高炉炼铁对原燃料质量的要求和影响
浅议焦炭质量对高炉炼铁的影响

浅议焦炭质量对高炉炼铁的影响【摘要】焦炭作为高炉炼铁过程中不可或缺的原料,在其中扮演着至关重要的角色。
本文通过探讨焦炭质量对高炉炼铁的影响,揭示了焦炭质量与高炉工艺参数、高炉温度、炉渣特性、炼铁效率以及产品质量之间的密切关系。
优质的焦炭不仅能提高高炉的炼铁效率,还能改善产品质量,降低生产成本。
提高焦炭质量对于改善高炉炼铁过程、提高产品质量具有重要的意义。
在实际生产中,需要针对具体情况优化焦炭的生产工艺,确保焦炭的品质符合高炉炼铁的要求。
焦炭质量的重要性不可忽视,只有不断提高焦炭的质量,才能有效提高高炉炼铁的效率和产品质量。
【关键词】焦炭、高炉、炼铁、质量、影响、效率、温度、炉渣、工艺参数、产品质量、炼铁质量、优化、生产工艺、高炉炼铁、煤焦炭。
1. 引言1.1 煤焦炭在高炉炼铁中的作用煤焦炭作为高炉炼铁的主要还原剂和燃料,在高炉冶炼过程中扮演着至关重要的角色。
煤焦炭可以提供充足的热量,将铁矿石还原为金属铁,并在炉内维持所需的高温。
煤焦炭中的固定碳和挥发分不仅能够作为还原剂参与还原反应,还能提供充足的燃料,确保高炉冶炼过程的持续进行。
煤焦炭中的灰分、硫分等杂质也会对炼铁过程产生一定影响,因此对煤焦炭的质量要求较高。
煤焦炭在高炉炼铁中扮演着多重作用,其质量直接影响到高炉的冶炼效率和产品质量。
对煤焦炭的质量控制和优化具有十分重要的意义,可以提高高炉的生产效率,减少能源消耗,改善产品质量。
1.2 焦炭质量对高炉炼铁的重要性焦炭质量对高炉炼铁的重要性不容忽视。
在高炉炼铁过程中,焦炭是一种重要的还原剂和燃料,其质量直接影响着炼铁的效率和产品质量。
优质的焦炭可以提高高炉的热效率,减少炉料消耗,降低能耗。
焦炭质量的好坏还会影响高炉的工艺参数,如温度、压力等,进而影响炼铁过程的稳定性和控制性。
提高焦炭质量是提高高炉炼铁效率和产品质量的重要手段。
只有不断优化焦炭的生产工艺,确保焦炭的质量稳定和优良,才能更好地发挥焦炭在高炉炼铁中的作用,提高炼铁的经济效益和产品质量。
高炉日常操作技术

高炉炼铁日常操作技术高炉操作者的任务是要保持合理炉型,实现炼铁生产的“高效、优质、低耗、长寿、环保”。
稳定顺行是组织炼铁生产的灵魂。
原燃料准备、烧结、球团、焦化、动力等工序均是要做好为炼铁服务。
在生产组织上,应统一服从炼铁领导。
这样,可以追求炼铁效益的最大化,不追求某个指标的先进性,要实现综合效益的最佳化。
即实现高效化生产、生产成本低、节能减排效果好、劳动效率高等。
高炉要实现统一操作,发扬团结协作精神,实现整体高炉的最佳化生产,不表扬某个工长的个人英雄主义,要提倡整个高炉操作协调统一,保证生产的稳定顺行。
进行红旗高炉的竞赛活动,推进企业炼铁科学技术进步,生产建设的发展。
1, 高炉炼铁是以精料为基础高炉炼铁应当认真贯彻精料方针,这是高炉炼铁的基础.,精料技术水平对高炉炼铁技术指标的影响率在70%,高炉操作为10%,企业现代化管理为10%,设备运行状态为5%,外界因素(动力,原燃料供应,上下工序生产状态等)为5%.。
高炉炼铁生产条件水平决定了生产指标好坏。
高炉工长的操作结果也要由高炉炼铁生产条件水平和工长的操作技能水平来决定。
用科学发展观来认知高炉炼铁的生产规律,要承认高炉炼铁是个有条件生产的工序.。
高炉工长要讲求生产条件,但不唯条件,重在加强企业现代化管理。
生产技术和企业现代化管理是企业行走的两个轮子,要重视两个轮子行走的同步,否则会出现来回摇摆或原地转圈。
精料方针的内容:·高,入炉料含铁品位要高(这是精料技术的核心),入炉矿含铁品位提高1%,炼铁燃料比降低1.5%,产量提高2.5%,渣量减少30kg/t,允许多喷煤15 kg/t。
原燃料转鼓强度要高。
<高炉炼铁工艺设计规范>要求,烧结矿转鼓强度≥71%~78%.焦炭转鼓强度M40≥78%~86%.大高炉对原燃料的质量要求是高于中小高炉。
如宝钢要求焦炭M40为大于88%,M10为小于6.5%,CRI小于26%,CSR大于66%。
高炉炼铁原料、燃料与质量检验

高炉炼铁原料、燃料与质量检验1. 概述高炉是炼铁的主要设备之一,它利用炼铁矿石和燃料进行高温反应,将矿石中的金属元素还原为铁,从而生产出铁水。
高炉炼铁的关键在于原料和燃料的选择与质量检验。
本文将介绍高炉炼铁的原料和燃料,以及对其质量进行检验的方法。
2. 高炉炼铁原料高炉的炼铁原料主要包括铁矿石和熔剂。
铁矿石是指含有铁的矿石矿石,常见的铁矿石有磁铁矿、赤铁矿和褐铁矿等。
