC
A : 轴向斜角 A.R. [° ] (-90° < A < 90°) R : 径向斜角 R.R. [° ] (-90° < R < 90°) C : 侧切刃角 [° ] (0° < C < 90°) T : 直斜角 [° ] (-90° < T < 90°) I : 刃倾角 [° ] (-90° < I < 90°)
=
Pkw =
D 20
×
铣削力计算公式详解

铣削力计算公式详解铣削力是指铣削过程中刀具对工件所施加的力,它是铣削加工过程中重要的参数之一。
铣削力大小的计算对于工件的加工质量、工具的寿命以及加工效率都有着重要的影响。
铣削力的计算公式通常是根据铣削的工艺参数以及材料的性质来推导,下面我们将详细解释铣削力的计算公式。
一、铣削力的基本概念为了更好地理解铣削力的计算公式,首先我们需要了解铣削力的基本概念。
在铣削加工过程中,刀具在与工件接触时会产生力的作用。
这些力包括主轴的进给力、切削力和阻力等。
其中,切削力是指刀具在切削过程中与工件发生力的作用,它是决定加工质量和加工效率的重要因素。
铣削力的大小与工件的材料性质、切削刀具的材料和几何形状、切削速度、进给速度、切削深度等因素密切相关。
因此,在进行铣削加工时,需要对铣削力进行精确地计算和控制,以保证加工质量和工具寿命。
二、铣削力的计算公式在铣削加工中,刀具施加在工件上的切削力可以用力学原理进行计算,一般来说,可以参考以下的铣削力计算公式:1.切削力Fc的计算公式切削力Fc是铣削中最常见的力。
在进行铣削加工时,切削力的大小直接影响着刀具的磨损情况和加工表面的加工质量。
切削力Fc的计算公式通常如下:Fc = kc * ae * ap * f //(1)其中,Fc为切削力,单位为牛顿(N);kc为切削力系数,其大小与材料性质、切削条件和刀具类型等有关;ae为轴向切削深度,单位为毫米(mm);ap为径向切削深度,单位为毫米(mm);f为给进量,单位为毫米/刀齿(mm/tooth)。
切削力Fc的大小与刀具材料、刀具的结构和铣削参数等因素有关。
在实际的工程中,我们需要根据具体的加工情况和工件材料来确定切削力系数kc的数值,然后通过公式(1)来计算切削力Fc的大小。
2.主轴的进给力Fr的计算公式除了切削力之外,铣削加工中还存在着主轴的进给力Fr。
主轴的进给力是指主轴在刀具与工件接触时所施加的力,它也是影响加工质量和加工效率的重要因素。
数控编程技巧CNC常用计算公式
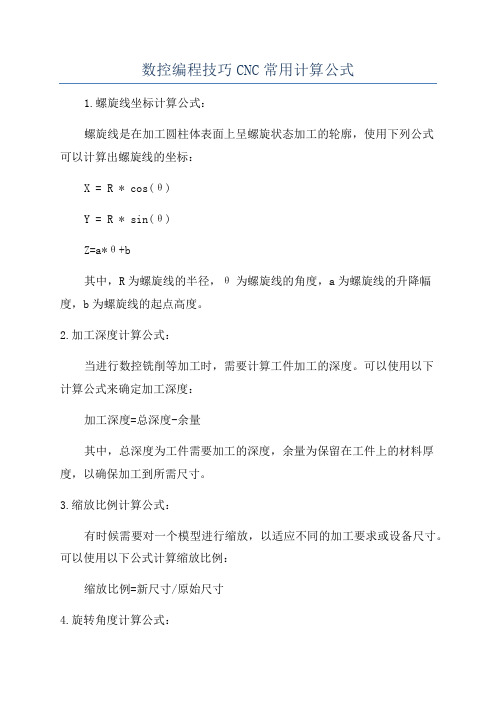
数控编程技巧CNC常用计算公式1.螺旋线坐标计算公式:螺旋线是在加工圆柱体表面上呈螺旋状态加工的轮廓,使用下列公式可以计算出螺旋线的坐标:X = R * cos(θ)Y = R * sin(θ)Z=a*θ+b其中,R为螺旋线的半径,θ为螺旋线的角度,a为螺旋线的升降幅度,b为螺旋线的起点高度。
2.加工深度计算公式:当进行数控铣削等加工时,需要计算工件加工的深度。
可以使用以下计算公式来确定加工深度:加工深度=总深度-余量其中,总深度为工件需要加工的深度,余量为保留在工件上的材料厚度,以确保加工到所需尺寸。
3.缩放比例计算公式:有时候需要对一个模型进行缩放,以适应不同的加工要求或设备尺寸。
可以使用以下公式计算缩放比例:缩放比例=新尺寸/原始尺寸4.旋转角度计算公式:当要在数控机床上进行旋转加工时,需要计算旋转的角度。
可以使用以下公式计算旋转角度:旋转角度=(旋转圈数*360°)+单圈旋转的角度其中,旋转圈数为旋转的圈数,单圈旋转的角度为旋转一圈时的角度。
5.加工速度计算公式:加工速度是在数控机床上进行工件加工时,刀具或工件在单位时间内所移动的距离。
可以使用以下公式计算加工速度:加工速度=进给速度*主轴转速6.内孔加工半径计算公式:当进行数控车削或镗削等内孔加工时,需要计算内孔的半径。
