直接还原铁作为废钢替代品在电弧炉中的应用
炼钢用直接还原铁的研制与应用

d e n n % b n ig a e t T e h i c y r d c d io s ma u a t r d b tr p o e swi xe a h a t o u iga d 1 i d n g n . h n te d r t u e rn i n fc u e y r o t rc s t e tr l e tmeh d el e e h n
分与铁精矿粉混合制成球团矿或烧结矿供高炉使用 , 另一部分直接供转炉使用, 不能实现氧化铁皮的高效
利用 。包钢耐 火厂现 有两条 9 1 10m 的隧道 0m、 条 2 窑。若 以氧化铁皮为原料 , 焦粉为还原剂 , 采用隧道窑 生产还 原铁。不仅可 以给转 炉炼钢提 供优 质原料 , 实 现氧化 铁皮资源 的有效利用 , 有利 于耐火 厂产业 而且
按配方准确称量 氧化 铁皮 及 还原剂 倒人 试验 室 小混沙机 内, 然后外 加 1 %的糊精 , 干混 5mn然后加 i, 人 20 的水继续混合 5mi .% n出料 , 10t 在 0 液压机上
以 20k 2 N的压 力压制成型 5 n 5 l O/ n× 0in试样 , l n 置
Ab t a t T e mo l e ln sa e p e s d b ln ig w t rn s a e a a tra . d i g2 sr c : h ud d ba k r rs e y b e d n i io c l sr w mae i1 a d n % a c l r t o e h c ee a rr — n f
o d c in o 8  ̄ n o k n i f8 h. h c o d r p a e s e c a n se l fr u t f1 2 0 C a d s a ig t e o me o w ih c u e l c t ls rp i t e —met gwi o v r r . l e ln t c n et s i h e
直接还原铁在八钢短流程生产线应用的实践分析
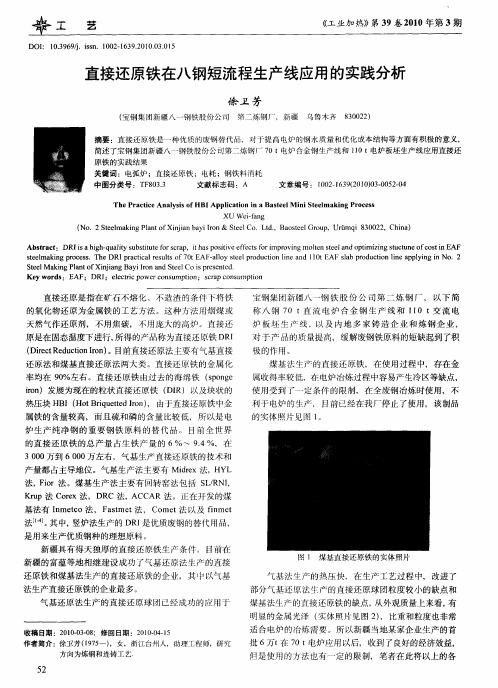
炉 板坯 生 产 线 ,以及 内地 多 家 铸 造 企业 和 炼 钢 企业 ,
对 于 产 品的质量提高,缓解废钢铁原料的短缺起 到了积
极 的作用 。
煤基法生产 的直 接还原铁,在使用过程 中,存在金
属收得率较低 ,在 电炉冶炼过程 中容易产生冷区等缺点, 使用受到 了一定条件 的限制,在 全废钢 冶炼时使用,不 利于电炉的生产, 目前已经在我厂 停止了使用,该制品
A b t a t DRIi g q lt u t u ef rs r p, iha stvee fct ri pr i g m o tnse n pt i i t un c ti sr c : sahih— uaiy s bsi t o ca t t spo ii fe sf o m ov n le tel d o i zngsuct eof os nEAF a m
气基还原法生产的直接还原球 团已经成功的应用于
se l k n r c s .Th tema ig p o e s e DRIp a t a e u t f 0 AF al y se l r d ci n l ea d 1 t AF sa r d ci n l e a p y n .2 r ci l s l o t c r s 7 E — l te o u t i n l o p o n O E lb p o u t i p l i g i No o n n
直接还原是 指在矿 石不熔 化 、不造渣 的条件下将铁
宝钢集 团新疆八 一钢 铁股 份 公司 第 二 炼钢 厂 , 以下 简 称八 钢 7 直 流 电炉 合 金钢 生 产 线 和 1 0 t 流 电 0t 1 交
钢渣直接还原铁在转炉中的应用试验

转炉 吨位 : 4 5 T转炉 ;
钢渣 制直 接还 原铁用 量 : 3 0 T; 钢渣 制直 接还 原铁尺 寸 : 1 6 0× 8 O m m; 钢渣 制直 接还 原铁体 积密 度 : 2 . 2 1 m 3 - 2 . 3 4 g , c m ; 冶炼 钢种 : H R B 4 0 0 、Q 2 4 5 R1 等。
1 . 1 试 验条 件
试验 配 比 : O . 5 T的钢 渣制 直接还 原铁 + 0 . 5 T废 钢。 试验 炉数 : 6 0 炉。 试验 小结 : 在第 二 阶 段 的试 用试 验 中 , 虽 然钢 渣 制 直接 还 原铁 的添加 比例 加大 , 但 是整个 冶炼 过程 非 常平稳 , 炉 况顺 行 , 钢水 质量 稳定 , 每炉 出钢 量 增加 0 . 0 2 T , 钢渣 制 直接 还原 铁 完全 可 以用 于炼钢生 产 , 替代 部分 优质废 钢 。
随 着循 环 冶 金 和绿 色冶 金 的 发展 , 各 大 钢企 逐 渐 意识 到 冶
2 现 场试验情 况
2 . 1 炉前试 验情 况
金 同废 综 合 利用 所 蕴含 的 巨 大经 济效 益 和肩 负 的社 会 责任 , 于 是 在 同废 的 循环 利 用上 展 开 了新 的研 究 与探 索 , 钢 渣 的综 合利 用 就是 其 中一项 。而 目前大 多 数钢 企 在钢 渣 磁选 出的钢 渣 铁精 粉 循环 利用 上 , 大多采 用烧结 配料 一 高炉一转 炉 的大循 环模 式 , 这 种传 统的循 环 利用方式 没 有充分 利 用钢渣铁 精 粉 的潜在 价值 , 造 成 资 源 的极 大浪 费 。同 时也 使 生产 流 程复 杂 化 , 增 加 了生产 过 程 中的物 质 和能量 的流失 。针 对钢 渣铁精 粉 的低端 利用 现状 , 我 们对 它 的循环 利 用进 行 了新 的 尝试 。选 用 钢渣 铁 精 粉和 铁矿 粉 作 为原 料 , 选 用 现有 的 隧道 窑 直接 还 原铁 生产 技 术 , 将 其还 原 焙烧 成直 接还 原 铁供 转 炉使 用 , 可 以代替 一半 的废 钢 。钢渣 制 直接 还 原 铁在 转 炉炼 钢 中 的成 功试 用 , 既 可 以弥 补 当前 市场 优质 废 钢 的不 足 , 又使 钢 渣铁 精 粉物 尽 其用 , 极 大 的 提升 了资 源的利 用价 值 。
