UG单动拉延模三维设计过程
Autoform R7.0单动拉延简例简介

punch 在坯料下方.
定义凹模
此处定义凹模从开始到拉延 结束的总行程
此处选择Tool cntr. (注:当为对称件时选择None)
设置binder
同样binder 在坯料下方,这里的binder 没有定义如图, 需要从Reference 定义,或由外部Import.点击 Reference 显示图,这里选择pick faces,到主窗口中 Shift+右键选择模型做为binder 的部分,此时会发现 选择时选框不完全框住一个片体的话将不能行中,如 果想大面积选择比较小的部分,需要在Options 中选 中Select crosseing 选项.完全选中后点击Include,选 中部位应实际显示,反之以网格显示则点击Toggle,点 击OK.同样Movement 的数值可修改也可使用默认 不变Required for force controlled tools only :Binder 的Columns 选择Tool center,如Add symmetrt 进行过设置,则此处选择None.
定义文件名 称
在此选择要打开 .IGS文件的路径
点击Apply(上图)检测模型中的缺陷和存在的孔洞,
如有缺陷和孔洞,将出现线框提示,根据显示部位 进行下一步操作。点击Mod 按钮,根据其中的功能
按需所取。如无其它要求,关闭当前对话窗口点击 图标或Model 中的Process generator(快捷键 Ctrl+I)打开对话框:(右图)要求选择仿真类型。 Incremental—用增量法计算(精度高、时间较长), One step—一步法计算(精度低、计算速度很快); 模具的工作方式Tool Setup 默认;板料厚度Sheet thickness 按实际给;Geometray refer to—按实际。 点击OK 出现(下图)Title,默认不管。
ug建模教程
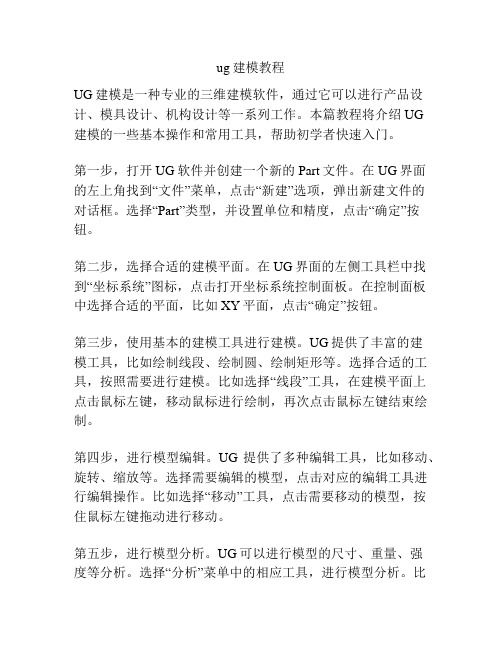
ug建模教程UG建模是一种专业的三维建模软件,通过它可以进行产品设计、模具设计、机构设计等一系列工作。
本篇教程将介绍UG建模的一些基本操作和常用工具,帮助初学者快速入门。
第一步,打开UG软件并创建一个新的Part文件。
在UG界面的左上角找到“文件”菜单,点击“新建”选项,弹出新建文件的对话框。
选择“Part”类型,并设置单位和精度,点击“确定”按钮。
第二步,选择合适的建模平面。
在UG界面的左侧工具栏中找到“坐标系统”图标,点击打开坐标系统控制面板。
在控制面板中选择合适的平面,比如XY平面,点击“确定”按钮。
第三步,使用基本的建模工具进行建模。
UG提供了丰富的建模工具,比如绘制线段、绘制圆、绘制矩形等。
选择合适的工具,按照需要进行建模。
比如选择“线段”工具,在建模平面上点击鼠标左键,移动鼠标进行绘制,再次点击鼠标左键结束绘制。
第四步,进行模型编辑。
UG提供了多种编辑工具,比如移动、旋转、缩放等。
选择需要编辑的模型,点击对应的编辑工具进行编辑操作。
比如选择“移动”工具,点击需要移动的模型,按住鼠标左键拖动进行移动。
第五步,进行模型分析。
UG可以进行模型的尺寸、重量、强度等分析。
选择“分析”菜单中的相应工具,进行模型分析。
比如选择“尺寸”工具,点击需要分析的特征,显示尺寸信息。
第六步,保存模型。
在完成模型建模后,选择“文件”菜单中的“保存”选项,选择保存路径和文件名,点击“保存”按钮。
以上就是UG建模的基本操作和常用工具的介绍。
通过学习和掌握这些内容,初学者可以快速入门UG建模,并能够进行基本的建模工作。
希望本篇教程能够帮助到大家。
UG建模教程
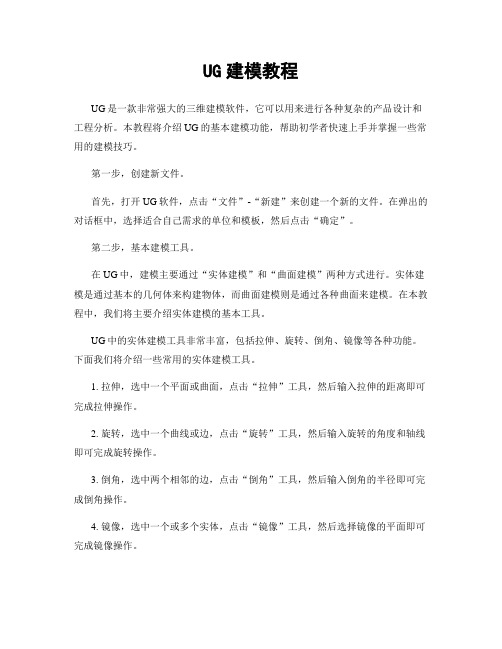
UG建模教程UG是一款非常强大的三维建模软件,它可以用来进行各种复杂的产品设计和工程分析。
本教程将介绍UG的基本建模功能,帮助初学者快速上手并掌握一些常用的建模技巧。
第一步,创建新文件。
首先,打开UG软件,点击“文件”-“新建”来创建一个新的文件。
在弹出的对话框中,选择适合自己需求的单位和模板,然后点击“确定”。
第二步,基本建模工具。
在UG中,建模主要通过“实体建模”和“曲面建模”两种方式进行。
实体建模是通过基本的几何体来构建物体,而曲面建模则是通过各种曲面来建模。
在本教程中,我们将主要介绍实体建模的基本工具。
UG中的实体建模工具非常丰富,包括拉伸、旋转、倒角、镜像等各种功能。
下面我们将介绍一些常用的实体建模工具。
1. 拉伸,选中一个平面或曲面,点击“拉伸”工具,然后输入拉伸的距离即可完成拉伸操作。
2. 旋转,选中一个曲线或边,点击“旋转”工具,然后输入旋转的角度和轴线即可完成旋转操作。
3. 倒角,选中两个相邻的边,点击“倒角”工具,然后输入倒角的半径即可完成倒角操作。
4. 镜像,选中一个或多个实体,点击“镜像”工具,然后选择镜像的平面即可完成镜像操作。
以上是一些基本的实体建模工具,通过这些工具的组合和应用,可以完成各种复杂的建模操作。
第三步,实例演练。
接下来,我们将通过一个实例来演练一下UG的建模操作。
假设我们要设计一个简单的杯子模型,下面是具体的步骤:1. 首先,创建一个底面圆形,选择“拉伸”工具,拉伸出杯子的高度。
2. 然后,选择“倒角”工具,给杯口和杯底添加一些倒角。
3. 最后,选择“镜像”工具,将杯子沿着一个平面进行镜像,完成整个杯子的设计。
通过这个简单的实例,我们可以看到UG的建模操作非常直观和高效,只需要几个基本的工具就可以完成一个复杂的物体设计。
第四步,高级建模技巧。
除了基本的建模工具之外,UG还提供了一些高级的建模技巧,比如曲面建模、装配设计、参数化建模等。
这些技巧可以帮助用户更加高效地进行建模和设计。
