精编【工艺流程】电厂工艺流程图
火电厂简易工艺流程;
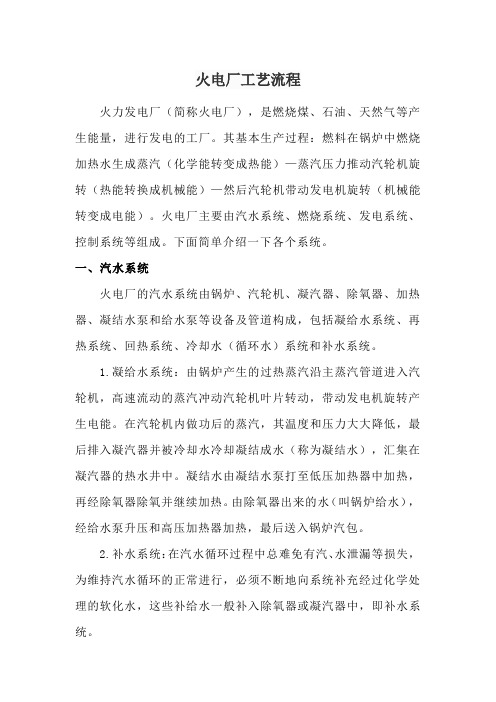
火电厂工艺流程火力发电厂(简称火电厂),是燃烧煤、石油、天然气等产生能量,进行发电的工厂。
其基本生产过程:燃料在锅炉中燃烧加热水生成蒸汽(化学能转变成热能)—蒸汽压力推动汽轮机旋转(热能转换成机械能)—然后汽轮机带动发电机旋转(机械能转变成电能)。
火电厂主要由汽水系统、燃烧系统、发电系统、控制系统等组成。
下面简单介绍一下各个系统。
一、汽水系统火电厂的汽水系统由锅炉、汽轮机、凝汽器、除氧器、加热器、凝结水泵和给水泵等设备及管道构成,包括凝给水系统、再热系统、回热系统、冷却水(循环水)系统和补水系统。
1.凝给水系统:由锅炉产生的过热蒸汽沿主蒸汽管道进入汽轮机,高速流动的蒸汽冲动汽轮机叶片转动,带动发电机旋转产生电能。
在汽轮机内做功后的蒸汽,其温度和压力大大降低,最后排入凝汽器并被冷却水冷却凝结成水(称为凝结水),汇集在凝汽器的热水井中。
凝结水由凝结水泵打至低压加热器中加热,再经除氧器除氧并继续加热。
由除氧器出来的水(叫锅炉给水),经给水泵升压和高压加热器加热,最后送入锅炉汽包。
2.补水系统:在汽水循环过程中总难免有汽、水泄漏等损失,为维持汽水循环的正常进行,必须不断地向系统补充经过化学处理的软化水,这些补给水一般补入除氧器或凝汽器中,即补水系统。
3.冷却水(循环水)系统:为了将汽轮机中做功后排入凝汽器中的乏汽冷凝成水,需由循环水泵从凉水塔抽取大量的冷却水送入凝汽器,冷却水吸收乏汽的热量后再回到凉水塔冷却,冷却水是循环使用的。
这就是冷却水或循环水系统。
二、燃烧系统燃烧系统是由输煤、磨煤、粗细分离、排粉、给粉、锅炉、除尘、脱硫等组成。
1.运煤:电厂的用煤量很大,主要靠铁路运输,约占铁路全部运输量的40%。
为保证电厂安全生产,一般要求电厂贮备十天以上的用煤量。
2.磨煤:由皮带输送机从煤场,通过电磁铁、碎煤机初步筛选,然后送到煤仓间的煤斗内,再经过给煤机进入磨煤机进行磨粉,磨好的煤粉通过空气预热器来的热风,将煤粉打进分离器,分离器将合格的煤粉(不合格的煤粉送回磨煤机),经过排粉机送至煤粉仓。
电厂生产工艺流程图介绍

燃煤发电厂主要生产过程是:1、输煤及燃运系统:运输→卸煤装置→煤场→碎煤机→皮带→原煤仓;储存在储煤场(或储煤罐)中的原煤由输煤设备从储煤场送到锅炉的原煤斗中,再由给煤机送到磨煤机中磨成煤粉。
2、制粉系统:原煤仓→给煤机→磨煤机→细粉分离器→燃烧器→炉膛;煤粉由一次风送到锅炉本体的喷燃器,由喷燃器喷到炉膛内燃烧。
3、风烟系统:(风)吸风口→冷风道→送风机→暖风器→空预器→热风道→磨煤机→燃烧器→炉膛;(烟)炉膛→屏过→对流过热器→省煤器→空预器→除尘器→引风机→烟囱→大气。
灰渣系统:(炉渣)炉膛冷灰斗→除渣装置→冲灰沟→灰渣泵→输灰管→灰场。
(飞灰)除尘器→集灰斗→除灰装置→运灰车→灰加工厂。
4、燃烧的煤粉放出大量的热能将炉膛四周水冷壁管内的水加热成汽水混合物。
5、锅炉汽水系统:主给水管→给水操作台→省煤器→汽包→下降管→下联箱→水冷壁→汽包→过热器→锅炉集汽联箱出口。
混合物被锅炉汽包内的汽水分离器进行分离:分离出的水经下降管送到水冷壁管继续加热;分离出的蒸汽送到过热器,加热成符合规定温度和压力的过热蒸汽,经管道送到汽轮机作功。
