压铸模具基础知识
压铸基础知识

压铸基础知识我们的锌铝合金属于其中的哪一种?2压力铸造简称压铸,是一种将熔融合金液倒入压室内,以高速充填钢制模具的型腔,并使合金液在压力下凝固而形成铸件的铸造方法。
压铸区别于其它铸造方法的主要特点是高压和高速。
压铸机、压铸合金与压铸模具是压铸生产的三大要素,缺一不可。
办公用品| 卫浴五金| 电子/| 机械| 五金|31.由于压入铸模内的合金液一般是在非真空的条件下急速冷却凝固的,如2.普通方法生产的压铸件不能进行高温热处理和焊接。
3.目前压铸某些内凹件、高熔点合金铸件还比较困难。
4.压铸设备价格高,模具制造需要一定周期,所以不宜单件或小批量生4的问题来源于模具,所以模具是我们生产最重要的工具。
5固定在壓鑄機定模安裝板上,有直澆道與固定在壓鑄機動模安裝板上,並隨動模安液體金屬在高壓下充滿型腔;借助於設在動模上的推出機構將鑄件推6使料液平稳且有序地填充到开腔中并在填充过程和凝固过程中把压力传迅到各个部位,以获得所需的组织紧密,外观清晰的产品母模仁公模仁7使料液平稳且有序地填充到开腔中并在填充过程和凝固过程中把压力传迅到各个部位,以获得所需的组织紧密,外观清晰的产品冷却料浇口主浇道8导套导柱9实现零件的正常脱模10实现与开模方向不一致的侧孔,11为满足成型工艺对模具温度要求,以保证各种零件的冷却定型循环水路循环水路12保证零件熔体在充填过程中模腔中的气体完全排出,以让零件熔体顺利充满型腔排气槽13模座垫块144 曲面分型1516指生產過程中因模具設計產生排气及生產過程中殘留於機台及地面指生產過程中從機台溶爐表面經過打渣劑而產生的浮渣料;指生產過程中出現的排渣及浮渣料經熔解產生的物料。
水口料17新格18康帅192021喷离型剂注汤中子退压进压退取件开模冷却成型射出合模中子进222324挥发;)性能稳定在空气中稀释剂不应挥发过决而变稠;2526时针月份标27台阶成型标准成型28高出293031磨砂机平面磨砂机32砂带按型号分有:60#、80#、120#、180#、240#、400#、1200#等;型号越大,表示表面砂粒越细,打磨的表面越光滑;通常在砂带内表面标示有砂带型号及砂带转动方向。
压铸知识培训资料
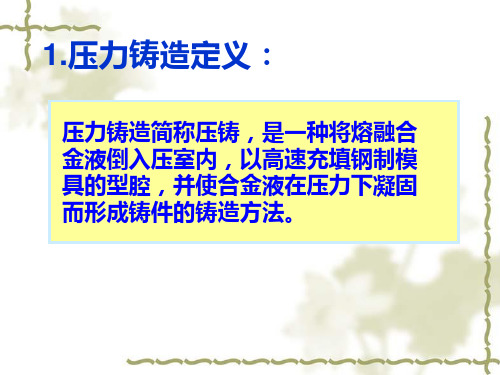
5.压铸机、压铸金属及压铸模具是组成压 铸工艺的3个要素。
卧式压铸机
立式压铸机
6.压铸机分类:
压铸机一般分为热压室压铸机和冷压室压铸机两大类。 冷压室压铸机按其压室结构和布置方式分为卧式压铸机 和立式压铸机(包括全立式压铸机)两种。 热压室压铸机(简称热空压铸机)压室浸在保温溶化坩 埚的液态金属中,压射部件不直接与机座连接,而是装 在坩埚上面。这种压铸机的优点是生产工序简单,效率 高;金属消耗少,工艺稳定。但压室,压射冲头长期浸 在液体金属中,影响使用寿命。并易增加合金的含铁量。 热压室压铸机目前大多用于压铸锌合金等低熔点合金铸 件,但也有用于压铸小型铝、镁合金压铸件。 冷室压铸机的压室与保温炉是分开的。压铸时,从保温 炉中取出液体金属浇入压室后进行压铸。
4.压力铸造适用材料及浇铸温度:
铝合金 铝硅系 610-650℃ 640-680℃ 600-620℃ 610650℃ 铝铜系 630-660℃ 660-700℃ 600-640℃ 630-660℃ 铝镁系 640-680℃ 660-700℃ 640-670℃ 650-690℃ 铝锌系 590-620℃ 620-660℃ 580-620℃ 600-650℃ 锌合金 420-440℃ 430-450℃ 400-420℃ 420-440℃ 镁合金 640-680℃ 660-700℃ 640-670℃ 650-690℃ 铜合金 普通黄铜 910-930℃ 940-980℃ 900-930℃ 900950℃ 硅黄铜 900-920℃ 930-970℃ 910-940℃ 910-940℃
7.压铸模具:
8.压铸工艺知识:
8-1、压力和速度的选择:按铸件结构确定。
8-2、浇注温度:从压定进入型腔时液态金属的平均温度。 8-3、压铸型的温度:在压铸前应进行预热。
压铸模知识点

铝合金压铸件的结构设计经验1。
考虑壁厚的问题,厚度的差距过大会对填充带来影响2。
考虑脱模问题,这点在压铸实际中非常重要,现实中往往回出现这样的问题,这比注塑脱模讨厌多了,所以拔模斜度的设置和动定模脱模力的计算要注意些,一般拔模斜度为1到3度,通常考虑到脱模的顺利性,外拔模要比内拔模的斜度要小些,外拔模也就1度,而内拔模要2~3度左右3。
设计时考虑到模具设计的问题,如果有多个位置的抽心位,尽量的放两边,最好不要放在下位抽心,这样时间长了下抽心会容易出问题4。
有些压铸件外观可能会有特殊的要求,如喷油、喷粉等,这时就要时结构避开重要外观位置便于设置浇口溢流槽5。
在结构上尽量的避免出现导致模具结构复杂的结构出现,如,不得不使用多个抽心或螺旋抽心等6。
对于需进行表面加工的零件,注意,需要在零件设计时给适合的加工留量,不能太多,否则加工人员会骂你的,而且会把里面的气孔都暴露出来的,不能太少,否则粗精定位一加工,得,黑皮还没干掉,你就等再在模具上打火花了,那给多少呢,留量最好不要大于0。
