ZGMn13高锰钢的切削加工特点
ZGMn13对切削刀具的要求

!"
!"#" $ %
机械制造 !" 卷 第 #!$ 期
制造・材料
角 !!" # $ % & $ ’()) 。 ! 涂层硬质合金刀具 * 为了增强切削刃的强度, 应该适当减小前角 !( 。 粗加工时 " +,- !’ 基 陶 瓷 刀 具 , !( # $ % & $ "(), 取大值, 精加工时取小值。 因为它的抗压强度很高, # 复合 ./’ 01 陶瓷刀具, 为了增强刀头强度可以选取较小的前角 !( # $ "")。 在切削加工时应该采用 $ 聚晶立方氮化硼刀具, 负前角以及宽刃, 可以增加刃口的强度。 -2 选择后角 "( 选择时, 主要考虑的是高锰钢的加工硬化严重和 线膨胀系数大, 后角应该尽可能选大, 这样可以减少与 已加工表面的摩擦, 从而既可以降低已加工表面的硬 化, 也可以提高已加工表面的质量。 但是后角不宜过 大, 如果后角太大, 切削刃强度和刀头强度就会降低, 这会影响刀具寿命甚至造成崩刃。 粗加工 % 硬质合金 3 45 6 刀具后角 "( # 7 & "-), 时取小值; 为增强切削刃强度, 精加工时取大值, 可以 减轻已加工表面的硬化, 提高已加工表面的质量。 因为后刀面上刀尖与工件 ! 涂层硬质合金刀具, 的弹性接触区比较大, 两者之间的摩擦和挤压都比较 严重, 所以应当适当增大后角, 取 "( # "( & "’)。 抗弯强度不及硬质合金, 所 " +,-!’ 基陶瓷刀具, 以 后角 "( # 8 & ""), 粗加 工时 取小 值, 精 加工 时 取大 值。 后角 "( # "( & "-)。 # 复合 ./’ 01 陶瓷刀具, 因为它的硬度高, 摩擦 $ 聚晶立方氮化硼刀具, 因数小, 导热性好, 所以为了提高切削刃的强度, 可以 适当减小后角, 一般取 "( # 8 & "()。 -2 ’ 选择副后角 "( 9 在选择副后角 "( 9的过程中, 主要考虑的是已加工 表面的加工硬化现象, 不管应用哪一种刀具材料, 都应 该尽量增大副后角。 但是副后角也不能过大, 如果太 大, 刀尖强度和刀头强度就会降低, 影响刀具寿命, 容 易打尖或刀头断裂。 所以副后角的选择范围一般在 8 & 刀 具材 料越 硬 , 抗 弯强 度 越高 , 摩 擦 因 数越 "()之间 , 大, 副后角越大。 粗加工时选择小值, 半精加工、 精加工 时选择大值。 -2 1 选择刃倾角 #: 由于高锰钢的抗拉强度很高, 所以切削加工时刀 头受力很大, 这就要求刀头具有很高的抗弯强度。 一般 都选择负的刃倾角, 以增加刀头的强度。 刃倾角的选择 范围一般都在 ( & $ -()之间, 刀具切削部分材料越脆, 抗弯强度越低, 选取负值较大的刃倾角。 例如, 硬质合 陶 瓷 刀 具 #: # $ "( & $ 金 3 45 6 刀 具 #: # ( & $ "(); 立方氮化硼刀具 #: # $ 8 & $ "%)。 粗加工时取小 -(); 值, 半精加工和精加工时取大值。 刃倾角的选择还和前 角的选择有关系, 前角选择越大, 刃倾角应该选择越 小; 为了增强刀尖强度和提高散热能力, 甚至可以选取 $ -( & $ ’()。 -2 % 选择主偏角 $; 主偏角的大小影响着刀头的强度、 刀头的散热状 况、 后刀面与工件过渡表面之间的摩擦及切削变形; 主 偏角的大小还和工艺系统的刚性以及前角、 后角、 刃倾 角的大小有关。 主偏角越大, 刀头的强度越低, 刀头的 散热状况越差, 后刀面与工件过渡表面之间的摩擦以 及切削变形越小。 所以在选择主偏角的时候应该辩证 地考虑问题, 一般情况下, 工艺系统的刚性越好以及所 选前角、 后角、 刃倾角越大, 主偏角越小。 考虑到高锰钢的加工硬化现象特别严重以及线膨 胀系数大的特点, 主偏角的选择: % 硬质合金 3 45 6 刀具主偏角选择较大 $; # 1( & 这样可以减小切削力, 缓减加工硬化现象, 并且可 %(), 以减小刀具与工件的摩擦。 当粗加工时, 因为加工余量 大, 切削力大, 选取较小值; 当精加工时, 加工余量较 小, 为了提高切削速度和已加工表面的质量, 应该选择 较大值。 它与硬质合金相比, 强度低, 抗断裂 ! 陶瓷刀具, 韧性差, 主偏角应该适当减小, 一般 $; # ’( & 1()。 强度韧性好, 表面耐磨、 耐 " 涂层硬质合金刀具, 高温, 为了提高刀具寿命, 主偏角可以适当减小 $; # 1( & 1%)。 硬度、 耐磨性、 热稳定性很高, # 立方氮化硼刀具, 导热性较好, 抗弯强度与断裂韧性介于陶瓷与硬质合 金之间, 一般主偏角 $; # ’% & 1%)。 -2 8 选择副偏角 $;9 副偏角 $;9的大小对已加工表面的质量影响很大。 生产中, 对于一般的工程材料, 在工艺系统刚性允许的 情况下, 往往通过减小副偏角 $; 9来降低已加工表面的 粗糙度值。 但是对于高锰钢这种材料来说, 有加工硬化 现象特别严重以及线膨胀系数大的特点, 因此副偏角 一般取 $;9 # "( & -(), 粗加工时, 取大值, $; 9不宜太小, 半精加工和精加工时取小值。 当刀具材料的摩擦因数 小时, 还可以适当减小 $; 9。 -2 < 选择刀尖圆弧半径 !& 刀尖圆弧半径 !& 影响着刀尖的强度、 刀尖的散热 面积、 刀尖与工件材料之间的摩擦、 已加工表面的质 量、 切削力的大小等。 它对以上因素的影响效果是:!& 增大, 刀尖的强度增大, 刀尖的散热面积增大, 刀尖与 工件材料之间的摩擦增大; 已加工表面的粗糙度值降 低; 切削力增大。 所以选择 !& 时应该辩证地考虑问题。 在高锰钢的加工中, 为了提高刀具寿命, 防止在切削过
