第二章 第六节 切削条件合理选择
切削条件的合理选择

3.改善工件材料切削加工性的途径
通常采用以下两种方法: (1) 调整材料的化学成分 在不影响工件的使用性能的前提下,在钢中适当
添加一些化学元素,如S、Pb等,能使钢的切削加工性得到改善,可获得易切钢, 易切钢的良好切削加工性主要表现在:切削力小、容易断屑,且刀具耐用度高, 加工表面质量好。另外在铸铁中适量增加石墨成分,也能改善其切削加工性。这 些方法常用在大批大量生产中。
二、 影响工件材料切削加工性的因素及改善切 削加工性的途径
1.工件材料物理力学性能对切削加工性的影响
工件材料的切削加工性能主要受其本身的物理力学性能的影响,材料的物理力学性能主要是指材料的强度、硬度、 塑性、韧性和热导率等。一般说来,工件材料的力学性能越好,其切削加工的难度就越大。可以根据它们的数值大 小来划分加工性等级,如表 4-2 所示。
因此,在实际生产过程中,常采用适当的热处理工艺,来改变 材料的金相组织和物理机械性能,从而改善金属材料的切削加工 性。
低碳钢由于塑性过高,通过冷拔或正火处理,可以适当降低其塑性,提高 硬度,改善其切削加工性。 高碳钢和工具钢的硬度偏高,且有较多的网状和片状渗碳体组织,较难切 削。通过球化退火,降低其硬度,并能得到球状渗碳体组织,有利于切削 加工。 马氏体不锈钢通常要通过调质处理到HRC28左右,硬度过低时,塑性较大, 不易得到较小的表面粗糙度值,硬度较高时,则切削时,会使刀具磨损增 大。
热轧状态的中碳钢,组织不均匀,有时表面还有硬皮,也不容易切 削。通过正火处理可以使其组织和硬度均匀,而改善了切削加工性。 有时中碳钢也可退火后加工。 铸铁件一般在切削前都要安排退火处理,以降低表层硬度,消除内 应力,改善其切削加工性。
(4) 材料的导热系数 在一般情况下,导热系数高的材料,切削热越容易
机制技术(3-2)合理切削条件选择

三、合理切削条件选择
㈠、工件材料的切削加工性 1、切削加工性的概念和衡量指标
根据相对加工性Kr的大小,将不同材料的切削加 工性分为8级(1~8)。
三、合理切削条件选择
三、合理切削条件选择
Kr仅反映不同材料对刀具使用寿命的影响程 度,并未反映表面粗糙度和断屑问题,仅对选择 切削速度有指导意义。若以某材料的Kr 乘以45钢 的切削速度即得该材料的许用切削速度。
⑶结构钢
碳素结构钢切削加工性取决于含碳量。 低碳钢硬度低,塑韧性高,变形大,断屑难,粘屑,加 工表面粗糙,加工性较差; 高碳钢硬度高,塑性低,切削力大,温度高,刀具耐用 度低,加工性差; 中碳钢性能适中,加工性良好。 合金结构钢强度硬度提高,切削加工性变差。
⑷难加工材料
高强度硬度,高塑性韧性或高脆性,耐高温,导热性差。
切削力大,温度高,刀具磨损快,断屑难,加工性差。
三、合理切削条件选择
㈠、工件材料的切削加工性 3、材料化学成分和金相组织的影响
三、合理切削条件选择
㈠、工件材料的切削加工性 4、改善切削加工性的途径
⑴、通过不同的热处理方法
对高碳钢:球化退火处理;
对低碳钢:冷拔、正火;
对铸铁:退火。
⑵、调整材料的化学成分
量ap,其次在工艺条件允许下选择较大的进给量f ,最后
根据合理的刀具使用寿命,用计算法或查表法确定切削速 度v 。这样使v、f 、ap 的乘积最大,以获得最大的生产率 精加工时则主要按表面粗糙度和加工精度要求确定切削用量。
三、合理切削条件选择
㈣、切削用量的选择
2.切削用量制订的步骤(以车削为例)
(1)背吃刀量ap的选择 粗加工时, ap由加工余量和工艺系统的刚度决定,尽可
切削用量的选择原则

切削用量的选择原则
第一段:切削用量是不可缺少的切削参数,它需要用户根据切削要求,从许多切削可能量中进行选择,以使工件表面满足要求,并节约切削能耗。
本文旨在为熟悉切削用量的选择原则提供指导,以便于切削过程的有效控制。
第二段:切削用量的选择要根据工件材料、加工工艺、刀具结构和辅助设备等多种因素进行综合考虑。
首先,要考虑工件材料的加工性能。
材料的脆硬度、塑性弹性模量、耐磨损性、密度等参数,影响切削用量的选择,同样的材料,切削量的大小可能不同。
第三段:其次,要考虑加工工艺的不同,切削参数的选择要考虑加工的精度要求,especiallY对于高精度加工,比如微机雕刻,它要求切削误差极其小,切削用量需要减小,也就是说要使末端刀具和工件表面接触面积增加,以提高切削精度,但切向力也需要相应减小.第四段:接下来,要考虑刀具结构参数,尤其是刃口尺寸、形状和角度,它们直接影响切削刃的切向力、摩擦力和压痕深度等特性,从而影响切削用量的选择.比如对于高速钢加工,可以选择尖角度较钝的刃口,并采用更大切口尺寸,以降低切削刃的切入力,消除切削热.
