导光板模具
导光板常见生产异常的原因分析及解决方法

导光板常见生产异常的原因分析及工艺解决方法以安全生产为已任以成型技术为核心走创新之路解决问题的九大步骤:发掘问题--选定题目--追查原因--分析资料--提出办法--选择对策--草拟行动--成果比较--标准化。
一.划伤现象:指导光板表面出现划伤痕迹。
如图所示:原因分析:1.前制程:a . 在安装模仁时不慎将模仁表面划伤;b . 在处理模具异常时(如:拆滑块保养模具等)不慎将模仁表面划伤;c . 在擦试模仁表面时,因棉花不洁净或手指甲造成的模仁表面划伤等。
2.后制程: a. 设备调试不合理:指产品在进行某一个后制程动作加工时被后制程设备的某个零部件刮伤产品表面;b. 当导光板表面与后制程设备的某部位接触并发生移动摩擦时,因与导光板接触面的不洁净(有粉粒、异物等)导致与导光板表面产生较大的摩擦而至产品表面划伤(如:裁切平台、抛光平台、清洁滚轮等);c. 检验员的作业手法不标准或检验员的粗心大意导致产品表面划伤等。
(如除毛时,除毛刀划伤产品等)。
备注:对于前制程的产品划伤,如果超出SIP检验标准范围,尽量改善轻微一点,便找相关工程判定,看能否签样继续生产,如果实在不能改善或改善轻微,且又不能签样生产,便更换划伤的模仁,重新试模开机生产。
解决方法:1.在安装模仁、擦试模仁或处理模具异常时严格按作业标准谨慎操作;2.对设备不合理的地方或零部件加以改善3.定时对所有与接触产品表面的部位进行清洁;4.加强对员工的教育训练,监督并严格要求作业员按照作业标准进行作业。
二、熔结痕(结合线)现象:由于我们一般采取多段并以慢快慢的方式进行进胶,对于那些高粘度且低流动的塑胶材料(如PC,PMMA),在两段相差很大的射出进胶时,容易在两股熔胶汇合之处不能完全融合,形成一条汇流线,称为熔结痕。
一般熔结痕产生在产品胶口处,因为我们第一段与第二段或三段的射速太慢,如图:原因分析:由于来自不同方向的熔融树脂因开始射出速度较慢部分熔料被冷却,在后面射出的结合处未完全融合而在产品表面产生的一条条分区线。
导光板模具冷却水路的设计与分析
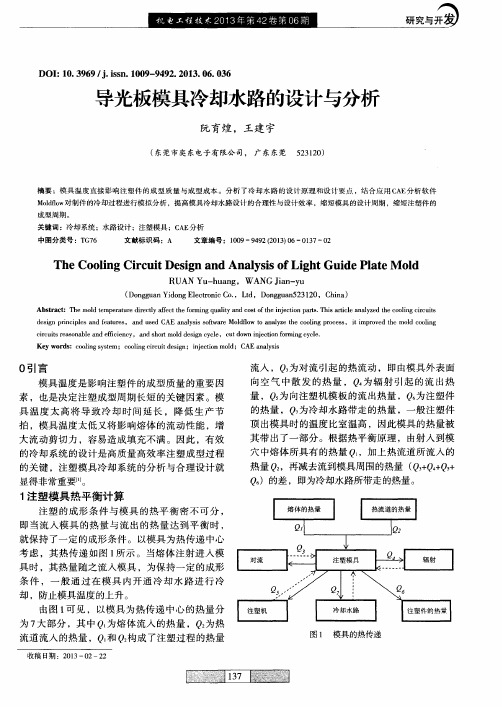
关键 词:冷却 系统 ;水路设 计 ;注塑模 具 ;C A E 分析
中图分类号 :T G 7 6 文献标识码 :A 文章编 号:1 0 0 9—9 4 9 2( 2 0 1 3 ) 0 6—0 1 3 7—0 2
Th e Co o l i n g Ci r c u i t De s i g n a n d An a l y s i s o f Li g h t Gu i d e Pl a t e Mo l d
d e s i g n p r i n c i p l e s a n d f e a t u r e s ,a n d u s e d CAE a n a l y s i s s o f t wa r e Mo l d l f o w t o a n ly a z e t h e c o o l i n g p r o c e s s ,i t i mp r o v e d t h e mo l d c o o l i n g
的热量 ,Q 为冷却水路带走 的热量 ,一般注塑件 顶 出模具 时 的温 度 比室温 高 ,因此 模 具 的 热量 被 其带出了一部分 。根据热平衡原理 ,由射人到模