熔剂是指在高炉中与铁矿石反应生成熔融物的物质,常用的熔剂有焦炭、石灰石和白云石等。
选择合适的原料是确保高炉正常运行和产生高质量铁水的关键。
2.1 铁矿石铁矿石是高炉炼铁的主要原料之一,其主要成分是金属铁和含铁矿物。
铁矿石的品质直接影响到高炉炼铁的效率和产品质量。
常用的铁矿石有磁铁矿、赤铁矿和褐铁矿。
铁矿石的选择应根据矿石的含铁量、熔点、熔化特性和矿石的硫、磷含量等因素进行。
2.2 熔剂熔剂是在高炉中与铁矿石反应生成熔融物的物质。
常用的熔剂有焦炭、石灰石和白云石等。
焦炭是一种含炭量高的固体燃料,其主要功能是提供炉料中的还原剂和燃料。
石灰石和白云石是主要的熔剂,其主要功能是将炉料中的硅、硫等杂质与炉渣反应生成易于分离的化合物。
3. 燃料燃料在高炉炼铁中主要用于提供热量,使高炉内的反应达到所需温度。
常用的燃料有焦炭、煤粉和天然气等。
焦炭是高炉炼铁中最常用的燃料,其具有高热值和较低的灰分和硫含量。
煤粉是一种常用的燃料,其选择应根据灰分、硫含量等指标来确定。
天然气作为清洁能源,其在高炉炼铁中的应用也逐渐增多。
4. 质量检验对高炉炼铁原料和燃料进行质量检验是保证高炉正常运行和铁水质量的关键。
常用的检验方法有化学分析和物理性能检测等。
4.1 化学分析化学分析是对铁矿石、熔剂和燃料中各种成分的含量进行检测的方法,常见的化学分析方法有样品溶解、滴定法、光谱法和电化学分析等。
通过化学分析可以了解原料和燃料中的铁、硫、磷等元素的含量,以及矿石的熔化特性等。
浅谈高炉炼铁原燃料质量改善对策
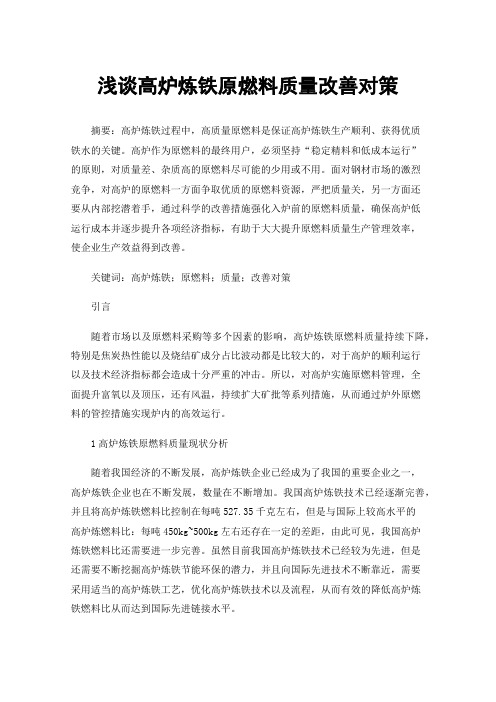
浅谈高炉炼铁原燃料质量改善对策摘要:高炉炼铁过程中,高质量原燃料是保证高炉炼铁生产顺利、获得优质铁水的关键。
高炉作为原燃料的最终用户,必须坚持“稳定精料和低成本运行”的原则,对质量差、杂质高的原燃料尽可能的少用或不用。
面对钢材市场的激烈竞争,对高炉的原燃料一方面争取优质的原燃料资源,严把质量关,另一方面还要从内部挖潜着手,通过科学的改善措施强化入炉前的原燃料质量,确保高炉低运行成本并逐步提升各项经济指标,有助于大大提升原燃料质量生产管理效率,使企业生产效益得到改善。
关键词:高炉炼铁;原燃料;质量;改善对策引言随着市场以及原燃料采购等多个因素的影响,高炉炼铁原燃料质量持续下降,特别是焦炭热性能以及烧结矿成分占比波动都是比较大的,对于高炉的顺利运行以及技术经济指标都会造成十分严重的冲击。
所以,对高炉实施原燃料管理,全面提升富氧以及顶压,还有风温,持续扩大矿批等系列措施,从而通过炉外原燃料的管控措施实现炉内的高效运行。
1高炉炼铁原燃料质量现状分析随着我国经济的不断发展,高炉炼铁企业已经成为了我国的重要企业之一,高炉炼铁企业也在不断发展,数量在不断增加。
我国高炉炼铁技术已经逐渐完善,并且将高炉炼铁燃料比控制在每吨527.35千克左右,但是与国际上较高水平的高炉炼燃料比:每吨450kg~500kg左右还存在一定的差距,由此可见,我国高炉炼铁燃料比还需要进一步完善。
虽然目前我国高炉炼铁技术已经较为先进,但是还需要不断挖掘高炉炼铁节能环保的潜力,并且向国际先进技术不断靠近,需要采用适当的高炉炼铁工艺,优化高炉炼铁技术以及流程,从而有效的降低高炉炼铁燃料比从而达到国际先进链接水平。
影响高炉炼铁的因素主要有两方面:原燃料质量水平对高炉炼铁生产的影响率在70%左右;操作水平、设备、管理、外界因素等占30%。
所以原、燃料的质量水平直接决定着铁水的质量与成本。
这就要求必须深刻认识到对炼铁原、燃料的共识—“精料方针”的重要性,并制定出有利于高炉冶炼的炉料质量指标。
主要高炉炼铁原料分析

高炉炼铁原料1.铁矿石和燃料高炉炼铁必备的三种原料中,焦炭作为燃料和还原剂,是主要能源;熔剂,如石灰石,主要用来助熔、造渣;铁矿石则是冶炼的对象。
这些原料是高炉冶炼的物质基础,其质量对冶炼过程及冶炼效果影响极大。
铁矿石铁矿石分类及特性高炉冶炼用的铁矿石有天然富矿和人造富矿两大类,含铁量在50%以上的天然富矿经适当破碎、筛分处理后可直接用于高炉冶炼。
贫铁矿一般不能直接入炉,需要破碎、富矿并重新造块,制成人造富矿(烧结矿或球团矿)再入高炉。
人造富矿含铁量一般在55%~65%之间。
由于人造富矿事先经过焙烧或者烧结高温处理,因此又称为熟料,其冶炼性能远比天然富矿优越,是现代高炉冶炼的主要原料。
天然块矿统称成为生料。
我国富矿储量很少,多数是含Fe30%左右的贫矿,需要经过富矿才能使用。
A. 矿石和脉石能从中经济合理的提炼出金属来的矿物成为矿石。
