铣削加工原理
数控铣削加工

数控铣削加工数控铣削加工是现代工业中非常重要的制造工艺之一。
它采用计算机控制的工具和机器,在三维坐标系下进行精密的硬质材料加工,确保部件尺寸精确、表面质量好并且生产效率高。
下面是一些关于数控铣削加工的详细介绍。
一、数控铣削加工的原理数控铣削加工设备通过计算机程序来控制工件在坐标系内的位置、方向和加工轨迹,从而完成各种形状的加工。
数控铣削加工的工作原理与手动操作的铣床是基本相同,但是数控铣削加工具有更高的精度和自动化程度。
二、数控铣削加工的设备数控铣削加工设备通常由数控系统、伺服电机、工作台、加工刀具等组成。
数控系统是整个设备的核心部分,它由电气元件、主控板、输入/输出接口、操作面板以及计算机软件等构成,它控制整个设备的运行和加工过程。
伺服电机是数控系统把指令转化为机械运动的执行部件,它们通过控制机械运动来实现加工与移动。
工作台是加工零件的位置,它通常具有载重能力和平移性能。
在加工过程中,工作台可以按照预先编好的程序移动,以便于定位及相对刀具进行加工。
加工刀具是数控铣削设备中最重要的部分,因为它们直接参与加工过程。
根据加工需要,可以使用直径、锥度和球形切削刀具来实现加工,它们可以依次更换或采用不同的切削方式来完成不同的加工任务。
三、数控铣削加工的优点数控铣削加工的优点主要体现在以下几个方面:1. 精度高。
数控铣削加工的精度达到了高水平,可以保证极高的形状和位置精度。
2. 自动化程度高。
数控铣削设备搭载了计算机控制系统,可以通过程序自动完成加工,而不需要人工干预。
3. 生产效率高。
相对于传统的手动铣床,数控铣削设备可以在更短的时间内完成同样的工作量,并且可以实现加工自动化,提高生产效率。
4. 应用范围广。
数控铣削加工适用于高精度、复杂形状零件的制造,如模具、零件、工具等。
四、数控铣削加工的应用数控铣削加工是一种重要的制造工艺,因此广泛应用于各种行业,如汽车、飞机、机械、模具制造、医疗仪器制造等。
下面是一些具体的应用场景:1. 汽车制造。
铣削实验报告

一、实验模块机械加工技术二、实验标题铣削加工工艺实验三、实验目的1. 了解铣削加工的基本原理和工艺特点。
2. 掌握铣床的组成、运动和用途。
3. 熟悉铣削加工的加工方法和测量方法。
4. 提高操作铣床的技能,确保加工质量。
四、实验日期及操作者实验日期:2023年4月10日实验操作者:张三五、实验原理铣削加工是利用铣刀在工件上做旋转运动,并通过刀具与工件的相对运动,对工件进行切削的一种加工方法。
铣削加工具有加工精度高、生产效率高、加工范围广等特点。
六、实验步骤1. 准备工作(1)检查铣床各部位是否完好,包括主轴、刀架、工作台等。
(2)调整铣床的刀具和工件位置,确保刀具与工件相对运动顺畅。
(3)检查铣刀的安装是否牢固,确保铣刀在加工过程中不会松动。
2. 加工过程(1)启动铣床,观察主轴旋转是否正常。
(2)根据工件加工要求,选择合适的铣刀和切削参数。
(3)将工件放置在工作台上,调整工件位置,确保加工精度。
(4)启动铣刀,进行铣削加工。
(5)观察加工过程,确保加工质量。
3. 加工结束(1)停止铣刀旋转,将工件从工作台上取出。
(2)检查工件加工质量,包括尺寸精度、表面质量等。
(3)清理机床,清理工件,做好保养工作。
七、实验环境实验地点:机械加工实验室实验设备:铣床、铣刀、工件、量具等。
八、实验过程及分析1. 实验过程本次实验以加工一个平面工件为例,具体步骤如下:(1)检查铣床各部位是否完好,调整刀具和工件位置。
(2)选择合适的铣刀和切削参数,如转速、进给量等。
(3)将工件放置在工作台上,调整工件位置,确保加工精度。
(4)启动铣刀,进行铣削加工。
(5)观察加工过程,确保加工质量。
2. 实验分析(1)铣削加工过程中,铣刀与工件相对运动顺畅,未出现异常现象。
(2)加工完成后,工件尺寸精度达到要求,表面质量良好。
(3)实验过程中,操作者严格按照操作规程进行,确保加工质量。
九、实验结论1. 通过本次实验,掌握了铣削加工的基本原理和工艺特点。
传统铣削的实验报告(3篇)

第1篇一、实验目的1. 了解传统铣削的基本原理和方法。
2. 掌握铣削加工的工艺参数及其对加工质量的影响。
3. 培养实际操作能力,提高铣削加工技能。
二、实验原理铣削是一种常用的金属加工方法,它是利用铣刀在工件表面进行旋转切削,使工件表面产生一定的形状和尺寸。
铣削加工具有生产效率高、加工精度高、表面质量好等优点。
三、实验设备与材料1. 实验设备:铣床、铣刀、夹具、工件等。
2. 实验材料:钢、铝、铜等金属材料。
四、实验步骤1. 铣床调整:调整铣床的床身、工作台、主轴等,确保铣削加工过程中的稳定性。
2. 铣刀安装:将铣刀安装到铣床主轴上,确保铣刀与主轴的同心度。
3. 工件装夹:将工件固定在夹具上,确保工件在铣削过程中的稳定性。
4. 铣削参数设置:根据加工要求,设置铣削速度、进给量、切削深度等参数。
5. 铣削加工:启动铣床,进行铣削加工。
6. 铣削过程观察:观察铣削过程中的现象,如切削力、振动等。
7. 完成铣削:达到加工要求后,停止铣削,拆除工件。
