蒸汽注塑技术的一些事儿
气辅注塑的缺陷及解决方法

气辅注塑的缺陷及解决方法一、引言气辅注塑是一种常用的塑料加工技术,通过注塑机将熔融的塑料材料注入模具中,利用注塑机的高压将塑料材料压实成型。
在这个过程中,气辅注塑存在一些缺陷,本文将重点讨论这些缺陷及其解决方法。
二、缺陷一:翘曲变形在气辅注塑过程中,塑料材料在注射模具中冷却固化,如果冷却速度不均匀或受到外力作用,就容易出现翘曲变形的情况。
这种翘曲变形不仅会影响产品的外观质量,还会导致产品尺寸不准确。
解决方法:1.优化模具设计,增加冷却系统,确保塑料材料能够均匀冷却,避免翘曲变形的发生。
2.调整注射工艺参数,控制注射温度和压力,使塑料材料充分流动,减少翘曲变形的可能性。
3.合理安排模具的开模顺序,避免产品在模具中停留时间过长,减少翘曲变形的机会。
三、缺陷二:气泡气辅注塑过程中,由于塑料材料的熔融状态和注射速度,有可能在产品内部产生气泡。
这些气泡不仅会影响产品的外观质量,还可能导致产品的强度下降。
解决方法:1.优化模具设计,增加通气孔,确保气体能够顺利排出,减少气泡的产生。
2.调整注射工艺参数,控制注射速度和压力,使塑料材料充分流动,减少气泡的形成。
3.采用真空辅助注塑技术,利用负压吸附气泡,确保产品的内部质量。
四、缺陷三:热缩变形在气辅注塑过程中,由于热胀冷缩的原理,塑料材料在冷却固化后会发生一定程度的热缩变形。
这种热缩变形不仅会影响产品的尺寸精度,还可能导致产品的装配困难。
解决方法:1.优化模具设计,增加冷却系统,加强对塑料材料的冷却,减少热缩变形。
2.调整注射工艺参数,控制注射温度和压力,使塑料材料充分流动,并在冷却过程中尽量减少热缩变形的发生。
3.采用后处理工艺,如热处理或压力调整,对产品进行形状稳定化处理,减少热缩变形的影响。
五、缺陷四:尺寸偏差在气辅注塑过程中,由于材料的收缩率和模具的磨损等因素,产品的尺寸往往会有一定的偏差。
这种尺寸偏差不仅会影响产品的装配性能,还可能导致产品无法正常工作。
注塑过程中常见的问题及解决方案

注塑过程中常见的问题及解决方案一、飞边(披锋)1. 问题描述- 这飞边就像塑料偷偷长出来的小翅膀,在注塑件的边缘或者分型面那里冒出来,看着可闹心了。
就像好好的一块蛋糕,边缘突然多出了一些不规则的奶油坨坨。
2. 解决方案- 首先得检查模具的合模力。
要是合模力不够,那塑料就会像调皮的小孩从门缝里挤出来。
适当增加合模力,把模具紧紧抱住,让塑料乖乖待在该待的地方。
- 模具的磨损也会导致飞边。
就像穿破了的鞋子会漏脚指头一样,磨损的模具缝隙变大了。
这时候就得修模啦,把那些磨损的地方补一补或者磨平。
- 注塑压力也不能太大。
如果压力太大,塑料就像被大力士猛推的水,到处乱流。
降低注塑压力,找到一个合适的值,既能把模具填满,又不会让塑料溢出来。
二、短射(缺料)1. 问题描述- 短射就像给一个杯子倒水,结果没倒满一样。
注塑件看着不完整,有些地方该有塑料的却空着,就像一个没发育好的小怪物。
2. 解决方案- 先看看注塑压力是不是太小。
压力小的话,塑料就像没力气的小蚂蚁,爬不到模具的每个角落。
增加注塑压力,让塑料充满整个模具型腔。
- 塑料的流动性也很关键。
如果塑料太黏,就像浓稠的糨糊,很难流到模具的远端。
这时候可以提高料筒温度,让塑料变得稀一点,流动性更好,就像把糨糊加热变成稀粥一样,能顺利流到各个地方。
- 浇口尺寸也可能有问题。
要是浇口太小,就像一个小得可怜的水龙头,水流不出来多少。
适当扩大浇口尺寸,让塑料能畅快地流进模具。
三、气泡(气穴)1. 问题描述2. 解决方案- 注塑速度可能太快了。
塑料像一阵风呼呼地冲进模具,把空气都裹在里面了。
降低注塑速度,让塑料慢慢流进去,就像散步一样,这样空气就有机会跑出来了。
- 模具的排气也很重要。
如果模具没有排气孔或者排气不良,空气就被困在里面出不来。
在模具上开排气槽或者使用透气钢材料,给空气一条逃跑的路。
- 塑料干燥不彻底也会产生气泡。
如果塑料里有水份,加热的时候就会变成水蒸气,形成气泡。
气辅注塑的缺陷及解决方法

气辅注塑的缺陷及解决方法气辅注塑是一种常见的注塑成型工艺,通过对塑料熔体进行喷射,并利用气体辅助实现产品成型。
然而,尽管这种工艺有许多优点,但也存在一些缺陷。
本文将探讨气辅注塑的缺陷,并提出相应的解决方法。
气辅注塑的主要缺陷之一是瓶颈效应。
由于气辅注塑需要在注射过程中注入气体,当气体进入熔体时,会导致熔体流动速度减慢,从而形成瓶颈效应。
这种效应会导致产品表面出现疤痕、气泡等缺陷。