穴 中熔 体所 具 有 的热量 Q ,加 上 热流 道 所 流人 的 热量 Q ,再减 去 流到模 具 周 围 的热量 ( Q , + p + Q +
的关键 ,注塑模具冷却系统的分析与合理设计就 显得非 常 重要” 】 。
Q )的差 ,即为冷却水路பைடு நூலகம்带走 的热量。
1 注塑模具热平衡计算
注 塑 的成 形 条 件 与 模 具 的热 平 衡 密 不 可 分 ,
即 当流入模具 的热量 与流 出的热量达到平衡 时 , 就保持 了一定的成形条件 。以模具为热传递 中心 考虑 ,其 热传递如 图 1 所示 。当熔体 注射进入模 具 时 ,其 热 量 随 之流 人 模 具 ,为保 持 一 定 的 成形
导光板工艺及其物料特性

而出光利用本身獨步旳開發技術、發揮 PC旳高強度、高耐熱旳特點之外、並提 升導光性能及透明性(清除黃底)、完 毕了導光板專用規格LC1500,LC1700。
导光板工艺及其物料特征
电光产品
导光板产品规格
导光板产品详细规格如下: 1.8 "最小厚度0.35mm 2.0 "最小厚度0.38mm 2.46 "最小厚度0.40mm 2.8 "最小厚度0.45mm 3.2 “最小厚度0.5mm 3.5 "最小厚度0.55mm 4.3 "最小厚度0.6mm
PC镜片简介(2/2)
PC1250Y透光率为88% ; 成型收缩率为0.35%--0.55%, 干燥温度105℃--120℃, 干燥时间为1—2H.
PMMA简介(1/3)
化学名称叫:聚甲基丙烯酸甲酯。
常见产品为 亚加力 也称有机玻璃!
超级透明PMMA材料主要用于手机保护 屏,该产品分为有硬化涂层,没有硬化涂 层两种.其特点是透光率极好,没有杂质, 静电保护膜, 目前尤其推荐用于硬化处 理旳PMMA材料,国内称为"生板".
PC出光(1/3)
出光運用獨家旳技術、針對不同製品規 格開發旳材料、讓顧客有多種規格能够 自由選擇。
導光板規格特點
雖然世界上有各種各樣旳塑膠材料、但 是透明材料旳種類有限、能在光學上旳 實用性更是少之又少。 從前、類似鏡 頭這些需要高度光學特征旳製品大多是 用像PMMA這種壓克力系旳塑膠。
PC出光(1/3)
2、耐腐蚀性:S136能抵抗水,水蒸气,弱有 机酸,稀释旳硝酸盐,碳酸盐等。由S136制 成旳模具,在潮湿旳环境中使用和贮存,或 在正常状态下模制腐蚀性旳塑料产品时,都 有良好旳抗锈及耐腐蚀性能。
导光板模具表面防刮花雾面处理工艺
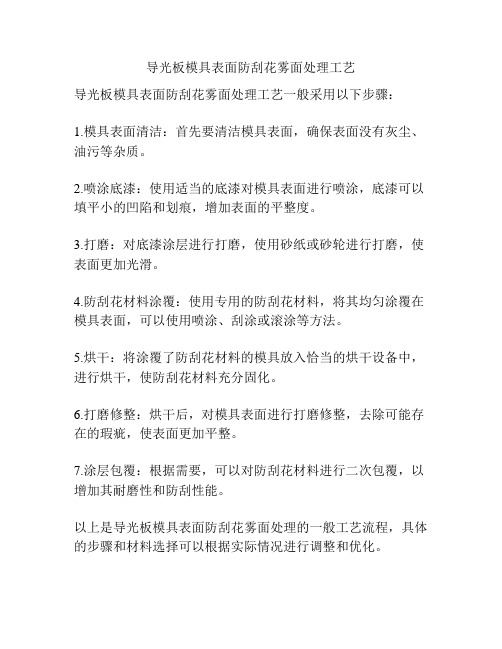
导光板模具表面防刮花雾面处理工艺
导光板模具表面防刮花雾面处理工艺一般采用以下步骤:
1.模具表面清洁:首先要清洁模具表面,确保表面没有灰尘、油污等杂质。
2.喷涂底漆:使用适当的底漆对模具表面进行喷涂,底漆可以填平小的凹陷和划痕,增加表面的平整度。
3.打磨:对底漆涂层进行打磨,使用砂纸或砂轮进行打磨,使表面更加光滑。
4.防刮花材料涂覆:使用专用的防刮花材料,将其均匀涂覆在模具表面,可以使用喷涂、刮涂或滚涂等方法。
5.烘干:将涂覆了防刮花材料的模具放入恰当的烘干设备中,进行烘干,使防刮花材料充分固化。
6.打磨修整:烘干后,对模具表面进行打磨修整,去除可能存在的瑕疵,使表面更加平整。
7.涂层包覆:根据需要,可以对防刮花材料进行二次包覆,以增加其耐磨性和防刮性能。
