一氧化碳变换
一氧化碳变换操作说明

一氧化碳变换流程叙述一、一氧化碳变换工艺过程说明从SHELL来的煤气化装置的粗合成气(温度:168℃,压力:3.8MPa(g),湿基CO:55.6%,干基CO:69.07%)进入煤气原料气分离器04S001,分离出夹带的液相水后进入原料气过滤器04S002,其中装有吸附剂,可以将粗合成气中的粉尘等对催化剂有害的杂质除掉。
然后粗合成气分成三部分。
一部分占总气量28.5%的粗合成气进入煤气预热器04E001,与第三变换炉04R003出口变换气换热至210℃,后进入蒸汽混合器04S003,进入该混合器前来自蒸汽管网的过热蒸汽(4.275MPa,282℃)与粗合成气混合。
进蒸汽混合器的蒸汽量由调节阀FV-04005调节,该蒸汽量与28.5%的粗合成气量是比例控制,保证进入一变的气、汽比不低于1.09,原料气管线设有TV-04003调节阀旁路(测温点TE-04003在一变的入口。
混合后的粗合成气进入煤气换热器04E002管侧与来自第一变换炉04R001出口的变换气换热。
合成气温度由TV-04003控制在约245℃左右,进入第一变换炉04R001进行变换反应(一变入口湿基CO:33.1%)。
控制第一变换炉出口变换气温度小于等于460℃,(干基CO:18.27%湿基CO:12.5)。
第一变换炉出口变换气在煤气换热器04E002(此换热器富裕量较大,壳侧设一150的旁路)与入第一变换炉的粗合成气换热,后与另一部分占总气量32%的粗合成气相混合。
随后进入1#淬冷过滤器04S004,在此用来自低压锅炉给水泵82P003A/B约11.78吨/时的低压锅炉给水(4.2 MPa,150℃)激冷到235℃后,保证进入二变的气、汽比不低于0.53。
入第二变换炉04R002的变换气温度由TIC-04006控制(测温点设在二变的入口)。
第二变换炉出口温度为351.4℃(干基CO:18.96%;湿基CO:14.7%)。
另外,占总气量39.5%的粗合成气与第二变换炉出口变换气相混合(原料气与变换气混合前设一分析调节阀AIC-04001,保证出变换的CO含量控制在指标以内)。
影响一氧化碳变换反应的因素
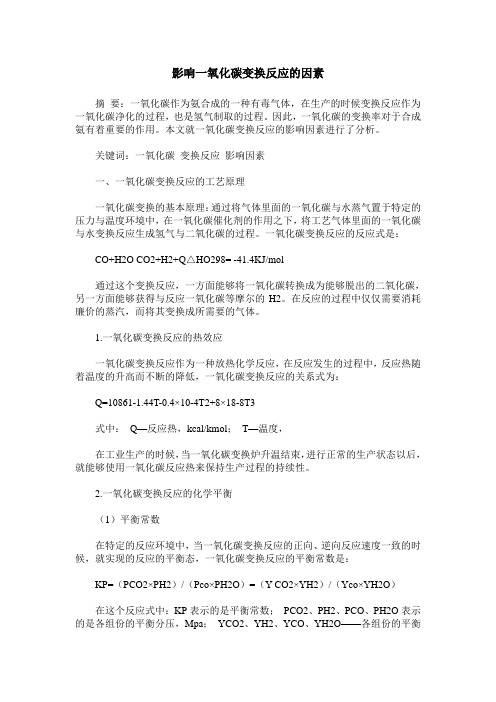
影响一氧化碳变换反应的因素摘要:一氧化碳作为氨合成的一种有毒气体,在生产的时候变换反应作为一氧化碳净化的过程,也是氢气制取的过程。
因此,一氧化碳的变换率对于合成氨有着重要的作用。
本文就一氧化碳变换反应的影响因素进行了分析。
关键词:一氧化碳变换反应影响因素一、一氧化碳变换反应的工艺原理一氧化碳变换的基本原理:通过将气体里面的一氧化碳与水蒸气置于特定的压力与温度环境中,在一氧化碳催化剂的作用之下,将工艺气体里面的一氧化碳与水变换反应生成氢气与二氧化碳的过程。
一氧化碳变换反应的反应式是:CO+H2O CO2+H2+Q△HO298= -41.4KJ/mol通过这个变换反应,一方面能够将一氧化碳转换成为能够脱出的二氧化碳,另一方面能够获得与反应一氧化碳等摩尔的H2。
在反应的过程中仅仅需要消耗廉价的蒸汽,而将其变换成所需要的气体。
1.一氧化碳变换反应的热效应一氧化碳变换反应作为一种放热化学反应,在反应发生的过程中,反应热随着温度的升高而不断的降低,一氧化碳变换反应的关系式为:Q=10861-1.44T-0.4×10-4T2+8×18-8T3式中:Q—反应热,kcal/kmol;T—温度,在工业生产的时候,当一氧化碳变换炉升温结束,进行正常的生产状态以后,就能够使用一氧化碳反应热来保持生产过程的持续性。
2.一氧化碳变换反应的化学平衡(1)平衡常数在特定的反应环境中,当一氧化碳变换反应的正向、逆向反应速度一致的时候,就实现的反应的平衡态,一氧化碳变换反应的平衡常数是:KP=(PCO2×PH2)/(Pco×PH2O)=(Y CO2×YH2)/(Yco×YH2O)在这个反应式中:KP表示的是平衡常数;PCO2、PH2、PCO、PH2O表示的是各组份的平衡分压,Mpa;YCO2、YH2、YCO、YH2O——各组份的平衡组成,摩尔分数,%;平衡常数KP表示反应达到平衡的状态下,变换反应的生成物与反应物之间的数量关系。
一氧化碳的变换技术62.
