玻璃窑炉烟气综合净化技术介绍(海元环境2014)
玻璃熔窑烟气治理中脱硫除尘脱硝技术的应用

玻璃熔窑烟气治理中脱硫除尘脱硝技术的应用玻璃熔窑是玻璃行业中不可或缺的关键设备,但同时也是造成大气污染的重要源头。
熔窑燃烧过程中产生的烟气中含有大量的二氧化硫、颗粒物和氮氧化物等有害物质,对环境和人体健康都造成了严重危害。
熔窑烟气治理中的脱硫、除尘、脱硝技术成为了解决大气污染问题的关键之一。
本文将重点探讨玻璃熔窑烟气治理中脱硫除尘脱硝技术的应用和发展。
熔窑烟气中的二氧化硫是主要的污染物之一,其排放对大气环境造成了严重影响。
脱硫技术在玻璃熔窑烟气治理中发挥了重要作用。
目前,常用的脱硫技术包括湿法石膏法脱硫、干法碱法脱硫和氨法脱硫等。
湿法石膏法脱硫是将熔窑烟气中的二氧化硫通过喷淋方式与石膏乳液反应生成硫酸钙并沉淀下来,以达到脱硫的效果。
这种方式脱除二氧化硫效率高,但同时也会产生大量的废水和固体废物,需要进行合理的处理和利用,以免造成二次污染。
干法碱法脱硫是利用碱性吸收剂如氢氧化钠或氨水与烟气中的二氧化硫发生中和反应,形成硫酸钠或硫酸铵,并通过除尘设备将其沉降下来。
这种脱硫方式无需处理大量的废水,但是吸收剂的再生和回收成本较高,需要对工艺进行进一步优化。
氨法脱硫是将氨气注入烟气中,与二氧化硫发生反应生成硫化氢和氮氧化物,再通过氧化反应生成硫酸和氮气,最终实现脱硫的目的。
氨法脱硫技术具有高效、节能、无废水排放等优点,是目前较为成熟的脱硫技术之一。
电除尘器是利用高压电场对烟气中的颗粒物进行电除尘,将其带电并沉积在集尘电极上,然后定期清理。
电除尘器具有除尘效率高、结构简单、运行稳定等优点,但对烟气温度、湿度等要求较高。
布袋除尘器是利用滤料对烟气中的颗粒物进行过滤,将其截留在滤袋表面,最终通过清灰系统将其清除。
布袋除尘器适用于处理高温、高湿、高粘度的烟气,能够有效地去除细小颗粒物。
湿法静电除尘器是将烟气通过喷水器进行湿化处理,使其与静电场产生作用,将颗粒物带电并沉淀下来,达到除尘的效果。
湿法静电除尘器能够有效地降低烟气温度和粉尘爆炸的隐患,是一种较为安全的除尘设备。
玻璃熔窑烟气治理中脱硫除尘脱硝技术的应用

玻璃熔窑烟气治理中脱硫除尘脱硝技术的应用一、玻璃熔窑烟气中有害物质的主要成分玻璃熔窑在生产过程中,熔化原料需要高温,使得烟气中产生大量的有害物质。
主要包括二氧化硫、颗粒物和氮氧化物等。
这些有害物质一旦排放到大气中,会对周围的环境造成污染,危害周围居民的健康。
二、脱硫技术在玻璃熔窑烟气治理中的应用1. 石膏法脱硫技术石膏法是目前应用最广泛的烟气脱硫技术之一,在玻璃熔窑烟气治理中也得到了广泛应用。
该技术主要是通过喷射石膏浆液或悬浮石膏颗粒在烟气中,使二氧化硫与石膏中的氢氧化钙发生反应生成硫酸钙结晶,达到脱除二氧化硫的目的。
石膏法脱硫技术具有脱硫效率高、操作稳定等优点,能够有效降低玻璃熔窑烟气中二氧化硫的排放浓度。
三、除尘技术在玻璃熔窑烟气治理中的应用1. 电除尘技术电除尘技术是一种常用的烟气除尘技术,它主要是利用电场作用将烟气中的颗粒物带电后收集在导电板上,达到除尘的目的。
在玻璃熔窑烟气治理中,电除尘技术能有效降低烟气中颗粒物的排放浓度,净化烟气,保护环境。
四、脱硝技术在玻璃熔窑烟气治理中的应用氮氧化物是烟气中的另一种重要污染物,它会对环境和人体健康造成危害。
在玻璃熔窑烟气治理中,采用脱硝技术对氮氧化物进行处理至关重要。
1. 尿素还原脱硝技术尿素还原脱硝技术是目前应用最广泛的烟气脱硝技术之一,其原理是在高温下将尿素喷入烟气中与氮氧化物发生还原反应,生成氮气和水,达到脱除氮氧化物的目的。
尿素还原脱硝技术在玻璃熔窑烟气治理中广泛应用,其脱硝效率高,操作稳定,成本低廉,受到了广泛关注和好评。
2. SCR技术SCR技术是一种基于催化剂的氮氧化物脱除技术,它通过将氨水喷入烟气中,在SCR 催化剂的作用下将氮氧化物转化为氮气和水,达到脱硝的目的。
SCR技术在玻璃熔窑烟气治理中也得到了一定的应用,其脱硝效率高,对烟气中的氮氧化物有良好的去除效果。
五、玻璃熔窑烟气治理中脱硫除尘脱硝技术的应用效果通过脱硫除尘脱硝技术的应用,玻璃熔窑烟气中的二氧化硫、颗粒物和氮氧化物等有害物质得到了有效去除,排放浓度大幅降低,达到了环保要求。
玻璃窑炉烟气综合治理工艺选择及其方案
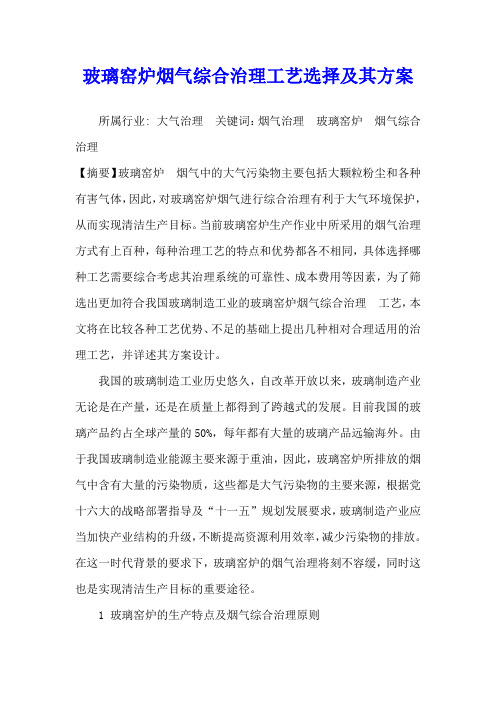
玻璃窑炉烟气综合治理工艺选择及其方案所属行业: 大气治理关键词:烟气治理玻璃窑炉烟气综合治理【摘要】玻璃窑炉烟气中的大气污染物主要包括大颗粒粉尘和各种有害气体,因此,对玻璃窑炉烟气进行综合治理有利于大气环境保护,从而实现清洁生产目标。
