一氧化碳变换.
一氧化碳的变换

一氧化碳变换时半水煤气借助于催化剂的作用,在一定温度下,水蒸气反应,生成二氧化碳和氢的工艺过程。
通过变换即除去了一氧化碳,又得到了合成氨的原料气氢和氨加工的原料气二氧化碳。
近年来,变换工段由于采用了低温高活性的催化剂和高串低,高-低-低(俗称“中串低”、“中-低-低”),全低变等多种新工艺流程,加强了热量回收利用,工段面貌发生了很大变化。
1、一氧化碳变换反应的基本原理时什么?其反应的特点时怎么样的?一氧化碳变换反应是在一定条件下,半水煤气中的一氧化碳和水蒸气反应生成氢气和二氧化塔的工艺过程。
CO + H2O <==> CO2 +H2+41kj/mol这是一个可逆放热反应,从化学平衡来看,降低反应温度,增加水蒸气用量,有利于上述可逆反应向二氧化碳和氢气的方向移动,提高平衡变换率。
但是水蒸气增加到一定值后,变换率增加幅度会变小。
温度对变化反应的速度影响较大,而且对正逆反应速度的影响不一样。
温度升高,放热反应即上述变换反应速度增加的慢,逆反应(吸热反应)速度增加得快。
因此,当变换反应开始时,反应物浓度大,提高温度,可加快变换反应,在反应的后一段,二氧化碳和氢的浓度增加,逆反应速度加快,因此,需降低反应温度,使逆反应速度减慢,这样可得到较高的变换率。
提高变化压力,分子间的有效碰撞次数,可以加快变换反应速度,提高催化剂的生产能力。
2“高串低”工艺与传统的高温变换工艺主要有什么不同?有何优点?传统的高温变换工艺,变换炉入口温度一般控制在320~340℃。
在流程设置上一般是一个变换炉,炉内装填铁-铬系催化剂,分两段或三段,半水煤气从上到下一次通过各段催化此后即完成变换过程。
“高串低”工艺与创痛的高温变换工艺主要不同之处是在原高变炉之后,又串联了一个装有钴-钼系列耐硫宽温催化剂的低变炉,形成高变串低变的工艺流程。
耐硫宽温变换催化剂在“高串低”工艺中被利用做低变催化剂。
低变炉入口气体温度一般可控制在210~230℃。
一氧化碳低温变换

一氧化碳的低温变换CO变换的工艺流程主要由原料气组成来决定的,同时还与催化剂、变换反应器的结构,以及气体的净化要求有关。
目前低温变换主要是串接在中温变换催化剂后作为一氧化碳深度变换的。
而入口一氧化碳含量5%-8% , 最高使用温度不超过300℃。
中变串低变流程一般采用两种方法,一是中变炉外加低变炉, 另一种为变换炉中一二层用中变触媒, 三层使用低温触媒。
两种方法都使系统出口一氧化碳含量降至1%左右, 起到稳定生产、增产节能之效果。
1.中(高)变-底变串联流程采用此流程一般与甲烷化脱除少量碳氧化物相配合。
这类流程先通过中(高)温变换将大量CO变换达到3%左右后,再用低温变换使一氧化碳含量降低到0.3%-0.5%,。
为了进一步降低出口气中CO含量,也有在低变后面串联一个低变的流程。
当CO含量较高时,变换气一般选择在炉外串低变;而一氧化碳含量较低时,可选择在炉内串低变。
中串低流程中要主要两个问题,一是要提高低变催化剂的抗毒性,防止低变催化剂过早失活;二是要注意中变催化剂的过度还原,因为与单一的中变流程相比,中串低特别是中低低流程的反应汽气比下降,中变催化剂容易过度还原,引起催化剂失活、阻力增大及使用寿命缩短。
2.全低变流程中(高)变-低变串联流程操作繁琐,设备增加,特别是特殊材料阀门的选用给管理带来了许多不便。
使用全低变变换催化剂代替原Fe-Cr系中变催化剂,在低温下完成变换即可克服以上两种工艺的缺点,又能达到理想的目的。
全低变工艺采用宽温区的钴钼系耐硫变换催化剂,主要有下列优点。
(1)催化剂的起始活性温度低,变换炉入口温度及床层热点温度低于中变炉入口及热点温度100-200℃。
这样,就降低了床层阻力,缩小了气体体积约20%,从而提高了变换炉的生产能力。
(2)变换系统处于较低的温度范围内操作,在满足出口变换气中CO含量的前提下,可以降低入炉蒸汽量,使全低变流程的蒸汽消耗降低。
使用全低变变换催化剂代替原。
一氧化碳的变换技术62.
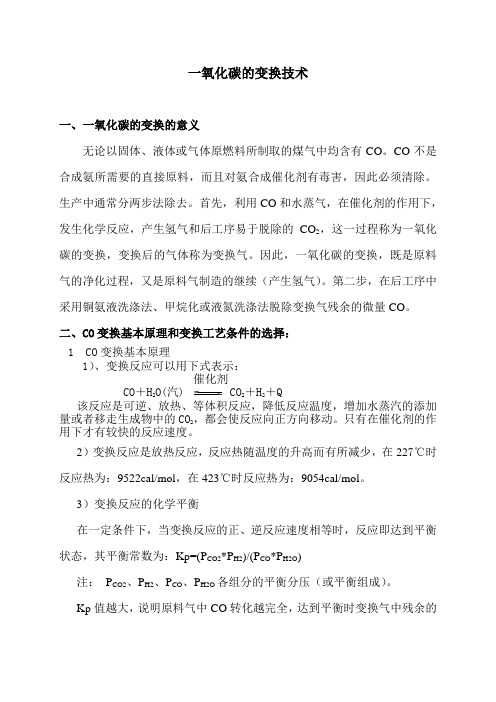
一氧化碳的变换技术一、一氧化碳的变换的意义无论以固体、液体或气体原燃料所制取的煤气中均含有CO 。
CO 不是合成氨所需要的直接原料,而且对氨合成催化剂有毒害,因此必须清除。
生产中通常分两步法除去。
首先,利用CO 和水蒸气,在催化剂的作用下,发生化学反应,产生氢气和后工序易于脱除的CO 2,这一过程称为一氧化碳的变换,变换后的气体称为变换气。
因此,一氧化碳的变换,既是原料气的净化过程,又是原料气制造的继续(产生氢气)。
第二步,在后工序中采用铜氨液洗涤法、甲烷化或液氮洗涤法脱除变换气残余的微量CO 。
二、CO 变换基本原理和变换工艺条件的选择:1 CO 变换基本原理1)、变换反应可以用下式表示:催化剂CO +H2O(汽2+H 2+Q该反应是可逆、放热、等体积反应,降低反应温度,增加水蒸汽的添加量或者移走生成物中的CO 2,都会使反应向正方向移动。
只有在催化剂的作用下才有较快的反应速度。
2)变换反应是放热反应,反应热随温度的升高而有所减少,在227℃时反应热为:9522cal/mol ,在423℃时反应热为:9054cal/mol 。
