转子体压铸工艺分析及模具设计-毕业论文
压铸模具设计范文

压铸模具设计范文压铸模具设计是指为了生产压铸件而设计的模具,其主要任务是将液态金属注入模具中,并在模具中冷却、凝固,最终得到所需形状的金属零件。
压铸模具设计的主要工作包括设计模具的结构、选材、计算模具的合理尺寸和形状等。
一、压铸模具结构设计1.模具整体结构设计:根据压铸件的形状和尺寸,确定模具的整体结构。
一般情况下,压铸模具采用上下模结构,上模为固定模,下模为活动模。
针对复杂形状的压铸件,可能需要设计多个滑模和拉杆。
2.模腔设计:根据压铸件的形状和尺寸,确定模腔的几何形状和尺寸。
模腔的设计应保证在模具关闭时,模腔中的液态金属能够充满整个腔体,并且在冷却凝固过程中,金属能够均匀收缩,避免产生缩孔和其他缺陷。
3.浇口和导流系统设计:浇口和导流系统的设计对于压铸件的质量和生产效率有着重要的影响。
浇口的设计应尽量避免金属的湍流流动,避免气泡的产生。
导流系统的设计应考虑金属的顺序填充和排气,以及冷却和凝固过程中的温度控制。
二、压铸模具选材压铸模具的选材应根据金属的性能和压铸工艺的要求来确定。
通常情况下,模具会选用高强度和耐磨损的合金钢作为材料,以保证模具的使用寿命和精度。
同时,还需要考虑模具的热传导性能,以确保压铸件能够快速冷却、凝固。
三、压铸模具尺寸和形状计算1.模具尺寸计算:模具尺寸的计算包括模腔尺寸、模板尺寸、滑模尺寸、导流系统尺寸等。
模具尺寸的计算需要考虑压铸件的最终尺寸、缩孔和收缩率等因素。
2.模具形状计算:模具的形状计算主要是指模腔内部的曲面和棱角的设计。
对于复杂形状的压铸件,需要使用CAD软件进行三维建模和形状优化,以确保模具的制造精度和压铸件的质量。
压铸模具设计需要充分考虑压铸件的形状和尺寸、材料的性能、压铸工艺要求等因素,通过合理的结构设计、选材和计算,能够提升压铸件的质量和生产效率。
在设计过程中,还需要考虑模具的制造难度和制造成本,以确保模具的可行性和经济性。
转子压铸模的设计改进

大功率电机转 子, 由于铸铝转 子直径大 , 型相 槽
对宽大, 铁心长 , 用铝量也相应增加很多, 实践证 明, 大功率电机转子压铸模结构和排 气面的设计
转 子铁心在旋转 的情况下把熔 化好的铝 水浇 入 铸 铝模 中, 利用离心力 的作用, 使铝水充满转 子
槽及铸铝模 两面端环 、 平衡 柱和风叶型腔 中, 形
c si g m o l ov d t ep o l m f h l mi u ly ro a tn u d s l e h r b e o e au n m e n t a
t er t r u f c . h o o r a e s Ke wo d : l c r t r Ro o Di— a tn u d y r s E e ti mo o c tr e c si g mo l
成熟, 大功率 电机转子现也逐步采用压力铸造 。
用浮动 式 上模 可 以改 进排 气 , 减 少转 子的缩孔 率 。 并 改 进的压铸 中模结 构解决了铸 铝转 子包皮铝问题。
关键词 : 电机 转子 压铸模 改 进 中图分类号 : M3 5 文献标 识码: T 0 A
DOI 编码 : 03 6 /. s l 0 —8 72 1 .60 9 1 .9 9ji n 0 6 2 0 .0 10 .1 s
d e c si g mo l o h t rr t r wa e c i e T e i— a tn u d f r t e mo o o o sd s r d. h b
a p i d f ai g t p p e a t f h o l mp o e x p l o t ・ e u p rp r em u d i r v d e - e l n - y o t -
压铸工艺与模具设计毕业论文

压铸工艺与模具设计毕业论文一、选题的依据及意义本课题来源于江铃汽车集团公司骨干企业,江铃汽车集团公司车厢饰件厂的全资子公司,江铃有色金属压铸厂。
该公司成立于2002年5月。
工厂总投入资金为四千万元人民币,自建立起就本着高起点,现代化的原则,工厂以生产铝合金压铸件及其加工为主,已为江铃汽车、奇瑞汽车及中华汽车配套生产变速器及发动机零部件,产品已出口欧洲,工厂还可生产路灯灯罩、电梯踏板、电机壳体等其它铝合金压铸件。
产品图如下所示:压力铸造是近代金属加工工艺中发展较快的一种少无切削的特种铸造方法。
它是将熔融金属在高压高速下充填铸型,并在高压下结晶凝固形成铸件的过程。
高压高速是压力铸造的主要特征。
常用的压力为数十兆帕,填充速度(浇口速度)约为16~80米/秒,金属液填充模具型腔的时间极短,约为0.01~0.2秒。
压力铸造特点如下:一、优点:(1)可以制造形状复杂、轮廓清晰、薄壁深腔的金属零件。
(2)压铸件的尺寸精度较高,可达IT11~IT13级,有时可达IT9级,表面粗糙度达Ra0.8~3.2um,有时达Ra0.4um,互换性好。
(3)材料利用率高。
(4)可以将其他材料的嵌件直接嵌铸在压铸件上。
(5)压铸件组织致密,具有较高的强度和硬度。
(6)可以实现自动化生产。
二、缺点:(1)由于高速充填,快速冷却,形腔中气体来不及排出,致使压铸件常有气孔及氧化夹杂物存在,从而降低了压铸件质量。
(2)压铸机和压铸模质量昂贵,不适合小批量生产。
(3)压铸件尺寸受到限制。
(4)压铸合金种类受到限制。
在此之上还发展出多种特殊压铸工艺,以解决压铸件的气孔和疏松问题。
迄今为止主要有真空压铸、充氧压铸、精速密压铸、半固态压铸等。
由于用这种方法生产产品具有生产效率高,工序简单,铸件公差等级较高,表面粗糙度好,机械强度大,可以省去大量的机械加工工序和设备,节约原材料等优点,且其缺点可以通过特殊压铸得到有效的克服,所以现已成为我国铸造业中的一个重要组成部分。
铸造工艺设计毕业设计论文

目录摘要 (1)1设计任务 (2)1.1 技术要求 (2)1.1.1生产条件 (2)1.1.2 铸件材质 (2)1.1.3 造型材料及造型方法 (2)1.2 设计的技术要求 (2)1.2.1 化学成分 (2)1.2.2 结构工艺性分析 (2)2 工艺方案的确定 (2)2.1 铸造及造型方法的确定 (2)2.1.1 铸造方法 (2)2.1.2 砂型材料 (2)2.1.3 造型方法 (3)2.2 分型面和浇注位置的确定 (3)2.2.1 分型面的确定 (3)2.2.2 浇注位置的确定 (4)2.3 铸造工艺参数的选择 (4)2.3.1 铸件尺寸公差 (4)2.3.2 铸件重量公差 (4)2.3.3 机械加工余量 (5)2.3.4 铸造收缩率 (5)2.3.5 起模斜度 (5)2.3.6 最小铸出孔及槽 (5)2.3.7 分型负数 (5)2.3.8 分芯负数 (5)3 浇注系统的设计 (5)3.1 浇注系统的类型 (5)3.2 阻流截面积的计算 (5)3.2.1 内浇道截面积 (5)3.2.2 横浇道截面积 (6)3.2.3 直浇道截面积 (6)3.3 冒口的计算和确定 (6)3.3.1 冒口补缩距离 (6)3.3.2 冒口尺寸确定 (7)4 铸件的熔炼要求 (7)4.1 温度要求 (7)4.2 球化处理 (7)4.3 孕育处理 (7)5 铸件的热处理 (7)5.1 退火处理 (7)5.1.1 高温石墨化退火 (7)5.1.2 低温石墨化退火 (8)5.2 冷却方式 (8)5.3 热处理工艺图 (8)6 铸件的数值模拟过程与分析 (8)6.1 铸件充型及凝固过程 (8)6.2 模拟过程对工艺的完善 (10)结论 (13)参考文献 (14)附图 (15)摘要合理的铸造工艺是保证铸件质量的关键。