当前玻璃窑炉生产作业中所采用的烟气治理方式有上百种,每种治理工艺的特点和优势都各不相同,具体选择哪种工艺需要综合考虑其治理系统的可靠性、成本费用等因素,为了筛选出更加符合我国玻璃制造工业的玻璃窑炉烟气综合治理工艺,本文将在比较各种工艺优势、不足的基础上提出几种相对合理适用的治理工艺,并详述其方案设计。
我国的玻璃制造工业历史悠久,自改革开放以来,玻璃制造产业无论是在产量,还是在质量上都得到了跨越式的发展。
目前我国的玻璃产品约占全球产量的50%,每年都有大量的玻璃产品远输海外。
由于我国玻璃制造业能源主要来源于重油,因此,玻璃窑炉所排放的烟气中含有大量的污染物质,这些都是大气污染物的主要来源,根据党十六大的战略部署指导及“十一五”规划发展要求,玻璃制造产业应当加快产业结构的升级,不断提高资源利用效率,减少污染物的排放。
在这一时代背景的要求下,玻璃窑炉的烟气治理将刻不容缓,同时这也是实现清洁生产目标的重要途径。
1 玻璃窑炉的生产特点及烟气综合治理原则在选择合理有效的玻璃窑炉烟气综合治理工艺之前,首先要考虑玻璃窑炉的生产特点及烟气综合治理原则,只有把握以上两点才能确保筛选出来的烟气综合治理工艺符合我国实际生产及环境标准的要求。
1.1 玻璃窑炉生产运行特点玻璃窑炉的生产运行特点主要表现为以下几点:(1)玻璃的生产制造一般采用持续、不间断的生产方式,这种流水线式的生产方法决定了玻璃窑炉的持续性运转特点;(2)玻璃窑炉是玻璃生产制造流程的重要环节,同时也是能源消耗的主要设备,而且我国目前所普遍采用的火焰炉融化率、能耗水平都远远低于国际标准[1];(3)玻璃窑炉的正常作业需要保持一定的燃烧气氛,否则将直接影响燃烧效果导致玻璃产品质量不合格,同时还有可能发生意外污染事故;(4)玻璃窑炉所排放的烟气需要经过余热锅炉的回收处理,用以供油系统的生产,烟气排放温度较高。
浮法玻璃熔窑中废气排放与脱硫技术综述

浮法玻璃熔窑中废气排放与脱硫技术综述浮法玻璃熔窑是玻璃制造过程中的重要环节,它不仅产生了大量的废气排放,还会释放出有害物质,对环境和人类健康产生潜在风险。
因此,研究和应用有效的废气排放与脱硫技术对保护环境和减少污染具有重要意义。
浮法玻璃熔窑中的废气排放主要包括烟气和废气两种类型。
烟气是熔窑中玻璃原料燃烧时产生的气体,其中含有的一氧化碳、二氧化硫、氮氧化物等对环境和健康有害。
废气是熔窑中被燃料和原料中的杂质以及玻璃的氧化还原反应产生的气体。
为了减少浮法玻璃熔窑中的废气排放对环境的危害,一些常见的废气排放与脱硫技术被提出并广泛应用。
其中,常见的废气处理方法包括烟气净化和废气处理两个方面。
对于烟气净化,常见的技术包括除尘、脱硫和脱氮等。
除尘是目前最常用的废气处理技术之一,常用的方法有静电除尘和布袋除尘等。
静电除尘利用静电力和气流力作用,将颗粒粉尘从烟气中分离出来,达到净化的效果。
布袋除尘则是将烟气通过纤维过滤袋,在滤袋上沉积颗粒粉尘,使净化后的气体通过。
脱硫和脱氮是为了去除烟气中的硫化物和氮氧化物等对环境和健康有害的物质。
常见的脱硫技术包括湿法脱硫和干法脱硫等,湿法脱硫利用吸收剂与烟气中的SO2发生化学反应,将SO2转化为可溶性的化合物而使其得到去除。
干法脱硫则是基于吸附剂吸附和化学吸收的原理,将烟气中的SO2转化为可溶性的化合物。
对于脱氮技术,常见的方法有选择性催化还原和选择性非催化还原等。
除了烟气净化,废气处理也是降低浮法玻璃熔窑废气排放对环境的影响的重要手段。
常见的废气处理技术包括高温燃烧、余热回收和再利用等。
高温燃烧是将废气引入燃烧炉内,在高温下进行燃烧分解,将有机废气转化为无害的二氧化碳和水蒸气等,从而实现净化的效果。
余热回收和再利用是将熔窑中排放的高温废气通过换热器进行余热回收,用于加热玻璃熔池等工序,以减少能源消耗和废气排放。
除了上述技术,还有一些新兴的废气排放与脱硫技术应用在浮法玻璃熔窑中,以进一步提高废气处理效果。
玻璃熔窑烟气治理中脱硫除尘脱硝技术的应用
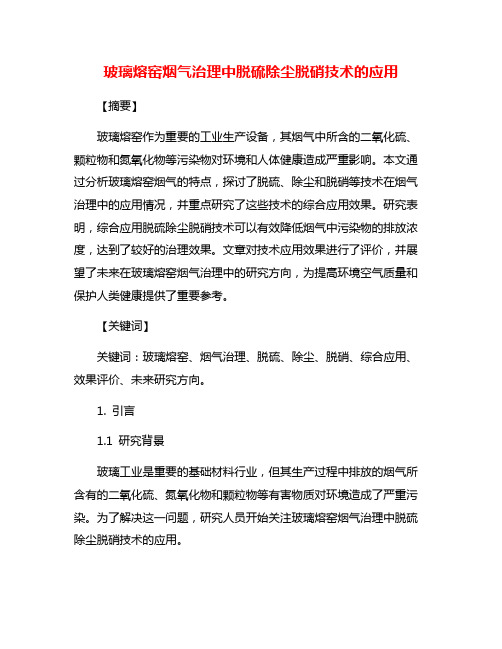
玻璃熔窑烟气治理中脱硫除尘脱硝技术的应用【摘要】玻璃熔窑作为重要的工业生产设备,其烟气中所含的二氧化硫、颗粒物和氮氧化物等污染物对环境和人体健康造成严重影响。
本文通过分析玻璃熔窑烟气的特点,探讨了脱硫、除尘和脱硝等技术在烟气治理中的应用情况,并重点研究了这些技术的综合应用效果。
研究表明,综合应用脱硫除尘脱硝技术可以有效降低烟气中污染物的排放浓度,达到了较好的治理效果。
文章对技术应用效果进行了评价,并展望了未来在玻璃熔窑烟气治理中的研究方向,为提高环境空气质量和保护人类健康提供了重要参考。
【关键词】关键词:玻璃熔窑、烟气治理、脱硫、除尘、脱硝、综合应用、效果评价、未来研究方向。
1. 引言1.1 研究背景玻璃工业是重要的基础材料行业,但其生产过程中排放的烟气所含有的二氧化硫、氮氧化物和颗粒物等有害物质对环境造成了严重污染。