UG单动拉延模三维设计过程

不能满足限制条件则要将气顶接柱做加强处理或 者加接杆
8确定模具长宽及端头 (1)将做好的凸凹模及压边圈工作部分装配入标准模版
(2)调整模架装配
选择tools菜单下的expressions调整模具闭合高、下模基准高、模具长 宽、压边圈行程、气垫行程
各序模具型面(和形状)的基准
2 确认拉延模行程和气顶位置 验证工艺卡所给行程。由工艺卡得知此制件压边力需80T,根据标准按每个气顶提供4T的力计算,最少 需要20个,再加上安全个数4个,需要24个气顶,沿分模线一周共可以布置28个气顶。
3 确定导向形式
根据制件形状确定模具的导向形式, 大 致分为外导向拉延,内导向拉延,四角 导向拉垫
(2)布置墩死垫
此制件产品在分模线以内,并且客户要求墩死垫 与调压垫对齐
(3)布置定位装置
自动线需布置传 感器
(4)布置限程装置 单动拉延模用退料螺钉限程
(5)设计气顶接柱
根据气垫顶起高度,压边圈行程,压边圈底面到 机床的距离可以确定气
UG单动拉延模三维设计过程
1分析工艺
首先拿到工艺后要分析各部分,分模线、坯料线、拉延后坯料线、重力坯料线、拉延筋、到底标记、左 右标记、CH孔,有时还有弹顶销、穿刺孔和破裂刀位置
分模线决定了凸模的外圈轮廓大小 坯料线决定了压料面的大小 从拉延前后坯料线可以看出板料在压料面上的流入情况 重力坯料线决定了定位板定位位置和高度 拉延筋可以控制板料的流入量 到底标记用来检测是否拉伸到位(设计在废料区) 左右标记是产品左右件的标识,来实现焊装白车身的目的 CH孔是在拉延(序)模上的拉延件上冲制的两个模具制造调试用的研模(定位)工艺孔。是带件研合
拉伸模设计流程

拉伸模设计流程拉伸模的种类:单动拉伸模、双动拉伸模和三动拉伸模。
在实际工作中,我们接触到最多的是单动拉伸模,双动拉伸模和三动拉伸模极少遇到。
下面我们着重来了解一下单动拉伸模的结构和设计流程,供大家参考。
单动拉伸模按照结构分为:一般结构(内导向)、外导向和箱式结构。
一般结构大家遇到的最多。
在制件比较细长,内导向比较困难时,才采用外导向和箱式结构。
一般结构的单动拉伸模设计流程分为下面几个步骤。
一、仔细看清设计任务书、工艺和机床参数1、设计任务书。
规定了一些设计规范、闭合高度等具体要求。
2、拉伸模的UG工艺文件。
第一层放置的是工艺片体,第二层放置的是分模线、坯料线和拉沿筋中心线,第三层放置的是CH孔和到底标记的位置。
3、机床参数。
主要看工作台气顶孔的位置、气顶行程、机床最大闭合高度、压板槽位置等参数。
二、实体设计首先将第一层的片体进行缝合,将缝合好的片体备份到第10层。
1、压边圈①初步确定模具中心。
一般将模具中心设在坯料的中心上。
②压料面。
将坯料线向外扩10mm,用扩出来的线和分模线拉伸出一个实体,用缝合好的片体进行裁减,得到的型面即为压边圈的压料面。
③压边圈上部铸造毛面。
一般做成平面,比最低型面低35-40mm。
按压料面最外棱边四周长出宽120x40mm。
如果型面复杂,可随型下降40mm。
④布置气顶。
尽量将模具中心与机床中心重合。
气顶布置在分模线周围,300左右一个。
如果移动机床中心,左右、上下最大偏移75mm。
⑤布置调压垫TS191、墩死垫TS191。
原则:每300-400mm一个,在压料面四周均匀分布,距离压料面35mm。
调压垫正下方必须有墩死垫相对应。
调压垫与气顶不能在Z向重合。
⑥布置压边圈立筋。
分模线向外偏10和60mm,布50mm的随型立筋,调压垫、气顶位置均有立筋。
⑦布置压边圈与上模导向。
详细参照天津汽车模具厂《冲模设计标准》导向基准TS-2106。
⑧布置档料板。
一般前后、左右各2块。
出料方向TS421,左右TS422,进料方向TS423。
拉延模(DR)设计流程

拉延模(DR)设计流程一、工艺图分析01.板料线:指的就是拉延坯料(毛坯钣金)的尺寸大小02.分模线:指的就是压边圈和凸模的分界线(侧壁和法兰面的交线)03.到底标记:目的就是检测产品在拉延的时候,到底拉延到位了没,拉到底了没,根据产品拉延痕迹的深浅钳工很方便就可以判断出来,一套模具放2个到底标记(有些大模具放3~4,具体个数请看工艺图),到底标记我们安装在上模,到底标记超出上模型面0.3mm,直径一般是Φ16,有些客户用Φ13,具体看工艺图上给的是多大就用多大的,misimi型号DCBA16。
如下:工艺图04.左右标记:就是给产品打logo用的(产品有左右两个产品),在产品上刻一个标记以便于产品区分,左产品刻L,右产品刻R,一般刻在外表面,方便观察,具体刻字及大小尺寸看工艺图,左右标记超出型面0.3mm05.拉延收缩线:指坯料拉延后收缩的尺寸大小(板料最终的位置),如下:工艺图06.拉延筋:目的用来控制材料(坯料拉延时)的流动速度,常见的有起皱(流动速度太快),破裂(流动速度太慢)07.CH孔:后工程模具(比如:修边、冲孔)用来研模型面用的,保证拉延后(回弹)的钣金能够与后工程模具型面保持一致,内板件做φ10,外板件做φ6,CH做盲孔(没有打通的孔)还是通孔看客户的要求,工艺图有CH孔就做出来,没有就不用做(有的公司工艺图上有CH孔,也不做出来,因为后面有整形)08.排气孔:我们一般设置在凹模的凹处,内板件做φ6,外板件做φ4目的是为了能够把凹模凹处里面的气体及时排出去,保证拉延质量,把凹模打通就可以二、结构设计拉延模按导向可以分为3种:内导(压边圈与凸模导向)+外导(压边圈与下模座四角导向)+腔体导(压边圈四周与下模座导向),腔体导用的极少,所以这里不做讲解,我们重点是内导和外导拉延模(单动)结构分为:上模+下模+压边圈+凸模等四部分09.模具导向用内导还是外导?如何选择?〓〓〓内导结构〓〓〓a.内导结构:凸模导向精度比较高,模具结构比较小,省钱,压边圈受侧向力(不适合压边圈受侧向力比较大的结构)b.我们尽量选择内导(省钱凸模精度高)c.