在目前的工作中,球墨铸铁QT450铸件的铸造工艺,是根据客户的要求进行设计的。
基于对铸件结构的分析,对几个铸造工艺方案进行了认真审议。
压铸毕业论文

摘要本文综述了压铸工艺设计的特点、发展现状以及未来的发展趋势,讨论了计算机技术在压铸方面的应用,分析铸件进行计算机数值模拟的目的和意义。
首先根据零件的特征和要求,查表计算,从而设计出浇注系统和集渣包,然后应用Pro-E绘制出零件的三维立体图,其次利用华铸CAE软件模拟压铸件的充型过程。
最后根据模拟的结果,分析模拟过程中出现卷气等缺陷的原因,从而改进浇注方案。
经过多次的计算机模拟和方案改进,最大程度的减少缺陷,最后确定最佳的浇注方案通过对平板生产的计算机数值模拟,从而实现了科学指导生产,为今后将CAD/CAE技术进一步应用到实际生产中进行了一些尝试。
关键词:平板;压铸;工艺设计;计算机模拟AbstractThis paper reviews the characteristics of the die casting process design, development status and future development trends,Discussed the application of computer technology in die-casting,analysis of the casting to the purpose and significance of the computer numerical simulation.First according to the characteristics and requirements of the parts,Look-up table calculation,To design the gating system and set dross ,application of Pro-E drawing three-dimensional map of the parts .Secondly, the use of HZ CAE software to simulate the die casting filling process.Finally, according to the simulation results,Analysis of the simulation volume and gas and other reasons for the defects, thus improving the casting program。
压铸工艺及压铸模具设计要点

压铸工艺及压铸模具设计要点压铸工艺及压铸模具设计要点压铸是一种利用压力将液态金属注入模具中,通过冷却凝固形成定形零件的制造方法。
压铸产品在重量、强度、尺寸方面都有非常高的准确性和稳定性,被广泛应用于汽车、摩托车、电子、通讯设备、家电等产业中,成为目前工业生产中不可或缺的一种制造技术。
下面将从压铸工艺及压铸模具设计要点两个方面进行阐述。
一、压铸工艺1. 材料准备:首先需要准备液态金属,一般使用的是微量合金钢、铝合金、镁合金、铜合金等牌号。
材料的纯度、质量直接影响产品的质量。
2. 模具设计:由于压铸的成形过程主要依靠模具的形状和大小,所以模具设计非常重要。
模具一般由流道、高压室、模腔等主要部分组成,需要用CAD 设计软件绘制出预想的产品三维模型,然后进行分析预测。
3. 夹具安装:很多压铸厂家采用自动化流水线作业,这样可以让夹具自动加载模具。
夹具的准确安装和保持最佳状态对产品稳定的尺寸和质量有着至关重要的作用。
4. 液态金属注入:注入过程需要注意金属温度的控制,因为如果注入过热的金属会造成热缩,也会加快金属与模具接触面损耗的速度。
注入金属的速度和压力也需要掌握恰当的水平。
5. 压力保持和冷却:完成注入后,需要将模具保持一定的压力,通常设置的保持时间在15-20秒之间,直到金属凝固成型,然后通过水冷却或空气冷却来加速金属的冷却,降低模腔温度,以便后续顺利脱模。
6. 脱模:经过强制冷却后,模具表面的金属固化成型,可以脱模取出。
如果模具内存在脱模困难的产品,则采用震动或喷水技术来辅助脱模。
二、压铸模具设计要点1. 模具材料:模具材料的决定因素是金属的特性和成本。
有些材料具有良好的抗磨损性和耐腐蚀能力,例如CrMoV 钢,有些材料则具有良好的导热性和导电性能,例如铝合金。
选用模具材料需要考虑两方面因素:一、材料的使用寿命;二、成本。
2. 模具结构:模具结构需要考虑到成品的尺寸、线条、强度和表面质量等因素。
通常情况下,模具结构应该是四侧对称的,以确保在生产过程中的稳定性和成品准确性。
压铸设计论文

压铸设计和工艺要素陈璐内容提要:随着我厂新产品的研制,铝压铸件已成为我厂产品中必不可少的材料之一,但由于近年来我厂的铝压铸产品质量一直没有达到理想的水平,因此,在这里我就大家简单介绍一下压铸知识。
希望能购作为提升我厂铝压铸产品质量的参考要点。
关键词:压铸件设计的工艺性压铸工艺参数压力铸造技术简介压力铸造技术是在普通铸造技术基础上发展起来的一种先进工艺,已有很长的发展历史。
它是将熔融的液态金属注入压铸机的压室,通过压射冲头(活塞)的运动,使液态金属在高压作用下高速通过模具浇注系统并充填模具型腔,在压力下金属开始结晶,迅速冷却凝固成铸件。
和普通铸件相比,压铸件内部组织致密,力学性能优良,尺寸精度高,表面质量好。
压铸工艺在机械工业、航天工业、汽车制造业和日用轻工业中,都占有重要地位。
一、压铸的基本原理和特点压铸是指在高压作用下,将液态或半液态金属以较高的速度充填压铸模具型腔,并在压力状态下结晶凝固,获得压铸件的工艺方法。
压铸生产具有高速、高压、充填时间短,并在高压状态下凝固成形的特点,因此压铸工艺具有以下优点:1)压铸件的尺寸精度高、表面质量好;2)可以生产出形状复杂、轮廓清晰、深腔薄壁的压铸件;3)压铸件组织致密,具有较高的强度和硬度;4)材料利用率高;5)生产效率高;6)经济效益好。
同样,压铸生产也存在以下缺点:1)压铸件易出现气孔和缩松;2)不适合小批量生产;3)模具的寿命低;4)受压铸件结构和合金种类所限。
二、压铸件设计的工艺性压铸件设计的工艺性好,可以简化模具结构,保证压铸件的质量,降低成本,提高经济效益。
压铸件的工艺性包括三方面的内容:压铸件的精度、压铸件的表面质量和压铸件的结构工艺性。
压铸件能获得较高的精度,而且稳定性也很好。
影响压铸件精度的主要因素有:模具的精度及工作情况、压铸机的精度及刚度、合金成分及性能、压铸件的结构、尺寸、压铸工艺参数等。
压铸件的表面粗糙度值,一般比模具成形表面的粗糙度值低两级。
定子片转子冲压工艺及其模具设计论文
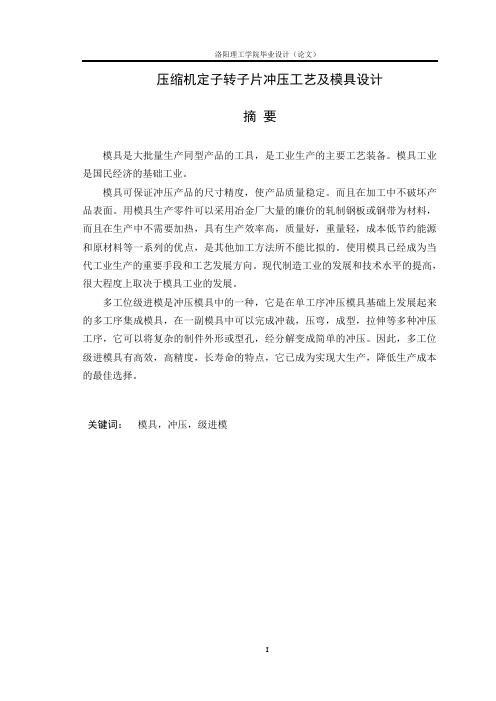
压缩机定子转子片冲压工艺及模具设计摘要模具是大批量生产同型产品的工具,是工业生产的主要工艺装备。
模具工业是国民经济的基础工业。
模具可保证冲压产品的尺寸精度,使产品质量稳定。
而且在加工中不破坏产品表面。
用模具生产零件可以采用冶金厂大量的廉价的轧制钢板或钢带为材料,而且在生产中不需要加热,具有生产效率高,质量好,重量轻,成本低节约能源和原材料等一系列的优点,是其他加工方法所不能比拟的。
