颗粒料异常外观的产生原因及改进办法
7种异常颗粒料产生原因及其改进办法
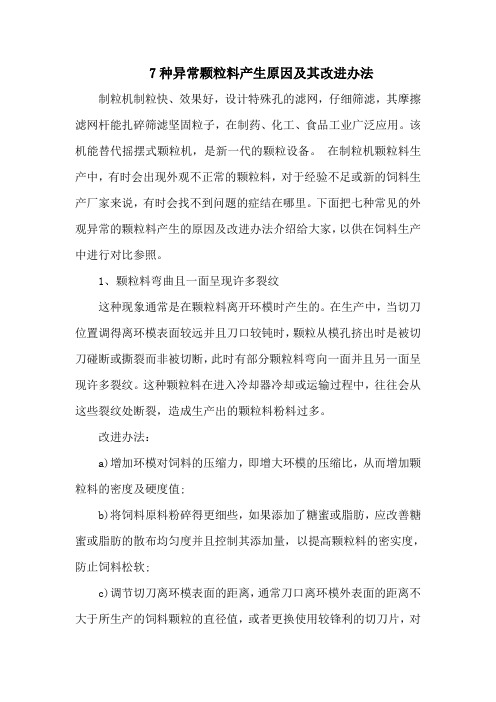
7种异常颗粒料产生原因及其改进办法制粒机制粒快、效果好,设计特殊孔的滤网,仔细筛滤,其摩擦滤网杆能扎碎筛滤坚固粒子,在制药、化工、食品工业广泛应用。
该机能替代摇摆式颗粒机,是新一代的颗粒设备。
在制粒机颗粒料生产中,有时会出现外观不正常的颗粒料,对于经验不足或新的饲料生产厂家来说,有时会找不到问题的症结在哪里。
下面把七种常见的外观异常的颗粒料产生的原因及改进办法介绍给大家,以供在饲料生产中进行对比参照。
1、颗粒料弯曲且一面呈现许多裂纹这种现象通常是在颗粒料离开环模时产生的。
在生产中,当切刀位置调得离环模表面较远并且刀口较钝时,颗粒从模孔挤出时是被切刀碰断或撕裂而非被切断,此时有部分颗粒料弯向一面并且另一面呈现许多裂纹。
这种颗粒料在进入冷却器冷却或运输过程中,往往会从这些裂纹处断裂,造成生产出的颗粒料粉料过多。
改进办法:a)增加环模对饲料的压缩力,即增大环模的压缩比,从而增加颗粒料的密度及硬度值;b)将饲料原料粉碎得更细些,如果添加了糖蜜或脂肪,应改善糖蜜或脂肪的散布均匀度并且控制其添加量,以提高颗粒料的密实度,防止饲料松软;c)调节切刀离环模表面的距离,通常刀口离环模外表面的距离不大于所生产的饲料颗粒的直径值,或者更换使用较锋利的切刀片,对于小直径的颗粒料也可采用薄刀片,并使薄刀片紧贴环模表面生产;d)使用粘结类的制粒助剂,有助于改善颗粒内部的结合力。
2、水平裂纹横过整个颗粒料与情形1中的现象有些类似,裂纹发生于颗粒的横切面,只是颗粒没有弯曲。
当将含有较多纤维的蓬松饲料制粒时,就有可能发生此种情况。
这种颗粒料往往是在将饲料挤入环模的造粒孔时,由于其中含有比孔径长的纤维,当颗粒被挤出后,因纤维的膨胀作用使颗粒料在横截面上产生横贯裂纹,产生枞树皮状的饲料外观。
改进的办法在于增加环模对饲料的压缩力,即增大环模的压缩比;控制纤维的粉碎细度,其最大长度不能超过粒径的三分之一;降低产量以减低饲料通过模孔时的速度,增加密实度;加长调质的时间,使用多层调质器或釜式调质器;当粉料水份过高或含有尿素时,亦有可能产生枞树皮状的饲料外观,应控制添加的水份和尿素含量。
影响饲料颗粒性状因素的分析及对策
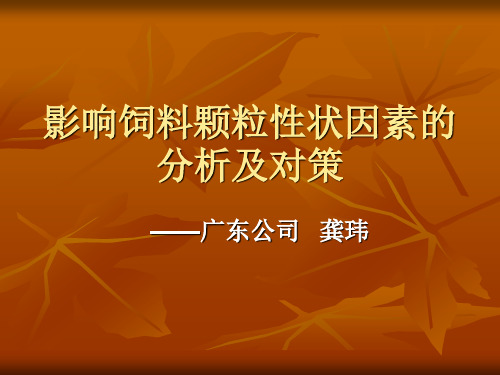
7影响水产单个颗粒或个体间颗粒颜色不一致 (即花料)的因素分析和对策
序号 1 2 原因 混合不均匀 调质水分不一致 改进方法 延长混合时间,改善混合效果 延长调质时间(低温调质),改善 调质性能
3
4 5
颗粒不均匀
7影响膨化料颗粒膨化率不高的因素的分析和对策
序号 1 2 原因 模具开孔率过高 物料中淀粉含量低 改进方法 更换合理模具 调整配方,增加淀粉含量
3
4
出模水分过低
喂料量低,产能低
调整蒸汽和水的注入量,使之合理
提高喂料转速
5
6 7
出模压力低
出模温度低 物料内含脂肪过高
提高出模时的工作压力
提高出模温度 调整配方
调整配方,增加淀粉含量 延长调质时间(检查调质器桨 叶)
7
调质水分过多
减少制粒时料的水分
4影响水产颗粒产生辐射式裂纹的因素分析和对策
序号 1 2 3 4 原因 含有较大的颗粒的原料 在冷却时不易软化 因软化程度不同而导致 收缩量差异而产生 改进方法 增加粉碎细度,控制粉状饲料粗 细度和均匀度 减少冷却风量,延长冷却时间 延长调质时间,蒸汽时间要饱和 减少冷却风量,延长冷却时间 延长调质时间,增加后熟化稳定 工序,提高调质温度 延长调质时间,蒸汽质量要饱和
7
8 9
压辊磨损不一致
模孔导料口磨损不一致 切刀不在合理位置
更换一致的压辊
修复模具,使之一致 调整切刀在切线位置上
12影响水产颗粒成品水分过高的因素分析和对策
序号 原因 改进方法
1 2
3 4 5 6 7 8 9
无烘干设备 模压缩比过低
颗粒剂、片剂、胶囊剂存在的问题及解决方法
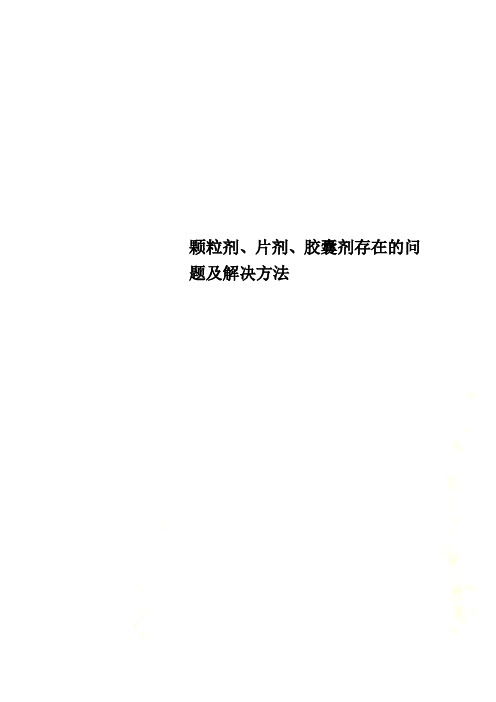
颗粒剂、片剂、胶囊剂存在的问题及解决方法颗粒剂、片剂、胶囊剂存在的问题及解决方法本文作者为北京中医药大学生药系研究生王建辉一.颗粒剂中药颗粒剂也称中药冲剂,指药材的提取物加适量赋型剂或部分药材细粉制成干燥顺粒或块状的内服药剂。
是在汤剂和糖浆剂的基础上发展起来的一种新剂型,一般按溶解性分为可溶性冲剂、混悬性冲剂和泡腾冲剂。
它保持了汤剂作用迅速,又克服了汤剂临用时煎煮不便的缺点,且口感好、体积小、服用、贮藏、运输方便。
但容易吸潮,由于工艺原因造成颗粒不均,色泽不均,它直接影响着顺粒剂质量和外观,现主要讨论一下色泽不均问题:1.如直接制粒时,稠浸肴与药粉及辅料棍合不均匀,浸膏不能均匀地湿润辅料,这时会出现色泽不一现象,为解决这一问题,经过多次实验证明,首先要把药粉及辅料充分混合均匀,再加稠浸青混合均匀,制粒时如色泽不均可加适量浓度乙醉调整,如再不均匀,制粒时把湿颗粒再次过筛,即可得外观颜色一致颗粒。
2.如要二次制粒是将浸青和药粉、辅料拌膏干燥粉碎的药粉进行制粒,制出的湿颗粒由于加乙醇浓度的不同,有时会出现大颗粒,烘干后颗粒大,整粒后颗粒不均匀。
解决这一方法是在湿粒未干时进行整粒.然后均匀喷洒些乙醇闷上后再烘干。
颗粒大,色泽深是由于乙醇浓度低、量大造成的。
如注意到以上几点可使颗粒均匀。
3.制备颗粒剂所用药粉或辅料粒度过大,可使颗粒色泽不一,解决方法是将药粉、辅料过筛,通常为100目筛为宜,这样可有效解决这一问题。
此外,由于原材料不同,药材质量、产地、采时、用药部位等方面可影响每批质量及外观,所以要尽可能保持原材料一致,不要轻易更换进药产地等方面。
在提取过程中每批要按同一处方投入(在没有特殊情况下),浸泡时间、加水量、温度、每批浓缩出的相对密度和体积都要保持一致。
所用辅料量每批要一致,否则也会出现颜色深浅不同的现象。
二.片剂随着中国几千年历史的发展,尤其是近年来中药及其制剂的广泛使用中药已成为独具特色的治病良药。
聚烯烃出现颗粒外观质量问题的原因及对策
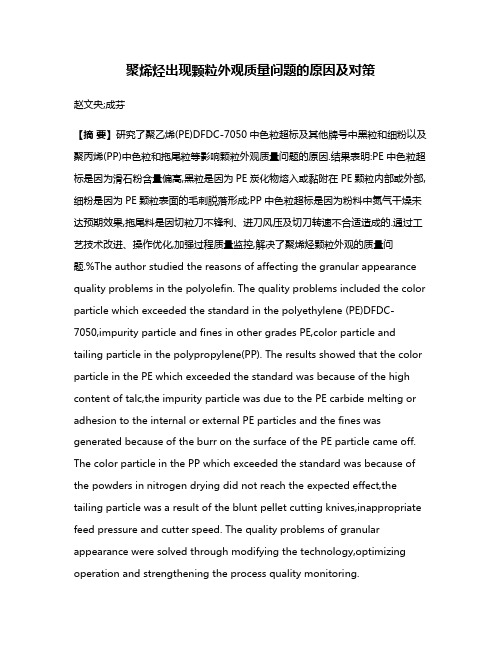
聚烯烃出现颗粒外观质量问题的原因及对策赵文央;成芬【摘要】研究了聚乙烯(PE)DFDC-7050中色粒超标及其他牌号中黑粒和细粉以及聚丙烯(PP)中色粒和拖尾粒等影响颗粒外观质量问题的原因.结果表明:PE中色粒超标是因为滑石粉含量偏高,黑粒是因为PE炭化物熔入或黏附在PE颗粒内部或外部,细粉是因为PE颗粒表面的毛刺脱落形成;PP中色粒超标是因为粉料中氮气干燥未达预期效果,拖尾料是因切粒刀不锋利、进刀风压及切刀转速不合适造成的.通过工艺技术改进、操作优化,加强过程质量监控,解决了聚烯烃颗粒外观的质量问题.