3)变换反应的化学平衡在一定条件下,当变换反应的正、逆反应速度相等时,反应即达到平衡状态,其平衡常数为:Kp=(P CO2*P H2)/(P CO *P H2O )注: P CO2、P H2、P CO 、P H2O 各组分的平衡分压(或平衡组成)。
Kp 值越大,说明原料气中CO 转化越完全,达到平衡时变换气中残余的CO含量越少。
由于变换反应是放热反应,降低温度有利于平衡向右移动,因此平衡常数随温度的降低而增大。
250℃时为86.51,450℃时为:7.311。
在工业生产中,受催化剂装填量、设备投资的经济效益等因素影响,反应不可能也没必要达到平衡,只能尽可能接近平衡。
实际的流程组合中,一般利用高温段之后再进行低温变换,就是为了提高反应平衡常数,从而提高变换率,降低变换气CO含量。
一氧化碳变换综述

的氧化铬、氧化铝、氧化锰、氧化钡等, 它们的存在,可增加催化剂抗烧结的作用, 延长催化剂使用寿命,增长催化剂的成型 性能和机械强度。 目前,中小型氮肥厂的低变催化剂均采用 Co-Mo系催化剂。Co-Mo系变换催化剂是 以Co, Mo为有效组份,以Al2O3为骨架, 碱金属或稀土金属的氧化物为辅助催化剂。 Co-Mo系变换催化剂使用前必须先进行硫 化,生成CoS, MoS2才能获得高的活性。 1.3.2 低变催化剂的主要成分
全低变的工艺流程
半水煤气 油 分 离 器 活 性 炭 滤 油 器
变 换 气 换 热 器
煤 气 换 热 器
第 一 变 换 炉
变换气 工段
变 换 气 冷 却 器
淬 冷 过 滤 器
淬 冷 过 滤 器
第 二 变 换 炉
Ⅰ
Ⅱ
半水煤气首先进入油水分离器,脱除部分固体和液体杂质后 进入活性炭滤油器,进一步脱除杂质。经净化的半水煤气 进入变换气换热器与从第二变换炉出来的变换气进行逆向 热交换,使其温度上升到180 ℃左右,变换气温度下降到 160 ℃左右。出变换气换热器的半水煤气再进入煤气换热 器与从第一变换炉出来的变换气进行逆向热交换,变换气 自身的温度下降到300 ℃左右,半水煤气升温到200 ℃左 右。出煤气换热器的半水煤气与来自管网的中压水蒸气混 合,一方面使半水煤气温度上升到变换反应温度,另一方 面使半水煤气增湿,并达到设计要求所需要的汽气比进入 第一变换炉发生变换反应,在第一变换炉内CO的变换率 可达到60%左右。经第一变换炉变换后出来的变换气进入 煤气换热器与半水煤气逆向换热后进入淬冷过滤器I,逆 向与喷淋下来的冷却水换热并使冷却水汽化,此时变换气 的温度下降到230 ℃左右,冷却水和变换气换热后汽化, 从而使蒸汽含量达到设计要求,湿变换气进入第二变换炉 第一段催化剂床层进行变换反应。经第二变换炉第一段催 化剂床层变换反应后CO的变换率可达到85%左右,温度
一氧化碳变换操作规程
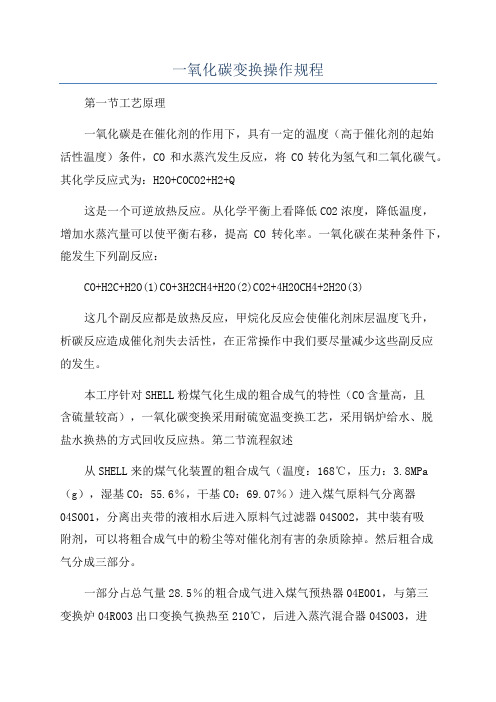
一氧化碳变换操作规程第一节工艺原理一氧化碳是在催化剂的作用下,具有一定的温度(高于催化剂的起始活性温度)条件,CO和水蒸汽发生反应,将CO转化为氢气和二氧化碳气。
其化学反应式为:H2O+COCO2+H2+Q这是一个可逆放热反应。
从化学平衡上看降低CO2浓度,降低温度,增加水蒸汽量可以使平衡右移,提高CO转化率。
一氧化碳在某种条件下,能发生下列副反应:CO+H2C+H2O(1)CO+3H2CH4+H2O(2)CO2+4H2OCH4+2H2O(3)这几个副反应都是放热反应,甲烷化反应会使催化剂床层温度飞升,析碳反应造成催化剂失去活性,在正常操作中我们要尽量减少这些副反应的发生。
本工序针对SHELL粉煤气化生成的粗合成气的特性(CO含量高,且含硫量较高),一氧化碳变换采用耐硫宽温变换工艺,采用锅炉给水、脱盐水换热的方式回收反应热。
第二节流程叙述从SHELL来的煤气化装置的粗合成气(温度:168℃,压力:3.8MPa (g),湿基CO:55.6%,干基CO:69.07%)进入煤气原料气分离器04S001,分离出夹带的液相水后进入原料气过滤器04S002,其中装有吸附剂,可以将粗合成气中的粉尘等对催化剂有害的杂质除掉。
然后粗合成气分成三部分。
一部分占总气量28.5%的粗合成气进入煤气预热器04E001,与第三变换炉04R003出口变换气换热至210℃,后进入蒸汽混合器04S003,进入该混合器前,来自蒸汽管网的过热蒸汽(4.4MPa,282℃)与粗合成气混合。
进蒸汽混合器的蒸汽量由调节阀FV-04005调节,该蒸汽量与28.5%的粗合成气量是比例控制,保证进入一变、汽、气比不低于1.09,原料气管线设有TV-04003调节阀旁路(测温点TE-04003在一变的入口。
混合后的粗合成气进入煤气换热器04E002管侧与来自第一变换炉04R001出口的变换气换热。
合成气温度由TV-04003控制在约255℃左右,进入第一变换炉04R001进行变换反应(一变入口湿基CO:33.1%)。
一氧化碳高温变换催化剂使用说明-图片版[1]
![一氧化碳高温变换催化剂使用说明-图片版[1]](https://img.taocdn.com/s3/m/310e8e95dd88d0d233d46ae2.png)
一氧化碳高温变换催化剂使用说明一、变换反应原理一氧化碳变换反应是指一氧化碳与水蒸汽作用生成二氧化碳和氢气的反应,反应如下:C O+H2O H2+C O2+41.19k J/m o l上式是一个典型的气固相反应,它在合成氨,合成甲醇,制氢气、羰基合成气、城市煤气工业中得到了广泛的应用。
