原料乳的预处理
乳品生产与质量监控作业指导书

乳品生产与质量监控作业指导书第1章乳品生产概述 (4)1.1 乳品的生产流程 (4)1.1.1 原料乳的采集 (4)1.1.2 预处理 (4)1.1.3 加工 (4)1.1.4 包装 (5)1.1.5 储存 (5)1.1.6 运输 (5)1.2 乳品的质量要求 (5)1.2.1 感官指标 (5)1.2.2 理化指标 (5)1.2.3 微生物指标 (5)1.2.4 食品添加剂 (5)1.3 乳品生产中的危害分析 (5)1.3.1 生物性危害 (5)1.3.2 化学性危害 (5)1.3.3 物理性危害 (6)1.3.4 生产过程危害 (6)1.3.5 储存和运输危害 (6)第2章原料乳的质量监控 (6)2.1 原料乳的验收标准 (6)2.2 原料乳的检验方法 (6)2.3 原料乳的质量控制 (6)第3章乳品加工设备与工艺 (7)3.1 乳品加工设备的选择与维护 (7)3.1.1 设备选择原则 (7)3.1.2 常用乳品加工设备 (7)3.1.3 设备维护与保养 (7)3.2 常见乳品加工工艺流程 (7)3.2.1 巴氏杀菌乳加工工艺 (7)3.2.2 灭菌乳加工工艺 (8)3.2.3 酸奶加工工艺 (8)3.2.4 奶粉加工工艺 (8)3.3 加工过程中的质量监控要点 (8)3.3.1 原料奶质量监控 (8)3.3.2 加工过程质量监控 (8)3.3.3 成品质量监控 (8)第4章乳品生产环境卫生管理 (8)4.1 生产环境卫生要求 (8)4.1.1 厂房与设施 (8)4.1.2 环境空气质量 (8)4.1.3 温湿度控制 (9)4.1.4 人员卫生管理 (9)4.2 清洁与消毒方法 (9)4.2.1 清洁方法 (9)4.2.2 消毒方法 (9)4.3 环境卫生监控 (9)4.3.1 监控指标 (9)4.3.2 监控方法 (9)4.3.3 持续改进 (9)第5章巴氏杀菌乳生产与质量监控 (9)5.1 巴氏杀菌乳的生产工艺 (9)5.1.1 原料乳验收 (10)5.1.2 预处理 (10)5.1.3 标准化 (10)5.1.4 均质 (10)5.1.5 杀菌 (10)5.1.6 冷却 (10)5.1.7 灌装 (10)5.1.8 封口 (10)5.1.9 标签 (10)5.2 杀菌参数的确定与控制 (10)5.2.1 杀菌温度 (10)5.2.2 杀菌时间 (10)5.2.3 杀菌设备 (10)5.2.4 温度控制 (11)5.3 巴氏杀菌乳的质量检验 (11)5.3.1 感官检验 (11)5.3.2 理化检验 (11)5.3.3 微生物检验 (11)5.3.4 保质期检验 (11)第6章硬质乳制品生产与质量监控 (11)6.1 硬质乳制品的生产流程 (11)6.1.1 原料验收 (11)6.1.2 原料处理 (11)6.1.3 发酵 (11)6.1.4 凝固 (11)6.1.5 切割与排放 (11)6.1.6 成型与压制 (12)6.1.7 沸煮 (12)6.1.8 冷却与包装 (12)6.2 发酵剂的选择与使用 (12)6.2.1 发酵剂的种类 (12)6.2.2 发酵剂的使用 (12)6.2.3 发酵剂的保存 (12)6.3 硬质乳制品的质量检验 (12)6.3.1 感官指标 (12)6.3.2 理化指标 (12)6.3.3 微生物指标 (12)6.3.4 检验方法 (12)6.3.5 检验频次 (12)6.3.6 异常处理 (13)第7章软质乳制品生产与质量监控 (13)7.1 软质乳制品的生产工艺 (13)7.1.1 原料选择与处理 (13)7.1.2 配料 (13)7.1.3 均质 (13)7.1.4 发酵 (13)7.1.5 冷却与老化 (13)7.1.6 成型与包装 (13)7.2 稳定剂的选择与应用 (13)7.2.1 稳定剂种类 (13)7.2.2 稳定剂的选择 (13)7.2.3 稳定剂的应用 (14)7.3 软质乳制品的质量检验 (14)7.3.1 感官检验 (14)7.3.2 理化指标检验 (14)7.3.3 微生物指标检验 (14)7.3.4 食品添加剂检验 (14)7.3.5 包装及标签检验 (14)第8章乳粉生产与质量监控 (14)8.1 乳粉的生产方法 (14)8.1.1 原料处理 (14)8.1.2 标准化 (14)8.1.3 均质 (15)8.1.4 浓缩 (15)8.1.5 干燥 (15)8.2 乳粉的喷雾干燥工艺 (15)8.2.1 原理 (15)8.2.2 工艺流程 (15)8.2.3 影响因素 (15)8.3 乳粉的质量检验 (15)8.3.1 感官指标 (15)8.3.2 理化指标 (15)8.3.3 微生物指标 (15)8.3.4 检验方法 (15)第9章乳品包装与储运 (16)9.1 乳品包装材料的选择 (16)9.1.1 包装材料要求 (16)9.1.2 常用包装材料 (16)9.2 乳品包装工艺 (16)9.2.1 清洁与消毒 (16)9.2.2 包装过程 (16)9.2.3 检验与标识 (16)9.3 乳品的储存与运输 (16)9.3.1 储存 (16)9.3.2 运输 (17)第10章乳品质量监控与召回制度 (17)10.1 乳品质量监控体系的建立 (17)10.1.1 监控目标与原则 (17)10.1.2 监控体系构建 (17)10.1.3 质量监控人员培训与管理 (17)10.2 乳品质量检验方法 (17)10.2.1 检验项目 (17)10.2.2 检验方法 (17)10.2.3 检验设备与试剂 (17)10.3 乳品召回制度与实施要点 (18)10.3.1 召回制度的建立 (18)10.3.2 召回流程 (18)10.3.3 实施要点 (18)第1章乳品生产概述1.1 乳品的生产流程乳品生产流程主要包括原料乳的采集、预处理、加工、包装、储存和运输等环节。
