注塑模具常见问题及解决办法【图解】
注塑模具不良现象的原因及处理办法

不良现象的原因及处理办法1.充填不足2.溢料3.气孔4.波纹5.银条纹6.表面晕喑7.融合线8.气泡9.黑条纹及烧痕10.龟裂11.离模溢料12.弯曲13.脱模不良14.直浇口的脱模不良15.材料的叠边不良不良现象及其原因处理办法3气孔在材料为充分干燥时,是挥发物或空气所致;大多时候发生在产品胶厚的位置,实际是材料的收缩引起的真空气泡[1] 流道或浇口过小[2] 成形品的壁厚差大[3] 材料的温度高[4] 离浇口的流动距离长[5] 脱模过早[6] 射出压力低[7] 冷却时间短[8] 保压不充分4 波纹[1]材料流动不畅i)将流道或浇口扩展。
ii)增强射出压力。
i)尽量使壁厚度要均匀。
ii)要使壁厚差不显著。
i)降低材料的温度。
ii)要改进发生气孔的部位的冷却条件。
i)增强射出压力。
ii)加快射出速度。
iii)在成形品上设置棱或厚层部位。
i)延长冷却时间。
i)增强射出压力。
i)延长冷却时间。
ii)降低模具温度。
i)延长保压时间。
ii)增强保压压力。
[2]模具温度低[3]进浇口过小i)升高材料的温度。
ii)换用流动性高的材料。
iii)增强射出压力。
iiii)设定冷料井。
加速射出速度。
i)采用热油机或热水机提高模温。
i)加大进浇口。
ii)升高材料的温度。
5 银条纹[1]水分或挥发成分[2]材料的温度过高[3]模具温度低[4]排气不良[5]成形品或模具的设计不良i)使材料充分干燥。
ii)使用料斗式装载机。
i)降低材料的温度。
ii)放慢射出速度。
i)升高模具温度。
i)在模具耦合面加上排气用的条缝。
ii)放宽模具与推挺钉梢的间隙。
iii)设置真空排气结构间隙i)放大浇口或流道。
ii)消除急剧的壁厚差现象。
[6]模具面上的水分或挥发成分[8]混入夹杂的材料[9]螺桨的运转不当6.表面晕暗[1] 润滑或挥发成分过多[2]脱模材过多7 融合线------实际是2股或多股材料汇合时,材料的融合线。
与材料汇合时,材料的粘度有很大的关系。
注塑过程中常见的问题及解决方案

注塑过程中常见的问题及解决方案一、飞边(披锋)1. 问题描述- 这飞边就像塑料偷偷长出来的小翅膀,在注塑件的边缘或者分型面那里冒出来,看着可闹心了。
就像好好的一块蛋糕,边缘突然多出了一些不规则的奶油坨坨。
2. 解决方案- 首先得检查模具的合模力。
要是合模力不够,那塑料就会像调皮的小孩从门缝里挤出来。
适当增加合模力,把模具紧紧抱住,让塑料乖乖待在该待的地方。
- 模具的磨损也会导致飞边。
就像穿破了的鞋子会漏脚指头一样,磨损的模具缝隙变大了。
这时候就得修模啦,把那些磨损的地方补一补或者磨平。
- 注塑压力也不能太大。
如果压力太大,塑料就像被大力士猛推的水,到处乱流。
降低注塑压力,找到一个合适的值,既能把模具填满,又不会让塑料溢出来。
二、短射(缺料)1. 问题描述- 短射就像给一个杯子倒水,结果没倒满一样。
注塑件看着不完整,有些地方该有塑料的却空着,就像一个没发育好的小怪物。
2. 解决方案- 先看看注塑压力是不是太小。
压力小的话,塑料就像没力气的小蚂蚁,爬不到模具的每个角落。
增加注塑压力,让塑料充满整个模具型腔。
- 塑料的流动性也很关键。
如果塑料太黏,就像浓稠的糨糊,很难流到模具的远端。
这时候可以提高料筒温度,让塑料变得稀一点,流动性更好,就像把糨糊加热变成稀粥一样,能顺利流到各个地方。
- 浇口尺寸也可能有问题。
要是浇口太小,就像一个小得可怜的水龙头,水流不出来多少。
适当扩大浇口尺寸,让塑料能畅快地流进模具。
三、气泡(气穴)1. 问题描述2. 解决方案- 注塑速度可能太快了。
塑料像一阵风呼呼地冲进模具,把空气都裹在里面了。
降低注塑速度,让塑料慢慢流进去,就像散步一样,这样空气就有机会跑出来了。
- 模具的排气也很重要。
如果模具没有排气孔或者排气不良,空气就被困在里面出不来。
在模具上开排气槽或者使用透气钢材料,给空气一条逃跑的路。
- 塑料干燥不彻底也会产生气泡。
如果塑料里有水份,加热的时候就会变成水蒸气,形成气泡。
注塑机和模具问题汇总与纠正措施
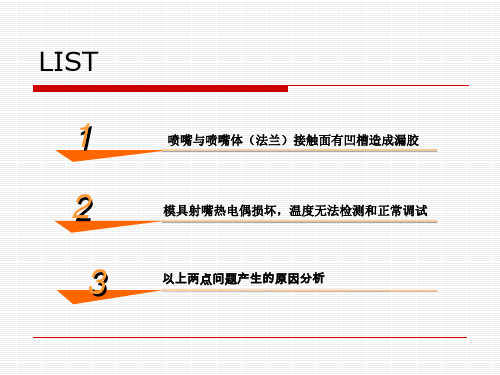
END
LIST
1 2 3
喷嘴与喷嘴体(法兰)接触面有凹槽造成漏胶 模具射嘴热电偶损坏,温度无法检测和正常调试 以上两点问题产生与喷嘴体(法兰) 接触面有凹槽造成漏胶
