氮化防腐油管技术介绍
油气田井下油管的防腐技术

油气田井下油管的防腐技术在石油工业中起着至关重要的作用,可以延长油管的使用寿命、提高生产效率,并保证油气的安全输送。
以下是一些常见的油气田井下油管防腐技术:
1. 油管涂层防腐技术
-环氧涂层:环氧涂层是最常用的油管防腐材料之一,具有良好的耐腐蚀性能和粘附性,可以有效防止金属表面受到腐蚀。
-聚乙烯涂层:聚乙烯涂层具有良好的机械性能和耐腐蚀性能,广泛应用于海底油气管道等环境中。
-聚胺脂涂层:聚胺脂涂层具有优异的耐化学腐蚀性能和耐磨损性能,适用于高腐蚀环境下的油管防腐。
2. 阴极保护技术
-镀锌:将油管表面镀上一层锌,利用锌的阳极保护作用保护油管不受腐蚀。
-牺牲阳极保护:在油管系统中加入一些更容易氧化的金属,如锌、铝等,使其成为“牺牲阳极”,保护油管不受腐蚀。
3. 管道涂层检测技术
-非破坏检测:采用超声波、X射线、磁粉探伤等非破坏检测技术对油管涂层进行定期检测,及时发现问题并进行修复。
-电化学阻抗谱分析:通过电化学阻抗谱分析技术,监测涂层的电化
学性能变化,评估防腐涂层的状况和耐腐蚀性能。
4. 管道防腐维护管理
-定期检查维护:定期对油管涂层进行检查和维护,及时修复涂层损坏或腐蚀部位。
-建立档案记录:建立完善的管道防腐维护档案,记录每次维护和检测的结果,制定科学的预防性维护计划。
通过以上技术手段和管理措施,可以有效延长油气田井下油管的使用寿命,确保油气输送系统的安全稳定运行。
同时,保障油气资源的开发利用,促进石油工业的持续发展。
长输管线防腐技术介绍

环氧/改性聚乙烯粉末防腐层 据报道,在美国还有一种新型的双层粉末结构,该结构是在FBE防腐层(0.30-0.64mm )上喷涂一层改性聚乙烯CMP和FBE属化学和机械粘结,不会分离,比传统的三层PE有所进步,其性能与双层FBE相似。2007年在美孚石油公司的管道工程中得以应用,但在国内还无使用先例。
纳米改性材料涂层 纳米技术是近年来出现的一门新兴技术,它带来了材料科学领域的重大革命。由于腐蚀防护所涉及的表面材料的性质由微观结构所决定,纳米技术的出现与应用无疑将给腐蚀控制技术的发展带来巨大的机遇。研究表明,利用纳米技术对有机涂层防腐材料进行改性,可有效提高其综合性能,特别是增加材料的机械强度、硬度、附着力,提高耐光性、耐老化性、耐候性等。例如TiO、SiO2、ZnO、Fe2O等纳米粒子对紫外线有散射作用,加入这样的纳米材料可有效增强材料的抗紫外线能力,使耐老化性显著提高。通过向材料中加入一些颗粒很小的纳米粒子,能增加材料的密封性,达到更好的防水、防腐效果。对于无机涂层材料,如对其结构进行纳米化,也能达到明显改善其塑性、韧性的作用。
玻璃钢管道与钢质管道相比,其优点主要体现在:价格比钢管便宜;安装简单;使用寿命在30年以上,是钢管的2~3倍,且其间无需维护;流体阻力小;对输送介质无污染;保温性能好。
电化学防护 根据调查数据和阴极保护相关规范,对沿线的土壤情况进行分析,得出以下结论:土壤的自然腐蚀性属于强腐蚀~极强腐蚀范围:管道沿线存在强烈的杂散电流的腐蚀条件,应当增加排流设施:测量数据显示构成微生物腐蚀的可能性很小;钢管在采用较好的防腐层的基础上必须增设阴极保护设施。
氮化防腐油管技术介绍

的洞。
难采公司长26-19井现场试验
修井记录
2004年11月27日油井转注, 油压28MPa,套管26MPa,历时180 天左右 。2005年6月17日油压、套 压突然下降,起井后查找原因,油 管腐蚀严重造成泄漏。为恢复注水, 决定更换氮化防腐油管,并实施保 护套管注水。
三、氮化层的微观组织
金属
放大倍数: 400× 腐蚀剂: 4%硝酸酒精
放大倍数: 400× 腐蚀剂: 4%硝酸酒精
微观组织
防腐层ε相
防腐层ε相
材料名称:42MnMo7(N80) 放大倍数: 400× 腐蚀剂: 4%硝酸酒精
N80氮化油管防腐层金相照片
材料名称: 37Mn5(J55) 放大倍数: 400× 腐蚀剂: 4%硝酸酒精
J55氮化油管防腐层金相照片
四、室 内 试 验
盐雾试验前的防腐油管短接
盐雾试验后的防腐油管短接
96小时盐雾试验后氮化和未氮化油管的对比
氮化防腐油管试样
被腐蚀掉的 油管机体 外防腐层
内防腐层
氮化防腐油管螺纹试样
被腐蚀掉的 油管机体
螺纹机体
外防腐层
五、氮化油管现场应用
(一)油管短接试验
下井时间:2003年7月 下井情况:同井下入氮化防腐油管和
(二)整井试验
中10-58 小集6-2井 官84-51 官922-1 专采41-35
2004.7-2007.6 2004.8-2007.6 2005.6-2007.6 2005.7-2007.6 2005.11-2007.6
小集6-2井现场试验
下入的防腐油管(2-7/8) 使用后的状况 同井同时下入的普通油管(3-1/2)使用后的状况
氮化油管宣传片