以上是导光板模具表面防刮花雾面处理的一般工艺流程,具体的步骤和材料选择可以根据实际情况进行调整和优化。
MP3导光板模具设计
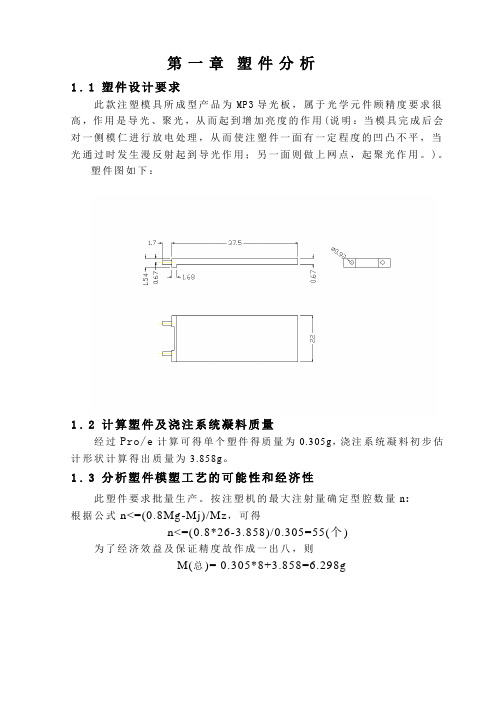
第一章塑件分析1.1塑件设计要求此款注塑模具所成型产品为MP3导光板,属于光学元件顾精度要求很高,作用是导光、聚光,从而起到增加亮度的作用(说明:当模具完成后会对一侧模仁进行放电处理,从而使注塑件一面有一定程度的凹凸不平,当光通过时发生漫反射起到导光作用;另一面则做上网点,起聚光作用。
)。
塑件图如下:1.2计算塑件及浇注系统凝料质量经过Pro/e计算可得单个塑件得质量为0.305g,浇注系统凝料初步估计形状计算得出质量为3.858g。
1.3分析塑件模塑工艺的可能性和经济性此塑件要求批量生产。
按注塑机的最大注射量确定型腔数量n:根据公式n<=(0.8Mg-Mj)/Mz,可得n<=(0.8*26-3.858)/0.305=55(个)为了经济效益及保证精度故作成一出八,则M(总)= 0.305*8+3.858=6.298g第二章模具结构2.1分型面的选择如下图所示,出于对模具结构、使用寿命、易于推出机构的设置、易于排气、模具加工的方便以及结合注塑机的技术规格(在设计中我已附带一份有关注塑机的技术规格书)等多方面原因考虑选择塑件的上表面为分型面。
2.2型腔型芯及浇口、流道的设计选用一模八腔布局,其型腔型芯部分布局及图纸已附,但有一点要说明,由于塑件很薄,为使开模时塑件留在动模侧,其动模侧部分脱模角是像到钩般反扣的。
如下局部放大图:由于塑件很薄且宽,为使塑料熔体在宽度方向流动得到更均匀的分配,减小内应力,避免流纹和定向效应,所以选用扇型浇口,浇口的厚度取塑件壁厚的2/3。
由于是一出八的结构所以要考虑选择哪种分流道为宜。
为使在相同情况下各型腔能同时注满,所以选择平衡式流道。
当然在保证必要的壁厚及注塑能饱满的情况下,我也尽可能的缩短了流程。
由于主流道部分在成型过程中,其小端入口处与注塑机喷嘴较高温度和压力的塑料熔体冷热交替地接触,很容易损坏,且对材料地要求较高,此模具为批量生产而设计,顾设计成浇口套(料嘴),便于日后更换。
导光板
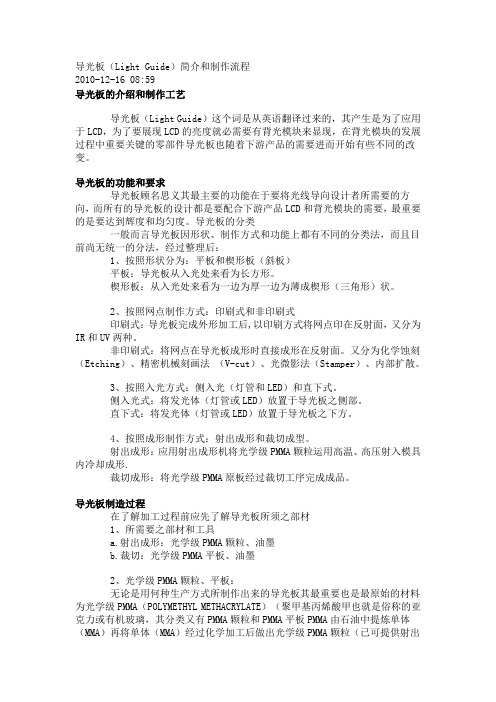
导光板(Light Guide)简介和制作流程2010-12-16 08:59导光板的介绍和制作工艺导光板(Light Guide)这个词是从英语翻译过来的,其产生是为了应用于LCD,为了要展现LCD的亮度就必需要有背光模块来显现,在背光模块的发展过程中重要关键的零部件导光板也随着下游产品的需要进而开始有些不同的改变。
导光板的功能和要求导光板顾名思义其最主要的功能在于要将光线导向设计者所需要的方向,而所有的导光板的设计都是要配合下游产品LCD和背光模块的需要,最重要的是要达到辉度和均匀度。
导光板的分类一般而言导光板因形状、制作方式和功能上都有不同的分类法,而且目前尚无统一的分法,经过整理后:1、按照形状分为:平板和楔形板(斜板)平板:导光板从入光处来看为长方形。
楔形板:从入光处来看为一边为厚一边为薄成楔形(三角形)状。
2、按照网点制作方式:印刷式和非印刷式印刷式:导光板完成外形加工后,以印刷方式将网点印在反射面,又分为IR 和UV两种。
非印刷式:将网点在导光板成形时直接成形在反射面。
