压铸车间生产现场管理18022553
压铸车间现场管理规定
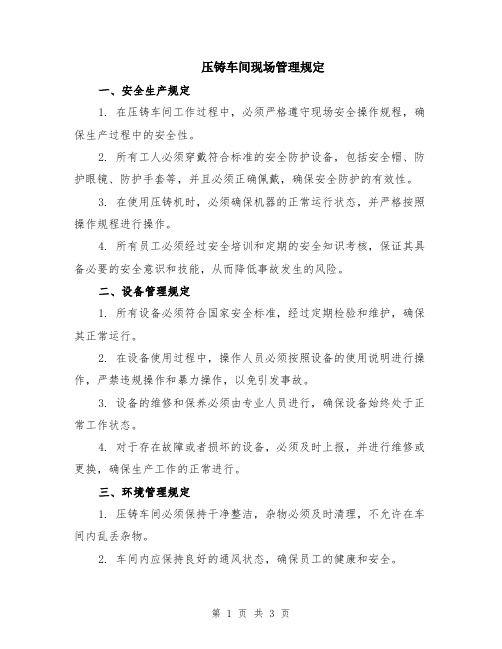
压铸车间现场管理规定一、安全生产规定1. 在压铸车间工作过程中,必须严格遵守现场安全操作规程,确保生产过程中的安全性。
2. 所有工人必须穿戴符合标准的安全防护设备,包括安全帽、防护眼镜、防护手套等,并且必须正确佩戴,确保安全防护的有效性。
3. 在使用压铸机时,必须确保机器的正常运行状态,并严格按照操作规程进行操作。
4. 所有员工必须经过安全培训和定期的安全知识考核,保证其具备必要的安全意识和技能,从而降低事故发生的风险。
二、设备管理规定1. 所有设备必须符合国家安全标准,经过定期检验和维护,确保其正常运行。
2. 在设备使用过程中,操作人员必须按照设备的使用说明进行操作,严禁违规操作和暴力操作,以免引发事故。
3. 设备的维修和保养必须由专业人员进行,确保设备始终处于正常工作状态。
4. 对于存在故障或者损坏的设备,必须及时上报,并进行维修或更换,确保生产工作的正常进行。
三、环境管理规定1. 压铸车间必须保持干净整洁,杂物必须及时清理,不允许在车间内乱丢杂物。
2. 车间内应保持良好的通风状态,确保员工的健康和安全。
3. 压铸车间内的垃圾、废弃物等需要分类处理,确保环境的卫生,并减少对环境的污染。
4. 在压铸过程中产生的废水、废气等需要按照相关规定进行处理,不得违规排放,损害环境。
四、员工管理规定1. 对于压铸车间的员工,必须进行合理的分工,明确各自的责任和职责。
2. 在工作过程中,员工必须严格按照操作规程进行操作,确保产品质量和生产工艺的稳定性。
3. 车间内严禁私自加班、夜间作业和危险动作,必须按照规定的工作时间进行工作。
4. 压铸车间的员工应保持团队合作和互助精神,共同维护良好的工作环境和生产秩序。
五、品质管理规定1. 在压铸车间进行生产过程中,必须按照品质管理规定进行操作,确保产品质量的稳定性。
2. 对于生产过程中出现的异常情况,必须及时上报,并采取相应的措施进行处理,确保产品的合格率。
3. 对于生产出的不合格品,必须进行正确的处理和记录,并对不合格品进行追踪,确保问题的及时解决和防范。
压铸生产现场管理规定(3篇)
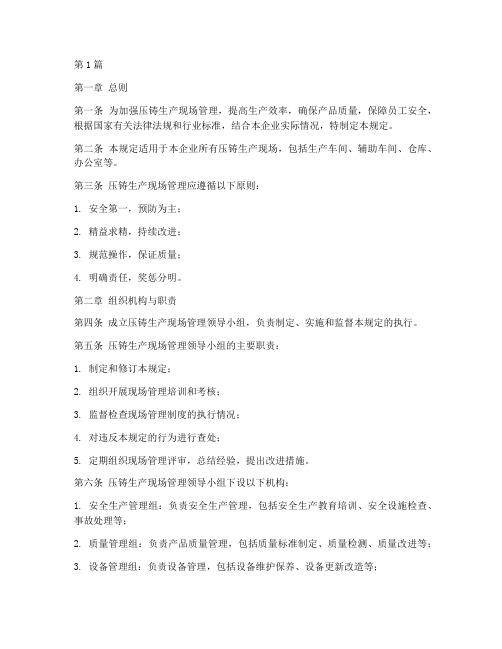
第1篇第一章总则第一条为加强压铸生产现场管理,提高生产效率,确保产品质量,保障员工安全,根据国家有关法律法规和行业标准,结合本企业实际情况,特制定本规定。
第二条本规定适用于本企业所有压铸生产现场,包括生产车间、辅助车间、仓库、办公室等。
第三条压铸生产现场管理应遵循以下原则:1. 安全第一,预防为主;2. 精益求精,持续改进;3. 规范操作,保证质量;4. 明确责任,奖惩分明。
第二章组织机构与职责第四条成立压铸生产现场管理领导小组,负责制定、实施和监督本规定的执行。
第五条压铸生产现场管理领导小组的主要职责:1. 制定和修订本规定;2. 组织开展现场管理培训和考核;3. 监督检查现场管理制度的执行情况;4. 对违反本规定的行为进行查处;5. 定期组织现场管理评审,总结经验,提出改进措施。
第六条压铸生产现场管理领导小组下设以下机构:1. 安全生产管理组:负责安全生产管理,包括安全生产教育培训、安全设施检查、事故处理等;2. 质量管理组:负责产品质量管理,包括质量标准制定、质量检测、质量改进等;3. 设备管理组:负责设备管理,包括设备维护保养、设备更新改造等;4. 环境管理组:负责环境保护管理,包括废水、废气、固体废弃物处理等。
第三章生产现场管理要求第七条安全生产管理1. 严格执行国家安全生产法律法规和行业标准;2. 建立健全安全生产责任制,明确各级人员的安全职责;3. 加强安全生产教育培训,提高员工安全意识和技能;4. 定期开展安全检查,及时发现和消除安全隐患;5. 做好事故报告、调查和处理工作。
第八条质量管理1. 严格执行国家产品质量法律法规和行业标准;2. 制定和实施质量管理体系,确保产品质量;3. 加强原材料、半成品、成品的质量检测;4. 对不合格产品进行追溯和整改;5. 定期开展质量评审,持续改进质量管理体系。
第九条设备管理1. 严格执行设备管理制度,确保设备正常运行;2. 定期对设备进行维护保养,及时发现和排除故障;3. 做好设备档案管理,确保设备信息的准确性和完整性;4. 加强设备更新改造,提高生产效率;5. 定期对设备进行检查,确保设备安全、可靠、高效。
压铸车间生产管理制度(5篇)
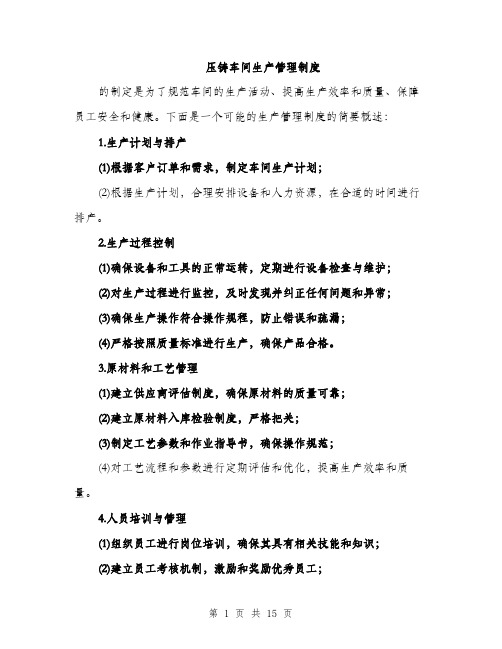
压铸车间生产管理制度的制定是为了规范车间的生产活动、提高生产效率和质量、保障员工安全和健康。
下面是一个可能的生产管理制度的简要概述:1.生产计划与排产(1)根据客户订单和需求,制定车间生产计划;(2)根据生产计划,合理安排设备和人力资源,在合适的时间进行排产。
2.生产过程控制(1)确保设备和工具的正常运转,定期进行设备检查与维护;(2)对生产过程进行监控,及时发现并纠正任何问题和异常;(3)确保生产操作符合操作规程,防止错误和疏漏;(4)严格按照质量标准进行生产,确保产品合格。
3.原材料和工艺管理(1)建立供应商评估制度,确保原材料的质量可靠;(2)建立原材料入库检验制度,严格把关;(3)制定工艺参数和作业指导书,确保操作规范;(4)对工艺流程和参数进行定期评估和优化,提高生产效率和质量。
4.人员培训与管理(1)组织员工进行岗位培训,确保其具有相关技能和知识;(2)建立员工考核机制,激励和奖励优秀员工;(3)制定安全操作规程,培训员工遵守安全规定,保证工作场所的安全和健康。
5.生产数据分析与改进(1)收集和分析生产数据,了解生产状况和问题;(2)定期召开生产会议,讨论生产问题并制定改进措施;(3)建立改进机制,持续优化生产流程,提高生产效率和质量。
以上只是一个简要的压铸车间生产管理制度的概述,实际制定时需要根据具体情况进一步细化和完善。
压铸车间生产管理制度(二)是指为了保证生产安全、提高生产效率和质量,加强管理和监督,规范车间内的工作流程和操作规范,制定的一系列管理措施和规定。
1. 人员管理:a. 严格按照招聘标准和程序,选拔、录用、培训、评价和奖惩员工;b. 设定工作岗位职责和权限,明确岗位要求和工作标准;c. 建立考勤制度和绩效考核制度,根据考核结果进行奖惩;d. 提供必要的安全防护设备和培训,确保员工身体健康和安全。