五、技术要求、检测方法 及质量控制
序号 1 2 3 4 项目 外观 氮化层厚度,μm 氮化层表面硬度,HV0.05 直线度,mm 氮化套管 氮化油管 J55 氮化套管 6 静水压试验 氮化油管 7 无损探伤,级别 抗拉强度,MPa N80-1 P110 J55 N80-1、N80Q P110 P110 性能指标 表面平整、无裂纹、无明显的凹坑等缺 陷 40-300 280-650 ≤3.18mm(1/8in) 符合表 4、表 5、表7要求 符合表10~表13要求 符合表C.45 要求 符合表C.48 要求 符合表C.52要求 符合表C.55要求 符合表C.56要求 符合表C.60要求 L2 GB/T 5777 GB/T 19830中10.12 试验方法 目测 GB/T 1354 GB/T 4340.1 GB/T 19830中8.9 GB/T 9253.2 GB/T 9253.2
垦71-86井试验情况
垦 71-86 位于垦西油田,是孤岛 油田腐蚀最严重的地区,在未 使用氮化油管以前,平均每1年 左右更换一次油管。2002年 9月 4日换用我厂生产的氮化油管, 2005 年初提出,在井下使用二 年多时间,能正常取出油管, 油管外表局部存在不同程度的 腐蚀和点蚀,氮化层局部被破 坏,个别丝扣倒角处存在腐蚀, 但可以正常使用。
氮化油管的防腐蚀特性
通过石油管材研究所于2000年10月的实验(2000管试 研字第028号)。实验结论为:从平均腐蚀速率明显可见, 有氮化层时腐蚀速率大大降低,说明这种氮化层在实验所 采用的油田模拟腐蚀环境中有很好的抗蚀性。
氮化处理工艺

氮化处理工艺氮化处理(Nitriding)是钢件对热处理外表面保护和强度改进的一种杀伤性表面处理,它是通过向钢件外表面通过气体渗入氮化物,来改变外表面层的组织结构,提升钢的硬度、耐久性和耐腐蚀性来实现的。
一、氮化处理原理氮化处理是一种表面强化处理技术,利用热处理温度下可结合钢表面进行化学反应生成金属氮化物混合物而实现,氮化物层具有很高的抗摩擦性、耐磨损性,很好的热韧性和抗腐蚀能力,这种处理可以满足磨损和耐腐蚀性需求,从而提高材料的性能与使用寿命。
二、氮化处理的类型1. 蒸汽氮化:也叫做温化氮化,是将空气中的氮分子通过蒸汽的形式放入钢材材料,适用于碱金属基体的氮化处理,能够制得一层较厚、硬度高、耐磨损性强、表面因含有少量氧化物而深灰色的氮化层;2. 气体氮化:主要利用蒸气冷凝或被氧化型非金属基体金属与空气中的氮化物进行反应,使金属表面形成一层深灰色、光滑、耐腐蚀的氮化层;3. 等离子氮化:它是利用等离子体技术,在低温条件下,以一种比压控制的低温的等离子体处理,使钢的表面形成一层由高分子组成的氮化膜;4.溅射氮化:溅射氮化是利用金属氮化物的表面溅射技术,将氮化物的单体的离子溅到钢的表面,使钢的表面形成氮化膜。
三、氮化处理的优缺点优点:1. 氮化处理可大大改善表面硬度,使其具有更好的耐磨性,延长使用寿命;2. 氮化处理可防止表面腐蚀,提高耐腐蚀性,使其具有更好的热韧性;3. 氮化处理可提高表面的抗冲击力,使其对冲击有更佳的表现;4. 氮化处理可改善表面质量,从而改善产品的外观,使其具有增加市场竞争力。
缺点:1. 氮化处理产生的氮化层膜残留不容易去除,容易在表面形成洼槽;2. 氮化处理时有些钢材表面温度过高,容易引起表面碳化、氢化;3. 氮化处理依赖设备质量,操作环境,控制体系等,不稳定;4. 氮化处理成本较高,工艺复杂度高。
四、氮化处理的注意事项1. 氮化处理的钢材材质需符合实际需求;2. 氮化处理室环境要求干净,过度脏污有可能导致产品质量不稳定;3. 氮化处理温度要控制在可接受的范围,保温时间也要适当,以免影响外观品质;4. 氮化处理后的表面要加以小心的处理,以保证表面硬度。
油管离子渗氮方法及防腐蚀耐磨性能分析

对 经离 子渗 氮 后 的试 样 进 行 磨 损试 验 , 与 并
未 经离 子渗 氮 的试 样 进 行 对 比 , 析离 子 渗 氮 对 分 提高油 管 耐 磨 性 的 效 果 。选 用 MM 1 型 万 能 W一A 磨 损机 , 别将 1 6号试样 和未 经 离子渗 氮处 理 分 ~ 的对 比试样 进 行 磨 损 试 验 。试 验条 件 为 : 擦 副 摩
成分可知 , 离子渗氮 层组织 以 ( eN 相 为主, F )
并 含少 量 的 + F:。 相 , ( e N) 由于渗 层 致 密 , 硬
石油化工腐蚀与防护
第2 9卷
度较 高 , 因此具 有 良好 的耐 磨 性 。从 表 2还 可 J
对离 子渗 氮试 样 和未渗 氮试样 进行 耐腐 蚀性 能 测试 , 并将 试 验 结果 进 行 了 比较 。试 验装 置 为 Q W0 0型盐 雾 腐蚀 试 验 箱 , 用 中性 盐雾 试 验 Y 9 采 ( S )试 验 条 件 : 化 钠 溶 液 质量 分 数 为 5 , NS , 氯 % p H为 6 5—7 2 喷雾 压 力 为 6 . ., 7~10k a试 验 8 P , 温 度 为 (5±1 ℃ , 3 ) 连续 喷雾 2 。 4h
傅 乐荥 牛 君 左 治江 , ,
(. 1 江汉 大学机 电与建筑工程学 院 , 湖北 武汉 4 0 5 ; 30 6
2大安恒锐采油设 备有限公 司 , 吉林 大安 1 12 ) 3 32
摘要 : 磨损 和腐蚀是造成 油管失效 的主要原 因, 通过 对油管 内壁进 行 离子渗 氮, 以提 高油管的
3 2 摩 擦 系数 比较 .
1 号试样和未处理试样在相同条件下摩擦磨
损 试验 结果 见 图 4 。从 图 4可 看 出 , 氮 试 样 的 渗 摩 擦 系数低 于未 渗 氮 试样 的摩 擦 系 数 , 同样 说 明 渗氮 试样抗 摩擦 磨损 能力 高于未 渗氮 试样 。
防腐油管技术综述

