品管部出货检验报告样板
【质量】OQC出货检验作业指导书,实例
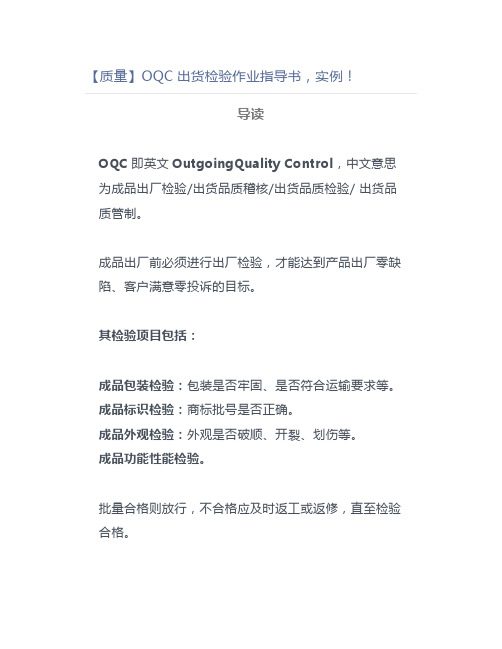
【质量】OQC出货检验作业指导书,实例!导读OQC即英文OutgoingQuality Control,中文意思为成品出厂检验/出货品质稽核/出货品质检验/ 出货品质管制。
成品出厂前必须进行出厂检验,才能达到产品出厂零缺陷、客户满意零投诉的目标。
其检验项目包括:成品包装检验:包装是否牢固、是否符合运输要求等。
成品标识检验:商标批号是否正确。
成品外观检验:外观是否破顺、开裂、划伤等。
成品功能性能检验。
批量合格则放行,不合格应及时返工或返修,直至检验合格。
OQC主要针对出货品的包装状态、防撞材料、产品识别/安全标示、配件(Accessory Kits)、使用手册/ 保证书、附加软体光碟、产品性能检测报告、外箱标签等,做一全面性的查核确认,以确保客户收货时和约定内容符合一致,以完全达标的方式出货。
OQC阶段的品检着重是「抽样检查」,当然,对高单价或高品级的产品,在OQC阶段对产品的整体状况(主体产品本身、配件、使用手册& 保证书、标示标签、包装等)再次进行全检(100% 全数检验)亦有其必要性。
OQC作业指导书1.目的:规范出货检验作业,确保产品正常出货,满足客户要求。
2.范围:出货产品的检验。
3.工作职责PMC:依据客户需求通知相关人员做好出货准备和派车;OQC:依据PMC的出货排程和产品标准进行检验;我们延伸一下,对职责进行了展开,供大家参考。
OQC岗位职责一:1、根据检验标准、样品、图纸或客户要求之标准进行成品及出货检验,对产成品进仓品质及出货的产品品质负责;2、根据客户要求或产品需要而需性能测试的产品,抽样交理性测试员,并跟进检验结果;3、负责将外观、尺寸、实配检验结果与性能测试结果结合填写在《成品检验报告单》与《OQC出货检验报告单》上;4、产成品进仓后,需监督仓库对仓存条件、化学反应及有效库存期限的控制,提前做好预防工作。
对库存产品的质量鉴定负责;5、负责周、月统计报告与分析,并确保其准确性与上交及时性;6、保持各部门的良好沟通;7、负责监督及维护现场7S执行情况;8、承接上级交给临时任务。
出货检验规范方案

一、目的:为了规范LED的出货检验规范,特制定本标准;二、范围:适用于本公司SMD LED,所有规格产品的出货检验;三、检验前的准备:1、检验条件:室内照明测试物距离光源为1M下,必要时以30倍(含)以上显微镜检验确认。
2、ESD防护:凡接触产品必须配带良好静电防护措施﹝手腕上必须配带防静电手环并接上电接地线,环上铁扣必须与手腕紧密接触,静电接地线的一端扣在手环上,一端夹在机台或桌子的地线上﹞; 作业过程中卷带拉出后需有空静电盒接,不可随意散在地上。
3、检验环境为:依WI-Q-113《车间环境控制实施标准》里定义的温湿度要求。
四、缺点定义:1、严重缺点(Critical Defect): 对使用者及维修者有发生危险及安全顾虑之缺点,以CR表示。
2、主要缺点(Major Defect): 会导致故障或实质降低实用机能, 而无法达到产品预期功能要求,以MA表示。
3、次要缺点(Minor Defect):与标准或规格有所差异, 但在使用上无明显影响,以MI表示。
五、抽样水准QC检验依据ANSI/ASQC Z1.4-2003.抽样计划正常检验(Ⅱ级水准)进行抽检。
产品尺寸,电性测试依特殊检验水平S-1进行抽样检测。
如客户有特殊要求时,依照客户要求执行。
六、检验工具:显微镜(10-30倍)、计算器、电脑ERP、镊子、卡尺、二次元、IS机、远方机、ROHS机。
七、不良品处理:不良标示隔离,判退要求领出返工或直接转入次品仓。
八、说明:备注:1.OQC将出货检验报告交主管审核后正式出货。
2.客户有特殊要求的按客户要求执行。
3.检验结果:对于合格品,ERP确认OK后点击审核通过,抽检确认OK后在发货单及外箱上盖“OQC PASS”印章。
4.对于不合格品,先进行标识隔离,同时开立异常报告单,并按《纠正预防管理程序》执行,材料返工重检OK,才可放行。