什么情况下用内导?凸模好放导板/压边圈受侧向力比较小的情况我们就用内导d.内导结构:是凸模(导板安装在凸模上)与压边圈导向〓〓〓外导结构〓〓〓a.外导结构:一般就是内导不好导向之后,考虑外导,外导结构比较大(相对于内导),所以成本比较高,压边圈受侧向力比较稳定,但凸模导向精度低点b.什么情况下用外导?内导用不了的情况下就用外导,比如:凸模导板放不下情况下就用外导比如:凸模型面落差比较大情况下就用外导(压边圈侧向力大)c.外导结构:是压边圈(导板安装在压边圈上)与下模座四角导向10.模具用整体式还是镶块式结构?如何选择?〓〓〓当料厚t<1.2a.压边圈(整体式MoCr)+凹模(整体式MoCr)+凸模(整体式MoCr)+下模座(HT300)〓〓〓料厚t>1.2或抗拉强度比较大的板a.压边圈(镶块式...)+凹模(镶块式...)+凸模(整体式MoCr)+下模座(HT300)整体式:一般指的板料比较薄,或者板料强度比较软的材质(压边圈+凹模)镶块式:一般指的板料比较厚,或者板料强度比较硬的材质(压边圈+凹模)凸模做镶块:一般是材质硬料厚比较厚型面比较复杂11.压边圈行程计算?保证板料放在压边圈(分模线外面的型面)上面不会碰到凸模(分模线里面的型面)且空有10左右mm余量,注意压边圈行程只能是5或0尾数模拟方式如下(用分模线外面片体整体往上移动超出凸模(不动)10mm左右,移动的行程就是压边圈行程,行程取0或5尾数,如10、15不要取11这样的行程数)12.顶杆数量计算:11-01单个顶杆可以提供4T-5T的力,所以说顶杆数量=压料力/5T,然后考虑受力均匀(对称),力尽量比理论压料力大一点压料力计算:PB=SB(mm)×γn(kg/mm2)×T(mm)注:SB压边圈面积(mm2)γn系数T:板厚(mm)内容γn例以拉深为主体的零件0.15W/HOTR、FRPILLER OTR一般件0.22T/GOTR、DOOR INR etc 以拉延为主体的零件0.29DOOR OTR、HOOD OTR11-02氮气弹簧极限取氮气弹簧行程的80%(大部分是KALLER,其次DADCO) 13.凸模(长度):小模具<1000,1000<中<2000,大模具>2000【通过凸模长度确定好了模具是小模具后,我们可以度确定压边圈宽度】14.压边圈宽度确定(单边宽度):板料线+压料区域(15中小模具~20大模具)+平衡块(60小+70中+80大)+10(安装面)+20空面(退刀面)=========【到了这一步就可以开始压边圈和凸模设计】=============== 15.凸模设计(★★★★★)15-1.创建基准平面XY平面,距离-600左右,把分模线投影到XY平面上,然后把投影的曲线优化一下(编辑曲线参数)15-2.把刚才投影的曲线(15-1)拉伸出一个实体,超出型面(片体)即可15-3.通过修剪体(或者拆分体)把实体(15-2)修剪掉,保留下面部分15-4.把工艺片体大致偏置-50(向下),凸模做50型面肉厚,15-5.用偏置曲线(勾选大致偏置)把之前投影好的曲线(15-1),往里面偏置10(做空刀),15-6.用编辑曲线参数(原有),把刚才偏置的曲线(15-5)优化一下15-7.偏置好的曲线(15-5),拉伸出一个实体,往外偏置26(大于10就行)15-8.用修剪体修剪实体,保留下面,再跟凸模求差这样空刀面就做出来了(铸件空刀面做10)15-9.把曲线(15-5)往里大致偏置40,之后编辑曲线参数优化这条曲线,15-10.偏置40的曲线拉伸一个实体出来,用片体(15-4)修剪实体,保留下面部分,然后求差15-11.导板安装面比导板单边加大5(目的是为了防止铸件缩水导致导板后面悬空),安装面底部凸出10,底部高度3015-12.导滑面上面低于导板10,下面超出超出导板15,下面倒圆角R5,压边圈往上抬一个行程之后,导滑面与导板接触50左右15-13.导板安装面到凸模肉厚40-50左右,15-14.导滑面为什么要超出导板?为了后期钳工好调整导板间隙15-15.凸模大小确定:凸模长度<1000,就是小模具,<1000<凸模长度<2000,就是中模具,>2000就是大模具15-16.导板放在凸模的1/6处15-17.导板安装面超出分模线5左右,目的是为了刀具能够下去加工安装面15-18.凸模高度确定:导板安装面到凸模肉厚40~50+安装面高度+安装面底部30+15安装面底部到凸模底部距离15-19.副筋做30厚,主筋做4015-20.筋之间的距离做到300内最好15-21.起吊牙安装面:必须在分模线里面5mm左右即可目的是为了防止压边圈和凸模干涉,起吊牙大小起步M16及以上15-22.定位键(凸模下面一般放3个键):目的是用来干嘛的?一来:钳工能够快速找到装配基准,二来:键是可以防侧向力凸模定位件做明键,目的是为了钳工好装配凸模上需要加两个销钉孔,用来精定位,挤紧凸模,后期模具修模可以用来作为加工基准15-23.凸模锁付,小模具6个,中大型8个,锁付块单颗螺丝的50宽,超出分模线50左右,要打螺丝和销钉的宽度做80,超出分模线50左右,销钉做对角线上16.压边圈设计(★★★★★)=======宽度确定(单边)==========板料线+压料面(15mm小模具~20mm中大模具)+平衡块(60小+70中+80大)+10平衡块安装面+20退刀面16-1.板料线拉伸实体,超出片体即可16-2.16-1拉好的实体按16-1要求把压边圈宽度偏置出来(4个面都要偏置)16-3.把片体扩大,超出16-2实体,用工艺片体修剪实体,保留下面16-4.用板料线拉伸实体(记得超出上面实体16-3)+单边加大15(小模具压料型面)16-5.用16-4实体拆分16-3实体,然后删掉16-4实体,留下压边圈里外实体16-6.工艺片体往下大致偏置20,然后用大致偏置20的片体修剪16-5外面的实体(压边圈外面的实体),保留下面(就是平衡块安装部分),然后16-5两个(压边圈里外实体)实体求和16-7.