8mm,这样加工出来的面基本看不到气孔的,因为有硬质层的保护。
7。
再有就是注意选料了,是用ADC12还是A380等,要看具体的要求了8。
铝合金没有弹性,要做扣位只有和塑料配合。
9。
一般不能做深孔!在开模具时只做点孔,然后在后加工!10。
如果是薄壁零件与不能太薄,而且一定要用加强肋,增加抗弯能力!由于铝铸件的温度要在800摄氏度左右!模具寿命一般比较短一般做如电机外壳的话只有80K左右就再见了!1.压铸件的设计与塑胶件的设计比较相似,塑胶件的一些设计常规也适用于压铸件。
2.对于铝合金,模具所受温度和压力比塑胶的大很多,对设计的正确性要求特严。
即使很好的模具材料,一旦有焊接,模具就几乎无寿命可言。
锌合金跟塑胶差不多,模具寿命较好。
3.不能有凹的尖角,避免模具崩角。
4.压铸件的精度虽然比较高,但比塑胶差,而且拔模力比塑胶大,通常结构不能太复杂,必要时应将复杂的零件分解成两件或多件。
压铸模具设计基础知识

熱室壓鑄鋅合金中的合金元素
---雜質元素-鐵
鋅合金中鐵元素含不能>0.02%,鐵 元素可:
☺ 增加合金的硬度
但同時
增加合金的脆性
和合金中的鋁發生反應形成Al5Fe2金屬間化合物, 造成鋁元素的損耗並形成浮渣
在壓鑄件中出現硬點
2024/2/1
压铸模具设计基础知识
五.壓鑄合金及其性能
熱室壓鑄鋅合金中的合金元素 ---雜質元素-硅
t1:F1為克服磨擦力(壓室中)
壓
t2:開始進入型腔﹐因澆口急減﹐阻力 力
F
增大﹐F2>F1,達到高速充填
t3:(快速增壓階段)快速充填直止充滿
型腔最大值F3為壓射壓力
t4:F4靜壓力﹐對鑄件壓實
時間t
(壓射力與時間關係曲線見右圖)
2024/2/1
压铸模具设计基础知识
六.壓鑄工藝
定義2﹕壓射壓力就是在充模剛結束時壓射沖頭作用在金屬液面上的力。 定義3﹕壓射壓力是以壓射比壓來表示﹐壓射比壓就是充模結束時﹐壓射
沖頭作用于單位面積金屬液面上的壓力。
P ﹕壓射比壓( Pa ) P= F 4F F: 壓射壓力(N)
A πd 2 d ﹕壓室直徑 (m) A﹕沖頭截面積( m 2 )
壓射比壓與壓射壓力成正比﹐與壓射沖頭的截面積成反比。
鋅合金的 壓射比壓
壁厚 =<3mm 30MPa 簡單 40MPa 復雜
壁厚 >3mm 50MPa 簡單 60MPa 復雜
有害雜質元素:鐵(Fe),硅(Si),鉛(Pb),鎘(Gd),錫(Sn)
來源於鋁
來源於鋅
2024/2/1
压铸模具设计基础知识
五.壓鑄合金及其性能
2024/2/1
压铸模具设计基础知识

压铸模具设计基础知识一、概述压铸模具是用于压铸工艺的模具,在金属、塑料等材料的制品生产过程中起到关键作用。
压铸模具的设计质量直接影响产品的质量和生产效率。
本文将介绍压铸模具设计的基础知识,包括设计原则、材料选择、结构设计等内容。
二、设计原则1.功能性原则压铸模具应该符合产品的设计要求,能够满足产品的结构、尺寸、表面质量等要求。
设计过程中需要充分考虑产品的功能性需求,确保模具能够满足生产要求。
2.可制造性原则在设计压铸模具时,需要考虑到模具的加工工艺和生产成本。
设计应尽量简化,避免复杂的结构和加工工艺,以降低生产成本。
3.可靠性原则压铸模具在长期使用中需要具有稳定可靠的性能。
设计中需要考虑模具的寿命、耐磨性等因素,确保模具能够长时间稳定运行。
4.易维护性原则模具在使用过程中可能会有损坏或磨损,设计时需要考虑模具的易维护性,便于维修和更换受损部件。
三、材料选择压铸模具的材料选择直接影响模具的寿命和性能。
常用的模具材料包括工具钢、合金钢、硬质合金等。
在选择材料时需要考虑以下因素:1.硬度模具材料应具有足够的硬度和强度,能够抵抗压力和磨损,确保模具的稳定性和寿命。
2.热稳定性压铸过程中温度较高,模具材料需要具有良好的热稳定性,不易变形或烧损。
3.耐磨性压铸模具在长期使用中会有磨损,需要选择耐磨性好的材料,延长模具的使用寿命。
4.耐蚀性部分压铸过程中会有化学物质接触,模具材料需要具有良好的耐腐蚀性,避免腐蚀损坏。
四、结构设计压铸模具的结构设计直接影响产品质量和生产效率。
在设计时需要考虑以下因素:1.分型设计合理的分型设计能够提高产品的成型效率和质量,减少缺陷产生。
分型设计应考虑产品的结构特点和成型过程中的收缩变形。
2.冷却系统设计冷却系统设计影响压铸过程中的温度控制和冷却速度,直接影响产品的组织和性能。
设计时应考虑冷却系统的布局和冷却介质的选择。
3.排气系统设计在压铸过程中需要排除模具内的气体,避免气泡和气孔产生。
压铸模具设计基础知识
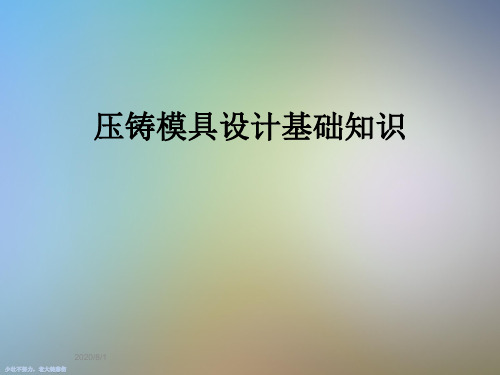
實際比壓應等于計算比壓乘以壓力損減系數K(約0.88). 比壓大小可通過調節壓鑄機的壓射力和更換不同直徑的 壓室來實現。
2020/8/1
六.壓鑄工藝
(二)充填速度及其選擇
充填速度是指熔融金屬地壓射沖頭壓力的作用下﹐通過內澆口時的線速度。
影響充填速度的因素有壓射速度﹐壓射比壓和內澆口截面積等。
根據等流量連續方程
鎂的加入可 ☺ 細化合金組織,從而增加壓鑄件的強度 ☺ 改善合金抗晶間腐蝕的能力 ☺ 改善合金的抗磨損性能 降低合金的流動性 易在合金熔融狀態下氧化損耗