6、主蒸汽系统及再热蒸汽系统:(主蒸汽)锅炉集汽联箱→主蒸汽管→汽机自动主汽门之前。
(再热蒸汽)汽机高压缸出口→再热器冷段管→再热器→再热器热段管→汽机中压缸进口过热蒸汽在汽轮机内作功推动汽轮机旋转,汽轮机带动发电机发电。
7、发电机发出的三相交流电通过发电机端部的引线经变压器升压后引出送到电网。
8、主凝结水系统:凝汽器→凝结水泵→轴封冷却器→低加→除氧器。
除氧器系统:除氧器及其相连的所有管路和附件(安全门,水位计等)。
主给水系统:除氧水箱下水管→低压给水管→给水泵→高压给水管→高加→主给水管。
、回热抽汽系统和加热器疏水系统:汽机抽汽管路→各回热加热器(高加、低加、除氧器)→疏水管路→疏水回收设备。
在汽轮机内作完功的过热蒸汽被凝汽器冷却成凝结水,凝结水经凝结泵送到低压加热器加热,然后送到除氧器除氧,再经给水泵送到高压加热器加热后,送到锅炉继续进行热力循环。
火电厂生产工艺流程图

冷却塔的作用是将挟带废热的冷却水在塔内与空气进行热交换,使废热传输给空气并散人大气。
如图1 所示的火电厂为例,锅炉会将水加热成高温高压蒸汽;推动汽轮机(2)作功使发电机(3)发电。
经汽轮机作功后的乏汽排入凝汽器(4),与冷却水进行热交换凝结成水,再用水泵打回锅炉循环使用。
这一热力循环过程中;乏汽的废热在凝汽器中传给了冷却水,使水温升高.挟带废热的冷却水,在冷却塔(5)中将其热量传给空气(6),从塔筒出口排人大气。
在冷却塔内冷却过的水变为低温水,水泵将其再送入凝汽器,循环使用。
前一循环为锅炉中水的循环,后一循环为冷却水的循环。
冷却塔中水和空气的热交换方式之一是,流过水表面的空气与水直接接触,通过接触传热和蒸发散热,把水中的热量传输给空气。
用这种冷却方式的称为湿式冷却塔(简称湿塔)。
湿塔的热交换效率高,水被冷却的极限温度为空气的湿球温度。
但是,水因蒸发而造成损耗;蒸发又依循环的冷却水含盐度增加,为了稳定水质,必须排掉一部分含盐度较高的水;风吹也会造成水的损失。
这些水的亏损必须有足够的新水持续补充,因此,湿塔需要有补给水的水源。
缺水地区,补充水有困难的情况下;只能采用干式冷却塔(简称干塔或空冷塔)。
干塔中空气与水(也有空气与乏汽)的热交换;是通过由金属管组成的散热器表面传热,将管内的水或乏汽的热量传输给散热器外流动的空气。
干塔的热交换效率比湿塔低,冷却的极限温度为空气的干球温度。
2.2 蒸发耗损量当冷却回水和空气接触而产生作用,把其水温降时,部分水蒸发会引起冷却回水之损耗,而其损耗量和入塔空气的湿球温度及流量有关,以数学表达式作如下说明:令:进水温度为T1℃,出水温度为T2℃,湿球温度为Tw,则*:R=T1-T2(℃)------------(1)式中:R:冷却水的温度差,对单位水量即是冷却的热负荷或制冷量Kcal/h 对式(1)可推论出水蒸发量的估算公式*:E=(R/600)×100% ------------ (2)式中:E----当温度下降R℃时的蒸发量,以总循环水量的百分比表示%,600-----考虑了各种散热因素之后确定之常数。
热电厂工艺流程

脱碳器图示及构造如图3-3-4:
第三章第二节 水化车间 图3-3-4 脱碳器构造图
第三章第三节 水化车间
阴床:如图3-3-5
作用:阴床内用OH-和 水中旳阴离子进行 互换,于水中旳 H+结合生成水, 从而到达水旳除盐 目旳后进入除盐水 箱贮存。
