国外电火花加工最新技术
EDM电火花加工与CNC切削加工之比较

EDM电火花加工与CNC切削加工之比较电火花技术与模具论坛航天电火花技术| 模具电火花加工| 技术论文投稿 | 广告发布 | 企业宣传视频电火花加工是利用浸在工作液中的两极间脉冲放电时产生的电蚀作用蚀除导电材料的特种加工方法,又称放电加工或电蚀加工,英文简称EDM。
技术以其高效率、高质量应用于航天、航空、汽车、模具和机床等行业中,尤其针对飞机薄壁零件及各种复杂的型面模具零件加工。
一. 电火花加工电火花加工是利用浸在工作液中的两极间脉冲放电时产生的电蚀作用蚀除导电材料的特种加工方法,又称放电加工或电蚀加工(英文简称EDM)。
1943年,苏联学者拉扎连科夫妇研究发明电火花加工,之后随着脉冲电源和控制系统的改进,而迅速发展起来。
最初使用的脉冲电源是简单的电阻-电容回路。
电火花加工能加工普通切削加工方法难以切削的材料和复杂形状的型孔和型腔的模具和零件:①加工各种硬、脆材料,如硬质合金和淬火钢等。
②加工深细孔、异形孔、深槽、窄缝和切割薄片等,如各类热锻模、压铸模、挤压模、塑料模和胶木膜等模具。
1. 电火花加工包括电极的制作和EDM放电加工。
(1)电极的制作电极制作主要采用三轴数控机床来加工,机床稳定性要好,三轴运动要均匀稳定不振动,主轴回转精度也要好。
可在同一台机床上进行电极的粗加工、半精加工和精加工。
石墨与紫铜电极在CNC加工的特点:①石墨电极加工性能好,易于加工各种复杂的形状,切削阻力为铜的1/5,加工效率为铜的两倍,且其强度很高,耐高温,热膨胀率极小,对于超高(50~90mm)、超薄(0.2~0.5mm)的电极,加工时不易变形。
②比重轻,比重为铜的1/5,常用于重、大及整体电极加工。
③石墨对刀具的磨损较为严重,加工时产生的灰尘比较大,可能入侵到机床的导轨丝杠和主轴等,这就要求石墨加工机床有相应的处理石墨灰尘的装置,机床密封性也要好,因为石墨有毒。
(2)电火花加工特点①电火花加工速度与表面质量:模具在电火花机加工一般会采用粗、中、精分档加工方式。
电火花新加工技术及其发展趋势
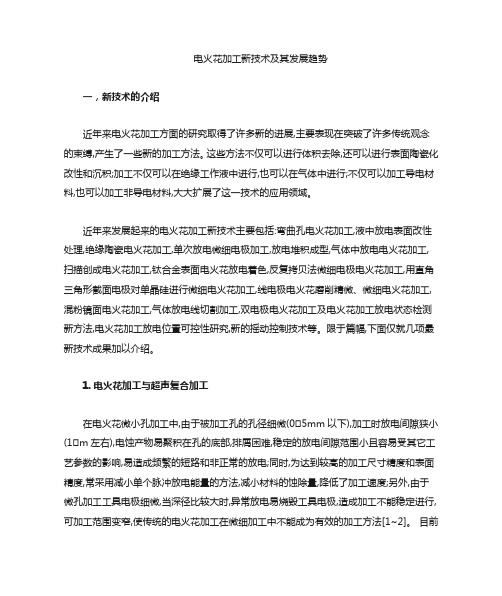
电火花加工新技术及其发展趋势一,新技术的介绍近年来电火花加工方面的研究取得了许多新的进展,主要表现在突破了许多传统观念的束缚,产生了一些新的加工方法。
这些方法不仅可以进行体积去除,还可以进行表面陶瓷化改性和沉积;加工不仅可以在绝缘工作液中进行,也可以在气体中进行;不仅可以加工导电材料,也可以加工非导电材料,大大扩展了这一技术的应用领域。
近年来发展起来的电火花加工新技术主要包括:弯曲孔电火花加工,液中放电表面改性处理,绝缘陶瓷电火花加工,单次放电微细电极加工,放电堆积成型,气体中放电电火花加工,扫描创成电火花加工,钛合金表面电火花放电着色,反复拷贝法微细电极电火花加工,用直角三角形截面电极对单晶硅进行微细电火花加工,线电极电火花磨削精微、微细电火花加工,混粉镜面电火花加工,气体放电线切割加工,双电极电火花加工及电火花加工放电状态检测新方法,电火花加工放电位置可控性研究,新的摇动控制技术等。
限于篇幅,下面仅就几项最新技术成果加以介绍。
1.电火花加工与超声复合加工在电火花微小孔加工中,由于被加工孔的孔径细微(0 5mm以下),加工时放电间隙狭小(1 m左右),电蚀产物易聚积在孔的底部,排屑困难,稳定的放电间隙范围小且容易受其它工艺参数的影响,易造成频繁的短路和非正常的放电;同时,为达到较高的加工尺寸精度和表面精度,常采用减小单个脉冲放电能量的方法,减小材料的蚀除量,降低了加工速度;另外,由于微孔加工工具电极细微,当深径比较大时,异常放电易烧毁工具电极,造成加工不能稳定进行,可加工范围变窄,使传统的电火花加工在微细加工中不能成为有效的加工方法[1~2]。
目前常采用的提高电火花加工能力的方法,如人工排气法,强迫冲液或抽液法、加速工作液循环等方法,常因加工条件或加工要求的限制而无法实现。
因此,为改善电火花加工性能,在微细加工中,采用超声电火花复合加工是非常有效的手段。
在电极上附加超声振动,就可以使电极端面频繁进入合适的放电间隙,提高火花击穿的概率;同时由于超声的空化作用和泵吸作用,可以增大被加工材料的去除量,加速工作液循环,改善间隙放电条件,从而提高被加工孔的深径比、加工稳定性、生产率和脉冲电源的利用率,并且在振幅得到良好控制的情况下,可以获得更高的加工精度。
电火花(EDM)放电加

电火花加工的基本系统
东江集团内部培训教材
电源向电极/工件系统提供直流脉冲。脉宽、 间歇、电压和电流值均由手工设置。电火花机 启动后,伺服微处理器若检测到放电间隙太大, 无法进行电蚀,它将[通知]伺服机制降低主轴 头。 一旦火花产生,主轴头的下降运动就停止。 这时,若火花间隙固定不变,电火花就不断蚀 除工件表面。当蚀除的金属达到一定的程度, 火花间隙变大时,微处理器也能检测到这一情 况,并[通知]伺服机制降低主轴头达到设置的 间隙,继续进行电火花加工。
东江集团内部培训教材
到了20世纪90年代,计算机控制系统能够 对所有的加工参数进行控制。它可以自动调节 电流强度、脉宽、间歇、伺服系统和其他设置, 从而提高加工效率。同时,在精加工回路和平 动加工控制方面也有了很大的进步。多轴向加 工及电极或工件的移位和旋转均可以实现程序 控制。
东江集团内部培训教材
右图:九张图片逐步显示了 单个电火花加工周期中发生 的情况,说明了热电模型形 成的过程。
东江集团内部培训教材
图解1:电压开始上升,带电电极慢慢靠近工件。 电极与工件之间是绝缘油,即电火花加工中的介 质油(火花油)。
东江集团内部培训教材
众所周知,火花油(介质油)是良好的绝缘物, 但是电压足够大时可以使它分解成带电离子,因此, 在产生电火花前的高压空载电压设定越高,就越容 易分解电离子 。悬浮在火花油中的石墨微粒和金属 微粒有助于电流的传导,这些微粒能够参与火花油 的电离,直接携带电流,还可以促进火花油被电离 击穿,随着带电离子的增多,火花油绝缘能力开始 下降。
电火花加工的历程
东江集团内部培训教材
• 电火花加工对传统加工的挑战