如铁元素广泛地、程度不同地分布在地壳的岩石和土壤中,有的比较集中,形成天然的富铁矿,可以直接利用来炼铁;有的比较分散,形成贫铁矿,用于冶炼及困难又不经济。
随着选矿和冶炼技术的发展,矿石的来源和范围不断扩大。
含铁较低的贫矿经过富选也可用于炼铁。
矿石中除了用来提炼金属的有用矿物外,还含有一些工业上没有提炼价值的矿物或岩石,称为脉石。
对冶炼不利的脉石矿物,应在选矿和其他处理过程中尽量去除。
但矿石中脉石的结构和分布直接影响矿石的选冶性能。
如果含铁矿物结晶颗粒比较粗大,则在选矿过程中易于实现有用矿物的单体分离;反之,如果含铁矿物呈颗粒结晶嵌布在脉石中,则要进一步细磨矿石才能分离出有用单体。
B.天然矿石的分类及特性天然铁矿石按其主要矿物分为磁铁矿、赤铁矿、褐铁矿和菱铁矿等几种,主要矿物组成及特征见下表。
常见铁矿石的组成及特征名称主要成分理论含铁实际富矿含铁颜色特性磁铁矿Fe3O4 72.40% 45-70% 黑P、S高,坚硬,致密,难还原赤铁矿Fe2O3 70.00% 55-60% 红P、S低,质软,易碎,易还原褐铁矿nFe2O3+mH2O 55.2~66.1% 37-55% 黄褐P高,质软疏松,易还原菱铁矿FeCO3 48.20% 30-40% 灰浅黄易破碎,焙烧后易还原磁铁矿,主要含铁矿物为Fe3O4,具有磁性。
高炉炼铁对炉料质量的要求及优化配矿技术
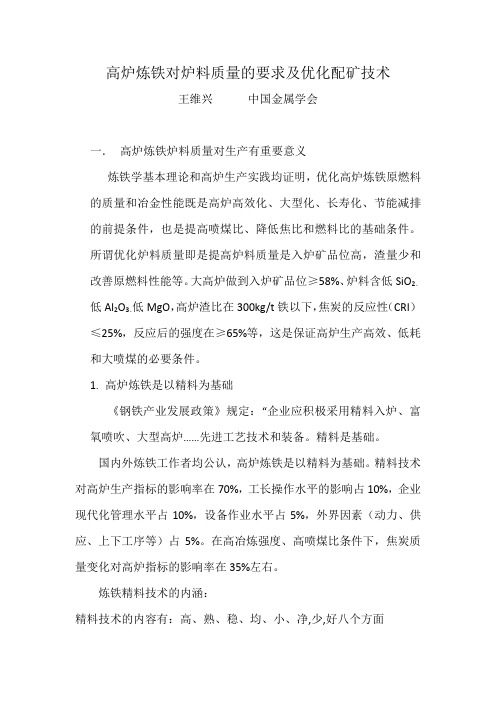
高炉炼铁对炉料质量的要求及优化配矿技术王维兴中国金属学会一.高炉炼铁炉料质量对生产有重要意义炼铁学基本理论和高炉生产实践均证明,优化高炉炼铁原燃料的质量和冶金性能既是高炉高效化、大型化、长寿化、节能减排的前提条件,也是提高喷煤比、降低焦比和燃料比的基础条件。
所谓优化炉料质量即是提高炉料质量是入炉矿品位高,渣量少和改善原燃料性能等。
大高炉做到入炉矿品位≥58%、炉料含低SiO2、低Al2O3、低MgO,高炉渣比在300kg/t铁以下,焦炭的反应性(CRI)≤25%,反应后的强度在≥65%等,这是保证高炉生产高效、低耗和大喷煤的必要条件。
1.高炉炼铁是以精料为基础《钢铁产业发展政策》规定:“企业应积极采用精料入炉、富氧喷吹、大型高炉……先进工艺技术和装备。
精料是基础。
国内外炼铁工作者均公认,高炉炼铁是以精料为基础。
精料技术对高炉生产指标的影响率在70%,工长操作水平的影响占10%,企业现代化管理水平占10%,设备作业水平占5%,外界因素(动力、供应、上下工序等)占5%。
在高冶炼强度、高喷煤比条件下,焦炭质量变化对高炉指标的影响率在35%左右。
炼铁精料技术的内涵:精料技术的内容有:高、熟、稳、均、小、净,少,好八个方面⑴高:入炉矿含铁品位高,原燃料转鼓指数高,烧结矿碱度高。
入炉矿品位高是精料技术的核心,其作用:矿品位在57%条件下,品位升高1%,焦比降%~%,产量增加%~%,吨铁渣量减少30公斤,允许多喷煤粉15公斤.;入炉铁品位在52%左右时,品位下降1%,燃料比升高%~%。
高碱度烧结矿是碱度在~2,2(倍),其转鼓强度高、还原性好。
⑵熟:指熟料(烧结和球团矿)比要高,一般>80%。
⑶稳:入炉的原燃料质量和供应数量要稳定。
要求炉料含铁品位波动±<%,碱度波动±<(倍),FeO含量波动±≤%,合格率大于80%~98%等。
详见表4和表5。
⑷均:入炉的原燃料粒度要均匀。
炼铁高炉总结报告

炼铁高炉总结报告炼铁高炉总结报告自从高炉在19世纪初期被引进以来,对于钢铁行业的发展起到了关键性的作用。
通过将铁矿石还原为铁,高炉为钢铁制造过程提供了重要的原料。
在过去的几十年中,随着技术的不断进步和创新,炼铁高炉已经变得越来越高效、环保和可持续。
首先,高炉技术的进步使炼铁过程更加高效。
传统的高炉通常采用休风制度,即周期性关闭高炉进行铸铁和铁渣的取出。
这种模式通常导致生产周期长、能源消耗多。
然而,现代高炉采用连续供料的方式,可以显著提高生产效率。
连续供料可以减少生产停顿时间,最大程度地提高铁矿石的还原效率。
此外,现代高炉还引入了先进的热处理技术,通过对高炉内部温度和气体流动的精确控制,可有效提高产量和质量。
其次,高炉技术的创新使生产过程更加环保。
以往,高炉烟气中含有大量有害气体,如二氧化硫和氮氧化物等。
然而,现代高炉通常配备了先进的烟气处理设备,例如脱硫和脱硝装置,能够有效降低排放物的含量。
此外,高炉的燃烧系统也不断改进,以提高燃烧效率和降低燃料的消耗。
这些创新可以显著减少对环境的负面影响,并使高炉生产更加可持续。
