锂离子电池电芯设计步骤
软包锂离子电池制作工艺流程详解

软包锂离子电池制作工艺流程详解2018-04-27电动知家1、软包电芯所谓的软包电芯,其实就是使用了铝塑包装膜作为包装材料的电芯。
相对来说,锂离子电池的包装分为两大类,一类是软包电芯,一类是金属外壳电芯。
金属外壳电芯又包括了钢壳与铝壳等等,近年来由于特殊需要有的电芯采用塑料外壳的,也可以划为此类。
二者的差别出了外壳材料不同,决定了其封装方式也不同。
软包电芯采用的是热封装,而金属外壳电芯一般采用焊接(激光焊)。
软包电芯可以采用热封装的原因是其使用了铝塑包装膜这种材料。
2、铝塑包装膜铝塑包装膜(简称铝塑膜)的构成见图,其截面上来看有三层构成:尼龙层、A l层与P P层。
三层各有各的作用,首先尼龙层是保证了铝塑膜的外形,保证在制造成锂离子电池之前,膜不会发生变形。
A l层就是一层金属A l构成,其作用是防止水的渗入。
锂离子电池很怕水,一般要求极片含水量都在P P M级,所以包装膜一定能够挡住水气的渗入。
尼龙不防水,无法起到保护作用。
而金属A l在室温下会与空气中的氧反应生成一层致密的氧化膜,导致水气无法渗入,保护了电芯的内部。
A l层在铝塑膜成型的时候还提供了冲坑的塑性,这个详见第3点。
P P是聚丙烯的缩写,这种材料的特性是在一百多摄氏度的温度下会发生熔化,并且具有黏性。
所以电池的热封装主要靠的就是P P层在封头加热的作用下熔化黏合在一起,然后封头撤去,降温就固化黏结了。
铝塑膜看上去很简单,实际做起来,如何把三层材料均匀地、牢固地结合在一起也不是那么容易的事。
很遗憾的是,现在质量好的铝塑膜基本上都是日本进口的,国产的不是没有,但质量还有待改进。
3、铝塑膜成型工序软包电芯可以根据客户的需求设计成不同的尺寸,当外形尺寸设计好后,就需要开具相应的模具,使铝塑膜成型。
成型工序也叫作冲坑(其实个人觉得应该是“铳坑”,但大家都这么写就随俗吧),顾名思义,就是用成型模具在加热的情况下,在铝塑膜上冲出一个能够装卷芯的坑,具体的见下图铝塑膜冲好并裁剪成型后,一般称为P o c k e t袋,见下图所示。
锂电池电芯的生产工艺

锂电池电芯的生产工艺一、锂电池生产制造流程及核心设备(一)生产流程锂电池的生产工艺分为前、中、后三个阶段,前段工序的目的是将原材料加工成为极片,核心工序为涂布;中段目的是将极片加工成为未激活电芯;后段工序是检测封装,核心工序是化成、分容。
锂电设备按照电池生产制造流程,划分为前段设备、中段设备、后段设备。
前段设备价值占比约40%,其中涂布机价值占75%,辊压机价值大于分切机。
三元材料对前段设备的性能要求更高,前段设备价值占比会逐步增加。
中段设备价值占比约30%,其中卷绕机价值占比70%。
目前卷绕机市场集中度较高,CR3达到60%-70%。
卷绕机高端市场受到韩国KOEM和日本CKD的竞争,国内高端市占率50%。
后段设备价值占比约30%,其中化成分容系统占70%,组装占30%(二)前段:打造涂覆有正负极活性物质的极片1、前段工序前段工序主要包括浆料搅拌、正负极涂布、辊压、分切、极片制作和模切。
搅拌:先使用锂电池真空搅拌机,在专用溶剂和黏结剂的作用下,混合粉末状的正负极活性物质,经过高速搅拌均匀后,制成完全没有气泡的浆状正负极物质。
涂布:将制成的浆料均匀涂覆在金属箔的表面,烘干,分别制成正、负极极片。
辊压:辊压机通过上下两辊相向运行产生的压力,对极片的涂布表面进行挤压加工,极片受到高压作用由原来蓬松状态变成密实状态的极片,辊压对能量密度的明显相当关键。
分切:将辊压好的电极带按照不同电池型号,切成装配电池所需的长度和宽度,要求在切割时不出现毛刺。
2、涂布机涂布的主要目的是将稳定性好、粘度好、流动性好的浆料,均匀地涂覆在正负极表面上。
其对锂电池的重要意义主要体现在一致性、循环寿命、安全性三方面。
在涂布过程中,若极片前、中、后三段位置正负极浆料涂层厚度不一致,或者极片前后参数不一致,则容易引起电池容量过低或过高,且可能在电池循环过程中形成析锂,影响电池寿命。
涂布过程要严格确保没有颗粒、杂物、粉尘等混入极片中,如果混入杂物会引起电池内部微短路,严重时导致电池起火爆炸。
软包锂离子电池制作工艺流程详解!