现象:目前漏胶情况呈上升趋势,造成原材料的浪费,加热圈会短路,同 时注塑压力也受到损失。 纠正措施: 1、更换新的喷嘴与喷嘴体;
2、把喷嘴与喷嘴体接触平面车平,垫一个铜垫在其中间。
2.模具射嘴热电偶损坏温度无法检测和调试
热电偶损坏,温度无法 检测和正常调试
纠正措施:对模具的这些射嘴的感温线进行维修。
3.以上两点问题产生的原因分析
1.喷嘴与喷嘴体(法兰)接触面有凹槽造成漏胶产生的机理: 新到注塑机在试机生产后,没有对喷嘴进行二次紧固,再加上在生产过程中由于注射
度设定过快,熔融物料产生的气体从喷嘴与喷嘴体(俗称法兰)接触面的间隙中不断排出 ,间隙逐渐增大,当间隙大于PC的溢边值后就开始轻微漏胶,漏出的塑胶和腐蚀性物质与 接触面不断的摩擦和腐蚀,漏胶量就会逐渐增大。 2.模具射嘴热电偶损坏的机理:
线路断路是热电偶不能正常工作的根本所在。之所以产生断路的实际情况是: Ⅰ.WHEN:3月16日。 Ⅱ.WHO:工艺员。 Ⅲ.WHERE:华瑞星注塑车间现场1号机台。 Ⅳ.WHY:射嘴堵进行清理,操作不当。 Ⅴ.WHAT:装模过程中感温线松动挂断或操作时短路。 Ⅵ.HOW:对模具射嘴进行维修,更换感温线。 Ⅶ.HOW MUCH:采购联系厂家报价。 Ⅷ.HOW MANY :共计有3个模具射嘴损坏。
注塑模具常见缺陷问题及改进方案
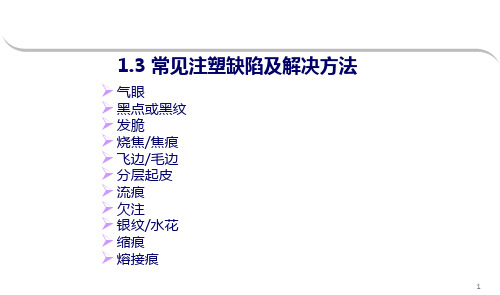
改进方法(2)
注塑机 工艺条件
▪检查止逆阀和料筒内壁是否磨损严重,上述磨损会导致
注塑压力和注塑量损失严重。
▪检查加料口是否有料或是否架桥。
▪增大注塑压力 ▪增大注塑速度,增强剪切热 ▪增大注塑量 ▪增大料筒温度和模具温度
21
成型问题-银丝/水花
银纹是指水分、空气或炭化物顺着流动方向在制件表面呈现发射状分 布的一种表面缺陷。
17
成型问题-欠注(缺料)
•欠注是指模具型腔不能被完全填充满的一种现象。
欠注形成原因
任何阻止聚合物熔体流动或使聚合物注塑量不足的因素均可能导致欠注现象。这 些因素包括:
• 熔体温度、模具温度或注塑压力和速度过低 • 原料塑化不均 • 排气不良 • 原料流动性不足 • 制件太薄或浇口尺寸太小 • 聚合物熔体由于结构设计不合理导致过早硬化
气眼可能引起的问题: 困在型腔内气体不能被及时排出,易导致出现表面 起泡,制件内部夹气,注塑不满等现象。
2
案例 (表面起泡)
Air bubble cut open
3
改进方法
结构设计 模具设计
工艺条件
• 减少厚度的不一致,尽量保证壁厚均匀. ▪ 在最后填充的地方增设排气口 ▪ 重新设计浇口和流道系统. ▪ 保证排气口足够大,使气体有足够的时间和空间排走.
5
改进方法
注塑机 工艺条件
•选择合适的注塑机吨位 •检查料筒内表面、螺杆表面是否刮伤积料. •降低料筒和喷嘴的温度. •清洁注塑过程的各个环节. •避免已经产生黑点/黑纹的料被重新回收利用.
6
案例 (黑纹)
7
改进方法
材料 模具设计
•采用无污染的原材料 •将材料置于相对封闭的储料仓中 •增加材料的热稳定性
注塑模具常见缺陷、产生原因和调整方法表

制件பைடு நூலகம்量不好:
1.有飞边
2.有缺料
3.有顶白
4.有拖花
5.变形大
6.级位大
7.溶接线明显
1.配合间隙过大;
2.走胶不畅, 困气;
3.顶针过小, 顶出不均匀;
4.斜度过小, 有毛刺, 硬度不足;
5.注塑压力不均匀, 产品形态强度不足;
6.加工误差;
7.离浇口远, 模温低。
注塑模具常见缺陷、产生原因和调整方法表
注塑模
装配缺陷
产 生 原 因
调 整 方 法
模具开闭
顶出复位
动作不顺
1.模架导柱、导套滑动不顺,配合过紧
2.斜顶、顶针滑动不顺。
3.复位弹簧弹力或预压量不足。
1修配或者更换导柱、导套。
2检查并修配斜顶、顶针配合。
3增加或者更换弹簧。
模具与注塑
机不匹配
1.定位环位置不对、尺寸过大或过小。
1.合理调整间隙及修磨工作部分分型面;
2.局部加胶, 加排气;
3.加大顶针, 均匀分布;
4.修毛刺, 加斜度, 氮化;
5.修整浇口, 压力均匀, 加强产品强度;
6.重新加工;
7.改善浇口, 加高模温。
2.模具的限位行程不够,模具的抽芯行程不够,模具的顶出行程不够;
1.检查浇注系统各段流道和浇口,修整有关零件;
2.检查各限位、抽芯、顶出行程是否符合设计要求,调整不符合要求的行程;
