反应器压差升高原因分析及处理措施修订稿
反应器压差升高原因分析及处理措施

反应器压差升高原因分析及处理措施曹智勇摘要:本文结合蜡油加氢装置第一运行周期2012年度的生产运行现状和操作特点,分析了装置反应器压差升高的原因,并针对原因分析,提出了解决问题的办法和措施,为装置的长周期运行提供帮助。
关键词:蜡油加氢催化剂床层压降一、前言260万t/a蜡油加氢处理装置以Ⅱ、Ⅲ常减压装置轻、重蜡油以及焦化蜡油为原料,生产加氢蜡油、石脑油、精制柴油等产品,为公司催化裂化装置提供优质原料增产高品值汽油,提高公司经济效益。
从第一生产周期运行情况来看,精制蜡油的脱硫、脱氮率较高、残炭含量低,但是反应器压差上升过快的问题一直是困扰装置长周期运行的主要问题。
2010年10月和2012年10月因反应器压差达到工艺卡片规定最大值而进行催化剂撇头;2013年9月床层压差达到1.2MPa,装置被迫降量生产,处理量只能维持240t/h,远低于设计值310t/h。
反应器压差上升不仅降低了装置的处理能力,增加了装置的能耗,而且还缩短了生产周期,造成人力、物力的浪费。
二、反应器压差上升快的原因分析图1 2012年蜡加床层压降变化曲线图从蜡油加氢装置2012年度的生产运行情况看,整个反应器床层最高点温度未超410℃(设计末期温度426℃),各床层径向温差稳定<6℃,未出现突然升高的现象,生产过程较平稳,但反应器压差上升的趋势很快的(如图1),究其原因分析,导致的影响因素较多,结合生产实际状况我认为主要影响因素包括原料性质的变化,催化剂结焦,催化剂床层局部塌陷和操作异常波动等方面,具体原因分析如下。
2.1 原料性质对床层压降的影响原料性质是影响床层压降上升的主要原因。
由于原料中的杂质如重金属,沥青质,污染物等汇集在催化剂床层上部及床层空隙,当达到一定数量后,就会在催化剂上部形成一层高密度的滤饼或床层催化剂的孔隙率下降,堵塞流体流道,造成床层压降上升,所以对已装填完催化剂的床层来讲,空隙率已定,原料油中的杂质含量就很关键。
浅析加氢反应器压差增大原因及应对探讨

浅析加氢反应器压差增大原因及应对探讨本文我们主要针对加氢反应器压差增大的原因进行分析和研究,如果加氢反应器压差增大时会产生那些危害,我们根据实际情况找出解决加氢反应器压差增大的办法和措施,进一步保障加氢反应器不会因为压差增大问题影响正常运行,积累一些解决加氢反应器压差增大问题的经验,为原油加工效率和质量的提高做出贡献。
标签:加氢反应器;压差增大;原因目前我国的科技正在不断的发展进步,石油企业的发展促进了原油加工业的崛起,保障汽油和柴油从原油中加工出来的质量进一步提升,将原油中的有用材质提炼出来,我们大部分采取加氢反应器进行原油的处理工作,处理主要是将原油进行分离工作,将有用材质和杂质进行分离,保留有用的物质,排除杂质,加氢反应器的应用在原油的加工中使用的十分广泛,对原油加工的效率和质量都有很大程度的提升,床层的压差会因为加氢反应器长时间的工作而慢慢的加大,随着使用时间的越来越长,压差的增加会超过设备的承受能力,容易造成设备生产时出现安全隐患,设备的使用性能降低,设备被迫停止运行,影响工作效率。
我们结合实际操作将加氢反应器压差增大的原因进行分析和研究,总结出有效降低加氢反应器压差的措施,保障加氢反应器的正常运行,为原油的加工处理工作提供保障。
1 加氢反应器压差增大产生的危害加氢反应器在工作过程中压差增大,内部的氢含量在循环的时候容易逐渐减少,影响进料量也逐渐减少,降低设备在空中运行的速度,催化剂的利用率会受到设备在空中停留的时间比较长而产生的焦炭影响,导致焦炭的堆积;原料油会因为加氢反应器效率的降低而产生的承受压力减小,出现浓度下降,能源消耗量大;床层的结构和催化剂颗粒在加氢反应器压差增大的时候会出现损坏,床层的温度和受力也会不均匀,床层发生结构变形和坍塌,催化剂颗粒散失;下游中的物质出现的逆向和横向的流动不均匀,是因为加氢反应器的压差增大导致蒸汽不能有效的穿过催化剂床层,发生物质的混乱。
2 加氢反应器压差增大的原因分析2.1 原料油中材质的影响加氢反应器在运行的过程中,原料油中有的細小固体颗粒在经过过滤器的时候不容易被过滤出去,很多都聚集在催化剂的床层位置,时间长颗粒就会越聚越多,焦粉、铁锈等都会慢慢在容器中产生,夹杂在催化剂颗粒之间,最终导致反应器压差增大。
钴钼加氢反应器压差大的原因分析与处理
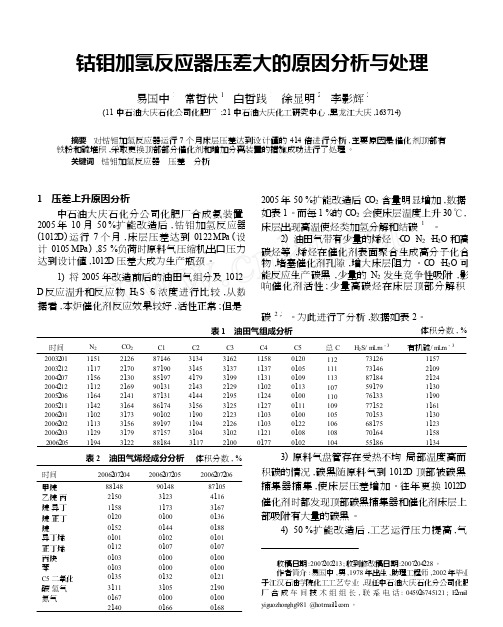
钴钼加氢反应器压差大的原因分析与处理易国中1 常哲伏1 白哲践1 徐显明2 李影辉2(11 中石油大庆石化公司化肥厂 ;21 中石油大庆化工研究中心 ,黑龙江大庆 ,163714)摘要 对钴钼加氢反应器运行 7 个月床层压差达到设计值的 414 倍进行分析 ,主要原因是催化剂顶部有 铁粉和硫堆积 ,采取更换顶部部分催化剂和增加分离装置的措施成功进行了处理 。
关键词 钴钼加氢反应器 压差 分析1 压差上升原因分析中石油大庆石化分公司化肥 厂 合 成 氨 装 置 2005 年 10 月 50 %扩能改造后 , 钴钼加氢反应器 (1012D ) 运行 7 个月 , 床层压差达到 0122 MPa ( 设 计 0105 MPa ) ,85 %负荷时原料气压缩机出口压力 达到设计值 ,1012D 压差大成为生产瓶颈 。
1) 将 2005 年改造前后的油田气组分及 1012 D 反应温升和反应物 H 2 S 、S 浓度进行比较 ,从数据看 ,本炉催化剂反应效果较好 ,活性正常 ; 但是2005 年 50 %扩能改造后 C O 2 含量明显增加 ,数据如表 1 。
而每 1 %的 C O 2 会使床层温度上升 30 ℃,床层出现高温使烃类加氢分解和结碳 1 。
2) 油田气带有少量的烯烃 、C O 、N 2 、H 2O 和高 碳烃等 ,烯烃在催化剂表面聚合生成高分子化合 物 ,堵塞催化剂孔隙 ,增大床层阻力 。
C O 、H 2O 可 能反应生产碳黑 ,少量的 N 2 发生竞争性吸附 ,影 响催 化 剂 活 性 ; 少 量 高 碳 烃 在 床 层 顶 部 分 解 积 碳2 ,3。
为此进行了分析 ,数据如表 2 。
