冲天炉熔炼工艺操作规程
冲天炉熔炼安全操作规程
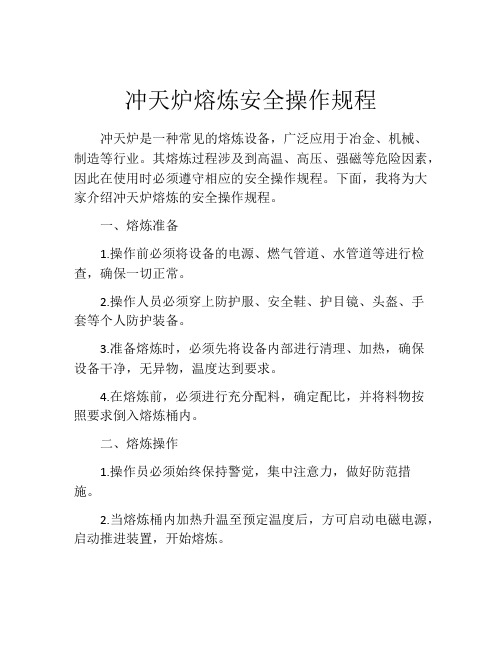
冲天炉熔炼安全操作规程冲天炉是一种常见的熔炼设备,广泛应用于冶金、机械、制造等行业。
其熔炼过程涉及到高温、高压、强磁等危险因素,因此在使用时必须遵守相应的安全操作规程。
下面,我将为大家介绍冲天炉熔炼的安全操作规程。
一、熔炼准备1.操作前必须将设备的电源、燃气管道、水管道等进行检查,确保一切正常。
2.操作人员必须穿上防护服、安全鞋、护目镜、头盔、手套等个人防护装备。
3.准备熔炼时,必须先将设备内部进行清理、加热,确保设备干净,无异物,温度达到要求。
4.在熔炼前,必须进行充分配料,确定配比,并将料物按照要求倒入熔炼桶内。
二、熔炼操作1.操作员必须始终保持警觉,集中注意力,做好防范措施。
2.当熔炼桶内加热升温至预定温度后,方可启动电磁电源,启动推进装置,开始熔炼。
3.操作员必须时刻关注设备运行情况,确保其正常运转、熔炼效果良好。
4.操作过程中必须保持适当的熔炼压力和速度,以充分熔化物料,并控制物质燃烧速度,防止设备损坏。
5.若发现设备出现异常,必须立即停机,排除故障。
如遇重大事故,应立即通知有关部门,做好报告和应急处理。
三、操作结束1.熔炼完成后,必须关闭电源、燃气管道及推进装置,将设备恢复到初始状态。
2.设备内残留的物料必须清理干净,避免对设备造成损坏。
3.设备必须经过检查,确认安全后方可下线。
以上就是冲天炉熔炼安全操作规程的基本内容。
在熔炼过程中,操作员必须时刻保持警觉,秉持安全第一的原则,保护好自己和周围的人员安全。
同时,也需要加强设备的保养和维护,做好熔炼前的准备工作,确保设备正常运转,从而最大程度地避免事故发生。
冲天炉熔炼工艺规程
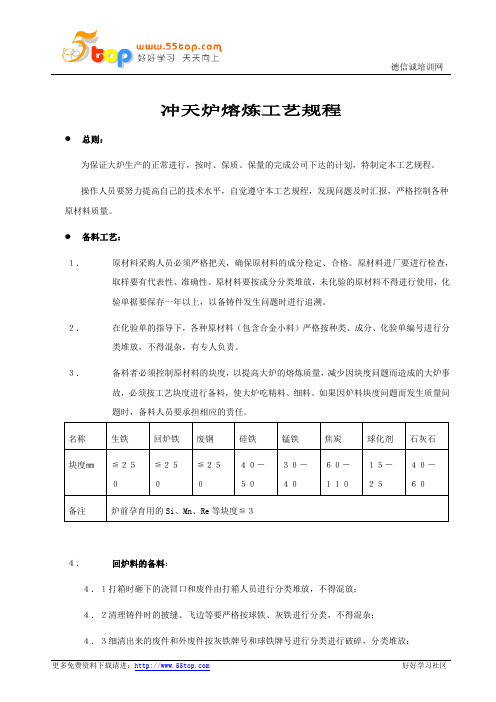
冲天炉熔炼工艺规程●总则:为保证大炉生产的正常进行,按时、保质、保量的完成公司下达的计划,特制定本工艺规程。
操作人员要努力提高自己的技术水平,自觉遵守本工艺规程,发现问题及时汇报,严格控制各种原材料质量。
●备料工艺:1.原材料采购人员必须严格把关,确保原材料的成分稳定、合格。
原材料进厂要进行检查,取样要有代表性、准确性。
原材料要按成分分类堆放,未化验的原材料不得进行使用,化验单据要保存一年以上,以备铸件发生问题时进行追溯。
2.在化验单的指导下,各种原材料(包含合金小料)严格按种类、成分、化验单编号进行分类堆放,不得混杂,有专人负责。
3.备料者必须控制原材料的块度,以提高大炉的熔炼质量,减少因块度问题而造成的大炉事故,必须按工艺块度进行备料,使大炉吃精料、细料。
如果因炉料块度问题而发生质量问题时,备料人员要承担相应的责任。
4.回炉料的备料:4.1打箱时砸下的浇冒口和废件由打箱人员进行分类堆放,不得混放;4.2清理铸件时的披缝、飞边等要严格按球铁、灰铁进行分类,不得混杂;4.3细清出来的废件和外废件按灰铁牌号和球铁牌号进行分类进行破碎,分类堆放;4.4外购的回炉铁,应进行化验后根据成分进行分类堆放,成分特殊时,应进行评审师是否能使用?如果成分特殊要进行特殊放置;4.5破碎铁要按照块度进行破碎,破碎人员要负责料场的管理,分类明确,质量合格。
4.6大炉返回的铁水饼及条铁,由大炉人员进行分类堆放或按照牌号加入料桶内;5.废钢、生铁的备料:5.1生铁必须破碎成单块,按照种类、牌号、化验单分类堆放;5.2废钢备料人员不得备用块度超标的废钢,废钢中不得有危险的容器、及不明物。
废钢的成分要求稳定、单一,废钢的厚度要大于3㎜,不得有严重的锈蚀、氧化;高Mn、Cr废钢要单独堆放,单独配料,杜绝混料,以免造成铸件的报废。
修炉、修包工艺:1.修后炉:1.1修炉前必须做好一切准备工作,检查上料口及周围、上料设施的情况,并将其清扫干净,确保设备及人员的安全;1.2修后炉时首先清除炉膛内部的挂渣,特别时风口及其周围的部分,熔化带以上不许修补的部位,如有挂渣、凸起应清除干净。
冲天炉熔炼操作工艺
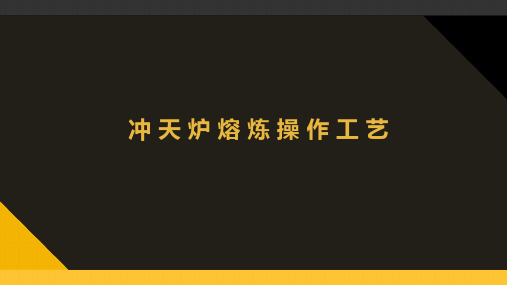
(7)熔化及控制
熔化初期应经常疏通风口,以保证风口畅通,观察并记录风量、风压的变化。从正式送风开始8~10min,在第一排风口可看到铁液滴快速下落,说明底焦高度合适。若大于10min,说明底焦高度偏高,应适当降低层焦量;若小于8min,说明底焦高度偏低,应适当增加层焦量,直至从风口看到底焦燃烧正常。冲天炉是连续熔化,应保证连续加料,始终保持炉料满炉 以满足炉料的充分预热,这对保证铁液温度稳定是很重要的。根据配料单,及时调整配料比例,每次调整前,应加一批隔离焦,处理好交界铁液。
冲天炉正常操作过程
(8)停风打炉
THANKS
冲天炉ห้องสมุดไป่ตู้炼操作工艺
A
燃料与原材料的选用
B
操作参数的选定
C
操作过程各个环节的控制
冲天炉熔炼操作工艺
冲天炉正常操作过程
(1)修炉
铲除炉壁表面残渣挂铁
刷上泥浆水
覆上修炉材料,敲打结实
修炉材料组成
40%~50%耐火泥
适量的水分
60%~50%石英砂
冲天炉正常操作过程
(1)修炉
修前炉则用老煤粉与耐火泥的混合料
结构紧实
尺寸正确
表面光滑
冲天炉正常操作过程
(2)烘炉
炉子修毕后,可在炉底和前炉装入木柴,引火烘炉;前炉必须烘透,以保证首包铁液温度。
(3)点火
烘炉后,开风前2.5~3h加入木柴,引火点着,并敞开风口盖作自然通风
冲天炉正常操作过程
(4)加底焦
待木柴燃旺后,由加料口往炉内加入三分之一的底焦,待其烧着后,再加入约一半左右的底焦,然后鼓小风几分钟,并测定底焦高度,再加底焦至规定的高度。这里的所谓底焦量,是指装入金属炉料以前加入炉内的全部焦炭量,而底焦高度则是从第一排风口中心线起,至底焦顶面为止的那一部分高度,炉缸内的底焦是不包括在底焦高度内的。
冲天炉熔炼安全操作规程模版

冲天炉熔炼安全操作规程模版一、概述本安全操作规程旨在规范冲天炉熔炼过程中的安全操作措施,保障人员和设备的安全。
所有从事冲天炉熔炼操作的人员必须遵守此规程。
二、安全准备1. 在进行冲天炉熔炼前,必须进行安全检查,确保设备正常运行,消防器材齐全并处于可用状态。
