弯管工艺规程及评定报告
弯管加工工艺技术
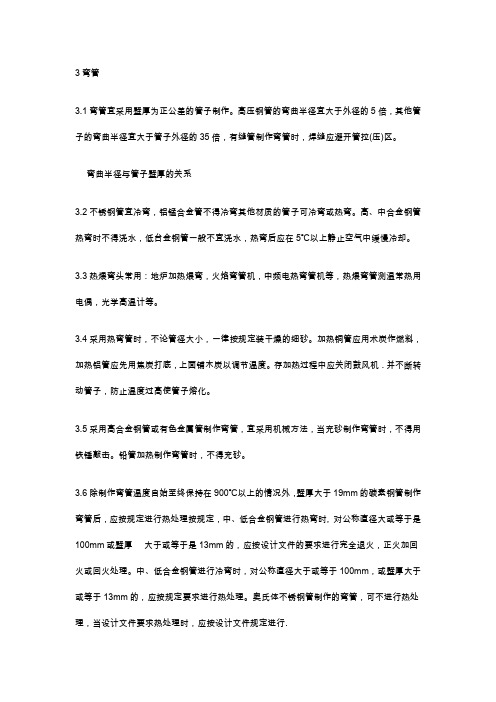
3弯管3.1弯管宜采用壁厚为正公差的管子制作。
高压钢管的弯曲半径宜大于外径的5倍,其他管子的弯曲半径宜大于管子外径的35倍,有缝管制作弯管时,焊缝应避开管拉(压)区。
弯曲半径与管子壁厚的关系3.2不锈钢管宜冷弯,铝锰合金管不得冷弯其他材质的管子可冷弯或热弯。
高、中合金钢管热弯时不得浇水,低台金钢管一般不宜浇水,热弯后应在5℃以上静止空气中缓慢冷却。
3.3热煨弯头常用:地炉加热煨弯,火焰弯管机,中频电热弯管机等,热煨弯管测温常热用电偶,光学高温计等。
3.4采用热弯管时,不论管径大小,一律按规定装干燥的细砂。
加热铜管应用术炭作燃料,加热铝管应先用焦炭打底,上面铺木炭以调节温度。
存加热过程中应关闭鼓风机.并不断转动管子,防止温度过高使管子熔化。
3.5采用高合金钢管或有色金属管制作弯管,宜采用机械方法,当充砂制作弯管时,不得用铁锤敲击。
铅管加热制作弯管时,不得充砂。
3.6除制作弯管温度自始至终保持在900℃以上的情况外,壁厚大于19mm的碳素钢管制作弯管后,应按规定进行热处理按规定,中、低合金钢管进行热弯时, 对公称直径大或等于是100mm或壁厚大于或等于是13mm的,应按设计文件的要求进行完全退火,正火加回火或回火处理。
中、低合金钢管进行冷弯时,对公称直径大于或等于100mm,或壁厚大于或等于13mm的,应按规定要求进行热处理。
奥氏体不锈钢管制作的弯管,可不进行热处理,当设计文件要求热处理时,应按设计文件规定进行.3.7输送剧毒流体或设计压力P大于或等于1OMPa的弯管,制作弯管前,后的壁厚之差,不得超过制作弯管前管子壁厚的10%;其它弯管,制作弯管前,后的管子壁厚之羞,不得超过制作弯管前管子壁厚的15%,且均不得小于管子的设计壁厚。
3.8输送剧毒流体或设计压力P大于或等于lOMPa的弯管,管端中心偏差值A不得超过1.5mm/m,当直管长度L人于3m时,其偏差不得超过5mm。
其他类别的弯管.管端中心偏差值Δ得超过3mm/m当直管长度L大于3m时,其偏差不得超过lOmm。
弯管制造典型工艺-1

目录弯管制造工艺流程示意图 (2)1.范围 (3)2.引用标准 (3)3.术语和定义 (3)4. 弯管制造工艺流程 (3)5. 弯管制造工艺要求 (3)6.通球表 (18)弯管制造工艺流程示意图注:1.D w≥133mm的钢管需做钢印移植;2.合金材料需做光谱检验。
1.范围本标准规定了锅炉平面弯管成形制造技术要求及验收要求。
本典型工艺适用于图1。
1~3个弯头的平面弯管,空间弯管可分解为几个平面弯管,分解后的平面弯管仍可参照本工艺。
图12.引用标准JB/T3375-2002《锅炉用材料入厂验收规则》JB/T1611-1993《锅炉管子制造技术条件》JB/T1612-1994《锅炉水压试验技术条件》JB/T1613-1993《锅炉受压元件焊接技术条件》JB/T1615-1991《锅炉油漆和包装技术条件》JB/T4308-1999《锅炉产品钢印及标记移植规定》JB/T4730.1~6-2005《承压设备无损检测》《蒸汽锅炉安全技术监察规程》19963.术语和定义H:停止点W:见证点4.弯管制造工艺流程见第2页《弯管制造工艺流程示意图》5.工艺要求5.1材料验收5.1.1 制造管子的材料应符合图纸设计要求,材料代用应按规定程序审批。
5.1.2制造管子用的钢材和焊接材料必须经过检验部门按JB/T3375-2002的规定进行入厂检验,未经检验或检验不合格者不准用于生产。
用于额定蒸汽压力不大于0.4MPa 的蒸汽锅炉和额定热功率不大于4.2MW 且额定出水温度小于120℃的热水锅炉的管子材料,如原始质量证明书齐全,且材料标记清晰、齐全时,可免于复检。
5.2 确定下料尺寸L5.2.1图1(c )中两端外倒角1×30°,且两端不需加长,下料长度L 按下列公式计算:公式一:()10232132211ααα++∆-⨯+++++++=l B L L L L L L L L b a中中 单位:mm 。
弯管工安全操作规程模版
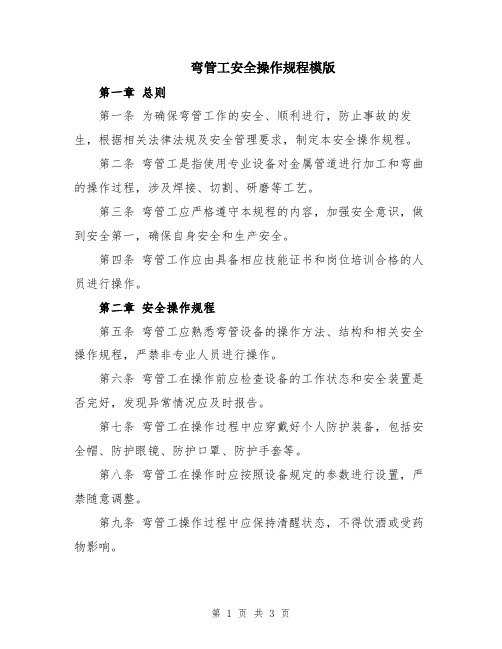
弯管工安全操作规程模版第一章总则第一条为确保弯管工作的安全、顺利进行,防止事故的发生,根据相关法律法规及安全管理要求,制定本安全操作规程。
第二条弯管工是指使用专业设备对金属管道进行加工和弯曲的操作过程,涉及焊接、切割、研磨等工艺。
第三条弯管工应严格遵守本规程的内容,加强安全意识,做到安全第一,确保自身安全和生产安全。
第四条弯管工作应由具备相应技能证书和岗位培训合格的人员进行操作。