%The author studied the reasons of affecting the granular appearance quality problems in the polyolefin. The quality problems included the color particle which exceeded the standard in the polyethylene (PE)DFDC-7050,impurity particle and fines in other grades PE,color particle and tailing particle in the polypropylene(PP). The results showed that the color particle in the PE which exceeded the standard was because of the high content of talc,the impurity particle was due to the PE carbide melting or adhesion to the internal or external PE particles and the fines was generated because of the burr on the surface of the PE particle came off. The color particle in the PP which exceeded the standard was because of the powders in nitrogen drying did not reach the expected effect,the tailing particle was a result of the blunt pellet cutting knives,inappropriate feed pressure and cutter speed. The quality problems of granular appearance were solved through modifying the technology,optimizing operation and strengthening the process quality monitoring.【期刊名称】《合成树脂及塑料》【年(卷),期】2015(032)005【总页数】3页(P49-51)【关键词】聚烯烃;颗粒外观;原因分析;措施【作者】赵文央;成芬【作者单位】中国石油化工股份有限公司镇海炼化分公司生产处,浙江省宁波市315207;焦作技师学院,河南省焦作市 4544002【正文语种】中文【中图分类】TQ325.1中国石油化工股份有限公司镇海炼化分公司(简称镇海炼化公司)有3套聚烯烃装置,2013年实际产量超过1 050 kt,是设计产能的110%。
影响颗粒料加工质量因素的分析和解决方法
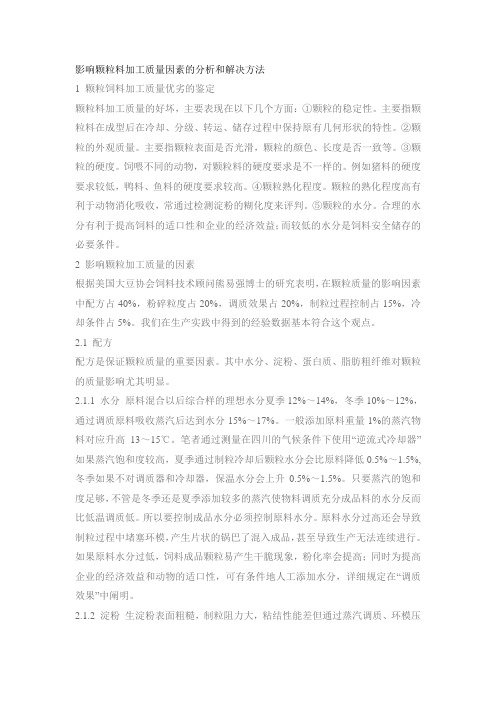
影响颗粒料加工质量因素的分析和解决方法1 颗粒饲料加工质量优劣的鉴定颗粒料加工质量的好坏,主要表现在以下几个方面:①颗粒的稳定性。
主要指颗粒料在成型后在冷却、分级、转运、储存过程中保持原有几何形状的特性。
②颗粒的外观质量。
主要指颗粒表面是否光滑,颗粒的颜色、长度是否一致等。
③颗粒的硬度。
饲喂不同的动物,对颗粒料的硬度要求是不一样的。
例如猪料的硬度要求较低,鸭料、鱼料的硬度要求较高。
④颗粒熟化程度。
颗粒的熟化程度高有利于动物消化吸收,常通过检测淀粉的糊化度来评判。
⑤颗粒的水分。
合理的水分有利于提高饲料的适口性和企业的经济效益;而较低的水分是饲料安全储存的必要条件。
2 影响颗粒加工质量的因素根据美国大豆协会饲料技术顾问熊易强博士的研究表明,在颗粒质量的影响因素中配方占40%,粉碎粒度占20%,调质效果占20%,制粒过程控制占15%,冷却条件占5%。
我们在生产实践中得到的经验数据基本符合这个观点。
2.1 配方配方是保证颗粒质量的重要因素。
其中水分、淀粉、蛋白质、脂肪粗纤维对颗粒的质量影响尤其明显。
2.1.1 水分原料混合以后综合样的理想水分夏季12%~14%,冬季10%~12%,通过调质原料吸收蒸汽后达到水分15%~17%。
一般添加原料重量1%的蒸汽物料对应升高13~15℃。
笔者通过测量在四川的气候条件下使用“逆流式冷却器”如果蒸汽饱和度较高,夏季通过制粒冷却后颗粒水分会比原料降低0.5%~1.5%,冬季如果不对调质器和冷却器,保温水分会上升0.5%~1.5%。
只要蒸汽的饱和度足够,不管是冬季还是夏季添加较多的蒸汽使物料调质充分成品料的水分反而比低温调质低。
所以要控制成品水分必须控制原料水分。
原料水分过高还会导致制粒过程中堵塞环模,产生片状的锅巴了混入成品,甚至导致生产无法连续进行。
如果原料水分过低,饲料成品颗粒易产生干脆现象,粉化率会提高;同时为提高企业的经济效益和动物的适口性,可有条件地人工添加水分,详细规定在“调质效果”中阐明。
颗粒饲料质量问题原因及解决方法

颗粒特性异常 UNUSUAL PELLET'S CHARACTERISTIC问题 PROBLEM原因 CAUSE解决 SOLUTION1. 颗粒表面光亮,内部 1. 调质后料的水份太低 - 增加蒸汽量干燥与发硬 . The moisture of feed after conditioner Increase Steam VolumeSurface of pellet is shine . is too low. - 减少蒸汽压力Inside pellet is dry and hard. Decrease Steam Pressure- 如果饲料吸湿能力低,增加蒸汽压力If feed has low ability of humidityabsorbtion, increase steam presure.- 在调质器喷水Sprey water at Conditioner.- 减少环模厚度Decrease DIE Thickness.问题 PROBLEM原因 CAUSE解决 SOLUTION2. 颗粒稳定性低 2. 原料脂肪含量高 - 在环模处喷脂肪代替在混合机里添加.Low Stability of Pellet Raw material contain high fat content. Sprey Fat at DIE face instead of addingin mixer.- 将调质后水份控制在16-17%Conditioning Feed's moisture is 16-17%- 将温度提高至摄氏85度Increase the temperature up to 85 °C- 提高蒸汽压力.Increse Steam Pressure.- 增加环模厚度Increase DIE Thickness.问题 PROBLEM原因 CAUSE解决 SOLUTION3. 颗粒形状似块状 3. - 颗粒表面几乎都是 - 将原料粉碎颗粒大小控制至适中.粗糙状,分级筛回粉过多 Particle size of grain should be suitablePellet surface is mostly rough.Too much dust returned from sieve- 环模太薄 - 采用厚的环模DIE is too thin. Use the thicker DIE.- 蒸气里有水所以制粒出来时 - 检查疏水器,蒸汽系统,减少蒸汽压力马上蒸发 Inspect water trap, steam system andThere is water in steam that reduce steam pressure.suddenly evaporate after coming - 减少蒸汽量out from DIE Decrease steam usage.问题 PROBLEM原因 CAUSE解决 SOLUTION4. 颗粒在一侧有裂纹 4. - 颗粒密度低,颗粒扳断多于切断 - 减少环模与切料刀的距离Pellet cracks on one side Low density of pellet. Shearing Reduce distance between DIE and Cutter.of pellet occured much more than - 将原料磨得更细一些cuting. Grind the material finer.