为了解决瓶颈效应带来的缺陷,可以采取以下措施。
首先,可以通过增加注射压力来增加熔体的流动速度,从而减轻瓶颈效应。
其次,可以调整气体注入的位置和时间,使气体能够更均匀地分布在熔体中,减少瓶颈效应的影响。
气辅注塑还存在气泡缺陷。
气泡是由于气体在注射过程中进入熔体而形成的。
气泡的存在会降低产品的质量,并且可能会导致产品的强度下降。
为了解决气泡缺陷,可以采取以下方法。
首先,可以通过加热熔体来减少熔体的粘度,从而提高气泡的排出效果。
其次,可以通过调整注射速度和注射压力来控制气泡的生成,使气泡更容易从熔体中排出。
气辅注塑还存在产品变形的缺陷。
由于气辅注塑需要在注射过程中注入气体,而气体的注入会对产品造成一定的压力,从而导致产品的变形。
为了解决产品变形的缺陷,可以采取以下措施。
首先,可以通过调整注射温度和注射速度来控制熔体的流动,从而减少产品的变形。
其次,可以通过增加模具的支撑结构来增加产品的稳定性,减少变形的发生。
气辅注塑还存在产品尺寸不一致的缺陷。
由于气辅注塑过程中需要注入气体,而气体的注入会对产品的尺寸产生一定的影响,从而导致产品的尺寸不一致。
为了解决产品尺寸不一致的缺陷,可以采取以下方法。
首先,可以通过调整注射温度和注射速度来控制熔体的流动,从而减少产品尺寸的变化。
其次,可以通过优化模具的结构和设计,使产品的尺寸更加稳定。
气辅注塑虽然有一些缺陷,但通过相应的解决方法,这些缺陷是可以被克服的。
在实际生产中,我们可以根据具体情况采取不同的措施,从而提高气辅注塑的成型质量,满足客户的需求。
蒸汽模高光注塑技术(急冷急热模)-应用探讨课件

二、蒸汽模技术所涉及的设备
蒸汽模技术对注塑机没有特殊要求,一般的注塑机都能满足要求 2.1 蒸汽模具 蒸汽模具对塑件质量的影响主要包括: 模具材料、模具设计与制造等两方面。 1) 模具材料 模具材料需要有较好的抛光性、耐腐蚀性、耐磨性、热强度、韧性和低的热膨 胀系数等。其中,抛光性、耐腐蚀性、热强度、热膨胀系数对高光模具尤为重 要。如果模具抛光性差、表面粗糙度大,或被腐蚀或注塑时有水分沉积,就无 法进行高光泽制件成型;温度的快速变动对模具材料的热强度、热膨胀系数也 有更高的要求。 在蒸汽模技术中,注塑模具由于受长期的快速加热与冷却,且温度呈现周期性 变化,故模具材料在使用过程中很容易发生热疲劳失效,从而导致型腔表面出 现龟裂,无法保证制件的成型质量。为预防模具成型零部件的热疲劳失效过早 发生,必须研究蒸汽模技术中模具成型零部件材料的热疲劳性,并选择合适的 模具材料及热处理方法,从而保证模具的精度及使用寿命。
4)模具温度高,塑料熔体在模具型腔中的流动性好,因此,非常有利于薄壁 塑件( 可薄至0.5mm以下) 的注塑成型。
5)介质环保,可以实现回收。通过专门配置的加热与冷却设备,利用蒸汽作 为加热介质,利用冷却水作为冷却介质,使用完的冷却水可以实现回收利用, 非常环保。
五、蒸汽模成型的主要影响因素
5.1 塑料材料 蒸汽模技术适用于各种制件,但是并不是所有的塑料都可以采用该技术,一般 适用成型ABS、PS、PC、PMMA等大多数工程塑料,尤其适合成型添加玻璃 纤维的增强塑料。可根据生产需要选取适当的塑料品种,如在电视机行业,前 壳塑胶材料一般是HIPS和ABS。作为常用的两种机壳材料,尽管ABS的成本 会大一些,但成型出的制件在耐冲击性、表面光泽度以及硬度方面都HIPS好, 所以在生产高光制件时,通常选用ABS。
气体辅助注塑成型技术简介.
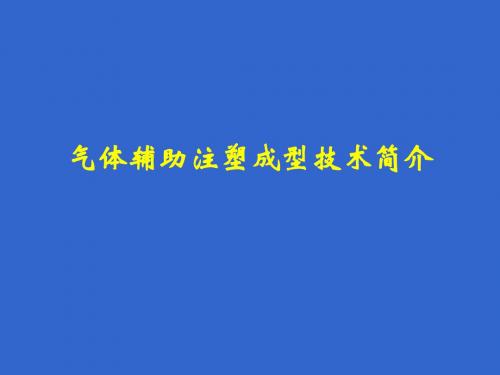
一、气体辅助注塑原理:
气体辅助注塑原理是把高压氮气经气辅 主控制器(分段压力控制系统)直接注射入 模腔内塑化塑料里,使塑件内部膨胀而造成 真空,但仍然保持产品表面的外形完整无缺, 减小产品表面的收缩、产品变形和翘曲,从 而达到提高产品的质量,降低成本的目的。
二、采用气体辅助注塑技术的优点:
应用气辅技术的国内公司:康佳、长虹、创维、科龙、 美的、海信等等;上海延锋伟世通、浙江远翅、上海龙贤汽 配、余姚塑料四厂、宁波国雅汽车内饰件厂以及各类注塑厂 都应用了气辅技术。
四、气体辅助注塑整系统的原理图:
A、整套系统
氮气 发生 器
低压 贮气缸
电动 高压 增压机
高压 贮气缸
气辅 主控 制器
单相电源 压缩空气 三相电源
六、气道形式:
• C、全部中空
七、我厂第一副气辅产品-前门拉手 (LZ111-6402101)
八、前门拉手采用气辅方案:
八、前门拉手采用气辅方案:
谢谢!