用于低碳排放钢铁生产的直接还原铁技术研究

用于低碳排放钢铁生产的直接还原铁技术研究近日,直接还原铁(DRI)的话题引起了很大关注,特别是在减少钢铁生产中二氧化碳排放的目标方面。
DRI是指在不熔化的情况下将氧化铁还原为金属铁。
未还原的矿石化合物依然不是理想的氧化物。
氧化铁原料(Fe203)以相同的形式进料和排出(球团进料,球团排出,块矿进料,块矿排出)。
热压块铁(HBI)是将DR1进行热压块(1,200T,650℃),从而形成高密度枕型压块,主要是为了便于安全运输和处理,用于商业DRI生产Q在中东和北非等废钢缺乏地区,DRI/HBI主要用作电弧炉(EAF)炼钢的初级金属原料,而在北美和欧洲等废钢丰富地区,则作为补充原料。
另外,HBI还可以选择性地用于高炉和转炉生产。
1矿石基金属物料DRI/HBI是电弧炉中使用的矿石基金属物料(OBMS)的一种形式。
另一种常用的OBM是商业生铁,在高炉中生产的铁水,温度超过1,370o C o 生铁是铁水凝固而成。
相对于废钢和生铁而言,DRI/HBI在全铁、金属化、金属铁和脉石水平方面处于不利地位;但DRI/HBI在减少二氧化碳排放方面具有更大的潜力。
2竖炉DR1工艺重点是气基竖炉DRI/HBI工艺。
典型工艺流程如下:2.1热还原气体的产生①天然气重整(Midrex工艺的催化重整;Hy1III的蒸汽重整)。
②原位重整(EnergironHy1ZR工艺)。
③气化煤、焦炉煤气。
2.2铁矿石装料球团矿和块矿的筛分和包覆(石灰石、白云石、铝土矿或水泥)。
2.3竖炉的还原煤气在约1,000。
C引入,有时候混入氧气。
2.4处理DR1产品冷DRI、热DR1或HBI。
自2023年以来,铁矿石(球团)成本大幅上升,铁矿石(球团)成本一直占据了成本的主导地位。
在此之前,天然气成本是决定DRI工厂选址的关键因素。
不过,当天然气价格上涨到7~10美元/MMBTU时,DRI生产的吸引力就大不如前了。
3DRI和低二氧化碳钢生产目前,业界对DRI/EAF炼钢工艺非常关注,主要与在全球范围内减少钢铁生产的二氧化碳排放有关。
焦炉煤气生产直接还原铁技术研究

焦炉煤气生产直接还原铁技术研究一、技术背景。
进展直接还原铁生产是电炉钢短流程进展的需要。
我国钢铁产量已持续连年居世界第一名,但钢铁工业结构不合理,主要体此刻低附加值产品多余,而高级钢材仍需入口。
随着我国钢铁工业结构的调整和对钢铁产品质量要求的提高,电炉钢短流程必然会取得较快进展。
传统的电炉冶炼以废钢作为主要原料,而我国废钢资源不足,每一年的废钢入口量都在1000万吨以上;另外,废钢中杂质元素的不断积累会对优质钢的生产造成不利影响。
直接还原铁作为废钢的重要替代品是电炉炼钢的理想原料,它具有纯净度高、成份稳固等长处,是进展钢铁生产短流程的基础。
利用焦炉煤气生产直接还原铁是钢铁行业实现节能减排的有效途径。
传统炼铁工艺受焦煤资源欠缺的影响,其进展受到制约。
进展直接还原铁生产不仅能够改变传统炼铁工艺长期以来对焦煤的依赖,同时能够减少二氧化碳排放量(与煤基直接还原相较,吨铁CO2排放量能够从2000kg降低到400kg以下),符合钢铁工业可持续进展的技术要求,是钢铁行业实现节能减排的有效途径。
多余焦炉煤气的存在为进展气基直接还原提供了根本动力。
我国焦化企业每一年产生大量多余的焦炉煤气,这为开展焦炉煤气竖炉法生产直接还原铁提供了可能。
另外,随着热风炉(和加热炉)技术的进步,利用单一的高炉煤气就可以够实现1300℃的风温,这使得利用低热值的煤制气加热焦炉(或用于加热炉),从而置换出部份焦炉煤气用于直接还原铁生产成为可能,这在必然程度上扩大了焦炉煤气的来源,为焦炉煤气规模化生产直接还原铁提供了保障。
焦炉煤气利用方式的选择。
两种途径:燃料化和资源化。
焦炉煤气中CH4:25%〜26%,H2 : 56%〜%,H2发烧值仅为2580kCal/m3约为曱烷的四分之一,因此,将焦炉煤气作发烧剂不尽合理。
由于氢气的还原潜能远远高于CO,因此将焦炉煤气用作还原剂更有利于其化学能的合理利用。
与天然气相较焦炉煤气中的甲烷含量更低,这使得其重整负荷减轻,耗氧量减少,能量消耗也降低。
直接还原铁在电弧炉炼钢中的应用
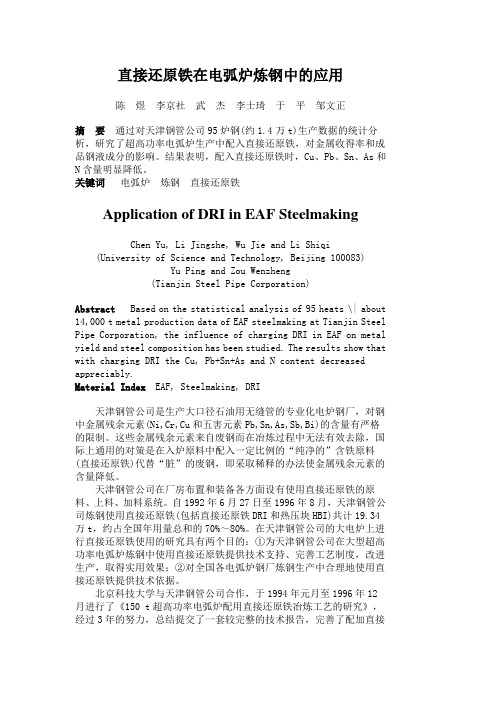
直接还原铁在电弧炉炼钢中的应用陈煜李京社武杰李士琦于平邹文正摘要通过对天津钢管公司95炉钢(约1.4万t)生产数据的统计分析,研究了超高功率电弧炉生产中配入直接还原铁,对金属收得率和成品钢液成分的影响。
结果表明,配入直接还原铁时,Cu、Pb、Sn、As和N含量明显降低。
关键词电弧炉炼钢直接还原铁Application of DRI in EAF SteelmakingChen Yu, Li Jingshe, Wu Jie and Li Shiqi (University of Science and Technology, Beijing 100083)Yu Ping and Zou Wenzheng(Tianjin Steel Pipe Corporation)Abstract Based on the statistical analysis of 95 heats \| about 14,000 t metal production data of EAF steelmaking at Tianjin Steel Pipe Corporation, the influence of charging DRI in EAF on metal yield and steel composition has been studied. The results show that with charging DRI the Cu, Pb+Sn+As and N content decreased appreciably.Material Index EAF, Steelmaking, DRI天津钢管公司是生产大口径石油用无缝管的专业化电炉钢厂,对钢中金属残余元素(Ni,Cr,Cu和五害元素Pb,Sn,As,Sb,Bi)的含量有严格的限制。