2. 所有从事熔炼作业的人员必须穿戴合适的个人防护装备,包括防火服、耐热手套、防护眼镜、耐酸碱靴等。
3. 了解熔炼物料的安全性质和危险特性,做好相应的防护措施。
三、操作要点1. 根据熔炼工艺要求,准备好所需的物料,并按照标准比例进行配料,确保配料的准确性和稳定性。
2. 在装料前,需检查熔炼炉的密闭性,确保无漏风现象。
3. 严禁将易燃物品或其他危险物品放置在炉周范围内,以避免引发火灾或爆炸。
4. 老化炉皮和冶炼渣应及时清理,以确保炉腔的正常使用。
5. 在熔炼过程中,应确保炉腔内的温度、压力和熔体的流动情况处于正常范围内。
如发现异常情况,应及时停机排查。
6. 操作人员在熔炼过程中应保持警觉,严禁戏水、嬉戏或与他人不当言行,确保操作专注和安全。
7. 熔炼过程中,操作人员应保持良好的通讯,及时与其他相关人员进行沟通,确保信息的畅通。
8. 在换班或作业结束时,需要对熔炼炉进行全面检查,确保设备和场地的安全。
四、紧急处理1. 发生火灾时,操作人员应立即拉响警钟,并按照紧急处理程序启动事故应急预案。
2. 发生气体泄漏或毒气中毒事故时,立即撤离现场,并通知专业人员进行处理。
3. 发生人身伤害事故时,立即寻求医疗救助,并向相关主管报告事故情况。
五、消防安全1. 冲天炉熔炼现场应配备足够数量的消防器材,并定期进行检查和维护。
2. 熔炼过程中,操作人员应保持消防通道畅通,严禁堆放易燃物品。
3. 熔炼过程中如发现明火或火星飞溅,应立即采取措施进行扑灭和防止火势扩大。
六、废弃物处理1. 废弃物应按照相关规定进行分类、封装和储存,并交由专门处理机构进行处理。
2. 废弃物处理记录应详细填写,并定期归档保存。
冲天炉铸造过程中安全操作规程(3篇)

冲天炉铸造过程中安全操作规程冲天炉是一种用于炼铁、炼钢等冶金熔炼过程的重要设备,但由于其操作过程涉及高温、高压、易燃等安全风险,因此需要制定一系列的安全操作规程,以确保人员安全和生产顺利进行。
以下是冲天炉铸造过程中的安全操作规程,共计____字:一、冲天炉基本安全操作规程1. 操作人员必须经过相应的技术培训,并持有相关的操作证书,方可从事冲天炉操作工作。
2. 在进入冲天炉作业区域前,必须戴上符合标准的防护帽、耐高温手套、防护眼镜、防护口罩等个人防护装备。
3. 在操作过程中,严禁饮酒、嚼槟榔等妨碍工作安全的行为。
4. 进入冲天炉作业区域前,必须检查有关设备和安全装置是否正常运行。
5. 炉前设有警示牌和安全标志的位置,不得随意移动或遮挡。
6. 严禁在冲天炉作业区域内吸烟或使用明火。
7. 操作人员在离开冲天炉作业区域前,必须停止设备运行,并将电源关闭。
8. 发现安全事故隐患或紧急情况时,应立即进行报警,并采取必要的安全措施。
9. 在冲天炉作业结束后,必须进行设备检查、清理和维护,确保设备安全。
二、冲天炉高温操作安全操作规程1. 操作人员必须戴上符合标准的高温防护服、耐高温手套、耐高温防护鞋等个人防护装备。
2. 在操作过程中,禁止随意触摸或接触高温部件,以免导致烫伤。
3. 炉体内温度高,操作人员不得长时间停留在炉旁,以免受热过度。
4. 在操作过程中,操作人员应保持清醒和注意力集中,以防意外发生。
5. 在高温操作过程中,必须经常检查冲天炉设备和管道的温度状况,如发现异常应及时采取措施。
6. 炉体内产生的高温气体和废气必须通过合适的通风设备进行排放。
7. 禁止将易燃物品置于冲天炉附近,以防高温引发火灾。
8. 结束高温操作后,必须等待冲天炉完全冷却后再进行设备检查和维护。
三、冲天炉高压操作安全操作规程1. 操作人员在进入冲天炉作业区域前,必须检查高压设备和管道的工作状态是否正常。
2. 炉体内的高压气体和流体必须遵循相关操作规程和安全标准进行控制和释放。
冲天炉熔炼工序工艺规程
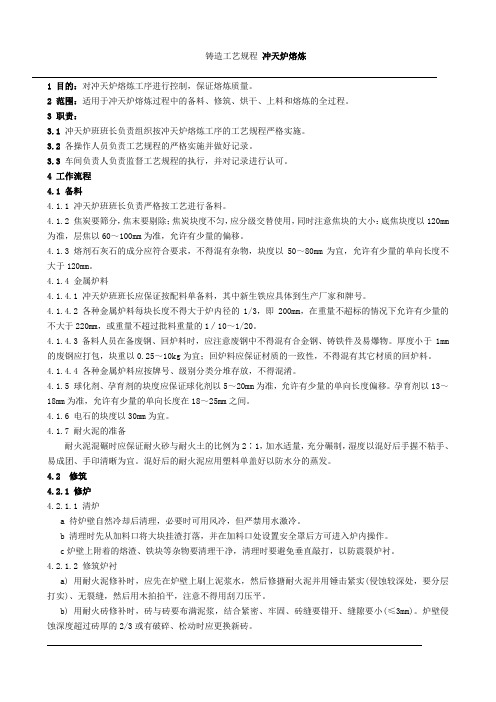
铸造工艺规程冲天炉熔炼1 目的:对冲天炉熔炼工序进行控制,保证熔炼质量。
2 范围:适用于冲天炉熔炼过程中的备料、修筑、烘干、上料和熔炼的全过程。
3 职责:3.1冲天炉班班长负责组织按冲天炉熔炼工序的工艺规程严格实施。
3.2各操作人员负责工艺规程的严格实施并做好记录。
3.3车间负责人负责监督工艺规程的执行,并对记录进行认可。
4 工作流程4.1 备料4.1.1 冲天炉班班长负责严格按工艺进行备料。
4.1.2 焦炭要筛分,焦末要剔除;焦炭块度不匀,应分级交替使用,同时注意焦块的大小:底焦块度以120mm 为准,层焦以60~100mm为准,允许有少量的偏移。
4.1.3 熔剂石灰石的成分应符合要求,不得混有杂物,块度以50~80mm为宜,允许有少量的单向长度不大于120mm。
4.1.4 金属炉料4.1.4.1 冲天炉班班长应保证按配料单备料,其中新生铁应具体到生产厂家和牌号。
4.1.4.2 各种金属炉料每块长度不得大于炉内径的1/3,即200mm,在重量不超标的情况下允许有少量的不大于220mm,或重量不超过批料重量的1∕10~1/20。
4.1.4.3备料人员在备废钢、回炉料时,应注意废钢中不得混有合金钢、铸铁件及易爆物。
厚度小于1mm 的废钢应打包,块重以0.25~10kg为宜;回炉料应保证材质的一致性,不得混有其它材质的回炉料。
4.1.4.4 各种金属炉料应按牌号、级别分类分堆存放,不得混淆。
4.1.5 球化剂、孕育剂的块度应保证球化剂以5~20mm为准,允许有少量的单向长度偏移。
孕育剂以13~18mm为准,允许有少量的单向长度在18~25mm之间。
4.1.6 电石的块度以30mm为宜。
4.1.7 耐火泥的准备耐火泥混碾时应保证耐火砂与耐火土的比例为2∶1,加水适量,充分碾制,湿度以混好后手握不粘手、易成团、手印清晰为宜。
混好后的耐火泥应用塑料单盖好以防水分的蒸发。
4.2 修筑4.2.1 修炉4.2.1.1 清炉a 待炉壁自然冷却后清理,必要时可用风冷,但严禁用水激冷。
冲天炉操作规程
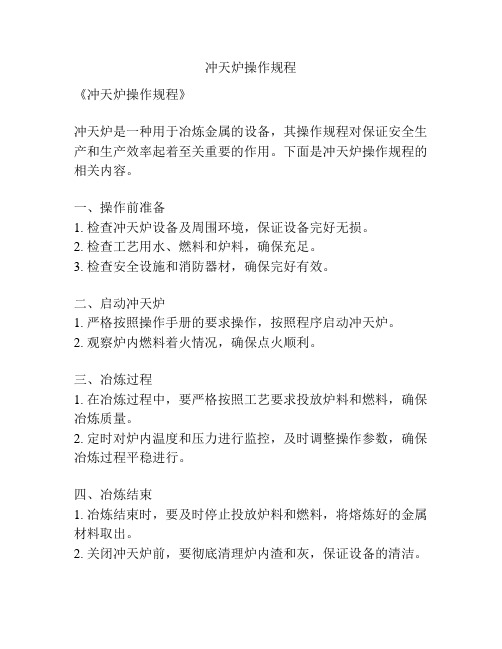
冲天炉操作规程
《冲天炉操作规程》
冲天炉是一种用于冶炼金属的设备,其操作规程对保证安全生产和生产效率起着至关重要的作用。
