罐式煅烧炉烘炉启动方案
烘炉方案
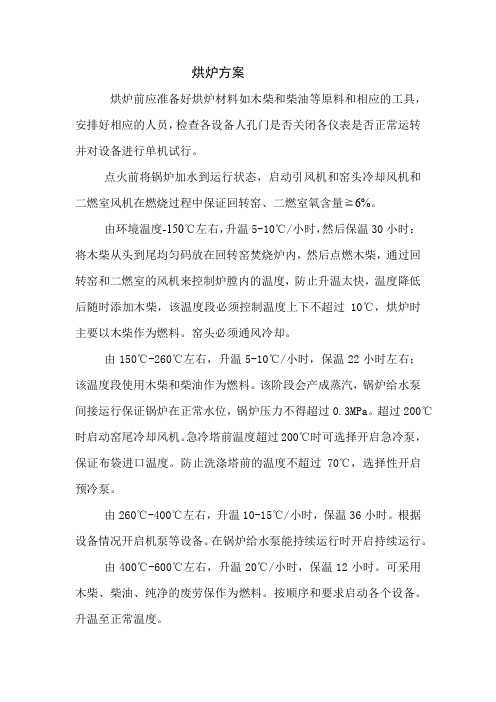
烘炉方案烘炉前应准备好烘炉材料如木柴和柴油等原料和相应的工具,安排好相应的人员,检查各设备人孔门是否关闭各仪表是否正常运转并对设备进行单机试行。
点火前将锅炉加水到运行状态,启动引风机和窑头冷却风机和二燃室风机在燃烧过程中保证回转窑、二燃室氧含量≧6%。
由环境温度-150℃左右,升温5-10℃/小时,然后保温30小时:将木柴从头到尾均匀码放在回转窑焚烧炉内,然后点燃木柴,通过回转窑和二燃室的风机来控制炉膛内的温度,防止升温太快,温度降低后随时添加木柴,该温度段必须控制温度上下不超过10℃,烘炉时主要以木柴作为燃料。
窑头必须通风冷却。
由150℃-260℃左右,升温5-10℃/小时,保温22小时左右;该温度段使用木柴和柴油作为燃料。
该阶段会产成蒸汽,锅炉给水泵间接运行保证锅炉在正常水位,锅炉压力不得超过0.3MPa。
超过200℃时启动窑尾冷却风机。
急冷塔前温度超过200℃时可选择开启急冷泵,保证布袋进口温度。
防止洗涤塔前的温度不超过70℃,选择性开启预冷泵。
由260℃-400℃左右,升温10-15℃/小时,保温36小时。
根据设备情况开启机泵等设备。
在锅炉给水泵能持续运行时开启持续运行。
由400℃-600℃左右,升温20℃/小时,保温12小时。
可采用木柴、柴油、纯净的废劳保作为燃料。
按顺序和要求启动各个设备。
升温至正常温度。
窑速为0-180℃,1/4圈每小时180-400℃小时,1/2圈每小时400-600℃小时,可维持转窑最低频率持续转窑烘炉的成败决定于温度能否按烘炉曲线进行控制。
升温降温时要保持平稳,防止温升太快损坏耐火材料。
温度保持阶段也要平稳,尽量减少波动。
升温曲线附后。
罐式煅烧炉天然气烘炉实践
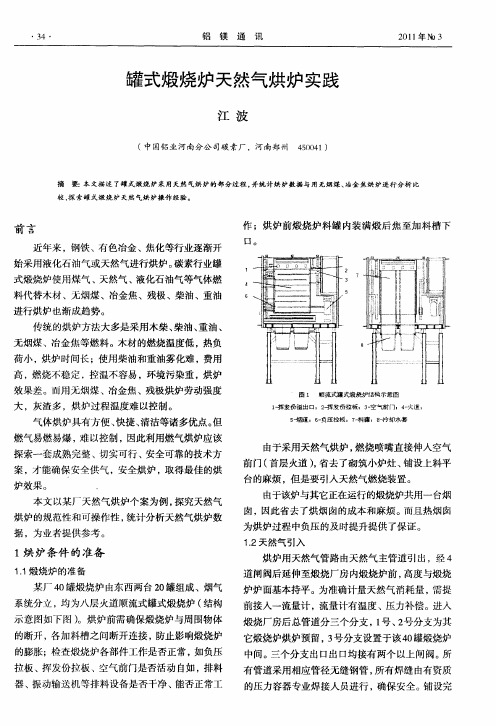
烘炉时 , 四周膨胀及位移需经常测量作为烘 炉 炉参考 ,主要以炉高膨胀量 的控制为主 ,如下表 :
表 4 炉 高膨胀数 据表
序 号 区 M温度 ℃ 区 膨胀 率% 班膨胀 嚣 m1 日膨胀 量 11 累计膨胀位 m i l 1 1 1 1
须对整个天然气管路及燃烧架进行充氮排除空气处 理 ,防止点火 困难或出现燃爆等危 险。 主管路天然气压力为 05 M a . p 左右 , 6 经过减压 阀减压 ,适 用于 煅烧 炉 烘炉 的压 力 为 0 01 0 . ~ .