一氧化碳变换反应是可逆放热反应,该反应在一般条件下进行得非常缓慢,远不能满足工业生产的需要。
在变换催化剂作用下,可显著提高变换反应的速度,并可防止和减少副反应。
根据化学平衡原理,反应温度越高,变换反应的平衡转化率越低。
在绝热的变换反应器中,为了获得较高的CO变换率,就需要尽可降低催化剂床层入口温度,以使床层出口温度尽可能低,这就要求催化剂具有良好的低温活性。
为了保证变换催化剂不被过度还原,必须在超过化学计量的汽气比下操作。
催化剂使用温度越高,必需采用的汽气比也越高。
如果使用低温活性好的催化剂,整个催化剂床层可在较低的温度下操作,则可以降低变换系统的操作汽气比,节省蒸汽消耗。
二、催化剂的装填催化剂的装填非常重要,将直接影响床层的压力降和气流分布,进而影响催化剂效能的正常发挥。
催化剂的装填方案应认真讨论,可装单一型号的催化剂,也可采用混装法。
如果要使用部分筛过的、比较完好的旧催化剂,应该在一段上部装三分之二的低温活性好的新催化剂;第三段应全装新催化剂;而在一段剩下的三分之一和二段温度较高的部位可装填部分旧催化剂。
这样装填既能发挥新催化剂的低温活性又能合理利用旧催化剂的剩余活性。
推荐装填高度比,二段式1:0.8,三段式1:1:1。
如此装填的目的在于保证一段在较高温度下加快变换反应的速度,而在变换炉最末端温度较低的条件下获得较高的变换率,在装填总量相等的情况下,变换率最高,或变换率一定的情况下蒸汽消耗最低。
1.催化剂装填之前要清除变换炉内杂物,并根据各段的催化剂装量,在炉内标出催化剂装填的高度。
2.炉篦上面要铺一层耐火球和金属网。
一氧化碳变换技术交流

℃
• 但实际上完全按最适宜温度曲线操作是不可能的,因 为在反应开始时,最适宜温度最高(以中温变换为例, 要达到620℃以上),大大超过催化剂的耐热温度, 而且热量的来源是个问题。随着反应的进行,要不断 地、准确地按照最适宜温度的需要移出反应热是极为 困难的,见二 段CO变换的T-x图。 图中: CD即为最适宜温度曲线,AB为平衡曲线,EF线为第 一段绝热反应线,FG线表示段间间接换热降温过程。 GH线表示第二段绝热反应线。。 • 变换过程的温度应综合各个方面因素来确定,主要原 则是: • 1)、反应开始温度应高于催化剂活性温度10~20℃ 左右。另外必须要高于气体露点温度20℃以上(防止 原料气析水,一是使催化剂粉碎结块,二是腐蚀设 备)。
CS2+4H2 2H2S+CH4+246 kJ∕mol MoO3+2H2S+H2 MoS2+3H2O+48.1 kJ∕mol CoO+H2S CoS+H2O+13.4 kJ∕mol • 升温硫化一般采用循环硫化法,升温硫化阶段所需要的热 量主要靠电加热器提供。 • 3)国内外Co-Mo系耐硫变换催化剂的发展历程 • ⑴1969年德国BASF公司开发成功的K8-11耐硫变换催化 剂(镁铝尖晶石复合材料为载体),1978年首次实现工业 化的应用,用于重油部分氧化法制合成气流程和加压煤气 化制合成氨流程的CO变换。它的主要特点是以镁铝尖晶 石为载体,硫化后活性高,耐高水蒸汽分压,可在高压下使用, 抗毒物能力强,能再生,平均寿命 3~5年。
• 由于变换反应是放热反应,降低温度有利于平衡 向右移动,因此平衡常数随温度的降低而增大。 例如:250℃时为86.51,450℃时为:7.311。 • 在工业生产中,受催化剂装填量、设备投资的经 济效益等因素影响,反应不可能也没必要达到平 衡,只能尽可能接近平衡。 • 实际生产的流程组合中,一般利用高温段之后再 进行低温变换,就是为了提高反应平衡常数,从 而提高变换率,降低变换气CO含量。
一氧化碳的变换

二、一氧化碳变换反应的化学平衡
(一)变换反应的热效应 变换反应的标准反应热△ H298 ,可以用有关气体的标准生成热数据进
行计算:
上一页 下一页 Байду номын сангаас回
其他副反应如下。
下一页 返回
项目三 一氧化碳的变换
(一)甲烷化反应 在一氧化碳与水蒸气共存的系统中,是含有C, H, O三个元素的系统。
从热力学角度,不但可能进行式(3一3一1)的变化反应,而且还可进行其 他反应,如:
上一页 下一页 返回
项目三 一氧化碳的变换
这一点与甲烷蒸气转化、煤气化等系统中所出现的反应式有相似之处。 但是,由于所用催化剂对反应式(3 -3-1)具有良好的选择性,从而抑制了 其他反应的发生。在计算反应系统平衡组成时,采用反应式(3-3-1)的平 衡关系,其结果基本符合实际情况。从以上反应式看,降低温度和增加 压力有利于生成甲烷的反应。但在实际生成中采用的工艺条件下,这一 副反应是不会发生的。降低床层的热点温度、增加水/气、提高空速都可 以抑制甲烷化副反应的影响。
还可进行其他反应:
由于所用的催化剂对变换反应有良好的选择性,可抑制其他反应的发生, 因此副反应发生的概率很小。
(二)变换反应的平衡常数 一氧化碳变换反应通常是在常压或压力不太高的条件下进行,故平衡常
数计算时各组分用分压表示已足够精确。因此平衡常数KD可用下式计算:
上一页 下一页 返回
项目三 一氧化碳的变换
平衡常数是温度的函数,可通过范特荷莆方程式计算:
不同温度下一氧化碳变换反应的平衡常数见表3-3 -2。
一氧化碳的变换.