1.开袋从拆开铝包袋到铝包袋封口须十分钟内完成。
2.仓管将包装确认好之材料放置待抽检区域。
出货检验标准出货检验报告_0
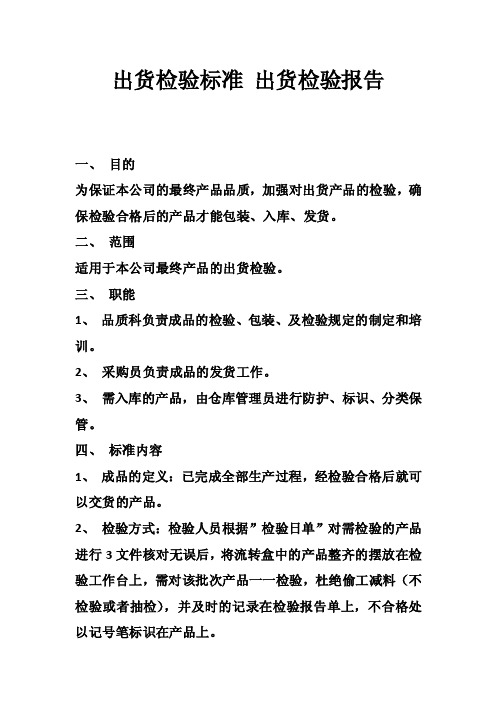
出货检验标准出货检验报告一、目的为保证本公司的最终产品品质,加强对出货产品的检验,确保检验合格后的产品才能包装、入库、发货。
二、范围适用于本公司最终产品的出货检验。
三、职能1、品质科负责成品的检验、包装、及检验规定的制定和培训。
2、采购员负责成品的发货工作。
3、需入库的产品,由仓库管理员进行防护、标识、分类保管。
四、标准内容1、成品的定义:已完成全部生产过程,经检验合格后就可以交货的产品。
2、检验方式:检验人员根据”检验日单”对需检验的产品进行3文件核对无误后,将流转盒中的产品整齐的摆放在检验工作台上,需对该批次产品一一检验,杜绝偷工减料(不检验或者抽检),并及时的记录在检验报告单上,不合格处以记号笔标识在产品上。
3、最终产品的判定a) 不合格品,需报废或返工的。
b) 不合格品,可特采接收的。
c) 合格产品,需入库的。
4、检验项目3.1外观的检测a)产品不得有磕碰、划伤、毛刺等现象b) 产品不得有材料缺陷。
c) 产品不得有裂纹、气孔、浃渣、焊接缺肉等现象。
d) 经过氮化的产品,观察氮化颜色:应该为均匀黑色或灰色,若出现金属色,则为不合格品。
e) 对于特殊工序加工的,如抛光等,必要时需借助专门测量仪器观测。
/news/21077BEE1171DCFF.htmld) 观察产品是否有按客户要求刻印的代号(刻印的位置、内容无误),如发现没有,则核对清楚后在规定位置刻印上代号。
3.2结构、尺寸的检测a) 根据客户图纸对产品进行一一检验,不得有漏检项。
3.3性能的检测:一般指材料的硬度要求、氮化质量、对产品特性影响较大的,需着重注意。
3.4附件检验人员应核对清楚是否有客户特别要求的指示,如提供的检测报告材料等。
3.5包装检测:检验人员检查产品的包装形态,确认产品的名称、规格、数量、包装要求、标识、邮寄地址是否符合要求,不符合要求则按包装文件重新包装、标识。
5、产品经检验判定后的处理4.1对于检验不合格的成品按照《不合格品控制程序文件》的相关内容进行处理。
来料、制程、成品抽样检验规范【范本模板】
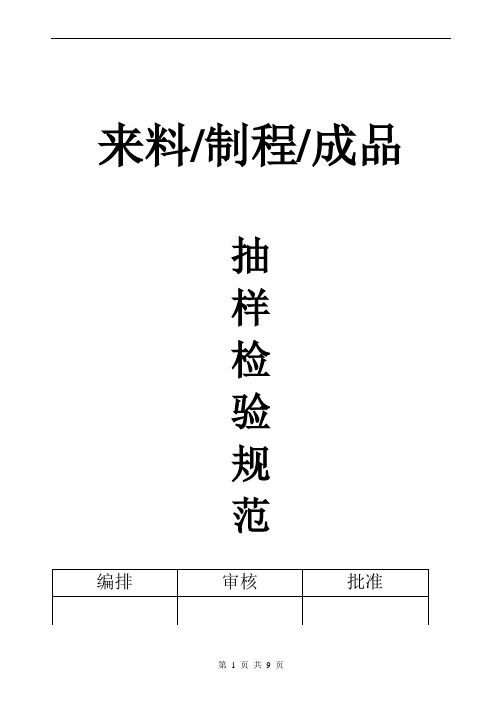
来料/制程/成品抽样检验规范1.目的:规范来料检验、成品检验之抽样水准、抽样方案以统一检验标准,确保来料及成品的质量稳定、良好.2.范围:适用本公司监督检查委外加工厂执行状况及委外加工厂执行IQC进料检验、制程检验、OQC成品出货检验的所有产品。
3.职责:a)IQC、IPQC、OQC负责执行本规定b)品管部负责监督执行并视产品实际情况制定、修改本规定4.内容:4。
1.来料检验1)抽样标准:按MIL-STD—105D Ⅱ级检查水平一次抽样进行2)合格质量水准AQL规定:①电子料MAJOR:0。
65;MINOR:2。
5②结构料MAJOR:1.0;MINOR:2.53)检查严格度:正常检验4)抽样方式:随机抽样5)抽样批量:每一订单作为一个检查批次6)生产部驻厂质检员对来料抽检的规定为,对3C关键性元器件采取每四批至少抽检一批确认外协加工厂来料检查执行情况,一般性器件采取每七批抽检一批的比例执行。
以上规定了来料检验通用抽样检验标准,部分物料特别规定的除外,参见具体物料检验标准,特殊情况由物料QE决定。
4。
2.制程检验1)抽样标准:按MIL—STD—105D Ⅱ级检查水平一次抽样进行2)合格质量水准AQL规定:①功能不良MAJOR:0.65;MINOR:2。
5②外观不良MAJOR:1.0;MINOR:2.53)检查严格度:正常检验4)抽样方式:随机抽样5)抽样批量:每四小时生产作为一个批量,低于4小时按照实际生产数量作为送检数量.6)生产部质检员依据每四批至少抽检一批的标准执行。
作业依据参见具体《物料检验标准》及《成品检验标准》,特殊情况由研发工程师决定.4。