系统分立 , 均为八层火道顺流式罐式煅烧炉 ( 结构
炉炉面基本持平 。为准确计量天然气消耗量 , 需提 前接入一流量计 , 流量计有温度、压力补偿 。进入 煅烧厂房后 总管道分三个分支 , 号 、 号分支为其 l 2 它煅烧炉烘炉预留, 号分支设置于该4 罐煅烧炉 3 0 中问。 三个分支 出口出口均接有两个 以上闸阀。 所 有管道采用相应管径无缝钢管 , 所有焊缝 由有资质
2 1 年№ 3 01
铝
镁
通
讯
・ 5・ 3
毕后 ,对管道进行检漏试 压。 另需制作简 易燃烧架 ,燃烧架 主管为无 缝钢 管 ,规格为 D 5 m 需要说 明的是 , N 0 m, 燃烧架以四 个或八个燃烧嘴为一组 ,每组长 2 m或 4 m,之 . 4 . 8
表 3 烘 炉 升 温 曲线
圈1 顺流式罐式煅烧炉结构示意囝
*t 发衔溢出口,2 g - - g - 发份拉板;3 气前 门;d 火遭  ̄ 一
5烟 遭 t 一 压拉 板 ,7 罐 , 8 却 水 套 — 6 负
探索一套成熟完整 、 切实可行 、 安全可靠的技术方
案, 才能确保安全供气 , 安全烘炉 , 取得最佳的烘
焙烧炉烘炉方案20241206

焙烧炉烘炉方案20241206焙烧炉是一种用于烘炉的设备,主要用于将物料进行加热处理,使其达到所需的烘炉效果。
下面是焙烧炉烘炉方案的详细介绍。
一、烘炉方案概述本次烘炉方案是基于焙烧炉的工作原理和要求,针对具体产品的烘炉需求,制定的一项详细操作方案。
方案主要包括焙烧炉的工作流程、参数调整、安全措施等内容。
二、焙烧炉工作流程1.准备工作:根据焙烧炉的要求和生产计划,安排好物料的加料和烘炉的调整工作。
同时,对焙烧炉进行检查,确保设备正常运行。
2.加料过程:将待烘炉的物料按要求投入焙烧炉的料斗中。
注意控制好物料的投入速度和数量,避免造成设备堵塞或过载。
3.参数调整:根据具体产品的要求,调整焙烧炉的温度、热量和时间等参数。
确保物料可以达到所需的烘炉效果。
4.烘炉过程:将参数调整好后,启动焙烧炉,开始进行烘炉过程。
期间需要对设备进行监控,确保其正常运行,并及时调整参数,以保证烘炉效果。
5.冷却过程:烘炉完成后,需要对物料进行冷却处理。
可以通过加入冷空气或水等方式进行冷却,以避免物料过热或产生其他不良后果。
6.取样检验:完成烘炉后,需要对物料进行取样检验。
根据检验结果,对烘炉过程的参数进行调整和优化,以提高烘炉效果。
7.清洗维护:每次烘炉完成后,需要对焙烧炉进行清洗和维护。
彻底清除物料残留和设备内部的污垢,以确保下次烘炉的正常运行。
三、参数调整在烘炉过程中,参数的调整对于烘炉效果至关重要。
以下是需要注意的几个参数:1.温度:根据具体产品的要求,调整焙烧炉的温度。
一般来说,温度要达到物料所需的最佳烘炉温度,但不能超过物料的耐受温度。
2.热量:通过调整燃料的供给和燃烧情况,控制焙烧炉的热量。
热量的控制需要根据物料的特性和要求进行调整,以达到所需的烘炉效果。
3.时间:烘炉的时间也是一个重要参数,它决定了物料在烘炉中停留的时间。
需要根据物料的特性和要求进行调整,以确保物料可以达到所需的烘炉效果。
四、安全措施在进行焙烧炉烘炉操作时,需要注意以下的安全措施:1.确保设备运行正常:在烘炉过程中,需要对设备进行监控,确保其正常运行和安全。
罐式煅烧炉烘炉
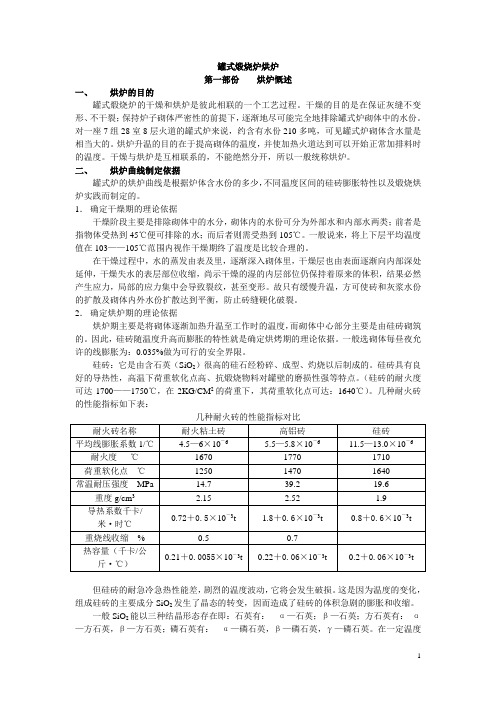
罐式煅烧炉烘炉第一部份烘炉慨述一、烘炉的目的罐式煅烧炉的干燥和烘炉是彼此相联的一个工艺过程。
干燥的目的是在保证灰缝不变形、不干裂;保持炉子砌体严密性的前提下,逐渐地尽可能完全地排除罐式炉砌体中的水份。
对一座7组28室8层火道的罐式炉来说,约含有水份210多吨,可见罐式炉砌体含水量是相当大的。
烘炉升温的目的在于提高砌体的温度,并使加热火道达到可以开始正常加排料时的温度。
干燥与烘炉是互相联系的,不能绝然分开,所以一般统称烘炉。
二、烘炉曲线制定依据罐式炉的烘炉曲线是根据炉体含水份的多少,不同温度区间的硅砖膨胀特性以及煅烧烘炉实践而制定的。
1.确定干燥期的理论依据干燥阶段主要是排除砌体中的水分,砌体内的水份可分为外部水和内部水两类;前者是指物体受热到45℃便可排除的水;而后者则需受热到105℃。
一般说来,将上下层平均温度值在103——105℃范围内视作干燥期终了温度是比较合理的。
在干燥过程中,水的蒸发由表及里,逐渐深入砌体里,干燥层也由表面逐渐向内部深处延伸,干燥失水的表层部位收缩,尚示干燥的湿的内层部位仍保持着原来的体积,结果必然产生应力,局部的应力集中会导致裂纹,甚至变形。
故只有缓慢升温,方可使砖和灰浆水份的扩散及砌体内外水份扩散达到平衡,防止砖缝硬化破裂。
2.确定烘炉期的理论依据烘炉期主要是将砌体逐渐加热升温至工作时的温度,而砌体中心部分主要是由硅砖砌筑的。
因此,硅砖随温度升高而膨胀的特性就是确定烘烤期的理论依据。
一般选砌体每昼夜允许的线膨胀为:0.035%做为可行的安全界限。
硅砖:它是由含石英(SiO2)很高的硅石经粉碎、成型、灼烧以后制成的。
硅砖具有良好的导热性,高温下荷重软化点高、抗煅烧物料对罐壁的磨损性强等特点。
(硅砖的耐火度可达1700——1750℃,在2KG/CM2的荷重下,其荷重软化点可达:1640℃)。