2. 安全管理:a. 制定生产安全管理制度,包括操作规程、事故应急预案等;b. 定期进行安全检查,发现问题及时整改,确保生产设备和环境安全;c. 加强职业健康和安全教育培训,提高员工的安全意识和自我保护能力。
压铸车间生产现场的管理制度
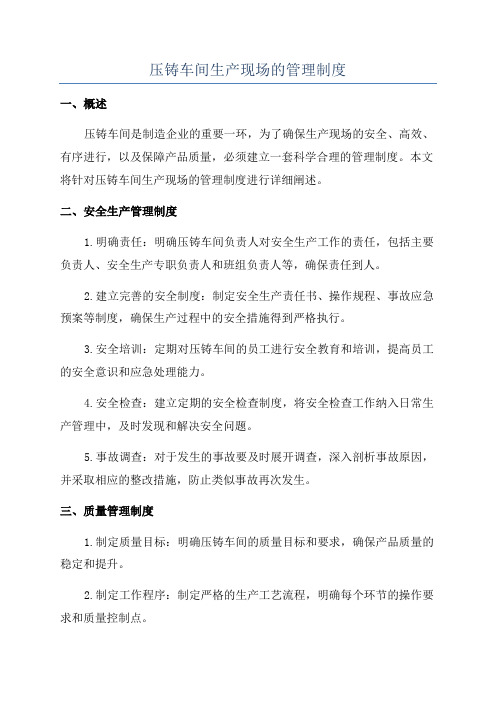
压铸车间生产现场的管理制度一、概述压铸车间是制造企业的重要一环,为了确保生产现场的安全、高效、有序进行,以及保障产品质量,必须建立一套科学合理的管理制度。
本文将针对压铸车间生产现场的管理制度进行详细阐述。
二、安全生产管理制度1.明确责任:明确压铸车间负责人对安全生产工作的责任,包括主要负责人、安全生产专职负责人和班组负责人等,确保责任到人。
2.建立完善的安全制度:制定安全生产责任书、操作规程、事故应急预案等制度,确保生产过程中的安全措施得到严格执行。
3.安全培训:定期对压铸车间的员工进行安全教育和培训,提高员工的安全意识和应急处理能力。
4.安全检查:建立定期的安全检查制度,将安全检查工作纳入日常生产管理中,及时发现和解决安全问题。
5.事故调查:对于发生的事故要及时展开调查,深入剖析事故原因,并采取相应的整改措施,防止类似事故再次发生。
三、质量管理制度1.制定质量目标:明确压铸车间的质量目标和要求,确保产品质量的稳定和提升。
2.制定工作程序:制定严格的生产工艺流程,明确每个环节的操作要求和质量控制点。
3.质量检测:建立完善的质量检测制度,包括对原材料的入库检测、生产过程中的监控检测以及最终产品的出厂检测等。
4.异常处理:对于生产中出现的异常情况,包括产品不良、设备故障等,要及时进行处理并记录,以便后续的分析和改进。
四、设备管理制度1.设备保养:建立设备保养计划,定期对设备进行保养、维修和检修,确保设备的正常运行。
2.设备检查:定期开展设备检查工作,对设备进行安全检查和性能检测,及时发现并处理设备存在的问题。
3.设备使用规范:制定设备使用规范,对操作人员进行培训,确保设备的正常使用和保养。
五、生产计划管理制度1.编制生产计划:根据市场需求和企业资源,合理编制生产计划,确保生产任务的顺利完成。
2.生产进度监控:建立生产进度监控机制,定期进行生产进度的汇报和分析,及时调整生产计划,以确保交货期的完成。
3.异常处理:对于生产过程中出现的异常情况,如设备故障、原材料短缺等,要及时进行处理,采取相应措施保证生产任务的完成。
压铸车间现场管理制度[2]
![压铸车间现场管理制度[2]](https://img.taocdn.com/s3/m/53299fcbe43a580216fc700abb68a98271feac2e.png)
压铸车间现场管理制度1. 背景和目的为了提高压铸车间的现场管理水平,确保生产安全和质量稳定,订立本管理制度。
本制度旨在明确压铸车间现场管理的规范要求,确保生产作业依照标准进行,有效监督和管理生产流程。
2. 适用范围本制度适用于公司压铸车间的全部工作人员,包括压铸车间的管理人员、操作工以及技术人员。
3. 管理标准3.1 现场秩序管理1.压铸车间内应保持乾净有序,材料、设备和工具放置到指定位置,禁止乱堆乱放。
2.禁止在压铸车间内吸烟,吃饭和热闹。
3.压铸车间内不得擅自调整设备、工艺参数或使用不合格的材料。
3.2 安全管理1.遵守压铸车间相关的安全操作规程,使用个人防护装备,确保工作安全。
2.定期进行安全培训,提高员工的安全意识和应急处理本领。
3.谙习并严格执行压铸车间的事故防备和应急措施,确保适时有效的处理各类突发事件。
3.3 设备管理1.确保设备在正常工作状态下使用,对设备进行定期检查和维护,确保设备的安全牢靠性。
2.配备专职维护和修理人员,适时处理设备故障和维护和修理需求。
3.4 品质管理1.压铸车间严格依照产品工艺流程操作,确保产品质量。
2.定期对产品进行质量检查和抽样检测,确保产品符合相关标准要求。
3.加强产品非合格品处理和追踪,防止不合格品流入下道工序。
3.5 生产计划与调度管理1.严格依照生产计划组织生产作业,确保按时交付。
2.依据生产情况适时调整生产进度,确保生产任务的完成。
3.6 资源管理1.合理使用和管理压铸车间的各类物资和工具,确保资源的充分利用。
2.做好库存管理,适时补充和调整库存,确保生产所需物资的供应。
4. 考核标准4.1 现场秩序管理考核1.检查现场乾净程度,评分参照:10分为最高分,0分为最低分。
2.检查材料、设备和工具放置是否符合规定,评分参照:10分为最高分,0分为最低分。
4.2 安全管理考核1.检查是否依照安全规程操作,评分参照:10分为最高分,0分为最低分。
2.检查安全培训合格情况,评分参照:10分为最高分,0分为最低分。
压铸厂生产现场管理制度
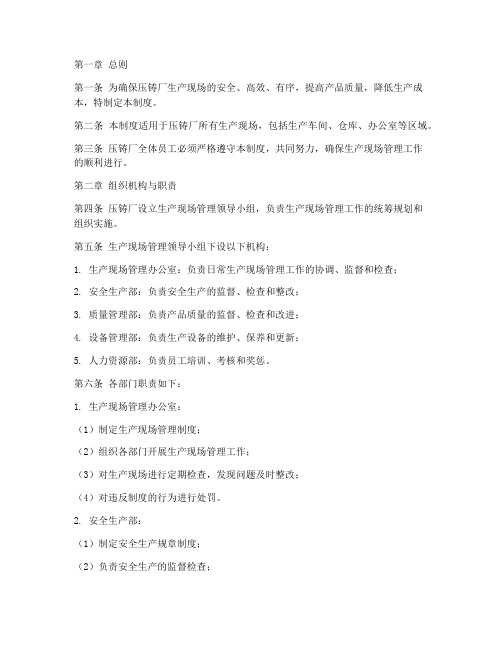
第一章总则第一条为确保压铸厂生产现场的安全、高效、有序,提高产品质量,降低生产成本,特制定本制度。
第二条本制度适用于压铸厂所有生产现场,包括生产车间、仓库、办公室等区域。
第三条压铸厂全体员工必须严格遵守本制度,共同努力,确保生产现场管理工作的顺利进行。
第二章组织机构与职责第四条压铸厂设立生产现场管理领导小组,负责生产现场管理工作的统筹规划和组织实施。
第五条生产现场管理领导小组下设以下机构:1. 生产现场管理办公室:负责日常生产现场管理工作的协调、监督和检查;2. 安全生产部:负责安全生产的监督、检查和整改;3. 质量管理部:负责产品质量的监督、检查和改进;4. 设备管理部:负责生产设备的维护、保养和更新;5. 人力资源部:负责员工培训、考核和奖惩。
第六条各部门职责如下:1. 生产现场管理办公室:(1)制定生产现场管理制度;(2)组织各部门开展生产现场管理工作;(3)对生产现场进行定期检查,发现问题及时整改;(4)对违反制度的行为进行处罚。
2. 安全生产部:(1)制定安全生产规章制度;(2)负责安全生产的监督检查;(3)对安全隐患进行整改;(4)组织安全生产培训。
3. 质量管理部:(1)制定产品质量管理制度;(2)负责产品质量的监督检查;(3)对质量问题进行整改;(4)组织质量改进活动。