第五段:最后,要考虑切削机床的驱动、辅助系统及其他因素,这些因素都会影响切削用量的选择.比如,利用液压机械手、磁浮支撑装置或向心力喷射装置等设备,可以减少刀具受到的横向切向力,从而提高切削精度,同时增大切削用量.
第六段:总之,切削用量的选择要按照工件材料、加工工艺、刀具结构和辅助设备等多种因素进行综合考虑,以确保加工工件的质量,确保切削过程的有效控制,以节约切削能耗.
第七段:由于切削用量对切削过程的控制有着至关重要的影响,因此需要用户熟悉切削用量的选择原则,才能做出正确的决定,以确保满足加工要求,同时节约切削能耗,提高切削效率。
切削条件的合理选择
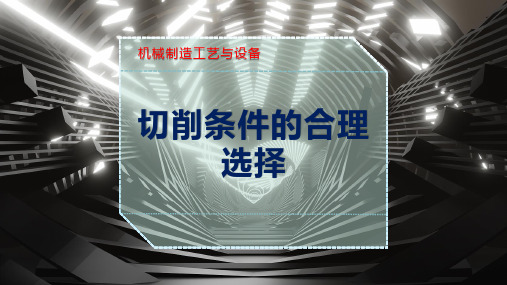
机械制造工艺与设备
谢谢观看!
2.改善工件材料切削加工性的基本方法 1)选择合理的热处理工序 2)选切削加工性好的工件材料 3)调整化学成分 4)其他方法
1.2 刀具几何参数
1.前角的选择 1)前角的功用
增大前角,可使切削刃锋利,减少切削变形和摩擦,从而减少切削力, 提高刀具寿命,还可以抑制积屑瘤的产生,改善加工质量。但前角过大, 会削弱切削刃的强度和散热情况,甚至造成崩刃。
2.切削用量的确定
切削速度的合理选择
粗加工时,切削速度vc选 的较小;精加工时,切削 速度vc选的较大。工件材 料强度、硬度较高时,应 选较小的切削速度vc ;在 断续切削和加工大件、细 长件、薄壁件时,应选用 较低的切削速度vc 。
进给量的合理选择
粗加工时,进给量f的 选择主要受切削力的限 制。半精加工和精加工 时,进给量f对工件的 已加工表面粗糙度的影 响较大,因此,其一般
2)前角的选择原则
1
2
3
当工件材料的强度、硬 度大时,为增加切削刃 刃口强度,应选择较小 的前角;当工件材料的 塑性大时,为减小变形, 应选择较大的前角;当 工件材料的脆性大时, 工件变形小,切削力集 中,应选择较小的前角。
当刀具材料的强度、 韧性较高时,可选 择较大的前角。
粗加工时,为增加切 削刃的强度,宜选择 较小的前角;精加工 时,为增加切削刃的 锋利性,宜选择较大 的前角。
2.后角的选择 1)后角的功用
增大后角能减小刀具后刀面与工件切削表面之间的摩擦,还可 使切削刃刃口锋利。但后角过大,使得楔角减小,切削刃刃口强度 减小,散热体积减小。 2)后角的选择原则
(1)当需要提高刀具刃口强度时,应适当减小后角。 (2)粗加工、强力切削及承受冲击载荷的刀具,为增加刀具强 度,后角应取小些;精加工时,因切削深度及进给量较小,增大后 角可提高刀具寿命和已加工表面的质量。
第二章第六节切削用量的选择方案

• 精加工多采用较高的切削速度,即可提高加工效率, 又要照顾到刀具使用寿命。
二、三要素的选定
1. ap的选定 • 一般根据加工性质与加工余量确定ap。切削加工一
般分为粗加工、半精加工和精加工。 (1)粗加工:考虑机床功率,系统刚度尽可能大
第六节 切削用量的选择
一、切削用量的选择原则
每次切削加工都必须选择切削速度、进给量和背吃刀量,这是 肯定的。
切削用量这三个要素与 生产效率、加工质量和加工成本都有非 常密切的关系。
我们在追求最高的生产效率、最好的加工质量和最低的加工成 本时如何选择切削用量三个要素呢?怎样选择才算合理呢? 下面让我们来分析一下切削用量三要素与生产效率、加工质 量和加工成本的关系。