这些金属残余元素来自废钢而在冶炼过程中无法有效去除,国际上通用的对策是在入炉原料中配入一定比例的“纯净的”含铁原料(直接还原铁)代替“脏”的废钢,即采取稀释的办法使金属残余元素的含量降低。
海绵铁简介——精选推荐

海绵铁简介一、直接还原铁(海绵铁)的用途直接还原铁(海绵铁)是精铁粉在炉内经低温还原形式的低碳多孔状物质,其化学成分稳定,杂质含量少,主要用作电炉炼钢的原料,也可作为转炉炼钢的冷却剂,如果经二次还原还可供粉末冶金用。
近年来由于钢铁产品朝小型轻量化、功能高级化、复合化方向发展,故钢材中非金属材料和有色金属使用比例增加,致使废钢质量不断下降。
废钢作为电炉钢原料,由于其来源不同,化学成分波动很大,而且很难掌握、控制,这给电炉炼钢作业带来了极大的困难。
如果用一定比例的直接还原铁(海绵铁)(30-50%)作为稀释剂与废钢搭配不仅可增加钢材的均匀性,还可以改善和提高钢的物理性质,从而达到生产优质钢的目的。
因此,直接还原铁(海绵铁)不仅仅是优质废钢的替代物,还是生产优质钢材必不可少的高级原料(天津无缝钢管公司国外设计中就明确要求必须配50%的直接还原铁(海绵铁))。
根据国外报导,高功率电炉冶炼时,炉料搭配30-50%直接还原铁(海绵铁),生产率提高10-25%,作业率提高25-30%。
1996年2月26日我们在鹿泉市轧钢厂三吨电炉上试验表明,在炉料中搭配30-50%直接还原铁(海绵铁),每吨炉料平均节约电能27%,节约炼钢时间28%,耗氧量降低22%,钢材物理性能明显提高。
就此,在电炉钢炉料中搭配一定量直接还原铁(海绵铁)不仅可以提高电炉的生产能力,而且还能降低电耗和生产成本。
国家统计局公布的数字显示,我国九七年的钢产量就已突破亿吨大关,成为世界第一产钢大国,但能源的消耗也是惊人的,吨钢能耗比日本和西方国家高出很多,除技术上的原因外,与我国不同工艺流程的比例有很大的关系。
截止目前,我国电炉钢产量只占总产量的25%,大大低于西方国家的平均值50%。
提高电炉钢的产量必须在电力供应和原料保证上做文章。
实践证明,纯净合格的直接还原铁(海绵铁),是电炉的理想原料,这在西方发达国家普遍得到了认可。
“九五”期间,冶金工业调整——优化钢材结构,由注重规模与产量转变为注重质量和效益,要提高钢的质量,如果原料仍以废钢为主,将是很困难的。
直接还原铁在中国
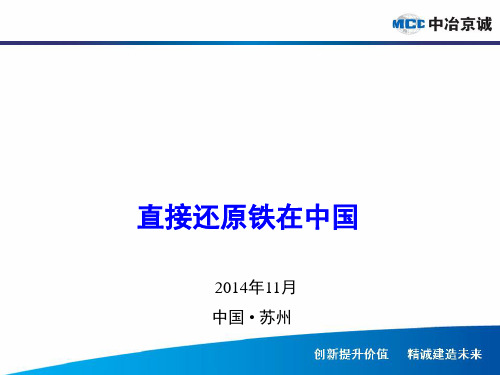
作为电弧炉炼钢原料 (可100%使用)
EAF
作为转炉炼钢的冷却剂
BOF
三、直接还原铁在炼钢中的应用
——DRI炼钢流程和热装铁水炼钢流程对比
DRI
EAF
LF
CCM
竖炉
废钢
BF
铁水
EAF
10
CCM LF
三、直接还原铁在炼钢中的应用
电炉炼钢
DRI为原料的电炉冶炼特点:
•采用连续加料方式加入,靠钢液熔池传热熔化; •钢中有害元素降低,力学性能提高,改善了加工性能; •实现平熔池冶炼,短弧埋弧冶炼为主,噪音小; •渣量大(DRI:140kg/t钢,废钢80~110kg/t钢); •电耗高(100%废钢380kWh/t,100%DRI550kWh/t)。
是国内缺乏廉价的还原气和优质的矿石资源。
我国能源特点:富煤贫油少气,分布不平衡,优质炼焦煤递减。(利用煤制气) 我国矿石资源特点:贫多富少,分布不平衡,复合共生矿居多。
硼镁铁矿
高磷铁矿 钒钛磁铁矿
高磷铁矿
硼镁铁矿 钒钛磁铁矿
贫、杂、多元素共生矿:400多亿吨 钒钛磁铁矿储量120亿吨----高炉冶
炼效率低,V和Ti回收率低; 高磷铁矿100亿吨----脱磷技术未解
决,无法利用,高品位近40亿吨, 低品位60亿吨; 菱铁矿、褐铁矿、赤铁矿160亿吨---选矿技术没有解决; 硼镁铁矿10亿吨----有价元素未得到 充分利用。
选择性气基还原的开发对冶炼复合共生矿具有极其重要意义!
6
二、我国发展直接还原的市场方向
山东(25)
还
河南(17)
江苏(4)
原 铁
重庆(3) 湖北(7)
上海(4) 安徽(4)
70t电弧炉应用热压块HBI冶炼的工艺实践

3 ・ 21 6 00年 1 O月
第3 l卷第 5期
特殊钢
S E I T L P C AL S EE
V0 - 1 No 5 l3 . . O tb r 2 1 co e 0 0
7 0t电弧 炉应 用 热压 块 HB 冶 炼 的 工艺 实践 I
秦 军
( 钢集 团新疆八一钢铁股份公司第 二炼 钢厂 , 宝 乌鲁木齐 80 2 ) 3 02
k / , 以炉 料 为 全 废 钢 时 不 宜 配加 热 压 块 , Wh t所 当加 入 3 % 铁 水 和 加 入 1 % 热 压 块 时 可 以 达 到 冶炼 过程 最 优 化 。 0 0 关键 词 7 电 弧 炉 0t 热 压块 电耗 冶 金 质 量
Pr c ie f r S e l a i g Pr c s f a 7 c f r a e b a tc o t em k n o e s o 0 t Ar u n c y
摘
要 7 电弧炉 的炉料装入量为 8 8 , 中热直接还原铁热压块 H I 1. 0t O一 lf 其 B 为 4 6—1. , 52t铁水 2 2 , 3~ 7t
其出钢量 7 7 , 7~ 8t电耗 3 6 34k / , 1 2 wh t氧耗 2 . 3 . t冶炼周期 4 9 7— 30m / , 8—5 i。生产 实践表 明 , 4m n 热压 块是 优质废钢的替代 品 , 可促进电弧炉脱磷和脱碳反应 , 降低氧耗 13~32m / , . . t但每增加 1 %热压块则增加 电耗 3 5 .