全脂奶粉制作工艺流程

全脂奶粉制作工艺流程原料乳验收→预处理→预热杀菌→浓缩→喷雾干燥→冷却→筛粉→包装→装箱→检验→成品制作方法1.原料乳验收和预处理:原料乳必须新鲜,不能混有异常乳,比重应为1.028~1.032(20℃),酸度不超过20°T,含脂率不低于3.1%,乳固体不低于11.5%。
杂菌数不超过20万个/毫升。
合格牛奶要进行过滤和净化等处理。
2.预热杀菌:目的是杀死乳中微生物和破坏酶的活性。
一般采用高温短时间杀菌法,或超高温瞬时间杀菌法。
若使用片式或管式杀菌器,通常采用的杀菌条件为80~85℃、保持30秒钟,或95℃,保持24秒钟。
若用超高温瞬时杀菌装置,则为120~150℃,保持1~2秒钟。
生产加糖乳粉时,加糖方法有三种:(1)预热杀菌时加糖;(2)蔗糖碾细后杀菌,将粉末与喷雾好的乳粉混合,然后装罐;(3)预热杀菌时加一部分糖,然后装罐时再加剩余的糖。
一般生产含糖35%的加糖乳粉时,可采用(2)、(3)法。
但按国家规定标准,加糖乳粉中蔗糖含量应在20%以下。
3.浓缩:原料乳经杀菌后,应立即进行真空浓缩。
一般浓缩至原料乳体积的1/4左右。
浓缩设备,一般小型乳品厂多用单效真空浓缩锅,较大型的乳品厂则都用双效或三效真空蒸发器,也有采用片式真空蒸发器的。
浓缩结束,浓缩乳应进行过滤,一般采用双联过滤器。
4.喷雾干燥:先将过滤的空气由鼓风机吸进,通过空气加热器加热至130~160℃后,送入喷雾干燥室。
同时将过滤的浓缩乳由高压泵送至喷雾器或由奶泵送至离心喷雾转盘,喷成10~20微米的乳滴与热空气充分地接触,进行强烈的热交换和质交换,迅速地排除水分,在瞬间完成蒸发,干燥。
随之沉降于干燥室底部,通过出粉机构不断地卸出,及时冷却。
最后进行筛粉和包装。
5.出粉、冷却:喷雾干燥室内的乳粉要求迅速连续地卸出及时冷却,以免受热过久,降低制品质量。
乳品工业常用的出粉机械有螺旋输送器、鼓型阀、涡旋气封阀和电磁振荡出粉装置等。
先进的生产工艺,是将出粉、冷却、筛粉、输粉、贮粉和称量包装等工序联接成连续化的生产线。
全脂乳粉
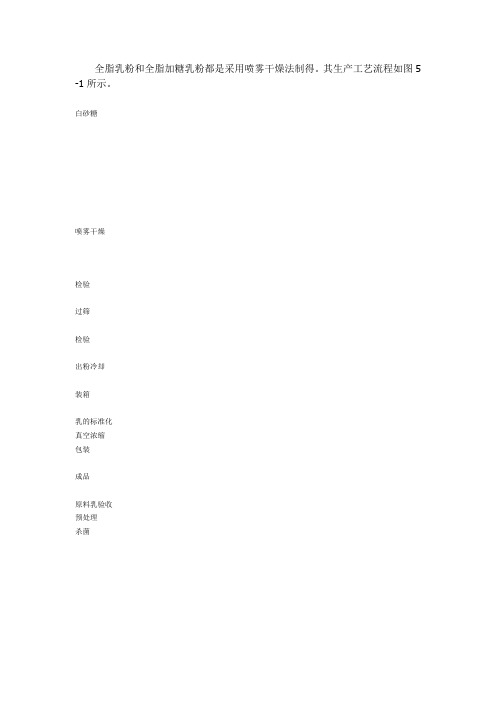
全脂乳粉和全脂加糖乳粉都是采用喷雾干燥法制得。
其生产工艺流程如图5 -1所示。
白砂糖喷雾干燥检验过筛检验出粉冷却装箱乳的标准化真空浓缩包装成品原料乳验收预处理杀菌④操作中,未能严格执行工艺条件及操作规程,严重影响杀菌效果。
⑤杀菌器的传热效果不良,如板式杀菌器水垢增厚,使传热系数降低,影响杀菌效果。
⑥杀菌器本身的故障。
保温杀菌罐的大小与搅拌器大小及转速配合不当,使罐的下部形成冷乳层,使杀菌温度不够;牛乳起泡时造成受热温度不匀;杀菌器保温层绝缘不良;自动控制系统发生故障;板式杀菌器的预热段胶垫破损时,造成生乳的混入,等等。
4. 乳粉的加糖及杀菌乳粉的加糖须按照我国部颁标准规定,所使用的蔗糖必须符合相应国家标准。
(1)加糖量的计算为保证乳粉含糖量符合国家规定标准,需预先经过计算。
根据标准化乳中蔗糖含量与标准化中干物质含量之比,必须等于加糖乳粉中蔗糖含量与乳粉中乳干物质含量之比,则牛乳中加糖量可按下述公式计算(5-1)(2)加糖方法及杀菌常用的加糖方法有以下三种①将糖投入原料乳中溶解加热,同牛乳一起杀菌。
②将糖投入水中溶解,制成浓度约为65%的糖浆溶液进行杀菌,再与杀菌过的牛乳混合。
③将糖粉碎杀菌后,再与喷雾干燥好的乳粉混匀。
前两种属于先加糖法,制成的产品能明显改善乳粉的溶解度,提高产品的冲调性。
第三种为后加糖法,采用该方法生产的乳粉体积小,从而节省了包装费用。
由于蔗糖具有热熔性,在喷雾干燥塔中流动性较差,所以当生产含糖35%的加糖乳粉时一般采用后加糖法,生产含糖20%以下的加糖乳粉采用先加糖法。
三、蒸发(浓缩)为了节约能源和保证产品质量,喷雾干燥前对杀菌乳必须进行浓缩。
乳浓缩是利用设备的加热作用,使乳中的水分在沸腾时蒸发汽化,并将汽化产生的二次蒸汽不当排除,从而使制品的浓度不当提高,直至达到要求的浓度的工艺过程。
浓缩技术对其工艺流程的设计、设备的选型、制造加工和具体操作提出了较高要求,随着科学技术及生产的发展,浓缩已趋向低温、快速、连续的发方向发展。
原料乳的验收和预处理

第一节 乳中微生物 一、乳中微生物及来源
(二)乳中微生物的来源
❖1、乳房内微生物的污染
❖2、挤乳过程中的微生物污染
❖3、挤乳后的细菌污染
第一节 乳中微生物 二、鲜乳中微生物的变化
(一)鲜乳在室温贮藏中微生物的变化 ❖1、抑制期 ❖2、乳链球菌期 ❖3、乳酸杆菌期 ❖4、真菌期 ❖5、胨化菌期
图3-2 鲜乳中的微生物菌群变化曲线