几种耐火砖的性能指标如下表:几种耐火砖的性能指标对比但硅砖的耐急冷急热性能差,剧烈的温度波动,它将会发生破损。
罐式煅烧炉烘炉技术分析
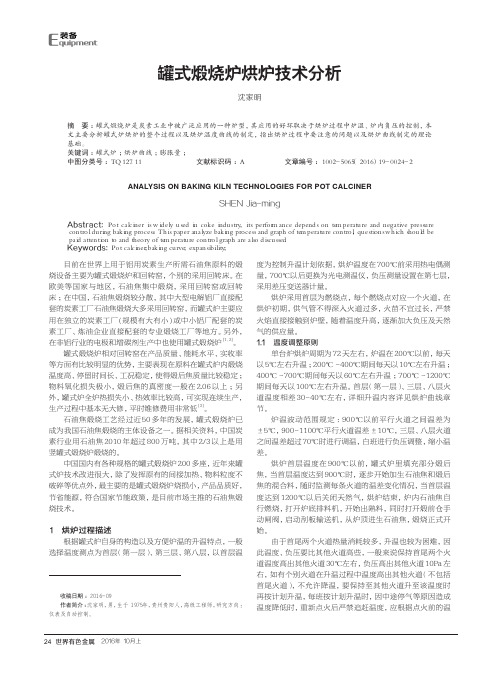
罐式煅烧炉烘炉技术分析沈家明(贵阳铝镁设计研究院,贵州 贵阳 550081)摘 要:罐式煅烧炉是炭素工业中被广泛应用的一种炉型,其应用的好坏取决于烘炉过程中炉温、炉内负压的控制,本文主要分析罐式炉烘炉的整个过程以及烘炉温度曲线的制定,指出烘炉过程中要注意的问题以及烘炉曲线制定的理论基础。
关键词:罐式炉;烘炉曲线;膨胀量;中图分类号:TQ127.11 文献标识码:A 文章编号:1002-5065(2016)19-0024-2ANALYSIS ON BAKING KILN TECHNOLOGIES FOR POT CALCINERSHEN Jia-ming(GuiYang Alaminum Magnesium Design and Research Institute,Guiyang 550081,China)Abstract: Pot calciner is widely used in coke industry, its performance depends on temperature and negative pressure control during baking process. This paper analyze baking process and graph of temperature control, questions which should be paid attention to and theory of temperature control graph are also discussed. Keywords: Pot calciner;baking curve; expansibility;目前在世界上用于铝用炭素生产所需石油焦原料的煅烧设备主要为罐式煅烧炉和回转窑,个别的采用回转床。
在欧美等国家与地区,石油焦集中煅烧,采用回转窑或回转床;在中国,石油焦煅烧较分散,其中大型电解铝厂直接配套的炭素工厂石油焦煅烧大多采用回转窑,而罐式炉主要应用在独立的炭素工厂(规模有大有小)或中小铝厂配套的炭素工厂、炼油企业直接配套的专业煅烧工厂等地方。
罐式煅烧炉流程

罐式煅烧炉流程下载温馨提示:该文档是我店铺精心编制而成,希望大家下载以后,能够帮助大家解决实际的问题。
文档下载后可定制随意修改,请根据实际需要进行相应的调整和使用,谢谢!并且,本店铺为大家提供各种各样类型的实用资料,如教育随笔、日记赏析、句子摘抄、古诗大全、经典美文、话题作文、工作总结、词语解析、文案摘录、其他资料等等,如想了解不同资料格式和写法,敬请关注!Download tips: This document is carefully compiled by theeditor.I hope that after you download them,they can help yousolve practical problems. The document can be customized andmodified after downloading,please adjust and use it according toactual needs, thank you!In addition, our shop provides you with various types ofpractical materials,such as educational essays, diaryappreciation,sentence excerpts,ancient poems,classic articles,topic composition,work summary,word parsing,copy excerpts,other materials and so on,want to know different data formats andwriting methods,please pay attention!罐式煅烧炉的工作流程详解罐式煅烧炉,作为一种特殊的热处理设备,广泛应用于化工、冶金、建材等行业,尤其在精细化工和新材料领域中起着至关重要的作用。
罐式煅烧炉烘炉方法探讨

罐式煅烧炉烘炉方法探讨陈 杰(贵阳铝镁设计研究院有限公司,贵州 贵阳 550081)摘 要:本文介绍了罐式煅烧炉烘炉的目的,分析升温曲线的制定原则,并对烘炉过程中负压、温度以及弹簧的调节进行探讨,对今后罐式炉的烘炉提供借鉴。