图3-3-5 阴床
第四节 汽机车间
第三章第四节 汽机车间 图3-4-5 冷凝塔构造图
第三章第四节 汽机车间
汽轮机:如图3-4-6 汽轮机是火力发电厂三大主要设备之一。它是以蒸汽为
工质,将热能转变为机械能旳高速旋转式原动机。它为发电 机旳能量转换提供机械能。
汽轮机旳工作原理:如图3-4-7 (1)冲动式汽轮机:具有一定压力和温度旳蒸汽首先在固定 不动旳喷嘴中膨胀加速,使蒸汽压力和温度降低,部分热能 变为动能。从喷嘴喷出旳高速汽流以一定旳方向进入装在叶 轮上旳动叶片流道,在动叶片流道中变化速度,产生作用力, 推动叶轮和轴转动,使蒸汽旳动能转变为轴旳机械能。 (2)反动式汽轮机:蒸汽流过喷嘴和动叶片时,蒸汽不但在 喷嘴中膨胀加速,而且在动叶片中也要继续膨胀,使蒸汽在 动叶片流道中旳流速提升。当由动叶片流道出口喷出时,蒸 汽便给动叶片一种反动力。动叶片同步受到喷嘴出口汽流旳 冲动力和本身出口汽流旳反动力。在这两个力旳作用下,动
670t/h大型) (3)按燃烧方式分类:悬浮燃烧锅炉、沸腾燃烧锅炉 (4)按循环方式分类:自然循环锅炉、强制循环锅炉、控制循环锅炉
第三章第二节 锅炉车间
过热器 汽包
省煤器
蒸发 受热 面
下降管
给水泵
联箱
自然循环锅炉
过热器 汽包
循环泵 省煤器
蒸发 受热 面
下降管
热电厂工艺流程图

平盘磨、碗式磨(如图3-1-4)、MPS 磨 / MPF 磨、E型磨 (3)高速磨煤机(>400 r/min): 风扇式磨煤机、 竖井磨煤机
上述一般可分成:直吹式制粉系统和储仓式制粉系统
图3-1-4碗式中速磨煤机
给水泵
联箱
控制循环锅炉
过热器 联箱
省煤器
蒸发 受热 面
给水泵 联箱
直流锅炉
图3-2-2 四种锅炉的示意图
第三章第二节 锅炉车间 图3-2-3 热电厂锅炉及燃烧器
第三章第二节 锅炉车间
汽包:如图3-2-4
能够承受汽包产生的空气压力和水位压力的一种工业设 备。接收省煤器来水,进行汽水分离,向循环水路供水, 向过热器输送饱和蒸汽。
第三章 热电厂工艺流程
➢第一节 燃运车间 ➢第二节 锅炉车间 ➢第三节 水化车间 ➢第四节 汽机车间
热电厂生产工艺流程可大致将全厂的生产环节分 为五个部分:机、炉、电、化、热(热网)。其中有 煤、水、汽及化学药品等原料或工质参与生产流程, 并通过工质的流动以做功或热传递的方式完成由燃料 向热(采暖)蒸汽(井口用)电(电动)转化的生产 任务,各系统相辅相成,缺一不可。现按照原料的流 向车间,逐一对热电厂工艺进行介绍。
• 烟气在锅炉内流动的过程中,热量传递方式为:在炉膛中以辐射 方式将热量传给水冷壁;在炉膛烟气出口处,以半辐射、半对流方 式将热量传给屏式过热器;在水平烟道和尾部烟道以对流方式传给 过热器、再热器、省煤器和空气预热器。
• 锅炉给水便经过省煤器、水冷壁、过热器变成过热蒸汽;并把汽轮 机高压汽缸做功后抽回的蒸汽变成再热蒸汽。
第三章第二节 锅炉车间
火电厂生产工艺流程图

冷却塔的作用是将挟带废热的冷却水在塔内与空气进行热交换,使废热传输给空气并散人大气。
如图1 所示的火电厂为例,锅炉会将水加热成高温高压蒸汽;推动汽轮机(2)作功使发电机(3)发电。
经汽轮机作功后的乏汽排入凝汽器(4),与冷却水进行热交换凝结成水,再用水泵打回锅炉循环使用。