表 1 油田气组成分析体积分数 , %H 2S/ m L ·m - 3N 2 CO 2 有机硫/ m L ·m - 3时间C1 C2 C3 C4 C5 总 C2003201 2003212 2004207 2004212 2005206 2005211 2006201 2006202 2006203 11511117 1156 1112 1164 1142 1102 1113 112921262170 2130 2169 2141 3164 3173 3156 3179 87146 87190 85197 90131 87131 86174 90102 89197 8715731343145 4179 2143 4144 3156 1190 1194 31043162 3137 3199 2129 2195 3125 2123 2126 3102 1158 1137 1131 1102 1124 1127 1103 1103 1121 01200105 0109 0113 0100 0111 0100 0122 0108 112111 113 107 110 109 105 106 108 7312673146 87184 59179 76133 77152 70153 68175 7016411572109 2124 1130 1190 1161 1130 1123 1158 200620511943122 8818431172100 0177 0102 104 5518611343) 原料气盘管存在受热不均 、局部温度高而积碳的情况 ,碳黑随原料气到 1012D 顶部被碳黑 捕集器捕集 , 使床层压差增加 。
重整二反压降过高的原因及整改措施
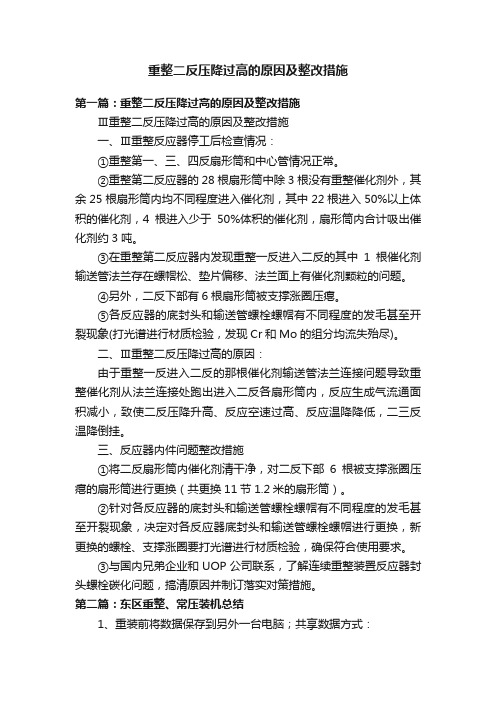
重整二反压降过高的原因及整改措施第一篇:重整二反压降过高的原因及整改措施Ⅲ重整二反压降过高的原因及整改措施一、Ⅲ重整反应器停工后检查情况:①重整第一、三、四反扇形筒和中心管情况正常。
②重整第二反应器的28根扇形筒中除3根没有重整催化剂外,其余25根扇形筒内均不同程度进入催化剂,其中22根进入50%以上体积的催化剂,4根进入少于50%体积的催化剂,扇形筒内合计吸出催化剂约3吨。
③在重整第二反应器内发现重整一反进入二反的其中1根催化剂输送管法兰存在螺帽松、垫片偏移、法兰面上有催化剂颗粒的问题。
④另外,二反下部有6根扇形筒被支撑涨圈压瘪。
⑤各反应器的底封头和输送管螺栓螺帽有不同程度的发毛甚至开裂现象(打光谱进行材质检验,发现Cr和Mo的组分均流失殆尽)。
二、Ⅲ重整二反压降过高的原因:由于重整一反进入二反的那根催化剂输送管法兰连接问题导致重整催化剂从法兰连接处跑出进入二反各扇形筒内,反应生成气流通面积减小,致使二反压降升高、反应空速过高、反应温降降低,二三反温降倒挂。
三、反应器内件问题整改措施①将二反扇形筒内催化剂清干净,对二反下部6根被支撑涨圈压瘪的扇形筒进行更换(共更换11节1.2米的扇形筒)。
②针对各反应器的底封头和输送管螺栓螺帽有不同程度的发毛甚至开裂现象,决定对各反应器底封头和输送管螺栓螺帽进行更换,新更换的螺栓、支撑涨圈要打光谱进行材质检验,确保符合使用要求。
③与国内兄弟企业和UOP公司联系,了解连续重整装置反应器封头螺栓碳化问题,搞清原因并制订落实对策措施。
第二篇:东区重整、常压装机总结1、重装前将数据保存到另外一台电脑;共享数据方式:a.在控制面板,管理工具里本地安全策略里,安全选项里:本地帐户的共享和安全模式改为经典模式,使用空白密码的本地帐户停用,来宾帐户状态启用。
b.用户权利指派中将拒绝从网络访问这台计算机Guest账户删除。
在运行里输入D0op52F$。
或E盘,D盘,就可打开。
c.共享的两台电脑Administrator取消密码。
反应器压差升高原因分析及处理措施

反应器压差升高原因分析及处理措施曹智勇摘要:本文结合蜡油加氢装置第一运行周期2012年度的生产运行现状和操作特点,分析了装置反应器压差升高的原因,并针对原因分析,提出了解决问题的办法和措施,为装置的长周期运行提供帮助。
关键词:蜡油加氢催化剂床层压降一、前言260万t/a蜡油加氢处理装置以Ⅱ、Ⅲ常减压装置轻、重蜡油以及焦化蜡油为原料,生产加氢蜡油、石脑油、精制柴油等产品,为公司催化裂化装置提供优质原料增产高品值汽油,提高公司经济效益。
从第一生产周期运行情况来看,精制蜡油的脱硫、脱氮率较高、残炭含量低,但是反应器压差上升过快的问题一直是困扰装置长周期运行的主要问题。
2010年10月和2012年10月因反应器压差达到工艺卡片规定最大值而进行催化剂撇头;2013年9月床层压差达到1.2MPa,装置被迫降量生产,处理量只能维持240t/h,远低于设计值310t/h。
反应器压差上升不仅降低了装置的处理能力,增加了装置的能耗,而且还缩短了生产周期,造成人力、物力的浪费。
二、反应器压差上升快的原因分析图1 2012年蜡加床层压降变化曲线图从蜡油加氢装置2012年度的生产运行情况看,整个反应器床层最高点温度未超410℃(设计末期温度426℃),各床层径向温差稳定<6℃,未出现突然升高的现象,生产过程较平稳,但反应器压差上升的趋势很快的(如图1),究其原因分析,导致的影响因素较多,结合生产实际状况我认为主要影响因素包括原料性质的变化,催化剂结焦,催化剂床层局部塌陷和操作异常波动等方面,具体原因分析如下。
2.1 原料性质对床层压降的影响原料性质是影响床层压降上升的主要原因。
由于原料中的杂质如重金属,沥青质,污染物等汇集在催化剂床层上部及床层空隙,当达到一定数量后,就会在催化剂上部形成一层高密度的滤饼或床层催化剂的孔隙率下降,堵塞流体流道,造成床层压降上升,所以对已装填完催化剂的床层来讲,空隙率已定,原料油中的杂质含量就很关键。
5-齐鲁分公司-石脑油加氢装置反应器床层差压快速上升原因分析及对策32-39--资料
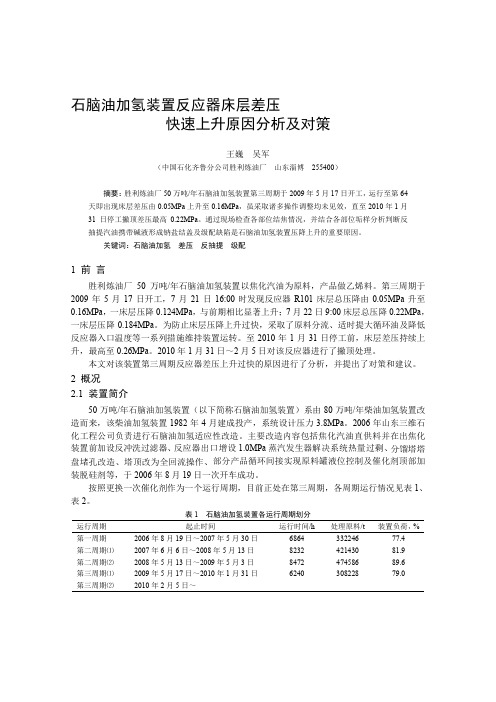
石脑油加氢装置反应器床层差压快速上升原因分析及对策王巍吴军(中国石化齐鲁分公司胜利炼油厂山东淄博255400)摘要:胜利炼油厂50万吨/年石脑油加氢装置第三周期于2009年5月17日开工,运行至第64天即出现床层差压由0.05MPa上升至0.16MPa,虽采取诸多操作调整均未见效,直至2010年1月31日停工撇顶差压最高0.22MPa。
通过现场检查各部位结焦情况,并结合各部位垢样分析判断反抽提汽油携带碱液形成钠盐结盖及级配缺陷是石脑油加氢装置压降上升的重要原因。
关键词:石脑油加氢差压反抽提级配1 前言胜利炼油厂50万吨/年石脑油加氢装置以焦化汽油为原料,产品做乙烯料。
第三周期于2009年5月17日开工,7月21日16:00时发现反应器R101床层总压降由0.05MPa升至0.16MPa,一床层压降0.124MPa,与前期相比显著上升;7月22日9:00床层总压降0.22MPa,一床层压降0.184MPa。