模具运水
不通或漏水
1模具运水通道堵塞,进出水管接头连接方式错误。
2封水胶圈和水管接头密封性不够。
1.检查冷却系统进出水管接头连接方式及各段水道,修整有关零件;
注塑模具各类问题原因分析及解决办法
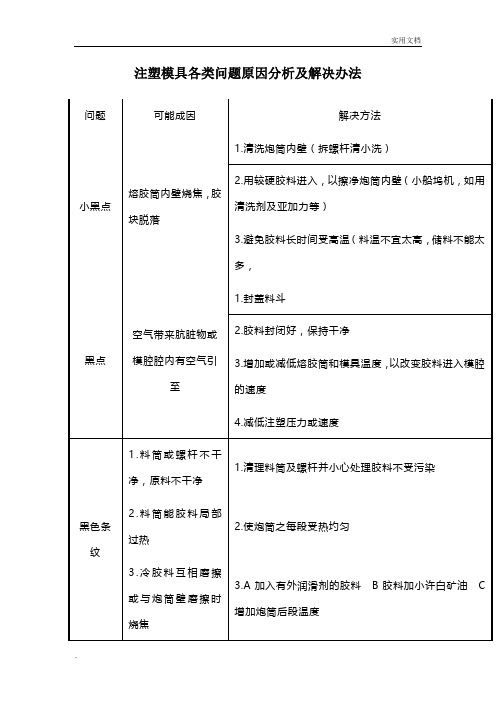
注塑模具各类问题原因分析及解决办法1注塑件收缩凹陷的原因分析注塑成型过程中,制品收缩凹陷是比较常见的现象。
造成这种情况的主要原因有:机台方面(1)射嘴孔太大造成融料回流而出现收缩,太小时阻力大料量不足出现收缩。
(2)锁模力不足造成飞边也会出现收缩,应检查锁模系统是否有问题。
(3)塑化量不足应选用塑化量大的机台,检查螺杆与料筒是否磨损。
模具方面(1)制件设计要使壁厚均匀,保证收缩一致。
(2)模具的冷却、加温系统要保证各部份的温度一致。
(3)浇注系统要保证通畅,阻力不能过大,如主流道、分流道、浇口的尺寸要适当,光洁度要足够,过渡区要圆弧过渡。
(4)对薄件应提高温度,保证料流畅顺,对厚壁制件应降低模温。
(5)浇口要对称开设,尽量开设在制件厚壁部位,应增加冷料井容积。
塑料方面结晶性的塑料比非结晶性塑料收缩历害,加工时要适当增加料量,或在塑料中加成换剂,以加快结晶,减少收缩凹陷。
加工方面(1)料筒温度过高,容积变化大,特别是前炉温度,对流动性差的塑料应适当提高温度、保证畅顺。
(2)注射压力、速度、背压过低、注射时间过短,使料量或密度不足而收缩压力、速度、背压过大、时间过长造成飞边而出现收缩。
(3)加料量即缓冲垫过大时消耗注射压力,过小时,料量不足。
(4)对于不要求精度的制件,在注射保压完毕,外层基本冷凝硬化而夹心部份尚柔软又能顶出的制件,及早出模,让其在空气或热水中缓慢冷却,可以使收缩凹陷平缓而不那么显眼又不影响使用。
2注塑件震纹的原因分析PS等刚性塑料制件在其浇口附近的表面,以浇口为中心的形成密集的波纹,有时称为震纹。
产生原因是熔体粘度过大而以滞流形式充模时,前端的料一接触到型腔表面便很快冷凝收缩起来,而后来的熔料又胀开已收缩的冷料继续前进过程的不断交替使料流在前进中形成了表面震纹。
解决办法(1)提高料筒温度特别是射嘴温度,还应提高模具温度。
(2)提高注射压力与速度,使其快速充模型腔。
(3)改善流道、浇口尺寸,防止阻力过大。
注塑模具损坏的原因及相关处理措施
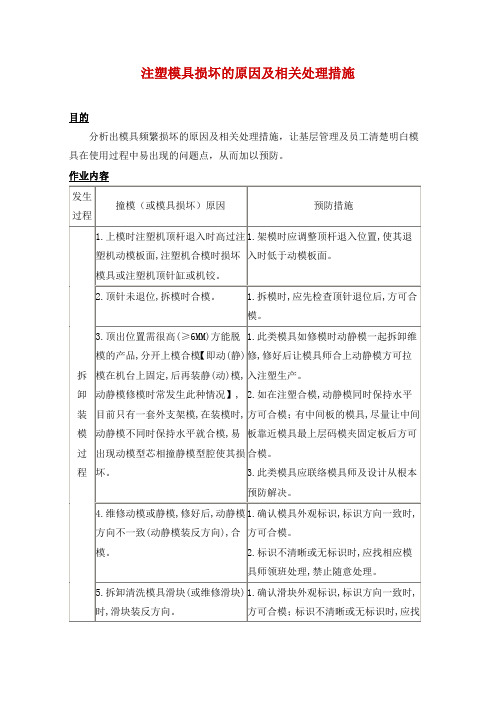
2.如在注塑合模,动静模同时保持水平方可合模;有中间板的模具,尽量让中间板靠近模具最上层码模夹固定板后方可合模。
3.此类模具应联络模具师及设计从根本预防解决。
4.维修动模或静模,修好后,动静模方向不一致(动静模装反方向),合模。
8.生产中,注塑机顶针松动,移位,产品未脱模,合模压模。
1.上模时应确认模具顶针状况。
2.生产中尽量不要使用过大的顶针压力,过快的顶针速度。
9.滑块未退到位,顶出时造成顶针坏或滑块损坏。
1.模具的润滑保养点检应作出规范。
10.开模速度过快,滑块移动偏位,顶出.码模夹装得太少,模具松动或模具未装紧,开模时,拉断导柱。
1.动静模每边至少装4个码模夹,且需锁紧。
2.座进的压力速度需尽量小,座进速度需缓慢进入。
10.分开卸模时,模具重心,惯性作用,动静模相撞损坏模具。
松最后一颗码模夹螺丝时,用手按住要卸的半边模,防止摆动;另在型腔放一个产品,防止相撞时损坏型腔。
11.用钢针铁条等尖锐硬物掏挖模具造成模具损坏。
1.员工培训保护模具方面的意识。
12.产品排气不良,用锉刀或粗砂纸打磨模具造成模具出现飞边或型腔损坏。
1.尽量用汽油或丙酮清洗模具,用飞边刀小心清理排气口杂物;要加排气需找模具师处理。
2.省模抛光需用1200#细或更细的砂纸。
3.禁止用砂纸大面积打磨模具。
作业内容
发生
过程
撞模(或模具损坏)原因
预防措施
拆
卸
装
模
过
程
1.上模时注塑机顶杆退入时高过注塑机动模板面,注塑机合模时损坏模具或注塑机顶针缸或机铰。
注塑模具在使用过程中常出现的问题

注射
浇口衬套 浇口、流道 浇口、
靠近浇口处 合模面 变厚或飞边
小顶杆 小顶杆托板
动模的变形(一般动模侧的变形比定模侧多 动模的变形 一般动模侧的变形比定模侧多) 一般动模侧的变形比定模侧多
4、模具温度不合适造成不良产品 、模具温度不合适造成不良产品
