化工原理第六章主要内容
化工原理第六章蒸馏

恒摩尔气流 恒摩尔液流
注意:V不一定等于V′,L不一定等于L′
溶液中两组分的摩尔汽化热相等,即rA rB; 因汽液两相温度不同而传递的热量可忽略; 假定 精馏塔保温良好,其热量损失可以忽略。
三、进料热状态参数q
1.进料热状况的定性分析:
A — — 过冷液体;
B — — 饱和液体;
加料板及其以下 ——提馏段
加料板以上 ——精馏段
间歇精馏:
——只有精馏段, 没有提馏段
第三节 双组分连续精馏的计算与分析
设计型计算: 操作型计算:
一、全塔物料衡算
F、D、W — kmol( A B) h
xF、xD、xW — kmolA kmol( A B) 总物料:F D W
Ln1 温度 易挥发汽化多
Vn yn
气相
液相
yn yn1 xn xn1
Ln1 x n1
Ln xn
n-1 n n+1
塔顶:纯A 塔釜:纯B
Vn1 y n 1
yn+1 tn+1 tn tn-1 xn
G O P
yn
t/℃
xn-1
0
x或y
1.0
加料位置 ——与原料液组成和温度相近的板上进料
240 101.33
pA
pB
0
,kPa ,kPa
101.33 116.9 135.5 155.7 179.2 204.2 40.0 46.0 54.0 63.3 74.3 86.0
0
温度℃
80.1
85
90
95
100
105
110.6 240
pA
0
,kPa
化工原理 第六章 蒸馏

相同时进行多次部分冷凝和部分汽
化。 精馏条件:塔顶的液体回流和塔 釜的产生的蒸汽回流。
29
t P=定值 t1
t P=定值 t1 t2 t3 1 2 3
xW x1
xF
y1
yF
x(y)
x1
x2 xF x3 y1
y2 y3 x(y)
图6-10 一次部分气化的图
图6-11 多次部分气化和冷凝的示意图
30
V HF 加料板F L’ hF V’ H F+1
L' L q F
L L q F
'
F L V ' V L'
V ' V (q 1)F
41
V F L V F L V (1-q)F F qF L L’ 汽液混合进料
V =V (1 q)F
V’
V’
L’ 冷液进料
p p xA p
0 A 0 B
0 A
0 B
0 B
0 P pB xA 0 0 p A pB
xB 1 x A
——泡点方程
若平衡的气相为理想气体,可用道尔顿分压定律:
0 pA pA yA x P P
yB 1 y A
——汽液两相平衡组成间的关系
0 0 0 pA pA p pB f A (t ) p f B (t ) —露点方程 yA xA 0 0 p p pA pB p f A (t ) f B (t )
3
传质过程或分离操作:物质在相间的转移过程。
蒸馏:将液体混合物部分气化,利用各组分的挥发 度不同的性质以实现分离目的的操作。
易挥发组分(轻组份):沸点低的组分 难挥发组分(重组份):沸点高的组分
化工原理讲稿8(第六章)(天大版).
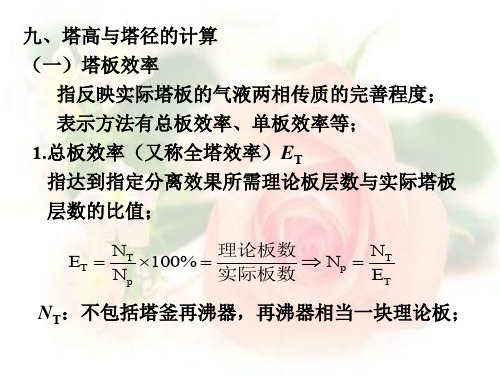
指反映实际塔板的气液两相传质的完善程度; 表示方法有总板效率、单板效率等; 1.总板效率(又称全塔效率)ET 指达到指定分离效果所需理论板层数与实际塔板 层数的比值;
ET
NT Np
100%
理论板数 实际板数
Np
NT ET
NT:不包括塔釜再沸器,再沸器相当一块理论板;
问: (1)此时产品组成将有何变化? (2)若维持xD不变,可采用哪些 措施,并比较这些方法的优缺点?
十二、特殊精馏 1.恒沸精馏
原理:在混合液中加入第三组分(称为挟带剂) 形成新的最低恒沸物;
2.萃取精馏 原理:向混合液中加入溶剂(又称萃取剂),萃取剂
不与原料液中任何组分形成恒沸物;
P73页 习题15、16;
xF 对xD, xW 的影响
b. 加料板位置上移
结论:xD , xW
加料板位置对xD, xW 的影响
c. R 结论:xD , xW
R 对xD, xW 的影响
d. q , R 不变, D不变, V’ 结论:xD , xW
q 对xD, xW 的影响
十一、 精馏装置的热量恒算
xn1 xn xn1 f '( yn )
xn1 xn
xn1 f '( xn1 )
习题16
1.y1 xD
F L'
2.