zgmn13是什么材料

zgmn13是什么材料
zgmn13是一种铝合金材料,具有良好的机械性能和耐腐蚀性能。
它主要由铝、锌、镁和锰等元素组成,具有轻质、高强度、耐腐蚀等特点,被广泛应用于航空航天、汽车制造、电子产品等领域。
首先,zgmn13具有优异的机械性能。
由于其含有适量的锌、镁和锰等合金元素,使得其强度和硬度得到显著提高,同时保持了较好的塑性和韧性。
这使得zgmn13在航空航天领域得到广泛应用,例如在飞机结构件、发动机零部件、航天
器外壳等方面发挥着重要作用。
其次,zgmn13具有良好的耐腐蚀性能。
铝合金本身具有良好的耐腐蚀性,而锌、镁和锰等元素的添加进一步提高了其耐腐蚀能力。
这使得zgmn13在汽车制造
领域得到广泛应用,例如在汽车车身、发动机零部件、制动系统等方面具有良好的抗腐蚀能力,能够有效延长汽车的使用寿命。
此外,zgmn13还具有较好的焊接性能和表面处理性能。
它可以通过不同的焊
接方法与其他材料进行连接,同时也可以通过阳极氧化、喷砂、喷涂等表面处理方法进行装饰和防护,使其在电子产品领域得到广泛应用,例如在手机外壳、笔记本电脑外壳、数码相机外壳等方面具有良好的装饰性和防护性能。
总的来说,zgmn13作为一种铝合金材料,具有轻质、高强度、耐腐蚀等优良
性能,被广泛应用于航空航天、汽车制造、电子产品等领域。
随着科技的不断进步,相信zgmn13在未来会有更广阔的应用前景,为各行业的发展提供更多可能性。
高猛高的切削加工

高锰钢的切削加工1.切削高锰钢时怎样选择刀具材料?高锰钢属难加工材料,对刀具材料要求较高。
一般来说,要求刀具材料红硬性高、耐磨性好,有较高的强度、韧性和导热系数。
切削高锰钢可选用硬质合金、陶瓷做刀具材科,也可以用cn25涂层刀片或cbn(立方氮化硼)刀具。
其中yg类硬质合金具有较高的抗弯强度和冲击韧性(与yt类硬质合金比较),可减少切削时的崩刃。
同时,yg类硬质合金的导热性较好,有利于切削热从刀尖散走,降低刀尖温度,避免刀尖过热软化。
yg类硬质合金的磨加工性较好,可以磨出锐利的刃口。
一般情况下,刀具的耐用度取决于刀具材料的红硬性、耐磨性和冲击韧性。
yg类硬质合金中含钴量较多时,抗弯强度和冲击韧性好,特别是提高了疲劳强度,因此适于在受冲击和震动的条件下作粗加工用;含钴量较少时,其硬度、耐磨性和耐热性较高,适合作连续切削的精加工。
yt类硬质合金具有较高的硬度和较高的耐热性,但与yg类硬质合金相比,其强度低、脆性大,导热性差。
因此,切削高锰钢时通常选用韧性好的yg类硬质合金作刀具材料。
应当注意的是,yg类硬质合金不适于高速切削,因为在高速切削钢料时,切削时的高温将使刀具前刀面上形成强烈的月牙洼磨损,并加速后刀面磨损,刀具耐用度降低。
在切削速度较高且切削过程较平稳的情况下可考虑选用yt类硬质合金作刀具材料。
yg类硬质合金中添加适量的(一般为0.5%~3%左右)tac(碳化钽)或nbc(碳化铌),可提高其硬度和耐磨性而不降低其韧性。
切削高锰钢可选硬质合金牌号有:yg8、yg6a、yg6x、yg8n、yw1、yw2a、yw3、yc45、767、798、813等。
采用陶瓷刀片进行高锰钢的精车、半精车,但不能加工粗车,可选用较高的切削速度,加工表面质量好,刀具耐用度高。
例如利用al2o3基陶瓷刀具切削50mn18cr4高锰钢比用硬质合金刀具效率提高1~4倍。
采用cbn(立方氮化硼)刀具:CBN刀具可以对高锰钢进行粗车,半精车,精车。
高锰钢ZGMn13的钻削加工小乔nbsp2010年1

高锰钢ZGMn13的钻削加工小乔 nbsp 2010年1 高锰钢ZGMn13的钻削加工小乔nbsp 2010年1高锰钢ZGMn13的钻削加工 2010年11月11日大连交通大学许立陈志慧摘要:高锰钢ZGMn13作为一种典型的难加工材料,由于其优良的耐磨性,价格低廉,所以广泛的应用于受冲击较大的零部件,本文在介绍高锰钢ZGMn13基本性能和钻削加工性的基础上.阐述了实践中可以用于ZGMn13钻削加工的刀具结构和材料。
关键词:ZGMn13;钻削;加工硬化;硬质合金;钻头1.引言自1882年英国人哈德菲尔德(Hadfield)发明了高锰钢.它的使用已经有一百多年的历史。
成为传统的耐磨材料,得到了广泛应用。
如挖掘机的铲斗、破碎机的颚板和衬板、坦克的履带板、主动轮、从动轮和履带支承滚轮、铁路辙叉等。
ZGMn13钢的耐磨特性是其它任何钢种不可比拟的。
但是,其有良好的工作性能的同时又表现出在对其进行切削时的难加工性。
它是一种典型的难加工材料,特别是在孔加工当中,由于钻削本身属于半封闭式加工,使得ZGMn13钢的钻削更加困难。
2.ZGMn13钢的基本性能ZGMn13钢的主要成分为:1.30%C、0.30%,0.80%Si、11.0%,14.0%Mn(Mn/C=10,12)。
ZGMn13钢铸件的性质硬而脆.机加工比较困难,不能实际应用。
其原因是在铸态组织中存在着碳化物。
实践证明,ZGMn13钢只有在全部获得奥氏体组织时才呈现出最为良好的韧性和耐磨性。