最后,高炉技术的发展也带来了更高的安全性。
高炉在操作过程中面临各种潜在的危险,如爆炸和火灾等。
为了降低这些风险,现代高炉引入了先进的监测和控制技术。
通过在高炉内安装传感器和控制系统,工作人员可以实时监测和控制高炉的运行情况,从而降低事故的发生几率。
此外,高炉还采取了严格的安全措施和培训,确保工作人员安全操作。
然而,尽管高炉技术有着众多的优势和创新,但仍存在一些挑战。
首先,高炉生产过程对能源的需求量大,特别是对煤炭等化石燃料的依赖。
这不仅导致能源消耗过大,还会产生大量温室气体的排放,对气候变化和环境造成负面影响。
其次,高炉废气中的有害物质,如颗粒物、重金属等,需要通过先进的处理技术进行净化,以防止对环境和人体健康的损害。
总而言之,炼铁高炉技术的进步和创新为钢铁制造行业提供了巨大的机遇。
高炉的高效、环保和安全特性使其成为钢铁行业不可或缺的生产工具。
高炉炼铁过程中的能源消耗与管理

高炉炼铁过程中的能源消耗与管理一、前言与背景高炉炼铁作为现代钢铁工业的基础,自19世纪末以来,一直是铁钢生产的主要方法。
高炉炼铁技术的出现和发展,对社会、经济和科技产生了深远影响。
它使得钢铁生产实现了规模化、低成本,极大地促进了工业革命和现代工业社会的形成。
同时,高炉炼铁过程也伴随着能源的消耗,据统计,能源消耗占到了高炉炼铁成本的很大一部分。
因此,研究和分析高炉炼铁过程中的能源消耗和管理,对于提高我国钢铁工业的能源利用效率,降低生产成本,提升竞争力具有重要意义。
二、高炉炼铁行业/领域的核心概念与分类高炉炼铁的概念高炉炼铁是一种利用焦炭和氧气反应产生的高温,将铁矿石还原成铁的过程。
其基本原理是在高温下,铁矿石中的氧化铁与一氧化碳反应,生成铁和二氧化碳。
高炉炼铁过程中,能源主要用于提供热能和动力能,其中热能主要用于维持高炉内的温度,动力能主要用于推动炉内物质的流动和完成各项机械作业。
高炉炼铁的分类高炉炼铁可以根据炉型、操作方式、燃料种类等不同标准进行分类。
按炉型可分为小型高炉、中型高炉和大型高炉;按操作方式可分为连续操作高炉和间歇操作高炉;按燃料种类可分为焦炭高炉和煤气高炉。
高炉炼铁的特征与应用领域高炉炼铁具有生产规模大、原料利用率高、产品品质好、能耗高等特征。
其应用领域广泛,几乎涵盖了所有钢铁生产领域。
高炉炼铁与其他领域的交叉与融合随着科技的发展,高炉炼铁技术与自动化、信息化、环保等领域日益交叉与融合。
例如,高炉炼铁过程的自动化控制,使得生产过程更加稳定,效率更高;信息化技术的应用,使得高炉炼铁过程的监测和控制更加精细;环保技术的应用,则有助于降低高炉炼铁过程中的污染排放。
三、关键技术或性能原理剖析高炉炼铁的关键技术高炉炼铁的关键技术主要包括燃料燃烧技术、还原反应技术、热量交换技术、原料处理技术等。
其中,燃料燃烧技术是高炉炼铁过程中能源消耗的主要部分,其效率的高低直接影响到高炉炼铁的能耗。
高炉炼铁的最新技术突破与创新成果近年来,高炉炼铁技术取得了许多重要突破和创新成果,如低焦比炼铁技术、高风温技术、煤气净化技术等。
高炉炼铁简述

(2)规模越来越大型化。 现在已有5000m3以上容积的高炉,日 产生铁万吨以上,日耗矿石近2万t,焦炭等 燃料5kt。 (3)机械化、自动化程度越来越高。 为了准确连续地完成每日成千上万吨原 料及产品的装入和排放,为了改善劳动条 件、保证安全、提高劳动生产率,要求有 较高的机械化和自动化水平。
品位即铁矿石的含铁量,它决定着矿石的 开采价值和入炉前的处理工艺。入炉品位 愈高,愈有利于降低焦比和提高产量,从 而提高经济效益。经验表明,若矿石含铁 量提高1%,则焦比降低2%,产量增加3%。
铁矿石分类及特性
矿石的贫富一般以其理论含铁量的 70% 来 评估。实际含铁量超过理论含铁量的 70% 称富矿。 但这并不是绝对固定的标准。因为它还与 矿石的脉石成分、杂质含量和矿石类型等 因素有关。如对褐铁矿、菱铁矿和碱性脉 石矿含铁量的要求可适当放宽。因褐、菱 铁矿受热分解出H2O和CO2后品位会提高。 碱性脉石矿含 CaO 高,冶炼时可少加或不 加石灰石,其品位应按扣去 CaO 的含铁量 来评价。
1.3 高炼铁原料和燃料
高炉炼铁原料
原料是高炉冶炼的物质基础,其质量 对冶炼过程及冶炼效果影响极大。目 前,炼铁的发展趋势之一就是采用精 料。
铁矿石分类及特性
一、矿石和脉石