4. 设备管理部:(1)制定设备管理制度;(2)负责生产设备的维护、保养和更新;(3)对设备故障进行及时处理;(4)组织设备改进活动。
5. 人力资源部:(1)制定员工培训计划;(2)负责员工考核和奖惩;(3)组织员工技能培训;(4)对员工进行思想教育。
第三章生产现场管理要求第七条生产现场应保持整洁、有序,不得堆放杂物,确保通道畅通。
第八条生产设备应保持完好,定期进行维护保养,确保设备正常运行。
第九条生产原料、半成品、成品应分类存放,标识清晰,便于管理。
第十条生产现场应定期进行清洁,确保生产环境整洁。
第十一条员工应遵守操作规程,严格按照工艺要求进行生产。
压铸车间现场管理制度
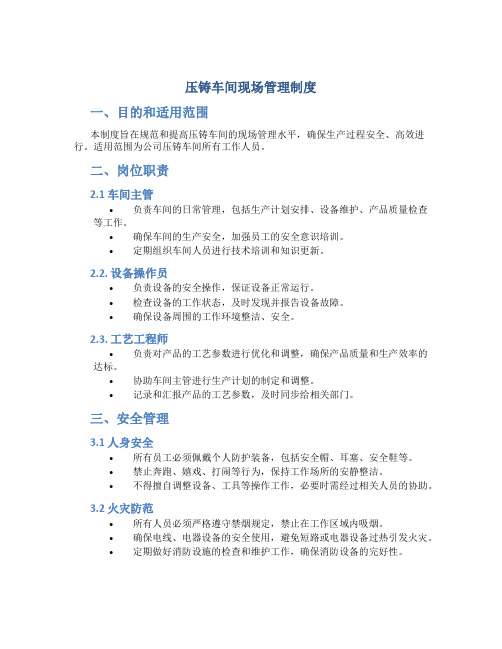
压铸车间现场管理制度一、目的和适用范围本制度旨在规范和提高压铸车间的现场管理水平,确保生产过程安全、高效进行。
适用范围为公司压铸车间所有工作人员。
二、岗位职责2.1 车间主管•负责车间的日常管理,包括生产计划安排、设备维护、产品质量检查等工作。
•确保车间的生产安全,加强员工的安全意识培训。
•定期组织车间人员进行技术培训和知识更新。
2.2. 设备操作员•负责设备的安全操作,保证设备正常运行。
•检查设备的工作状态,及时发现并报告设备故障。
•确保设备周围的工作环境整洁、安全。
2.3. 工艺工程师•负责对产品的工艺参数进行优化和调整,确保产品质量和生产效率的达标。
•协助车间主管进行生产计划的制定和调整。
•记录和汇报产品的工艺参数,及时同步给相关部门。
三、安全管理3.1 人身安全•所有员工必须佩戴个人防护装备,包括安全帽、耳塞、安全鞋等。
•禁止奔跑、嬉戏、打闹等行为,保持工作场所的安静整洁。
•不得擅自调整设备、工具等操作工作,必要时需经过相关人员的协助。
3.2 火灾防范•所有人员必须严格遵守禁烟规定,禁止在工作区域内吸烟。
•确保电线、电器设备的安全使用,避免短路或电器设备过热引发火灾。
•定期做好消防设施的检查和维护工作,确保消防设备的完好性。
3.3 事故报告和应急处理•发生事故时,工作人员应立即报告上级主管,并采取必要的应急措施。
•全体员工必须参加应急演练,熟悉各类突发事件的应对措施。
•对于事故原因的调查和分析,需要成立专门的调查小组进行。
四、日常管理4.1 生产计划管理•车间主管负责编制生产计划,确保根据市场需求合理安排生产任务。
•生产计划需及时与相关部门沟通和确认,确保生产资源的充足。
4.2 设备维护管理•按照设备使用说明书和保养手册,制定设备维护计划并执行。
•定期对设备进行检查和保养,及时发现并修复设备故障。
•对于关键设备,设立备件库存,确保设备维修时的快速响应。
4.3 质量管理•建立和完善产品质量检测标准,确保产品质量符合要求。
公司压铸生产车间现场管理制度
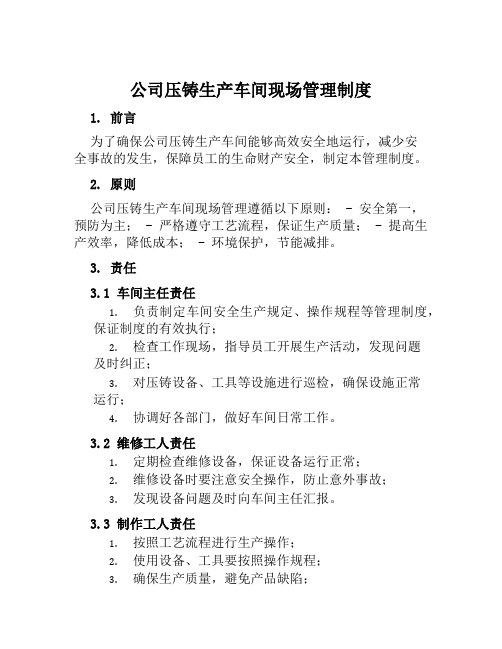
公司压铸生产车间现场管理制度1. 前言为了确保公司压铸生产车间能够高效安全地运行,减少安全事故的发生,保障员工的生命财产安全,制定本管理制度。
2. 原则公司压铸生产车间现场管理遵循以下原则: - 安全第一,预防为主; - 严格遵守工艺流程,保证生产质量; - 提高生产效率,降低成本; - 环境保护,节能减排。
3. 责任3.1 车间主任责任1.负责制定车间安全生产规定、操作规程等管理制度,保证制度的有效执行;2.检查工作现场,指导员工开展生产活动,发现问题及时纠正;3.对压铸设备、工具等设施进行巡检,确保设施正常运行;4.协调好各部门,做好车间日常工作。
3.2 维修工人责任1.定期检查维修设备,保证设备运行正常;2.维修设备时要注意安全操作,防止意外事故;3.发现设备问题及时向车间主任汇报。
3.3 制作工人责任1.按照工艺流程进行生产操作;2.使用设备、工具要按照操作规程;3.确保生产质量,避免产品缺陷;4.发现问题及时汇报。
4. 安全措施4.1 设备安全1.对压铸设备进行定期检查维护,避免设备故障引发安全事故;2.禁止私自更改设备的参数、程序,以免发生人身伤害或设备故障;3.新员工必须接受安全培训并参观、了解压铸生产车间的安全规程,保证员工操作上的安全。
4.2 人员安全1.压铸设备操作必须由经过培训和考试合格的操作员进行;2.压铸生产车间的出入口必须保持通畅,防止发生拥挤、堵塞;3.操作员必须穿戴劳保用品,如手套、护目镜等;4.定期开展消防安全演练,提高员工的应急响应能力。
5. 生产管控5.1 产品质量管控1.每一道工序都必须按照操作规程进行,保证产品质量;2.每批产品必须进行质量检测,检测合格后方可出厂;3.检测不合格的产品必须安全处理,避免再次被使用。
5.2 生产计划控制1.根据客户订单量和要求,编制生产计划;2.每天制定生产任务单,保证生产有序进行;3.必要时调整生产计划,确保按时完成客户订单。
2023年压铸车间现场管理规定
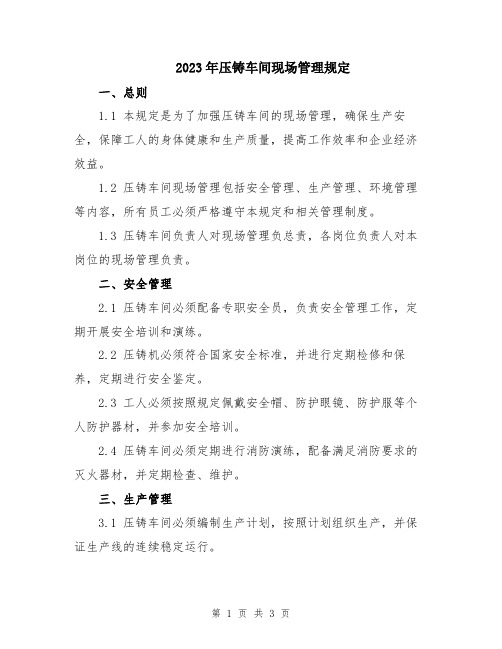
2023年压铸车间现场管理规定一、总则1.1 本规定是为了加强压铸车间的现场管理,确保生产安全,保障工人的身体健康和生产质量,提高工作效率和企业经济效益。
1.2 压铸车间现场管理包括安全管理、生产管理、环境管理等内容,所有员工必须严格遵守本规定和相关管理制度。
1.3 压铸车间负责人对现场管理负总责,各岗位负责人对本岗位的现场管理负责。
二、安全管理2.1 压铸车间必须配备专职安全员,负责安全管理工作,定期开展安全培训和演练。
2.2 压铸机必须符合国家安全标准,并进行定期检修和保养,定期进行安全鉴定。
2.3 工人必须按照规定佩戴安全帽、防护眼镜、防护服等个人防护器材,并参加安全培训。
2.4 压铸车间必须定期进行消防演练,配备满足消防要求的灭火器材,并定期检查、维护。
三、生产管理3.1 压铸车间必须编制生产计划,按照计划组织生产,并保证生产线的连续稳定运行。
3.2 压铸机的操作必须经过培训合格,并持证上岗,严禁无证操作。
3.3 压铸机必须按照工艺要求进行调试和保养,保证产品质量。
3.4 产品必须进行严格的质量检测,合格产品方可出厂,不合格产品必须及时返修或报废。
3.5 压铸车间必须定期清洁、消毒,并做好设备保养工作。
四、环境管理4.1 压铸车间必须符合国家环境保护要求,安装大气污染治理设备,定期进行检测和维护。