传统 的 9 C r , 1 3 C r 马氏体不锈钢 自 2 0世 纪 7 0年代 开发 以
来, 作为油气工业用管材得 到广泛应用 , 获得 了良好 的声誉 , 并 列入 A P I S P E C 5 C T标准 。这两个钢种 在含 C O 以及 C l 一 的酸 性环境 下具有很好 的耐腐蚀性 能。 目前 , 世界 1 3 — 1 5 C r 油井管 的
所不 同 , 在整个安装过程 中都涉及 到电气控制和机械部件 的 安装 , 整个安装过程 比较复杂 , 涉及到多工种协 同作业 , 在安装 的过程中要 严格按照设计要求进行安装 , 将安装质量控制好 , 并
目前 ,国产 油井 管产品已经覆盖 了 A P I S p e c 5 C T标准 内
庆大学 出版社 , 2 0 1 3 .
防腐油管技术综述
韩民强
( 渤海石油装备 ( 天津 ) 新世 纪机械制造有限公 司, 天津 3 0 0 2 8 0 )
摘
要: 对 国 内外 油 管 防 腐技 术进 行 阐述 , 并 针 对 我 国油 井 腐蚀 状 况进 行 分 析 及展 望 。
关键词 : 油管 ; 防腐 ; 工艺 ; 水质
高压玻璃钢管道是 由在缠绕设备上浸渍 了高粘结能力的低Байду номын сангаас 黏度树脂基体 的高强度玻璃纤维按设定的角度和铺层缠绕于芯
模上 , 经 固化 、 脱模 、 加工制得 。其最 大特 点是 优 良的耐腐蚀性 能、 高耐久性和轻质高强 1 . 4 热扩散渗锌技术 热扩散渗锌技术作为上世纪初发展起来的一项金属表面处理 技术 , 以其 良好的耐腐蚀 陛得到广泛的应用。 渗锌是一种将钢铁材 料和锌粉混合加热,进而使锌吸附于材料表面形成渗锌保护层 的 化学热处理过程。渗锌镀层被认为是所有锌制表面中最坚固的。
氮化处理的优缺点

氮化处理的优缺点
氮化处理是一种表面处理方法,通过在材料表面形成氮化物层,从而改善材料的硬度、耐磨性、耐腐蚀性等特性。
它的优点主要包括:
1. 提高硬度:氮化处理能显著提高材料的硬度,使其具有较好的耐磨性和耐腐蚀性,从而延长材料的使用寿命。
2. 提高表面质量:氮化处理能改善材料的表面光洁度和平滑度,减小表面粗糙度,从而提高材料的表面质量。
3. 增加材料的强度:氮化处理可以增加材料的抗拉强度、抗压强度和抗弯强度,提高材料的机械性能。
4. 节约材料成本:相比于其他提高材料性能的方法,氮化处理可以在较低的温度和压力条件下进行,不需复杂的设备和工艺,节约了材料成本。
然而,氮化处理也存在一些缺点:
1. 局限性:氮化层只存在于材料表面,对于大尺寸或复杂形状的零部件来说,处理效果会受到限制。
而且,氮化层也不适用于所有材料,对于某些材料而言,氮化处理可能不适用或效果不佳。
2. 表面脆性:虽然氮化处理能提高材料的硬度和强度,但同时也会增加材料的脆性。
这就需要在设计和使用过程中特别注意,
避免材料的断裂和损坏。
3. 加工复杂性:氮化处理需要进行预处理和后续处理,涉及到高温高压的条件,加工工艺相对复杂。
这可能会带来额外的时间和成本。
综上所述,氮化处理具有提高硬度、改善表面质量和增加强度等优点,但同时也存在局限性、表面脆性和加工复杂性等缺点。
因此,在实际应用时需要综合考虑材料性能需求和处理成本,选择合适的表面处理方式。
油管离子渗氮方法及防腐耐磨性能分析

油管离子渗氮方法及防腐耐磨性能分析Research on Oil Pipelines Corrosion and Wear Resistance Property byPlasma Nitriding Method傅乐荣1牛君2左治江1(1.江汉大学机电与建筑工程学院,湖北武汉430056;2大安恒锐采油设备有限公司,吉林大安131322)School of Mechanical-electrical & Architecture Engineering, Jiang Han University, Wuhan, 430056Daan Hengrui Oil Equipment Co., Ltd.[摘要]对油管内壁进行离子渗氮以提高其使用寿命,是一种国内外还未用于油管批量生产的新工艺方法,本文介绍了油管离子渗氮的基本原理和工艺,对离子渗氮油管的耐磨性和耐腐蚀性能进行了测试,结果表明,离子渗氮油管不仅具有高的耐磨性,还提高了油管的耐腐蚀能力。
Abstract:Plasma nitriding oil pipelines inner wall could increase its service life, which is a new process method that didn’t apply to batch production in domestic and foreign at present. This paper introduced the basic principle and technology of plasma nitriding process. The wear resistance and corrosion resistance were tested after plasma nitriding treatment. The results showed that plasma nitriding oil pipelines not only had high wear resistance, but also improved the tubing corrosion resistance.[关键词] 油管离子渗氮耐磨性耐腐蚀性能Key words:oil pipelines;Plasma nitriding ;wear resistance;corrosion resistance[中图分类号] [文献标识码][课题项目]本文系武汉市科技攻关项目“大装炉量油管内壁离子渗氮工艺分析与设备研制”(项目编号:201010621230)的研究成果利用大型卧式油管离子渗氮专用设备,对油管进行离子渗氮处理,其内壁表层获得了较为均匀的渗层,表面硬度达到~550Hv,实际使用寿命提高了3倍以上[1]。
氮化处理