8. 清理:清理铣床、铣刀、工件等,为下一次实验做好准备。
五、实验结果与分析1. 铣削速度对加工质量的影响:铣削速度越高,加工效率越高,但过高的铣削速度会导致切削温度升高,使工件表面产生烧伤,降低加工质量。
实验结果表明,铣削速度在100-150m/min范围内时,加工质量较好。
2. 进给量对加工质量的影响:进给量越大,加工效率越高,但过大的进给量会导致切削力增大,使工件表面产生振纹,降低加工质量。
实验结果表明,进给量在0.2-0.3mm/r范围内时,加工质量较好。
3. 切削深度对加工质量的影响:切削深度越大,加工效率越高,但过大的切削深度会导致切削力增大,使工件表面产生振纹,降低加工质量。
实验结果表明,切削深度在0.5-1.0mm范围内时,加工质量较好。
六、实验结论1. 传统铣削加工是一种常用的金属加工方法,具有生产效率高、加工精度高、表面质量好等优点。
2. 铣削加工的工艺参数对加工质量有较大影响,合理设置铣削速度、进给量、切削深度等参数,可提高加工质量。
铣边机工作原理

铣边机工作原理
铣边机是一种用于对材料进行铣削加工的机械设备,其工作原理如下:
1. 运转电机启动:铣边机通过电机提供驱动力,使铣刀转动以实现铣削加工。
2. 调节铣刀位置:根据需要加工的材料和加工要求,通过调节铣刀位置使其与待加工材料接触。
3. 行进方式:铣边机可以通过手动或自动方式进行移动,并根据需求进行适当速度调节。
4. 材料加工过程:铣刀接触到待加工材料后,以高速旋转的方式将材料表层一点一点地切削、去除,实现对材料的铣削作用。
5. 冷却润滑:在铣削过程中,由于摩擦和热量产生,铣边机通常需要通过冷却润滑系统为切削部分提供冷却润滑剂,以保持工作温度和延长刀具寿命。
6. 控制系统:铣边机通常也配备一套控制系统,用于监测和调整机器的工作状态,以确保加工质量和安全。
总的来说,铣边机通过旋转的铣刀对待加工材料进行切削、去除,实现对材料边缘的整形加工。
通过调整刀具的位置和运动方式,可以实现不同形状和要求的边缘加工。
《铣削加工工艺》课件

铣削加工适用于各种金属材料的加工,如钢铁、有色金属等,尤其适用于加工平面、沟 槽、齿形等复杂形状。在航空制造业中,铣削加工广泛应用于机翼、机身和发动机部件 的制造;在汽车制造业中,铣削加工用于发动机、变速器和底盘部件的制造;在模具制
造业中,铣削加工用于模具型腔和型芯的加工。
铣削加工的发展趋势
总结词
工件表面质量不佳是铣削加工中常见的问题 之一,它可能影响工件的外观和使用性能。
详细描述
工件表面质量不佳的原因可能包括机床精度 不足、刀具磨损、切削参数选择不当等。为 了提高工件表面质量,可以采取一系列措施 ,如提高机床精度、定期检查和更换刀具、
优化切削参数等。
THANKS
感谢观看
02
切削速度是指铣刀在单位时间内所转过的弧长,通常以米/分钟为单 位。
03
进给速度是指铣刀在进给系统中每分钟所移动的距离,通常以毫米/ 分钟为单位。
04
铣削深度是指铣刀在工件表面上所切削的深度,通常以毫米为单位。
铣削深度与进给速度的确定
铣削深度的确定应根据工件的材料、硬度、铣刀的材质和规格以及加工要求等因素 综合考虑。
02
CATALOGUE
铣削加工的基本原理
铣削力的产生与影响
总结词
了解铣削力的产生原因及其对铣削加工的影响
详细描述
铣削力是铣削加工过程中的主要作用力,其产生与切削层的形成和切屑的排出 有关。铣削力的方向、大小和变化直接影响铣削加工的效率、刀具的磨损和加 工质量。
铣削加工的切屑形成与控制
总结词
掌握切屑的形成机理及切屑控制的方法
齿轮铣削是一种针对齿轮的铣削 工艺,主要用于加工各种齿轮。
齿轮铣削工艺主要采用指状铣刀 进行加工,通过调整刀具的角度 和切削参数,可以获得较好的加
铣削加工_精品文档
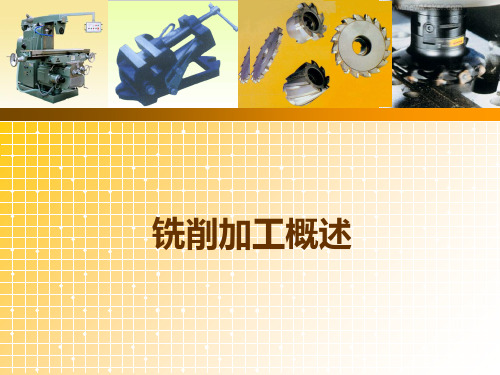
铣 削 要 素
a)圆周铣削
b)端面铣削
铣削. 用量要素
14
三、铣削方式
铣削方式是指铣削时铣刀相对于工件的运动和
位置关系。
它对铣刀寿命、工件表面粗糙度、铣削过程平 铣 削 稳性及生产率都有较大的影响。
方
式
铣平面时根据所用铣刀的类型(切削刃在铣刀
上的分布:圆柱面和端平面)不同,可分为圆周
.
48
加垫平行垫铁装夹工件 加垫圆棒装夹工件
压板的结构
.
49
.
上一页50
TSK万能倾斜分度盘
上.一页
51
3.万能分度头
是铣床的重要精密附件。
用途:多边形工件、花键轴、牙嵌式离合器、齿轮等圆周分度和螺旋槽加工。
在成批和大量生产中得到广泛的
应用。
.
38
二、X6132型卧式万能升降台铣床
铣床型号X6132具体含义如下:
.
39
如图所示为X6132型铣床, 它是国产铣床中最典型、应用 最广泛的一种卧式万能升降台 铣床。X6132型铣床的主要特 征是铣床主轴轴线与工作台台 面平行。结构完善,变速范围 大,刚性较好,操作方便,有 纵向进给间隙自动调节装置, 工作台可以回转45°,工艺范 围较广。
本 (1)了解铣床的种类及X6132型铣床的传动系
节 教
统;
学 (2)掌握铣床的主要部件及功用,各类铣床
要 求
的运用特点;
.