4.2 压铸车间必须规范垃圾分类和处理,垃圾必须及时清理,并做好消毒工作。
4.3 压铸车间必须严禁乱倒废弃物和污染物,保持车间的整洁、清爽。
4.4 压铸车间必须严格控制废气、废水的排放,定期进行监测,确保不超过国家标准。
五、其他管理5.1 压铸车间必须制定岗位责任制和班组责任制,明确员工的权责,确保岗位和职责落实到位。
5.2 压铸车间必须建立良好的工作和沟通机制,定期召开车间例会和学习交流会,解决工作中出现的问题。
5.3 压铸车间必须建立健全的考核制度,对员工进行定期考核,并根据考核结果进行奖惩。
公司压铸生产车间现场管理制度
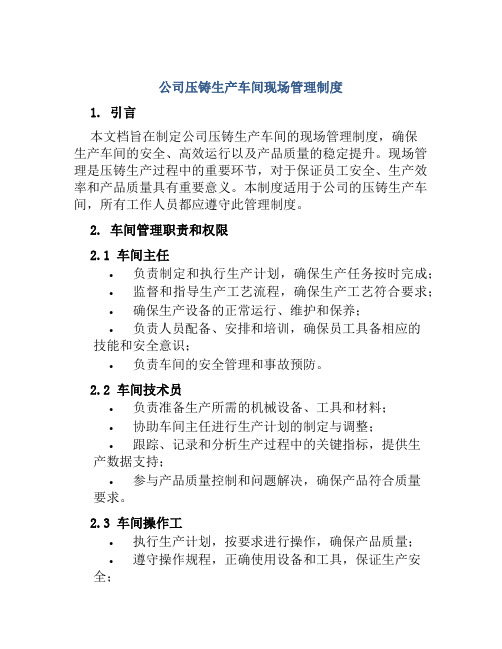
公司压铸生产车间现场管理制度1. 引言本文档旨在制定公司压铸生产车间的现场管理制度,确保生产车间的安全、高效运行以及产品质量的稳定提升。
现场管理是压铸生产过程中的重要环节,对于保证员工安全、生产效率和产品质量具有重要意义。
本制度适用于公司的压铸生产车间,所有工作人员都应遵守此管理制度。
2. 车间管理职责和权限2.1 车间主任•负责制定和执行生产计划,确保生产任务按时完成;•监督和指导生产工艺流程,确保生产工艺符合要求;•确保生产设备的正常运行、维护和保养;•负责人员配备、安排和培训,确保员工具备相应的技能和安全意识;•负责车间的安全管理和事故预防。
2.2 车间技术员•负责准备生产所需的机械设备、工具和材料;•协助车间主任进行生产计划的制定与调整;•跟踪、记录和分析生产过程中的关键指标,提供生产数据支持;•参与产品质量控制和问题解决,确保产品符合质量要求。
2.3 车间操作工•执行生产计划,按要求进行操作,确保产品质量;•遵守操作规程,正确使用设备和工具,保证生产安全;•及时上报异常情况和问题,确保问题能迅速得到解决;•参与车间的5S管理,保持工作环境的整洁有序。
3. 车间生产流程管理3.1 计划制定与调整1.车间主任根据订单和交付要求制定生产计划;2.考虑设备利用率、技术可行性和人力资源等因素,制定合理的生产计划;3.在生产过程中,根据实际情况及时调整生产计划,确保生产线平稳运行。
3.2 设备管理1.车间主任负责设备的正常运行、维护和保养;2.操作工严格按照操作规程正确使用设备,并定期对设备进行保养和维修;3.发现设备故障或异常情况,及时上报并协助维修人员进行处理。
3.3 质量管理1.操作工严格按照工艺规范操作,确保产品质量符合要求;2.技术员参与产品质量控制,进行抽样检验和测试;3.发现质量问题,立即停工并上报,配合相关人员进行问题解决。
3.4 5S管理1.保持车间内外环境整洁有序;2.安置工具和材料时要有规定的摆放位置;3.定期进行清理、整理和维护,防止杂物积存。
压铸车间生产管理制度

压铸车间生产管理制度第一章总则第一条为了规范压铸车间的生产管理,提高生产效率和产品质量,确保生产安全,制定本制度。
第二条压铸车间生产管理制度适用于压铸车间全体员工,包括厂长、车间主任、班组长和普通生产工人等。
第三条压铸车间生产管理制度的执行机构为压铸车间管理人员,由车间主任负责具体执行。
第四条压铸车间生产管理制度应当和公司的其他相关制度相衔接,形成一个完整的生产管理体系。
第五条压铸车间生产管理制度的内容包括生产安全管理、生产计划管理、生产设备管理、产品质量管理等方面。
第二章生产安全管理第一条压铸车间生产安全管理应当遵守国家相关法律法规和公司安全管理规定,确保生产过程中员工的人身安全和设备的完好。
第二条压铸车间生产安全管理要求在生产过程中,必须严格执行安全操作规程,杜绝违章操作和危险行为。
第三条压铸车间生产安全管理应当定期进行安全生产培训,提高员工的安全意识和安全技能。
第四条压铸车间生产安全管理要求在生产现场设置完善的安全设施和预防措施,确保生产过程中的安全。
第三章生产计划管理第一条压铸车间生产计划管理要求根据订单和市场需求,制定合理的生产计划,确保生产进度。
第二条压铸车间生产计划管理要求生产计划的执行不能超过设备和人力的实际承载能力,否则会影响生产效率。
第三条压铸车间生产计划管理要求针对生产计划中的紧急订单和重大任务,及时调整生产计划,确保按时完成。
第四条压铸车间生产计划管理要求对生产计划的执行情况进行定期追踪和评估,分析产生偏差的原因并进行改进。
第四章生产设备管理第一条压铸车间生产设备管理要求对生产设备进行定期的维护保养,确保设备的正常运转和稳定性。
第二条压铸车间生产设备管理要求严格执行设备操作规程,杜绝违章操作和设备损坏。
第三条压铸车间生产设备管理要求建立设备使用台账,记录设备的使用情况和维护保养情况。
第四条压铸车间生产设备管理要求对设备的更换和更新进行合理规划,确保设备的更新换代。
第五章产品质量管理第一条压铸车间产品质量管理要求严格执行产品质量标准,确保产品符合标准要求。
压铸车间现场安全管理制度
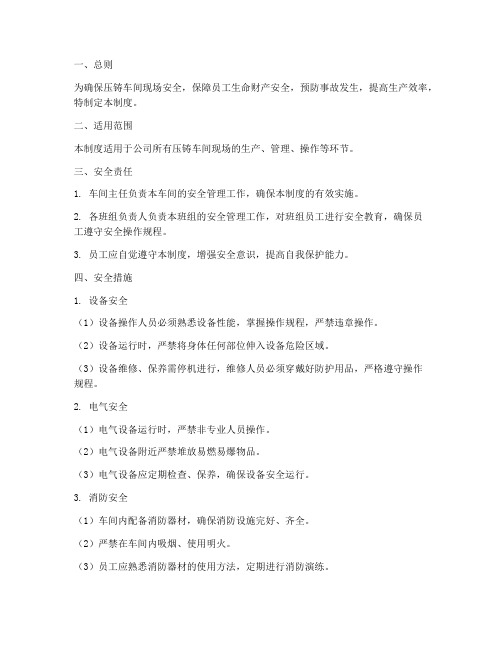
一、总则为确保压铸车间现场安全,保障员工生命财产安全,预防事故发生,提高生产效率,特制定本制度。
二、适用范围本制度适用于公司所有压铸车间现场的生产、管理、操作等环节。
三、安全责任1. 车间主任负责本车间的安全管理工作,确保本制度的有效实施。
2. 各班组负责人负责本班组的安全管理工作,对班组员工进行安全教育,确保员工遵守安全操作规程。
3. 员工应自觉遵守本制度,增强安全意识,提高自我保护能力。
四、安全措施1. 设备安全(1)设备操作人员必须熟悉设备性能,掌握操作规程,严禁违章操作。
(2)设备运行时,严禁将身体任何部位伸入设备危险区域。
(3)设备维修、保养需停机进行,维修人员必须穿戴好防护用品,严格遵守操作规程。
2. 电气安全(1)电气设备运行时,严禁非专业人员操作。
(2)电气设备附近严禁堆放易燃易爆物品。
(3)电气设备应定期检查、保养,确保设备安全运行。
3. 消防安全(1)车间内配备消防器材,确保消防设施完好、齐全。
(2)严禁在车间内吸烟、使用明火。
(3)员工应熟悉消防器材的使用方法,定期进行消防演练。
4. 人员安全(1)员工进入车间必须穿戴好劳动保护用品,如工作服、安全帽、工作鞋等。
(2)严禁酒后上岗,工作中严禁打闹、嬉戏。
(3)高空作业时,必须佩戴安全带,并系好保险钩。
(4)作业区域应保持整洁,严禁堆放杂物。