平动头、线切割加工、数控(CNC)加工, 旋转主轴、自动换刀和自适应系统等技术代表 了电火花加工从原先的 [巫术]转变为广为接受、 发展迅速的技术。这些改革使电火花加工机操 作简便,精确度增加,表面光洁度得以改善。 尽管在速度方面,它无法同传统的铣削、研磨 媲美,但已经有了极大的提高。电火花加工的 魅力还在于它可以实现无人管理操作。
电火花EDM加工原理介绍
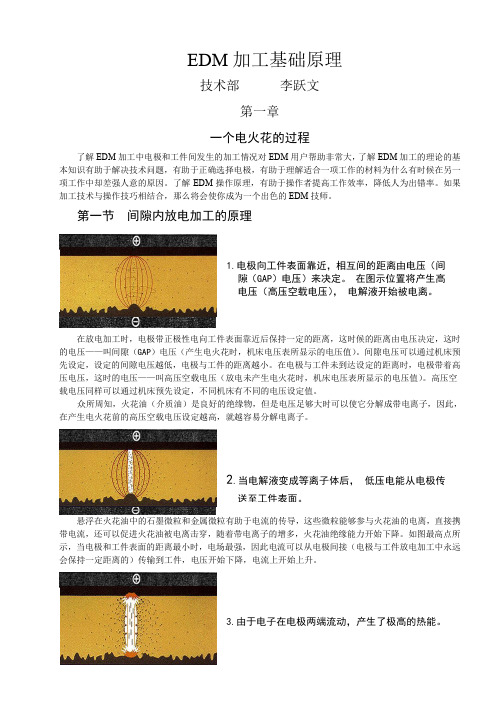
3.由于电子在电极两端流动,产生了极高的热能。
随着电流的上升增加,热量快速积聚,使部分火花油、工件和电极气化,形成放电通道,而产生电火 花。
4.随着电流流过电极 ,在电化学反应的作用下,产 生一个氢气泡。
随着不断的电流流过电极,热量不断上升,一个气泡试图向外膨胀,但由于离子受到强烈的电磁场作 用,不断冲向放电通道,这股冲力抑制了气泡的膨胀。此时,电流不断增加,电压继续下降。
此时新的火花(介质)油涌入型腔,冲走杂质,冷却工件和电极表面。在这时候,若没有足够的火花 油及油压把抛离出来的熔融金属冲走,重铸层变厚,蚀除量降低。但是大压力的冲油,又会把电极表面来 不及冷却的熔融层冲走,使电极损耗增大。熔点低的电极材料熔融层更厚,被冲走的会更多,所以当铜和 石墨做电极时,铜电极冲油过大会增加损耗就是这个原理,石墨的结构颗粒度比铜大及熔点比铜高,冲油 压力要比铜更大,排除杂物更好而不会增加损耗。
加工表面连成一片的蚀坑峰谷可用光洁度测量仪测定,通常用峰谷间算术平均值表示,单位是(μm Ra)。
第四节 工件材料
电火花加工时改变的不仅是工件表面,还有它的次表面。加工后的工件表面结构分为三层(图 1-3)。 电火花加工表面冲击层是由被抛出的熔融金属和少量电极微粒冲击而成。这一层很容易去除。 下一层是硬质层(氧化层)。电火花加工实质上改变了硬质层的冶金结构和特性。在介质油的作用下, 熔融金属迅速冷却,未被抛出去的熔融金属就凝固在型腔中形成了硬质层。这层硬而脆的氧化层会出现显 微裂纹。如果这一层太厚,或者通过抛光无法变薄或去除,那么这块工件可能在有些使用条件下过早损坏。 最后一层是受热层或退火层。它只是受热,并没有熔化。硬质层和受热层的厚度由工件材料的散热能 力和加工能量决定。不管如何,改变的金属层都会影响工件表面原来的属性。 数控电火花机床上的自动精加工电路能够有效减少硬质层的形成,但仍然无法消除退火层。
电火花加工的实例
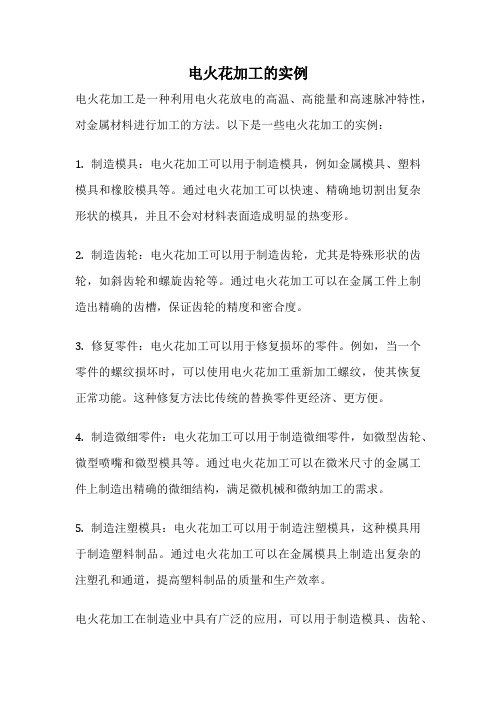
电火花加工的实例
电火花加工是一种利用电火花放电的高温、高能量和高速脉冲特性,对金属材料进行加工的方法。
以下是一些电火花加工的实例:
1. 制造模具:电火花加工可以用于制造模具,例如金属模具、塑料模具和橡胶模具等。
通过电火花加工可以快速、精确地切割出复杂形状的模具,并且不会对材料表面造成明显的热变形。
2. 制造齿轮:电火花加工可以用于制造齿轮,尤其是特殊形状的齿轮,如斜齿轮和螺旋齿轮等。
通过电火花加工可以在金属工件上制造出精确的齿槽,保证齿轮的精度和密合度。
3. 修复零件:电火花加工可以用于修复损坏的零件。
例如,当一个零件的螺纹损坏时,可以使用电火花加工重新加工螺纹,使其恢复正常功能。
这种修复方法比传统的替换零件更经济、更方便。
4. 制造微细零件:电火花加工可以用于制造微细零件,如微型齿轮、微型喷嘴和微型模具等。
通过电火花加工可以在微米尺寸的金属工件上制造出精确的微细结构,满足微机械和微纳加工的需求。
5. 制造注塑模具:电火花加工可以用于制造注塑模具,这种模具用于制造塑料制品。
通过电火花加工可以在金属模具上制造出复杂的注塑孔和通道,提高塑料制品的质量和生产效率。
电火花加工在制造业中具有广泛的应用,可以用于制造模具、齿轮、
微细零件和修复零件等,为工业生产提供了高效、精确和可靠的加工方法。
模具现代制造技术

镜面模具材料不单是化学成分问题,更主要的是冶炼时要求采用真空脱气、氩气保护铸锭、垂直连铸连轧、柔锻等一系列先进工艺,使镜面模具钢具内部缺陷少、杂质粒度细、弥散程度高、金属晶粒度细、均匀度好等一系列优点,以达到抛光至镜面的模具钢的要求。
三、新一代模具CAD/CAM软件技术
目前,英、美、德等国及我国一些高等院校和科研院所开发的模具软件,具有新一代模具CAD/CAM软件的智能化、集成化、模具可制造性评价等特点 。
新一代模具软件应建立在从模具设计实践中归纳总结出的大量知识上。这些知识经过了系统化和科学化的整理,以特定的形式存储在工程知识库中并能方便地被模具所调用。在智能化软件的支持下,模具CAD不再是对传统设计与计算方法的模仿,而是在先进设计理论的指导下,充分运用本领域专家的丰富知识和成功经验,其设计结果必然具有合理性和先进性。
现代模具制造技术朝着加快信息驱动、提高制造柔性、敏捷化制造及系统化集成的方向发展。
一、高速铣削:第三代制模技术
高速铣削加工不但具有加工速度高以及良好的加工精度和表面质量,而且与传统的切削加工相比具有温升低(加工工件只升高3℃),热变形小,因而适合于温度和热变形敏感材料(如镁合金等)加工;还由于切削力小,可适用于薄壁及刚性差的零件加工;合理选用刀具和切削用量,可实现硬材料(HRC60)加工等一系列优点 。因此,高速铣削加工技术仍是当前的热门话题,它已向更高的敏捷化、智能化、集成化方向发展,成为第三代制模技术。
在电火花加工技术进步的同时,电火花加工的安全和防护技术越来越受到人们的重视,许多电加工机床都考虑了安全防护技术。目前欧共体已规定没有“CE”标志的机床不能进入欧共体市场,同时国际市场也越来越重视安全防护技术的要求。
目前,电火花加工机床的主要问题是辐射骚扰,因为它对安全、环保影响较大,在国际市场越来越重视“绿色”产品的情况下,作为模具加工的主导设备电火花加工机床的“绿色”产品技术,将是今后必须解决的难题。
电火花加工
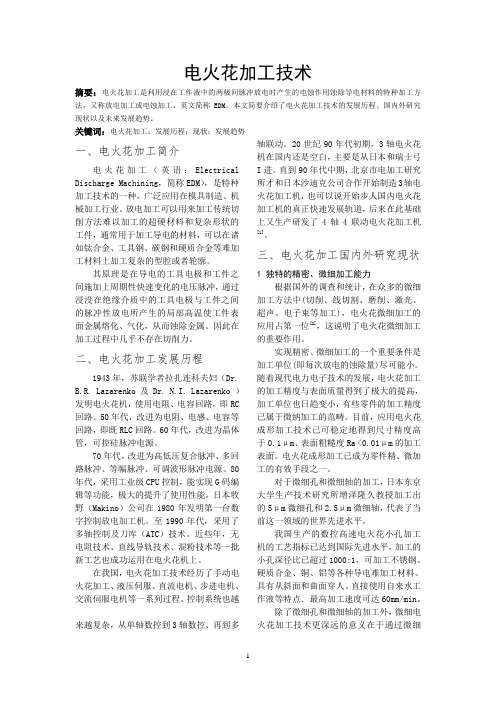
电火花加工技术摘要:电火花加工是利用浸在工作液中的两极间脉冲放电时产生的电蚀作用蚀除导电材料的特种加工方法,又称放电加工或电蚀加工,英文简称EDM。