第一节 乳中微生物 一、乳中微生物及来源
(一)乳中的微生物种类 ❖3、原料乳中的乳酸菌 ❖(1)乳酸球菌 ❖ ①乳酸乳球菌 ❖ ②嗜热链球菌 ❖ ③乳酸乳球菌乳脂亚种 ❖ ④粪肠球菌 ❖ ⑤肠膜明串珠菌
第一节 乳中微生物 一、乳中微生物及来源
(一)乳中的微生物种类 ❖3、原料乳中的乳酸菌 ❖(2)乳酸杆菌 ❖ ①德氏乳杆菌保加利亚亚种菌 ❖ ②嗜酸乳杆菌 ❖ ③干酪乳杆菌
❖ 原料乳的几种污染来源包括: ❖ 手工挤奶对原料乳的污染; ❖ 水对原料奶的污染; ❖ 机械挤奶对原料乳的污染。
第二节 原料乳检验与验收 一、原料乳的质量要求
(二)原料乳的质量控制 ❖5. 原料乳的贮存与运输
❖ 挤奶结束后应尽快(2h内)将原料乳冷却至10℃以下。 原料乳在符合贮存温度的条件下贮存不得超过24h,过长 会使原料乳中的嗜冷菌大量繁殖,影响原料乳质量。
第一节 乳中微生物 一、乳中微生物及来源
(一)乳中的微生物种类 ❖1、原料乳中的病原微生物
❖(1)葡萄球菌:葡萄球菌是一群革兰氏阳性球菌, 因常堆聚成葡萄串状 ❖(2)结核菌:侵入人体后引起的结核病是一种具 有强烈传染性的慢性消耗性疾病 ❖(3)溶血性链球菌:溶血性链球菌又称沙培林
第一节 乳中微生物 一、乳中微生物及来源
第二节 原料乳检验与验收 一、原料乳的质量要求
奶酪加工

奶酪的生产方法是,首先对鲜奶进行快速的巴氏灭菌(70℃几秒钟或66℃15秒钟)。
然后加入发酵剂(链球菌属),鲜奶中的糖和乳糖开始转变成乳酸。
当达到适当的酸值时,加入凝乳酶,使奶蛋白质变性而产生“凝块”。
将凝块切成片,用蒸汽热烫的方法使其干燥。
蒸汽的温度高低取决于所生产奶酷的种类。
热烫法能使奶酪颗粒收缩凝聚并挤干凝块。
酸度、温度和奶酪的新鲜度都会加速凝块的形成。
凝块沉落到桶底,互相堆积在一起,析出的乳清从桶底流出。
凝乳酶、酸和热橄使酷蛋白发生变化,凝块从橡胶状变成面团状。
将凝块切成小块,加入食盐以溶解某些蛋白质,并有助于捏合,同时也适当地控制熟化过程中细菌的活性。
将小块凝乳谢谢模具中压干即成为奶酪。
最后,将奶酪翻转、冲洗、加油和裹包,入库使其熟化。
奶酪的味道和种类取决于制造工艺以及所选用的发酵菌种。
一、Feta 奶酪:产品含水量55%,脂肪22%。
(一)牛奶标准化到P/F=0.90,然后进行巴氏杀菌(72℃或62℃,30min)。
希腊人喜欢羊奶制成的纯白光滑的奶酪。
山羊奶也可用来制备白色奶酪。
如果需要制备光滑细腻的牛奶奶酪,可以选择脂肪含量高达为 5.5~6.0%的牛奶。
如果不希望奶酪有奶油的颜色,可以用0.03~0.04%的二氧化钛处理。
在酶凝乳前,二氧化钛用温水稀释10倍然后加入牛奶中。
另外,也可用均质牛奶生产出白色的牛奶奶酪。
(二)调整牛奶温度到30℃,每1000kg牛奶中加入3%的乳酸菌(ctis)和/或乳酪菌(S.sremoris)菌和3g解脂酶。
成熟大约1h直到滴定酸度(TA)0.05%以上,pH为6.6~6.5为宜。
(三)每1000kg牛奶加120ml凝乳酶。
首先将凝乳酶用其10倍的水稀释,然后与牛乳混合,搅拌3min,再静置45~60min。
(四)用12.8mm的小刀切块后轻轻搅拌20min。
将凝块和乳清加入成型器中,在30℃下排除乳清2h。
然后将凝块放置在温度为18℃、相对湿度为85%的房间内,用清洁的布覆盖、过夜。
原料乳的预处理

原料乳得预处理一、储存罐(奶仓)得构成:搅拌器、探孔、温度指示、低液位电极、气动液位指示器、高液位电极二、储存罐得作用及操作注意事项:1、奶仓得搅拌大型奶仓必须带有某种形式得搅拌设施,以防止稀奶油由于重力得作用从牛乳中分离出来。
搅拌必须十分平稳,过于剧烈得搅拌将导致牛乳中混入空气与脂肪球得破裂,从而使游离得脂肪在牛乳得解脂酶得作用下分解。
因此,轻度得搅拌就是牛乳处理得一条基本原则。
2、罐内温度指示罐内得温度显示在罐得控制盘上,一般可使用一个普遍温度计,但使用电子传感器得越来越多,传感器将信号送至中央控制台,从而显示出温度。
3、液位指示有各种方法来测量罐内牛乳液位,气动液位指示器通过测量静压来显示出罐内牛乳得高度,压力越大,罐内得液位越高,指示器把读数传递给表盘显示出来。
4、低液位保护所有牛乳得搅拌必须就是轻度得,因此,搅拌器必须被牛乳覆盖以后再启动。
为此,常在开始搅拌所需液位得罐壁安装一根电极。
罐中得液位低于该电极时,搅拌停止,这种电极就就是通常所说得低液位指示器(LL)。
5、溢流保护为防止溢流,在罐得上部安装一根高液位电极(HL)。
当罐装满时,电极关闭进口阀,然后牛乳由管道改流到另一个大罐中。
6、空罐指示在排乳操作中,重要得就是知道何时罐完全排空。
否则当出口阀门关闭以后,在后续得清洗过程中,罐内残留得牛乳就会被冲掉而造成损失。
另一个危害就是,当罐排空后继续开泵,空气就会被吸入管线,这将影响后续加工。
因此在排乳线路中常安装一根电极(LLL),以显示该罐中得牛乳已完全排完。
该电极发出得信号可用来启动另一大罐一、乳化罐得作用就是将一种或多种物料(水溶性固相、液相或胶状物等)溶于另一种液相,并使其水合成为相对稳定得乳化液。