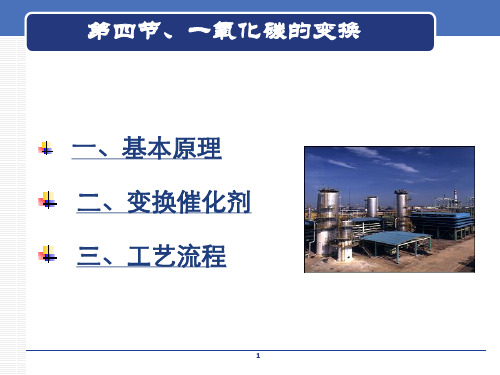
11
(二)、氧化锌法
❖氧化锌脱硫性能的好坏用硫容 量表示。所谓硫容就是每单位质 量氧化锌能脱除S的量。一些数 据如图所示。一些定性结论如下: 温度上升,硫容增加;空速增加, 硫容降低;汽气比上升,硫容下 降。
2、氧化锌脱硫剂:
100
ya,ya’ —分别为原料及变换气中一氧化碳的摩尔分率(干 基)
2
二、变换催化剂
❖ 1、中(高)变催化剂:
▪
以三氧化二铁为活性中心
▪ 铬、铜、锌、钴、钾等氧化物,可提高催化剂的活性
▪ 镁、铝等氧化物,可提高催化剂的耐热和耐毒性能。
❖ 目前常见的中(高)变换催化剂有:
▪ 铁铬系催化剂:以FeO3加Cr2O3为助催化剂。 ▪ 钴钼系催化剂:针对重油含S量高的耐高S变换催化剂。
K
0 p
pH2O
/
pH2S
10
❖ 一些条件下平衡S含量的计算值如下:
水蒸气含量/%
0.50 10 20
平衡硫含量/10-6 200℃ 0.000025 0.00055 0.005
300℃ 0.0008 0.018 0.16
400℃ 0.009 0.20 1.80
❖ 实际上天然气等原料中水蒸气含量很低,所以即使温度在400℃也可满足S含量 <0.1× 10-6的要求。 200℃含水20%时,S<0.005× 10-6,因此氧化锌也用在变 换工序作变换催化剂的保护剂。
提高其稳定性。 ❖ (2)低变催化剂的还原: ❖ CuO+H2=Cu+H2O △H0298=-86.7kJ/mol ❖ CuO+CO=Cu+CO2 △H0298=-127.7kJ/mol
一氧化碳变换
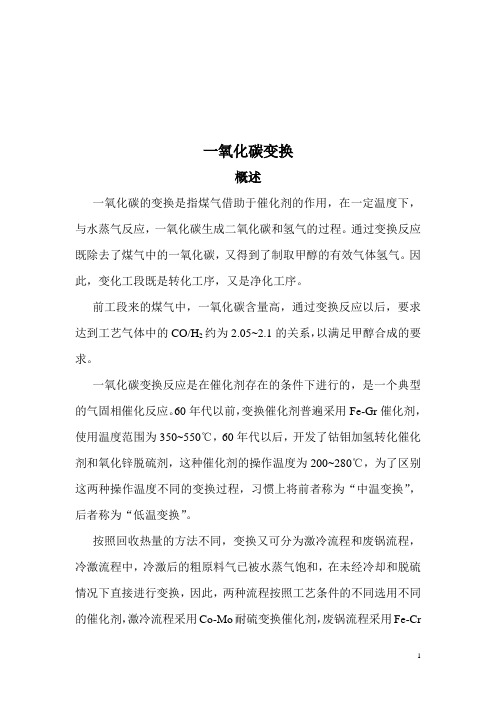
一氧化碳变换概述一氧化碳的变换是指煤气借助于催化剂的作用,在一定温度下,与水蒸气反应,一氧化碳生成二氧化碳和氢气的过程。
通过变换反应既除去了煤气中的一氧化碳,又得到了制取甲醇的有效气体氢气。
因此,变化工段既是转化工序,又是净化工序。
前工段来的煤气中,一氧化碳含量高,通过变换反应以后,要求达到工艺气体中的CO/H2约为2.05~2.1的关系,以满足甲醇合成的要求。
一氧化碳变换反应是在催化剂存在的条件下进行的,是一个典型的气固相催化反应。
60年代以前,变换催化剂普遍采用Fe-Gr催化剂,使用温度范围为350~550℃,60年代以后,开发了钴钼加氢转化催化剂和氧化锌脱硫剂,这种催化剂的操作温度为200~280℃,为了区别这两种操作温度不同的变换过程,习惯上将前者称为“中温变换”,后者称为“低温变换”。
按照回收热量的方法不同,变换又可分为激冷流程和废锅流程,冷激流程中,冷激后的粗原料气已被水蒸气饱和,在未经冷却和脱硫情况下直接进行变换,因此,两种流程按照工艺条件的不同选用不同的催化剂,激冷流程采用Co-Mo耐硫变换催化剂,废锅流程采用Fe-Cr变换催化剂。
第一节变换反应原理变换过程为含有C、H、O三种元素的CO和H2O共存的系统,在CO变换的催化反应过程中,除了主要反应CO+H2O=CO2+H2以外,在某种条件下会发生CO分解等其他副反应,分别如下:2CO=C+CO22CO+2H2=CH4+CO2CO+3H2=CH4+H2OCO2+4H2=CH4+2H2O这些副反应都消耗了原料气中的有效气体,生成有害的游离碳及无用的甲烷,避免副反应的最好方法就是使用选择性好的变换催化剂。
一、变换反应的热效应一氧化碳变换反应是一个放热反应,CO+H2O=CO2+H2+41kJ/gmol反应的热效应视H2O的状态而定,若为液态水,则是微吸热反应,若是水蒸气,则为放热反应。
变换反应的反应热随温度的升高而降低,具体反应热列表如下:表1 CO+H2O=CO2+H2的反应热温度℃25 200 250 300 350 400 450 500 550 △HkJ/gmol 41 39.8 39.5 39 38.5 38 37.6 37 36.6压力对变换反应的反应热影响较小,一般不做考虑。
一氧化碳变换

中温变换工艺设计方案目录前言 (2)1、背景 (2)2、分类 (2)3、工艺方法的选择 (2)反应原理 (3)中温变换催化剂 (4)工艺流程 (6)工艺条件 (7)设计体会与收获 (8)参考文献 (9)前言氨是一种重要的化工产品,主要用于化学肥料的生产。
合成氨生产经过多年的发展,现已发展成为一种成熟的化工生产工艺。
合成氨的生产主要分为:原料气的制取;原料气的净化与合成。
粗原料气中常含有大量的C,由于CO是合成氨催化剂的毒物,所以必须进行净化处理,通常,先经过CO变换反应,使其转化为易于清除的CO2和氨合成所需要的H2。
因此,CO变换既是原料气的净化过程,又是原料气造气的继续。
最后,少量的CO用液氨洗涤法,或是低温变换串联甲烷化法加以脱除。
1、背景变换是合成氨生产中的重要工序,同时也是一个耗能重点工序,而外加蒸汽量的大小,是衡量变换工段能耗的主要标志。