关键词:罐式煅烧炉;烘炉;升温曲线;温度;负压中图分类号:TQ127.11;TQ054 文献标识码:A 文章编号:1002-5065(2019)08-0219-2Discussion on drying method of pot calcinerCHEN Jie(Guiyang Aluminum Magnesium Design & Research Institute Co., Ltd.,Guiyang 550081,China)Abstract: This paper introduces the purpose of drying pot calciner, analyses the principle of setting the heating curve, and probes into the adjustment of negative pressure, temperature and spring in the drying process, so as to provide reference for the future drying pot calciner.Keywords: pot calciner; baking furnace; heating curve; temperature; negative pressure罐式煅烧炉作为炭素生产主要设备之一,具有煅烧质量稳定,炭质烧损少,无外加燃料煅烧石油焦等优点[1]。
煅烧是煅烧炉将生石油焦在隔绝空气的情况下进行间接加热,除去生石油焦中的水分和挥发份,使石油焦真密度和导电性增加的过程。
煅烧炉性能的优劣,直接影响煅后焦的质量和产能,而影响煅烧炉性能的关键一步就是烘炉启动。
烘炉的方案及具体步骤
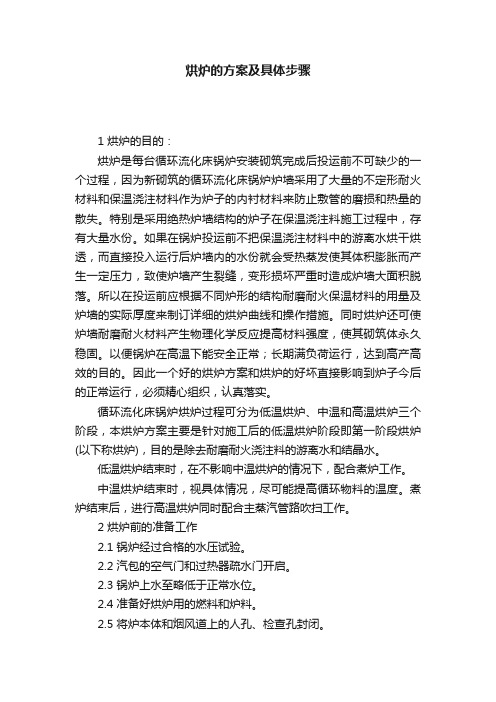
烘炉的方案及具体步骤1 烘炉的目的:烘炉是每台循环流化床锅炉安装砌筑完成后投运前不可缺少的一个过程,因为新砌筑的循环流化床锅炉炉墙采用了大量的不定形耐火材料和保温浇注材料作为炉子的内衬材料来防止敷管的磨损和热量的散失。
特别是采用绝热炉墙结构的炉子在保温浇注料施工过程中,存有大量水份。
如果在锅炉投运前不把保温浇注材料中的游离水烘干烘透,而直接投入运行后炉墙内的水份就会受热蒸发使其体积膨胀而产生一定压力,致使炉墙产生裂缝,变形损坏严重时造成炉墙大面积脱落。
所以在投运前应根据不同炉形的结构耐磨耐火保温材料的用量及炉墙的实际厚度来制订详细的烘炉曲线和操作措施。
同时烘炉还可使炉墙耐磨耐火材料产生物理化学反应提高材料强度,使其砌筑体永久稳固。
以便锅炉在高温下能安全正常;长期满负荷运行,达到高产高效的目的。
因此一个好的烘炉方案和烘炉的好坏直接影响到炉子今后的正常运行,必须精心组织,认真落实。
循环流化床锅炉烘炉过程可分为低温烘炉、中温和高温烘炉三个阶段,本烘炉方案主要是针对施工后的低温烘炉阶段即第一阶段烘炉(以下称烘炉),目的是除去耐磨耐火浇注料的游离水和结晶水。
低温烘炉结束时,在不影响中温烘炉的情况下,配合煮炉工作。
中温烘炉结束时,视具体情况,尽可能提高循环物料的温度。
煮炉结束后,进行高温烘炉同时配合主蒸汽管路吹扫工作。
2 烘炉前的准备工作2.1 锅炉经过合格的水压试验。
2.2 汽包的空气门和过热器疏水门开启。
2.3 锅炉上水至略低于正常水位。
2.4 准备好烘炉用的燃料和炉料。
2.5 将炉本体和烟风道上的人孔、检查孔封闭。
2.6 参与烘炉人员应熟悉烘炉工艺及锅炉运行规程。
2.7 绘制烘炉曲线图(耐火材料厂家提供)。
3 锅炉烘炉的必备条件3.1水压试验完成。
3.2排气和放水管道已达到正常使用条件。
3.3所有水和蒸汽管道吊架已正确安装完毕。
3.4烟道、风道门孔安装完毕。
3.5吹灰器孔临时性封堵。
3.6锅炉本体保温完毕。
罐式煅烧炉10步操作法
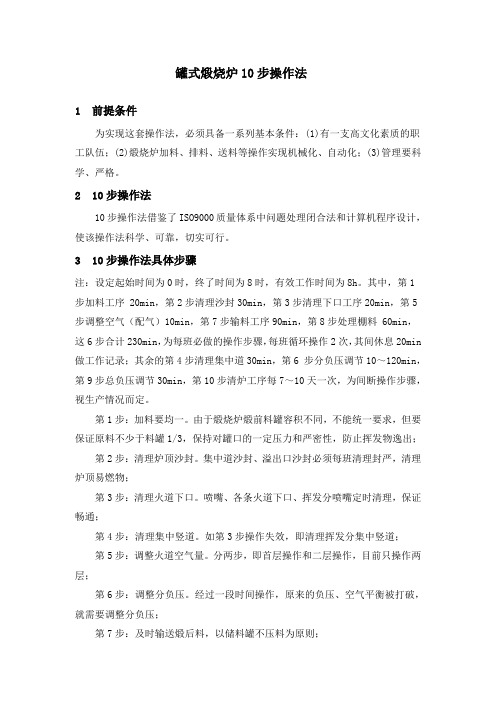
罐式煅烧炉10步操作法1 前提条件为实现这套操作法,必须具备一系列基本条件:(1)有一支高文化素质的职工队伍;(2)煅烧炉加料、排料、送料等操作实现机械化、自动化;(3)管理要科学、严格。
2 10步操作法10步操作法借鉴了ISO9000质量体系中问题处理闭合法和计算机程序设计,使该操作法科学、可靠,切实可行。
3 10步操作法具体步骤注:设定起始时间为0时,终了时间为8时,有效工作时间为8h。
其中,第1步加料工序 20min,第2步清理沙封30min,第3步清理下口工序20min,第5步调整空气(配气)10min,第7步输料工序90min,第8步处理棚料 60min,这6步合计230min,为每班必做的操作步骤,每班循环操作2次,其间休息20min 做工作记录;其余的第4步清理集中道30min,第6 步分负压调节10~120min,第9步总负压调节30min,第10步清炉工序每7~10天一次,为间断操作步骤,视生产情况而定。
第1步:加料要均一。
由于煅烧炉煅前料罐容积不同,不能统一要求,但要保证原料不少于料罐1/3,保持对罐口的一定压力和严密性,防止挥发物逸出;第2步:清理炉顶沙封。
集中道沙封、溢出口沙封必须每班清理封严,清理炉顶易燃物;第3步:清理火道下口。
喷嘴、各条火道下口、挥发分喷嘴定时清理,保证畅通;第4步:清理集中竖道。
如第3步操作失效,即清理挥发分集中竖道;第5步:调整火道空气量。
分两步,即首层操作和二层操作,目前只操作两层;第6步:调整分负压。
经过一段时间操作,原来的负压、空气平衡被打破,就需要调整分负压;第7步:及时输送煅后料,以储料罐不压料为原则;第8步:处理棚料。
如果发现棚料现象,及时采取措施,并进一步调整,防止结焦;第9步:总负压调整。
原料挥发分发生较大变化,局部调整负压不奏效,就要调整总负压和配比;第10步:清炉、检查配比。
经过一定时间,炉体火道、集中道被焦灰堵塞,需清炉,并检查前一段时间配比效果,制定新一轮原料配比。
锅炉的烘炉和煮炉操作规程

本文档可编辑修改!