为了使ZGMn13钢得到良好纯奥氏体组织,必须进行“水韧处理”。
水韧处理是淬火处理的操作,其方法是把钢加热至临界点温度以上(约1000—1100?)保温一段时间,使钢中碳化物能全部溶解到奥氏体中去,然后迅速浸淬于水中冷却。
由于冷却速度非常快,碳化物来不及从奥氏体中析出,因而保持了均匀的奥氏体状态。
ZGMn13的原始硬度与45号钢(正火)相近,约为HB180,220。
当ZGMn13钢受到强大的冲击时.表面层硬度迅速提高到HB450,550,这种加工硬化层能够达到0.3mm。
Mn13高锰钢性能特点
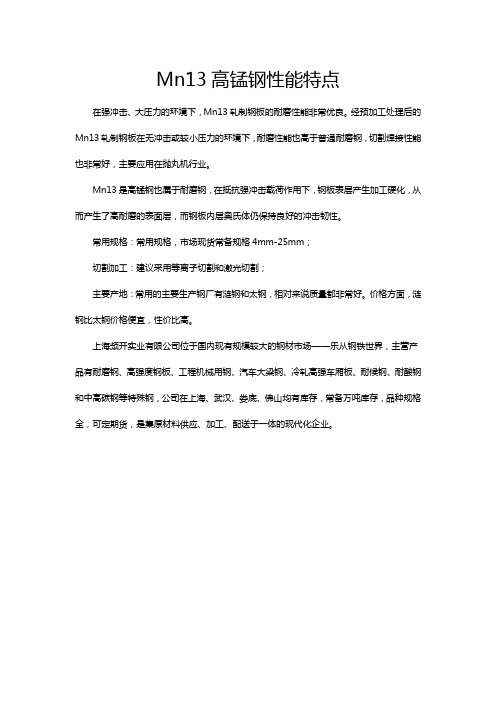
Mn13高锰钢性能特点
在强冲击、大压力的环境下,Mn13轧制钢板的耐磨性能非常优良。
经预加工处理后的Mn13轧制钢板在无冲击或较小压力的环境下,耐磨性能也高于普通耐磨钢,切割焊接性能也非常好,主要应用在抛丸机行业。
Mn13是高锰钢也属于耐磨钢,在抵抗强冲击载荷作用下,钢板表层产生加工硬化,从而产生了高耐磨的表面层,而钢板内层奥氏体仍保持良好的冲击韧性。
常用规格:常用规格,市场现货常备规格4mm-25mm;
切割加工:建议采用等离子切割和激光切割;
主要产地:常用的主要生产钢厂有涟钢和太钢,相对来说质量都非常好。
价格方面,涟钢比太钢价格便宜,性价比高。
上海频开实业有限公司位于国内现有规模较大的钢材市场——乐从钢铁世界,主营产品有耐磨钢、高强度钢板、工程机械用钢、汽车大梁钢、冷轧高强车厢板、耐候钢、耐酸钢和中高碳钢等特殊钢,公司在上海、武汉、娄底、佛山均有库存,常备万吨库存,品种规格全,可定期货,是集原材料供应、加工、配送于一体的现代化企业。
Mn13技术协议Mn13高锰钢特点Mn13机械性能

Mn13技术协议Mn13高锰钢特点Mn13机械性能
Mn13高锰钢的特点:一是外来冲击载荷越大,其自身表层耐磨性越高;二是随着表面硬化层的逐渐磨损,新的加工硬化层会连续不断形成。
Mn13高锰耐磨钢板交货状态:固溶热处理
Mn13高锰耐磨钢板化学成分
Mn13钢板标准要求化学成分
Mn13高锰钢化学成分成品分析
Mn13高锰耐磨钢板力学性能
Mn13钢标准要求力学性能
Mn13高锰钢机械性能
Mn13钢板为奥氏体加工硬化钢,在遭受震动或物料强冲击后具有高水平的耐磨损的特性,在冲击载荷磨损工况下使用,具有表面奥氏体组织形变诱发马氏体相变的特性,表层硬度和强度随着组织的相强变化、位错强化而急剧提高,但是其基体内层组织仍然为奥氏体,仍具有较高的塑韧性。
高锰耐磨钢Mn13是抵抗强冲击、大压力物料磨损等耐磨材料中的有效客观选择,具有其它耐磨材料无法比拟的加工硬化特性,在较大冲击载荷或较大接触应力的作用下,钢板表层产生加工硬化,表面硬度由HB200迅速提升到HB500以上,从而产生高耐磨的表面层,而钢板内层奥氏体仍保持良好的冲击韧性。
Get清风车削加工高锰钢耐磨铸件刀具材质及切削参数解决高硬度铸件难于加工问题
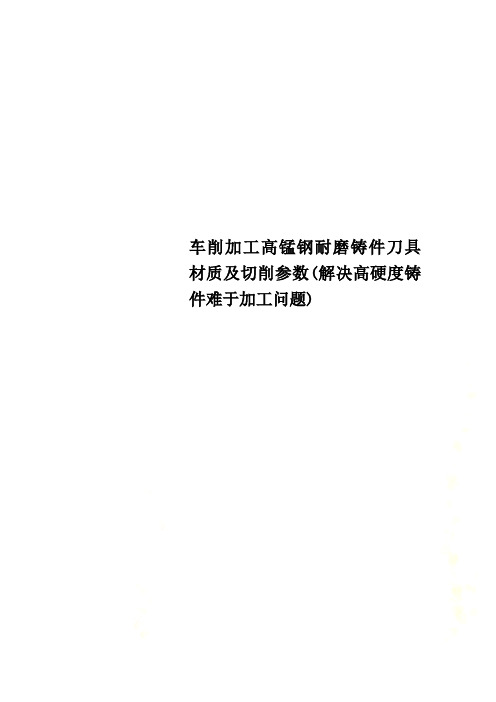
车削加工高锰钢耐磨铸件刀具材质及切削参数(解决高硬度铸件难于加工问题)车削加工高锰钢耐磨铸件刀具材质及切削参数〔解决高硬度铸件难于加工问题〕高锰钢材质〔ZGMN13〕加工〔粗车〕遇到刀具车不动,掰刀〔加工效率低下〕问题,品牌市场部高锰钢铸件一般存在铸造缺陷夹渣砂孔,刀具经常出现掰刀,崩刃。
高锰钢材质工件由于这些铸造缺陷造成了刀具难于切削加工问题。
车削工时短、加工余量小的,刀具牌号常选YS8、YW1合金,陶瓷刀具。
如果工件大或加工余量大,车削硬化会非常严重,如果是批量生产,用加夹车刀最划算。
有夹砂、断续车等恶劣工况,硬质合金刀头就会非常吃力造成粗车崩刀,精车烧刀。
针对高锰钢材质耐磨铸件可选用BN-K1材质刀具,此BN-K1材质刀片性能:硬度高,抗冲击性强,韧性好,耐高温。
BN-K1材质追求高的抗冲击性能,针对高硬度短铁屑工件研发,具备高硬度的同时,其抗冲击性能更优异,适合大余量粗加工高硬度铸铁件如高铬合金,高锰钢,高镍铬合金,冷硬铸铁,白口铸铁;广泛应用于矿山机械,冶金机械,水泥、电力设备耐磨备件行业。
零件的材料为铸造高锰钢〔ZGMn13〕,在加工过程中具有一下的特点。
高锰钢材料强度较高,尤其是高温时强度要比一般钢材大得多,再加工塑性变形大,加工时加工时硬化现象严重,因此在车削高锰钢材料时,车削力一般都比车削普通碳素钢时大得多。
车削温度高,高锰钢材料的导热系数都比拟低,车削过程中切削的塑性变形,使材料产生硬化,增大了切削抗力,加快车刀的磨损,甚至产生崩刀容易粘刀,高锰钢由于加工硬化严重,容易产生冷焊和熔焊等粘刀现象。
粘刀不利于切屑的排除,容易使铁屑堵赛,刀具容易崩刃或打刀,以及使刀具产生粘结磨损。
加工高锰钢难点主要是高锰钢机加工过程存在加工硬化现象,且由于加工高锰钢防止不了高锰钢铸件外表夹砂问题比拟费刀具。
华菱超硬品牌加工高锰钢刀具牌号为BN-K1.广泛应用于加工高锰钢,提高高锰钢机加工效率,降低高锰钢机加工刀具本钱。
高锰钢ZGMn13的钻削加工
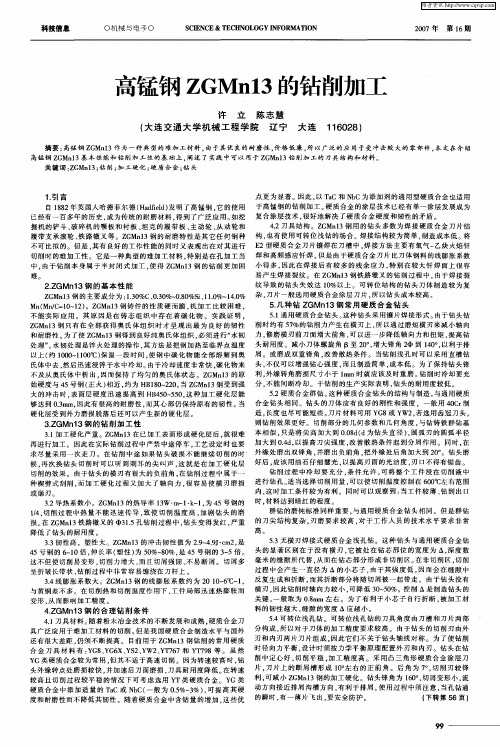
关 键 词 : G 1 ; 削 ; 工硬 化 ; 质 合 金 ; 头 Z Mn 3 钻 加 硬 钻
1 引 言 .