3.成品出货检验1)抽样标准:按MIL—STD-105E(等同GB2828-87)Ⅱ级检查水平一次抽样方案进行2)合格质量水准AQL规定:①主机/键盘:CR:0。
4,MAJOR:0。
65;MINOR:2.53)检验严格度:正常检验4)抽样方式:随机抽样5)抽样批量①一般以客户每次的订单数量作为一个批量检验。
OQC出货检验程序(含表格)

OQC出货检验程序(ISO9001-2015)1.0目的:为确保生产线所生产的成品品质符合客户品质要求,对整个出货检验过程进行有效的管理,特制定本程序.2.0范围:适用于汕头市万晖实业有限公司所有产品出货品质检验作业.3.0职责:3.1OQC:出货品质检验、品质判定、状态标识、异常反馈与跟踪、检验结果记录。
3.2QE:制定或修订出货品质检验标准、异常原因分析、异常跟踪及作业指导。
3.3生产部:出货待检通知、不合格批的重工作业、不合格品处理.3.4仓库:成品入库管理、库存超保质期成品再检通知。
3.5业务部:成品特采申请、重工作业安排.4.0定义无5.0作业内容5.1入库成品待检通知生产部入库待检的成品必须是经FQC全检并判定合格(需贴合格标识)的产品,入库前需核对入库数量与检验数量是否相符,最后将待检之成品移入成品仓库指定的出货待检区域。
然后开立《出货待检通知单》通知OQC进行出货检验。
5.3出货品质检验作业5.3.1检验依据OQC检验时依据《成品检验规范》、《产品检验标准书》、工程样办等对产品进行品质检验和判定,抽样作业时按照MIL-STD-105E普通Ⅱ级抽样,合格质量允收水准(AQL):致命缺陷(CRI):0、主要缺陷(MAJ):0.65、次要缺陷(MIN):1.5,若客户有特别要求按照客户要求的允收水准进行抽样作业,具体参照《抽样检验计划》执行.5.3.2检验项目检验项目包括:外观/尺寸/结构/特性/包装/标识等项目,具体检验项目参照《成品检验规范》中规定检验项目进行检验.5.3.3OQC出货检验作业时应按照抽样计划规定的抽检数量从待检批中的不同部位、不同箱号的箱子中抽取指定数量进行检验,尽量减少不量流入客户端.检验完成后需在《出货待检通知单》上进行品质判定,然后将《出货待检通知单》归还生产部.5.3.4正常情况出货检验需在6个工作小时内完成,急出货情形需在2个工作小时内完成检验.检验结果是否合格都需真实且详细的记录于《OQC成品检查报告》上,以便追溯和统计分析.5.3.5经OQC检验合格批次,由生产部门填写《成品入仓单》办理入库.5.4检验状态标识检验合格在标签上盖PASS印章,不合格贴红色REJECT标签,特采使用贴黄色特采使用标签.挑选或加工使用则贴挑选/加工使用标签.具体参考《产品标识与追溯性控制程序》.5.5品质异常反馈及处理经抽检判不合格批次,需在产品外箱上贴上红色的不合格(REJECT)标签,并将判定结果记录于《成品待检通知单》上并归还仓库,同时OQC开立《出货检验异常报告》给OQC组长确认/主管审核/经理核准,然后由业务/PMC/生产/品质/工程等相关单位会签评审.最终由(副)总经理批准,不合格批的处理方式按(副)总经理批准意见执行,会签完后将此单给责任单位进行原因分析和制定改善对策,至于检验发现之不合格品的处理方式参照《不合格品的控制程序》执行.5.6特采放行作业5.6.1经OQC检验不合格批产品,经公司(副)总经理批准决定特采使用的,由业务开立《特采申请单》并附上《出货检验异常报告》给品质部/工程部/生产部/PMC等相关单位会签评审,由公司(副)总经理批准执行,最后由OQC将不合格标签撕下,在标签上盖PASS印章,若是经客户同意特采使用需在外箱贴特采使用标识.5.7不合格批重工再检判重工的不合格批,OQC需对重工过程进行跟踪(包括重工项目是否与反馈之项目相符,重工之数量是否与判退的数量相符等内容),重工后生产部必须重新报验此批,并在《出货待检通知单》上注明”已重工”字样.重工再检OQC必须再次填写《OQC成品检查报告》,报告上需详细注明为”重工再检”字样,并详细记录《出货检验异常报告》编号和其他相关信息,以便于追溯.5.8库存成品再检所有库存成品超过保存期限,仓库必须重新提报给OQC重检和判定.重检后原标识需更换,若重检判不合格,需开立《出货检验异常报告》给相关单位会签评审,不合格批的处理参照5.5/5.6/5.7执行,不合格品参照《不合格品控制程序》执行.5.9控制计划的传递和执行5.9.1在新产品投产之前,由品质经理针对此项产品的特殊特性内容,对检查员进行培训,要求品管员严格按特殊特性的内容执行检查。
