板料成形回弹特征及其控制技术
先进高强度钢板冲压成形回弹的预测与控制

累,具有较强的均匀变形能力。
几个钢种的成形极限图的对比图见图1.2。
成形极限图能较全面的表征各类钢在各种应力状态下的成形性,从图1.2可以看出:双相钢和DP600的成形性相当,TRIP600的成形性和IF钢相当,且在深拉延和平面应变区的成形性还优于IF钢。
②回弹回弹是指冲压构件脱模后,偏离原在模具中形状的一种变形量。
高强度钢的机械性能和普通低碳钢有很大差异,钢板高强度化易引起塑性下降,成形性变差,而屈服强度的提高则引起面畸变和回弹效应,增加形状不稳定性。
典型的成形缺陷有开裂、形状不良、尺寸精度不良和卡模具等。
材料强度升高时,残余应力增大,易产生变形后弹性回复引起的形状不良和尺寸精度不良等。
这是高强度钢板成形中最为严重的问题【n。
导致由这类材料冲压而成的汽车冲压件的回弹量远大于使用普通低碳钢板的冲压件,回弹问题更加突出。
图1.3几种钢回弹对比图Fig1.3Spdngbackofdifferentsteels从图1.3可以看出,随着板料强度的提高,回弹越严重。
由于先进强度钢独特的材料性能,成形后的回弹比普通钢及传统高强度钢大。
因此回弹是先进高强度钢冲压成形工艺的设计难点。
利用有限元仿真软件,分析先进高强度钢的回弹特性,可有效指导先进高强度钢冲压成形设计。
1.4冲压回弹的分析和控制方法冲压回弹分析是回弹控制的基础,回弹分析的准确程度,决定了回弹控制的有效性。
只有准确预测回弹,才能从根本上解决回弹问题。
1.4.1冲压回弹的分析方法常用的回弹的分析方法有两种,解析方法和有限元方法。
①解析法重庆大学硕士学位论文2先进高强度钢介绍2先进高强度钢介绍2.1先进高强度钢简介根据国际上对超轻钢汽车的研究(ULSAB.AVC),把屈服强度在210-550N/ram2范围内的钢板称为高强度钢板;屈服强度大于550N/ram2的钢板称为超高强度钢板。
根据强化机理的不同又分为普通高强度钢板和先进高强度钢板。
其中,普通高强度钢板主要包括高强度IF(无『自J隙原子)钢、烘烤硬化钢、含磷(P)钢、各向同性(IS)钢、碳一锰(C.Mn)钢和高强度低合金(HsLA)钢;先进高强度钢主要包括双相(DP)钢、相交诱发塑性(踊P)钢、复相(cP)钢、贝氏体(BP)钢和马氏体(MP)钢等。
板料成形回弹特征及其控制技术

中很 难 有效 克 服 的 成形 缺 陷 之 一 . 接 触压 力 的消 除 而 自动 释 放 掉 .回 模拟精度虽然不高 .但计算速度很
它 不 仅 降 低 了产 品 质 量 和 生 产 效 弹 的 驱动 力 一 般 是朝 着 板 料 原 始形 快 .可 以为 模 具在 设 计 阶段 提 供 一 率 .还 制约 了 自动 化装 配 生产 线 的 状 变形 。 因此 .冲压 成 形 中的最 终 个 定 性 的参考 方案 。T C. u 学 . Hs 等 实 施 .是 我 国 汽 车 制造 工 业 中亟 待 产 品形 状 不 但依 赖 于 凹模 形状 .而 者采 用隐式T (oa L ga ga L T tl a r n in)
回弹 是 板 材 冲压 成 形 过 程 的 主 致使 板 料 产 生 很 大 的弹 性 应 变 能