可以使用以下计算公式:内孔半径=工件半径-内孔深度7.平均切削速度计算公式:平均切削速度是切削过程中单位时间内切削边缘的长度。
可以使用以下计算公式计算平均切削速度:平均切削速度=π*刀具直径*主轴转速以上只是一些常见的计算公式示例,具体的计算公式还取决于加工过程中的具体要求和工件形状。
在实际应用过程中,还需要结合具体的加工情况和数控机床的参数来确定合适的计算公式。
切削加工常用计算公式

附录3:切削加工常用计算公式1.切削速度Vc (m/min)1000nD Vc ⨯π⨯=主轴转速n (r/min)D 1000Vc n ⨯π⨯=金属切除率Q (cm 3/min)Q = V c ×a p ×f净功率P (KW)3p 1060Kcf a V c P ⨯⨯⨯⨯=每次纵走刀时间t (min)n f l t w⨯=以上公式中符号说明D — 工件直径 (mm)ap — 背吃刀量(切削深度)(mm)f — 每转进给量 (mm/r )lw — 工件长度 (mm)精选文库 2. 铣削加工铣削速度Vc (m/min)1000nD Vc ⨯π⨯=主轴转速n (r/min)D 1000Vc n ⨯π⨯=每齿进给量fz (mm)z n Vffz ⨯=工作台进给速度Vf (mm/min)z n fz Vf ⨯⨯=金属去除率Q (cm 3/min)1000Vfae ap Q ⨯⨯=净功率P (KW)61060KcVf ae ap P ⨯⨯⨯⨯=扭矩M (Nm)n 1030P M 3⨯π⨯⨯=以上公式中符号说明D — 实际切削深度处的铣刀直径(mm )Z — 铣刀齿数a p — 轴向切深 (mm)a e — 径向切深 (mm)精选文库3. 钻削加工切削速度Vc (m/min)1000n d Vc ⨯π⨯=主轴转速n (r/min)d1000Vc n ⨯π⨯=每转进给量f (mm/r)nVf f =进给速度Vf (mm/min)n f Vf ⨯=金属切除率Q (cm 3/min)4Vc f d Q ⨯⨯=净功率P (KW)310240kc d Vc f P ⨯⨯⨯⨯=扭矩M (Nm)n1030P M 3⨯π⨯⨯=以上公式中符号说明:d — 钻头直径 (mm)kc1 — 为前角γo=0、切削厚度hm=1mm 、切削面积为1mm 2时所需的切削力。
(N/mm 2)mc — 为切削厚度指数,表示切削厚度对切削力的影响程度,mc 值越大表示切削厚度的变化对切削力的影响越大,反之,则越小γo — 前角 (度)。
铣削用量进给量给速度

铣削用量进给量给速度————————————————————————————————作者:————————————————————————————————日期:铣削用量如何确定? 1. 铣削速度υ指铣刀旋转的圆周线速度,单位为m/min 。
2.计算公式:1000dnπυ=3. 式中 d ——铣刀直径,mm;n ——主轴(铣刀)转速,r/min;从上公式可得到主轴(铣刀)转速 dn πυ1000=表一铣削速度υ推荐表工件材料 硬度/HB 铣削速度υ/m/min高速钢铣刀 硬质合金铣刀 低、中炭钢<22021~40 60~150 225~290 15~36 54~115 300~425 9~15 36~75 高炭钢<220 18~36 60~130 225~325 14~21 53~105 325~375 8~21 36~48 375~425 6~10 35~45 合金钢 <220 15~35 55~120 225~325 10~24 37~80 325~425 5~9 30~60 工具钢 200~250 12~23 45~83 灰铸铁110~140 24~36 110~115 150~225 15~21 60~110 230~290 9~18 45~90 300~320 5~10 21~30 可锻铸铁110~160 42~50 100~200 160~200 24~36 83~120 200~240 15~24 72~110 240~280 9~11 40~60 铸 钢低炭100~150 18~27 68~105 中炭 100~160 18~27 68~105 160~200 15~21 60~90 200~240 12~21 53~75 钢炭 180~2409~18 53~80 铝合金 180~300 360~600 铜合金 45~100 120~190 镁合金180~270150~600进给量在铣削过程中,工件相对于铣刀的移动速度称为进给量。