1 锅炉的烘炉和煮炉操作规程
烘炉操作 1.、对于炉墙新砌的锅炉和长时间使用的锅炉,在投入运行前,必须进行烘炉。
2、水位保持在最低水位,首先燃用木柴,燃烧必须均匀稳定。
3、一昼夜后,火堆可占至炉排面积三分之一,炉内水温不超过70℃。
4、三昼夜后,可用煤逐渐代替木柴烘炉,烟道挡板要开到烟道面积三分之一至六分之一。
5、一星期后,可投入运行,对于冬季砌筑的炉墙,烘炉时间应加长。
煮炉操作 1、新安装和检修后的锅炉,现运行前必须把炉内部的锈、油脂和污垢通过煮炉加以排除。
2、锅炉上水到最高水位。
每一锅炉水加12—15公斤的碳酸钠或氢氧化钠。
3、升起微火将水烧开,产生蒸汽,通过空气阀排出,水位要保持一定。
4、加热24小时后,停炉冷却,排除冷水,及时用水冲洗干净,直至炉筒,联箱内壁无油垢和锈班,煮炉才算合格。
罐罐式煅烧炉烘炉操作规程

目录1烘炉的目的................................................ 2烘炉曲线及烘炉方法........................................ 3烘炉前的准备.............................................. 4烘炉技术操作.............................................. 5烘炉温度控制.............................................. 6弹簧调整.................................................. 7安全注意事项.............................................. 8烘炉组织机构..............................................32罐罐式煅烧炉烘炉操作规程1烘炉的目的罐式炉简介32罐煅烧炉为顺流式八层火道罐式煅烧炉,它是对预焙阳极的生产原料石油焦进行煅烧的主体设备,炉子的结构特点是:1.1.1主体由粘土耐火砖砌筑,罐式炉的心脏罐体、火道部分使用硅砖砌筑,上下部分和四周使用粘土砖砌筑。
1.1.2炉子每四罐为一组,共八组;八层火道、火道和挥发份道自成一个体系,炉子设置两条预热空气道,一条由炉底通过沿前墙到喷火嘴处,一条由炉底通过折回到炉底四层,利用四层剩余的挥发份提高温度,即可降低炉底温度,又可预热空气。
烘炉目的罐式煅烧炉的寿命长短主要与耐火材料质量、砌筑质量及使用维护等三个方面有关,其中罐式煅烧炉的烘炉质量的好坏直接影响到罐式炉的使用寿命和安全生产。
烘炉就是对新砌炉子进行加热,把炉内的水分逐渐烘干,消除内应力,增加泥浆的粘结力,提高炉体的强度,同时对砌体进行高温烧结,使其达到正常生产时的热状态。
罐罐式煅烧炉烘炉操作规程
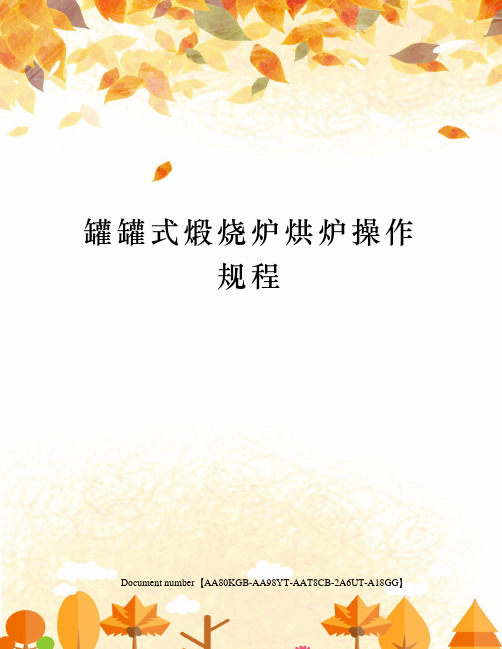
罐罐式煅烧炉烘炉操作规程Document number【AA80KGB-AA98YT-AAT8CB-2A6UT-A18GG】目录32罐罐式煅烧炉烘炉操作规程1烘炉的目的1.1罐式炉简介32罐煅烧炉为顺流式八层火道罐式煅烧炉,它是对预焙阳极的生产原料石油焦进行煅烧的主体设备,炉子的结构特点是:1.1.1主体由粘土耐火砖砌筑,罐式炉的心脏罐体、火道部分使用硅砖砌筑,上下部分和四周使用粘土砖砌筑。
1.1.2炉子每四罐为一组,共八组;八层火道、火道和挥发份道自成一个体系,炉子设置两条预热空气道,一条由炉底通过沿前墙到喷火嘴处,一条由炉底通过折回到炉底四层,利用四层剩余的挥发份提高温度,即可降低炉底温度,又可预热空气。
1.2烘炉目的罐式煅烧炉的寿命长短主要与耐火材料质量、砌筑质量及使用维护等三个方面有关,其中罐式煅烧炉的烘炉质量的好坏直接影响到罐式炉的使用寿命和安全生产。
烘炉就是对新砌炉子进行加热,把炉内的水分逐渐烘干,消除内应力,增加泥浆的粘结力,提高炉体的强度,同时对砌体进行高温烧结,使其达到正常生产时的热状态。
随着温度的变化,组成硅砖的主要成分SiO2将发生晶体的转化,因而造成了砖的体积发生急剧的膨胀和收缩。
一般SiO2以三种结晶形态存在,即石英有:α—石英、β—石英,方石英有:α—方石英、β—方石英,磷石英有:α—磷石英、β—磷石英、γ—磷石英。
在一定温度范围内,SiO2的不同结晶形态及其同素异构体是比较稳定的,但是如果超过了这一温度范围,达到晶体转化温度,SiO2的晶体就要发生转变。
随着温度的变化,由SiO2的晶体转化所引起的体积急剧变化,一般可以认为是在瞬间完成的(当有矿化剂Ca、Fe存在时转化更快)。
SiO2 在加热和冷却过程中晶体形态转化示意图所以在117℃、163℃、270℃、537℃、870℃等几个关键升温阶段都是硅砖晶体转换最激烈温度区,并伴随着硅砖的膨胀,因此在关键升温区要缓慢升温。