氮化处理目录• 一、氮化用钢简介• 二、氮化处理技术:• 三、气体氮化技术:• 四、液体氮化技术:• 五、离子氮化技术:氮化处理又称为扩散渗氮。
气体渗氮在1923年左右,由德国人Fry 首度研究发展并加以工业化。
由于经本法处理的制品具有优异的耐磨性、耐疲劳性、耐蚀性及耐高温,其应用范围逐渐扩大。
例如钻头、螺丝攻、挤压模、压铸模、鍜压机用鍜造模、螺杆、连杆、曲轴、吸气及排气活门及齿轮凸轮等均有使用。
一、氮化用钢简介传统的合金钢料中之铝、铬、钒及钼元素对渗氮甚有帮助。
这些元素在渗氮温度中,与初生态的氮原子接触时,就生成安定的氮化物。
尤其是钼元素,不仅作为生成氮化物元素,亦作为降低在渗氮温度时所发生的脆性。
其他合金钢中的元素,如镍、铜、硅、锰等,对渗氮特性并无多大的帮助。
一般而言,如果钢料中含有一种或多种的氮化物生成元素,氮化后的效果比较良好。
其中铝是最强的氮化物元素,含有0.85~1.5%铝的渗氮结果最佳。
在含铬的铬钢而言,如果有足够的含量,亦可得到很好的效果。
但没有含合金的碳钢,因其生成的渗氮层很脆,容易剥落,不适合作为渗氮钢。
一般常用的渗氮钢有六种如下:(1)含铝元素的低合金钢(标准渗氮钢)(2)含铬元素的中碳低合金钢SAE 4100,4300,5100,6100,8600,8700,9800系。
(3)热作模具钢(含约5%之铬)SAE H11 (SKD – 61)H12,H13(4)肥粒铁及麻田散铁系不锈钢SAE 400系(5)奥斯田铁系不锈钢SAE 300系(6)析出硬化型不锈钢17 - 4PH,17 – 7PH,A – 286等含铝的标准渗氮钢,在氮化后虽可得到很高的硬度及高耐磨的表层,但其硬化层亦很脆。
相反的,含铬的低合金钢硬度较低,但硬化层即比较有韧性,其表面亦有相当的耐磨性及耐束心性。
因此选用材料时,宜注意材料之特徵,充分利用其优点,俾符合零件之功能。
至于工具钢如H11(SKD61)D2(SKD – 11),即有高表面硬度及高心部强度。
氮化处理技术在船舶制造领域中的应用前景分析

氮化处理技术在船舶制造领域中的应用前景分析氮化处理技术是一种通过在材料表面形成氮化物层来改善其硬度、耐磨性和耐腐蚀性能的表面处理技术。
在船舶制造领域中,由于船舶在海洋环境中长时间暴露于高湿度、高盐度和强腐蚀性的环境中,对船舶材料的耐腐蚀性能提出了更高的要求。
因此,氮化处理技术在船舶制造领域中有着广阔的应用前景。
首先,船舶的核心结构材料一般采用碳钢或不锈钢。
这些材料在长期航行过程中容易受到海水的腐蚀,导致结构材料的减薄和强度降低。
而通过氮化处理技术可以在材料表面形成一层氮化物层,有效提高材料硬度和耐磨性,从而延长材料使用寿命,减少船舶维修和更换的成本。
其次,船舶的推进系统和螺旋桨通常是由铜合金制成,因为铜合金具有良好的导热性能和耐腐蚀性能。
然而,在海洋环境中,铜合金也容易受到海水的侵蚀,导致腐蚀速度加快。
通过氮化处理技术可以增加铜合金材料的硬度和耐磨性,降低腐蚀速度,提高螺旋桨的推进效率和寿命。
此外,在船舶的油田勘探和开采活动中,氮化处理技术还可以应用在油井套管和油井工具的制造中。
由于海底油气开采条件恶劣,对套管和工具的耐压和耐腐蚀性能有较高的要求。
氮化处理技术可以提高套管和工具材料的硬度和耐腐蚀性能,增加其在高压和腐蚀性介质下的工作寿命,减少油井维修和更换的次数。
最后,船舶的防污涂层也可以应用氮化处理技术。
当前船舶防污涂层主要采用有机涂层,但长时间的海洋暴露容易导致涂层老化和破损,从而降低防污性能。
而氮化处理技术可以形成一层硬度高、耐磨性好的氮化物涂层,有效提高防污涂层的使用寿命和效果,降低船舶的摩擦阻力,提高船舶的航行速度和燃油效率。
总之,氮化处理技术在船舶制造领域中具有广泛的应用前景。
通过提高材料的硬度和耐磨性,降低材料的腐蚀速度,能够有效延长船舶材料的使用寿命,降低船舶的维修成本。
随着船舶制造技术的不断进步,氮化处理技术将会进一步得到应用和推广,为船舶制造行业带来更大的效益和发展机遇。
在船舶制造领域中,氮化处理技术不仅可以应用于船舶的结构材料和推进系统,还可以应用于船舶的其他重要部件。
油管防腐技术的研究及应用