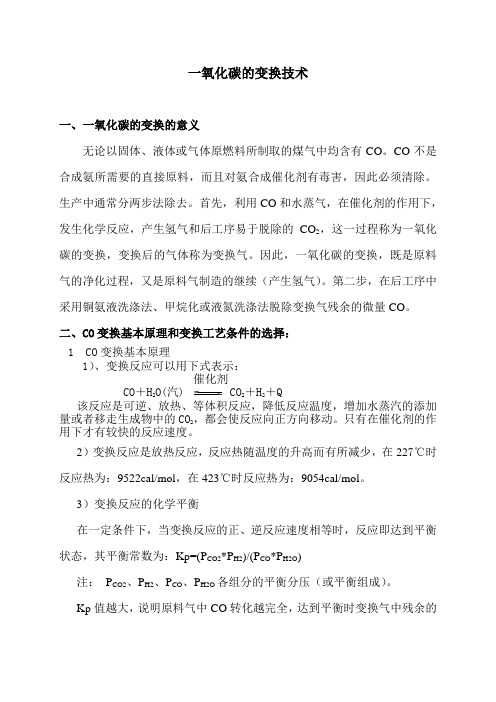
一氧化碳的变换技术一、一氧化碳的变换的意义无论以固体、液体或气体原燃料所制取的煤气中均含有CO 。
CO 不是合成氨所需要的直接原料,而且对氨合成催化剂有毒害,因此必须清除。
生产中通常分两步法除去。
首先,利用CO 和水蒸气,在催化剂的作用下,发生化学反应,产生氢气和后工序易于脱除的CO 2,这一过程称为一氧化碳的变换,变换后的气体称为变换气。
因此,一氧化碳的变换,既是原料气的净化过程,又是原料气制造的继续(产生氢气)。
第二步,在后工序中采用铜氨液洗涤法、甲烷化或液氮洗涤法脱除变换气残余的微量CO 。
二、CO 变换基本原理和变换工艺条件的选择:1 CO 变换基本原理1)、变换反应可以用下式表示:催化剂CO +H2O(汽2+H 2+Q该反应是可逆、放热、等体积反应,降低反应温度,增加水蒸汽的添加量或者移走生成物中的CO 2,都会使反应向正方向移动。
只有在催化剂的作用下才有较快的反应速度。
2)变换反应是放热反应,反应热随温度的升高而有所减少,在227℃时反应热为:9522cal/mol ,在423℃时反应热为:9054cal/mol 。
3)变换反应的化学平衡在一定条件下,当变换反应的正、逆反应速度相等时,反应即达到平衡状态,其平衡常数为:Kp=(P CO2*P H2)/(P CO *P H2O )注: P CO2、P H2、P CO 、P H2O 各组分的平衡分压(或平衡组成)。
Kp 值越大,说明原料气中CO 转化越完全,达到平衡时变换气中残余的CO含量越少。
由于变换反应是放热反应,降低温度有利于平衡向右移动,因此平衡常数随温度的降低而增大。
250℃时为86.51,450℃时为:7.311。
在工业生产中,受催化剂装填量、设备投资的经济效益等因素影响,反应不可能也没必要达到平衡,只能尽可能接近平衡。
实际的流程组合中,一般利用高温段之后再进行低温变换,就是为了提高反应平衡常数,从而提高变换率,降低变换气CO含量。
一氧化碳变换综述

的氧化铬、氧化铝、氧化锰、氧化钡等, 它们的存在,可增加催化剂抗烧结的作用, 延长催化剂使用寿命,增长催化剂的成型 性能和机械强度。 目前,中小型氮肥厂的低变催化剂均采用 Co-Mo系催化剂。Co-Mo系变换催化剂是 以Co, Mo为有效组份,以Al2O3为骨架, 碱金属或稀土金属的氧化物为辅助催化剂。 Co-Mo系变换催化剂使用前必须先进行硫 化,生成CoS, MoS2才能获得高的活性。 1.3.2 低变催化剂的主要成分
全低变的工艺流程
半水煤气 油 分 离 器 活 性 炭 滤 油 器
变 换 气 换 热 器
煤 气 换 热 器
第 一 变 换 炉
变换气 工段
变 换 气 冷 却 器
淬 冷 过 滤 器
淬 冷 过 滤 器
第 二 变 换 炉
Ⅰ
Ⅱ
半水煤气首先进入油水分离器,脱除部分固体和液体杂质后 进入活性炭滤油器,进一步脱除杂质。经净化的半水煤气 进入变换气换热器与从第二变换炉出来的变换气进行逆向 热交换,使其温度上升到180 ℃左右,变换气温度下降到 160 ℃左右。出变换气换热器的半水煤气再进入煤气换热 器与从第一变换炉出来的变换气进行逆向热交换,变换气 自身的温度下降到300 ℃左右,半水煤气升温到200 ℃左 右。出煤气换热器的半水煤气与来自管网的中压水蒸气混 合,一方面使半水煤气温度上升到变换反应温度,另一方 面使半水煤气增湿,并达到设计要求所需要的汽气比进入 第一变换炉发生变换反应,在第一变换炉内CO的变换率 可达到60%左右。经第一变换炉变换后出来的变换气进入 煤气换热器与半水煤气逆向换热后进入淬冷过滤器I,逆 向与喷淋下来的冷却水换热并使冷却水汽化,此时变换气 的温度下降到230 ℃左右,冷却水和变换气换热后汽化, 从而使蒸汽含量达到设计要求,湿变换气进入第二变换炉 第一段催化剂床层进行变换反应。经第二变换炉第一段催 化剂床层变换反应后CO的变换率可达到85%左右,温度
一氧化碳的变换
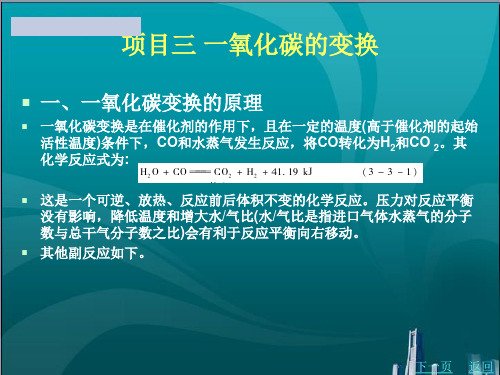
上一页 下一页 返回
项目三 一氧化碳的变换
但水蒸气用量是变换过程中最主要的消耗指标,尽量减少其消耗对过程 的经济性具有重要意义。同时水蒸气比例过高,还将造成催化剂床层阻 力增加,CO停留时间缩短,余热回收设备负荷加重等。
平衡常数是温度的函数,可通过范特荷莆方程式计算:
不同温度下一氧化碳变换反应的平衡常数见表3-3 -2。
(三)平衡含量的计算
以1 mol湿原料气为基准,
分别为初始组成中CO,
H2O ,CO2和H2的体积分数,xD为CO的平衡转化率(或变换率),则各组 分的平衡含量分别为:
上一页 下一页 返回
项目三 一氧化碳的变换
②平衡变换率是变换反应达到化学平衡时,有多少CO(干)进行了变换反 应。平衡只是一种理想状态,所以,平衡变换率可用来衡量CO变换的 最大程度。
二、一氧化碳变换反应的化学平衡
(一)变换反应的热效应 变换反应的标准反应热△ H298 ,可以用有关气体的标准生成热数据进
行计算:
上一页 下一页 返回上一页 下一ຫໍສະໝຸດ 返回项目三 一氧化碳的变换
温度对反应平衡的计算可以通过范特荷莆方程式计算。所以,根据气体 的组分及各温度的平衡常数,可以计算出经过一氧化碳变换后气体的平 衡组成。
2.压力的影响 一氧化碳变换反应是等分子反应。反应前后气体分子数相同,气体总体
积不变。若为理想气体,压力对反应的平衡没有影响。日前的工业操作 条件下:压力在4 MPa以下,温度为200℃~500℃时,压力对变换反应没 有显著的影响。 3.蒸汽添加量的影响
一氧化碳变换技术交流

℃
• 但实际上完全按最适宜温度曲线操作是不可能的,因 为在反应开始时,最适宜温度最高(以中温变换为例, 要达到620℃以上),大大超过催化剂的耐热温度, 而且热量的来源是个问题。随着反应的进行,要不断 地、准确地按照最适宜温度的需要移出反应热是极为 困难的,见二 段CO变换的T-x图。 图中: CD即为最适宜温度曲线,AB为平衡曲线,EF线为第 一段绝热反应线,FG线表示段间间接换热降温过程。 GH线表示第二段绝热反应线。。 • 变换过程的温度应综合各个方面因素来确定,主要原 则是: • 1)、反应开始温度应高于催化剂活性温度10~20℃ 左右。另外必须要高于气体露点温度20℃以上(防止 原料气析水,一是使催化剂粉碎结块,二是腐蚀设 备)。