点 更 为显 著 。因此 , T C和 N C为 添 加 剂 的通 用 型 硬 质 合 金 也 适用 以 a b
硬 自 18 8 2年英 国人 哈 德 菲尔 德 ( d e ) 明 了高 锰 钢 . 的使 用 于 高锰 钢 的钻 削 加 工 。 质 合 金 的 涂 层 技 术 已经 有 单 一 涂 层 发 展 成 为 Haf l 发 id 它 已经 有 一 百 多 年 的历 史 。 为传 统 的耐 磨 材 料 , 到 了 广 泛 应 用 。 挖 复 合涂 层 技 术 , 好 地 解 决 了硬 质 合 金 硬 度 和韧 性 的矛 盾 。 成 得 如 很 42刀 具 结 构 。Z Mn 3钢用 的 钻 头 多 数 为 焊 接 硬 质 合 金 刀 片结 . G 1 掘 机 的铲 斗 、 破碎 机 的 颚 板 和 衬 板 、 克 的 履 带 板 、 动 轮 、 动轮 和 坦 主 从 也 制 履 带支 承 滚轮 、 路 辙叉 等 。Z Mn 3钢 的 耐磨 特 性 是 其 它 任 何 钢 种 构 , 有使 用 可转 位 浅 钻 的场 合 。焊接 结 构 较 为 简 单 , 造 成本 低 。将 铁 G l 2型硬 质 合 金 刀 片 镶 焊 在 刀 槽 中 , 接 方 法 主 要 有 氧 气 一 炔 火 焰钎 焊 乙 不可 比拟 的。 但 是 , 其有 良好 的工 作 性 能 的同 时 又 表 现 出在 对 其 进 行 E 但是 由于硬质合金刀片比刀体钢料 的线膨胀系数 切 削时 的难 加 工 性 。 它是 一 种 典 型 的难 加 工 材 料 , 别 是 在 孔 加 工 当 焊和高频感应钎焊 。 特
高锰钢的切削加工性讲解

返回
刃倾角
• 为了保持刀尖部分的强度,切削高锰钢时 一般应选择负刃倾角。
• 选用硬质合金刀具时,λs =-5°~0°。
• 选用陶瓷刀具时,λs =-10°~-5°。
刀尖圆弧半径
• 切削高锰钢时,不论采用何种刀具材料,刀尖 部分都应修磨出较大的圆弧半径,以加强刀 尖强度,提高刀具耐用度.一般粗车时rε=1~ 2 mm;半精车时 rε=0.5~1 mm;精车时 rε=0.2~0.5mm。工艺系统刚性好时取大 值,反之取小值 。
前后角
主副偏角
刃倾角
前角与后角
1. 切削高锰钢时,为了减轻加工硬化,要求刀具保持 锋利.但一般不可以采用大前角,因为前角大不利 于保证刃口强度和改善散热条件.常采用较小前 角或负前角及较大后角,但后角太大也会削弱刃 口强度引起崩刃。 2. 采用硬质合金刀具时,γ0=-3°~3°, α0=8°~12°;采用陶瓷刀具时,γ0=-5°~10°,α0=5°~10°。粗车时取小值,精车时取 大值。
返回
铣削ZGMn13的刀具磨损曲线
结束
水韧处理:
所谓水韧处理,就是把钢加热到1000℃~ 1100℃,保温一段时间,使钢中的碳化物全部 溶入奥氏体中,然后迅速冷却,使碳化物来不 及从奥氏体中析出,从而保持了单一的均匀 的奥氏体组织.
铁碳合金相图
返回
高锰钢在切削过程中,由于塑性变形大, 奥氏体组织转变为细晶粒的马氏体组织, 从而产生严重的硬化现象。加工前硬度一 般为HBS200~220,加工后表面硬度可达 HBW450~550,硬化层深度0.1~0.3 mm, 其硬化程度和深度要比45号钢高几倍。严 重的加工硬化使切削力增大,加剧了刀具 磨损,也容易造成刀具崩刃而损坏。
4. 高锰钢在切削过程中,由于塑性变形和切 削力的影响,切削层及表层下一定深度范围 内会产生严重的加工硬化现象。为了使刀 尖避开毛坯表层和前一次走刀造成的硬化 层,应选择较大的切削深度和进给量。 5. 一般粗车时αp =3~6 mm,f=0.3~0.8 mm/r;大件粗车时可取αp =6~10 mm; 半精车时αp =1~3 mm;f=0.2~0.4 mm/r;精车时口αp ≤1 mm;f≤0.2mm/r。
ZGMn13高锰钢的切削加工特点
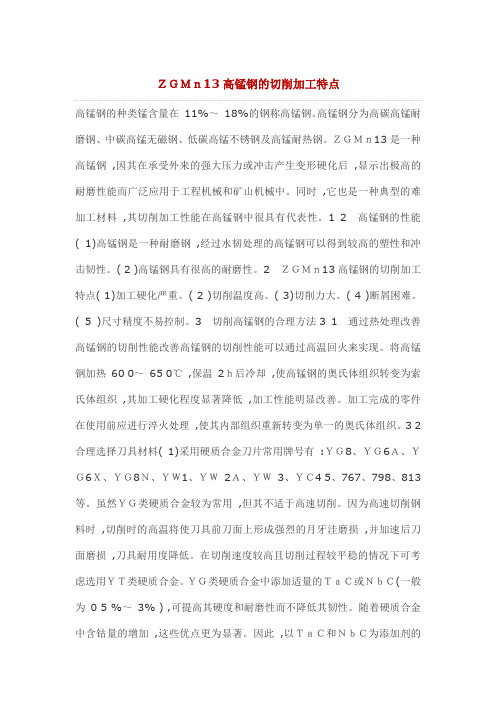
高锰钢的种类锰含量在11%~18%的钢称高锰钢。
高锰钢分为高碳高锰耐磨钢、中碳高锰无磁钢、低碳高锰不锈钢及高锰耐热钢。
ZGMn13是一种高锰钢,因其在承受外来的强大压力或冲击产生变形硬化后,显示出极高的耐磨性能而广泛应用于工程机械和矿山机械中。
同时,它也是一种典型的难加工材料,其切削加工性能在高锰钢中很具有代表性。
1 2高锰钢的性能( 1)高锰钢是一种耐磨钢,经过水韧处理的高锰钢可以得到较高的塑性和冲击韧性。
( 2 )高锰钢具有很高的耐磨性。
2ZGMn13高锰钢的切削加工特点( 1)加工硬化严重。
( 2 )切削温度高。
( 3)切削力大。
( 4 )断屑困难。
( 5 )尺寸精度不易控制。
3切削高锰钢的合理方法3 1通过热处理改善高锰钢的切削性能改善高锰钢的切削性能可以通过高温回火来实现。
将高锰钢加热60 0~65 0℃,保温2h后冷却,使高锰钢的奥氏体组织转变为索氏体组织,其加工硬化程度显著降低,加工性能明显改善。
加工完成的零件在使用前应进行淬火处理,使其内部组织重新转变为单一的奥氏体组织。
3 2合理选择刀具材料( 1)采用硬质合金刀片常用牌号有:YG8、YG6A、YG6X、YG8N、YW1、YW2A、YW3、YC4 5、767、798、813等。
虽然YG类硬质合金较为常用,但其不适于高速切削。
因为高速切削钢料时,切削时的高温将使刀具前刀面上形成强烈的月牙洼磨损,并加速后刀面磨损,刀具耐用度降低。
在切削速度较高且切削过程较平稳的情况下可考虑选用YT类硬质合金。
YG类硬质合金中添加适量的TaC或NbC(一般为0 5 %~3% ) ,可提高其硬度和耐磨性而不降低其韧性。
随着硬质合金中含钴量的增加,这些优点更为显著。
因此,以TaC和NbC为添加剂的通用型硬质合金也适用于高锰钢的切削加工。
( 2 )采用金属陶瓷刀片采用金属陶瓷刀片进行高锰钢的精车、半精车,可选用较高的切削速度,加工表面质量好,刀具耐用度高。
高锰钢的切削加工性教材
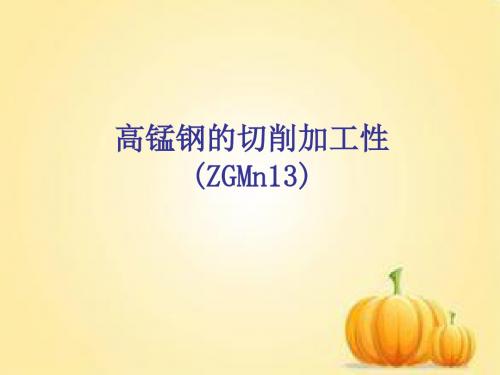
铣削ZGMn13的刀具磨损曲线
结束
水韧处理:
所谓水韧处理,就是把钢加热到1000℃~ 1100℃,保温一段时间,使钢中的碳化物全部 溶入奥氏体中,然后迅速冷却,使碳化物来不 及从奥氏体中析出,从而保持了单一的均匀 的奥氏体组织.