- 增加环模厚度Increase DIE's thickness.- 增加料的调质糊化度Increase gelatinization of feed in conditioner.问题 PROBLEM原因 CAUSE解决 SOLUTION5. 颗粒形状似松树 5. - 饲料含有较高的纤维原料, - 增加环模厚度.Shape of pellet is like Pine tree.饲料密度低,尿素含量高 Increase DIE's thickness.Feed contain high fiber ingredient.Feed density is low and containmuch content of Uria.- 原料纤维比颗粒直径长 - 将原料磨细一些Length of ingredient fiber is longer Grind material finner.than pellet diameter.- 含有较高尿素的饲料湿度太高 - 减少蒸汽量,增加蒸汽压力Too high humidity of high urea feed Reduce steam usage, increase steam pressure.- 饲料脂肪含量高 - 在环模前添加脂肪代替在混合机添加Feed contain high fat. Add fat at Die front instead at the mixer.- 减少喂料器速度Reduce speed of feeder.问题 PROBLEM原因 CAUSE解决 SOLUTION6. 颗粒沿长度方向 6. 配方原料密度小,纤维高, - 将原料磨得细一些有裂纹(冷却后)冷却后沿长度方向撕裂。
影响制粒机效率的各方面因素
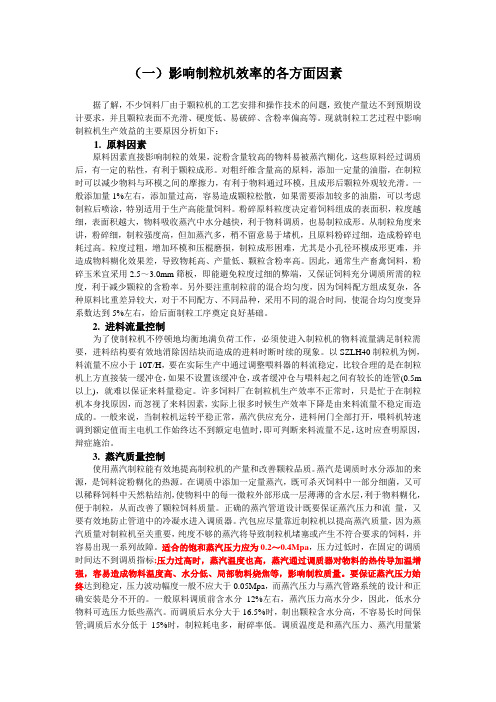
(一)影响制粒机效率的各方面因素据了解,不少饲料厂由于颗粒机的工艺安排和操作技术的问题,致使产量达不到预期设计要求,并且颗粒表面不光滑、硬度低、易破碎、含粉率偏高等。
现就制粒工艺过程中影响制粒机生产效益的主要原因分析如下:1. 原料因素原料因素直接影响制粒的效果,淀粉含量较高的物料易被蒸汽糊化,这些原料经过调质后,有一定的粘性,有利于颗粒成形。
对粗纤维含量高的原料,添加一定量的油脂,在制粒时可以减少物料与环模之间的摩擦力,有利于物料通过环模,且成形后颗粒外观较光滑。
一般添加量1%左右,添加量过高,容易造成颗粒松散,如果需要添加较多的油脂,可以考虑制粒后喷涂,特别适用于生产高能量饲料。
粉碎原料粒度决定着饲料组成的表面积,粒度越细,表面积越大,物料吸收蒸汽中水分越快,利于物料调质,也易制粒成形。
从制粒角度来讲,粉碎细,制粒强度高,但加蒸汽多,稍不留意易于堵机,且原料粉碎过细,造成粉碎电耗过高。
粒度过粗,增加环模和压棍磨损,制粒成形困难,尤其是小孔径环模成形更难,并造成物料糊化效果差,导致物耗高、产量低、颗粒含粉率高。
因此,通常生产畜禽饲料,粉碎玉米宜采用2.5~3.0mm筛板,即能避免粒度过细的弊端,又保证饲料充分调质所需的粒度,利于减少颗粒的含粉率。
另外要注重制粒前的混合均匀度,因为饲料配方组成复杂,各种原料比重差异较大,对于不同配方、不同品种,采用不同的混合时间,使混合均匀度变异系数达到5%左右,给后面制粒工序奠定良好基础。
2. 进料流量控制为了使制粒机不停顿地均衡地满负荷工作,必须使进入制粒机的物料流量满足制粒需要,进料结构要有效地消除因结块而造成的进料时断时续的现象。
以SZLH40制粒机为例,料流量不应小于10T/H,要在实际生产中通过调整喂料器的料流稳定,比较合理的是在制粒机上方直接装一缓冲仓,如果不设置该缓冲仓,或者缓冲仓与喂料起之间有较长的连管(0.5m 以上),就难以保证来料量稳定。
颗粒色泽不均匀问题的解决措施
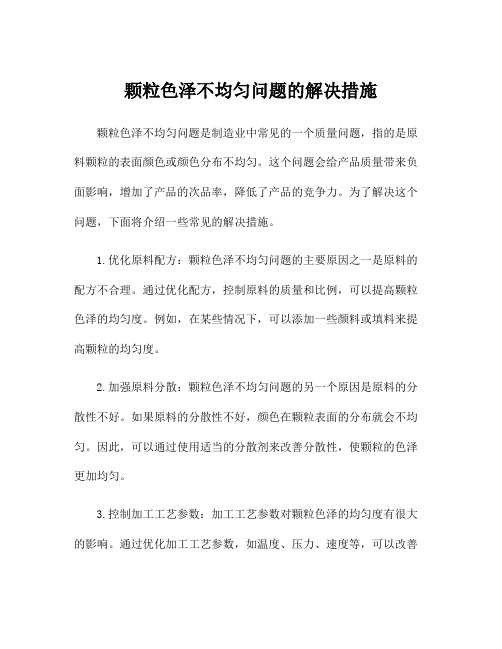
颗粒色泽不均匀问题的解决措施颗粒色泽不均匀问题是制造业中常见的一个质量问题,指的是原料颗粒的表面颜色或颜色分布不均匀。
这个问题会给产品质量带来负面影响,增加了产品的次品率,降低了产品的竞争力。
为了解决这个问题,下面将介绍一些常见的解决措施。
1.优化原料配方:颗粒色泽不均匀问题的主要原因之一是原料的配方不合理。
通过优化配方,控制原料的质量和比例,可以提高颗粒色泽的均匀度。
例如,在某些情况下,可以添加一些颜料或填料来提高颗粒的均匀度。
2.加强原料分散:颗粒色泽不均匀问题的另一个原因是原料的分散性不好。
如果原料的分散性不好,颜色在颗粒表面的分布就会不均匀。
因此,可以通过使用适当的分散剂来改善分散性,使颗粒的色泽更加均匀。
3.控制加工工艺参数:加工工艺参数对颗粒色泽的均匀度有很大的影响。
通过优化加工工艺参数,如温度、压力、速度等,可以改善颗粒色泽的均匀度。
例如,在某些情况下,可以增加混合时间或改变混合速度来提高颗粒色泽的均匀度。
4.定期检查设备状态:设备状态的不良也会影响颗粒色泽的均匀度。
定期检查设备的磨损程度、清洁程度等,并进行及时维修和清洁,可以减少因设备状态不良而导致的颗粒色泽不均匀问题。
5.优化操作流程:操作流程的不合理也会导致颗粒色泽不均匀。
通过优化操作流程,减少人为因素的影响,可以提高颗粒色泽的均匀度。
例如,在某些情况下,可以采取自动化控制手段来减少人为因素的干扰。
6.引入在线检测系统:为了及时发现和解决颗粒色泽不均匀问题,可以引入在线检测系统。
通过在线检测系统,可以及时监测和调整颗粒的色泽,避免颗粒色泽不均匀问题的发生。
7.建立完善的质量管理体系:建立完善的质量管理体系是解决颗粒色泽不均匀问题的关键。
通过建立适当的质量管理体系,可以有效地监控颗粒的色泽,并采取相应的措施进行调整和改进。
总结起来,解决颗粒色泽不均匀问题需要从多个方面进行考虑和改进。
通过优化配方、加强原料分散、控制加工工艺参数、检查设备状态、优化操作流程、引入在线检测系统和建立完善的质量管理体系,可以有效地解决这个问题,提高产品的质量和竞争力。
黑点、杂质形成原因及改善对策

黑点、杂质形成原因分析及对策黑点、杂质的缺陷是在正常生产过程中产生废品率的最重要因素。
它主要是影响制品外观从而导致报废。
杂质和绝大多数黑点都是外来物质,和原料本身无关,而少部分黑点、杂质是由原料本身造成。
黑点、杂质特征是颗粒较小、呈黑褐色,一般不反光,颗粒大时杂质呈层状、脆、易碎、破碎后多孔,其分布有两大特性:1、有的整体性无规则零散分布,有的是局部无规则零散分布,有时则仅偶尔出现在某一局部区域;2、这类黑点、杂质有时仅出现在制品表层,有时则不论表里深浅都有,不过距表层较近的内部黑点比表层黑点来颜色要浅,更深层的黑点则根本看不到。
有意思的是将这两点联系起来会发现,仅出现在某局部区域的杂质必然是表层的黑点,而黑点分布不论表里深浅的必然是整体性无规则零散分布。
这是由于内部存在的杂质必然是成型前就存在的,而仅成型时才出现的杂质必然只分布在表面。
这样,杂质就分为成型前和成型时形成两大类:一、成型前黑点、杂质成因:1 原料加工时,由于种种原因,异物不干净而使原料出现黑点;2 造粒不纯造成黑点;3 原料混入色母或带斑点的粉碎料块、料屑;4 料不纯,低熔点料中混入了高熔点料粒;5 包装、运输、贮藏过程中可能出现杂质混入,它明显特征是原料开包后,仔细观察,可以看到在料颗粒表面有异物、杂质;6 加料过程中的杂质、异物如下图为吸引或上料器及料斗的简图;除了5、11不会直接对料斗料造成污染,其他部分均可能在上料过程式中污染原料,造成制品黑点、杂质。