CS2+4H2 2H2S+CH4+246 kJ∕mol MoO3+2H2S+H2 MoS2+3H2O+48.1 kJ∕mol CoO+H2S CoS+H2O+13.4 kJ∕mol • 升温硫化一般采用循环硫化法,升温硫化阶段所需要的热 量主要靠电加热器提供。 • 3)国内外Co-Mo系耐硫变换催化剂的发展历程 • ⑴1969年德国BASF公司开发成功的K8-11耐硫变换催化 剂(镁铝尖晶石复合材料为载体),1978年首次实现工业 化的应用,用于重油部分氧化法制合成气流程和加压煤气 化制合成氨流程的CO变换。它的主要特点是以镁铝尖晶 石为载体,硫化后活性高,耐高水蒸汽分压,可在高压下使用, 抗毒物能力强,能再生,平均寿命 3~5年。
• 由于变换反应是放热反应,降低温度有利于平衡 向右移动,因此平衡常数随温度的降低而增大。 例如:250℃时为86.51,450℃时为:7.311。 • 在工业生产中,受催化剂装填量、设备投资的经 济效益等因素影响,反应不可能也没必要达到平 衡,只能尽可能接近平衡。 • 实际生产的流程组合中,一般利用高温段之后再 进行低温变换,就是为了提高反应平衡常数,从 而提高变换率,降低变换气CO含量。
一氧化碳变换工艺流程及设备
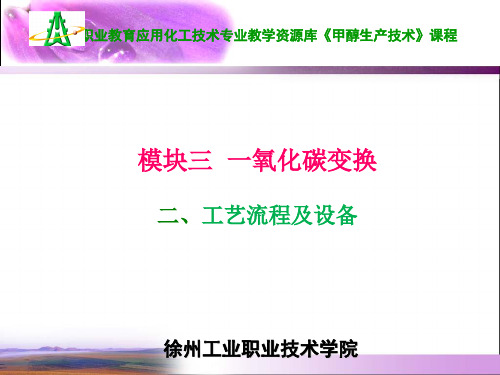
脱硫剂
ZnO+H2S = ZnS+H2O
主要活性物质:ZnO 载体:Al2O3 促进剂:铜、钼、锰的氧化物生
不可再生,送往锌冶炼厂回收
职业教育应用化工技术专业教学资源库《甲醇生产技术》课程
模块三 一氧化碳变换
二、工艺流程及设备
徐州工业职业技术学院
第二节 一氧化碳变换工艺流程及设备
一、一氧化碳变换工艺流程
二、一氧化碳变换主要设备
1.变换炉
2.热交换器
3.变换气水冷器
4.余热回收器
三、氧化锌法
原理
转化吸收式脱硫——有机硫化物在氧化锌催化作用下与氢 发生转化反应,转化为硫化氢,然后被氧化锌吸收
一氧化碳变换反应温度
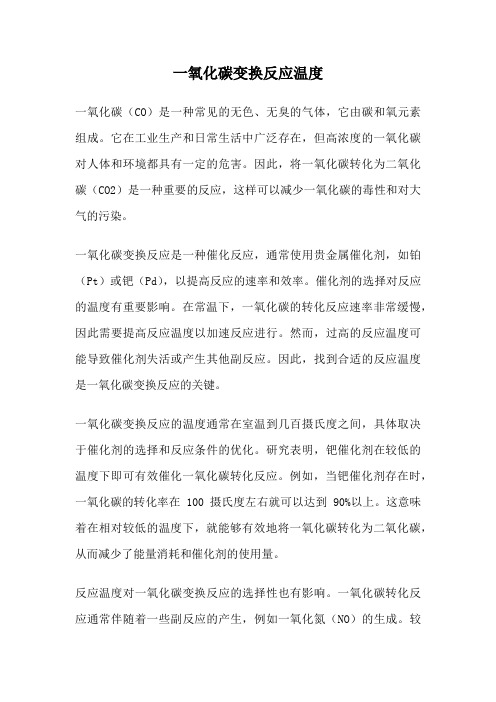
一氧化碳变换反应温度一氧化碳(CO)是一种常见的无色、无臭的气体,它由碳和氧元素组成。
它在工业生产和日常生活中广泛存在,但高浓度的一氧化碳对人体和环境都具有一定的危害。
因此,将一氧化碳转化为二氧化碳(CO2)是一种重要的反应,这样可以减少一氧化碳的毒性和对大气的污染。
一氧化碳变换反应是一种催化反应,通常使用贵金属催化剂,如铂(Pt)或钯(Pd),以提高反应的速率和效率。
催化剂的选择对反应的温度有重要影响。
在常温下,一氧化碳的转化反应速率非常缓慢,因此需要提高反应温度以加速反应进行。
然而,过高的反应温度可能导致催化剂失活或产生其他副反应。
因此,找到合适的反应温度是一氧化碳变换反应的关键。
一氧化碳变换反应的温度通常在室温到几百摄氏度之间,具体取决于催化剂的选择和反应条件的优化。
研究表明,钯催化剂在较低的温度下即可有效催化一氧化碳转化反应。
例如,当钯催化剂存在时,一氧化碳的转化率在100摄氏度左右就可以达到90%以上。
这意味着在相对较低的温度下,就能够有效地将一氧化碳转化为二氧化碳,从而减少了能量消耗和催化剂的使用量。
反应温度对一氧化碳变换反应的选择性也有影响。
一氧化碳转化反应通常伴随着一些副反应的产生,例如一氧化氮(NO)的生成。
较高的反应温度可能导致一氧化氮的生成增加,从而降低了一氧化碳的转化率。
因此,在优化反应温度时,不仅需要考虑反应速率,还需要考虑反应的选择性,以实现高效的一氧化碳转化。
反应温度还与反应系统的热力学平衡有关。
一氧化碳转化反应是一个可逆反应,根据Le Chatelier原理,在较高的温度下,反应平衡会偏向生成较少的产物,即一氧化碳。
因此,在选择反应温度时,需要在反应速率和产物选择性之间进行权衡,以获得最佳的反应效果。
一氧化碳变换反应的温度选择是一个复杂而关键的问题。
合适的反应温度能够提高反应速率和选择性,减少能量消耗和催化剂的使用量。
钯催化剂在较低的温度下已经显示出良好的催化性能,为一氧化碳变换反应的实际应用提供了新的可能性。
一氧化碳的变换

二、一氧化碳变换反应的化学平衡
(一)变换反应的热效应 变换反应的标准反应热△ H298 ,可以用有关气体的标准生成热数据进
行计算:
上一页 下一页 Байду номын сангаас回
其他副反应如下。
下一页 返回
项目三 一氧化碳的变换
(一)甲烷化反应 在一氧化碳与水蒸气共存的系统中,是含有C, H, O三个元素的系统。
从热力学角度,不但可能进行式(3一3一1)的变化反应,而且还可进行其 他反应,如:
上一页 下一页 返回
项目三 一氧化碳的变换
这一点与甲烷蒸气转化、煤气化等系统中所出现的反应式有相似之处。 但是,由于所用催化剂对反应式(3 -3-1)具有良好的选择性,从而抑制了 其他反应的发生。在计算反应系统平衡组成时,采用反应式(3-3-1)的平 衡关系,其结果基本符合实际情况。从以上反应式看,降低温度和增加 压力有利于生成甲烷的反应。但在实际生成中采用的工艺条件下,这一 副反应是不会发生的。降低床层的热点温度、增加水/气、提高空速都可 以抑制甲烷化副反应的影响。
还可进行其他反应:
由于所用的催化剂对变换反应有良好的选择性,可抑制其他反应的发生, 因此副反应发生的概率很小。
(二)变换反应的平衡常数 一氧化碳变换反应通常是在常压或压力不太高的条件下进行,故平衡常
数计算时各组分用分压表示已足够精确。因此平衡常数KD可用下式计算:
上一页 下一页 返回
项目三 一氧化碳的变换
平衡常数是温度的函数,可通过范特荷莆方程式计算:
不同温度下一氧化碳变换反应的平衡常数见表3-3 -2。
一氧化碳的变换.