铁碳合金相图
返回
高锰钢在切削过程中,由于塑性变形大, 奥氏体组织转变为细晶粒的马氏体组织, 从而产生严重的硬化现象。加工前硬度一 般为HBS200~220,加工后表面硬度可达 HBW450~550,硬化层深度0.1~0.3 mm, 其硬化程度和深度要比45号钢高几倍。严 重的加工硬化使切削力增大,加剧了刀具 磨损,也容易造成刀具崩刃而损坏。
高 锰 钢 金 相 组 织
高锰钢的切削加工特点:
1. 2. 3. 4. 5. 加工硬化严重 切削力大 切削温度高 断屑困难 尺寸精度不易控制
切削高锰钢的合理方法:
一、通过热处理改善切削加工性 二、合理选择切削刀具的刀具材料 三、合理选择刀具几何参数 四、合理选择切削用量
切削前的热处理
改善高锰钢的切削性能可以通过高温回 o 火来实现。将高锰钢加热 600-650 C 保温 2h 后冷却,使高锰钢的奥氏体组织转变 为索氏体组织,其加工硬化程度显著降 低,加工性能明显改善。加工完成的零 件在使用前应进行淬火处理,使其内部 组织重新转变为单一的奥氏体组织。
刃口倒棱
• 为了保证刃口有足够的强度,减少崩刃现象, 一般应将刃口修磨出负倒棱. • 硬质合金刀具倒棱宽度 bγ1=0.2~0.8 mm, 倒棱前角 γ01=-10°~-5°;如采用陶瓷刀 具,bγ1=0.2 mm,γ01=-20°。
切削用量选择
1. 高锰钢的切削加工性很差,为了维持一定的 刀具耐用度,切削速度应低些 。 2. 采用硬合金刀具时, Vc=20~40 m/min,其 中,较低的速度用于粗车,较高的速度用于 半精车和精车。 3. 采用陶瓷刀具时, 可以选用较高的切削速 度, 一般 Vc=50~80 m/min 。
ZGMn13对切削刀具的要求

① 硬质 合金 ( Yw) 具 。 一5—8 , 加 工 时 取 刀 取 。粗 小 值 , 加 工 时 取 大 值 。 且 要 强 化 切 削 刃 磨 出 负 倒 棱 精 并 ( 一 负倒 棱 宽 度 b 第 0 2~0 8mm,第 一 负 倒 棱 前 . .
Z M l . 5~1 3 10 G n 3—30 9 . 51. O~1 .0 40
≤00 5≤00 0 . 3 . 7
≤3 0 0 复杂件 用于结构复杂 , 以韧性为主的高
n 3—4O 9 l . O一12 .O
03 . O~0 8 .O
≤0
.
0 0 4
C 15 2 5 3 O r.O~ . 0 ≥7 5≥2
C Mn S i S P 其 它
力 学 性 能 o & r b a k
硬 度 用 途
MP % ( c . B a J・ m S H
Z Mn 3—110 G l .O~14 .5 Z Mn3— .O~1 3 G l 20 9 .5
Z GM
可避免地 会受 到刀具 的剧烈 冲击 和摩擦 , 而在第 一 、 从 第 二 、 三 变 形 区都 会 产 生 加 工 硬 化 。 一 变 形 区 的 加 第 第
表 1 高 锰 钢 铸 件 ( B T 6 0—1 9 ) 能 、 分及 用 途 G / 58 98性 成 化学成分 / % 牌 号
加 剧 。 就 使 得 高 锰 钢 的切 削 加 工 难 上 加 难 。 这
钢 , 般 俗 称 为 “ 锰 钢 ” 我 国 高 锰 钢 铸 件 的 国 家 标 准 一 高 。
GB/ 6 0— 1 9 的 牌 号 有 : GMn 3—1 ZG T5 8 98 Z l 、 Mn 3—2、 l
高锰钢的切削加工

高锰钢的切削加工1.高锰钢有哪几种?其性能如何?锰含量约为11%~18%的钢称高锰钢。
常用的铸造高锰钢ZMn13的化学成分为:Mn含量11%~14%,c含量1.0%~1.4%,Si含量0.3%~1.0%,P含量<0.03%,S含量<0.05%。
高锰钢是一种耐磨钢,经过水韧处理的高锰钢可以得到较高的塑性和冲击韧性。
所谓水韧处理,就是把钢加热到1000℃~1100℃,保温一段时间,使钢中的碳化物全部溶入奥氏体中,然后迅速冷却,使碳化物来不及从奥氏体中析出,从而保持了单一的均匀的奥氏体组织。
经过水韧处理的高锰钢称为高锰奥氏体钢。
其力学性能为:σb=980 MPa,σs=392 MPa,HB210,δ=80%,αk=2.94 MJ /m2。
高锰钢具有很高的耐磨性,虽然它的硬度只有HB210,但它的屈服点σs较低,只有σb的40%,因此具有较高的塑性和韧性。
高锰钢在受到外来压力和冲击载荷时,会产生很大的塑性变形或严重的加工硬化现象,钢被剧烈强化,硬度显著提高,可达HB450~550,因此有了较高的耐磨性。
高锰钢可分为高碳高锰耐磨钢、中碳高锰无磁钢、低碳高锰不锈钢和高锰耐热钢。
几种高锰钢的牌号和性能见表5-1。
2.高锰钢有哪些切削加工特点?高锰钢锰含量高达11%~18%,具有较高的塑性和韧性,在切削加工中有以下特点:(1)加工硬化严重:高锰钢在切削过程中,由于塑性变形大,奥氏体组织转变为细晶粒的马氏体组织,从而产生严重的硬化现象。
加工前硬度一般为HB200~220,加工后表面硬度可达HB450~550,硬化层深度0.1~0.3 mm,其硬化程度和深度要比45号钢高几倍。
严重的加工硬化使切削力增大,加剧了刀具磨损,也容易造成刀具崩刃而损坏。
(2)切削温度高:由于切削功率大,产生的热量多,而高锰钢的导热系数比不锈钢还低,只有中碳钢的1/4,所以切削区温度很高。
当切削速度Vc<50 m/min 时,高锰钢的切削温度比45号钢高200℃~250 ℃,因此,刀具磨损严重,耐用度降低。
高锰钢切削加工工艺性能的分析

高锰钢切削加工工艺性能的分析作者:孙广军来源:《工业设计》2018年第04期摘要:本文论述了高锰钢材料的特性,列举了高锰钢零件切削加工工艺性能及切削加工加工过程中经常出现的不良现象,分析了出现切削问题的原因,并以高锰钢材料的车削加工为例指出了提高切削加工工艺性能的刀具参数、切削用量和辅助切削的特殊方法,为提高高锰钢材料的切削效率提供参考。
关键词:高锰钢;切削加工;切削加工工艺参数高锰钢是一种耐磨钢,锰的含量通常在1O%-18%之间。
在常温下,通过对高锰钢进行水韧处理,可得到均匀启勺单相奥氏体组织,单相奥氏体组织的强度、硬度比较低,具有很好的塑性及韧性。
当材料表面遇到冲击、突然加压或摩擦后发生塑性变形,同时材料表面被剧烈强化,硬度可达HBW450-550,表面获得良好的耐磨性,同时材料内部仍保持良好的塑性及韧性。