广泛适用于食用油类、粉类、糖类等原辅料得乳化混合,某些涂料、油漆乳化分散也使用乳化罐,尤其适用于某些难溶胶状类添加剂如CMC、黄原胶等,对基质粘度大,固料含量比较高得物料配置乳化更显功效。
江西农业大学食品类专业2018年专业试卷及答案-畜产品加工学B
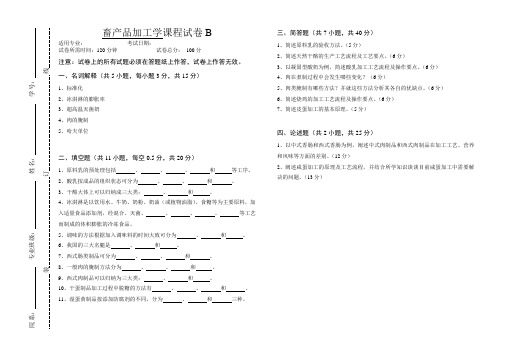
畜产品加工学课程试卷B适用专业: 考试日期:试卷所需时间:120分钟 试卷总分: 100分注意:试卷上的所有试题必须在答题纸上作答,试卷上作答无效。
一、名词解释(共5小题,每小题3分,共15分)1、标准化2、冰淇淋的膨胀率3、超高温灭菌奶4、肉的腌制5、哈夫单位二、填空题(共11小题,每空0.5分,共20分)1、原料乳的预处理包括 、 、 、 和 等工序。
2、酸乳按成品的组织状态可分为 、 、 和 。
3、干酪大体上可以归纳成三大类: 、 和 。
4、冰淇淋是以饮用水、牛奶、奶粉、奶油(或植物油脂)、食糖等为主要原料,加入适量食品添加剂,经混合、灭菌、 、 、 、 等工艺而制成的体积膨胀的冷冻食品。
5、调味的方法根据加入调味料的时间大致可分为 、 和 。
6、我国的三大名腿是 、 和 。
7、西式肠类制品可分为 、 、 和 。
8、一般肉的腌制方法分为 、 、 和 。
9、西式肉制品可以归纳为三大类: 、 和 。
10、干蛋制品加工过程中脱糖的方法有 、 、 和 。
11、湿蛋黄制品按添加防腐剂的不同,分为 、 和 三种。
三、简答题(共7小题,共40分)1、简述原料乳的验收方法。
(5分)2、简述天然干酪的生产工艺流程及工艺要点。
(6分)3、以凝固型酸奶为例,简述酸乳加工工艺流程及操作要点。
(6分)4、肉在煮制过程中会发生哪些变化?(6分)5、肉类腌制有哪些方法?并就这些方法分析其各自的优缺点。
(6分)6、简述烧鸡的加工工艺流程及操作要点。
(6分)7、简述皮蛋加工的基本原理。
(5分)四、论述题(共2小题,共25分)1、以中式香肠和西式香肠为例,阐述中式肉制品和西式肉制品在加工工艺、营养和风味等方面的差别。
(12分)2、阐述咸蛋加工的原理及工艺流程,并结合所学知识谈谈目前咸蛋加工中需要解决的问题。
(13分)院系: 专业班级: 姓名: 学号:装 订 线畜产品加工学考试卷B参考答案一、名词解释1、标准化:每天收购的原料乳质量差异大且生产班次不固定,使原料奶中脂肪等含量达到均匀一致而进行的调整。
乳品加工技术 原料乳的预处理

乳温5-8℃
2-2-2 原料乳的预处理
图3-4 浸没式冷却器 A.奶桶外冷却 B.奶桶内冷却 C.奶罐内冷却
3、冷却罐及浸没式冷却法
✓ 这种冷却器可以插入贮乳槽或奶桶 中以冷却牛乳。
✓ 浸没式冷却器中带有离心式搅拌器, 可以调节搅拌速度,并带有自动控 制开关,可以定时自动进行搅拌, 故可使牛乳均匀冷却,并防止稀奶 油上浮。
2-2-2 原料乳的预处理
五、原料乳的运输
✓ 1、防止乳在途中升温,特别是在夏季,运输最好在夜间 或早晨,或用隔热材料盖好桶;
✓ 2、所采用的容器须保持清洁卫生,严格杀菌; ✓ 3、夏季必须装满盖严,以防震荡;冬季不得装得太满,
避免因冻结而使容器破裂;
✓ 4、长距离运送乳时,最好采用乳槽车。
2-2-2 原料乳的预处理
三、原料乳的冷却
(二)冷却方法 ✓ 1、水池冷却法 ✓ 2、板式热交换器冷却 ✓ 3、冷却罐及浸没式冷却法
2-2-2 原料乳的预处理
1
2
34
1 23 4
3-2 水池冷却乳的方法 1.量乳器 2.过滤器 3.接收槽 4.开关
1、水池冷却法✓ 最普通而易的方法是将装乳的奶桶 放在水池中用冰水或冷水进行冷却。
✓ 为了加速冷却,需经常进行搅拌,并 按照水温进行排水和换水。
✓ 水池冷却的缺点是:冷却缓慢、耗水
量多,劳动强度大、不易管理。
2-2-2 原料乳的预处理 原料乳
2、板式热交换器冷却
板器式热交乳水乳换流或槽过冷(板盐罐水)式)中热进。交行换热器交与换制后冷流剂入(贮冷 特点:构造简单,价格低廉,冷却 效率也比较高,适于小规模加工厂
2-2-2 原料乳的预处理
四、原料乳的贮存
6.3原料乳的验收和预处理
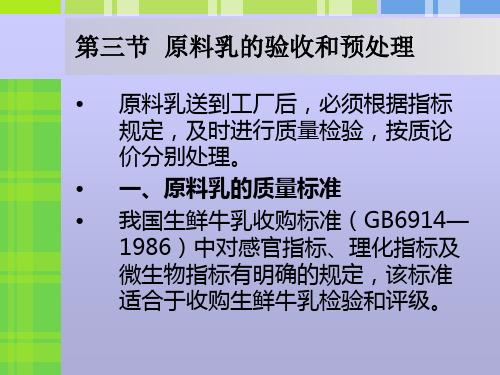
• ②稀释倾注平板法 • 平板培养计数是取样稀释后,接种于 琼脂培养基上,培养24 h后计数,测 定样品的细菌总数。该法测定样品中 的活菌数,需要时间较长。
• ③直接镜检法(费里德氏法) 利用显微镜 直接观察确定鲜乳中微生物数量的一种方法。 取一定量的乳样,在载玻片上涂抹一定的面 积,经过干燥、染色,镜检观察细菌数,根 据显微镜视野面积,推断出鲜乳中的细菌总 数,而非活菌数。 • 直接镜检比平板培养法更能迅速判断结果, 通过观察细菌的形态,还能推断细菌数增多 的原因。
• (3)抗生素残留量检验 • 牧场用抗生素治疗乳牛的各种疾病,特别是 乳房炎,有时用抗生素直接注射乳房部位进 行治疗。经抗生素治疗过的乳牛,其乳中在 一定时期内仍残存抗生素。对抗生素有过敏 体质的人饮用该乳后,会发生过敏反应,也 会使某些菌株对抗生素产生抗药性。我国规 定乳牛最后一次使用抗生素后5天内的乳不 得收购。
• (4)煮沸试验 • 牛乳的酸度越高,其稳定性越差。 在 加热的条件下高酸度易产生乳蛋白质 的凝固。因此,用煮沸试验来验证原 料乳中蛋白质的稳定性,判断其酸度 高低,测定原料乳在超高温杀菌中的 稳定性。