模具温度过低, 模具温度过低,则造成填 充不足,表面模糊不清, 充不足 , 表面模糊不清 , 产 生熔接痕等毛病 ; 生熔接痕 等毛病;过高则成 等毛病 型周期加长, 引起收缩 收缩等 型周期加长 , 引起 收缩 等 , 应根据树脂及成型品形状选 择适当的模具温度且使温度 择适当的模具温度且使 温度 恒定。 恒定。
一般来说,聚碳酸酯、聚甲基丙烯酸甲酯( 一般来说,聚碳酸酯、聚甲基丙烯酸甲酯( 有机 玻璃)等高粘度树脂的模具温度高 聚乙烯、 模具温度高;聚乙烯 玻璃 ) 等高粘度树脂的 模具温度高 聚乙烯 、 苯乙烯 等低粘度树脂的模具温度低, 等低粘度树脂的模具温度低,特别需要注意稳定温度 的树脂为尼龙、聚甲醛、聚丙烯等结晶性树脂。 的树脂为尼龙、聚甲醛、聚丙烯等结晶性树脂。利用 尼龙 这种树脂精密成型时,应尽力将模具温度变动辐度控 这种树脂精密成型时, 制到± ℃以下。 制到±5℃以下。 结晶性树脂在高温模具慢慢冷却和在低温模具急 结晶性树脂 在高温模具慢慢冷却和在低温模具急 剧冷却时,收缩情况有所不同,慢慢冷却收缩大, 剧冷却时,收缩情况有所不同,慢慢冷却收缩大,急 剧冷却收缩小。 剧冷却收缩小。
分型面
顶杆
确定可紧贴着移动侧,另外, 确定可紧贴着移动侧,另外,型芯 冷却好,可紧紧抱住型芯,故情况良好。 冷却好,可紧紧抱住型芯,故情况良好。 固定侧脱模斜度小 难于开模, 脱模斜度小, 固定侧脱模斜度小,难于开模, 应尽可能用硬的材料,仔细研磨。 应尽可能用硬的材料,仔细研磨。
注塑模具出现的问题及原因分析!

注塑制品开裂的原因分析开裂,包括制件表面丝状裂纹、微裂、顶白、开裂及因制件粘模、流道粘模而造成或创伤危机,按开裂时间分脱模开裂和应用开裂。
主要有以下几个方面的原因造成:1.加工方面:(1)加工压力过大、速度过快、充料愈多、注射、保压时间过长,都会造成内应力过大而开裂。
(2)调节开模速度与压力防止快速强拉制件造成脱模开裂。
(3)适当调高模具温度,使制件易于脱模,适当调低料温防止分解。
(4)预防由于熔接痕,塑料降解造成机械强度变低而出现开裂。
(5)适当使用脱模剂,注意经常消除模面附着的气雾等物质。
(6)制件残余应力,可通过在成型后立即进行退火热处理来消除内应力而减少裂纹的生成。
2.模具方面:(1)顶出要平衡,如顶杆数量、截面积要足够,脱模斜度要足够,型腔面要有足够光滑,这样才防止由于外力导致顶出残余应力集中而开裂。
(2)制件结构不能太薄,过渡部份应尽量采用圆弧过渡,避免尖角、倒角造成应力集中。
(3)尽量少用金属嵌件,以防止嵌件与制件收缩率不同造成内应力加大。
(4)对深底制件应设置适当的脱模进气孔道,防止形成真空负压。
(5)主流道足够大使浇口料未来得及固化时脱模,这样易于脱模。
(6)主流道衬套与喷嘴接合应当防止冷硬料的拖拉而使制件粘在定模上。
3.材料方面:(1)再生料含量太高,造成制件强度过低。
(2)湿度过大,造成一些塑料与水汽发生化学反应,降低强度而出现顶出开裂。
(3)材料本身不适宜正在加工的环境或质量欠佳,受到污染都会造成开裂。
4.机台方面:注塑机塑化容量要适当,过小塑化不充分未能完全混合而变脆,过大时会降解。
注塑制品气泡的原因分析气泡(真空泡)的气体十分稀薄属于真空泡。
一般说来,如果在开模瞬间已发现存在气泡是属于气体干扰问题。
真空泡的形成是由于充注进塑料不足或压力较低。
在模具的急剧冷却作用下,与型腔接角的燃料牵拉,造成体积损失的结果。
解决办法:(1)提高注射能量:压力、速度、时间和料量,并提高背压,使充模丰满。
注塑常见质量问题及改善指引 PPT
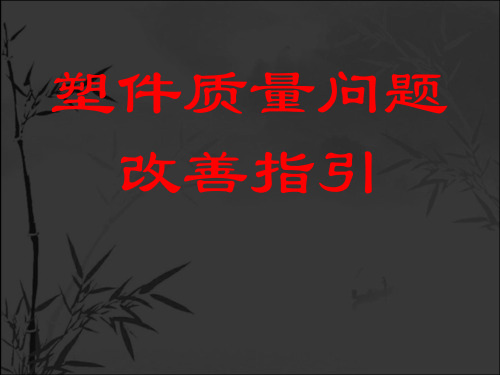
一.填充不足(缺胶、缺料)
表现为注塑件不完整或细节不完全.是因为塑料未 完全充满模腔所致. **改善指引: 检讨成型工艺 增加注射压力 增加注射速度 增加熔胶温度 增加注射时间 适当增加背压 检查注塑机 检查料斗量及料斗口是否堵塞 是否正确设置了喷射行行程
六.银条纹
由于气泡及充填过程中沿拉应力的垂直方向产生应力 集中点使塑件对外呈现银纹现象. **改善指引 检讨成型工艺 熔胶温度太高至挥发物过多:降低料筒温度(尤其是 后端温度) 也可能熔胶温度太低至充填不稳定,内应力增大:相 应增高料温及喷嘴温度. 可能胶料滞留在料筒内时间过长,需减短总周期时 间. 增加或减小射胶速度. 适当调低注射压力. 适当增高背压(如过高需调低)及减小螺杆转速.