为防止床层压降上升过快,采取了原料分流、适时提大循环油及降低反应器入口温度等一系列措施维持装置运转。
至2010年1月31日停工前,床层差压持续上升,最高至0.26MPa。
2010年1月31日~2月5日对该反应器进行了撇顶处理。
本文对该装置第三周期反应器差压上升过快的原因进行了分析,并提出了对策和建议。
2 概况2.1 装置简介50万吨/年石脑油加氢装置(以下简称石脑油加氢装置)系由80万吨/年柴油加氢装置改造而来,该柴油加氢装置1982年4月建成投产,系统设计压力3.8MPa。
2006年山东三维石化工程公司负责进行石脑油加氢适应性改造。
主要改造内容包括焦化汽油直供料并在出焦化装置前加设反冲洗过滤器、反应器出口增设1.0MPa蒸汽发生器解决系统热量过剩、分馏塔塔盘堵孔改造、塔顶改为全回流操作、部分产品循环间接实现原料罐液位控制及催化剂顶部加装脱硅剂等,于2006年8月19日一次开车成功。
按照更换一次催化剂作为一个运行周期,目前正处在第三周期,各周期运行情况见表1、表2。
预加氢反应器压降增大原因分析及应对措施

预加氢反应器压降增大原因分析及应对措施预加氢反应器是炼油厂重要的装置之一,用于加工重质原油,将其转化为轻质产品。
在预加氢反应器中,加氢气通过催化剂和原料油进行反应,主要是加氢裂化、加氢脱硫和加氢脱氮等反应,将原料油中的硫、氮等杂质去除,提高产品的质量。
在反应过程中,反应器内部会发生一定的压降,如果压降增大,会影响设备的正常运行,甚至对生产造成严重影响。
预加氢反应器的压降增大原因分析及应对措施尤为重要。
一、压降增大原因分析1. 催化剂失活催化剂是预加氢反应器的关键组成部分,其活性直接影响反应器的运行性能。
由于长时间的使用和反应条件的变化,催化剂会逐渐失去活性,导致反应器的压降增大。
随着使用时间的增加,催化剂表面可能会产生积炭和焦炭,使得活性表面积减小,从而增大了反应器的压降。
2. 原料油中的杂质过多原料油中可能含有大量的硫、氮等杂质,这些杂质会在反应器中与加氢气发生反应,生成硫化氢、氨等气体,同时生成沉淀物质,引起催化剂的中毒和堵塞,从而增大了反应器的压降。
3. 反应器操作条件异常如果反应器操作条件发生异常,如温度升高、压力降低、进料质量流量变化等,都可能导致反应器内部发生异常反应或堵塞现象,从而增大了压降。
4. 反应器堵塞在预加氢反应器中,催化剂床和管道可能会出现堵塞现象,导致气液流动受阻,进而增大了反应器的压降。
二、应对措施1. 催化剂管理对催化剂进行定期检查和维护,及时更换失活的催化剂。
在更换催化剂时,应注意清除积炭和焦炭,恢复催化剂的活性表面积,减小压降。
2. 原料油预处理加强原料油的预处理,通过减少原料油中的硫、氮等杂质,可以减少反应器内部的异常反应,减小压降。
3. 反应器操作条件控制严格控制反应器的操作条件,避免发生异常情况,保证反应器内部的正常运行,减小压降。
4. 清洗反应器定期对反应器进行清洗,清除催化剂床和管道中的积垢和沉淀物质,保持反应器内部的畅通,减小压降。
5. 增加反应器冷却在反应器进料口增加冷却装置,可降低进料温度,减少异常反应的发生,从而减小压降。
催化重整装置预加氢反应器压差高的原因分析及对策
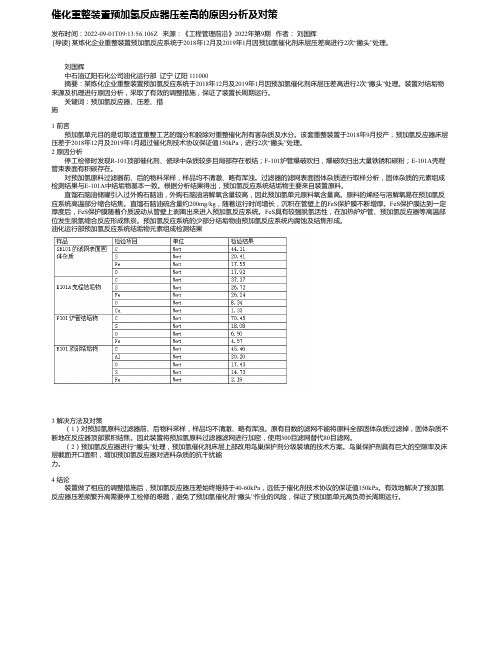
催化重整装置预加氢反应器压差高的原因分析及对策发布时间:2022-09-01T09:13:56.106Z 来源:《工程管理前沿》2022年第9期作者:刘国辉[导读] 某炼化企业重整装置预加氢反应系统于2018年12月及2019年1月因预加氢催化剂床层压差高进行2次“撇头”处理。
刘国辉中石油辽阳石化公司油化运行部辽宁辽阳 111000摘要:某炼化企业重整装置预加氢反应系统于2018年12月及2019年1月因预加氢催化剂床层压差高进行2次“撇头”处理。
装置对结垢物来源及机理进行原因分析,采取了有效的调整措施,保证了装置长周期运行。
关键词:预加氢反应器、压差、措施1 前言预加氢单元目的是切取适宜重整工艺的馏分和脱除对重整催化剂有害杂质及水分。
该套重整装置于2018年9月投产,预加氢反应器床层压差于2018年12月及2019年1月超过催化剂技术协议保证值150kPa,进行2次“撇头”处理。
2 原因分析停工检修时发现R-101顶部催化剂、瓷球中杂质较多且局部存在板结;F-101炉管爆破吹扫,爆破吹扫出大量铁锈和碳粉;E-101A壳程管束表面有积碳存在。
对预加氢原料过滤器前、后的物料采样,样品均不清澈、略有浑浊。
过滤器的滤网表面固体杂质进行取样分析,固体杂质的元素组成检测结果与E-101A中结垢物基本一致。
根据分析结果得出,预加氢反应系统结垢物主要来自装置原料。
直馏石脑油储罐引入过外购石脑油,外购石脑油溶解氧含量较高,因此预加氢单元原料氧含量高。
原料的烯烃与溶解氧易在预加氢反应系统高温部分缩合结焦。
直馏石脑油硫含量约200mg/kg,随着运行时间增长,沉积在管壁上的FeS保护膜不断增厚。
FeS保护膜达到一定厚度后,FeS保护膜随着介质波动从管壁上剥离出来进入预加氢反应系统。
FeS具有较强脱氢活性,在加热炉炉管、预加氢反应器等高温部位发生脱氢缩合反应形成焦炭。
预加氢反应系统的少部分结垢物由预加氢反应系统内腐蚀及结焦形成。
预加氢反应器压降增大原因分析及应对措施

预加氢反应器压降增大原因分析及应对措施预加氢反应器是炼油厂重要的设备之一,主要用于将石脑油中的硫、氮等杂质物质进行加氢处理,以便降低产品的环境污染性和提高产品质量。
预加氢反应器在运行过程中常常会出现压降增大的情况,这对设备的正常运行和生产效率会造成很大的影响。
本文将对预加氢反应器压降增大的原因进行分析,并提出应对措施,以期为相关行业人士提供一些参考和借鉴。
1. 反应器填料积垢预加氢反应器中常采用填料来增加反应表面积,促进反应物质的接触和反应。
填料表面容易积聚杂质物质,如沉积物、焦炭等,导致填料孔隙度和传质性能下降,从而增大了反应器的压降。
2. 气液分离不完全预加氢反应器在反应过程中产生的气体和液体混合物需要进行分离,以便再次进入反应器进行反应。
如果气液分离不完全,就会导致反应器内气体流通受阻,压降增大。
3. 反应器堵塞在运行中,预加氢反应器管道、阀门、换热器等部位会因为焦炭、沉积物等杂质物质的堆积而发生堵塞,造成流体流通不畅,从而使得压降增大。