这一热力循环过程中;乏汽的废热在凝汽器中传给了冷却水,使水温升高.挟带废热的冷却水,在冷却塔(5)中将其热量传给空气(6),从塔筒出口排人大气。
在冷却塔内冷却过的水变为低温水,水泵将其再送入凝汽器,循环使用。
前一循环为锅炉中水的循环,后一循环为冷却水的循环。
冷却塔中水和空气的热交换方式之一是,流过水表面的空气与水直接接触,通过接触传热和蒸发散热,把水中的热量传输给空气。
用这种冷却方式的称为湿式冷却塔(简称湿塔)。
湿塔的热交换效率高,水被冷却的极限温度为空气的湿球温度。
但是,水因蒸发而造成损耗;蒸发又依循环的冷却水含盐度增加,为了稳定水质,必须排掉一部分含盐度较高的水;风吹也会造成水的损失。
这些水的亏损必须有足够的新水持续补充,因此,湿塔需要有补给水的水源。
缺水地区,补充水有困难的情况下;只能采用干式冷却塔(简称干塔或空冷塔)。
干塔中空气与水(也有空气与乏汽)的热交换;是通过由金属管组成的散热器表面传热,将管内的水或乏汽的热量传输给散热器外流动的空气。
干塔的热交换效率比湿塔低,冷却的极限温度为空气的干球温度。
2.2 蒸发耗损量当冷却回水和空气接触而产生作用,把其水温降时,部分水蒸发会引起冷却回水之损耗,而其损耗量和入塔空气的湿球温度及流量有关,以数学表达式作如下说明:令:进水温度为T1℃,出水温度为T2℃,湿球温度为Tw,则*:R=T1-T2(℃)------------(1)式中:R:冷却水的温度差,对单位水量即是冷却的热负荷或制冷量Kcal/h 对式(1)可推论出水蒸发量的估算公式*:E=(R/600)×100% ------------ (2)式中:E----当温度下降R℃时的蒸发量,以总循环水量的百分比表示%,600-----考虑了各种散热因素之后确定之常数。
(工艺流程)电厂工艺流程图
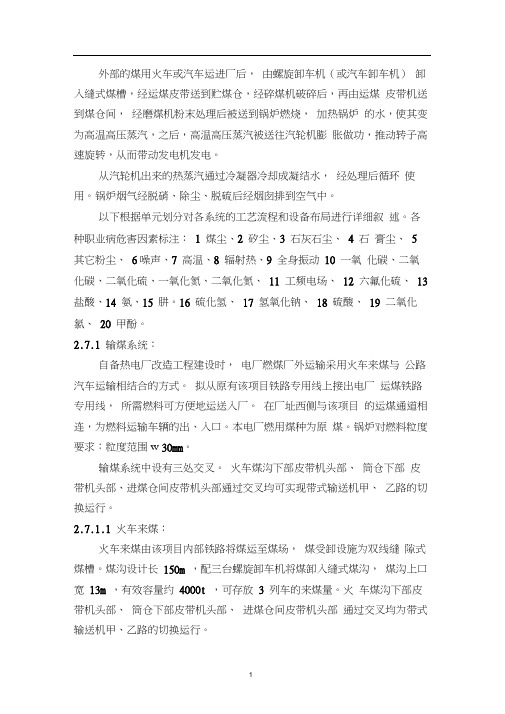
外部的煤用火车或汽车运进厂后,由螺旋卸车机(或汽车卸车机)卸入缝式煤槽,经运煤皮带送到贮煤仓,经碎煤机破碎后,再由运煤皮带机送到煤仓间,经磨煤机粉末处理后被送到锅炉燃烧,加热锅炉的水,使其变为高温高压蒸汽,之后,高温高压蒸汽被送往汽轮机膨胀做功,推动转子高速旋转,从而带动发电机发电。
从汽轮机出来的热蒸汽通过冷凝器冷却成凝结水,经处理后循环使用。
锅炉烟气经脱硝、除尘、脱硫后经烟囱排到空气中。
以下根据单元划分对各系统的工艺流程和设备布局进行详细叙述。
各种职业病危害因素标注:1 煤尘、2 矽尘、3 石灰石尘、4 石膏尘、5其它粉尘、6噪声、7 高温、8 辐射热、9 全身振动10 一氧化碳、二氧化碳、二氧化硫、一氧化氮、二氧化氮、11 工频电场、12 六氟化硫、13 盐酸、14 氨、15 肼。
16 硫化氢、17 氢氧化钠、18 硫酸、19 二氧化氯、20 甲酚。
2.7.1 输煤系统:自备热电厂改造工程建设时,电厂燃煤厂外运输采用火车来煤与公路汽车运输相结合的方式。
拟从原有该项目铁路专用线上接出电厂运煤铁路专用线,所需燃料可方便地运送入厂。
在厂址西侧与该项目的运煤通道相连,为燃料运输车辆的出、入口。
本电厂燃用煤种为原煤。
锅炉对燃料粒度要求:粒度范围w 30mm。
输煤系统中设有三处交叉。
火车煤沟下部皮带机头部、筒仓下部皮带机头部、进煤仓间皮带机头部通过交叉均可实现带式输送机甲、乙路的切换运行。
