设备利用率分析表表格
大型医疗设备运行情况分析报告

大型医疗设备运行情况分析报告尊敬的领导:根据贵院于2021年1月1日至2021年12月31日期间的大型医疗设备运行情况,我对其进行了详细的分析和总结,并编写了该报告,旨在为管理层提供决策依据和改进建议。
一、概述本报告主要对贵院的大型医疗设备运行情况进行全面分析,包括设备数量、设备类型、故障情况、维修工作、使用效率等方面。
二、设备概况截至2021年12月31日,贵院共拥有大型医疗设备200台,包括CT扫描仪、核磁共振仪、超声诊断仪等多种类型。
其中,CT扫描仪占比最大,共有80台,核磁共振仪和超声诊断仪分别为60台和40台。
三、设备故障情况1. 故障率在过去一年的运行中,贵院的大型医疗设备平均故障率为5%,仅有10台设备出现故障。
2. 故障类型设备故障主要包括硬件故障、软件故障和系统故障。
硬件故障占比58%,软件故障占比32%,系统故障占比10%。
3. 故障原因经过分析,设备故障的主要原因是设备老化、操作不当、电路故障以及供电异常等。
四、维修工作1. 维修时间在设备出现故障后,平均维修时间为2天,最长维修时间为7天。
其中,软件故障的维修时间相对较短,为1天;硬件故障和系统故障的平均维修时间分别为3天和4天。
2. 维修费用设备维修费用主要包括维修材料费、人工费和设备停机损失费用。
根据统计数据,贵院全年设备维修费用总计为100万元,其中人工费占比最大,为60%。
五、使用效率1. 使用率贵院的大型医疗设备使用率为80%,即设备在365天内的使用时间为292天。
2. 使用时段分析根据数据统计,设备的使用时间主要集中在工作日上午和下午,周末的使用率较低。
3. 设备利用率设备利用率为50%,即设备运行时间中只有一半时间处于使用状态,另一半时间处于待机状态。
六、问题与建议1. 设备更新大部分设备已使用多年,随着技术的不断进步和设备老化,故障率增加,建议逐步更新设备,提升设备的性能和稳定性。
2. 维修团队建设加强维修团队的培训和管理,提高其技术水平和应急处置能力,减少设备维修的时间和费用。
设备利用率OEE计算

如何计算工厂的整体设备效能日本工厂设备维修保养协会的Seiichi Nakajima曾表示,对于分散式生产的制造商来说,工厂整体设备效能(以下简称OEE)如果能达到85%,就可以被公认为世界一流的。
然而实际上目前并没有一个通用的工厂整体设备效能的计算方法。
在进行车间的OEE 的数据处理计算时,应考虑多种因素。
下面介绍的方法包含了一种计算生产线或生产流程的OEE,它也可推广用于计算整个工厂的OEE。
计算生产线或生产流程上的OEE如果所有的机器相对于生产率和生产能力来说其贡献是相同的,那么计算生产线的OEE就简单了。
但是完全均衡的生产线几乎没有,并且它也不能代表大多数工厂的真实情况。
另外,大多数工厂并非都是一条笔直的生产线,其生产的产品部件能从一台机器非常和谐的传到另一台机器而且设备之间也非常谐调。
实际上,一个生产流程往往是非常复杂的,生产线上的机器有些是串联关系,有些是并行工作,而且它们常常还有旁路流程。