D
V
'
L
'
x1
V
'
yW
WxW
3.yW
1
xW ( 1)xW
化工原理-6章蒸馏

y x 1 ( 1)x
——相平衡方程
当 α为已知时,可用相对挥发度表示了气液相平衡关系。
当 1 当 1
y=x, 即相平衡时气相的组成与液相的组成相同, 不能用蒸馏方法分离。
则y>x,α愈大,y比x大的愈多,组分A和B愈易分离。
三、双组分理想溶液的气液平衡相图
双组分理想溶液的汽液平衡关系用相图表示比较直观、 清晰,而且影响蒸馏的因素可在相图上直接反映出来。蒸馏 中常用的相图为恒压下的温度-组成( t-x-y )图和气相-液 相组成( x-y )图。
当生产任务要求将一定数量和组成的原料分离成指定组成 的产品时,精馏塔计算的内容有:出液和塔釜残液的流量、塔 板数、进料口位置、塔高、塔径等。
6.4.1 全塔物料衡算
1.全塔物料衡算
单位时间为基准
总物料衡算: qn,F=qn,D+qn,W 易挥发组分物料衡算:
qn,FxF=qn,DxD+qn,WxW qn,F、qn,D、qn,W——流量,kmol/h
二、蒸馏的分类
1、按蒸馏方法:简单蒸馏、平衡蒸馏(闪蒸)、精馏、特殊精馏。 2、按操作压力:常压;减压;加压。 3、按原料液组分数:双组分蒸馏和多组分蒸馏 4、按操作方式:间歇蒸馏和连续蒸馏。
三、蒸馏操作的特点
优点:* 适用面广,液体混合物和气体混合物均可 * 操作流程较简单,无需其他外加介质
缺点:* 能耗大
一、利用饱和蒸气压计算气液平衡关系
法国物理学家拉乌尔在1887年研究含有非挥发性溶质的 稀溶液的行为时发现的,可表述为:“在某一温度下,稀溶 液的蒸气压等于纯溶剂的蒸气压乘以溶剂的摩尔分数”。
PA PA0 xA ——拉乌尔定律
pA0——纯组分A在溶液温度下的饱和蒸气压,Pa; xA——溶液中组分A的摩尔分数;
(化工原理)第6章:质量传递过程基础

D z
c0 cBm
cA1 cA2
对于理想气体
cBm
cB2 cB1
ln
cB2 cB1
cB1 c0 cA1 cB2 c0 cA2
NA
D RTz
p pBm
pA1 pA2
p pBm
pBm
pB2 pB1
ln
pB2 pB1
pB1 p pA1 pB2 p pA2
c cBm
称为漂流因子 反应总体流动对传质通量的影响
NA ky y yi
NA kx xi x
NA kG pA pAi
NA kL cAi cA
传质系数 k=f (D,η,ρ,u,d )
经验关联式很多,但普遍偏差较大 主要通过实验获得
JA
DAB
dcA dz
yi Ki xi
NA
D z
c0 cBm
cA1 cA2
NA
D RTz
主体中高度湍流传质阻力为零,即无浓度
O
距离 z
相际传质双膜模型
梯度。 ④ 相界面上气液处于平衡状态,无传质阻
力存在。
(2)总传质速率方程
① 气膜和液膜传质速率方程 对气相:
NA kG pA pAi
化工原理 第六章 吸收
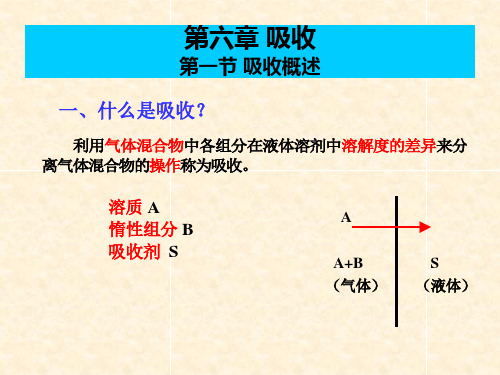
由 y * mx得,
Y* mX 1 Y * 1 X
*
mX Y 1 (1 m)X
当溶液浓度很低时,X≈0, 分母约等于1. 上式简化为:
Y mX
*
亨利定律的几种表达形式也可改写为
P * x , c HP E y Y * ℃ 下 , 测 得 氨 在 水 中 的 平 衡 数 据 为 : 0.5gNH3/100gH2O浓度为的稀氨水上方的平衡分压为400Pa, 在该浓度范围下相平衡关系可用亨利定律表示,试求亨利系
——逆流吸收塔操作线方程
在m—n截面与塔顶截面之间作组分A的衡算
VY LX 2 VY2 LX
L L Y X (Y2 X 2 ) V V
——逆流吸收塔操作线方程
表明 : 塔内任一截面的气相浓度Y与液相浓度X之间成直线 关系,直线的斜率为L/V。
吸收操作线总是位于平衡线的上方,
s
EM s
1000 7.32 104 kmol / m3 Pa 7.59 10 4 18
E 7.59 10 4 m 3 0.749 P 101.33 10
三、用气液平衡关系分析吸收过程
1、判断过程的方向
例:在101.3kPa,20℃下,稀氨水的气液相平衡关系为 :
L L Y1 X 1 Y2 X 2 V V
吸收率 A 混合气中溶质A 被吸收的百分率
Y2 Y1 (1 A )
2、吸收塔的操作线方程式与操作线
在 m—n截面与塔底截面之间作组分A的衡算
VY LX1 VY1 LX
L L Y X (Y1 X 1 ) V V
操作线位于平衡线下方,则应进行脱吸过程。
并流吸收塔的操作线:
化工原理第六章6
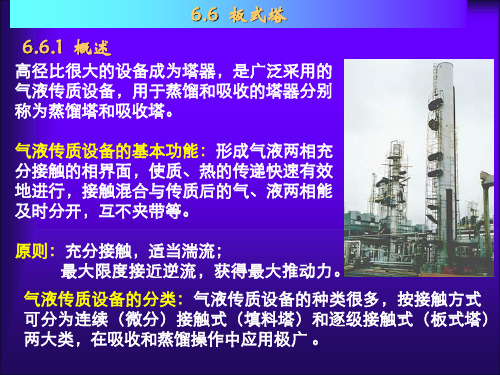