2020/8/1
五.壓鑄合金及其性能
熱室壓鑄鋅合金中的合金元素
---雜質元素-鎘,鉛
鎘在合金中的含量絕對不能>0.003% 降低合金的機械性能 造成合金晶間腐蝕 鉛在合金中的翎量絕對不能>0.003% 降低合金的時效機械性能 當含量超過0.005%時,造成合金晶間腐蝕
2020/8/1
五.壓鑄合金及其性能
2020/8/1
五.壓鑄合金及其性能
熱室壓鑄鋅合金中的合金元素 ---合金元素-鋁
鋁的加入可`
☺ 降低合金對鐵的反應能力,因此降低了合金對鋅鍋,鵝 頸及模具的侵蝕 ☺ 降低合金的熔點 ☺ 增加合金的流動性能 ☺ 改善合金的機械性能 產生Fe2 Al5浮渣,造成其含量的下降
压铸模具设计基础知识
2020/8/1
一. 鑄造工藝
砂型鑄造 金屬型鑄造
特種鑄造
壓力鑄造 重力鑄造 低壓鑄造 熔模鑄造 陶瓷型鑄造 連續鑄造 離心鑄造 真空吸鑄
永久型鑄造
2020/8/1
二. 壓鑄概論
❖ 壓力鑄造概念: (鋁,錫,鋅,镁,鉛,銅,合金) 即將溶融合金在高壓,高速條件下充型並在高壓下冷卻凝固成型的一 種精密鑄造方法, 簡稱壓鑄,其最終產品是壓鑄件.
压铸模具基础知识介绍ppt

对采购的材料进行质量检验,确保材料符合设计 要求。
材料储存与保管
对检验合格的原材料进行储存和保管,确保材料 在制造过程中不受损坏或变质。
模具加工阶段
粗加工
对模具毛坯进行粗加工,去除多余 的材料,初步形成模具的形状和结 构。
中间检查
对粗加工完成的模具进行中间检查 ,确保模具的形状和结构符合设计 要求。
02
压铸模具制造过程
设计阶段
1 2
模具设计
根据产品需求,进行模具的结构设计,确定模 具的形状、结构、尺寸等参数。
模具材料选择
根据模具的使用条件和寿命要求,选择合适的 材料,如铸铁、铸钢、铝合金等。
3
模具零件的标准化
对模具的零件进行标准化设计,以提高制造效 率和降低成本。
备料阶段
材料采购
根据模具设计要求,采购合适的材料,如钢材、 铝合金等。
04
压铸模具的使用与维护
压铸模具的使用方法
模具安装
根据模具尺寸、形状和压铸机型 号,正确安装模具,确保定位准 确、紧固可靠。
模具预热
使用前对模具进行预热,提高模 具温度,降低成型难度,提高产 品质量。
模具调试
根据产品要求和工艺参数,调试 模具压力、温度、时间等参数, 确保压铸件质量符合要求。
压铸模具的维护保养
压铸模具基础知识介绍ppt
xx年xx月xx日
contents
目录
• 压铸模具概述 • 压铸模具制造过程 • 压铸模具材料选择与处理 • 压铸模具的使用与维护 • 压铸模具的设计案例分析 • 总结与展望
01
压铸模具概述
定义与特点
定义
压铸模具是一种金属铸造工艺中使用的模具,通过将熔融的 金属注入到模具型腔中,冷却凝固后得到所需形状的零件。
压铸模具结构基础知识

压铸模具结构基础知识压铸模具,听起来是不是很高大上?别担心,今天我们就来聊聊这个看似复杂其实很有趣的话题。
压铸模具其实就是用来生产金属零件的一种工具,它们的结构就像是机械界的“画板”,把金属液体像画颜料一样,一股脑儿地倒进去,等它冷却下来,就变成了我们需要的零件。
听起来简单吧?但背后的门道可多了。
1. 压铸模具的基本构造1.1 模具的主要部件首先,压铸模具的结构可以说是五花八门,但基本上离不开几个主要部件。
你想啊,模具里有一个“型腔”,就是我们说的零件的模样。
这一部分就像是你做蛋糕的模具,倒进去液体金属后,等它冷却下来,就能拿到你想要的形状。
除此之外,还有“型芯”,这东西可不是开玩笑的,它负责在模具中创造出复杂的内部形状,想想看,蛋糕里如果你想要个洞,必须得有个“芯”才能做出来。
接着,我们还得提到“合模系统”。
这个系统就像模具的心脏,负责把模具的两部分紧紧合在一起,防止金属液体从缝隙里漏出去。
不然一不小心,整个车间都成了“金属河”,那可就麻烦了!另外还有“冷却系统”,想象一下,金属液体在模具里翻滚得热火朝天,这时候得有冷却水道来帮忙降温,不然模具可是会变得“热火朝天”的哦。
1.2 模具的工作原理说到这里,可能有小伙伴会问,压铸模具到底是怎么工作的呢?简单来说,就是把金属加热到液态,然后用高压把它们注入模具型腔里。
听起来是不是有点像“万里长征走一回”?没错,压铸的过程就像是一场冒险,液体金属要穿越各种管道,最终落到“家”里——型腔中。
一旦金属注入,冷却系统就开始发挥作用,帮忙把这股热量赶走。
冷却完成后,模具打开,零件就“呼之欲出”了!这时,像是经历了一场“历险”的金属,终于变成了我们所需的产品,真是个让人兴奋的时刻。
2. 压铸模具的应用领域2.1 日常生活中的应用压铸模具的应用可谓是无处不在。
想想你的手机、汽车,甚至是厨房里的炊具,很多零件都是通过压铸模具制作出来的。
你见过那些闪亮亮的铝合金轮毂吗?没错,它们也是压铸的结果!生活中很多看似不起眼的小物件,背后其实都藏着压铸模具的智慧。
压铸模具基础知识1

2020/11/14
压铸模具基础知识1
压铸模具基础知识1
压铸模具基础知识1
压铸模具基础知识1
压铸模具基础知识1
ห้องสมุดไป่ตู้
压铸模具基础知识1
压铸模具基础知识1