下面是冲天炉操作规程的相关内容。
一、操作前准备
1. 检查冲天炉设备及周围环境,保证设备完好无损。
2. 检查工艺用水、燃料和炉料,确保充足。
3. 检查安全设施和消防器材,确保完好有效。
二、启动冲天炉
1. 严格按照操作手册的要求操作,按照程序启动冲天炉。
2. 观察炉内燃料着火情况,确保点火顺利。
三、冶炼过程
1. 在冶炼过程中,要严格按照工艺要求投放炉料和燃料,确保冶炼质量。
2. 定时对炉内温度和压力进行监控,及时调整操作参数,确保冶炼过程平稳进行。
四、冶炼结束
1. 冶炼结束时,要及时停止投放炉料和燃料,将熔炼好的金属材料取出。
2. 关闭冲天炉前,要彻底清理炉内渣和灰,保证设备的清洁。
五、安全操作
1. 操作人员要严格遵守操作规程,不得擅自更改操作流程。
2. 在操作过程中,要严格遵守安全操作规定,确保人身安全。
3. 发现设备异常或安全隐患时,要及时上报,并停止冶炼操作。
《冲天炉操作规程》的制定和执行,能够在一定程度上提高冶炼生产效率,保护设备和人员的安全。
希望所有操作人员严格遵守规程,确保冲天炉设备的正常运行和生产的顺利进行。
冲天炉熔炼操作规程
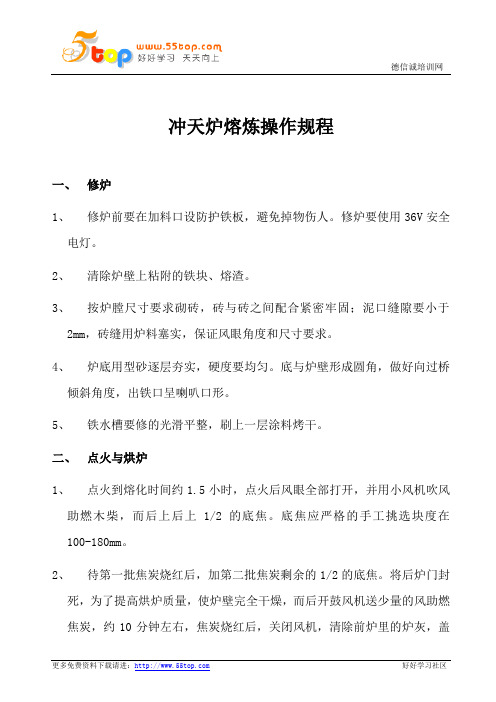
冲天炉熔炼操作规程一、修炉1、修炉前要在加料口设防护铁板,避免掉物伤人。
修炉要使用36V安全电灯。
2、清除炉壁上粘附的铁块、熔渣。
3、按炉膛尺寸要求砌砖,砖与砖之间配合紧密牢固;泥口缝隙要小于2mm,砖缝用炉料塞实,保证风眼角度和尺寸要求。
4、炉底用型砂逐层夯实,硬度要均匀。
底与炉壁形成圆角,做好向过桥倾斜角度,出铁口呈喇叭口形。
5、铁水槽要修的光滑平整,刷上一层涂料烤干。
二、点火与烘炉1、点火到熔化时间约1.5小时,点火后风眼全部打开,并用小风机吹风助燃木柴,而后上后上1/2的底焦。
底焦应严格的手工挑选块度在100-180mm。
2、待第一批焦炭烧红后,加第二批焦炭剩余的1/2的底焦。
将后炉门封死,为了提高烘炉质量,使炉壁完全干燥,而后开鼓风机送少量的风助燃焦炭,约10分钟左右,焦炭烧红后,关闭风机,清除前炉里的炉灰,盖好炉盖上料。
三、上料1、上料人员应提前将称提前调好,掌握自己所上的品种规格重量。
2、上第一批料的石灰石用量是正常用量的2.5倍。
炉料长度不要大于炉经的1/3,炉料中不得混有轴承钢、密封金属罐。
3、上满炉料后,预热炉料30分钟开始溶化,开风半分钟后关闭风眼。
4、密切关注前炉观查孔,禁止上大料。
使炉内保持充满状态,使炉料能够充分预热。
5、大炉操作人员在大炉溶化时,随时观察风眼变化,使风眼保持明亮畅通。
6、更换新材料牌号时,应加隔焦,是正常层焦的2倍。
四、打炉1、停炉前先打开风眼观察孔,而后停风。
2、炉底不得有积水,应提前铺好一层干砂防止铁水飞溅。
3、炉料落炉后,材料分清走。
五、风机操作的有关注意事项1、每次开车前必须检查润滑是否适量,新风机运行100小时后,更换润滑剂,以后每半年检查一次,检修、跟换润滑剂,平时不需要填加润滑剂。
2、开车前盘车三转。
冲天炉熔炼安全操作规程
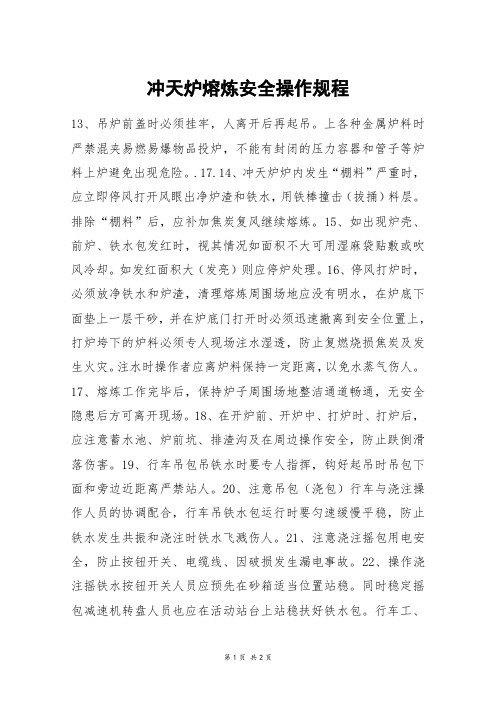
冲天炉熔炼安全操作规程13、吊炉前盖时必须挂牢,人离开后再起吊。
上各种金属炉料时严禁混夹易燃易爆物品投炉,不能有封闭的压力容器和管子等炉料上炉避免出现危险。
.17.14、冲天炉炉内发生“棚料”严重时,应立即停风打开风眼出净炉渣和铁水,用铁棒撞击(拔捅)料层。
排除“棚料”后,应补加焦炭复风继续熔炼。
15、如出现炉壳、前炉、铁水包发红时,视其情况如面积不大可用湿麻袋贴敷或吹风冷却。
如发红面积大(发亮)则应停炉处理。
16、停风打炉时,必须放净铁水和炉渣,清理熔炼周围场地应没有明水,在炉底下面垫上一层干砂,并在炉底门打开时必须迅速撤离到安全位置上,打炉垮下的炉料必须专人现场注水湿透,防止复燃烧损焦炭及发生火灾。
注水时操作者应离炉料保持一定距离,以免水蒸气伤人。
17、熔炼工作完毕后,保持炉子周围场地整洁通道畅通,无安全隐患后方可离开现场。
18、在开炉前、开炉中、打炉时、打炉后,应注意蓄水池、炉前坑、排渣沟及在周边操作安全,防止跌倒滑落伤害。
19、行车吊包吊铁水时要专人指挥,钩好起吊时吊包下面和旁边近距离严禁站人。
20、注意吊包(浇包)行车与浇注操作人员的协调配合,行车吊铁水包运行时要匀速缓慢平稳,防止铁水发生共振和浇注时铁水飞溅伤人。
21、注意浇注摇包用电安全,防止按钮开关、电缆线、因破损发生漏电事故。
22、操作浇注摇铁水按钮开关人员应预先在砂箱适当位置站稳。
同时稳定摇包减速机转盘人员也应在活动站台上站稳扶好铁水包。
行车工、浇注工要集中注意力,相互配合,平稳浇注,确保浇注安全。
23、铁水浇注前或浇注中应有专人监视指挥,非操作人员不得站在浇注现场.18.观看滞留。
24、当浇注途中砂箱跑铁水时应有专人有条不紊地予以处置堵漏,防止漏铁水接触到电器或电源上,以防触电或烧伤事故发生。
25、冲天炉在熔炼过程中各岗位各工种操作人员严禁违章违规操作。
因操作人员违章违规操作对设备的损坏及人员伤害事故均由当事人负责。
冲天炉熔炼设备操作规程

冲天炉熔炼设备操作规程1目的规范冲天炉熔炼的生产过程,确保提供温度和成分都符合要求的铁水,防止和消除熔炼过程中可能出现的各种故障。
2适用范围适用于公司冲天炉铸造铁水的熔炼。
3工艺规定3.1 备料3.1.1焦碳、生铁、铁合金、石灰石等材料的成分,性能及其它质量指标必须经技检部检验合格后使用。
3.1.2金属料的最大尺寸不得超过加料口附近炉径的三分之一。
3.1.3废钢、回炉铁锈蚀严重的必须处理方可投炉。
3.1.4 各类炉料分类堆放,不得混杂,未经处理的弹壳,废枪支等危险物不得混入,防止橡胶、塑料等有害杂物的投炉。
3.1.5 各类炉料保持干燥、洁净,防止附着泥砂。
3.1.6 铁合金的粒度为20—80mm,如受潮应烘干后使用。
3.1.7 孕育剂干净无水分,粒度为5—10mm。