矿石是矿物的集合体。但是,在当前科学技术条件 下,能从中经济合理地提炼出金属来的矿物才称为 矿石。矿石的概念是相对的。例如铁元素广泛地、 程度不同地分布在地壳的岩石和土壤中,有的比较 集中,形成天然的富铁矿,可以直接利用来炼铁, 堪称矿石;有的比较分散,形成贫铁矿,用于冶炼 既困难又不经济。
(4)生产的联合性。 从高炉炼铁本身来说,从上料到排放渣 铁,从送风到煤气回收,各系统必须有机 地协调联合工作。从钢铁联合企业中炼铁 工序的地位来说,炼铁工序也是非常重要 的一环,高炉休风或减产会给整个联合企 业的生产带来严重影响。因此,高炉工作 者要努力防止各种事故,保证联合生产的 顺利进行。
炼铁毕业论文
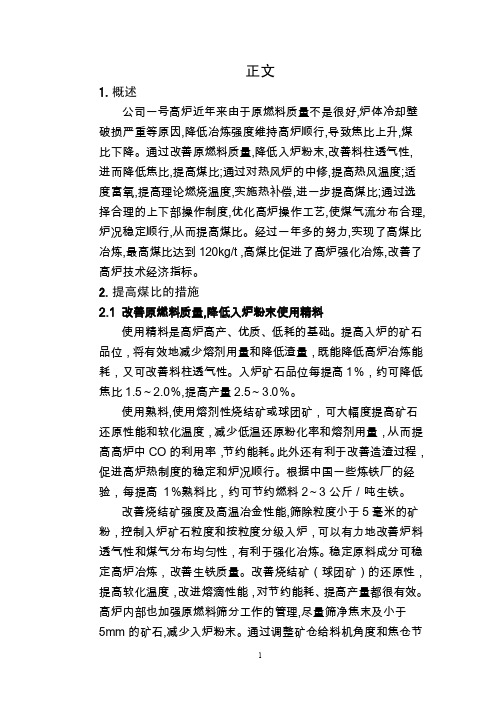
正文1.概述公司一号高炉近年来由于原燃料质量不是很好,炉体冷却壁破损严重等原因,降低冶炼强度维持高炉顺行,导致焦比上升,煤比下降。
通过改善原燃料质量,降低入炉粉末,改善料柱透气性,进而降低焦比,提高煤比;通过对热风炉的中修,提高热风温度;适度富氧,提高理论燃烧温度,实施热补偿,进一步提高煤比;通过选择合理的上下部操作制度,优化高炉操作工艺,使煤气流分布合理,炉况稳定顺行,从而提高煤比。
经过一年多的努力,实现了高煤比冶炼,最高煤比达到120kg/t ,高煤比促进了高炉强化冶炼,改善了高炉技术经济指标。
2.提高煤比的措施2.1 改善原燃料质量,降低入炉粉末使用精料使用精料是高炉高产、优质、低耗的基础。
提高入炉的矿石品位,将有效地减少熔剂用量和降低渣量,既能降低高炉冶炼能耗,又可改善料柱透气性。
入炉矿石品位每提高1%,约可降低焦比1.5~2.0%,提高产量2.5~3.0%。
使用熟料,使用熔剂性烧结矿或球团矿,可大幅度提高矿石还原性能和软化温度,减少低温还原粉化率和熔剂用量,从而提高高炉中CO的利用率,节约能耗。
此外还有利于改善造渣过程,促进高炉热制度的稳定和炉况顺行。
根据中国一些炼铁厂的经验,每提高1%熟料比,约可节约燃料2~3公斤/吨生铁。
改善烧结矿强度及高温冶金性能,筛除粒度小于5毫米的矿粉,控制入炉矿石粒度和按粒度分级入炉,可以有力地改善炉料透气性和煤气分布均匀性,有利于强化冶炼。
稳定原料成分可稳定高炉冶炼,改善生铁质量。
改善烧结矿(球团矿)的还原性,提高软化温度,改进熔滴性能,对节约能耗、提高产量都很有效。
高炉内部也加强原燃料筛分工作的管理,尽量筛净焦末及小于5mm的矿石,减少入炉粉末。
通过调整矿仓给料机角度和焦仓节流闸开度,减小矿筛和焦筛上矿层及焦层厚度,延长筛分时间,减少入炉粉末,改善了料柱透气性,为进一步提高煤比创造有利条件。
提高焦炭质量,降低焦炭灰分,每降低1%,可降低焦比1.5~2.0%,提高产量2.5~3.0%。
天钢2000m3高炉原燃料条件劣化的应对

怎样调 整高炉操 作 , 应原燃料 条件 的改变 , 证高 适 保 炉顺行 ,在优质操作指标 与成本 之间找到平衡点 , 是
当前优化操作的主要课题 。 2 原燃料条件变化情况及对高炉产生的影响
21 烧 结矿 质 量 变化 .
原燃料条件劣化造成 高炉透气性降低 , 压差 控制 由 2 1 的小于 1 5k a 00年 5 P ,升 高到 2 1 年 小于 15 01 6
(钢 铁 冶 炼 )
一 9 1—
天律 素 " 4 -
炉渣有 良好 的流动性 , 因此 20 0m3 0 高炉控制炉渣 中 先 改善炮泥质 量 , 同时采取混 配 的方式 , 不但 改善 了 铁 口通 道状态 , 同时使炮泥 消耗降低 到 0 6k/ . g 。其 4 t 次根据 鞍钢专 家建议 ,适当降低铁 口深度 ,由 30 0 0
3 调 整 炉料 结 构 。 少生 矿 配 比 . 2 减
在“ 保证 中心 , 当控 制边 缘 ” 适 的指导 思想下 , 适 当加长风 口, 0 高炉共 2 20 0m3 8个风 口,00年 为 4 21
个 50mm, 以少量 4 0m 大 部为 4 0m 2 1 0 配 7 m, 5 m,0 1
层厚度保持不低 于 4 0I 6 l T m。 33 调整布料矩 阵 .. 2 原 料冶 金性能变 差 时 , 软熔 区间变宽 , 高炉 透气
点, 是高炉 的主要任务 。
31 加 强槽 下管理 , . 减少入 炉粉末
性变 差 , 不易 吹透 中心 , 边缘气流加强 , 使 造成边缘软
1 引言
原燃料
操作
技术
高强度
冶炼 影响 。图 1 20 0m, 为 0 高炉入炉 品位变化趋势 。
降低高炉炼铁燃料比的技术措施
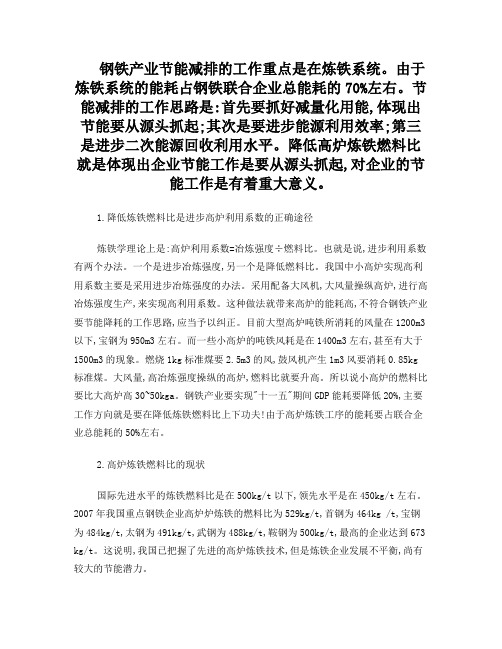
钢铁产业节能减排的工作重点是在炼铁系统。