2.7.1.1 火车来煤:火车来煤由该项目内部铁路将煤运至煤场,煤受卸设施为双线缝隙式煤槽。
煤沟设计长150m ,配三台螺旋卸车机将煤卸入缝式煤沟,煤沟上口宽13m ,有效容量约4000t ,可存放3 列车的来煤量。
火车煤沟下部皮带机头部、筒仓下部皮带机头部、进煤仓间皮带机头部通过交叉均为带式输送机甲、乙路的切换运行。
2.7.1.2 汽车来煤汽车来煤为与大同路相连的该项目运煤通道将煤运至煤场。
汽车来煤采用自卸或机械卸车的方式将煤卸入地下缝式煤槽,煤槽上口宽8m ,长约94m ,有效容量约2500t 。
火电厂工艺流程图

火电厂工艺流程图火电厂工艺流程是指火力发电厂在发电过程中的主要步骤和流程。
下面是对火电厂工艺流程的一个简单描述:火电厂的工艺流程主要包括燃料供应、燃烧、锅炉产生蒸汽、蒸汽带动汽轮机发电、发电后处理以及废气处理等环节。
首先,火电厂需要获得燃料供应。
常用的燃料包括煤炭、油和天然气等。
这些燃料通过输送管道或火车运输到火电厂的燃料库存。
然后,燃料通过输送装置进入燃烧炉。
接下来,燃烧炉中的燃料被点火燃烧。
燃烧产生的高温气体通过锅炉的管道传送给锅炉。
在锅炉中,高温气体传热给水,使水转化为蒸汽。
这些高温气体中的污染物如二氧化硫和氮氧化物等也会被减少。
然后,锅炉产生的蒸汽通过管道输送到汽轮机。
蒸汽的压力和流速差异驱动汽轮机旋转。
汽轮机产生的机械能通过发电机转化为电能。
发电机产生的电能经过变压器升压后输送到主电网。
在发电后处理环节,锅炉中的废渣被清除。
废渣包括灰渣和烟气中的颗粒物。
灰渣通过设备收集起来,可以用于建筑材料的制造或者通过封存设施进行储存。
最后,对烟气中的污染物进行处理。
常用的处理方法包括电除尘和脱硫。
电除尘通过电场原理,将烟气中的细小颗粒物收集起来。
脱硫是通过添加化学剂或喷射气体来吸附和还原烟气中的二氧化硫。
火电厂工艺流程图主要包括燃料输送系统、锅炉系统、蒸汽和能量转换系统、发电系统和废气处理系统等。
燃料输送系统包括燃料供应和燃烧系统;锅炉系统由锅炉和烟气处理设备组成;蒸汽和能量转换系统包括蒸汽管道和汽轮机等;发电系统由发电机和变压器组成;废气处理系统包括废渣处理和气体净化设备等。
总的来说,火电厂工艺流程是指火力发电厂在发电过程中的主要步骤和环节。
通过对燃料供应、燃烧、锅炉产生蒸汽、蒸汽带动汽轮机发电、发电后处理以及废气处理等环节的描述,可以得到一个简单的火电厂工艺流程图。
- 1、下载文档前请自行甄别文档内容的完整性,平台不提供额外的编辑、内容补充、找答案等附加服务。
- 2、"仅部分预览"的文档,不可在线预览部分如存在完整性等问题,可反馈申请退款(可完整预览的文档不适用该条件!)。
- 3、如文档侵犯您的权益,请联系客服反馈,我们会尽快为您处理(人工客服工作时间:9:00-18:30)。
【工艺流程】电厂工艺流程图xxxx年xx月xx日xxxxxxxx集团企业有限公司Please enter your company's name and contentv外部的煤用火车或汽车运进厂后,由螺旋卸车机(或汽车卸车机)卸入缝式煤槽,经运煤皮带送到贮煤仓,经碎煤机破碎后,再由运煤皮带机送到煤仓间,经磨煤机粉末处理后被送到锅炉燃烧,加热锅炉的水,使其变为高温高压蒸汽,之后,高温高压蒸汽被送往汽轮机膨胀做功,推动转子高速旋转,从而带动发电机发电。