3.2铸造工艺配方为确保刹车盘的铸造材质,满足GB/T9439—1988、JB/T7945—1955中关于HT250之规定,针对客户要求,结合本公司生产实际特制定冲天炉配方(冲天炉分配方B、配方B):冲天炉熔炼配方B:采用固定的张店14#原料铁冲天炉熔炼配方B:3.3修炉与烘炉:3.3.1 修炉须在大炉冷却后进行,必要时可鼓风吹冷,但不得用水浇冷。
3.3.2 冲天炉修炉时,先铲除炉壁表面的残渣挂铁,小于半块或破碎松动的耐火砖换成新砖,清理时避免水平或过重敲击,耐火砖的接触面要涂满耐火泥,贴合紧密,砖缝要小于2mm,上下砖缝必须错开,然后刷上泥浆水,覆上修炉材料,并用锤敲打结实,修炉材料由40—50%耐火泥和60—50%石英砂及适量的水泥混制而成,炉膛尺寸,风口大小,形状、斜度、位置应符合工艺要求。
3.3.3 修前炉使用老煤粉与耐火泥的混合料,炉壁必须结构紧实,尺寸正确,表面光滑。
3.3.4 炉壁与炉底交界处应修出半径为40—60mm的园角,并向出铁口方向倾斜5°—6°。
3.3.5 过桥保持平直并与观察孔在同一直线上。
冲天炉炉操作规程 JN7
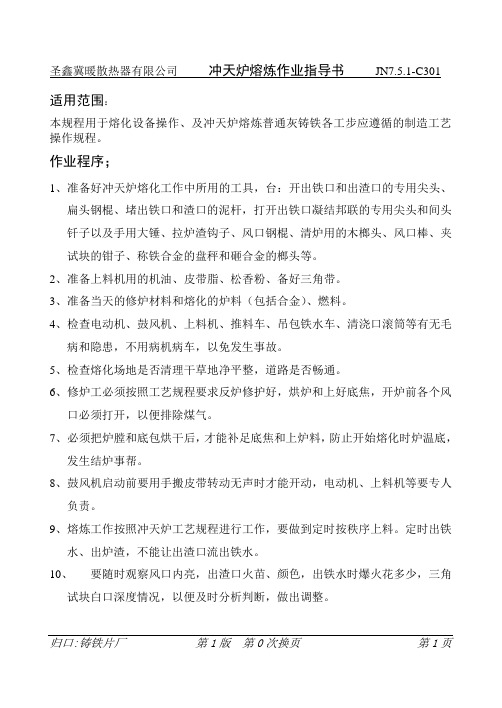
适用范围:本规程用于熔化设备操作、及冲天炉熔炼普通灰铸铁各工步应遵循的制造工艺操作规程。
作业程序;1、准备好冲天炉熔化工作中所用的工具,台:开出铁口和出渣口的专用尖头、扁头钢棍、堵出铁口和渣口的泥杆,打开出铁口凝结邦联的专用尖头和间头钎子以及手用大锤、拉炉渣钩子、风口钢棍、清炉用的木榔头、风口棒、夹试块的钳子、称铁合金的盘秤和砸合金的榔头等。
2、准备上料机用的机油、皮带脂、松香粉、备好三角带。
3、准备当天的修炉材料和熔化的炉料(包括合金)、燃料。
4、检查电动机、鼓风机、上料机、推料车、吊包铁水车、清浇口滚筒等有无毛病和隐患,不用病机病车,以免发生事故。
5、检查熔化场地是否清理干草地净平整,道路是否畅通。
6、修炉工必须按照工艺规程要求反炉修护好,烘炉和上好底焦,开炉前各个风口必须打开,以便排除煤气。
7、必须把炉膛和底包烘干后,才能补足底焦和上炉料,防止开始熔化时炉温底,发生结炉事帮。
8、鼓风机启动前要用手搬皮带转动无声时才能开动,电动机、上料机等要专人负责。
9、熔炼工作按照冲天炉工艺规程进行工作,要做到定时按秩序上料。
定时出铁水、出炉渣,不能让出渣口流出铁水。
10、要随时观察风口内亮,出渣口火苗、颜色,出铁水时爆火花多少,三角试块白口深度情况,以便及时分析判断,做出调整。
归口:铸铁片厂第1版第0次换页第1页熔炼工艺规程:一、准备工作:1、准备好炉前所用工具和材料。
2、准备好炉前检验用的三角试块的模型和工具。
3、检查溅温计是否正常。
4、检查原材料的数量和质量。
5、准备好配料表、加料单。
二、炉前工操作规程:1、从加料口放入引火材料然后加入木柴,从工作门点烯,对炉子进行烘干,且要烘干烘透。
炉子烘干后,即可进行底焦的点火工作,站抚加入一些大2、块的引火木柴,等烯着后再加40%底焦,并打开风口和出铁口,用自然通风使焦碳燃烧,待炉内四周呈暗红色时,再加其余20%底焦,并调整到适当高度。
3、底焦加好后并燃烧后,加入石灰石,首次加入量为批料中石灰石的两倍,且石灰石要加在炉堂中心,4、然后要严格按配料单进行装料,秤量要准确,秤量允许误差5-8%,并且做好加料单记录。
冲天炉熔炼操作工艺介绍
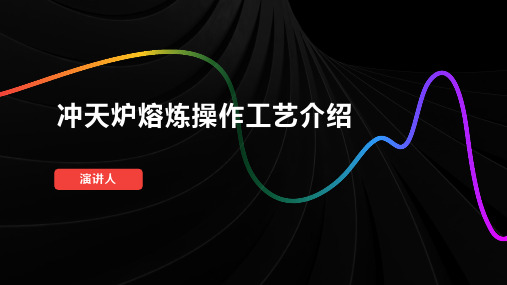
演讲人
目录
01. 冲天炉熔炼原理 02. 冲天炉熔炼操作 03. 冲天炉熔炼安全与环保
冲天炉熔炼原理
熔炼过程
01
装料:将炉料装入冲 天炉内,包括铁料、 焦炭、熔剂等
05
脱磷:铁水中的磷元 素在高温下与氧化钙 反应,生成磷石灰, 降低铁水中的磷含量
02
预热:将炉料预热至 一定温度,使炉料中 的水分蒸发,提高炉 料的透气性
原料称量:按
3
照熔炼配方称
量原料
原料混合:将各 4 种原料混合均匀, 确保熔炼效果
熔炼过程控制
温度控制:根据不同金属的熔点,控制炉
01
温在合适的范围内
气氛控制:通过调整炉内气氛,保证金属 02 的纯度和质量
熔炼时间控制:根据金属的熔化速度和熔 03 炼要求,控制熔炼时间
炉料配比控制:根据金属的熔炼要求和炉
事故处理与预防
操作人员必须 定期对设备进 制定应急预案,
经过专业培训, 行检查和维护, 提高事故处理 具备相应的操 确保设备安全 能力 作技能和经验 可靠
01
03
05
02
严格遵守操作 规程,避免违 规操作
04
配备必要的安 全防护设备, 如灭火器、防 毒面具等
06
加强环保意识, 减少废气、废 水、废渣等污 染物排放
01 冲天炉熔炼是一种利用高温和氧化还原反应进 行金属熔炼的方法。
02 反应过程中,燃料燃烧产生高温,使金属氧化物 和碳发生氧化还原反应,生成金属和二氧化碳。
03 反应过程中,金属氧化物被还原,碳被氧化, 产生大量的热能,使金属熔化。
04 反应过程中,金属和熔渣分离,形成金属液和 熔渣,分别排出。
冲天炉冶炼操作规程冶炼规程

冲天炉冶炼操作规程一、材料准备1、焦炭、石灰石、生铁、回炉铁,废钢以及修炉、修包用的材料(耐火砖、耐火泥、焦炭粉等)的成份,性能主其他质量指标,均应符合有关规定。
2、焦炭:焦炭入厂应妥善保管,并保持干燥,使用前应筛选,块度应符合1.1规定。
(表1.1)3、石灰石不得混有杂物,块度为20-60mm。
4、金属炉料:4.1所有金属炉料每块长度不得大于加料口处最小直径的1/3,每块金属炉料的最大重量不应超过表1.2规定。
4.2锈蚀严重的废钢,除锈后方能使用。
废钢块度差别较大时应搭配使用。
厚度小于3mm的应不超过该批料废钢重的20%,厚度小于1mm的应捆扎打包使用,严防合金钢混入。
(表1.2)4.3 新生铁、回炉铁应分类堆放,粘附的砂泥、熔渣应清理干净。
4.4投炉铁合金的块度应为20-80mm,碎小的应粘结成块备用,铁合金应放置于干燥处,如受潮应烘干。
4.5加料前仔细检查,遇有可疑物品应及时处理并报告有关人员,严格避免爆炸物品及其它有害杂物加入炉内。
5、孕育剂:5.1孕育剂的粒度应在2-10mm范围内。
5.2孕育剂应注意防潮。
如受潮、应在使用前烘干。
6、修炉、修包材料:6.1耐火砖,存放时时应注意防潮,搬运时应避免损坏。