成品出货检验报告
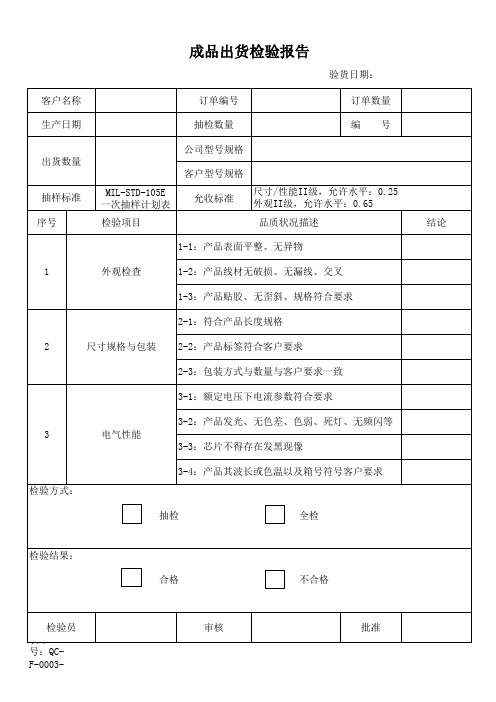
3
电气性能
3-3:芯片不得存在发黑现像
检验方式:
3-4:产品其波长或色温以及箱号符号客户要求
抽检 全检
检验结果: 合格 不合格
检验员 表单 号:QCF-0003-
审核
批准Biblioteka 成品出货检验报告验货日期:
客户名称
订单编号
订单数量
生产日期
抽检数量
编 号
出货数量
抽样标准 序号
公司型号规格
MIL-STD-105E 一次抽样计划表
检验项目
客户型号规格
允收标准
尺寸/性能II级,允许水平:0.25 外观II级,允许水平:0.65
品质状况描述
结论
1-1:产品表面平整、无异物
1
外观检查
1-2:产品线材无破损、无漏线、交叉
1-3:产品贴胶、无歪斜、规格符合要求
2-1:符合产品长度规格
2
尺寸规格与包装 2-2:产品标签符合客户要求
2-3:包装方式与数量与客户要求一致
3-1:额定电压下电流参数符合要求
3-2:产品发光、无色差、色弱、死灯、无频闪等
喷塑厂产品出货检验报告
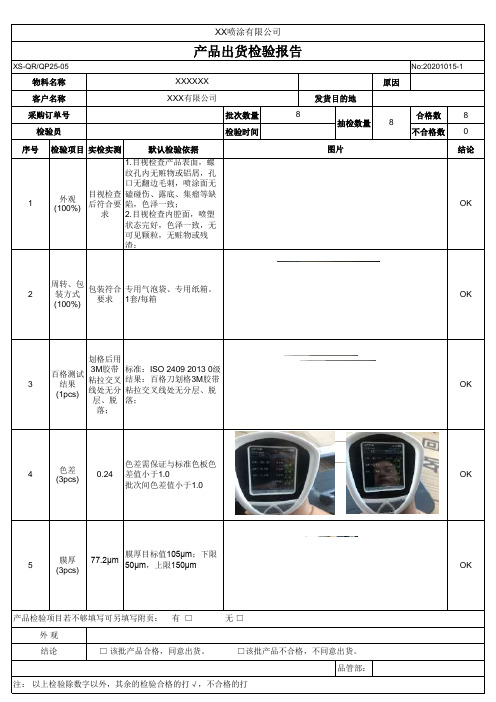
原因
批次数量合格数8检验时间
不合格数
0序号
检验项目实检实测
默认检验依据
结论
1
外观
(100%)
目视检查后符合要求 1.目视检查产品表面,螺纹孔内无赃物或铝屑,孔口无翻边毛刺,喷涂面无
磕碰伤、露底、集瘤等缺
陷,色泽一致;
2.目视检查内腔面,喷塑
状态完好,色泽一致,无可见颗粒,无赃物或残渣;
OK
2
周转、包
装方式
(100%)
包装符合要求专用气泡袋、专用纸箱。
1套/每箱
OK
3
百格测试
结果
(1pcs)
划格后用3M 胶带
粘拉交叉
线处无分
层、脱落;
标准:ISO 2409 2013 0级结果:百格刀划格3M 胶带粘拉交叉线处无分层、脱落;
OK
4
色差(3pcs)
0.24
色差需保证与标准色板色差值小于1.0
批次间色差值小于1.0
OK
5
膜厚(3pcs)
77.2μm
膜厚目标值105μm ;下限50μm ,上限150μm
OK
品管部:
XX 喷涂有限公司
产品出货检验报告
XS-QR/QP25-05
No:20201015-1
物料名称客户名称XXX 有限公司
发货目的地
采购订单号抽检数量8
检验员XXXXXX
图片
8注: 以上检验除数字以外,其余的检验合格的打√,不合格的打×
产品检验项目若不够填写可另填写附页: 有 □ 无 □
外 观结论
□ 该批产品合格,同意出货。
□该批产品不合格,不同意出货。
成品出货检验流程
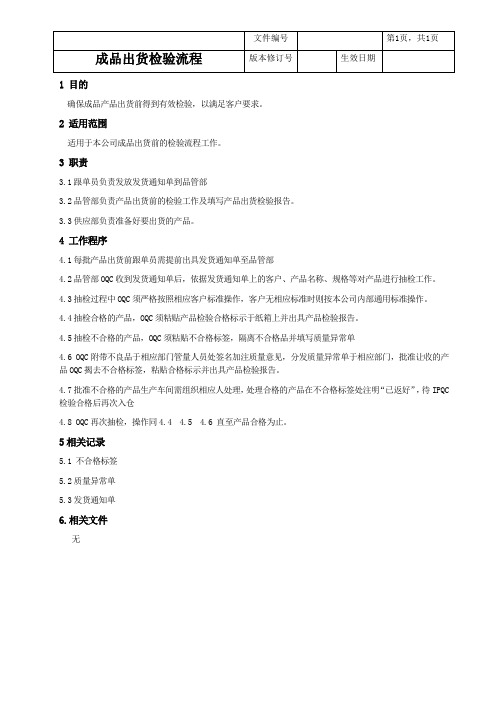
1 目的
确保成品产品出货前得到有效检验,以满足客户要求。
2 适用范围
适用于本公司成品出货前的检验流程工作。
3 职责
3.1跟单员负责发放发货通知单到品管部
3.2品管部负责产品出货前的检验工作及填写产品出货检验报告。
3.3供应部负责准备好要出货的产品。
4 工作程序
4.1每批产品出货前跟单员需提前出具发货通知单至品管部
4.2品管部OQC收到发货通知单后,依据发货通知单上的客户、产品名称、规格等对产品进行抽检工作。
4.3抽检过程中OQC须严格按照相应客户标准操作,客户无相应标准时则按本公司内部通用标准操作。
4.4抽检合格的产品,OQC须粘贴产品检验合格标示于纸箱上并出具产品检验报告。
4.5抽检不合格的产品,OQC须粘贴不合格标签,隔离不合格品并填写质量异常单