使用模具已经成为当代工业生产的重要手段和工艺发展方向。
现代制造工业的发展和技术水平的提高,很大程度上取决于模具工业的发展。
多工位级进模是冲压模具中的一种,它是在单工序冲压模具基础上发展起来的多工序集成模具,在一副模具中可以完成冲裁,压弯,成型,拉伸等多种冲压工序,它可以将复杂的制件外形或型孔,经分解变成简单的冲压。
因此,多工位级进模具有高效,高精度,长寿命的特点,它已成为实现大生产,降低生产成本的最佳选择。
关键词:模具,冲压,级进模The Stamping Process And Mold Design Of Stator And RotorPiece Of CompressorABSTRACTMolds to form a mass production of industrial production facilities, is the main techniques and equipment。
Mold industry is the foundation of the national economy industry。
Tool to ensure accuracy of the ram of the product sizes, and make products quality。
And the process of the surface of the product。
Die in the production of parts of the metallurgical factory of rolled steel plates or with a material,And in production don't need, with high efficiency, quality, light weight and low cost to save energy and raw materials for a range of advantages,is Other process could compare with。
基于电机转子压力铸造工艺分析

基于电机转子压力铸造工艺分析摘要:电机转子作为电机的重要元件,直接关系到电机的质量。
基于此,本文主要对电机转子压力铸造工艺进一步分析,旨在提高其制造质量。
关键词:电机转子;压力铸造;工艺;优点一、引言电机转子:也是电机中的旋转部件。
电机由转子和定子两部分组成,它是用来实现电能与机械能和机械能与电能的转换装置。
电机转子分为电动机转子和发电机转子。
电机转子分为内转子转动方式和外转子转动方式两种。
内转子转动方式为电机中间的芯体为旋转体,输出扭矩(指电动机)或者收入能量(指发电机)。
外转子转动方式即以电机外体为旋转体,不同的方式方便了各种场合的应用。
现有的电机转子在适用过程中会发热,然而现有的电机转子上安装的降温风扇叶片不能够转动,不能满足转子正反转时的散热需求。
本设计通过设置热管能够快速的将来自转子铁芯的热量传导走,避免转子铁芯局部过热,散热装置的设置,能够适用于正反转的转子,通过第一引风叶轮和第二引风叶轮的设置,增强了降温效果。
二、电机转子及压力铸造技术的概述电机转子,包括电枢轴(1)、转子铁芯(2)、散热孔(3)、第一引风叶轮(4)、第一单向轴承(5)、第二单向轴承(6)、散热装置(7)和第二引风叶轮(16),其特征在于:所述电枢轴(1)的外侧固定有转子铁芯(2),所述转子铁芯(2)的对应两侧均开设有散热孔(3),所述第一引风叶轮(4)通过第一单向轴承(5)套设在电枢轴(1)的外侧,所述第二引风叶轮(16)通过第二单向轴承(6)套设在电枢轴(1)的外侧,且第一引风叶轮(4)和第二引风叶轮(16)位于转子铁芯(2)的同一侧,所述电枢轴(1)的外侧靠近转子铁芯(2)的另一侧安装有散热装置(7)。
根据设计要求1所述的电机转子,其特征在于:所述散热装置(7)由圆柱筒(8)、电动机(9)、主动齿轮(10)、从动齿轮(11)、第一锥齿轮(12)、第二锥齿轮(13)、换向轴(14)、扇叶(15)、惯性传感器(21)、PLC控制器(22)和扭力传感器(20)组成,所述圆柱筒(8)套结固定在电枢轴(1)的外侧,所述圆柱筒(8)的一侧内壁固定有电动机(9),所述电动机(9)的输出轴端部通过键固定有主动齿轮(10),所述电枢轴(1)的外侧通过轴承套接有从动齿轮(11),且从动齿轮(11)与主动齿轮(10)啮合,所述从动齿轮(11)远离转子铁芯(2)的一侧固定有第一锥齿轮(12),且第一锥齿轮(12)通过轴承套接在电枢轴(1)的外侧,所述换向轴(14)的一端固定有第二锥齿轮(13),且第二锥齿轮(13)与第一锥齿轮(12)相啮合,所述换向轴(14)的另一端穿过圆柱筒(8)侧壁与扇叶(15)的一端固定连接,且换向轴(14)与圆柱筒(8)的连接处通过轴承转动连接,所述圆柱筒(8)的另一侧内壁固定有惯性传感器(21)和PLC控制器(22),所述圆柱筒(8)的外侧固定有扭力传感器(20),且扭力传感器(20)套设在其中一个换向轴(14)外侧,所述惯性传感器(21)的输出端和扭力传感器(20)的输出端均电性连接PLC控制器(22)的输入端,所述PLC控制器(22)的输出端电性连接电动机(9)。
电机铸铝转子压铸工艺的研究与分析
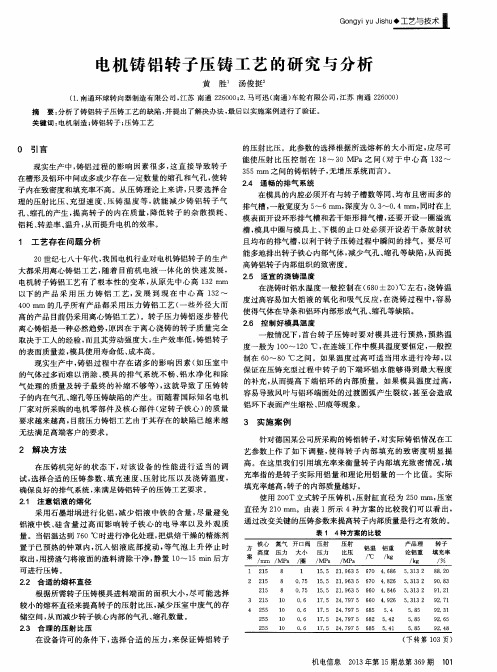
的补充 , 从而提高下端 铝环 的内部质量 。如 果模具 温度 过高 ,
容 易导 致 风 叶与 铝 环 端 面 处 的 过 渡 圆 弧 产 生 裂 纹 , 甚至会造成
铝环下表 面产生缩松 、 凹痕等现象 。
3 实 施 案 例
针对德 国某公 司所采购的铸铝转子 , 对 实际铸铝情况在 工 艺参数上作 了 如下 调整 , 使得 转子 内部 填充 的致 密度 明显 提 高 。在这里我们 引用填充率来衡量转子 内部填充 致密情况 , 填 充率指的是转子实 际用 铝量 和理论用 铝量 的一个 比值 。实际
G 。 n g v t v u 一 一 s n u : 三 兰 量 茎 薯
电机铸 铝 转 子 压铸 工 艺 的研 究 与分析
黄 胜 汤俊挺
( 1 . 南通 环球 转 向器制造 有 限公 司 , 江苏 南 通 2 2 6 0 0 0 ; 2 . 马可 迅 ( 南通) 车轮有 限公 司 , 江 苏 南通 2 2 6 0 0 0 ) 摘 要: 分 析 了铸铝 转子 压铸 工艺 的缺 陷 , 并 提出 了解决 办法 , 最后 以实施 案例 进行 了验 证 。
的气 体 过 多而 难 以 消 除 、 模具 的排气 系统不 畅 、 铝 水 净 化 和 除
在 浇铸 时铝 水 温 度 一 般 控 制 在 ( 6 8 0 i 2 0 ) ℃左右 , 浇 铸 温
度过高容易加大铝液 的氧化 和吸气反应 , 在 浇铸过程 中, 容 易
使得气体在导条和铝环 内部形成气孔 、 缩孔等缺陷。
2 . 5 适 宜 的 浇 铸 温 度
1 工艺存在 问题分析
2 O世纪七八十年代 , 我 国电机行业对 电机铸铝转子 的生产
大都采用离心铸铝工 艺 , 随 着 目前 机 电液 一 体 化 的 快 速 发 展 ,
转子体压铸工艺分析及模具设计_毕业设计说明书