因此直接计算生产线或生产流程的OEE而不计算各单个机器的OEE是不可能的。
生产线或生产流程的OEE计算,在理论上认为整个生产线或生产流程是一个单独的机器,它理论上的生产周期等于生产流程中瓶颈机器的生产周期。
例如,如果一条生产线上有三个机器,它们的生产周期分别为:3秒,2秒和4秒,则总的生产流程周期为4秒,即为瓶颈机器的生产周期。
生产线作为一个整体,在4秒钟之内它只能生产一个产品。
一个生产流程的关键是它要在瓶颈机器这一环节上保持一个高的可用度、生产率和优质率。
在典型的生产流程中各台机器的加工生产之间都有一定的时间冗余,如果这个时间冗余能够控制或允许一些机器短暂时间的停机,而不影响整个的生产流程,则它并不影响整个生产线或生产流程上的生产率。
如果这个时间冗余不能弥补其它机器的短暂停机时间,瓶颈机器就会由于没有原料而停机或阻塞下面的流程,而不能生产出额外的资料。
在所有的情形下,监控瓶颈机器的可用度和生产率,可提供一个非常好的整个生产线的生产剖面。
生产统计员一般要做的表格
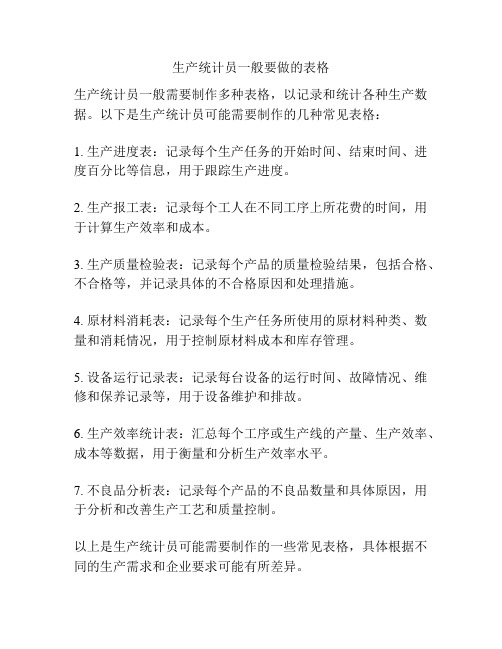
生产统计员一般要做的表格生产统计员一般需要制作多种表格,以记录和统计各种生产数据。
以下是生产统计员可能需要制作的几种常见表格:1. 生产进度表:记录每个生产任务的开始时间、结束时间、进度百分比等信息,用于跟踪生产进度。
2. 生产报工表:记录每个工人在不同工序上所花费的时间,用于计算生产效率和成本。
3. 生产质量检验表:记录每个产品的质量检验结果,包括合格、不合格等,并记录具体的不合格原因和处理措施。
4. 原材料消耗表:记录每个生产任务所使用的原材料种类、数量和消耗情况,用于控制原材料成本和库存管理。
5. 设备运行记录表:记录每台设备的运行时间、故障情况、维修和保养记录等,用于设备维护和排故。
6. 生产效率统计表:汇总每个工序或生产线的产量、生产效率、成本等数据,用于衡量和分析生产效率水平。
7. 不良品分析表:记录每个产品的不良品数量和具体原因,用于分析和改善生产工艺和质量控制。
以上是生产统计员可能需要制作的一些常见表格,具体根据不同的生产需求和企业要求可能有所差异。
8. 工时统计表:记录每个员工或工作组的工作时间、加班时间等,用于计算工资和控制工时成本。
9. 生产设备利用率统计表:记录每个生产设备的有效运行时间、停机时间、维修时间等,用于评估设备利用率和提升设备效率。
10. 产能分析表:根据生产任务和产能要求,记录每个工序或生产线的产能情况,用于规划和优化生产安排。
11. 库存管理表:记录原材料、半成品和成品的库存数量和变动情况,用于控制库存水平和进行周转分析。
12. 生产成本统计表:根据生产任务和相关成本项,统计每个生产任务的生产成本,包括人工成本、材料成本、设备折旧等,并进行成本分析和控制。
13. 客户订单统计表:记录客户的订单数量、交付日期、是否按时交付等信息,用于跟踪订单进展和满足客户需求。
14. 生产报表:根据上述表格的数据,综合分析和汇总生产数据,制作生产报表,用于向管理层提供有关生产情况的汇报和决策支持。
生产设备状况汇总表

汇报人:
,a click to unlimited possibilities
汇报人:
CONTENTS
添加目录标题 设备基本信息 设备运行状况 设备性能参数 设备维护保养 设备故障处理
PART ONE
PART TWO
设备名称:生产线
设备型号: XXXXX
设备产地: XXXXX
设备购置时间: XXXX年XX月
日常检查:每日对设备进行检 查,确保设备正常运行
定期保养:按照规定的时间间 隔对设备进行保养,包括清洗、 润滑、更换零部件等
故障排除:及时排除设备故障, 确保设备正常运行
安全防护:采取安全防护措施, 防止设备发生意外事故
设备名称:XXX 维护保养时间:XXXX年XX月XX日 维护保养内容:清洗、润滑、检查、调整等 维护保养人员:XXX 备注:无
设备故障率:设备在运行过程中出 现故障的概率
设备可靠性:设备在规定条件下和 规定时间内完成规定功能的概率
添加标题
添加标题
添加标题
添加标题
设备可用性:设备在需要时能够正 常工作的概率
设备维修性:设备出现故障后能够 及时修复的概率
PART FIVE
日常维护保养周期 二级维护保养周期
一级维护保养周期 三级维护保养周期
定期检查设备运行状况,及时发现并解决问题 定期清洗设备,保持设备清洁和正常运行 定期更换易损件,确保设备稳定性和可靠性 建立设备维护保养档案,记录设备维护保养情况
PART SIX
机械故障:设 备部件磨损、 断裂等机械问
题
电气故障:电 路、电机等电
气部件故障
液压故障:液 压系统泄漏、 压力不稳等问
设备每小时的产量
设备生产效设备精度等级 设备测量范围 设备分辨率 设备重复定位精度
生产管理表格大全

生产管理表格1.市场计划
表1-1 设厂计划(一)
表1-2 设厂计划(二)
表1-3 设厂计划(三)
2.生产计划
表2-1 长远生产计划表
表2-2 生产计划综合报表
表2-3 月份产销计划汇总表
表2-4 产销计划拟定表
表2-5 设备利用率分析表
表2-6 生产效率分析表
表2-7 月份生产计划表(一)
表2-8 月份生产计划表(二)
表2-9 订单安排记录表(一)
表2-10 工作量分析
表2-11 产量记录表
表2-12 工作日报单
表2-13 制造月报表
表2-14 各部门合格率控制表
表2-15 时间研究记录表
表2-16 生产记录表
表2-17 用料记录单
表2-18 制造异常反应表
表2-19 制造通知单
表2-20 标准作业时间评定表(一)
表2-21 突发性工作量分析表(二)
表2-22 最重要作业时间分析
表2-23 作业标准时间研究表
3.进度安排
表3-1 生产进度安排检查表
表3-2 生产进度计划表
表3-3 生产管理安排核对表
表3-4 生产故障分析表
表3-5 生产进度表(一)
表3-6 机器工作负荷图表(一)表3-7 生产进度控制表(一)4.生产记录
表4-1 生产状况记录表
表4-2 部门机器运转日记
表4-3 生产用料记录单
表4-4 考核人员记录表各
表4-5 生产班次产量记录表5.生产日报
表5-1 生产日报表
表5-2 作业日报表(范例A)
表5-3 作业日报表(范例B)6.生产月报