五、安全检查与考核1. 车间主任每月至少组织一次安全检查,发现问题及时整改。
2. 班组负责人每周至少组织一次安全检查,对班组员工进行安全教育。
3. 员工应自觉接受安全检查,对发现的安全隐患及时报告。
4. 对违反本制度的行为,根据情节轻重,给予相应处罚。
六、附则1. 本制度由车间主任负责解释。
2. 本制度自发布之日起施行。
压铸车间生产现场管理
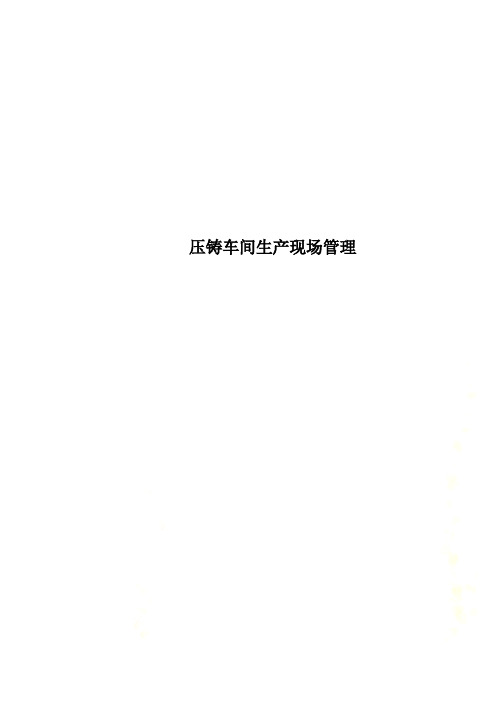
压铸车间生产现场管理压铸车间生产现场管理来源:责任编辑:信息中心发布时间:2011-7-24 23:53:22浏览71次生产现场管理是对以生产作业场所为主体的生产活动进行计划,组织和控制的总称。
对生产过程各种要素包括人、机、料、法、能、信等进行合理配置和优化组合,从而达到提高产品质量、提高劳动生产率、降低各种消耗,使企业取得显著经济效益。
一、生产现场管理内容生产现场管理的内容主要有:工序管理、物流管理和环境管理。
(一)工序管理工序――是指一个(或一组)工人在一个工作地,对一个(和同时几个)工作进行加工所连续完成的工作内容,是产品生产的基本单位。
工序管理包括工序要素管理和产品要素管理两大项1. 工序要素管理――就是对工序使用的劳动力、设备、原材料和压铸件的管理。
压铸生产是一个复杂的生产过程,其技术参数多、变化大,而且对铸件质量影响显著。
随着压铸件领域的不断扩大和生产批量的不断增大,过去依靠经验确定压铸技术参数的方法己不适应当今压铸技术发展的需要,必须采用科学的方法确定合理的压铸技术参数并实施有效的控制。
劳动力管理:根据工种、技术水平进行岗位优化组合、合格上岗,严格遵守劳动纪律和操作规程。
设备管理:对压铸机、模具、工具必须保持完好、齐全,做好日常保养。
原材料和压铸件管理:材料保证供应,保质、保量;铸件堆放有序,防止碰伤、划伤。
2. 压铸机的选择应考虑以下几个方面2.a、根据压铸件的合金种类和大小、生产类型,初步确定压铸机的类型。
2.锌、锡、铅及镁(小件)等合金宜选用热室压铸机,铝、镁(大件)、铜等合金应选用冷室压铸机。
产品品种少、批量大时,应选用自动化程度高配备齐全的压铸机。
2.b、确定压铸机基本机型后,根据压铸件的外形尺寸、重量、壁厚和技术条件确定压铸机机型,核算其锁模力、压室充满度、容模空间尺寸、压射能量。
2.c.确定压铸机机型后还要考虑空压射速度、液压系统和控制、可靠性等。
2.产品要素管理――对产品品种、数量、质量、交货期、成本的管理。
压铸车间生产管理制度(5篇)
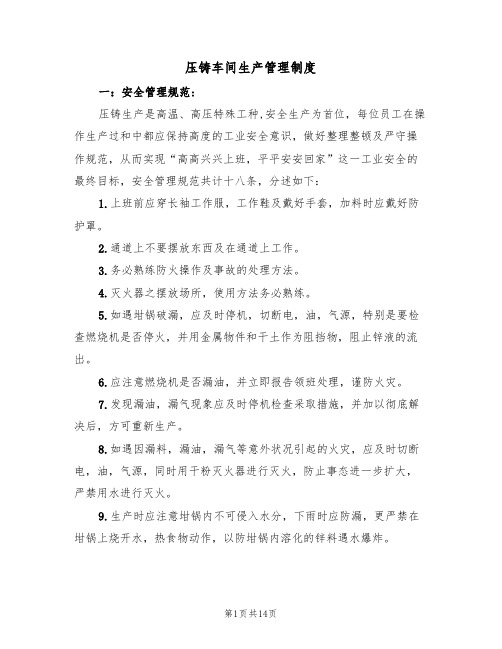
压铸车间生产管理制度一:安全管理规范:压铸生产是高温、高压特殊工种,安全生产为首位,每位员工在操作生产过和中都应保持高度的工业安全意识,做好整理整顿及严守操作规范,从而实现“高高兴兴上班,平平安安回家”这一工业安全的最终目标,安全管理规范共计十八条,分述如下:1.上班前应穿长袖工作服,工作鞋及戴好手套,加料时应戴好防护罩。
2.通道上不要摆放东西及在通道上工作。
3.务必熟练防火操作及事故的处理方法。
4.灭火器之摆放场所,使用方法务必熟练。
5.如遇坩锅破漏,应及时停机,切断电,油,气源,特别是要检查燃烧机是否停火,并用金属物件和干土作为阻挡物,阻止锌液的流出。
6.应注意燃烧机是否漏油,并立即报告领班处理,谨防火灾。
7.发现漏油,漏气现象应及时停机检查采取措施,并加以彻底解决后,方可重新生产。
8.如遇因漏料,漏油,漏气等意外状况引起的火灾,应及时切断电,油,气源,同时用干粉灭火器进行灭火,防止事态进一步扩大,严禁用水进行灭火。
9.生产时应注意坩锅内不可侵入水分,下雨时应防漏,更严禁在坩锅上烧开水,热食物动作,以防坩锅内溶化的锌料遇水爆炸。
10.料头锌锭应确保在干燥状态下投入使用,未经许可不可带有油分,水分的料头料屑倒入坩锅。
11.从坩锅中打捞出来的锌渣等,必须放于干燥的铸铁槽中,不得置于地板上,避免爆炸危险。
12.如因电气系统故障应关掉总开关后提出报告,不得私自拆卸。
13.每套压铸机中间应使用挡屏,以防溅料伤人。
14.走过压铸机旁应注意溅料危险。
15.操作人员,加料人员,应分清工作,加料作业时应进行招呼互相配合,同时劝阻非生产人员进入不安全区域。
16.换模具应两人配合,吊换模具时应仔细确认安全后方可搬迁吊装,谨慎作业,锁模时应用____个以上螺丝,并注意检查锁模螺丝的螺纹是否完好,严禁模具撞击或伤人。
17.整理整顿模具应停机后方可进行。
18.工具,配件使用后应放置于工具箱内,以防随意放置伤人,更严禁置放于机台内。
压铸车间生产管理制度
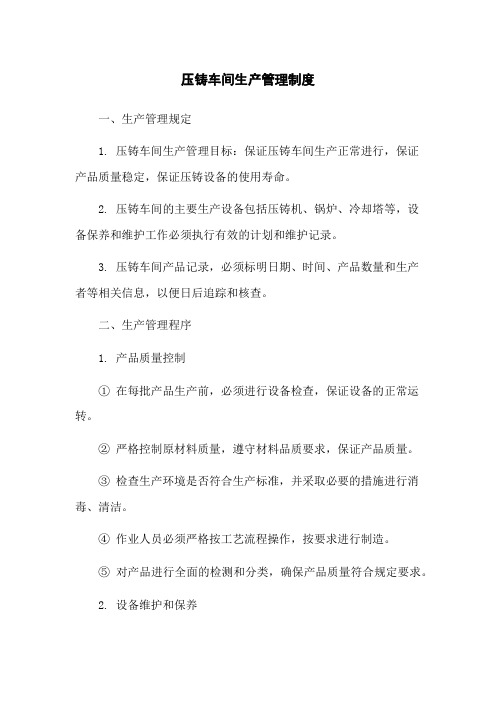
压铸车间生产管理制度一、生产管理规定1. 压铸车间生产管理目标:保证压铸车间生产正常进行,保证产品质量稳定,保证压铸设备的使用寿命。
2. 压铸车间的主要生产设备包括压铸机、锅炉、冷却塔等,设备保养和维护工作必须执行有效的计划和维护记录。
3. 压铸车间产品记录,必须标明日期、时间、产品数量和生产者等相关信息,以便日后追踪和核查。
二、生产管理程序1. 产品质量控制①在每批产品生产前,必须进行设备检查,保证设备的正常运转。
②严格控制原材料质量,遵守材料品质要求,保证产品质量。
③检查生产环境是否符合生产标准,并采取必要的措施进行消毒、清洁。
④作业人员必须严格按工艺流程操作,按要求进行制造。
⑤对产品进行全面的检测和分类,确保产品质量符合规定要求。
2. 设备维护和保养①根据设备生产周期,执行月度、季度和年度保养计划。
②对设备进行日常维护,发现故障立即停机检查治理。
③对设备进行全面保养,清洁、保养维护,保证设备状态良好。
④关键设备备件必须储备足够,确保设备故障时能够及时维修。
3. 生产管理流程①生产任务单的制定:每天生产任务单由压铸车间主管制定,明确生产任务单内容及生产周期。
②生产计划的制定:根据生产任务单,进行生产计划的制定,确定生产过程中的各项操作要求、质量标准和制造周期。
③生产任务单的分配:压铸车间主管必须根据生产计划分配任务,明确各个环节的责任,确保每个操作环节有专人负责,保证生产任务的准确完成。
④生产管理的监督和检查:压铸车间生产主管必须对生产过程进行全面的监督和检查,及时发现问题并实行整改措施,确保生产任务能够顺利进行。