天津职业技术师范大学Tianjin University of Technology and Education 毕业设计转子体压铸工艺分析及模具设计专业:材料成型及控制工程班级学号:材料0711班-12号天津职业技术师范大学本科生毕业设计转子体压铸工艺分析及模具设计Die-casting process analysis and die design of the rotorbody摘要压力铸造是目前成型有色金属铸件的重要成型工艺方法。
压铸的工艺特点是铸件的强度和硬度较高,形状较为复杂且铸件壁较薄,而且生产率极高。
压铸模具是压力铸造生产的关键,压铸模具的质量决定着压铸件的质量和精度,而模具设计直接影响着压铸模具的质量和寿命。
因此,模具设计是模具技术进步的关键,也是模具发展的重要因素。
本文通过对转子体的分析,设计其压铸模具。
对其铸件外形及其分析,得出一模一腔的模具结构。
根据铸件的特点,需要采用中心浇口,尽量避免铸件出现气孔、填不满、凝固不均等问题,由于大批量生产,采用二次分模,自动脱料的方案,并完成整体模具的设计,其中包括冷却水道的设计、浇注系统的设计、顶出系统的设计等,以及压铸机的选择与校核。
此设计通过UG软件设计完成,在设计过程中结合自身设计的结构选择标准件,来完成装配后的最终模具效果。
在设计过程中,利用ProCast软件来分析压铸件的各项结果和从中发现问题,通过分析可以仿真出铝合金成型过程中的充填、流动、凝固等过程,准确预测铸件中可能存在的缺陷。
利用模流分析技术,能预先分析模具设计的合理性,减少试模次数,加快产品研发,提高企业效率。
关键词:转子体;压铸;模流分析;模具设计ABSTRACTDie-casting molding technology is playing a key role in non-ferrous metal structure forming processes. Die-casting process’s features are the strength and hardness of die casting on high, thin-walled castings with complex shape can be cast, and the production is efficient. The die-casting die is the key for the process of die casting, its quality decides the quality and accuracy of castings, and the design of the die-casting die affects its quality and operating life directly. Therefore, designing the die-casting die is the key to technological progress; it is also an important factor in the development of mold.In this paper,through analysis of the rotor body, design of its die-casting mold, through its shape and analysis, obtain the one mode of a cavity of the mold structure. According to the characteristics of the casting, use the center gate, try to avoid casting appears holes, filled up, solidification uneven, and other issues, due to mass production, use the second parting, auto-off the program of material and complete the overall design of the mold, which including the design of cooling channels, gating system design, the top of the system design, as well as the selection and checking of the die casting machine. This design was completed by UG, combined with the structure of design in the design process to select standard parts, to complete the final assembly mold effect. In the process of design ,use ProCast software to analyze the results of the die casting and problem from analysis. ProCast can simulate the filling, flow, solidification process in the aluminum alloy molding process, accurately predict the possible defects in the casting.The mold flow analysis can pre-analysis of the rationality of the mold design, reduce the number of test mode, speed up product development, increase business efficiencies.Keywords: rotor body ;die-casting;mold flow analysis; mold design目录1 绪论 (1)1.1 压铸的基本概念 (1)1.2 压铸生产的特点 (1)1.3 压铸产业的发展 (2)1.4 毕业设计内容 (2)2 零件分析 (3)2.1 零件简介 (3)2.2 零件结构分析 (4)3 压铸成形分析 (5)3.1 ProCast的简介 (5)3.2 ProCast模拟分析能力 (5)3.3 模拟流程 (5)3.4 模拟结果及分析 (5)3.5 结论 (12)4 分型面、浇注系统和排溢系统设计 (12)4.1 分型面设计 (12)4.2 浇注系统设计 (13)4.3 溢流槽和排气槽设计 (17)5 压铸机选择 (20)5.1 压铸机介绍 (20)5.2 关于压铸机各参数的计算 (21)6 压铸成形零件尺寸计算 (25)6.1 确定合金综合收缩率 (25)6.2 明确压铸件成形件尺寸类型及计算 (26)7 压铸模机构设计 (30)7.1 推出机构设计 (30)7.1.1推出机构设计原则 (30)7.1.2 铸件顶杆的确定 (30)7.2推出机构复位与导向 (31)7.2.1 推板导向 (31)7.2.2复位机构设计 (32)7.2.3 推板限位装置 (32)8 模具结构设计 (33)8.1模具结构设计概述 (33)8.2 模体尺寸 (34)8.3模板导向的设计 (34)8.3.1导向机构的功用 (34)8.3.2 导向结构的设计原则 (35)8.3.3导柱的设计 (35)8.3.4导套的设计 (36)9 冷却系统设计 (37)9.1 概述 (37)9.2 冷却水道的设计计算 (37)10 压铸模工作过程 (39)结论 (40)参考文献 (41)致谢 (42)1 绪论1.1 压铸的基本概念压铸是一种合金液在高压作用下高速填充型腔,并在高压下凝固形成铸件的特殊铸造方法,主要用于有色金属,如锌合金、铝合金、镁合金、铜合金等。