从汽轮机出来的热蒸汽通过冷凝器冷却成凝结水,经处理后循环使用。
锅炉烟气经脱硝、除尘、脱硫后经烟囱排到空气中。
以下根据单元划分对各系统的工艺流程和设备布局进行详细叙述。
各种职业病危害因素标注:1煤尘、2矽尘、3石灰石尘、4石膏尘、5其它粉尘、6噪声、7高温、8辐射热、9全身振动10一氧化碳、二氧化碳、二氧化硫、一氧化氮、二氧化氮、11工频电场、12六氟化硫、13盐酸、14氨、15肼。
16硫化氢、17氢氧化钠、18硫酸、19二氧化氯、20甲酚。
2.7.1输煤系统:自备热电厂改造工程建设时,电厂燃煤厂外运输采用火车来煤与公路汽车运输相结合的方式。
拟从原有该项目铁路专用线上接出电厂运煤铁路专用线,所需燃料可方便地运送入厂。
在厂址西侧与该项目的运煤通道相连,为燃料运输车辆的出、入口。
本电厂燃用煤种为原煤。
锅炉对燃料粒度要求:粒度范围≤30mm。
输煤系统中设有三处交叉。
火车煤沟下部皮带机头部、筒仓下部皮带机头部、进煤仓间皮带机头部通过交叉均可实现带式输送机甲、乙路的切换运行。
2.7.1.1火车来煤:火车来煤由该项目内部铁路将煤运至煤场,煤受卸设施为双线缝隙式煤槽。
煤沟设计长150m,配三台螺旋卸车机将煤卸入缝式煤沟,煤沟上口宽13m,有效容量约4000t,可存放3列车的来煤量。
火车煤沟下部皮带机头部、筒仓下部皮带机头部、进煤仓间皮带机头部通过交叉均为带式输送机甲、乙路的切换运行。
2.7.1.2汽车来煤汽车来煤为与大同路相连的该项目运煤通道将煤运至煤场。
汽车来煤采用自卸或机械卸车的方式将煤卸入地下缝式煤槽,煤槽上口宽8m,长约94m,有效容量约2500t。
拟设计有3台汽车卸车机,共9个货位,另有6个自卸车货位,煤槽下带式输送机配叶轮给煤机。
2.7.1.3原煤运输工艺火车煤沟的煤通过1号带式输送机、汽车煤槽的煤通过2号带式输送机分别与3号带式输送机相连,进入全厂运煤系统。
煤(汽车来煤、火车来煤)经卸煤沟进入运煤系统。
来煤通过1号甲(乙)带式输送机、汽车煤槽的煤通过2号甲(乙)带式输送机分别与3号带式输送机相连,进入全厂运煤系统。
原煤经3号甲(乙)带式输送机的煤、经4号甲(乙)带式输送机送至5号甲甲(乙)带式输送机(犁式卸料器)和除铁器,经6号可逆配仓输送机进入筒仓。
筒仓的煤经其下部设环式叶轮给煤机,经调配送给7号甲、乙带式输送机,再通过8号甲、乙带式输送机(带有除铁器)和盘式除铁器后进入滚轴筛。
滚轴筛出来的煤如粒度如不满足要求则进入环锤式碎煤机破碎,然后进入9号甲(乙)带式输送机,如粒度满足要求的煤直接进入9号甲(乙)带式输送机,此后再依次经10号甲(乙)带式输送机、11号甲(乙)带式输送机、犁煤卸料器(乙)进入原煤仓。
输煤工艺流程图见图2-3。
2.7.1.4输煤主要设备a.输煤设备:厂内运煤系统均由固定带式输送机组成。
带式输送机由二种带宽规格组成,煤沟至筒仓的1号~6号带式输送机,其胶带宽B=1200mm;筒仓下7号带式输送机至煤仓间9号带式输送机,其胶带宽B=1000mm。
b.输煤系统设三级除铁设施,除铁设备采用二级永磁带式除铁器,一级盘式除铁器。
带式除铁器安装在5号转运站及碎煤机室内,盘式除铁器安装在8号皮带机中部采光间内。
c.本工程输煤系统在9号带式输送机上的电子皮带秤计量装置。