软包锂离子电池制作工艺流程详解!1软包电芯所谓的软包电芯,其实就是使用了铝塑包装膜作为包装材料的电芯。
相对来说,锂离子电池的包装分为两大类,一类是软包电芯,一类是金属外壳电芯。
金属外壳电芯又包括了钢壳与铝壳等等,近年来由于特殊需要有的电芯采用塑料外壳的,也可以划为此类。
二者的差别出了外壳材料不同,决定了其封装方式也不同。
软包电芯采用的是热封装,而金属外壳电芯一般采用焊接(激光焊)。
软包电芯可以采用热封装的原因是其使用了铝塑包装膜这种材料。
2铝塑包装膜铝塑包装膜(简称铝塑膜)的构成见图,其截面上来看有三层构成:尼龙层、Al(铝)层与PP层。
三层各有各的作用,首先尼龙层是保证了铝塑膜的外形,保证在制造成锂离子电池之前,膜不会发生变形。
Al层就是一层金属Al构成,其作用是防止水的渗入。
锂离子电池很怕水,一般要求极片含水量都在PPM级,所以包装膜一定能够挡住水气的渗入。
尼龙不防水,无法起到保护作用。
而金属Al在室温下会与空气中的氧反应生成一层致密的氧化膜,导致水气无法渗入,保护了电芯的内部。
Al层在铝塑膜成型的时候还提供了冲坑的塑性,这个详见第3点。
PP是聚丙烯的缩写,这种材料的特性是在一百多摄氏度的温度下会发生熔化,并且具有黏性。
所以电池的热封装主要靠的就是PP层在封头加热的作用下熔化黏合在一起,然后封头撤去,降温就固化黏结了。
铝塑膜看上去很简单,实际做起来,如何把三层材料均匀地、牢固地结合在一起也不是那么容易的事。
很遗憾的是,现在质量好的铝塑膜基本上都是日本进口的,国产的不是没有,但质量还有待改进。
3铝塑膜成型工序软包电芯可以根据客户的需求设计成不同的尺寸,当外形尺寸设计好后,就需要开具相应的模具,使铝塑膜成型。
成型工序也叫作冲坑(其实个人觉得应该是“铳坑”,但大家都这么写就随俗吧),顾名思义,就是用成型模具在加热的情况下,在铝塑膜上冲出一个能够装卷芯的坑,具体的见下图。
公众号《机械工程文萃》,工程师的加油站!铝塑膜冲好并裁剪成型后,一般称为Pocket袋,见下图所示。
191113 软包锂离子电芯设计指南

一、设计 3、极片长度简单计算(以中型号为例)
A=B=极耳宽度+3+3;C=卷芯宽度/2+8; D=(卷芯宽度+卷芯厚度)*2+C;L1=正极 片长度(不含尾部短空箔)+C
卷芯构图
E=卷针宽度+5;F=卷针宽度*3+5;短料 长=正极片短料长+18~22;长料长=正极 片长料长+8~12;L2=E/F+短料长/长料长
体系2: 正极:ZX: RC: SP: NMP=100: 1.6: 1.3: 40 负极:FS: SF: CMC: SBR: H2O=100: 1: 1.6: 4.2: 92 设计压实比:正极4.10±0.05,负极1.45±0.05 电解液:LD 混料容量发挥:141~142mAh/g(以1500mAh电芯容量为基准) 面密度比:2.12 体系特点:设计容量较低,常温&45℃循环性能好(可满足0.5C/500周 80%), 长时间常温存储性能好
4)、正极耳处贴胶纸要求: 胶纸长度需保证完全覆盖极耳,并覆盖极耳胶 0.1~1mm 5)、模壳设计: 上模腔尺寸:宽度=电池宽度最大值-1.0~2.5