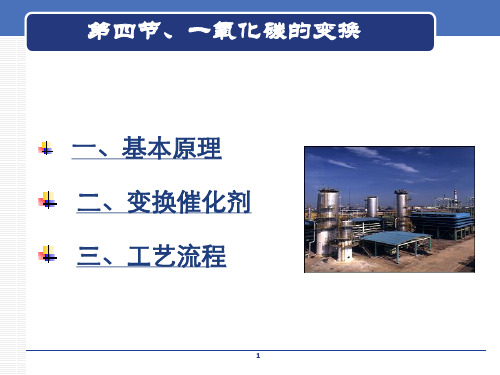
11
(二)、氧化锌法
❖氧化锌脱硫性能的好坏用硫容 量表示。所谓硫容就是每单位质 量氧化锌能脱除S的量。一些数 据如图所示。一些定性结论如下: 温度上升,硫容增加;空速增加, 硫容降低;汽气比上升,硫容下 降。
2、氧化锌脱硫剂:
100
ya,ya’ —分别为原料及变换气中一氧化碳的摩尔分率(干 基)
2
二、变换催化剂
❖ 1、中(高)变催化剂:
▪
以三氧化二铁为活性中心
▪ 铬、铜、锌、钴、钾等氧化物,可提高催化剂的活性
▪ 镁、铝等氧化物,可提高催化剂的耐热和耐毒性能。
❖ 目前常见的中(高)变换催化剂有:
▪ 铁铬系催化剂:以FeO3加Cr2O3为助催化剂。 ▪ 钴钼系催化剂:针对重油含S量高的耐高S变换催化剂。
K
0 p
pH2O
/
pH2S
10
❖ 一些条件下平衡S含量的计算值如下:
水蒸气含量/%
0.50 10 20
平衡硫含量/10-6 200℃ 0.000025 0.00055 0.005
300℃ 0.0008 0.018 0.16
400℃ 0.009 0.20 1.80
❖ 实际上天然气等原料中水蒸气含量很低,所以即使温度在400℃也可满足S含量 <0.1× 10-6的要求。 200℃含水20%时,S<0.005× 10-6,因此氧化锌也用在变 换工序作变换催化剂的保护剂。
提高其稳定性。 ❖ (2)低变催化剂的还原: ❖ CuO+H2=Cu+H2O △H0298=-86.7kJ/mol ❖ CuO+CO=Cu+CO2 △H0298=-127.7kJ/mol
一氧化碳变换反应工艺流程
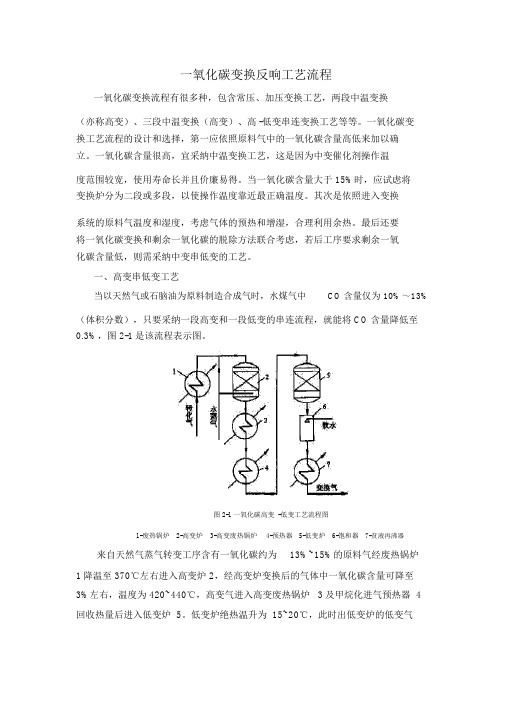
一氧化碳变换反响工艺流程一氧化碳变换流程有很多种,包含常压、加压变换工艺,两段中温变换(亦称高变)、三段中温变换(高变)、高 -低变串连变换工艺等等。
一氧化碳变换工艺流程的设计和选择,第一应依照原料气中的一氧化碳含量高低来加以确立。
一氧化碳含量很高,宜采纳中温变换工艺,这是因为中变催化剂操作温度范围较宽,使用寿命长并且价廉易得。
当一氧化碳含量大于 15%时,应试虑将变换炉分为二段或多段,以使操作温度靠近最正确温度。
其次是依照进入变换系统的原料气温度和湿度,考虑气体的预热和增湿,合理利用余热。
最后还要将一氧化碳变换和剩余一氧化碳的脱除方法联合考虑,若后工序要求剩余一氧化碳含量低,则需采纳中变串低变的工艺。
一、高变串低变工艺当以天然气或石脑油为原料制造合成气时,水煤气中CO含量仅为 10%~13%(体积分数),只要采纳一段高变和一段低变的串连流程,就能将 CO含量降低至0.3%,图 2-1是该流程表示图。
图 2-1一氧化碳高变 -低变工艺流程图1-废热锅炉2-高变炉3-高变废热锅炉4-预热器5-低变炉6-饱和器7-贫液再沸器来自天然气蒸气转变工序含有一氧化碳约为13%~15%的原料气经废热锅炉1降温至 370℃左右进入高变炉 2,经高变炉变换后的气体中一氧化碳含量可降至3%左右,温度为 420~440℃,高变气进入高变废热锅炉3及甲烷化进气预热器 4 回收热量后进入低变炉 5。
低变炉绝热温升为 15~20℃,此时出低变炉的低变气中一氧化碳含量在 0.3%~0.5%。
为了提升传热成效,在饱和器6中喷入少许软水,使低变气达到饱和状态,提升在贫液再沸器7中的传热系数。
二、多段中变工艺以煤为原料的中小型合成氨厂制得的半水煤气中含有许多的一氧化碳气体,需采纳多段中变流程。
并且因为来自脱硫系统的半水煤气温度较低,水蒸气含量较少。
气体在进入中变炉以前设有原料气预热及增湿装置。
此外,因为中温变换的反响放热多,应充足考虑反响热的转移和余热回收利用等问题。
一氧化碳变换
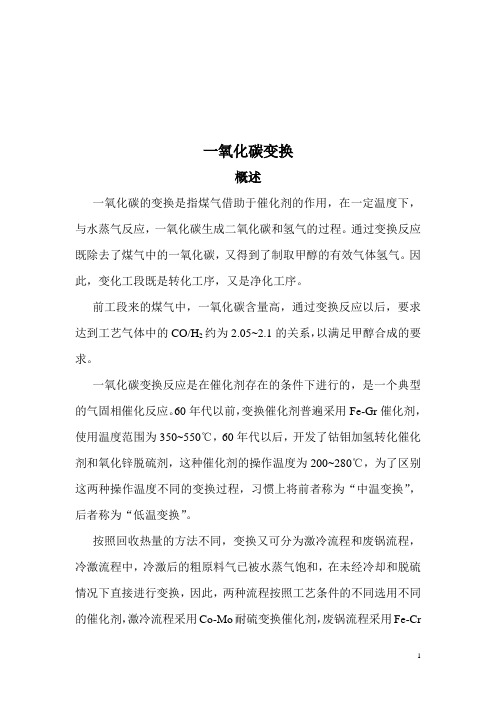
一氧化碳变换概述一氧化碳的变换是指煤气借助于催化剂的作用,在一定温度下,与水蒸气反应,一氧化碳生成二氧化碳和氢气的过程。
通过变换反应既除去了煤气中的一氧化碳,又得到了制取甲醇的有效气体氢气。
因此,变化工段既是转化工序,又是净化工序。
前工段来的煤气中,一氧化碳含量高,通过变换反应以后,要求达到工艺气体中的CO/H2约为2.05~2.1的关系,以满足甲醇合成的要求。
一氧化碳变换反应是在催化剂存在的条件下进行的,是一个典型的气固相催化反应。
60年代以前,变换催化剂普遍采用Fe-Gr催化剂,使用温度范围为350~550℃,60年代以后,开发了钴钼加氢转化催化剂和氧化锌脱硫剂,这种催化剂的操作温度为200~280℃,为了区别这两种操作温度不同的变换过程,习惯上将前者称为“中温变换”,后者称为“低温变换”。
按照回收热量的方法不同,变换又可分为激冷流程和废锅流程,冷激流程中,冷激后的粗原料气已被水蒸气饱和,在未经冷却和脱硫情况下直接进行变换,因此,两种流程按照工艺条件的不同选用不同的催化剂,激冷流程采用Co-Mo耐硫变换催化剂,废锅流程采用Fe-Cr变换催化剂。
第一节变换反应原理变换过程为含有C、H、O三种元素的CO和H2O共存的系统,在CO变换的催化反应过程中,除了主要反应CO+H2O=CO2+H2以外,在某种条件下会发生CO分解等其他副反应,分别如下:2CO=C+CO22CO+2H2=CH4+CO2CO+3H2=CH4+H2OCO2+4H2=CH4+2H2O这些副反应都消耗了原料气中的有效气体,生成有害的游离碳及无用的甲烷,避免副反应的最好方法就是使用选择性好的变换催化剂。