液层阻力 hl 气体通过液层的阻力损失 hl 由以下三个方面构成: (1) 克服板上充气液层的静压; (2) 气体在液相分散形成气液界面的能量消耗; (3) 通过液层的摩擦阻力损失。 其中(1)项远大于后两项之和。如果忽略充气液层中所含气体 造成的静压,则可由清液层高度代表 hl。可用下式计算
hl hw how
F1型浮阀结构简单,易于制造,应用最普遍,为定型产品。 阀片带有三条腿,插入阀孔后将各腿底脚外翻 90°,用以限 制操作时阀片在板上升起的最大高度;阀片周边有三块略向 下弯的定距片,以保证阀片的最小开启高度。 F1型浮阀分轻阀和重阀。轻阀塔板漏液稍严重,除真空操作 时选用外,一般均采用重阀。
浮阀塔板的流体力学性能 浮阀塔板上的气、液流程 浮阀塔板的板面结构: 鼓泡区(有效区、开孔区) 降液管区 受液盘区 液体安定区 边缘区 溢流堰
填料塔 在圆柱形壳体内装填一定高度的填料, 液体经塔顶喷淋装臵均匀分布于填料层 顶部上,依靠重力作用沿填料表面自上 而下流经填料层后自塔底排出;气体则 在压强差推动下穿过填料层的空隙,由 塔的一端流向另一端。气液在填料表面 接触进行质、热交换,两相的组成沿塔 高连续变化。
气体
溶剂
填料塔
规整填料 塑料丝网波纹填料
降液管
液 相
堰
气相
溢流式塔板应用很广,按塔板的具体结构形式可分为: 泡罩塔板、筛孔塔板、浮阀塔板、网孔塔板、舌形塔板等。
逆流塔板(穿流式塔板): 塔板间没有降液管,气、液两相同时由 塔板上的孔道或缝隙逆向穿流而过,板 上液层高度靠气体速度维持。 优点:塔板结构简单,板上无液面差, 板面充分利用,生产能力较大; 缺点:板效率及操作弹性不及溢流塔板。
H d hw how h f h
化工原理 第六章 蒸馏(传质过程)
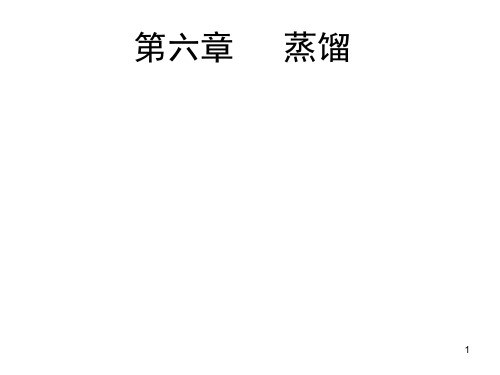
t
121.9℃
X=0.383
负偏差
x y
x y
y
y
x
x
19
挥发度与相对挥发度
挥发度:表示某种溶液易挥发的程度。 若为纯组分液体时,通常用其当时温度下饱和蒸 气压PA°来表示。 若为混合溶液时,各组分的挥发度,则用它在一 定温度下蒸气中的分压和与之平衡的液相中该组 分的 摩尔分数之比来表示, vA = pA / xA vB = pB / xB
演示
37
xn
xn 1 yn 1 yn
第四节 双组分连续精馏计算
38
物料衡算
F—原料(液)摩尔流量,kmol/h; D—馏出液摩尔流量,kmol/h; W—釜残液摩尔流量,kmol/h; 总物料衡算 易挥发组分的物料衡算
D xD F xF
F D W
D F ( xF xW ) xD xW
xn 1
n 1
yn xn yn 1
n
n 1
T-x(y) 图
t 假设蒸汽和液体充分接触,并在离 n 1 开第 n 层板时达到相平衡,则 yn 与 xn t n t n 1 平衡,且yn>yn+1,xn<xn-1。
这说明塔板主要起到了传质作用, 使蒸汽中易挥发组分的浓度增加, 同时也使液体中易挥发组分的浓度 减少。
t5 t4 t3 t2 t1
E D
C
B A
x(y)
温度-组成图( t-x-y 图)
12
上述的两条曲线将tx-y图分成三个区域。
液相线以下的区域 代表未沸腾的液体, 称为液相区 气相线上方的区域 代表过热蒸气,称为 过热蒸气区; 二曲线包围的区域 表示气液同时存在, 称为气液共存区。
化工原理讲稿8(第六章)(天大版)
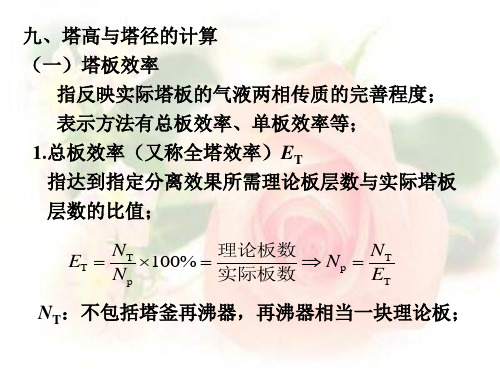
对 全 回 流 操 作 : y n +1 = x n、 y n = x n −1 y n − y n +1 x n −1 − x n E mV = y * − y = f ( x ) − x n n +1 n n 则: x n −1 − x n E = x n −1 − x n = x n −1 − x n = mL x n −1 − x n * x n −1 − f '( y n ) x n −1 − f '( x n −1 )
习题16 习题
1. y1 = xD F = L ' ⇒ L ' x1 = V ' yW + WxW 2. D = V ' α xW 3. yW = 1 + (α − 1) xW 4.EmV y1 − yW = y1 * − yW