由于高锰钢具有良好的耐磨性能及抗冲击性能,其广泛应用于采石、挖掘、采矿、铸造、煤炭工业及钢铁行业。
由于高锰钢组织具有导热系数低、线膨胀系数大、伸长率大和易加工硬化等特点,造成高锰钢材料切削加工工艺性能很差,车削加工的过程中容易出现加工硬化、切削力大、切削温度高、加工精度低及断屑困难的问题。
严重影响了高锰钢制品的成品率机加工效率,造成高锰钢制品加工成本提高。
因此需要根据高锰钢材料的特性探索合理的切削加工工艺参数,有效地解决高锰钢的切削加工难题。
1高锰钢切削加工过程中容易出现的问题1.1加工硬化由于水韧处理后的高锰钢组织为均匀的单相奥氏体组织,由于面心立方晶格的结构特点,受到外力作用晶格容易发生滑移,同时诱发硬度较低的奥氏体组织转变为高硬度的马氏体组织,使材料加工面发生加工硬化现象(硬度可达HBW 500)。
使))具磨损严重。
1.2切削力大,刀尖处应力集中严重经X射线衍射仪及比对标准卡片分析得出高锰钢工件在切削过程中,材料表面会发生氧化反应生成Mn203,经金相显微镜测定氧化层厚度约为o.1-o.3mm。
高锰钢切削加工工艺性能的分析

技术与实践INDUSTRIAL DESIGN 工业设计 / 137作者简介孙广军/1963年生/男/天津人/中级工程师/研究方向为高锰钢材料ZGMn13车削加工或钻削(山西运城043605)高锰钢切削加工工艺性能的分析ANAL YSIS ON THE CUTTING PROCESS PERFORMANCE OF HIGH MANGANESE STEEL国营华晋冶金铸造厂 孙广军1.2切削力大,刀尖处应力集中严重经X 射线衍射仪及比对标准卡片分析得出高锰钢工件在切削过程中,材料表面会发生氧化反应生成Mn 2O 3,经金相显微镜测定氧化层厚度约为0.1~0.3mm 。
氧化层的存在使切削力显著增加。
经实验测定利用硬质合金刀具车削高锰钢外圆时的切削力是普通中碳钢的1.6倍左右。
用YG 类硬质合金刀具车削高锰钢工件时,车削速度小于20m/min 时刀具前刀面上的平均应力约为1000Mpa ,是普通中碳钢的3~4倍。
刀尖处为应力集中点,容易造成刀具嘣刃。
1.3切削温度高由于高锰钢工件需要较大的切削力及切削功率,因此,工件表面因切削产生的热量多,加上高锰钢材料导热系数低,工件表面切削区的温度很高,刀具切削刃热磨损严重,降低车刀的使用寿命。
1.4加工精度低由于高锰钢材料导热系数低,工件切削温度高,加上高锰钢材料的线膨胀系数大,导致工件加工面易产生热变形,影响车削精度。
同时,在高温、高压作用下刀具易形成积屑瘤和鳞刺,造成工件加工面粗糙度大且加工精度低。
1.5切屑韧性大,强度高,不易断屑经过水韧处理后的高锰钢组织为均匀的单相奥氏体组织,具有极高的韧性,约为45#钢的8倍,材料的伸长率大及变形系数都比较大,切削加工时切屑不易卷曲和断屑,处理困难。
2改善高锰钢切削加工工艺性能的措施2.1加工前后进行热处理高锰钢工件加工之前,高锰钢工件加热至600~650摄氏度,保温两小时后冷却,这种热处理方式为高温回火处理,高温回火处理可使高锰钢内部的奥氏体组织转变为索氏体组织,回火索氏体比奥氏体具有更好的机械性能,有效降低了高锰钢切削加工时的加工硬化现象,从而改善了高锰钢的切削加工性能。
高锰钢加工

一、高锰钢的特性和切削加工性
高锰钢是一种机械行业常用的耐磨钢,有些衬板类无需加工,但有些零件,由于其设计需要又不得不加工。高锰钢常采用水韧处理,即把铸件加热到1000-1100°C后,急速水冷,使碳化物来不及从奥氏体中析出,从而获得单一均匀奥氏体金相组织,这时的高锰钢才具有较好的使用性能;如高强度,高韧性,高耐磨性。其重要性能是,在较大的冲击或接触应力的作用下,表层迅速产生加工硬化,能承受很大的冲击载荷。
(2)后角:为了减小后面的摩擦与磨损,减轻加工表面的加工硬化,后角α0=6 °-13 °,粗车时取小值,精车时取大值。
(3)切削用量
1.吃刀量,加工高锰钢时,吃刀量宜取中等数值,既避免切削力过大,又避免加速刀具磨损。一般我们选用:粗车ap=5-6mm,精车ap=0.5-1mm。2.进给量。由于加工高锰钢时硬化层深度较大,因而进给量宜选较大值。一般取f=0.2-0.3mm/r。3.切削速度,用硬质合金刀具加工高锰钢时,切削力大,切削温度高,刀具磨损快,所以切削速度不宜太快。一般取Vc=20-30m/min,其中较低的速度用于粗车,较高的速度用于半精车或精车。
三、高锰钢的合理切削条件
经过多达十多种盘类零件和轴类零件的车削加工,我们总结出了高锰钢的合理加工工艺。
(一)刀具材料:优先采用YM052,YM053刀具材料
(二)刀具几何参数及角度如下:
(1)前角:针对高锰钢切削力大和导热性差的特点,刀具的前角应选用较小值,以增强切削刃强度和散热体积。一般前角γ0=-5 °-8°,粗车时取小值,精车时取大值。
高锰钢的切削加工性很差,具有以下特点:
1.切削时,塑性变形大,加工硬化严重。致使单位切削力很大,车外圆时比加工45号钢增大60%以上。2.由于切削力大,使单位切削功率增大,单位时间内产生的热量多,而高锰钢自身导热性能又差,致使切削区温度高达1000°C以上,刀具磨损严重,刀具寿命低。3.高锰钢塑性大,切削时易形成积屑瘤和鳞刺。4.切屑强度大,韧性高,不易折断。
高锰钢的性能特点及强化原理

《材料冶金学》专题之一高锰钢的性能特点及强化原理1概述自Hadfield 1882年发明高锰钢以来,至今已有100多年的历史。
高锰钢一般是指含碳量为0 9%~1 3%,含锰量为11 0%~14 0%的铸钢,即ZGMn13。
此材料在1000~1100℃之间为单一奥氏体组织,为保持此组织,需高温淬火,即在1100~1050℃间的温度内立即水淬至常温。
经过处理后的材料具备很好的韧性,受冲击载荷时发生表面硬化,其具有很高的耐磨性,故称之为耐磨钢。
因此高锰钢被广泛应用于机械制造、冶金、矿山、建材、电力和铁路等部门所使用的金属耐磨体,如挖掘机斗齿、球磨机衬板、破碎壁、轧臼壁、拖拉机履带板、风扇磨冲击板、破碎机颚板、铁道路岔等。
但由于此材料加工硬化快,不易切削加工,一般只限于铸造。
2高锰钢的性能特点2.1高锰钢的机械性能高锰钢的铸态组织是由奥氏体、碳化物、珠光体和通常存在的少量磷共晶等所组成。
碳化物数量多时会在晶界上以网状出现,钢的性能很脆。