一、变换反应的热效应一氧化碳变换反应是一个放热反应,CO+H2O=CO2+H2+41kJ/gmol反应的热效应视H2O的状态而定,若为液态水,则是微吸热反应,若是水蒸气,则为放热反应。
变换反应的反应热随温度的升高而降低,具体反应热列表如下:表1 CO+H2O=CO2+H2的反应热温度℃25 200 250 300 350 400 450 500 550 △HkJ/gmol 41 39.8 39.5 39 38.5 38 37.6 37 36.6压力对变换反应的反应热影响较小,一般不做考虑。
一氧化碳变换动力学研究

文献。回归得到的幂函数型动力学方程如下: 宏观动力学方程:
活化能Ea=39.96kj/mol 相关系数 本征动力学方程:
活化能Ea=55.22kj/mol 相关系数
通过对动力学方程进行统检验,表明所得动力学方程是高度显著的,与实验数据的 拟合是良好的。
谢谢大家!
2. 从一氧化碳来源方面考虑催化剂 在国内煤资源较为丰富,现国内大型煤化工项目多数采用以煤为原料造气、变换、合 成技术,因此变换催化剂的需求量非常大且不断增长。但煤含硫量高,因此开发活性和稳 定性都很高的新型耐硫变换催化剂就显得十分重要。 3. 从热力学方面考虑催化剂 一氧化碳变换的化学式为: CO+H2O=CO2+H2 -450keal/NmCO 一氧化碳变换反应为放热反应,在高温下反应向左进行,在低温下反应向右进行,使CO 变换更完全。 由于一氧化碳的变换是可逆的放热反应,温度对反应的进行有一定的影响, 对一氧化碳的转化率也有一定影响,起初一氧化碳的转化率的转化率会随温度的升高而增 大,但当温度达到一定程度时,反应会向逆方向进行,此时转化率下降,所以反应加热到 一定程度后必然会适当降温到合适的温度才能保证转化率高且催化剂不失活,这就要求催 化剂具有活性高,起燃温度低和操作温度区间宽的CO变换催化剂。 4. 从节能方面考虑催化剂 一氧化碳变换是放热反应,所以要求的温度不能过高,温度过高消耗资源更多,因此 成本更高,所以选择低温催化剂就可以了。
5. 结论 Co-Mo系宽温耐硫变换催化剂 钴钼系耐硫宽温变换催化剂是在20世纪60年代中后期研制的一种变换催化 剂,主要是为满足以重油、渣油、煤或高含硫汽油为原料制取合成氨原料气的需 要,该催化剂具有很高的低温活性。它比铁系高温变换催化剂起活温度低100~ 150℃ ,甚至在160℃时就显示出优异的活性,其最突出的优点是耐硫和抗毒性能 很强,具有较宽的活性温区(160~500 ℃),具有耐硫无上限等特点,另外还具有 强度高、使用寿命长等优点,但其致命的缺点是使用前需要繁琐的硫化过程。 因此,Co-Mo系宽温耐硫变换催化剂符合一氧化碳变换催化剂的要求,适合 一氧化碳变换。
一氧化碳变换

一氧化碳变换概述一氧化碳的变换是指煤气借助于催化剂的作用,在一定温度下,与水蒸气反应,一氧化碳生成二氧化碳和氢气的过程。
通过变换反应既除去了煤气中的一氧化碳,又得到了制取甲醇的有效气体氢气。
因此,变化工段既是转化工序,又是净化工序。
前工段来的煤气中,一氧化碳含量高,通过变换反应以后,要求达到工艺气体中的CO/H2约为2.05~2.1的关系,以满足甲醇合成的要求。
一氧化碳变换反应是在催化剂存在的条件下进行的,是一个典型的气固相催化反应。
60年代以前,变换催化剂普遍采用Fe-Gr催化剂,使用温度范围为350~550℃,60年代以后,开发了钴钼加氢转化催化剂和氧化锌脱硫剂,这种催化剂的操作温度为200~280℃,为了区别这两种操作温度不同的变换过程,习惯上将前者称为“中温变换”,后者称为“低温变换”。
按照回收热量的方法不同,变换又可分为激冷流程和废锅流程,冷激流程中,冷激后的粗原料气已被水蒸气饱和,在未经冷却和脱硫情况下直接进行变换,因此,两种流程按照工艺条件的不同选用不同的催化剂,激冷流程采用Co-Mo耐硫变换催化剂,废锅流程采用Fe-Cr 变换催化剂。
第一节变换反应原理变换过程为含有C、H、O三种元素的CO和H2O共存的系统,在CO变换的催化反应过程中,除了主要反应CO+H2O=CO2+H2以外,在某种条件下会发生CO分解等其他副反应,分别如下:2CO=C+CO22CO+2H2=CH4+CO2CO+3H2=CH4+H2OCO2+4H2=CH4+2H2O这些副反应都消耗了原料气中的有效气体,生成有害的游离碳及无用的甲烷,避免副反应的最好方法就是使用选择性好的变换催化剂。
一、变换反应的热效应一氧化碳变换反应是一个放热反应,CO+H2O=CO2+H2+41kJ/gmol反应的热效应视H2O的状态而定,若为液态水,则是微吸热反应,若是水蒸气,则为放热反应。
变换反应的反应热随温度的升高而降低,具体反应热列表如下:表1 CO+H2O=CO2+H2的反应热压力对变换反应的反应热影响较小,一般不做考虑。
一氧化碳变换基本原理(精)
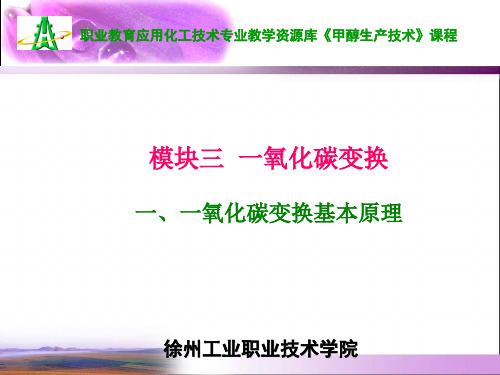
Ⅰ
原料气
Ⅱ Ⅲ
职业教育应用化工技术专业教学资源库《甲醇生产技术》课程
模块三 一氧化碳变换
一、一氧化碳变换基本原理
徐州工业职业技术学院
学习任务与目标