由于炼铁系统的能耗占钢铁联合企业总能耗的70%左右。
节能减排的工作思路是:首先要抓好减量化用能,体现出节能要从源头抓起;其次是要进步能源利用效率;第三是进步二次能源回收利用水平。
降低高炉炼铁燃料比就是体现出企业节能工作是要从源头抓起,对企业的节能工作是有着重大意义。
1.降低炼铁燃料比是进步高炉利用系数的正确途径炼铁学理论上是:高炉利用系数=冶炼强度÷燃料比。
也就是说,进步利用系数有两个办法。
一个是进步冶炼强度,另一个是降低燃料比。
我国中小高炉实现高利用系数主要是采用进步冶炼强度的办法。
采用配备大风机,大风量操纵高炉,进行高冶炼强度生产,来实现高利用系数。
这种做法就带来高炉的能耗高,不符合钢铁产业要节能降耗的工作思路,应当予以纠正。
目前大型高炉吨铁所消耗的风量在1200m3以下,宝钢为950m3左右。
而一些小高炉的吨铁风耗是在1400m3左右,甚至有大于1500m3的现象。
燃烧1kg标准煤要2.5m3的风,鼓风机产生1m3风要消耗0.85kg标准煤。
大风量,高冶炼强度操纵的高炉,燃料比就要升高。
所以说小高炉的燃料比要比大高炉高30~50kga。
钢铁产业要实现"十一五"期间GDP能耗要降低20%,主要工作方向就是要在降低炼铁燃料比上下功夫!由于高炉炼铁工序的能耗要占联合企业总能耗的50%左右。
2.高炉炼铁燃料比的现状国际先进水平的炼铁燃料比是在500kg/t以下,领先水平是在450kg/t左右。
2007年我国重点钢铁企业高炉炉炼铁的燃料比为529kg/t,首钢为464kg /t,宝钢为484kg/t,太钢为491kg/t,武钢为488kg/t,鞍钢为500kg/t,最高的企业达到673 kg/t。
这说明,我国已把握了先进的高炉炼铁技术,但是炼铁企业发展不平衡,尚有较大的节能潜力。
高炉炼铁的燃料比是:进炉焦比+喷煤比+小块焦比。
喷煤比是不计算量换比。
强化原燃料质量控制 促进高炉生产

术经济指标明显下滑。面对不利 因素的影响 ,首
钢通过强化原燃料质量管理 ,落实精料措施 ,首
业使用的焦炭质量 、入炉焦比情况见表 பைடு நூலகம்。
由表 1 可见 ,入炉焦 比低 于 30 k/ 的企 7 gt 业 ( 如宝 钢 、马 钢 和太 钢 ) 的焦 炭 灰 分均 在 1. % 以下 ,质量属于准 I 25 级焦 以上水平。 首钢 自 产焦炭产量 只能满 足高炉生产 5 % 0
S R NGT EN G T E H D QUA I Y C T OL OF T l A AT R L N L T ON R IE R W M- E S A D
FUEL FOR ROM OTI P NG F P B RODUCTI ON
HUANG Do g u L eg a g C nhi IW i u n HEN F q a G u u n
维普资讯
强化 原 燃 料 质 量 控 制 促 进 高 炉 生产
黄东辉 李伟广 成富全
(技 术 研 究 院 )
摘 要 介绍了首钢通过强化高炉原燃料质量控制,稳定提高高炉原燃料质量,促进炼铁厂高炉焦比降低
的情况 。 关键词 原燃料 质量管理 高 炉 生产
表 4 0 4— 2 0 2 0 0 5年首钢 烧结矿质量情 况
注 i( )首钢 的数 据 为 20 1 05年数 据 ,其余 企业 的数据 为
20 0 4年上半年数据 ; ( )首钢 A为外购焦炭 。 2 首钢 B为 白产焦炭 ; ( )‰ 为焦炭抗碎强度 , 0 3 为焦炭耐磨强度 。
影响,首钢炼铁厂 的炼铁 原燃料质量有所下降,
1 首钢炼铁厂原燃 料质量变化情况
论高炉炼铁节能降耗及资源合理利用技术高永

论高炉炼铁节能降耗及资源合理利用技术高永发布时间:2021-10-24T08:28:54.827Z 来源:《基层建设》2021年第20期作者:高永[导读] 摘要:随着社会的日益发展对于各行各业都提出了更高的要求,也带来了更多的挑战。
承德建龙特殊钢有限公司河北承德 067200摘要:随着社会的日益发展对于各行各业都提出了更高的要求,也带来了更多的挑战。
钢铁企业面临不断缩小的利润空间,其发展形势较为严峻。
要想在激烈的竞争之中站稳脚跟,相应企业应当在进行高炉炼铁时采取合理的节能降耗措施,并对原有的高炉炼铁技术进行优化,这样才能够有效拓宽自身的发展空间。
本文就高炉炼铁节能降耗及资源合理利用相关技术的实际操作和优化策略展开了讨论,以期为钢铁行业的发展提供一些帮助。
关键词:高炉炼铁;节能降耗;资源合理利用一、铁焦技术铁焦技术最早出现于日本,发展至今其在实际应用中发挥了一定的作用,但与此同时此项技术发展在目前并未十分成熟。