要 缺 陷 之一 .严 重 影 响着 成 形 件 的 在 模 具 与板 料 动 态 接触 过 程 中存 在 程 .并应 用该 算法模 拟 了3 复 杂冲 个
成 形 质量 和 尺 寸精 度 .是 实 际工 艺 于板 料 中 的这 种 弹 性应 变 能 会 随 着 压件 的卸 载 回 弹过 程 ,这种 算 法 的
解决 的关键性问题 。
且 依 赖 于 成 形后 存 储 在 板 料 中 的弹 算法 .引入 Hi- 次 方屈 服 函数模拟 l l
板料弯曲回弹分析与控制

Ana l y s i s a nd Co n t r o l o f Be S he e t Me t a l s
板料弯曲回弹及工艺控制

板料弯曲回弹及工艺控制板料在弯曲过程中,产生塑性变形的同时会产生弹性变形。
当工件弯曲后去除外力时,会立即发生弹性变形的恢复,结果使弯曲件的角度和弯曲半径发生变化,与模具相应形状不一致,即产生回弹。
回弹是弯曲成形过程的主要缺陷,它的存在造成零件的成形精度差,显著地增加了试、修模工作量和成形后的校正工作量,故在冲压生产中,掌握回弹规律非常重要。
如果在设计模具前,能准确掌握材料的回弹规律及回弹值大小,设计模具时可预先在模具结构及工作部分尺寸上采取措施,试冲后即使尺寸精度有所差异,其修正工作量也不会太大,这不仅可以缩短模具制造周期,而且有利于模具成本的降低及弯曲件精度的提高。
1 弯曲回弹的表现形式弯曲回弹的表现形式有下列二个方面(如图1所示):(a) 弯曲半径增加:卸载前板料的内半径r (与凸模的半径吻合),在卸载后增加至r0,半径的增量为△r二r0一r(b) 弯曲件角度增大:卸荷前板料的弯曲角为α(与凸模的顶角吻合),在卸荷后增大到α0,角度增量为△α=α0一α图1 回弹导致弯曲角和弯曲半径变化2 弯曲回弹产生的原因弯曲回弹的主要原因是由于材料弹性变形所引起的。
板料弯曲时,内层受压应力,外层受拉应力。
弹塑性弯曲时,这两种应力尽管超过屈服应力,但实际上从拉应力过渡到压应力时,中间总会有一段应力小于屈服应力的弹性变形区。
由于弹性变形区的存在,弯曲卸载后工件必然产生回弹。
在相对弯曲半径较大时,弹性变形区占的比重大,回弹尤其显著。
回弹是由于在板厚方向应力或应变分布不均匀而引起的。
这种应力和应变的不均匀分布是弯曲的特点,对于只施加弯矩的弯曲方式,要有效减少回弹是困难的。
为了使回弹减小,应尽量使板厚断面内的应力和应变分布均匀,为此可采取在纵向纤维方向对板料进行拉伸或压缩的方法,也可采用在板厚方向施加强压的方法。
在沿板的长度方向单纯拉伸变形的场合,除去外力后,由于在整个板厚断面内变形的恢复是均匀的,所以不会发生形状的变化。
板材与型材弯曲回弹控制原理与方法

板材与型材弯曲回弹控制原理与方法
在机械制造和建筑行业中,板材与型材的弯曲加工是非常常见的操作。
而在弯曲完成后,材料往往会出现一定的回弹现象,导致加工精度受到影响。
因此,如何控制弯曲回弹,提高加工精度成为了重要的问题。
一、弯曲回弹原理
当一段材料被弯曲后,由于材料内部的分子结构发生了变化,使得材料内部存在的应力分布也发生了改变。
在材料恢复到原始状态之前,这些应力将继续作用于材料,导致弯曲回弹现象的发生。
二、弯曲回弹控制方法
1. 选择合适的弯曲工艺