为了解决这一问题,研究人员开始关注玻璃熔窑烟气治理中脱硫除尘脱硝技术的应用。
在过去的研究中,玻璃熔窑烟气的处理往往只注重其中一种有害物质的治理,而忽略了其他有害物质的排放。
开展综合应用技术研究,实现对多种有害物质同时进行控制,显得尤为重要。
随着环保意识的增强和法律法规的不断完善,对玻璃熔窑烟气排放标准的要求也越来越严格,传统的治理技术已经不能满足要求,因此需要不断探索新的治理技术和方法。
开展玻璃熔窑烟气治理中脱硫除尘脱硝技术的应用研究,对降低玻璃行业的环境污染、改善大气质量具有重要意义。
内容到此结束。
1.2 研究意义研究玻璃熔窑烟气治理中脱硫除尘脱硝技术的应用具有重要的意义。
玻璃熔窑作为工业生产过程中的重要环节,其烟气排放中含有大量的有害物质,对环境和人体健康造成严重影响。
通过引入脱硫、除尘、脱硝等技术来降低烟气中有害物质的排放,不仅可以保护环境,改善空气质量,还能有效减少对人体的危害,提高生产过程中的安全性和健康性。
玻璃熔窑烟气治理技术的研究和应用,对我国玻璃工业的可持续发展具有重要意义。
玻璃熔窑余热烟气利用技术
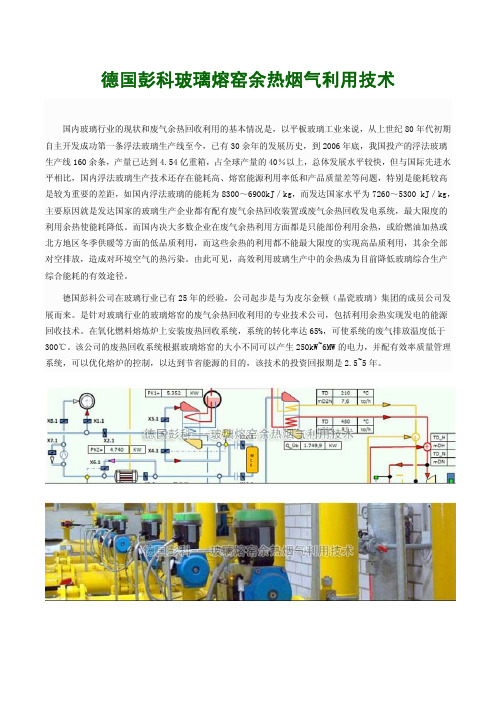
德国彭科玻璃熔窑余热烟气利用技术国内玻璃行业的现状和废气余热回收利用的基本情况是,以平板玻璃工业来说,从上世纪80年代初期自主开发成功第一条浮法玻璃生产线至今,已有30余年的发展历史,到2006年底,我国投产的浮法玻璃生产线160余条,产量已达到4.54亿重箱,占全球产量的40%以上,总体发展水平较快,但与国际先进水平相比,国内浮法玻璃生产技术还存在能耗高、熔窑能源利用率低和产品质量差等问题,特别是能耗较高是较为重要的差距,如国内浮法玻璃的能耗为8300~6900kJ/kg,而发达国家水平为7260~5300 kJ/kg,主要原因就是发达国家的玻璃生产企业都有配有废气余热回收装置或废气余热回收发电系统,最大限度的利用余热使能耗降低。
而国内决大多数企业在废气余热利用方面都是只能部份利用余热,或给燃油加热或北方地区冬季供暖等方面的低品质利用,而这些余热的利用都不能最大限度的实现高品质利用,其余全部对空排放,造成对环境空气的热污染。
由此可见,高效利用玻璃生产中的余热成为目前降低玻璃综合生产综合能耗的有效途径。
德国彭科公司在玻璃行业已有25年的经验,公司起步是与为皮尔金顿(晶瓷玻璃)集团的成员公司发展而来。
是针对玻璃行业的玻璃熔窑的废气余热回收利用的专业技术公司,包括利用余热实现发电的能源回收技术。
在氧化燃料熔炼炉上安装废热回收系统,系统的转化率达65%,可使系统的废气排放温度低于300℃。
该公司的废热回收系统根据玻璃熔窑的大小不同可以产生250kW~6MW的电力,并配有效率质量管理系统,可以优化熔炉的控制,以达到节省能源的目的,该技术的投资回报期是2.5~5年。
该公司的产品主要包括4类:1.废热回收系统(WHR)在玻璃生产行业(浮法玻璃和瓶罐玻璃)在氧化燃料熔炼炉上安装废热回收系统,系统的转化率高达65%,优于其他同类技术产品,一般投资回报期是2.5~5年,能源效率值达到25%;过硬的系统技术,以及可以实现较低为废气温度(低于300℃),废热回收系统的利用时间可以达到98%以上。
玻璃窑炉烟气综合治理技术
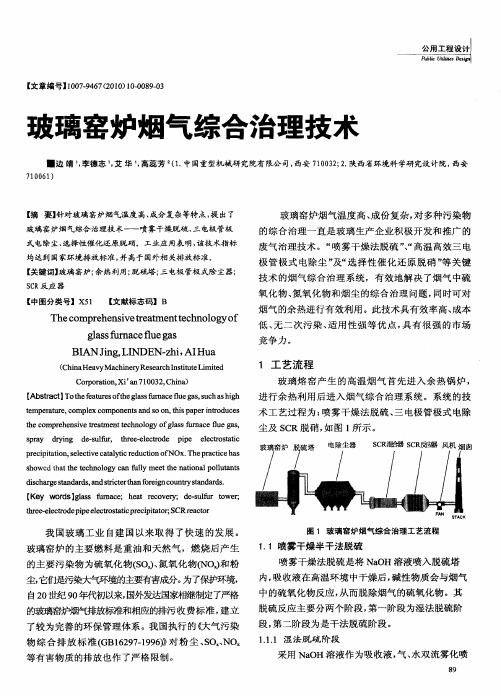
式电除尘、 选择性催化还原脱硝 。工业应用表 明, 该技术指标
均达到 国家环境排放标准 , 高于国外相 关排放标 准。 并 【 关键词】 玻璃 窑炉; 热利用 ; 余 脱硫塔; 电极 管极 式除尘器; 三
公用工程设计I
Pu l b/ c Ⅱt s /e i s
I
【 章 编 号 】0 79 6 (0 0 1.0 90 文 10 .4 72 1) 00 8 —3
玻璃 窑炉烟气 综合治理技术
一 边 靖 李德志 ,艾 华 高蕊芳 (. , , , 1 中国重型机械研 究院有限公 司, 西安 7 0 3; . 1 0 2 2 陕西省环境科学研究设计院 , 西安
【 e w rs gas un c;h a rcvr;d- l r twe; K y od ]ls rae et eo e f y es f o r uu
t r e ee to e i e l to tt p e i i t r S h e - lcr d p p e e r s i r c ̄ t o ; CRr a tr c a c I a e co
进 行 余 热 利用 后进 入 烟 气综 合 治 理系 统 。系统 的技 术 工 艺 过程 为 : 雾 干燥 法 脱硫 、 电极 管 极式 电除 喷 三 尘及 S R脱硝 , 图 1 示 。 C 如 所
囱