污染源包括:空气中的灰尘、料状悬浮物、异料料屑、异料料粒、粉状色母、染色剂等。
为杜绝异物杂质造成黑点,必须加强管理,控制从原料进厂至加料各环节(包括回用过程)。
换料时,必须仔细清理可能原先料或屑滞留的部位,特别备料箱、料斗、漏斗、下摆夹扣紧处等。
正常生产时,要特别注意加料源——备料箱的清洁。
停止生产后,应将加料系统对外界环境暴露处——上料管的上料端口密封,以防污染,做到环环相扣,封闭管理。
讲解减少涂装颗粒的控制措施

讲解减少涂装颗粒的控制措施汇报人:2023-12-15•涂装颗粒问题概述•生产环境控制•原材料质量控制目录•涂装工艺过程控制•人员操作规范培训•质量检测体系完善01涂装颗粒问题概述颗粒问题定义与分类颗粒问题定义涂装过程中,涂膜表面或内部出现的大小不一、形状各异的颗粒物。
颗粒分类按照颗粒来源可分为外界颗粒和内部颗粒;按照颗粒大小可分为大颗粒和小颗粒。
施工环境不洁,空气中灰尘、杂质等漂浮物附着在涂膜表面。
涂料本身含有杂质,或施工过程中涂料搅拌不均匀,导致颗粒沉淀在涂膜内部。
颗粒产生原因分析内部颗粒产生原因外界颗粒产生原因颗粒会导致涂膜表面不平整,影响产品的外观质量。
外观质量防腐性能使用寿命颗粒的存在会破坏涂膜的致密性,降低产品的防腐性能。
颗粒会加速涂膜的老化和破损,缩短产品的使用寿命。
030201颗粒对产品质量影响02生产环境控制定期清扫车间地面,保持地面无灰尘、油污等污染物。
地面清洁定期清洁车间墙面和天花板,防止积尘和蛛网。
墙面与天花板清洁确保生产设备和工具在使用前后进行清洁,避免残留物影响涂装质量。
设备与工具清洁车间清洁度管理空气过滤系统优化高效过滤器选用高效过滤器,有效去除空气中的微小颗粒和污染物。
定期更换滤芯根据使用情况,定期更换过滤器滤芯,保持过滤效果。
车间通风加强车间通风,保持空气流通,降低污染物浓度。
定期对生产设备进行检查,确保设备处于良好工作状态。
设备定期检查按照设备保养要求,定期对生产设备进行保养,延长设备使用寿命。
设备保养发现设备异常情况时,及时处理并记录,防止问题重复出现。
异常处理生产设备维护与保养03原材料质量控制选用品牌知名度高、质量稳定的涂料产品,确保涂料本身质量可靠。
选择优质涂料建立严格的涂料检验标准,对涂料的外观、粘度、细度、遮盖力、干燥时间等性能指标进行检测,确保涂料符合使用要求。
检验标准涂料选择与检验标准底材处理及前处理工艺优化底材处理对底材进行除油、除锈、磷化等处理,提高底材的附着力和涂装效果。
聚酯切粒外观质量的影响因素及改进措施

聚酯切 粒 系统 的脱 盐水 分为溢 流水 、 喷淋 水 、
随着 切粒 机负 荷 变 化及 时 调节 刀速 ; 调 节 刀
4 . 2 及 时调整 生产 负荷
置产 量波 动时 , 切粒 机负荷 发生 变化 , 水流量 没及 时调 节到 最佳点 , 与 负荷变 化不 匹配 , 缺乏最 佳工 艺参 数配 合 , 导 致熔体 铸条 不稳定 , 容 易相互 粘连
产生粘 粒 、 并粒 等异状 切粒 。
3 . 5 脱 盐 水
板, 进入切割室 , 经前 后 引 料辊 引入 到 动 、 定 刀 间
隙处 , 经动刀螺旋刃的旋转作用 , 被切成颗粒 。切 粒经 干燥 器脱 水 干 燥后 进 人 振 动 筛 , 再 输 送 到 包
装工段 进 行成 品包 装外 销 , 如 图 1所示 。
收稿 日期 : 2 0 1 7 — 0 7 — 1 9 ;修改稿收到 日期 : 2 0 1 7 — 0 9 36。 作者简 介:何达 ( 1 9 8 5 一) , 男, 工程师 , 从事聚酯 、 涤纶短纤 维生产管理工作 。E — m a i l : h e d a . O s h @s i n o p e c . e o m。
关键词 : 聚酯 切粒ቤተ መጻሕፍቲ ባይዱ 切片 外观质量 中 图分 类 号 : T Q 3 2 3 . 4
因素 对策 文章 编 号 : 1 0 0 1 — 0 0 4 1 ( 2 0 1 7 ) 0 6 — 0 0 7 3 — 0 3
文 献 标 识 码 :B
中 国石 化股 份有 限公 司天 津分 公 司 ( 简称 天
力 也减 小 , 铸 带条 进入动 刀 的速度 变慢 , 出现异 常 切粒 ; 当 引料 间 隙进一 步增 大时 , 铸 带条将 不 能引 入前后 引料 辊之 间 , 熔体 堆 积在生 头板上 , 引起 光 电故 障 报警 , 导 致 熔体 放 流 ; 反之, 如果 引 料 间隙
挤出造粒四大常见问题及解决对策

挤出造粒四大常见问题及解决对策一、断条1.原料有杂料,检查下料口的物料中是否含有杂料。
2.塑化不良,需提高加工温度。
(对于玻纤增强复合材料而言,往往是由于温度过高引起的。
)3.抽真空的力度不够,检查真空的运转是否良好,密封是否达到要求;密封是否达到要求4.过滤网堵塞,换过滤网。
5.口模孔数不对,料流失衡。
6.未加多孔板(玻纤类产品除外),熔体扰动而造成断条,断条主要集中在左侧。
7.挤出压力太低,螺杆内的物料不充实,需提高喂料频率、加大过滤网目数。
二、冒料没有塑化的物料1.适当降低喂料量或者降低螺杆转速。
2.升高前面段的温度,加快物料在机筒中的塑化;如增强料玻纤口前后的常规调节:输送及其熔化区温度适当提升5-10℃,将玱纤口后殌加热区温度适当调低10-20℃。
3.调整前面的螺杆组合,使前后输送平衡幵加快物料在机筒中的塑化。
塑化好的物料1.喂料太大;降低喂料频率。
2.真空盖开口。
3.机头网板出现炭化、填充等堵塞现象;清理机头。
4.螺杆排列错误(比如反向螺纹块的位置不排气口的位置过于接近,一般需要间隔一个螺纹的距离)。
三、粒子外观1.粒子两端的有孔问题。
两端都有孔:说明料里含的低分子物质戒水份较多,真空排气没抽干净戒原料含的低分子戒水成分较多。
只有一端有孔:说明料里含的低分子物质戒水份较少,没有严格要求时可以接受。
解决:前处理(干燥、密封等);加强真空排气(同时要考虑到螺杆设计);提高水槽温度。
2.粒子发泡。
出过高,原料成分的分解等。
原料含水分过高;原料(较差的副牌料)不耐温或成分使用不当,相互间化学反应而发;现多个孔,或者表面粗糙真空度不够;温度3.颗粒表面光滑平整问题。
颗粒表面光滑平整,要看所用的原材料的成分——玻纤、无机矿物、表面较粗燥的阻燃剂等物质。
但相比对下,同个料批次有差异,原因有:1)不均匀——数量多?时间短?机器?加工温度不够,塑化不好;螺杆组合不合理戒转速低,剪切不够,物料熔化不好;润滑剂过多戒加工特征特殊(如滑、低熔点),物料表面打滑剪切无效;2)机器问题,如模孔不平整、不够光滑等;3)原料成分间相容性不好(也包括色粉色母在内),出现分层、析出等。
木屑颗粒机制粒外形异常及解决方法
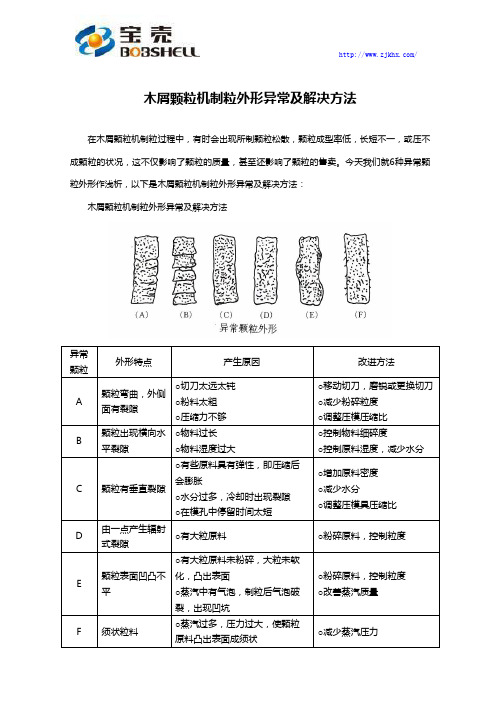
/
木屑颗粒机制粒外形异常及解决方法
在木屑颗粒机制粒过程中,有时会出现所制颗粒松散,颗粒成型率低,长短不一,或压不成颗粒的状况,这不仅影响了颗粒的质量,甚至还影响了颗粒的售卖。
今天我们就6种异常颗粒外形作浅析,以下是木屑颗粒机制粒外形异常及解决方法:
木屑颗粒机制粒外形异常及解决方法
异常颗粒外形特点产生原因
改进方法
A
颗粒弯曲,外侧面有裂隙○切刀太远太钝○粉料太粗○压缩力不够○移动切刀,磨锐或更换切刀○减少粉碎粒度○调整压模压缩比B
颗粒出现横向水平裂隙
○物料过长○物料湿度过大
○控制物料细碎度○控制原料湿度,减少水分C 颗粒有垂直裂隙
○有些原料具有弹性,即压缩后会膨胀
○水分过多,冷却时出现裂隙○在模孔中停留时间太短
○增加原料密度○减少水分○调整压模具压缩比D
由一点产生辐射式裂隙○有大粒原料