本文简要介绍了电火花加工技术的发展历程、国内外研究现状以及未来发展趋势。
关键词:电火花加工;发展历程;现状;发展趋势一、电火花加工简介电火花加工(英语:Electrical Discharge Machining,简称EDM),是特种加工技术的一种,广泛应用在模具制造、机械加工行业。
放电加工可以用来加工传统切削方法难以加工的超硬材料和复杂形状的工件,通常用于加工导电的材料,可以在诸如钛合金、工具钢、碳钢和硬质合金等难加工材料上加工复杂的型腔或者轮廓。
其原理是在导电的工具电极和工件之间施加上周期性快速变化的电压脉冲,通过浸没在绝缘介质中的工具电极与工件之间的脉冲性放电所产生的局部高温使工件表面金属熔化、气化,从而蚀除金属。
因此在加工过程中几乎不存在切削力。
二、电火花加工发展历程1943年,苏联学者拉扎连科夫妇(Dr.B.R. Lazarenko 及 Dr. N.I. Lazarenko )发明电火花机,使用电阻、电容回路,即RC 回路。
50年代,改进为电阻、电感、电容等回路,即既RLC回路。
60年代,改进为晶体管,可控硅脉冲电源。
70年代,改进为高低压复合脉冲、多回路脉冲、等幅脉冲、可调波形脉冲电源。
80年代,采用工业级CPU控制,能实现G码编辑等功能,极大的提升了使用性能。
日本牧野(Makino)公司在1980年发明第一台数字控制放电加工机。
至1990年代,采用了多轴控制及刀库(ATC)技术。
近些年,无电阻技术、直线导轨技术、混粉技术等一批新工艺也成功运用在电火花机上。
在我国,电火花加工技术经历了手动电火花加工、液压伺服、直流电机、步进电机、交流伺服电机等一系列过程。
控制系统也越来越复杂,从单轴数控到3轴数控、再到多轴联动。
20世纪90年代初期,3轴电火花机在国内还是空白,主要是从日本和瑞士弓I进。
电火花表面强化技术.
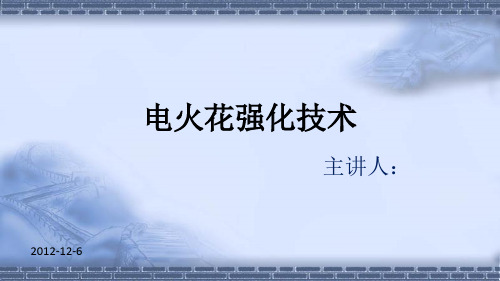
与其它常见的表面处理技术相比,如电镀,热喷涂,常规表面化学
热处理等。电火花强化技术的优点可以归纳为以下几点:
1.设备简单,操作容易,不需要专业操作人员。 2.热输入较小,被强化的工件基体不会产生整体退火或热变形。 3.强化层与基体冶金结合,结合强度较高,不会发生剥落现象。 4.工艺参数可控,电极材料选择范围广。 5.应用范围广,对于一般几何形状的平面或曲面均可进行强化。
3、脉冲频率:脉冲频率主要影响强化层的表面致密度,当脉冲频率提高 时,单位时间内放电次数增多,每次过渡的电极熔融颗粒变小,所获的 强化层致密度将提高,光洁度增加,同时也可在一定程度上提高硬度。 但是对于给定的电规准,脉冲频率不可过大,否则可能造成电容器充电 不足或放电不完全,从而降低强化层厚度。 4、强化时间:强化时间对强化层影响较为复杂。在某一最佳强化时间之 前,强化层厚度随强化时间增加而增大,且强化层组织较均匀、致密, 这是因为在强化初期,电极材料向基体过渡量较小,强化层较薄,尚未 完全覆盖工件表层,故表面存在的缺陷也很少,表面质量较好。当强化 时间超过这最佳强化时间的后强化层厚度增幅放缓,且表面粗糙度显著 提高,这是因为随着电极熔滴不断向工件沉积,强化层表面的强化点和 电蚀凹坑会不断叠加,加上强化过程一般由人手工操作,也会使熔滴涂 覆不均匀性增加,故表面粗糙度升高。但是进一步增加强化时间,粗糙 反而又会下降,其原因是强化层表面凸起的较大颗粒与电极间的间距相
强化的物理化学过程
1、超高速淬火 类似于焊接,电火花强化也是一个快速加热,快速冷却的过程。电 火花放电过程十分短暂,但是在瞬间可以释放出大量的热能,使得工件 表面很小的面积熔化以及部分气化。火花放电结束后,被加热的金属部 分在周围冷的金属以及冷的气体介质中,会快速冷却,发生高速淬火。 2、渗氮、渗碳 在电火花放电通道区域内,温度很高,空气中的氮分子呈原子状态, 与受高温熔化的金属有关元素化合成高硬度的金属氮化物,如氮化铁、 氮化铬等。如若在强化过程中采用气体保护(如氩气),则生成的氮化 物将大幅减少。另外来自石墨电极或周围介质的碳元素也会形成金属碳 化物,如碳化铁、碳化铬等。
LIGA相关技术
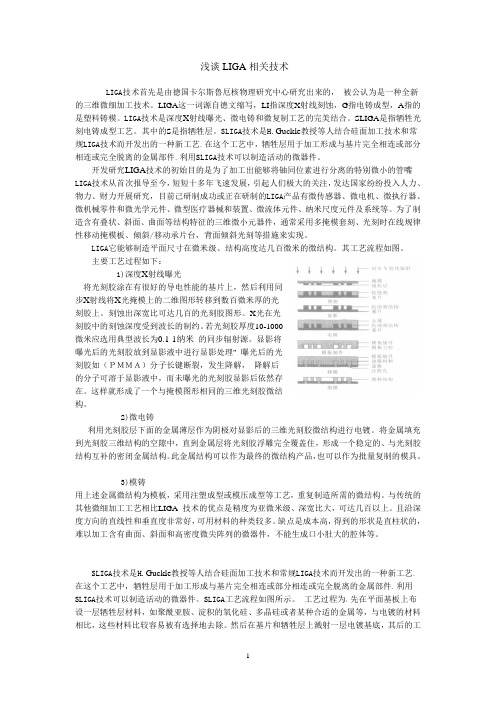
浅谈LIGA相关技术LIGA技术首先是由德国卡尔斯鲁厄核物理研究中心研究出来的,被公认为是一种全新的三维微细加工技术。
LIGA这一词源自德文缩写,LI指深度X射线刻蚀,G指电铸成型,A指的是塑料铸模。
LIGA技术是深度X射线曝光、微电铸和微复制工艺的完美结合。
SLIGA是指牺牲光刻电铸成型工艺。
其中的S是指牺牲层。
SLIGA技术是H.Guckle教授等人结合硅面加工技术和常规LIGA技术而开发出的一种新工艺。
在这个工艺中,牺牲层用于加工形成与基片完全相连或部分相连或完全脱离的金属部件。
利用SLIGA技术可以制造活动的微器件。
开发研究LIGA技术的初始目的是为了加工出能够将铀同位素进行分离的特别微小的管嘴LIGA技术从首次报导至今,短短十多年飞速发展,引起人们极大的关注,发达国家纷纷投入人力、物力、财力开展研究,目前己研制成功或正在研制的LIGA产品有微传感器、微电机、微执行器、微机械零件和微光学元件、微型医疗器械和装置、微流体元件、纳米尺度元件及系统等。
为了制造含有叠状、斜面、曲面等结构特征的三维微小元器件,通常采用多掩模套刻、光刻时在线规律性移动掩模板、倾斜/移动承片台,背面倾斜光刻等措施来实现。
LIGA它能够制造平面尺寸在微米级、结构高度达几百微米的微结构。
其工艺流程如图。
主要工艺过程如下:1)深度X射线曝光将光刻胶涂在有很好的导电性能的基片上,然后利用同步X射线将X光掩模上的二维图形转移到数百微米厚的光刻胶上。
刻蚀出深宽比可达几百的光刻胶图形。
X光在光刻胶中的刻蚀深度受到波长的制约。
若光刻胶厚度10-1000微米应选用典型波长为0.1-1纳米的同步辐射源。
显影将曝光后的光刻胶放到显影液中进行显影处理" 曝光后的光刻胶如(PMMA)分子长键断裂,发生降解,降解后的分子可溶于显影液中,而未曝光的光刻胶显影后依然存在。