压铸模具基础知识1
压铸模具基础知识1
压铸模具基础知识1
压铸模具基础知识1
压铸模具基础知识1
压铸模具基础知识1
压铸模具基础知识1
压铸模具基础知识1
压铸模具基础知识1
压铸模具基础知识1
压铸模具基础知识1
压铸模具基础知识1
压铸模具基础知识1
压铸模具基础知识1
压铸模具基础知识1
压铸模具基础知识1
压铸模具基础知识1
压铸模具基础知识1
压铸模具基础知识1
压铸模具基础知识1
压铸模具基础知识1
压铸模具基础知识1
压铸模具基础知识1
压铸模具基础知识1
压铸模具基础知识1
压铸模具基础知识1
压铸模具基础知识1
压铸模具基础知识1
压铸模具基础知识1
压铸模具基础知识1
压铸模具基础知识1
压铸模具基础知识1
压铸模具基础知识1
压铸模具基础知识1
压铸模具基础知识1
压铸模具基础知识1
压铸模具基础知识1
压铸模具基础知识1
压铸模具基础知识1
压铸模具基础知识1
压铸模具基础知识1
压铸模具基础知识1
压铸模具基础知识1
压铸模具基础知识1
压铸模具基础知识1
压铸模具基础知识1
压铸模具基础知识1
压铸模具基础知识1
压铸模具基础知识1
压铸模具基础知识1
压铸模知识
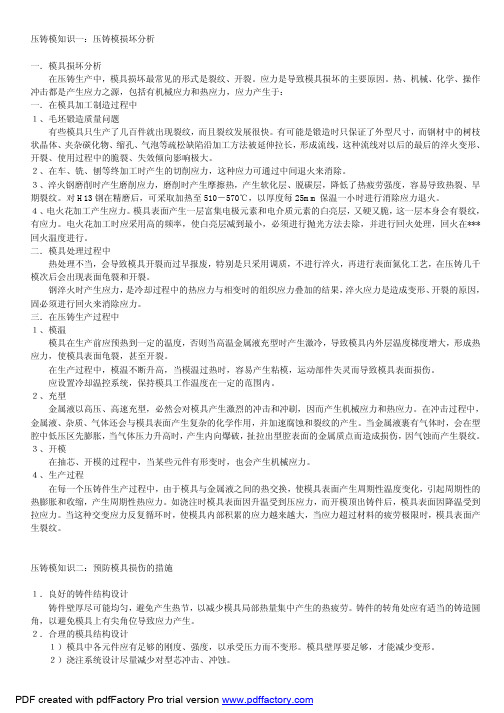
压铸模知识一:压铸模损坏分析一.模具损坏分析在压铸生产中,模具损坏最常见的形式是裂纹、开裂。
应力是导致模具损坏的主要原因。
热、机械、化学、操作冲击都是产生应力之源,包括有机械应力和热应力,应力产生于:一.在模具加工制造过程中1、毛坯锻造质量问题有些模具只生产了几百件就出现裂纹,而且裂纹发展很快。
有可能是锻造时只保证了外型尺寸,而钢材中的树枝状晶体、夹杂碳化物、缩孔、气泡等疏松缺陷沿加工方法被延伸拉长,形成流线,这种流线对以后的最后的淬火变形、开裂、使用过程中的脆裂、失效倾向影响极大。
2、在车、铣、刨等终加工时产生的切削应力,这种应力可通过中间退火来消除。
3、淬火钢磨削时产生磨削应力,磨削时产生摩擦热,产生软化层、脱碳层,降低了热疲劳强度,容易导致热裂、早期裂纹。
对H13钢在精磨后,可采取加热至510-570℃,以厚度每25mm保温一小时进行消除应力退火。
4、电火花加工产生应力。
模具表面产生一层富集电极元素和电介质元素的白亮层,又硬又脆,这一层本身会有裂纹,有应力。
电火花加工时应采用高的频率,使白亮层减到最小,必须进行抛光方法去除,并进行回火处理,回火在***回火温度进行。
二.模具处理过程中热处理不当,会导致模具开裂而过早报废,特别是只采用调质,不进行淬火,再进行表面氮化工艺,在压铸几千模次后会出现表面龟裂和开裂。
钢淬火时产生应力,是冷却过程中的热应力与相变时的组织应力叠加的结果,淬火应力是造成变形、开裂的原因,固必须进行回火来消除应力。
三.在压铸生产过程中1、模温模具在生产前应预热到一定的温度,否则当高温金属液充型时产生激冷,导致模具内外层温度梯度增大,形成热应力,使模具表面龟裂,甚至开裂。
在生产过程中,模温不断升高,当模温过热时,容易产生粘模,运动部件失灵而导致模具表面损伤。
应设置冷却温控系统,保持模具工作温度在一定的范围内。
2、充型金属液以高压、高速充型,必然会对模具产生激烈的冲击和冲刷,因而产生机械应力和热应力。
压铸模具设计基础知识

压铸模具设计基础知识压铸模具是制造压铸件的关键设备,它直接影响着压铸产品的质量和生产效率。
下面将详细介绍压铸模具设计的基础知识。
一、压铸模具的分类压铸模具一般可分为冷室压铸模具和热室压铸模具两大类。
冷室压铸模具适用于铝合金和铜合金的压铸生产,相对简单,但适用于高温熔融的压铸合金。
热室压铸模具适用高熔点压铸合金,具有较高的耐热性和抗高温挤压性能。
二、压铸模具的结构1.压铸模具主要由模架、模座、模芯、出料系统和冷却系统等组成。
2.模架是模具的主架构,起着支撑模具部件和固定模具部件的作用。
3.模座是连接模具与注射机的部件,将模具安装在注射机上,保证注射过程的稳定性。
4.模芯是模具中用来形成产品内部空洞的零件,它通常由多段组成,可以根据产品的形状进行组装。
5.出料系统是将熔融的金属注入模腔的路径,通常由进料口、浇口和溢流槽等组成。
6.冷却系统是保证模具持续工作的关键部分,它能够快速降温和加热模具,确保产品冷却时间的缩短和生产效率的提高。
三、压铸模具设计的基本原则1.单向释放原则:保证产品易于从模具中脱模,避免产品损坏。
2.对称设计原则:尽量保证模具零件左右对称,以降低模具零部件制造和装配的难度。
3.预防变形原则:通过模具结构设计和冷却系统的合理布局来降低模具零件的变形,确保产品的尺寸精度。
4.合理浇注和冷却系统原则:通过优化浇注系统设计和加强冷却系统的作用,提高压铸产品表面质量,并缩短冷却时间。
5.合理安装和调整原则:确保模具零件的安装和调整精度,提高模具的使用寿命和产品的质量。
四、压铸模具设计的步骤1.确定产品的设计要求和材料性能,进行产品分析和模具选型。
2.进行模具结构设计,包括模腔结构、模芯结构、冷却系统和出料系统等设计。
3.进行模具零部件设计,包括模板、模座、模芯、冷却水口等零部件的形状和尺寸设计。