○粉碎原料,控制粒度
E
颗粒表面凹凸不平
○有大粒原料未粉碎,大粒未软
化,凸出表面
○蒸汽中有气泡,制粒后气泡破裂,出现凹坑
○粉碎原料,控制粒度○改善蒸汽质量
F 须状粒料○蒸汽过多,压力过大,使颗粒原料凸出表面成须状
○减少蒸汽压力。
20140327制粒过程中出现异常颗粒原因及应对措施
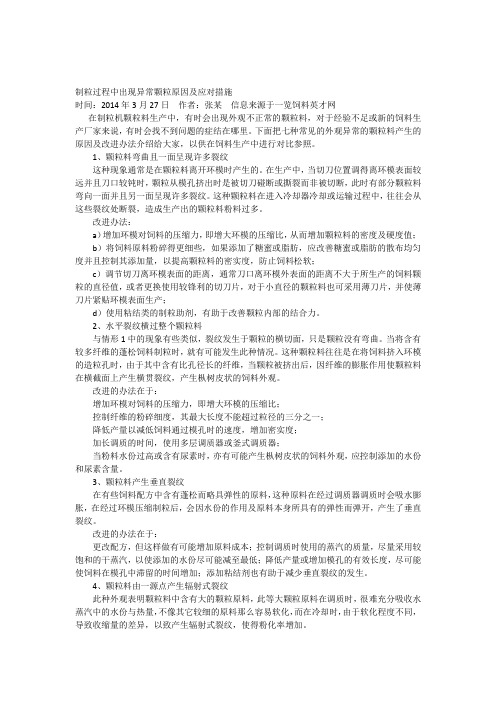
制粒过程中出现异常颗粒原因及应对措施时间:2014年3月27日作者:张某信息来源于一览饲料英才网在制粒机颗粒料生产中,有时会出现外观不正常的颗粒料,对于经验不足或新的饲料生产厂家来说,有时会找不到问题的症结在哪里。
下面把七种常见的外观异常的颗粒料产生的原因及改进办法介绍给大家,以供在饲料生产中进行对比参照。
1、颗粒料弯曲且一面呈现许多裂纹这种现象通常是在颗粒料离开环模时产生的。
在生产中,当切刀位置调得离环模表面较远并且刀口较钝时,颗粒从模孔挤出时是被切刀碰断或撕裂而非被切断,此时有部分颗粒料弯向一面并且另一面呈现许多裂纹。
这种颗粒料在进入冷却器冷却或运输过程中,往往会从这些裂纹处断裂,造成生产出的颗粒料粉料过多。
改进办法:a)增加环模对饲料的压缩力,即增大环模的压缩比,从而增加颗粒料的密度及硬度值;b)将饲料原料粉碎得更细些,如果添加了糖蜜或脂肪,应改善糖蜜或脂肪的散布均匀度并且控制其添加量,以提高颗粒料的密实度,防止饲料松软;c)调节切刀离环模表面的距离,通常刀口离环模外表面的距离不大于所生产的饲料颗粒的直径值,或者更换使用较锋利的切刀片,对于小直径的颗粒料也可采用薄刀片,并使薄刀片紧贴环模表面生产;d)使用粘结类的制粒助剂,有助于改善颗粒内部的结合力。
2、水平裂纹横过整个颗粒料与情形1中的现象有些类似,裂纹发生于颗粒的横切面,只是颗粒没有弯曲。
当将含有较多纤维的蓬松饲料制粒时,就有可能发生此种情况。
这种颗粒料往往是在将饲料挤入环模的造粒孔时,由于其中含有比孔径长的纤维,当颗粒被挤出后,因纤维的膨胀作用使颗粒料在横截面上产生横贯裂纹,产生枞树皮状的饲料外观。
改进的办法在于:增加环模对饲料的压缩力,即增大环模的压缩比;控制纤维的粉碎细度,其最大长度不能超过粒径的三分之一;降低产量以减低饲料通过模孔时的速度,增加密实度;加长调质的时间,使用多层调质器或釜式调质器;当粉料水份过高或含有尿素时,亦有可能产生枞树皮状的饲料外观,应控制添加的水份和尿素含量。
颗粒饲料霉变的原因分析及应对措施
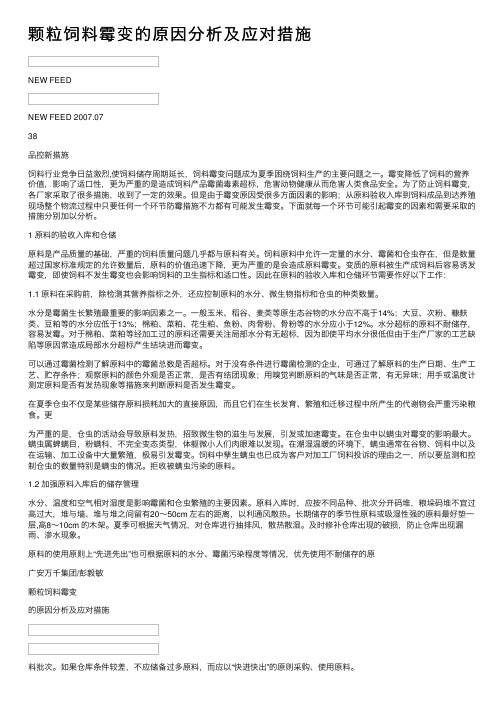
颗粒饲料霉变的原因分析及应对措施NEW FEEDNEW FEED 2007.0738品控新措施饲料⾏业竞争⽇益激烈,使饲料储存周期延长,饲料霉变问题成为夏季困绕饲料⽣产的主要问题之⼀。
霉变降低了饲料的营养价值,影响了适⼝性,更为严重的是造成饲料产品霉菌毒素超标,危害动物健康从⽽危害⼈类⾷品安全。
为了防⽌饲料霉变,各⼚家采取了很多措施,收到了⼀定的效果。
但是由于霉变原因受很多⽅⾯因素的影响;从原料验收⼊库到饲料成品到达养殖现场整个物流过程中只要任何⼀个环节防霉措施不⼒都有可能发⽣霉变。
下⾯就每⼀个环节可能引起霉变的因素和需要采取的措施分别加以分析。
1 原料的验收⼊库和仓储原料是产品质量的基础,严重的饲料质量问题⼏乎都与原料有关。
饲料原料中允许⼀定量的⽔分、霉菌和仓⾍存在,但是数量超过国家标准规定的允许数量后,原料的价值迅速下降,更为严重的是会造成原料霉变。
变质的原料被⽣产成饲料后容易诱发霉变,即使饲料不发⽣霉变也会影响饲料的卫⽣指标和适⼝性。
因此在原料的验收⼊库和仓储环节需要作好以下⼯作:1.1 原料在采购前,除检测其营养指标之外,还应控制原料的⽔分、微⽣物指标和仓⾍的种类数量。
⽔分是霉菌⽣长繁殖最重要的影响因素之⼀。
⼀般⽟⽶、稻⾕、麦类等原⽣态⾕物的⽔分应不⾼于14%;⼤⾖、次粉、糠麸类、⾖粕等的⽔分应低于13%;棉粕、菜粕、花⽣粕、鱼粉、⾁⾻粉、⾻粉等的⽔分应⼩于12%。
⽔分超标的原料不耐储存,容易发霉。
对于棉粕、菜粕等经加⼯过的原料还需要关注局部⽔分有⽆超标,因为即使平均⽔分很低但由于⽣产⼚家的⼯艺缺陷等原因常造成局部⽔分超标产⽣结块进⽽霉变。
可以通过霉菌检测了解原料中的霉菌总数是否超标。
对于没有条件进⾏霉菌检测的企业,可通过了解原料的⽣产⽇期、⽣产⼯艺、贮存条件;观察原料的颜⾊外观是否正常,是否有结团现象;⽤嗅觉判断原料的⽓味是否正常,有⽆异味;⽤⼿或温度计测定原料是否有发热现象等措施来判断原料是否发⽣霉变。
颗粒外观对高压聚乙烯电缆料的影响及对策
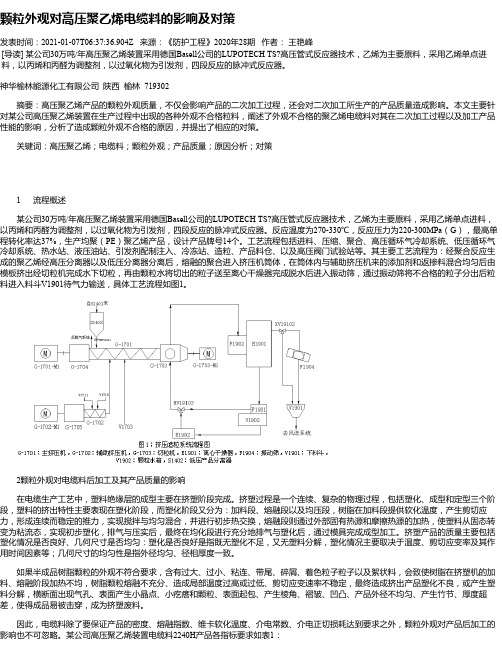
颗粒外观对高压聚乙烯电缆料的影响及对策发表时间:2021-01-07T06:37:36.904Z 来源:《防护工程》2020年28期作者:王艳峰[导读] 某公司30万吨/年高压聚乙烯装置采用德国Basell公司的LUPOTECH TS?高压管式反应器技术,乙烯为主要原料,采用乙烯单点进料,以丙烯和丙醛为调整剂,以过氧化物为引发剂,四段反应的脉冲式反应器。
神华榆林能源化工有限公司陕西榆林 719302摘要:高压聚乙烯产品的颗粒外观质量,不仅会影响产品的二次加工过程,还会对二次加工所生产的产品质量造成影响。
本文主要针对某公司高压聚乙烯装置在生产过程中出现的各种外观不合格粒料,阐述了外观不合格的聚乙烯电缆料对其在二次加工过程以及加工产品性能的影响,分析了造成颗粒外观不合格的原因,并提出了相应的对策。
关键词:高压聚乙烯;电缆料;颗粒外观;产品质量;原因分析;对策1 流程概述某公司30万吨/年高压聚乙烯装置采用德国Basell公司的LUPOTECH TS?高压管式反应器技术,乙烯为主要原料,采用乙烯单点进料,以丙烯和丙醛为调整剂,以过氧化物为引发剂,四段反应的脉冲式反应器。
反应温度为270-330℃,反应压力为220-300MPa(G),最高单程转化率达37%,生产均聚(PE)聚乙烯产品,设计产品牌号14个。
工艺流程包括进料、压缩、聚合、高压循环气冷却系统、低压循环气冷却系统、热水站、液压油站、引发剂配制注入、冷冻站、造粒、产品料仓、以及高压阀门试验站等。
其主要工艺流程为:经聚合反应生成的聚乙烯经高压分离器以及低压分离器分离后,熔融的聚合进入挤压机筒体,在筒体内与辅助挤压机来的添加剂和返掺料混合均匀后由模板挤出经切粒机完成水下切粒,再由颗粒水将切出的粒子送至离心干燥器完成脱水后进入振动筛,通过振动筛将不合格的粒子分出后粒料进入料斗V1901待气力输送,具体工艺流程如图1。
2颗粒外观对电缆料后加工及其产品质量的影响在电缆生产工艺中,塑料绝缘层的成型主要在挤塑阶段完成。
影响PE颗粒外观的原因分析及对策

影响PE颗粒外观的原因分析及对策王艳峰;金俊杰;华军;李健功【摘要】PE颗粒的外观质量直接影响产品的二次加工,分析了造成颗粒外观质量不合格的原因,并提出了相应的对策.指出了只要加强管理,提高操作人员对造成颗粒不合格因素的判断和处理能力,严格执行并不断优化各项工艺指标,就能有效地提高聚乙烯颗粒产品外观质量.【期刊名称】《甘肃科技》【年(卷),期】2012(028)018【总页数】3页(P29-31)【关键词】聚乙烯颗粒;外观;产品质量;原因;对策【作者】王艳峰;金俊杰;华军;李健功【作者单位】中国石油兰州石化公司乙烯厂,甘肃兰州730060;中国石油兰州石化公司乙烯厂,甘肃兰州730060;中国石油兰州石化公司乙烯厂,甘肃兰州730060;中国石油兰州石化公司乙烯厂,甘肃兰州730060【正文语种】中文【中图分类】TQ325对于PE的产品质量,除物理、化学及介电性能等需符合要求外,还包括PE颗粒的外观质量,外观质量的控制主要在挤压造粒阶段完成。