【 src】 oh a rs f e l sun c u ssc g Ab t t T eet e t a rae e a,uh s i a t f u oh g sf l f g ah h
浮法玻璃退火窑的废气净化与减排技术

浮法玻璃退火窑的废气净化与减排技术浮法玻璃生产是目前全球主流的大规模玻璃生产工艺之一,它能够高效地生产出大面积、高质量的玻璃。
然而,浮法玻璃生产过程中产生的废气对环境造成了很大的负担,需要采取有效的净化与减排技术来保护环境。
一、废气的组成与排放特点浮法玻璃生产过程中,废气的主要组成成分包括氮氧化物、二氧化硫、颗粒物等。
其中,氮氧化物主要是由燃料燃烧产生,其排放浓度较高;二氧化硫主要是由燃料中的硫含量和原料中的硫化物产生;颗粒物则是由玻璃窑炉燃烧和玻璃材料熔化过程中的挥发物以及废气中的固体颗粒物组成。
这些废气排放中含有的有害物质对环境和人体健康都有不良影响。
二、废气净化技术1. 喷射吸附净化技术喷射吸附净化技术是一种常见的废气净化技术,它通过喷射吸收剂将废气中的污染物吸附到吸收剂上,达到净化的目的。
在浮法玻璃退火窑的废气净化中,可以采用活性炭、吸附脱硝剂等吸附剂来吸附废气中的氮氧化物和二氧化硫。
2. 湿式洗涤净化技术湿式洗涤净化技术是一种利用水或液体吸收剂将废气中的污染物溶解或吸附的净化技术。
在浮法玻璃退火窑的废气净化中,可以采用碱液洗涤技术将废气中的二氧化硫洗涤出来。
3. 直接吸附净化技术直接吸附技术是指将废气中的污染物直接吸附到具有吸附能力的材料上,如活性炭、分子筛等。
这种技术简单、高效,适合浮法玻璃退火窑废气净化中颗粒物的处理。
4. 表面复合催化剂技术表面复合催化剂技术是指采用特殊催化剂将废气中的污染物催化转化为无害物质。
这种技术可同时处理废气中氮氧化物和二氧化硫。
三、废气减排技术除了采取废气净化技术外,还可以采取废气减排技术来降低废气的排放量。
1. 高效燃烧技术采用高效燃烧技术可以提高燃料的利用率,减少废气中的氮氧化物排放。
例如,采用预混燃烧技术,将燃料与空气进行充分混合燃烧,可以降低燃烧温度,减少氮氧化物的生成。
2. 氧燃烧技术采用氧燃烧技术可以将空气中的氮氧化物排放量降低到极低水平。
通过提供高纯度的氧气进行燃烧,可以有效减少氮氧化物的生成。
玻璃窑炉烟气脱硫脱硝技术精品PPT课件

34
烟气中NOx产生主要来源于三方面: 1.原料中少量硝酸盐分解。 2.燃料中含氮物质的燃烧 3.空气中氮的燃烧,即热力型NOx。这是最主要的生成方式 玻璃窑炉废气中的NOx,初始90%一95%为NO,但在排放
过程中,随着温度的下降而逐渐转化为NO2
35
燃烧中控制
燃料调节技术 氧气、燃料燃烧技术
(5)
2SO32-+O2→2SO42-
(6)
26
MgO+SO2→MgSO3
(7)
2NaOH+SO3→Na2SO4+H2O
(8)
2 CaSO3+O2→CaSO3
(9)
2 CaSO3+O2 → 2 CaSO4
(10)
2 MgSO3+ →2 MgSO4
(11)
27
1、环境治理效果显著 1)脱硫工艺简单、效果较好。采用间断高效喷氨法,经
目前商业上应用比较广泛的是运行温度处于 280℃~420℃的中温催化剂,以TiO2为载体,上面 负载钒、钨和钼等主催化剂或助催化剂。其反应式 为: 4NH3+4NO+O2=6H2O 8NH3+6NO2=7N2+12H2O 4NH3+2NO2+O2=3N2+6H2O
39
工艺过程: 在催化剂作用下,向温度约280℃~420℃的烟气中
简称FGD)技术
5
脱硫技术分类
按
抛弃法 脱硫混合物
脱
直接排放
按
硫
脱
产
硫
物
剂
是
种
否
类
回
划
收
再生法 脱硫副产物
分
璃窑炉烟气综合治理的工艺选择

璃窑炉烟气综合治理的工艺选择摘要:近两年,国家环保要求的提高,玻璃窑炉也进入了脱硝快车道,现部分玻璃生产企业已陆续安装了SCR脱硝装置。
根据玻璃窑炉脱硝工程经验及各种工艺的了解,对比各种工艺,为后期项目实施提出参考。
关键词:玻璃窑、SCR工艺、玻璃窑灰分、工艺布置Abstract:The past two years,With the Country environmental requirements increased,glass kilns entered the fast lane of denitrification. Now part of the glass manufacturers have been gradually installed SCR denitration devices. According the engineering experience of glass kilns denitrification and the understanding of various process,comparison of the different techniques,made reference to the late implementation of the project.Keywords:Glass kilns;SCR process;Glass kiln ash;Process layout.随着国家对环境保护标准的不断提高,“十二五”期间,NOx首次列入约束性指标体系。