十四.碎裂
注塑件表面有细水裂纹裂缝 **改善指引: 检讨成型工艺 调整注射压力:升高压力.使充模顺畅,降低粘度 过高压力致内应力大易开裂,故需降低 调整料筒温度:过高温度,使料降解 过低温度,使熔接位强度不足 适当增大射胶速度 适当提高模温,减小分取向性
十四.碎裂
十.黑褐斑点
Hale Waihona Puke
检查注射机. 胶料困于炮筒装置的〝死角〞或不流动区,使它 在高温下停留时间过久:将筒和螺杆拆下来彻 底清洁与聚合物接触的表面. 检查模具. 浇口过小,增大浇口尺寸. 塑件壁部分太窄,材料在高压下流过时产生衰变 ,需检查修正,保持壁厚厚的正确性和一致性. 检查胶料 材料中混入的热敏感的其它已多次回用的胶料, 检查来源,清除杂质.
塑件(可能连水口)在模内被粘住,不能出模或出 模困难. **改善指引: 检讨成型工艺. 模内胶料过度充填:减低注射量,减低注射速 度. 料温过高需适当调低. 保压时间过长:减少螺杆向前时间. 增加冷却时间或缩短冷却时间(视型腔或型 芯粘模而不同). 在允许的情况下借助脱剂脱模.
注塑模具常见问题解决方案

模具加工前对设计图做倒扣、干涉全局检查,对强脱类产品倒扣大小,论证其 可行性分析 TPE、TPU等软胶类产品前模需要做粗纹路,防止注塑过程产生真空而粘模。
深腔、深筋位、孔柱位等容易粘模部位加强EP的布置、特殊部位顶针做延时。
侧向抽芯(滑块、斜顶)大面积的深腔或孔位包胶考虑2次抽芯或者延时抽芯
模具圆弧曲面类分型面加工不到 圆弧曲面类分型面,前、后模距封胶位15-20mm以外做避空。利于CNC加工保
位,采用手工打磨
证精度,减少手工打磨工艺。
模具型腔加工超差
模芯加工完后需要用3次元、投影仪设备进行尺寸检测。
模具结构设计不合理
对半出前、后模的胶位,为防止产品出现逆断差,产品外形周圈将后模比前模做 小0.05-0.1,内部碰穿孔位后模比前模做大0.05,具体可视产品工艺要求进行调整。
模具注塑受力不平衡,偏载
模胚增加直身或者斜度定位锁。
产品周圈分型面和熔胶未端需要加强排气、深筋、深柱超过6-8mm以上需要做 排气镶件。 加大虎口定位面积、模胚增加直身或者斜度定位锁。
模板强度不够,支撑柱太少
模板根据开框深度和模具大小适当加大板的厚度,中小型模具框底部厚度一般取 30-60左右,唧嘴附近、胶位区域因注塑压力相对较大,撑头布置尽量多。
侧向抽芯(滑块、斜顶)大面积的深腔或孔位包胶考虑2次抽芯或者延时抽芯
圆筒、深腔类产品、深筋位、孔柱位视情况做后模先抽、推板或者2次顶出。
2.批峰 断差
原因分析
解决对策
模具碰穿、插穿面尺寸精度超差 碰穿面与插穿面,公模面负公差控制-0.015-0mm;母模面正公差控制+0.015-0
模导向定位精度不够 模具排气不良
注塑常见产品缺陷及解决方法ppt课件
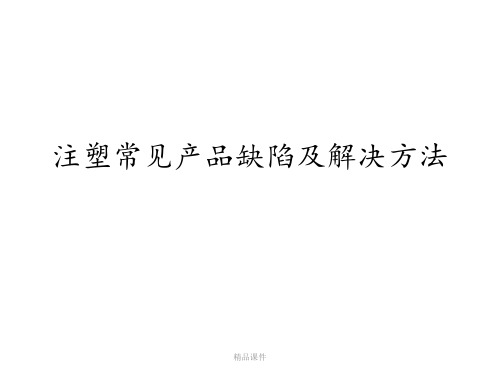
精品课件
走料不齐
原因: 1.注塑压力太低. 2.注塑速度太慢. 3.注塑时间太短. 4.保压压力过小. 5.保压时间过短. 6.保压切换位置过早. 7.模具疏气不良. 8.模具表面温度太低. 9.熔胶温度过低. 10.物料粘度过高.
精品课件
走料不 齐
解决方法: 1.注塑中断后重新开机,可 能前几啤会报废. 2.提高注塑和补缩压力. 3.提高注塑量和注塑速度.( 注塑压力要足够) 4.提高模具温度. 5.提高料温. 6.清洁模具的疏气系统. 7.检查料垫是否足够. 8.调节适合的保压转换点( 填充至95%-99%). 9.检查浇口和炮嘴有没有被 堵塞.