因此,尽量减少其用量对其过程的节能降耗具有重要意义。
从70年代以来,我国在变换工艺的节能降耗方面,进行了大量的科研开发和技改工作,先后开发了中变、中变串低变、全低变等变换工艺,使蒸汽消耗量从传统的中变消耗1 t/tNH 以上,降低到200 kg/tNH,从而形成一种能耗低、稳定可靠、周期长的变换工艺。
2、分类一氧化碳变换的工艺流程包括中变-低变串联流程、多段中变流程、全低变流程、中低低流程等。
3、工艺方法的选择变换工艺流程的设计,首先应依据原料气中的一氧化碳含量高低来加以确定。
以煤为原料气的中小型氨厂制得的半水煤气中含有较高的一氧化碳,所以需采用多段中变流程。
中变催化剂操作温度范围较宽,而且价廉易得,使用寿命长。
因此,在一氧化碳转换工艺设计中,我组选用中温变换工艺。
反应原理变换反应可用下式表示:此外,一氧化碳与氢之间还可发生下列反应(1-2) O H C H CO 22+⇔+(1-3)但是,由于变换所用催化剂对反应式(1-1)具有良好的选择性,从而抑制了其他副反应的发生。
一氧化碳变换

一氧化碳变换概述一氧化碳的变换是指煤气借助于催化剂的作用,在一定温度下,与水蒸气反应,一氧化碳生成二氧化碳和氢气的过程。
通过变换反应既除去了煤气中的一氧化碳,又得到了制取甲醇的有效气体氢气。
因此,变化工段既是转化工序,又是净化工序。
前工段来的煤气中,一氧化碳含量高,通过变换反应以后,要求达到工艺气体中的CO/H2约为2.05~2.1的关系,以满足甲醇合成的要求。
一氧化碳变换反应是在催化剂存在的条件下进行的,是一个典型的气固相催化反应。
60年代以前,变换催化剂普遍采用Fe-Gr催化剂,使用温度范围为350~550℃,60年代以后,开发了钴钼加氢转化催化剂和氧化锌脱硫剂,这种催化剂的操作温度为200~280℃,为了区别这两种操作温度不同的变换过程,习惯上将前者称为“中温变换”,后者称为“低温变换”。
按照回收热量的方法不同,变换又可分为激冷流程和废锅流程,冷激流程中,冷激后的粗原料气已被水蒸气饱和,在未经冷却和脱硫情况下直接进行变换,因此,两种流程按照工艺条件的不同选用不同的催化剂,激冷流程采用Co-Mo耐硫变换催化剂,废锅流程采用Fe-Cr 变换催化剂。
第一节变换反应原理变换过程为含有C、H、O三种元素的CO和H2O共存的系统,在CO变换的催化反应过程中,除了主要反应CO+H2O=CO2+H2以外,在某种条件下会发生CO分解等其他副反应,分别如下:2CO=C+CO22CO+2H2=CH4+CO2CO+3H2=CH4+H2OCO2+4H2=CH4+2H2O这些副反应都消耗了原料气中的有效气体,生成有害的游离碳及无用的甲烷,避免副反应的最好方法就是使用选择性好的变换催化剂。
一、变换反应的热效应一氧化碳变换反应是一个放热反应,CO+H2O=CO2+H2+41kJ/gmol反应的热效应视H2O的状态而定,若为液态水,则是微吸热反应,若是水蒸气,则为放热反应。
变换反应的反应热随温度的升高而降低,具体反应热列表如下:表1 CO+H2O=CO2+H2的反应热压力对变换反应的反应热影响较小,一般不做考虑。
一氧化碳变换反应工艺流程

一氧化碳变换反应工艺流程一氧化碳变换流程有许多种,包括常压、加压变换工艺,两段中温变换(亦称高变)、三段中温变换(高变)、高-低变串联变换工艺等等。
一氧化碳变换工艺流程的设计和选择,首先应依据原料气中的一氧化碳含量高低来加以确定。
一氧化碳含量很高,宜采用中温变换工艺,这是由于中变催化剂操作温度范围较宽,使用寿命长而且价廉易得。
当一氧化碳含量大于15%时,应考虑将变换炉分为二段或多段,以使操作温度接近最佳温度。
其次是依据进入变换系统的原料气温度和湿度,考虑气体的预热和增湿,合理利用余热。
最后还要将一氧化碳变换和残余一氧化碳的脱除方法结合考虑,若后工序要求残余一氧化碳含量低,则需采用中变串低变的工艺。
一、高变串低变工艺当以天然气或石脑油为原料制造合成气时,水煤气中CO含量仅为10%~13%(体积分数),只需采用一段高变和一段低变的串联流程,就能将CO含量降低至0.3%,图2-1是该流程示意图。
图2-1一氧化碳高变-低变工艺流程图1-废热锅炉2-高变炉3-高变废热锅炉4-预热器5-低变炉6-饱和器7-贫液再沸器来自天然气蒸气转化工序含有一氧化碳约为13%~15%的原料气经废热锅炉1降温至370℃左右进入高变炉2,经高变炉变换后的气体中一氧化碳含量可降至3%左右,温度为420~440℃,高变气进入高变废热锅炉3及甲烷化进气预热器4回收热量后进入低变炉5。
低变炉绝热温升为15~20℃,此时出低变炉的低变气中一氧化碳含量在0.3%~0.5%。
为了提高传热效果,在饱和器6中喷入少量软水,使低变气达到饱和状态,提高在贫液再沸器7中的传热系数。