表6-1 生产月报表
表6-2 生产计划科月报表
表6-3 工作效率及工时月报表。
生产效率分析表格
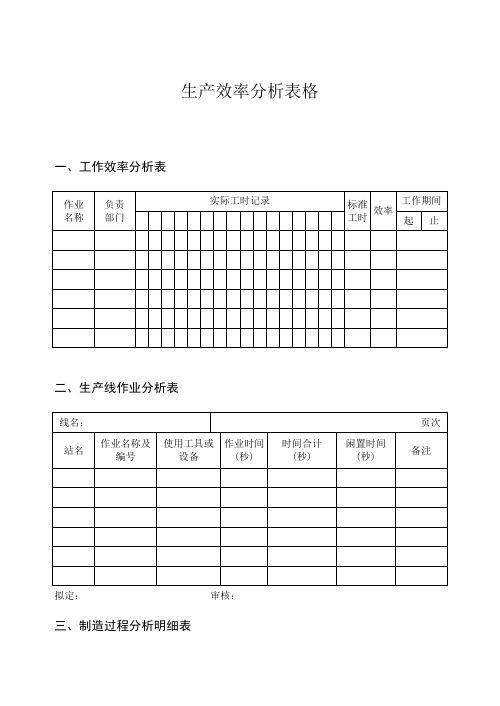
生产效率分析表格一、工作效率分析表
二、生产线作业分析表
拟定:审核:
三、制造过程分析明细表
拟定:审核:四、产量分析表
五、各制造过程产量分析表
348
六、月份各部门生产效率分析表
审核:填表:
349
七、月份各产品产出率报告表
核对:
八、月份完工产品效率汇总表
350
九、生产效率不佳原因分析表
月份:
十、零件自制外购对比分析表
日期:
初拟:修订:批示:审核:分析人:
351
十一、经济生产量分析表
十二、工厂设备投资经济效益分析
续表352
审核:分析表:
十三、机器生产效率统计表
机别:月份:
353
十四、设备利用率分析
期间:月日至月日资料来源:□资料分析
□抽查
审核:分析员:十五、生产进度异常原因分析
354
续表
十六、生产故障分析表
部门:年月编号:
355。
设备统计分析表
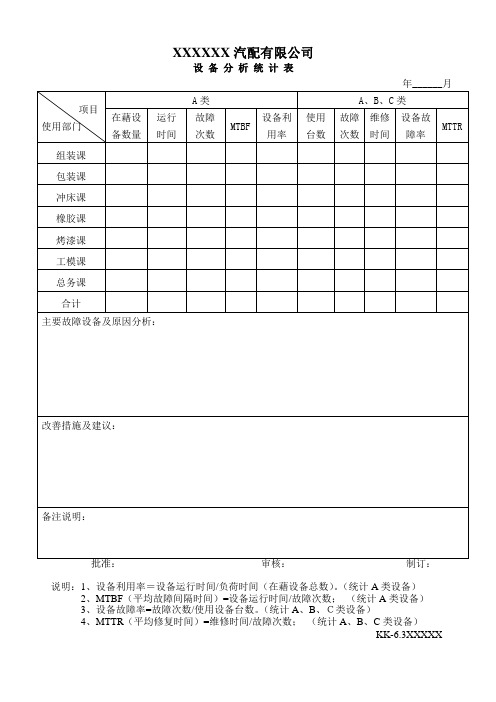
设备分析统计表
__________年______月
项目
使用部门
A类
A、B、C类
在藉设备数量
运行时间
故障次数
MTBF
设备利用率
使用台数
故障次数
维修时间
设备故障率
MTTRBiblioteka 组装课包装课冲床课
橡胶课
烤漆课
工模课
总务课
合计
主要故障设备及原因分析:
改善措施及建议:
备注说明:
批准:审核:制订:
说明:1、设备利用率=设备运行时间/负荷时间(在藉设备总数)。(统计A类设备)
2、MTBF(平均故障间隔时间)=设备运行时间/故障次数;(统计A类设备)
3、设备故障率=故障次数/使用设备台数。(统计A、B、C类设备)
4、MTTR(平均修复时间)=维修时间/故障次数;(统计A、B、C类设备)
KK-6.3XXXXX
设备综合效率(OEE)
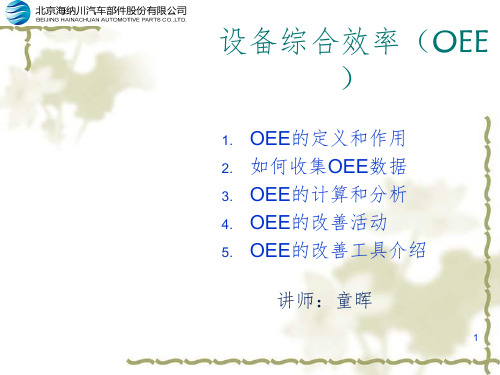
监测诊断
定期修理
不定期检修
状况早期发现准确及时报告
突发修理
减轻负荷提高强度,提高可靠性
按故障后果决定适当的维修策略
技术改造以改善设备性能与精度
适当技术措施提高可维修性
故障根源诊断
27
改变设计,永久消灭故障
设备综合效率Level评价表
Level 1
1
突发 ·慢性故障并发
1
Level 2 大部分是偶发故障
❖ OEE要应用在一台机器上(视一条生产 线为一台机器也可)而不能应用在整个 生产车间或全厂上,这样才有意义。
16
理论速度和实际速度
理论Cycle Time : 设备制造公司提示的或者设备设置后 最佳的状态下单位产品的生产所需要的时间(更新改造 后的设备按当前状态计算)。 实际Cycle Time : 作业环境和限制条件等发生影响后实 际开动时得到的结果上平均使用的开动速度
设备综合效率(OEE )
1. OEE的定义和作用 2. 如何收集OEE数据 3. OEE的计算和分析 4. OEE的改善活动 5. OEE的改善工具介绍
讲师:童晖
1
什么是OEE?