总之,压铸车间生产管理制度的有效执行,可以大大提高产品质量和生产效率,降低成本和废品率,使企业获得更好的经济效益。
压铸车间现场管理制度

压铸车间现场管理制度引言压铸车间是生产航空零部件的紧要环节,因此对于压铸车间的管理需要严格、精细。
本文档旨在阐述压铸车间现场管理的制度和规范,以提高压铸车间生产效率,保证生产质量和安全。
责任管理压铸车间负责人压铸车间负责人是压铸车间生产管理的最高领导者,对压铸车间内全部工作负有全面负责。
其职责包括:•订立压铸车间生产经营计划•负责组织实施各项管理制度•管理和调动压铸车间各类人员•负责与上级、同级、下级沟通协调等压铸车间作业管理岗压铸车间作业管理岗是负责车间现场生产和作业管理的岗位,其职责包括:•实施现场安全管理制度,防止事故风险•管理车间的生产计划、生产过程、生产结果,并做好数据统计工作•帮助车间负责人完成各项工作压铸车间技术工程师压铸车间技术工程师是车间生产技术支持和技术管理岗位,其职责包括:•负责生产过程中的技术配置•针对生产中显现的技术问题进行解决•完成新产品或新工艺的开发压铸车间质量管理人员压铸车间质量管理人员是负责对压铸产品质量进行管理的岗位,其职责包括:•负责生产中的质量监管•针对生产中显现的质量问题进行解决•完善产品质量考核体系并进行质量报告现场管理规范安全生产安全生产是压铸车间最基本的管理规范之一,其目的是避开工作过程中显现意外伤亡和财产损失。
在压铸车间的安全生产管理中,应注意以下事项:•保持车间清洁卫生,避开杂物聚积•各类机床设备经过使用后应保持良好的状态并分类归位•严格依照生产安全制度操作机床设备•开启各类设备时须确保无人操作机床设备•确保生产原材料加工、储存、使用安全生产过程管理生产过程管理是压铸车间的重点之一,通过规范生产过程可以提高生产效率和产品质量。
在压铸车间的生产过程管理中,应注意以下事项:•依照生产计划生产,确保生产充足需求•严格依照生产工艺、质量标准进行生产•在生产过程中适时对机床设备状态进行检查和维护•产品合格后,如有需要应搭配进行保密加工质量管理压铸车间作为生产车间之一,产品的质量自然成为了其重中之重的问题。
压铸车间现场管理制度 (共4篇)
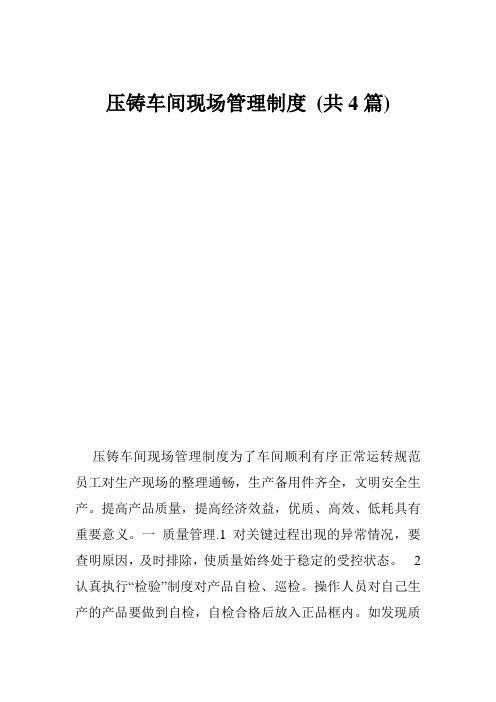
压铸车间现场管理制度(共4篇)压铸车间现场管理制度为了车间顺利有序正常运转规范员工对生产现场的整理通畅,生产备用件齐全,文明安全生产。
提高产品质量,提高经济效益,优质、高效、低耗具有重要意义。
一质量管理.1 对关键过程出现的异常情况,要查明原因,及时排除,使质量始终处于稳定的受控状态。
2 认真执行“检验”制度对产品自检、巡检。
操作人员对自己生产的产品要做到自检,自检合格后放入正品框内。
如发现质量事故时做到责任者查不清不放过、事故原因不排除不放过预防措施不制定不放过。
3 车间要对所生产的产品质量做到不合格的材料不投产、不合格的半成品不转序. 二工艺管理1 严格贯彻执行工艺规程,严禁员工私自调整工艺参数。
2 对新工人和工种变动人员进行岗位技能培训,合格并有师傅指导方可上岗操作。
3 严格按照工艺参数要求生产,严格按照产品技术要求、按规定进行认真检查,对有故障部位做好记录。
4 对原材料、半成品、零配件、进入车间后要进行自检,符合标准或有让步接收手续方可投产,否则不得投入生产。
5 新制作的模具生产要有合格样品才能生产调试,调试合格后当班必须做好试生产工艺卡在现在挂好。
生产中判定无异常且首件产品合格方可投入生产。
否则立即停止生产。
三定置管理1 定置摆放、工件按区域按类放置,合理使用工位器具。
2 生产中及时运转不装过多高出铁框、勤检查、勤清理,轻放,保证产品外观完好。
4 加强不合格品管理,有记录,标识明显,处理及时。
5 安全通道内不得摆放任何物品,不得阻碍6 消防器材定置摆放, 不得随意挪作他用, 保持清洁卫生, 周围不得有障碍物四设备管理1 车间设备指定专人维修管理2 严格执行公司设备使用、维护、保养、管理制度,认真执行设备保养制度,严格遵守操作规程。
3 做到设备管理“三步法”,坚持日清扫、周维护、月保养,每天上班后检查设备的操纵控制系统、安全装置、润滑油路畅通,油线、油毡清洁、油压油位标准、并按润滑图表注油,油质合格,待检查无问题方可正式工作。
压铸车间现场管理规定
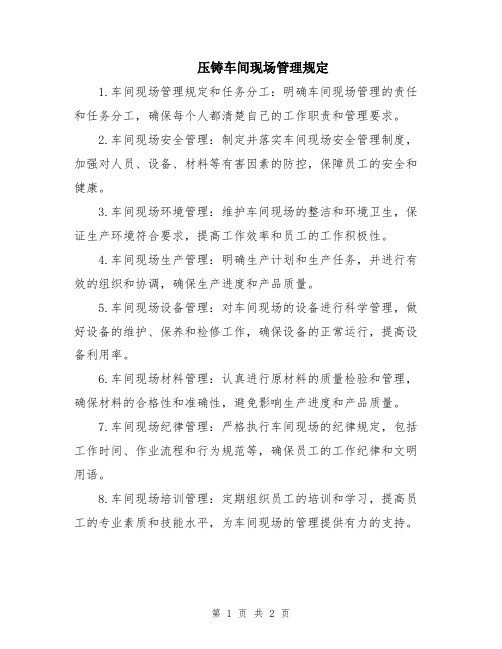
压铸车间现场管理规定
1.车间现场管理规定和任务分工:明确车间现场管理的责任和任务分工,确保每个人都清楚自己的工作职责和管理要求。
2.车间现场安全管理:制定并落实车间现场安全管理制度,加强对人员、设备、材料等有害因素的防控,保障员工的安全和健康。
3.车间现场环境管理:维护车间现场的整洁和环境卫生,保证生产环境符合要求,提高工作效率和员工的工作积极性。
4.车间现场生产管理:明确生产计划和生产任务,并进行有效的组织和协调,确保生产进度和产品质量。
5.车间现场设备管理:对车间现场的设备进行科学管理,做好设备的维护、保养和检修工作,确保设备的正常运行,提高设备利用率。
6.车间现场材料管理:认真进行原材料的质量检验和管理,确保材料的合格性和准确性,避免影响生产进度和产品质量。
7.车间现场纪律管理:严格执行车间现场的纪律规定,包括工作时间、作业流程和行为规范等,确保员工的工作纪律和文明用语。
8.车间现场培训管理:定期组织员工的培训和学习,提高员工的专业素质和技能水平,为车间现场的管理提供有力的支持。
9.车间现场改进管理:鼓励员工积极提出改进意见和建议,对车间现场存在的问题进行分析和改进,提高生产效率和产品质量。
10.车间现场沟通管理:建立有效的沟通机制,加强车间现场内部和外部的沟通,及时解决问题和协调工作关系。
以上是压铸车间现场管理的一些规定,可以根据实际情况进行适当调整和完善。
压铸车间现场管理规定(3篇)
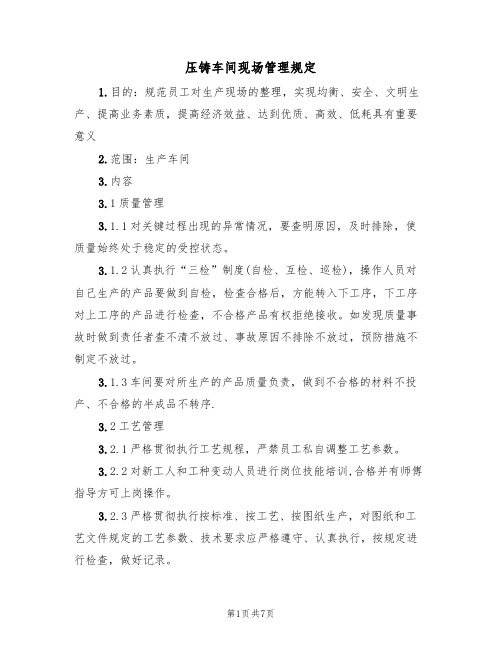
压铸车间现场管理规定1.目的:规范员工对生产现场的整理,实现均衡、安全、文明生产、提高业务素质,提高经济效益、达到优质、高效、低耗具有重要意义2.范围:生产车间3.内容3.1质量管理3.1.1对关键过程出现的异常情况,要查明原因,及时排除,使质量始终处于稳定的受控状态。