车、铣、钻、镗切削计算

车、铣、钻、镗切削计算车削功率和扭矩计算Vc= 3.14 xD xRPM1000V=Vc xap xfr(mm 3/min)Time=Lfr xN P=Vc xap xfr xkc60037.2 举例:车削不锈钢外圆,工件直径60mm,切深3mm,走刀量0.2mm/r, 切削速度200m/min, 材料单位切削力为2900N/mm2,加工长度为120mmF 力=Kc xfr xapT=F 力x(D/2)=P x9549/RPMRPM=(200X1000)/(3.14X60)=1061转每分钟金属去除率V=200x2x0.2=80 立方厘米每分钟每加工一个零件的时间=120/(0.2x1061)=0.57分钟车削功率P=(200x3x0.2x2900)/60037.2=5.8千瓦车削力=2900 x0.2x3=1740牛顿=177.5公斤车削扭矩T=1740 x30=52.2牛顿米铣削功率和扭矩的计算铣削三要素Cutting data formulas铣削功率和扭矩的计算Power consuming and Torque force Torque (Nm) = kW (nett) x 9549RPMU 钻钻削功率和扭矩的计算Power consuming and Torque force 例:工件材料为高合金钢,硬度HRC50,钻削直径20mm ,Vc =40m/min ,f =0.07mm/r ,Kc =4500N/mm 2,η=0.9,计算钻削功率和扭矩。
P=Kc ⨯f ⨯Vc ⨯(D 2-d 2)D ⨯240000 ⨯η钻削功率P =4500 ⨯0.07 ⨯40 ⨯20/240000 ⨯0.9=1.2KW转速n=40 ⨯1000/3.14 ⨯20=636rpm扭矩T=1.2 ⨯9549/636=18NMT=F 力x(D/2)=P x9549/RPMD: hole diameter d: core diamerer镗削功率和扭矩计算P=Vc xap xfr xkc 60037.2T=F力x(D/2) =P x9549/RPM 举例:镗削奥氏体不锈钢,工件硬度HB200, 工件直径60mm,切深3mm,走刀量0.2mm/r, 切削速度100m/min, 材料单位切削力为2900N/mm2,加工长度为120mm计算镗削功率时注意Vc减半,即Vc镗=1/2Vc车RPM=(100X1000)/(3.14X60)=531转每分钟金属去除率V=100x2x0.2=40 立方厘米每分钟每加工一个零件的时间=120/(0.2x531)=1.13分钟镗削功率P=(100x3x0.2x2900)/60037.2=2.90千瓦镗削力=2900 x0.2x3=1740牛顿=177.5公斤镗削扭矩T=1740 x30=52.2牛顿米Thanks!。
铣削原理及切削参数计算

通过增加主轴倾斜提高Ve
n=
ve x 1000 π x De
rpm
铣削原理及切削参数计算
切削区域由刀尖点移到侧向
铣削原理 – 铣削公式
金属去除率:
铣削原理及切削参数计算
Q = (ap x ae x Vf )/1000
fz =
Vf
n x zn
铣削原理 ——铣削计算
面铣刀直径80mm, 6个刀片刃口,若刀片的切削速 度为150m/min, 问主轴的转速是多少?如果每齿进刀量 为fz=0.2mm/z, 问机床的工作台进刀量是多少?