* O verall * E quipment * E fficiency
综合 设备 效率
OEE
OEE是一个独立的测量工具,它用来表 现实际的生产能力相对于理论产能的比 率。它由时间利用率,设备性能率以及 产品合格率指数三个关键要素组成
型号
产能(个/分 生产数量 )
不良品
A
63
12600
180
B
60
12000
160
C
60
15000
150
oee设备综合效率表格

竭诚为您提供优质文档/双击可除oee设备综合效率表格篇一:oee设备综合效率三种叫法和计算公式并举例子oee(设备综合效率)是衡量设备综合性时间损失大小的指标,反应设备在负荷时间内有多少时间是有价值的开动时间。
叫法之一:oee=时间开动率×性能开动率×良品率即:(1)〔时间开动率〕:是衡量测定因故障、准备、调整等导致停止损失大小的指标。
时间开动率=(负荷时间—停止时间)/负荷时间*100% (2)〔性能开动率〕:是衡量因空转、小停工及速度降低等导致时间损失大小的指标。
性能开动率=(基准节拍*产量)/开动时间*100%(3)〔良品率〕:是衡量保证充分满足消费者质量要求的指标。
良品率=合格品件数/生产总件数*100%叫法之二:oee=时间利用率*设备性能率*产品合格率=(合格的产品*设计速度)/负荷时间1.时间利用率=(负荷时间-停机损失)/负荷时间*100%=(有效)利用时间/负荷时间2.设备性能率=(生产产品数*设计速度)/利用时间*100%3.质量合格率=(生产产品数-不合格品)/生产产品数*100%其实:设计速度即基本节拍工厂/车间的设备综合效率=(1#设备综合效率*产量+2#设备综合效率*产量+…+n#设备综合效率*产量)÷总产量叫法之三:oee=可使用率x工作表现率x品质率1.可使用率:指实际运转时间与可用时间(负荷时间)之比。
(1)可用时间:指从一天(或一个月)的工作时间中,减去生产计划、计划保养,以及日常管理上必要的的停顿时间后所剩下的时间。
(2)停机时间(停止时间):指因故障、setup、调整、更换模具等所停止的时间。
(3)公式:可使用率=(可用时间-停机时间)/可用时间x100%2.工作表現率包括速度运转率与纯运转率。
(1)速度运转率系指设备原有这能力(包括周期时间、循环数)对实际速度之比;纯运转率指在单位时间内设备有无以一定速度在运转,由此可以求得日报上无法出现的小故障损失。
设备总效率—OEE
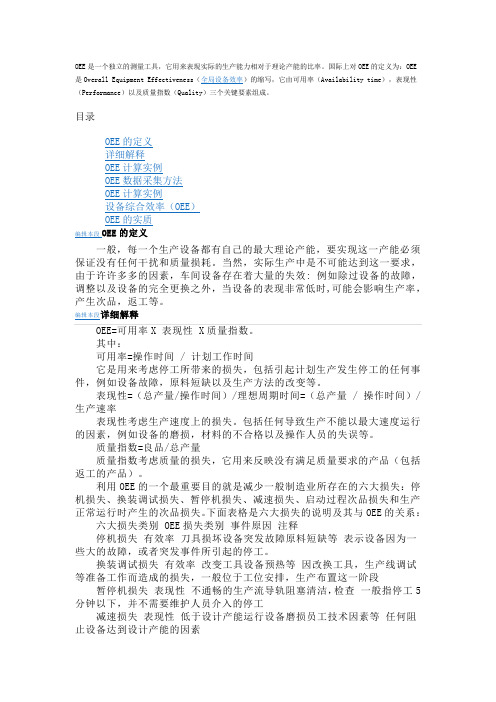
OEE是一个独立的测量工具,它用来表现实际的生产能力相对于理论产能的比率。
国际上对OEE的定义为:OEE是Overall Equipment Effectiveness(全局设备效率)的缩写,它由可用率(Availability time),表现性(Performance)以及质量指数(Quality)三个关键要素组成。
目录OEE的定义详细解释OEE计算实例OEE数据采集方法OEE计算实例设备综合效率(OEE)OEE的实质编辑本段OEE的定义一般,每一个生产设备都有自己的最大理论产能,要实现这一产能必须保证没有任何干扰和质量损耗。
当然,实际生产中是不可能达到这一要求,由于许许多多的因素,车间设备存在着大量的失效: 例如除过设备的故障,调整以及设备的完全更换之外,当设备的表现非常低时,可能会影响生产率,产生次品,返工等。
编辑本段详细解释OEE=可用率X 表现性 X质量指数。
其中:可用率=操作时间 / 计划工作时间它是用来考虑停工所带来的损失,包括引起计划生产发生停工的任何事件,例如设备故障,原料短缺以及生产方法的改变等。
表现性=(总产量/操作时间)/理想周期时间=(总产量 / 操作时间)/ 生产速率表现性考虑生产速度上的损失。