d.筛分设备采用一级筛分一级破碎方案,选用滚轴筛,滚轴筛通过能力为600t/h,破碎设备选用环锤式碎煤机,碎煤机出力为400t/h,入料粒度≤350mm,出料粒度≤30mm。
当来煤粒度不需要破碎时,可经过旁路直接进入系统。
筛碎设备双路布置,一路运行,一路备用。
e.设置6个储煤筒仓,筒仓直径¢22m,每个筒仓容量为1×104t,可满足本期2×1080t/h锅炉最大连续蒸发量时燃用约9天。
筒仓下部向带式输送机配煤采用环式叶轮给煤机。
带式输送机向原煤仓配煤采用固定式双(单)侧可变槽角犁式卸料器完成。
输煤主要设备及布局见表2-11 。
表2-11 输煤系统主要设备及布局表2.7.2 燃烧系统破碎至≤30mm的煤由运输皮带输送至原煤仓内,经由连接在给煤机将原煤送入落煤管。
在混煤箱里,煤经过热风预干燥后,再由螺旋输送器送入磨煤机内,然后经旋转筒体内钢球的连续运动研磨成粉。
然后由给煤机将煤直接送入锅炉内。
锅炉所需的空气由送风机提供,锅炉燃烧所需的一次风、二次风均采用独立系统。
由一次风机提供并经空气预热器加热后的正压热一次风在磨煤机前下部的进风口与正压冷一次风混合进入磨煤机。
一次风与煤粉组成风粉混合物,经燃烧器喷入炉膛燃烧。
二次风系统的送风机采用室内、外吸风方式。
送风机出口的空气进入空气预热器加热,空气预热器出口的热风接至锅炉两侧的二次风大风箱进入燃烧器的各个二次风口,作为主要的助燃风。
锅炉燃烧产生的烟气,从炉膛出口出来后依次通过省煤器、脱硝系统和空气预热器后进入双室五电场除尘器,再由引风机引入锅炉脱硫系统脱硫后由烟囱排入大气。
锅炉产生的蒸汽一部分送入汽轮机发电,一部分送入热网系统供热,锅炉产生的灰渣进入锅炉除灰渣系统处理。
本工程设烟气脱硝系统。
烟气从炉膛出口通过尾部受热面,在省煤器出口烟气分两路进入SCR 脱硝装置进行脱硝,脱硝后的烟气再分别进三分仓空气预热器,然后通过烟道进入电气除尘器,再可调吸风机经烟囱排至大气。
本期工程二台炉合用一座高210m 钢筋混凝土烟囱。
燃烧工艺流程图见图2-4。
燃烧系统主要设备:每台锅炉设置3台双进双出钢球磨煤机,6台电子秤给煤机、6只圆筒钢结构原煤斗。
采用5台运行、1台备用的运行方式;每炉配2台单速离心式风机,配2台可调轴流式送风机、2台离心式密封风机。
配置2套双室五电场除尘器。
两台锅炉共用一座高210m的烟囱。
燃烧系统主要设备及布局见表2-12。
表2-12 锅炉燃烧系统主要设备及布局2.7.3 热力系统锅炉产生的高压蒸汽通过主蒸汽管道,到汽轮机前再分两根分别接到汽轮机高压缸左右侧主汽门的管道,蒸汽输入汽轮机高压缸内做功,推动汽轮机转子高速运转,带动发电机发电。
做功后的蒸汽通过冷再热蒸汽管道进入再热器再加热,再通过热再热蒸汽管道回到汽轮机中压缸做功。
从汽轮机低压缸排出的蒸汽,经排汽装置通过1根的管道,流向空冷凝汽器,凝结水经排汽装置联箱收集于凝结水箱中,通过凝结水泵送入中压精处理装置处理后送入轴封加热器、各级低压加热器,最后至除氧器。
凝结水再循环管道由轴封加热器后引出至排汽装置。
高压加热器疏水串联疏水至除氧器,低压加热器疏水串联疏水至排汽装置。
热力工艺流程见图2-5。
热力系统主要设备:热力系统按7级抽汽回热系统设计,配3台低压加热器,3台高压加热器,1台除氧器;每台机组配3台50%容量的电动调速给水泵,2台运行,1台备用。
给水泵出口都单独接至除氧器给水箱。