1 . ~1 . n o tl 2 —2 .i a pn i ud a u ti 7 —7 . ee t c p we o s mp in 3 6 — 3 4 46 5 2 ta d h tmea 3 7 t t tp i g l i mo n s 7 s q 8 t l cr o r c n u t 1 i o 2
直接还原铁热装热送新装备技术开发

直接还原铁热装热送新装备技术开发①潘宏涛② 李少英 王少臣 李佳辉(中冶京诚工程技术有限公司 北京100176)摘 要 直接还原铁(Directreductioniron,DRI)热装热送是降低电弧炉电能消耗的重要措施。
本文研究了不同DRI、废钢比例条件下,电弧炉电能消耗与DRI热送温度的关系,结果表明,当DRI取代废钢进行电弧炉冶炼时,DRI入炉温度每增高100℃,每吨钢可节省电能约25kW·h。
此外以“输送能耗最低、输送装置简单”为原则,提出了新型直接还原铁热装热送设备的设计思路,该设备具有转运过程中所需的密闭、保温和计量的功能,同时也实现了造渣料与DRI分层协同加料的功能,设备结构简单可靠,输送能耗低、效率高,解决了当前热装热送设备动能消耗大、设备磨损快、物料流速难以控制、易卡料等问题,为实现直接还原铁高效热装热送创造了重要条件。
关键词 直接还原铁 热装热送 氢基竖炉 电弧炉中图法分类号 TF321 TF702 TF803.21 文献标识码 ADoi:10 3969/j issn 1001-1269 2023 04 004DevelopmentofNewEquipmentTechnologyforHotDirectReductionIronChargingandDeliveryPanHongtao LiShaoying WangShaochen LiJiahui(MCCCapitalEngineering&ampResearchIncorporationLimited,Beijing100176)ABSTRACT Directreducediron(DRI)hotchargingandhotdeliveryisanimportantmeasuretoreduceelectricenergyconsumptioninelectricarcfurnaces.Tosolvetheproblemsofthecurrenthotchargingandhotconveyingequipment,suchashighkineticenergyconsumption,fastequipmentwear,difficultcontrolofmaterialflowrate,andextremelysusceptibletojamming,anewtypeofhotchargingandhotconveyingequipmentfordirectreducedironisdesigned.Theequipmenthasthefunctionsofsealing,heatpreservationandmeteringrequiredinthetransferprocess,andalsorealizesthefunctionoflayeredcollaborativefeedingofslagformingmaterialsandDRI.Theequipmentissimpleandreliableinstructure,lowinenergyconsumptionandhighinefficiency,whichhascreatedimportantconditionsforachievingefficienthotchargingandhotdeliveryofdirectreducediron.KEYWORDS Directreducediron Hotchargingandhotdelivery Hydrogenbasedverticalfurnace Electricarcfurnace1 前言在“碳达峰、碳中和”的战略背景下,钢铁产业高端化、绿色化、低碳化发展是时代的必然要求。
DRI ( 直接还原铁)和HBI (热压铁块)的贸易和运输

DRI(直接还原铁)和HBI(热压铁块)的贸易和运输DRI(DirectReducedIron)“直接还原铁”是一种高品质冶金产品(97%的纯铁含量)通过矿粉,球团或矿块同天然气或煤加热化学的还原反应中得到,反应温度比铁的溶点低。
相对高品位的铁矿作为填料。
矿粉可以直接应用,不需要烧结过程。
生产1吨的DRI,大概需要1。
5吨的铁矿。
(一)直接还原法生产生铁直接还原法是指在低于熔化温度之下将铁矿石还原成海绵铁的炼铁生产过程,其产品为直接还原铁(即DRI),也称海绵铁.该产品未经熔化,仍保持矿石外形,由于还原失氧形成大量气孔,在显微镜下观察团形似海绵而得名。
海绵铁的特点是含碳低(<1%),并保存了矿石中的脉石。
这些特性使其不宜大规模用于转炉炼钢,只适于代替废钢作为电炉炼钢的原料。
直接还原法分气基法和煤基法两大类。
前者是用天然气经裂化产出H2和CO气体,作为还原剂,在竖炉、罐式炉或流化床内将铁矿石中的氧化铁还原成海绵铁。
主要有Midrex法、HYLIII法、FIOR法等。
后者是用煤作还原剂,在回转窑、隧道窑等设备内将铁矿石中的氧化铁还原。
主要有FASMET法等。
直接还原法的优点有:(1)流程短,直接还原铁加电炉炼钢;(2)不用焦炭,不受炼焦煤短缺的影响;(3)污染少,取消了焦炉、烧结等工序;(4)海绵铁中硫、磷等有害杂质与有色金属含量低,有利于电炉冶炼优质钢种。
直接还原法的缺点有:(1)对原料要求较高:气基要有天然气;煤基要用灰熔点高、反应性好的煤;(2)海绵铁的价格一般比废钢要高。
直接还原法已有上百年的发展历史,但直到20世纪60年代才获得较大突破.进入20世纪90年代,其生产工艺日臻成熟并获得长足发展。
其主要原因是:(1)天然气的大量开发利用,特别是高效率天然气转化法的采用,提供了适用的还原煤气,使直接还原法获得了来源丰富、价格相对便宜的新能源。
(2)电炉炼钢迅速发展以及冶炼多种优质钢的需要,大大扩展了对海绵铁的需求。
现代电弧炉高效低耗炼钢技术在我国的应用与发展