这种低塑性、低韧性的钢在铸态下是无法使用的。
但通过固溶处理(即水韧处理)后,在强冲击工况下它变成一种高强度、高塑性、韧性好、特别耐磨的材料。
其性能对比如表1:σb (Mpa)σ0.2(Mpa)δ(%)αKJ/cm2HB铸态性能343.23―392.27 294.20―490.330.5―59.80―29.42200―300水韧处理性能617.82―1274.86343.23―470.7215―85196.13―294.20180―225表1:高锰钢在铸态下和水韧处理后性能对比以上是高锰钢在常温下的各种机械性能,但具有奥氏体组织的高锰钢在加热时会发生组织转变,性能会发生很大的变化。
当温度超过125℃时,在奥氏体中开始有碳化物析出。
随着温度的提高析出量增加,钢的性能变脆,塑、韧性下降。
图1是高锰钢经1050℃水韧处理后加热温度和延伸率的关系;图2是化学成分为 C1.12%, Mn13.56%, Si0.63%, S0.012%,P0.092%, Ti0.06%的高锰钢,经水韧处理后加热到不同温度,保温5小时水冷后测得的冲击韧性。
硬质合金群钻钻削ZGMn13高锰钢干切削实验研究
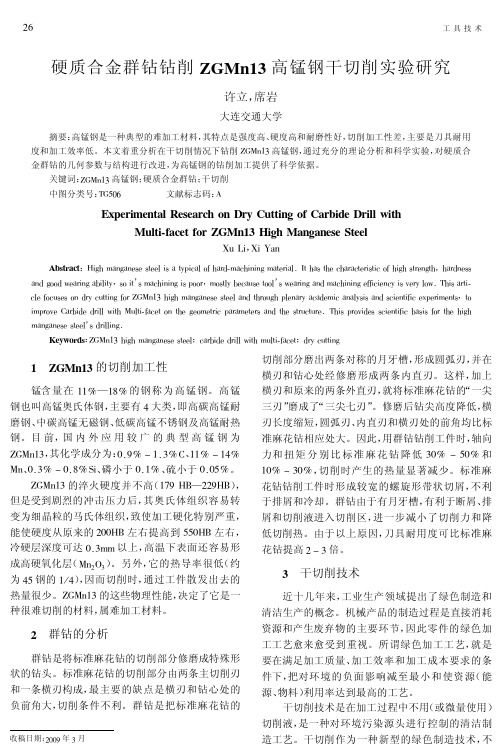
! 钻削实验
! " # 切削用量的优化 在切削加工中, 切削用量选用得合理与否, 直接 影响到加工质量、 生产成本和生产效率。长期以来, 金属切削加工中的切削用量是从有关切削手册中查 取或凭经验确定的, 但从切削用量手册上只能得到 一个范围值, 很难得到一个最优的切削用量。在实 际生产中, 由于使用的机床、 刀具及工件材料等具体 条件不同, 有时无法凭借手册或经验确定最合理的 切削用量, 而通过试验来获取切削用量成本高且效 率低, 可以充分利用计算机辅助切削用量的优化方 法寻求最佳的切削用量。 在切削用量三要素中, ! 主要取决于孔径的大 小, 根据生产实际的需要为某些定值, 而不参与优 化。因此切削用量的优化主要是切削速度 " 及进给 量 # 的优化组合。以单个工序用最大生产效率作为 标准, 目标函数的自变量为进给量 # 和主轴转速 $ 。 当切削速度及进给量取某一数值时, 可使生产效率 最大, 这一数值就是最优的切削用量。以刀具耐用 度 %、 机床功率 & 、 主轴转速 $ 及刀具进给量 # 为约 束条件, 根据切削速度 " 及进给量 # 的取值范围, 采 用 !"#$"% 编制了求解程序用以计算目标函数, 进 而优化切削用量。优化结果如下: 进给量 ! & ’()), 主轴转速 $ & ./( - , )01。 # & (*(+)) , -, ! " $ 刀具材料的优选 目前, 切削难加工材料 (如 23!1’4 等) 应用较 多的刀具材料有: 硬质合金、 陶瓷、 立方氮化硼刀具 等。陶瓷刀具的最大缺点是脆性大、 强度低, 它的导 热系数比硬质合金低而热膨胀系数却高于硬质合金 特别是抗疲劳强度及抗断裂韧性低的 ’(5 6 4(5 ,
高锰钢零件的车削加工
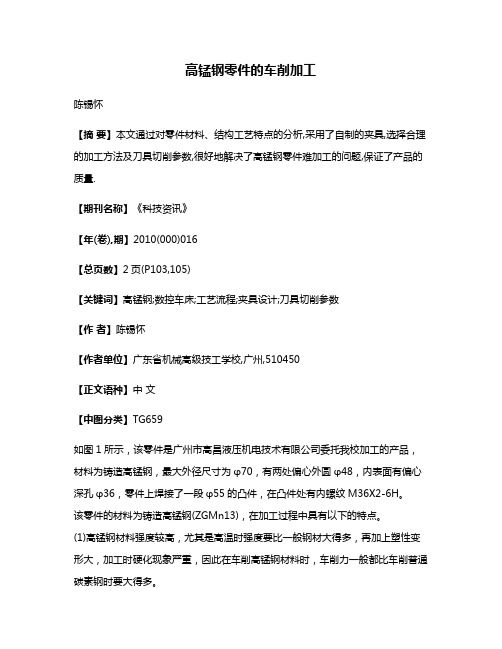
高锰钢零件的车削加工陈锡怀【摘要】本文通过对零件材料、结构工艺特点的分析,采用了自制的夹具,选择合理的加工方法及刀具切削参数,很好地解决了高锰钢零件难加工的问题,保证了产品的质量.【期刊名称】《科技资讯》【年(卷),期】2010(000)016【总页数】2页(P103,105)【关键词】高锰钢;数控车床;工艺流程;夹具设计;刀具切削参数【作者】陈锡怀【作者单位】广东省机械高级技工学校,广州,510450【正文语种】中文【中图分类】TG659如图1所示,该零件是广州市高昌液压机电技术有限公司委托我校加工的产品,材料为铸造高锰钢,最大外径尺寸为φ70,有两处偏心外圆φ48,内表面有偏心深孔φ36,零件上焊接了一段φ55的凸件,在凸件处有内螺纹M36X2-6H。
该零件的材料为铸造高锰钢(ZGMn13),在加工过程中具有以下的特点。
(1)高锰钢材料强度较高,尤其是高温时强度要比一般钢材大得多,再加上塑性变形大,加工时硬化现象严重,因此在车削高锰钢材料时,车削力一般都比车削普通碳素钢时要大得多。
(2)车削温度高,高锰钢材料的导热系数都比较低,车削时产生的切削热不易散开,使大量热量集中在刀尖处。
(3)高锰钢材料的变形系数一般都比较大,由于车削过程中切屑的塑性变形,使材料产生了硬化,增大了切削抗力,加快车刀的磨损,甚至产生崩刃。
(4)容易粘刀,高锰钢由于加工硬化严重,容易产生冷焊和熔焊等粘刀现象。
粘刀不利于切屑的排除,容易使铁屑发生堵塞,刀具容易崩刃或打刀,以及使刀具产生粘结磨损。
(1)首先在原料上划出偏心孔的中心,然后到钻床上将所有待加工产品都钻好φ30mm的偏心孔。
(2)用四爪卡盘夹紧φ 70mm的两端面,调试,车削凸台。
(3)在凸台上钻孔并扩好孔。
(4)车削内螺纹M36X2-6H。
(5)安装夹具,调试,夹持工件即夹紧凸台的端面与φ70mm的外圆,校正,检测。
(6)粗加工偏心外圆φ40,留0.3mm~0.5mm余量。
- 1、下载文档前请自行甄别文档内容的完整性,平台不提供额外的编辑、内容补充、找答案等附加服务。
- 2、"仅部分预览"的文档,不可在线预览部分如存在完整性等问题,可反馈申请退款(可完整预览的文档不适用该条件!)。
- 3、如文档侵犯您的权益,请联系客服反馈,我们会尽快为您处理(人工客服工作时间:9:00-18:30)。
高锰钢的种类锰含量在11%~18%的钢称高锰钢。
高锰钢分为高碳高锰耐磨钢、中碳高锰无磁钢、低碳高锰不锈钢及高锰耐热钢。
ZGMn13是一种高锰钢,因其在承受外来的强大压力或冲击产生变形硬化后,显示出极高的耐磨性能而广泛应用于工程机械和矿山机械中。
同时,它也是一种典型的难加工材料,其切削加工性能在高锰钢中很具有代表性。
1 2高锰钢的性能( 1)高锰钢是一种耐磨钢,经过水韧处理的高锰钢可以得到较高的塑性和冲击韧性。
( 2 )高锰钢具有很高的耐磨性。
2ZGMn13高锰钢的切削加工特点( 1)加工硬化严重。
( 2 )切削温度高。
( 3)切削力大。
( 4 )断屑困难。
( 5 )尺寸精度不易控制。
3切削高锰钢的合理方法3 1通过热处理改善高锰钢的切削性能改善高锰钢的切削性能可以通过高温回火来实现。