又分为化学蚀刻(Etching)、精密机械刻画法(V-cut)、光微影法(Stamper)、内部扩散。
3、按照入光方式:侧入光(灯管和LED)和直下式。
侧入光式:将发光体(灯管或LED)放置于导光板之侧部。
直下式:将发光体(灯管或LED)放置于导光板之下方。
4、按照成形制作方式:射出成形和裁切成型。
射出成形:应用射出成形机将光学级PMMA颗粒运用高温、高压射入模具内冷却成形.裁切成形:将光学级PMMA原板经过裁切工序完成成品。
导光板制造过程在了解加工过程前应先了解导光板所须之部材1、所需要之部材和工具a.射出成形:光学级PMMA颗粒、油墨b.裁切:光学级PMMA平板、油墨2、光学级PMMA颗粒、平板:无论是用何种生产方式所制作出来的导光板其最重要也是最原始的材料为光学级PMMA(POLYMETHYL METHACRYLATE)(聚甲基丙烯酸甲也就是俗称的亚克力或有机玻璃,其分类又有PMMA颗粒和PMMA平板PMMA由石油中提炼单体(MMA)再将单体(MMA)经过化学加工后做出光学级PMMA颗粒(已可提供射出成形所始用),再将光学级PMMA颗粒用压铸法(Casting)或压出法(Injection)来制作光学级PMMA平板,目前业界所认同的PMMA制造商如下:(日)三菱丽阳Mitsubishi Rayon、(日)住友化学Sumitomo、(日)旭化成 Asahicasei、(日)库拉雷 Kuraray、(台)奇美化学、(韩)世和 Sehwa、3、油墨:分为UV和IR两种4、平板裁切导光板制作方式为三个部份:第一是压克力板外形加工;第二是网板制作;第三是印刷,其工序流程分别为a. 压克力外形加工=原板裁切〉镜面刨光〉成形加工。
导光板成型工艺

导光板成型工艺
导光板成型工艺是一种用于光学器件制造的重要工艺,它可以有效地改善光学器件的光学性能和使用效果。
导光板通常是由光学级材料制成的,具有高透明度和优良的光学性能,它可以将光线引导到需要的位置,提高光学器件的亮度和清晰度。
导光板的成型工艺主要包括材料选择、模具设计、注塑成型、后处理等步骤。
首先是材料选择,导光板通常采用光学级聚合物材料,如聚碳酸酯(PC)、聚甲基丙烯酸甲酯(PMMA)等,这些材料具有优异的光学性能和加工性能,能够满足导光板的制造要求。
接下来是模具设计,模具的设计直接影响导光板的成型质量和性能。
在模具设计中,需要考虑导光板的形状、尺寸、厚度等因素,保证导光板的光学表面光滑度和尺寸精度。
此外,还需要考虑模具的冷却系统,确保导光板成型过程中温度均匀分布,避免产生缺陷。
注塑成型是导光板成型工艺的关键步骤,通过将加热熔融的光学级材料注入到模具中,经过冷却凝固后得到导光板的成品。
在注塑成型过程中,需要控制注塑温度、压力和速度等参数,确保导光板的成型质量和表面光滑度。
最后是导光板的后处理,包括去除模具、修整边缘、热处理等步骤,以提高导光板的光学性能和稳定性。
通过后处理,可以进一步改善导光板的表面光滑度和透明度,确保其在光学器件中的应用效果。
总的来说,导光板成型工艺是一项复杂的工艺过程,需要在材料选择、模具设计、注塑成型和后处理等方面进行精心设计和控制。
只有通过科学合理的工艺流程和严格的质量控制,才能生产出具有优异光学性能和稳定性的导光板产品,满足不同光学器件的需求。