设: F = 1kmol / h Dx D x F − xW x D 0.2 − xW 0.28 η D = 0.8 = = = ⇒ xW = 0.0857 Fx F x D − xW x F 0.28 − xW 0.2 D = 0.57 kmol / h、 W = 0.43kmol / h F = L ' F W ⇒ L ' x1 = V ' y W + Wx W ⇒ y W = x1 − xW D D D = V ' 1 0.43 ⇒ 0.206 = x1 − × 0.094 ⇒ x1 = 0.158 0.57 0.57 y1 = x D = 0.28 y1 − y W α xW 2.5 × 0.094 = = 0.206 由于: E mV = 其中: yW = y1 * − y W 1 + (α − 1) xW 1 + 1.5 × 0.094 α x1 2.5 × 0.158 = = 0.319 y1 * = 1 + (α − 1) x1 1 + 1.5 × 0.158 0.28 − 0.206 E mV = = 0655 0.319 − 0.206
化工原理 第六章 吸收

M液 M剂
表6-1某些气体水溶液的亨利系数值(E×10-6/kPa)
由表6-1中的数值可知:不同的物系在同一个温度下 的亨利系数E值不同;当物系一定时,亨利系数随温度升 高而增大,温度愈高,溶解度愈小。所以亨利系数值愈大, 气体愈难溶。在同一溶剂中,难溶气体的值很大,而易溶 气体的值很小。
编辑ppt
体,则混气中的A组分有:
cA
nA V
pA RT
(6-5)
编辑ppt
第二节 吸收中的气液相平衡
二、气液相平衡关系 气液相平衡关系是指气液两相达到平衡时,被吸收的 组分(吸收质)在两相中的浓度关系,即吸收质在吸收剂 中的平衡溶解度。 1.气体在液体中的溶解度 在恒定的压力和温度下,用一定量的溶剂与混合气体 在一密闭容器中相接触,混合气中的溶质便向液相内转移, 而溶于液相内的溶质又会从溶剂中逸出返回气相。随着溶 质在液相中的溶解量增多,溶质返回气相的量也在逐渐增 大,直到吸收速率与解吸速率相等时,溶质在气液两相中 的浓度不再发生变化,此时气液两相达到了动态平衡。平 衡时溶质在气相中的分压称为平衡分压,用符号 表示; 溶质在液相中的浓度称为平衡溶解度,简称溶解度;它们 之间的关系称为相平衡关系。
化工原理
第六章 吸 收
编辑ppt
第一节 概 述
一、吸收综述 吸收就是分离气体混合物的单元操作,即是用适当的液体吸收剂处理 气体混合物,利用混合气中各组分在液体溶剂中溶解度的不同而分离气体 混合物的操作,其实质是一种典型的气、液相扩散传质过程。 吸收系统包括气、液两个相,气相由可溶于吸收剂的气体组分(称为吸 收质或溶质)和不溶或难溶于吸收剂的惰性组分(称为惰性气或载体)组成, 液相则是液体吸收剂(或称为溶剂);吸收操作所得到的溶液称为吸收液, 其成分为吸收剂和溶解于其中的吸收质;排除的气体称为吸收尾气,其主 要成分应为惰性组分和残余的溶质。 吸收的原理:就是利用混气中,各组分在吸收剂中有不同的溶解度的 特点,选择适宜的吸收剂对混合气中组分进行选择性吸收,以达到从混合 气中分离或提纯组分之目的。 与吸收操作相反,使吸收质从吸收剂中分离出来的操作称为解吸或脱 吸。其目的是循环使用吸收剂或回收溶质,实际生产中吸收过程和解吸过 程往往联合使用。 吸收和蒸馏一样也牵涉到气、液两相间的质量传递,但蒸馏是依据混 液中各组分挥发度的不同而得以分离;吸收则基于混气中各组分在吸收剂 中的溶解度不同而得以分离;蒸馏属双向传质,吸收为单相传质。
陈敏恒_化工原理_第六章(全)

A’=1.35m2
4.1 沸腾给热 1. 大容积饱和沸腾 过程特点:汽液两相共存
有利:气泡搅动液体,液体冲刷表面 不利:有可能气泡连成气膜,将液体与加热面隔开 2.沸腾条件 ①过热度(t-tS) —气泡存在之必须
2.α的影响因素 ①物性:ρ, μ, Cp, λ ②设备因素(定性尺寸):l ③流动因素:强制对流:u 自然对流: βgΔt α=f (ρ, μ, λ, l, u, βgΔt, Cp) 基本量纲4个(M,L,T,θ),变量8个, 无量纲准数=8-4=4,即 3 2 l lu Cp gtl f( , , ) 2 Nu=f(Re, Pr, Gr) 强制对流Nu=f(Re, Pr); 自然对流Nu=f(Gr, Pr)
自然对流的冷源、热源应放在恰当的位置
2.强制对流 在外力或Δp作用下引起流动
3.3 对流给热过程的数学描述 1.牛顿冷却定律 q (T TW ) 其中:TW: 壁温;T: 流体主体温度; α:给热系数 W/m2℃ 工程处理方法—分离变量法 ① 便于分解组合传热系数K
T TW TW tW tW t q 1 / 1 / 1/2
第六章 传热
1 概述 1.1 传热目的 ①加热、冷却物料 ②回收热量或冷量 设法促进传热 ③保温,减少热量或冷量损失 设法阻止传热 传热还用于其它单元操作 如蒸发,精馏
1.2传热机理 ①传导—分子热运动(自由电子迁移) ②对流—流体宏观迁移引起载热 ③辐射—电磁波 热水瓶为什么能保温? 1.3冷热流体接触方式 ①蓄热式
2.4 球壳导热
dt Q 4r dr r2 dr t2 Q 2 4 dt r1 r t1 4 ( t1 t 2 ) 4r1r2 ( t1 t 2 ) Q 1 1 r2 r1 r1 r2