油管防腐技术的研究及应用摘要:文章在对油管腐蚀状况进行调查、研究的基础上,总结出了油管腐蚀的一般规律和腐蚀的典型性,并在对腐蚀的类型、机理以及对腐蚀的影响因素的研究基础上,提出了有效的防腐工艺技术措施,这对于提高油气田的防腐工艺技术水平有一定的实用及参考价值。
关键词:腐蚀;油管腐蚀;油管;防腐工艺修复油管在经过加热、清洗、探伤和试压等工序后,由于油管内外表面的油污被清洗掉,金属本体直接与空气接触,现场露天存放,腐蚀速度很快。
一般经过一个小时后,内外表面便开始出现红色锈斑,随着时间的推移,腐蚀面积会逐步扩大,一周以后,金属表面裸露处将大面积腐蚀,伴有铁红色锈沫出现。
时间再往后延长,腐蚀向深度扩展,原来未裸露的部分,出现内部腐蚀,形成锈皮脱落,导致修复油管不能下井使用,只能再次修复后使用。
因此,正确认识油管防腐知识,增加油管使用年限,是一项急需而重要的工作,它直接关系着原油生产能否正常进行。
1腐蚀因素分析①油管材质的影响。
对中原油田采油六厂马厂、桥口及白庙油区的10口油气井油管的腐蚀资料进行了分析,它表明在同种情况下,油管材质不同,油管受腐蚀的程度也会有所不同。
从油管材质的化学成分分析来看,我们发现油管材质中铬含量增加,会增加油管表面钝化膜的稳定性,而钼含量的增加,会减少Cl-的破坏作用,从而使油管的耐点蚀性能增强。
②H2S、Cl-、CO2的影响。
对发生腐蚀油气井的腐蚀环境及腐蚀因素进行分析后可以看出,油管在使用过程中,受腐蚀性气体H2S、CO2、Cl-和硫酸盐还原菌(SRB)等共同作用发生腐蚀。
③腐蚀类型的影响。
油管在含酸气气井的腐蚀属电化学腐蚀。
即:金属与电解质溶液接触时,由于金属表面的不均匀性,在金属表面出现阳极和阴极区,阳极和阴极区通过金属本身互相闭合而形成许多腐蚀微电池,电化学腐蚀就是通过这些阳极和阴极区反应过程进行的。
H2S在溶解在水中立即电离,使水有酸性,同时对油管产生电化学腐蚀,它的反应式表示为: H2S=H++HS-,HS-=H++S2-。
氮化处理工艺 -回复

氮化处理工艺 -回复
氮化处理工艺是指将材料表面暴露在氮气环境中,通过热处理使氮原子渗透到材料表层形成氮化层的一种表面处理技术。
氮化处理可以提高材料的硬度、耐磨性、耐腐蚀性和高温性能,同时还可以改善材料的表面光洁度和抗氧化性能。
常见的氮化处理工艺包括气体氮化、盐浴氮化和离子氮化等。
气体氮化是将材料置于高温高氮气氛中进行处理,通过热扩散使氮原子渗透到材料表层形成氮化层。
盐浴氮化是将材料浸泡在含有氮化剂的盐浴中加热处理,使氮原子渗透到材料表层。
离子氮化则是通过在真空中向材料表面轰击氮离子,使氮原子从离子束中沉积到材料表面。
氮化处理可以应用于各种材料,包括金属、陶瓷和塑料等。
它被广泛应用于工业领域,如航空航天、汽车、机械制造等。
氮化处理可以提高材料的硬度和耐磨性,延长材料的使用寿命,同时还可以改善材料的表面品质和耐蚀性能。
需要指出的是,氮化处理是一项复杂的工艺,需要控制好处理温度、氮气浓度和处理时间等参数,以确保处理效果的稳定性和一致性。
油管耐磨抗蚀氮化新工艺与应用