第二章安全操作规程第五条弯管工应熟悉弯管设备的操作方法、结构和相关安全操作规程,严禁非专业人员进行操作。
第六条弯管工在操作前应检查设备的工作状态和安全装置是否完好,发现异常情况应及时报告。
第七条弯管工在操作过程中应穿戴好个人防护装备,包括安全帽、防护眼镜、防护口罩、防护手套等。
第八条弯管工在操作时应按照设备规定的参数进行设置,严禁随意调整。
第九条弯管工操作过程中应保持清醒状态,不得饮酒或受药物影响。
第十条弯管工应严格按照操作规程进行操作,不得擅自改变操作方法。
第十一条弯管工在操作过程中应保持设备周围的通道畅通,不得堆放杂物或放置障碍物。
第十二条弯管工应定期对设备进行维护保养,确保设备的正常运转。
第十三条弯管工操作完毕或暂停时,应及时关闭设备电源,清理现场并归还工具。
第十四条弯管工应定期参加安全培训,了解最新的安全操作规程和技术要求。
第十五条弯管工在操作过程中如发现异常情况或存在安全隐患应立即停止作业并上报。
第十六条弯管工不得将工作权力和责任转移给其他人员,严禁代替他人进行操作。
第三章安全事故处理第十七条弯管工在发生安全事故时,应立即停止作业,确保自身安全。
第十八条弯管工应立即向上级主管报告事故情况,并配合调查及处理工作。
第十九条弯管工应积极参与事故的处理工作,向有关部门提供必要的情况和资料。
第二十条弯管工应积极配合事故调查组进行调查工作,如实提供情况和证据。
第二十一条弯管工在事故处理过程中应保护现场,避免继续扩大事故范围。
管子弯曲作业指导书
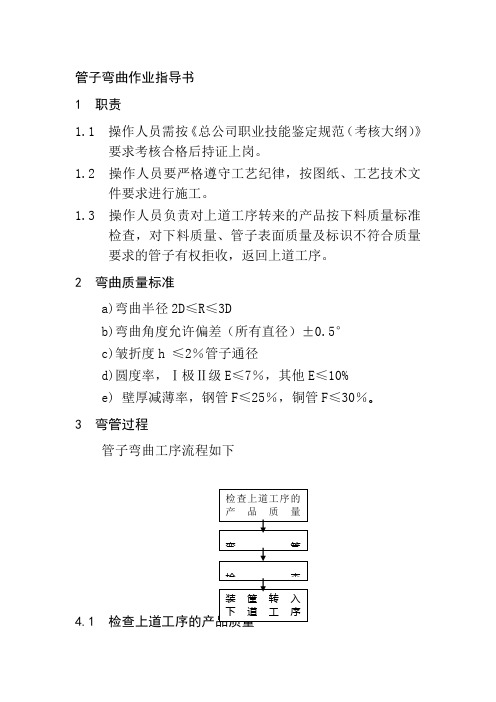
管子弯曲作业指导书
1 职责
1.1 操作人员需按《总公司职业技能鉴定规范(考核大纲)》
要求考核合格后持证上岗。
1.2 操作人员要严格遵守工艺纪律,按图纸、工艺技术文
件要求进行施工。
1.3 操作人员负责对上道工序转来的产品按下料质量标准
检查,对下料质量、管子表面质量及标识不符合质量
要求的管子有权拒收,返回上道工序。
2 弯曲质量标准
a)弯曲半径2D≤R≤3D
b)弯曲角度允许偏差(所有直径)±0.5°
c)皱折度h ≤2%管子通径
d)圆度率,Ⅰ极Ⅱ级E≤7%,其他E≤10%
e) 壁厚减薄率,钢管F≤25%,铜管F≤30%。
3 弯管过程
管子弯曲工序流程如下
4.1。
焊接弯管检验报告
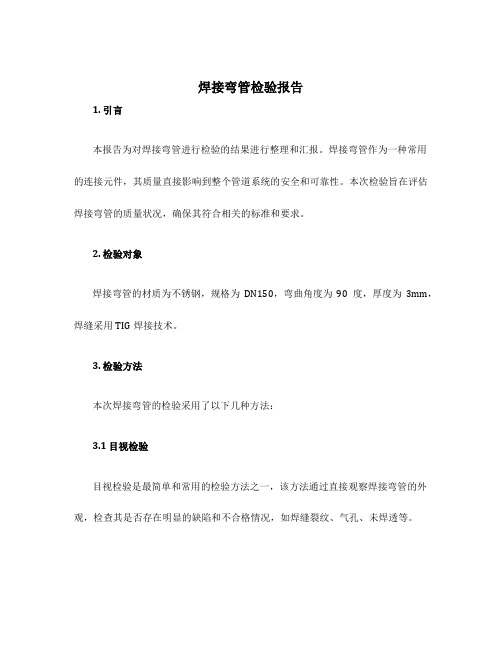
焊接弯管检验报告1. 引言本报告为对焊接弯管进行检验的结果进行整理和汇报。
焊接弯管作为一种常用的连接元件,其质量直接影响到整个管道系统的安全和可靠性。
本次检验旨在评估焊接弯管的质量状况,确保其符合相关的标准和要求。
2. 检验对象焊接弯管的材质为不锈钢,规格为DN150,弯曲角度为90度,厚度为3mm,焊缝采用TIG焊接技术。
3. 检验方法本次焊接弯管的检验采用了以下几种方法:3.1 目视检验目视检验是最简单和常用的检验方法之一,该方法通过直接观察焊接弯管的外观,检查其是否存在明显的缺陷和不合格情况,如焊缝裂纹、气孔、未焊透等。
3.2 射线检测射线检测是一种无损检测方法,通过对焊接弯管进行射线照射,利用射线的透射、散射和吸收等特性,来检测焊接弯管内部是否存在缺陷,如气孔、夹杂、边界不连续等。
3.3 声波检测声波检测是另一种无损检测方法,该方法通过将超声波传入焊接弯管,利用超声波在不同材料中传播速度和反射特性的差异,来检测焊接弯管内部是否存在缺陷,如裂纹、夹杂等。
4. 检验结果经过上述的检验方法,对焊接弯管的质量状况进行了评估,检验结果如下:4.1 目视检验结果通过目视检验,焊接弯管外观上未发现明显的焊缝裂纹、气孔和未焊透等不合格情况,焊接质量良好。
4.2 射线检测结果射线检测显示焊接弯管内部未发现明显的气孔、夹杂和边界不连续等缺陷,符合相关标准要求。
4.3 声波检测结果声波检测未检测到焊接弯管内部的裂纹、夹杂等缺陷,符合相关标准要求。
5. 结论综上所述,经过目视检验、射线检测和声波检测三种方法的检验,焊接弯管质量良好,符合相关的标准和要求。
该焊接弯管可以安全使用于管道系统中。
6. 建议在焊接弯管的生产和使用过程中,建议加强对焊接工艺的控制和监督,确保焊接质量的稳定性和可靠性。
另外,在检验过程中,还可以引入更多的检验方法,以提高检测的准确性和可靠性。
参考文献•XXX标准•XXX技术规范以上就是焊接弯管检验报告的内容,根据要求,本文档采用Markdown文本格式输出,方便阅读和编辑。
弯管制作工艺范文

弯管制作工艺范文1.材料准备:首先选择合适的管材作为原料,通常使用金属管材,如钢管、铝管、铜管等。
管材应具备良好的可弯曲性和韧性,以确保在加工过程中不会出现断裂或变形。
另外,还要根据弯曲的需求选择相应尺寸和材质的弯头和配件。