高度=电池高度最大值-4.0~5.2 冲头尺寸:宽度=上模腔宽度-0.4~0.6 高度=上模腔高度-0.4~0.6 冲头倒角R≈卷芯厚度/2
6)、卷针宽度: 卷针宽度≈卷芯宽度-卷芯厚度-0~3
二、常用体系
体系5: 正极:ZX:JH:RC10214: SP: NMP=75: 25: 1.6: 1.6: 50 负极:918: FSN-1:SP: CMC: SBR: H2O=50: 50: 1.0: 1.5: 2.6: 82 设计压实比:正极4.0±0.05,负极1.6±0.05 电解液:L 混料容量发挥:145~146mAh/g(以1500mAh电芯容量为基准) 面密度比:2.18 体系特点:设计容量较高,循环较好
软包锂离子电池制作工艺流程详解

软包锂离子电池制作工艺流程详解2018-04-27电动知家1、软包电芯所谓的软包电芯,其实就是使用了铝塑包装膜作为包装材料的电芯。
相对来说,锂离子电池的包装分为两大类,一类是软包电芯,一类是金属外壳电芯。
金属外壳电芯又包括了钢壳与铝壳等等,近年来由于特殊需要有的电芯采用塑料外壳的,也可以划为此类。
二者的差别出了外壳材料不同,决定了其封装方式也不同。
软包电芯采用的是热封装,而金属外壳电芯一般采用焊接(激光焊)。
软包电芯可以采用热封装的原因是其使用了铝塑包装膜这种材料。
2、铝塑包装膜铝塑包装膜(简称铝塑膜)的构成见图,其截面上来看有三层构成:尼龙层、A l层与P P层。
三层各有各的作用,首先尼龙层是保证了铝塑膜的外形,保证在制造成锂离子电池之前,膜不会发生变形。
A l层就是一层金属A l构成,其作用是防止水的渗入。
锂离子电池很怕水,一般要求极片含水量都在P P M级,所以包装膜一定能够挡住水气的渗入。
尼龙不防水,无法起到保护作用。
而金属A l在室温下会与空气中的氧反应生成一层致密的氧化膜,导致水气无法渗入,保护了电芯的内部。
A l层在铝塑膜成型的时候还提供了冲坑的塑性,这个详见第3点。
P P是聚丙烯的缩写,这种材料的特性是在一百多摄氏度的温度下会发生熔化,并且具有黏性。
所以电池的热封装主要靠的就是P P层在封头加热的作用下熔化黏合在一起,然后封头撤去,降温就固化黏结了。
铝塑膜看上去很简单,实际做起来,如何把三层材料均匀地、牢固地结合在一起也不是那么容易的事。
很遗憾的是,现在质量好的铝塑膜基本上都是日本进口的,国产的不是没有,但质量还有待改进。
3、铝塑膜成型工序软包电芯可以根据客户的需求设计成不同的尺寸,当外形尺寸设计好后,就需要开具相应的模具,使铝塑膜成型。
成型工序也叫作冲坑(其实个人觉得应该是“铳坑”,但大家都这么写就随俗吧),顾名思义,就是用成型模具在加热的情况下,在铝塑膜上冲出一个能够装卷芯的坑,具体的见下图铝塑膜冲好并裁剪成型后,一般称为P o c k e t袋,见下图所示。
191115 软包锂离子电芯设计指南-2
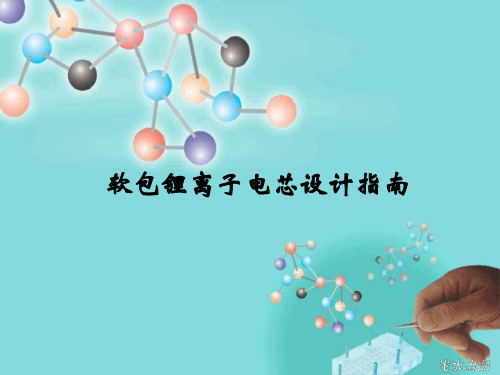
电芯容量
输入正极面密度 负极面密度
2.3 软包电池的设计原则
1)模壳:上模腔尺寸:宽度=电池宽度最大值-(1.0~5.5) 高度=电池高度最大值-(2.2~6.2)