将高锰钢加热60 0~65 0℃,保温2h后冷却,使高锰钢的奥氏体组织转变为索氏体组织,其加工硬化程度显著降低,加工性能明显改善。
加工完成的零件在使用前应进行淬火处理,使其内部组织重新转变为单一的奥氏体组织。
3 2合理选择刀具材料( 1)采用硬质合金刀片常用牌号有:YG8、YG6A、YG6X、YG8N、YW1、YW2A、YW3、YC4 5、767、798、813等。
虽然YG类硬质合金较为常用,但其不适于高速切削。
因为高速切削钢料时,切削时的高温将使刀具前刀面上形成强烈的月牙洼磨损,并加速后刀面磨损,刀具耐用度降低。
在切削速度较高且切削过程较平稳的情况下可考虑选用YT类硬质合金。
YG类硬质合金中添加适量的TaC或NbC(一般为0 5 %~3% ) ,可提高其硬度和耐磨性而不降低其韧性。
随着硬质合金中含钴量的增加,这些优点更为显著。
因此,以TaC和NbC为添加剂的
通用型硬质合金也适用于高锰钢的切削加工。
( 2 )采用金属陶瓷刀片采用金属陶瓷刀片进行高锰钢的精车、半精车,可选用较高的切削速度,加工表面质量好,刀具耐用度高。
如采用A12 0 3基陶瓷刀具切削高锰钢,比用硬质合金刀具效率提高1~4倍。
( 3)采用CN2 5涂层刀片和CBN(立方氮化硼)刀具在使用CBN刀具时应注意被切削材料含锰量不能高于14% ,否则,CBN可能与Mn元素产生化学反应使刀具磨损严重,切削性能下降。
3 3合理选用刀具几何参数( 1)前角与后角采用硬质合金刀具时,γ0 =- 3~3° ,α0 =8~12° ;采用陶瓷刀具时,γ0 =- 5~- 10° ,α0 =5~10°。
粗车时取小值,精车时取大值。
( 2 )主偏角与副偏角采用硬质合金刀具时,一般取kr=2 5~ 4 5° ,kr′=10~ 2 0°。
工艺系统刚性好时取小值,反之可适当增大主偏角和副偏角;采用陶瓷刀具,主偏角还可大些,一般取kr=4 5~60°,精车时可取kr=60~90°。
( 3)刃倾角采用硬质合金刀具,λs=- 5~0° ;采用陶瓷刀具时,λs=- 10~- 5°。
( 4 )刀尖圆弧半径一般粗车时r=1~2mm;半精车时r=0 5~1mm;精车时r=0 2~0 5mm。
工艺系统刚性好时取大值,反之取小值。
3 4合理选择切削用量切削高锰钢时,切削速度不宜高。
采用硬质合金刀具时,vc=2 0~4 0m/min,其中,较低的速度用于粗车,较高的速度用于半精车和精车。
采用陶瓷刀具时,可以选用较高的切削速度,一般vc=5 0~80m/min。
高锰钢在切削过程中,由于塑性变形和切削力的影响,切削层及表层下一定深度范围内会产生严重的加工硬化现象。
因此应选择较大的切削深度和进给量。
一般粗车时ap=3~6mm,f=0 3~0 8mm/r;大件粗车时可取ap=6~10mm;半精车时ap=1~3mm;f=0 2~
0 4mm/r;精车时ap≤ 1mm;f≤ 0 2mm/r。
4钻削ZGMn13高锰钢应注意的问题ZGMn13高锰钢应用广泛,其锰含量高达11%~14%。
经水韧处理后,在受到剧烈冲击压力时,会产生很强的硬化现象,硬度可达HB4 5 0~ 5 5 0 ,硬化层深度达0 3mm左右,加之导热系数很低,给切削带来很大困难。
尤其在钻削时,刀具磨损严重,耐用度降低。
因此,常用硬质合金群钻钻削ZGMn13高锰钢。
钻削时应注意以下问题:( 1)合理设计切削部分参数常用硬质合金群钻的本体为 4 0Cr制造,切削部分为YG8或YW硬质合金。
切削部分的形状与铸铁群钻近似,将钻尖高加大到0 0 8D(D为钻头直径) ,圆弧刃的圆弧半径加大到0 4D,以提高刀尖强度,改善散热条件起到分屑作用。
同时,在外缘处磨出双重锋角,并磨出负前角,把外缘处后角加大到2 0°。
钻头磨好后,要用油石仔细鐾研刃口,不能有锯齿。
( 2 )合理选择切削用量切削速度太低或进给量太大,会使切削力增加,容易造成崩刃。
取vc=30~ 4 0m/min,f=0 0 7~0 1mm/r比较合适。
( 3)要充分使用冷却液高锰钢的线膨胀系数大,钻孔时使用切削液要充分,有条件的可将工件浸在冷却液中钻孔,以防止因孔的收缩将钻头咬死损坏。
( 4 )严格控制钻头磨钝标准钻削过程中如听到刺耳的尖叫声或发现钻头外缘转角处后角和棱边磨损约1mm时,应及时将钻头重磨,否则继续使用将加快钻头磨损以至损坏。
( 5 )严禁中途停车钻削时应采用自动进给,尽量不用手动进给,以免加重硬化现象,使钻削更加困难。
同时,严禁中途停车,以防切削力过大造成“闷车” ,使钻头崩碎。
( 6)机床状态良好硬质合金群钻钻削高锰钢时,要求机床刚性好、振动小。
硬质合金的韧性比高速钢低得多,强烈的振动和切削时的高温,会加快钻头磨损,造成崩刃或开焊。
5高
锰钢切削方法的新进展同其他难加工材料一样,高锰钢的切削加工也得到了广泛深入的研究,近些年来取得了一些成果。
行之有效的方法主要有以下几种:( 1)加热切削法加热切削是把工件的整体或局部通过各种方式加热到一定温度后再进行切削加工的一种方法。
其目的就是通过加热来软化工件材料,使工件材料的硬度、强度有所下降,易于产生塑性变形,减小切削力,提高刀具耐用度和生产率。
同时,改变切屑形态,减小振动,减小表面粗糙度值。
实验证明,用等离子加热车削高锰钢ZGMn13,刀具耐用度明显提高,换刀次数显著减少,效率提高5倍左右;加工后表面金相组织无变化,也无加工硬化。
( 2 )磁化切削法磁化切削是使刀具或工件或两者同时在磁化条件下进行的切削方法。
既可将磁化线圈绕于工件或刀具上,在切削过程中给线圈通电使其磁化,也可直接使用经过磁化处理的刀具进行切削。
实验表明,磁化切削可使工件表面粗糙度值减小,刀具耐用度明显提高。
据资料介绍,美国已开发成功交流脉冲磁化机,可磁化高速钢刀具、硬质合金刀具等,分别用于车削、铣削、刨削等。
在车削中,因刀具材料与工件材料的不同,可提高效率在 4 0 %~30 0 %。
( 3)低温切削法低温切削是指用液氮( - 186℃)、液体CO2( - 76℃)及其他低温液体切削液,在切削过程中冷却刀具或工件,以保证切削过程顺利进行。
这种切削方法可有效控制切削温度,减少刀具磨损,提高刀具耐用度,提高加工精度、表面质量和生产率。
近年来,低温切削技术在国外得到较大发展,国内也正积极研究。
难加工材料采用低温切削工艺的经济性和必要性主要取决于工件本身的价值和常温传统切削加工的成本,要综合考虑采用低温切削是否经济可行。