• (5)乳成分的测定 • 近年来随着分析仪器的发展,乳品检 测方法出现了很多高效率的检验仪器。 如采用光学法来测定乳脂肪、乳蛋白、 乳糖及总干物质,并已开发使用各种 微波仪器。
第三节 原料乳的验收和预处理
• 原料乳送到工厂后,必须根据指标 规定,及时进行质量检验,按质论 价分别处理。 一、原料乳的质量标准 我国生鲜牛乳收购标准(GB6914— 1986)中对感官指标、理化指标及 微生物指标有明确的规定,该标准 适合于收购生鲜牛乳检验和评级。
• •
(一) 感官指标
•
正常牛乳呈白色或微带黄色,不得 含有肉眼可见的异物,不得有红色、 绿色或其他异色。不能有苦味、咸 味、涩味和饲料味、青贮味、霉味 等异常味。
原料乳的验收和预处理
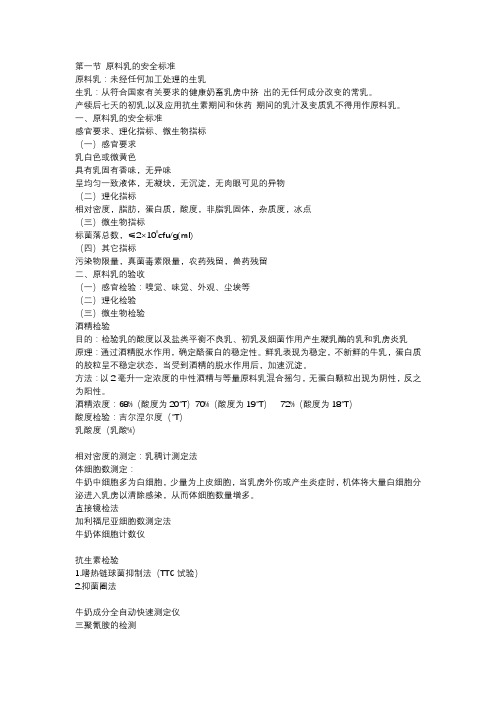
酸度检验:吉尔涅尔度(°T)
乳酸度(乳酸%)
相对密度的测定:乳稠计测定法
体细胞数测定:
牛奶中细胞多为白细胞,少量为上皮细胞,当乳房外伤或产生炎症时,机体将大量白细胞分泌进入乳房以清除感染,从而体细胞数量增多。
直接镜检法
加利福尼亚细胞数测定法
牛奶体细胞计数仪
抗生素检验
1.嗜热链球菌抑制法(TTC试验)
2.抑菌圈法
牛奶成分全自动快速测定仪
三聚氰胺的检测
第二节 原料乳的预处理
一、原料乳的收购与运输
乳桶运输、奶槽车运输
注意事项:
收购检验
降温,低温运输
容器保持清洁卫生,严格杀菌
夏季应该装满盖严,以防震荡,冬季不能装太满,防止解冻使容器破裂
(三)微生物检验
酒精检验
目的:检验乳的酸度以及盐类平衡不良乳、初乳及细菌作用产生凝乳酶的乳和乳房炎乳
原理:通过酒精脱水作用,确定酪蛋白的稳定性。鲜乳表现为稳定,不新鲜的牛乳,蛋白质的胶粒呈不稳定状态,当受到酒精的脱水作用后,加速沉淀。
方法:以2毫升一定浓度的中性酒精与等量原料乳混合摇匀,无蛋白颗粒出现为阴性,反之为阳性。
三、原料乳的冷却
目的:降温,抑制微生物繁殖,防止乳酸度升高,保证乳的新鲜度和质量。
方法:水池冷却、冷却罐即浸没式冷却器、板式热交换器冷却
四、原料乳的贮存(防止温度升高,有良好的绝热保温措施)
贮乳灌
五、原料乳的标准化
原理:脂肪与无脂干物质之间的比值标准化
手段:添加稀奶油和脱脂乳来进行调节
第一节 原料乳的安全标准
原料乳:未经任何加工处理的生乳
第七章乳的验收及预处理

原料乳的验收主要包括感观检测、理化指标 测定、微生物检验三方面。
一、原料乳的质量标准
(一)理化指标 (二)感官指标 (三)细菌指标 (四)其他
(一)原料乳的理化指标(GB6914-86)99页
项目
密度(20℃/4℃) 脂肪(%) 蛋白质(%)
四、原料乳的贮存
为了保证工厂连续生产的需要,
必须有一定的原料乳贮存量, 一般应不少于工厂1d的处理量。 冷却后的乳应尽可能保持低温, 以防止温度升高保存性降低。
因此,贮存原料乳的设备,要
有良好的绝热保温措施,并配 有适当的搅拌机构,定时搅拌
乳液防止乳脂肪上浮而造成分
布不均匀。
贮乳槽的要求: 1. 有绝缘层的不锈钢,具有保冷作用,但非制冷设备,经 24小时 T<3℃
6.体细胞数
正常乳中的体细胞,多数来源于上皮组织的单核细胞,如 有明显的多核细胞(白细胞)出现,可判断为异常乳。 常用的方法有直接镜检法(同细菌检验)或加利福尼亚细胞 数测定法(GMT法)。 GMT法是根据细胞表面活性剂的表面张力,细胞在遇到表
面活性剂时会收缩凝固。细胞越多,凝集状态越强,出现 的凝集片越多。
产的乳和停药后3d内的乳
添加有防腐剂、抗菌素和其他任何有碍食品卫生的乳。
二、原料乳的验收
1.感官检验 2.酒精检验 3.滴定酸度 4.比重 5.细菌数 6.体细胞数 7.抗生物质检验 8.乳成分的测定
1.感官检验
鲜乳的感官检验主要是进行嗅觉、味觉、外观、尘埃 等的鉴定。 正常鲜乳为乳白色或微带黄色,不得含有肉眼可见的 异物,不得有红、绿等异色,不能有苦、涩、咸的滋
CIP 清洗过程
酸奶加工原料乳预处理工艺流程
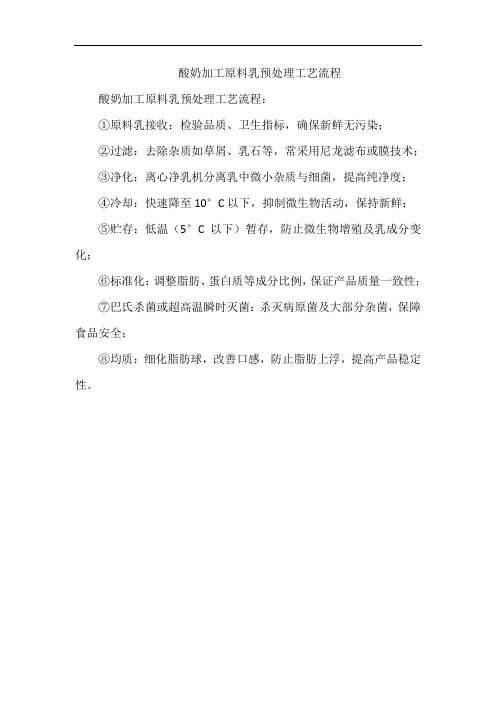
酸奶加工原料乳预处理工艺流程
酸奶加工原料乳预处理工艺流程:
①原料乳接收:检验品质、卫生指标,确保新鲜无污染;
②过滤:去除杂质如草屑、乳石等,常采用尼龙滤布或膜技术;
③净化:离心净乳机分离乳中微小杂质与细菌,提高纯净度;
④冷却:快速降至10°C以下,抑制微生物活动,保持新鲜;
⑤贮存:低温(5°C以下)暂存,防止微生物增殖及乳成分变化;
⑥标准化:调整脂肪、蛋白质等成分比例,保证产品质量一致性;
⑦巴氏杀菌或超高温瞬时灭菌:杀灭病原菌及大部分杂菌,保障食品安全;
⑧均质:细化脂肪球,改善口感,防止脂肪上浮,提高产品稳定性。
原料乳的验收和预处理
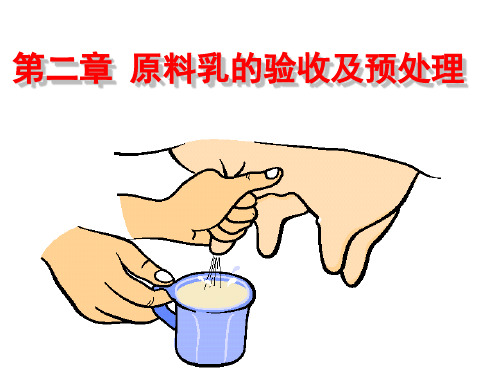
2019/5/21
1
学习目标
1.了解原料乳的质量标准及验收方法。 2.掌原料乳净化和冷却方法。
一、原料乳的质量标准
我国规定生鲜牛乳收购的质量标准 (GB6914—86)包括感官指标、理化指标 及微生物指标。
质量标准