选择合适的弯曲工艺是减少弯曲回弹的关键。
常用的弯曲工艺包括冷弯、热弯和滚弯等。
冷弯工艺的回弹最大,而热弯和滚弯工艺则可以减少回弹。
2. 适当增加弯曲角度
在弯曲时,适当增加弯曲角度可有效减少回弹。
但是过分增加弯曲角度会导致破坏材料。
3. 采用预压弯曲方法
预压弯曲方法是指在正式弯曲前先对材料进行一定的预压弯曲,以减小材料内部应力分布的差异,从而减少回弹。
但是预压弯曲方法要求对材料和弯曲机具有更高的要求。
4. 加工后热处理
通过加工后热处理,可以改变材料内部的分子结构,从而减少回弹。
但是加工后热处理时间和温度的控制需要非常精准。
三、结论
以上是板材与型材弯曲回弹控制原理与方法的介绍。
在实际生产中,需要综合考虑材料的性质、弯曲工艺的选择、弯曲角度的控制、预压弯曲和加工后热处理等因素,以减少回弹现象,提高加工精度。
板料成形回弹模拟

第6卷第3期1999年9月塑性工程学报JOU RNAL O F PLA ST I C IT Y EN G I N EER I N GV o l16 N o13Sep t1 1999板料成形回弹模拟Ξ(北京航空航天大学 100083) 张晓静 周贤宾摘 要 本文阐述了板料成形数值模拟中回弹问题的研究历史和发展现状,总结了回弹模拟的算法,从成形过程模拟和回弹计算两方面系统分析了影响回弹模拟准确性和收敛性的主要因素及改进方向,并进一步讨论了模具设计中回弹的补偿算法。
关键词 板料成形 回弹模拟 有限元 动态显式 静态隐式1 前 言在板料成形领域,回弹是模具设计中要考虑的关键因素,零件的最终形状取决于成形后的回弹量。
回弹现象主要表现为整体卸载回弹、切边回弹和局部卸载回弹,当回弹量超过允许容差后,就成为成形缺陷,影响零件的几何精度。
因此,回弹一直是影响、制约模具和产品质量的重要因素。
随着汽车工业和航空工业的发展,对薄板壳类零件成形精度的要求越来越高,特别是近年来由于高强度薄钢板和铝合金板材的大量使用,回弹问题更为突出,成为汽车和飞机等工业领域关注的热点问题。
目前,回弹计算功能及回弹模拟精度,已成为衡量板料成形有限元模拟软件技术水平的重要标志之一。
本文旨在总结板料成形回弹模拟计算的研究历史和发展现状,分析影响回弹模拟精度的主要因素及存在问题,希望能对板料成形有限元数值模拟技术的研究者提供一些启发,也为工艺和科研人员更好地利用现有的有限元分析软件,解决工程实际问题提供一些帮助。
2 研究历史与发展现状在过去几十年间,世界各国在回弹的预测及减小方法方面作了大量的工作,建立了一些描述和预测零件回弹的数学模型。
早期的工作主要基于解析法对一些简单零件纯弯曲或拉弯成形的回弹进行分析[1,2]。
M ai H uang和Jam es C.Gerdeen[3]总结了1994年以前板料成形回弹问题的研究状况,分析了双曲度可展曲面零件的回弹规律,并介绍了大约90篇参考文献。
【干货】冲压成型工艺如何控制回弹?
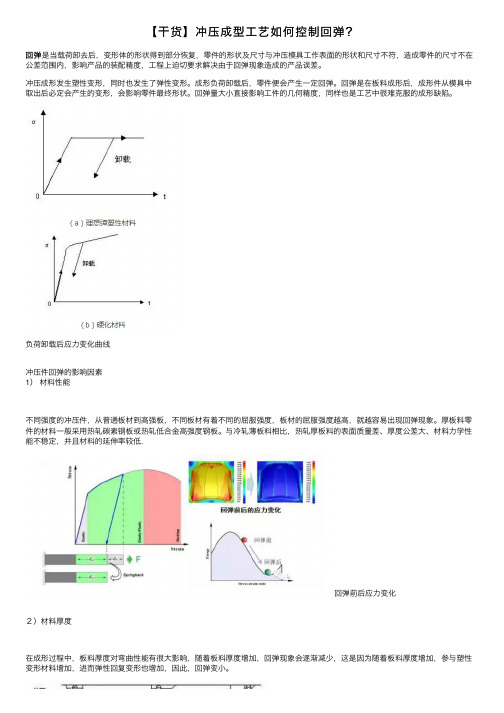
【⼲货】冲压成型⼯艺如何控制回弹?回弹是当载荷卸去后,变形体的形状得到部分恢复,零件的形状及尺⼨与冲压模具⼯作表⾯的形状和尺⼨不符,造成零件的尺⼨不在回弹公差范围内,影响产品的装配精度,⼯程上迫切要求解决由于回弹现象造成的产品误差。