4.进行模具零部件的制造和装配,进行试模和测试,及时修复和调整模具零部件。
5.进行模具的调试和优化,包括调整出料系统、冷却系统等,确保模具的正常工作。
压铸模具有哪些结构-压铸模具知识

压铸模具有哪些结构-压铸模具知识压铸模具是由定模和动模两个主要部分组成的。
下面,店铺为大家分享压铸模具的结构,希望对大家有所帮助!成型部分在定模与动模合拢后,成形一个构成铸件形状的空腔,称为型腔。
按压铸件结构不同,型腔可以全部设在定模或动模内,或定、动模内各占一部分,构成型腔的零件即为成型零件。
成型零件包括固定和活动的镶块与型芯,如图中的11、12、20所示。
此外,浇注系统和排溢系统也是型腔的一部分。
模架包括各种模板、座、架等构架零件。
作用是将模具各部分按要求的相互位置装配和固定,并能使模具安装到压铸机上,图的1、2、3、4、9、10、18、19就属于这类零件。
导向零件图中的18、19为导向零件,其作用是引导动模和定模合拢或分离,并保证分合模的精度要求。
推出机构这是将铸件从模具中推出的机构,包括顶出和复位零件,还包括机构自身的导向和定位零件。
如图中的21、22、23、24、25、26、27,对于重要和易损处(如浇道、浇口)的推杆,应采取与成型零件相同的材料来制造。
浇注系统它是型腔与压室或喷嘴相连的通道,引导金属液按规定的方向进入模具的型腔,且直接影响金属液进入成型部分的速度和压力,由直浇道,横浇道和内浇道组成,如图中14、15、16、17所示。
排溢系统是指排气槽和溢流槽系统。
排气槽是排除压室、浇道和型腔中气体的通道;而溢流槽是储存冷金属盒涂料余烬的小空腔,溢流槽还具有调节模具温度的.作用,有时在难以排气的深腔部位设置通气塞,借以改善该处的排气条件。
抽芯机构对某些铸件,当型芯抽出方向与开合模方向不一致时,还需要在模具上设抽芯机构,以便将铸件从模具中取出,如图中的5、6、7、8、11所示。
抽芯机构也是压铸模具中十分重要的结构单元,其形式是多种多样的。
冷却—加热装置为了保持模具温度场的分布符合工艺的需要,有时模具内要设置冷却装置或冷却—加热装置,这对实现科学的控制工艺参数和确保铸件质量尤其重要。
具有良好的冷却(或冷却—加热)系统的模具,其寿命可以大大延长。
压铸模知识点

铝合金压铸件的结构设计经验1。
考虑壁厚的问题,厚度的差距过大会对填充带来影响2。
考虑脱模问题,这点在压铸实际中非常重要,现实中往往回出现这样的问题,这比注塑脱模讨厌多了,所以拔模斜度的设置和动定模脱模力的计算要注意些,一般拔模斜度为1到3度,通常考虑到脱模的顺利性,外拔模要比内拔模的斜度要小些,外拔模也就1度,而内拔模要2~3度左右3。
设计时考虑到模具设计的问题,如果有多个位置的抽心位,尽量的放两边,最好不要放在下位抽心,这样时间长了下抽心会容易出问题4。
有些压铸件外观可能会有特殊的要求,如喷油、喷粉等,这时就要时结构避开重要外观位置便于设置浇口溢流槽5。
在结构上尽量的避免出现导致模具结构复杂的结构出现,如,不得不使用多个抽心或螺旋抽心等6。
对于需进行表面加工的零件,注意,需要在零件设计时给适合的加工留量,不能太多,否则加工人员会骂你的,而且会把里面的气孔都暴露出来的,不能太少,否则粗精定位一加工,得,黑皮还没干掉,你就等再在模具上打火花了,那给多少呢,留量最好不要大于0。
8mm,这样加工出来的面基本看不到气孔的,因为有硬质层的保护。
7。
再有就是注意选料了,是用ADC12还是A380等,要看具体的要求了8。
铝合金没有弹性,要做扣位只有和塑料配合。
9。
一般不能做深孔!在开模具时只做点孔,然后在后加工!10。
如果是薄壁零件与不能太薄,而且一定要用加强肋,增加抗弯能力!由于铝铸件的温度要在800摄氏度左右!模具寿命一般比较短一般做如电机外壳的话只有80K左右就再见了!1.压铸件的设计与塑胶件的设计比较相似,塑胶件的一些设计常规也适用于压铸件。
2.对于铝合金,模具所受温度和压力比塑胶的大很多,对设计的正确性要求特严。
即使很好的模具材料,一旦有焊接,模具就几乎无寿命可言。
锌合金跟塑胶差不多,模具寿命较好。
3.不能有凹的尖角,避免模具崩角。
4.压铸件的精度虽然比较高,但比塑胶差,而且拔模力比塑胶大,通常结构不能太复杂,必要时应将复杂的零件分解成两件或多件。
压铸模具基础知识

(19) 分流锥:
调整直浇道的截面积,改变金属液流向,减少金属液消 耗量。内部设有冷却系统。
材料:H13、SKD61 热处理: HRC43~47
(20) 垫块: 对模具起支承作用,提高后模刚性,减
少生产时由机器冲击波而引的模具瞬间变形制作材料为普 通铸铁或45#钢。位置和尺寸的控制是关键
材料: T8A、T10A、40cr 热处理: HRC 42~47
(5).滑块
作用: 连结型芯和斜销配合作抽芯运动的组件,和斜销配 合 共同完 成抽芯动作。
参数: 滑块的高度B ,宽度C按型芯尺寸决定,.滑块的长 度A与B, C有关,为使滑块工作时稳定要求 A≥0.7C A≥B
材料: T8A、T10A、H13 热处理: HRC 42~47
合金压铸模
压铸模具基础知识
前言
压铸:高温融熔金属液,在高速 高压状态下以一 定的条件快速充填型腔,并在一定压力作 用下快速冷却过程。