• (2)工件材料强度、硬度高时,应选较低的vc。 • (3)切削合金钢比切削中碳钢切削速度降低20%~30%;切削
调质状态的钢比切削正火、退火状态钢要降低切削速度 20%~30%;切削有色金属比切削中碳钢的切削速度可提高 100%~300%。
• (4)刀具材料的切削性能愈好,切削速度也选得愈高,如硬质 合金钢的切削速度比高速钢刀具可高几倍,涂层刀具的切削 速度比未涂层刀具要高,陶瓷、金刚石和CBN刀具可采用更 高的切削速度。
f ↑ → 残留面积↑ Ra↑
v c → 通过积屑瘤来影响
2.切削用量与生产率 (1) 生产率
1 w
tw
tw
tm
tct
tm T
tot
tm ( ----- 机动时间)基本工艺时间 tct ----- (安装、调整、换刀)辅助工艺时间 tot ----- 其他辅助时间
切削 用量的合理选择
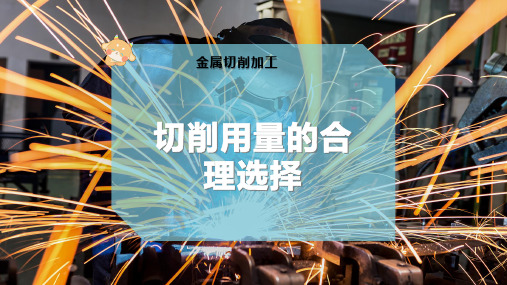
2)根据机床说明书,取机床实际进给量 =0.51mm/r。 3)检验机床进给机构允许的进给量。参考CA6140车床说 明书,查出机床进给机构允许的最大进给抗力为:FMfmax= 3528N。 计算切削时进给力为:
统、工件刚度以及精加工时表面粗糙度要求,确定进给量。
3)根据刀具寿命,确定切削速度。 4)所选定的切削用量应该是机床功率所允许的。
1.2切削用量的合理选择方法
1.背吃刀量的合理选择
背吃刀量一般是根据加工余量来确定。 粗加工(表面粗糙度Ra=50~12.5μm)时,尽可能一 次走刀即切除全部余量,在中等功率的机床上加工,取 ap=8~10mm;加工余量太大或余量不均匀、工艺系统刚性 不足或者断续切削时,可分几次走刀。 半精加工(Ra=6.3~3.2μm)时,取ap=0.5~2mm。 精加工(Ra=1.6~0.8μm)时,取ap=0.1~0.4mm。
1.5切削用量的优化概念
切削用量的优化是指在一定的预定目标及约束条件下, 选择最佳的切削用量。
在实际生产中,由于各种条件(加工零件、机床、刀 具、夹具等)都在变化,很难确定出一组最合理的切削用 量数值。
利用切削用量优化的方法,在确定加工条件下,综合 考虑各个因素,通过计算机辅助设计,能找出满足高效、 低成本、高利润和达到表面质量要求的一组最佳的切削用 量参数。实际切削用量的优化过程就是建立优化目标的数 学模型,用计算机求极值。主要目标函数有三个。
床功率是否允许。 在实际生产中,切削用量的合理选择,既可参照有关 手册的推荐数据,也可凭经验根据选择原则确定。
1.3车削用量的合理选择例题
切削用量的合理选择

切削用量的合理选择(2008-07-13 15:37:22)标签:刀具寿命用量生产率切削性能杂谈分类:数控刀具技术切削用量不仅是在机床调整前必须确定的重要参数,而且其数值合理与否对加工质量、加工效率、生产成本等有着非常重要的影响。
所谓“合理的”切削用量是指充分利用刀具切削性能和机床动力性能(功率、扭矩),在保证质量的前提下,获得高的生产率和低的加工成本的切削用量。
一制订切削用量时考虑的因素切削加工生产率在切削加工中,金属切除率与切削用量三要素ap、f、v均保持线性关系,即其中任一参数增大一倍,都可使生产率提高一倍。
然而由于刀具寿命的制约,当任一参数增大时,其它二参数必须减小。
因此,在制订切削用量时,三要素获得最佳组合,此时的高生产率才是合理的。