包括任何导致生产不能以最大速度运行的因素,例如设备的磨损,材料的不合格以及操作人员的失误等。
质量指数=良品/总产量质量指数考虑质量的损失,它用来反映没有满足质量要求的产品(包括返工的产品)。
利用OEE的一个最重要目的就是减少一般制造业所存在的六大损失:停机损失、换装调试损失、暂停机损失、减速损失、启动过程次品损失和生产正常运行时产生的次品损失。
下面表格是六大损失的说明及其与OEE的关系:六大损失类别 OEE损失类别事件原因注释停机损失有效率刀具损坏设备突发故障原料短缺等表示设备因为一些大的故障,或者突发事件所引起的停工。
换装调试损失有效率改变工具设备预热等因改换工具,生产线调试等准备工作而造成的损失,一般位于工位安排,生产布置这一阶段暂停机损失表现性不通畅的生产流导轨阻塞清洁,检查一般指停工5分钟以下,并不需要维护人员介入的停工减速损失表现性低于设计产能运行设备磨损员工技术因素等任何阻止设备达到设计产能的因素启动过程次品损失质量指数报废、重工等设备预热,调节等生产正式运行之前产生的次品生产过程次品损失质量指数报废、重工等生产稳定进行时产生的次品表一六大损失与OEE的关系编辑本段OEE计算实例我们举一个例子来说明OEE的计算方法:设某设备某天工作时间为8h, 班前计划停机15min, 故障停机30min,设备调整25min, 产品的理论加工周期为0.6 min/件, 一天共加工产品450件, 有20件废品, 求这台设备的OEE。
OEE分析方法简介

一、OEE分析方法简介1.OEE的定义OEE即为设备综合利用率,是SEMA组织于1999年提出的一项用于衡量设备生产能力的计算方法标准,是实际合格产量与负荷时间内理论产量的比值。
OEE不仅考虑设备在时间上的利用情况,同时也考虑由于操作和工艺造成的性能降低和产品合格率问题,更全面的体现设备在生产中的利用情况和有设备生产出的产品的质量问题。
运用OEE方法还可以识别出并系统地降低由于统计波动和依存关系而带来的瓶颈工序设备的效率损失,使隐藏的或损失掉的产能释放出来,进而优化企业的生产工序,促进企业有效产能的提高。
2.OEE的计算综合设备利用率OEE的计算公式如下:OEE=时间运行效率×性能运行效率×良品率×100%(1)时间运行效率是有效运行时间按与负荷时间的比值,其计算公式如下:时间运行效率=(负荷时间-停止损失时间)或负荷时间× 100%其中,负荷时间=理论工作时间–休止损失时间(2)性能运行效率是一个衡量实际加工产品所用时间与开动时间的速度损失的指标,指设备的实际运行速度和设备的固有设计能力之间的比值。
计算公式如下:性能运行效率=负荷时间/理论工作时间(3)合格品率是指合格品数量所占的比例,是用设备的生产精度反映设备的运行状况。
其计算公式如下:合格品率=合格品数量/生产数量×100%3.影响OEE的损失分析通过对OEE定义的分析,可以将影响设备综合效率的主要损失归为6个大类:故障或停机损失;准备和调试损失;空转和暂停损失;速度低下损失;质量缺陷和返工;启动损失。
(1)故障或停机损失是指故障停机造成的时间损失和由于生产缺陷产品导致的数量损失。
因偶发故障造成的设备故障通常是明显的,且在整个损失中占较大比例,所以应投入了大量时间努力去寻找,并提高设备可靠度的研究来尽量避免这种故障。
(2)准备和调试损失是指因准备和调试而导致停机和产生废品所造成的损失。
一般发生在一个产品生产结束再生产另一种产品时。
设备利用率统计分析图表(年度)