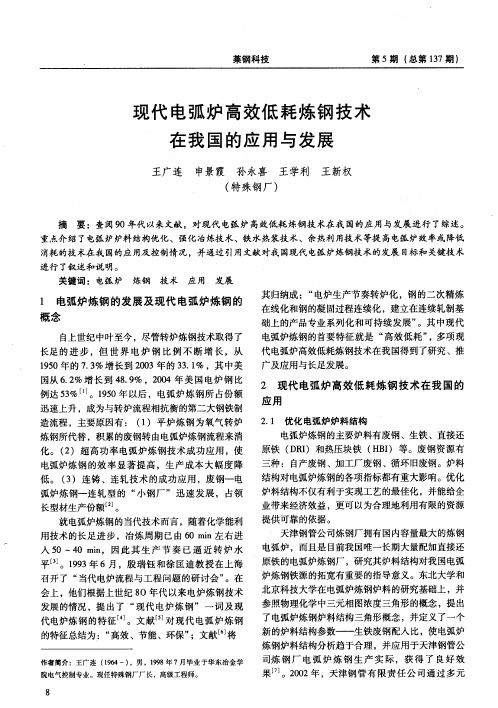
长足的进 步 ,但 世界 电炉 钢 比例 不 断 增 长,从
15 年的 7 3 90 . %增长到 20 年 的 3. % ,其中美 03 31
国从 62 增 长 到 4 .% ,20 .% 89 04年 美 国 电炉 钢 比
代 电弧炉高效低耗炼钢技术在我国得到了研究 、推 广 及应 用与 长足发 展 。
莱钢 科技
第 5期 ( 总第 17期 ) 3
现代 电弧 炉 高效低 耗炼 钢 技 术
在 我 国的应 用 与发 展
王广连 申景霞 孙永喜 王 学利 王新权
( 殊钢厂 ) 特
摘
要:查阅9 0年代以来文献,对现代 电弧炉高效低耗 炼钢技术在我 国的应用与发展进行 了综述。
重点介绍了电孤炉炉料 结构优化、强化冶炼技术、铁水热装技术、余热利用技 术等提高电孤炉效率或降低 消耗的技术在我国的应用及控制情况 ,并通过 引用文献对我国现代电弧炉炼钢技术的发展 目标和关键技术
作者简介:王广连 (94一) 男 ,19 年 7 16 , 98 月毕业于华东冶金学
原铁的电弧炉炼钢厂 ,研究其炉料结构对我国电弧 炉炼钢铁源 的拓宽有重要的指导意义。东北大学和 北京科技大学在电弧炉炼钢炉料的研究基础上 ,并 参照物理化学中三元相图浓度三角形的概念 ,提出
了电弧炉炼 钢炉 料结构 三角 形概 念 ,并 定义 了一个
1 mn 5 i,电耗下降 2 5 W /,电极单耗下降约 O一 0k h t 02k/;在铁水比为 3 %及氧耗为 4 t . gt 3 0m / 的条
件下 最 低 冶 炼 周 期 为 3 mn 5 i,对 应 电 耗 为
2 0k h t 1 W / [
。
20 年 ,文献 对我 国钢铁 厂部分国产电炉 04 刮 氧枪使用情况进行 了统计 ,见表 1 。
积极发展直接还原铁(DRI)生产技术,应对21世纪电炉废钢紧缺的挑战
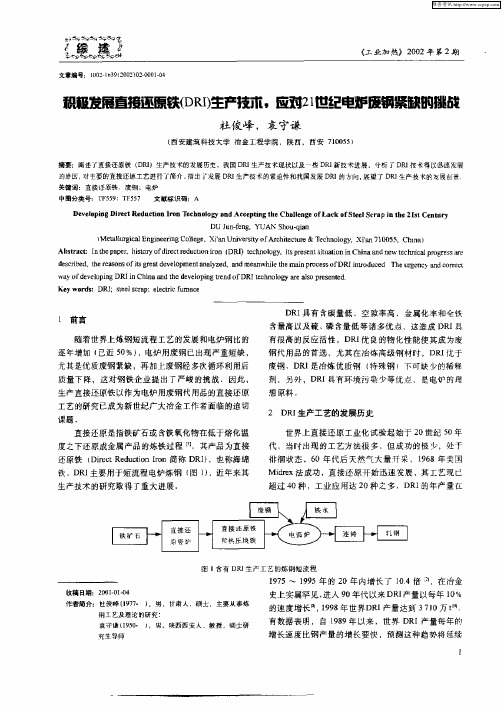
尤其是优质废钢 紧缺,再 加上废钢经 多次循环利用后
质 量下 降 ,这 对 钢 铁 企 业 提 出 了严 峻 的挑 战 因 此 ,
废钢 。DR 是冶炼优质钢 ( 殊钢 J不可映少的稀释 1 特
剂 ,另外 ,D I 有 环 境 污 染 少 等 优 点 ,是 电 炉 的 理 R 具
袁 守 谦 (90 J 15 ・ , 究 生 导师
史上实属罕见 进人 9 年 代以来 D I 0 R 产量以每年 1 % 0 的速 度 增 长 19 9 8年 世 界 D j 量 达 到 3 1 R 产 0万 t 7
,
维普资讯
誊
文章编 号: [0 一69 20 )2 0 】0 02L3 (020 - 0一4 0
《加 2年2 工 热0 第 业 》2 期 0
还原铁( R) D I 生产技i 。应鸡2 世纪电I废钢紧缺呐挑砘 f i l 誉 ;
杜俊峰 ,袁守谦
D v lpn e e o i gDie tRe u t nI o e h o o y a dAc e t gt eCh l n eo La k o S e l c a nt e 2 s Ce t r rc d c o r nT c n l g n i cpi n h a l g f c f t e r pi h 1 t n u y e S
超过 4 O种 ,工业应用达 2 O种之 多,D I R 的年产量在
圉l 含有 DR 生 产工艺 的炼钢 短 流程 I
17 9 5~ 19 9 5年的 2 O年 内增长 了 1. 04倍 。 ,在冶金
收稿 日期 :2 0 —1 ] 0 1 一4 0
电弧炉炼钢用原辅材料

3 电弧炉炼钢用原辅材料凡加入电弧炉(含感应炉和炉外精炼的钢包炉、VD/VOD炉)内直接参与炼钢冶金过程的物料统称为原材料。
如废钢、生铁、铁水、铁合金、石灰、萤石、氧气等。
生产中所指的原材料通常还包括辅助材料,即指那些虽不直接参与炉内反应,却是冶炼反应赖以正常有效地进行所必不可少的物质,如电极、耐火材料等。
原材料是电弧炉炼钢的基础,没有好的原材料及现代的管理,要想炼出优质的、成本较低的钢是不可能的,国内外先进的炼钢厂无一不是特别注重原材料的优化与管理。
我国炼钢行业过去曾对原材料供应与管理重视不够,对成品钢只就冶炼与浇注工艺而研究其质量,很多情况是欲速则不达。
现在随着钢铁生产技术的发展,特别是对钢材质量的要求的不断提高,国内钢铁生产企业已认识到原材料对炼钢质量的重要性,这是我国钢铁工业赶超国际水平和新品研发的一个良好开端。
对我公司来讲,生产油井管就必须重视炼钢原材料的供应与管理工作,以保证我公司的优质无缝钢管生产有一个可靠的坯料基础。
3.1 电弧炉炼钢原材料的分类电弧炉炼钢的原材料可分为两大类:金属料;非金属料。
金属料:包括废钢、生铁、铁水、直接还原铁(DRI)、铁合金、铁矿石和氧化铁皮等。
非金属料:包括造渣材料,如石灰、萤石、白云石、碳球(碳粉)、高铝钒土等;合成渣料,如脱硫剂,熔融合成精炼渣等;耐火材料,如炉底耐材、钢包耐材、中包耐材等;其它用途材料,如电极、增碳剂、保温剂、保护渣等。
电弧炉炼钢的原材料按用途又可分为:金属料,氧化剂及造渣材料,还原剂,电极,耐火材料等。
3.2 金属料3.2.1 废钢3.2.1.1 废钢的种类及来源废钢是炼钢的主要金属料之一。
电炉炼钢原料中,废钢用量约占60~100%。
根据来源不同,废钢通常分为本厂返回废钢和社会购入废钢两类。
返回废钢包括:炼钢车间的模铸汤道、注余、包底、连铸坯的头尾坯、锻轧废品、废钢材(坯)。
返回废钢含锈及杂质较少,化学成份相近,收得率高,是炼钢优质原料,使用返回废钢可以大量回收贵重金属合金元素,减少贵重金属和铁合金消耗,节约电耗,降低成本,具有很大的经济意义。
DRI ( 直接还原铁)和HBI (热压铁块)的贸易和运输

DRI ( 直接还原铁)和HBI (热压铁块)的贸易和运输DRI ( Direct Reduced Iron) “直接还原铁”是一种高品质冶金产品(97%的纯铁含量)通过矿粉,球团或矿块同天然气或煤加热化学的还原反应中得到,反应温度比铁的溶点低。
相对高品位的铁矿作为填料。
矿粉可以直接应用,不需要烧结过程。