精品课件
困 气
原因: 1.注塑速度过快. 2.背压过高. 3.疏气不足,气体包封. 4.流道尺寸偏小. 5.熔体温度过高,需降低剪 切. 解决方法: 1.降低注塑速度. 2.清洁困气位置的疏气槽. 3.降低锁模力. 4.降低保压压力. 5.降低螺杆的转速. 6.降低熔胶温度.
精品课件
困气
烧
发
黑
白
精品课件
变形
解决方法: 1.加长冷却时间. 2.加长保压时间. 3.增加或降低注塑压力. 4.增加或降低模温. 5.根据产品变形的方向适当 的设置不同的前后模温(变 形趋向模温高的一側) 6.采用多段保压,高到低或 低到高设置保压压力.
精品课件
夹具(定型模)
精品课件
热水机&冷水机
精品课件
此课件下载可自行编辑修改,供参考! 感谢您的支持,我们努力做得更好!
精品课件
精品课件
柱位的缩水
精品课件
喷 射纹
原因: 1.注塑速度过慢或过快. 2.注塑压力太低. 3.保压时间过长. 4.模具冷却不均已. 5.模具浇口附近温度较低. 6.模具表面温度太低. 7.模具浇口尺寸太小. 8.浇口位置设计不合理. 9.浇口流程过长. 10.熔胶温度过低. 解决方法: 1.降低注塑速度(多级注塑). 2提高料温,提高模具温度. 3.提高浇口的深度(为壁厚的 60%-80%比较安全) 4.改用扇形浇口.
注塑模具各类问题原因分析及解决办法
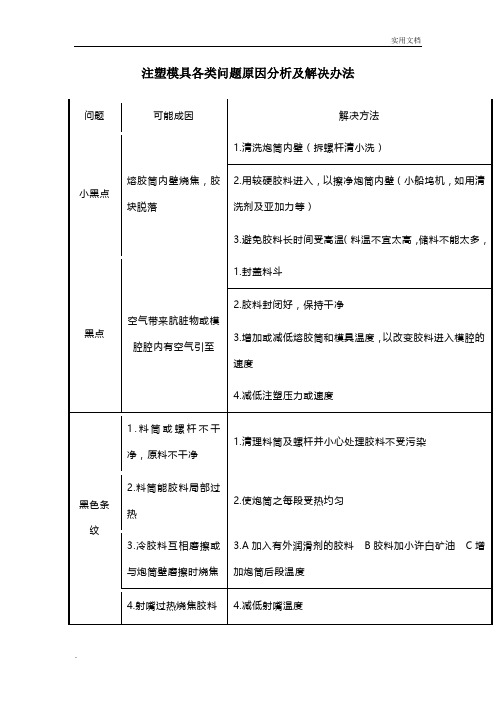
注塑模具各类问题原因分析及解决办法注塑成型过程中,制品收缩凹陷是比较常见的现象。
造成这种情况的主要原因有:机台方面(1)射嘴孔太大造成融料回流而出现收缩,太小时阻力大料量不足出现收缩。
(2)锁模力不足造成飞边也会出现收缩,应检查锁模系统是否有问题。
(3)塑化量不足应选用塑化量大的机台,检查螺杆与料筒是否磨损。
模具方面(1)制件设计要使壁厚均匀,保证收缩一致。
(2)模具的冷却、加温系统要保证各部份的温度一致。
(3)浇注系统要保证通畅,阻力不能过大,如主流道、分流道、浇口的尺寸要适当,光洁度要足够,过渡区要圆弧过渡。
(4)对薄件应提高温度,保证料流畅顺,对厚壁制件应降低模温。
(5)浇口要对称开设,尽量开设在制件厚壁部位,应增加冷料井容积。
塑料方面结晶性的塑料比非结晶性塑料收缩历害,加工时要适当增加料量,或在塑料中加成换剂,以加快结晶,减少收缩凹陷。
加工方面(1)料筒温度过高,容积变化大,特别是前炉温度,对流动性差的塑料应适当提高温度、保证畅顺。
(2)注射压力、速度、背压过低、注射时间过短,使料量或密度不足而收缩压力、速度、背压过大、时间过长造成飞边而出现收缩。
(3)加料量即缓冲垫过大时消耗注射压力,过小时,料量不足。
(4)对于不要求精度的制件,在注射保压完毕,外层基本冷凝硬化而夹心部份尚柔软又能顶出的制件,及早出模,让其在空气或热水中缓慢冷却,可以使收缩凹陷平缓而不那么显眼又不影响使用。
2注塑件震纹的原因分析PS等刚性塑料制件在其浇口附近的表面,以浇口为中心的形成密集的波纹,有时称为震纹。
产生原因是熔体粘度过大而以滞流形式充模时,前端的料一接触到型腔表面便很快冷凝收缩起来,而后来的熔料又胀开已收缩的冷料继续前进过程的不断交替使料流在前进中形成了表面震纹。
解决办法(1)提高料筒温度特别是射嘴温度,还应提高模具温度。
(2)提高注射压力与速度,使其快速充模型腔。
(3)改善流道、浇口尺寸,防止阻力过大。
(4)模具排气要良好,要设置足够大的冷料井。
注塑机加工模具常见问题及解决办法
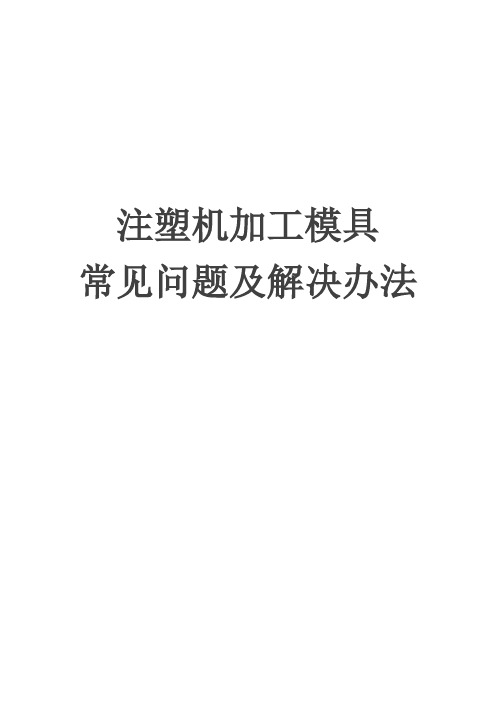
注塑机加工模具常见问题及解决办法问题一:塑胶呈波浪原因:因浇口或其它部分狭窄,熔态塑料推动固化塑件前移时,表面产生波纹。
解决方法:1.增加注直径2.提高注咀及模具温度3.提高料筒高度4.加快注塑速度5.减慢注料速度6.更改模具冷却水进口位,使其远离浇口7.扩大浇口。
问题二::塑件呈银纹形原因:因塑料含水份,混料不均匀,注塑时夹气,添加剂或脱模剂过多。
解决方法:1.加强回压2.减慢注速3.清理料筒4.提高模温5.改浇口位置6.扩大流道及浇口7.烘料8.料门中安装红外线灯。
问题三:塑胶接口不良原因:因塑料温度太低,不能熔化,或因气体排泄不足导致两股以上分流混合而产生发状细线或气泡。