4. 反应物料变质反应器内的反应物料,如加氢催化剂、氢气等,由于长期使用或受到杂质的影响,可能会发生变质,使得反应活性降低,反应速率减慢,从而导致压降增大。
5. 设备老化预加氢反应器作为重要设备,长期的运行使用会使得设备本身产生老化现象,如管道漏气、设备结构变形等,进而影响了气体和液体的流通,导致压降增大。
二、应对措施1. 加强预防性维护定期对预加氢反应器进行清洗、检修、更换填料等维护工作,保持设备的清洁和正常运行状态,以预防填料积垢和设备堵塞的问题发生。
2. 优化气液分离系统改进气液分离设备和工艺,提高分离效率,确保反应气体和液体能够有效分离,减少气液混合物对反应器运行的影响。
3. 加强监测和检测通过安装质量传感器和巡视设备,定期进行设备运行监测,一旦发现反应器压降增大的情况,及时进行检测分析,找出问题的原因。
4. 优化操作工艺合理控制加氢反应器的操作参数,如温度、压力、流量等,以最大程度地减少设备运行对填料和催化剂的影响,确保反应器处于最佳运行状态。
柴油加氢装置反应器压降升高原因分析及解决措施

置停工。分别从原料、垢物、催化剂等方面排查分析,确定造成压降快速升高的主要原因为:
系统内存在硫化亚铁腐蚀;DCC 轻油的多
环芳烃含量较高,易引起缩合生焦副反应,在系统内沉积,垢物和缩合物形成黏糊状结垢物,
随原料油进入反应器,积聚在催化剂床层,造成压降升高。通过对进料换热器、加热炉等系统
爆破吹扫、冷油冲洗、更换新鲜催化剂及新型进料分配盘等措施,装置开工运行正常。
关键词:柴油加氢;反应器;压降;原因;措施
中图分类号:TE966
文献标识码:B
文章编号:1671-4962(2021)01-0025-04
Cause analysis and solutions for reactorpressure drop rise of diesel hydrogenation unit
某公司 240×104 t/a 柴油加氢装置采用大连 (抚顺)石油化工研究院(FRIPP)的加氢改质异构 降凝工艺技术,选用 FRIPP 研发的加氢改质异构 降凝配套催化剂。装置于 2013 年投产,主要加工 常压直馏柴油,冬季生产-10#低凝柴油,夏季生产 5#柴油。2020 年 4 月大检修后,5 月 11 日、17 日装 置 2 次开工过程中,均出现反应器床层压降快速升 高而被迫停工。大检修期间,FHUDS-6 精制剂和 FC-20 改质异构降凝催化剂进行再生,同时为解决 装置冬季生产低凝柴油时加热炉负荷大的问题, 在第 3 床层装填部分 FDW-3 临氢降凝催化剂。 1 反应器压降升高情况
炼油与化工
2021 年 第 1 期
REFINING AND CHEMICAL INDUSTRY
25
柴油加氢装置反应器压降升高原因分析及解决措施
薛瑶瑶,田金光,王万里,徐西娥
评价试验反应器压降升高的原因分析及对策
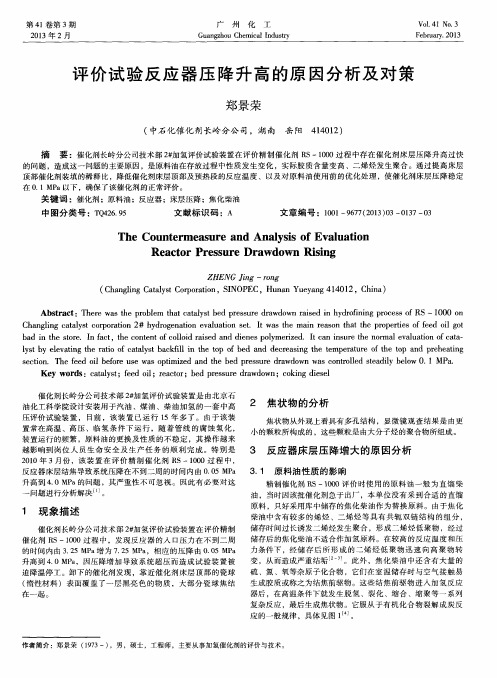
( 中石化催 化 剂 长岭 分公 司 ,湖 南 岳阳 4 1 4 0 1 2 )
摘 要 :催化剂长岭分公司技术部 2 # 加氢评价试验装置在评价精制催化剂 R S 一1 0 0 0 过程中存在催化剂床层压降升高过快
的问题 ,造成这一 问题 的主要原 因 ,是原料油在存放过程 中性质发 生变化 ,实 际胶质含量 变高 、二烯 烃发生聚 合。通 过提高 床层 顶 部催 化剂装填 的稀释 比 ,降低催化 剂床层顶部及预热段 的反应温度 、以及对原 料油使用 前的优化 处理 ,使催化剂 床层压 降稳定
在0 . 1 MP a以下 ,确油 ;反应器;床层压降;焦化柴油
中 图分 类号 :T Q 4 2 6 . 9 5
文 献标 识码 :A
文 章编 号 :1 0 0 1 — 9 6 7 7 ( 2 0 1 3 ) 0 3 — 0 1 3 7 — 0 3
压评价试 验装置 , 目前 ,该 装 置 已运行 1 5年 多 了。由于该 装 置常在 高温 、高压 、临氢条 件 下运 行 ,随 着管 线 的腐蚀 氢 化 , 装置运行 的频繁 ,原料油的更换及 性质 的不稳定 ,其操作 越来
2 焦 状 物 的 分 析
焦状 物从外观上看具有多孑 L 结构 ,显微镜 观查结 果是 由更 小 的颗粒 所构成的 ,这些颗粒是 由大分子烃 的聚合物所 组成。
Th e Co u n t e r me a s u r e a n d An a l y s i s o f Ev a l u a t i o n
Re a c t o r Pr e s s u r e Dr a wdo wn Ri s i ng
Z HE NG in r g— — r o n g
柴油加氢装置反应器压降升高原因分析及解决措施

柴油加氢装置反应器压降升高原因分析及解决措施发布时间:2021-06-02T06:17:18.417Z 来源:《中国科技人才》2021年第9期作者:武小丽[导读] 某石油企业的180万吨/年柴油加氢装置,采用中石化开发的SRH液相循环加氢技术。
玉门油田炼油厂加氢车间甘肃酒泉 735200摘要:目前,柴油加氢装置经过长周期运行面临的一个重要问题,由于目前国内同类装置较少,可借鉴经验不多,本文主要讨论柴油加氢装置反应器压降升高原因,并提出一些建议措施,希望可以对柴油加氢装置长周期生产提供参考。
关键词:柴油加氢装置;反应器;压降升高1 柴油加氢装置特点某石油企业的180万吨/年柴油加氢装置,采用中石化开发的SRH液相循环加氢技术。
装置于2018年12月建成投产,产品硫质量分数小于10μg/g,符合国Ⅴ柴油标准。
本装置主要技术特点:(1)SRH技术采用独特的供氢系统,在新鲜原料进入反应器前,将所需的氢气溶解在进料中,同时循环油中含有大量的饱和氢,用于加氢处理反应,由于取消循环氢系统,装置能耗较低,装置在标定时,能耗仅为267.10MJ/t,仅相当于传统滴流床工艺能耗的一半左右,节能效果明显。
(2)催化剂完全浸泡在柴油中,脱硫脱氮等加氢过程直接在全液相床层中反应,提高了催化剂的利用效率,由于循环油的比热容比循环气大很多,因而大大地降低了反应床层的温升,并可降低裂化等副反应,反应氢耗较低。
(3)由于反应器温升较小,使反应器在更接近于等温的条件下操作,可以延长催化剂的使用寿命。
2 项目概况柴油加氢装置运行两年后,出现了故障,企业于2021年1月大检修后,2月5日、15日装置2次开工过程中,均出现反应器床层压降快速升高而被迫停工。
大检修期间,FHUDS-6精制剂和FC-20改质异构降凝催化剂进行再生,同时为解决装置冬季生产低凝柴油时加热炉负荷大的问题,在第3床层装填部分FDW-3临氢降凝催化剂。