——END——
B、简易系统
氮气 缸瓶
气动 高压 增压机
压缩空气
单相电源
高压 贮气缸
气辅 主控 制器
单相——以定量塑化塑料充填入模腔内。所需塑料 份量要通过试验找出来,以保证在充氮期间,气体不 会把成品表面冲破及能有一理想的充氮体积。
2、充气期——注塑期中或后,不同时间注入气体,气体 注入的压力必需大于注塑压力,以达至产品成中空状 态。
模具的工作寿命; 7、降低注塑机的锁模压力,可高达50%; 8、提高注塑机的工作寿命和降低耗电量。
三、气体辅助注塑技术的应用:
基本上所有用于注塑的热塑性塑料及一般的工程材料 (如PS、HIPS、PP、ABS…)都适用于气辅技术。
高光蒸汽注塑模具技术

排气槽(红色) 集气槽(黄色)
排气孔
20~50mm
图12
料流末端的排气镶件(红色)
图13
高光蒸汽模具加工工艺特点
加工条件:
1、CNC加工:表面光洁度0.005mm以内。 2、孔加工:蒸汽孔偏摆度<=0.3‰,孔壁光滑,抵御急热急
冷,提高模具寿命。 3、配模:活动顺畅,较普通模具在热涨方向松配,太紧烧
死,太松披风。 4、抛光:关键要素---高光效果决定产品品质。
注塑机的要求:
温控设备要形成闭环,灵敏度高。 无尘车间生产,用专用保护膜包装保护。 熟悉高模注塑特点,熟悉调机缺陷解决思路。
高光模具后期保养
模具保养:清理排气槽+专用洗剂清洗型腔+专用防锈油。
综合:高模比普模高约20%~40%。
高光蒸汽注塑技术将会被广泛应用和迅速扩展,模具研发 具有广阔市场前景。
特点四:高温模具设计问题点解决。
中托边
I
中托边 采用青铜加石墨材料制做中托边和导套机构,有效防止模
具拖伤和保证开合模顺畅。
II
中间位置设计前后模定位机构,有效保证模具合模准确定 位,同时中间位置避免模具膨胀装配不顺畅情况。
III
设计可转式斜顶座结构,消除加工精度误差造 成装配上的影响,减少装配工作量。
• 高模具材料: 1、模具钢ቤተ መጻሕፍቲ ባይዱ:
S136、NAK80、LKM838H、LKM818H、 CENA#1 2、塑胶材料: PMMA/ABS、PC/ABS、高光ABS、HIPS
• 高模特点:配件耐热性。
1、高模加热和冷却 加长连接管直接进出,取消防水圈。见下页图片。
RHCM蒸汽注塑成型工艺及模具技术
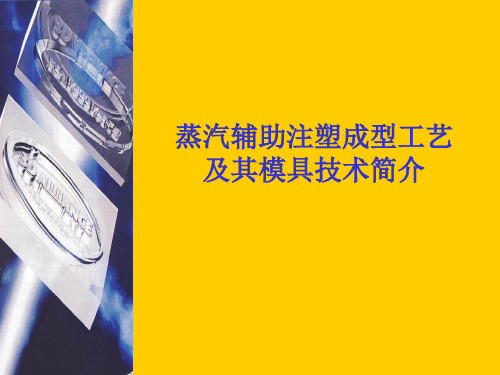
高速模具温度调节系统构成
控制器
[蒸汽加速]流量图
模具温度的调节程序
• 将模具的温度迅速调节到成型温度以上 (例:ABS:100-120℃)
• 达到温度(例:120℃)时,同时进行注射 充填
• 急速冷却模具,降低到制品取出温度(例: 60℃),开模取出制品
为什么溶接痕会消失
为什么银线纹会消失
为什么复原性Байду номын сангаас提高
应用范畴
• 汽车等厚外壳及外观零件 • 办公自动化设备、弱电、家电产品的外壳
或机壳 • 大型LCD用透光板、大口径塑性镜头等光
学仪器用的零件 • 簿壁的外壳注塑品 • 精密质量要求的注塑品
• 适用树脂
用途举例
注塑品样品
模具:样品模具(簿壳) 。 树脂名称:聚ABS(加20%的玻纤)。 模具温度:120℃=射出温度→80℃=冷却、 脱模温度。 注塑成形周期:40~50秒
有关迅速加热与冷却模具 设计基本要点
• 模具温调机之间配管、软管连接的注意 点
–软管软管的连接 注意压力损失
–单向连接器使用上的注意点
有关迅速加热与冷却模具 设计基本要点
• 模具温调机之间配管、软管连接的注意点
–根据冷却水管的连接方法不同冷却效率也不同
采用蒸汽加速器优点总结
• 大幅度提高外观品质,无需后续喷涂,可 以缩短成形周期。
• 采用了出类拔萃的抗老化性与可靠性高的 阀门和小型触摸式控制面板,可以有效集 中的控制成形的全行程。
• 适用于从小型到大型的注塑机及与之相对 应的模具。
系统设计组成
阀门控制单元 系统设计非常简单。控制整机的阀门控制单元,把送 进模具的升温与冷却介质连接在一起。和注塑机的连 动只是在成形开始或射出出现异常时才动作,不需要 进行大幅度地改造。
蒸汽模高光注塑技术(急冷急热模)-应用探讨

三、3.1蒸塑件汽结构模的技优化术设计中的关键技术
蒸汽模成型技术作为高光无熔痕成型技 术之一,其塑件的结构设计与普通塑件不同, 即需要根据高光无熔痕模具的成型特点对塑 件进行优化设计,如制件的脱模斜度、圆角 过渡、螺钉柱固定结构等都需要调整,以满 足高光无熔痕注塑成型的工艺要求。
三、3.2蒸成型汽过模程模技拟和术浇注中系统的优化关键技术
二、2.2蒸模具汽温度模控技制系术统 所涉及的设备
模具温度控制系统包括: 冷却塔、蒸汽锅炉、 压缩机、高光温度控制柜等生产设备。该温 度控制系统有时也可用高光蒸汽模温机代替。 高光温度控制柜是系统非常关键的一部分, 它根据模具上的温度传感器反馈的温度控制 着高温蒸汽和冷却水的切换,并与注塑机控 制系统实时互换信号,从而进行熔体的注射、 保压以及开模顶出动作,以完成整个注塑过 程!整个注塑成型。