1.感官指标 正常牛乳白色或微带黄色,不得含有肉眼 可见的异物,不得有红色、绿色或其他异 色。不能有苦味、咸味、涩味和饲料味、 青贮味、霉味异常味。
Ⅰ
≤50
Ⅱ
≤100
≥4h ≥2.5h
Ⅲ
≤200
≥1.5h
Ⅳ
≤400
≥40min
此外,许多乳品收购单位还规定下述情况之一者不 得收购:
①产犊前15d内的末乳和产犊后7d内的初乳; ②牛乳颜色有变化、呈红色、绿色或显著黄色者; ③牛乳中有肉眼可见杂质者; ④牛乳中有凝块或絮状沉淀者; ⑤牛乳中有畜舍味、苦味、霉味、臭味、涩味、煮
(2)收奶过程
• 收奶过程包括原料乳质量的验收、计量、净 乳、冷却和贮存。
1.脱气装置 2.过滤器 3.牛乳流量计 4.中间贮存罐 5.预杀菌和冷却或仅为冷却 6.奶仓
• 收. 奶系统如图所示,用奶槽车把牧场或
奶站的原料乳运回乳品厂,由脱气装置 (1)将牛乳中的气体除去,通过过滤器(2) 将杂质过滤,由流量计(3)计量后,在中 间贮存罐(4)暂存,经板式热交换器(5)预 杀菌和冷却或仅为冷却后,再用离心泵 送到奶仓(6)贮存。
微生物检验 ①细菌检查:
美兰还原试验 细菌总数测定 直接镜检 ②细胞数检验
直接镜检法 CMT法 ③抗生素残留量检验
TTC试验 滤纸圆片法 SNAP抗生素残留检测 系统
三、计量
炼 乳

全脂乳中的SNF SNF1= ×100% 100 全脂乳中的F
(2)稀奶油中SNF2的计算
100 稀奶油中的F2 ×脱脂乳中SNF1 × 100% 100
计算依据:酪乳与脱脂乳非脂乳固体比例相等
2.含脂率不足时标准化的计算 在脂肪不足时可添加稀奶油,需要的量为
(SNF R)- F C= F2-(SNF2 R ×M
5.冷却结晶方法
分为间歇式及连续式两大类。 间歇式冷却结晶通常采用蛇管冷却结晶器。 分为三个阶段: 第一阶段为冷却初期,即浓乳出料后乳温在 50℃左右,应迅速冷却至35℃左右; 第二阶段为强制结晶期,继续冷却至接近28℃, 可投入晶种,搅拌。保温0.5h左右,以充分形成 晶核; 第三阶段冷却后期 把炼乳冷却至20℃搅拌1h, 即完成冷却结晶操作。
(2) 加糖方法 ① 将糖直接加于原料乳中,然后预热。 ② 原料乳和65%~75%的浓糖浆分别经95℃, 5min杀菌,冷却至57℃后混合浓缩。 ③ 在浓缩将近结束时,将杀菌并冷却的浓糖 浆吸入浓缩罐内。 加糖方法不同,乳的黏度变化和成品的增稠 趋势不同。一般来讲,糖与乳接触时间越长,变 稠趋势就越显著。由此可见,上述3种加糖方法 中,第三种为最好
例l:炼乳中总乳固体的含量为28%,蔗糖含 量为45%,其蔗糖比为多少? 解: 45 % Rs= 100 % 28 % ×100%=62.5% 根据所要求的蔗糖比,也可以计算出炼乳中 的蔗糖含量。
例2:炼乳中总乳固体含量为28%,脂肪为8%.标准 化后原料乳的脂肪含量为3.16%,非脂乳固体含量 为7.88%,欲制得蔗糖含量45%的炼乳,试求100kg 原料乳中应添加蔗糖多少? 解:浓缩比 28 8 Rc= 7 . 88 =2.53
牛奶预处理高温工作描述
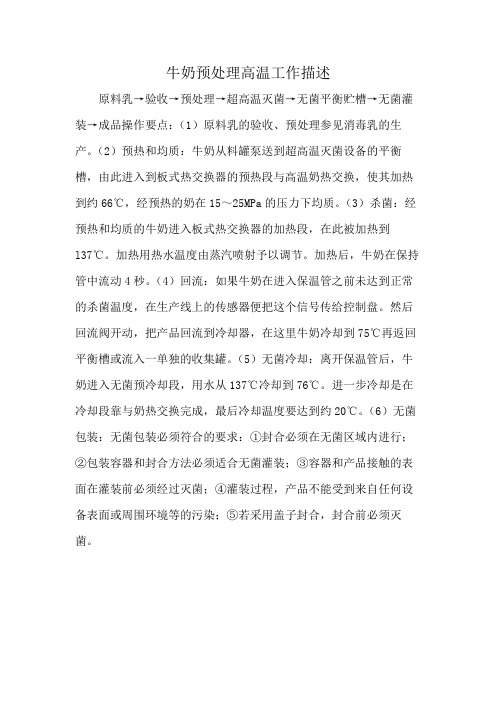
牛奶预处理高温工作描述
原料乳→验收→预处理→超高温灭菌→无菌平衡贮槽→无菌灌装→成品操作要点:(1)原料乳的验收、预处理参见消毒乳的生产。
(2)预热和均质:牛奶从料罐泵送到超高温灭菌设备的平衡槽,由此进入到板式热交换器的预热段与高温奶热交换,使其加热到约66℃,经预热的奶在15~25MPa的压力下均质。
(3)杀菌:经预热和均质的牛奶进入板式热交换器的加热段,在此被加热到
l37℃。
加热用热水温度由蒸汽喷射予以调节。
加热后,牛奶在保持管中流动4秒。
(4)回流:如果牛奶在进入保温管之前未达到正常的杀菌温度,在生产线上的传感器便把这个信号传给控制盘。
然后回流阀开动,把产品回流到冷却器,在这里牛奶冷却到75℃再返回平衡槽或流入一单独的收集罐。
(5)无菌冷却:离开保温管后,牛奶进入无菌预冷却段,用水从137℃冷却到76℃。
进一步冷却是在冷却段靠与奶热交换完成,最后冷却温度要达到约20℃。
(6)无菌包装:无菌包装必须符合的要求:①封合必须在无菌区域内进行;
②包装容器和封合方法必须适合无菌灌装;③容器和产品接触的表面在灌装前必须经过灭菌;④灌装过程,产品不能受到来自任何设备表面或周围环境等的污染;⑤若采用盖子封合,封合前必须灭菌。
- 1、下载文档前请自行甄别文档内容的完整性,平台不提供额外的编辑、内容补充、找答案等附加服务。
- 2、"仅部分预览"的文档,不可在线预览部分如存在完整性等问题,可反馈申请退款(可完整预览的文档不适用该条件!)。
- 3、如文档侵犯您的权益,请联系客服反馈,我们会尽快为您处理(人工客服工作时间:9:00-18:30)。
原料乳的预处理一、储存罐(奶仓)的构成:搅拌器、探孔、温度指示、低液位电极、气动液位指示器、高液位电极二、储存罐的作用及操作注意事项:1、奶仓的搅拌大型奶仓必须带有某种形式的搅拌设施, 以防止稀奶油由于重力的作用从牛乳中分离出来。
搅拌必须十分平稳,过于剧烈的搅拌将导致牛乳中混入空气和脂肪球的破裂,从而使游离的脂肪在牛乳的解脂酶的作用下分解。