3.1.2认真执行“三检”制度(自检、互检、巡检),操作人员对自己生产的产品要做到自检,检查合格后,方能转入下工序,下工序对上工序的产品进行检查,不合格产品有权拒绝接收。
如发现质量事故时做到责任者查不清不放过、事故原因不排除不放过,预防措施不制定不放过。
3.1.3车间要对所生产的产品质量负责,做到不合格的材料不投产、不合格的半成品不转序.3.2工艺管理3.2.1严格贯彻执行工艺规程,严禁员工私自调整工艺参数。
3.2.2对新工人和工种变动人员进行岗位技能培训,合格并有师傅指导方可上岗操作。
3.2.3严格贯彻执行按标准、按工艺、按图纸生产,对图纸和工艺文件规定的工艺参数、技术要求应严格遵守、认真执行,按规定进行检查,做好记录。
3.2.4对原材料、半成品、零配件、进入车间后要进行自检,符合标准或有让步接收手续方可投产,否则不得投入生产。
3.2.5新制作的工装应进行检查和试验,判定无异常且首件产品合格方可投入生产。
3.2.6在用工装应保持完好,合理使用设备、量具、工位器具,保持精度和良好的技术状态。
3.3定置管理3.3.1定置摆放、工件按区域按类放置,合理使用工位器具。
3.3.2及时运转、勤检查、勤转序、勤清理、标志变化,应立即转序,不拖不积,稳拿轻放,保证产品外观完好。
3.3.4加强不合格品管理,有记录,标识明显,处理及时。
3.3.5安全通道内不得摆放任何物品,不得阻碍3.3.6消防器材定置摆放,不得随意挪作他用,保持清洁卫生,周围不得有障碍物3.4设备管理3.4.1车间设备指定专人管理3.4.2严格执行公司设备使用、维护、保养、管理制度,认真执行设备保养制度,严格遵守操作规程。
- 1、下载文档前请自行甄别文档内容的完整性,平台不提供额外的编辑、内容补充、找答案等附加服务。
- 2、"仅部分预览"的文档,不可在线预览部分如存在完整性等问题,可反馈申请退款(可完整预览的文档不适用该条件!)。
- 3、如文档侵犯您的权益,请联系客服反馈,我们会尽快为您处理(人工客服工作时间:9:00-18:30)。
生产现场管理是对以生产作业场所为主体的生产活动进行计划,组织和控制的总称。
对生产过程各种要素包括人、机、料、法、能、信等进行合理配置和优化组合,从而达到提高产品质量、提高劳动生产率、降低各种消耗,使企业取得显著经济效益。
一、生产现场管理内容生产现场管理的内容主要有:工序管理、物流管理和环境管理。
(一)工序管理工序――是指一个(或一组)工人在一个工作地,对一个(和同时几个)工作进行加工所连续完成的工作内容,是产品生产的基本单位。
工序管理包括工序要素管理和产品要素管理两大项1. 工序要素管理――就是对工序使用的劳动力、设备、原材料和压铸件的管理。
压铸生产是一个复杂的生产过程,其技术参数多、变化大,而且对铸件质量影响显著。
随着压铸件领域的不断扩大和生产批量的不断增大,过去依靠经验确定压铸技术参数的方法己不适应当今压铸技术发展的需要,必须采用科学的方法确定合理的压铸技术参数并实施有效的控制。
劳动力管理:根据工种、技术水平进行岗位优化组合、合格上岗,严格遵守劳动纪律和操作规程。
设备管理:对压铸机、模具、工具必须保持完好、齐全,做好日常保养。
原材料和压铸件管理:材料保证供应,保质、保量;铸件堆放有序,防止碰伤、划伤。
2. 压铸机的选择应考虑以下几个方面、根据压铸件的合金种类和大小、生产类型,初步确定压铸机的类型。
2.锌、锡、铅及镁(小件)等合金宜选用热室压铸机,铝、镁(大件)、铜等合金应选用冷室压铸机。
产品品种少、批量大时,应选用自动化程度高配备齐全的压铸机。
、确定压铸机基本机型后,根据压铸件的外形尺寸、重量、壁厚和技术条件确定压铸机机型,核算其锁模力、压室充满度、容模空间尺寸、压射能量。
.确定压铸机机型后还要考虑空压射速度、液压系统和控制、可靠性等。
2.产品要素管理――对产品品种、数量、质量、交货期、成本的管理。
品种、数量一般以销定产,按合同要求按时交货,同时要考虑生产的连续性。
要对重点工艺加强质量管理,工序的质量控制要严格遵守工艺纪律和操作规程。
成本控制是对工序成本定额进行控制。
1、质量管理质量管理是指:在质量方面指挥和控制组织的协调的活动。
可以作以下解释:质量管理是组织经营管理的一部分,它的职能是计划、组织、指挥和控制;首要任务是制定质量方针、质量目标并使之贯彻和执行。
质量管理工作是通过质量策划、质量控制、质量保证和质量改进等活动来进行。
为实施质量管理,需要建立质量体系。
质量管理必须由最高管理者领导,它的实施涉及到组织中的所有成员。
2、质量控制与质量改进质量控制是质量管理的一部分,致力于满足质量要求。
质量改进是质量管理的一部分,致力于增强满足质量要求的能力。
3、压铸件的质量与检验方法A、压铸件质量压铸件质量包括外观质量、内在质量和使用质量。
外观质量是指铸件表面粗糙度、表面质量、尺寸公差、形位公差和质量偏差等。
内在质量是指铸件的化学成分、物理和力学性能、金相组织以及在铸件内部存在的孔洞、夹杂物和裂纹等。
使用质量是指铸件能满足各种使用要求和工作的性能,如耐磨性、耐腐蚀性和切削性、焊接性等。
B、质量标准质量标准有国家标准(GB)、国际标准或企业标准,我国是国际标准化组织(ISO)的主要成员之一,国际标准可以等效地视为国家标准。
铸件质量标准有精度标准、表面质量标准和功能质量标准。
C、铸件缺陷铸件缺陷有广义与狭义之分。
广义的铸件缺陷是指铸件质量特征没有到达分等标准(合格品、一等品、优等品),铸件生产厂质量管理差,产品质量得不到保证。
狭义的铸件缺陷是铸件上可检测出的包括在GB5611-85铸造名词术语标准中的全部名目。
铸件经检验后可分为合格品、返修品、废品三类。
铸件废品率P是铸件废品总量(内、外废)占合格品量W及内废量W1和外废量W2之和的百分比。
铸件缺陷率是有缺陷铸件数量与生产总量之比的百分数。
缺陷率通常大于废品率。
铸件缺陷数用计件表示。
D、铸件缺陷检查方法铸件缺陷检查普遍采用的有以下一些方法:①外观检查②化学分析检查③力学性能检测④低倍检验(宏观检验)⑤金相检查⑥无损检验。
E、提高产品质量意义质量是企业的生命线,是提高企业竞争能力的重要之柱,是提高企业经济效益的重要条件。
5、生产过程质量控制质量A、做.好技术检验工作(1) 检查方法分类按工艺阶段分:预先检查、首件检查、中间检查、最后检查;按检查数量分:全数检查、抽样检查;按检查人员分:专业检查、自检、互检;按检查性质分:外观检查、理化检查。