刀具寿命切削用量三要素对刀具寿命影响的大小,按顺序为v、f、ap。
因此,从保证合理的刀具寿命出发,在确定切削用量时,首先应采用尽可能大的背吃刀量;然后再选用大的进给量;最后求出切削速度。
加工表面粗糙度精加工时,增大进给量将增大加工表面粗糙度值。
因此,它是精加工时抑制生产率提高的主要因素。
二刀具寿命的选择原则切削用量与刀具寿命有密切关系。
在制定切削用量时,应首先选择合理的刀具寿命,而合理的刀具寿命则应根据优化的目标而定。
一般分最高生产率刀具寿命和最低成本刀具寿命两种,前者根据单件工时最少的目标确定,后者根据工序成本最低的目标确定。
选择刀具寿命时可考虑如下几点:根据刀具复杂程度、制造和磨刀成本来选择。
复杂和精度高的刀具寿命应选得比单刃刀具高些。
对于机夹可转位刀具,由于换刀时间短,为了充分发挥其切削性能,提高生产效率,刀具寿命可选得低些,一般取15-30min。
对于装刀、换刀和调刀比较复杂的多刀机床、组合机床与自动化加工刀具,刀具寿命应选得高些,尤应保证刀具可靠性。
车间内某一工序的生产率限制了整个车间的生产率的提高时,该工序的刀具寿命要选得低些;当某工序单位时间内所分担到的全厂开支M较大时,刀具寿命也应选得低些。
金属工艺学 下册(第六版) 邓文英 宋力宏 课后题答案
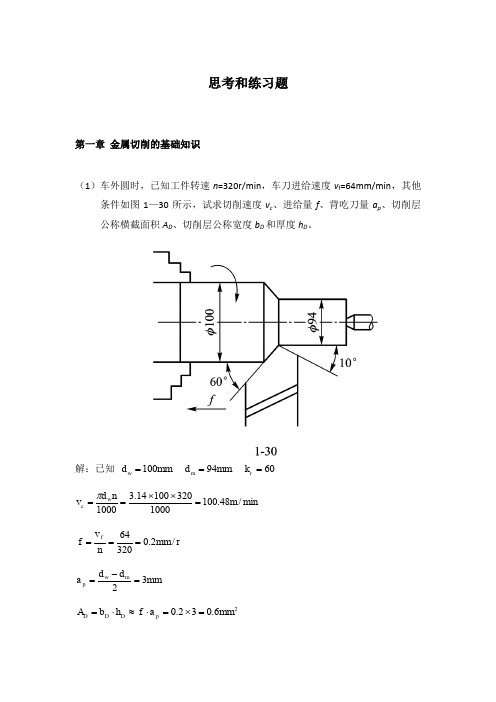
解: h = dw dm 86 80 3mm
2
2
tm
d w
(lw l1 l2 ) h vc f ap
PE=4.5kW,试问电动机功率是否足够? 解:查表 1-2 kc=1962Mpa Fc Kc ap f 1962 4 0.3 2354.4N Pm 103 Fc vc 103 2354.4 100 60 3.924kw P PE 4.5 0.75 3.375kw Pm 答经上述计算电机功率是不足的。
43.49r/min
(2)根据图 2-30 所示的传动系统图,试列出其传动链,并求:1、主轴Ⅴ有几 级转速?2、主轴Ⅴ的最高转速和最低转速各为多少?
解:传动链:电动机(1440r/min)-
34
48
41
-Ⅰ-
-Ⅱ-
41
22
-Ⅲ-
-
60
28
(9)假设题(8)的其他条件不变,仅工件材料换成灰铸铁 HT200(退火,170HBS) 或铝合金 LY12(淬火及时效,107HBS),试计算这种情况下的切削力 Fc 和 切削功率 Pm。它们与加工 45 刚时相比有何不同?为什么?
解:查表 1-2 灰铸铁 HT200(退火,170HBS)kc1=1118Mpa;铝合金 LY12(淬火及 时效,107HBS)kc2=834Mpa
(3)在一般情况下,K 类硬质合金适于加工铸铁件,P 类硬质合金适于加工钢件。 但在粗加工铸钢件毛坯时,却要选用牌号为 K20 的硬质合金,为什么?
切削参数的选择
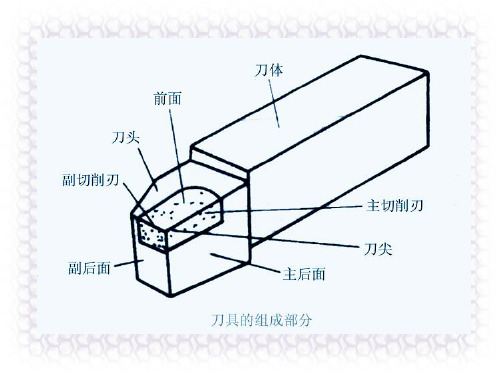
刃。
课堂问题?
2、正交平面参考系各参考面的概念? 基面pr、切削平面ps、正交平面po
❖正交平面参考系时各参考面 : ❖ 基面pr——过切削刃选定点平行或垂直刀
具安装面(或轴线)的平面。 ❖ 切削平面ps——过切削刃选定点与切削
刃相切并垂直于基面的平面。 ❖ 正交平面po——过切削刃选定点同时垂
直于切削平面和基面的平面。
课堂问题?