解决方法:1.提高料温2.提高注温3.增加注速4.接缝线外设冷料池5.设放气口6.改变浇口位或浇口7.不要用脱模剂8.转用易流动的低粘度类原料。
问题四:塑件呈现空洞原因:因塑料在熔料固化期间表面接触低温模壁,收缩集中于厚壁段而造成空洞,或因夹气做成空洞。
解决方法:1.提高注压(及二次压力)2.延长注时3.降低料筒固化温度4.消减模壁厚度至6mm以下,必要时设置等壁厚助线,及去除多余壁厚5.扩大浇口6.缩短流道7.调匀模温8.更改浇口位置,排除夹气。
问题五:塑件欠注或缺料原因:因机械注塑及塑化性能不足,料流不良,浇口截面太细,模壁太薄或泄气不良。
解决方法:1.增加注料速率,如仍不足,则需换重型机械2.装防漏注阀式螺杆3.提高注压4.提高料筒、注咀固化及模具温度5.查电热线是否断线6.查注咀是否堵塞,增加循环速度7.提高模具放气能力8.加大浇口截面9.增加产品壁厚10.加设助线,改造料流11.选用低粘度原料12.加润滑剂。
问题六:合模边挤出塑料原因:因料温及注压过高,或锁模力不足。
解决方法:1.降低注压及筒固化温度2.缩短注时3.减少注料速度4.改用高锁模力机5.改造合模表面紧配合及清理合模表面6.转用低粘度料。
问题七:塑件表面呈凹痕原因:因塑件表面误时冷却,因其表面凹痕。
塑料模具注射时常见问题原因分析和解决办法

塑料模具注射时常见问题原因分析和解决办法刚开机时产品跑披锋,生产一段时间后产品缺胶的原因及解决方案。
刚开机时注塑机料管内的熔胶由于加热时间长,熔胶粘度低,流动性好,产品易跑披锋,生产一段时间后由于熔胶不断把热量带走,造成熔胶不足,粘度大,流动性差,使产品缺胶。
在生产一段时间后,逐渐提高料管温度来解决。
2.在生产过程中,产品缺胶,有时增大射胶压力和速度都无效,为什么?解决方法?是因为生产中熔胶不断把热量带走,造成熔胶不足,胶粘度大,流动性差,使产品缺胶。
提高料管温度来解决。
3.产品椭圆的原因及解决方法。
产品椭圆是由于入胶不均匀,造成产品四周压力不匀,使产品椭圆,采用三点入胶,使产品入胶均匀。
4.精密产品对模具的要求。
要求模具材料刚性好,弹变形小,热涨性系数小。
5.产品耐酸试验的目的产品耐酸试验是为了检测产品内应力,和内应力着力点位置,以便消除产品内应力。
6.产品中金属镶件受力易开裂的原因及解决方法。
产品中放镶件,在啤塑时由于热熔胶遇到冷镶件,会形成内应力,使产品强度下降,易开裂。
在生产时,对镶件进行预热处理。
7.模具排气点的合理性与选择方法。
模具排气点不合理,非但起不到排气效果,反而会造成产品变形或尺寸变化,所以模具排气点要合理。
选择模具排气点,应在产品最后走满胶的地方和产品困气烧的地方开排气。
8.产品易脆裂的原因及解决方法。
产品易脆裂是产品使用水口料和次料太多造成产品易脆裂,或是料在料管内停留时间过长,造成胶料老化,使产品易脆裂。
增加新料的比例,减少水口料回收使用次数,一般不能超过三次,避免胶料在料管内长时间停留。
9.加玻纤产品易出现泛纤的原因及解决方法是由于熔胶温度低或模具温度低,射胶压力不足,造成玻纤在胶内不能与塑胶很好的结合,使纤泛出。
加高熔胶温度,模具温度,增大射胶压力。
10.进料口温度对产品的影响。
进料口温度的过高或过低,都会造成机器回料不稳定,使加料量不稳定,而影响产品的尺寸和外观。
- 1、下载文档前请自行甄别文档内容的完整性,平台不提供额外的编辑、内容补充、找答案等附加服务。
- 2、"仅部分预览"的文档,不可在线预览部分如存在完整性等问题,可反馈申请退款(可完整预览的文档不适用该条件!)。
- 3、如文档侵犯您的权益,请联系客服反馈,我们会尽快为您处理(人工客服工作时间:9:00-18:30)。
塑料模具,是塑料加工工业中和塑料成型机配套,赋予塑料制品以完整构型和精确尺寸的工具。
由于塑料品种和加工方法繁多,塑料成型机和塑料制品的结构又繁简不一,所以,塑料模具的种类和结构也是多种多样的。
注塑模具常见问题及解决办法详细介绍如下:
1.浇口脱料困难
在注塑过程中,浇口粘在浇口套内,不易脱出。
开模时,制品出现裂纹损伤。
此外,操作者必须用铜棒尖端从喷嘴处敲出,使之松动后方可脱模,严重影响生产效率。
这种故障主要原因是浇口锥孔光洁度差,内孔圆周方向有刀痕。
其次是材料太软,使用一段时间后锥孔小端变形或损伤,以及喷嘴球面弧度太小,致使浇口料在此处产生铆头。
浇口套的锥孔较难加工,应尽量采用标准件,如需自行加工,也应自制或购买专用铰刀。