今年,全国各地除在火电上提出了严格要求和整改期限,在水泥、玻璃等建材行业同样受到环保部门的重视。
在平板玻璃行业,部分厂家已经安装了SCR脱硝装置,效果达到《平板玻璃工业大气污染物排放标准》GB26453-2011要求。
但由于玻璃行业整体的低迷,脱硝减排工作也受到一定的影响。
现有必要玻璃行业脱硝技术的分析比较和沉淀总结。
玻璃熔窑烟气治理中脱硫除尘脱硝技术的应用
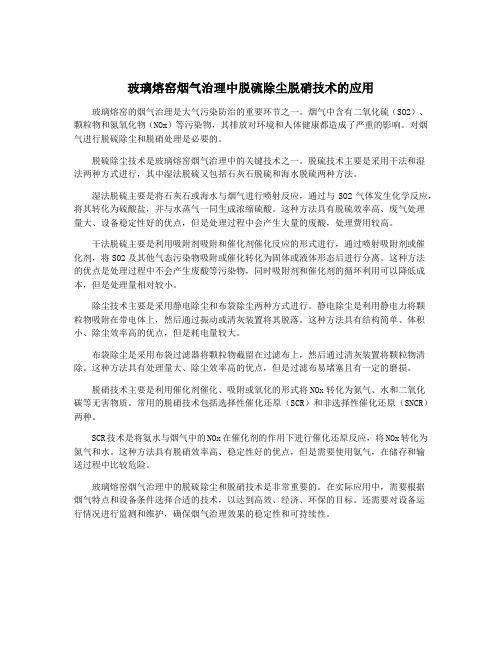
玻璃熔窑烟气治理中脱硫除尘脱硝技术的应用玻璃熔窑的烟气治理是大气污染防治的重要环节之一。
烟气中含有二氧化硫(SO2)、颗粒物和氮氧化物(NOx)等污染物,其排放对环境和人体健康都造成了严重的影响。
对烟气进行脱硫除尘和脱硝处理是必要的。
脱硫除尘技术是玻璃熔窑烟气治理中的关键技术之一。
脱硫技术主要是采用干法和湿法两种方式进行,其中湿法脱硫又包括石灰石脱硫和海水脱硫两种方法。
湿法脱硫主要是将石灰石或海水与烟气进行喷射反应,通过与SO2气体发生化学反应,将其转化为硫酸盐,并与水蒸气一同生成浓缩硫酸。
这种方法具有脱硫效率高、废气处理量大、设备稳定性好的优点,但是处理过程中会产生大量的废酸,处理费用较高。
干法脱硫主要是利用吸附剂吸附和催化剂催化反应的形式进行,通过喷射吸附剂或催化剂,将SO2及其他气态污染物吸附或催化转化为固体或液体形态后进行分离。
这种方法的优点是处理过程中不会产生废酸等污染物,同时吸附剂和催化剂的循环利用可以降低成本,但是处理量相对较小。
除尘技术主要是采用静电除尘和布袋除尘两种方式进行。
静电除尘是利用静电力将颗粒物吸附在带电体上,然后通过振动或清灰装置将其脱落。
这种方法具有结构简单、体积小、除尘效率高的优点,但是耗电量较大。
布袋除尘是采用布袋过滤器将颗粒物截留在过滤布上,然后通过清灰装置将颗粒物清除。
这种方法具有处理量大、除尘效率高的优点,但是过滤布易堵塞且有一定的磨损。
脱硝技术主要是利用催化剂催化、吸附或氧化的形式将NOx转化为氮气、水和二氧化碳等无害物质。
常用的脱硝技术包括选择性催化还原(SCR)和非选择性催化还原(SNCR)两种。
SCR技术是将氨水与烟气中的NOx在催化剂的作用下进行催化还原反应,将NOx转化为氮气和水。
这种方法具有脱硝效率高、稳定性好的优点,但是需要使用氨气,在储存和输送过程中比较危险。
玻璃熔窑烟气治理中的脱硫除尘和脱硝技术是非常重要的。
在实际应用中,需要根据烟气特点和设备条件选择合适的技术,以达到高效、经济、环保的目标。
玻璃烟气综合治理工艺分析
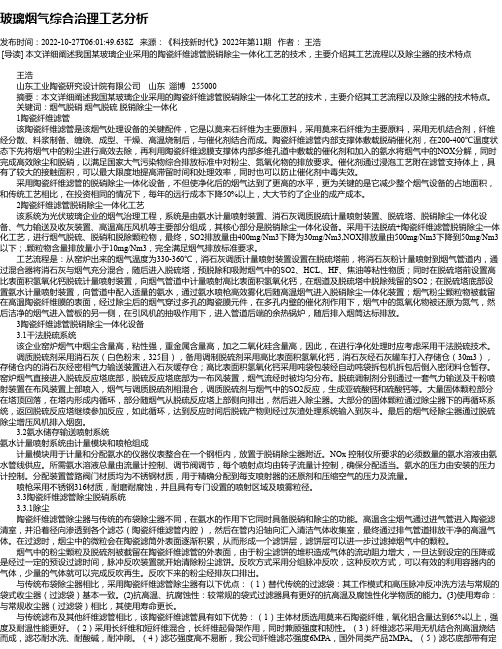
玻璃烟气综合治理工艺分析发布时间:2022-10-27T06:01:49.638Z 来源:《科技新时代》2022年第11期作者:王浩[导读] 本文详细阐述我国某玻璃企业采用的陶瓷纤维滤管脱硝除尘一体化工艺的技术,主要介绍其工艺流程以及除尘器的技术特点王浩山东工业陶瓷研究设计院有限公司山东淄博 255000摘要:本文详细阐述我国某玻璃企业采用的陶瓷纤维滤管脱硝除尘一体化工艺的技术,主要介绍其工艺流程以及除尘器的技术特点。
关键词:烟气脱硝烟气脱硫脱销除尘一体化1陶瓷纤维滤管该陶瓷纤维滤管是该烟气处理设备的关键配件,它是以莫来石纤维为主要原料,采用莫来石纤维为主要原料,采用无机结合剂,纤维经分散、料浆制备、缠绕、成型、干燥、高温烧制后,与催化剂结合而成。
陶瓷纤维滤管内部支撑体敷载脱硝催化剂,在200-400℃温度状态下先将烟气中的粉尘进行高效去除,再利用陶瓷纤维滤膜支撑体内部多维孔道中敷载的催化剂和加入的氨水将烟气中的NOX分解,同时完成高效除尘和脱硝,以满足国家大气污染物综合排放标准中对粉尘、氮氧化物的排放要求。
催化剂通过浸泡工艺附在滤管支持体上,具有了较大的接触面积,可以最大限度地提高滞留时间和处理效率,同时也可以防止催化剂中毒失效。
采用陶瓷纤维滤管的脱硝除尘一体化设备,不但使净化后的烟气达到了更高的水平,更为关键的是它减少整个烟气设备的占地面积,和传统工艺相比,在投资相同的情况下,每年的远行成本下降50%以上,大大节约了企业的成产成本。
2陶瓷纤维滤管脱硝除尘一体化工艺该系统为光伏玻璃企业的烟气治理工程,系统是由氨水计量喷射装置、消石灰调质脱硫计量喷射装置、脱硫塔、脱硝除尘一体化设备、气力输送及收灰装置、高温高压风机等主要部分组成,其核心部分是脱销除尘一体化设备。