压铸模是压铸生产中重要的工艺装备,它对生产能否 顺利进行,铸件质量的优劣起着极为重要作用,它与 压铸生产工艺、生产操作存在着又互相影响互为制约, 关系极密切系。
在压铸机中板上,随中板作并合运动,与定模部分
分开合拢。一般抽芯机构和顶出机构大多在这个部
分。
抽芯机构:
作用: 抽动与开模方向运动不一致成型零件的 活动型芯机构。
抽芯机构主要包括:斜导柱、侧面型芯、滑块、 导 滑槽、限位块、螺杆、弹簧、螺母、螺 钉等部分组成。如下图所示。
(3).斜销
溢流槽
溢流槽的结构形式: (1)布置在模具分型面上的溢流槽 (2)布置在模具型腔内部的溢流槽。 其形式有: 杆形溢流槽 管形溢流槽 环形溢流槽 双级溢流槽 波纹状溢流槽
压铸应知应会

一、基本知识1、压铸的定义:压力铸造简称压铸,是在高压作用下,将液态或半液态金属以及高的速度充填入金属铸型(模具)型腔,并在压力作用下凝固而获得铸件的方法。
1、可用于压铸的合金:铝合金、锌合金、铜合金、镁合金等。
2、压铸的特点:高速、高压、高效率、铸件复杂、轮廓清晰、铸件表层组织致密、铸件具有较高的硬度和强度。
3、压铸循环过程:(1)合模(2)缩紧模具(3) 浇铸熔化的合金液(4)把熔化金属射入模中(压射)(5)凝固、冷却(6)开模(7)取件(8)清理、冷却模具并喷涂脱模剂。
4、公司所采用的压铸机名称及型号:280吨卧式冷室压铸机、400吨卧式冷室压铸机、550吨卧式冷室压铸机、630吨卧式冷室压铸机、700吨卧式冷室压铸机、800吨卧式冷室压铸机、1250吨卧式冷室压铸机、1600吨卧式冷室压铸机。
5、压铸机型号中所指的280吨或1600吨是指其锁模力。
6、压铸生产工艺的三大要素:合金材料、压铸机、压铸模具。
7、压铸的工艺过程:压铸工艺过程二、压铸工艺1、压铸工艺的定义:压铸工艺是将压铸机、压铸模和合金三大要素有机地组合而加以综合运用的过程。
2、压铸参数:影响压铸生产的主要压铸(工艺)参数有压射力、铸造压力、合(锁)模力、压射速度、压射行程、浇铸温度、模具温度、填充时间、增压建压时间、保压时间、留模时间、压室充满度、脱模剂配比、脱模剂喷涂时间等。
3、压射力:压射力是压铸机压射机构中推动压射活塞运动的力。
它是反映压铸机功能的一个主要参数。
压射力的大小,由压射缸的截面积和系统液压油的压力所决定。
压室内熔融金属在单位面积上所受的压力称为比压。
比压也是压射力与压室截面积的比值。
合金熔液在大压射力(比压)作用下填充型腔,合金温度升高,流动性改善,晶粒细化有利于铸件成型质量的提高。
保证质量的前提下选择尽可能低的压射力。
复杂铸件、薄壁件选择大的压射力(压射比压),反之选择小的压射力(压射比压)4、铸造压力:增压时熔融金属在单位面积上所受的压力称为铸造压力。
压铸模具资料

一、专业术语解释:1.全壁厚充填——液态金属压入型腔后即扩展至型腔壁,然后沿着整个型腔截面向前流动,直至全部充满型腔。
2.压铸合金——用于压铸生产的合金,主要有铝合金、锌合金、镁合金、铜合金。
3.充填速度——液态金属在压力作用下通过内浇道进入型腔时的线速度。
4.胀型力——压铸时液态金属充满型腔后对型腔所产生的反压力。
5.模具预热温度——为使压铸模能正常工作而在压铸前将压铸模预先加热到一定的温度。
6.持压时间——液态金属充满型腔到完全凝固,在压射冲头压力作用下持续的时间。
7.活动型芯——抽芯机构中的成型零件,成型压铸件上与开模方向不一致的侧凹或侧孔。
8.环型浇道——内浇道呈环型的适用于圆筒类或中间带孔压铸件的浇注系统。
9.实际收缩率——室温下模具成型尺寸与压铸件实际尺寸的差值与模具成型尺寸之比。
10.复位杆——控制推出机构,使之在合模时回到准确位置的杆件。
11.压射力――压铸机压射机构推动压射活塞的力。
12.冷压室压铸机――压铸机的压室与保温炉(或熔炼炉)分开的压铸机。
13.脱模斜度――为了便于压铸件脱出模具的型腔和型芯,而在压铸件上设的斜度。
14.分型面――压铸模动模与定模部分的结合面。
15.真空压铸――在压铸过程中应用真空技术,在压铸模中建立真空的特殊压铸工艺。
16.压铸模热平衡――压铸时在单位时间内模具吸收的热量与散发的热量相等而达到一个平衡状态。
17.导柱、导套――模具中的导向零件,确保动、定模在安装和合模时精确定位,防止动、定模错位。
18.推出机构――压铸件成型后,将压铸件从压铸模型腔中推出的机构。
19.计算收缩率――包括了压铸件收缩值及模具成型零件在工作温度时的膨胀值,计算成型零件成型尺寸所采用的收缩率。
20.压铸模CAD――利用计算机技术完成压铸工艺和压铸模设计过程中的信息检索、方案构思、分析计算、工程绘图和文件编制等工作二、填空1)压铸是压力铸造的简称,其实质是在压力作用下,使液态或半液态金属以较高的速度充填压铸模型腔,并在压力下成形和凝固而获得铸件的方法。
压铸模具基础知识与压铸原理

压铸模具基础知识与压铸原理压铸模具基本知识与原理一、压铸模具重要参数:1,决定着铸件的形状和尺寸公差等级;2,其浇注系统特别是浇口位置决定了熔融金属的填充状况;3,溢流排气系统影响着熔融金属的溢渣排气条件‘4,控制和调节压铸过程的热平衡;5,决定了铸件的表面质量及变形程度;6,模具的强度限期制了压射比压的最大限度;7,影响着生产操作的效率。