油 管 耐磨 抗 蚀 氮化 新 工 艺与应 用
孙 卫 娟
( 东胜利职业学院 机电工程系 , 山 山东 东 营 2 7 9 ) 50 7
摘 要 : 对油、 井油管存在的腐蚀 、 问题 , 针 水 偏磨 对油管的腐蚀 、 磨损机理和螺纹副 的失效进行分析 , 并对油管耐磨
防腐 处理 措 施 进 行 评 价 , 为 脉 冲 真 空 氮 化 防 腐 工 艺 是 国 内 最 新 研 究 开 发 的 一 种 表 面化 学 处 理 技 术 , 该 工 艺 处 认 用 理 的 防腐 油管 能从 根 本 上解 决油 管材 质 表 层 的耐 磨 、 蚀 性 , 可 以推 广 的 一 种 新技 术 。 抗 是
4 使 用说 明
4 1 操作 步骤 .
打捞 落物 的 目的。在 钻 塞 过程 中 , 因钻 头 底 部 为 圆
形, 接触 面积 小 , 但稳 定 , 对钻 压要求 不严 , 对扭 矩要 求 也不 高 。钻头分 2部 分 同 时对 灰 塞 进行 切 削 , 因
而 钻进速 度快 , 施工 周期 短 。
S UN e— a W i n j u
( p rme t f c . Elc., h n o g S e g iVoa in lI siue, n ig 2 7 9 , ia De a t n Me h & o et S a d n hn l c to a n ttt Do gyn 5 0 7 Ch n ) Ab t a t s r c :Ba e n t e p o e s o u or o i nd de i to a i g,t c n s o u o r — s d o h r blm f t be c r son a v a i n we rn he me ha i m f t be c r o
油气管道防腐技术及应用
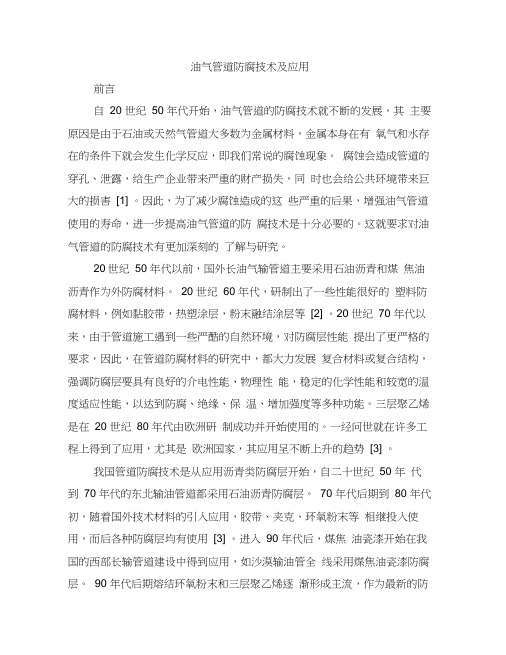
油气管道防腐技术及应用前言自20 世纪50 年代开始,油气管道的防腐技术就不断的发展,其主要原因是由于石油或天然气管道大多数为金属材料,金属本身在有氧气和水存在的条件下就会发生化学反应,即我们常说的腐蚀现象。
腐蚀会造成管道的穿孔、泄露,给生产企业带来严重的财产损失,同时也会给公共环境带来巨大的损害[1] 。
因此,为了减少腐蚀造成的这些严重的后果,增强油气管道使用的寿命,进一步提高油气管道的防腐技术是十分必要的。
这就要求对油气管道的防腐技术有更加深刻的了解与研究。
20世纪50 年代以前,国外长油气输管道主要采用石油沥青和煤焦油沥青作为外防腐材料。
20 世纪60 年代,研制出了一些性能很好的塑料防腐材料,例如黏胶带,热塑涂层,粉末融结涂层等[2] 。
20 世纪70 年代以来,由于管道施工遇到一些严酷的自然环境,对防腐层性能提出了更严格的要求,因此,在管道防腐材料的研究中,都大力发展复合材料或复合结构,强调防腐层要具有良好的介电性能、物理性能,稳定的化学性能和较宽的温度适应性能,以达到防腐、绝缘、保温、增加强度等多种功能。
三层聚乙烯是在20 世纪80 年代由欧洲研制成功并开始使用的。
一经问世就在许多工程上得到了应用,尤其是欧洲国家,其应用呈不断上升的趋势[3] 。
我国管道防腐技术是从应用沥青类防腐层开始,自二十世纪50 年代到70 年代的东北输油管道都采用石油沥青防腐层。
70 年代后期到80 年代初,随着国外技术材料的引入应用,胶带、夹克、环氧粉末等相继投入使用,而后各种防腐层均有使用[3] 。
进入90 年代后,煤焦油瓷漆开始在我国的西部长输管道建设中得到应用,如沙漠输油管全线采用煤焦油瓷漆防腐层。
90 年代后期熔结环氧粉末和三层聚乙烯逐渐形成主流,作为最新的防腐材料,双层熔结环氧也有的少量应用[4] 。
目前,国内油气管道防腐技术已达到了发达国家20 世纪末的防腐水平。
经过多年的发展,防腐技术也有了很大的进步与发展。
氮化的作用和工艺要求

氮化的作用和工艺要求
氮化是一种工艺过程,通过在材料表面引入氮元素来改变其表面性质。
氮化常用于金属和合金的处理,其作用和工艺要求如下:
作用:
1.硬度增加:氮化可以显著提高材料表面的硬度和耐磨性,使其更耐用和耐磨损。
2.耐腐蚀性提高:经过氮化处理后的材料表面通常具有更好的抗腐蚀性能,更耐高温、耐腐蚀。
3.改善表面摩擦性能:氮化可以改善材料的表面润滑性能,降低摩擦系数。
4.提高导热性和电性能:在某些情况下,氮化处理可以提高材料的导热性和电性能。
工艺要求:
1.温度和时间控制:氮化过程通常需要在高温下进行,要求温度和时间能够精确控制。
常见的氮化方法包括气体氮化和盐浴氮化,它们的工艺条件略有不同。
2.氮气气氛:在气体氮化过程中,氮气气氛的控制是至关重要的。
材料暴露在氮气中,氮原子渗透到材料表面形成氮化层。
3.材料表面准备:在进行氮化处理之前,材料的表面通常需要经过清洁和抛光等处理,以确保氮原子能够充分渗透并均匀分布在表面。
4.冷却和处理后工艺:氮化完成后,通常需要适当的冷却和后续处理,如淬火、回火等,以保证材料具有理想的性能和结构。
5.工艺环境控制:控制氮化过程的工艺环境,包括气氛、压力、温度和处理时间等,对于确保氮化效果至关重要。
氮化是一种有效的材料表面处理方法,可以显著改善材料的性能,但需要在合适的工艺条件下进行,以确保所需的性能提升。
氮化基础

氮化基础氮化处理技术氮化作为热处理中的一项重要处理工艺,它有着多种形式。
每一种工艺都对应着不同的性能特点,希望在此大家谈谈自己的经验与看法,以便共同提高。
我单位的氮化处理常用的就有六种,当然了也包括了复合氮化技术。
复合氮化——QPQ这一类氮化处理的特点是:高耐磨、高抗氧化能力。
它主要克服的是摩擦磨损,其抗咬合能力非常的强,接近渗硫后的效果。
概念:(软)氮化是向钢的表面层渗入氮原子的过程,其目的是提高表面硬度和耐磨性,以及提高疲劳强度和抗腐蚀性。
它是利用氨气或含氮原子的有机液体在加热时分解出活性氮原子,被钢吸收后在其表面形成氮化层,同时向心部扩散。
氮化通常利用专门设备或井式渗(氮)碳炉来进行。
适用于各种高速传动精密齿轮、机床主轴(如镗杆、磨床主轴),高速柴油机曲轴、阀门、工具等。
氮化工件工艺路线:锻造-退火-粗加工-调质-精加工-除应力-粗磨-氮化-精磨或研磨(一般情况下氮化后直接使用)。
由于氮化层薄,并且较脆,因此要求有较高强度的心部组织,所以要先进行调质热处理,获得回火索氏体,提高心部机械性能,保证氮化层质量。
钢在氮化后,不再需要进行淬火便具有很高的表面硬度及耐磨性。
氮化处理温度低,变形很小,它与渗碳、感应表面淬火相比,变形小得多。
钢的软氮化:又名氮碳共渗;氮碳共渗是向钢的表层同时渗入碳和氮的过程,习惯上氮碳共渗又称作氰化。
目前以气体氮碳共渗(即气体软氮化)应用较广。
其主要目的是提高钢的硬度、耐磨性、疲劳强度和抗咬合性渗氮(软氮化)的常见缺陷一、硬度偏低生产实践中,工件渗氮(软氮化)后其表面硬度有时达不到工艺规定的要求,轻者可以返工,重者则造成报废。
造成硬度偏低的原因是多方面的:设备方面:如系统漏气造成氧化;材料:如材料选择欠佳;前期热处理:如基体硬度太低,表面脱碳严重等;预先处理:如进炉前的清洁方式及清洁度。
工艺方面:如渗氮(软氮化)温度过高或过低,时间短或氮势不足等等。
所以具体情况要具体分析,找准原因,解决问题。
氮化工艺技术