在挤压造粒过程中,如果操作控制不当,会造成PE产品颗粒变色、形状不规整等外观不合格颗粒,影响产品的二次加工,同时PE颗粒的外观变化,也可以在一定程度上反映生产工艺与设备的运行状况,必要时根据其变化及时采取有效措施进行调整,生产出合格而优质的PE产品。
因此外观质量合格的PE颗粒产品,不仅是客户的要求,也是控制产品质量的重要方面。
兰州石化公司20万 t/a的低密度聚乙烯(LDPE)装置引进德国Basell公司LUPOTECHT@管式法反应器技术。
以过氧化物为引发剂,丙烯或丙醛为相对分子质量调节剂,采用乙烯单点进料,过氧化物四点注入的脉冲式反应,最大单程转化率可达35%,包括压缩聚合,挤压造粒及风送系统[1]。
挤压造粒系统选用日本神户制钢有限公司(KOBE STEEL LTD)KE600型主挤压机、UP 650N型切粒机及KTXD3型辅助挤压机。
其主要工艺流程为:经聚合反应生成的聚乙烯经高压分离器以及低压分离器分离后,熔融的聚合进入挤压机筒体,在筒体内与辅助挤压机来的添加剂和返掺料混合均匀后由模板挤出经切粒机完成水下切粒,再由颗粒水将切出的粒子送至离心干燥器完成脱水后进入振动筛,通过振动筛将不合格的粒子分出后粒料进入料斗V1901待气力输送,具体工艺流程如图1所示。
外观缺陷不良原因及对策
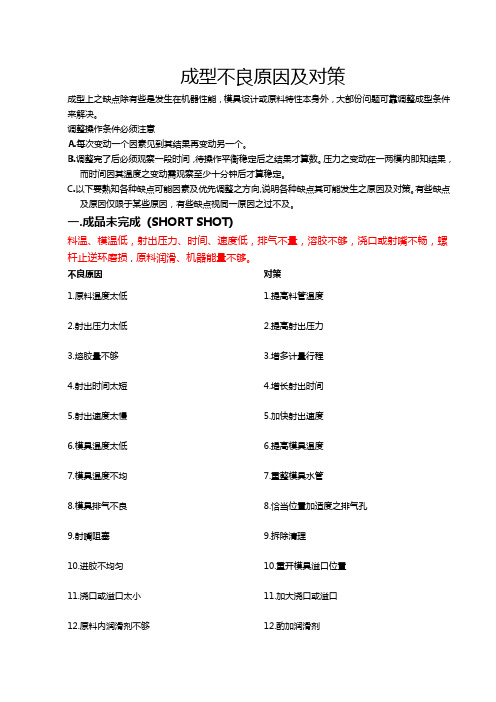
成型不良原因及对策成型上之缺点除有些是发生在机器性能,模具设计或原料特性本身外,大部份问题可靠调整成型条件来解决。
调整操作条件必须注意A.每次变动一个因素见到其结果再变动另一个。
B.调整完了后必须观察一段时间,待操作平衡稳定后之结果才算数。
压力之变动在一两模内即知结果,而时间因其温度之变动需观察至少十分钟后才算稳定。
C.以下要熟知各种缺点可能因素及优先调整之方向,说明各种缺点其可能发生之原因及对策。
有些缺点及原因仅限于某些原因,有些缺点视同一原因之过不及。
一.成品未完成(SHORT SHOT)料温、模温低,射出压力、时间、速度低,排气不量,溶胶不够,浇口或射嘴不畅,螺杆止逆环磨损,原料润滑、机器能量不够。
不良原因对策1.原料温度太低 1.提高料管温度2.射出压力太低 2.提高射出压力3.熔胶量不够 3.增多计量行程4.射出时间太短 4.增长射出时间5.射出速度太慢 5.加快射出速度6.模具温度太低 6.提高模具温度7.模具温度不均7.重整模具水管8.模具排气不良8.恰当位置加适度之排气孔9.射嘴阻塞9.拆除清理10.进胶不均匀10.重开模具溢口位置11.浇口或溢口太小11.加大浇口或溢口12.原料内润滑剂不够12.酌加润滑剂13.螺杆止逆环(过胶圈)磨损13.拆除检查修理14.机器能量不够14.更换较大机器二. 缩水溶胶量、射出压、时间、保压,冷却温度不足,射出速度太快,溢口不平衡,射料嘴阻塞,温度过高,模温不当,排气不良,成品本身或其肋(RIB)及柱(BOSS)过厚,料管过大,螺杆止逆环磨损不良原因对策1.熔胶量不足 1.增加熔胶计量行程2.射出压力不足 2.提高射压3.保持压力不够 3.提高或增加保持压力4.射出时间太短 4.增长射出时间5.射出速度太快 5.减少射出速度6.溢口不平衡 6.调整模具入口大小或位置7.射料嘴阻塞7.拆除清理8.温度过高8.降低温度9.模温不当9.调整适当温度10.冷却温度不够10.酌延冷却时间11.排气不良11.在缩水处设排气孔12.成品本身或其肋(RIB)及柱(BOSS)过厚12.检讨成品13.料管过大13.更换较小规格料管14.螺杆止逆环磨损14.拆除检修三. 成品黏膜(PRODUCT STICKING)射出压力太高,射胶量过多,保压时间太久,射出速度太快,料温太高,进料不均使部分过饱,冷却时间不足,模具温过高或过低,模具内脱模倒角(UNDER-CUT),模具表面不光不良原因对策填料过饱(OVERPACK)1.射出压力太高2.降低射出压力2.射胶量过多 2.使用脱模剂3.保压时间太久 3.减少射出时间4.射出速度太快 4.降低射出速度5.料温太高 5.降低料温6.进料不均使部分过饱 6.变更溢口大小或位置7.冷却时间不足7.增加冷却时间8.模具温过高或过低8.调整模温及两侧相对温度9.模具内脱模倒角(UNDER-CUT) 9.修模具除却倒角10.模具表面不光10.打光模具四. 浇道(水口) 黏膜(SPRUE STICKING)射出压力太高,原料温度过高,浇道过大,浇道冷却不够,浇道脱模角不够,浇道凹弧(SPRUE BUSHING)与射嘴之配合不正. 无浇道抓锁,填料过饱不良原因对策1.射出压力太高 1.降低射出压力2.原料温度过高 2.降低原料温度3.浇道过大 3.修改模具4.浇道冷却不够 4.延长冷却时间或降低料管温度5.浇道脱模角不够 5.修改模具增加角度6.浇道凹弧(SPRUE BUSHING)与射嘴之配合不6.重新调整与配合正7.浇道内表面不光或有脱模倒角,其外孔有损坏7.检修模具8.无浇道抓锁(SNATCH PIN) 8.加设抓销9.填料过饱9.降低射出量、时间及速度五. 毛头、披风(FLASH)原料温度太高,射出压力太高,填料过饱,合模线或靠密面不良,锁模压力不够,制品投影面积过大不良原因对策1.原料温度太高 1.降低原料温度、降低模具温度2.射出压力太高 2.降低射出压力3.填料过饱 3.降低射出时间、速度及计量4.合模线或靠密面不良 4.检修模具5.锁模压力不够 5.增加锁模压力6.制品投影面积过大 6.更换锁模压力较大之机器六. 开模时或顶出时成品破裂填料饱和,模温太低,部分脱模角不够,有脱模角,成品脱模时不能平衡脱离,顶针不够或位置不当,脱模时模具产生真空现象不良原因对策1.填料饱和 1.降低射出压力、时间、速度及胶量2.模温太低 2.升高模温3.部分脱模角不够 3.检修模具4.有脱模角 4.检修模具5.成品脱模时不能平衡脱离 5.检修模具6.顶针不够或位置不当 6.检修模具7.脱模时模具产生真空现象7.开模或顶出慢速,加进气设备七. 结合线(PARTING LINES)原料熔融不佳,模具温度过低,射出速度太慢,射出压力过低,原料不洁或渗有它料,脱模油太多,浇道及溢口过大或过小,模穴内空气排除不及时不良原因对策1.原料熔融不佳 1.提高原料温度、提高背压加快螺杆转速2.模具温度过低 2.提高模具温度3.射出速度太慢 3.增加射出速度4.射出压力过低 4.提高射出压力5.原料不洁或渗有它料 5.检查原料6.脱模油太多 6.脱模油尽量少用或不用7.浇道及溢口过大或过小7.调整模具入口尺寸或改变位置8.模穴内空气排除不及8.增开排气孔或检查是否有阻塞八. 流纹(FLOW LINES)原料熔融不佳,模具温度太低,射出速度太快或太慢,射出压力太高或太低,原料不洁或渗有它料,溢口过小产生射纹,成品断面厚薄相差太多不良原因对策1.原料熔融不佳 1.提高原料温度、提高背压、加快螺杆速度2.模具温度太低 2.提高模具温度3.射出速度太快或太慢 3.调整适当射出速度4.射出压力太高或太低 4.调整适当射出压力5.原料不洁或渗有它料 5.检查原料6.溢口过小产生射纹 6.加大溢口7.成品断面厚薄相差太多7.变更成品设计或溢口位置九.银纹、气疮(SILVER STREAKS)原料含有水份,原料温度过高或模具过热,原料中含其它添加物如润滑剂,染料等分解质,原料中其它添加物混合不均,射出速度太快,模具温度太低,原料颗粒粗细不均,料管内夹有空气,原料在模内流程不当不良原因对策1.原料含有水份 1.原料彻底烘干、提高背压2.原料温度过高或模具过热 2.降低原料温度,射嘴及前段温度过高3.原料中含其它添加物如润滑剂 3.减少其使用量或更换4.染料等分解质 4.耐温较高之替代品5.原料中其它添加物混合不均 5.彻底混合均匀6.射出速度太快 6.减慢射出速度7.模具温度太低7.提高模具温度8.原料颗粒粗细不均8.使用粒状均匀之原料9.料管内夹有空气9.降低料管后段温度、提高温度及背压10.原料在模内流程不当10.调整溢口之大小及位置、模具温度保持平均十. 成品表面不光泽模具温度太低,原料之计量不够,模内过多脱模油,模内表面有水,模内表面不光不良原因对策1.模具温度太低 1.提高模具温度2.原料之计量不够 2.增加射出压力时间及计量3.模内过多脱模油 3.擦拭干净4.模内表面有水 4.擦拭并检查是否有漏水5.模内表面不光 5.模具打光十一. 成品变形(WARPING)成品顶出时尚未冷却,成品形状及厚薄不对称,填料过多,几个溢口进料不均匀,顶出系统不平衡,模具温度不均匀,进溢口部份之原料太松太紧。