30
铣床的运动
主运动:主轴(铣刀)的回转运动 主电动机的回转运动,经主轴变速机构传递主 轴,使主轴回转。主轴转速共18级。 进给运动:工作台(工件)的纵向、横向和垂直 方向的移动。 进给电动机的回转运动经进给变速机构,分别传 递给三个进给方向的进给丝杠,进给速度各18 级。
铣刀的切削原理

铣刀的切削原理
铣刀是一种常用的机械切削工具,用于铣削金属、木材和其他各种材料。
其切削原理主要包括以下几个方面:
1. 刀具旋转:铣刀通过主轴与刀座相连接,并在机床上高速旋转。
刀具的旋转提供切削运动和切削力。
2. 刀具进给:铣刀在旋转的同时,通过机床进给系统,控制刀具相对于工件的位置和移动速度。
刀具进给决定切削深度和工件上每单位时间的切削长度。
3. 切削力:由于刀具与工件之间的相对运动,切削力在切削过程中产生。
切削力作用于刀具上,使其对工件进行切削。
切削力主要由径向切削力和轴向切削力组成。
4. 切削削角:铣刀的切削削角是刀具切削过程中的重要参数。
它决定了切削过程中切削面的形状和切削力的大小。
常见的切削削角有前角、主后角和径向后角。
5. 切削液:为了降低切削温度、减小摩擦和磨损,并帮助排屑和冷却刀具,通常在铣削过程中会使用切削液进行冷却和润滑。
总之,铣刀的切削原理是通过旋转的刀具与工件的相对运动,形成一定的切削力,对工件进行切削加工。
切削过程中,刀具的旋转和进给以及切削力的作用是关键
因素。
铣削原理及切削参数计算

高速铣削推荐
ok
切削力小而稳定 切削热量少
大
切削力波动大 切削热量大
小
• 小切削深度 • 大进给步距
大
大
• 大切削深度 • 小进给步距
球刀粗加工推荐条件表
材料硬度
软材料(S55C) HRC <35
预硬钢(NAK80/P20) 35-45 HRC
热处理材料(S136/STAVAX) 45-52 HRC
ED = 2 * Ad * ( D -Ad )
End of Presentation Thank you
Makino Confidential
• P-与加工面平行的步距 预期的表面光洁度决定 精加工中的步距=径向进给量
h
2
P = h * 8r
P
残留高度与步距
平坦表面
2
P = h * 8r
步距
•平坦表面: 斜度在10~15°以内, •在平坦表面上,为得到理论表面残留高度,步距须略小于P值, 具体应视斜度而定.
残留高度与步距
大角度斜面
o
A
热处理材料(SKD11) 52-60 HRC
推荐切削条件 (球刀直径x %)
Rd: 50% Ad: 10%
Rd: 45% Ad: 6~8%
Rd: 40% Ad: 5~6%
Rd: 35~40% Ad: 3~5%
注:刀具长径比 L/D = 5以内
表面残留高度与步距
• h-表面残留高度 预期的表面光洁度
A = 加工斜面的角度 (相对于水平面)
A:与X-Y的夹角
球刀有效直径的计算
球刀有效直径:球刀实际参与切削部分的直径. 在选择切削用量时以其有效直径来进行转速的计算.
铣削加工工艺基础知识概述
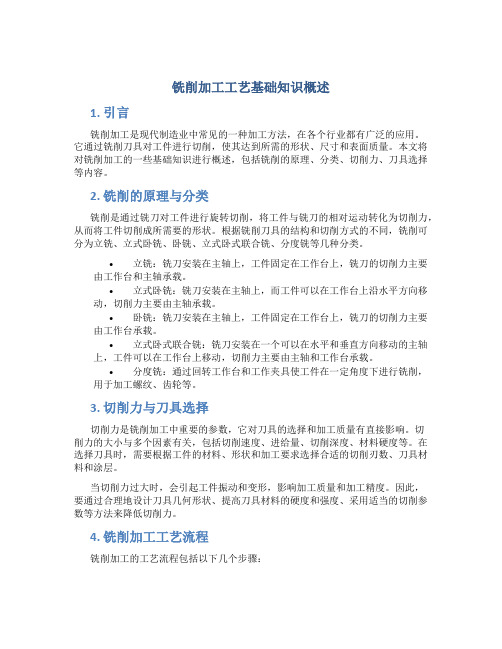
铣削加工工艺基础知识概述1. 引言铣削加工是现代制造业中常见的一种加工方法,在各个行业都有广泛的应用。
它通过铣削刀具对工件进行切削,使其达到所需的形状、尺寸和表面质量。
本文将对铣削加工的一些基础知识进行概述,包括铣削的原理、分类、切削力、刀具选择等内容。
2. 铣削的原理与分类铣削是通过铣刀对工件进行旋转切削,将工件与铣刀的相对运动转化为切削力,从而将工件切削成所需要的形状。
根据铣削刀具的结构和切削方式的不同,铣削可分为立铣、立式卧铣、卧铣、立式卧式联合铣、分度铣等几种分类。
•立铣:铣刀安装在主轴上,工件固定在工作台上,铣刀的切削力主要由工作台和主轴承载。
•立式卧铣:铣刀安装在主轴上,而工件可以在工作台上沿水平方向移动,切削力主要由主轴承载。
•卧铣:铣刀安装在主轴上,工件固定在工作台上,铣刀的切削力主要由工作台承载。
•立式卧式联合铣:铣刀安装在一个可以在水平和垂直方向移动的主轴上,工件可以在工作台上移动,切削力主要由主轴和工作台承载。
•分度铣:通过回转工作台和工作夹具使工件在一定角度下进行铣削,用于加工螺纹、齿轮等。
3. 切削力与刀具选择切削力是铣削加工中重要的参数,它对刀具的选择和加工质量有直接影响。
切削力的大小与多个因素有关,包括切削速度、进给量、切削深度、材料硬度等。
在选择刀具时,需要根据工件的材料、形状和加工要求选择合适的切削刃数、刀具材料和涂层。
当切削力过大时,会引起工件振动和变形,影响加工质量和加工精度。
因此,要通过合理地设计刀具几何形状、提高刀具材料的硬度和强度、采用适当的切削参数等方法来降低切削力。
4. 铣削加工工艺流程铣削加工的工艺流程包括以下几个步骤:1.设计加工方案:根据零件的形状、尺寸和加工要求,确定铣削加工方案,包括选择合适的刀具、加工顺序和切削参数等。
2.设计加工夹具:根据工件的形状和要求,设计合适的加工夹具,用于固定工件,保证加工精度和稳定性。
3.加工前准备:对铣削机床进行检查,检查刀具和夹具的磨损情况,清洁工作台和切削润滑系统。
铣削加工原理及特点
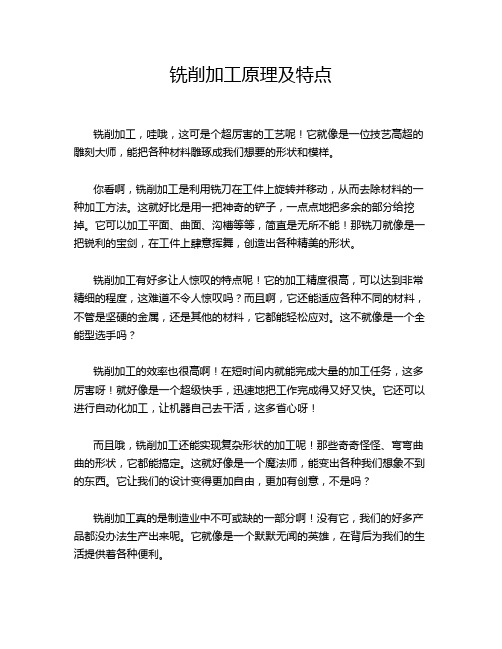
铣削加工原理及特点
铣削加工,哇哦,这可是个超厉害的工艺呢!它就像是一位技艺高超的雕刻大师,能把各种材料雕琢成我们想要的形状和模样。
你看啊,铣削加工是利用铣刀在工件上旋转并移动,从而去除材料的一种加工方法。
这就好比是用一把神奇的铲子,一点点地把多余的部分给挖掉。
它可以加工平面、曲面、沟槽等等,简直是无所不能!那铣刀就像是一把锐利的宝剑,在工件上肆意挥舞,创造出各种精美的形状。
铣削加工有好多让人惊叹的特点呢!它的加工精度很高,可以达到非常精细的程度,这难道不令人惊叹吗?而且啊,它还能适应各种不同的材料,不管是坚硬的金属,还是其他的材料,它都能轻松应对。
这不就像是一个全能型选手吗?