生产1吨的DRI,大概需要1.5吨的铁矿。
(一)直接还原法生产生铁直接还原法是指在低于熔化温度之下将铁矿石还原成海绵铁的炼铁生产过程,其产品为直接还原铁(即DRI),也称海绵铁。
该产品未经熔化,仍保持矿石外形,由于还原失氧形成大量气孔,在显微镜下观察团形似海绵而得名。
海绵铁的特点是含碳低(<1%),并保存了矿石中的脉石。
这些特性使其不宜大规模用于转炉炼钢,只适于代替废钢作为电炉炼钢的原料。
直接还原法分气基法和煤基法两大类。
前者是用天然气经裂化产出H2和CO气体,作为还原剂,在竖炉、罐式炉或流化床内将铁矿石中的氧化铁还原成海绵铁。
主要有Midrex法、HYL Ⅲ法、FIOR法等。
后者是用煤作还原剂,在回转窑、隧道窑等设备内将铁矿石中的氧化铁还原。
主要有FASMET法等。
直接还原法的优点有:(1)流程短,直接还原铁加电炉炼钢;(2)不用焦炭,不受炼焦煤短缺的影响;(3)污染少,取消了焦炉、烧结等工序;(4)海绵铁中硫、磷等有害杂质与有色金属含量低,有利于电炉冶炼优质钢种。
直接还原法的缺点有:(1)对原料要求较高:气基要有天然气;煤基要用灰熔点高、反应性好的煤;(2)海绵铁的价格一般比废钢要高。
直接还原法已有上百年的发展历史,但直到20世纪60年代才获得较大突破。
进入20世纪90年代,其生产工艺日臻成熟并获得长足发展。
其主要原因是:(1)天然气的大量开发利用,特别是高效率天然气转化法的采用,提供了适用的还原煤气,使直接还原法获得了来源丰富、价格相对便宜的新能源。
(2)电炉炼钢迅速发展以及冶炼多种优质钢的需要,大大扩展了对海绵铁的需求。
电炉用部分替代废钢的金属炉料

1 2
办 全
28 月 一 0 年2 第 期 0
电 炉 用 部 分 替 代 废 钢 的 金 属 炉 料
丁 于
( 海 宝钢 工程技 术有 限公 司 上 海 上 2 10 ) 090
摘
要: 介绍 了电炉用各种金属炉料的特点和使 用效果。结果表 明, 铁水、 直接还原铁、 碳化铁等部分替代 废钢 作 为 电炉金 属 炉料 , 不仅 能 解决废 钢供 应短 缺 的 问题 , 有 利 于提 高钢 的质量 。 还
进 口, 这将 消耗 大 量 外 汇 , 影 响 到 电 炉钢 的经 济 也
水 中的碳 和 钢 渣 中 的氧 易 发 生 剧 烈 反 应 而 导 致 喷
溅。
效益 , 并且废钢 中 c 、n us 等有 害元素在 电炉炼钢 中 尚无 有效 方法 去除 , 而限制 了产 品 品种并 最 终 影 从 响 电炉钢 的质量 。这 样 , 在废 钢 中配 人 一定 量 的 替 代品就成为 了现代电炉冶炼的主流趋势。
传 统 电炉冶炼 采用 废钢 作 为 金属 炉料 , 多 向 最 炉料 中配 加 1%生 铁 块作 为替 代 品。 随着 我 国连 0 铸技 术 的普 遍 运 用 , 钢 厂 自产 循 环 废 钢 不 断 减 炼 少 , 电炉 钢 产 量 所 占的 比重 却 在 逐 步 提 高 , 而 并且
盖 , 溜槽 易粘 冷钢 而发 生堵 塞 。 但
铁水热装使 电炉具有转炉的某些特征 , 配合炉 内供 氧脱 碳技 术 的发 展 , 电炉 产 品更 具 有 市场 竞 使 争力。
2 直接还原铁 (R ) DI
直 接还 原 技 术 已有 10多 年 的 发 展 历 史 。直 0
加 1 需 增 加 氧 耗 ~1 m/, 降 低 电耗 ~ %, N 3t 可
电炉炼钢原料及直接还原铁生产技术
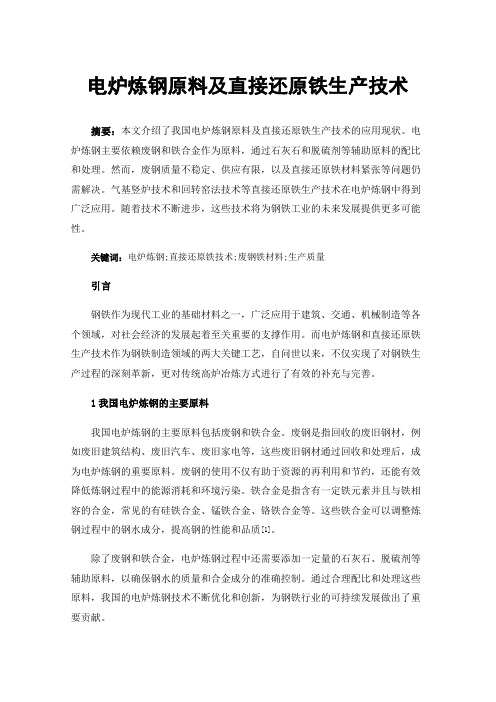
电炉炼钢原料及直接还原铁生产技术摘要:本文介绍了我国电炉炼钢原料及直接还原铁生产技术的应用现状。
电炉炼钢主要依赖废钢和铁合金作为原料,通过石灰石和脱硫剂等辅助原料的配比和处理。
然而,废钢质量不稳定、供应有限,以及直接还原铁材料紧张等问题仍需解决。
气基竖炉技术和回转窑法技术等直接还原铁生产技术在电炉炼钢中得到广泛应用。
随着技术不断进步,这些技术将为钢铁工业的未来发展提供更多可能性。
关键词:电炉炼钢;直接还原铁技术;废钢铁材料;生产质量引言钢铁作为现代工业的基础材料之一,广泛应用于建筑、交通、机械制造等各个领域,对社会经济的发展起着至关重要的支撑作用。
而电炉炼钢和直接还原铁生产技术作为钢铁制造领域的两大关键工艺,自问世以来,不仅实现了对钢铁生产过程的深刻革新,更对传统高炉冶炼方式进行了有效的补充与完善。
1我国电炉炼钢的主要原料我国电炉炼钢的主要原料包括废钢和铁合金。
废钢是指回收的废旧钢材,例如废旧建筑结构、废旧汽车、废旧家电等,这些废旧钢材通过回收和处理后,成为电炉炼钢的重要原料。
废钢的使用不仅有助于资源的再利用和节约,还能有效降低炼钢过程中的能源消耗和环境污染。
铁合金是指含有一定铁元素并且与铁相容的合金,常见的有硅铁合金、锰铁合金、铬铁合金等。
这些铁合金可以调整炼钢过程中的钢水成分,提高钢的性能和品质[1]。
除了废钢和铁合金,电炉炼钢过程中还需要添加一定量的石灰石、脱硫剂等辅助原料,以确保钢水的质量和合金成分的准确控制。
通过合理配比和处理这些原料,我国的电炉炼钢技术不断优化和创新,为钢铁行业的可持续发展做出了重要贡献。
2电炉炼钢原料应用现状电炉炼钢技术是一种利用电力作为能源、直接还原铁生产钢水的先进冶炼工艺。
相较于传统高炉冶炼方式,电炉炼钢具有能耗低、环境友好、低碳排放等优势,因此在近年来得到了广泛应用和不断发展。
2.1废钢铁料量较少、质量较差尽管废钢在电炉炼钢中是重要的原料,但目前我国面临废钢铁料量较少和质量参差不齐的问题。
炼钢中的直接还原技术及其应用

炼钢中的直接还原技术及其应用随着钢铁行业的发展,炼钢技术也在不断的变革与创新。
直接还原技术作为一种新型炼钢技术,已经开始得到广泛的应用。
本文将从直接还原技术的基础和应用方面进行阐述,以期为读者提供更深入的了解。
一、直接还原技术的基础直接还原技术是使用还原剂将炉料中的氧化铁还原为金属铁的炼钢技术。
与传统的高炉技术相比,在直接还原技术中,直接使用还原剂还原炉料中的氧化铁,不需要通过高温和高压使其发生氧化还原反应。
这种技术具有明显的优点,主要表现在以下几个方面:1.制造成本低:由于直接还原技术不需要高压和高温,所需能源也更少,因此生产成本低于传统的高炉技术。