二、多段中变工艺以煤为原料的中小型合成氨厂制得的半水煤气中含有较多的一氧化碳气体,需采用多段中变流程。
而且由于来自脱硫系统的半水煤气温度较低,水蒸气含量较少。
气体在进入中变炉之前设有原料气预热及增湿装置。
另外,由于中温变换的反应放热多,应充分考虑反应热的转移和余热回收利用等问题。
粗原料气的制取—一氧化碳变换(合成氨生产)

(1)硫化
Co-Mo系耐硫变换催化剂出厂时成品是以氧化物状态存在的,活 性很低,需要通过硫化,使其转化为硫化物方能显示其活性。催化剂 装入变换炉后,用含硫的工艺气体进行硫化。
(2)反硫化
由于催化剂的活性组分在使用时是以硫化物形式存在的,在CO变 换过程中,气体中有大量水蒸气,催化剂中的活性组分MoS2与水蒸气 有一水解反应平衡关系,化学反应式为:
• 变换反应进行的程度用变换率(平衡转化率)表示,即已经转换的一氧化碳量与变换前
的总一氧化碳量之比:
x (nCO n'CO ) nCO
• 变换过程存在H2O,气体组成表示有两种方式;一种是包括H2O的湿基组成,一种是不 包括H2O的干基组成。
• 若分析得到变换前后CO的干基组成分别为y和y’ ,1mol干基气体变换后为(1+y·x)mol的
来源
原料气
原料气 高变催化剂 工艺蒸汽或 冷激用水
毒害作用
损害物理性能; 氨溶解在冷凝水 中,会溶解铜
中毒程度
要求
暂时性
低变温度要高 于气体露点
生成硫化亚铜 永久性 小于1cm3/m3
氯化铜
永久性
小于 0.03ml/m3
Fe-Cr系(高变):活性温度高,抗硫性差。寿命为3~5年 Cu-Zn系(低变):低温活性好,但活性温度范围窄,对硫十分敏感,寿命短。
CONTENTS
01
03
02
04
一氧化碳变换:既是原料气制造的继续,又是净化过程。粗 原料气含CO 12 % ~40%,通常分两步将CO除去:
高温变换
一氧化 碳变换
使大部分CO转化为CO2和H2
低温变换
一氧化 将CO 降到0.3%左右 碳变换
一氧化碳变换工艺及催化剂分析

一氧化碳变换工艺及催化剂分析一氧化碳(CO)是一种无色、无味、无臭的气体,在环境中广泛存在,并且对人体健康和环境造成严重影响。
因此,探索有效的一氧化碳变换工艺和催化剂具有重要意义。
1.光催化:光催化是利用光能激发催化剂上的电子从而促进一氧化碳的转化。
常见的光催化剂包括二氧化钛(TiO2)、二氧化锌(ZnO)等。
这些光催化剂具有良好的光催化活性,可以通过吸收可见光或紫外光来激活,并参与一氧化碳转化反应。
光催化反应的优点是能量消耗低、选择性高、反应速率快,但其缺点是催化剂的稳定性较差,光催化效果易受环境条件影响。
2.电催化:电催化是利用电能输入到催化剂上,将一氧化碳电催化转化为二氧化碳。
常见的电催化剂包括铂(Pt)、钯(Pd)等贵金属材料。
这些电催化剂具有很好的电催化活性,可以高效地将一氧化碳氧化为无害的二氧化碳。
电催化反应的优点是能耗低、转化效率高,但其缺点是贵金属催化剂成本高、易受染料、杂质等的污染。
3.热催化:热催化是将一氧化碳和氧气在催化剂的存在下加热反应,使其发生氧化反应。
常见的热催化剂包括铂(Pt)、钼(Mo)等。
这些热催化剂具有高的氧化活性,可以在适当的温度和压力下将一氧化碳转化为二氧化碳。
热催化反应的优点是反应条件相对温和、催化剂稳定性较好,但其缺点是转化速率较慢、能耗较高。
催化剂的选择对一氧化碳变换的效果起着至关重要的作用。
常见的一氧化碳变换催化剂主要有贵金属催化剂、氧化物催化剂和过渡金属氧化物催化剂等。
贵金属催化剂具有高的催化活性和稳定性,在一氧化碳变换过程中表现出了较好的效果。
然而,由于贵金属催化剂的成本较高,因此在实际应用中存在一定的限制。
氧化物催化剂具有良好的催化活性和稳定性,并且相对贵金属催化剂来说成本较低,在一氧化碳变换中广泛应用。
过渡金属氧化物催化剂由于其良好的催化活性和稳定性,也被广泛研究和应用于一氧化碳变换中。
总之,一氧化碳变换工艺及催化剂的选择在净化空气、保护环境方面具有重要意义。
一氧化碳变换
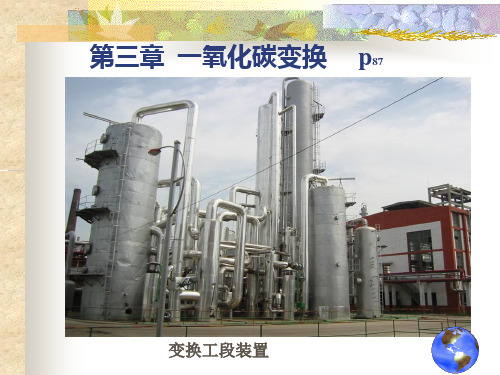
注:实际生产中,可测定原料气和变换气中的CO,且视为干基, 一氧化碳的转化率:
xp
ya ya (1
ya ya
)
100%
原料气 中CO含
量
变换气 中CO含
量
生产中用途:可测定原料气和变换气中的CO,判断问题; 确定催化剂用量
二、工艺条件对变换反应的影响
P100
温度
压力 影响因素 空速
低变催化剂的还原和钝化
还原剂:一氧化碳、氢气 反应:CuO+H2=Cu+H2O
CuO+CO=Cu+CO2 载体:氮气、过热蒸汽、天然气 毒物:硫化物、氯化物、冷凝水、油
南化集团研究院(南化院)铜系催化剂 NB207型一氧化碳低温变换催化剂
三、耐硫变换催化剂
组分:氧化钴、氧化钼 活性组分:硫化钴、硫化钼 载体:三氧化二铝 助剂:碱金属
第三节 工艺流程
工艺流程中应考虑的问题:
1、根据原料气co含量,满足变换率的要求
天然气制原料气、 有无甲醇产品时催
化剂的选择
2、防止催化剂超温
分段和段间降温方式
3、反应余热的充分利用,
达到催化剂反应温度降低能 耗
4、蒸气的回收和利用
降低外供蒸汽消耗
5、延长催化剂寿命
介质的净化
难点:方案的确定和流程的布置
第一节 一氧化碳变换的基本原理及热力学
一、化学平衡和平衡转化率 1、热效应
反应热:⊿H298,R=-4.868-1.2184T+1.1911×10-3T2-4.0625×10-6T3
温度/℃ 25
200 250 300 350 400 450
⊿H298,R -41.18 -40.07 -39.67 -39.25 -38.78 -38.32 -37.86 kJ/mol
一氧化碳变换反应方程式
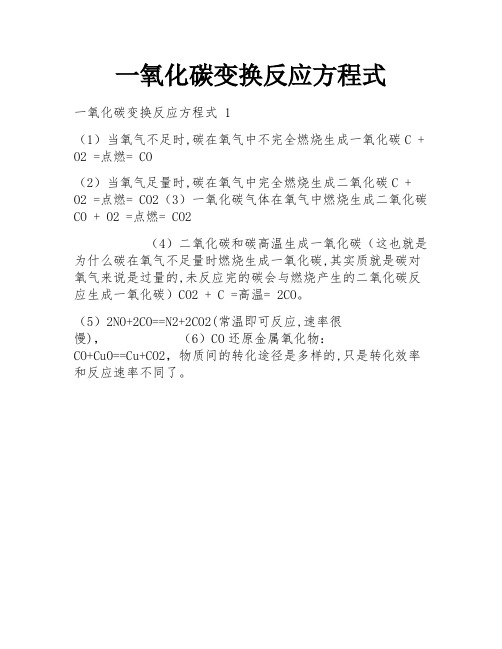
一氧化碳变换反应方程式
一氧化碳变换反应方程式 1
(1)当氧气不足时,碳在氧气中不完全燃烧生成一氧化碳C + O2 =点燃= CO
(2)当氧气足量时,碳在氧气中完全燃烧生成二氧化碳C +
O2 =点燃= CO2(3)一氧化碳气体在氧气中燃烧生成二氧化碳CO + O2 =点燃= CO2
(4)二氧化碳和碳高温生成一氧化碳(这也就是为什么碳在氧气不足量时燃烧生成一氧化碳,其实质就是碳对氧气来说是过量的,未反应完的碳会与燃烧产生的二氧化碳反应生成一氧化碳)CO2 + C =高温= 2CO。
(5)2NO+2CO==N2+2CO2(常温即可反应,速率很
慢),(6)CO还原金属氧化物:
CO+CuO==Cu+CO2,物质间的转化途径是多样的,只是转化效率和反应速率不同了。
co变换反应平衡曲线
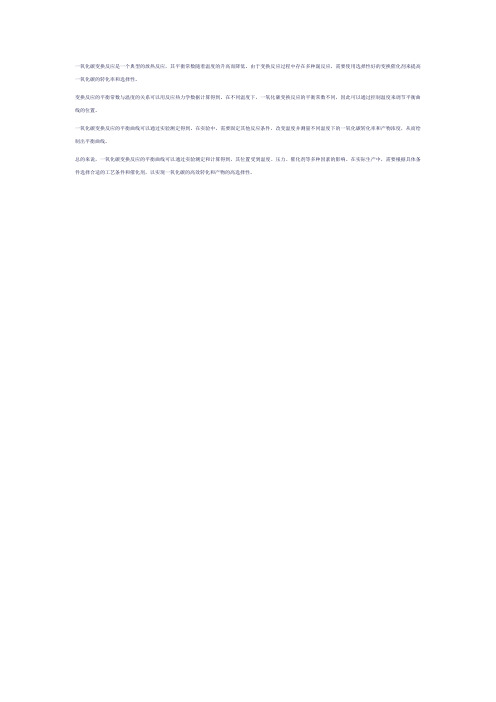
一氧化碳变换反应是一个典型的放热反应,其平衡常数随着温度的升高而降低。
由于变换反应过程中存在多种副反应,需要使用选择性好的变换催化剂来提高一氧化碳的转化率和选择性。
变换反应的平衡常数与温度的关系可以用反应热力学数据计算得到。
在不同温度下,一氧化碳变换反应的平衡常数不同,因此可以通过控制温度来调节平衡曲线的位置。
一氧化碳变换反应的平衡曲线可以通过实验测定得到。
在实验中,需要固定其他反应条件,改变温度并测量不同温度下的一氧化碳转化率和产物浓度,从而绘制出平衡曲线。
总的来说,一氧化碳变换反应的平衡曲线可以通过实验测定和计算得到,其位置受到温度、压力、催化剂等多种因素的影响。
在实际生产中,需要根据具体条件选择合适的工艺条件和催化剂,以实现一氧化碳的高效转化和产物的高选择性。
一氧化碳变换题库
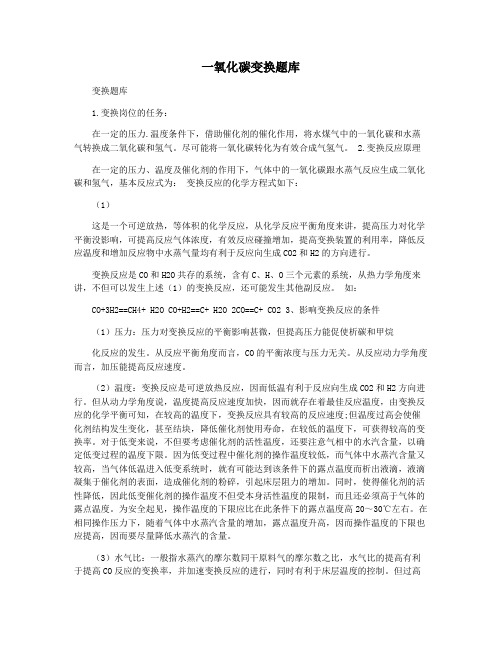
一氧化碳变换题库变换题库1.变换岗位的任务:在一定的压力.温度条件下,借助催化剂的催化作用,将水煤气中的一氧化碳和水蒸气转换成二氧化碳和氢气。
尽可能将一氧化碳转化为有效合成气氢气。
2.变换反应原理在一定的压力、温度及催化剂的作用下,气体中的一氧化碳跟水蒸气反应生成二氧化碳和氢气,基本反应式为:变换反应的化学方程式如下:(1)这是一个可逆放热,等体积的化学反应,从化学反应平衡角度来讲,提高压力对化学平衡没影响,可提高反应气体浓度,有效反应碰撞增加,提高变换装置的利用率,降低反应温度和增加反应物中水蒸气量均有利于反应向生成CO2和H2的方向进行。
变换反应是CO和H2O共存的系统,含有C、H、O三个元素的系统,从热力学角度来讲,不但可以发生上述(1)的变换反应,还可能发生其他副反应。
如:CO+3H2==CH4+ H2O CO+H2==C+ H2O 2CO==C+ CO2 3、影响变换反应的条件(1)压力:压力对变换反应的平衡影响甚微,但提高压力能促使析碳和甲烷化反应的发生。
从反应平衡角度而言,CO的平衡浓度与压力无关。
从反应动力学角度而言,加压能提高反应速度。
(2)温度:变换反应是可逆放热反应,因而低温有利于反应向生成CO2和H2方向进行。
但从动力学角度说,温度提高反应速度加快,因而就存在着最佳反应温度,由变换反应的化学平衡可知,在较高的温度下,变换反应具有较高的反应速度;但温度过高会使催化剂结构发生变化,甚至结块,降低催化剂使用寿命,在较低的温度下,可获得较高的变换率。
对于低变来说,不但要考虑催化剂的活性温度,还要注意气相中的水汽含量,以确定低变过程的温度下限。
因为低变过程中催化剂的操作温度较低,而气体中水蒸汽含量又较高,当气体低温进入低变系统时,就有可能达到该条件下的露点温度而析出液滴,液滴凝集于催化剂的表面,造成催化剂的粉碎,引起床层阻力的增加。
同时,使得催化剂的活性降低,因此低变催化剂的操作温度不但受本身活性温度的限制,而且还必须高于气体的露点温度。
- 1、下载文档前请自行甄别文档内容的完整性,平台不提供额外的编辑、内容补充、找答案等附加服务。