采用干法脱硫+陶瓷纤维滤管脱销除尘一体化工艺,进行烟气脱硫、脱硝和脱除颗粒物,最终,SO2排放量由400mg/Nm3下降为30mg/Nm3,NOX排放量由500mg/Nm3下降到50mg/Nm3以下;,颗粒物含量排放量小于10mg/Nm3,完全满足烟气排放标准要求。
玻璃窑炉烟气综合净化工艺[发明专利]
![玻璃窑炉烟气综合净化工艺[发明专利]](https://img.taocdn.com/s3/m/02835a9901f69e3142329468.png)
专利名称:玻璃窑炉烟气综合净化工艺
专利类型:发明专利
发明人:周永信,宋海农,杨崎峰,陆立海,詹馥蔓,王爱,黄宣宣,杨长钫,覃海涛,黄山
申请号:CN201510407816.0
申请日:20150713
公开号:CN104984640A
公开日:
20151021
专利内容由知识产权出版社提供
摘要:本发明公开了一种玻璃窑炉烟气综合净化工艺,它的工艺流程是:将玻璃窑炉产生的高温烟气流经余热锅炉进行余热回收,在余热锅炉380~420℃温度段将烟气引入高温电除尘器系统进行高温烟气除尘处理,并使除尘达标后的烟气温度降至350~400℃,以满足SCR脱硝催化剂最佳活性温度要求,再将除尘烟气引入到SCR脱硝系统中进行NO的脱除,将脱硝后的烟气引回到余热锅炉中继续进行余热回收,待余热锅炉内的烟气温度降至170~180℃时将烟气引入半干法脱硫系统,使脱硫处理后的达标烟气降至140~160℃后经烟囱排入大气环境中。
经本发明工艺处理后的玻璃窑炉烟气粉尘排放浓度低于50mg/m,NO排放浓度低于700mg/m,SO排放浓度低于400mg/m,达到玻璃行业相关国家环保排放标准的规定。
申请人:广西博世科环保科技股份有限公司
地址:530007 广西壮族自治区南宁市高新区科兴路12号
国籍:CN
代理机构:广西南宁公平专利事务所有限责任公司
代理人:刘小萍
更多信息请下载全文后查看。
玻璃熔窑高硼烟气处理技术综述-化工论文-化学论文

玻璃熔窑高硼烟气处理技术综述-化工论文-化学论文——文章均为WORD文档,下载后可直接编辑使用亦可打印——1 引言随着工业技术的发展和社会的进步,重视节能和环保成为玻璃企业的共识,为此,玻璃行业在节能上做出了各种努力[1].由于富氧燃烧具有节能与环保双重优点,天然气富氧燃烧技术在玻璃行业逐步得到广泛应用。
玻璃熔窑采用天然气富氧燃烧,氧含量每增加1%,理论燃烧温度提高约60 ℃,烟气量平均约减少3% ,排放的烟气含尘浓度低于50 mg / Nm3,SO2浓度小于400 mg/Nm3[2].硼氧化物(B2O3)具有增加玻璃低温黏度、降低高温黏度的作用,还有很高的热吸收系数和质量吸收系数,玻璃生产中通过添加硼元素生产高硼硅酸盐玻璃[3].高硼硅酸盐玻璃具有优良的化学稳定性、较低的热膨胀系数和良好的机械性能[4-6],已经广泛地应用在精密光电领域和药用玻管管制瓶领域。
但是,由于玻璃熔窑内的高温导致B2O3挥发,B2O3挥发不仅会消耗大量的原料,降低玻璃的质量,同时还对炉窑有很大的侵蚀,缩短炉窑的使用寿命[7,8].硼氧化物随烟气排放到环境中,会与空气中的水反应生成硼酸产生酸雨,对环境造成污染。
烟气中含有的大量B2O3会造成烟气较高,易产生结露现象而糊袋,增加了工程处理难度。
为此,国内外对玻璃熔窑含硼烟气处理成为热点。
本文针对含硼烟气源头减量技术、处理干扰因素和处理技术的优点与不足进行分析,为玻璃行业高硼烟气处理技术的研究和技术发展方向提供参考。
2 含硼烟气源头减量技术玻璃熔窑烟气中硼化物来源于投加的硼砂原料,高硼玻璃配合料中硼化物的化学组成一般为11% ~15% (质量比).氧化硼熔点为450 ℃ ,在低温下容易挥发。
刘小青等[9]采用差热分析(DSC)和热重分析(TG)进行配合料升温失重研究,结果表明硼酸转变为硼化物是一个逐步脱水的过程。
在69 ~100 ℃范围内H3BO3逐渐脱水成为HBO2,100 ~231 ℃范围内HBO2进一步脱水成为H2B4O7,231 ~320 ℃范围内H2B4O7最终脱水成为B2O3.在玻璃熔窑1000 ℃高温作用下,玻璃配合料中B2O3挥发率为8. 9% ~12. 78%,挥发的B2O3成为玻璃熔窑烟气中硼化物的源头[7].也有多位学者对B2O3挥发的机理和影响因素展开研究[10],以期在源头减少玻璃熔制排放烟气中B2O3的量。
玻璃窑炉烟气净化方法的选择与实例说明

玻璃窑炉烟气净化方法的选择与实例说明
郑鸿
【期刊名称】《能源与环境》
【年(卷),期】2009(000)002
【摘要】介绍玻璃窑炉烟气净化方法并以实例说明其技术设计特点,对其进展及应用前景进行分析.