2.设计规划:根据需要制作弯管的要求,设计弯管的形状、角度和弯曲半径等参数。
在设计过程中需要考虑弯管的功能、安装环境、外观要求等因素。
3.弯管操作:将管材端部插入弯曲机械设备的弯头中,紧固好固定装置。
调整弯头的角度和位置,使其与设计要求一致。
启动弯曲机械设备,开始对管材进行弯曲加工。
通过调整弯曲机械设备的各个参数,如轴向力、旋转角度和速度等,使管材能够平稳、均匀地进行弯曲,避免局部过度压力导致管材变形或破损。
4.弯管检验:制作完成后,进行弯管的质量检验。
主要检查弯管的弯曲角度、形状和尺寸是否符合设计要求。
可以使用测量工具如坡度计、角尺、卷尺等进行测量。
同时,还需要检查弯管表面是否存在裂纹、凹陷或其他缺陷。
5.表面处理:根据需要对弯管的表面进行处理。
可采用砂光、抛光、喷涂等方法进行处理,以增加弯管的耐腐蚀性和美观度。
6.包装运输:根据弯管的尺寸和形状,选择合适的包装材料将其包装好。
在装箱过程中需要注意避免弯管的碰撞和磨损,以免影响其质量。
7.应用领域:弯管广泛应用于建筑、汽车、航空航天、石油化工等行业。
如建筑中的暖通空调管道、汽车中的排气管、航天器中的管路系统等。
总结:弯管制作工艺涉及到材料准备、设计规划、弯管操作、弯管检验、表面处理和包装运输等环节。
通过合理的设计和精湛的加工技术,可以制作出符合设计要求的高质量弯管。
弯管实验总结报告
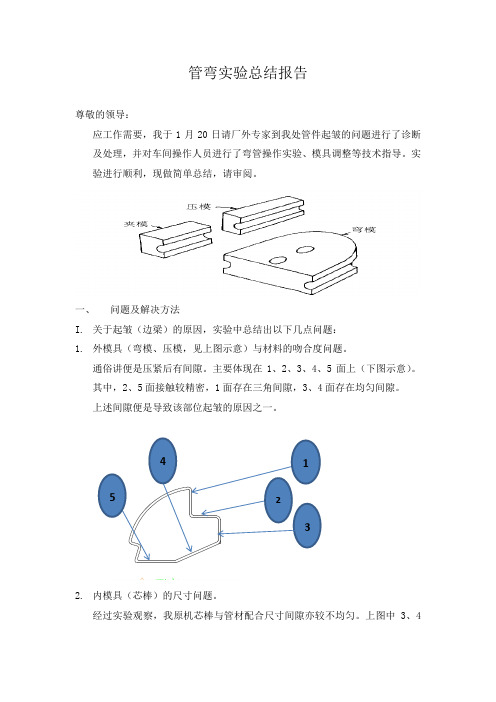
管弯实验总结报告尊敬的领导:应工作需要,我于1月20日请厂外专家到我处管件起皱的问题进行了诊断及处理,并对车间操作人员进行了弯管操作实验、模具调整等技术指导。
实验进行顺利,现做简单总结,请审阅。
一、 问题及解决方法I. 关于起皱(边梁)的原因,实验中总结出以下几点问题:1. 外模具(弯模、压模,见上图示意)与材料的吻合度问题。
通俗讲便是压紧后有间隙。
主要体现在1、2、3、4、5面上(下图示意)。
其中,2、5面接触较精密,1面存在三角间隙,3、4面存在均匀间隙。
上述间隙便是导致该部位起皱的原因之一。
2. 内模具(芯棒)的尺寸问题。
经过实验观察,我原机芯棒与管材配合尺寸间隙亦较不均匀。
上图中3、4面尤甚。
故此两面间隙也是导致该部位起皱的原因之一。
上述问题解决方法阐述:根据相关资料得知,理想的弯管状态是材料被夹紧后内外各面与模具紧密贴合,没有均匀间隙或斜角间隙。
这样的状态在管件弯曲的过程中能保证管件在受压后各接触面沿着弯模的曲线形变,且在内模的抵压下形成均匀弧形。
若有某一面或某几个面贴合较紧而其他面间隙较大,则有间隙面必会出现不规则曲面,即褶皱。
该情况间隙越大越明显。
上述1、2问题在实验中采取了加垫板的方法,即采用薄铁板塞入模具配合间隙,使内外模具与管材配合较贴切(有合适间隙),弯管后得出褶皱显著减轻。
但这种方法仅适用于单件实验,将来批量加工必须修正模具或重新开发模具。
最主要的就是弯模和芯棒。
3.弯前定位与弯后反弹量确定问题根据设备情况,我们当前弯管操作之起点(管材末端)后的各弯定位点需要根据图纸计算各角度弧长确定,并经实际弯管试验测量位移变化后确定其到达角度后的实际末端位移。
然而,管材在弯出角度的时候必然会有反弹且反弹量会根据材质与热处理情况的不同而不同。
这样的话盲目计算或者仅靠经验操作得出的结果会与图纸要求相差很多。
该问题解决方法阐述:这种情况就需经过多次试验得出最为理想的弯曲角度进而得到每个角度弯后中线圆弧长(即理论末端正确位移量),也就能确定最终的弯前定位点。
钢管弯管工艺参数介绍

硬管弯管工艺参数一、目的为了满足硬管产品弯管工艺的要求,确保产品在装配后两端的密封效果可靠,有必要对硬管产品弯管所涉及到的相关弯管工艺参数进行整理并归类,供设计时选用。
二、相关弯管工艺参数的定义:1、最合适弯曲半径R:弯曲时为了保证弯曲圆弧处圆滑,不褶皱而规定的最合适弯曲R轮半径。
2、最短距离L1:从管端口至弯曲起弯点间的距离。
(见附图)3、最短距离L2:连续两道圆弧间直线段距离。
(见附图)三、相关弯管工艺参数的主要内容:一)为了保证弯曲圆弧质量,对以下不同规格的硬管弯曲时所选用的最合适弯曲半径进行统计,供设计参考并选用。