铣削加工的效率也很高啊!在短时间内就能完成大量的加工任务,这多厉害呀!就好像是一个超级快手,迅速地把工作完成得又好又快。
它还可以进行自动化加工,让机器自己去干活,这多省心呀!
而且哦,铣削加工还能实现复杂形状的加工呢!那些奇奇怪怪、弯弯曲曲的形状,它都能搞定。
这就好像是一个魔法师,能变出各种我们想象不到的东西。
它让我们的设计变得更加自由,更加有创意,不是吗?
铣削加工真的是制造业中不可或缺的一部分啊!没有它,我们的好多产品都没办法生产出来呢。
它就像是一个默默无闻的英雄,在背后为我们的生活提供着各种便利。
总之,铣削加工真的是太神奇、太重要了!它的存在让我们的世界变得更加丰富多彩,让我们的生活变得更加美好。
难道你不这么认为吗?。
常用加工工艺

常用加工工艺随着工业的发展,各种加工工艺也越来越多样化。
本文将介绍几种常用的加工工艺,并对其原理和应用进行详细阐述。
一、车削加工车削加工是一种通过旋转工件,利用切削刀具将工件上的材料削除的工艺。
它是金属加工中最常用的一种工艺之一。
在车床上进行车削加工时,切削刀具的刀尖沿工件轴向移动,同时工件也在旋转。
通过控制切削刀具和工件的相对运动,可以实现对工件形状和尺寸的精确控制。
车削加工广泛应用于制造各种轴类零件和外表面精度要求较高的零件。
二、铣削加工铣削加工是一种通过切削刀具旋转的刀尖,对工件上的材料进行切削的工艺。
与车削加工相比,铣削加工可以实现对工件表面的各种不规则形状的加工,如凹槽、齿轮等。
铣削加工通常在铣床上进行,通过控制切削刀具和工件的相对运动,可以获得所需的加工效果。
铣削加工广泛应用于制造各种复杂形状的零件。
三、钻削加工钻削加工是一种通过旋转刀具,在工件上进行孔加工的工艺。
钻削加工通常在钻床上进行,钻床上的刀具称为钻头。
钻头的刀尖具有尖锐的切削边,可以将工件上的材料削除,形成孔洞。
钻削加工可以实现对工件的径向孔和轴向孔的加工。
钻削加工广泛应用于制造各种孔加工。
四、铸造工艺铸造工艺是一种通过将熔融金属或其他物质倒入模具中,待其冷却凝固后取出的工艺。
铸造工艺可以制造出各种形状复杂的零件,且成本较低。
铸造工艺通常包括砂型铸造、金属型铸造和压铸等。
砂型铸造是最常用的一种铸造工艺,它通过在模具中填充湿砂,然后将熔融金属倒入模具中,待其冷却凝固后取出。
金属型铸造是一种使用金属模具进行铸造的工艺,它可以制造出更精确的零件。
压铸是一种通过将熔融金属注入金属模具中,并施加高压使其充满模具并冷却凝固的工艺。
五、焊接工艺焊接工艺是一种通过加热工件和填充材料,使其熔化并形成牢固连接的工艺。
焊接工艺广泛应用于金属材料的连接。
常见的焊接工艺包括电弧焊、氩弧焊和激光焊等。
电弧焊是一种通过电弧产生高温,使工件和填充材料熔化并形成连接的工艺。
铣削加工的范围
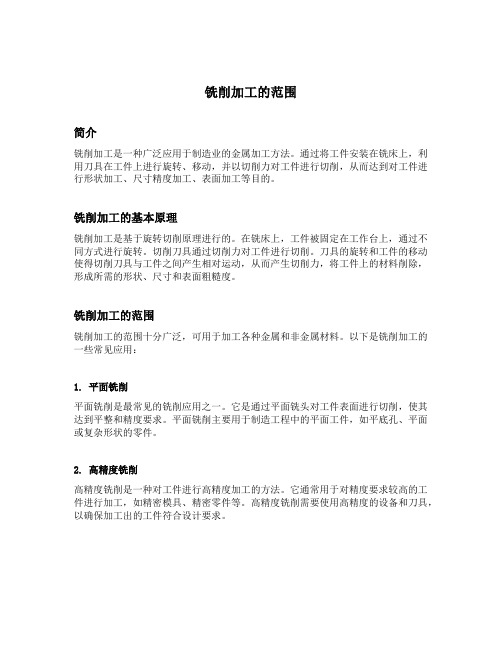
铣削加工的范围简介铣削加工是一种广泛应用于制造业的金属加工方法。
通过将工件安装在铣床上,利用刀具在工件上进行旋转、移动,并以切削力对工件进行切削,从而达到对工件进行形状加工、尺寸精度加工、表面加工等目的。
铣削加工的基本原理铣削加工是基于旋转切削原理进行的。
在铣床上,工件被固定在工作台上,通过不同方式进行旋转。
切削刀具通过切削力对工件进行切削。
刀具的旋转和工件的移动使得切削刀具与工件之间产生相对运动,从而产生切削力,将工件上的材料削除,形成所需的形状、尺寸和表面粗糙度。
铣削加工的范围铣削加工的范围十分广泛,可用于加工各种金属和非金属材料。
以下是铣削加工的一些常见应用:1. 平面铣削平面铣削是最常见的铣削应用之一。
它是通过平面铣头对工件表面进行切削,使其达到平整和精度要求。
平面铣削主要用于制造工程中的平面工件,如平底孔、平面或复杂形状的零件。
2. 高精度铣削高精度铣削是一种对工件进行高精度加工的方法。
它通常用于对精度要求较高的工件进行加工,如精密模具、精密零件等。
高精度铣削需要使用高精度的设备和刀具,以确保加工出的工件符合设计要求。
3. 零件加工铣削加工可用于制造各种类型的零件。
通过选择不同的刀具和加工参数,可以加工出各种形状的零件,包括曲线、孔和凸凹面等。
铣削加工常用于汽车制造、航空航天、机械制造等行业的零件加工。
4. 曲面铣削曲面铣削是一种用于加工曲面形状的铣削方法。
曲面铣削通常需要使用球头刀具,沿着曲面轨迹对工件进行切削,以获得所需的曲面形状。
曲面铣削在制造工程中的应用较广,如模具制造、汽车车身等。
5. 螺纹加工螺纹加工是一种将螺纹形状切削到工件表面的方法。
螺纹加工通常需要使用螺纹铣刀或螺纹刀具进行切削。
它常用于制造螺纹连接件,如螺栓、螺母等。
螺纹加工在机械制造中应用广泛,如汽车制造、机械设备制造等。
铣削加工的优势铣削加工具有以下几个优势:1. 加工效率高铣削加工采用旋转切削原理,能够在较短的时间内加工出复杂形状和高精度的工件。
铣床的原理
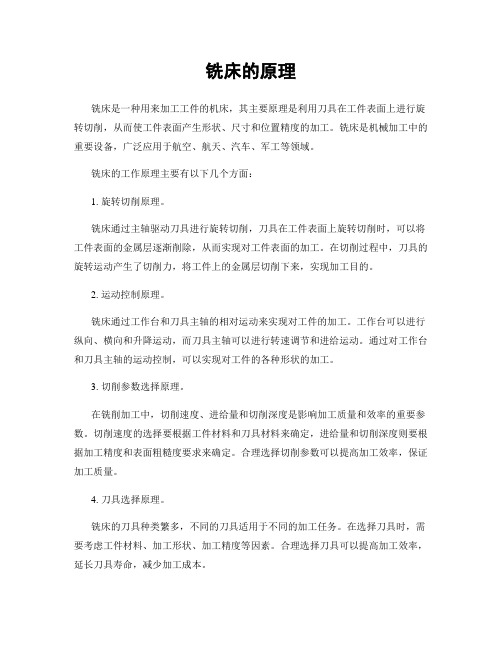