- 2、"仅部分预览"的文档,不可在线预览部分如存在完整性等问题,可反馈申请退款(可完整预览的文档不适用该条件!)。
- 3、如文档侵犯您的权益,请联系客服反馈,我们会尽快为您处理(人工客服工作时间:9:00-18:30)。
课后任务 请通过检索文献资料,找出解释加压操作优缺点的理由
CO变换的工艺条件: 汽气比
1. 汽气比概念
H2O/CO之比 2. 水蒸汽的作用
变换反应的原料;热载体;抑 制副反应(费托合成)
3. 汽气比与CO变换率关系
同一温度下,汽气比越高,平 衡转化率越高,且反应速度加快
结论: 并不是越大越好,因为能 耗高
2. 动力学角度考虑
温度越高,反应速度常数增大,反应速度越快。温度高有利
结论:反应应沿最佳温度线进行 ,在催化剂的活性温度范围内
选择最佳的操作温度 Te 平衡温度, Tm 最适宜操作温度, E1正反应活化能,E2逆反应活化能 此时,反应器利用率最高,催化剂用量最少
课后任务
变换气
工业生产中,为什么要将催化剂
CO变换工艺条件的选 择
学习任务与目标
1.什么是CO变换反应?
2.为什么要进行CO变换? 3.CO变换反应具有哪些特点? 4.如何选择CO变换的条件? 通过学习,希望大家能够学会根据反应的特点及工程需 要合理选择反应条件
何为CO变换?
CO与水蒸气反应,称为CO变换反应,简称
变换,此反应需要在催化剂参与下进行
分断装填? 请结合流程回答这一问题 说明:流程中,I、II、III是催 化剂,段间是间壁式换热器。
Ⅰ
原料气
Ⅱ Ⅲ
CO变换的工艺条件: 压力
1. 热力学角度考虑 变换反应是等体积反应,压力对平衡无影响 2. 动力学角度考虑 压力越高,反应速度越快。加压对反应有利 结论:反应应在加压条件下进行 ,通常压力为0.8-4.0MPa , 小型厂低些,大型厂高些。
Cat
H2+CO2 -41.2kJ/mol
目的
转化成H2S,为脱硫创造条件。
CO变换应该在何种条件下 进行?
一个化学反应的条件应该如何确定
请大家思考!
?
——了解反应的特点,再选择
CO变换反应的特点
1. 可逆反应:化学平衡的问题,平衡转化率 2. 放热反应:热力学与动力学问题,温度 3. 等体积反应:热力学与动力学问题,压力 4. 催化反应:没有催化剂参加是不行的
CO变换的工艺条件: CO2
平衡角度考虑
除去生成物,有利于平衡向正方向进行。CO2低
好 结论: CO2应保持在较低水平 如:生产中,若选用中变串低变工艺,可在两
个变换炉之间串入脱碳装置。
CO变换的工艺条件: 小结
讨论1:温度
讨论2:压力
讨论3:汽气比 讨论4:CO2
职业教育应用化工技术专业教学资源库《甲醇生产技术》课程
模块三 一氧化碳变换
一、
徐州工业职业技术学院
模块三 一氧化碳变换
1.调整组成 净化工序任务 2.清除杂质 保证甲醇合成催化剂的寿命 使氢碳比符合甲醇合成要求
调整组成所采用的方法主要是进行一氧化碳变换反应
清除杂质包括硫化氢与有机硫化物的清除和二氧化碳的脱除 二氧化碳的脱除兼有调整组成与维持催化剂较高活性状态的双重作用 甲醇合成原料气的组成调整与杂质清除的工艺视原料气组成 不同有很大差异:以天然气为原料的情况下,不但无需变换工 序,还要外加二氧化碳,以满足甲醇合成的合理组成需要。以 煤与重油为原料,其净化过程最为复杂,要配置变换、脱 硫.脱碳工序,有时甚至需要二次脱硫,
CO变换的工艺条件: 压力
1. 加压的优点
增加空速,提高生产能力 设备体积小,节省投资 有利于热能回收 热能的品位得以提高,有利于热量回收。 费托合成 CO+H2 →CnH2n+2nH2O 被抑制 电耗降低
2. 加压的缺点
腐蚀加剧(点蚀 ),设备使用寿命缩短。尤其是采用耐硫变换催化剂流程 有机硫转化率下降
CO+H2O
Cat
H2+CO2 -41.2kJ/mol
为何进行CO变换?
主要反应
次要反应
为何进行CO变换? 比如,某炉气的组成:
H2为41%
CO为38.5%,CO2为5.5%,
CH4为0.2%,O2为0.2%,N2 为14.6%。
பைடு நூலகம்
为何进行CO变换?
CO+H2O
1.调整氢碳比例
CO是合成甲醇的原料之一,但在以重油、煤为原料 的原料气中, (H2-CO2)/(CO+CO2)不在2.1~2.15之间, 部分变换的目的是“调整氢碳比例”在此范围,变换率得维 持在较低的水平。 2.将有机硫转换成无机硫(H2S) 经变换,将原料气中大部分有机硫(COS、CS2)
反应 特点
欲使变换过程在最佳工艺条件下进行,达到高产、 优质和低耗的目的,就必须分析各工艺条件对反 应的影响,综合选择最佳条件
CO变换的工艺条件: 温度
1. 热力学角度考虑
变换反应是放热反应,对一定的原料气初始组成,温度的降低,平衡向 正反应方向移动,Kp值增大,平衡变换率越高,变换气中CO的平衡含量降 低。温度低有利