序号 管材规格(mm) 最合适弯曲半径R 序号管材规格(mm) 最合适弯曲半径R1 Φ4.76x0.7 ≥15 19 Φ28x1.5 ≥1052 Φ6.0x0.7 ≥15 20 Φ31.8x1.5 ≥503 Φ6.35x0.7 ≥20 21 Φ35x1.2 ≥804 Φ8.0x0.7 ≥30 22 Φ38.1x1.5 ≥505 Φ10x0.7 ≥30 23 Φ54x1.5 ≥806 Φ12x0.7 ≥30 24 Φ57x1.8 ≥867 Φ12x1 ≥30 25 Φ60x1.2 ≥728 Φ8x1 ≥25 26 Φ63x1.2 ≥769 Φ10x1 ≥20 27 Φ70x2.5 ≥8510 Φ10x2 ≥20 28 Φ80x1.5 ≥10011 Φ12x1 ≥30 29 Φ90x1.5 ≥11012 Φ14x1.5 ≥35 30 Φ100x1.5 ≥12013 Φ15x1.5 ≥40 31 Φ101.6x1.5 ≥12214 Φ16x1.5 ≥40 32 Φ110x1.8 ≥13215 Φ18x1.5 ≥45 33 Φ120x2 ≥14516 Φ20x1.5 ≥5017 Φ22x1.5 ≥7018 Φ25x1.5 ≥70二)为了确保油管装配后的有效连接并密封可靠,必须要保证弯曲起弯后切点至管端口距离L1不小于下表中规定的数值。
弯管加工工艺范文
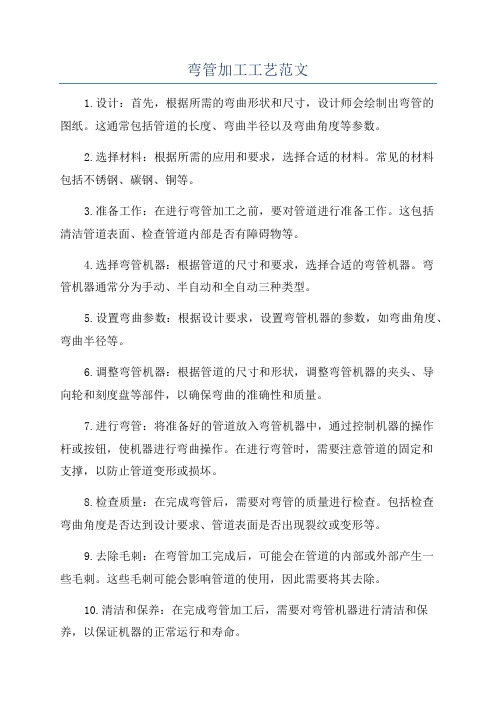
弯管加工工艺范文1.设计:首先,根据所需的弯曲形状和尺寸,设计师会绘制出弯管的图纸。
这通常包括管道的长度、弯曲半径以及弯曲角度等参数。
2.选择材料:根据所需的应用和要求,选择合适的材料。
常见的材料包括不锈钢、碳钢、铜等。
3.准备工作:在进行弯管加工之前,要对管道进行准备工作。
这包括清洁管道表面、检查管道内部是否有障碍物等。
4.选择弯管机器:根据管道的尺寸和要求,选择合适的弯管机器。
弯管机器通常分为手动、半自动和全自动三种类型。
5.设置弯曲参数:根据设计要求,设置弯管机器的参数,如弯曲角度、弯曲半径等。
6.调整弯管机器:根据管道的尺寸和形状,调整弯管机器的夹头、导向轮和刻度盘等部件,以确保弯曲的准确性和质量。
7.进行弯管:将准备好的管道放入弯管机器中,通过控制机器的操作杆或按钮,使机器进行弯曲操作。
在进行弯管时,需要注意管道的固定和支撑,以防止管道变形或损坏。
8.检查质量:在完成弯管后,需要对弯管的质量进行检查。
包括检查弯曲角度是否达到设计要求、管道表面是否出现裂纹或变形等。
9.去除毛刺:在弯管加工完成后,可能会在管道的内部或外部产生一些毛刺。
这些毛刺可能会影响管道的使用,因此需要将其去除。
10.清洁和保养:在完成弯管加工后,需要对弯管机器进行清洁和保养,以保证机器的正常运行和寿命。
弯管加工工艺具有许多优点。
首先,它可以根据需要制作各种形状和尺寸的管道,满足不同工业应用的需求。
其次,相比于其他加工方法,弯管加工可以减少焊接和连接的次数,降低成本和加工时间。
此外,弯管加工还可以减少管道系统中的接头和连接,提高管道系统的密封性和可靠性。
然而,弯管加工也存在一些挑战。
首先,弯管加工过程中,管道可能会受到压力和变形,容易产生裂纹和变形等质量问题。
其次,对于一些特殊形状和要求较高的管道,弯管加工可能需要精密的设备和操作技术,增加了加工难度和成本。
总之,弯管加工工艺是一种常用的金属管道加工方法,具有广泛的应用前景。
弯管制作工艺
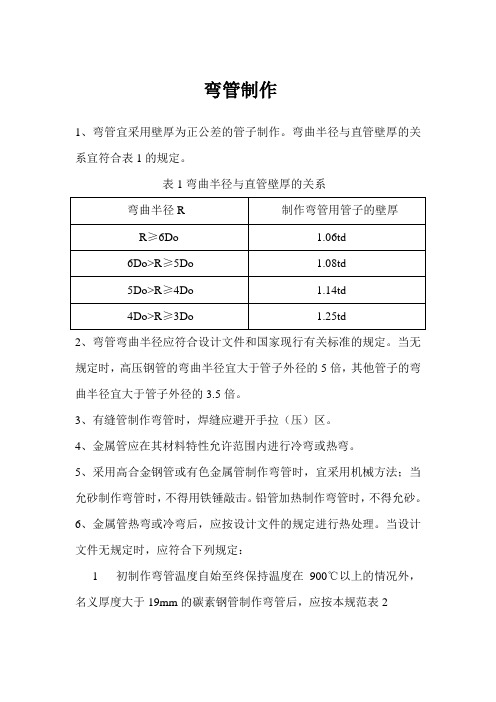
弯管制作1、弯管宜采用壁厚为正公差的管子制作。
弯曲半径与直管壁厚的关系宜符合表1的规定。
表1弯曲半径与直管壁厚的关系弯曲半径R 制作弯管用管子的壁厚R≥6Do 1.06td6Do>R≥5Do 1.08td5Do>R≥4Do 1.14td4Do>R≥3Do 1.25td2、弯管弯曲半径应符合设计文件和国家现行有关标准的规定。
当无规定时,高压钢管的弯曲半径宜大于管子外径的5倍,其他管子的弯曲半径宜大于管子外径的3.5倍。
3、有缝管制作弯管时,焊缝应避开手拉(压)区。
4、金属管应在其材料特性允许范围内进行冷弯或热弯。
5、采用高合金钢管或有色金属管制作弯管时,宜采用机械方法;当允砂制作弯管时,不得用铁锤敲击。
铅管加热制作弯管时,不得允砂。
6、金属管热弯或冷弯后,应按设计文件的规定进行热处理。
当设计文件无规定时,应符合下列规定:1 初制作弯管温度自始至终保持温度在900℃以上的情况外,名义厚度大于19mm的碳素钢管制作弯管后,应按本规范表2表2 管道热处理基本要求母材类别名义厚度t(mm)母材最小规定抗拉强度(Mpa)热处理温度(℃)恒温时间(mim/mm)最短恒温时间(h)碳钢(C)、≤19全部不要求——碳锰钢(C-Mn) >19 全部600~650 2.4 1 铬钼合金钢≤19≤490不要求——(C-Mo、Mn-Mo、Cr-Mo) >19 全部600~720 2.4 1 Cr≤0.5%全部>490 600~720 2.4 1 铬钼合金钢(C-Mo)≤13≤490不要求——0.5%<Cr≤2%>13 全部700~750 2.4 2全部>490 700~750 2.4 2 铬钼合金钢(Cr-Mo)≤13全部不要求——2.25%≤Cr≤3%>13 全部700~760 2.4 2 铬钼合金钢(Cr-Mo)3%<Cr≤10%全部全部700~760 2.4 2 马氏体不锈钢全部全部不要求——铁素体不锈钢全部全部不要求——奥氏体不锈钢全部全部不要求——低温镍钢≤19全部不要求——(Ni≤4%)>19 全部600~640 1.2 1 注:热处理的加热速率和冷却速率应符合下列规定:1 当加热温度升至400℃时,加热速率不应超过(205×25/t)℃/h,且不得大于205℃/h。