铣床的原理铣床是一种用来加工工件的机床,其主要原理是利用刀具在工件表面上进行旋转切削,从而使工件表面产生形状、尺寸和位置精度的加工。
铣床是机械加工中的重要设备,广泛应用于航空、航天、汽车、军工等领域。
铣床的工作原理主要有以下几个方面:1. 旋转切削原理。
铣床通过主轴驱动刀具进行旋转切削,刀具在工件表面上旋转切削时,可以将工件表面的金属层逐渐削除,从而实现对工件表面的加工。
在切削过程中,刀具的旋转运动产生了切削力,将工件上的金属层切削下来,实现加工目的。
2. 运动控制原理。
铣床通过工作台和刀具主轴的相对运动来实现对工件的加工。
工作台可以进行纵向、横向和升降运动,而刀具主轴可以进行转速调节和进给运动。
通过对工作台和刀具主轴的运动控制,可以实现对工件的各种形状的加工。
3. 切削参数选择原理。
在铣削加工中,切削速度、进给量和切削深度是影响加工质量和效率的重要参数。
切削速度的选择要根据工件材料和刀具材料来确定,进给量和切削深度则要根据加工精度和表面粗糙度要求来确定。
合理选择切削参数可以提高加工效率,保证加工质量。
4. 刀具选择原理。
铣床的刀具种类繁多,不同的刀具适用于不同的加工任务。
在选择刀具时,需要考虑工件材料、加工形状、加工精度等因素。
合理选择刀具可以提高加工效率,延长刀具寿命,减少加工成本。
5. 加工过程控制原理。
铣削加工过程中,需要对切削力、切削温度、切削振动等进行控制,以保证加工质量。
在加工过程中,可以通过刀具形状设计、切削参数选择、冷却润滑等手段来控制加工过程中的各种因素,从而保证加工质量。
总之,铣床是一种重要的机械加工设备,其工作原理涉及到切削原理、运动控制原理、切削参数选择原理、刀具选择原理和加工过程控制原理等方面。
了解铣床的工作原理,可以帮助操作人员更好地进行加工操作,提高加工效率,保证加工质量。
铣削加工

16
背吃刀量ap
1. 切 削 用 量
侧吃刀量ac
铣削速度vc
进 给 量
17
切 削 刃 分 布 位 置
圆 周 铣 削
切削刃分布在刀具 圆周表面的切削方 式Fra bibliotek端 面 铣 削
切削刃分布在刀具端 面上的铣削方式
18
1-1.铣削用量
铣削用量:背吃刀ap、 侧吃刀量ae、 铣削速度vc 进给量
19
1-1背吃刀量ap
31
顺铣
32
逆铣
33
四.铣削力
34
§2 铣 床
35
XA6132型万能升降铣床
36
X8126型万能工具铣床
37
X2010A型龙门铣床
38
圆形工作台铣床
1-主轴箱;2-立柱; 3-圆工作台; 4-滑座;5-床身
39
图所示为在立式双头回转铣床上加工 柴油机连杆端面的情形,夹具沿圆周排列 紧凑,使铣刀的空程时间缩短到最低隈度, 且因机床有两个主轴,能顺次进行粗铣和 精铣,因而大大提高了生产效率。
49
直接分度法 n=40/z
例:有一零件需要加工为8等分。
n=40/z=40 /8=5(转)
50
角度分度法
51
52
53
简单分度法
54
差动分度法
55
差动分度法是利用配换挂轮将分度头主轴 和侧轴连接起来,并松开分度盘侧面紧固 螺钉后进行的分度方法。
56
57
58
通过切削刃基点并垂直于工作平面方向上测量的吃 刀量,即平行于铣刀轴线测量的切削层尺寸。
1-2侧吃刀 ae 平行于工作平面并垂直于切削刃基点的进给 运动方向上测量的吃刀量,即垂直于铣刀轴 线测量的切削层尺寸。
铣刨磨工程训练实习报告

一、实习背景为了更好地将理论知识与实践操作相结合,提高我们的动手能力,学院组织了一次为期一周的铣刨磨工程训练实习。
通过这次实习,我们深入了解了铣刨磨加工的基本原理、操作方法和工艺流程,为今后从事相关技术工作打下了坚实的基础。
二、实习目的1. 理解铣刨磨加工的基本原理和工艺流程。
2. 掌握铣刨磨加工设备的操作方法和注意事项。
3. 提高动手能力,培养团队协作精神。
4. 了解工程实际,为今后从事相关工作积累经验。
三、实习内容1. 铣削加工(1)铣削加工原理:铣削加工是利用铣刀旋转切削,使工件表面产生一定的切削厚度,从而达到加工目的。
铣削加工分为顺铣和逆铣两种方式。
(2)铣削加工设备:实习中,我们学习了铣床的组成、运动和用途,包括卧式铣床、立式铣床和龙门铣床等。
(3)铣削加工操作:在实习过程中,我们学习了铣削加工的基本操作,如铣削平面、沟槽、轮齿等。
同时,我们还了解了铣削加工中刀具的选择、切削参数的确定等。
2. 刨削加工(1)刨削加工原理:刨削加工是利用刨刀直线运动,使工件表面产生一定的切削厚度。
刨削加工分为水平刨削、垂直刨削和斜刨削。
(2)刨削加工设备:实习中,我们了解了刨床的组成、运动和用途,包括牛头刨床、龙门刨床等。
(3)刨削加工操作:在实习过程中,我们学习了刨削加工的基本操作,如刨削平面、沟槽等。
3. 磨削加工(1)磨削加工原理:磨削加工是利用磨具高速旋转,使工件表面产生一定的切削厚度。
磨削加工分为外圆磨削、内圆磨削、平面磨削等。