这样就形成了一个与掩模图形相同的三维光刻胶微结构。
2)微电铸利用光刻胶层下面的金属薄层作为阴极对显影后的三维光刻胶微结构进行电镀。
电火花线切割加工技术详解
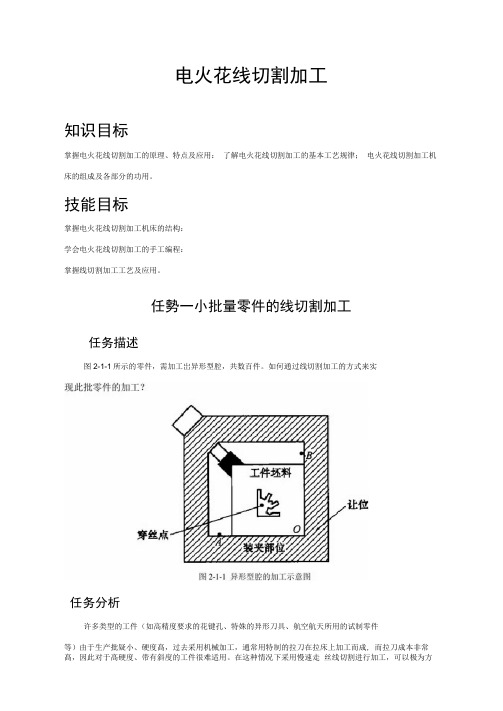
电火花线切割加工知识目标掌握电火花线切割加工的原理、特点及应用:了解电火花线切割加工的基本工艺规律;电火花线切割加工机床的组成及各部分的功用。
技能目标掌握电火花线切割加工机床的结构:学会电火花线切割加工的手工编程:掌握线切割加工工艺及应用。
任勢一小批量零件的线切割加工任务描述图2-1-1所示的零件,需加工岀异形型腔,共数百件。
如何通过线切割加工的方式来实任务分析许多类型的工件(如高精度要求的花键孔、特姝的异形刀具、航空航天所用的试制零件等)由于生产批疑小、硬度髙,过去采用机械加工,通常用特制的拉刀在拉床上加工而成, 而拉刀成本非常髙,因此对于髙硬度、带有斜度的工件很难适用。
在这种情况下采用慢速走丝线切割进行加工,可以极为方便地满足加工要求。
知识准备一、电火花线切割加工的原理、特点及应用随着电火花加工技术的发展,在成形加工方而逐步形成两种主要加工方式:电火花成形加工和电火花线切割加工。
电火花线切割加工(wircculEDM,简称WEDM)自20世纪50 年代末产生以来,获得了极其迅速的发展,已逐步成为一种高精度和高自动化的加工方法,在模具制造、成形刀具加工、难加工材料和精密复杂零件的加工等方而获得了广泛应用。
目前电火花线切割机床已占电加工机床的60%以上。
1•电火花线切割加工的发展电火花线切割加工历经半个多世纪的发展,已经成为先进制造技术领域的重要组成部分。
电火花线切割加工不需要制作成形电极,能方便地加工形状复杂、大厚度的工件,且工件材料的预加工虽少,因此在模具制造、新产品试制和零件加工中得到了广泛应用。
尤其是进入20世纪90年代后,随着信息技术、网络技术、航空和航天技术、材料科学技术等髙新技术的发展,电火花线切割加工技术也朝着更深层次、更髙水平的方向发展。
我国上海仪表工程师于20世纪60年代独创的特种快速走丝电火花加工机床,经过30 多年的发展和完善,现已成为模具加工不可缺少的装备,也是中国模具生产企业装备数量最多的电火花加工机床。
edm技术加工工艺
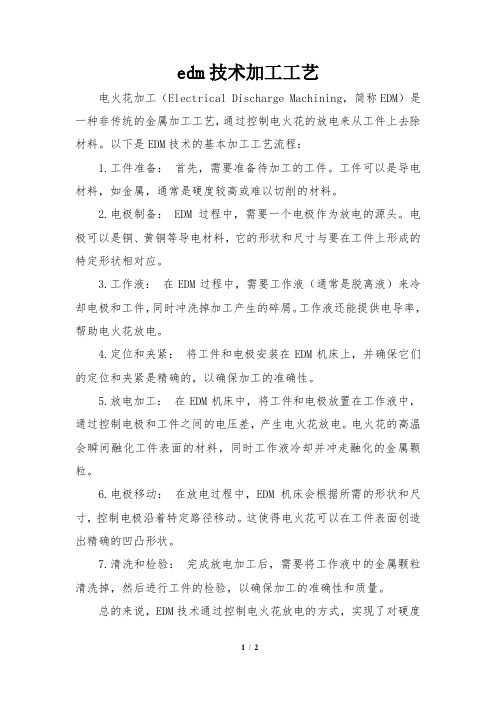
edm技术加工工艺
电火花加工(Electrical Discharge Machining,简称EDM)是一种非传统的金属加工工艺,通过控制电火花的放电来从工件上去除材料。
以下是EDM技术的基本加工工艺流程:
1.工件准备:首先,需要准备待加工的工件。
工件可以是导电材料,如金属,通常是硬度较高或难以切削的材料。
2.电极制备: EDM过程中,需要一个电极作为放电的源头。
电极可以是铜、黄铜等导电材料,它的形状和尺寸与要在工件上形成的特定形状相对应。
3.工作液:在EDM过程中,需要工作液(通常是脱离液)来冷却电极和工件,同时冲洗掉加工产生的碎屑。
工作液还能提供电导率,帮助电火花放电。
4.定位和夹紧:将工件和电极安装在EDM机床上,并确保它们的定位和夹紧是精确的,以确保加工的准确性。
5.放电加工:在EDM机床中,将工件和电极放置在工作液中,通过控制电极和工件之间的电压差,产生电火花放电。
电火花的高温会瞬间融化工件表面的材料,同时工作液冷却并冲走融化的金属颗粒。
6.电极移动:在放电过程中,EDM机床会根据所需的形状和尺寸,控制电极沿着特定路径移动。
这使得电火花可以在工件表面创造出精确的凹凸形状。
7.清洗和检验:完成放电加工后,需要将工作液中的金属颗粒清洗掉,然后进行工件的检验,以确保加工的准确性和质量。
总的来说,EDM技术通过控制电火花放电的方式,实现了对硬度
较高或难以切削材料的精确加工。
它在制造业中常用于生产模具、模具零件、工艺修整、刻蚀等领域,为复杂形状和高精度要求的工件加工提供了一种高效可靠的解决方案。
国外电弧增材制造技术的研究现状及展望

国外电弧增材制造技术的研究现状及展望展开全文科技媒体3D打印网讯增材制造技术又称“3D打印”技术,以“今日设计,明日产品”的理念受到高校、研究院所以及航空航天等大型企业的广泛关注。
经过近一个世纪的发展,它从依据粘接原理开发的叠层成形技术逐渐发展到以紫外光为热源的光固化成形技术,再发展到现在以电弧、电子束、激光等高能束为热源的快速熔化成形技术,实现了有机材料、无机非金属材料、金属材料产品的快速制造。
针对金属材料,根据高能束热源分为电弧增材制造、激光增材制造、电子束增材制造等技术,原材料一般有金属粉末和焊丝两种形式。
热源的差异导致增材制造技术在成形精度、沉积效率以及对复杂零件敏感程度等方面的差别。
电弧增材制造技术(WireArcAdditiveManufacture,WAAM)是一种利用逐层熔覆原理,采用熔化极惰性气体保护焊接(MIG)、钨极惰性气体保护焊接(TIG)以及等离子体焊接电源(PA)等焊机产生的电弧为热源,通过丝材的添加,在程序的控制下,根据三维数字模型由线-面-体逐渐成形出金属零件的先进数字化制造技术。
它不仅具有沉积效率高;丝材利用率高;整体制造周期短、成本低;对零件尺寸限制少;易于修复零件等优点,还具有原位复合制造以及成形大尺寸零件的能力。
较传统的铸造、锻造技术和其它增材制造技术具有一定先进性,与铸造、锻造工艺相比,它无需模具,整体制造周期短,柔性化程度高,能够实现数字化、智能化和并行化制造,对设计的响应快,特别适合于小批量、多品种产品的制造。
WAAM技术比铸造技术制造材料的显微组织及力学性能优异;比锻造技术产品节约原材料,尤其是贵重金属材料。
与以激光和电子束为热源的增材制造技术相比,它具有沉积速率高、制造成本低等优势。
与以激光为热源的增材制造技术相比,它对金属材质不敏感,可以成形对激光反射率高的材质,如铝合金、铜合金等。
与SLM技术和电子束增材制造技术相比,WAAM技术还具有制造零件尺寸不受设备成型缸和真空室尺寸限制的优点。
电火花线切割加工工艺技术