压铸模具设计毕业论文

中文题目:螺杆套压铸模具设计外文题目:Screw set of die casting mold design毕业设计(论文)共页(其中外文文献及译文页)图纸共张完成日期:答辩日期辽宁工程技术大学本科毕业设计(论文)学生诚信承诺保证书本人郑重承诺:《》毕业设计(论文)的内容真实、可靠,系本人在指导教师的指导下,独立完成。
如果存在弄虚作假、抄袭的情况,本人承担全部责任。
学生签名:年月日辽宁工程技术大学本科毕业设计(论文)指导教师诚信承诺保证书本人郑重承诺:我已按学校相关规定对同学的毕业设计(论文)的选题与内容进行了指导和审核,确认由该生独立完成。
如果存在弄虚作假、抄袭的情况,本人承担指导教师相关责任。
指导教师签名:年月日摘要在压铸生产中,压铸模与压铸工艺,生产操作存在着相互制约,相互影响的密切关系。
所以,金属压铸模的设计,实质上是对压铸生产过程中预计产生的结构和可能出现各种问题的综合反映。
因此,在设计过程中,必须通过分析压铸件的机构特点。
了解压铸工艺参数能够实施的可能程度,掌握在不同情况下的填充条件以及考虑对经济效果的影响等因素,设计出结构合理,运行可靠,满足生产要求的压铸模来。
同时由于金属压铸模结构较为复杂,制造精度要求精度高,当压铸模设计并制造完成后,其修改的余地不大,所以在模具设计时应周密思考,谨慎细致,力争不出现原则性错误,以达到最经济的设计目标。
关键词:压铸模,压铸工艺,模具设计AbstractIn die casting production, die casting die and die casting process, the production operation exists restrict each other, the close relationship between the influence each other。
So, metal die-casting die design, is essentially to die casting process is expected to produce the structure and may appear all sorts of the comprehensive reflection of a problem Therefore, in the design process, must through the analysis of the characteristics of die casting institutions Understand the die casting technology parameters of the implementation of the possible to degree, master in the different conditions in the filling to consider economic conditions and the effects of factors to design the reasonable structure, reliable operation, and meet the production requirements of the die casting dieAnd because the metal die-casting die structure is relatively complex, manufacture accuracy high precision, when die casting die design and manufacture, after the completion of the revision of the room is not big, so in the mold design should be careful thinking, careful meticulous, strive to appear not of principle error, in order to achieve the most economic design goal压铸是近代金属加工工艺中发展较快的一种高效率,少无切削的金属成型精密铸造方法。
压铸工艺及压铸模具设计
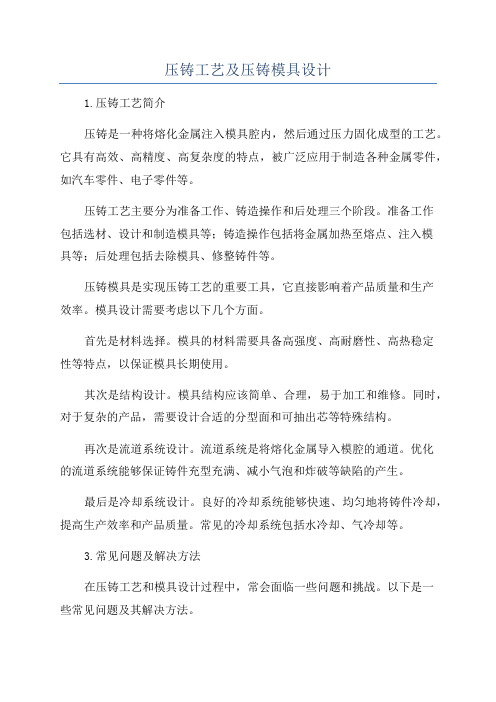
压铸工艺及压铸模具设计1.压铸工艺简介压铸是一种将熔化金属注入模具腔内,然后通过压力固化成型的工艺。
它具有高效、高精度、高复杂度的特点,被广泛应用于制造各种金属零件,如汽车零件、电子零件等。
压铸工艺主要分为准备工作、铸造操作和后处理三个阶段。
准备工作包括选材、设计和制造模具等;铸造操作包括将金属加热至熔点、注入模具等;后处理包括去除模具、修整铸件等。
压铸模具是实现压铸工艺的重要工具,它直接影响着产品质量和生产效率。
模具设计需要考虑以下几个方面。
首先是材料选择。
模具的材料需要具备高强度、高耐磨性、高热稳定性等特点,以保证模具长期使用。
其次是结构设计。
模具结构应该简单、合理,易于加工和维修。
同时,对于复杂的产品,需要设计合适的分型面和可抽出芯等特殊结构。
再次是流道系统设计。
流道系统是将熔化金属导入模腔的通道。
优化的流道系统能够保证铸件充型充满、减小气泡和炸破等缺陷的产生。
最后是冷却系统设计。
良好的冷却系统能够快速、均匀地将铸件冷却,提高生产效率和产品质量。
常见的冷却系统包括水冷却、气冷却等。
3.常见问题及解决方法在压铸工艺和模具设计过程中,常会面临一些问题和挑战。
以下是一些常见问题及其解决方法。
首先是翘曲和变形问题。
由于金属在冷却过程中会有收缩和变形,容易导致铸件产生翘曲和变形。
解决方法可以是增加冷却系统,控制金属温度等。
其次是气孔和缺陷问题。
气孔和缺陷是常见的铸件质量问题,可能是由于金属中的气体未能完全排出或模具内部有不完全填充的区域导致。
解决方法可以是优化流道和冷却系统,增加压力等。
最后是模具使用寿命问题。
模具在使用过程中会受到磨损、冲击和热应力等的影响,容易损坏。
解决方法可以是选用高耐磨材料、增加模具表面硬度等。
4.发展趋势随着科技的发展和需求的变化,压铸工艺和模具设计也在不断发展和改进。
未来的发展趋势主要包括以下几个方面。
首先是数字化和智能化。
通过数字化技术和智能化设备,可以实现对压铸工艺和模具设计的更精确和高效的控制。
转子体压铸模设计

均匀性要求较高 。 根据铸件 的外形结构和技术要求 , 确定 采用
中心浇 口。 其优 点是 :
() 1金属液从 中心导入后 , 流向分液面 ,
有利于型腔 内气体的排除 。
( ) 属液流程均匀 。 2金
此零件工作时转速高达 5 0 r i,装配前必须做 动平 衡 5 0/ n m
第 3 8卷 第 5期 ・ 术 学
Vof3 . 8 No. 5
湖
南
农
机
2 年 5 月 01 1
M a 2011 y.