(2)磨削加工设备:实习中,我们了解了磨床的组成、运动和用途,包括外圆磨床、内圆磨床、平面磨床等。
(3)磨削加工操作:在实习过程中,我们学习了磨削加工的基本操作,如磨削外圆、内圆、平面等。
四、实习心得体会1. 实习过程中,我们深刻体会到了理论知识与实践操作相结合的重要性。
通过实习,我们对铣刨磨加工有了更加深入的了解,为今后从事相关工作打下了基础。
2. 实习过程中,我们学会了正确使用铣刨磨加工设备,掌握了基本的操作方法。
第五章__铣削加工
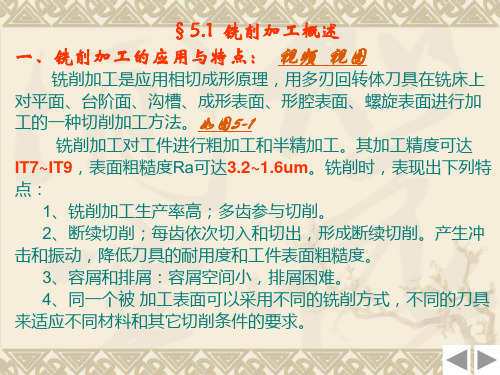
系统代号意义:
锥柄(JT或ST)—圆柄杆接杆(ZB)—刀具; 锥柄(JT或ST)—锥柄杆接杆(KH)—刀具; 锥柄(JT或ST)—带扁尾的莫氏锥柄刀具(M); 锥柄直接接镗孔刀具(JT或ST—T) 锥柄直接连接(JT或ST-X); 弹簧夹头刀柄(JT或ST-Q) TMG10 中字母的含义: Q—弹簧夹头模块; M—有扁尾莫氏锥孔模块; MW—无扁尾莫氏圆锥模块; Z—装钻夹头、短锥模块; KJ—装扩孔钻、铰刀模块; G—攻丝夹头模块; XMA、XMB、XMC—装面铣刀模块; XSL—装三面刃铣刀和套式立铣刀模块; TS—双刃镗刀模块; XP—装削平圆柱铣刀模块; TK—可调镗刀架模块; TQW—倾斜微调镗刀模块; TQC—倾斜粗镗刀模块; TZC—直角粗镗刀模块; TF—浮动铰刀模块 ;
顺铣:
铣刀切出工件时的切削速度方向与工件的进给方向相 同如图5-5。 顺铣的特点: 顺铣时,刀齿的切削厚度ac从最大逐渐减至零,避免了 逆铣时的刀齿挤压、滑行现象,已加工表面加工硬化程度大大 地减轻表面质量也较高,刀具耐用度提高了。同时,垂直方向 的切削分力始终压向工作台,避免了工件的振动。Flash5-2 铣削力的纵向分力方向始终与驱动工作台移动的纵向力方 向相同,丝杠与螺母传动副有间隙如图5-6工作台会出现窜动。 严重时会出现打刀现象。 顺铣应用: 一般应用于零件的平面精加工。 但如采用顺铣时必须要
二、铣削要素
铣削时,铣刀相邻的两个刀齿在工件上先后形成的两个过渡 表面之间的一层金属层为铣削层。 1、铣削用量 (1)背吃刀量: 平行于铣刀轴线测量的切削层尺寸为背吃刀量。端铣时, 为切削层深度;周铣削时,为被加工表面的宽度。 (2)侧吃刀量: 垂直于铣刀轴线测量的切削层尺寸为侧吃刀量端铣时,为 被加工表面宽度;周铣削时为切削层深度。如图5-2 (3)铣削速度: 铣削速度是铣刀主运动的线速度: dn n为转速r/mm vc 1000 d为铣刀的直径
铣削的工作原理特点和应用

铣削的工作原理特点和应用1. 工作原理铣削是一种通过刀具旋转而物料移动的切削加工方法,常用于将工件表面切削成所需形状和尺寸的加工过程。
铣削的工作原理如下:•切削刀具:铣削过程中,切削刀具通过旋转运动,将工件表面切削下去。
切削刀具通常采用高速旋转的刀片,根据切削所需形状和材料特性选择合适的刀具。
•切削动力:铣削过程中,切削刀具通过切削力作用于工件,将工件表面切削下去。
切削动力是通过铣床或加工中心的主轴传递给切削刀具的。
•切削运动:铣削过程中,切削刀具旋转运动的同时,由于工件的进给动作,将工件表面切削下去。
切削运动是切削刀具与工件相对运动的结果,使刀具切削下去并切削出所需的形状。
2. 特点铣削具有以下几个特点:•多功能性:铣削可以加工各种形状和尺寸的工件,包括平面、曲面、孔位、齿槽等,具有广泛的应用领域。
•高精度:铣削过程中,切削刀具通过旋转运动,能够实现对工件表面的精确切削,保证产品的尺寸和形状精度。
•高效率:铣削可以采用高速切削,有效提高加工效率,节省生产时间。
•灵活性:铣削过程中,可以通过调整刀具、工件和机床的位置关系,实现不同切削形式和切削方向,满足不同加工要求。
•刀具寿命长:铣削刀具经过适当的刀具损耗和刃口修整,可以延长刀具寿命,降低加工成本。
•适用性广泛:铣削适用于各种材料的加工,包括金属材料、非金属材料等。
3. 应用铣削在各个行业具有广泛的应用,主要包括以下几个方面:•机械制造业:铣削在机械制造业中常用于加工零件表面、孔洞、齿轮等,以满足产品的精确尺寸和形状要求。
•车辆制造业:对于汽车、飞机、火车等交通工具的制造,铣削是必不可少的加工方法,用于加工汽车零件、飞机翼型等。
•电子电器业:铣削在电子电器业中主要用于加工电子元器件、印刷电路板等,提高产品的精度和可靠性。
•仪器仪表业:铣削在仪器仪表业中常用于加工各种精密仪器的外壳、尺寸和形状要求。
•船舶制造业:铣削在船舶制造业中用于加工船体零件、船舶轴轴承等,提高船舶的安全性和稳定性。
铣削的原理

铣削的原理铣削是一种常见的机械加工方法,通过旋转刀具对工件进行切削,以达到加工工件的目的。
在工业生产中,铣削广泛应用于各种金属和非金属材料的加工,具有高效、精度高等优点。
本文将介绍铣削的原理及其相关知识。
首先,铣削的原理是利用刀具对工件进行切削。