【总页数】2页(P85-86)
【作者】郑鸿
【作者单位】福建省丰泉环保控股有限公司,福建福州,350007
【正文语种】中文
【中图分类】X701.3
【相关文献】
1.玻璃窑炉烟气综合治理的工艺选择与方案设计 [J], 陈学功;尹海滨
2.铝用阳极焙烧烟气净化方法探讨 [J], 余宏伟;赵倩倩
3.选择性催化还原法烟气脱硝系统改造实例分析 [J], 陈安新;张军梅
4.循环流化床锅炉烟气脱硝工艺的选择实例 [J], 王连庆
5.玻璃窑炉烟气综合治理的工艺选择 [J], 陈学功;尹海滨;
因版权原因,仅展示原文概要,查看原文内容请购买。
- 1、下载文档前请自行甄别文档内容的完整性,平台不提供额外的编辑、内容补充、找答案等附加服务。
- 2、"仅部分预览"的文档,不可在线预览部分如存在完整性等问题,可反馈申请退款(可完整预览的文档不适用该条件!)。
- 3、如文档侵犯您的权益,请联系客服反馈,我们会尽快为您处理(人工客服工作时间:9:00-18:30)。
三、玻璃窑炉PM2.5、SO2、NOX脱除技术
3.1干式高温电除尘器系统技术
燃用劣质石油焦时,粉尘特性: 强腐蚀性、强吸湿性、强粘性、低比电阻,易二次飞扬
根据古越龙山燃用石油焦项目的实施、改造提效,初步结论与原则:
二电场配置,初始电除尘效率还不错,粉尘排放40~120mg/Nm3左右,但 运行一段时间后,除尘效率会下降,定时冲洗清洗效果不错,反应器旁路的 必要性。 二电场配置,经烟气调质处理,运行稳定性提高及粉尘排放有明显降低, 粉尘排放可达到40~70mg/Nm3。 要达到20~50mg/Nm3的粉尘排放,宜设计3~4个电场,确保低排放稳定运 行。
二、技术研发及成果
5.3万m3/y中温脱硝催化剂生产装置
三、玻璃窑炉PM2.5、SO2、NOX脱除技术
3.1干式高温电除尘器系统技术
燃用石油焦时,玻璃窑炉高温粉尘理化物性(低PH值)
对除尘、脱硝设备结构件的腐蚀严重,降低催化剂的机械稳定性能
三、玻璃窑炉PM2.5、SO2、NOX脱除技术
3.1干式高温电除尘器系统技术
三、玻璃窑炉PM2.5、SO2、NOX脱除技术
玻璃烟气脱硝催化剂选型应考虑: 工况波动 物理性堵塞 化学性失活 燃料变化 燃料特殊性
玻璃炉窑初始NOX浓度高达2500~10000mg/Nm3、微细尘量大且粘性强、碱金 属浓度高,SO3含量高,特别当采用石油焦作燃料,除尘器效果欠佳时,催化 剂用量应有足够的裕量,该工况时,使用寿命仅为火电厂的1/3~4/5;电除尘器 的选型、裕量、运行稳定性、维护质量极大影响催化剂的实际使用寿命。
三、玻璃窑炉PM2.5、SO2、NOX脱除技术
3.1干式高温电除尘器系统技术
燃用石油焦时,电除尘器入口粉尘与灰斗粉尘比电阻比较
三、玻璃窑炉PM2.5、SO2、NOX脱除技术
3.1干式高温电除尘器系统技术
燃用石油焦时,不同位置取样粉尘的烧失量。有机物高。
未燃尽的高分子有机物含量高,也是造成该粉尘粘性强的原因之一
三、玻璃窑炉PM2.5、SO2、NOX脱除技术
3.1干式高温电除尘器系统技术
燃用劣质石油焦时,粉尘中SO3高,造成粘性及强腐蚀
三、玻璃窑炉PM2.5、SO2、NOX脱除技术
3.2烟气脱硫技术-氨法脱硫技术
左二图为山东齐鲁石 化2×135MW氨法脱 硫图片 左二图为杭州钢铁厂 氨法脱硫图片 设计或操作不合理造 成的“气溶胶”二次污 染,造成周围环境很 恶劣,腐蚀极严重。
适宜于SO2浓度0~10000mg/Nm3,脱硫效率95%~99%,脱硫温度50℃ 左右,吸收塔与烟囱一体式设计是经济的方案,有少量废水,布置在引 风机之后。
三、玻璃窑炉PM2.5、SO2、NOX脱除技术
3.3选择性催化还原脱硝(SCR)系统流程示意图
300℃ ~420 ℃
三、玻璃窑炉PM2.5、SO2、NOX脱除技术
一、玻璃窑炉污染物特征、污染现状及相关政策
污染物特征、污染现状
辽宁中部 京津冀 山东半岛 长三角 珠三角 海峡西岸 武汉周边 长株潭 成渝地区
河北、广东、山东等地区玻璃炉窑集中,PM2.5、NOX污染物排放强度大
一、玻璃窑炉污染物特征、污染现状及相关政策
玻璃窑炉烟气的特征 PM2.5: 300~900mg/Nm3 NOX : 3000~10000mg/Nm3 SO2: 300~3500mg/Nm3
9.69% 3.76% 3.82% 2.96% 5.72%
SO3
46.42%
Na2O
12.56%
MgO
2.4%
P2O5
0.61%
K2O
0.66%
As2O5
0.04%
SiO2
10.45%
累计
100%
上图:燃用石油焦玻璃烟气中粉尘
成份分析
一、玻璃窑炉污染物特征、污染现状及相关政策
V2O5是SO2
V2O5 SO3
一、玻璃窑炉污染物特征、污染现状及相关政策
燃用石油焦玻璃烟气高温除尘及SCR脱硝的技术难题
如何解决因粘性粉尘在瓷套内的附着导致的瓷套炸裂? 如何解决因粉尘粘结在阴极线上造成的电晕封密、低电压/低电流、 火花过频、短路断电、电除尘器运行一段时间后效率下降难题? 如何解决高浓度SO3导致的ABS二次气溶胶污染难题?