6.2耐火粘土、焦炭分、石英砂等存放时应防止受潮,不得混入杂物,混合耐火材料的配制应根据工艺规定的配方进行。
6.3充填炉底用砂须筛除其中混杂的铁块、熔渣等杂物。
7、点火木柴:应干燥易燃,长度在500mm以下,粗细为60-150mm。
8、其它材料:8.1保温、聚渣、脱硫用之草灰、苏打等材料必须干燥或预热。
8.2堵口泥料及基它材料均应按要求及时准备。
二、熔化及控制1、准备1.1开风前必须准备好熔化过程所需的全部工具、仪表、试样砂型和完整的炉前记录表格。
1.2按规定准备好炉前处理用孕育剂、合金、保温聚渣和脱硫等材料,以及堵口泥塞。
2、送风:2.1按规定检查和启动风机,运转正常后关闭风眼。
2.2在熔炼过程中风眼应保持明亮、畅通,如有结渣应及时排除。
冲天炉熔炼工艺操作规程
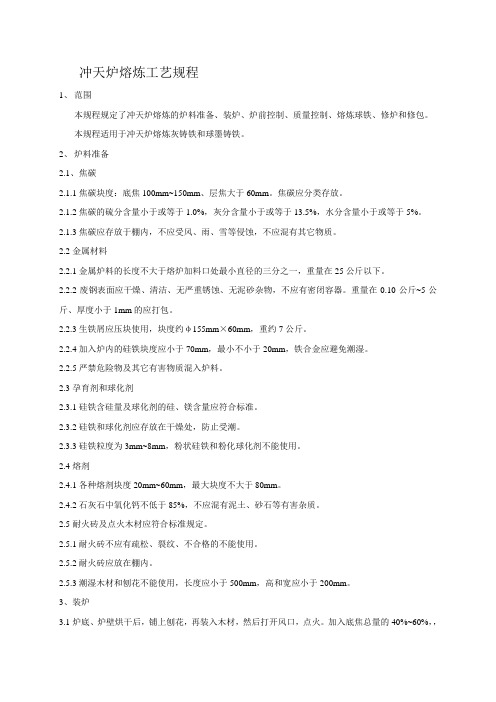
冲天炉熔炼工艺规程1、范围本规程规定了冲天炉熔炼的炉料准备、装炉、炉前控制、质量控制、熔炼球铁、修炉和修包。
本规程适用于冲天炉熔炼灰铸铁和球墨铸铁。
2、炉料准备2.1、焦碳2.1.1焦碳块度:底焦100mm~150mm、层焦大于60mm。
焦碳应分类存放。
2.1.2焦碳的硫分含量小于或等于1.0%,灰分含量小于或等于13.5%,水分含量小于或等于5%。
2.1.3焦碳应存放于棚内,不应受风、雨、雪等侵蚀,不应混有其它物质。
2.2金属材料2.2.1金属炉料的长度不大于熔炉加料口处最小直径的三分之一,重量在25公斤以下。
2.2.2废钢表面应干燥、清洁、无严重锈蚀、无泥砂杂物,不应有密闭容器。
重量在0.10公斤~5公斤、厚度小于1mm的应打包。
2.2.3生铁屑应压块使用,块度约φ155mm×60mm,重约7公斤。
2.2.4加入炉内的硅铁块度应小于70mm,最小不小于20mm,铁合金应避免潮湿。
2.2.5严禁危险物及其它有害物质混入炉料。
2.3孕育剂和球化剂2.3.1硅铁含硅量及球化剂的硅、镁含量应符合标准。
2.3.2硅铁和球化剂应存放在干燥处,防止受潮。
2.3.3硅铁粒度为3mm~8mm,粉状硅铁和粉化球化剂不能使用。
2.4熔剂2.4.1各种熔剂块度20mm~60mm,最大块度不大于80mm。
2.4.2石灰石中氧化钙不低于85%,不应混有泥土、砂石等有害杂质。
2.5耐火砖及点火木材应符合标准规定。
2.5.1耐火砖不应有疏松、裂纹、不合格的不能使用。
2.5.2耐火砖应放在棚内。
2.5.3潮湿木材和刨花不能使用,长度应小于500mm,高和宽应小于200mm。
3、装炉3.1炉底、炉壁烘干后,铺上刨花,再装入木材,然后打开风口,点火。
加入底焦总量的40%~60%,,等全部烧着后再加入余下底焦,随后短时鼓风,吹净灰分,趟透过桥,并从风口处观察和测量底焦高度、进行调整。
3.2装料时注意炉料均匀分布,在熔化过程中使炉料料柱与装料口平齐。
冲天炉熔炼安全操作规程(正式)

编订:__________________单位:__________________时间:__________________冲天炉熔炼安全操作规程(正式)Standardize The Management Mechanism To Make The Personnel In The Organization Operate According To The Established Standards And Reach The Expected Level.Word格式 / 完整 / 可编辑文件编号:KG-AO-9021-12 冲天炉熔炼安全操作规程(正式)使用备注:本文档可用在日常工作场景,通过对管理机制、管理原则、管理方法以及管理机构进行设置固定的规范,从而使得组织内人员按照既定标准、规范的要求进行操作,使日常工作或活动达到预期的水平。
下载后就可自由编辑。
1、操作工必须掌握冲天炉熔炼的生产技术和安全技术操作规程,注意安全用电和加强自我安全防护意识。
上班前不准喝酒和操作中吸烟。
使用好劳保用品。
2、冲天炉在开炉前,必须清除炉坑周围障碍物。
工作场地,炉前坑和炉底部不得有积水及明水;不准堆放易燃、易爆、易碎、腐蚀有毒物品。
非生产人员(外来人员)杜绝入内与操作人员聊天或滞留熔炼现场。
3、检查上料地车、扒车、行车、钢丝绳、链条和各种吊具,电器设备、电源等性能是否确保安全、可靠。
检查鼓风机、抽水机、脱硫装置、除尘设备运行可否正常。
4、检查炉底,炉底立柱,前炉和后炉炉门,前炉盖,堵孔泥塞装置和风眼盖等部份确保牢靠或密封。
修炉时注意重物坠落伤人,注意检查照明线路、电风扇、风镐等电动工具的安全绝缘性能。
5、检查大小铁水包、出铁槽、出渣槽、浇口杯和各种开炉用具是否符合生产技术和安全技术要求。
确保其修好、修牢烘干和备齐达到使用性能良好。
6、出铁前,铁水包应对准出铁槽放正、放稳。
出铁水时操作人员(炉前工)必须站在出铁槽侧面操作,并穿戴好工作服、防护眼镜、安全帽、防护手套、劳保鞋等劳保用品。
冲天炉操作工艺守则
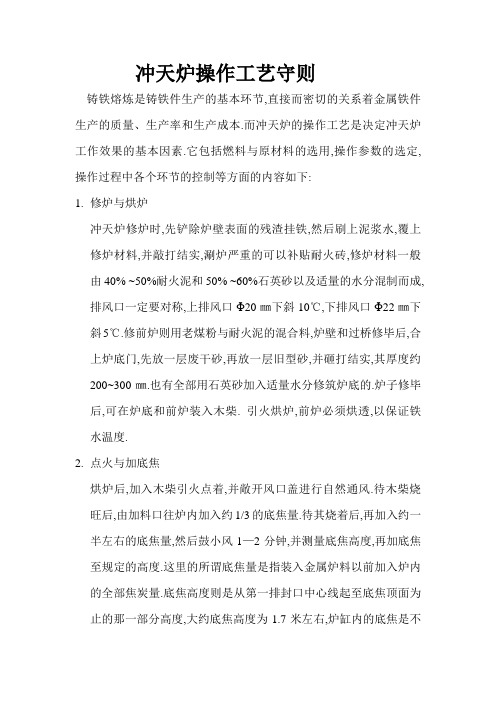
冲天炉操作工艺守则铸铁熔炼是铸铁件生产的基本环节,直接而密切的关系着金属铁件生产的质量、生产率和生产成本.而冲天炉的操作工艺是决定冲天炉工作效果的基本因素.它包括燃料与原材料的选用,操作参数的选定,操作过程中各个环节的控制等方面的内容如下:1.修炉与烘炉冲天炉修炉时,先铲除炉壁表面的残渣挂铁,然后刷上泥浆水,覆上修炉材料,并敲打结实,涮炉严重的可以补贴耐火砖,修炉材料一般由40% ~50%耐火泥和50% ~60%石英砂以及适量的水分混制而成,排风口一定要对称,上排风口Φ20㎜下斜10℃,下排风口Φ22㎜下斜5℃.修前炉则用老煤粉与耐火泥的混合料,炉壁和过桥修毕后,合上炉底门,先放一层废干砂,再放一层旧型砂,并砸打结实,其厚度约200~300㎜.也有全部用石英砂加入适量水分修筑炉底的.炉子修毕后,可在炉底和前炉装入木柴. 引火烘炉,前炉必须烘透,以保证铁水温度.2.点火与加底焦烘炉后,加入木柴引火点着,并敞开风口盖进行自然通风.待木柴烧旺后,由加料口往炉内加入约1/3的底焦量.待其烧着后,再加入约一半左右的底焦量,然后鼓小风1—2分钟,并测量底焦高度,再加底焦至规定的高度.