1.什么是CO变换反应?
2.为什么要进行CO变换? 3.CO变换反应具有哪些特点? 4.如何选择CO变换的条件? 通过学习,希望大家能够学会根据反应的特点及工程需 要合理选择反应条件
反应 特点
欲使变换过程在最佳工艺条件下进行,达到高产、 优质和低耗的目的,就必须分析各工艺条件对反 应的影响,综合选择最佳条件
主要反应
次要反应
比如,某炉气的组成:
H2为41%
CO为38.5%,CO2为5.5%,
CH4为0.2%,O2为0.2%,N2
为14.6%。
三、为何进行CO变换? CO+H2O
温度越高,反应速度常数增大,反应速度越快。温度高有利
结论:反应应沿最佳温度线进行 ,在催化剂的活性温度范围内
选择最佳的操作温度 Te 平衡温度, Tm 最适宜操作温度, E1正反应活化能,E2逆反应活化能 此时,反应器利用率最高,催化剂用量最少
CO变换的工艺条件: 压力
1. 热力学角度考虑 变换反应是等体积反应,压力对平衡无影响 2. 动力学角度考虑 压力越高,反应速度越快。加压对反应有利 结论:反应应在加压条件下进行 ,通常压力为0.8-4.0MPa , 小型厂低些,大型厂高些。
CO变换的工艺条件: CO2
平衡角度考虑
除去生成物,有利于平衡向正方向进行。CO2低
好 结论: CO2应保持在较低水平 如:生产中,若选用中变串低变工艺,可在两
粗原料气的制取—一氧化碳变换(合成氨生产)

(1)硫化
Co-Mo系耐硫变换催化剂出厂时成品是以氧化物状态存在的,活 性很低,需要通过硫化,使其转化为硫化物方能显示其活性。催化剂 装入变换炉后,用含硫的工艺气体进行硫化。
(2)反硫化
由于催化剂的活性组分在使用时是以硫化物形式存在的,在CO变 换过程中,气体中有大量水蒸气,催化剂中的活性组分MoS2与水蒸气 有一水解反应平衡关系,化学反应式为:
• 变换反应进行的程度用变换率(平衡转化率)表示,即已经转换的一氧化碳量与变换前
的总一氧化碳量之比:
x (nCO n'CO ) nCO
• 变换过程存在H2O,气体组成表示有两种方式;一种是包括H2O的湿基组成,一种是不 包括H2O的干基组成。
• 若分析得到变换前后CO的干基组成分别为y和y’ ,1mol干基气体变换后为(1+y·x)mol的
来源
原料气
原料气 高变催化剂 工艺蒸汽或 冷激用水
毒害作用
损害物理性能; 氨溶解在冷凝水 中,会溶解铜
中毒程度
要求
暂时性
低变温度要高 于气体露点
生成硫化亚铜 永久性 小于1cm3/m3
氯化铜
永久性
小于 0.03ml/m3
Fe-Cr系(高变):活性温度高,抗硫性差。寿命为3~5年 Cu-Zn系(低变):低温活性好,但活性温度范围窄,对硫十分敏感,寿命短。
CONTENTS
01
03
02
04
一氧化碳变换:既是原料气制造的继续,又是净化过程。粗 原料气含CO 12 % ~40%,通常分两步将CO除去:
高温变换
一氧化 碳变换
使大部分CO转化为CO2和H2
低温变换
一氧化 将CO 降到0.3%左右 碳变换
一氧化碳变换工艺及催化剂分析

一氧化碳变换工艺及催化剂分析一氧化碳(CO)是一种无色、无味、无臭的气体,在环境中广泛存在,并且对人体健康和环境造成严重影响。
因此,探索有效的一氧化碳变换工艺和催化剂具有重要意义。
1.光催化:光催化是利用光能激发催化剂上的电子从而促进一氧化碳的转化。
常见的光催化剂包括二氧化钛(TiO2)、二氧化锌(ZnO)等。
这些光催化剂具有良好的光催化活性,可以通过吸收可见光或紫外光来激活,并参与一氧化碳转化反应。
光催化反应的优点是能量消耗低、选择性高、反应速率快,但其缺点是催化剂的稳定性较差,光催化效果易受环境条件影响。
2.电催化:电催化是利用电能输入到催化剂上,将一氧化碳电催化转化为二氧化碳。
常见的电催化剂包括铂(Pt)、钯(Pd)等贵金属材料。
这些电催化剂具有很好的电催化活性,可以高效地将一氧化碳氧化为无害的二氧化碳。
电催化反应的优点是能耗低、转化效率高,但其缺点是贵金属催化剂成本高、易受染料、杂质等的污染。
3.热催化:热催化是将一氧化碳和氧气在催化剂的存在下加热反应,使其发生氧化反应。
常见的热催化剂包括铂(Pt)、钼(Mo)等。
这些热催化剂具有高的氧化活性,可以在适当的温度和压力下将一氧化碳转化为二氧化碳。
热催化反应的优点是反应条件相对温和、催化剂稳定性较好,但其缺点是转化速率较慢、能耗较高。
催化剂的选择对一氧化碳变换的效果起着至关重要的作用。
常见的一氧化碳变换催化剂主要有贵金属催化剂、氧化物催化剂和过渡金属氧化物催化剂等。
贵金属催化剂具有高的催化活性和稳定性,在一氧化碳变换过程中表现出了较好的效果。
然而,由于贵金属催化剂的成本较高,因此在实际应用中存在一定的限制。
氧化物催化剂具有良好的催化活性和稳定性,并且相对贵金属催化剂来说成本较低,在一氧化碳变换中广泛应用。
过渡金属氧化物催化剂由于其良好的催化活性和稳定性,也被广泛研究和应用于一氧化碳变换中。
总之,一氧化碳变换工艺及催化剂的选择在净化空气、保护环境方面具有重要意义。
- 1、下载文档前请自行甄别文档内容的完整性,平台不提供额外的编辑、内容补充、找答案等附加服务。
- 2、"仅部分预览"的文档,不可在线预览部分如存在完整性等问题,可反馈申请退款(可完整预览的文档不适用该条件!)。