希望随着技术的不断进步和工艺的改进,导光板制造工艺能够实现更高的精度和效率,为光学器件的发展提供更好的支持和保障。
光学导光板工艺流程

光学导光板工艺流程一、原材料准备。
咱先来说说原材料的事儿。
光学导光板的原材料那可得精挑细选呢。
一般来说,会用到特殊的光学级塑料,这种塑料就像是导光板的灵魂伴侣一样重要。
它得有很好的透明度,就像清澈的水晶一样,这样才能保证光线在里面顺利地跑来跑去。
而且呀,这原材料的纯度也要高,不能有太多杂质,不然就像在干净的马路上突然出现好多小石子,会阻碍光线的传播呢。
在准备原材料的时候,供应商的选择也很关键哦。
要找那些靠谱的、口碑好的供应商,就像找好朋友一样,得能信任才行。
二、模具制作。
接下来就是模具制作啦。
模具就像是给导光板打造一个专属的小房子一样。
这个小房子的形状和尺寸可都是按照导光板的设计要求来的呢。
制作模具的师傅那可都是手艺高超的人,他们要把每一个细节都处理得妥妥当当。
模具的表面得光滑得像溜冰场一样,这样导光板成型的时候才不会被磕磕绊绊。
而且模具的精度要求也很高,稍微有一点偏差,导光板可能就会长得歪歪扭扭啦。
这就好比盖房子的时候,地基要是没打好,房子肯定就不稳当。
在这个过程中,设计师和模具师傅要不停地沟通,就像两个人在聊天一样,互相理解对方的想法,这样才能打造出完美的模具。
三、注塑成型。
然后就是注塑成型啦。
把准备好的原材料放到注塑机里,就像把小宝贝放进温暖的小摇篮一样。
注塑机这个大机器就开始工作啦,它会把原材料加热融化,然后按照模具的形状把融化的材料注进去。
这个过程就像是在做蛋糕一样,把面糊倒进模具里,然后等着它成型。
不过呢,注塑的时候温度和压力都要控制得刚刚好,温度太高了,材料可能就会变得太稀,像水一样流得到处都是,成型就失败了;温度太低了,材料又不容易流动,导光板就会有缺陷。
压力也是一样的道理,太大了可能会把模具撑坏,太小了导光板又不饱满。
这就需要操作人员特别细心,像照顾小婴儿一样照顾这个注塑过程。
四、光学处理。
注塑成型之后,导光板还需要进行光学处理呢。
这个光学处理就像是给导光板化妆一样,让它变得更漂亮更实用。
导光板成型工艺
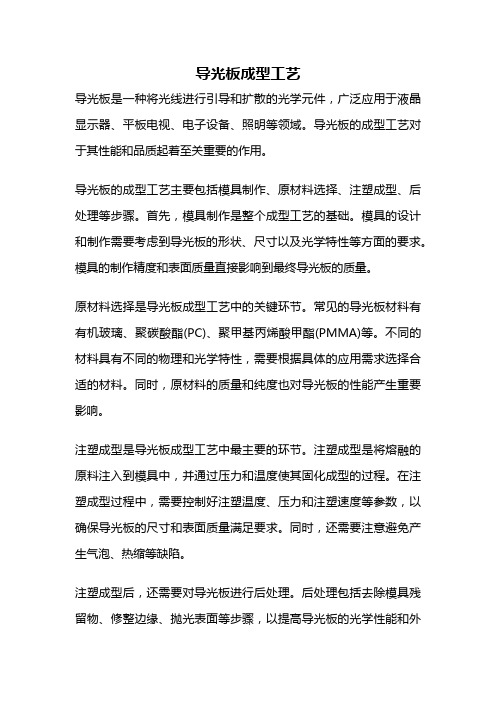
导光板成型工艺导光板是一种将光线进行引导和扩散的光学元件,广泛应用于液晶显示器、平板电视、电子设备、照明等领域。
导光板的成型工艺对于其性能和品质起着至关重要的作用。
导光板的成型工艺主要包括模具制作、原材料选择、注塑成型、后处理等步骤。
首先,模具制作是整个成型工艺的基础。
模具的设计和制作需要考虑到导光板的形状、尺寸以及光学特性等方面的要求。
模具的制作精度和表面质量直接影响到最终导光板的质量。
原材料选择是导光板成型工艺中的关键环节。
常见的导光板材料有有机玻璃、聚碳酸酯(PC)、聚甲基丙烯酸甲酯(PMMA)等。
不同的材料具有不同的物理和光学特性,需要根据具体的应用需求选择合适的材料。
同时,原材料的质量和纯度也对导光板的性能产生重要影响。
注塑成型是导光板成型工艺中最主要的环节。
注塑成型是将熔融的原料注入到模具中,并通过压力和温度使其固化成型的过程。
在注塑成型过程中,需要控制好注塑温度、压力和注塑速度等参数,以确保导光板的尺寸和表面质量满足要求。
同时,还需要注意避免产生气泡、热缩等缺陷。
注塑成型后,还需要对导光板进行后处理。