4.6 OQC附带不良品于相应部门管量人员处签名加注质量意见,分发质量异常单于相应部门,批准让收的产品OQC揭去不合格标签,粘贴合格标示并出具产品检验报告。
4.7批准不合格的产品生产车间需组织相应人处理,处理合格的产品在不合格标签处注明“已返好”,待IPQC 检验合格后再次入仓
4.8 OQC再次抽检,操作同4.4 4.5 4.6 直至产品合格为止。
5相关记录
5.1 不合格标签
5.2质量异常单
5.3发货通知单
6.相关文件
无。
成品出货检验程序,成品包装、入库和出货前质量检验规定

1.目的为保证产品满足客户要求对产品在出厂前质量进行验证。
2.范围成品包装、入库和出货前对包装成品、库存成品、出货成品的检验流程。
3.定义出货检验(FQC/OQC,英文全程为Final Quality Control/Outgoing Quality Control):是指产品在出货之前,为保证出货产品满足客户品质要求,所进行的检验,经检验合格的产品才能予以放行出货。
出货检验一般实行抽检,出货检验结果记录有时根据客户要求提供给客户。
4.职责4.1.品管部4.1.1.品管部QE:A.成品检验标准、原始订单、检验等依据的收集、建立和提供;B.质量异常的稽核和提报、追踪;C.质量记录的整理存档,统计分析;D.客户验货准备、陪同及记录,验货结果、客户要求事项等的整理发布,处理结果追踪。
4.1.2.品检PQC:A.包装成品(含首件检验)、库存成品的检验和判定。
B.成品检验记录的填写、质量记录的收集、汇总给品管部QE统计;C.质量问题的反馈、处理、追踪及纠正预防措施的落实及跟踪;D.不良品的管制、标识。
4.1.3.品管部OQC:A.整理准备检验依据,并依照进行检验。
B.库存成品\出货成品检验的执行及异常的反馈、监督处理。
C.出货检验报告的填写、汇总。
4.2.资材仓库:成品包装、成品储存、成品装货。
4.3.制造单位:产品的自检、质量异常的纠正预防措施的提出和处理。
4.4.技术部:技术资料、包装方式、装柜方式的确定和辅导。
成品出货检验工作流程图:5.作业内容5.1.包装成品首件确认5.1.1.批量成品包装前,由包装组依据《制造命令单》、《包装作业指导书》、有效的产品图纸,《产品检验规范》等文件,详细了解客户的包装要求(如唛头、标签、条形码等),使用对应的包装材料和包装方法进行包装,必要时通知技术部进行辅导。
5.1.2.首件制作完成由品检人员进行首件确认,首件确认必须完成如下的检验项目:A.确认包装的正确性:包装材料的材质、规格、尺寸和包装方式、产品及所需零配件数量。
热处理出货检验报告

热处理出货检验报告
永大真空热处理
客户名称交货日期
出货检验报告来料材质抽测材质
检硬度规格 HRC 实测硬度 HRC 来料重量发货重量验 HS HS 项来料变形HV 热处理变形 HV 来料日期深冷处理目 m/m m/m
一 (略图) (说明)
式热 ? 两处 ? 联理 ? ? 方 Hr Hr Hr 客法户说 ? ? ? ? 明
品
管
检验结果 1 材质确定: 判定备注
1、材质检测以火花TEST,而非光谱议 2 硬度确认:
2、材料硬度公差?2HRC
3、来料变形如0.5m/m经热处理后变形量1-3倍 3 变形确认:
550*700*25/32?1m/m
4、热处理变形合格不合格 4 数量确认: 550*700*25以下1.5m/m
课长: 组长: 品管员:
表单编号:QP-017-04-A。
成品出货检验规范

成品出货检验规范1. 0目的为控制本厂所有生产的出货成品的品质最终能完全达到客户之期望值.2.0范围:适用于本厂所有生产之出货成品.3.0 职责3.1装配负责于成品之装配包装.3.2 QA负责于成品的抽样检查.3.3仓库部负责成品之搬运、储存、装柜.4.0检验标准:4.1依据MIL-STD-105E Level II单次抽样计划,AQL值:CR:0 MAJ:1.5 MIN:4.0.4.2依据订单、包装资料以及《成品检验标准》。
5.0 作业程序5.1生产部将包装好的成品摆放于装配部成品区,挂好待检牌,同时填写好“成品入库单”,或先入仓库待检区通知品管部QA员检查。