HUNAN AGRI cUL TURAL MACHI NER Y
转子体压铸模设 计
孙 路
100 ) 5 32 ( 阿城 继 电器股 份有 限公 司 , 龙 江 哈尔滨 黑
De i n o h e c s i e f r Ro o o y sg f t e Di- a t ng Di o t r b d
SUN Lu
ce gR l o t, abn h n e y C . d H ri,He o ̄i g 1Байду номын сангаас0 0,hn) a L . i n a 5 3 2C ia l n
Ab t a t h t c u e c a a tr t s o h e c si g d e fr r t r b d s itu u e . d i r e o me tt e sr c=T e sr tr h rc e i i f te Di - a t i o o o o y i n r d c dAn n o d r t e h u sc n h g e e u r n s or i d n ia e st n n fr , e meh d ,e t r g t , c n at g u o t t p i gi ih r rq i me t f t i e t l d n i a d u i m t to s c n e a es o d p r n ,a tmai sr p n , s c y o h e i c i s u e .No h r d cin e ce c a e n i c e s d sd w t e p o u t f in y h s b e a r a e . o i
压铸工艺与模具设计毕业论文
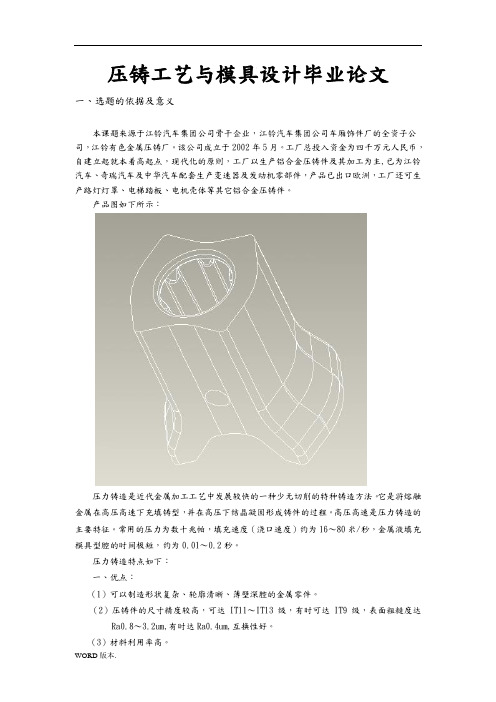
压铸工艺与模具设计毕业论文一、选题的依据及意义本课题来源于江铃汽车集团公司骨干企业,江铃汽车集团公司车厢饰件厂的全资子公司,江铃有色金属压铸厂。
该公司成立于2002年5月。
工厂总投入资金为四千万元人民币,自建立起就本着高起点,现代化的原则,工厂以生产铝合金压铸件及其加工为主,已为江铃汽车、奇瑞汽车及中华汽车配套生产变速器及发动机零部件,产品已出口欧洲,工厂还可生产路灯灯罩、电梯踏板、电机壳体等其它铝合金压铸件。
产品图如下所示:压力铸造是近代金属加工工艺中发展较快的一种少无切削的特种铸造方法。
它是将熔融金属在高压高速下充填铸型,并在高压下结晶凝固形成铸件的过程。
高压高速是压力铸造的主要特征。
常用的压力为数十兆帕,填充速度(浇口速度)约为16~80米/秒,金属液填充模具型腔的时间极短,约为0.01~0.2秒。
压力铸造特点如下:一、优点:(1)可以制造形状复杂、轮廓清晰、薄壁深腔的金属零件。
(2)压铸件的尺寸精度较高,可达IT11~IT13级,有时可达IT9级,表面粗糙度达Ra0.8~3.2um,有时达Ra0.4um,互换性好。
(3)材料利用率高。
(4)可以将其他材料的嵌件直接嵌铸在压铸件上。
(5)压铸件组织致密,具有较高的强度和硬度。
(6)可以实现自动化生产。
二、缺点:(1)由于高速充填,快速冷却,形腔中气体来不及排出,致使压铸件常有气孔及氧化夹杂物存在,从而降低了压铸件质量。
(2)压铸机和压铸模质量昂贵,不适合小批量生产。
(3)压铸件尺寸受到限制。
(4)压铸合金种类受到限制。
在此之上还发展出多种特殊压铸工艺,以解决压铸件的气孔和疏松问题。
迄今为止主要有真空压铸、充氧压铸、精速密压铸、半固态压铸等。
由于用这种方法生产产品具有生产效率高,工序简单,铸件公差等级较高,表面粗糙度好,机械强度大,可以省去大量的机械加工工序和设备,节约原材料等优点,且其缺点可以通过特殊压铸得到有效的克服,所以现已成为我国铸造业中的一个重要组成部分。
基于电机转子压力铸造工艺分析

基于电机转子压力铸造工艺分析摘要:本文主要对电机转子压力铸造工艺进一步分析。
压铸工艺方法是金属熔体在一定的压力下被压入可分的金属永久性中的一种铸造方法。
关键词:电机转子;压力铸造;工艺;优点引言:压铸工艺方法是金属熔体在一定的压力下被压入可分的金属永久性中的一种铸造方法。
其充型过程与砂型铸造过程不同,压力铸造属于特种铸造的范畴,它是一种将液态或半固态金属在高压下,以较高的速度填充入铸模的型腔内,并使金属或合金在压力下凝固结晶形成铸件的铸造方法。
一、压力铸造技术的概述随着世界各种经济市场互相依存性的日益增强,压铸工业的发展越来越国际。
例如,压铸工业是北美制造工业中一个充满生机的组成部分,北美的压铸工业己进入国际市场并参与剧烈的竞争。
建国50多年来,我国的压铸工业从无到有,压铸生产有了相当大的发展,随着我国汽车、摩托车、家用电器、计算机等工业的发展,对压铸件的需要量日益增加,以生产优质、精密、大型压铸件的压铸工业得到高速的增长和发展。
压力铸造技术是压铸行业的重要依托技术。
我国压铸企业有1000多家,铝压铸件仍占主导地位,2002年达41.6万吨,占压铸件总产量的66.7%。
我国原铝年产量2年达到274万吨。
铝合金压力铸造技术已经在航空航天、轻工建材、通讯、电子、汽车等领域得到广泛应用。
在西方发达国家,压缩机的大部分电机转子都采用铝合金压铸件,柴油机铝合金缸盖、缸体的比例也与日俱增。
近年来,这一趋势在我国表现的也非常明显。
二、压力铸造存在的问题由于压铸过程比较错综复杂,涉及人员、设备、环境,生产的压铸件很容易出现各种缺陷。
压铸件不能进行较多余量的机械加工,以免气孔暴露在铸件的表面,削弱压铸件的工作性能。
压铸件也不能进行热处理,因为滞留在压铸件内的高压气体,在压铸件高温热处理的保温过程中会发生膨胀,而此时金属在高温下软化,使得压铸件起泡,有时压铸件表面甚至被气体鼓破,形成孔洞。
转子、机座、端盖等铝合金压铸是电机生产的一个重要工序,在压铸生产中,常常会遇到很多质量问题,使得压铸件存在或多或少的缺陷。
微电机转子压铸工艺
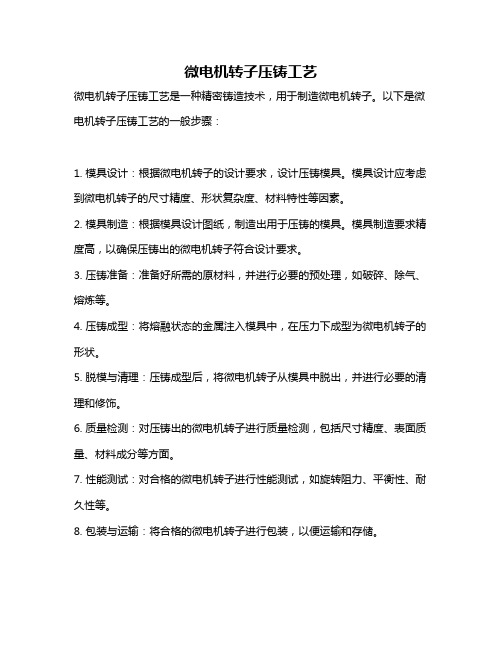
微电机转子压铸工艺
微电机转子压铸工艺是一种精密铸造技术,用于制造微电机转子。
以下是微电机转子压铸工艺的一般步骤:
1. 模具设计:根据微电机转子的设计要求,设计压铸模具。
模具设计应考虑到微电机转子的尺寸精度、形状复杂度、材料特性等因素。
2. 模具制造:根据模具设计图纸,制造出用于压铸的模具。
模具制造要求精度高,以确保压铸出的微电机转子符合设计要求。
3. 压铸准备:准备好所需的原材料,并进行必要的预处理,如破碎、除气、熔炼等。
4. 压铸成型:将熔融状态的金属注入模具中,在压力下成型为微电机转子的形状。
5. 脱模与清理:压铸成型后,将微电机转子从模具中脱出,并进行必要的清理和修饰。
6. 质量检测:对压铸出的微电机转子进行质量检测,包括尺寸精度、表面质量、材料成分等方面。
7. 性能测试:对合格的微电机转子进行性能测试,如旋转阻力、平衡性、耐久性等。
8. 包装与运输:将合格的微电机转子进行包装,以便运输和存储。
微电机转子压铸工艺的特点是可生产出具有高精度、复杂形状的微小零件,同时具有生产效率高、成本低等优势。
然而,压铸过程中容易出现的问题包括气孔、缩孔、疏松等,需要在工艺实施中加以控制和解决。
铸造工艺毕业论文

摘要首先,分析零件的技术条件,明确零件的材料组成以与性能要求。
对零件结构的铸造工艺性进行分析,明确零件的结构特点,找出可能存在的结构问题。
提出改进措施或预防缺陷的措施。
其次,根据零件结构特点,技术要求,生产要求,生产批量,生产条件选择铸造与造型方法。
由零件的结构特点,提出多种浇注和分型方案,综合对比分析,选择最为理想的浇注位置与分型面。
制定出详细的铸造工艺方案。
再次,根据铸造工艺方案和零件的特点,选用适宜的工艺参数,设计铸件的补缩系统,浇注系统。
绘制出铸造工艺图。
最后,设计铸造工艺装备,包括模板和芯盒,绘制模板和芯盒的装配图。
关键字:铸造工艺性;铸造工艺方案;铸造工艺参数;补缩系统;浇注系统AbstractFirstof all, I analyse the technical conditions of the parts to clear the material composition and performance requirements of parts ,analyse the casting process of the part structure to clear the structural features of parts ,identify possible structural problem andpropose measures to improve the structure of parts or the prevention of defective。