中药颗粒剂包装过程中常见质量问题和解决方法
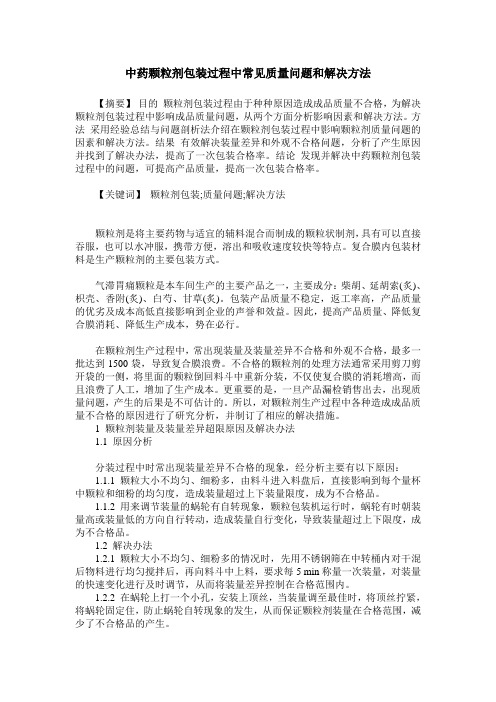
中药颗粒剂包装过程中常见质量问题和解决方法【摘要】目的颗粒剂包装过程由于种种原因造成成品质量不合格,为解决颗粒剂包装过程中影响成品质量问题,从两个方面分析影响因素和解决方法。
方法采用经验总结与问题剖析法介绍在颗粒剂包装过程中影响颗粒剂质量问题的因素和解决方法。
结果有效解决装量差异和外观不合格问题,分析了产生原因并找到了解决办法,提高了一次包装合格率。
结论发现并解决中药颗粒剂包装过程中的问题,可提高产品质量,提高一次包装合格率。
【关键词】颗粒剂包装;质量问题;解决方法颗粒剂是将主要药物与适宜的辅料混合而制成的颗粒状制剂,具有可以直接吞服,也可以水冲服,携带方便,溶出和吸收速度较快等特点。
复合膜内包装材料是生产颗粒剂的主要包装方式。
气滞胃痛颗粒是本车间生产的主要产品之一,主要成分:柴胡、延胡索(炙)、枳壳、香附(炙)、白芍、甘草(炙)。
包装产品质量不稳定,返工率高,产品质量的优劣及成本高低直接影响到企业的声誉和效益。
因此,提高产品质量、降低复合膜消耗、降低生产成本,势在必行。
在颗粒剂生产过程中,常出现装量及装量差异不合格和外观不合格,最多一批达到1500袋,导致复合膜浪费。
不合格的颗粒剂的处理方法通常采用剪刀剪开袋的一侧,将里面的颗粒倒回料斗中重新分装,不仅使复合膜的消耗增高,而且浪费了人工,增加了生产成本。
更重要的是,一旦产品漏检销售出去,出现质量问题,产生的后果是不可估计的。
所以,对颗粒剂生产过程中各种造成成品质量不合格的原因进行了研究分析,并制订了相应的解决措施。
1 颗粒剂装量及装量差异超限原因及解决办法1.1 原因分析分装过程中时常出现装量差异不合格的现象,经分析主要有以下原因:1.1.1 颗粒大小不均匀、细粉多,由料斗进入料盘后,直接影响到每个量杯中颗粒和细粉的均匀度,造成装量超过上下装量限度,成为不合格品。
1.1.2 用来调节装量的蜗轮有自转现象,颗粒包装机运行时,蜗轮有时朝装量高或装量低的方向自行转动,造成装量自行变化,导致装量超过上下限度,成为不合格品。
注塑外观颗粒不良报告 (sample)
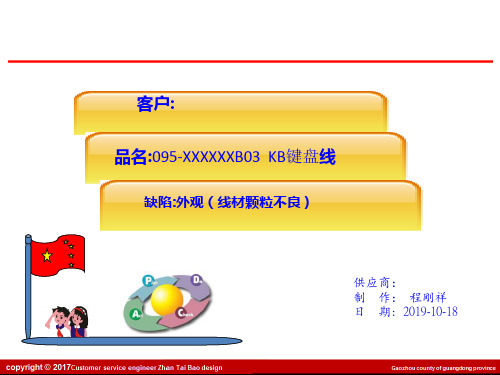
2019-10-19 程刚祥
资 料
<<质量通知单>>,
Completion Date:
Superintendent:
此款产品暂未安排生产,待后续生产连续三批追踪产品生产状况.
D7. PREVENT RECURRENCE (系統預防對策): 将不良图片做成<<质量通知单>>,并订于<制造规格>后,对作业员进 行岗前倡导,供后续每批生产作业员了解客户反映状况,制程生产作 重点确认.
D5.CORRECTIVE ACTIONS (改善對策)
Completio n Date:
Superin tendent:
1.冲洗炮筒务必保证出线外观完整无缺,不得有外观不良现象.对第一卷线注明首件字 样。
2.裁线人员对开机第1卷务必自检,不得让此不良流出。
3. 品管跟进标示是否到位,以及机台冲料是否OK,才可量产;品管员在各工序抽检 时,要跟进首卷的线材外观.
1.参与实施产品开发、研制工作、制定开发计划; 2、 按研发计划 完成技术文件编制及图纸设计工作及时记录各种工作要 素,编制 完整的产品文件。 3、 汇同产品生产部门完成试生产,处理试生 产中的设计问题。 4、 总结产品研发经验,持续产品的改进,并 根据客户或公司有关部门的 合理要求进行设计修改和设计改进, 完成产品定型工作。 5、 协助质量、销售部门解决客户技术问题 和搞好客户服务。 6、 为产品的投标提供技术支持。 7、 接受 部门领导布置的专项任务和临时性任务。
D2: PROBLEM DESCRIPTION (问题叙述)
Байду номын сангаас
群光客诉
品 名: 095-XXXXXR-B03 KB线
- 1、下载文档前请自行甄别文档内容的完整性,平台不提供额外的编辑、内容补充、找答案等附加服务。
- 2、"仅部分预览"的文档,不可在线预览部分如存在完整性等问题,可反馈申请退款(可完整预览的文档不适用该条件!)。
- 3、如文档侵犯您的权益,请联系客服反馈,我们会尽快为您处理(人工客服工作时间:9:00-18:30)。
生产中,颗粒饲料产品有时会出现不同程度的外观质量缺陷。
现将颗粒饲料中常出现的加工缺陷归纳如下,并分析缺陷产生的原因,提出各种改进措施。
1 颗粒弯曲且一面呈现许多裂纹1.1 产生原因:这种现象通常是在颗粒离开环模时产生的。
原因有:①当切刀刀口位置离环模与压辊啮合区表面较远或切刀平面与啮合区切线角度不合理或刀口较钝时,颗粒从模孔挤出时是被切刀碰断的或撕裂而非被切断的;②减压孔过大。
这2种情况会造成有部分颗粒弯曲且一面呈现许多裂纹。
1.2改进措施:①增大环模的压缩比,增大环模、压辊对物料的压缩力;从而增加颗粒料的密度、硬度和强度;②提高粉碎细度;③如果添加了糖蜜或油脂应控制添加量并改善糖蜜或油脂的散布均匀度。
以提高饲料的密实度,防止饲料松软;④调节切刀与环模表面的距离和角度;⑤使用较比较薄的切刀(1~1.2mm厚的锰钢片性能较好)并且生产过程中磨损后要及时磨锋利;⑥必要时使用粘结剂,改善颗粒料内部的结合力;⑦减压孔直径与有效孔直径差应控制在0.2~0.4mm。
2水平裂纹横向贯穿整个颗粒2.1 产生原因:与颗粒弯曲显现类似,裂纹发生于颗粒的横切面,只是没有弯曲。
其产生原因主要:①含有较多纤维的蓬松饲料制粒时,由于其中含有比孔径长的纤维,当颗粒被挤出后,因纤维的膨胀作用使颗粒在横切面上产生贯穿的裂纹。
②调质温度低或时间短,调质不充分,饲料熟化度不够。
③粘结性原料含量过少。
④调质后水分高。
2.2 改进措施:①增大环模的压缩比,增大环模压辊对物料的压缩力;从而增加颗粒料的密度、硬度和强度;②提高粉碎细度,使其中最长的纤维长度不超过粒径的三分之一;③降低产量以减小饲料通过模孔的速度,增加密实度。
④提高调质质量:加长调质时间,或使用多层调质器或高效调质器。
⑤当粉料的水分过高或含有尿素时,也可能产生枞树皮状的裂纹,应控制添加的水份和尿素含量。
3 颗粒产生纵向裂纹3.1 产生原因:①配方中含有蓬松而略带弹性的原料,在经过调质是会吸水膨胀,经过环模压缩制粒后,会因水分的作用及原料本身的弹性而弹开,产生纵向裂纹。
②环模压比过低。
③调质温度低或时间短,调质不充分,饲料熟化度不够。
3.2 改进措施:①如果有必要而且配方成本允许,调整配方。
②使用较饱和的干蒸汽降低粉料调质后的水分。
③降低产量或加大压缩比,尽可能地延长饲料在环模中的时间;④有必要时添加粘结剂,也可以减少颗粒产生纵向裂纹。