弯管工艺守则

弯管工艺守则一、弯管前的准备工作1、材料选择选用符合设计要求的管材,材质、规格和壁厚应符合标准。
检查管材表面质量,确保无裂纹、凹陷、划伤等缺陷。
2、弯管设备的检查与调试检查弯管机的各个部件是否正常,如模具、夹具、传动系统等。
调试弯管机的参数,如弯曲角度、弯曲半径、推进速度等,以适应即将进行的弯管操作。
3、测量与标记根据设计图纸,准确测量管材需要弯曲的位置和长度,并做好标记。
使用合适的量具,如卷尺、角尺等,确保测量的准确性。
二、弯管操作要点1、装夹管材将管材正确地安装在弯管机的夹具上,确保管材的中心线与弯管模具的中心线重合。
夹紧管材,防止在弯曲过程中发生移动或松动。
2、弯曲过程启动弯管机,按照预设的参数进行弯曲操作。
控制弯曲速度,避免过快或过慢,以保证弯曲质量。
在弯曲过程中,密切观察管材的变形情况,如有异常应立即停机检查。
3、弯曲角度的控制利用弯管机上的角度测量装置,实时监测弯曲角度,确保达到设计要求。
对于精度要求高的弯管,可进行多次微调,以达到准确的角度。
4、弯曲半径的控制根据设计要求选择合适的弯管模具,确保弯曲半径符合规定。
检查弯曲后的管材半径,如有偏差应及时调整工艺参数或更换模具。
三、弯管后的处理1、外观检查检查弯曲后的管材外观,是否有褶皱、裂纹、过度变薄等缺陷。
对于表面有轻微缺陷的管材,可以进行修复处理,如打磨、补焊等。
2、尺寸测量再次测量弯曲后的管材尺寸,包括弯曲角度、弯曲半径、长度等,确保符合设计要求。
如有尺寸偏差过大的情况,应分析原因,采取相应的纠正措施。
3、去应力处理对于某些材质的管材,弯曲后可能会产生残余应力,需要进行去应力处理,如热处理等。
去应力处理应按照相关标准和规范进行,确保管材性能不受影响。
四、质量检验标准1、弯曲角度偏差一般情况下,弯曲角度偏差应控制在±1°以内。
对于高精度要求的弯管,角度偏差应更小,具体根据设计要求确定。
2、弯曲半径偏差弯曲半径偏差应不超过设计半径的±5%。
薄壁不锈钢管弯管工艺
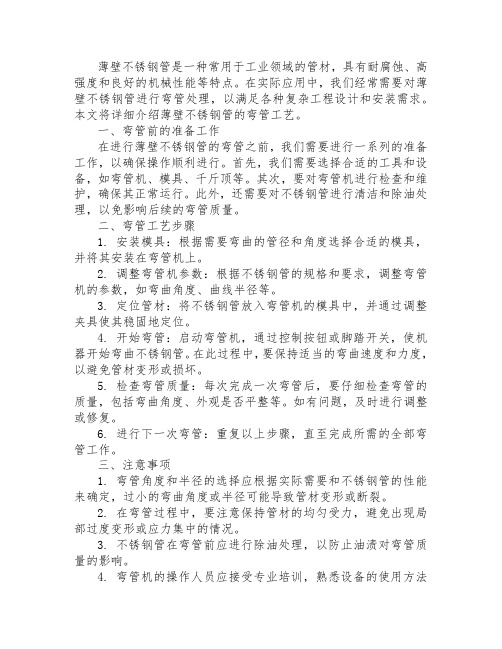
薄壁不锈钢管是一种常用于工业领域的管材,具有耐腐蚀、高强度和良好的机械性能等特点。
在实际应用中,我们经常需要对薄壁不锈钢管进行弯管处理,以满足各种复杂工程设计和安装需求。
本文将详细介绍薄壁不锈钢管的弯管工艺。
一、弯管前的准备工作在进行薄壁不锈钢管的弯管之前,我们需要进行一系列的准备工作,以确保操作顺利进行。
首先,我们需要选择合适的工具和设备,如弯管机、模具、千斤顶等。
其次,要对弯管机进行检查和维护,确保其正常运行。
此外,还需要对不锈钢管进行清洁和除油处理,以免影响后续的弯管质量。
二、弯管工艺步骤1. 安装模具:根据需要弯曲的管径和角度选择合适的模具,并将其安装在弯管机上。
2. 调整弯管机参数:根据不锈钢管的规格和要求,调整弯管机的参数,如弯曲角度、曲线半径等。
3. 定位管材:将不锈钢管放入弯管机的模具中,并通过调整夹具使其稳固地定位。
4. 开始弯管:启动弯管机,通过控制按钮或脚踏开关,使机器开始弯曲不锈钢管。
在此过程中,要保持适当的弯曲速度和力度,以避免管材变形或损坏。
5. 检查弯管质量:每次完成一次弯管后,要仔细检查弯管的质量,包括弯曲角度、外观是否平整等。
如有问题,及时进行调整或修复。
6. 进行下一次弯管:重复以上步骤,直至完成所需的全部弯管工作。
三、注意事项1. 弯管角度和半径的选择应根据实际需要和不锈钢管的性能来确定,过小的弯曲角度或半径可能导致管材变形或断裂。
2. 在弯管过程中,要注意保持管材的均匀受力,避免出现局部过度变形或应力集中的情况。
3. 不锈钢管在弯管前应进行除油处理,以防止油渍对弯管质量的影响。
4. 弯管机的操作人员应接受专业培训,熟悉设备的使用方法和安全操作规程,以确保人身安全和操作质量。
四、常见问题及解决办法1. 弯管过程中出现管材折断的情况:可能是由于不锈钢管的质量问题或者弯曲力度过大导致的,需要更换质量可靠的管材或调整弯曲参数。
2. 弯管后出现不平整或外观不良的情况:可能是由于模具损坏或者弯管机参数调整不当导致的,需要进行相应的维修或调整。
弯管制作工艺方案