罐式煅烧炉烘炉启动方案

40罐煅烧炉烘炉启动方案(初稿)一、烘炉时间安排根据生产运行部安排,40罐煅烧炉计划12月中旬启动烘炉,预计2月中旬烘炉结束,2月底实现达标达产。
二、分厂烘炉组织机构为了确保40罐煅烧炉烘炉工作的顺利进行和烘炉过程的有效控制,分厂成立40罐煅烧炉烘炉领导小组,组成如下:组长:****副组长:*****,*****技术负责人:****、****记录负责人:*****安全负责人:*****成员:****************三、烘炉前的准备1、机械设备的验收、试车:只有在所有设备的验收、单体、联动试车结束,确保设备无故障的情况下,才可点火烘炉。
2、清除料罐内的所有杂物后,方可填料准备烘炉。
3、参加烘炉的人员必须进行培训后,方可进行烘炉操作。
4、炉体膨胀各检测点布置到位、测温装置安装到位。
5、烘炉时使用工器具准备齐全.6、制定烘炉专用记录表准备齐全。
四、烘炉曲线1、烘炉曲线的制定原则:整个烘炉过程中不损坏炉体的严密性,保证有一座优质、耐用的煅烧炉投产。
2、烘炉曲线的制定依据:(1)日膨胀率不大于0。
035%;(2)硅砖生产厂家提供的升温曲线。
3、烘炉曲线的作用:正常情况下,升温严格按照烘炉曲线执行,当水分排出量过大、炉体膨胀量超过设定值时,需要进行保温.4、理论烘炉曲线的计算(昼夜安全膨胀率取0。
035%)5、烘炉曲线根据理论烘炉曲线的计算,在实际升温过程中,需要将多个不同小温度范围合并成一个温度区间,在该区间,升温速度取多个不同小温度范围内的最小升温速度,计算所得烘炉曲线如下:在实际烘炉过程中,当水分排出量过大、炉体膨胀量超过设定值时,需要进行保温操作,一般总烘炉时间会比计划曲线多2~5天。
三、炉烘技术要求1、所有参加烘炉人员必须熟悉烘炉曲线,对炉体的全部测温孔、测负压孔、看火孔、拉板砖以及各通道要掌握其位置及作用.2、温度的测量及要求(1)温度的测点定为首层末端40个、七层40个、烟道2个。
(2)900℃以下采用镍铬-镍硅热电偶,900℃以上采用光电传感器检测温度。
启动锅炉烘炉施工方案

启动锅炉烘炉施工方案一、项目概述本次施工项目是为了启动锅炉烘炉,确保其正常工作并达到预定的效果。
本项目的施工方案将包括以下内容:锅炉安装、烘炉操作流程、施工安全措施等。
二、施工准备1.对施工现场进行清理,确保平整且无障碍物。
2.检查锅炉和烘炉设备,确保其完好无损。
3.为施工人员提供必要的安全设备和工具。
4.针对施工过程中可能出现的问题,制定应急预案。
三、施工步骤1.锅炉安装根据施工图纸和设计要求,在指定位置搭建支架,并将锅炉设备安装在其上。
安装过程中要确保设备稳定,并按要求进行固定。
2.烘炉操作流程a.接通电源首先检查电源是否稳定,并确保电源满足锅炉和烘炉设备的要求。
然后将电源接通,并根据设备操作手册,逐步完成设备的启动过程。
b.点火锅炉烘炉设备启动后,进行点火操作。
点火过程中要保持燃料供应稳定,同时根据设备要求调整空气供应量,确保燃烧充分。
c.温度调控在点火后,根据所烘炉材料的要求,调整温度控制装置,使炉内温度逐渐升高,并保持在所规定的范围内。
d.压力控制根据锅炉设备的要求,调整燃料供应量和排烟装置,控制炉内的压力,确保压力稳定,并符合标准要求。
e.断电和停炉测试运行一段时间后,根据施工要求,逐步停止烘炉设备。
首先断开燃料供应和电源,并进行热处理过程的冷却。
四、施工安全措施1.施工现场应设置安全警示标志,并禁止无关人员进入。
2.所有参与施工的人员必须配备符合要求的安全防护用品,并遵守施工现场的安全规章制度。
3.对于涉及高温和高压的设备操作,必须进行专业培训,并指定专人负责操作。
4.针对施工过程中可能出现的火灾、漏电等危险情况,设置相应的应急设备和消防器材,并定期进行检查和维护。
5.在施工完成后,对施工现场进行清理,并确保锅炉和烘炉设备的安全。
五、总结与验收施工完成后,对锅炉烘炉设备进行功能测试,并调整设备参数,确保其正常工作。
同时对施工现场进行验收,确保施工过程符合相关技术规范和标准要求。
以上是启动锅炉烘炉的施工方案,通过按照上述步骤进行施工,可以确保锅炉烘炉设备的正常工作并达到预定的效果。
碳素厂煅烧炉烘炉工艺流程
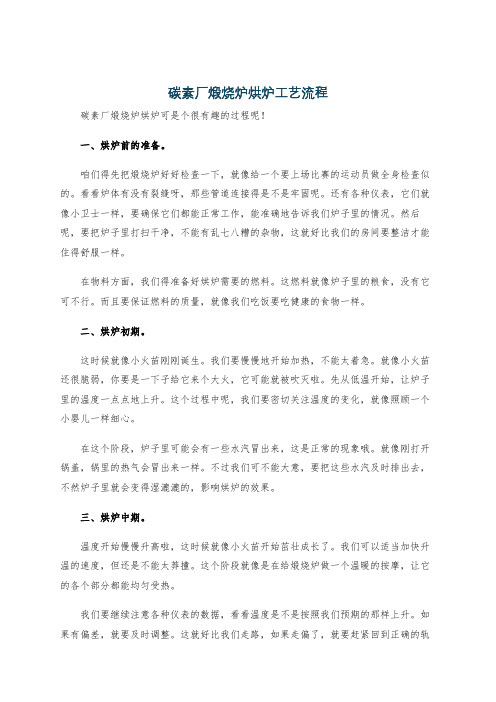
碳素厂煅烧炉烘炉工艺流程碳素厂煅烧炉烘炉可是个很有趣的过程呢!一、烘炉前的准备。
咱们得先把煅烧炉好好检查一下,就像给一个要上场比赛的运动员做全身检查似的。
看看炉体有没有裂缝呀,那些管道连接得是不是牢固呢。
还有各种仪表,它们就像小卫士一样,要确保它们都能正常工作,能准确地告诉我们炉子里的情况。
然后呢,要把炉子里打扫干净,不能有乱七八糟的杂物,这就好比我们的房间要整洁才能住得舒服一样。