3台高压加热器和3台低压加热器正常疏水都采用逐级回流以利用疏水热量。
高压加热器疏水串联疏水至除氧器,低压加热器疏水串联疏水至排汽装置。
轴封加热器疏水单独回流入排汽装置,疏水管路设置多级水封。
真空系统中设置3台水环式真空泵用以抽取空冷凝汽器内不凝结而分离出的气体。
每台机组均设置高、低压两个辅助蒸汽联箱向机组提供在启动、停机、正常运行和甩负荷等工况下符合参数要求的蒸汽。
其汽源来自老厂高压辅助蒸汽联箱、四段抽汽、冷再热蒸汽。
热力系统设备布局见表2-13 。
表2-13 热力系统主要设备及其布局表热网生产工艺流程2.7.4热网站工艺本工程冬季是以供热为主、发电为辅的热电厂,本次在电厂内建热网首站,利用汽机抽汽加热外网供热热水。
本工程热网站为独立建筑,热网系统采用一级换热闭式循环、间接供热方式,以水为热媒。
热网循环水经热网循环水泵升压后,进入基加吸热,水温由60℃升至110℃,然后进入供热管网供给热用户。
本系统设有1台低压除氧器,由化学软化水箱来的补充水经软化水泵后进入低压除氧器,除氧水经热网补水泵进入热网循环泵入口的热网回水管道中循环。
热网疏水系统设有基加疏水泵,正常情况下,基加疏水返回到本机回热系统。
本次拟采用4台基本热网加热器设5台热网循环泵,其中一台备用,供水温度110℃,回水温度60℃,热网循环水量为8600t/h。
设有1台低压除氧器。
热网站生产工艺流程见图2-6。
2.7.5电气系统本工程两台机组,分别采用发电机-变压器-线路组接入厂外接入距电厂1km 和2km 的220kV 新总降和九降压。
采用两台370MVA 、220kV 三相主变压器,主变高压侧经绝缘母线套筒接入厂内220kV GIS ,低压侧通过离相封母接发电机出线套管。
高压侧采用全链式分相封闭母线,由发电机出线分支引出;低压侧采用共箱封闭母线,分别接入每台机组设置的两段6kV 母线。
每台机组低压工作厂用电动力配电中心(PC )分别按汽机和锅炉配置。
高压侧经绝缘母线套筒接入厂内110kV GIS 接入老厂的110kV 母线上,低压侧采用共箱封闭母线,分别“T ”接接入两台机组的两段6kV 母线。
电气及发电系统生产工艺流程见图2-7。
电气及发电系统主要设备及布局,见表2-14 。
表2-14 电气系统主要设备及布局2.7.6直接空冷系统采用直接空冷系统,单排管空冷凝汽器设计。
汽轮机排出的乏汽经由主排汽管道引出汽机房“A”列外,垂直上升至一定高度后,水平分管,再从水平分管分出支管,垂直上升,引至空冷凝汽器顶部。
蒸汽从空冷凝汽器上部联箱进入,与空气进行表面换热后冷凝。
进入空冷凝汽器的乏汽在轴流风机的作用下冷却成凝结水。
凝结水经空冷凝汽器下部的各单元凝结水管汇集至凝结水竖直总管,接至布置在汽机房内的排汽装置下部凝结水箱内。
通过凝结水泵打入凝结水凝结水精处理装置进行处理。
排汽主管道内的疏水通过疏水管道排至排汽装置下部的凝结水箱内。
直接空冷系统的风机均采用大直径的采用变频调速轴流风机。
每个空冷凝汽器单元拟配置一台轴流式风机,变频调速,每台机组共配置30台风机;两台机组共设清洗水泵一台。
本工程空冷凝汽器由顺流管束和逆流管束两部分组成。
按单排管空冷凝汽器进行设计,30个空冷凝汽器单元分6列垂直于A列布置,每列有5个空冷凝汽器单元,其中4个为顺流,1个为逆流,逆流空冷凝汽器放置在单元中部。
每台300MW机组共有300个管束。