冲头尺寸:宽度=上模腔宽度-(0.4~1) 高度=上模腔高度-(0.4~0.8)
2)宽度:卷芯宽度=上模腔宽度-(0.5~1.40) 隔膜宽度=上膜壳高度-(0.5~1.50) 负极宽度=隔膜宽度- (1.0~2.20) 正极宽度=负极宽度-( 1.0~2.20 )
负极的面密度
1.05 =
* C (C为常数)
正极的面密度
正极的面密度
=
负极的面密度
C 1.05
= K (K为常数)
即方型和软包电池中常说的面密度比。
1.2 正负极效率的匹配
电池的电压=正极电势-负极电势。 充电过程:正极电势会升高,负极电势会降低,电池的电压逐渐上升; 放电过程:正极的电势降低,负极的电势升高,电池的电压逐渐降低。
定制电池的厚度、形状,并可做出弧 形等特殊形状;
3.2 软圆柱的最大区别是没有金属外壳,采用铝塑膜外包装, 同时隔离膜采用涂胶工艺,电解液改用现场聚合or凝胶性电解液。
其结构主要分为Nylon、Al 和 PP,三个部分:示意图如右图: Nylon :可以有效阻止空气尤其是氧的渗透,维持电芯内部的环境,同
三、软包锂离子电池的组成
3.1 软包锂离子电池的特点
①高能量密度:能量密度高达 580~630Wh/L;
②安全性能好:采用铝塑包装,内部质 量隐患可立即通过外包装变形而显示 出来,一旦发生安全隐患,不会爆炸 ,只会鼓胀;
③更轻便:比同等规格的钢壳液锂轻40 %,比铝壳液锂轻20%;
④更薄:厚度最小可做到2.0~2.5mm ⑤形状可定制:可根据客户的要求灵活
商用cr2032锂离子电池制作流程

商用cr2032锂离子电池制作流程1.铜箔选切:首先,需要将铜箔按照规定的大小进行切割。
Copper foil cutting: First, the copper foil needs to be cut according to the specified size.2.极片制备:将阳极和阴极材料分别准备好,确保其质量达标。
Electrode preparation: Prepare the anode and cathode materials separately to ensure their quality meets the standard.3.钢丝网涂布:将钢丝网浸入电解液中,然后涂布在阳极和阴极上。
Wire mesh coating: Dip the wire mesh into the electrolyte and then coat it onto the anode and cathode.4.干燥处理:对涂布好的电极进行干燥处理,确保其表面干净无尘。
Drying treatment: Dry the coated electrodes to ensure their surface is clean and dust-free.5.钢丝网粘合:将涂布好的钢丝网粘合到阳极和阴极上,以提高电池的导电性能。
Wire mesh bonding: Bond the coated wire mesh onto the anode and cathode to improve the battery's conductivity.6.卷绕铝箔:通过特定的设备将阳极和阴极卷绕在铝箔上。