这里的所谓底焦量是指装入金属炉料以前加入炉内的全部焦炭量.底焦高度则是从第一排封口中心线起至底焦顶面为止的那一部分高度,大约底焦高度为1.7米左右,炉缸内的底焦是不包括在底焦高度内的.3.装料与开风加完底焦后,加入石灰石,其加入量约为层焦石灰石用量的2倍,然后封闭冲天炉工作门,关上风口盖鼓风三、四分钟,再敞开风口,自然通风,并进行装料.一般先熔化低牌号的铸铁,然后熔化高牌号的,每批金属料一般先加废钢,然后新生铁、回炉铁与铁合金,加入一批金属料后再加层焦和石灰石,石灰石量约占层焦重量的30%每上10批料补加一批接力焦以补充底炭,换料时要加适量的隔焦防止混料.4.停风与打炉停风时先打开部分风口,然后关风,停风的时间要掌握好,既要防止因停风过早而造成铁水量的不足,也要避免停风过晚而造成底焦和炉衬的烧损,停风前要确保炉内有1~2批压炉料.以上冲天炉的操作工艺已定为一种工艺纪律,要严肃执行,不得随意更改,不能玩忽职守,要尽职尽责.如有违规现象,本公司必会严惩不怠,严肃处理,情节严重的还要追加经济处罚.沈阳市明锋铸业有限公司技术质量部2007年3月20日。
冲天炉熔炼安全操作规程
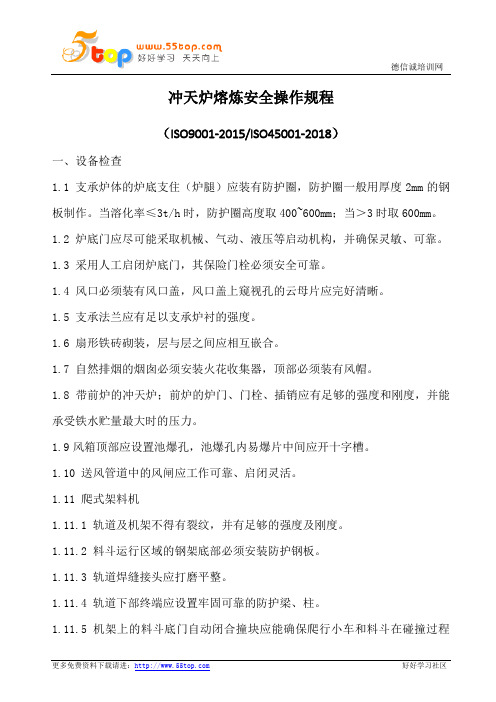
冲天炉熔炼安全操作规程(ISO9001-2015/ISO45001-2018)一、设备检查1.1 支承炉体的炉底支住(炉腿)应装有防护圈,防护圈一般用厚度2mm的钢板制作。
当溶化率≤3t/h时,防护圈高度取400~600mm;当>3时取600mm。
1.2 炉底门应尽可能采取机械、气动、液压等启动机构,并确保灵敏、可靠。
1.3 采用人工启闭炉底门,其保险门栓必须安全可靠。
1.4 风口必须装有风口盖,风口盖上窥视孔的云母片应完好清晰。
1.5 支承法兰应有足以支承炉衬的强度。
1.6 扇形铁砖砌装,层与层之间应相互嵌合。
1.7 自然排烟的烟囱必须安装火花收集器,顶部必须装有风帽。
1.8 带前炉的冲天炉;前炉的炉门、门栓、插销应有足够的强度和刚度,并能承受铁水贮量最大时的压力。
1.9风箱顶部应设置池爆孔,池爆孔内易爆片中间应开十字槽。
1.10 送风管道中的风闸应工作可靠、启闭灵活。
1.11 爬式架料机1.11.1 轨道及机架不得有裂纹,并有足够的强度及刚度。
1.11.2 料斗运行区域的钢架底部必须安装防护钢板。
1.11.3 轨道焊缝接头应打磨平整。
1.11.4 轨道下部终端应设置牢固可靠的防护梁、柱。
1.11.5 机架上的料斗底门自动闭合撞块应能确保爬行小车和料斗在碰撞过程中运行正常、平稳。
1.11.6 爬行小车在全行程内应运行平稳、无卡阻现象。
1.11.7 车轮无裂纹、空载时四个车轮均应接触轨道。
1.11.8 轮轴上的压板和防松垫圈应齐全、紧固可靠。
1.11.9 滑轮应完好、严禁有裂纹或缺口,并应装有防止钢丝绳滑出轮槽的卡板。
1.11.10 料斗应装置平衡配重,防止料斗底门因自重,炉料负荷或振动而自动打开。
1.11.11 料斗门自动启闭装置的行程滑槽、滑块、撞轮应运行灵活、平稳、可靠。
1.11.12 滑槽压板应安装牢固,并保证料斗底门的自动启闭灵活、可靠。
1.11.13 绞接料斗底门和滑块的边杆应有足够的强度和刚度,其安装位置应保证当料斗底门自动启闭时能按设计轨灵活、平稳地运行,不出现“死点”。
冲天炉熔炼安全操作规程范本
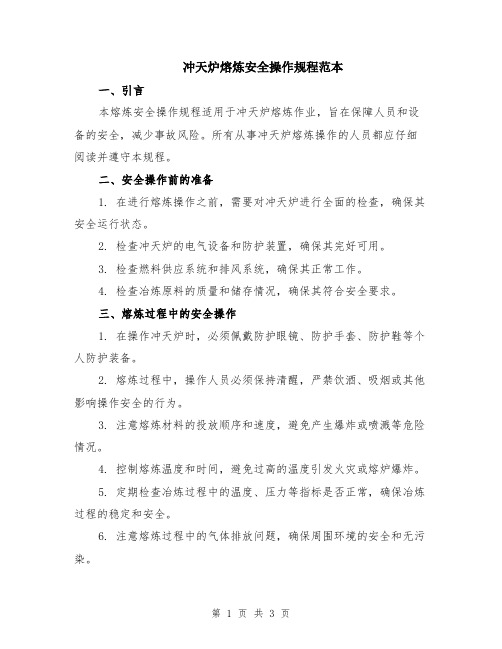
冲天炉熔炼安全操作规程范本一、引言本熔炼安全操作规程适用于冲天炉熔炼作业,旨在保障人员和设备的安全,减少事故风险。
所有从事冲天炉熔炼操作的人员都应仔细阅读并遵守本规程。
二、安全操作前的准备1. 在进行熔炼操作之前,需要对冲天炉进行全面的检查,确保其安全运行状态。
2. 检查冲天炉的电气设备和防护装置,确保其完好可用。
3. 检查燃料供应系统和排风系统,确保其正常工作。
4. 检查冶炼原料的质量和储存情况,确保其符合安全要求。
三、熔炼过程中的安全操作1. 在操作冲天炉时,必须佩戴防护眼镜、防护手套、防护鞋等个人防护装备。
2. 熔炼过程中,操作人员必须保持清醒,严禁饮酒、吸烟或其他影响操作安全的行为。
3. 注意熔炼材料的投放顺序和速度,避免产生爆炸或喷溅等危险情况。
4. 控制熔炼温度和时间,避免过高的温度引发火灾或熔炉爆炸。
5. 定期检查冶炼过程中的温度、压力等指标是否正常,确保冶炼过程的稳定和安全。
6. 注意熔炼过程中的气体排放问题,确保周围环境的安全和无污染。
7. 注意冶炼过程中的能源消耗情况,合理利用能源,减少能源浪费和环境污染。
8. 操作人员离开熔炼现场前,必须关闭熔炼设备,确保其停止运行。
四、事故应急处理1. 在发生事故时,操作人员首先要确保自己的安全,迅速报告相关部门。
2. 接到事故报告后,相关人员需要立即采取措施避免事故蔓延,并启动事故应急预案。
3. 在事故处理过程中,操作人员要积极配合救援工作,确保事故得到及时控制和处理。
4. 事故处理完毕后,需要对事故原因进行调查和分析,总结教训,提出改进措施。
五、安全教育与培训1. 所有从事冲天炉熔炼操作的人员必须接受相关的安全教育和培训,掌握相关操作技能和安全知识。
2. 定期组织安全培训,提高操作人员的安全意识和技能水平。
3. 相关人员应及时了解和学习最新的安全操作规程和技术标准,保持工作知识的更新与提升。
六、安全生产责任1. 各级管理人员应严格履行安全生产责任,建立健全安全管理制度和考核机制。
冲天炉熔炼安全操作规程
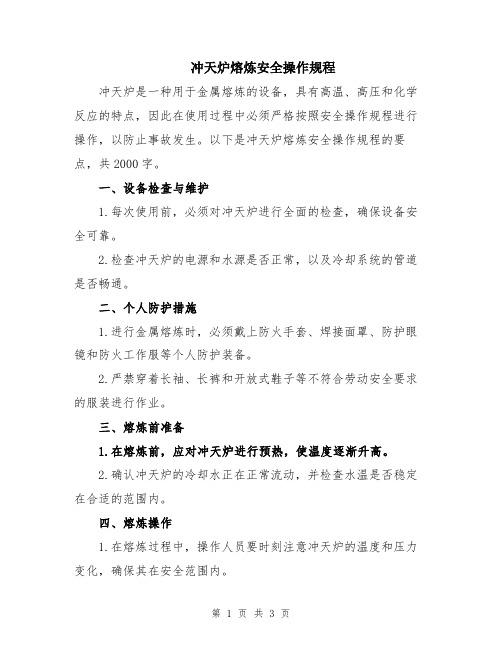
冲天炉熔炼安全操作规程冲天炉是一种用于金属熔炼的设备,具有高温、高压和化学反应的特点,因此在使用过程中必须严格按照安全操作规程进行操作,以防止事故发生。
以下是冲天炉熔炼安全操作规程的要点,共2000字。
一、设备检查与维护1.每次使用前,必须对冲天炉进行全面的检查,确保设备安全可靠。
2.检查冲天炉的电源和水源是否正常,以及冷却系统的管道是否畅通。
二、个人防护措施1.进行金属熔炼时,必须戴上防火手套、焊接面罩、防护眼镜和防火工作服等个人防护装备。