因此,轻度的搅拌是牛乳处理的一条基本原则。
2、罐内温度指示罐内的温度显示在罐的控制盘上, 一般可使用一个普遍温度计,但使用电子传感器的越来越多,传感器将信号送至中央控制台,从而显示出温度。
3、液位指示有各种方法来测量罐内牛乳液位,气动液位指示器通过测量静压来显示出罐内牛乳的高度, 压力越大,罐内的液位越高,指示器把读数传递给表盘显示出来。
4、低液位保护所有牛乳的搅拌必须是轻度的,因此,搅拌器必须被牛乳覆盖以后再启动。
为此,常在开始搅拌所需液位的罐壁安装一根电极。
罐中的液位低于该电极时,搅拌停止,这种电极就是通常所说的低液位指示器(LL)。
5、溢流保护为防止溢流,在罐的上部安装一根高液位电极(HL)。
当罐装满时,电极关闭进口阀,然后牛乳由管道改流到另一个大罐中。
6、空罐指示在排乳操作中,重要的是知道何时罐完全排空。
否则当出口阀门关闭以后,在后续的清洗过程中,罐内残留的牛乳就会被冲掉而造成损失。
另一个危害是,当罐排空后继续开泵,空气就会被吸入管线,这将影响后续加工。
因此在排乳线路中常安装一根电极(LL L) ,以显示该罐中的牛乳已完全排完。
该电极发出的信号可用来启动另一大罐的排乳,一、乳化罐的作用是将一种或多种物料(水溶性固相、液相或胶状物等)溶于另一种液相,并使其水合成为相对稳定的乳化液。
广泛适用于食用油类、粉类、糖类等原辅料的乳化混合,某些涂料、油漆乳化分散也使用乳化罐,尤其适用于某些难溶胶状类添加剂如CMC、黄原胶等,对基质粘度大,固料含量比较高的物料配置乳化更显功效。
二、乳化罐的构成乳化罐是一种三个同轴搅拌混合器,适用于稳定均质乳化,产生的颗粒非常小,乳化质量取决于在准备阶段颗粒是如何被散布的,颗粒越小,聚集到表面上的趋势越弱,因而乳化被破坏的机会越小。
乳化罐采用上部同轴三重型搅拌器,液压升降开盖,快速均质搅拌器转速:0-3000r/min(变频调速)、慢速刮壁搅拌器搅拌自动紧贴罐底及罐壁。
采用真空吸料、特别对粉体物料利用真空吸入避免粉尘飞扬。
整个工序在真空条件下进行,防止物料在高速搅拌后产生气泡,能达到卫生无菌要求。
本系统配有CIP清洗系统、容器与物料接触部分采用SUS316L材料制造、内表面镜面抛光(卫生级)。
三、乳化罐的工作原理离心式高速乳化头在工作时可产生巨大的旋转吸力,将转子正上方的物料旋转吸下,然后高速抛向定子,经过转定子间的高速剪切、碰撞、粉碎后,物料汇集至出口而喷出,同时罐底防涡流挡板将旋转力转化为上下翻腾力,从而使罐内物料混合均匀,防止粉料在页面堆积聚团,从而达到水合乳化的目的。
四、乳化罐的操作:开机前设备的检查1. 检查乳化罐是否具备“完好”和“清洁”标识2. 乳化罐在加入物料前,先打开纯化水阀喷淋,淋洗乳化罐内壁,并将淋洗水全部排出3.ﻩ检查乳化罐的底部出料阀,应已关闭4.ﻩ接通乳化罐电源开关,电压表应显示为380+5%,红色电源指示灯应亮5.ﻩ打开上盖上的视灯镜,再次检查乳化罐内,应不得有任何异物,以防止乳化头在告诉运转时碰撞受损6. 检查乳化罐上盖,应与机体全部密合,是否密合,可调节,方法如下:(1)在上升开盖和下降肝淖铸程中,乳化机的慢速搅拌和乳化头应该停止运行,才能运行(2)ﻩ按绿色“上升”按钮,乳化罐上盖应自动上升,当上升到期望的高度时,按红色“停止”按钮,上盖应停止上升,,按绿色“下降”按钮,上盖应自动下降,当与机体密合时,按“停止”按钮,停止下降7.ﻩ打开乳化罐夹套的冷却水进出水阀,准备乳化操作8.ﻩ以上操作符合要求后,可进行下步操作五、操作步骤1. 首先加入物料,严禁空罐开机,物料不得低于5%容积。
以免烧坏搅拌机轴套。
添加物料不能超过罐体容积的百分之七十,以免搅拌时物料溢出,造成烫伤。
2. 打开搅拌电机断路器,开始搅拌。
3. 打开蒸汽截止阀,调至合适开度。
4.检查疏水阀有无排水。
观察罐体温度表,温度超过设定值时适当关小截止阀。
警告与报警处理:运行中要严格执行工艺操作规程,严禁超温、超压、超负荷运行六、安全注意1.安全锁禁止在真空状态下误打开上盖。
2.如上盖与容体没有完好对准,密闭度不够,停用。
3.如果上盖没有完全提升,倾倒功能停用。
4.当上盖开时,混合和均质马达,真空泵停用。
5.限动微动开关自动执行上盖的开/关。
6.各参数可按用户要求予以变化,并达到最佳性能。
一、均质机介绍:均质机是用于对粘度低于0.2Pa.s,温度低于80℃的液体物料(液-液相或液-固相)的均质\乳化的一种设备.主要应用于食品或化工行业,如:乳品、饮料、化妆品、药品等产品的生产过程中的均质、乳化工序。
食品加工中的均质机的应用:食品加工中的均质机是指将物料的料液在挤压,强冲击与失压膨胀的三重作用下使物料细化,从而使物料能更均匀的相互混合,比如奶制品加工中使用均质机使牛奶中的脂肪破碎的更加细小,从而使整个产品体系更加稳定。
牛奶会看起来更加洁白。
均质主要通过均质机来进行的。
是食品、乳品、饮料的行业的重要加工设备。
二、均质机工作原理:转子和定子的精密配合,工作头(转子和定子锻件制造)爪式结构,双向吸料,剪切效率高。
间歇式高剪切分散乳化均质机是通过转子高速平稳的旋转,形成高频、强烈的圆周切线速度、角向速度等综合动能效能;在定子的作用下,定、转子合理狭窄的间隙中形成强烈、往复的液力剪切、摩擦、离心挤压、液流碰撞等综合效应,物料在容器中循环往复以上工作过程,最终获得产品。