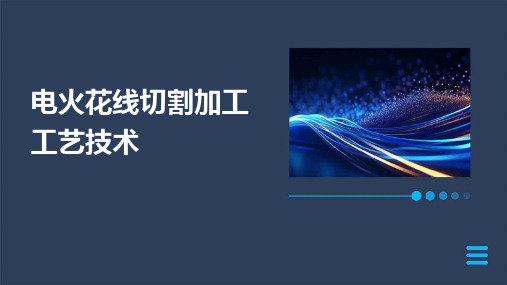
穿丝路径规划
在穿丝过程中,应保持钼丝一定的张力,避免过松或过紧,以确保加工精度和延长钼丝使用寿命。
保持钼丝张力
在穿入导轮后,应调整钼丝的垂直度,确保其在加工过程中稳定运行,提高切割精度。
调整钼丝垂直度
根据工件形状、尺寸和加工要求,选择合适的装夹方式,确保工件稳定、不易变形。
感谢观看
THANKS
复合材料
热导率
材料的热导率决定了切割过程中热量散失的快慢,热导率高的材料能够更快地将热量传递出去,提高切割效率。
导电性
材料的导电性能直接影响电火花线切割加工的放电效果,导电性好的材料更容易产生电火花。
硬度
材料的硬度对切割精度和表面质量有较大影响,硬度较高的材料更难切割,容易造成刀具磨损。
03
材料存储和运输
确定装夹方式
工件找正
合理分配夹紧力
定期检查夹具
在装夹工件前,应进行找正处理,确保工件与机床坐标系对齐,提高加工精度。
根据工件材质、尺寸和加工要求,合理分配夹紧力,避免工件变形或夹伤。
定期对夹具进行检查和维护,确保其完好无损,提高装夹精度和稳定性。
在加工过程中出现断丝现象时,应及时停机检查,排除故障,如调整张力、更换新钼丝等。
脉冲宽度决定了单个脉冲的能量,脉冲宽度越大,能量越高,切割效率提高,但同时也会增加电极丝损耗和影响加工精度。
能量密度是脉冲宽度和脉冲电压的乘积,它决定了电火花线切割的加工能力和效率。
能量密度
脉冲宽度
脉冲间隔是指相邻两个脉冲之间的时间,脉冲间隔越长,放电时间越短,加工效率降低,但可以减少电极丝损耗和加工表面粗糙度。
电火花线切割加工工艺技术
电火花线切割加工技术

电火花线切割加工技术摘要:电火花线切割加工是在电火花加工基础上于20世纪50年代末最早在前苏联发展起来的一种新的工艺形势,是用线状电极靠火花放电对工件进行切割,故称为线切割,随着电加工设备及加工工艺的发展,加工模具的工艺路线,在不断的改进。
该文以线切割的加工原理及发展过程为背景,对彩虹彩色显像管总厂零件分厂的模具加工工艺路线作简单介绍。
关键词:线切割;工艺路线;变革;精度;效率Wire cut edm technologyAbstract: The experimental research of EDM process of conductive engeering ceramics using a special power supply by controlling pulse discharging energy, is discussed. The basic principle of electrolytic machining and the superiority of its processing technology were introduced. The ECM/EDM (electrochemical melting and electric discharge machining) compound machining process was stated. And the foreign developing status quo of the ECM/EDM compound processing of deep and small holes was mentioned.一:电火花线切割的应用范围:在目前的生产中,数控电火花线切割技术应用广泛,不仅是因其加工效率高精度高,更重要的是其加工范围广泛。
数控电火花线切割可加工下列工件:1、电火花成形用电极线切割技术适合加工一般穿孔加工用、带锥度型腔加工用及微细复杂形状的电极,同时还有铜钨、银钨合金之类的电极材料。
电火花表面毛化加工技术的新应用

特 别 要 注 意 的 是 喷 砂 法 对 模具 品 质 寿
,
命 的影 响
。
由 于 钢 砂 的 作 用 是 使模 具 材料
, , ,
。
因 此 这 种表 面 毛 化 加 工 技 术
,
,
产 生 塑 性 变形 而 形 成 毛 化 表面 因 此 喷 砂
对 于 提 高 产 品整 体的外 观 形 象 具 有 重 要 的
时 模具 型 腔 的 硬 度 必 须低 于 钢 砂 的 硬 度 如
果 模 具在 喷砂 毛 化 后 仅 依 靠喷 砂 而 强 化 的 表 面 冷作 硬 化 层 硬 度 那 么 模具 本 身 应 具 有 的 防蚀 功 能就会 受 到 限 制 就 会 限 制模 具 材
料 的选 择 而 不 能使 用 高 强 度 高 硬 度 的 模 具
, ,
。
学 毛 化 电 解 毛 化 等 工 艺技 术 在 表 面 毛 化 工艺 方 面 还 存 在 不成 熟的 因 素 而 未 被 广 泛
地采 用
。
、
,
大差 值
构造
。
。
放 电加 工 面 在 加 工 过 程 中
,
,
,
受 急 热 和 急 冷 变 化 所 以有 特 殊 的 微 细 结 晶
从 垂 直于 放 电 加 工 面 的 方 向 向下 看
, ,
,
使 得放 电成型 加 工成 为 型 腔模 具 加工 的 主
要 手 段 之 一 由 于 放 电 成 型 加 工 本 身具 有 的 一 些 特 点 使 得 它 能 解决 一 些 机 械 加 工 方 法 不 能 解决 的 问 题
、 、
。
加 工 有 三 个 最 致 命 的 缺 点 首先 难 以 控 制
电火花加工的工作原理
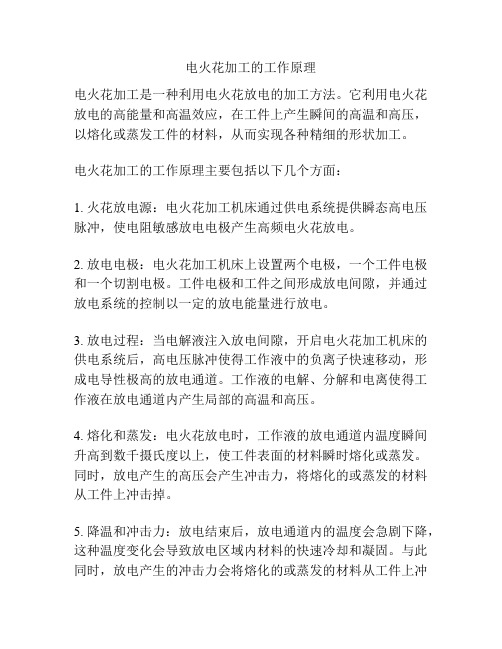
电火花加工的工作原理
电火花加工是一种利用电火花放电的加工方法。
它利用电火花放电的高能量和高温效应,在工件上产生瞬间的高温和高压,以熔化或蒸发工件的材料,从而实现各种精细的形状加工。
电火花加工的工作原理主要包括以下几个方面:
1. 火花放电源:电火花加工机床通过供电系统提供瞬态高电压脉冲,使电阻敏感放电电极产生高频电火花放电。
2. 放电电极:电火花加工机床上设置两个电极,一个工件电极和一个切割电极。
工件电极和工件之间形成放电间隙,并通过放电系统的控制以一定的放电能量进行放电。
3. 放电过程:当电解液注入放电间隙,开启电火花加工机床的供电系统后,高电压脉冲使得工作液中的负离子快速移动,形成电导性极高的放电通道。