lm = 加工长度mm n = 主轴转速(转每分)rpm
Mc = 扭矩Nm Pc = 净功率kW Q = 金属去除率cm3/min
vc = 切削速度m/min vf = 每分钟进给mm/min zc = 刀具有效齿数 zn = 刀具齿数
ηmt = 有效系数
铣削原理及切削参数计算
切削参数——切削参数的计算
Q=
ap x ae x vf 1000
Pc (kW)主轴净功率
Pc
=
ap x 60
ae x vf x kc x 106 x η
Mc (Nm)主轴扭矩
Mc
=
fn
x
π x Dc2 4000
x
kc
( ) ae/Dc ≥ 0,1平均切削厚度
hm
=
sin πx
κr x 180 x ae
Dc x arcsin
x fz ae
Dc
铣削原理及切削参数计算
铣削原理 – 总结
检查机床功率和刚度,以保证所用的铣刀直径能够在机床使用刀具 的悬伸尽可能短;
CNC常用计算公式

CNC常用计算公式在数控加工中,常用的计算公式有:1.转速计算公式:转速(rpm)= 配置的主轴转速(rpm)/ 刀具直径(mm)* 主轴转鼓数(转/齿)2.进给速度计算公式:进给速度(mm/min)= 进给速度设定值(mm/min)/ 预设倍率3.切削速度计算公式:切削速度(m/min)= π × 刀具直径(mm)× 主轴转速(rpm)/ 10004.主轴转速计算公式:主轴转速(rpm)= 切削速度(m/min)× 1000 / π × 刀具直径(mm)5.驱动轴向力计算公式:驱动轴向力(N)= 刀具直径(mm)× 进给速度(mm/min)× 切削力系数6.切削力计算公式:切削力(N)= 轴向切削力(N)÷ cos(铣削角度)7.铣削力计算公式:铣削力(N)=铣削切削阻力(kB)×轴向力(kN)^铣削阻力指数8.主轴电机功率计算公式:主轴电机功率(kW)=铣削力(N)×铣削力系数(kW/N)9.等分计算公式:切削刀数 = 刀具直径(mm)× π / 距离圆周长度(mm)10.速度比计算公式:速度比=同刃次数/刀具齿数11.加工时间计算公式:加工时间(min)= 切削长度(mm) / 进给速度(mm/min) + 换刀时间(min)12.总加工时间计算公式:总加工时间(min)= 加工时间(min)× 加工个数 + 装夹时间(min)13.检测时间计算公式:检测时间(min)= 检测长度(mm) / 检测速度(mm/min) + 置零时间(min)14.总时间计算公式:。
铣削公式和定义 工程.doc

铣削公式和定义工程公式切削速度 (vc)(m/min)主轴转速 (n)(rpm)每齿进给量 (fz)(mm)金属去除率 (Q)(cm?/min)工作台进给或进给速度 (vf)(mm/min)扭矩 (Mc)(Nm)净功率要求 (Pc) (kW)平均切屑厚度 (hm),侧铣(mm)面铣(mm)在将工件中央对准铣刀放置时。