2.严禁穿着长袖、长裤和开放式鞋子等不符合劳动安全要求的服装进行作业。
三、熔炼前准备1.在熔炼前,应对冲天炉进行预热,使温度逐渐升高。
2.确认冲天炉的冷却水正在正常流动,并检查水温是否稳定在合适的范围内。
四、熔炼操作1.在熔炼过程中,操作人员要时刻注意冲天炉的温度和压力变化,确保其在安全范围内。
2.操作人员必须熟悉并掌握熔炼过程中的不同温度区域的特点,以便在需要时做出相应的调整。
五、熔炼后处理1.在熔炼结束后,应立即关闭冲天炉,并断开电源。
2.冷却后,操作人员必须仔细检查冲天炉的各个部位是否正常,并清理熔炼产物和残渣。
六、事故应急措施1.遇到紧急情况时,操作人员要立即停止熔炼工作,采取安全避险措施,并及时向主管部门报告。
2.如发生火灾,需立即使用灭火器进行扑灭,必要时撤离现场并报警呼叫消防人员。
七、禁止行为1.严禁在熔炼设备周围堆放可燃物品,以免引发火灾。
2.禁止将熔炼设备用于非金属材料的熔炼,以防止设备损坏和事故发生。
八、员工培训和考核1.操作人员必须参加冲天炉熔炼的相关培训,并定期进行监测和考核,以提高安全意识和应急处理能力。
2.鼓励员工提出关于冲天炉安全操作的建议和改进建议,以不断完善现有的安全操作规程。
九、设备定期检修和维护1.定期进行冲天炉的检修和维护,确保设备的正常运行和使用寿命。
2.对冲天炉的关键部件进行定期更换和更新,以保证设备的安全可靠性。
冲天炉熔炼安全操作规程范本

冲天炉熔炼安全操作规程范本第一章总则第一条目的与依据为了保障冲天炉熔炼作业的安全和顺利进行,减少事故发生,特制定本规程。
本规程遵循《中华人民共和国安全生产法》、《中华人民共和国炉窑行业安全生产规程》等相关法律法规第二条适用范围本规程适用于我公司冲天炉的熔炼作业。
第二章工艺概述第三条工艺流程冲天炉的熔炼作业主要分为以下几个步骤:1. 原材料准备2. 装料3. 点火预热4. 加热恒温5. 卸料6. 清理维护第四条作业人员职责1. 熔炼工:负责冲天炉的日常操作和生产工作。
2. 检修工:负责冲天炉的维护、检修和故障排除。
3. 安全员:负责安全监督和事故预防工作。
第三章安全操作规程第五条熔炼工作前的准备1. 熔炼工在进入作业区域前,必须穿戴好安全防护装备,包括防火服、防护鞋、防护眼镜、耳塞等。
2. 在检查设备和工具是否完好无损后,方可开始作业。
3. 确保作业区域干燥、通风良好。
第六条原材料准备1. 原材料必须经过验收合格方可使用。
2. 进行熔炼作业前,必须对原材料进行分类、清理,并将其堆置整齐。
第七条装料1. 在进行装料前,必须确保熔炼炉的温度已经降到合适的状态。
2. 装料必须按照工艺要求准确称量,严禁超量装料。
3. 装料结束后,必须关闭装料设备,并进行严密封堵。
第八条点火预热1. 在点火前,必须进行相关安全检查,确保点火环境安全。
2. 使用专业点火设备进行点火,禁止使用明火和易燃物进行点火。
3. 点火后应加强监控,确保点火过程的安全。
第九条加热恒温1. 在加热恒温过程中,必须定时检查熔炉的温度和压力。
2. 出现异常情况时,必须停止供热,及时排除故障。
3. 加热恒温过程中,必须严格禁止随意开启炉门、炉盖,以防发生爆炸危险。
第十条卸料1. 在卸料前,必须确保熔炉内温度降至安全温度。
2. 卸料时,必须按照工艺要求进行操作,禁止随意抖动炉体。
3. 卸料结束后,需对炉体进行清理,清除残渣。
第十一条清理维护1. 清理炉体时,必须确认炉体已经冷却到安全温度。
- 1、下载文档前请自行甄别文档内容的完整性,平台不提供额外的编辑、内容补充、找答案等附加服务。
- 2、"仅部分预览"的文档,不可在线预览部分如存在完整性等问题,可反馈申请退款(可完整预览的文档不适用该条件!)。
- 3、如文档侵犯您的权益,请联系客服反馈,我们会尽快为您处理(人工客服工作时间:9:00-18:30)。
冲天炉熔炼工艺规程
1、范围
本规程规定了冲天炉熔炼的炉料准备、装炉、炉前控制、质量控制、熔炼球铁、修炉和修包。
本规程适用于冲天炉熔炼灰铸铁和球墨铸铁。
2、炉料准备
2.1、焦碳
2.1.1焦碳块度:底焦100mm~150mm、层焦大于60mm。
焦碳应分类存放。
2.1.2焦碳的硫分含量小于或等于1.0%,灰分含量小于或等于1
3.5%,水分含量小于或等于5%。
2.1.3焦碳应存放于棚内,不应受风、雨、雪等侵蚀,不应混有其它物质。
2.2金属材料
2.2.1金属炉料的长度不大于熔炉加料口处最小直径的三分之一,重量在25公斤以下。
2.2.2废钢表面应干燥、清洁、无严重锈蚀、无泥砂杂物,不应有密闭容器。
重量在0.10公斤~5公斤、厚度小于1mm的应打包。
2.2.3生铁屑应压块使用,块度约φ155mm×60mm,重约7公斤。
2.2.4加入炉内的硅铁块度应小于70mm,最小不小于20mm,铁合金应避免潮湿。
2.2.5严禁危险物及其它有害物质混入炉料。
2.3孕育剂和球化剂
2.3.1硅铁含硅量及球化剂的硅、镁含量应符合标准。
2.3.2硅铁和球化剂应存放在干燥处,防止受潮。
2.3.3硅铁粒度为3mm~8mm,粉状硅铁和粉化球化剂不能使用。
2.4熔剂
2.4.1各种熔剂块度20mm~60mm,最大块度不大于80mm。
2.4.2石灰石中氧化钙不低于85%,不应混有泥土、砂石等有害杂质。
2.5耐火砖及点火木材应符合标准规定。
2.5.1耐火砖不应有疏松、裂纹、不合格的不能使用。
2.5.2耐火砖应放在棚内。
2.5.3潮湿木材和刨花不能使用,长度应小于500mm,高和宽应小于200mm。
3、装炉
3.1炉底、炉壁烘干后,铺上刨花,再装入木材,然后打开风口,点火。
加入底焦总量的40%~60%,,
等全部烧着后再加入余下底焦,随后短时鼓风,吹净灰分,趟透过桥,并从风口处观察和测量底焦高度、进行调整。
3.2装料时注意炉料均匀分布,在熔化过程中使炉料料柱与装料口平齐。
3.3严格按配料规定加料。
加料应过秤,称量允差为5%,并做好装料记录。
3.4装料顺序:焦碳、熔剂、回炉铁及铁屑、生铁、铁合金、废钢。
3.5焦碳加入量根据焦耗及铁水温度进行调整。
3.6严格遵守各种牌号铸铁的炉料配比,未经班组长、技术员同意,不能随意变更炉料。