计划开机时间实际运行时间当月利用率计划开机时间实际运行时间当月利用率计划开机时间实际运行时间当月利用率计划开机时间实际运行时间当月利用率计划开机时间实际运行时间当月利用率计划开机时间实际运行时间1设备A 16015093.75%14013092.86%16015093.75%16515090.91%16015093.75%1601502设备B 16013081.25%1007070.00%16013081.25%16013081.25%16013081.25%1601303设备C 16015093.75%14013092.86%16015093.75%16015093.75%16015093.75%1601504设备D 16015093.75%14013092.86%16015093.75%16015093.75%16015093.75%1601505设备E 16014087.50%12010083.33%16014087.50%16014087.50%16014087.50%1601406设备F16015093.75%14013092.86%16015093.75%16015093.75%16015093.75%160150序号车间设备编号设备名称生产管理工具——生产计划与控制管理设备利用率统计分析图表(年度)说明:本表格主要用于统计和分析各类设备全年各月的设备利用率,可以帮助管理者有效掌握机器设备全年度的运行情况(包括各类设备利用率比较分析、整体设备月度利用率趋势分析),并及时采取改进措施。
该表中设备利用率计算方式是依据设备运行时间利用率来计算的。
(表格中含自动计算公式,分析图将根据数据变化自动生成和变化,数据为模拟数据。
)左图为各类设备年度利用率比较分析图,右图为整体设备全年每月的利用率分析及趋势图。
差距值若为负数,自动显示红色予以警示。
编制部门/车间: 时间周期: 编制日期:1月份2月份3月份4月份5月份6月份70.00%75.00%80.00%85.00%90.00%95.00%100.00%设备A设备B设备C设备D设备E设备F 设备G 设备H90.00%88.00%89.00%90.00%91.00%92.00%93.00%1月2月3月4月5月6月7月8月9月10月11月12月年度合计目标值年。
设备效益分析报告

设备效益分析报告1. 引言本报告旨在对某公司设备的效益进行分析,帮助公司了解设备的运行情况、产出效率以及潜在问题。
通过对各项数据的分析和对比,为公司决策提供参考依据,提高设备的利用率和生产效率。
2. 设备概况首先,我们对公司的设备情况进行了整理和统计。
目前公司共计拥有20台设备,包括生产设备和辅助设备。
生产设备主要用于产品的加工和组装,而辅助设备则用于提供供电、供水、通风等支持性服务。
各设备的品牌、型号、采购时间以及预计寿命都被记录在表格中,以便日后作为设备更换和维护的依据。
3. 设备利用率分析设备的利用率是衡量设备使用效益的重要指标之一。
通过对设备的运行时间、故障时间以及维修时间的统计,我们得出以下数据:•总运行时间:365天 x 24小时 = 8760小时•平均故障时间:300小时•平均维修时间:100小时根据以上数据,计算得出设备的平均利用率为:设备利用率 = (总运行时间 - 总故障时间 - 总维修时间)/ 总运行时间设备利用率 = (8760小时 - 300小时 - 100小时)/ 8760小时 = 89.4%以上数据显示公司设备的平均利用率达到了89.4%,属于较高水平。
4. 设备产出效率分析除了设备的利用率外,设备的产出效率也是重要的指标之一。
通过对产品产量和设备运行时间的对比,我们可以得出设备的产出效率。
根据统计数据,公司通过这些设备共生产出了500,000个产品,并且运行了8760小时。
因此,设备的产出效率为:设备产出效率 = 产品产量 / 设备运行时间设备产出效率 = 500,000个产品 / 8760小时≈ 57个产品/小时以上数据显示公司设备的产出效率为每小时57个产品。
5. 设备维护与维修分析设备的正常维护和及时维修对于设备的性能和效益至关重要。