3、车刀各刀具角度的概念? 前副角偏γ角o、κrˊ后、角刃α倾o、角主λs偏角κr 、
❖ 前角γo——在主切削刃选定点的正交平面 po内,前刀面与基面之间的夹角。
❖ 后角αo——在正交平面po内,主后刀面与 切削平面之间的夹角。
❖ 主偏角κr——主切削刃在基面上的投影与进 给方向的夹角。
❖ 正交平面参考系时各 参考面 :(右图)
❖ 基面pr——过切削刃选 定点平行或垂直刀具安 装面(或轴线)的平面。
❖ 切削平面ps——过切削 刃选定点与切削刃相切 并垂直于基面的平面。
❖ 正交平面po——过切削 刃选定点同时垂直于切 削平面和基面的平面。
正交平面参考系
❖ 对于法平面参考系:
❖ 则由pr、ps、pn三平面组成,其中:
❖ 刀具前角的合理选择,主要由刀具材 料和工件材料的种类与性质决定。
❖ ① 刀具材料
❖ 强度和韧性大的刀具材料可以选择大的前角,而脆性 大的刀具甚至取负的前角。
❖ 下图是不同刀具材料韧性的变化
立方氮化硼刀具 陶瓷刀具 硬质合金刀具
高速钢刀具
❖ ② 工件材料
刀具韧性增强,前角取大
❖ 加工钢件等塑性材料时,切屑沿前刀面流出时和前刀
❖ 刀具几何参数的合理选择:是指在保证加工质量 的前提下,选择能提高切削效率,降低生产成本, 获得最高刀具耐用度的刀具几何参数。
机械类-金属切削条件的合理选择
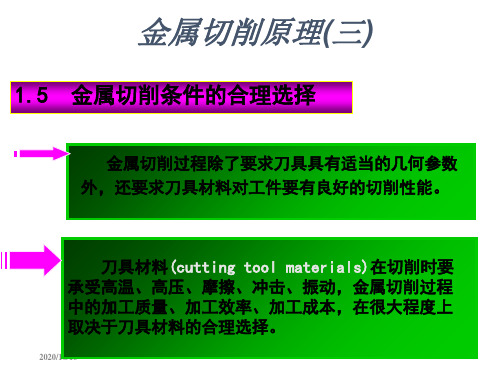
后再热压锻轧制成。适用于制造精密刀具、大尺寸(滚刀、
插齿刀)刀具、复杂成形刀具、拉刀等。
2020/10/16
(3)硬质合金
•(碳硬化质钨合W金C、(c碳ar化bi钛deTsi)C是、由碳高化硬钽度Ta和C、高碳熔化点铌的N金bC属等碳)和化金物属
粘结剂(Co、Mo、Ni等)用粉末冶金工艺制成。
•定硬性质好合,耐金磨刀性具好常,温耐硬热度性为达8890~0~931H0R0A0,°化C学。稳硬定质性合好金,刀热具稳
2020/10/16
(4)刀具材料的切削性能愈好,切削速度也选得愈高。
(5)精加工时,应尽量避开积屑瘤和鳞刺产生的区域。 (6)断续切削及加工大件、细长件和薄壁工件时,应 适当降低切削速度。 (7)在易发生振动的情况下,切削速度应避开自激振 动的临界速度。
2020/10/16
3.粗、精加工选择切削用量的原则
(WC+TiC+TaC+(NbC)+Co) :YW,属M类
2020/10/16
2)常用硬质合金的牌号及其性能
❖K (YG)(钨钴类)类硬质合金:有较好的韧性、磨削性、
导热性,
❖适合加工短切屑的金属或非金属材料,如淬硬钢、铸铁、
铜铝合金、塑料等。
❖其代号有K01、K10、K20、K30、K40等,数字越大,耐磨
允许的切削速度比高速钢刀具高5~10倍 。
•但强度、韧度均较高速钢低,工艺性也不如高速钢。 •端常铣制刀成等各的种刀型柄式(刀的体刀)片上,使焊用接。或机械夹固在车刀、刨刀、
2020/10/16
1)硬质合金的分类
➢钨钴类(WC+Co);YG,属K类 ➢钨钛钴类(WC+TiC+Co);YT,属P类 ➢钨 钛 钽 ( 铌 ) 类 硬 质 合 金
机械制造技术基础 第二章 第六节 刀具磨损和刀具寿命
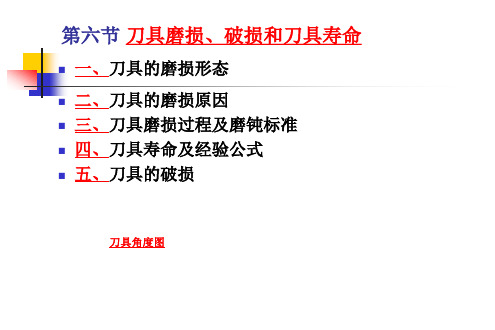
五、刀具破损
刀具破损分为脆性破损和塑性破损。脆性破损又分为早期和后期两种。 早期脆性破损——切削刚开始或短时间切削后即发生破损,前后刀面尚未产生明显的磨损 (一般VB≤0.1mm)。 后期脆性破损——加工一段时间后,刀具材料因疲劳而引起的破损。