工作液的电解、分解和电离使得工作液在放电通道内产生局部的高温和高压。
4. 熔化和蒸发:电火花放电时,工作液的放电通道内温度瞬间升高到数千摄氏度以上,使工件表面的材料瞬时熔化或蒸发。
同时,放电产生的高压会产生冲击力,将熔化的或蒸发的材料从工件上冲击掉。
5. 降温和冲击力:放电结束后,放电通道内的温度会急剧下降,这种温度变化会导致放电区域内材料的快速冷却和凝固。
与此同时,放电产生的冲击力会将熔化的或蒸发的材料从工件上冲
击掉,并将其带走。
综上所述,电火花加工通过高能量的电火花放电,在工件表面产生高温和高压,使材料熔化或蒸发,达到精细加工的目的。
它在航空航天、模具制造、微细加工等领域具有重要的应用价值。
电火花加工技术研究和应用的现状

电火花加工技术研究和应用的现状上海船舶设备研究所樊仁才(旁听证号:P201109042)1 引言电火花加工(Electrical Discharge Machining ,简称EDM)技术是在一定介质中通过工具电极和工件电极之间的脉冲放电的电蚀作用对工件进行加工的方法。
该项技术在20世纪40年代开始研究并逐步应用于生产。
从最初只能去除折断在工件中的钻头、丝锥、切割硬质合金刀片开始,经过半个多世纪的发展,电火花加工现在已成为精密模具、复杂形状零件以及精密微小孔加工的重要装备,在航空航天、模具制造等领域获得了极为广泛的应用。
近年来,电火花技术的研究和应用日新月异(见下表1),并在精密微细化、智能化、个性化、绿色环保化和高效化等方面获得了长足的发展[1][2]。
表1电火花加工的最新技术[3]2 独特的精密、微细加工能力“电火花加工的优点就是精密加工”,精密电火花加工一直是电火花加工技术的一个重要发展方向。
信息、航空航天、电子、国防等领域尖端科学技术发展对模具的精密化及精密产品零件的加工要求,又促进了电火花加工技术的发展。
根据国外的调查和统计,在众多的微细加工方法中(切削、线切割、磨削、激光、超声、电子束等加工),电火花微细加工的应用占第一位[4],这说明了电火花微细加工的重要作用。
实现精密、微细加工的一个重要条件是加工单位(即每次放电的蚀除量)尽可能小。
随着现代电力电子技术的发展,电火花加工的加工精度与表面质量得到了极大的提高,加工单位也日趋变小,有些零件的加工精度已属于微纳加工的范畴。
目前,应用电火花成形加工技术已可稳定地得到尺寸精度高于0.1μm、表面粗糙度Ra <0.01μm的加工表面。
电火花成形加工已成为零件精、微加工的有效手段之一。
[1]曹凤国,张勤俭,翟力军等.国际电火花加工技术的五大趋势.机械工人(冷加工),2005(2): 33~36.[2]曹凤国,张勤俭,翟力军等.国际电火花加工技术发展的五大趋势.电气制造,2006(3): 21~24.[3]王克锡.电火花加工的最新发展(上).金属加工(冷加工),2008(8): 65~70.[4]Uhlmann E.Pihz S Jerzembeck S. Micro machining of cylindrical parts by electrical discharge grinding.l4th International Sympo sium on Electromachining.Edinburgh,2.1 微细孔和微细轴加工产品的微型化是现代生产所追求的目标之一,微细加工在近代加工技术中是一个新的领域。
火花沉积技术国内外研究的最新进展

火花沉积技术国内外研究的最新进展摘要:电火花沉积技术以其节能、汽车材料、环保等优势作为修复研究热点之一,广泛应用于航空军事、能源、电力、医疗矿山冶金等领域,以及精密机械零部件的制造与维修,为了总结这项技术在国内外的基本原理和技术特点,研究的最新进展,对加快这项技术研究及其应用提出了具体建议。
关键词:电火花沉积;进展;原理;工艺特点引言:现代工业的快速发展对材料的耐磨性、耐腐蚀性和耐高温性提出了更高的要求。
在高速、高温、高压、高氧化和高温腐蚀等恶劣条件下,大多数材料损伤发生在材料表面,如高温下的磨损和氧化,这使得材料表面强化技术成为国内外研究的热点之一。
有许多表面强化技术,包括电镀、渗透、热喷涂、EDM、冲浪、激光涂层和气相沉积。
其中,电火花沉积技术是表面强化技术的一个重要组成部分,它具有与基体冶金结合良好、耐磨耐蚀性好、不同材料之间容易沉积、电气材料易于选择等优点,节能、节材、环保,广泛应用于航空航天、汽车、能源、军工、电能、医疗、冶金矿山等领域,以及精密机械零部件的制造和维修得到迅速普及和应用,显示出更广阔的应用前景。
以下重点介绍国内外电火花加工技术的研究现状和进展。
一、电火花表面沉积技术原理及特点沉积工艺如图2所示。
图1电火花表面沉积技术工作原理图图2电火花表面沉积工艺示意图采用分析手段对沉积层进行微观分析。
分析结果表明:沉积层是由电极材料和工件材料通过冶金结合后形成的;沉积强化层组织细密,厚度达5-15um,硬度达到HV 1200以上(相当于HRC72 ),具有优良的物理化学性能和机械性能。
EDM表面沉积技术不仅能有效改善工件的表面性能,而且与传统的表面强化工艺如表面化学热处理、激光镀膜、电镀、,等离子弧和热喷涂的热焊接。
主要体现在以下几个方面:(1) EDM是空气沉积,易实现YG硬质合金、碳钢、黄铜等不同材料的增强层;(2)热输入非常小,电弧的热作用仅发生在工件表面的一小部分,工件的整个基体保持在室温下。
电火花加工的原理

电火花加工的原理电火花加工(Electric Discharge Machining,EDM)是一种非传统的金属加工技术,在航天、航空、汽车、模具、电子、医疗器械、手表等领域得到广泛应用。
其基本原理是在工件和电极间通过电弧放电击穿介质,利用电弧放电的高温高压作用,以腐蚀剥蚀的方式将工件上的材料去除,从而达到加工目的。
具有精度高、加工效率高、能够加工高硬度材料等优点。
本文将从原理、加工过程、影响因素、特点等方面对电火花加工进行详细介绍。
一、原理电火花加工是利用电脉冲的闪放放电从工件表面抽掉微小粒子的一种电化学加工方法。