3.7发生搭棚现象时,装炉工要立即报告班组长,不应无故停风。
3.8停止装料应经班组长许可。
3.9装料完毕,应加压铁,压铁层数不能超过两层。
3.10无论开始送风或停止送风都应先把风口盖打开,方能开动或停止风机。
4、炉前控制
4.1点火前应打开风口,开炉前应准备好炉前用的各种工具及各种炉前处理合金。
4.2应保持风量计的完好正常,开风后15分钟内应随时注意风量、风压及加氧量等数值与波动。
送氧应在开风5分钟以后,铁料开始熔化时进行,送氧后风量相应减少到规定值。
4.3风眼必须经常保持明亮,遇有严重结渣,应马上清除,清理风口时不能停风,不能同时捅两个风口,注意铁水熔化速度及温度,以便随时调整风量,加氧风口应随时注意氧枪喷嘴与焦碳距离变化,发现异常及时调节。
4.4出铁槽应经常保持清洁,不应有冷铁在内。
4.5风带内进风口附近的铁渣应在开风前清理干净。
4.6处理交界铁水时,前批料应在后批料下来前出清。
交界铁水降级使用,浇注不重要铸件。
4.7熔化后期应减小风量,未经班组长同意不能任意停风。
中途停氧之后应补足底焦并调整风量到正常值,同时将氧枪喷嘴与焦碳距离调到最大。
5、质量控制
5.1开炉点火前对各种使用的原材料按工艺规定进行检查。
5.2开炉后记录各项工艺控制参数,并及时通知炉前控制工。
5.3对铁水温度进行检查,前期出炉温度不低于1400℃,中期出炉温度不低于1440℃,后期不低于1420℃,铁水浇注温度为1300℃~1450℃,薄壁件小件取上限,厚大件取下限。
5.4浇注三角试片及机械性能试棒的砂型均应与铸型相类似,且应具有代表性。
5.5铁水浇入三角试块铸型后,待到暗红色时,取出侵入水中,然后击断,检验试块断口的白口深度
(或宽度),如不符合规定应马上采取处理措施。
5.6在熔化高牌号铸铁时,开风后第一批铁水作废或浇注要求不高的铸件。
铸铁的化学成分及机械性能应符合表1的规定。
表1 铸铁的化学成分及机械性能
6、碱性冲天熔炼球墨铸铁(以下简称球铁)
6.1熔化
6.1.1球铁用原材料应在第5~7批料开始加,石灰石加入量应不少于批焦量的二分之一.
6.1.2球铁配料用生铁含磷量≤0.06%,含硫量≤0.03%。
6.1.3球铁出铁温度应控制在1400℃~1460℃。
当低于此范围时,不能浇注小件和薄壁件;当高于1460℃时应注意合金的覆盖与捣实。
6.2球化处理
6.2.1球化处理采用包内冲入法。
6.2.2用稀土镁硅铁合金作球化剂时,使用前应将碎块、粉末筛除,球花剂加入量为该包铁水的1.6~2.2%。
6.2.3球化反应时间:从第一次堵出铁口开始计,应控制在1~2分钟,严防球化不良。
待反应基本停止,立即补满铁水,吊出进行扒渣;当浇包高度超过1.6m时,也可一次将铁水装满浇包进行处理。
6.3扒渣
6.3.1用专用扒渣工具将铁水表面渣子扒净,立即覆盖草灰1~2锹。
稍加搅拌后进行二次扒渣,应将渣扒净以防止“回硫”。
6.3.2扒渣时应使包向后倾斜,从包后面扒出渣子,不能从包嘴处扒渣,以免损坏包嘴。
6.4孕育处理
6.4.1一次孕育:使用75#硅铁,粒度5mm~20mm。
加入量为铁水重量的0.6%~0.8%。
使用时覆盖在球化剂上面。
6.4.2二次孕育;使用75#硅铁,每块重约0.5Kg~3.5Kg,厚度≤70mm。
加入量为铁水总重的0.4%~0.6%。
加入时轻放在铁水表面,并用铁棍轻点助熔,不应搅拌铁水面,待其开始发红熔化即覆盖草灰或珍珠岩准备浇注。
6.5炉前球化检验
采用火苗法、三角试块法和快速金相法进行检验。
6.6浇注
6.6.1浇注前撇渣时,不应将浮硅块或浮硅层破坏。
6.6.2接到炉前检验合格通知后应在15分钟内(以出铁口开始计)应全部浇完,超过15分钟浇不完的铁水报废。
6.6.3浇注中应注意观察铁流火苗情况和流淌出的铁片、铁豆是否有缩陷,发现异常应立即停止浇注、并迅速报告技术员或班组长,采取处理措施。
6.6.4每炉次用中期铁水浇注三根试块,试块冷却至700℃以下才能开箱。
7、修炉及修包
7.1清理
7.1.1清理时先从加料口把大块挂渣打落,并在加料口处放好安全罩,修炉人员戴好安全帽后再进行炉内清理和修炉。
7.1.2清理炉壁时,不能用锤子垂直敲打炉壁。
砖面不应残留炉渣、铁片等。
7.2修补炉壁
7.2.1砌砖时,耐火粘土等材料应布满全部接触面,砖与砖之间缝隙不应超过3mm、上下层砖缝应错开。
7.2.2炉壁的耐火砖有侵蚀及松动裂纹现象时,应用耐火材料补平,保证质量及原有尺寸。
7.2.3修炉时按规定尺寸修理,修完后检查并记录各主要部位尺寸。
主要部位尺寸应符合以下规定:熔化带为Φ1050mm~Φ1140mm,风口区为Φ900mm~950mm,炉缸去为Φ780mm~820mm。
7.3修风口
7.3.1修风口时应保证工艺规定的风口大小及位置、形状不应任意改变。
其中1排风口为Φ20mm×8mm×5°,2排风口为Φ30mm×8mm×10°。
7.3.2在炉内风口上都应凸起20mm~30mm。
7.4修出铁口和出渣口。
7.4.1出铁口处炉壁为70mm,直径为30mm,出渣口处厚度为60mm,直径为50mm,内外做成喇叭状。
7.4.2前炉和大炉之间过桥尺寸为45mm×150mm。
7.5修出铁槽及前炉。
7.5.1前炉的修理与风口以下的炉壁相同。
7.5.2出铁槽的修理与修炉壁相同,其斜度与炉底一样。
表面应刷一层涂料,保证其光洁平直。
7.5.3焦碳粉应过60号筛才能使用。
7.6修理炉底
7.6.1修炉底首先用修炉材料将炉底空隙覆好,避免炉底材料漏掉。
7.6.2修炉底前应先将炉底门气眼清理干净。
7.6.3将炉底门关好后,铺上炉底材料,并使其有合适的强度与水分。
7.6.4炉底以出铁口为准,厚度为200mm~250mm,斜度为1:12(即5°~6°)。
7.6.5炉底与炉壁连接处要有圆角,半径为50~80mm。
7.7烘炉
7.7.1点火前首先把风口打开,点火应在开风前2小时~3小时,点火时间不能过短或过长。
装木柴应先从工作门装入部分木柴,并用较小的木柴铺满炉底,以免将炉底砸坏,最后从加料口将木柴加足。
7.7.2大炉、前炉的炉底及出铁槽修好后填入木柴用慢火烘干。
7.7.3开始装料前应先装入部分焦碳,鼓风烘燃必须超过20分钟。