3 压降升高情况3月5日,装置具备进料条件后开始进料,进料量为90t/h,穿透床层后在16 min内进料量提至180 t/h,反应器床层总压降由0.241MPa上升至0.59MPa,其中第1床层压降由0.121MPa上升至0.50MPa,之后,通过多次适当升温、降量调整操作,仍无法解决压降高问题,而且压降有缓慢升高趋势。
重整反应进料板式换热器压差异常升高原因分析及应对措施
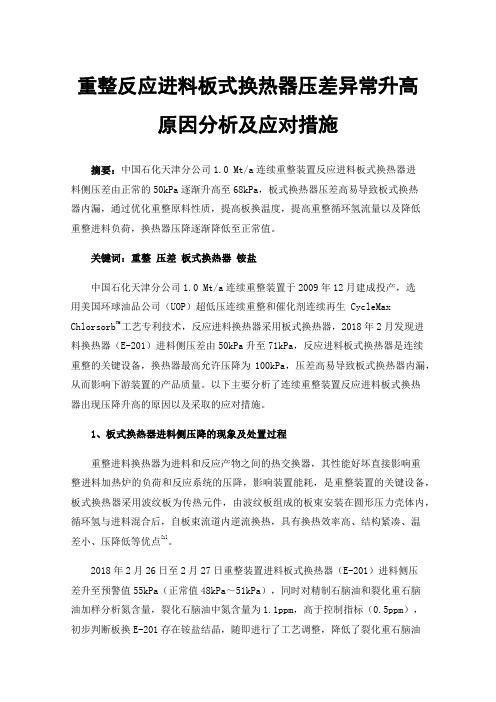
重整反应进料板式换热器压差异常升高原因分析及应对措施摘要:中国石化天津分公司1.0 Mt/a连续重整装置反应进料板式换热器进料侧压差由正常的50kPa逐渐升高至68kPa,板式换热器压差高易导致板式换热器内漏,通过优化重整原料性质,提高板换温度,提高重整循环氢流量以及降低重整进料负荷,换热器压降逐渐降低至正常值。
关键词:重整压差板式换热器铵盐中国石化天津分公司1.0 Mt/a连续重整装置于2009年12月建成投产,选用美国环球油品公司(UOP)超低压连续重整和催化剂连续再生 CycleMax Chlorsorb TM工艺专利技术,反应进料换热器采用板式换热器,2018年2月发现进料换热器(E-201)进料侧压差由50kPa升至71kPa,反应进料板式换热器是连续重整的关键设备,换热器最高允许压降为100kPa,压差高易导致板式换热器内漏,从而影响下游装置的产品质量。
以下主要分析了连续重整装置反应进料板式换热器出现压降升高的原因以及采取的应对措施。
1、板式换热器进料侧压降的现象及处置过程重整进料换热器为进料和反应产物之间的热交换器,其性能好坏直接影响重整进料加热炉的负荷和反应系统的压降,影响装置能耗,是重整装置的关键设备,板式换热器采用波纹板为传热元件,由波纹板组成的板束安装在圆形压力壳体内,循环氢与进料混合后,自板束流道内逆流换热,具有换热效率高、结构紧凑、温差小、压降低等优点[1]。
2018年2月26日至2月27日重整装置进料板式换热器(E-201)进料侧压差升至预警值55kPa(正常值48kPa~51kPa),同时对精制石脑油和裂化重石脑油加样分析氮含量,裂化石脑油中氮含量为1.1ppm,高于控制指标(0.5ppm),初步判断板换E-201存在铵盐结晶,随即进行了工艺调整,降低了裂化重石脑油进装置量,重整负荷由124t/h降至114t/h,同时循氢量由78000Nm3/h提高至83000Nm3/h、换热器进料温度由99℃提高至110℃。
加氢反应器压差增大原因及处理对策
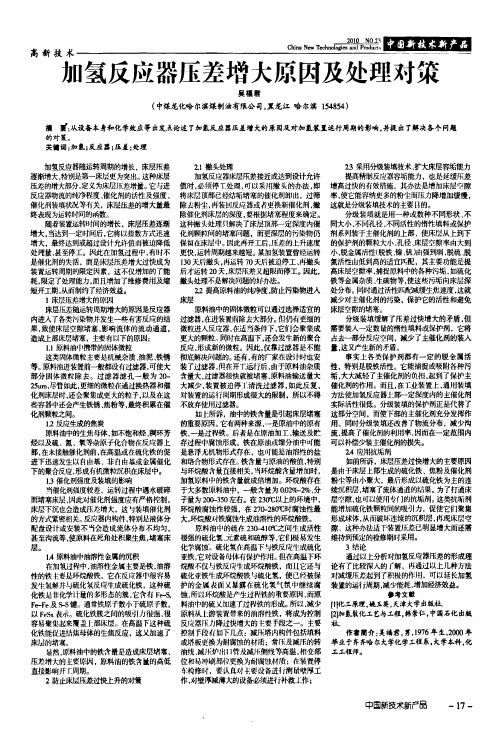
”采用分级装填技术、扩大床层容垢能力 提高精制反应器容垢能力。也足延缓压差 增高过快的有效措施,其办法是增加床层窄隙 率.使它能容纳更多的粉尘而压力降增加缓慢, 这就是分级装填技术的主要目的。 分级装填就是用一种或数种不同形状、不 同大小、不同孔径、不同活性的惰性填料或保护 剂系列装于主催化剂的上部、使床层从上到下 的保护剂的颗粒大小、孔径、床层空隙牢由大到 小,脱金属活 性( 脱铁、镍、钒) 由强到弱 ,脱硫、脱 氮活性由低到高的适宜匹配,其主要功能足提 高床层空隙率.捕捉原料中的各种污垢,如硫化 铁等金属杂质、生碳物等.使这些污垢向床层深 处分布。同时通过活性匹配减缓生焦速度,这就 减少对主催化剂的污染,保护它的活性和避免 床层 空隙 的堵塞 。 分级装填缓解了压差过快增大的矛盾,但 需要装入一定数最的惰性填料或保护剂,它将 占去一部分反应空间,减少了主催化剂的装入 量,这 又产生新的矛 盾。 事实 上各类 保护剂 都有 一定的 脱金属 活 性。特别是脱铁活性。它能捕捉或吸附各种污 垢,大大减轻了主催化剂的负担.起到了保护主 催化剂的作用。而且.在工业装置上,通用装填 方法使加氢反应器上部一定深度内的主催化剂 实际活性很低。分级装填的保护剂正是代替了 这部分空间,而使下部的主催化剂充分发挥作 用。同时分级装填还改善了物流分布,减少沟 流,提高了催化剂的利用率,因而在一定范围内 可以补偿少装主催化剂的损失。 2. 4应用 抗垢 剂 如前所诉,床层压差过快增大的主要原因 是由于床层上部生成的硫化铁、焦粉及催化剂 粉尘等由小聚大.最后形成以硫化铁为主的连 续{冗积层,堵塞了流体通道的结果。为了打通床 层窄隙,也可以使用专门的抗垢剂。这类抗垢剂 能增加硫化铁颗粒间的吸引力,促使它们聚集 形成球体,从而破坏连续的沉积层,再现床层宅 隙。这种办法适于装置压差已明显增大而还需 维持到预定的检修期时采用。 3结论 通过 以上 分析 x于力 Ⅱ氢 反应器 压差 的形 成理 论有了比较深入的厂解,f 耳通过以上几种方法 对减缓压蔗起到了积极的作用.可以延长加氢 装置 的运行 周期, 减少 能耗, 增加经 济效益 。
预加氢反应器压降增大原因分析及应对措施

预加氢反应器压降增大原因分析及应对措施预加氢反应器是燃料加氢过程中的核心设备之一,其内部氢气压力的控制对加氢过程的效率和安全性具有重要影响。
但在实际运行中,预加氢反应器常常出现压降增大的问题,影响了加氢装置的正常运行。
本文将从原因分析和应对措施两个方面,对预加氢反应器压降增大问题进行探讨。
一、原因分析1. 活性炭堵塞:预加氢反应器中常使用活性炭作为催化剂载体,但长时间运行后,活性炭往往存在堵塞的问题。
堵塞会导致气体流动受阻,气体通道断裂,从而增加气体流通过程中的阻力,进而导致压降增大。
2. 催化剂失活:预加氢反应器中的催化剂往往会因为杂质的存在、积灰、温度过高等因素而失活。
催化剂失活后,反应效率降低,起不到催化作用,从而导致压降增大。
3. 温度过高:预加氢反应器中温度过高会导致催化剂的失活和活性炭的烧结,从而影响反应器的正常运行。
高温也会引起氢气的体积膨胀,增加气体流通的阻力,进一步导致压降增大。
4. 压力波动:预加氢反应器内气体的压力波动也会导致压降增大。
压力波动会引起气体流通速度的变化,进而影响气体流通的阻力,导致压降增大。
二、应对措施1. 定期进行清洗:定期对预加氢反应器进行清洗,特别是对活性炭进行清洗,以防止其堵塞。
可以使用蒸汽、酸碱或超声波等方法对反应器进行清洗,提高气体流通的畅通度,减小压降增大的程度。
2. 催化剂管理:定期更换催化剂,防止其失活。
在更换催化剂之前,可以进行一些试验性的活化处理,以提高催化剂的活性和使用寿命。
3. 控制温度:采取降低温度的措施,例如增加冷却介质的流量或采用辅助冷却装置。