冲压成形发⽣塑性变形,同时也发⽣了弹性变形。
成形负荷卸载后,零件便会产⽣⼀定回弹。
回弹是在板料成形后,成形件从模具中取出后必定会产⽣的变形,会影响零件最终形状。
回弹量⼤⼩直接影响⼯件的⼏何精度,同样也是⼯艺中很难克服的成形缺陷。
负荷卸载后应⼒变化曲线冲压件回弹的影响因素1)材料性能不同强度的冲压件,从普通板材到⾼强板,不同板材有着不同的屈服强度,板材的屈服强度越⾼,就越容易出现回弹现象。
厚板料零件的材料⼀般采⽤热轧碳素钢板或热轧低合⾦⾼强度钢板。
与冷轧薄板料相⽐,热轧厚板料的表⾯质量差、厚度公差⼤、材料⼒学性能不稳定,并且材料的延伸率较低.回弹前后应⼒变化2)材料厚度在成形过程中,板料厚度对弯曲性能有很⼤影响,随着板料厚度增加,回弹现象会逐渐减少,这是因为随着板料厚度增加,参与塑性变形材料增加,进⽽弹性回复变形也增加,因此,回弹变⼩。
板料界⾯的切向应⼒随着厚板料零件材料强度级别的不断提⾼,回弹所造成零件尺⼨精度的问题越来越严重,模具设计和后期的⼯艺调试都要求对零件回弹的性质及⼤⼩有所了解,以便采取相应的对策和补救⽅案。
对于厚板料零件,其弯曲半径与板厚之⽐⼀般都很⼩,板厚⽅向的应⼒及其应⼒变化不容忽视.。
3)零件形状不同形状零件回弹差异很⼤,形状复杂的零件⼀般都会增加⼀序整形,防⽌成形不到位出现回弹现象,⽽更有⼀部分特殊形状零件⽐较容易出现回弹现象,如U形零部件,在分析成形过程中,必须考虑回弹补偿事宜。
4)弯曲中⼼⾓弯曲中⼼⾓的值越⼤就表⽰回弹累积值越⼤,这样就会造成严重的回弹现象,冲压件形变的长度随着弯曲中⼼⾓的增⼤⽽增⼤。
5)模具间隙配合情况模具在设计时就要在相对⼯作部分留有⼀倍料厚的间隙,在间隙中容纳产品。
板料成形回弹模拟及补偿技术研究现状
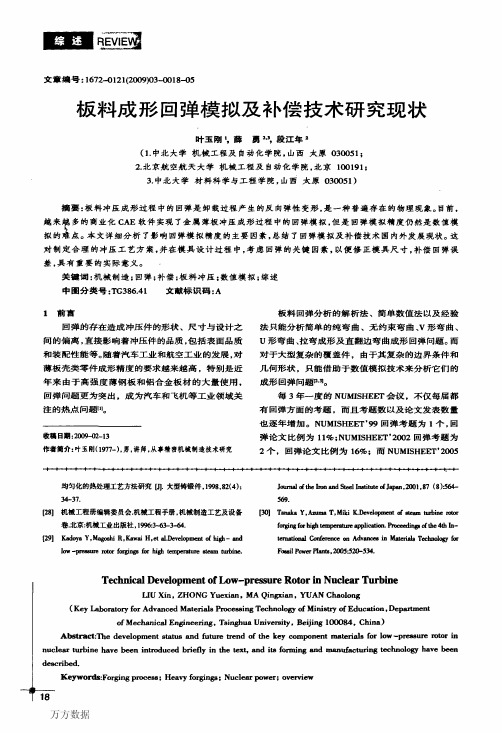
steam
turbine
rotor
forging for
application.Pmceedinss dthe 4th In—
Y,M%,oehi R。Kawai H,et a1.Development of IIigh—and
rotor
territorial C叩fe唧脱Oll Advances in M砒e血118 Technology for
收藕日期:2009-02—13 作者简介:叶玉刚(1977一),男,讲师,从事精密机械制造技术研究
成形回弹问题鲫。 每3年一度的NUMISHEET会议。不仅每届都
有回弹方面的考题。而且考题数以及论文发表数量 也逐年增加。NUMISHEET’99回弹考题为1个。回 弹论文比例为11%;NUMIsHEET’2002回弹考题为 2个,回弹论文比例为16%;而NUMlSHEET’2005
弹控制,将在线识别的冲头行程一冲压力曲线参数
作为人工神经网络的输入,以此来识别材料参数和 工艺参数,输出控制压边力以减小回弹。wu和
量:啪filli妒.1等人研究了回弹量的模具补偿方法。其基
本思想是基于有限元仿真,通过迭代算法对模具形 状进行不断修正,使得最后成形的零件在回弹后恰 好满足设计形状要求。如果冲压成形和回弹模拟精 度能够得到保证。这些回弹控制方法都能取得较满 意的结果。 国内外学者在数值模拟技术的材料模型、求解 算法、求解过程、单元技术等方面进行了大量的研 究,也取得了一定的进展叫.。.11.12一。 3.1材料模型方面的研究。