锥孔需经过研磨至Ra0.4以上。
此外,必须设置浇口拉料杆或者浇口顶出机构。
2.导柱损伤
导柱在模具中主要起导向作用,以保证型芯和型腔的成型面在任何情况下互不相碰,不能以导柱作为受力件或定位件用。
在以下几种情况下,注射时动,定模将产生巨大的侧向偏移力:(1).塑件壁厚要求不均匀时,料流通过厚壁处速率大,在此处产生较大的压力;(2).塑件侧面不对称,如阶梯形分型面的模具相对的两侧面所受的反压力不相等。
3.大型模具
因各向充料速率不同,以及在装模时受模具自重的影响,产生动定模偏移。
在上述几种情况下,注射时侧向偏移力将加在导柱上,开模时导柱表面拉毛,损伤,严重时导柱弯曲或切断,甚至无法开模。
为了解决以上问题在模具分型面上增设高强度的定位键四面各一个,最简便有效的是采用圆柱键。
导柱孔与分模面的垂直度至关重要.在加工时是采用动,定模对准位置夹紧后,在镗床上一次镗完,这样可保证动,定模孔的同心度,并使垂直度误差最小。
此外,导柱及导套的热处理硬度务必达到设计要求。
4.动模板弯曲
模具在注射时,模腔内熔融塑料产生巨大的反压力,一般在600~1000公斤/厘米。
模具制造者有时不重视此问题,往往改变原设计尺寸,或者把动模板用低强度钢板代替,在用顶杆顶料的模具中,由于两侧座跨距大,造成注射时模板下弯。
故动模板必须选用优质钢材,要有足够厚度,切不可用A3等低强度钢板,在必要时,应在动模板下方设置支撑柱或支撑块,以减小模板厚度,提高承载能力。
5.顶杆弯曲,断裂或者漏料
自制的顶杆质量较好,就是加工成本太高,现在一般都用标准件,质量差。
顶杆与孔的间隙如果太大,则出现漏料,但如果间隙太小,在注射时由于模温升高,顶杆膨胀而卡死。
更危险的是,有时顶杆被顶出一般距离就顶不动而折断,结果在下一次合模时这段露出的顶杆不能复位而撞坏凹模。
为了解决这个问题,顶杆重新修磨,在顶杆前端保留10~15毫米的配合段,中间部分磨小0.2毫米。
所有顶杆在装配后,都必须严格检查起配合间隙,一般在0.05~0.08毫米内,要保证整个顶出机构能进退自如。
6.冷却不良或水道漏水
模具的冷却效果直接影响制品的质量和生产效率,如冷却不良,制品收缩大,或收缩不均匀而出现翘面变形等缺陷。
另一方面模整体或局部过热,使模具不能正常成型而停产,严重者使顶杆等活动件热胀卡死而损坏。
冷却系统的设计,加工以产品形状而定,不要因为模具结构复杂或加工困难而省去这个系统,特别是大中型模具一定要充分考虑冷却问题。
7.定距拉紧机构失灵
摆钩,搭扣之类的定距拉紧机构一般用于定模抽芯或一些二次脱模的模具中,因这类机构在模具的两侧面成对设置,其动作要求必须同步,即合模同时搭扣,开模到一定位置同时脱钩。
一旦失去同步,势必造成被拉模具的模板歪斜而损坏,这些机构的零件要有较高的刚度和耐磨性,调整也很困难,机构寿命较短,尽量避免使用,可以改用其他机构。
在抽心力比较小的情况下可采用弹簧推出定模的方法,在抽芯力比较大的情况下可采用动模后退时型芯滑动,先完成抽芯动作后再分模的结构,在大型模具上可采用液压油缸抽芯。
斜销滑块式抽芯机构损坏。
这种机构较常出现的毛病大多是加工上不到位以及用料太小,主要有以下两个问题。
斜销倾角A大,优点是可以在较短的开模行程内产生较的大抽芯距。
但是采取过大的倾角A,当抽拔力F为一定值时,在抽芯过程中斜销受到的弯曲力P=F/COSA,也越大,易出现斜销变形和斜孔磨损。
同时,斜销对滑块产生向上的推力N=FTGA也越大,此力使滑块对导槽内导向面的正压力增大,从而增加了滑块滑动时的摩擦阻力。
易造成滑动不顺,导槽磨损。
根据经验,倾角A不应大于25
8.有些模具因受模板面积限制
导槽长度太小,滑块在抽芯动作完毕后露出导槽外面,这样在抽芯后阶段和合模复位初阶段都容易造成滑块倾斜,特别是在合模时,滑块复位不顺,使滑块损伤,甚至压弯破坏。
根据经验,滑块完成抽芯动作后,留在滑槽内的长度不应小于导槽全长的2/3.
9.最后在设计
制造模具时,应根据塑件质量的要求,批量的大小,制造期限的要求等具体情况,既能满足制品要求,在模具结构上又最简便可靠,易于加工,使造价低,生产出来这样的模具才是极好的。
制造模具时,应根据塑件质量的要求,批量的大小,制造期限的要求等具体情况,既能满足制品要求,在模具结构上又最简便可靠,易于加工,使造价低,生产出来这样的模具才是极好的。