合理控制反应器的温度,避免高温热源对催化剂和活性炭的影响,减小压降增大的风险。
4. 压力稳定:采取措施降低气体压力的波动,例如增加反应器的操作稳定性,保持进料压力的稳定等。
减小压力波动可以减小压降增大的程度,提高反应器的运行效率和稳定性。
预加氢反应器压降增大问题的原因主要包括活性炭堵塞、催化剂失活、温度过高和压力波动等。
加氢反应器压差增大原因分析及处理措施
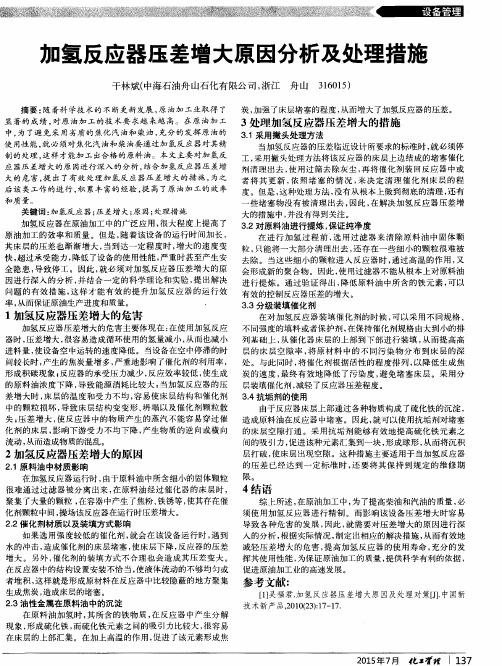
加氢反应器压差增大原 因分析 及处 理措施
干林 斌 ( 中海 石 油舟 山石化 有 限公 司 , 浙江
摘要: 随着科 学技 术 的不 断更 新发展 , 原 油加 工业取 得 了
舟山
3 1 6 0 1 5 )
炭, 加强 了床层堵塞 的程度 , 从而增大 了加氢反应 器的压差 。
显 著 的成 绩 , 对原 油加 工的技 术要 求越 来越 高 。在 原 油加 工 3处理 加氢 反应器压差增大的措施 中, 为 了避 免采 用 劣质 的焦化 汽 油和 柴油 , 充 分 的发 挥 原 油的 3 . 1 采 用撇 头处 理方 法 使 用性能 , 就 必须对 焦化 汽 油和柴 油要 通过加 氢反应 器对其精 当加 氢反 应器的 压差临近 设计 所要求 的标 准时 , 就 必须停 制的处理 , 这样 才 能加 工 出合 格 的原 料油 。本文主要 对加 氢反 工 , 采用撇 头处理 方法将 该反应 器的 床层上边 结成 的堵塞 催化
应 器压差增 大的 原 因进行 深入 的分析 , 结合 加氢反应 器压 差增 剂清 理 出去 , 使 用过 筛去 除灰 尘 , 再 将催 化剂 装 回反应 器 中或 大的危 害 。 提 出了有效 处理加 氢反 应 器压 差增 大的措 施 , 为之 者 将 其更 新 , 依 照堵 塞 的 情 况 , 来 决 定 清 理 催化 剂 床 层 的 程 后 该 类工作 的进 行 , 积 累丰 富的 经验 , 提 高 了原 油加 工的 效 率 度 。但是 , 这种 处理方 法 , 没有从 根本上 做到彻 底的清理 , 还有
催化重整装置预加氢反应器压降升高原因分析及处理措施

· 232 ·
Hale Waihona Puke 本文主要通过对预加氢反应器压降增大是由于结垢物对压降的影响杂质对压降的影响循环氢纯度的影响原料方面因素的影响还有反应温度操作压力空速的工艺条件影响以及催化剂破碎对压降的影响提出了针对这些原因的一些处理措施
区域治理
调查与发现
催化重整装置预加氢反应器压降升高原因分析及处理措施
杨柏林王艳涛 辽阳石化公司芳烃厂,辽宁辽阳111003
摘要:本文主要通过对预加氢反应器压降增大是由于结垢物对压降的影响、杂质对压降的影响、循环氢纯度的影响、原料方面因素的 影响,还有反应温度、操作压力、空速的工艺条件影响,以及催化剂破碎对压降的影响,提出了针对这些原因的一些处理措施。
关键词:预加氢系统;压降;原因分析;措施
催化重整装置的预加氢反应器是固定 床反应器.它的催化剂床层实质是过滤床。 根据过滤原理可知,随着大量的粉末被截 留在催化剂颗粒间的空隙,床层的空隙越 来越小。在对预加氢催化剂进行多次的过 筛处理并采取措施之后,压降过大的情况 有效改善。
作: 1炉管炭化处理和蒸汽吹扫主要用于燃
烧炉管内的焦炭,防止焦炭在正常生产过 程中进入反应器。
2增加预加氢反应器顶部的污染篮。保 护剂和主催化剂装载量。将反应器顶部污 物篮从原来的18增加到24。增加过滤面积. 并将杂质沉积在系统中。污垢篮不会大量 进入催化剂床。
3在线水冲洗预加氢反应产物热交换器 的阀门。氯化铵和硫化铵很容易溶于水。 将压力注入管道中以加压,溶解并消除结 晶塞。铵盐不能沉积在低温部分。
一、预加氢反应器压降增大的原因分析 1原料分析 1.1结垢物对压降的影响 在处理预加氢反应器压降的增加并分 析其原因时.我们可以首先检查并分析原 料油的组成。一般来说,预加氢体系中原 料油含量较高的组分主要是S和N。在我 们清理预加氢反应器的同时,我们会发现 大量的污染物质。结焦物主要由烯烃聚合 物组成,由腐蚀设备中由非烃化合物引发 的聚合反应产生,所述非烃化合物也包含 硫的次要组分,然后生成FeS。 1.2杂质对压降的影响 预加氢反应体系中的原料含有更多的 S和N。加氢反应后。S和N产生H2S和 NH3。这两种物质可以进一步反应成(NH4) 2S。如果原料中的杂质在进料过程中仍然 含有CI。则预加氢反应后会产生HCI。最 后HCl和NH3生成NH4CI。预加氢补充氢 气中硫含量高达99.6mg/g,易生成硫化 铵盐。此外,原料油可能含有金属杂质如砷, 铅和铜,它们容易还原成金属并附着在催 化剂上,这大大降低了催化剂的活性并进 一步导致堵塞,导致增加的压力预氢化反 应器。 1.3循环氢纯度的影响 循环氢纯度反应氢气分压。在氢纯度 过低或氢含量波动的情况下,预加氢反应 过程会受到影响。然而,预加氢反应不能 有效地完成。这将增加产生的焦炭量,并 最终导致预氢化反应器压降的增加。 2工艺条件
催化重整预加氢反应器压降过高的原因分析及对策
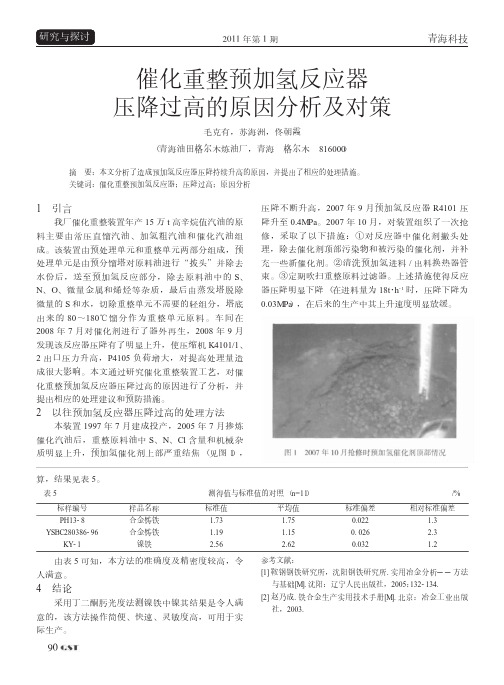
压 降 不 断 升高, 2007 年 9 月 预 加 氢反 应 器 R4101 压 降升至 0.4MPa。2007 年 10 月,对装置组织了一次抢 修 , 采 取 了 以 下 措 施 : ① 对 反 应 器 中 催 化 剂 撇 头处 理,除去催化剂顶部污染物和被污染的催化剂,并补 充一些新催化剂。②清洗预加 氢进料 / 出料 换热器管 束 。③定期吹扫 重整原料 过滤 器 。 上 述 措 施 使 得 反 应 器压降明显下降 ( 在进料量为 18t · h- 1 时,压降下降为 0.03MPa ),在后来的生产中其上升速度明显放缓。
机网协调的一个关键。本文通过对发电厂同期操作的分析,提出了有关发电机并网过程中值得重视的几个问题,对提高 发电厂同期装置的自动化水平和并网操作质量具有一定参考价值。 关键词:发电厂;同期操作;自动化;并网
1
引言
发电机并网是一项既简单又事关重大的操作。说
2
以往预加氢反应器压降过高的处理方法
本装置 1997 年 7 月建 成 投 产, 2005 年 7 月 掺 炼
催 化 汽 油 后 ,重 整 原 料 油 中 S、 N、 Cl 含 量和 机 械 杂 质明显上升,预加氢催 化剂上部严 重结焦 ( 见图 1 ), 算,结果见表 5。