注意: aros和arcsin用度表示特定切削力 (kc) (N/mm?)如果γ0,使用γ0= 0°,那么公式变为:特定铣刀公式具有直切削刃的刀具在特定深度的最大切削直径(mm)。
面铣 (对中工件) 直切削刃和侧铣 (ae >Dcap/2) mm。
侧铣 (ae >Dcap/2) 直切削刃,mm。
使用圆刀片的刀具在特定深度的最大切削直径(mm)。
面铣圆刀片 (ae >Dcap/2)mm。
侧铣 (ae >Dcap/2) 和圆刀片 (ap球头立铣刀在特定深度的最大切削直径(mm)。
每齿进给量 (mm/齿),刀具对中。
每齿进给量 (mm/齿),侧铣。
内圆坡走铣 (3轴) 或圆弧铣 (2轴) 计算公式周边进给率(mm/min)刀具中心进给率(mm/min)径向切深(mm)对于实体式工件, Dw = 0和 ae eff = Dm/2每齿进给量(mm)当扩孔时每齿进给量(mm)外圆坡走铣 (3轴) 或圆弧铣 (2轴)计算公式周边进给率(mm/min)刀具中心进给率(mm/min)每齿进给量(mm)铣刀主偏角– kr (度)主切削刃角 (kr) 是影响切削力方向和切屑厚度的主要因素。
刀具直径– Dc (mm)刀具直径 (Dc)在PK部位上测量,主切削刃在这里与平行刃带相遇。
Dc 是在大多数情况下出现在订货号的直径,但CoroMill 300除外,它使用D3 。
要考虑的最重要直径是(Dcap) –在实际切削深度 (ap) 处的有效切削直径–用于计算实际切削速度 (ve)。
铣削加工

16
背吃刀量ap
1. 切 削 用 量
侧吃刀量ac
铣削速度vc
进 给 量
17
切 削 刃 分 布 位 置
圆 周 铣 削
切削刃分布在刀具 圆周表面的切削方 式Fra bibliotek端 面 铣 削
切削刃分布在刀具端 面上的铣削方式
18
1-1.铣削用量
铣削用量:背吃刀ap、 侧吃刀量ae、 铣削速度vc 进给量
19
1-1背吃刀量ap
31
顺铣
32
逆铣
33
四.铣削力
34
§2 铣 床
35
XA6132型万能升降铣床
36
X8126型万能工具铣床
37
X2010A型龙门铣床
38
圆形工作台铣床
1-主轴箱;2-立柱; 3-圆工作台; 4-滑座;5-床身
39
图所示为在立式双头回转铣床上加工 柴油机连杆端面的情形,夹具沿圆周排列 紧凑,使铣刀的空程时间缩短到最低隈度, 且因机床有两个主轴,能顺次进行粗铣和 精铣,因而大大提高了生产效率。
49
直接分度法 n=40/z
例:有一零件需要加工为8等分。
n=40/z=40 /8=5(转)
50
角度分度法
51
52
53
简单分度法
54
差动分度法
55
差动分度法是利用配换挂轮将分度头主轴 和侧轴连接起来,并松开分度盘侧面紧固 螺钉后进行的分度方法。
56
57
58
通过切削刃基点并垂直于工作平面方向上测量的吃 刀量,即平行于铣刀轴线测量的切削层尺寸。
1-2侧吃刀 ae 平行于工作平面并垂直于切削刃基点的进给 运动方向上测量的吃刀量,即垂直于铣刀轴 线测量的切削层尺寸。