氮化工艺技术氮化工艺技术是一种利用高温气氛中的氮气与固体或液体材料发生反应,形成氮化物薄膜或氮化物材料的技术。
该技术具有独特的优点,广泛应用于材料加工、电子器件制备、表面改性等领域。
氮化工艺技术主要分为两种类型:气氛氮化和离子氮化。
气氛氮化是在高温氮气气氛下,通过氮化源或氨气在材料表面形成氮化物薄膜的过程。
这种方法具有操作简单、适用性广、成本低的优点。
离子氮化是将待处理物体放置在低压辉光放电等离子体中,通过离子轰击和表面反应形成氮化物薄膜。
这种方法具有薄膜质量优良、成膜速率快的优点。
氮化工艺技术在材料加工领域具有重要应用。
一方面,氮化工艺可用于制备高硬度和高氮含量的刀具涂层。
这种涂层具有优异的耐磨性和高温性能,可以显著提高刀具寿命和切削加工质量。
另一方面,氮化工艺还可用于金属、陶瓷、玻璃等材料的表面改性。
通过氮化处理,可在表面形成致密、高硬度的氮化物层,显著提高材料的抗磨损、耐腐蚀和绝缘性能。
氮化工艺技术在电子器件制备领域也有广泛应用。
一方面,氮化工艺可用于制备氮化硅(Si3N4)绝缘层。
这种绝缘层具有优异的耐电压和绝缘性能,可用于封装电子元器件,提高器件的可靠性和稳定性。
另一方面,氮化工艺还可用于制备氮化硼(BN)材料。
氮化硼具有高热导率和良好的绝缘性能,可用于制备高功率电子器件的散热材料。
除了以上应用,氮化工艺技术也被广泛应用于太阳能电池、光学薄膜等领域。
例如,氮化硅材料可用于制备太阳能电池的抗反射膜,提高光电转换效率。
氮化硼材料可用于制备光学薄膜的硬度保护层,延长薄膜的使用寿命。
总之,氮化工艺技术是一种重要的表面工艺技术,具有广泛的应用前景。
随着材料科学和制备技术的不断发展,氮化工艺技术将进一步完善和推广,为各领域的材料加工和器件制备提供更多可能性。
氮化处理技术在塑料制品中的应用研究与展望