Secondly, According to structural characteristics of parts, technical requirements, production requirements, production volume, production conditionsI choose methods of casting and modeling. According to the structural characteristics of components, I develop a variety of pouring and partingprogrammes, analyse comprehensively and comparatively, choose the best pouring position and parting plan anddevelop a detailed programme of casting process. Again,according to the programme and structural characteristics of parts,I selectthe appropriate technical parameters , design feeding system and pouring system.of the casting,map out the casting process plans.Finally, I design the casting process equipment, including the template s and core-boxesand drawtheassembly plans of template and core-box. Keyword:Casting process;Casting process programme;Castingprocess parameters;Feeding system ;Cating system.摘要IABSTRACTII绪论11 零件材料性能分析22 零件结构的铸造工艺性分析33 铸造工艺方案的确定63.1分型的分析比较与选择6方案一6方案二7方案三83.2造型方案93.3造型〔芯〕方法的选择93.4铸型种类的选择93.5浇注位置的确定103.6砂箱中铸件数目的确定103.7砂芯的设计11砂芯尺寸11下芯顺序124 铸造工艺参数的选择124.1铸件线收缩率124.2机械加工余量124.3起模斜度的选取135 铸件体积的计算145.1实体部分体积155.2去除部分体积175.3铸件与铸型的体积186 冒口的设计196.1热节分析与热节圆的计算196.2冒口的设计19初步方案19改进方案a20改进方案b20改进方案c216.6冒口的验算227 浇注系统的设计237.1浇包的选择237.2浇注系统的设计247.3工艺出品率的验算25.8 补缩距离的计算与冷铁的安放26 8.1圆筒的补缩核算268.2圆筒的支撑壁的补缩核算269 铸造工艺装备设计279.1模板的设计279.2芯盒的设计2710 总结28致谢29参考文献30绪论铸造工艺设计就是根据铸造零件的结构特点,技术要求,生产批量和生产条件等,确定铸造工艺方案和工艺参数,绘制铸造工艺图,编制工艺卡等技术文件的过程。
- 1、下载文档前请自行甄别文档内容的完整性,平台不提供额外的编辑、内容补充、找答案等附加服务。
- 2、"仅部分预览"的文档,不可在线预览部分如存在完整性等问题,可反馈申请退款(可完整预览的文档不适用该条件!)。
- 3、如文档侵犯您的权益,请联系客服反馈,我们会尽快为您处理(人工客服工作时间:9:00-18:30)。
转子体压铸工艺分析及模具设计-毕业论文天津职业技术师范大学Tianjin University of Technology and Education专业:材料成型及控制工程班级学号: 材料0711班-12号学生姓名: 江艳平指导教师: 段磊讲师二〇一二年六月天津职业技术师范大学本科生毕业设计转子体压铸工艺分析及模具设计Die-casting process analysis and die design of the rotorbody专业班级:材料0711班学生姓名:江艳平指导教师:段磊讲师学院:机械工程学院2012 年 6 月摘要压力铸造是目前成型有色金属铸件的重要成型工艺方法。
压铸的工艺特点是铸件的强度和硬度较高,形状较为复杂且铸件壁较薄,而且生产率极高。
压铸模具是压力铸造生产的关键,压铸模具的质量决定着压铸件的质量和精度,而模具设计直接影响着压铸模具的质量和寿命。
因此,模具设计是模具技术进步的关键,也是模具发展的重要因素。
本文通过对转子体的分析,设计其压铸模具。
对其铸件外形及其分析,得出一模一腔的模具结构。
根据铸件的特点,需要采用中心浇口,尽量避免铸件出现气孔、填不满、凝固不均等问题,由于大批量生产,采用二次分模,自动脱料的方案,并完成整体模具的设计,其中包括冷却水道的设计、浇注系统的设计、顶出系统的设计等,以及压铸机的选择与校核。
此设计通过UG软件设计完成,在设计过程中结合自身设计的结构选择标准件,来完成装配后的最终模具效果。
在设计过程中,利用ProCast软件来分析压铸件的各项结果和从中发现问题,通过分析可以仿真出铝合金成型过程中的充填、流动、凝固等过程,准确预测铸件中可能存在的缺陷。
利用模流分析技术,能预先分析模具设计的合理性,减少试模次数,加快产品研发,提高企业效率。
关键词:转子体;压铸;模流分析;模具设计ABSTRACTDie-casting molding technology is playing a key role in non-ferrous metal structure forming processes. Die-casting process’s features are the strength and hardness of diecasting on high, thin-walled castings with complex shape can be cast, and the production is efficient. The die-casting die is the key for the process of die casting, its quality decides the quality and accuracy of castings, and the design of the die-casting die affects its quality and operating life directly. Therefore, designing the die-casting die is the key to technological progress; it is also an important factor in the development of mold.In this paper,through analysis of the rotor body, design of itsdie-casting mold, through its shape and analysis, obtain the one mode ofa cavity of the mold structure. According to the characteristics of the casting, use the center gate, try to avoid casting appears holes, filled up, solidification uneven, and other issues, due to mass production, use the second parting, auto-off the program of material and complete the overall design of the mold, which including the design of cooling channels, gating system design, the top of the system design, as well as the selection and checking of the die casting machine. This design was completed by UG, combined with the structure of design in the design process to select standard parts, to complete the final assembly mold effect. In the process of design ,use ProCast software to analyze the results of the die casting and problem from analysis. ProCast can simulate the filling, flow, solidification process in the aluminum alloy molding process, accurately predict the possible defects in the casting.The mold flow analysis can pre-analysis of the rationality of the mold design, reduce the number of test mode, speed up product development, increase business efficiencies.Keywords: rotor body ;die-casting;mold flow analysis; mold design 目录1 绪论 ..................................................................... .. (1)1.1 压铸的基本概念 ..................................................................... (1)1.2 压铸生产的特点 ..................................................................... (1)1.3 压铸产业的发展 ..................................................................... (1)1.4 毕业设计内容...................................................................... .................. 