化工原理第六章主要内容
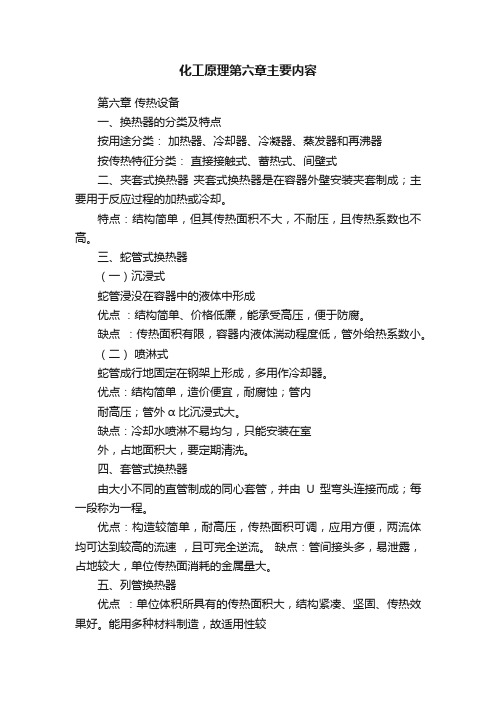
化工原理第六章主要内容第六章传热设备一、换热器的分类及特点按用途分类:加热器、冷却器、冷凝器、蒸发器和再沸器按传热特征分类:直接接触式、蓄热式、间壁式二、夹套式换热器夹套式换热器是在容器外壁安装夹套制成;主要用于反应过程的加热或冷却。
特点:结构简单,但其传热面积不大,不耐压,且传热系数也不高。
三、蛇管式换热器(一)沉浸式蛇管浸没在容器中的液体中形成优点:结构简单、价格低廉,能承受高压,便于防腐。
缺点:传热面积有限,容器内液体湍动程度低,管外给热系数小。
(二)喷淋式蛇管成行地固定在钢架上形成,多用作冷却器。
优点:结构简单,造价便宜,耐腐蚀;管内耐高压;管外α 比沉浸式大。
缺点:冷却水喷淋不易均匀,只能安装在室外,占地面积大,要定期清洗。
四、套管式换热器由大小不同的直管制成的同心套管,并由U 型弯头连接而成;每一段称为一程。
优点:构造较简单,耐高压,传热面积可调,应用方便,两流体均可达到较高的流速,且可完全逆流。
缺点:管间接头多,易泄露,占地较大,单位传热面消耗的金属量大。
五、列管换热器优点:单位体积所具有的传热面积大,结构紧凑、坚固、传热效果好。
能用多种材料制造,故适用性较强,操作弹性较大,尤其在高温、高压和大型装置中多采用列管式换热器。
(一)列管换热器的构造和形式主要部件:壳体、管束、管(花)板、顶盖(封头)管束装在壳体内,固定于管板上1.固定管板式(G )两端管板和壳体制成一体,结构简单,成本低;壳程清洗和检修困难;不进行热补偿或采用补偿圈进行热补偿;不宜用于两流体温差过大(大于70℃)和壳程流体压强过高的场合。
2.浮头式换热器(F)一端管板不与外壳连为一体,形成可沿轴向自由浮动的浮头进行热补偿;整个管束可以从壳体中抽出,管、壳程均便于清洗和检修;允许两程温差较大;结构比较复杂,造价较高。
3. U 型管式换热器每根管子都弯成U 型,进出口分别安装在同一管板的两侧,每根管子可以自由伸缩进行热补偿;封头用隔板分成两室,形成双管程;管程不易清洗。
化工原理第六章(双组分连续精馏的计算与分析)
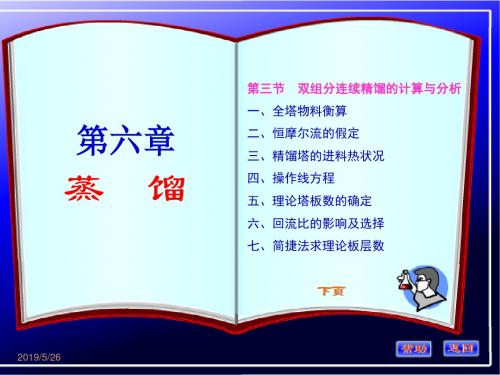
L' W ym1 V ' xm V ' xw
提 馏 操 作 线
( xm=xW , ym+1=xW ) 截距=- WxW/V’
2019/5/26
(4)提馏操作线方程的其他表现形式
令: R ' L' ——再沸比 W
【说明】再沸比R’是提馏段内各块塔板下降的液体 量与塔底引出的釜液(馏残液)量之比。
2019/5/26
【解】依题意知 xF=0.84 xD=0.98 xw=0.002 F=235kmol/h
据 F=D+W FxF=DxD+Wxw
∴ 235=D+W 0.84×235=0.98D+0.002W 联立后可解得: D=201.36kmol/h
W=33.64kmol/h 即塔顶采出量为 201.36kmol/h
第六章
蒸馏
第三节 双组分连续精馏的计算与分析 一、全塔物料衡算 二、恒摩尔流的假定 三、精馏塔的进料热状况 四、操作线方程 五、理论塔板数的确定 六、回流比的影响及选择 七、简捷法求理论板层数
2019/5/26
【精馏过程的计算内容】
1、设计型计算 (1)根据精馏塔的塔板层数以 确定塔的高度; (2)适宜的加料位置。 2、操作型计算 (1)确定产品的流量或组成; (2)确定适宜的操作回流比; (3)计算冷凝器、再沸器的热 负荷等。
2019/5/26
三、精馏塔的进料热状况
1、五种进料热状态 ①温度低于泡点的冷液体; ②泡点下的饱和液体; ③温度介于泡点和露点之间的气液混合物; ④露点下的饱和蒸气; ⑤温度高于露点的过热蒸气。
2019/5/26
【结论】进料热状况不同,其温度不同,状态亦不同。
《化工原理》第六章 蒸发
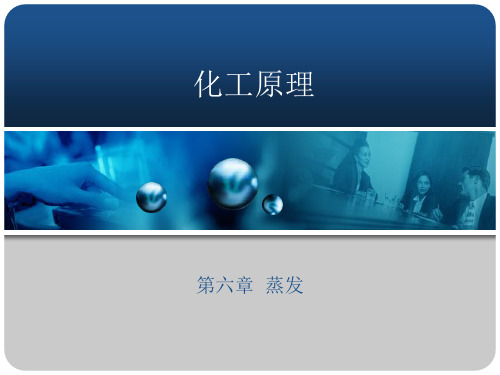
或
w W = F 1 − 0 w1
(6-1)
第二节 单效蒸发
式中 ——原料液的流量,kg/h; ——单位时间从溶液中蒸发的水分量,即蒸 发量,kg/h; ——原料液中溶质的质量分数; ——完成液中溶质的质量分数。 2.加热蒸汽消耗量 加热蒸汽消耗量通过热量衡算求得。通常,加热蒸汽 为饱和蒸汽,且冷凝后在饱和温度下排出,则加热蒸汽仅 放出潜热用于蒸发。若料液在低于沸点温度下进料,对热 量衡算式整理得: Q = Dr = Fc (t − t ) + Wr + Q (6-2)
第二节 单效蒸发