前后的对比。 从图3(a)可以看出,制件在Z轴方向的变形比较严重,翘曲现象
明显。从图3(b)可以看出,在Moldflow软件进行优化以后,Z 轴方向设置术与优中化 的关键技术
由于蒸汽管道和冷却管道是共用的,因此正确设置管道尤 型技术对蒸汽管道的排布讲究合理性和有效性。合理的排 提高注塑效率,而且起到使塑件受热和冷却更加均匀,减 的作用。其设计原则是:根据塑件形状特征来设计模具的 的随形冷却管道,实现模腔内部熔体温度的动态控制,使 动达到最佳状态。
蒸汽高光注塑技术 应用探讨
蒸1汽模技术的基本原理 蒸2汽模技术所涉及的设备
目录 蒸3汽模技术中的关键技术
蒸4汽模技术的优势 蒸汽5 模成型的主要影响因素
一蒸、汽模蒸成型汽技术模的技成型术工艺的过程基是: 本原理
模具合模后,首先在加热冷却管道内通入高 温蒸汽,把模具温度提高到一个高的设定值, 然后注射塑料熔体,在保压转入冷却后,用 气压吹走通道内的残留蒸汽,开始注入冷水, 使模具温度快速下降到一个设定值,再向加 热冷却管道内通入空气,把冷水完全吹走, 开模取制件,然后进入下一次注塑循环。
注塑工艺注意事项及参数调整

注塑工艺注意事项及参数调整◆温度温度的测量和控制在注塑中是十分重要的。
虽然进行这些测量是相对简单的,但多数注塑机都没有足够的温度采点或线路。
在多数注塑机上,温度是由热电偶感应的。
一个热电偶基本上由两条不同的电线尾部相接而组成的。
如果一端比另一端热,将产生一个微小的电讯;越是加热,讯号越强。
◆温度的控制热电偶也广泛应用作温度控制系统的感应器。
在控制仪器上,设定需要的温度,而感应器的显示将与设定点上产生的温度相比较。
在这最简单的系统中,当温度到达设定点时,就会关闭,温度下降后电源又重新开启。
这种系统称为开闭控制,因为它不是开就是关。
注塑车间◆熔胶温度熔胶温度是很重要的,所用的射料缸温度只是指导性。
熔胶温度可在射嘴处量度或使用空气喷射法来量度。
射料缸的温度设定取决于熔胶温度、螺杆转速、背压、射料量和注塑周期。
您如果没有加工某一特定级别塑料的经验,请从最低的设定开始。
为了便于控制,射料缸分了区,但不是所有都设定为相同温度。
如果运作时间长或在高温下操作,请将第一区的温度设定为较低的数值,这将防止塑料过早熔化和分流。
注塑开始前,确保液压油、料斗封闭器、模具和射料缸都处于正确温度下。
◆注塑压力这是引起塑料流动的压力,可以用在射嘴或液压线上的传感器来测量。
它没有固定的数值,而模具填充越困难,注塑压力也增大,注塑线压力和注塑压力是有直接关系。
◆第一阶段压力和第二阶段压力在注塑周期的填充阶段中,可能需要采用高射压,以维持注塑速度于要求水平。
模具经填充后便不再需要高压力。
不过在注塑一些半结晶性热塑性塑料(如PA及POM)时,由于压力骤变,会使结构恶化,所以有时无须使用次阶段压力。
◆锁模压力为了对抗注射压力,必须使用锁模压力,不要自动地选择可供使用的最大数值,而要考虑投影面积,计算一个适合的数值。
注塑件的投影面积,是从锁模力的应用方向看到的最大面积。
对大多数注塑情况来说,它约为每平方英寸2吨,或每平方米31兆牛顿。
然而这只是个低数值,而且应当作为一个很粗略的经验值,因为,一旦注塑件有任何的深度,那么侧壁便必须考虑。
气辅注塑工艺的应用
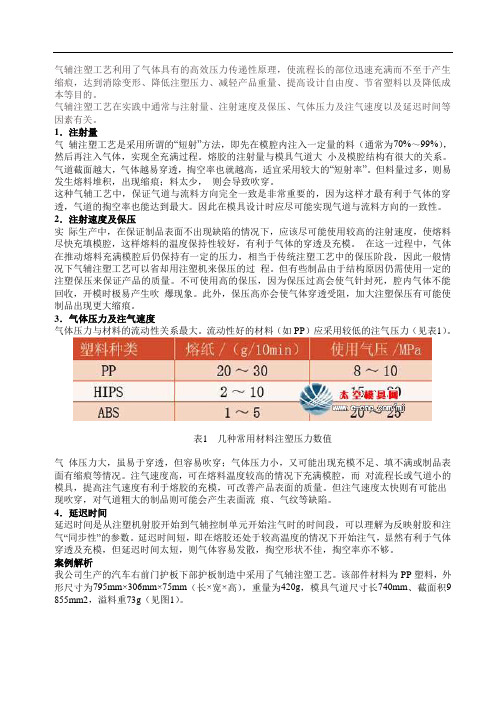
气辅注塑工艺利用了气体具有的高效压力传递性原理,使流程长的部位迅速充满而不至于产生缩痕,达到消除变形、降低注塑压力、减轻产品重量、提高设计自由度、节省塑料以及降低成本等目的。
气辅注塑工艺在实践中通常与注射量、注射速度及保压、气体压力及注气速度以及延迟时间等因素有关。
1.注射量气辅注塑工艺是采用所谓的“短射”方法,即先在模腔内注入一定量的料(通常为70%~99%),然后再注入气体,实现全充满过程。
熔胶的注射量与模具气道大小及模腔结构有很大的关系。
气道截面越大,气体越易穿透,掏空率也就越高,适宜采用较大的“短射率”。
但料量过多,则易发生熔料堆积,出现缩痕;料太少,则会导致吹穿。
这种气辅工艺中,保证气道与流料方向完全一致是非常重要的,因为这样才最有利于气体的穿透,气道的掏空率也能达到最大。
因此在模具设计时应尽可能实现气道与流料方向的一致性。
2.注射速度及保压实际生产中,在保证制品表面不出现缺陷的情况下,应该尽可能使用较高的注射速度,使熔料尽快充填模腔,这样熔料的温度保持性较好,有利于气体的穿透及充模。
在这一过程中,气体在推动熔料充满模腔后仍保持有一定的压力,相当于传统注塑工艺中的保压阶段,因此一般情况下气辅注塑工艺可以省却用注塑机来保压的过程。
但有些制品由于结构原因仍需使用一定的注塑保压来保证产品的质量。
不可使用高的保压,因为保压过高会使气针封死,腔内气体不能回收,开模时极易产生吹爆现象。