Aluminum foil winding: Wind the anode and cathode onto aluminum foil using specific equipment.7.装配电芯:将卷绕好的阳极和阴极装配成电芯,并封装在保护壳中。
锂离子动力电池设计步骤及要求

锂离子动力电池设计介绍摘要:本文简要介绍了锂离子动力电池设计的基本原则、设计要求、评价锂离子动力电池性能的主要指标和锂离子动力电池设计的基本步骤,并结合 8Ah锰酸锂动力电池的设计实例,详细介绍了锂离子动力电池设计过程中各主要参数的确定方法、计算过程以及设计过程中相关细节的注意事项,结合本公司实际生产能力和生产设备的实际工况,确定了正负极极片分段的设计思路,将正负极极片分别分为四段,卷成两个电芯,采用内部并联的方式与电池的极柱链接,成功的解决了生产中极片过长极片不易加工和卷绕不易对齐的难题,为动力电池的设计提供重要的参考依据。
1 锂离子动力电池的设计基础1.1 动力电池设计的基本原则动力电池设计,就是根据用电设备的要求,为设备提供工作电源或动力电源。
因此,动力电池设计首先必须根据用电设备需要及电池的特性,确定电池的电极、电解液、隔膜、外壳以及其他部件的参数,对工艺参数进行优化,并将它们组成有一定规格和指标(如电压、容量、体积和重量等)的电池组。
动力电池设计是否合理,关系到电池的使用性能,必须尽可能使其达到设计最优化。
1.2 动力电池的设计要求动力电池设计时,必须了解用电设备具对电池性能指标及电池使用条件,一般应考虑以下几个方面:1电池工作电压;2电池工作电流,即正常放电电流和峰值电流;3电池工作时间,包括连续放电时间、使用期限或循环寿命;4电池工作环境,包括电池工作环境及环境温度;5电池最大允许体积;锂离子动力电池由于其具有优良的性能,使用范围越来越广,有时要应用于一些特殊场合,因而还有一些特殊要求,如耐冲击、振动、耐高低温、低气压等。
在考虑上述基本要求时,同时还应考虑材料来源、电池特性的决定因素、电池性能、电池制造工艺、技术经济分析和环境温度。
1.3 评价动力电池性能的主要指标动力电池性能一般通过以下几个方面来评价:1容量。
电池容量是指在一定放电条件下,可以从电池获得的电量,即电流对时间的积分,一般用Ah表示,它直接影响电池的最大工作电流和工作时间。
软包锂离子电池生产工艺的流程设计
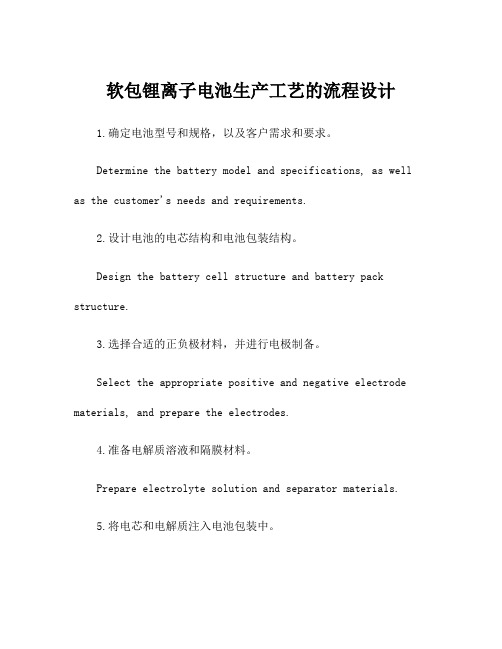
软包锂离子电池生产工艺的流程设计1.确定电池型号和规格,以及客户需求和要求。
Determine the battery model and specifications, as well as the customer's needs and requirements.2.设计电池的电芯结构和电池包装结构。
Design the battery cell structure and battery pack structure.3.选择合适的正负极材料,并进行电极制备。