后处理包括去除模具残留物、修整边缘、抛光表面等步骤,以提高导光板的光学性能和外观质量。
后处理的质量和细节决定了导光板的最终品质。
导光板成型工艺的优化可以改善导光板的光学性能和制造效率。
通过合理调整注塑温度和压力等参数,可以降低导光板的内应力,减少光学畸变和色差。
同时,采用先进的模具制造技术和材料选择方法,可以提高导光板的表面光洁度和抗刮伤性能。
导光板成型工艺是影响导光板性能和品质的关键环节。
通过合理选择原材料、优化注塑成型参数以及精细的后处理,可以生产出高品质的导光板产品。
随着技术的不断进步和应用领域的拓展,导光板成型工艺也在不断创新和提升,为各行各业提供更好的光学解决方案。
- 1、下载文档前请自行甄别文档内容的完整性,平台不提供额外的编辑、内容补充、找答案等附加服务。
- 2、"仅部分预览"的文档,不可在线预览部分如存在完整性等问题,可反馈申请退款(可完整预览的文档不适用该条件!)。
- 3、如文档侵犯您的权益,请联系客服反馈,我们会尽快为您处理(人工客服工作时间:9:00-18:30)。
导光板和胶框注塑成型要点首先介绍导光板(Light Guide)的原理:导光板是利用光学级压克力板材吸取从灯发出来的光在光学级压克力板材表面的停留,当光线射到各个导光点时,反射光会往各个角度扩散,然后破坏反射条件由导光板正面射出。
通过各种疏密、大小不一的导光点,可使导光板均匀发光。
反射片的用途在于将底面露出的光反射回导光板中,用来提高光的使用效率。
一:导光板模具要点:○1根据产品大小及出模数和机台吨位确定模架尺寸。
○2顶出系统:制作中在顶针下的合理(备注:顶出平衡,顺利脱模)的情况下数量尽量放少,以降低生产中顶针发热膨胀烧死断裂的比例及多余的毛边(以胶框为重点)。
○3冷却系统(备注:主要保持模具恒温)务必做好,才可以保证生产一直正常。
○4排气系统(备注:主要是排除成型过程模腔的气体和树脂产生的气体,减少阻力,以防前端树脂烧焦或产生的气体脏污)位置要合理(光源处要大要多)及深度Z控制在0.03mm以下。
○5脱模系统:模具要有脱模斜度(斜度就产品结构及厚度而定),模具产品横切面需要经过省模抛光处理,以至生产中脱模正常。
○6冷料井必需要有深度Z控制在2—4mm,主要是藏射嘴前端一点冷胶。
○7胶框针点浇口位置、大小、数量要合理(这样可以控制到产品的尺寸、变形、局部毛边及成型难易度等)二:试模要点:○1首先确认产品图档和模具编码是否一致,再看产品大小来确定机台吨位及机台号码。
○2在模具稼动、合模力、顶针长度、机械手确认OK后,试模初步要避免撑模现象(这样对机器保养很好)首先把机器的射胶压力、速度相对调小一点、位置放大点,再根据经验判断产品的熔胶量不可以过大,然后再按成型情况慢慢调试就OK。
○3产品成型及外观OK后首要品管确认产品结构,然再尺寸及导光板光学效果。
○4试模过程中要注意以下细节:a:顶出是否正常(顶针长度,顶出平衡,弹簧力度),b:脱模是否顺畅(看有没有粘模现象)c:冷却循环流道是否通畅(是否漏水,有没有堵塞),d:成型是否困难排气系统是否OK,e:浇口位置、数量是否正确(主要针对胶框),f:产品是否变形(看是顶出不平衡、还是残余应力粘模引致),以上问题对能否生产顺利很是重要,需要及时跟模具部门沟通且尽快改善以备生产。