沸点升高对蒸发操作的传热推动力温度差不利,例如 用120℃的饱和水蒸汽分别加热20%(质量分数)NaOH水溶 液和纯水,并使之沸腾,有效温度差分别为 20%(质量分数)NaOH水溶液 ∆t ∆t =T − t =120-108.5=11.5℃ ∆t = T − T =120-100=20℃ 纯水 由于溶液的沸点升高,致使蒸发溶液的传热温度差较 蒸发纯水的传热温度差下降了8.5℃,下降的度数称为温 度差损失,用 ∆ 表示。由于 ∆ = ∆t − ∆t = (T − T ) − (T − t ) = t − T (6-8)
' p0 1 0 损
第二节 单效蒸发
式中 Q——蒸发器的热负荷或传热量,kJ/h ; D——加热蒸气消耗量,kg/h; Cp0——原料液比热容,kJ/(㎏·℃); t0——原料液的温度,℃; t1——溶液的沸点,℃; r ——加热蒸汽的汽化潜热,kJ/㎏; r’——二次蒸汽的汽化潜热,kJ/㎏; Q损 ——蒸发器的热损失,kJ/h 。
第二节 单效蒸发
工业上的蒸发操作经常在减压下进行,减压操作具有 下列特点: (1)减压下溶液的沸点下降,有利于处理热敏性的物 料,且可利用低压的蒸汽或废蒸汽作为加热剂。 (2)溶液的沸点随所处的压强减小而降低,故对相同 压强的加热蒸汽而言,当溶液处于减压时可以提高传热总 温度差;但与此同时,溶液的黏度加大,使总传热系数下 降。 (3)真空蒸发系统要求有造成减压的装置,使系统的 投资费和操作费提高。
化工原理 第六章 精馏
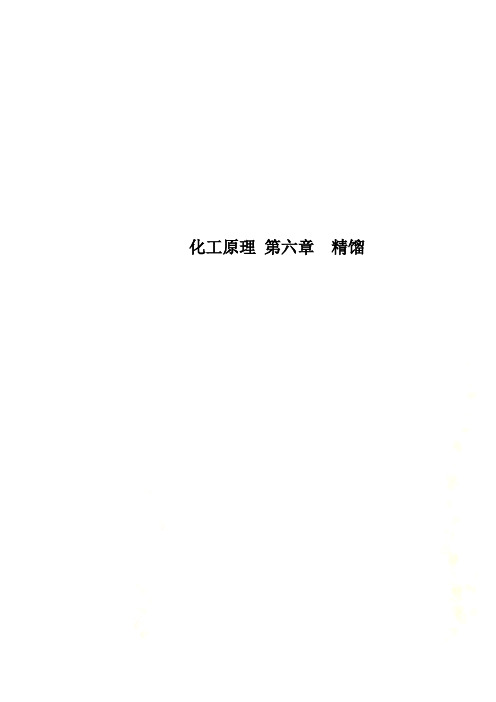
化工原理第六章精馏第六章精馏一、精馏过程的数学描述在化工生产中,常根据混合液中各组分挥发度的不同,以精馏实现均相混合液的分离,二元连续精馏的基本流程如图6-1所示。
精馏过程的实质是伴有传热的传质过程,传质推动力取决于相互接触汽液两相偏离平衡的程度。
因此精馏过程的严格分析除了要应用相平衡、物料衡算两关系外,还需结合热量衡算及传质速率方程。
为了避开后两关系使分析得以简化,在工程上常引入似下两个概念:(1)理论板,(2)恒摩尔流,前者将影响板上传质速率的全部因素包括在塔板效率中;后者则是对热量衡算的简化。
于是精馏过程的数学描述可归结为全塔物料衡算、逐板组成变化两关系。
以图6-1的流程分离理想溶液;其已知量、未知量之间的关系可用图6-2表示。
图6-2表明,描述二元连续精馏的基本方程为 )(1W F D W D F x x R q N N f x Wx Dx Fx W D F ,,,,,,α=+=+= 由于三式中共涉及11个基本变量)(1R q N N x x x W D F W D F ,,,,,,,,,,α,因此其自由度为8,即须给定其中8个独立变量,才能确定另外3个变量。
二、精馏操作型问题的特点及基本类型精馏操作型问题的特点是:精馏塔已经给定(设塔板效率已知)。
即N 、N 1(或进料位置,通常不一定是最佳进料位置)为巳知量,其主要类型如下。
(1)对现有的精馏塔,在给定精馏条件下,核算其可能达到的分离程度。
如:已知N 、N 1、α、F 、x F 、q 、R 及W ,求D 、x D 、x W 。
(2)对运行中的精馏塔,当某一操作条件改变时,分析分离效果的变化,是否能获得合格的产品及为此需采取的措施;还会产生什么其他的影响。
如:(6-1)①已知N、N1、α、F、x F、q、R不变,若V'减少时,分析D、x D、x W的变化趋势;②已知N、N1、α、F、x F、q、V'不变,若x F下降,能否采取什么措施使x F不降低?通常对类型2,操作条件的变化将引起塔内液,汽流量的改变,并影响塔板效率,若这一影响甚小而能忽略,便可把操作中精馏塔的理论板数视为不变。
化工原理-热传
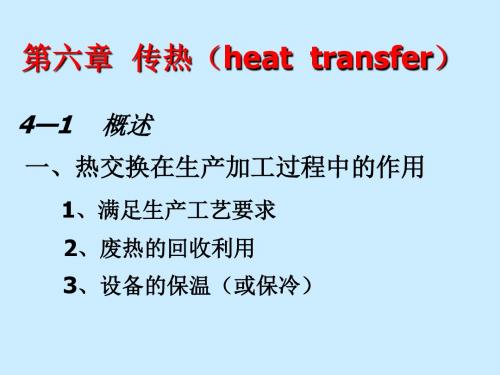
④固体表面的特征尺寸,用L表示。 则用函数形式表示为:
α=f(u、L、ρ、μ、λ、cp、βgΔt)
准数方程式( 由无量纲量组成的准数关系式,由量纲分析得)
Nu=AReaPrbGrc
Nu=AReaPrbGrc
各准数的意义: Re雷诺数 Re =d uρ/μ 表示流体的运动状态对对流给热的影响。 Nu 努塞尔数 Nu = αL/ λ 表示对流使给热系数增大的倍数(相对于纯导)。 Pr 普朗特数 Pr = cpμ/λ 表示流体物性对对流给热的影响。 Gr格拉斯霍夫数 表示自然对流对对流给热的影响。 以上准数关系式中的A、a、b、c需通过实验确定。 使用实验方程式(经验关联式)时应注意: 1、适用范围 2、定性温度 3、特性尺寸
非金属
(A)对于大多数均质的固体 λ = λ 0(1+αt)
式中 λ -- t 温度下固体的导热系数, W/(m℃);
λ 0-- 0℃下固体的导热系数, W/(m℃);
α --温度系数, 1/℃;