铣削刀具一般由刀柄、刀杆和刀片组成,刀片上有多个切削刃,刀具在旋转的同时,沿着工件的表面进行切削,将工件上的材料去除,从而形成所需的形状和尺寸。
其次,铣削的原理还包括切削力和切削热的产生。
在铣削过程中,刀具对工件进行切削时,会产生切削力,这是由于刀具对工件材料的切削作用所产生的力。
同时,切削过程中还会产生大量的切削热,这是由于刀具与工件之间的摩擦和切削作用所产生的热量。
另外,铣削的原理还涉及到切屑的形成。
在铣削过程中,刀具对工件进行切削时,会将工件上的材料切削下来,形成切屑。
切屑的形成不仅会影响加工表面的质量,还会影响刀具的寿命和加工效率。
此外,铣削的原理还包括切屑的排除和切削液的使用。
在铣削过程中,切屑的排除对于保证加工质量和刀具的正常使用至关重要。
同时,为了降低切削热和摩擦,提高切削效率,通常会使用切削液来冷却和润滑切削区域。
最后,铣削的原理还涉及到刀具的选择和加工参数的确定。
不同的工件材料和加工要求需要选择不同类型的刀具,同时还需要确定合适的切削速度、进给速度和切削深度等加工参数,以保证加工质量和提高加工效率。
综上所述,铣削的原理涉及到刀具的切削、切削力和切削热的产生、切屑的形成、切屑的排除和切削液的使用、刀具的选择和加工参数的确定等多个方面。
了解铣削的原理对于提高加工质量、提高生产效率具有重要意义,也为工程师和操作人员提供了指导和参考。
希望本文能够帮助读者更好地理解铣削的原理,为实际生产提供帮助。
第1铣工技术铣削原理ppt课件
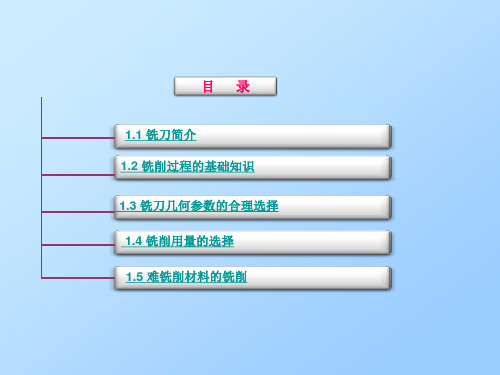
1.2 铣削过程的基础知识
1.2.1铣削过程中的变形
刀具在金属切削过程的实质是被切削金属在刀具切削刃和前刀面的挤压作 用下,产生剪切滑移的变形过程,如图1-2所示。在刀具切削力的作用下,被 切割的金属层首先产生压缩弹性变形,当剪应力超过材料屈服极限后,在与受 力方向成45°方向上产生最大剪应力,金属内部晶格发生滑移,即在剪切面上 产生塑性变形。刀具继续前进,切削力增大,由于切削刃的刀楔作用,产生应 力集中,使切削刃附近金属剪应力超过强度极限而被剥离。切削层产生塑性变 形的同时,在切削刃附近剥离,形成切割作用。变形后剥离的金属层在刀具前 刀面的挤推作用下,沿前刀面流出,即产生切屑。
2)指状铣刀 指状铣刀包括立铣刀和键槽铣刀等,尺寸规格一般只标注外
圆直径。如锥柄立铣刀上标有Ф18,则表示该立铣刀的外圆直径
是18 mm。 3)盘形铣刀 角度铣刀和半圆铣刀等盘形铣刀,一般以外圆直径×宽度×
内孔直径×角度(或圆弧半径)表示。例如,角度铣刀的外圆直 径为80 mm,宽度为22 mm,内孔直径为27 mm,角度为60°,则标
记为80×22×27×60°。同样道理,在半圆铣刀的末尾标有8R,
则表示铣刀圆弧半径为8 mm。
1.1.3 铣刀的主要参数
铣刀是一种多切削刃的刀具,在了解铣刀的组成和几何角度时, 可把铣刀看做是由多把简单的切刀组合而成的,如图1-1(a)所示。 如图1-1(b)所示为铣刀各部分名称及相关的辅助平面。
2.积屑瘤对切削加工影响 积屑瘤冷焊在刀具切削刃和前刀面的前端,其形成后便可代替切 削刃和前刀面进行切削,从而保护了切削刃和前刀面。但是积屑瘤的 稳定性较差,当积屑瘤达到一定高度时,常因冷焊接的破裂而脱落( 部分或全部),有可能把刀具前刀面靠近刀尖的表面金属带走一部分 ,反而容易加剧刀具的磨损。 积屑瘤在切削过程中的产生和脱落,还常常将积屑瘤碎片黏结在 已加工表面上,增大了已加工表面的粗糙度。积屑瘤表面粗糙会使已 加工表面产生误差复映
- 1、下载文档前请自行甄别文档内容的完整性,平台不提供额外的编辑、内容补充、找答案等附加服务。
- 2、"仅部分预览"的文档,不可在线预览部分如存在完整性等问题,可反馈申请退款(可完整预览的文档不适用该条件!)。
- 3、如文档侵犯您的权益,请联系客服反馈,我们会尽快为您处理(人工客服工作时间:9:00-18:30)。
一、銑削原理
以銑刀的旋轉運動和工件的進給運動相配合進行的切削加工方法稱為銑削
主運動:將金屬材料切削下來的運動叫主運動
進給運動:逐步地把金屬層投入切削的運動稱為進給運動
二、順銑和逆銑
1.順銑
銑刀的旋轉方向與工件的進給方向相同時,稱為順銑
A.順銑的優點:
A-1.順銑時,切削力向下,有壓緊工件的作用,對於不易夾緊的及細長工件較為合適
A-2.順銑時刀刃切入容易,對已加工面的擠壓磨擦較小,故刀刃磨損較慢,加工出的工件表面粗糙度較好
A-3.順銑對消耗在進給運動方面的功率較小,切削時較輕松
B.順銑的缺點:
B-1.順銑時,刀刃從工件表面切入,因此當工件表面有硬皮或雜質時,刀刃容易磨損的損壞
B-2.順銑時,因銑刀的作用力方向與工件進給方向相同,所以會拉動工作台,當絲杆間隙較大時,工作台被拉動後,由於每齒進
給易突然增大,會造成刀齒折斷,甚至工件夾具機台損壞的後
果,所以在絲杆間隙大而且切削阻力較大時,嚴禁用順銑進行
工作.