弯管制作工艺方案1弯管加工制作工艺流程2弯管加工方式本工程结构呈花瓣形状,构件多为空间多向弯曲,深化设计过程中运用多段平面弯管进行拟合的思路,将空间多向弯曲构件转换为平面内单向弯曲构件,有效地解决了空间多向弯曲构件加工的难题,使得加工效率更高,精度更有保证。
弯管加工一般采用两种方式,分别为冷弯加工成形与热加工成形。
对于需进行弯管的构件,截面≥800mm的钢管采用中频弯圆,对截面<800mm的钢管采用机械冷弯。
先确定其弯曲半径、弯曲管件的起始点及终点,并做好标记,然后用JXW-700型弯管机或弯制模具进行管件的弯圆。
弯曲后,钢管表面不能出现折痕和凹凸不平的现象。
弯圆后切割端头,并在工装划出纵向直线,相隔 90°四条及节点圆周环线,并打样冲眼,以便于钢管的对接。
当钢管采用热加工成形时,一般采用中频或高频弯管机,加热温度应控制在900~1000℃;碳素结构钢管和低合金结构管在温度下降到400℃以下时应结束加工,低合金结构钢应自然冷却。
中高频弯圆的钢管避免多次加热。
多次加热会导致材质变脆,造成硬化。
同时,加工温度过低时,应避免强行弯曲。
JXW-700型弯管机制弯模具中频弯管机中频弯管机制作成品3弯管放样利用计算机数控模拟放样,使单根杆件两端在同一水平线内,确定弯管半径,放样时应留出足够的余量,如下图:4弯管厚度减薄补偿弯管在制作过程中,由于外径表面存在拉伸作用,厚度难以避免存在减薄的情况,按照相关规范,壁厚与设计壁厚的的差值不得大于±1mm及设计壁厚的10%中的较小值。
如果制作成品差值不满足要求时,需加大管壁以满足设计要求。
弯管制作厚度减薄率计算方式如下:式中φ——弯曲角度,radD——外直径,mmδ1——弯曲后外侧管壁壁厚,mmδ0——弯曲前外侧管壁壁厚,mm根据以上公式可知弯管壁厚减薄率的计算公式为:式中C——弯管壁厚减薄率由于理论计算与实际操作偏差,弯管批量制作前,应进行试弯试验,经检定合格后得出相应工艺参数后,才能进行批量制作。
弯管工艺检验规程
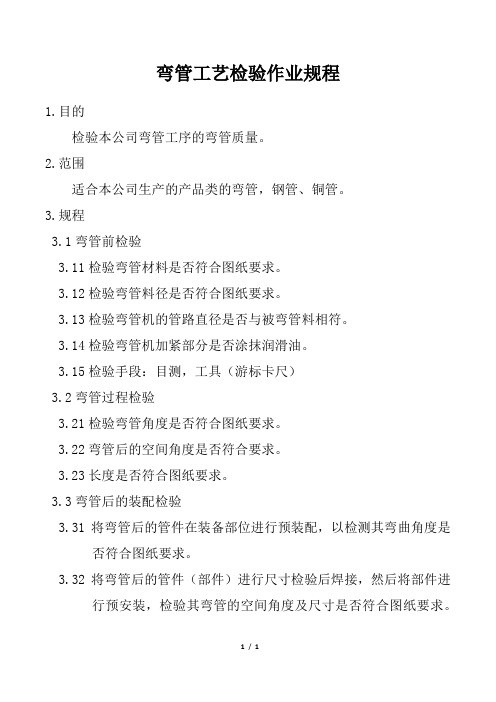
弯管工艺检验作业规程
1.目的
检验本公司弯管工序的弯管质量。
2.范围
适合本公司生产的产品类的弯管,钢管、铜管。
3.规程
3.1弯管前检验
3.11检验弯管材料是否符合图纸要求。
3.12检验弯管料径是否符合图纸要求。
3.13检验弯管机的管路直径是否与被弯管料相符。
3.14检验弯管机加紧部分是否涂抹润滑油。
3.15检验手段:目测,工具(游标卡尺)
3.2弯管过程检验
3.21检验弯管角度是否符合图纸要求。
3.22弯管后的空间角度是否符合要求。
3.23长度是否符合图纸要求。
3.3弯管后的装配检验
3.31将弯管后的管件在装备部位进行预装配,以检测其弯曲角度是
否符合图纸要求。
3.32将弯管后的管件(部件)进行尺寸检验后焊接,然后将部件进
行预安装,检验其弯管的空间角度及尺寸是否符合图纸要求。
1/ 1。
弯管成型工艺评定记录

下料长度mm
材质
《
φ×8
8
1700
API 5L X42
成型工艺参数
加热温度
工进速度
感应加热功率
感应加热频率
冷却水温度
流速
【
热处理温度
850±50℃
25-60mm/min
60KW
1000HZ
30℃
10m/s
520℃
弯管尺寸和外观检验
椭圆度
>
曲率半径
端面平面度
钝边
直管段直径偏差
762
φ~φ
弯曲角度
操作人:
评定人:
&
评定日期:
《
抚通亿通石油化工设备厂
弯管工艺评定报告
评定记录编号:YT/JL508-04 A/0
№:
工艺编号:YT/JS-14 A/0/NO:
产品名称
规格型号
材质
角度
生产设备
弯曲半径
执行标准
弯管90°5D
φ×
API 5L X42
@
90°
YY-200#弯管机
R=762
ASME
材料
规格
原材料规格/㎜
`
130
137
128
137
126
129
外弧弯曲段
《
127
131
130
133
127
126
其他:磁粉探伤:合格,探伤人员:关少华柳俊江报告编号:140420
:弯管Biblioteka 型工艺评定结论:依据标准的要求,通过对弯管φ×成型工艺试验,经检验完全符合标准要求,
上述检验结果属实,该成型工艺能够支持生产规格 _φ×钢管的生产。
WB36钢弯管工艺评定
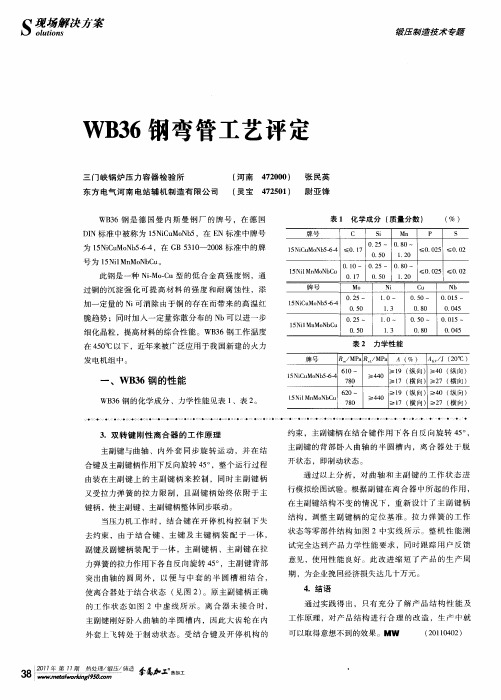
WB 6钢 的化学 成分 、力学 性 能见表 1 3 、表 2 。
L● n● ●f ◆ l ● l ● 0u● [ ● 00 ● t ● r t ● 00 ● 0 ◆ 00 ● ( 、 、 、 、 ● L ◆ L ◆ 0 l ● 0 ◆ 、 、) l ◆ ● lL◆ ( 1◆ l 。 l
、
WB 6钢 的性能 3