Select the appropriate positive and negative electrode materials, and prepare the electrodes.4.准备电解质溶液和隔膜材料。
Prepare electrolyte solution and separator materials.5.将电芯和电解质注入电池包装中。
Inject the battery cell with electrolyte into the battery pack.6.进行电池封装,确保密封性能。
Perform battery sealing to ensure sealing performance.7.进行电池充放电性能测试。
Conduct battery charge and discharge performance tests.8.进行电池循环寿命和安全性能测试。
Conduct battery cycle life and safety performance tests.9.进行电池的外观检验和电性能测试。
Conduct battery appearance inspection and electrical performance tests.10.进行电池的包装和标识。
Perform battery packaging and labeling.11.对成品电池进行质量检验和性能测试。
锂离子软包电池制备工艺

锂离子软包电池制备工艺一、组装电芯1、放置收缩膜:将锂离子软包电池电芯安装在收缩膜工位,放置收缩膜,放置收缩膜时应当注意保持膜的横向和纵向走向一致;2、安装外封:在电芯的上面及横向安装外膜,外膜贴合航空插头,将航空插头接口提起,使外膜有足够的松紧度;3、绕线:将外膜绕入电芯下部,将电芯下部外膜绕入电芯中,绕线的时候要注意绕线密度,不能过大,也不能过小;4、外膜绑定:将外膜上海和下海的表面的挡水线固定,外膜两端绑定,把这个步骤做好;5、连接插头:将外膜的上海和下海两侧的插头相连接,把外膜和插头连接到一起;6、热焊接螺母:将外膜两端的螺母装在航空插头上,把螺母焊接在航空插头上,焊接的时候要注意热焊的温度,热焊时间不能过长,以免影响电芯的使用寿命;7、封装点胶:在电池外壳的上部和横向用点胶机完成封装,点胶的时候注意用量,不能过大,也不能过小;8、收缩膜:将收缩膜固定在电池外膜的表面,把它们热收缩,这样就完成了锂离子软包电池组装的工艺。
二、电池测试1. 尺寸测试:测试锂离子软包电池尺寸的标准,以确保电池的外形尺寸达到客户要求;2. 容量测试:将锂离子软包电池放入容量测试仪中,按照规定配置参数,测试电池的容量是否达到要求;3. 阻抗测试:将锂离子软包电池放入阻抗测试仪中,测试电池的内部阻抗是否符合规定;4. 动态测试:放入动态测试仪中,测试电池的偏离电压、放电及充电过程中的参数是否符合规定。
三、充电放电1、偏离电压:将锂离子软包电池放入充电器中,将充电器设置好偏离电压,把偏离电压调到合适的位置;2、充电:将锂离子软包电池放入充电器中,按照规定的参数进行充电;3、放电:将锂离子软包电池放入放电仪中,按照规定的参数进行放电;4、放电完成:把锂离子软包电池从放电仪中取出,把电池从充电器中取出,完成充电放电的流程。