三:生产的不良和改善方案:A:胶框:○1料脆:a:首先考虑成型温度(210℃—280℃)是否正常(可以适当把温度降下来),b:然后看料的配比是否有问题(看是次料放的比例大了),c:看熔胶速度是否太快(螺杆转速太快那树脂剪切热就很容易上升,因为树脂融化60%来自剪切热)d:看射胶终止位置实际值是否很大(如果残余料太多留在射嘴(温度偏高)部很容易使树脂分解)减小熔胶位置就OK.○2变形:a:在模具脱模斜度和省模抛光OK的情况下,那就首先改善工艺参数(提高树脂温度《前提不要料脆》加大射胶速度、减小射胶压力,保压压力、背压、放大终止位置《保证尺寸OK 的情况下》还有一个参数很微妙就是要把第一段保压减小速度加快时间减到最小,但第二段压力就要加很大速度放慢时间相对是第一段的两倍),b:如果工艺参数无法改善的情况下就要分析模具问题(针点浇口位置、数量是否正确,顶出是否平衡《顶针数量是否合理》是否粘模等)c:还要注意产品堆放和运输的时候引起的变形○3产品内凹主要原因是残余应力引致的,a:就调机参数关键就要放在压力上考虑问题(近可能用最小的压力《射胶压力、保压压力》成型产品,特别是解压的最后一段压不可以大,b:如果是在产品中间内凹就好办(在中间加一个很小针点浇口就OK)○4尺寸问题:a:产品尺寸如果出现一边大一边小相差很大的情况下就要处理模具(进胶不均匀改浇口的位置,控制浇口大小)b:尺寸偏小:分下例几种情况:1:长度尺寸偏小(主要是放小终止位置效果明显,加大射胶压力,也可以适当加一点熔胶位置)偏大反之OK2:宽度尺寸偏小:(主要加大保压来改善效果明显,射胶压力加大,转保压切换位置放小)偏大反之就OK3:厚度尺寸偏小:(可以把合模力放小,射胶压力、保压加大,终止位置放小,速度放慢)偏大把合模力调大有很明显的效果,其他反之就OK)。
○5油污脏污:a:生产之前务必要模具部门清洗模具(每个细节很重要,特别是顶针部分)b:生产前要把机台清理干净(润滑系统油污,灰尘)重点是生产过程中的保持。
C:制作出来的产品经用美工刀修过毛边后需要经过超声(超声波里的清洗粉比例一定要到位)清洗(重点清洗完后产品上的水一定要烘干,)要不然综合以上两种情况就会出现产品部粘黑胶。
d:产品加工一切OK后装入吸塑盒及时盖上保护膜。
e:环境保持干净卫生,无尘也是很重要。
B:导光板:○1:产品尾部发黄:a:首要考虑料筒温度(260℃—350℃)是否过高《在保证效果尺寸的情况下可以降下来》b: 看熔胶速度是否太快(螺杆转速太快那树脂剪切热就很容易上升,因为树脂融化60%来自剪切热)《减小熔胶速度》c:再者考虑烘料温度(80℃—115℃)是否过高及烘料时间(一般3—4小时就OK)是否太长。
d:查看料筒和烘料机的感温线是否异常。
e: 看射胶终止位置实际值是否很大(如果残余料太多留在射嘴(温度偏高)部很容易使树脂分解)减小熔胶位置就OK.f:看生产周期是否太长《周期太长料就是在料筒停留时间太长引致树脂分解而发黄》缩短周期。
g:最后考虑原料是否出了问题。
○2尾部的厚度和光源的厚度有点相差:a:模具部门是在网点模芯在拿去腐蚀前磨模面垫的斜度不够引致。
b:保压压力太大和保压时间太长《可以全部减小》射胶压力减小,转保压切换位置加大。