I 5
u Nb - 4 Mo 5 6-
≥1 ( 向 ) >4 ( 向 ) 9 纵 / 0 纵
70 8
i Mn Nb 1 Mo Cu
≥1 ( 向 ) >2 ( 向 ) 7 横 I 7 横
≥4 0 4
6 0~ 2
≥1 ( 向 ) >4 ( 向 ) 9 纵 / 0 纵
在 4 0 以下 ,近 年来 被广 泛应用 于 我 国新 建 的火 力 5℃ 发 电机组 中。
一
O 5 . 0
表 2 力 学 性 能
牌 号 l NC 5 i R / aRL MP 4 f ) A v J (O ) MP / a % K/ 2 ℃ 6 O~ l
≥4 0 4
号 为 1 N l Mo b u 5 iMn N C 。
O 2 ~ 0 8 . 5 . 0~ 1 5Ni Mo 5 6- ≤0. 7 Cu Nb - 4 1 0 5 .O 12 . O ≤0. 2 ≤O O 0 5 . 2
0. 0 ~ O 2 1 . 5~ O 8 . O~
使离 合器 处 于结 合状 态 ( 图 2) 见 。原 主 副键 柄 正 确 的工 作 状 态 如 图 2中虚 线 所 示 。离 合 器 未接 合 时 , 主 副键 刚好 卧 人 曲 轴 的半 圆槽 内 ,因 此 大齿 轮 在 内
弯管检测报告
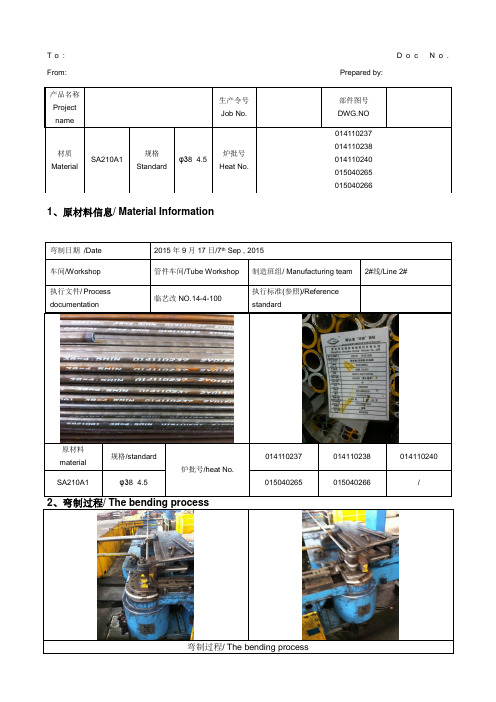
1、原材料信息/ Material Information2、弯制过程/ The bending process弯制过程/ The bending process产品名称 Project name生产令号 Job No.部件图号 DWG.NO材质 MaterialSA210A1规格 Standardφ38×4.5炉批号 Heat No.014110237014110238 014110240 015040265 015040266弯制日期 /Date 2015年9月17日/7th Sep , 2015 车间/Workshop 管件车间/Tube Workshop制造班组/ Manufacturing team 2#线/Line 2#执行文件/ Process documentation临艺改NO.14-4-100 执行标准(参照)/Reference standard原材料material 规格/standard炉批号/heat No.014110237014110238014110240SA210A1φ38×4.5015040265015040266/弯管机弯制参数/Machine data of bending 椭圆度测量(Ovality measurement)测量点编号/Measurement point number 壁厚测量/Thickness measurement4、测量数据/Measured data检测数据依据图编号,依次对每批次炉号测量三只弯管,测量数据见表(弯管内侧壁厚需解剖后测量): Testing data according to the drawing number, each heat No. measuring three bends. Data shows in the table. (Inside thickness data needs cutting)Thickness Inspection PointThickness Inspection PointBend half-and-half cut openR38*厚度数据仅供参考/The thickness data is for reference only.5、掰开后PT检测/ PT test After opening the bends45°90°PT检测/PT test6、结论Result对成品尺寸按要求进行测量,符合标准要求。
船舶管系弯管
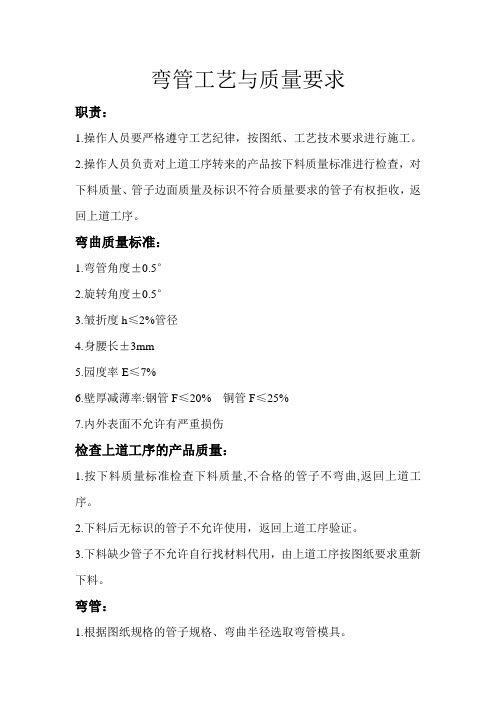
弯管工艺与质量要求
职责:
1.操作人员要严格遵守工艺纪律,按图纸、工艺技术要求进行施工。
2.操作人员负责对上道工序转来的产品按下料质量标准进行检查,对下料质量、管子边面质量及标识不符合质量要求的管子有权拒收,返回上道工序。
弯曲质量标准:
1.弯管角度±0.5°
2.旋转角度±0.5°
3.皱折度h≤2%管径
4.身腰长±3mm
5.园度率E≤7%
6.壁厚减薄率:钢管F≤20% 铜管F≤25%
7.内外表面不允许有严重损伤
检查上道工序的产品质量:
1.按下料质量标准检查下料质量,不合格的管子不弯曲,返回上道工序。
2.下料后无标识的管子不允许使用,返回上道工序验证。
3.下料缺少管子不允许自行找材料代用,由上道工序按图纸要求重新下料。
弯管:
1.根据图纸规格的管子规格、弯曲半径选取弯管模具。