此项技术主要是使用微黏结霉或非黏结煤等价格更低的结煤作为原料,再生产煤矿资源,并且这些结煤还可以与铁矿粉按照一定的比例混合,在其成为块状后进行干馏处理,从而能够得到三七成比例的铁焦。
最后还需要对其进行二次处理,然后才能得到较好的炼铁效果。
据相关研究和实践表明,此项技术能够使主焦煤和焦的使用量大幅减少,同时也说明了铁焦对于高炉炼铁过程中的反应速率的提高有着十分重要的作用,另外,这也说明了在高炉炼铁中铁焦含量即使达到百分之三十也不会对高炉炼铁质量产生较大的影响[1]。
二、高炉喷吹炼铁技术的具体操作方式(一)高炉喷吹生物质和木炭技术生物质可以算得上是高炉炼铁领域内的一种新型能源,属于有机物的一种。
而对于这种有机物,主要应用于热解行为。
其中,可在碳化温度下,不断减少二氧化碳的排放量。
相关学者在研究中发现,生物质与废塑料多应用于高炉炼铁多个工艺环节中,在这些环节中,企业并不需要使用过多的是人力、物力和财力。
高炉炼铁原料1
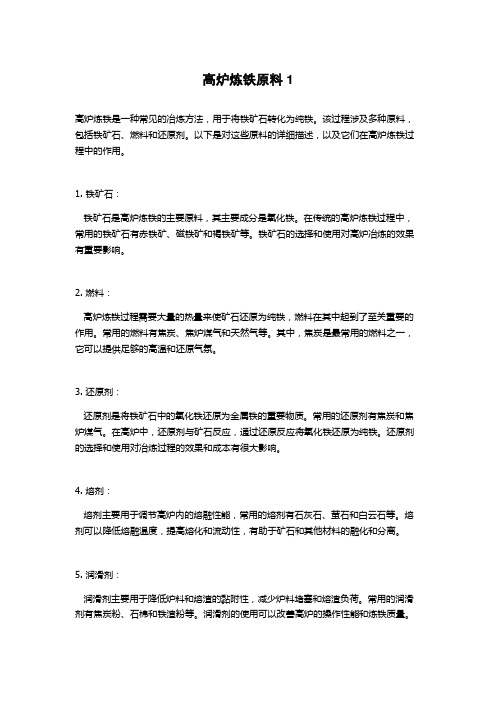
高炉炼铁原料1高炉炼铁是一种常见的冶炼方法,用于将铁矿石转化为纯铁。
该过程涉及多种原料,包括铁矿石、燃料和还原剂。
以下是对这些原料的详细描述,以及它们在高炉炼铁过程中的作用。
1. 铁矿石:铁矿石是高炉炼铁的主要原料,其主要成分是氧化铁。
在传统的高炉炼铁过程中,常用的铁矿石有赤铁矿、磁铁矿和褐铁矿等。
铁矿石的选择和使用对高炉冶炼的效果有重要影响。
2. 燃料:高炉炼铁过程需要大量的热量来使矿石还原为纯铁,燃料在其中起到了至关重要的作用。
常用的燃料有焦炭、焦炉煤气和天然气等。
其中,焦炭是最常用的燃料之一,它可以提供足够的高温和还原气氛。
3. 还原剂:还原剂是将铁矿石中的氧化铁还原为金属铁的重要物质。
常用的还原剂有焦炭和焦炉煤气。
在高炉中,还原剂与矿石反应,通过还原反应将氧化铁还原为纯铁。
还原剂的选择和使用对冶炼过程的效果和成本有很大影响。
4. 熔剂:熔剂主要用于调节高炉内的熔融性能,常用的熔剂有石灰石、萤石和白云石等。
熔剂可以降低熔融温度,提高熔化和流动性,有助于矿石和其他材料的融化和分离。
5. 润滑剂:润滑剂主要用于降低炉料和熔渣的黏附性,减少炉料堵塞和熔渣负荷。
常用的润滑剂有焦炭粉、石棉和铁渣粉等。
润滑剂的使用可以改善高炉的操作性能和炼铁质量。
除了以上描述的主要原料外,高炉炼铁过程中还需要添加一些辅助原料和助剂,如矿石细粉、石灰石粉和石英砂等。
这些原料和助剂主要用于调节和改善炉内反应条件和熔渣特性,以提高炼铁的效率和质量。
综上所述,高炉炼铁涉及多种原料,其中铁矿石、燃料、还原剂、熔剂和润滑剂等是最主要的原料。
这些原料在炼铁过程中起到不同的作用,包括提供还原物质、产生热量、调节熔融性能、降低黏附性等。
通过合理选择和使用这些原料,可以提高高炉的冶炼效率和炼铁质量。
高炉炼铁原料和燃料及质量检验

⑥矿石的高温性能。矿石是在炉内逐渐受热、升 温的过程中被还原的。矿石在受热及被还原的过 程中及还原后都不应因强度下降而破碎,以免矿 粉堵塞煤气流通孔道而造成冶炼过程的障碍。为 了在熔化造渣之前,矿石更多地被煤气所还原, 矿石的软化熔融温度不可过低,软化与熔融的温 度区间不可过宽。这样一方面可保证炉内有良好 的透气性,另一方面可使矿石在软熔前达到较高 的还原度,以减少高温直接还原度,降低能源消 耗。块矿的软熔性能与酸性球团相近,但软熔温 度均低于烧结矿。
⑤小
原燃料的粒度要偏小,球团矿8~16mm,烧结矿 5~50mm,焦炭30~75mm,块矿5~15mm。中 小高炉使用的原燃料粒度可偏小一些。
⑥少
入炉粉末要少(<5mm的要小于3%),炉料中含 有害杂质(S、P、K、Na、Zn、Pb、F等)要少。 炉料中碱金属含量<0.3%,Pb含量小于0.15%。
②熟
熟料比(烧结矿+球团矿)要高。目前不再追求 100%的熟料比,如宝钢熟料比为81%,增加高品 位块矿,可有效提高入炉品位,有利于节能减排。 但熟料比不宜低于80%,否则会使燃料比升高。
③稳
原燃料供应的数量、比例和质量要稳定。原燃料 稳定是高炉生产的灵魂。
④均
原燃料的粒度和成分要均匀。这是高炉提高料柱 透气性有效办法。大、中、小粒度的炉料混装会 有填充作用,减少有效空间。一般要求矿石 5~15mm的粒度要小于30%,焦炭在炉缸的空间 在40%。
高炉炉况分析
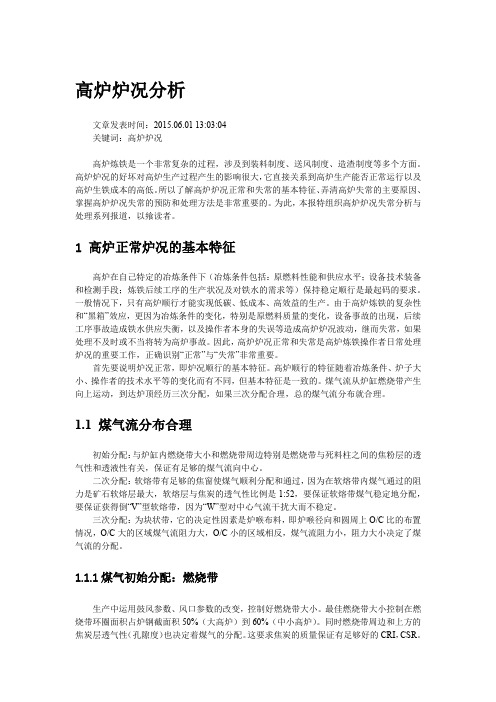