用分模线拉实体出来,超出16-6实体,往外偏置3mm(凸模与压边圈间隙),然后求差(16-6实体与16-7实体)16-8.用分模线拉实体出来,超出16-7实体,往外偏置13mm(压边圈10mm 空刀),然后用工艺片体往下大致偏置50,用偏置出来的片体修剪刚刚拉伸出来的实体,保留下面,然后再与实体(压边圈)求差,压边圈10mm的空刀面就出来了16-9.压边圈底面替换到导滑面底面16-10.把顶杆位置数量确定好(拉实体方便观察),16-11.顶杆位置确定好了,就可以挖压边圈导滑面避位(导滑面左右35,靠近压边圈里面两边倒R30角,上面留35),再与压边圈实体求差16-12.凸模导板安装面可以与凸模求和,起吊牙安装面也可以与凸模求和16-13.工艺片体往下大致偏置60(做压边圈面板40厚),然后用偏置出来的片体拆分实体压边圈16-14.压边圈底部里面一圈线连接起来,往外面偏置曲线40(做40厚主筋),编辑曲线参数优化曲线,然后拉伸片体(实体)拆分实体压边圈(下面部分),然后压边圈下面外面部分从底部拆分40厚的主筋,上下里3个实体求和(压边圈求和)16-15.平衡块:小模具平衡块60+10安装面,厚度10mm,平衡块安装面比型面要低5-10mm,平衡块安装面离型面20mm距离,目的是为了刀具在加工平衡块安装面的时候方便退刀,平衡块可以保证压边圈受力均匀,提高拉延的稳定性,同时试模钳工可以用来调整进料阻力,16-16.平衡块之间的距离做到300左右(不是死的可以根据模具适当调整距离),平衡块要考虑受力均匀16-17.平衡块下面必须有筋支撑,顶杆位置也要有筋支撑,筋做30厚16-18.平衡块下面是蹲死块,蹲死块是安装在下模,位置大小和平衡块一样,底部要有筋支撑16-19.顶杆垫块:我们一般用两颗螺丝的型号,防止垫块转动,上面有筋支撑17.凸模锁付,对角要做两个销钉,用来精定位的,挤紧凸模,修模找基准定位键一来是给钳工用来找装配基准的,二来可以防侧向力18.压边圈卸料螺钉计算:80(不变的)+行程(变的)+20(不变的)安全余量19.安装面我们一般直径做0或5的尾数20.压边圈卸料螺钉放4个(在四个角落)21.卸料螺钉过孔单边加大1mm22.端头导板之间的距离取压边圈宽度的1/2~2/3之间23.端头要做防呆设计,宽度单边缩小10mm,目的是防止钳工(现场人员)装反模具(旋转180)24.外定位定位面与板料线对齐,外定位直线部分做到10-15mm,并且外定位直面底面在压料面下面,防止板料卡在里面,拉断外定位板25.起吊棒(4个)能够承受2套模具重量,四面补强50mm厚,里面补强30厚26.铸件与铸件做15避位间隙(凸模与压边圈),铸件与钢件做10避位间隙,钢件与钢件做5避位间隙27.下模设计(★★★★★)27-01.压板宽度做到120mm,厚度50mm27-02.压板槽宽度40,深度40,台阶面10,单边25,27-03.T型槽尽量选择距离比较远的,受力面积比较大,27-04.副筋30,主筋40(受力的地方),模座外面一圈都是主筋40副筋之间的距离一般在300内(300不是固定的)27-05.副筋到压板槽之间的距离做到100左右,如果空间不够做到80左右27-06.凸模受力筋(主筋最外面一圈就是)支撑到底,下模座要做出来,上模座也要做出来27-07.平衡块下面就是蹲死块,蹲死块下面必须有筋(30厚副筋)支撑,局部加强区域做到受力面2/3就可以28.上模设计(★★★★★)28-01.上模设计:用压边圈外形(宽度一致,长度和端头对其,简单理解为平衡块的安装区域面)创建实体出来(创建方块命令),28-02.把工艺片体打开,扩大面(修剪延伸),保证工艺片体超出01实体,然后进行修剪,保留上部分28-03.再用压料型面区域创建实体,拉伸实体超出02实体(创建方块),然后把02实体进行拆分,拆分完厚删除刚刚拉伸的实体28-04.再用工艺片体往上大致偏置20,用大致偏置20的片体修剪上模外面部分,保留上部分,然后两个实体求和28-05.再用工艺片体往上大致偏置60然后修剪上模实体,保留下面28-06.上模主筋(最外面一圈)、副筋做出来,替换到机床上台面28-07.压板宽度120,厚度5029.外定位板:定位直面做到10-15MM(拉延模),修边模做到15-20MM(回弹)、定位板直面处底面要低于压料面5mm左右,目的为了防止板料跑到里面,拉延时候拉断外定位板30.导板窥视孔:基本上导板都要挖出来窥视孔,目的是为了钳工方便测量或者观察导板与倒滑面之间的间隙(导板间隙0.05mm)31.模具结构:上模小,下模大可以,上模大下模小不可以!!!32.贴字:F(前)+(→)送料方向+产品号+零件号+模具号+(OP10-DR)工序号+材质(HT300国产灰口铸铁FC300日本材质)(凸模材质MoCr国产=GM241M日本)修边模(铸件刀块材质是7CrSiMnMoV=空冷钢=日本ICD5)钢件刀块国产材质Cr12日本SKD11(DC53整形TD处理)美国D2 33.拉延模材质(整体式模具=凸模+凹模+压边圈材质MoCr+下模座TH300)(镶块式模具=凸模(MoCr85%+Cr12)+凹模(Cr12)+压边圈(Cr12)+下模座HT300)MoCr(铸件)Cr12(钢件)=SKD11(钢件)34.粗加工基准面:做L型加工基准面,目的是用来开粗加工用的35.三销孔:用来精加工模具或者后期模具修模找基准用的(铰出来盲孔+线割通孔(钢件))三销孔长度方向2个,宽度方向1个,三销孔尽量设置在高处,但是要考虑翻转损坏三销孔(我们就设置在低处)36.键槽:键槽大小28或32,具体大小看公司要求,目的是用来模具放在加工机台上时能够快速定位找到装配基准(机加工公用模板)37.