2 2 零件分析 ..................................................................... .. (3)2.1 零件简介 ..................................................................... .. (3)2.2 零件结构分析...................................................................... .................. 4 3 压铸成形分析 ..................................................................... (5)3.1 ProCast的简介 ..................................................................... . (5)3.2 ProCast模拟分析能力 ..................................................................... . (5)3.3 模拟流程 ..................................................................... (5)3.4 模拟结果及分析 ..................................................................... . (5)3.5 结论 ..................................................................... ................................ 11 4 分型面、浇注系统和排溢系统设计 (12)4.1 分型面设计 ..................................................................... .. (12)4.2 浇注系统设计...................................................................... . (12)4.3 溢流槽和排气槽设计 ..................................................................... ..... 16 5 压铸机选择 ..................................................................... .. (19)5.1 压铸机介绍 ..................................................................... .. (19)5.2 关于压铸机各参数的计算 (20)6 压铸成形零件尺寸计算 ..................................................................... . (24)6.1 确定合金综合收缩率 ..................................................................... .. (24)6.2 明确压铸件成形件尺寸类型及计算 .................................................... 24 7 压铸模机构设计 ..................................................................... (28)7.1 推出机构设计...................................................................... . (28)7.1.1推出机构设计原则 (28)7.1.2 铸件顶杆的确定 ......................................................................28I7.2推出机构复位与导向 ..................................................................... (29)7.2.1 推板导向 ..................................................................... . (29)7.2.2复位机构设计 ..................................................................... (29)7.2.3 推板限位装置 ..................................................................... ..... 30 8 模具结构设计 ..................................................................... . (31)8.1模具结构设计概述 ..................................................................... . (31)8.2 模体尺寸 ..................................................................... (32)8.3模板导向的设计 ..................................................................... .. (32)8.3.1导向机构的功用 ..................................................................... .. 328.3.2 导向结构的设计原则 (33)8.3.3导柱的设计 ..................................................................... . (33)8.3.4导套的设计 ..................................................................... .......... 33 9 冷却系统设计 ..................................................................... . (35)9.1 概述 ..................................................................... (35)9.2 冷却水道的设计计算 ..................................................................... ...... 35 10 压铸模工作过程 ..................................................................... ...................... 37 结论 ..................................................................... ........................................ 38 参考文献 ..................................................................... ........................................ 39 致谢 ..................................................................... . (40)II天津职业技术师范大学2012届本科生毕业设计1 绪论1.1 压铸的基本概念压铸是一种合金液在高压作用下高速填充型腔,并在高压下凝固形成铸件的特殊铸造方法,主要用于有色金属,如锌合金、铝合金、镁合金、铜合金等。