此外,保压高亦会使气体穿透受阻,加大注塑保压有可能使制品出现更大缩痕。
3.气体压力及注气速度气体压力与材料的流动性关系最大。
流动性好的材料(如PP)应采用较低的注气压力(见表1)。
表1 几种常用材料注塑压力数值气体压力大,虽易于穿透,但容易吹穿;气体压力小,又可能出现充模不足、填不满或制品表面有缩痕等情况。
注气速度高,可在熔料温度较高的情况下充满模腔,而对流程长或气道小的模具,提高注气速度有利于熔胶的充模,可改善产品表面的质量。
蒸汽模注塑成形技术的机理及应用研究

提高熔接痕区域的性能成为 当前研究 的重点与热点 。 蒸 汽模注 塑技术通 过精 确控 制蒸汽 和冷却水 在 注塑不 同阶段 的循 环进 出 , 实现 模具 的快 速 升温 和
降温 , 高 了塑 料熔体 在 型腔 中的流动性 , 提 提高 了制 品的注 塑 效 率 …。该 技 术 最 大 程 度 地 消 除 了 熔 接
痕问题 , 些 年 来 , 于大 型 复杂 制 品 的逐 渐 增 多 , 近 由 以及 人 们 对 制 品 外 观 和 内 在 性 能 的 要 求 越 来 越 高 , 对 注 塑 件 熔 接 痕 的分 析 受 到 普 遍 的 关 注 。 因此 , 何 如
1 蒸 汽 模 注 塑 成 形技 术 的机 理
精 密注塑成 形一般 是指成 形制 品的精 度和表 面 质量均要 求很 高 的工 艺 , 而 , 然 由于 成 形材 料 、 形 成 工艺 、 模具设 计 、 品设 计 及设 备 等 因 素 的影 响 , 制 注 塑成 形制 品经常 出 现各 种 难 以避 免 的 表观 缺 陷 , 如 熔 接痕 、 表面粗糙 度值 大 、 曲变形 等 。尤其是熔 接 翘
模冷却 , 使模 具型 腔 表 面 的温 度 出现 升 高 和下 降 的
变化 。为使模 具 温度 稳 定 应注 意 以下 方 面 : 先模 首
(Gu n z o HOM ce c a g h u EC S in e& Te h oo yC ,L d Gu n z o 1 6 3, ia) c n lg o. t , a g h u 5 0 6 Chn
Ab ta t sr c :T h s p p r a ay e e t a d ma s t a s e e h n s o h t a — sபைடு நூலகம்it d h a i i a e n ls s h a n s r n f r m c a im f t e se m a sse e tng m od p o c in a d t e ef c ft e p r t r n t e m od n o e s o m p r d t i e t c n l l r du to n h fe to het m e a u eo h li g pr c s .C a e h sn w e h o — o t h r d to a o dng t c n lgy, i s o st a h sne tc n lgy i s f lt l i a e gy wih t e t a iin lm l i e h o o t h w h tt i w e h o o s u e u o ei n t m
最新气辅注塑成型技术介绍
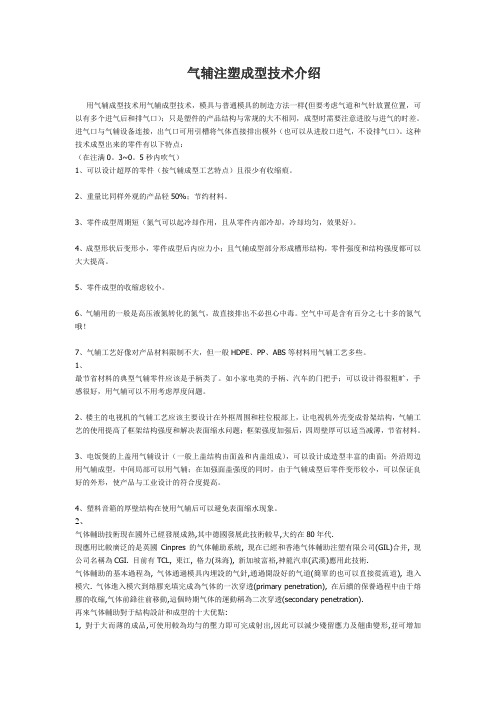
气辅注塑成型技术介绍用气辅成型技术用气辅成型技术,模具与普通模具的制造方法一样(但要考虑气道和气针放置位置,可以有多个进气后和排气口);只是塑件的产品结构与常规的大不相同,成型时需要注意进胶与进气的时差。
进气口与气辅设备连接,出气口可用引槽将气体直接排出模外(也可以从进胶口进气,不设排气口)。
这种技术成型出来的零件有以下特点:(在注满0。
3~0。
5秒内吹气)1、可以设计超厚的零件(按气辅成型工艺特点)且很少有收缩痕。
2、重量比同样外观的产品轻50%;节约材料。
3、零件成型周期短(氮气可以起冷却作用,且从零件内部冷却,冷却均匀,效果好)。
4、成型形状后变形小,零件成型后内应力小;且气辅成型部分形成槽形结构,零件强度和结构强度都可以大大提高。
5、零件成型的收缩虑较小。
6、气辅用的一般是高压液氮转化的氮气,故直接排出不必担心中毒。
空气中可是含有百分之七十多的氮气哦!7、气辅工艺好像对产品材料限制不大,但一般HDPE、PP、ABS等材料用气辅工艺多些。
1、最节省材料的典型气辅零件应该是手柄类了。
如小家电类的手柄、汽车的门把手;可以设计得很粗旷,手感很好,用气辅可以不用考虑厚度问题。
2、楼主的电视机的气辅工艺应该主要设计在外框周围和柱位根部上,让电视机外壳变成骨架结构,气辅工艺的使用提高了框架结构强度和解决表面缩水问题;框架强度加强后,四周壁厚可以适当减薄,节省材料。
3、电饭煲的上盖用气辅设计(一般上盖结构由面盖和内盖组成),可以设计成造型丰富的曲面;外沿周边用气辅成型,中间局部可以用气辅;在加强面盖强度的同时,由于气辅成型后零件变形较小,可以保证良好的外形,使产品与工业设计的符合度提高。