2.环保节能:使用直接还原技术炼钢可以减少CO2和NOx等大气污染物的排放,一定程度地保护了环境。
另外,由于直接还原技术对能源的需求更小,也有利于节能减排。
3.操作简便:在直接还原技术中,制造过程更加简单直接,操作也更加方便,更容易实现自动化和智能化。
以上3个方面是直接还原技术的主要优点。
相比于传统的高炉技术,直接还原技术在生产成本、环保和操作方便等方面都有更多的优势。
二、直接还原技术的应用1.直接还原工艺的应用直接还原技术的应用范围很广,从小型加工厂到大型钢铁制造企业都在使用该技术。
其中,直接还原工艺是一种常见的应用方式。
直接还原工艺主要包括三部分:还原反应、冶金物理化学过程和钢水净化过程。
还原反应过程是指在以还原剂为主体的还原反应中,将冶金炉中的氧化铁还原为冶金铁的化学反应过程。
冶金物理化学过程是指冶金炉内金属铁的脱硫、脱锰、脱孔及相应物理化学反应。
钢水净化过程是指将冶金炉内钢水经过捞渣、渣加剂、精炼等工艺处理后实现除杂,使钢水纯净。
直接还原工艺是炼钢企业中最常用的炼钢技术之一,它主要的应用优势在于高效、短周期、节能、环保等方面。
2.直接冶炼的应用直接冶炼是指将原料中的氧化铁直接还原至金属铁进行炼制的技术。
在直接冶炼过程中,仅使用还原剂,不需要其它辅助材料。
铁水在电弧炉中的使用
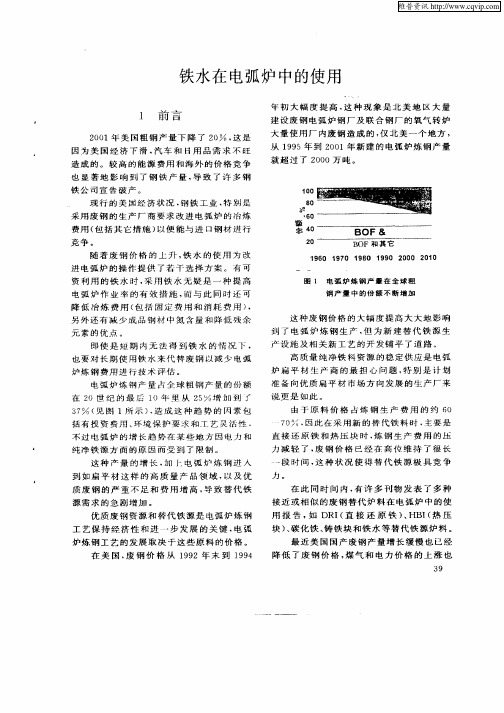
39
维普资讯
进 一 步 降 低 了 替 代 铁 源 炉 料 的 需 求 , 为 它 因
们 的 相 对 费 用 已经 增 高 了 。
1980 1 990 2000 2010
进 电 弧 炉 的 操 作 提 供 了若 干 选 择 方 案 。有 可 资 利 用 的 铁 水 时 , 用 铁 水 无 疑 是 一 种 提 高 采 电 弧 炉 作 业 率 的 有 效 措 施 , 与 此 同 时 还 可 而 降 低 冶 炼 费 用 ( 括 固 定 费 用 和 消 耗 费 用 ) 包 ,
另 外还 有 减 少 成 品 钢 材 中 氮 含 量 和 降 低 残 余 元 素的优点 。 即使 是 短期 内无 法得 到铁 水 的情况 下 ,
图 1 电 弧 炉 炼 钢 产 量 在 全 球 粗 钢 产 量 中 的 份 额 不 断 增 加
这 种 废 钢 价 格 的 大 幅 度 提 高 大 大 地 影 响
1 0O
80
Байду номын сангаас
采 用 废 钢 的 生 产 厂 商 要 求 改 进 电弧 炉 的 冶 炼 费用 ( 括 其 它 措 施 ) 包 以便 能 与 进 口钢 材 进 行
竞争 。 随 着 废 钢 价 格 的 上 升 , 水 的 使 用 为 改 铁
・ 6O
鬟o 4
20
BO F &
BOF 和 其 它
优 质 废 钢 资 源 和 替 代 铁 源 是 电 弧 炉 炼 钢 工 艺 保 持 经 济 性 和 进 一步 发 展 的 关 键 , 弧 电
- 1、下载文档前请自行甄别文档内容的完整性,平台不提供额外的编辑、内容补充、找答案等附加服务。
- 2、"仅部分预览"的文档,不可在线预览部分如存在完整性等问题,可反馈申请退款(可完整预览的文档不适用该条件!)。
- 3、如文档侵犯您的权益,请联系客服反馈,我们会尽快为您处理(人工客服工作时间:9:00-18:30)。
摘 要 :为了满足用户对优质钢和纯净钢的要求 ,直接还原铁作为废钢的替代品用 于电弧炉炼钢应是一种可行的选择 。概述了直接还原铁的特点 ,指出高比例使用 DRI 可以得到 N、Cu、Cr 、Ni 、As、Sn 等含量低的钢 ,直接还原铁可认为是一种较好的电弧炉炼 钢原料 。
关键词 :直接还原铁 ; w (N) ;电弧炉 ;泡沫渣 中图分类号 :TF741. 8 文献标识码 :A 文章编号 :1001 - 1447 (2004) 05 - 0053 - 05
Keywords :DRI ; w (N) ; EAF ;foamed slag
1 前 言
电弧炉短流程炼钢工艺投资省 ,见效快 ,因此 发展很快 。但随炉容量的逐渐扩大 ,作为电弧炉 炼钢的主要炉料 ———废钢越来越少 。而废钢经过 多次循环利用 ,残余元素及有害元素 (铬 、铜 、锡 、 铝等) 急剧增加 ,不利于提高产品质量 ,难以生产 出优质的清洁钢 。20 世纪 60 年代以后 ,直接还 原技术进入工业化阶段 ,为缺少废钢地区提供了 发展电弧炉炼钢的可能性 。而直接还原铁具有其 自身的优点 ,残余元素及有害元素含量低 。实践 证明 ,在提高产品的质量方面 ,直接还原铁是比较 理想的废钢替代料 。在使用轻质的废钢时 ,可配 加 DRI ,减轻废钢中的残存元素及有害元素的影 响 ,既能生产出质量比较高的钢 ,又可以合理地利 用废钢资源 。因此在废钢资源越来越少的情况
大量新产的没有钝化的直接还原铁必须堆放 在惰性气体清洗过的地仓内 ,或采用压块形式 ,或 用惰性液体和固体填塞 DRI 中的微孔 ,可降低其 氧化性 ,也可堆放在有盖的通风良好的场地内 ,使 其老化 (进行时效) [2] 。在时效时 ,将产生热量 ,而 且产生的很快 。为了消散这些热量 ,每层新料厚 度限制在 1. 5 m 以内 。时效过的直接还原铁 ,如 能保持干燥 ,或置于有盖的仓库内 ,或用帆布复盖 (不能用不透气的有水分凝结的材料) ,可安全地 储存 。
(7) 二 次 氧 化 。因 为 DRI 有 很 高 的 孔 隙 度 (45 %~70 %) ,容易二次氧化 。而压块的比表面 积较小 ,因而氧化性低 。
为减 少 二 次 氧 化 可 采 取 产 品 制 造 时 钝 化 处 理[2] 。钝化是指在 DRI 的所有内外表面形成一层 薄的四氧化三铁覆盖的保护膜 ,大部分的钝化性是 在最初几个小时内形成的 ,逐渐达到低的氧化性。
(1) 块度 。在外形尺寸方面有别于废钢 ,合适 的 DRI 粒度为 10~100 mm。粒度过小 ,容易飘浮 在渣中 ,也容易被除尘系统抽走而损失 ; 粒度过 大 ,则传热慢 ,易堆集粘结 ,不易熔化 。
(2) 密度 。DRI 密度比液态渣大时有助于快
作者简介 :王海兵 (1965 - ) ,男 ,四川内江人 ,工程师 ,主要从事炼钢技术质量管理方面的研究.