百位线:上下模都要做,主要是用来加工底面时,控制加工量的,直径40,半圆形式表示,距离底面10038.V型槽:放在模具中心,加工时用来快速取中39.运输连接板:连接上下模,搬运(移模)的时候保证模具不会晃动,40.安全区域:100*100小模具,120*120中模具,150*150大模具有条件的情况下我们做10的凸台,没有条件就5凸台,目的是:就是试模工作人员使用的41.起吊棒处倒圆角(起吊处),倒R20,目的就是为了保护我们钢丝绳不会被直角面损坏42.到底标记:(misimi型号DCBA16)43.汽车四大工艺:冲压工艺+焊装工艺+涂装工艺+总装工艺44.英文简称:DR(拉延)+TR(修边)+PI(冲孔)+FL(翻边)+RST(整形)+CTR(侧修边)+CPI(侧冲孔)+CFL(侧翻边)+CRST(侧整形)+CAM(斜楔)+BEND(折弯)+SEP(分离)+BUR(翻孔)+BL(落料)45.销钉植入深度2直径46.快速定位孔:就用顶杆孔作为快速定位孔47.排水孔:直径φ40,开口向上的铸件就要做出来,一来清洗模具时水能够及时排出来,二来冲压的时候机床上流下的油液能够及时排出48.拉延模板料定位用外定位板来定位,到了修边模就可以用型面和外定位板来定位,翻遍整形模可以用型面和定位孔以及外定位板来定位。
拉延类模具三维设计流程bvxn

从起重棒上 LINK过来的 补肉,可以与 模具本体进 行布尔运算
标准件的安装不可能一步到位,许多标准件如定位板,调 整垫块,导板等位置需要经常调整,而且这些标准件与铸件结 构有很多的关联。LINK过来的部分是与标准件有关联的,会 跟随标准件位置的变化而变化,因而无需另外调整。
LINK完成以后,可以将原标准件上的此部分移动到不可见的图 层中,此时LINK的部分就可以与模具本体进行布尔运算了。
将坯料线,分模线,中心线投影到上步所生成的基准面上;以后 操作如不加说明,均是在此基准面上进行。
将分模线向外偏置3mm得到压边圈的口线,口线再向外偏置 10mm退刀得到随型筋的内边界,将此线再向外偏置40mm得到随 型筋。
将坯料线向外偏置10mm得到压料面的外边界。 调入机床合理选择气顶,应注意气顶尽量选择靠近分模线并均匀
布置,一般开始时将所有靠近分模线的气顶保留,并校核压边力 是否足够。布置时还应考虑是否需要偏心以使气顶布置更加合理。
由于以上部分曲线为工艺事先给定,故可以不用参 数化。
此图为以上各步骤完成后的状况,其中上部平面中
曲线为工艺所给的各曲线,下部平面中为投影后并经 过口线偏置的曲线。
根据上述步骤所得压料面来大致确定模具的尺寸,其中前后向考 虑调压垫的摆放位置,一般情况下调压垫安装台边界要距离压料 面30mm以上,如果上模,压边圈的调压垫的安装面高度均在压 料面以下,可考虑距压料面10mm以上即可。考虑模具前后向尺 寸时还需考虑压边圈的强度。其强度标准可参考本文第四页。
装配标准件,运用ASSEMBLIES 中ADD EXISTING COMPONENT命令
w 压边圈中的导板、起重棒、定位板、调整垫块等标准件的安装是 通过装配命令来实现的。装配时应注意用基准面进行位置约束。 图示为装配刚刚开始时,导入起重棒。
UG运动仿真基本流程(参考模板)

运动仿真基本流程计算机仿真的过程,实际上就是凭借系统的数学模型,并通过该模型在计算机上的运行,来执行对该模型的模拟、检验和修正,并使该模型不断趋于完善的过程。
1.在试图求解问题之前,实际系统的定义最为关键,尤其是系统的包络边界的识别。
对一个系统的定义主要包括系统的目标、目标达成的衡量标准、自由变量、约束条件、研究范围、研究环境等等,这些内容必须具有明确的定义准则并已于定量化处理。
2.一旦有了这些明确的系统定义,结合一定的假设和简化,在确定了系统变量和参数以及他们之间的关系后,即可方便的建立描述所研究系统的数学模型。
3.接下来做的工作是实现数学模型向计算机执行的转变,计算机执行主要是通过程序设计语言变成的程序来完成的,为此,研究人员必须在高级语言和专用仿真语言之间做出选择。
4.计算机仿真的目的,主要是为了研究或再现实际系统的特征,因此模型的仿真运行是一个反复的动态过程;并且有必要对仿真结果做出全面的分析和论证。
否则,不管仿真模型建立的多么精确,不管仿真运行次数多么大,都不能达到正确的辅助分析者进行系统抉择的最终目的。
用户通过计算机进行运动仿真的过称为:1.进入运动仿真模块2.建立连杆创建连杆的第一步是从连杆和运动付工具条中单击连杆图标,弹出连杆对话框。
对话框中显示默认的名字,输入名字后按回车键即可。
连杆对话框的第二项是自定义质量特性,它是一个可选项,在不涉及反作用力时可以将它关闭而使用自定义的质量特性。
但尽管如此,有时还是要定义质量特性,此时其他窗口将被激活。
包括质量、质心、惯性矩、初始速度等。
接着要定义材料,材料是计算质量和惯性矩的关键因素。
3创建运动付定义运动付以前机构中的连杆是在空中浮动的,没有约束的。
创建运动付的操作分为三步:(1)选择运动付要约束的连杆(2)确定运动付的原点(3)确定运动付的方向单击运动工具条中的运动付图标,或从菜单中选择插入-运动付,弹出运动付对话框。
4定义运动驱动运动驱动是赋在运动付上控制运动的运动服参数。
利用UGNX6.0软件的运动仿真功能让模具“动起来”

利用UGNX6.0软件的运动仿真功能让模具“动起来”随着中国汽车行业的快速发展,各汽车厂为了尽可能早的抢占市场,对汽车模具的生产周期要求越来越短,精度要求越来越高,这就对模具设计以及制造等各个环节提出了更高的要求.随着CAD/CAM技术的深入应用,二维设计逐渐显现出越来越多的劣势,三维设计也就自然而然的成为国内汽车模具设计人员必须掌握的设计手段。
对模型进行运动仿真也就有了依据。
UGNX自带的机构运动分析模块MOTION提供机构仿真分析和文档生成功能,可在U G环境定义机构,包括铰链、连杆、弹簧、阻尼、初始运动条件、添加阻力等,然后直接在UG中进行分析,仿真机构运动。