表5 标样编号 PH13- 8 YSBC280386- 96 KY- 1 样品名称 合金铸铁 合金铸铁 镍铁 测得值与标准值的对照 ( n=11 ) 标准值 1.73 1.19 2.56 平均值 1.75 1.15 2.62 参考文献: [1] 鞍钢钢铁研究所,沈阳钢铁研究所. 实用冶金 分析 ── 方 法 与基础[M]. 沈阳:辽宁人民出版社,2005: 132- 134. [2] 赵 乃 成 . 铁 合 金 生产实 用 技术 手 册 [M]. 北 京 : 冶 金 工业 出版 社,2003. 标准偏差 0.022 0. 026 0.032 /% 相对标准偏差 1.3 2.3 1.2 图1 2007 年 10 月抢修时预加氢催化剂顶部情况
某水泥厂SCR脱硝反应器压差升高原因及对策
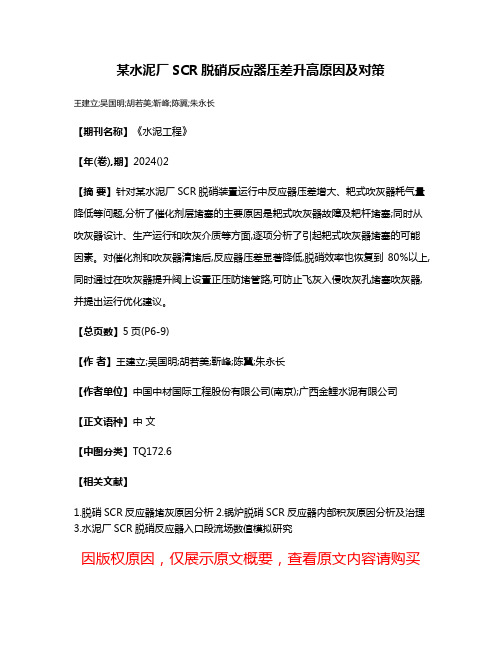
某水泥厂SCR脱硝反应器压差升高原因及对策
王建立;吴国明;胡若美;靳峰;陈翼;朱永长
【期刊名称】《水泥工程》
【年(卷),期】2024()2
【摘要】针对某水泥厂SCR脱硝装置运行中反应器压差增大、耙式吹灰器耗气量降低等问题,分析了催化剂层堵塞的主要原因是耙式吹灰器故障及耙杆堵塞;同时从吹灰器设计、生产运行和吹灰介质等方面,逐项分析了引起耙式吹灰器堵塞的可能因素。
对催化剂和吹灰器清堵后,反应器压差显著降低,脱硝效率也恢复到80%以上,同时通过在吹灰器提升阀上设置正压防堵管路,可防止飞灰入侵吹灰孔堵塞吹灰器,并提出运行优化建议。
【总页数】5页(P6-9)
【作者】王建立;吴国明;胡若美;靳峰;陈翼;朱永长
【作者单位】中国中材国际工程股份有限公司(南京);广西金鲤水泥有限公司
【正文语种】中文
【中图分类】TQ172.6
【相关文献】
1.脱硝SCR反应器堵灰原因分析
2.锅炉脱硝SCR反应器内部积灰原因分析及治理
3.水泥厂SCR脱硝反应器入口段流场数值模拟研究
因版权原因,仅展示原文概要,查看原文内容请购买。
- 1、下载文档前请自行甄别文档内容的完整性,平台不提供额外的编辑、内容补充、找答案等附加服务。
- 2、"仅部分预览"的文档,不可在线预览部分如存在完整性等问题,可反馈申请退款(可完整预览的文档不适用该条件!)。
- 3、如文档侵犯您的权益,请联系客服反馈,我们会尽快为您处理(人工客服工作时间:9:00-18:30)。
反应器压差升高原因分析及处理措施WEIHUA system office room 【WEIHUA 16H-WEIHUA WEIHUA8Q8-反应器压差升高原因分析及处理措施曹智勇摘要:本文结合蜡油加氢装置第一运行周期2012年度的生产运行现状和操作特点,分析了装置反应器压差升高的原因,并针对原因分析,提出了解决问题的办法和措施,为装置的长周期运行提供帮助。
关键词:蜡油加氢催化剂床层压降一、前言260万t/a蜡油加氢处理装置以Ⅱ、Ⅲ常减压装置轻、重蜡油以及焦化蜡油为原料,生产加氢蜡油、石脑油、精制柴油等产品,为公司催化裂化装置提供优质原料增产高品值汽油,提高公司经济效益。
从第一生产周期运行情况来看,精制蜡油的脱硫、脱氮率较高、残炭含量低,但是反应器压差上升过快的问题一直是困扰装置长周期运行的主要问题。
2010年10月和2012年10月因反应器压差达到工艺卡片规定最大值而进行催化剂撇头;2013年9月床层压差达到,装置被迫降量生产,处理量只能维持240t/h,远低于设计值310t/h。
反应器压差上升不仅降低了装置的处理能力,增加了装置的能耗,而且还缩短了生产周期,造成人力、物力的浪费。
二、反应器压差上升快的原因分析图1 2012年蜡加床层压降变化曲线图从蜡油加氢装置2012年度的生产运行情况看,整个反应器床层最高点温度未超410℃(设计末期温度426℃),各床层径向温差稳定<6℃,未出现突然升高的现象,生产过程较平稳,但反应器压差上升的趋势很快的(如图1),究其原因分析,导致的影响因素较多,结合生产实际状况我认为主要影响因素包括原料性质的变化,催化剂结焦,催化剂床层局部塌陷和操作异常波动等方面,具体原因分析如下。
原料性质对床层压降的影响原料性质是影响床层压降上升的主要原因。
由于原料中的杂质如重金属,沥青质,污染物等汇集在催化剂床层上部及床层空隙,当达到一定数量后,就会在催化剂上部形成一层高密度的滤饼或床层催化剂的孔隙率下降,堵塞流体流道,造成床层压降上升,所以对已装填完催化剂的床层来讲,空隙率已定,原料油中的杂质含量就很关键。
混合原料中的氮含量、残炭含量、重金属含量随焦化蜡油量的增加而上升,原料性质随之变差。
焦化蜡油掺炼量较大时,原料过滤器压差上升快,切换频繁,不得不开副线。
焦化蜡油中的焦粉等杂质直接进入反应器。
短时间内对反应器床层压差产生了不良的影响。
反应器一床层压差随焦化蜡油掺炼比例的增加而快速上升。
图2 2012年原料量及焦蜡掺炼比从图2的数据可以看出2012年1-4月焦化蜡油掺炼比较低,平均在以下。
从表1的数据可以看出1-4月混合原料的性质在2012年全年中处于较好的水平,从图3中可以看出,1-4月反应器一床层压差较为稳定,一直处于左右。
自5月开始逐步提高焦化蜡油的掺炼比率,原料的性质随之变差,反应床层压差开始上升。
反应器一床层压差由(250t/h进料)开始上升,至9月份备料结束以后,一床层压差上升至 MPa(260t/h进料)。
10月份焦化蜡油掺炼比例有所下降,但混合进料性质未明显改善,10月9日处理量降至最低180t/h,但是一床层压差仍然达到了,装置停工,进行催化剂撇头工作。
图3 2012年反应器一床层压差变化其中FIC1014A为反应总进料量,PDI1204A为反应器一床层压差单位限定值1月2月3月4月5月6月7月8月9月10月11月12月氮含量mg/kg≯20001718 1450 1487 1590 1732 2010 2381 2058 1976 1828 1609 1651 残炭%(m/m) ≯1铁mg/kg ≯镍mg/kg≯2 2钒mg/kg钙mg/kg表1 2012年各月混合原料平均氮含量、残炭、重金属含量分析原料过滤器的运行对床层压降的影响原料中的污染物需要在原料进入反应器前脱掉,在蜡油加氢装置实际生产过程中,原料过滤器是一台关键的设备,从当前实际而言,应用于加氢装置的过滤器,要求将原料携带的>25μm的杂质除去,脱除率一般要求达到98%,以保证进入反应器的原料尽可能的洁净。
本装置设计选用了国产的自动反冲洗过滤器,投用后,进行了颗粒分析,>25μm颗粒的脱除率为%,但由于原料性质差过滤器差压大,长期开副线运行,使得部分原料没有经过原料过滤器而进入原料缓冲罐,使得带入反应器的杂质量大大增加,影响很大。