锂离子电芯中试生产线设计流程
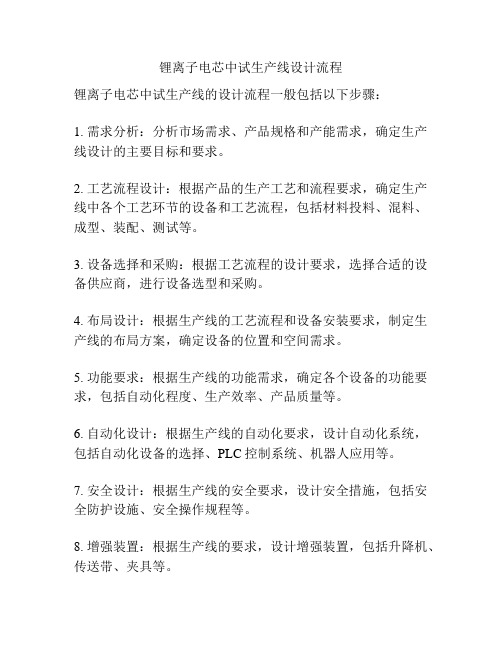
锂离子电芯中试生产线设计流程锂离子电芯中试生产线的设计流程一般包括以下步骤:1. 需求分析:分析市场需求、产品规格和产能需求,确定生产线设计的主要目标和要求。
2. 工艺流程设计:根据产品的生产工艺和流程要求,确定生产线中各个工艺环节的设备和工艺流程,包括材料投料、混料、成型、装配、测试等。
3. 设备选择和采购:根据工艺流程的设计要求,选择合适的设备供应商,进行设备选型和采购。
4. 布局设计:根据生产线的工艺流程和设备安装要求,制定生产线的布局方案,确定设备的位置和空间需求。
5. 功能要求:根据生产线的功能需求,确定各个设备的功能要求,包括自动化程度、生产效率、产品质量等。
6. 自动化设计:根据生产线的自动化要求,设计自动化系统,包括自动化设备的选择、PLC控制系统、机器人应用等。
7. 安全设计:根据生产线的安全要求,设计安全措施,包括安全防护设施、安全操作规程等。
8. 增强装置:根据生产线的要求,设计增强装置,包括升降机、传送带、夹具等。
9. 能源管理:根据生产线的能源消耗情况,设计节能措施,包括能源回收、设备优化等。
10. 环境保护:根据生产线的环境要求,设计环境保护措施,包括有害物质排放处理、废水处理、废气处理等。
11. 软件系统设计:根据生产线的信息化需求,设计软件系统,包括生产调度系统、数据采集和分析系统等。
12. 设备安装和调试:按照设计方案,安装设备,并进行设备调试和调整。
13. 运行与维护:生产线正式投入使用后,进行运行和维护,包括设备的日常检修、保养和故障排除。
14. 过程优化:根据生产线的运行情况和产品质量要求,进行不断优化,提高生产效率和产品质量。
15. 安全评估和改进:对生产线的安全性进行评估和改进,确保工作环境的安全和操作人员的安全。
以上是锂离子电芯中试生产线设计流程的一般步骤,具体设计过程中还需要根据实际情况进行调整和完善。
锂离子电池设计流程

电池设计流程1、根据客户对安全性及容量的要求,选择相应的体系;客户对安全性要求较高时,可选择铁锂或锰酸锂体系,对容量要求较高时,可选择钴酸锂及三元体系。
2、根据电池的厚度选择制作单芯或多芯电池,并选择内部或外部连接;较厚的电池在制作中不方便,应选择多芯以减短极片的长度,电池太厚内部连接后不容易L型封口,因此要选择外部连接;3、查看是否有此型号电池,如没有,打印一份与此型号电池相似的工艺(查找电池的宽度及厚度相似的型号,并查看此型号电池的卷芯宽度是否合适):1)如果打印工艺与需设计电池的厚度及宽度相同,可以通过调整面密度计算容量是否能够满足,如能满足,可以直接试卷绕;2)如果卷芯宽度窄于电池宽度0.8~2mm(小型号电池可以是0.8~1mm,大型号电池必须在1mm 以上),此型号电池的厚度与需设计电池的厚度相近,则可以不必修改卷针的尺寸;3)如果卷芯宽度与电池宽度相差不足0.8mm(小型号电池),或者卷芯的宽度比电池宽度小1mm(大型号电池),电池的厚度与打印的工艺厚度相差较大时,则要更改卷针的尺寸。