DRI 连 续 加 料 的 量 不 等 , 可 以 是 10 % ~ 100 %的用量 。使用 DRI 时 ,先在炉内熔化废钢 , 待形成熔池后 ,连续喂入 DRI。高比例使用 DRI 时也可采取留钢操作 ,即将前炉的剩余钢水或更 多的钢水留在炉内 。
直接还原铁在 1 540~1 580 ℃范围内熔化 。 如进料太慢 ,熔池会升温 ,冶炼时间就长 ;如进料 太快 ,因其导热性差而“冻结”。直接还原铁的熔 化速度取决于输入的电功率 、电炉的热效率和熔 化过程电能的需要量 。为维持此熔池温度 ,喂料 速度一般应等于直接还原铁的熔化速度 ,即每百 万瓦 28~32 kg/ min 。一般前期加料速度约为正 常喂料速度的 1/ 2 ~1/ 3 , 中期应在全负荷下喂 料 ,熔炼后期应减缓加料速度以便使钢水快速升 温而达到出炉温度的要求 。用这种装料方式后炉 料离电弧较近 ,比成批装料熔化速度快 。
(2) 当单位能耗达到 200 kWh/ t 时 ,加入 DRI 的速度为 1 000 kg/ min ;
·54 ·
(3 ) 废 钢 熔 清 后 , 加 入 DRI 的 速 度 为
2 500 kg/ min ; (4) 当熔池温度达 1 560 ℃时 ,加入的速度为
2 800~3 000 kg/ min ; (5) 剩余 10~15 t DRI 时 ,加入 DRI 的速度为
3 直接还原铁的使用操作
3. 1 成批装料 直接还原铁用于电弧炉炼钢 ,其配比不等 ,可
全用 DRI 作为炉料炼钢 。如果所用的直接还原铁 的比例为 30 %以下 ,则可用料罐装入 。此种装料 作业料罐底部装轻废钢 ,随后装入重废钢和 DRI , 这样可以避免 DRI 结块太多 。DRI 主要装在料罐 的下半部 ,使 DRI 尽可能装入炉内中心底部 ,防止 直接还原铁接近炉壁以及冷区结块而不能熔化 。 然而 ,当电弧从上部加热相当厚的 DRI 料层时 ,熔 化的金属便充填各个 DRI 球团之间的空隙并凝
5 DRI 对电弧炉炼钢的影响
5. 1 生产率 由于 DRI 有别于废钢的特性 ,对电弧炉炼钢
有一定的影响 。成批加入 DRI 料时 ,熔化炉料的 速度慢 ,同时 ,由于渣量增加 ,消耗的电能增加 。 一般来说 ,生产率随 DRI 料的增加而降低 。
连续加料时 ,减少了补加废钢的次数 (特别是 补加低密度的废钢时 ,补料次数较多) ,可防止因 大块废钢滑落折断电极而停工 。在补加一次料的 情况下 ,代替废钢的效果不大 ,当代替轻质废钢 时 ,可减少 2~3 次的装料时间 ,节省的时间就可 观了 。这样 ,热损失小 ,熔化速度加快 ,熔化和精 炼又同时进行 ,最终使冶炼时间缩短 。但大量使 用 DRI ,由于传热慢 ,同时还补加石灰 ,增加能量 消耗 ,还原 DRI 中的氧化铁需吸热 ,冶炼时间有可
在连续加料时 ,应加入一定量的石灰 ,使炉渣 的碱度不致降低 。由于使用 DRI 炼钢时碱度不 高 ,对炉衬侵蚀较严重 ,尤其对渣线部位 。因此可 加一些白云石质石灰 , 形成 CaO 、MgO 、SiO2 、FeO 渣系 ,碱度约为 2 ,当 w ( FeO) 为 10 %~15 %时可 溶解 MgO 达 12 %~16 %[4] 。装入一定量的白云 石质石灰 ,以保持渣中的 MgO 为 12 %或更多一 些[5] ,也保护了耐火材料免受浸蚀 。
结 ,不能渗入到球团深部 ,球团易烧结在一起且密 度小 ,难以落入钢水中 ,延长了熔化时间 。实践表 明 ,成批加入大于总炉料的 30 %的 DRI 时 ,由于 DRI 传热慢 ,会出现难熔问题 ,恶化其经济技术指 标 ,需使用连续加料技术 。 3. 2 连续加料
连续加料一般从炉顶喂料孔加入 。一是于炉 顶的几何中心开孔 ,使 DRI 垂直落入 ;而另一种是 在炉顶半径的中间开孔 ,经轨道抛射落入炉内中 心区域 。炉顶上部的连续喂料系统必须有足够的 高度 ,以保证 DRI 具有足够的动能以快速穿过渣 层。
2004 年 10 月
October 2004
·综述与评介·
钢 铁 研 究
Research on Iron & Steel
第 5 期 (总第 140 期)
No. 5 (Sum140)
直接还原铁作为废Biblioteka 替代品在电弧炉中的应用王海兵 (攀枝花钢铁集团公司 成都钢铁有限责任公司 ,四川 攀枝花 610069)
天津某厂配加超过 35 %的 DRI 炼钢时 ,采用 炉顶连续加料方式 。先使废钢熔化 ,再将 DRI 加 入到熔池中 。加入 100 %的 DRI 炼钢时 ,采用留 钢留渣操作 。具体操作如下[6] :
(1) 最后一篮废钢料单位能耗达 100 kWh/ t 时 ,开始加入 DRI 的速度为 500 kg/ min ;
下 ,直接还原铁作为电炉炼钢原料越来越受到人 们的重视 。
2 直接还原铁的主要特点
直接还原铁就是指铁矿石在低于熔化温度下 进行还原得到的海绵状的金属铁 ,简称 DRI。还 原过程中 ,形成多孔性的 DRI ,其比表面积 (包括 外表面和开口气孔的内表面) 较大 ,极易氧化 。为 了降低其氧化速度 ,可在直接还原过程的最后阶 段热态下料 ,并在冷却前挤压成块 ,这就是 HRI , 是 DRI 的压块形式 。DRI 的主要特性如下[1] 。
D RI AS A SUBSTITUTE OF SCRAP USED FOR STEELMAKING IN EL ECTRIC ARC FURNACES
WANG Hai - bing (Chengdu Iron and Steel Co. Ltd ,Panzhihua Iron and Steel corp . , Panzhihua 610069 ,China)
(4) w (C) 。DRI 的 w (C) 一般波动在 1. 0 %~ 3. 0 % ,分别与金属化率 95 %和 85 %相对应 。
(5) 脉石 。最初用的与高炉炼铁一样的铁矿 石 ,DRI 脉石含量较高 ,但用经选矿后的富铁矿石 时 ,DRI 脉石含量一般不超过 4 %。