通过对设备的维修记录和维护计划的分析,我们可以得出以下结论:•平均维修时间为100小时,这表明设备的维修及时性较好。
•维修次数较少,表明设备的可靠性较高。
设备综合效率OEE详解
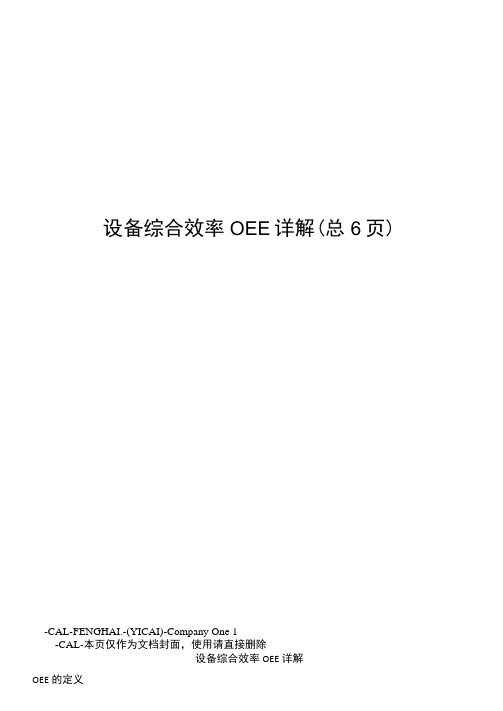
设备综合效率OEE详解(总6页) -CAL-FENGHAI.-(YICAI)-Company One 1-CAL-本页仅作为文档封面,使用请直接删除设备综合效率OEE详解OEE的定义一般,每一个生产设备都有自己的最大理论产能,要实现这一产能必须保证没有任何干扰和质量损耗。
当然,实际生产中是不可能达到这一要求,111于许许多多的因素,车间设备存在着大量的失效:例如除过设备的故障,调整以及设备的完全更换之外,当设备的表现非常低时,可能会影响生产率,产生次品,返工等。
OEE是一个独立的测量工具,它用来表现实际的生产能力相对于理论产能的比率。
国际上对OEE的定义为:OEE是Overall Equipment Effectiveness (设备综合效率)的缩写,它由可用率,表现性以及质量指数三个关键要素组成,即:OEE二可用率X表现性X质量指数。
其中:可用率=操作时间/计划工作时间它是用来考虑停工所带来的损失,包括引起计划生产发生停工的任何事件,例如设备故障,原料短缺以及生产方法的改变等。
表现性二理想周期时间/ (操作时间/总产量)=(总产量/操作时间)/生产速率表现性考虑生产速度上的损失。
包括任何导致生产不能以最大速度运行的因素,例如设备的磨损,材料的不合格以及操作人员的失误等。
质量指数二良品/总产量质量指数考虑质量的损失,它用来反映没有满足质量要求的产品(包括返工的产品)。
利用OEE的一个最重要U的就是减少一般制造业所存在的六大损失:停机损失、换装调试损失、暂停机损失、减速损失、启动过程次品损失和生产正常运行时产生的次品损失。
下面表格是六大损失的说明及其与OEE的关系:表一六大损失与OEE的关系OEE计算实例我们举一个例子来说明OEE的计算方法:设某设备某天工作时间为8h,班前计划停机15min,故障停机30min,设备调整25min,产品的理论加工周期为min/件,一天共加工产品450件,有20件废品,求这台设备的OEE。
设备综合效率(OEE)

型号
A B C D
产能(个/分 ) 63 60 60 79
生产数量
12600 12000 15000 13790
不良品
180 160 150 188
设备 LOSS的构造和指标
设备
6大 LOSS
管理指标
作业时间
负荷时间
计划 维持
开动时 间
停止 LOSS
纯开动时间
速度 LOSS
价 值 不良 加动时间 LOSS
通过8大损失计算TEEP
设备
八大损失
利用率计算
负荷时间
计划停机 外部因素
设备 利用率
=
工作时间 开动时间
停
开动时间
机 损
失
净开动
速
时间
度
损
失
设备故障 安装调整
空转短暂 停机 速度降低
时间 开动率
=
性能 开动率
=
有价 废 值开 品 动时 损 间失
加工废品
初期未 达产
合格 品率
=
产能利用率TEEP=设备利用率×OEE
间
管理损失
运作损失
生产线管理损失
后勤和运输
测量和调节损失
能源损失
成
备品备件损失
原材料损失
本
联合利华世界500强在经过近10年的OEE的管理,2010年 才从12大损失向16大损失迈进。
其中它是先做6大损失到9大损失到12大损失不断的摸索中 才有今天的成绩。数据显示联合利华洗衣粉的产量从2004年 日产260T/D到2010年日产近1000T/D。其中生产机器只增加 了50%。在OEE的数据支撑下结合一些优良的管理方法再 加上公司员工的群策群力下设备的效率平均提高了48.6%。