设计人员可以分析反作用力、图解合成位移、速度、加速度曲线,反作用力可输入有限元分析。
采用UGNX自带的机构运动分析模块MOTION提供机构的仿真分析功能可以极其方便的对设计方案进行模拟、验证、修改、优化,彻底改变传统机械设计方案需要组织研究团队进行复杂设计计算,制造物理机验证结果的冗长过程,缩短生产周期,节约设计成本。
一旦熟练的掌握了此方法,就可以在极短的时间内给出完整且极具说服力的设计方案。
接下来本文将结合模具实例介绍三维实体模具实现运动仿真的简单过程。
图1是一套拉延模具的三维示意图。
第一步:数据准备阶段在进行运动仿真模拟之前我们需要对已经设计好的三维模具进行简单的数据整理:由于模具设计工程师大都习惯按照最终工作状态来开展设计,然而进行运动仿真时我们一般都习惯于从非工作状态开始进行。
这步操作很简单:假设这套模具在非工作状态所有的上模内容需要沿着Z轴正方向移动1000mm,压边圈组件的工作行程是120mm(需要沿着Z轴正方向移动120mm)。
那么我们按着要求移动相关实体模型到指定位置即可。
移动前后效果见图1和图2。
图1 模具工作状态图2 模具非工作状态(打开状态)第二步:进入运动仿真模块数据准备完成以后我们首先要进入运动仿真模块才能进行相关操作。
UG拉伸总结

UG拉伸总结1. 引言UG(Unigraphics)是一款常用于CAD(计算机辅助设计)的软件。
在UG中,拉伸(Extrusion)是一种常见的建模操作,用于将二维轮廓沿着指定方向拉伸形成三维实体。
本文将对UG中的拉伸操作进行总结,包括拉伸类型、操作步骤、注意事项等。
2. 拉伸类型UG中的拉伸操作主要分为两种类型:盲拉伸和到指定距离拉伸。
2.1 盲拉伸盲拉伸是将二维轮廓无限延伸至指定方向的拉伸方式。
在UG中,盲拉伸通常有两种选择:沿法线拉伸和沿轴向拉伸。
•沿法线拉伸:拉伸操作将沿着法线方向(即与轮廓垂直)进行,使得轮廓呈现出立体形状。
•沿轴向拉伸:拉伸操作将沿轮廓所在的轴线方向进行,使得轮廓平面在延伸方向上按比例进行拉伸。
2.2 到指定距离拉伸到指定距离拉伸是将二维轮廓按照指定的距离进行拉伸的方式。
在UG中,可以通过指定拉伸距离或选择已存在的实体作为拉伸距离。
•指定拉伸距离:用户可以直接输入拉伸距离,UG将根据该距离对轮廓进行拉伸。
•选择已存在实体:用户可以选择已存在的实体作为拉伸距离,轮廓将沿该实体的延伸方向进行拉伸。
3. 拉伸操作步骤在UG中进行拉伸操作的步骤如下:1.打开UG软件,新建或打开一个模型文件。
2.选择要进行拉伸操作的二维轮廓。
在UG中,可以使用绘图工具创建轮廓,也可以导入已有的二维轮廓文件。
3.在功能区中选择“拉伸”工具或使用快捷键进行拉伸操作。
根据需要选择盲拉伸或到指定距离拉伸。
4.根据选择的拉伸类型,设置拉伸方向、距离等参数。
在盲拉伸中可以选择沿法线或沿轴向拉伸,而到指定距离拉伸则需要指定拉伸距离或选择已存在实体。
5.确认设置无误后,点击“确定”按钮或按下回车键进行拉伸操作。
6.检查拉伸结果,如有需要可以对拉伸后的实体进行进一步编辑和调整。
4. 注意事项在进行UG拉伸操作时,需要注意以下事项:•拉伸操作需要选择合适的拉伸类型和参数,以确保得到所需的模型形状。
•若盲拉伸方向不正确或距离设置错误,可能会导致模型变形或不符合预期。
ug建模流程
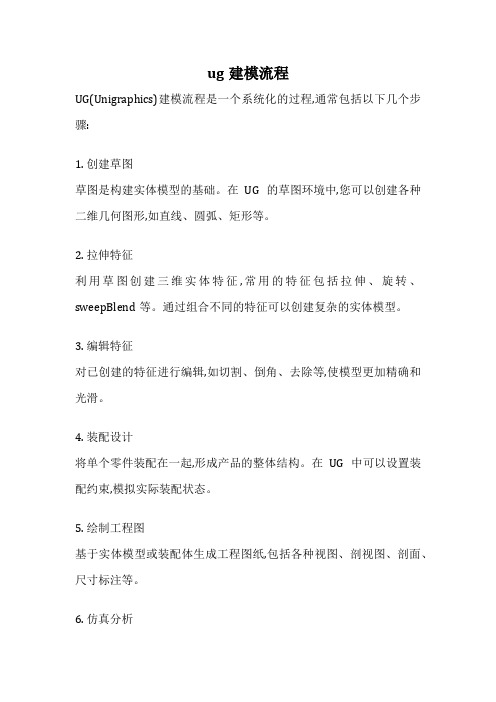
ug建模流程
UG(Unigraphics)建模流程是一个系统化的过程,通常包括以下几个步骤:
1. 创建草图
草图是构建实体模型的基础。
在UG的草图环境中,您可以创建各种二维几何图形,如直线、圆弧、矩形等。
2. 拉伸特征
利用草图创建三维实体特征,常用的特征包括拉伸、旋转、sweepBlend等。
通过组合不同的特征可以创建复杂的实体模型。
3. 编辑特征
对已创建的特征进行编辑,如切割、倒角、去除等,使模型更加精确和光滑。
4. 装配设计
将单个零件装配在一起,形成产品的整体结构。
在UG中可以设置装配约束,模拟实际装配状态。
5. 绘制工程图
基于实体模型或装配体生成工程图纸,包括各种视图、剖视图、剖面、尺寸标注等。
6. 仿真分析
利用UG的仿真模块对模型进行静力学分析、动力学分析、热分析等,优化设计。
7. 数据管理
使用UG的数据管理功能对模型数据进行组织和管理,实现版本控制和共享协作。
整个建模过程需要反复迭代和优化,直至满足设计要求。
掌握UG建模流程对于设计人员来说是必不可少的技能。
基于UG的汽车覆盖件拉延工艺设计
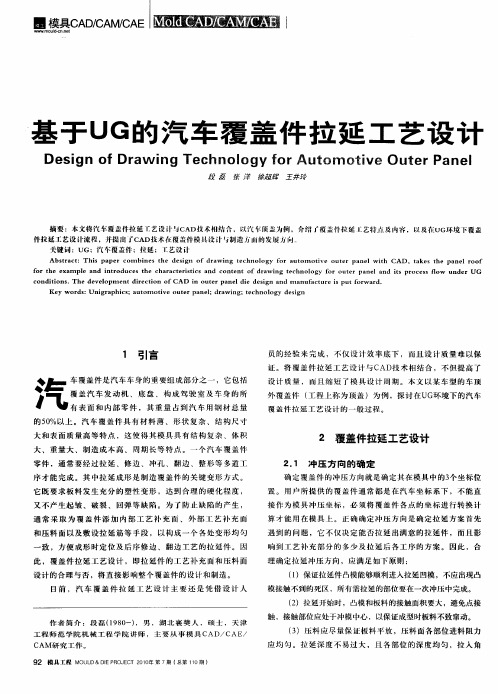
理 确 定 拉 延 冲 压 方 向 ,应 满 足 如下 原 则 : ( )保证 拉 延 件 凸模 能够 顺 利 进入 拉 延 凹模 ,不应 出现 凸 1
模 接 触 不到 的 死区 ,所有 需拉 延 的 部位 要 在一 次 冲压 中 完成 。 () 拉延 开 始 时 , 凸模 和板 料 的接 触 面积 要 大 ,避 免 点接 2
响 到 工 艺 补 充 部 分 的 多 少 及 拉 延 后 各 工 序 的 方 案 。 因 此 ,合
致 , 方 便 成 形 时 定 位 及 后 序 修 边 、 翻 边 工 艺 的 拉 延 件 。 因
此 ,覆 盖 件 拉 延 工 艺 设 计 , 即拉 延 件 的 工 艺 补 充 面 和 压 料 面 设 计 的 合 理 与 否 ,将 直 接 影 响 整 个 覆 盖 件 的设 计 和 制 造 。 目 前 ,汽 车 覆 盖 件 拉 延 工 艺 设 计 主 要 还 是 凭 借 设 计 人
序 才 能 完 成 。其 中 拉 延 成 形 是 制 造 覆 盖 件 的 关 键 变 形 方 式 。
2 覆盖件拉延工艺设计
2 1 冲 压 方 向 的确 定 .