- 3、如文档侵犯您的权益,请联系客服反馈,我们会尽快为您处理(人工客服工作时间:9:00-18:30)。
内蒙古伊泽矿业投资有限公司培训教材一氧化碳变换郭建礼生产准备组2006.7.15一氧化碳变换概述一氧化碳的变换是指煤气借助于催化剂的作用,在一定温度下,与水蒸气反应,一氧化碳生成二氧化碳和氢气的过程。
通过变换反应既除去了煤气中的一氧化碳,又得到了制取甲醇的有效气体氢气。
因此,变化工段既是转化工序,又是净化工序。
前工段来的煤气中,一氧化碳含量高,通过变换反应以后,要求达到工艺气体中的CO/H2约为2.05~2.1的关系,以满足甲醇合成的要求。
一氧化碳变换反应是在催化剂存在的条件下进行的,是一个典型的气固相催化反应。
60年代以前,变换催化剂普遍采用Fe-Gr催化剂,使用温度范围为350~550℃,60年代以后,开发了钴钼加氢转化催化剂和氧化锌脱硫剂,这种催化剂的操作温度为200~280℃,为了区别这两种操作温度不同的变换过程,习惯上将前者称为“中温变换”,后者称为“低温变换”。
按照回收热量的方法不同,变换又可分为激冷流程和废锅流程,冷激流程中,冷激后的粗原料气已被水蒸气饱和,在未经冷却和脱硫情况下直接进行变换,因此,两种流程按照工艺条件的不同选用不同的催化剂,激冷流程采用Co-Mo耐硫变换催化剂,废锅流程采用Fe-Cr 变换催化剂。
第一节变换反应原理变换过程为含有C、H、O三种元素的CO和H2O共存的系统,在CO变换的催化反应过程中,除了主要反应CO+H2O=CO2+H2以外,在某种条件下会发生CO分解等其他副反应,分别如下:2CO=C+CO22CO+2H2=CH4+CO2CO+3H2=CH4+H2OCO2+4H2=CH4+2H2O这些副反应都消耗了原料气中的有效气体,生成有害的游离碳及无用的甲烷,避免副反应的最好方法就是使用选择性好的变换催化剂。
一、变换反应的热效应一氧化碳变换反应是一个放热反应,CO+H2O=CO2+H2+41kJ/gmol反应的热效应视H2O的状态而定,若为液态水,则是微吸热反应,若是水蒸气,则为放热反应。
变换反应的反应热随温度的升高而降低,具体反应热列表如下:表1 CO+H2O=CO2+H2的反应热压力对变换反应的反应热影响较小,一般不做考虑。
二、变换反应的化学平衡1、变换反应的平衡常数变换反应的平衡常数随压力的增加而减小,而且与原料气组成有关,CO变换反应是可逆放热反应,平衡常数随着温度的升高而降低。
2、变换率和平衡变换率CO的变换程度通常用变换率来表示,它定义为反应后变换了的CO量与反应前气体中CO量之比。
CO变换率X%=(n co0-n co)/n co0×100式中n co0、n co分别表示变换反应前后的CO摩尔数。
反应达到平衡时的变换率叫做平衡变换率。
增加内容从以上的讨论可以得出:⑴降低反应温度,或增加蒸汽用量,可使反应向生成H2和CO2的方向进行,而降低变换气中CO的平衡浓度,若温度高,蒸汽用量少,可能使反应发生逆向,CO浓度反而比原料气中CO增加。
⑵在变换气中CO浓度一定的条件下,降低反应温度是降低蒸汽用量的必要手段。
⑶在不能降低反应温度的条件下,只求降低变换气中CO的浓度将会使蒸汽用量增加,因此,工艺上必须选择合适的变换气CO含量。
三、变换反应的动力学1、反应机理研究表明,变换反应进行时,水蒸气分子首先在催化剂表面形成吸附层,由于CO分子的碰撞而生成CO2,并离开催化剂表面。
2、扩散过程的影响一般认为,对于变换反应,内扩散的影响不容忽视。
内表面利用率不仅与催化剂的尺寸、结构及反应活性有关,而且与操作温度及压力等因素有关。
对于同一尺寸的催化剂,在相同压力下由于温度的升高,CO扩散速度有所增加,但在催化剂内表面反应的速度常数增加更为迅速,总的结果是温度升高,内表面利用率降低。
在相同的温度及压力下,小颗粒的催化剂具有较高的内表面利用率,这是因为催化剂尺寸越小,毛细孔的长度越短,内扩散阻力越小,故内表面利用率较高。
对于同一尺寸的催化剂,在相同温度下,随着压力的提高,反应速度增大,而CO有效扩散系数又显著变笑,故内表面利用率随压力的增加而迅速下降。
第二节中变催化剂早期的变换催化剂的研究工作在于提高活性,降低活行温度下限,抑制生成碳黑、甲烷的副反应,也就是提高催化剂的选择性。
后来在以Fe2O为主体的基础上,对添加Cr、Al、Cu、Zn、CO、Ni、Mn 和K的氧化物进行了大量研究工作,从而发现它们可以提高催化剂的活性、改善催化剂耐热及抗毒性能。
最后确定了以Fe2O3为主体,Cr2O3为主要添加剂的Fe-Cr系催化剂,一般含Fe2O380~90%,含Cr2O37~14%,并含有K2O、Al2O3等成分。
一、制备方法活性、选择性及使用寿命是催化剂的重要性能,这些性质与它的物理和化学结构有着密切的关系,而催化剂的物理和化学结构是由制备条件所控制的。
国内外Fe-Cr系催化剂制备方法有三种。
⑴机械混合法先将FeSO4溶解,在一定条件下加入(NH4)2CO3中和,制取的FeCO3经过热煮、水洗、过滤、干燥而得半成品,然后按规定的比例加入CrO3,有些还加入KOH、MgO等,混合后碾压,再造粒、干燥、打片、焙烧等制得成品。
此方法的优点是:方法简单,操作容易,处理量大。
但操作条件差,从微观角度来说,各组分混合可能不十分均匀。
⑵混沉法为了改善操作条件,将中和后的FeCO3经热煮后借助二价铁的还原性,加入CrO3将六价铬还原为三价铬。