1、刀具脆性破损的形态 ⑴ 崩刃 ——在切削刃上产生小的缺口,刀具还能继续切削。陶瓷、立方氮化硼等脆性材 料的刀具常发生这种崩刃。 ⑵ 碎断——切削刃上发生小块碎裂或大块断裂,不能继续正常切削。 刀尖与切削刃处发生小 碎块属于早期碎断,一般还可重磨再用,硬质合金和陶瓷 刀具断续切削时常出现 这种早期碎断;刀尖处发生大块断裂,不可能再重磨使 用,多数是断续切削较长 时间后,没有及时换刀,因刀具材料疲劳而造成断裂。 ⑶ 剥落——在前、后到面上几乎平行于切削刃而剥下一层碎片,经常连切削刃一起剥落。 多是断续切削时的一种早期破损现象。陶瓷铣刀片易出现这种破损;硬质合金刀 具形成积屑瘤时,也会造成这种破损。 ⑷ 裂纹破损——在较长时间断续切削后,由于疲劳而引起裂纹的一种破损。 有因热冲击而引起的通常垂直或倾斜于切削刃的热裂纹;也有因机械冲击而 发生的平行于切削刃或成网状的机械疲劳裂纹。
3、边界磨损 —— N区磨损。 边界磨损严重的宏观原因是: 主切削刃与工件待加工表面接触处,切削刃切削的是上道工序的硬化层或毛坯表面; 另此处存在很高的应力梯度及很高的温度梯度,这将引起很大的剪应力。 副切削刃与已加工表面接触处,由于加工硬化作用,副切削刃与工件接触处的切削厚 度减薄到零,引起这部分刀刃打滑;同时,这部分也存在一定的应力梯度及温度梯度,也 会引起较大的剪应力。
后刀面的磨损带 往往不均匀,可分为:C区、B区、N区,如图。 C区——刀尖部分,(因刀尖部分强度较低,散热条件又差)磨损比较严重,用其最大 值VC表示其磨损程度。
01-教材参考内容——切削用量的合理选择

径;改进刀具几何参数可使刀具耐用度有较大幅度提高。
因此,刀具耐用度是衡量刀具几何参数合理和先进与否的重要标志之一。
前角Y o增大,切削温度降低,耐用度提高;前角Y o太大,刀刃强度低、散热差且易磨损,故耐用度T反而下降。
主偏角k r减小,可增加刀具强度和改善散热条件,故耐用度T或刀具耐用度允许的切削速度o T 增高。
此外,适当减少副偏角k'r和增大刀尖圆弧半径r e都能提高刀具强度,改善散热条件使刀具耐用度T或刀具耐用度允许的切削速度oT提高。
(3)加工材料的影响加工材料的强度、硬度越高,产生的切削温度越高,故刀具磨损越快,刀具耐用度T 越低。
此外,加工材料的延伸率越大或导热系数越小,均能使切削温度升高从而使刀具耐用度T 降低。
(4)刀具材料的影响刀具切削部分材料是影响耐用度的主要因素,改善刀具材料的切削性能,使用新型材料,能促进刀具耐用度成倍提高。
一般情况下,刀具材料的高温硬度越高、越耐磨,耐用度T 也越高。
但在带冲击切削、重型切削和对难加工材料切削时,决定刀具抗破损能力的主要指标是冲击韧性。
普通陶瓷材料的抗弯强度约为硬质合金的1/3,因此,切削时受到轻微冲击也易破损。
为了增强刀具的韧性、提高刀具抗弯强度,目前研制了新型陶瓷,并在刀具几何参数方面选用较小的前角、负刃倾角和倒棱等参数。
2.5切削用量的合理选择所谓"合理,的切削用量是指充分利用刀具切削性能和机床动力性能(功率、扭矩),在保证零件加工质量的前提下,获得高的生产率和低的加工成本的切削用量。
2.51切削用量选择原则根据不同的加工条件和加工要求,又考虑到切削用量各参数对切削过程规律的不同影响,制定切削用量时应从以下几个主要方面考虑。
(1)切削加工生产率在切削加工中,金属切除率与切削用量三要素ap 、f、oc均呈线性关系,即其中任一参数增大一倍,都可使生产率提高一倍。
然而由于刀具耐用度的制约,当任一参数增大时,其他二参数必须减小。
切削条件的选择

在相同的切削条件下,使用同一型号 (最好是同一把)刀具,在同一磨钝标准 (例如VB = 0.3 mm)下,切削两种不同的工 件材料,刀具寿命高的比寿命低的切削加工 性好。
一、工件材料的切削加工性
1.切削加工性的概念和衡量指标
标准二 用切削力和切削温度来衡量
在刀具寿命相同的条件下,切削力大或 者切削温度高,切削加工性差。机床动力不 足常用此指标。