2.逆銑
銑刀的旋轉方向與工件的進給方向反時的銑削方式稱為逆銑
A.逆銑的優點
A-1.逆銑時(由於刀刃阻力不是以工件的外表切放),故對表面有硬皮的毛坯件進行切削時,對刀刃的損壞影響較小
A-2.逆銑時,切削阻力與工件進給方向相反,銑削中不會改變絲杆間隙方向,銑削平穩,可進行重切削
B.逆銑的缺點
B-1.逆銑時,垂直作用力向上,容易導致工件被拉起(臥銑由這突出)
B-2.逆銑時,由於刀刃開始切入時要滑移一小段距離,故刀刃易磨損,并使已加工面受到冷擠壓和磨擦,影響工件的表面粗糙度
B-3.逆銑時消耗在進給運動方面的功率較大
綜合上述,在一般情況下,均應采用逆銑,由於順銑也有較多優點,故在精切削或機台絲杆間隙小時可采用順銑
3.對稱銑削
工件處在銑刀中間時的銑削稱為對稱銑削刀齒的前半部分為逆銑,後半部分為順銑,故工件和作台容易產動,此外對窄長的工件容易造成變形和彎曲,只有在工件寬度接近銑刀直徑時采用
三、切削用量(銑削)
1.進給量( F )
工件在銑削時,相對銑刀的進給速度叫進給量
A.每齒進給量( S齒毫米/每尺)MM/2
在銑刀轉過一個刀齒的時間內,工件沿進給方向所移動的距離
B.每分鐘進給量(S毫米/分鐘)mm/min
在一分鐘的時間內,工件沿進給方向所移動的距離
一般在銑床或說明書上記載數值均為每分鐘進給量
C.進給量的計算公式﹕F=S齒*T*N
T=銑刀刀刃數N=主軸轉數(rpm)
2.切削速度
銑刀刀刃上最大直徑處,在一分鐘內所走過的距離,代號V=m/min,在銑床上是以銑床主軸轉速來調整切削速度,但是對銑刀使用等因素的影,是以切削進度來考慮的,因此,大多數情況下是在選擇合理的切削速度後,再根據切削速度,銑刀直徑來計算轉速轉速(轉/分)=100*切削速度(米/分)/3.14*銑刀直徑(毫米) (n=1000*Q/3.14*D)
3.切削寬度
在既垂直於銑削深度,同時又垂直於進給方向測量出的被切削金屬層的尺寸叫銑削寬度
4.切削深度
工件已加工表面和待加工表面之間的垂直距離叫銑削深度
用立銑刀銑槽時,切削深度不宜超過銑刀直徑的0.5倍,側銑時依切削寬度不同而切削深度不同,若切削寬主為1/2D時,切削深度約為D
5.選用原則
A.銑削深度,銑削寬度和進給量三者決定了銑削體積,若銑削體積增
大時,應降低銑削速度,即降低轉速
B.銑刀直徑越大時其轉速越低﹔銑刀直徑越小,其轉速越高
C.碳化鎢刀具比高速鋼之銑削速度高兩倍,且需較快之進給,即使用
碳化鎢刀具時,所選用之轉速,進給量均應高於高速鋼銑刀
D.提高銑削速度而降低進給量能得到較好之面粗度
E.加工硬質材質時,應選較小之銑削速度﹔加軟材質時,應采用較大
之銑削速度
F.在確保品質的前提下,首先應選用較大的切削寬度,較大的銑削深
度,再選用較大的每齒進給量,最後確定銑削速度
四、粗加工與精加工
為了得到光亮準確的加工表面,在銑削加工中應先粗銑後精銑
1.粗銑
粗銑為重切削,必須在短時間內去掉多余材料,因為銑削深度﹑銑削寬度﹑進給量應選擇較大,但為了保証銑刀之壽命,則應選擇較小的切削速度,刀具選用上選擇刀齒較少切屑槽較大且較堅固之銑刀,粗加工一般須留0.15~0.3mm左右精加工量,軟材料預留多一些,硬材料預留少一些
2.精銑
精銑為輕切削,需保証光滑表面及精確之尺寸,為達到此目的,需選用較高的銑削速度和較小的進給量及切削深度,精銑時應注意因每齒切削量大小,導致刃口在工件表面磨擦而非切削的現象,容易造成銑刀磨耗,故應根據面精度及尺寸要求合理選用進刀量及轉速
五、切削液
1.切削液之作用
A.降低刀具及工件溫度
B.減少切屑﹑刀具及工件間的摩擦
C.增加工件表面的光滑度
D.減少動力消耗,增加切削效率
E.沖刷切屑離開加工區域
F.延長刀具之使用壽命
G.減少刀具及工件可能發生的腐蝕鏽損
2.加工對切削液之要求
A.在物理上和化學上反應穩定,不變質
B.對加工人員無毒性,無損害
C.對工件,機台不會產生腐蝕
D.淡色透明,無揮發性,且不易著火
3.切削液的種類
A.以冷卻為主的切削液
此類要削液一般為水溶液,其價格低廉,流動性好,散熱快,可用
20~30倍水稀釋
B.以潤滑為主的切削液
此類切削液大都是油類,潤滑性較好,但流動性差,散熱慢
4.切削液的選用
A.粗加工時,應選用以冷卻為主的切削液
B.精加工時,應選用以潤滑為的切削液
C.加工鑄鐵和黃銅時,不宜使用切削液
D.在用硬質合金刀具作高速切削時,因刀具耐熱性好,一般不需使用
切削液如需使用切削液,則需從開始切削前就充分連續澆注,避免硬質合金因驟冷驟驟熱而碎裂。