其加工原理是利用电极间放电的高温高压效应,通过金属电极和工件上材料的反复电弧放电腐蚀、气化和溶解,使工件表面逐渐形成所需要的轮廓形状。
电弧放电腐蚀时会释放出高温和高压,将材料去除。
法则是在工件和电极之间形成电弧放电,在电极与工件接触底部的位置放电并生成热脱积过程,继而对工件进行加工。
二、加工过程1.热脱积过程当电极和工件接触之后,通过施加不同频率的脉冲电流,一系列闪电放电就在电极和工件之间反复发生,使工件表面材料被局部加热,压力蒸发产生的气体被排出,产生蚀刻物质。
2.形成水孔在每个放电的瞬间,电弧在工件和电极之间形成一个气态介质区域,这个地区的空气和蒸汽被抽出,形成一个小孔或某种形状的孔道。
当内腔填充时,材料被疏松起来。
3.清除工件表面的热脱积产物使用电极和工件之间的冷却剂来吹洗清理的剩余热脱积物质并加速加工物表面的光洁度。
三、影响因素1. 工作液质量也是影响加工精度的关键因素之一。
2. 电极材料和工作电流强度,也会影响加工效果,通常选择耐腐蚀性强的金属材料。
3. 工件材料也很重要,硬材料如钨合金、钢铁铸造件等可以使用电火花加工进行加工。
而软材料则不具备可切削性,难以加工。
4. 脉冲时间控制精度是主要的电火花加工参数。
5. 加工的形状、尺寸、表面状态和要求的加工精度等也会影响加工效果。
- 1、下载文档前请自行甄别文档内容的完整性,平台不提供额外的编辑、内容补充、找答案等附加服务。
- 2、"仅部分预览"的文档,不可在线预览部分如存在完整性等问题,可反馈申请退款(可完整预览的文档不适用该条件!)。
- 3、如文档侵犯您的权益,请联系客服反馈,我们会尽快为您处理(人工客服工作时间:9:00-18:30)。
图12 电火花加工的绝缘陶瓷小孔
6单次放电微细电极加工
毛利尚武教授在研究用细小钨电极 (加.1mm)对工件表面进行液中表面改性处理 时,当选择合适大的电规准和加工极性时,单脉 冲放电就可使钨电极前端变细变尖,即可得到钨 微细轴和探针。图13是单脉冲放电加工的微细 轴和其前端,前端微细轴的直径为359m,长
高了材料去除率并降低了电极损耗。 日本东京农工大学的韩福柱与国枝政典应
用混沌理论分析了放电点分布。认为放电点的分 布混沌的。通过计算吸引子的维数可以区别不同 的放电状态。放电点的混沌程度愈强,则放电过 程与稳定。通过浑河不同的脉冲,可以增加放电 点分布的混沌性。
ቤተ መጻሕፍቲ ባይዱ
3 电火花加工放电状态检测新方法4液中放电表面改性处理
× V
* 茸 聒 骂 脚
味宣(岿)
麓g盏裟嚣皇簧;飘
图20电极损耗率的比较
图16气体电火花附 着堆积的微细圆柱(直 径约140uITI,高
22mm)
图17电火花附着堆 积后电火花去除加工
缩空气中放电来代替液体介质中的放电来修形、 修锐金属基金刚石砂轮,其结果表明经过这样处 理后的砂轮的磨削性能同传统的修形方法几乎相 同。这种方法同样可以修曲曲线轮廓。
10
特种加工技术
的负极,电极错开半个直径进行电火花去除加工 所得的样件。图18是电火花附着堆积加工断面, 黑色小坑是硬度试验压痕,其硬度为HV500, 远高于¥45C钢的硬度HV200。
8 气体中放电电火花加工
日本东京农工大学国枝正典副教授开展了气 体中放电电火花加工,气体中线切割加工的研 究。图19气体中电火花加工原理,是使用管电 极,
川伸哉博士等,通过计算钢打钢时正极和负极的 温度分布,选择合适的电参数,使得工具电极的 放电点温度超过其材料的沸点,工件电极的温度 在其材料的熔点和沸点之间,在空气中进行了电 火花堆积造型实验,图16是气体电火花附着堆 积的微细圆柱(直径约1409m,高2.2mm),工 件和电极都是S45C钢,电极直径0.1mm,放电 电流2.5A,脉宽59s,工件接脉冲电源负极,加 工时间6.3小时。图17是电火花附着堆积后其 他参数不变,仅将加工极性变为电极接脉冲电源
综
述
元件,具有自主间隙调节功能.结构简单,且可 以通过调节其姿态实现三维曲线孔的加工。但这 一装置的加工性能取决于整体动力学性能,如形 状记忆合金弹簧的热惯性与刚度、偏置弹簧的刚 度.放电电流的大小等。该实验装置的加工试验 表明其整体加工效率在相同的加工规准下,仅为 普通电火花加工机床的l,l∞l,2。
图Il电火花加工的绝缘冉瓷螺纹孔
绝缘陶瓷ZrO:上电火花加工的螺纹孔,图 12是在绝缘陶瓷Zr02上电火花加工的100个 00.3mm小孔。他们还把这一技术同混粉工作液 相结合,结果发现加工表面质量得以提高 (&,41sm),而且由于可以用较宽的脉宽来进行 加工(241as)从而提高了加工效率。加工Si3N4 的速度可以和磨削相当。
2弯曲孔电火花加工装置
日本电气通信大学机械工程与智能系统系的 石田与竹内发明了一种用于模具三维冷却通道加 工用的自主式弯曲孔加工装置,并称其为“自动 放电间隙控制器”。这一装置巧妙地运用了一个 螺旋压缩弹簧和一个有形状记忆合金制成的伸长 式弹簧使之具有自行走和放电间隙自动调节功
图l 自动放电问隙控制善
实验证实,平均间隙电压和加工问隙的大 小与间隙的污染程度几乎没有直接关联,而运用 间隙超声波传导系数却可以直接反映间隙的污染 情况。利用这种检测方法,有希望获得加工状态 的新的信息,对于改进加工控制策略,提高加工 性能具有重要的应用价值。
德国汉堡大学的A.Belm∞等人针对击穿 延时信号的分散性所引起的屯极间隙伺服系统过 进给现象.选用相对短路频率和相对开路频率作 为控制系统的输入信号,并通过模糊控制策略提
关键词:电火花加工放电沉积气体中放电加工陶瓷材料加工微细电火花加工
1 前言
近年来电火花加工方面的研究取得了许多 新的进展。主要表现在突破了许多传统观念的束 缚,产生了一些新的加工方法。使得这一方法不 仅可以进行体积去处,还可以进行表面陶瓷化改 性和沉积。加工不仅可以在绝缘工作液中进行. 也可以在气体中进行。不仅可以加工导电材料, -也可以加工非导电材料。大大扩展了之一技术的 应用领域。