氮化处理技术在塑料制品中的应用研究与展望氮化处理技术是一种通过在材料表面形成氮化物层的方法,可以显著提高材料的硬度、耐热性、耐磨损性和耐腐蚀性。
在塑料制品领域,氮化处理技术的应用得到了广泛关注和研究。
本文将对氮化处理技术在塑料制品中的应用研究进行探讨,并展望未来的发展方向。
首先,氮化处理技术可以克服塑料制品在硬度和耐磨损性方面的缺陷。
由于塑料制品的相对软性和易磨损性,其在一些应用中容易出现磨损和损坏的情况。
而通过氮化处理,可以在塑料表面形成硬度较高的氮化物层,从而显著提高塑料制品的硬度和耐磨损性。
这使得塑料制品可以在更为恶劣的工作环境下使用,延长使用寿命,降低维修和更换成本。
其次,氮化处理技术也可以提高塑料制品的耐热性。
由于塑料制品的热稳定性较差,常常在高温环境下发生软化甚至熔化的现象。
而氮化处理技术可以通过形成氮化物层来提高塑料制品的耐热性。
氮化物具有较高的熔点和热导率,可以有效地改善塑料制品在高温下的使用性能。
此外,氮化处理技术还可以增强塑料制品的耐腐蚀性。
常见的塑料材料如聚氯乙烯(PVC)、聚乙烯(PE)等在一些酸、碱等腐蚀性介质下容易发生腐蚀,导致材料性能下降。
而通过氮化处理技术,可以在塑料表面形成氮化物层,起到一定的防腐蚀作用,提高塑料制品的耐腐蚀性,延长使用寿命。
尽管氮化处理技术在塑料制品中的应用前景广阔,但仍存在一些挑战和局限性。
首先,目前氮化处理技术仍处于发展阶段,对于不同类型的塑料材料和工艺参数的氮化处理效果仍需要进一步研究和优化。
其次,氮化处理技术在大规模应用时可能面临成本高、加工周期长、设备复杂等问题。
此外,氮化处理技术对于塑料制品的应用范围仍存在一定限制,不同类型的塑料材料在氮化处理中的适应性可能存在差异。
在未来的发展中,可以通过以下途径进一步推动氮化处理技术在塑料制品中的应用。
首先,可以加大对于不同类型塑料材料的氮化处理研究和优化,以提高处理效果和适用范围。
其次,可以探索和优化氮化处理技术的工艺参数,以缩短加工周期、降低成本并提高生产效率。
- 1、下载文档前请自行甄别文档内容的完整性,平台不提供额外的编辑、内容补充、找答案等附加服务。
- 2、"仅部分预览"的文档,不可在线预览部分如存在完整性等问题,可反馈申请退款(可完整预览的文档不适用该条件!)。
- 3、如文档侵犯您的权益,请联系客服反馈,我们会尽快为您处理(人工客服工作时间:9:00-18:30)。
四、室 内 试 验
盐雾试验前的防腐油管短接
盐雾试验后的防腐油管短接
96小时盐雾试验后氮化和未氮化油管的对比
氮化防腐油管试样
被腐蚀掉的 油管机体 外防腐层
内防腐层
氮化防腐油管螺纹试样
被腐蚀掉的 油管机体
螺纹机体
外防腐层
五、氮化油管现场应用
(一)油管短接试验
下井时间:2003年7月 下井情况:同井下入氮化防腐油管和
三、氮化层的微观组织
金属
放大倍数: 400× 腐蚀剂: 4%硝酸酒精
放大倍数: 400× 腐蚀剂: 4%硝酸酒精
微观组织
防腐层ε相
防腐层ε相
材料名称:42MnMo7(N80) 放大倍数: 400× 腐蚀剂: 4%硝酸酒精
N80氮化油管防腐层金相照片
材料名称: 37Mn5(J55) 放大倍数: 400× 腐蚀剂: 4%硝酸酒精
经过3年的现场试验应用,防腐耐磨效果得到了大港油 田公司的认可;在2006年底,一次性推广应用3800吨氮 化油管,用于注水井、抽油机井的防腐治理。
六、氮化防腐油管的优点
1、一次处理可产生内外两个防腐层。 2、耐腐蚀层均匀、致密,抗腐蚀能力强。 3、耐腐蚀层在油管机体上产生,内孔没有缩径,不会
剥离、串皮。 4、表面硬度高,不怕挤压、磕碰和大钳卡咬。 5、油管螺纹得到强化,防止“粘扣”,提高丝扣寿命。 6、对油井管杆偏磨起到缓解作用。
氮化防腐油管技术介绍
内容
一、金属的氮化 二、氮化层的结构和性质 三、氮化层(金属、油管)的微观组织 四、室内试验 五、现场应用 六、氮化防腐油管的优点
一、金属的氮化
将金属材料放入富氮的活性介质(离子状态)中加 热,使氮离子( N- )渗入钢的表面,改变表面化学成份 ,在金属表面形成一层富氮的化合物层,使表面合金化 ,在不改变材料基本性能的情况下,提高材料表面的硬 度、耐磨性、抗腐蚀性,从而使该金属材料成为一种新 型的复合材料 。
通过氮化处理技术可以显著提高金属表 面的抗腐蚀性能,这一技术具有广泛的适用 性;因此应用领域在日益扩大,目前已经发 展成为一种成熟的表面防腐技术。
官84-51井现场试验
修井记录
1999年6月投产 2004年12月检电第92根油管丝扣漏。 2005年1月 检电查漏,第133根油管
腐蚀造成管体有1个3mm孔。 2005年5月检电查漏,第56根油管漏。 2005年6月检电,第72根油管漏,更
换氮化防腐油管。
官922-1井现场试验
修井记录
1994年10月投产 2003年11月检电,油管丝扣腐蚀磨损严重 2004年 1月 检电查漏,第29根油管腐蚀造
(二)整井试验
中10-58 小集6-2井 官84-51 官922-1 专采41-35
2004.7-2007.6 2004.8-2007.6 2005.6-2007.6 2005.7-2007.6 2005.11-2007.6
ห้องสมุดไป่ตู้
小集6-2井现场试验
下入的防腐油管(2-7/8) 使用后的状况 同井同时下入的普通油管(3-1/2)使用后的状况
氮化油管生产现场
经氮化防腐处理的油井管
二、氮化层的结构和性质
结构组成:
白 亮 层 20-30 μ
扩 散 层 0.1-0.2mm
白亮层
化学性质:
扩散层
化学成分为Fe2-3N,性质稳定 的化合物,具有良好的抗腐蚀性能。
物理性质:
组织均匀致密,硬度高,有良好的 耐磨性,被称为ε相,在金相显微镜 下呈白亮色,故称为“白亮层”。
(低温化学热处理:)
(将工件放在一定的活性介质中加热并保温,使介质分解 或电离,产生的能渗入元素的活性原子或离子,在保温过程 中不断地被工件表面吸附,并向工件内部扩散渗入,以改变 工件表层的化学成分,使表面合金化,从而改善钢材的组织 和性能,在工件表层获得高硬度、耐磨损、耐腐蚀的同时, 心部仍保持良好的韧性。如渗碳、渗氮、渗硼等非金属;渗 铬、镍、铝等金属。碳氮共渗抽油泵泵筒、氮化防腐油管都 是采用这种化学热处理方法得到的产品。)
成2个2mm的洞。 2004年7月检电,单流阀因腐蚀泄漏。 2005年7月检电,第95根油管腐蚀造成8mm
的洞。
难采公司长26-19井现场试验
修井记录
2004年11月27日油井转注, 油压28MPa,套管26MPa,历时180 天左右 。2005年6月17日油压、套 压突然下降,起井后查找原因,油 管腐蚀严重造成泄漏。为恢复注水, 决定更换氮化防腐油管,并实施保 护套管注水。
不锈钢内衬油管短接各一个 起出时间:2004年9月
同时下入和起出的氮化油管与不锈钢内衬油管
(2003年7月~2004年9月)
氮化油管与不锈钢内衬油管外表面防腐性能对比
清洗后的氮化油管与不锈钢内衬油管内表面
氮化油管内表面
不锈钢内衬油管内表面
新氮化油管
下井12个月后起出的氮化油管
下井12个月后起出的普通油管