确 定 覆 盖 件 的 冲 压 方 向 就 是 确 定 其 在 模 具 中 的 3 坐 标 位 个
它 既 要 求 板 料 发 生 充 分 的 塑 性 变 形 ,达 到 合 理 的 硬 化 程 度 ,
又 不 产 生 起 皱 、 破 裂 、 回 弹 等 缺 陷 。为 了防 止 缺 陷 的 产 生 ,
置 。 用 户 所 提 供 的 覆 盖 件 通 常 都 是 在 汽 车 坐 标 系下 ,不 能 直
接 作 为 模 具 冲 压 坐 标 ,必 须 将 覆 盖 件 各 点 的 坐 标 进 行 转 换 计 算 才 能 用 在 模 具 上 。 正 确 确 定 冲 压 方 向 是 确 定 拉 延 方 案 首 先
ug模具设计教程实例
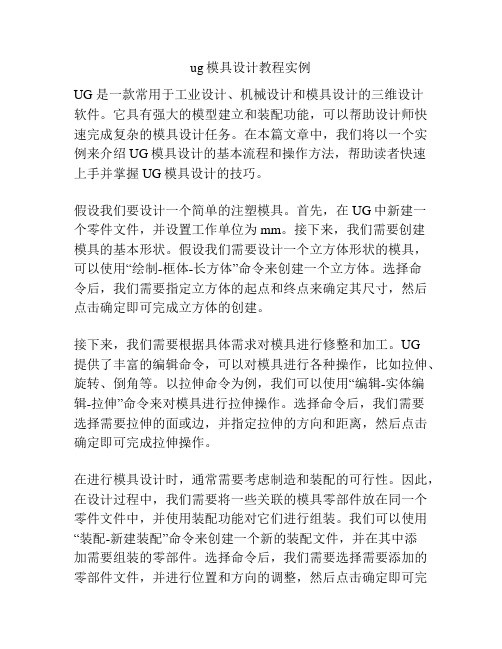
ug模具设计教程实例UG 是一款常用于工业设计、机械设计和模具设计的三维设计软件。
它具有强大的模型建立和装配功能,可以帮助设计师快速完成复杂的模具设计任务。
在本篇文章中,我们将以一个实例来介绍UG模具设计的基本流程和操作方法,帮助读者快速上手并掌握UG模具设计的技巧。
假设我们要设计一个简单的注塑模具。
首先,在UG中新建一个零件文件,并设置工作单位为mm。
接下来,我们需要创建模具的基本形状。
假设我们需要设计一个立方体形状的模具,可以使用“绘制-框体-长方体”命令来创建一个立方体。
选择命令后,我们需要指定立方体的起点和终点来确定其尺寸,然后点击确定即可完成立方体的创建。
接下来,我们需要根据具体需求对模具进行修整和加工。
UG提供了丰富的编辑命令,可以对模具进行各种操作,比如拉伸、旋转、倒角等。
以拉伸命令为例,我们可以使用“编辑-实体编辑-拉伸”命令来对模具进行拉伸操作。
选择命令后,我们需要选择需要拉伸的面或边,并指定拉伸的方向和距离,然后点击确定即可完成拉伸操作。
在进行模具设计时,通常需要考虑制造和装配的可行性。
因此,在设计过程中,我们需要将一些关联的模具零部件放在同一个零件文件中,并使用装配功能对它们进行组装。
我们可以使用“装配-新建装配”命令来创建一个新的装配文件,并在其中添加需要组装的零部件。
选择命令后,我们需要选择需要添加的零部件文件,并进行位置和方向的调整,然后点击确定即可完成零部件的组装。
完成模具的基本设计后,我们可以开始进行更详细的设计和优化。
UG 提供了丰富的分析和仿真功能,可以对模具进行各种性能和强度的分析。
我们可以使用“分析-应力分析”命令来对模具的强度进行分析。
选择命令后,我们需要指定需要分析的零部件,设置加载和边界条件,然后点击确定即可进行应力分析。
根据分析结果,我们可以对模具进行调整和优化,以满足设计要求。
在完成模具设计后,我们可以使用UG 提供的绘图功能生成模具图纸。
UG 自带了一套丰富的绘图工具和符号库,可以帮助设计师快速制作高质量的模具图纸。
拉延模三维绘图方法总结

拉延模绘图方法步骤准备工作:1、查找需要的线面:打开数模造型,显示拉延序工作层,包括型面、料片线、拉延筋中心线、模口线、工作坐标系辅助线(红绿蓝三条)。
2、导出新文件:利用File→Export→Part,将上述四项内容导出为一个新文件。
3、缝合型面及检查:将原DL工序文件关闭,打开新导出的文件,使用Insert→Combine body→Sew命令将型面缝合并检查(Analysis→Examine Geometry中的Face-Face Intersections 和Sheet Boundaries两项即可),如缝合好的型面上有红色边界线,则需对型面做修改,可用的命令有:桥接曲线,抽取曲线(面),桥接面,网格曲面,延伸片体,裁剪片体等。
4、重新定位:先将坐标系原点移动至工作坐标系辅助线上,Z轴负向对正冲压方向。
将补好的面及所的线全部选中,点击Edit→Transform→Reposition,将型面及相关线移动到坐标原点,然后保存并另存为新文件。
5、预设置:打开新文件,将图层设置好,把各线、面归入所属的层中,将过中心原点的三个基准面做出。
6、确定行程:将型面按前视图方位放置好,测量型面的垂直高度,圆整成整数。
一、凸模(分体式)1、做压料面:利用Insert→Design Feature→Extrude,把料片线沿冲压方向拉伸一定长度(上下超过型面曲面),点击Insert→Trim→Trim Body或Split命令将拉伸出来的实体用型面曲面裁剪或者分割开,保留下部。
用Extrude命令将模口线拉伸(若拉成实体则将侧表面抽取出来),把上步保留的实体用该曲面裁剪或分割,保留内部实体。
注意做裁剪或分割命令时,用来分割的片体任一边界都必须要超过被分割的实体,否则会出现“非歧义实体”的错误提示。
2、做凸模避让:将上步拉伸过的不用的曲线、曲面删除(若删不去则先去参),拉伸模口线(拉伸参数要求从0开始,另一边超过实体),得曲面,将曲面去参数,然后用Transform 命令将该曲面向-Z向平移50mm(也可40mm,根据技术协议),点击Insert→Offset/Scale→Thicken Sheet,将平移后的曲面前后各加厚10,即参数中将第一第二偏置设为+10,-10。
ug拉延设计教学

UG拉延设计教学UG拉延设计是一种用于零件设计和制造的三维建模技术。
UG是Unigraphics的简写,是一种专业的计算机辅助设计(CAD)软件,被广泛应用于汽车、机械、工业设计等领域。
UG拉延设计是UG软件的核心功能之一,它通过将二维轮廓转换为三维形状,来创建复杂的零件和组件。
UG拉延设计的主要目的是在制造过程中实现高效率、可靠性和成本效益。
UG拉延设计的基本原理是通过拉伸操作在二维轮廓上创建材料的增加。
该过程通常包括以下几个步骤:1. 创建草图:首先,在UG软件中创建一个包含所需轮廓的草图。
这个轮廓可以是任何形状,如圆形、矩形或自定义形状。
2. 拉伸操作:将草图拉伸为所需的长度和形状。
UG软件提供了多种拉伸选项,例如线性拉伸、圆锥形拉伸和倾斜拉伸等,以适应不同的需求。