高炉炉况分析文章发表时间:2015.06.01 13:03:04关键词:高炉炉况高炉炼铁是一个非常复杂的过程,涉及到装料制度、送风制度、造渣制度等多个方面。
高炉炉况的好坏对高炉生产过程产生的影响很大,它直接关系到高炉生产能否正常运行以及高炉生铁成本的高低。
所以了解高炉炉况正常和失常的基本特征、弄清高炉失常的主要原因、掌握高炉炉况失常的预防和处理方法是非常重要的。
为此,本报特组织高炉炉况失常分析与处理系列报道,以飨读者。
1 高炉正常炉况的基本特征高炉在自己特定的冶炼条件下(冶炼条件包括:原燃料性能和供应水平;设备技术装备和检测手段;炼铁后续工序的生产状况及对铁水的需求等)保持稳定顺行是最起码的要求。
一般情况下,只有高炉顺行才能实现低碳、低成本、高效益的生产。
由于高炉炼铁的复杂性和“黑箱”效应,更因为冶炼条件的变化,特别是原燃料质量的变化,设备事故的出现,后续工序事故造成铁水供应失衡,以及操作者本身的失误等造成高炉炉况波动,继而失常,如果处理不及时或不当将转为高炉事故。
因此,高炉炉况正常和失常是高炉炼铁操作者日常处理炉况的重要工作,正确识别“正常”与“失常”非常重要。
首先要说明炉况正常,即炉况顺行的基本特征。
高炉顺行的特征随着冶炼条件、炉子大小、操作者的技术水平等的变化而有不同,但基本特征是一致的。
煤气流从炉缸燃烧带产生向上运动,到达炉顶经历三次分配,如果三次分配合理,总的煤气流分布就合理。
1.1 煤气流分布合理初始分配:与炉缸内燃烧带大小和燃烧带周边特别是燃烧带与死料柱之间的焦粉层的透气性和透液性有关,保证有足够的煤气流向中心。
二次分配:软熔带有足够的焦窗使煤气顺利分配和通过,因为在软熔带内煤气通过的阻力是矿石软熔层最大,软熔层与焦炭的透气性比例是1:52,要保证软熔带煤气稳定地分配,要保证获得倒“V”型软熔带,因为“W”型对中心气流干扰大而不稳定。
三次分配:为块状带,它的决定性因素是炉喉布料,即炉喉径向和圆周上O/C比的布置情况,O/C大的区域煤气流阻力大,O/C小的区域相反,煤气流阻力小,阻力大小决定了煤气流的分配。
- 1、下载文档前请自行甄别文档内容的完整性,平台不提供额外的编辑、内容补充、找答案等附加服务。
- 2、"仅部分预览"的文档,不可在线预览部分如存在完整性等问题,可反馈申请退款(可完整预览的文档不适用该条件!)。
- 3、如文档侵犯您的权益,请联系客服反馈,我们会尽快为您处理(人工客服工作时间:9:00-18:30)。
高炉炼铁对原燃料质量的要求和影响
1.2011年上半年我国钢铁生产情况
2011年上半年我国钢铁生产是处于增长阶段,平均日产钢199.77万吨,已是接近年产钢7亿吨的水平,祥见表1.
表1 2011年上半年我国钢铁主要产品产量情况单位:万吨
2011年前7个月我国进口铁矿石388634万吨,比上年增长7.81%,进口焦炭36万吨,比去年下降46.37%;出口焦炭2627.21万吨,比去年增加32.4%。
2.我国钢铁工业发展趋势
根据我国“十二五”发展规划,GDP值增长速度在8%,我国钢铁的需求量还有发展的空间。
预计我国钢产量的顶峰会在8.0亿吨左右,并要维持5~8年。
主要是,我国正处在工业化时代,基本建设任务大,钢材65%是用于基本建设。
农民还没开始大量使用钢材。
所以说,我国钢产量还有一定发展空间。
现在我国钢的生产能力已达9.2亿吨,只是其中还有部分落后的产能要淘汰,也还在建设新的钢铁设备(一部分是淘汰落后设备的替代,
一部分就是扩大产能)。
2011年上半年我国铁钢比为0.9259,上年为0.9358.铁的增速低于钢的增速。
但近年我国铁钢比不会有较大变化。
因我国废钢短缺,电价高,短流程发展不起来。
世界炼铁界公认,目前融熔还原炼铁在能耗和成本上是竞争不过高炉。
直接还原成功的案例是在特出条件下实现的。
所以,高炉还是产铁的主要设备。
短期内高炉是打不倒,而且还在得到不断的完善和提升。
综上所述,我国钢铁还要发展,高炉是炼铁的主要设备,对焦炭的需求也不会减弱。
这是发展的大趋势。
我们要有清醒的认识。
三年内,我国炼铁对进口铁矿石的依存度会下降。
但炼铁燃料比下降的空间不是很大了。
因炼铁的生产条件很难有较大的改善(特别是矿石品位、焦炭质量等)。
3.GB 50427--2008《高炉炼铁工艺设计规范》对原燃料质量的要求
2008年公布的《高炉炼铁工艺设计规范》对烧结、焦炭、球团、入炉块矿、煤粉质量均有具体要求。
祥见表2~9.
表2 入炉原料含铁品位及熟料率要求
注:不包括特殊矿。