4、塑料音箱的厚壁结构在使用气辅后可以避免表面缩水现象。
2、气体輔助技術現在國外已經發展成熟,其中德國發展此技術較早,大約在80年代.現應用比較廣泛的是英國Cinpres的气体輔助系統, 現在已經和香港气体輔助注塑有限公司(GIL)合并, 現公司名稱為CGI. 目前有TCL, 東江, 格力(珠海), 新加坡富裕,神龍汽車(武漢)應用此技術.气体輔助的基本過程為, 气体通過模具內埋設的气針,通過開設好的气道(簡單的也可以直接從流道), 進入模穴. 气体進入模穴到熔膠充填完成為气体的一次穿透(primary penetration), 在后續的保養過程中由于熔膠的收縮,气体前鋒往前移動,這個時期气体的運動稱為二次穿透(secondary penetration).再來气体輔助對于結构設計和成型的十大优點:1, 對于大而薄的成品,可使用較為均勻的壓力即可完成射出,因此可以減少殘留應力及翹曲變形,並可增加机械強度.3、2,成品肉厚減少,可以節約成本(老板笑了)3,可以減少肋骨可輪轂的收縮凹陷,改進成品表面的品質(品管笑了)4,可以降低樹脂的收縮率,提高成品的精密度.5,大量減少鎖模力,可用小頓位取代大吨位(老板又笑了).6,利用气体管道的設計來加強成品的結构強度(需要努力學習和交流哦)7,減少流道數目,節省塑料的使用.8,縮短成型周期.9,改變我們傳統的設計觀念及限制可以使用的成品厚薄比(觀念重要哦).10,改變傳統設計觀念使各附加零件盡可能設計一体化.從前几個月看到實際的東西,發現這個東西不好做,塑膠机徬邊有一大堆不良品,主要是气体把壁吹破了,這是我個人收集的一些資料和觀點要討論气体輔助分析的可以到moldflow 版哦.∙气辅注塑成型技术介绍∙一、前言气辅注塑工艺是国外八十年代研究成功,九十年代才得到实际应用的一项实用型注塑新工艺,其原理是利用高压隋性气体注射到熔融的塑料中形成真空截面并推动熔料前进,实现注射、保压、冷却等过程。
气辅注塑原理

气辅注塑原理气辅注塑是一种新型的注塑技术,它是在传统注塑技术的基础上发展而来的。
它采用了气体辅助注塑的原理,通过在注塑过程中注入气体,使得塑料材料在注塑过程中得到更好的填充和冷却,从而提高了注塑产品的质量和生产效率。
气辅注塑的原理是在注塑过程中,通过在模具中注入气体,使得塑料材料在注塑过程中得到更好的填充和冷却。
在注塑过程中,塑料材料会受到很大的压力,这会导致塑料材料在注塑过程中出现缩孔、气泡等缺陷。
而气辅注塑技术可以通过注入气体的方式,使得塑料材料在注塑过程中得到更好的填充和冷却,从而避免了这些缺陷的产生。
气辅注塑技术的优点在于可以提高注塑产品的质量和生产效率。
在传统注塑技术中,塑料材料在注塑过程中往往会出现缩孔、气泡等缺陷,这会导致注塑产品的质量下降。
而气辅注塑技术可以通过注入气体的方式,使得塑料材料在注塑过程中得到更好的填充和冷却,从而避免了这些缺陷的产生。
同时,气辅注塑技术还可以提高注塑产品的生产效率,因为它可以使得塑料材料在注塑过程中更加均匀地填充模具,从而减少了注塑周期和注塑成本。
气辅注塑技术的应用范围非常广泛,它可以用于生产各种塑料制品,如塑料零件、塑料容器、塑料管道等。
在汽车、电子、医疗、家电等行业中,气辅注塑技术已经得到了广泛的应用。
在汽车行业中,气辅注塑技术可以用于生产汽车零部件,如仪表板、门板、座椅等。
在电子行业中,气辅注塑技术可以用于生产电子产品外壳、键盘、鼠标等。
在医疗行业中,气辅注塑技术可以用于生产医疗器械、医疗用品等。
在家电行业中,气辅注塑技术可以用于生产电视机外壳、空调外壳、洗衣机外壳等。
气辅注塑技术是一种非常有前途的注塑技术,它可以提高注塑产品的质量和生产效率,同时还可以应用于各种行业中。
随着科技的不断发展,气辅注塑技术将会得到更加广泛的应用,为各行各业的发展带来更多的机遇和挑战。
蒸汽辅助注塑模具介绍
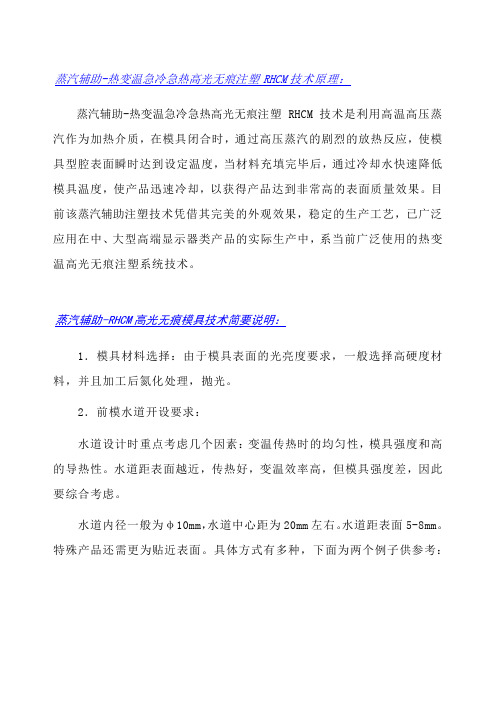
蒸汽辅助-热变温急冷急热高光无痕注塑RHCM技术原理:
蒸汽辅助-热变温急冷急热高光无痕注塑RHCM技术是利用高温高压蒸汽作为加热介质,在模具闭合时,通过高压蒸汽的剧烈的放热反应,使模具型腔表面瞬时达到设定温度,当材料充填完毕后,通过冷却水快速降低模具温度,使产品迅速冷却,以获得产品达到非常高的表面质量效果。
目前该蒸汽辅助注塑技术凭借其完美的外观效果,稳定的生产工艺,已广泛应用在中、大型高端显示器类产品的实际生产中,系当前广泛使用的热变温高光无痕注塑系统技术。
蒸汽辅助-RHCM高光无痕模具技术简要说明:
1.模具材料选择:由于模具表面的光亮度要求,一般选择高硬度材料,并且加工后氮化处理,抛光。
2.前模水道开设要求:
水道设计时重点考虑几个因素:变温传热时的均匀性,模具强度和高的导热性。
水道距表面越近,传热好,变温效率高,但模具强度差,因此要综合考虑。