在物料方面,我们得准备好烘炉需要的燃料。
这燃料就像炉子里的粮食,没有它可不行。
而且要保证燃料的质量,就像我们吃饭要吃健康的食物一样。
二、烘炉初期。
这时候就像小火苗刚刚诞生。
我们要慢慢地开始加热,不能太着急。
就像小火苗还很脆弱,你要是一下子给它来个大火,它可能就被吹灭啦。
先从低温开始,让炉子里的温度一点点地上升。
这个过程中呢,我们要密切关注温度的变化,就像照顾一个小婴儿一样细心。
在这个阶段,炉子里可能会有一些水汽冒出来,这是正常的现象哦。
就像刚打开锅盖,锅里的热气会冒出来一样。
不过我们可不能大意,要把这些水汽及时排出去,不然炉子里就会变得湿漉漉的,影响烘炉的效果。
三、烘炉中期。
温度开始慢慢升高啦,这时候就像小火苗开始茁壮成长了。
我们可以适当加快升温的速度,但还是不能太莽撞。
这个阶段就像是在给煅烧炉做一个温暖的按摩,让它的各个部分都能均匀受热。
我们要继续注意各种仪表的数据,看看温度是不是按照我们预期的那样上升。
如果有偏差,就要及时调整。
这就好比我们走路,如果走偏了,就要赶紧回到正确的轨道上。
而且这个时候可能会有一些轻微的声响从炉子里传出来,这也是正常的,就像东西在加热的时候会发出一点小声音,就像爆米花在锅里爆开的那种感觉,不过没那么大声啦。
四、烘炉后期。
温度已经升得比较高了,快接近我们最终想要的温度啦。
这个时候就像冲刺阶段,我们要更加谨慎。
虽然温度已经很高了,但还是要保证升温的平稳性。
不能因为快到终点了就放松警惕。
在这个阶段,我们还要检查炉体的膨胀情况。
罐式炉调温操作规程

罐式炉调温操作规程罐式炉是一种常见的加热设备,广泛应用于实验室、工厂等场所。
调温是罐式炉运行的基本操作之一,正确的调温操作可以保证设备安全运行和实验的准确性。
下面是一份罐式炉调温操作规程,供参考:一、开机准备1. 打开炉门,检查炉腔内无杂物,炉底及炉排清洁无堵塞。
2. 检查电源线的插头和接线是否牢固,电源开关处于关闭状态。
3. 检查电热管的连接是否良好,无接触不良的现象。
4. 检查温度控制仪表的显示是否正常。
5. 检查上下限限制器设置是否合理。
6. 预先确认好所需加热温度和加热时间,并做好相应的记录。
二、开机操作1. 将电源线插头插入电源插座,并确认电源开关处于关闭状态。
2. 根据所需加热温度设置好温度控制仪表,确保设定温度与实际温度相符。
3. 关闭炉门,将试样或样品放入炉腔内,注意摆放的均匀性和稳定性。
4. 打开电源开关,启动罐式炉。
5. 等待炉温上升到设定的加热温度,过程中可以观察温度控制仪表的变化。
三、稳定加热1. 炉温接近设定温度时,可适当调低电源开关的输出功率,以缓慢加热至设定温度,避免温度过高。
2. 当炉温达到设定温度后,及时关闭电源开关。
3. 确认设备处于稳定状态后,开始计时记录加热时间。
四、关机操作1. 加热时间到达后,关闭电源开关,停止加热。
2. 等待罐式炉温度降至安全范围,一般不低于环境温度30℃以下。
3. 打开炉门,将样品取出,注意避免烫伤。
4. 清理炉腔内的杂物和残留物。
5. 拔掉电源插头,关闭电源开关。
6. 根据需要对操作过程进行记录,以便于后续分析和参考。
附加注意事项:1. 在操作过程中,不可将可燃、易燃物品放置在罐式炉附近,以防发生火灾。
2. 调整加热温度时,应逐渐增加或降低,避免温度变化过大。
3. 在加热过程中,应密切观察温度变化,如有异常情况及时采取应急措施。
4. 罐式炉停机后,应保持通风良好,以免温度过高或物品变质。
5. 罐式炉长时间不使用时,应将设备清洁彻底并进行保养,以延长使用寿命。
- 1、下载文档前请自行甄别文档内容的完整性,平台不提供额外的编辑、内容补充、找答案等附加服务。
- 2、"仅部分预览"的文档,不可在线预览部分如存在完整性等问题,可反馈申请退款(可完整预览的文档不适用该条件!)。
- 3、如文档侵犯您的权益,请联系客服反馈,我们会尽快为您处理(人工客服工作时间:9:00-18:30)。
40 罐煅烧炉烘炉启动方案(初稿)
一、烘炉时间安排
根据生产运行部安排,40 罐煅烧炉计划12 月中旬启动烘炉,预计2月中旬烘炉结束,2 月底实现达标达产。
二、分厂烘炉组织机构
为了确保40 罐煅烧炉烘炉工作的顺利进行和烘炉过程的有效控制,分厂成立40 罐煅烧炉烘炉领导小组,组成如下:
组长:副组长:***** ,***** 技术负责人:**** 、**** 记录负责人:
*****
安全负责人:*****
成员:
三、烘炉前的准备
1、机械设备的验收、试车:只有在所有设备的验收、单体、联动试车结束,确保
设备无故障的情况下,才可点火烘炉。
2、清除料罐内的所有杂物后,方可填料准备烘炉。
3、参加烘炉的人员必须进行培训后,方可进行烘炉操作。
4、炉体膨胀各检测点布置到位、测温装置安装到位。