机加工及材料重量计算公式
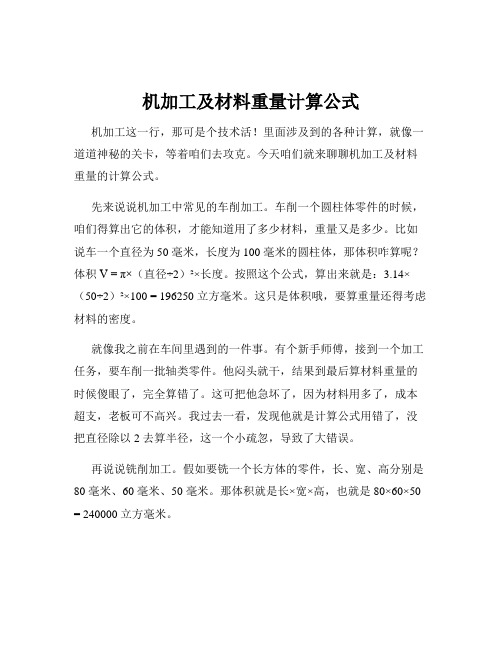
机加工及材料重量计算公式机加工这一行,那可是个技术活!里面涉及到的各种计算,就像一道道神秘的关卡,等着咱们去攻克。
今天咱们就来聊聊机加工及材料重量的计算公式。
先来说说机加工中常见的车削加工。
车削一个圆柱体零件的时候,咱们得算出它的体积,才能知道用了多少材料,重量又是多少。
比如说车一个直径为 50 毫米,长度为 100 毫米的圆柱体,那体积咋算呢?体积V = π×(直径÷2)²×长度。
按照这个公式,算出来就是:3.14×(50÷2)²×100 = 196250 立方毫米。
这只是体积哦,要算重量还得考虑材料的密度。
就像我之前在车间里遇到的一件事。
有个新手师傅,接到一个加工任务,要车削一批轴类零件。
他闷头就干,结果到最后算材料重量的时候傻眼了,完全算错了。
这可把他急坏了,因为材料用多了,成本超支,老板可不高兴。
我过去一看,发现他就是计算公式用错了,没把直径除以 2 去算半径,这一个小疏忽,导致了大错误。
再说说铣削加工。
假如要铣一个长方体的零件,长、宽、高分别是80 毫米、60 毫米、50 毫米。
那体积就是长×宽×高,也就是 80×60×50 = 240000 立方毫米。
在钻孔加工中,计算材料去除的体积也有讲究。
比如钻一个直径 20 毫米,深度 30 毫米的孔,那体积就是π×(直径÷2)²×深度,即 3.14×(20÷2)²×30 = 9420 立方毫米。
对于材料重量的计算,得先知道材料的密度。
不同的材料密度可不一样,像钢的密度大概是 7.85 克/立方厘米,铝的密度约 2.7 克/立方厘米。
还是拿前面车削的那个圆柱体零件来说,如果是钢材质的,把体积 196250 立方毫米换算成立方厘米,就是 196.25 立方厘米。
铣削力计算公式详解

铣削力计算公式详解铣削力是在铣削加工过程中切削刀具对工件所产生的力。
在进行铣削加工时,切削力的大小和刀工的功率直接关系到加工的效率和质量。
因此,对铣削力的计算和分析对于选用合适的切削参数和刀具具有很大的意义。
铣削力的计算是一个复杂的工程问题,涉及到材料力学、切削力学、热力学等多个领域的知识。
通常情况下,我们可以通过经验公式或者专业软件来计算和预测铣削力的大小。
下面将详细介绍铣削力的计算公式及其相关知识。
一、切削力的大小与刀具的进给量、转速、切削深度、切削速度等因素有关。
为了能够有针对性地确定切削参数,我们必须首先了解切削力的计算公式及其影响因素。
铣削力的计算公式通常可以通过以下几种方法进行估算:1.经验公式2.力矩平衡法3.数值模拟下面将分别对这三种方法进行详细介绍。
1.经验公式经验公式是根据大量的实验数据总结得出的,它可以简单、直观地估算切削力的大小。
通常情况下,经验公式需要根据不同的刀具和工件材料来选择不同的参数。