均质前需要进行预热。
达到60~65℃,均质方法一般采用二段式,即第一段均质使用较高的压力(16.7~20.6MPa),目的是破碎脂肪球,第二段均质使用低压(3.4~4.9MPa),目的是分散已破碎的小脂肪球,防止粘连。
三、均质机特点:运转稳定、噪音小、清洗方便、机动灵活,可连续使用,对物料可进行超细分散、乳化。
可广泛适用于工业生产的乳化、均质和分散。
能使料液在挤研、强冲击与失压膨胀的三重作用下使料质细化混合。
本设备是食品.乳品.饮料等工业的重要设备。
对牛奶豆乳等各类乳品饮料,在高压下进行均质,能使乳品液中的脂肪球显著细化,使其制品食用后易于消化吸收,提高使用价值。
四、均质机工作流程:1、ﻩ开机前先打开冷却水。
2、ﻩ打开电源。
3、ﻩ加入物料,并给均质机缓慢加压。
红色手柄是粗调手柄,黑色手柄是细调手柄。
4、ﻩ生产结束后,先用黑色手柄慢慢卸压,之后再用红色手柄慢慢卸压,使其在无压状态。
5、关闭电源。
五、均质机使用注意事项:1、生产过程中严禁断冷凝水及无物料运作。
2、卸压时注意手柄顺序。
3、每次使用后,均质机应清洗干净。
时间温度要求:90℃,300s一、超高温管式瞬时灭菌机工作原理:一般物料由离心泵泵入灭菌机中冷热料热交换装置中而得到预热,再经过充满高压的高温桶,物料被迅速加热到杀菌温度并在此前后保持约3秒,其中的微生物及酶类很快被杀灭。
物料出高温桶后通过与冷料的热交换获得冷却,一般温度低于65℃。
如果下道工序需要提高温度则可通过调节角式截止阀或循环等途径达到要求,反之则通过接入冷却水来降低出料温度。
出料通过节流阀控制,此阀能使在维持一定压力下物料的沸点高于最高温度。
正常生产时调节此阀,由泵的推动力克服弹簧压力而产生背压控制流量,在清洗灭菌机时则应全部开启。
循环贮槽可用来配制酸碱溶液,对盘管内壁积垢进行有效清洗。
由于同时采用不锈钢三通旋塞,流量可以得到适当调节。
预热经巴氏杀菌后,产品通常能立即达到要求的加工温度,但往往在最终加工之前,牛乳需要冷却和暂时贮存,下面举例说明。
用于酸奶生产的牛乳在进入发酵罐之前预热至40-45℃,在罐中进行接种,热水作为加热介质。
牛乳也可以在加入其它成份前预热,如一些不同乳基产品所需的巧克力粉、糖、脂肪等。
管式热交换器在某些情况下,管式热交换器(THE)也用于乳制品的巴氏杀菌/超高温处理。
管式热交换器,如图6.1.17所示,不同于板式热交换器,它在产品通道上没有接触点,这样它就可以处理含有一定颗粒的产品。
颗粒的最大直径取决于管子的直径,在UHT处理中,管式热交换器要比板式热交换器运行的时间长。
从热传递的观点看,管式热交换器比板式热交换器的传热效率低。
管式热交换器现有两种截然不同的类型:多个/单个流道,多个/单个管道。
多个/单个流道多流道的管式热交换器的传热面,包含一系列不同直径的管子。
这些管子同心放置在顶盖两端的轴线上,管子通过2个O型密封在顶盖上,又通过一个轴线压紧螺栓将其安装成一个整体。
两种热交换介质以逆流的方式交替地流过同心管的环形通道。
最外侧的通道流过的是所提供的介质。
顶盖的两端既是分布器,又是收集器。
它将一种介质引入一组通道,又从另一端排出。
波纹状构造的管子保证了两种介质的紊流状态,以实现最大的传热效率。
可以使用这种类型的管式热交换器直接加热产品/进行产品热回收。
单一通道是指在两个同心通道之间密闭了一条环状的产品通道。
多个/单个管道多管道的管式热交换是基于传统的列管式热交换器的原理,其产品流过一组平行的通道,提供的介质围绕在管子的周围,通过管子和壳体上的螺旋波纹,产生紊流,实现有效的传热。
该交换器的传热面是一组平行的波纹管或是光滑管。
这些管子焊接在管板的两端,如图.1.19所示。
管板与出口的管壳通过一个双O型环密(2)(活动设计)。
这种设计可以通过旋开末端的螺栓,将产品管道从管壳中取出,这部分是可拆的,以便于检查。
活动头设计减缓了热膨胀的影响,而且还可将管壳中的产品管束进行不同的组合,以适应不同的应用场合。
单管是指只有一个进口管允许粒经小于50mm的颗粒物料通过。
多个/单个管子非常适用于高压、高温状况下的物料加工。
二、特点:1、连续生产,灭菌时间极短。
2、由于受热时间短可获得优质产品。
3、由于采用超高温灭菌,故灭菌效果特佳。
4、与离心泵或高压均质机串联使用,应用范围很广,适宜于高粘度物料的灭菌。
5、由于设计上采用有冷热料的热交换器具有废热利用的经济效果,故蒸汽消耗量小。
三、操作方法:1、操作前检查、准备:每次使用前,必须对灭菌机的状态进行全面检查,包括安全阀、疏水阀、压力表和温度表以及管道是否畅通等,同时需要在贮槽中贮满清水,并将进料管道接好。
2、循环调温:开启贮槽上端的清水阀,启动进料泵,使清水在灭菌机中开始循环,再缓慢打开蒸汽使灭菌温度达到工艺要求,同时通过冷却水的大小调节出料温度。
3、排水进料:当达到预定要求后,关闭清水阀,将旋转弯管转至溢流管上,将清水排出,待贮槽中的清水放尽时,迅速打开进料三通旋塞进料;4、灭菌:当旋转弯管开始排出物料时,即转动弯管使物料流入贮槽中,同时打开出料三通旋塞排料,注意保持杀菌中的温度等。