5、烘炉时使用工器具准备齐全。
6、制定烘炉专用记录表准备齐全。
四、烘炉曲线
1、烘炉曲线的制定原则:整个烘炉过程中不损坏炉体的严密性,保证有一座优
质、耐用的煅烧炉投产。
2、烘炉曲线的制定依据:(1)日膨胀率不大于0.035%;(2)硅砖生产厂家
提供的升温曲线。
3、烘炉曲线的作用:正常情况下,升温严格按照烘炉曲线执行,当水分排出量过
大、炉体膨胀量超过设定值时,需要进行保温。
4、理论烘炉曲线的计算(昼夜安全膨胀率取0.035%)
5、烘炉曲线
根据理论烘炉曲线的计算,在实际升温过程中,需要将多个不同小温度范围合并成一个温度区间,在该区间,升温速度取多个不同小温度范围内的最小升温速度,计算所得烘炉曲线如下:
在实际烘炉过程中,当水分排出量过大、炉体膨胀量超过设定值时,
需要进行保温操作,一般总烘炉时间会比计划曲线多2~5 天。
三、炉烘技术要求
1、所有参加烘炉人员必须熟悉烘炉曲线,对炉体的全部测温孔、测负压孔、看火
孔、拉板砖以及各通道要掌握其位置及作用。
2、温度的测量及要求
(1)温度的测点定为首层末端40 个、七层40个、烟道2个。
(2)900℃以下采用镍铬—镍硅热电偶,900℃以上采用光电传感器检测温度。
(3)温度的波动范围,在800℃前各火道每班允许误差± 5℃,在800℃后各火道之间每班允许误差± 10℃。
(4)所有测温点,要求小时观测1-2 次,按小时记录1 次。
3、负压的测量及要求
(1)负压测点选为:首层火道、烟道2 个。
(2)用薄壳压力计进行测量,要求2 小时记录1次。
(3)烘炉过程中的负压根据实际情况确定。
4、膨胀的测量及要求:
(1)采用炉高日膨胀来控制升温速度。
(2)炉高膨胀点定为6 个,炉侧测点8个。
(3)膨胀测量时间要求每班测两次,接班与班中各一次(每间隔4 小时)。
(4)对膨胀量的要求
(5)经常检查炉体四周有无影响炉体膨胀的地方和障碍物,特别是发现四周大墙膨胀很小或不膨胀时,更要仔细寻找影响炉体膨胀的障碍物。
5、弹簧的调整
(1)烘炉开始时,横向弹簧约为5吨,纵向为约6 吨。
一直到烘炉结束。
(2)正常情况下,每天8 点班调整一次。
6、料罐加料要求
点火前罐内加满煅后料,料面高度加至料斗高度的1/3 处。
当开始排料后,前
期加入原料为生熟焦各约50%,温度升到1100℃以上,过度到正常生产配料。
7、燃料供应烘炉用燃料为天然气。
四、烘炉操作
1、烘炉方法烘炉采用首层为燃烧点,每燃烧点对应一个条火道,所以在烘炉初期,供气管道不得深入火道过多、火焰长度不宜过长,严禁火焰直接接触到硅砖部分,随着温度的逐步升高,逐渐加大燃料供给量。
2、点火
(1)开副烟道。
(2)打开八层负压拉板,关闭其它各层挥发分拉板砖及空气拉板砖。
(3)调整各道负压,第一层边道为12Pa、中间各道10Pa。
(4)按开炉点火操作顺序从1-40 号点火。
(5)点火后重新调整负压为规定值。
3、点火操作顺序:
(1)首先检查各道前天然气阀门是否处于关闭状态。
(2)点火前首先开启天然气总阀门,点火时再开分阀门,即控制阀。
(3)先放入火种,再少量打开天然气控制阀。
(4)引燃后及时根据火焰长度来调节控制阀;使用过程中勤检查天然气燃烧状况,火焰为红、黄色、发暗、冒烟说明缺氧,火焰短白亮刺眼,说明空气
多。
4、点火注意事项
1)人不能从近距离、正面对着点火孔。
2)点火失败后先关闭天然气阀门,停3-5 分钟后再点火
3)先点火后开气,开少许即可。
4)突然停气应急处理:
1)首先关闭天然气阀门,记录停气时间,查清停气原因
2)及时封闭燃烧进气口,根据炉温调整总负压,禁止直接切断负压源。
3)通知送气后,记录送气时间,检查气源压力是否在规定范围内。
4)先试点火,合适后再进行烘炉操作。
5、负压调整
第八层负压在点火时控制在20Pa左右,八层负压的调整要随着炉温的上升逐步提高。
负压调整原则:(1)低温时负压小,高温时负压大。
(2)边火道负压大,中间火道负压小。
(3)负压的递增要随第一至第八层温差的增加,逐渐加大。
(4)火道之间的负压差的调整用负压拉板调整,总体负压的调整用副烟道闸板调整。
6、温度调整
烘炉过程中,以第一层末端温度作为烘炉的控制温度,每小时检查1-2 次,每小时记录1 次,其它部位温度每2 小时记录1 次。
一般从以下几个方面调整温度:(1)在保持天然气质量和压力稳定的前提下,要根据检测温度及时调节天然气量的多少。
(2)负压大小对温度的影响较大。
不同的温度阶段要求调整不同的负压,而且随着炉温的升高而逐步增大负压。
(3)炉体四周大墙和表面的裂缝,对边火道的温度影响较大。
因此要随时用石棉绳堵塞,烘炉结束后,应在裂缝处灌浆或抹灰,以保持炉体严密。
(4)边火道消耗热量较多,烘炉后期升温也较困难。
此时适当多给些燃料,负压比其它火道适当高些,可以降低火道之间的温差。