⑤提高调质质量:加长调质时间,或使用多层调质器或高效调质器。
⑥必要时增加后熟化工序。
4颗粒产生辐射式裂纹4.1 产生原因这种外观主要是由于颗粒中含有较大的颗粒,这些大颗粒在调质时,很难充分吸收水蒸汽中的水分和热量,不象其它较细的原料那么易软化,而在冷却时,由于软化程度不同,导致收缩量的差异,以致产生辐射式裂纹。
4.2 改进措施:①控制原料的粉碎细度和颗粒均匀度。
②使调质充分均匀,让原料各组分都能充分均匀软化。
③减少冷却风量,延长冷却时间。
④必要时增加后熟化工序。
5颗粒表面凹凸不平5.1 产生原因:饲料中的表面凹凸不平,影响了饲料的美观,投喂到水中,饲料各部分的耐水性不同,使饲料在短时间内溃散。
原因在于:①制粒的粉料中含有没有粉碎过或半碎的大颗粒原料,调质过程中未能充分软化,在通过模孔时就不能很好地和其它原料结合在一起,使颗粒显得凹凸不平。
②调质后的原料中夹杂有蒸汽泡,蒸汽泡使饲料在压制成颗粒的过程中产生气泡,当颗粒被挤出环模的一瞬间,由于压力的变化导致气泡破裂而在颗粒表面产生凹凸不平现象。
任何含有纤维的饲料皆可能发生此种情况。
5.2 改进措施:①妥善控制粉料的细度、改善调质效果从而在调质时使所有原料都能充分软化。
②对于含纤维比较多的原料,由于容易夹杂蒸汽泡,因此不要在这种配方中加入太多的蒸汽。
6颗粒出现腮须状6.1 产生原因如果加入的蒸汽量过多,过多的蒸汽游离于纤维或粉料中未被充分吸收,而在颗粒挤出环模时,因压力的急剧变化蒸汽泡爆裂而将纤维或颗粒原料凸出表面,形成腮须,尤其在生产高淀粉、高纤维含量的饲料时,使用的蒸汽过多,情况越严重。
6.2 改进措施改善调质质量。
高淀粉、高纤维含量的饲料,应使用(0.1~0.2MPa)的低压蒸汽。
蒸汽压力越低,开始凝结的时间越短,有利让蒸汽中的水分与热量能充分释放给饲料吸收。
假若蒸汽压力太高,带压的蒸汽进入调质器的瞬间易出现闪蒸,在温度降到100℃之前不会则蒸汽不会凝结。
于是有部分蒸汽储积在调质后的饲料原料中,当制粒时就导致上面所述的腮须状颗粒效应,总之应特别注意蒸汽的压力调节。
另外要注意改善调质质量让添加的蒸汽充分被原料吸收。
7单个颗粒或个体间颗粒颜色不一致,俗称“花料”7.1 产生原因饲料的颜色不均匀容易使养殖户对产品的质量产生怀疑。
一般来说,饲料颜色不均匀与熟化和混合调质过程相关。
原料的粉碎粒度不够容易导致原料混合不均匀,从而影响饲料颗粒不同部位的熟化程度。
另外,熟化过程中温度过高、颗粒大小不一等因素也会影响饲料颗粒的颜色。
主要表现为从环模挤出的个别颗粒的颜色比其它正常颗粒的颜色深或者浅,或者单个颗粒的表面颜色不一致,从而影响整批饲料的外观质量。
综合而言,原因主要有:①饲料配方成分复杂,原料品种多;①混合不均匀;③调质不均匀,制粒前的粉料水分含量不一致;④重复制粒的回机料添加量过大;⑤环模孔内壁粗糙度、模辊间隙、模辊磨损量不一致,环模内布料不均匀等造成环模出料不均匀;⑥粉碎细度达不到要求;⑦粉料在料仓中有分级现象。
7.2 改进措施:①改善混合效果;②提高调质质量:加长调质时间、使用多层调质器或高效调质器、延长调质时间;③控制粉料的细度和均匀度;④制回机料添加量,添加回机料必须经过混合;⑤修整或更换环模、压辊;⑥调整模辊间隙到最佳位置,并且使所有的间隙一致。
8颗粒耐水性差8.1 产生原因饲料的耐水性是指饲料在水中的抗溶蚀能力,通常以规定条件下饲料在水中的溶失率表示。
国家标准中规定对虾饲料的耐水性要达到30 min。
饲料耐水性差会导致饲料在未被摄食前就溶散在水中,造成饲料的浪费,并且污染水质。
颗粒耐水性差的原因有:①调质时间短、调质温度低,造成调质不充分温度低熟化度不够、水分不足。
②淀粉等粘结性原料含量不足。
③环模的压缩比过低。
④脂肪含量过高或粗纤维含量过高。
⑤粉碎细度不够。
8.2 改进措施:①提高原料水分、调整浆叶角度延长调质时间、增加调质蒸汽。
②对调质器夹层加蒸汽加热、必要时增加后熟化稳定设备。
③调整配方适当增加淀粉含量、减少脂肪、粗纤维的含量;必要时添加粘结剂。
④加大环模的压缩比、提高粉碎细度。
9 颗粒料含粉多9.1 养殖户经常因为饲料中料粉过多而投诉。
粉料产生原因有3类:①因为饲料颗粒表面不光滑、颗粒松散、切口不整齐等在运输过程中饲料易粉化;②分级筛粉料口被堵塞,制粒冷却产生的粉料没有被筛分出来。
③成品仓中物料是呈漏斗型下料的,颗粒料的流动性好会先下,粉料流动性差会积聚,到一定的时候会坍塌,这种坍塌下来的颗粒料含粉特别高。
如果接料时不注意检查将这种料清出来,会造成一批料中有个别的几包粉料特别重。
9.2 改进措施:①针对饲料颗粒表面不光滑、颗粒松散、切口不整齐等原因,产生的粉料可以采取如下措施:根据原料的特性和颗粒要求选择合适的环模开孔面积、压缩比和喂料量;在设计配方时考虑颗粒粉化的影响适当减少脂肪、纤维的含量,增加淀粉含量;通过延长调质时间、增加调质水分和温度等措施提高调质质量,提高饲料熟化度;提高粉碎细度:调整或修磨切刀使颗粒切口整齐。
②清理或检修分级筛。
③接料过程中注意检查饲料含粉率;将含粉率,超标的料重新筛分;针对鱼料等对含粉率,有严格要求的颗粒料,必要时在成品仓下,接料称前加一台震动筛,对饲料进行二次筛分。
10 颗粒长短不一10.1 产生原因长短不一的饲料颗粒影响饲料的整体外观,另外也会导致饲料不能充分被动物利用,造成浪费。
颗粒长短不均匀的原因有:①在同一时刻制粒室内物料分布不均匀;②制粒机的喂料量不均匀,调质效果波动很大;③模辊间隙不一致;④压辊磨损不一致;⑤环模导料口的磨损量,沿轴向不一致或环模上被堵死的孔较多;⑥沿环模的轴向,两端的出料速度小于中间的速度。
⑦设计环模时减压孔相比有效孔过大,有的颗粒在减压孔中被摔断;小粒径的环模因减压孔长,尤其易产生颗粒长短不均匀的现象。
⑧切刀的位置或角度不合理。
10.2 改进措施:①调整布料刮刀的长短、宽窄或角度。
②刚开设生产和快结束生产时喂料量小且不均匀,导致颗粒长度偏短,如果要求高要接出来。
生产过程中要保持喂料量、蒸汽调质的稳定,投入的切刀数量要和产量相匹配,必要时要牺牲产量保证得到合适的颗粒长度。
③调节压辊调节螺丝使每个模辊间隙一致。
④新环模要配新压辊,使用中的每个压辊磨损量要一致;如果压辊、环模轴向磨损不一致,必要时要将高的地方打磨掉。
⑤修理环模的导料口;及时清理,环模上被堵死的孔。
⑥在设计环模时,沿环模的轴向,两端的3排孔压缩比可以比中间的小1~2mm(根据配方和粒径选择)。
⑦在设计环模时对颗粒长短要求严格的产品,例如鱼料有效孔直径与减压孔直径差要控制在0.2~0.4mm范围内。
⑧切刀厚度控制在1.5mm内,刀口锋利,刀口位于压辊和环模的啮合线上,切刀平面于压辊环模啮合面切线上翘3~5度角。
⑨定期检查环模与制粒机的同轴度,超标时要修配环模、调节主轴承间隙或更换主轴和空轴轴承。
11 成品水分过高11.1 产生原因:饲料颗粒水分过高,不利于饲料的储存,易发霉发酵。
造成颗粒料水分过高的原因有:①原料水分过高。
②蒸汽饱和度不够,调质后水分过高。
③调质温度过低。
④烘干或冷却时间不够。
⑤烘干或冷却设备产能不足或发生故障。
⑥环境温度低和相对湿度高。
11.2 改进措施:①控制原料水分夏季12%~14%,冬季10%~12%。
②调质后水分控制在15%~17%,冬季取下线;控制调质温度,特别是冬季调质温度最好控制在80℃以上。
③提高蒸汽的饱和度。
④延长烘干或冷却时间。
⑤控制制粒机产量,使之与烘干机或冷却器产能相匹配。
⑥检查冷却风网是否有短路或堵塞显现;检查冷却器的布料和下料是否均匀。
⑦在冬季对冷却器进行保温或加蒸汽盘管加热冷却风。