最常用的经验公式之一是菲利普公式,其计算公式为:F_c = K_c * D * d * f其中,F_c为切削力,K_c为切削力系数,D为刀具直径,d为切削深度,f为进给量。
菲利普公式是最简单、最常用的切削力计算公式之一。
但是,它只适用于一定范围内的切削参数和材料。
在实际应用中,由于不同的材料、刀具和加工条件的不同,菲利普公式可能会存在一定的误差。
因此,在进行铣削力计算时,还需要结合实际情况来选择合适的切削力计算公式。
2.力矩平衡法力矩平衡法是一种比较常见的精确计算切削力大小的方法。
它是基于切削力与切削热量之间的平衡关系来进行计算的。
通过分析刀具与工件之间的瞬时力平衡状态,可以得到切削力的大小。
这种方法对于复杂工件和刀具的铣削力计算特别有效。
力矩平衡法的基本思想是:对于切削过程中的每一小段切削刀具,刀具上的切削力与切屑推力之间存在一个平衡关系。
因此,我们可以通过对切屑推力的测量来间接测得切削力的大小。
铣刀功率和切削力计算【秘籍】

大家知道铣刀功率和切削力计算是怎样的吗?下面,小编为大家简单介绍一下,一起来看看吧。
一、按照主轴转速1000rpm ,进给速度0.1mm/转,钻穿1.8mm 约需要时间1s 。
切削力Ff刀具材料:高速钢加工方式:钻公式:Ff=309*D*f^(0.8)*(Kp)功率:D = 8功率:f = 0.1功率:Kp = 0.75(按铜合金多相平均HB>120)计算结果= 293.839切削力矩M工件材料:灰铸铁(HB190)刀具材料:高速钢加工方式:钻公式:M=0.21*D^(2)*f^(0.8)*(Kp)功率:D = 8功率:f = 0.1功率:Kp = 0.75(按铜合金多相平均HB>120)计算结果= 1.597二、铣削切削力计算:铣削切削力计算类别:工件材料:碳钢、青铜、铝合金、可锻铸铁等刀具材料:高速钢铣刀类型:端铣刀公式:F=(Cp)*(ap)^(1.1)*(fz)^(0.80)*D^(-1.1)*B^(0.95)*z*(Kp) 功率:Cp = 294功率:ap = 1.8功率:fz = 0.5功率:D = 8功率:B = 8功率:z = 4功率:Kp = 0.75计算结果= 707.914扩展资料:钻铣床铣刀切削力计算方法:一切削力的来源,切削合力及其分解,切削功率研究切削力,对进一步弄清切削机理,对计算功率消耗,对刀具、机床、夹具的设计,对制定合理的切削用量,优化刀具几何参数等,都具有非常重要的意义。
金属切削时,刀具切入工件,使被加工材料发生变形并成为切屑所需的力,称为切削力。
切削力来源于三个方面:克服被加工材料对弹性变形的抗力;克服被加工材料对塑性变形的抗力;克服切屑对前刀面的摩擦力和刀具后刀面对过渡表面与已加工表面之间的摩擦力。
切削力的来源上述各力的总和形成作用在刀具上的合力Fr(国标为F)。
为了实际应用,Fr 可分解为相互垂直的Fx(国标为Ff)、Fy(国标为Fp)和Fz(国标为Fc)三个分力。
铣平面表面粗糙度计算公式

铣平面表面粗糙度计算公式