3. 添加特征:在拉伸操作之后,可以根据具体要求添加附加特征,如圆角、倒角、孔洞等。
这些特征可以通过UG软件的其他功能来实现,并且可以在整个设计过程中进行修改和调整。
UG拉延设计的优势在于其灵活性和可扩展性。
UG软件提供了许多高级功能,如草图编辑、特征建模、实体联接等,以帮助设计师更好地完成设计任务。
此外,UG拉延设计还具有以下几个重要的优点:1. 高效率:UG软件提供了许多自动化工具和快捷键,可以大大提高设计师的工作效率。
通过使用UG拉延设计,设计师可以在短时间内创建复杂的零件和组件。
2. 可靠性:UG拉延设计的工作流程经过多年的发展和验证,已经成为一种可靠的设计方法。
通过使用UG软件进行设计,设计师可以减少错误和缺陷的发生,并提高最终产品的质量。
3. 成本效益:UG软件是一种成本效益高的CAD工具。
与传统的设计方法相比,使用UG软件设计可以减少开发和制造的时间和成本。
UG软件还提供了模拟和分析功能,可以帮助设计师在设计阶段评估和改进产品性能。
UG拉延设计在多个行业中得到了广泛的应用。
在汽车行业,UG 拉延设计被用于创建汽车零件和车身结构。
- 1、下载文档前请自行甄别文档内容的完整性,平台不提供额外的编辑、内容补充、找答案等附加服务。
- 2、"仅部分预览"的文档,不可在线预览部分如存在完整性等问题,可反馈申请退款(可完整预览的文档不适用该条件!)。
- 3、如文档侵犯您的权益,请联系客服反馈,我们会尽快为您处理(人工客服工作时间:9:00-18:30)。
Φ15 深20
(4)电器路位置
(5)模具防反
(6)防护板运输连接板
11 检查干涉和薄弱处
利用UG中的section命令和干涉检查软件检查 模具干涉处和过薄过厚处.
(5) 布置定位键
7压边圈工作部分
(1)布置调压垫
(2)布置墩死垫
此制件产品在分模线以内,并且客 户要求墩死垫与调压垫对齐
(3)布置定位装置
自动线需布 置传感器
(4)布置限程装置
单动拉延模用退料螺钉限程
(5)设计气顶接柱
根据气垫顶起高度,压边圈行程,压 边圈底面到机床的距离可以确定气 顶接柱的高度此高度限制条件为:气 顶接柱最高高度=2X接柱直径,如 不能满足限制条件则要将气顶接柱做 加强处理或者加接杆
模具左右侧挖夹持孔
减重孔按照客户提供标准挖,如客 户没具体要求,按照TS标准做 流水孔为Φ40的圆孔,保证每个底 空都不积水 过线孔保证每个底空都贯通
10 设计任务书及客户要求
(1)压板槽、上模快卡、下模快速定位的要求
压板槽
上模快夹
(2)气顶接柱加垫和气顶躲空要求
(3)键槽和加工基准孔
要给螺钉留足 取放空间,一 般要140mm 高度空间
背部倒角 60°便于 清沙
(3)打螺钉位置 沿凸模轮廓线均匀布置,并校核受力
(4)凸模起吊布置
起吊有2种形式: (1)起吊螺纹孔(2)铸入式螺孔套 具体哪种形式看客户要求 1起吊位置 起吊和翻转的对角线交点要与凸模重 心重合,保证在同一高度 2起吊螺纹孔的加工面不要凸出分模线 3铸入式螺孔套要保证周围壁厚
8确定模具长宽及端头
(1)将做好的凸凹模及压边圈工作部分装配入标准模版
(2)调整模架装配
选择tools菜单下的expressions调整模具闭合高、下模基准高、模具长 宽、压边圈行程、气垫行程
(3)调整吊耳起重棒大小及上下模压边圈高度
(4)调整导腿长宽及导板安装位置
•导腿长度至少占整体宽度的1/3,最好能做到2/5左右
单要分析各部分,分模线、坯料线、拉延后坯 料线、重力坯料线、拉延筋、到底标记、左右标记、CH 孔,有时还有弹顶销、穿刺孔和破裂刀位置 分模线决定了凸模的外圈轮廓大小 坯料线决定了压料面的大小 从拉延前后坯料线可以看出板料在压料面上的流入情况 重力坯料线决定了定位板定位位置和高度 拉延筋可以控制板料的流入量 到底标记用来检测是否拉伸到位(设计在废料区) 左右标记是产品左右件的标识,来实现焊装白车身的目的 CH孔是在拉延(序)模上的拉延件上冲制的两个模具制造 调试用的研模(定位)工艺孔。是带件研合各序模具型面 (和形状)的基准
至此凸凹模压边圈工作面层部分完毕
6凸模工作部分 (1)导板的安装
此制件压边圈行程为120mm,导板行程至少180mm,故选择200mm长导板,位 置如图所示,导板安装面要在分模线以外3~5mm,便于加工
L l L/6<l<L/4
(2)凸模螺钉台 为固定凸模要设计螺钉安装台,一般为内嵌式,大小为50mmX50mm, 高度为5mm或10mm
4暂定基准高
根据机床对操作高的要求 自动线看是否要求前后序操作高一致或是 浮动范围
5凸凹模及压边圈工作面层的设计
(1)用sew命令缝面
(2)结果有报错
(3)对报错区域面进行处理
(4)得到缝好的曲面
(5)拉伸一长方体检查缝好的面是否可以裁体,如可以则 进入下一步骤
(6)用缝好的面在Z正负方向各偏置60得到2个面
•导腿宽度根据模具宽度而定,一般遵循下表
•导腿导板保证上模触料时已 导入30mm即可,通常使用 125mm长导板即可满足要求, 保证导腿上所有导板同一安 装高度,同时刃入,稳定性 好
9 布筋、挖夹持孔、减重孔及流水孔过线孔
调压垫墩死垫下必有筋,受力部必 有筋支撑
凸凹模分模线内加强筋必对应
(7)用分模线拉伸出一个柱体,用缝好的面和向Z-方向偏 置的面裁出凸模面层,用分模线做出随型筋
(8)用坯料线向外侧偏置20mm,用偏置后的曲线拉伸出一 个长方体,用型面和沿Z+偏置面裁出凹模面层,用分模线向 内外各偏25mm做出随型筋
(9)将做完凹模余下的实体用Z-偏置面裁剪得到压边圈型 面,用分模线拉伸实体,并将边界扩大3mm,布尔减得到压 边圈型面
2 确认拉延模行程和气顶位置
验证工艺卡所给行程。由工艺卡得知此制件压边力需80T, 根据标准按每个气顶提供4T的力计算,最少需要20个,再加 上安全个数4个,需要24个气顶,沿分模线一周共可以布置 28个气顶。
3 确定导向形式
根据制件形状确定模具的导向形式, 大 致分为外导向拉延,内导向拉延,四角 导向拉延