催化剂装填对床层压降的影响催化剂装填过程中形成的床层空隙率也是决定决定床层压力降大小的一个关键因素,包括装填方式和催化剂本身特性。
从装填方式的角度分析,对于相同容积的反应器,催化剂采用密相装填时,相对于布袋装填方式,床层空隙率要下降5-7个单位,在实际生产中,床层压力降相应增加。
催化剂本身物性,如粒径的不同在床层形成的空隙率也就不同,如果催化剂装填不良和催化剂强度差,粉尘多,装置投产后催化剂粉碎而引起床层压降急剧上升,往往表现在床层中部和底部堵塞,由于现在催化剂生产厂提供的催化剂具有足够的强度,所以因催化剂强度差而引起的床层压降上升实际生产中是很少见的;但由于支撑瓷球强度不够,在实际生产中破碎,细粉很可能会堵塞床层空隙,造成床层压降上升。
内构件的影响反应器中的内构件对床层压降产生不良影响主要有以下几种情况:一,对物料均匀分配作用的内构件,如入口扩散器,冷氢箱等,如果该部分内构件分配效果不佳,引起床层偏流或者沟流,极易在床层产生热点,使物料在死角处积聚生焦,堵塞床层,造成床层压降升高。
二,对催化剂床层支撑作用的内构件,如果该部分内构件存在强度不够,安装质量问题造成各隔栅之间填充物脱落使隔栅间隙增大,隔栅和其他内构件的膨胀量相差较大,造成床层塌陷,出现上层催化剂落入下层入口冷氢箱或者床层的现象,影响物流均匀分配和流动,造成床层压降升高。
三,出口收集器,如果催化剂或者瓷球强度不够,在生产中出现粉碎,会使得大量粉末集中在出口收集器的丝网上,从而缩小出口收集器的流通面积,造成床层压降升高。
操作参数变化的影响在实际生产中,反应操作参数的变化对床层压力降也有一定的影响,如进料量,循环氢纯度,循环量,循环比,原料带水等。
比如,2013年5月~10月的时间里,装置处理量达246t/h,总体积空速达h,主剂体积空速值达到h,远高于国内同类蜡加装置的主剂体积空速值(h)。
过高的空速将积累在第一床层的粉尘向下带入第二床层,因第二床层装填的催化剂堆积密度远高于第一床层,导致二床层压降远高于第一床层。
所以进料量增大,循环氢纯度降低,循环量增大都会使床层压降即刻表现出增大的趋势,但随着操作参数的优化,又会降低而趋于平稳,所以,生产中要关注操作参数的变化,正确分析床层压降的变化原因。
目前国内外固定床加氢装置都十分重视对催化剂床层压力降的控制,并在实际生产中摸索出了一些值得借鉴的经验和方法,结合蜡油加氢装置的实际情况,针对以上原因我认为可采取以下措施。
三针对催化剂床层压降增长过快制定的相应措施严格控制原料性质原料性质是引起床层压降增加的主要原因,故此要加强原料在生产,贮存,运输过程中的管理和控制。
具体方法有:(1)精心操作常减压装置,重视减压侧线腐蚀工作,严格控制干点和残炭,有效的降低减压馏分fe离子含量和沥青质含量。
(2)原料罐应采用氮气或者其他惰性气体来气封,防止原料油和空气接触,馏分油在60~90℃下与空气中的氧及罐铁壁反应,生成胶质等大分子低聚物,进入反应器后缩合生焦。
有实验证明,VGO在同样温度,时间,在空气环境下储存,其残炭比在氮封环境下储存的残炭大4~7倍。
(3)对装置供原料油线应考虑防腐或材质升级,有效降低原料fe离子含量,2012年10月13日原料罐VGO分析fe离子含量μg/g,进装置前分析含量为μg/g,增加了一倍,主要原因是原料酸值高,达到g,在输送过程中产生了腐蚀。
随着我厂加工原油的变化,腐蚀情况不容忽视。
做好过滤器运行的操作对于原料过滤器,要保证>25μm杂质脱除率在95%以上,原料进入反应器前,要严格过滤,严禁开过滤器的副线,加强对过滤器的操作运行情况的检查,定期抽芯检查等,降低过滤器的切换频率,保证过滤器的正常工作,尽可能防止机械杂质带入床层。
提高装置催化剂床层的容垢能力在催化剂装填时,就要考虑床层的容垢能力,增加床层的空隙率。
国内外普遍采用的分级装填技术就是为了解决这一课题。
分级装填就是用一种或者数种不同形状,不同大小,不同孔径,不同活性的惰性填料或者保护剂列装在精制反应器上部,使得床层从上到下形成尺寸和床层空隙率由小到大,脱金属活性由低到强,脱硫脱氮活性由低到高的适宜匹配,从而达到提高床层空隙率,使污垢分散在整个床层,提高床层的容垢能力的目的。
据国外加氢装置经验,当床层有效空隙率减少到20~25%时,床层压降就达到临界点,此时压降呈指数曲线上升。
对不同形状的催化剂,可利用的空隙率也不同,有效空隙率高的,不仅床层起始压降低,而且相应可以容纳较多污垢,延长达到极限压力降的时间。
内构件安装的改进通过本次床层压差的出现和停工处理,充分说明反应器内构件的安装的重要性,安装时应注意以下几点:(1)冷氢管与隔栅圆孔应当有极好的同心度,防止因膨胀量不同出现间隙偏差。
(2)冷氢管与隔栅圆孔之间间隙中在填装充物前,可考虑增加底部托盘或者焊接固定物,进一步降低间隙。
(3)各隔栅之间增铺与内构件相同材质的不锈钢丝网,防止隔栅间填充物脱漏。
(4)各层次间卸料连通管应尽量整管安装,如果分节安装,必须考虑下部一节插入下一床层的深度应具备足够的下落余量。
优化工艺控制,平稳操作加强对操作人员的技能培训及平稳率的考核力度,严格按照工艺操作规程的要求进行生产操作,保证反应温度,反应压力,进料量,循环氢纯度,循环量等关键参数的平稳控制。
尽可能减少装置紧急停车等事故造成的催化剂冲击,破碎。
四总结与改进在日常生产中我们应严格按照上述5方面来指导工作,目前反应器床层压降升高后,装置一般在操作上多采取降量、降低掺炼,加强原料性质控制减少直供料等手段来调整生产,床层压降过高时一般对反应器是进行撇头处理。
撇头操作中,要根据床层某一深度下粉尘含量<1%作为终止撇头的条件,由于反应器压降涉及整个催化剂床层总的有效空隙率,撇头后,会将更深层的污染物保留在床层中,床层压力降上升很快,导致开工周期越来越短,所以,撇头处理只是解决床层压降高时不得已而为之的办法。
因而我们在工作中要从原料的源头抓起,精心操作,加强动静设备监控和岗位技术练兵等方面的工作,不断提高业务技能适应现代化生产企业的要求。
加氢精制作为石油深加工的重要手段,对提高重油加工率和产品质量有十分重要的作用。
随着我国石化工业的发展以及对石油产品的需求结构变化,加氢工艺得到了快速发展和广泛应用。
因此对这样一套操作难度大,工艺条件苛刻的生产装置,希望通过以上对反应器压降增大的因素及所采取的措施分析,为我们在日后的生产过程中提供一些切实有效的方法,给蜡油加氢装置长周期运行提供保障。