二、压铸模具基本要求定义:1,所生产的压铸件,应保持铸件图纸所规定的尺寸和各项技术要求,减少机械加工部位和加工余量,2,模具应适应压铸生产的工艺要求,在设计、审图、制作时要核实铸件脱模结构,冷却,模具结构等;3,应采用先进的结构,减少操作程序,动作准确可靠,构件钢性良好,具有足够的硬度,便于拆卸和维修;4,模具的各种零件应具备良好的机械加工工艺和热处理工艺和热处理工艺条件,选材适当,分差配合等级合理;5,符合压铸机的技术规范,准确选定安装尺寸,能充分发挥压铸机的生产能力;6,尽可能实现标准化,通用化以缩短设计和制造周期,便于管理;7,具备加执和冷却的条件,有利于使模具各部位达到理想的热平衡状态,提高模具的使用寿命。
三、压铸模具的主要组成部分及作用:序号各部分名称作用1定模定模是压铸模的主要组成部分,它与机器压射部分相连接,并固定在压铸机的定模板上,浇注系统与压室相通,是铸件型腔镶块的一个重要部分。
2动模动模是压铸模的另一个主要组成部分,它与定模组成压铸模成型部分的一个整体,它一般固定在模架上,模架又固定在压铸机动模板上,随动模板作开合运动,与定模部分分开,合拢,一般抽芯机构和顶出机构全部在这个部分。
3成型部分(又称型腔及型芯部分)成型部分由镶块及型芯组成装在动定模上,模具在合拢后,构成铸件的形成空腔,通常称型腔,是决定铸件几何形状和尺寸公差等级的部位。
4浇注系统浇注系统是熔融金属进入型腔的通道,它是沟通模具型腔与机器压室的部分,对压铸工艺因素、速度、以及排气、排渣、填充条件起着主要作用。
- 1、下载文档前请自行甄别文档内容的完整性,平台不提供额外的编辑、内容补充、找答案等附加服务。
- 2、"仅部分预览"的文档,不可在线预览部分如存在完整性等问题,可反馈申请退款(可完整预览的文档不适用该条件!)。
- 3、如文档侵犯您的权益,请联系客服反馈,我们会尽快为您处理(人工客服工作时间:9:00-18:30)。
(1)在横浇道的未端和型腔深处。
(2)在金属液最后充填部位。
(3)在金属液的汇合处及容易产生涡流卷气和氧
化夹渣的区域。
(4)需要防止涡流和紊流改善液态金属流动状态
的部位。
(5)在内浇口的两侧或其它金属不易直接充填死
合金压铸模
压铸模具基础知识
前言
压铸:高温融熔金属液,在高速 高压状态下以一 定的条件快速充填型腔,并在一定压力作 用下快速冷却过程。
压铸模是压铸生产中重要的工艺装备,它对生产能否 顺利进行,铸件质量的优劣起着极为重要作用,它与 压铸生产工艺、生产操作存在着又互相影响互为制约, 关系极密切系。
陷部位的2.5~3.5倍, 如果为了平衡模具温度则其容积可以加大 .
排气槽
在压铸时模具型腔内的部分气体约30% 在型腔内不能顺利排出而卷入金属液体中在 填充过程中,会产生反压力,迫使流速下降, 造成铸件冷隔欠铸气孔疏松等缺陷。为了消 除由此而产生的铸件缺陷,要开设排气槽, 排气槽一般和溢流槽配合,设在积渣槽后端。 有些情况下也单独开设排气槽。
(6).限位块
作用: 滑块抽出后要求稳固保持在一定位置上,以便于再
次合模时斜销准确插入滑块斜孔,使滑块准确复位.
抽 拨总距离 = 抽芯距离 + 安全值
(8) .弹簧、螺杆、螺母:
▪ 滑块运动后依靠弹簧张力使滑块紧贴在限位块 的侧面.
▪ 主要参数: 弹簧张力>滑块的身重 , 确保滑块定
(17).推板、固定板:
推板:推板承受压铸机顶出杆作用力,沿导柱
运动。应具有一定的强度
固定板:固定顶杆复位杆等零件沿导柱运动。
顶杆台沉孔等高
材料:45#。
(18).支脚
端面紧固在压铸机墙板上,另一端和模体结合承受机器锁模力,并承受顶 出铸件时的顶出反力。紧固形式必须可靠,其高度尺寸要满足完成顶出 铸件动作。调节模具的厚度
气顺畅部位。
(3) 内浇口布置应考虑尽可能取在金属液流不正面冲击
型芯的部位。
(4) 内浇口布置应考虑取在铸件不易变形的部位。
(5) 内浇口布置应考虑设置在铸件成形后易去除浇口或
冲切浇口部位。
(6) 对于不充许有气孔存在铸件,内浇口应设置在金属
液最终都能保持压力部位。
(7)充填金属液先充填型腔深处再次流向分型面,以达到
角部位。
(6)在大平面上易产生铸件缺陷部位。 (7)在型腔温度较低部位藉以提高型腔温度。 (8)铸件壁厚较厚易产生缩孔部位。 (9)铸件壁厚变化过大难以填充部位。 (10)其它排气条件不良区域。
二 溢排系统:
据熔融金属在模具内填充情况,而开设排气通道。 用于容纳液态金属在充填过程中排出气体、杂物冷污合金等。
位准确. (9).楔紧源自:作用:承受反压力,防止滑块在压射过程中后退。
参数:楔紧斜度角 = 斜销角度 + 3°~5°
紧固形式: 定位螺钉紧固.
材料: T10A
热处理: HRC40~50
液压抽芯机构:
主要由液压缸行程控制开关、侧面型芯、液压
抽芯器等部分组成。
(10).动模套板:
其重要作用是:
(1).决定着铸件形状和尺寸公差级. (2).浇注系统决定了熔融金属的填充状况. (3).控制和调节压铸过程热平衡. (4) 模具的强度限制了压射比压的最大限度. (5) 影响着压铸生产的生产效率.