t --固体的温度, ℃.(B)t↑ λ金属↓,λ非金属↑; 纯度↓ λ金属及λ非金属↓ (C)绝热材料的λ通常 < 0.2 W/m℃ (D)热传导过程物质的导热系数通常按平均值计算
所得的结果适当加以修正。
(1)对于高粘度液体 α=0.027(λ/d )Re0.8Pr 0.33 (μ/μw)0.14 式中 μ——液体在定性温度下的粘度; μw——液体在壁温下的粘度。 适用范围是: Re>104; L/d>30—40; Pr=0.5—100的各种液体(不适用于液体金属)。 特性尺寸:管内径d; 定性温度:除μw以外,其余都取液体进出口温度的平均值。 (μ/μw)0.14可以按下式取值: 液体被加热时 (μ/μw)0.14=1.05 液体被冷却时 (μ/μw)0.14=0.95
化工原理第六章(概述、双组分溶液的气液相平衡)
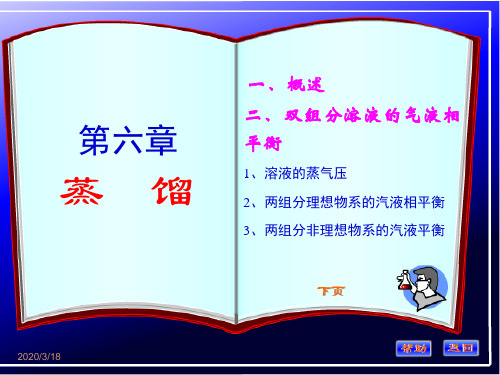
甲醇—水溶液平衡数据(101.3kPa)
t(℃) 100 96.4 91.2 87.7 81.7 78.0 75.3
x
0 0.02 0.06 0.10 0.20 0.30 0.40
y
0 0.134 0.304 0.418 0.579 0.665 0.729
t(℃) 73.1 71.2 69.3 67.6 66.0 65.0 64.5
2020/3/18
(2)在相同温度下,不同液体的饱和蒸气压不同。 液体的挥发能力越大,其饱和蒸气压就越大。 【例如】25 ℃时,乙醇(A)、水(B)的饱和蒸气 压分别为: pA0=7.86kPa pB0=3.17kPa 【结论】饱和蒸气压是表示液体挥发能力的属性之 一。
2020/3/18
(3)液体混合物在一定温度下也具有一定的蒸气压 ,但其中各组分的蒸气压(分压pA)与其单独存在 时的饱和蒸气压(pA0)不同。 (4)对于二组分混合物,由于B组分的存在,使A组 分在气相中的蒸气分压比其在纯态时的饱和蒸气压 要小。
0.2031
0.3801
100
95
90
102℃
85
80
0.0
0.2
0.4 x y0.6
0.8
1.0
常压下苯-甲苯体系的温度组成图(t-x-y)
2020/3/18
汽液共存区 泡点线
泡点 液相区
P=101.3kPa
过热蒸 汽区
露点
露点线
【相关信息】压力(P), 温度(t),组成(x,y)。
【结构特点】两条线;两个点;三个区。
2020/3/18
(4)按操作压力 【常压蒸馏】常压下泡点为室温至150℃左右的液体 混合液,一般采用常压(大约1atm)蒸馏; 【加压蒸馏】常压下为气态(如空气、石油气)或 常压下泡点为室温的混合物,常采用加压(操作压 力高于1atm)蒸馏; 【减压蒸馏】对于常压下泡点较高或热敏性混合物 (高温下易发生分解,聚合等变质现象),宜采用 减压(操作压力低于1atm)蒸馏。
化工原理第六章

第三节 多效蒸发
图6-4 逆流加料法的蒸发流程示意图
第三节 多效蒸发
优点: (1) 蒸发的温度随溶液浓度的增大而增高,这样各效 的黏度相差很小,传热系数大致相同; (2) 完成液排出温度较高,可以在减压下进一步闪蒸 增浓. 缺点: (1)辅助设备多,各效间须设料液泵; (2)各效均在低于沸点温度下进料,须设预热器(否 则二次蒸汽量减少),故能量消耗增大. 一般来说,逆流加料法宜于处理黏度随温度和浓度变化 较大的料液蒸发,但不适用于热敏性物料的蒸发.
第三节 多效蒸发
一,多效蒸发的操作原理
由蒸发器的热量恒算可知,在单效蒸发器中每蒸发1㎏的水需要 消耗1㎏多的生蒸汽.在大规模的工业生产中,水分蒸发量很大,需 要消耗大量的生蒸汽.如果能将二次蒸汽用作另一蒸发器的加热蒸汽, 则可减少生蒸汽消耗量.由于二次蒸汽的压力和温度低于生蒸汽的压 力和温度,因此,二次蒸汽作为加热蒸汽的条件是:该蒸发器的操作 压力和溶液沸点应低于前一蒸发器.采用抽真空的方法可以很方便地 降低蒸发器的操作压力和溶液的沸点.每一个蒸发器称为一效,这样, 在第一效蒸发器中通入生蒸汽,产生的二次蒸汽引入第二效蒸发器, 第二效的二次蒸汽再引入第三效蒸发器,以此类推,末效蒸发器的二 次蒸汽通入冷凝器冷凝,冷凝器后接真空装置对系统抽真空.于是, 从第一效到最末效,蒸发器的操作压力和溶液的沸点依次降低,因此 可以引入前效的二次蒸汽作为后效的加热介质,即后效的加热室成为 前效二次蒸汽的冷凝器,仅第一效需要消耗生蒸汽,这就是多效蒸发 的操作原理.
第二节 单效蒸发
式中
f
——较正系数,无因次.由下式计算得到 (6-12) 0.0162(T + 273 )
f =
' 2
r'
化工原理:第6章 总结
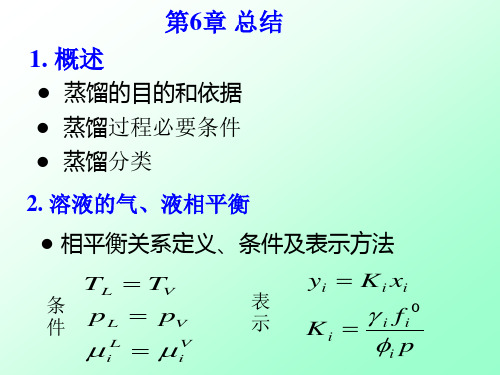
xn
qnL
qnW xW qqnF
qnW
直到 xn xw
则 n为所需的理论板数.