剂表面会有严重的粘结。声波清灰+压缩空气吹灰藕合协同清灰方式效 果更佳,压缩空气中的水、油含量符合要求。
三、玻璃窑炉PM2.5、SO2、NOX脱除技术
4S.4C吹R灰系系统统组成及关键技术—吹灰器
采用过饱和蒸汽吹灰器具有很强的清灰效果,因蒸汽的喷入导致烟气湿度 增加,会增加灰的粘性、加剧局部高浓度H2SO4腐蚀、降低催化剂的结构稳 定性、降低催化剂使用寿命。在燃用石油焦粉工况时,不推荐使用。
如何解决粘性粉尘导致的排灰不畅难题? 如何解决粉尘附着在催化剂表面导致化学活性下降问题? 如何解决高SO3强氧化导致催化剂结构机械稳定性下降难题? 如何解决因粘性粉尘附着在催化剂表面导致运行阻力上升难题?
二、技术研发及成果
与浙江大学合作,5.3万m3/y中温SCR催化剂 SCR催化剂脱硝装置4个行业标准牵头起草单位 授予专利24项,发明专利4项,其中玻璃炉窑除尘、脱硝、脱硫专利9项。
三、玻璃窑炉PM2.5、SO2、NOX脱除技术
系统组成及关键技术— 催化剂的种类
蜂窝式,活性高、 表面积大,催化剂 用量小,性能稳定
板式,不锈钢骨架,适 宜于高尘环境,催化剂 用量稍大
波纹式,纤维基材, 适宜于低尘环境
玻璃窑炉脱硝常用催化剂为:锐钛型TiO2为载体,V2O5为活性组分,WO3 和MoO3为助剂的中温催化剂。
(有害)
300 ℃ ~420℃是“效率、安全、经济”平衡的选择。
三、玻璃窑炉PM2.5、SO2、NOX脱除技术
SCR脱硝反应机理
NH3 NH3
催化剂 催化剂
NOx NO
NOx
原烟气 NO 原烟气
NOx NO
NH3 NH3
NH3 NH3
NHБайду номын сангаас NH3
NOx NOx
NOx NOx
H2O H2O N2 N2
三、玻璃窑炉PM2.5、SO2、NOX脱除技术
3.2烟气脱硫技术-氨法脱硫技术
优势:
可实现SO2的资源化。SO2浓度高、且氨源廉价时。
劣势:
难以保障副产硫铵的稳定销路; 氨源廉价、易得; “气溶胶”二次污染; 设备、环境的腐蚀严重
玻璃窑炉烟气量小,除非工业园统筹考虑副产硫铵的集中处理,否则玻 璃烟气的脱硫技术应慎重选择氨法脱硫工艺。
SCR脱硝反应机理
还原剂:液氨、氨水、尿素
反应温度:300 ℃ ~420℃
主要反应式为:
4NO+4NH3 +O2 2NO2+4NH3+O2
催化剂 催化剂
4N2+6H2O 3N2+6H2O (有利)
主要副反应:4NH3+3O2
NH3+H2O+SO3 NH3+O2
2N2+6H2O
NH4HSO4 NOX+H20
一、玻璃窑炉污染物特征、污染现状及相关政策
燃用石油焦粉时,烟气及灰份特点
下图:石油焦成份分析
V2O5 Ni2O3 Fe2O3 Al2O3 CaO
TiO2 ZnO SO3 累计
4.01 % 1.22 % 0.75 % 0.16 % 0.23 % 0.58% 0.39% 92% 100%
V2O5 Ni2O3 Fe2O3 Al2O3 CaO
一、玻璃窑炉污染物特征、污染现状及相关政策
NO3-/SO42-值的升高,治理重点己从“硫污染”转向“硝污染”
一、玻璃窑炉污染物特征、污染现状及相关政策
污染物特征、污染现状
化工厂高浓度NOX污染
炼焦工序废气NOX污染 玻璃窑炉废气NOX污染
玻璃窑炉烟气量不大,但NOX污染物浓度高,对局部环境造成很大危害更大
三、玻璃窑炉PM2.5、SO2、NOX脱除技术
3.2烟气脱硫技术-干法/半干法烟气脱硫技术
包括烟道循环流化床(CFB)、喷雾半干法(SDA) 增湿循环半干法(NID、RSD、OH-CFB)等。
经济的SO2浓度低于3500mg/Nm3,入口烟气温度≥110℃,且≤180℃,脱 硫效率80%~95%,运行温度:70~95℃ ,钙硫比:1.1~1.5,包含袋式除尘 器的总运行阻力降:1800~3300Pa
三、玻璃窑炉PM2.5、SO2、NOX脱除技术
系统组成及关键技术—催化剂的失活
一、磨蚀、粉碎或解体
粗颗粒飞灰,对催化剂迎 风面的磨蚀,机械强度下 降造成的粉碎或解体属失 活。
催化剂表面速度偏差<15% 防冲刷
NSR偏差<5% 温度偏差<±15℃
防NH3逃逸 防烧结、防堵塞
三、玻璃窑炉PM2.5、SO2、NOX脱除技术
SC4R.4系吹统灰组系成统及关键技术—吹灰系统
玻璃炉窑虽粉尘浓度不高,特别是掺烧石油焦粉时, 未燃尽有机物及SO3含 量极高,粉尘具有极强的吸湿性和粘附性。仅采用声波清灰效果欠佳,催化
H2O
H2O 净烟气
N2
净烟气
N2 H2O
H2O
三、玻璃窑炉PM2.5、SO2、NOX脱除技术
SCR系统组成及关键技术—反应器
烟道导 流板
原烟气 喷氨
通过CFD数模计算和1:10物模测试优化烟道、 反应器的设计,保证进入第一层催化剂表面烟 气达到以下要求
整流器
烟气入射角偏差<10°防冲刷、磨蚀
催化剂 净烟气
燃用石油焦时,各点粉尘成份分析
1#、2#电场粉尘比电阻比较
三、玻璃窑炉PM2.5、SO2、NOX脱除技术
3.1干式高温电除尘器系统技术