水道内径一般为φ10mm,水道中心距为20mm左右。
水道距表面5-8mm。
特殊产品还需更为贴近表面。
具体方式有多种,下面为两个例子供参考:
1
3.热电隅埋设要点:可根据模具大小,在每边埋设1-2个热电隅(一般为K 型,实际参与控制的热电隅只有一个,其余测温只为观察)。
埋设点一般距模具表面3-5mm,热电隅孔垂直于水道,埋设时一定要确保电隅探测点与模具紧密接触,热电隅测出的温度主要用于工艺参考,
相对值的重要性大于绝对值(很多工厂实际生产时,当工艺稳定后,不用温度控制,而直接用动作时间周期来控制。
见下图:
4.模具后模:一般后模用油温机保持恒温50-600C。
气体辅助注塑成型工艺(试模知识2)

气体辅助注塑有改善外观、节约材料、缩短周期、减低内应力等优点。
但是由於气辅工艺发展的时间不长,在调试中气体不易控制,加上许多初次接触的工艺人员经验不足,常常会造成生产中废品增多。
本文着重说明气体辅助成型工艺、结构特点及成型缺陷的应对措施。
工艺原理气辅成型(GIM)是指在塑胶充填到型腔适当的时候(90%~99%)注入高压惰性气体,气体推动熔融塑胶继续充填满型腔,用气体保压来代替塑胶保压过程的一种新兴的注塑成型技术。
它是将熔融的树脂通过高压,高速注入型腔,再把高压气体引入到制件的壁厚部位,产生中空截面,驱动熔体完成充填过程并进行保压在气辅成型工艺调试时,需要注意以下因素:1. 对於气针式面板模具来讲,气针处压入放气时,最容易产生进气不平衡,造成调试更加困难。
其主要现象为缩水。
解决方法为放气时检查气体流畅性。
2. 胶料的温度是影响生产正常进行的关键因素之一。
气辅产品的质量对胶料温度更加敏感。
射嘴料温过高会造成产品料花、烧焦等现象;料温过低会造成冷胶、冷嘴,封堵气针等现象。
产品反映出的现象主要是缩水和料花。
解决方法为检查胶料的温度是否合理。
3. 手动状态下检查封针式射嘴回料时是否有溢料现象。
如有此现象则说明气辅封针未能将射嘴封住。
注气时,高压气体会倒流入料管。
主要现象为水口位大面积烧焦和料花,并且回料时间大幅度减少,打开封针时会有气体排出。
主要解决方法为调整封针拉杆的长短。
4. 检查气辅感应开关是否灵敏,否则会造成不必要的损失。
5. 气辅产品是靠气体保压,产品缩水时可适当减胶。
主要是降低产品内部的压力和空间,让气体更容易穿刺到胶位厚的地方来补压。
气辅成型优点1. 减少残余应力、降低翘曲问题。
传统注塑成型,需要足够的高压以推动塑料由主流道至最外围区域;此高压会造成高流动剪应力,残存应力则会造成产品变形。
GIM中形成中空气体流通管理(Gas Channel)则能有效传递压力,降低内应力,以便减少成品发生翘曲的问题。
气体辅助注塑成型技术研究

气体辅助注塑成型技术研究气体辅助注塑成型技术是近年来发展起来的一项新型注塑成型技术。
与传统注塑成型技术相比,其最大的优点是可以在注塑过程中控制气体压力,从而在塑料制件中形成中空区域或类似泡沫的结构,改善制件的物理性能和外观质量。
气体辅助注塑成型技术的基本原理是在注塑射出过程中,通过向塑料中注入惰性气体(如氮气、空气)来改变塑料的结构和性质。
在注塑成型过程中,首先将塑料材料加热至熔融状态,然后将熔融塑料通过射出装置注入模具中形成塑料制件。
在这个过程中,通过向塑料中注入气体来影响塑料的形态和性质,从而得到具有更好物理性能和外观质量的塑料制件。
具体来说,气体辅助注塑成型技术主要分为两种形式:一种是在注塑成型过程中向塑料中注入惰性气体,如氮气、空气等,以形成中空区域或类似泡沫的结构;另一种是在注塑成型过程中通过向模腔中加压气体来控制塑料的形态和性质。
气体辅助注塑成型技术的应用范围非常广泛,其中最典型的应用就是制造汽车零部件。
比如,汽车中的仪表盘、门板、车顶、挡风玻璃支架等都可以通过气体辅助注塑成型技术来制造。
此外,气体辅助注塑成型技术还可以应用于家具、电子产品、医疗器械等领域。
气体辅助注塑成型技术相对于传统注塑成型技术的优点主要有以下几个方面:首先,可以大大降低制造成本。
在传统注塑成型过程中,由于塑料结构设计的限制,往往需要采用更大的注塑机和更多的材料,从而带来更高的制造成本。
而在气体辅助注塑成型技术中,通过控制气体压力,可以有效减小制品的体积和重量,降低成本。
其次,可以提高制品的质量。
在气体辅助注塑成型过程中,通过向塑料中注入惰性气体可以形成中空区域或类似泡沫的结构,从而使得制品具有更好的物理性能和外观质量。
比如,汽车零部件可以通过气体辅助注塑成型技术来制造,可以使得这些零部件更轻、更坚固,有效提高车辆整体性能。
最后,气体辅助注塑成型技术还可以提高生产效率。
由于气体辅助注塑成型技术可以使得制品更容易脱模,同时生产过程也更加稳定,从而大大提高生产效率和制品质量。
气体辅助注塑成型简介
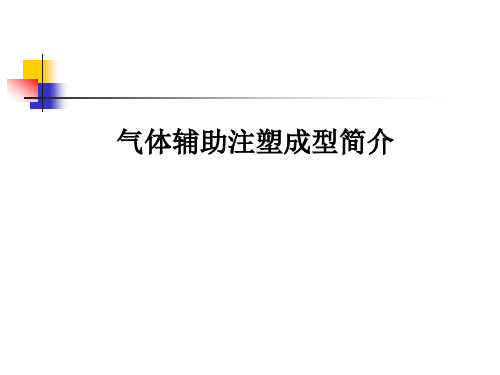
1.什么是气体辅助注射成型?