下面通过对压铸模结构介绍,分析模具中每一个构件的作用、 对模具基本结构形式、固定方法、选用材料及热处理等有一个
(1)、铸件容易附在型腔上,增加顶出困难,且 损伤型腔表面。
(2)、增加压铸的循环时间。 (3)、铸件易产生气孔与收缩不良的缺陷 (4)、离型剂容易挥发和变质。
▪ 4 模具温度过低对压铸生产的影响
直浇道尺寸的确定是跟据铸件结构和重量等要 求来选择确立。
在直浇道的中心设有较长的分流锥,以调整直浇道的截
面积,改变金属液流向,减少金属液消耗量。为了满足高效
率生产的需要,要求在浇口套和分流锥部位设置冷却系统。
直浇道
: 2。横浇道
指直浇道的未端到内浇口前端之部分,对金属液起稳流 和导向作用。设计要求减少金属液的流动阻力,保证金属液 等截面积流动,不宜突然收缩或扩张,防止涡气。
命。
浇口套材料: H13、、3Cr2W8V、
冷却水套材料 :45 #
热处理 : HRC43~47
(15).导柱和导套:
作用: 起导向作用,保证动、定模在安装和合模时的正确位
置,导柱和导套应有足够的刚性和耐磨性,要求配合
间隙合理,模具较大时应开设储油槽,防止冷焊。
导柱直径:D=K√F .(F:模具分型表面积 K:系数
定模是压铸模的主要组成部分, 定模和压铸机的压射部 分相连,并固定在压机压射部分和浇注系统相通,是压 铸件型腔的重要组成部分。主要由定模镶块、定模套板、 导柱、锲紧块、斜导柱、浇口套、定模抽芯机构等部分 组成。
(2)动模 :
动模是压铸模的另一个重要组成部分, 动模是和定
模形成压铸模成型部分的另一个整体,它一般固定
▪
小,P=Alp(Ucosa –sina) p代表比压 ZN 80 AL 100—120
▪
CU 120—160 kg/cm2 u合金对型芯的磨擦系数 0.2—0.25
▪ 斜销长度 = 固定部分 + 工作段尺寸 + (5~10) cm
▪ 材料: T8A、T10A、 热处理: HRC(50~55)
(4).导滑槽: 作用: 限定滑块运动轨迹的组件
第二部分 压铸模浇排系统
一、 浇注系统:
引导金属液以一定的方式充填型腔,对金属液流动方向、 压力传递、充填速度、排气条件、模具的热平衡都能起 到控制和调节作用。 包括三个方面:
1。 直浇道 :
要求:有利压射力传递和金属液充填
平稳,。
对于冷室压铸模一般由压室和浇口套组成。
横浇道长度:取(直浇道)1/2 +(35~50) 横浇道长度尺寸不可以过短小,否则使金属液起稳流和导向
作用不明显。
横浇道
3、内浇口:
内浇口应使金属液以最佳的流动状态充填型腔应先充填
型腔深腔部位,最后流向分型面,避免先封闭分型
面,避免金属液对型芯等薄弱部位冲击,易导致型
芯变形。
内浇口调整着从横浇道输送过来金属液速度,其位置和方向最
排气效果
(8)除特殊件外,内浇口的开设以单澆口为主
二 溢排系统:
据熔融金属在模具内填充情况,而开设排气通 道。
用于容纳液态金属在充填过程中排出气体、杂物冷 污合金等。
溢流槽
具排气、储气、存渣、调温、增力、移缺、控流 等作用。
良好的排气条件取决于排气槽的合理布局及位置、 数量、尺寸、容积、结构形式等方面。
和调节,以保持模具的热平衡。
1、 模具加热的方法。 (1)、用燃气加热。 (2)、用模具温度控制装置加热。 (3)、用电热棒加热。
2、 模具的预热温度
▪ 锌合金模具 140℃~180℃
铝合金模具 150℃~200℃ 镁合金模具 170℃~210℃ 铜合金模具 250℃~300℃
3 模具温度过高对压铸生产的影响
0.07~0.09)
导柱高度:为确保合模时安全,导柱高度应大于最高型芯高
度. 材料: T8A
热处理: HRC50~55.
(16).推杆:
作用:和其它顶出组件配合顶出铸 件.推杆
布置应使铸件各部位受顶压力均衡,据铸件
形状和要求不同,顶杆有不同种类。控制顶
针的数量。
材料: H13、 SKD61
溢流槽
溢流槽的结构形式: (1)布置在模具分型面上的溢流槽 (2)布置在模具型腔内部的溢流槽。 其形式有: 杆形溢流槽 管形溢流槽 环形溢流槽 双级溢流槽 波纹状溢流槽
为了使溢流槽发挥作用,获取较好效果不致消耗过多 金属,增加投影面积,及影响填充流态或引起其它反 作用,故在设置溢流槽位置时应慎重考虑。 其容积占整个铸件的20~30%,特殊情况时占50%。 如果金属铸件局部有缩孔缺陷,则其容积范围可为缺
材料:H13、4Cr5MoV1Si、3Cr2W8V、8407、
SKD61
热处理: HRC43~47
(14).浇口套 冷却水套:
作用:浇口套构成直浇道,保证压射冲头动作顺畅,确保
金属液压力传递和填充平稳,浇口套的直径据铸件所
需比压和铸件的重量选定。要求内側面表面光度高。
对于冷室压铸机模具的制作精度求更高,影响锤头寿
排气槽
排气槽具体可分为分型面上排气和型腔深 处的排气,排气槽在分型面上大多做成曲折 形,并尽可能在模具的上下方,以防金属液 溅出而影响安全。在型腔深处的可以用型芯 和顶针间隙排气。
三 加热和冷却系统: 压铸模具在压铸生产前应进行充分地预热,并在压
铸过程中保持在一定温度范围内。 压铸生产中模具的温度由加热与冷却系统进行控制
作用:起固定支撑定模镶块作用,定模套板受
拉伸、弯曲、压缩三种应力。因此,此板
尺寸和模具质量,刚性关系密切,应充分
重视。
▪
材料:45# A3
(11).型芯:
作用:用来形成鋳件在开模方向或不