5.2 QA员接到通知后,根据“入库单”准备齐相关“订单”、“包装资料”、“成品检验标准”于装配部成品区按照MIL-STD-105E Level II单次抽样对成品进行抽取样本检查。
5.3 QA对抽取之样本第一外箱,根据外箱跌落测试规范进行外箱跌落测试.测试之后对其该箱之内外箱及产品进行特别之功能及外观检查.检查后之良品与不良品同此批一同判定,其它物料性测试依据客户要求按相应《测试进行》或客户标准执行。
测试结果记录于“QA Test Report”中。
5.4 QA对其抽成品检查后,合格品按要求正常之装回原箱,不合格品通知装配负责人一同对其进行核对,确认.5.5 QA抽查后,统计其不合格总数,据“AQL允收之标准”对该批成品进行判定;不合格数量不超过“AQL允收标准”时,此批为合格,QA在成品标识单上盖〝 QA PASS〞章,然后QA填写好“成品检验报告”交于主管核实,并于“入库单”上签名,同时与“成品检验报告”复写件交于仓库,通知入库或转移至成品区。
5.6如统计其不合格总数超过其“AQL允收标准”,QA员填写好“成品检验报告”并同不合格样板交品管部主管最终确认.如确认为不合格,QA员填写“品质异常报告书”与不合格样板一同交生产部主管,并在成品标识单上盖“QA Reject”章由生产部对不合格品进行纠正及返工改善,QA对其进行追踪,及对该批纠正之后的产品进行重检并把检验结果记录于“成品检验报告”上。
原创品管检验报告

原创品管检验报告1.定义:进料检验又称来料检验,是工厂制止不良物料进进生产环节的首要控制点,进料检验由品质部IQC执行。
2.明确检测要项IQC在对来货检验前首先要清楚该批货物的品质检测要项,不明之处要向本部分主管询问直到清楚明了,必要时IQC验货员可从来货中随机抽取两件货样交IQC主管判别。
来货检验时样品并附相应的品质检测说明,不可在不明来货检验与验证项目方法和品质允收标准的情况下进行验收。
二、进料检验流程三、进料检验项目与方法1.外观检测一般用目视手感限度样品进行验证2.尺寸检测一般用卡尺千分尺塞规等量具验证3.结构检测一般用拉力器扭力器压力器验证4.特性检测如电气的物理的化学的机械的,一般采用检测仪器和特定方法来验证四、进料检验方式的选择1.全检方式适用于来货数目少价值高不答应有分歧格品物料或工厂指定进行全检的物料2.免检方式适用于大量低值辅助性材料或经认定的免检厂来料,以及生产急用而特批免检。
对于后者IQC应跟进生时的品质状况。
3.抽样检验方式适用于均匀数目较多经常性使用的物料一般工厂均采用此种验货方式根据其类型不同抽样检验又可分以下几种:(1)规准型抽样检验是在权衡供需双方利益与损失的条件下判定送检批是否合格。
(2)允收水准允收水准(AccptableQualityLevel)是客供双方均可接受的一种不良品(率)以符号AQL表示,一般适用于AQL型抽样计划的类型:向不同供给商应商采购同类货品时送货被判为分歧格供方损失较大时合格标准的批尽可能允收时(3)调整型抽样检验按供给商以往业绩和该批检验结果采用正常检验、严检检验、减量检验等(4)连续生产型抽样检验连续生产型抽样检验适用于大量连续生产的产品物料,不断活动时采用的验货类型(5)选别型抽样检验选别时抽样检验对判为分歧格的比采用全数检验并将全检后的拒收品退回供给商换回同数良品五、检验结果的处理方式1.允收经IQC验证分歧格品数低于限定的分歧格品个数时则判为该批来货允收,IQC应在验收单上签名盖检验合格印单通知仓库收货2.拒收若分歧格品数大于限定的不良品个数则判定该送检批为拒收,IQC 应进时填制IQC退货报告,经相关部分会签后交货仓采购部输退货事宜同时在该送检批货品外箱标签上盖退货字样并挂退货标识牌3.特采所谓特采即进料经IQC检验品质低于答应水准IQC虽提出退货的要求,但工厂由于生产的感恩而做出的特别采用的要求,若非迫不得已工厂应尽可能不启用特采即使采用也要按严格的程序办理。
制程检验规范范本
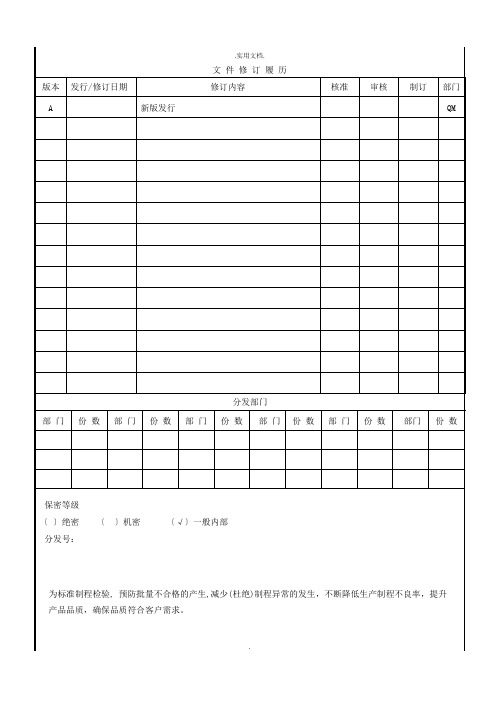