例题6.5.1、P38
(2)图解法:
Q
xD
R 1
W
xW
zF
D
xD N=9(包含釜)
2. 影响 N 的因素分析
(1)R: R ↑→N ↓ →塔设备费↓
动画示意
(2)q:q ↑ → N ↓。
re
(3)分离要求: xD↑ 、 xW ↓→ N ↑
理想溶液----相对挥发度α 变化不大,可取一平均值作为常 数处理;
非理想物系---- α不能作为常数处理。
◆ 相平衡常数与相对挥发度的关系
ih
Ki Kh
◆ 压力对相平衡的影响
P 升高,t 升高 , 下降,对分离不利, p 下降,t 下降 , 升高,对分离有利 。
1. 非理想溶液的气液相平衡
精馏段:q nVn 1 q nVn q nV
qnLn qnLn1 qnL
提馏段:q n Vn 1 q n Vn q n V
qn Ln qn Ln1 qn L
(2) 进料的热状态参数 q
q
H mV
H mF r
每摩尔进料变为饱和蒸 气所需热量
进料的摩尔汽化热
qnL ' qnL qqnF
确定此时的适宜回流比R
Rm in
xD yWe yWe xWe
适宜回流比的选择是 一个经济问题
6.7 恒沸精馏 和萃取精馏
(1) 应用: ① 具有恒沸点的液相混合物 ② 具有较小相对挥发度的物系
(2) 原理: 在液相混合物中加入第三组分(质量分离剂), 改变原溶液中各组分间的相对挥发度。
- 1、下载文档前请自行甄别文档内容的完整性,平台不提供额外的编辑、内容补充、找答案等附加服务。
- 2、"仅部分预览"的文档,不可在线预览部分如存在完整性等问题,可反馈申请退款(可完整预览的文档不适用该条件!)。
- 3、如文档侵犯您的权益,请联系客服反馈,我们会尽快为您处理(人工客服工作时间:9:00-18:30)。
第六章 传热设备
一、换热器的分类及特点
按用途分类: 加热器、冷却器、冷凝器、蒸发器和再沸器
按传热特征分类: 直接接触式、蓄热式、间壁式
二、夹套式换热器 夹套式换热器是在容器外壁安装夹套制成;主要用于反应过程的加热或冷却。
特点:结构简单,但其传热面积不大,不耐压,且传热系数也不高。
三、蛇管式换热器
(一)沉浸式
蛇管浸没在容器中的液体中形成
优点 :结构简单、价格低廉,能承受高压,便于防腐。
缺点 :传热面积有限,容器内液体湍动程度低,管外给热系数小。
(二) 喷淋式
蛇管成行地固定在钢架上形成,多用作冷却器。
优点:结构简单,造价便宜,耐腐蚀;管内
耐高压;管外α 比沉浸式大。
缺点:冷却水喷淋不易均匀,只能安装在室
外,占地面积大,要定期清洗。
四、套管式换热器
由大小不同的直管制成的同心套管,并由U 型弯头连接而成;每一段称为一程。
优点:构造较简单,耐高压,传热面积可调,应用方便,两流体均可达到较高的流速 ,且可完全逆流。
缺点:管间接头多,易泄露,占地较大,单位传热面消耗的金属量大。
五、列管换热器
优点 :单位体积所具有的传热面积大,结构紧凑、坚固、传热效果好。
能用多种材料制造,故适用性较
强,操作弹性较大,尤其在高温、高压和大型装置中多采用列管式换热器。
(一)列管换热器的构造和形式
主要部件: 壳体、管束、管(花)板、顶盖(封头)
管束装在壳体内,固定于管板上
1.固定管板式(G )
两端管板和壳体制成一体,结构简单,成本低;
壳程清洗和检修困难;
不进行热补偿或采用补偿圈进行热补偿;
不宜用于两流体温差过大(大于70℃)和壳程流体压强过高的场合。
2.浮头式换热器(F)
一端管板不与外壳连为一体, 形成可沿轴向自由浮动的浮头进行热补偿;
整个管束可以从壳体中抽出,管、壳程均便于清洗和检修;
允许两程温差较大;
结构比较复杂,造价较高。
3. U 型管式换热器
每根管子都弯成U 型,进出口分别安装在同一管板的两侧,每根管子可以自由伸缩进行热补偿; 封头用隔板分成两室,形成双管程;
管程不易清洗。
⎧⎪⎧⎪⎨⎪⎨⎩⎪⎪⎪⎩夹套式浸没式蛇管式间壁式喷淋式套管式
列管式
(二)列管换热器的选用和设计
1.流程的选择
不清洁的物料走易于清洗的一侧;α小的流体走管内;腐蚀性物料走管内;高压流体走管内;高温或要保温(冷)的流体走管内;蒸汽一般走壳程;粘度大的流体走壳程(装有挡板时)。
2. 流速的选择
液体流速的选择主要依据粘度大小而定。
一般液体的流速选择范围为:管程0.5~3m/s;壳程0.2~1.5m/s
气体的流速选择范围为:管程5~30 m/s;壳程3~15m/s
3.换热管规格及其在管板上排列方法
管子的规格:Φ19×2mm和Φ25×2.5mm
管长:1.5m、2.0m、3.0m、6.0m
排列方式:正三角形排列正方形直列正方形错列
正三角形排列紧凑,传热效果好,但管外清洗困难;
正方形排列传热效果要差些,管外清洗容易;
正方形错列使传热效果有所改善。
固定管板式换热器:Φ25×2.5mm正三角形排列;
浮头式换热器:Φ19×2mm正三角形排列;Φ25×2.5mm正方形排列
一般L/D=4~6
4.阻力损失的计算
(1)管程阻力损失
(2)壳程阻力损失
5.列管换热器的选用和设计计算步骤
(1)根据工艺任务,计算热流量Q和平均温差∆t m,按估计的K,估算传热面积A。
(2)试选适当型号的换热器。
由u和V估算单管程的管子根数,由管子根数和估算的A估算管子长度,再由系列标准选适当型号。
(3)计算管程、壳程阻力损失。
(4)核算传热系数K和传热面积A。
分别计算管程和壳程的α,确定垢阻,求出K,并与估算的K进行比较。
如果相差较多,应重新估算。
根据计算的K和∆t m,计算A,选定的换热器面积应比计算值大10%~25%。
六、换热器的强化途径
1、增大单位体积内的传热面积A/V
直接接触传热,可增大A 和湍动程度,使Q↑;
采用高效新型换热器改进传热面结构来增大A和湍动程度,使Q↑
2、增大平均传热温差∆tm
两侧变温情况下,尽量采用逆流或接近逆流流动。
3、增大传热系数K
尽可能减小控制性热阻;
提高较小的α;
延缓垢层形成速度及定期清洁垢层。
提高α的方法(无相变):
增大流速;
管内添加扰流元件;
改变传热面形状。