○3光学效果:a:光源亮尾部暗:产品填充太满,射胶速度太快,终止位置太小,料筒温度、模具温度太高,《减小速度,放大终止位置,降低料筒、模具温度》如果是光源暗尾部亮反之就OK《附加:要加大射胶压力》b:锯齿主要是控制灯口效果:1灯口视觉效果暗就说明锯齿深度太深《可以用锯齿在台湾1000型号的砂纸上水平方向刷齿处理》2灯口视觉效果偏亮就说明锯齿深度太浅《一般是换齿处理,但我一般还可以采用把磨面可以磨粗,还可以喷砂处理来改善》3:如果光源视觉效果有射线,光斑,光速可以改变锯齿的角度来改善。
如果通过工艺参数调校,现场效果处理还不可以达到满意效果最后就需从新换咬花菲林方可达到效果。
○4变形:一般大尺寸(3.8寸—15寸)才会出现这种情况,这样的变形一般是模具温差引致《要很好的控制前后模的温度》,还解压来减小内应力效果会更好。
○5划伤:a:人为因素:1:作业员操作手法不正确,作业员的指甲划伤:2:放产品时出现重叠,触碰现象引致。
3:已包好产品存放不合理,堆太多,存放周转箱中的间隙太大引致运输过程的插伤。
b:夹臂程序没有调好操作中引致划伤。
C:顶出不平衡,产品触碰到顶针、模仁引致的划伤.d:模具上的固定划伤。
关键是在培训作业员的手法,灌输品质意识很是重要。
○6气纹:a:熔胶时排气不良(熔胶速度放慢,加大背压《背压不可以太大以防黑点》)。
b:模具排气不良,要求模具部门重新开排气槽。
c:射胶第一段速度太快,位置太大没有起到排气的作用。
d:中心主流道离产品距离太近,没有起到缓冲的作用。
○7暗斑(俗称夹线):就导光板来说主要是冷胶引致。
a:加深冷料井。
b:熔胶松退位置不合理可以相对加大松退位置。
C:要看暗斑位置可以采用多段射胶,是在暗斑的位置相对速度放慢就可以改善。
d:就胶框的夹线的处理方法就不同,那就要提高料温,加大压力,加快速度方可以改善。
四:机器设备检查及保养:○1锁模系统:a:通过观察模具闭合是否困难和运行中是否有震动来判断模板的平行度。
b:手动闭合模检查各活动部件是否有震动异常。
C:运转中点检各安全按钮、紧急停止及安全门是否在安全使用。
《重点安全第一》.○2射座部:a:料筒温度表是否与设定值相同,隔热罩是否松动,加热线绝缘层是否破裂,硬化。
b:射嘴有没有漏胶(每2个小时一次)螺杆尾部是否漏水及冷却效果是否良好。
○3每天必须对每台机器进行清扫《重点在于保持》○4润滑系统:a:每周一要看打油马达是否运转正常及润滑油的是否是在标准水平线。
○5机械手:a:运转中看气管有没有漏气,气压表是否是在标准气压(4—5个)之间。
b:定时排除过气阀过滤网内的水,检查缓冲器是否损坏、弹力够不够,看各个动作是否正常运转。
导光板发黄分析及处理导光板等透明塑料制件变色、发黄,主要是材料过热造成。
产生原因:A. 温度偏高, 电脑显示的温度比实际测量的温度有较大偏差.同时,也可以检查感温头是否有抵到感温孔底部,如果没有抵到的话,就会有这种情况.B. 排气不良. 射速太快,导致模具内的空气来不及排出,高压空气同样会使塑料变黄一、模具1)模具排气不良,高温高压下充模发生绝热压缩,塑料发生氧化。
2)浇注系统流道及进胶口的尺寸过小,在高温、高压下充模,发生过剪切作用而使塑料变色、发黄。
3)模具内不适当的油类润滑剂、脱模剂等附着在制品表面或氧化变色、发黄。
以下和机器有关C.螺杆压缩比不当,PC 料有低中高三种粘度的原料,要根据不同粘度的PC做相应的压缩比D. 螺杆,料管磨损,特别是计量段那边. 螺杆与料管内壁间隙增大,导致PC料滞留时间过长而偏黄E. 螺杆芯部强度不够,PC料粘度大,扭矩也大,造成螺杆弯曲与料管内孔磨擦升温. 熔胶时排气不良。