能。具体原理如图1所示。电极被安装在轴上. 形状记忆台金弹簧在没有放电电流流过时处于收 缩状态,被偏置弹簧顶住。当整个机构距离工件 足够近时,电极与工件间产生火花放电,放电电 流通过形状记忆合金弹簧,产生热量使得弹簧温 度升高,导致形状记忆合金弹簧伸长,使电极远 离工件,放电间隙增大,其结果将使空载率增加、 有效放电率降低,流过形状记·『乙合金的平均放电 电流也随之下降,从而引起形状记忆合金的收 缩,带动电极向工件方向移动。当达到一定平衡 时就可以稳定地进行加工。这一自动调节功能与 间隙伺服系统的作用是完全相同的。其有效行程 范围取决于偏置弹簧与形状记忆合金弹簧的设 计。实际加工时还需要有一个蠕动机构配合,随 着工件被蚀除,将其不断地向前推进并保持在其 有效的调节行程范围内。这一机构无需其他驱动
和热影响层构成。图7是用TiC烧结体电极对 ¥45C表面处理后的X衍射分析结果,其含有明 确的TiC衍射峰、Fe3C衍射峰和Fe的衍射峰。 说明表面含有TiC、Fe3C和Fe。图8是用TiC
E侧略誓耐
图6是用TiC烧结体电极对¥45C表面处理后的 断面照片和电子探针分析结果,加工面积
100mm2,峰值电流I,=8A,脉宽‘=8“s,脉间 “=1289s,工件接脉冲电源的正极。基体主要成 分Fe从基体到表面层的浓度逐渐减少,在最表 面几乎为零,另一方面,Ti的浓度越接近表面 层越高。Ti扩散渗透到工件材料基体内,在处 理膜和基体的界面附近,即成分浓度变化为零的 区域其组织形态和基体的不同,这一区域为热影 响层。表面处理改性膜由成分浓度变化的层(硬 质层)
8圣亲’冀黼S花E加M吾蔫喜S。U。B。3.04勰在
毛利尚武教授、斋藤长男教授和三菱电机 名古屋制作所合作开展的液中电火花放电表面改 性处理的研究,主要有硅电极液中电火花放电表 面改性处理,混粉(硅粉等)液中电火花放电表 面改性处理,粉末压结体电极液中电火花放电表 面改性处理,细小电极液中电火花放电表面改性 处理等。图4为压结粉末电极在液中电火花放 电表面处理的原理is],图5是用硅电极表面处 理后的不锈钢在王水中浸泡50min后的断面照 片,可以看出经过处理后的表面,没有任何腐蚀 的痕迹。
旦———一 一——
壁登塑三堡查
国外电火花加工最新技术
赵万生郭永丰耿春明
(哈尔滨工业大学)
摘要: 介绍了国外近年来电火花加工研究的最新成果,其中包括液中电火花表面改 性处理,单次放电微细轴电极和探针电火花加工,放电沉积造型加工,绝缘陶瓷电火花加工, 气体中放电加工,扫描创成电火花加工,钛合金电火花线切割表面着色,弯曲孔电火花加工 和放电状态的超声检测等电火花加工最新技术,可为我国的电加工研究提供借鉴。
图18电火花附着堆积加工断面
雷19气体电^花加工原理
高速气体为Dns_介质,电极旋转,高速气体从管 电极中喷出进行电火花加工的。气体放电电火花 加工安全,不污染环境,电极损耗率非常低,放 电加工时的反作用力非常小,有利于微细加工. 选择合适的气体时,加工表面再凝固层(白层) 非常小。图20是电极损耗率的比较,图21是加 工断面观察结果,图22是气体中WEDG加工的 微细轴,图23是气体中电火花三维扫描创成加 工样件。富山地方大学岩井等人还利用大气获压
目前国外的电火花加工新技术主要有线电 极电火花磨削精微、微细电火花加工,混粉镜面 电火花加工,液中放电表面改性处理,单次放电 微细轴电极和探针电火花加工,放电堆积成型加 工,绝缘陶瓷电火花加工,气体中放电电火花加 工,气体中放电线切割加工,双电极电火花加工, 电火花放电点位置的检测和控制,线切割放电点 位置的检测和控制,扫描创成电火花加工,钛合 金电火花线切割表面着色,反复反拷精微、微细 电火花加工,弯曲孔电火花加工,电火花直线电 机伺服控制,新的摇动控制技术等。限于篇幅, 今就以下几项日本的放电加工最新技术成果加以 介绍。
毛利尚武教授和斋藤长男教授在研究用硅电极进 行大面积镜面电火花加工时,发现了一个有趣的 现象,从而萌发了在煤油中用放电进行表面改性 的概念.开始了渍中放电表面改性处理的研究。 他们采用硅电极,峰值电流lp=l~4A,脉宽tr-2~ 5ps电火花精加工SUS304(18Cr-8Ni钢),13Cr 钢,SKI-I-51(高速钢),SKI).61,SKD.11等 3~5min后,获得了用王水也不腐蚀的加工表 面。对于处理后的13Cr钢在空气(炉内)中,900 ℃加热20h,氧化也不向其内部扩展。图3是用 硅电极电火花加工过的SUS304工件浸泡在王水 中30分钟后的断面SEM照片和ERMA分析结 果.表面已融熔入16%的Si,呈玻璃状的非晶 态,结合强度非常高,进行30%的永久变形的 反复拉伸实验,也不产生剥离和裂纹Is,7]。
距基体表面的距离(岬)
图8表面处理后的硬
烧结体电极对¥45C表面处理后的硬度分布,加 工面积400ram2,加工时问32分钟,峰值电流 Ip=SA,脉宽t{=2ps,脉间to=64p,s和脉宽tj=8I_ts, 脉问to=128ps,处理后的硬度提高明显,由基体 内距基体表面约100m到处理表面,其硬度都高 于基体的硬度,硬度逐渐增高,越接近表面,硬 度越高,最高硬度约时基体的5倍。图9是冲 了2.5万次后冲头磨损的对比,处理后的冲头比 不处理的耐磨得多。
日本三菱电机公司的今井、广井与中野研 究了用超声波对电火花加工放电状态检测的方 法。他们用图2所示的装置对加工间隙的超声波 传导系数进行了试验研究。通过改变间隙的大 小、金属粉末浓度、吹入间隙的气泡含量对间隙 的超声波传导系统进行了测试。试验证实了在间
图2加工间隙的超声波检测方法
隙距离5~80pJn范围内间隙的大小与间隙的超 声波传导系统几乎无关。间隙中金属粉末浓度在 O~O_39,ml范围内金属粉末的浓度与间隙的超声 波传导系数几乎无关。但随着间隙中加入的气泡 流量在0~50ml/min范围内变化,相对于没有气 泡和金属粉末的间隙的超声波传导系数之比由 100%逐步下降到55%左右。因此得到间隙的超 声传导系数主要受到间隙气泡含量的影响。实际 加工过程中气泡浓度随着加工的进行而增加,因 此.间隙的超声波传导系数也随之下降,但经多 一个抬刀过程,气泡会被排除出而恢复到接近初 始值。加工规准愈大,则间隙的超声波传导系数 下降愈迅速,尤以峰值电流影响最为显著。