切削速度的选择:可按照刀具使用寿命求出切削速度。并考虑到, 精加工避开积屑瘤产生的速度范围;粗加工应对机床效率进行校 验;断续切削,宜适当降低速度,减少冲击和热应力;加工大型、 细长、薄壁工件,选择较低的切削速度。
3.6 磨削原理
磨削加工是机械加工中常用的一种加工方法,主 要用于精加工,有十分重要的地位。磨削加工可 以使工件达到IT5~IT7级精度和Ra1.25~0.08m 的表面粗糙度,高精度磨削可以获得 Ra<0.01m的表面粗糙度。
磨削的三个阶段 t1:初磨阶段;t2:稳磨阶段;t3:光磨阶段
3.6.3 磨削温度
• 一、基本概念 1、磨粒磨削点温度 磨粒磨削点温度是磨粒切削刃与切屑接触点的温度,是磨 削中温度最高的部位,可达1000~1400℃,也是磨削热的 主要热源。该温度不但影响磨削表面质量,且与磨粒的磨 损和切屑熔化焊接现象有密切关系。 2、砂轮磨削区温度 砂轮磨削区温度是砂轮与工件接触区的平均温度。它影响 工件表面的烧伤、裂纹和加工硬化。一般情况下,没有特 别注明时的“磨削温度”,就是指砂轮磨削区温度,可用 人工热电偶或半人工热电偶法测定。
二、影响工件材料切削加工性的因素
1.工件材料的物理力学性能对切削加工性 的影响 硬度强度越高、切削力越大,切削温度越 高,切削加工性越差。 伸长率越大,塑性越大,加工性越差,韧 性高,切削力和温度高,不易断屑,加工 性差。 热导率越大,由切削带走,工件散出的热 量越多,有利于降温,加工性越好。
- 1、下载文档前请自行甄别文档内容的完整性,平台不提供额外的编辑、内容补充、找答案等附加服务。
- 2、"仅部分预览"的文档,不可在线预览部分如存在完整性等问题,可反馈申请退款(可完整预览的文档不适用该条件!)。
- 3、如文档侵犯您的权益,请联系客服反馈,我们会尽快为您处理(人工客服工作时间:9:00-18:30)。
K r v60 v60
三.材料切削加工性的改善
改善途径
调整化学成分,发展易切钢 进行合适的热处理 改变工艺方法,如低碳钢冷拉降低塑性 改变切削条件,如选择合适的刀具材料,
几何参数,切削用量与切削液等
(1) 高速钢(HHS)
高速钢HHS:W、Mo和Cr含较 高的合金工具钢,许用切削速 度高于一般的合金工具钢。
W、Mo溶于基体,提高红硬性; W、Mo、Cr等形成高硬度的碳 化物,提高硬度和耐磨性。
高速钢HHS的分类
钨系高速钢
工艺性好,通用性好;但硬 W18Cr4V 度不高
钼系高速钢
韧性好、碳化物细小均匀; W6Mo5Cr4V2 但易脱碳,淬火温度范围窄
高钴高速钢
高温硬度高,基体强度高, W2Mo9Cr4VCo8 耐磨性好;但价格昂贵。
高碳高钒高速钢 高温硬度高,韧性好,耐磨 W12Cr4V4Mo 性好;但价格昂贵,难刃磨。
高钒含铝高速钢 耐磨性好,硬度高,可磨性 W6Mo5Cr4V2Al 差
稀土高速钢
晶粒细小,碳化物分布均匀, W14Cr4VMnRe 韧性最好;但价格较贵。
四. 难加工材料
高强度钢、不锈钢、高温合金、钛合金等
1. 材料硬度高(高温硬度高); 2. 加工硬化大; 3. 有高硬度的硬质点; 4. 导热性差,切削温度高; 5. 强度大,特别是高温强度大; 6. 化学活性大; 7. 弹性变形大
§6-2 刀具切削性能
提高刀具切削性能的措施:
•设计合理,制造质量高; •合理选材; •合理的几何参数
金属切削原理 Principle of Metal Cutting
第六章 切削条件合理选择
切削条件对以下因素产生影响
生产率 加工质量 生产成本
切削条件涉及以下几方面
工件材料的切削加工性 刀具的切削性能
刀具切削部分的材料 合理的刀具几何参数
切削液 刀具耐用度和切削用量的合理选择
§6-1 工件材料的切削加工性
(2) 硬质合金
由高硬度高熔点的金属碳化物和金属粘结 剂组成,经过粉末冶金方法制造的。
金属碳化物有:WC、TiC、TaC、NbC等,
金属粘结剂有:Co、Mo、Ni等。