铣削是一种常用的加工方式,在铣削过程中,表面粗糙度对零件的质量和性能有着重要影响。
因此,计算铣削后表面粗糙度是非常必要的。
铣削平面表面粗糙度的计算公式如下:
Ra = (0.8 + 7.5 / f) * (1.25 * (f * Ap)^0.25) 其中,Ra为铣削后的表面粗糙度,单位为μm;f为进给量,单位为mm/tooth;Ap为铣削深度,单位为mm。
该公式是基于国际标准ISO 16610-21与ASME B46.1的计算方法,能够比较准确地计算铣削后表面的粗糙度。
但需要注意的是,该公式仅适用于铣削平面表面。
对于其他形状的表面,需要使用相应的公式进行计算。
为了获得更好的表面质量,不仅需要选择合适的铣削参数,还需要选择合适的工具和切削液,并且保持刀具的锋利度。
同时,对于高要求的表面质量,还需要进行二次加工或采用其他的表面处理方法。
- 1 -。
铣床圆打孔计算公式
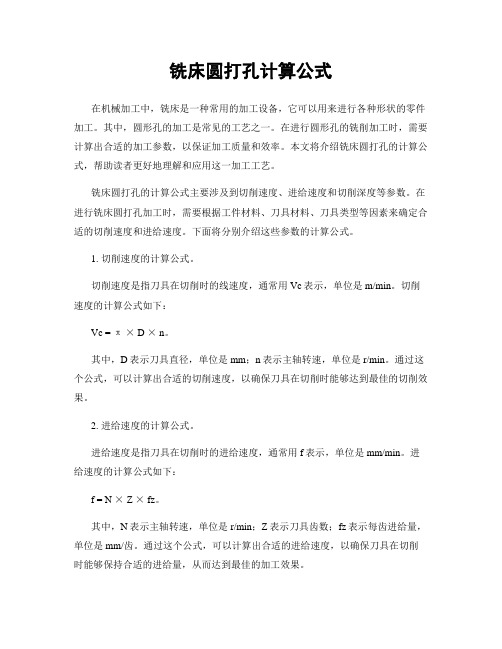
铣床圆打孔计算公式在机械加工中,铣床是一种常用的加工设备,它可以用来进行各种形状的零件加工。
其中,圆形孔的加工是常见的工艺之一。
在进行圆形孔的铣削加工时,需要计算出合适的加工参数,以保证加工质量和效率。
本文将介绍铣床圆打孔的计算公式,帮助读者更好地理解和应用这一加工工艺。
铣床圆打孔的计算公式主要涉及到切削速度、进给速度和切削深度等参数。
在进行铣床圆打孔加工时,需要根据工件材料、刀具材料、刀具类型等因素来确定合适的切削速度和进给速度。
下面将分别介绍这些参数的计算公式。
1. 切削速度的计算公式。
切削速度是指刀具在切削时的线速度,通常用Vc表示,单位是m/min。
切削速度的计算公式如下:Vc = π× D × n。
其中,D表示刀具直径,单位是mm;n表示主轴转速,单位是r/min。
通过这个公式,可以计算出合适的切削速度,以确保刀具在切削时能够达到最佳的切削效果。
2. 进给速度的计算公式。
进给速度是指刀具在切削时的进给速度,通常用f表示,单位是mm/min。
进给速度的计算公式如下:f = N × Z × fz。
其中,N表示主轴转速,单位是r/min;Z表示刀具齿数;fz表示每齿进给量,单位是mm/齿。
通过这个公式,可以计算出合适的进给速度,以确保刀具在切削时能够保持合适的进给量,从而达到最佳的加工效果。
3. 切削深度的计算公式。
切削深度是指刀具在切削时的切削深度,通常用ap表示,单位是mm。
切削深度的计算公式如下:ap = D d。
其中,D表示刀具直径,单位是mm;d表示孔径,单位是mm。
通过这个公式,可以计算出合适的切削深度,以确保刀具在切削时能够达到最佳的切削效果。
在进行铣床圆打孔加工时,需要根据工件材料、刀具材料、刀具类型等因素来确定合适的切削速度、进给速度和切削深度。
通过上述公式的计算,可以得到合适的加工参数,从而保证加工质量和效率。
除了上述参数外,还需要注意刀具的选择、刀具刃口的磨削、切屑的排除等问题。