2.根据管子外径、弯曲半径、管子材质、管子壁厚等,选择芯棒规格、回强度数、芯棒提前量、滑板压力、助推压力。
检查:
1.自检-正式弯管前,换好模具,先弯曲一根管子,按弯管质量标准进行检查,合格后方可进行批量弯曲。
2.互检-弯好后,由领班等成员对度数、身腰长短、转角等进行检查后,施工人员在托盘单上签名,方可转入下道工序。
- 1、下载文档前请自行甄别文档内容的完整性,平台不提供额外的编辑、内容补充、找答案等附加服务。
- 2、"仅部分预览"的文档,不可在线预览部分如存在完整性等问题,可反馈申请退款(可完整预览的文档不适用该条件!)。
- 3、如文档侵犯您的权益,请联系客服反馈,我们会尽快为您处理(人工客服工作时间:9:00-18:30)。
式中:D:弯管直管段外径; Dmax:弯管横截面上的最大外径; Dmin:弯管横截面上的最小外径, 三、波浪度要求: 弯曲部分波浪度应符合设计要求,弯管表面不允许有明显褶皱,内弧侧波 浪度 h 应不大于 1.32mm,且波浪间距 f 与波浪度 h 之比(f/h)应大于 150. 四、减薄率要求: 弯曲外弧侧最大减薄率应不大于 9%。 五、弯曲角要求: 弯管弯曲角度最大偏差为±0.5°。 六、弯管平面度要求: 弯管公称直径 DN≤20mm 时,平面度 a 1mm 。 弯管公称直径 DN 大于 20mm 时,平面度 a 2mm 。 七、弯管的弯曲半径(R)允许偏差为: 弯曲半径 R 不大于 30mm 时,弯管弧的弯曲半径 R 的最大偏差为 2mm;
1
c.按规定进行试验并出具试验报告。 六、评定结果处理: 1.技术工程部组织相关专业人员对评定数据进行综合判定; a.当重复评定能够达到要求时,可视为评定有效。 b.当评定结果与首次评定结果又差异时,要识别是正常的波动还是异常波动, 必要时进行第三次评定,以重复验证评定结果。 2.评定结果不满足评定要求的,应查找原因,重新制定评定方案并实施。 3.评定结果符合要求的,由技术工程部负责收集整理评定资料并保存。
编制:XXX
审核:
批准:
2
弯管工艺评定报告
序号:
项目名称 设备规格/型号 评定名称 XXXXX 半自动单头弯管机 弯管工艺评定 时间 地点 评定原因 XX车间 新工艺生产
编号:
评定目的
规范弯管工艺评定,确保弯管产品质量
原材料机械性能: 屈服强度 牌号 304 弯管指导工艺规范: 1.母管表面处理; 2.设备检查; 3.调整曲率半径; 4.上机定位; 5.弯管操作; 6.下机; 7.割取弯管; 205
编制:XXX
审核:
批准:
5
极限抗拉强度
MPa(min)
延伸率
(%)
厚度(最大) 布氏 201 洛氏 92
MPa(min)
515
40
8.依据标准对弯管进行标识;
过程评定结论: 此过程严格遵守工艺文件操作。
3
弯管检测项点: 一、整体外观: 无裂纹、折叠、重皮、凹陷、尖锐划痕,弯管处无过烧组织,无晶间裂纹。 二、椭圆度要求: 椭圆度符合设计要求,弯管距管端 100mm 范围内,椭圆度应不大于母管 规定值,弯曲部分椭圆度应不大于 1%。 圆度 B 的计算公式;
4
弯曲半径 R 大于 30mm 时,弯管弧的弯曲半径 R 的最大偏差为 3mm; 八、合金钢弯管热处理后的硬度值,金相组织和晶粒度符合相应钢管技术标准 要求。 九、端面垂直度和平面度: 弯管公称直径 DN≤20mm 时,弯管端面的垂直度 Q≤1mm; 弯管公称直径 DN 大于 20mm 时,弯管端面的垂直度 Q≤1.5mm; 弯管平面度应不大于 0.5mm。 检验评定结论: 通过以上项点检测项点检验验证,此工艺能够满足产品设计要求,可以指 导正式生产。
弯管工艺评定规程
序号: 编号: 一、目的:规范弯管工艺评定,确保弯管产品质量 二、适用范围:适用于本公司XXXXX不锈钢管弯管工艺质量的验证; 三、评定的提出: 1.新作业方式用于生产; 2.新工艺应用于生产时; 3.其他认为应该进行弯管工艺评定时。 若条件符合其中之一,必须进行弯管工艺评定。 四、评定准备: 1.在接到评定通知后,技术工程部准备评定的具体实施方案; 2.评定的实施,由技术工程部,生产部,质保部,生产车间进行评定; 3.在评定之前,质保部必须进行弯管过程确认,确保过程质量; 4.生产部、生产车间做好生产、设备及操作人员安排。 五、评定程序: 1.评定应达到的要求:原材料的应用,应达到相应极限抗拉强度、屈服强度 及延伸率标准的最低要求。 2.弯管工序按批准的工艺文件进行相应的弯管操作。 3.质保部对整个工艺评定过程进行详细质量跟踪。 4.试验检测: a.过程无误后,进行机械性能、整体平面度相关试验、检测; b.机械性能按技术要求检测,在机械性能及整体平面度试验中,注意不要改变 样件的性能