适用于公司生产制程品管检验控制。
3.1 首件:指生产制程中加工生产的产品,经自我确认、判定符合要求后,拟进行批量生产前的1-3台(个)产品(半成品、成品)。
3.2全检:对制程中的产品或产品的某些检验工程进行100%检验。
3.3巡检:指对生产过程中影响产品品质的因素进行随机抽样检验、确认。
4.1.1 负责制程中产品外观、检验流程、检验标准、检验标准、检验站的编制和设置.4.1.2 IPQC:负责对产品、物料首件确认的主导工作,并对产品首件做出合格与否的判定;制程品质检控,品质异常之追踪与确认;主导不合格品或异常品管问题的提出、跟进、落实、效果确认。
4.1.3 FQC:负责制程中产品外观、产品指定工程的全检。
4.1.4 测试员:负责制程中产品接地、耐压、点亮的全检4.2.1 参与新产品、试产、设计变更首件确实认,负责制程中产品电气、结构、功能、测试标准,品质异常、不合格品原因的分析及改善对策的提出。
4.2.2 负责制程中产品SOP的制定,工装夹具制作,工艺跟进改善,产能效率的提升,结构性能异常的跟进与落实。
4.2.3 负责制程中仪器、设备测试标准的制定;机器、设备、仪器、仪表、治夹具、工具运行状况的监控,设备的正常运转的巡视及日常保养工作监管。
4.3 业务部:参与新客户第一次生产及客户要求变更后首次生产时首件确实认。
4.4 生产部4.4.1 负责首件的制作与送样确认,自验互检。
4.4.2 制程中5M1E 的落实及制造过程的监控,配合IPQC与PIE的工作;品质异常的受理与改善,改善对策的具体实施.生产、检验前作业准备5.1.1.1生产部门在开拉生产前进行自我核查,发现不合格品及异常,采取措施立即纠正,再行生产。
5.1.1.2 生产部门开拉生产前需查核领用物料是否与制令工单相符,是否有相应的BOM、或样品,工作环境是否符合产品生产需求,各作业工站是否悬挂相应的SOP,人员对作业方法、产品品质是否清楚了解。
成品出货检验报告
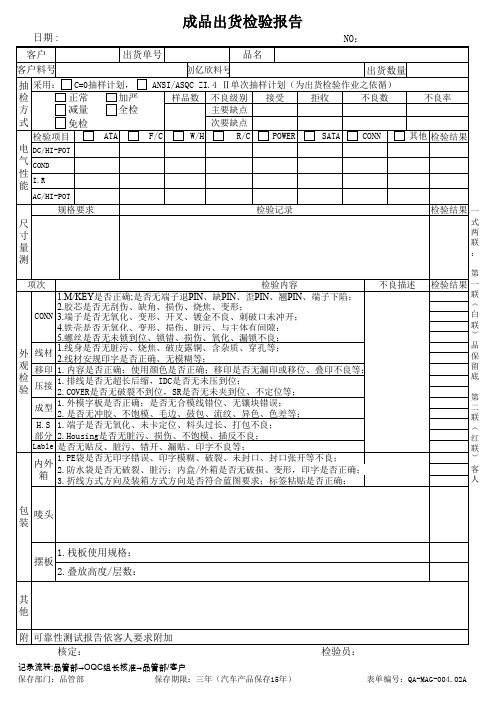
检验员:
表单编号:QA-MAG-004.02A
成品出货检验报告
日期 :
NO:
客户
出货单号
品名
客户料号
创亿欣料号
出货数量
抽 采用: C=0抽样计划, ANSI/ASQC ZI.4 Ⅱ单次抽样计划(为出货检验作业之依循)
检
正常
加严
样品数 不良级别 接受
拒收
不良数
不良率
方
减量
全检
主要缺点
式
免检
次要缺点
检验项目
ATA
F/C
W/H
R/C POWER
SATA CONN
成型
1.外模字板是否正确;是否无合模线错位、无镶块错误; 2.是否无冲胶、不饱模、毛边、鼓包、流纹、异色、色差等;
H.S 1.端子是否无氧化、未卡定位、料头过长、打包不良;
部分 2.Housing是否无脏污、损伤、不饱模、插反不良;
Lable 是否无贴反、脏污、错开、漏贴、印字不良等;
内外 箱
1.PE袋是否无印字错误、印字模糊、破裂、未封口、封口张开等不良; 2.防水袋是否无破裂、脏污;内盒/外箱是否无破损、变形,印字是否正确; 3.折线方式方向及装箱方式方向是否符合蓝图要求;标签粘贴是否正确;
4.铁壳是否无氧化、变形、损伤、脏污、与主体有间隙;
5.螺丝是否无未锁到位、锁错、损伤、氧化、漏锁不良;
外 观
线材 移印
1.线身是否无脏污、烧焦、破皮露铜、含杂质、穿孔等; 2.线材安规印字是否正确、无模糊等; 1.内容是否正确;使用颜色是否正确;移印是否无漏印或移位、叠印不良等;
检 验
压接
1.排线是否无超长后缩,IDC是否无未压到位; 2.COVER是否无破裂不到位,SR是否无未夹到位、不定位等;
OQC出货检验管理办法
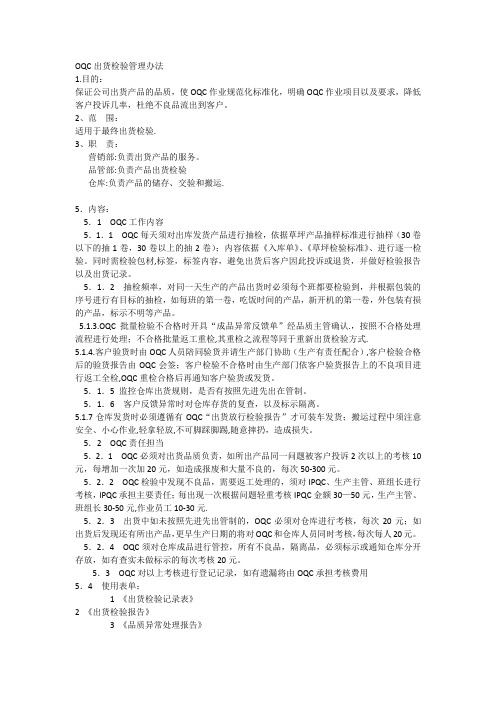
OQC出货检验管理办法1.目的:保证公司出货产品的品质,使OQC作业规范化标准化,明确OQC作业项目以及要求,降低客户投诉几率,杜绝不良品流出到客户。
2、范围:适用于最终出货检验.3、职责:营销部:负责出货产品的服务。