其他操作同机械混合法。
由于改善了操作条件,减少了六价铬对人体的毒害,组分间的混合也比较均匀,提高了产品产量。
但各组分也可能仍不均匀。
上述两种方法,一般都采用(NH4)2CO3作为沉淀剂,在焙烧过程中,往往因碳酸盐分解而使催化剂强度降低,在使用过程中易粉化。
⑶共沉法该法是将催化剂各组分液相混合,并有碱为沉淀剂。
在一定的条件下,使之同时沉淀出来,因此各组分的均匀程度是比较好的。
所以产品质量稳定,活性高,强度好。
但是,沉淀的料浆是氢氧化物胶体结构,给洗涤带来了很大麻烦,并且硫酸根不易洗去,本体含硫高,但所得催化剂成品质量好,目前还是Fe-Cr系催化剂的最好制备方法。
为了解决催化剂本体含硫高的问题,现在已研究采用铁的硝酸盐代替F eSO4作为原料,以共沉法工艺生产高变催化剂。
二、中变催化剂的型号、组分、作用国内主要的中变催化剂:B107、B109、B112、B113、B114、B115、B116、B117、WB-2、WB-3、DGB、B118、B121等,其特性见下表:铁的氧化物是中变催化剂的活性组分,但纯Fe3O4的活性温度范围很窄,而且在低汽气比条件下有可能发生过度还原而变为FeO,甚至还原到铁,从而引起CO的甲烷化和歧化反应。
工业上用的中变催化剂都是添加Cr2O3的,它起稳定剂的作用,可以防止和延缓催化剂因高温烧结而使晶粒长大和表面积减小,当Fe2O3还原成Fe3O4时,Cr2O3可提高活性相Fe3O4的分散度,增大比表面积。
导致催化剂活性增加。
铬的氧化物还起另外一个作用,在一般条件下,从Cr3+转变为Cr是非常困难的,而Fe3+还原为Fe是比较容易的,因而在反应条件下Cr3+可以防止铁氧化物的过度还原。
在中变催化剂中,钾是有效的助催化剂,钾含量不同的催化剂其活性有很大差别。
加入少量的钾盐对于催化剂的活性、耐热性和强度都是有利的。
就容易使催化剂结皮、阻塞孔道,致使活性下降和床层阻力上涨。
催化剂一般含0.2~0.4%的K2O。
三、物理结构与活性和强度的关系中变催化剂中的Fe2O3需经还原成Fe3O4后才具有活性,但在还原过程中铁的氧化物或盐类都会发生变化,并对最终催化剂的活性和强度有很大的影响。
研究表明,催化剂活性随Cr2O3的量增至14%而达到最大值,一般在实际生产中,工业上中变催化剂的Cr2O3含量都小于14%。
另外Cr2O3进入了Fe3O4的晶格以后,形成了固溶体。
这种Fe3O4-Cr2O3与Fe3O4相比,具有较高的分散度和比表面积以防止Fe3O4的再结晶。
中变催化剂往往是由于压力降的上涨而不是因活性的丧失而停止使用的,即催化剂的强度对它的使用寿命起很重要的作用。
引起催化剂破碎的原因有:⑴搬运过程中磨损;⑵装填过程中互相冲击;⑶升温还原和生产过程中催化剂某些组分还原和氧化引起应力变化;⑷生产过程中的压力降、催化剂重量以及因床层和反应器的热胀冷缩而引起的外力。
前两种原因引起的破坏与催化剂的制作工艺有关,后两种原因引起的破坏与催化剂的还原情况和使用情况有关。
中变催化剂在开始投入使用后,其强度会下降,主要是由于催化剂在升温和还原前后结构上的变化引起的。
因此在升温还原过程中要严格控制升温速率,控制升温过程中水和二氧化碳的放出速度,如果还原速度太快以及水和二氧化碳放出的量过大,催化剂的孔结构会发生剧烈变化,强度会严重减弱。
另外在升温还原过程中,催化剂的晶体结构也发生变化,也引起其强度降低。
四、中变催化剂的主要特性中变催化剂具有相当高的选择性,在正常操作条件下不会发生甲烷化和析碳反应,中变催化剂的使用寿命,与它的活性、强度、和操作条件有关,它的耐热性和抗毒性也与活性和强度有关,而且大型化工企业的中变催化剂的本体含硫量也有很高的要求。
1、活性操作温度、催化剂颗粒大小和毒物等对中变催化剂的活性都有影响。
⑴操作温度:催化剂在生产过程中必须具有稳定的活性,即活性随时间的下降速度越慢越好。
温度对活性的下降速度影响很大。
随着时间的延长,活性逐渐衰退,可以采用提高操作温度的方法以弥补活性的衰退,但操作的温升范围是有限的,一般只有30~50℃。
必须慎重,分几年内逐步升温,否则将缩短催化剂的使用寿命。
⑵催化剂颗粒大小:中变催化剂的活性随颗粒的减小而增加。
当压力增大时,影响更为显著。
但是最适宜的颗粒大小还必须考虑变换炉的阻力降等因素。
⑶毒物:原料气中的某些杂质会使中变催化剂的活性显著下降。
最常见的毒物是H2S ,H2S与催化剂反应式如下:Fe3O4+H2S+H2=FS+H2O上述反应是可逆的,因此H2S不是永久性毒物。
一般认为,当气体中H2S的浓度低于200ppm时,活性不受影响。
一旦中毒了,当使用含H2S低的原料气时,催化剂的活性也可以较快地恢复。
但如果这一过程反复进行,实际上会加快催化剂活性下降速度,而且将引起催化剂的破碎。
2、强度催化剂的强度是评价催化剂性能优劣的重要指标,对于中变催化剂来说,甚至比活性更为关键。
因此必须保证还原态的中变催化剂具有很好的强度。
从目前的催化剂制造技术来说,已能生产密度较低且还原态强度高的催化剂了。
3、催化剂的本体含硫量本体含硫量高的催化剂耐毒性比较好,它们一般都能在H2S含量在20~200ppm的系统中使用,而活性不受影响。
低硫催化剂适用于高变直接串低变和需要回收CO2的流程。
五、中变催化剂的使用寿命。