气体辅助注塑成型其原理是利用高压气体在塑件内部产生中空截面,利用 气体保压代替塑料注射保压,消除制品缩痕,完成注射成型过程。 气体辅助注塑成型的工艺过程主要包括塑料熔体注射、气体注射、气体保 压三个阶段。气体辅助注射成型过程首先是向模腔内进行树脂的欠料注射,然后 把经过高压压缩的氮气导入熔融物料当中,气体沿着阻力最小方向流向制品的低 压和高温区域。当气体在制品中流动时,它通过置换熔融物料而掏空厚壁截面。 这些置换出来的物料充填制品的其余部分。当填充过程完成以后,由气体继续提 供保压压相比,气体辅助注塑成型有更多的工艺参数需要确 定和控制,因而对于制品设计、模具设计和成型过程的控制都有特殊的要求。
5. 气辅成型常见问题及对策
⑹气道与薄壁连接处缩凹 气道由于气体穿透,导致气道与薄壁接触部分壁厚较大,解决方法: 1.在气道与薄壁接触位置增设防缩槽 2.气道与薄壁连接处尽量不采用圆角过渡 3.尽量增大气道表面积,以利于迅速冷却 ⑺气体穿透不均 原因: 1.熔体流动不平衡 2.气道布局不合理 3.模具精度差,导致塑件壁厚不均 解决方法: 1.修改浇口布局 2.修改气道布局 3.提高模具制造精度
2.气体辅助注射成型有什么优点?
(1)解决制件表面缩痕问题,能够大大提高制件的表面质量。 (2)局部加气道增厚可增加制件的强度和尺寸稳定性,并降低制品内应力,减 少翘曲变形。 (3)节约原材料,最大可达40%~50%。
(4)简化制品和模具设计,降低模具加工难度。
(5)降低模腔压力,减小锁模力,延长模具寿命。 (6)冷却加快,生产周期缩短。
5. 气辅成型常见问题及对策
⑴制件表面银纹(streak) 浇口处料流速度过快,剪切速率过大 修改浇口类型,或者增大浇口尺寸,减小料流速度
- 1、下载文档前请自行甄别文档内容的完整性,平台不提供额外的编辑、内容补充、找答案等附加服务。
- 2、"仅部分预览"的文档,不可在线预览部分如存在完整性等问题,可反馈申请退款(可完整预览的文档不适用该条件!)。
- 3、如文档侵犯您的权益,请联系客服反馈,我们会尽快为您处理(人工客服工作时间:9:00-18:30)。
蒸汽注塑技术的一些事儿
如何生产出无熔痕、无流痕、无流线、无缩痕,表面高光的外壳产品,对于平板电视机、电脑液晶显示器、空调、汽车内饰件来说尤为重要。
使用高光注塑技术就可以很好地解决此问题。
高光注塑的工艺原理
在合模前及合模过程中对模具进行加温、合模完成后,温度达到设定条件即进行注射。
注射过程中模具继续维持高温,这样可以使胶料注射时在模具内保持很好的流动性。
注射完成,在保压冷却时,则对模具进行降温处理,又可以大大缩短制品的冷却时间,从而提高生产效率。
蒸汽无痕高光注塑
技术目前在国内尚属于一项先进的生产工艺。
由于这一技术大大改善了制品的表面质量和表面强度,并可取消后续的喷涂或喷漆等工艺、既保护了环境和操作人员的人身健康,又因减少工艺流程,省去了昂贵的二次加工费用,在大幅度降低生产成本的同时,节省能源与材料。
传统工艺
传统的做法是采用模温机对模具进行加温,但这种方法的不足之处如下:
①无法满足高光注塑中快速升温及快速降温的需要;
②升温幅度较小,制品表面的熔接痕只能得到减轻而无法消除;
③由于塑料硬度越高,流动性越差。
因此采用此种工艺制品表面的
硬度只能达到HB级无法满足实际使用需要;
④模具升温时受热膨胀,降温时又会收缩,使锁模力很不稳定。
容易造成制品打不满,烧焦,内应力大等各种缺陷。
高光注塑技术
在传统工艺基础上发展而来的蒸汽高光注塑技术则针对以上缺陷分别做了改进:
①此技术在模具中开水管,需要升温时通蒸汽,需要降温时通冷水,冷却完毕后则用压缩空气将残留水分吹出,以确保能实现快速升温、降温;
②以最大程度地消除熔接痕夹、水纹缺胶等各种制品故障;
③由于升温幅度较大,宜使用H甚至2H硬度级别的塑料,使制品表面硬度大大提高;
④由于在模具内部开设管道时,只对模具内表面进行升温或降温,模具的整体膨胀较小,因此减少了由于锁模力的不稳定而带来的各种制品缺陷。