品管部:负责产品出货检验仓库:负责产品的储存、交验和搬运.5.内容:5.1 OQC工作内容5.1.1 OQC每天须对出库发货产品进行抽检,依据草坪产品抽样标准进行抽样(30卷以下的抽1卷,30卷以上的抽2卷);内容依据《入库单》、《草坪检验标准》、进行逐一检验。
同时需检验包材,标签,标签内容,避免出货后客户因此投诉或退货,并做好检验报告以及出货记录。
5.1.2 抽检频率,对同一天生产的产品出货时必须每个班都要检验到,并根据包装的序号进行有目标的抽检,如每班的第一卷,吃饭时间的产品,新开机的第一卷,外包装有损的产品,标示不明等产品。
5.1.3.OQC批量检验不合格时开具“成品异常反馈单”经品质主管确认.,按照不合格处理流程进行处理;不合格批量返工重检,其重检之流程等同于重新出货检验方式.5.1.4.客户验货时由OQC人员陪同验货并请生产部门协助(生产有责任配合),客户检验合格后的验货报告由OQC会签;客户检验不合格时由生产部门依客户验货报告上的不良项目进行返工全检,OQC重检合格后再通知客户验货或发货。
5.1.5 监控仓库出货规则,是否有按照先进先出在管制。
5.1.6 客户反馈异常时对仓库存货的复查,以及标示隔离。
5.1.7仓库发货时必须遵循有OQC“出货放行检验报告”才可装车发货;搬运过程中须注意安全、小心作业,轻拿轻放,不可脚踩脚踢,随意摔扔,造成损失。
5.2 OQC责任担当5.2.1 OQC必须对出货品质负责,如所出产品同一问题被客户投诉2次以上的考核10元,每增加一次加20元,如造成报废和大量不良的,每次50-300元。
5.2.2 OQC检验中发现不良品,需要返工处理的,须对IPQC、生产主管、班组长进行考核,IPQC承担主要责任;每出现一次根据问题轻重考核IPQC金额30—50元,生产主管、班组长30-50元,作业员工10-30元.5.2.3 出货中如未按照先进先出管制的,OQC必须对仓库进行考核,每次20元;如出货后发现还有所出产品,更早生产日期的将对OQC和仓库人员同时考核,每次每人20元。
QA检查管理规范(含表格)

QA检查管理规范(IATF16949-2016/ISO9001-2015)1.0目的:为规范QA作业流程,保证出货产品的质量满足客户的需求,特制定本检查指引。
2.0适用范围:适用品保课QA检验。
3.0名词定义:QA:指Quality Assurance 品质保证。
是品保课职能部门之一,其依据内部流程和标准,对产线完成品进行抽样检验。
AQL:Acceptable Quality Level。
指允收品质水准,也可称质量允收水平。
OBA:Out of BOX Assurance,指开箱检验:就是在产线的包装工位前或后一工位,按抽样计划要求,随机抽取样本进行检验。
其特点是:通过在线抽检,能以最快速度检验在线生产完成品,发现异常及时处理,并节约品管人员抽检时打开包装及装箱的时间。
4.0职责:品保课负责落实本指引规定相关事宜,各相关部门配合执行。
5.0作业内容:5.1 抽样计划不同客户的产品抽样计划会有差别,具体选择参照《抽样计划》。
5.2 生产线组批原则为:5.2.1 生产尽量按相同人员、机器、设备、物料、方法、环境、时间生产品集合组成检验批;5.2.2 QA在线进行抽检时所抽检的产品数量依据不同产品进行定义,定义的依据是:a.考虑检验单片产品外观、功能及其它检验项目所需的时间。
所属时间长的,抽检数量适量缩小,反之,抽检数量加大;b.考虑制程品质状况和客户品质要求。
制程品质不理想的,抽检数量适当增加,反之缩小;客户品质要求严格的,抽检数量适当加大,反之减少;c.如客户有明确要求的,须按客人要求进行抽样,但必须在《抽样计划》上加以注明.5.3检验标准及要求5.3.1PCBA检查标准按照《外观检验标准》,未尽事宜,参考IPC-A-610D要求。
5.3.2各检验场的光照度标准:工作台面在自然光或日光灯下,光照度标准应在500LM以上,由QA人员使用照度计每天一次检测当工段所有检验工位的光照度,并记录在【光照度测量记录表】中。