如某压铸厂采用自检为100~200件检查一次,巡查每天四次,或全检三种方式进行。
(2) 质量控制点的设置一般是在某些工序之前或之后、在产品发生责任变化、质量容易波动工序等进行检查。
例如某压铸厂铸件质量检查点如下:压铸→检查→去水口、披锋→检查→机加工→抛光→整形→检查。
(3) 运豪公司压铸过程质量检查工作指引(锌合金压铸)1)、检验依据①压铸件(已确认)的样板、客户提供的样板;②产品质量检查指引;③压铸件的技术文件;④产品抽样计划使用方法。
2)、首件检查①产品新投产或重新投产;②产品新投产时,应按照标准样板或有关技术文件检验,并核发生产指令;③首件检查数量不少于6件,如有要求的则要进行试装、试烤油漆或测量尺寸;④如工件要喷透明油漆及光黑油的应试喷油;⑤试烤油漆的数量不少于12件,其他试验数量不少于6件;⑥结果记录于《巡机记录报告》上,并注明“首件检查”字样。
3)、巡回检查①每2小时内对各机位至少巡查一次,抽查数量不少于10件,如对产品质量有怀疑应加严检查。
②结果记录于《巡机记录报告》。
4)、工序完成后检查(略)。
5)、产品检查的项目及内容产品检查的项目及内容见表16)在检查过程中,如发现品质异常问题,应及时填写《品质异常处理单》,并按照“纠正措施程序”处理。
品质异常处理单见表2。
2、质量控制的统计分析方法(方法有多种,这里只介绍几种)(1)、调查表法调查表也叫统计分析表,将铸件按名称、缺陷种类与个数、铸件数量列表统计。
它是整理数据和粗略分析原因的一种工具。
统计分析表见表3。
(2)控制图法控制图又称管理图,图1示它是不合格品数的控制图,又称pn图。
是每隔一段时间从工序中抽样来研究工序是否处于稳定状态的一种图形。
通常抽查的样组要多于25组,每组铸件数要相同且多于100个,每组缺陷铸件最好在5个之内。
根据图中各点排列的走向来判断生产过程是否处于受控状态。
(3)排列图法排列图又称主次因素图。
影响产品质量因素很多,而主要因素往往只是少数几项,排列图能有效地找出影响铸件质量的主要因素。
只有抓这几个少数因素,就提供了解决质量问题的捷径。
例如,某厂调查某一时间锌合金压铸产品主次因素分析图,如图2示。
一般将累计数在0%~80%左右作为首先要解决的缺陷。
(4)因果分析图因果分析图(又称鱼刺图或树枝图),如图3示。
将引起压铸件缺陷原因分为人、机、工艺、材料和环境五个大原因。
每个大原因再细化出中原因,中原因又分出小原因。
大原因——工艺、材料、压铸机、操作者、环境。
中原因(工艺方面)——浇注系统工艺、金属液充填方式、压铸工艺参数设置(压射力、压射速度、充填时间、模具温度、浇注温度、开模时间等)等。
小原因(影响模具温度)——生产速度、压铸件尺寸与形状、模具结构、模具材料、冷却水道尺寸和位置、冷却介质流量及种类、脱模剂状况、其它(室温等)。
罗列出小原因后,要分析和找出哪些是产生缺陷的主要原因,哪些是次要原因。
然后集中力量,针对这些主要原因的问题,在生产中加以解决。
(二)、物流管理物流是指车间内的材料、压铸件、金属液和其他材料向下一道工序转移过程。
物流管理要解决以下三个问题:物流路线最短;在制品占有量最小;搬运效率要高。
搞好物流管理要做好六方面工作:①、选择合适的生产组织形式;②、进行合理车间布置,缩短运输距离;③、搞好生产过程分析;④、提高搬运效率;⑤、需要制定合理的在制品定额;⑥、搞好各个生产环节和工序之间的能力平衡。
(三)、环境管理压铸车间的环境保护主要考虑三个方面:一是大气污染物,二是水的污染物,三是高温和热辐射。
1、压铸车间在工厂总平面布置中的位置一个完整的压铸生产企业要正常运作应有生产车间、辅助车间、动力设施、仓库及运输、行政管理及后勤等。
而一个产品厂则还有机加工车间、装配车间和其他车间。
压铸车间在工厂总平面布置中的位置应考虑以下几点:a. 压铸车间属热加工车间,产生烟气较多,从环境保护考虑,应将压铸车间布置在夏季主要风向的下风区,并在离工厂入口较远地方,也不应当锻压、砂型铸造车间靠在一起。
b. 考虑铸件的运输方便,尽可能靠近机械加工车间。
c. 根据本厂生产规模技术水平和发展可能型,宜留又发展余地。
d. 创造良好工作环境,应充分利用自然通风和自然采光,避免西晒,厂房的纵向天高軸线应与夏季风主导风向成60~90角,以便排出烟气和有害气体。
e. 根据防火要求,压铸车间与邻近建筑物之间应有一定距离,在车间周围应有消防车行驶道路。
f. 合金压铸车间应是独立单层建筑,车间地面应高于其他地面。
2、压铸车间的布置A、平面布置原则a. 车间的平面布置首先要考虑物料(炉料、金属液、铸件及浇注系统等)流程通畅、紧凑,避免来回输送。
b. 在充分利用车间面积的同时应考虑压铸机维修,压铸型装坼、维护和存放场地。
C .主要生产工部(压铸、熔化)应布置在具有良好采光和通风地方。
d. 办公室的位置应保证工作人员出入方便,并有较良好的工作环境,生活间应避免通过车间再到生活间。
B、压铸工部的布置a. 压铸机的布置应根据规模大小分别集中布置,对于自动化程度高的压铸车间,宜按机组布置,便于生产管理。
b. 根据厂房条件和压铸机的大小不同可采用单列布置和双列(多列)布置,压铸机可垂直车间墙面,也可平行车间墙面布置,无论采用那种布置方法,压铸机最突出部分到墙面距离不应小于1米,车间内人行道不应小于1.5米,电瓶车的不应少于3米。
c. 两台压铸机之间应根据压铸机的大小和周边设备多少、铸件装具、浇口余料放置情况,留有足够距离,以保证设备的运行、检修,模具装拆和清理、工人的操作等方面要求,并根据需要在压铸机外围设置防护网和金属隔板。
d. 压铸工部厂房内应有起重设备,便于吊运模具和压铸机的零部件。
e. 充分考虑操作人员的人体生理数据,保证足够的工作活动空间,较好的作业环境和职业安全卫生措施。
C、熔化工部的布置a. 熔化工部尽可能与压铸工部分开布置,根据不同的需要可布置在车间中部或端部,尽量采用少污染的能源。
b. 应有足够的面积用于放置原材料、回炉料(仓库应另设置)和加料操作并留有运送金属液的通道。
二、现场管理方法现场管理方法有:“5S活动”、定置管理、目视管理、目标管理等。
(一)、“5S”活动“5S”是整理、整顿、清扫、清洁和素养,有的加了一个习惯,叫“6S”活动。