金属碳化物具有高硬度、高熔点、化学稳 定、热稳定等特点,因而硬质合金的耐磨 性和红硬性较好,刀具的耐用度较高。同 类硬质合金粘结剂含量越多刀具的韧性越 好,但硬度越低。
HHS的选择
根据工件材料的性质:一般选择通用型,难 加工材料选高钴、高钒高速钢。
根据工件的形状和刀具的类型:简单刀具可 选择高钒高速钢,复杂刀具可选择钨系、钼 系低钴高速钢(不可选高钒高速钢),钻头 选钼系高速钢。
根据加工方式:断续加工选用韧性较好的钼 系高速钢和稀土高速钢。若选用高钴、高钒 高速钢必须采用适当的热处理,提高其韧性
立方氮化硼 1400~
(CBN)
1500℃
金刚石
550~600℃ 1200℃ 700℃以下
(4) 其他性能
良好的导热性 抗粘附性
高温高压下刀具与工件材料在接触面处抵抗熔 结的能力
工艺性
热处理性能,可加工性,刃磨性能
2. 刀具材料的种类及其选用
高速钢 硬质合金 陶瓷 金刚石 立方氮化硼
可加工性 可加工性的刀具耐用度指标 材料可加工性的改善 难加工材料
一. 材料的切削加工性
定义:一定条件下工件材料切削加 工的难易程度
材料可加工性的衡量:刀具耐用度、 已加工表面的完整性、切屑的控制
通常使用刀具耐用度作为衡量切削 加工性的指标
二. 衡量切削加工性的指标
绝对指标vT:刀具的耐用度为T分钟时,某种 材料加工时允许的切削速度。vT越大,材料的 可加工性越好。
硬质合金的选用
符号 成分
钨钴类 YG WC+Co
牌号
YG8
硬度/红硬性
低/低
强度和韧性
大
导热性
大
抗氧化和粘结性 低
钨钴钛类
通用类
YT
YW
WC、TiC+Co WC、TiC、 TaC(NbC)+Co
YT14 高/高 小
YW3 较高/高 大
小
高
高
工件材料
脆性材料 塑性材料
塑性、脆性材料 均可
刀具磨损
后刀面磨损 前刀面磨损 前、后刀面磨损
一.刀具切削部分的材料 1. 刀具材料应具备的性能
强度和韧性 硬度和耐磨性 耐热性 其他性能
(1) 强度和韧性
强度:
抗弯强度σb(GPa或者Kg/mm2)
韧性:
冲击韧性ak(KJ/m2或者Kg/cm2))
(2) 硬度和耐磨性
影响耐磨性的因素:硬度;硬质点性质 数量和分布;显微组织;抗粘结性
由较软的六方氮化硼经过高温高压法 转化而成。
特点:硬度很高、耐磨性好、耐热性 高、化学稳定、摩擦系数低。可直接 加工淬火钢、铸铁、高温合金等,可 以使工件产生残余压应力。
二. 合理的刀具几何参数
前角 后角 主偏角 刃倾角
1. 前角的功用及选择
前 影响切削区的变形程度:前角↑ 角 前刀面的挤压↓ 塑性变形↓ 切 的 削在前刀面的摩擦阻力↓ 切削力 功 ↓ 切削热↓。 用 影响切削刃与刀头的强度、受力性
(4) 金刚石
天然,PVD、CVD。
特点:硬度最高、耐磨性好、摩擦系 数最低、导热系数最大、强度和韧性 不高,热稳定性差,刃磨困难,和铁 和钛有很强的化学亲和力。
用途:主要用于有色金属及其合金、 非金属材料的半精加工、精加工和超 精加工。不由于加工黑色金属、钛及 其合金。
(5) 立方氮化硼
切削力
重载、大切削力
(3) 陶瓷
以为Al2O3或Si3N4为主要成分,添加少 量粘结剂高温烧结而成的一种微晶显微 组织的刀具材料。
特点:硬度很高、耐磨性好、耐热性高、 化学稳定、摩擦系数低、强度和韧性差, 脆性大,易崩刃,刃磨困难。
用途:主要用于精加工和半精加工,大 件零件和高精度零件加工。
工具钢
HRC60~65 高速钢
硬质合金 HRA89~94
立方氮化硼 HV8000~
(CBN)
9000
陶瓷 金刚石
HRC 60~70 HRA91~95 HV1000
(3) 耐热性(红硬性)
高温下保持高硬度的力,通常采用刀具材料硬 度显著降低时的温度表示
工具钢 硬质合金
200~250℃ 高速钢 800~1000℃ 陶瓷