4、根据客户要求查找合适的模具:1)看是否有此型号模具,如果没有,是否可以选择其它的型号代替(选择模具宽度与卷芯高度相同的模具,封侧边;如没有,可选择宽度与卷芯宽度相同的模具,封底边);2)模具的宽度比电池的宽度窄0.5~1mm左右,模具的高度根据电池的大小有所不同,比电池的高度小4~7mm;5、根据模具的尺寸修改隔膜及极片宽度:1)单芯电池隔膜宽度比模具窝的高度小1mm左右,多芯电池隔膜宽度比模具窝小2~3mm;2)负极宽度比隔膜宽度小2mm;3)为了方便卷绕,正极的宽度根据电池的大小,一般比负极窄2~4mm;6、修改极片的长度:1)电池在充放电时厚度会增加,卷绕圈数越多的电池,厚度增加也会越大,因此电池的厚度比卷芯的厚度厚0.6~1.5 mm;2)先计算出半圈的厚度,为正极的压片厚度加负极的压片厚度加两层隔膜的厚度;3)查看卷芯厚度与宽度,如厚度比需设计电池的厚度厚时,则要减短极片。
电芯制作过程
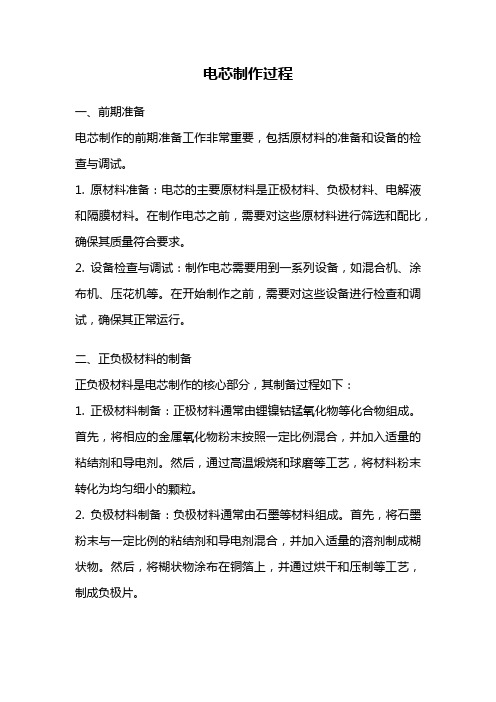
电芯制作过程一、前期准备电芯制作的前期准备工作非常重要,包括原材料的准备和设备的检查与调试。
1. 原材料准备:电芯的主要原材料是正极材料、负极材料、电解液和隔膜材料。
在制作电芯之前,需要对这些原材料进行筛选和配比,确保其质量符合要求。
2. 设备检查与调试:制作电芯需要用到一系列设备,如混合机、涂布机、压花机等。
在开始制作之前,需要对这些设备进行检查和调试,确保其正常运行。
二、正负极材料的制备正负极材料是电芯制作的核心部分,其制备过程如下:1. 正极材料制备:正极材料通常由锂镍钴锰氧化物等化合物组成。
首先,将相应的金属氧化物粉末按照一定比例混合,并加入适量的粘结剂和导电剂。
然后,通过高温煅烧和球磨等工艺,将材料粉末转化为均匀细小的颗粒。
2. 负极材料制备:负极材料通常由石墨等材料组成。
首先,将石墨粉末与一定比例的粘结剂和导电剂混合,并加入适量的溶剂制成糊状物。
然后,将糊状物涂布在铜箔上,并通过烘干和压制等工艺,制成负极片。
三、电芯装配电芯装配是将正负极材料、电解液和隔膜材料按照一定的顺序组装在一起,形成电芯的过程。
1. 电解液注入:首先,在一个密封的容器中,将电解液注入其中。
电解液通常由有机溶剂和盐类组成,具有良好的离子导电性能。
2. 正负极片叠放:将正负极片按照一定的顺序叠放在一起,中间用隔膜材料隔开。
隔膜材料通常由聚烯烃等材料制成,具有良好的电离子透过性和机械强度。
3. 卷绕:将叠放好的正负极片和隔膜材料进行卷绕,形成电芯的基本结构。
卷绕时需要注意绝缘和紧密度的要求,以确保电芯的安全和性能。
4. 异型成型:将卷绕好的电芯进行异型成型,使其具有规定的形状和尺寸。
异型成型通常通过热压和模具等工艺完成。
四、电芯封装封装是保护电芯的重要环节,主要包括壳体封装和密封工艺。
1. 壳体封装:将电芯放入金属壳体中,并密封封口。
壳体通常由铝合金或钢材制成,具有良好的机械强度和热传导性能。
2. 密封工艺:通过焊接、压合等工艺,将壳体与电芯的正负极引线连接起来,并确保连接处的密封性。