Paper-
拟,不仅接触摩擦最为严重,而且非线性问题最为突
出。单元的优劣及尺寸的影响、接触算法及摩擦模型 的科学性、本构方程及硬化规律的合理性、有限元算
板材成形的回弹预测和控制的研究

1引 言
板材 冲压 成 形过 程是 一 个包 含 材料 的大变 形 、 大转 移 、接 触碰 撞 、摩 擦 磨 损 等 多种 非 线 性 因素 耦 合 的过 程 .因此 其 模 具 的 设计 和成 形 精 度 的控 制 非 常 困难 .从 而造 成 板 材 成形 过 程 中容 易 产 生 起 皱 、破 裂 和 回 弹等 缺 陷 。经 过 长期 的工 程 实 践 和不 断 地 研 究 .针 对 起 皱 和 破 裂 问题 已经 有 了许 多有 效 的分 析方 法 和 控 制措 施 。然 而 .复 杂 形 状 冲压件 的回弹 问题 一直 没有 获得 很好 的解 决 办法 。 回 弹是 冷 冲 压 成 形过 程 中不 可 避 免 的物 理 现
回弹 预 测 及 控 制 方 面 也 连续 进 行 了有 益 的 研 究 ,
几 何 形 状 、摩 擦 接 触 等众 多 因 素密 切 相 关 ,所 以 板 材 成 形 的 回 弹 问题 非 常复 杂 ,它 不 能 简 单 地 理 解 为 弹 性 卸 载 过 程 。可 能还 伴 有 局 部 加 载 过 程 ,
件 回弹误差 。
在 近几 年 的研究 中 ,A rs 出了使用 多步 法 ye 提
成 形 工 艺 以减 小 冲 压 过程 中 的 回 弹 [ 。C o 8 h u和 ]
Hu g 析 了几种 在 U形 弯 曲工艺 中减 小 回弹 的技 n分
术 ,与 成形 结 果 的优 化 分 析相 结 合 ,得 出 了每 种 工艺 的最优 成形参 数 [。 9 ] 32模具 型面 补偿 法 .
解决成型回弹的措施

解决成型回弹的措施主要有以下几种:
1. 拉弯:这种方法是在板料弯曲的同时施加切向拉力,改变板料内部的应力状态和分布情况,让整个断面处于塑性拉伸变形范围内,卸载后内外层的回弹趋势相互抵消,减小了回弹。
2. 局部压缩:通过减薄外侧板料的厚度来增加外侧板料的长度,使内外层的回弹趋势相互抵消。
3. 多次弯曲:将弯曲成形分成多次来进行,以消除回弹。
4. 内侧圆角钝化:从弯曲部位的内侧进行压缩,以消除回弹。
5. 变整体拉延成为部分弯曲成形:将零件一部分采用弯曲成形后再通过拉延成形以减少回弹。
6. 控制残余应力:拉延时在工具的表面增加局部的凸包形状,在后道工序时再消除增加的形状,使材料内的残余应力平衡发生变化,以消除回弹。
7. 负回弹:在加工工具表面时,设法使板料产生负向回弹。
上模返回后,制件通过回弹而达到要求的形状。
8. 电磁法:利用电磁脉冲冲击材料表面,可以纠正由于回弹造成的形状和尺寸误差。
9. 控制模具和工艺参数:优化模具设计和工艺参数,如弯曲角、模具工作部分尺寸等,以降低回弹。
10. 材料选择:选择具有较低弹性模量和应变时效的材
料,或通过材料改性来降低回弹。
在解决成型回弹时,应根据实际情况选择合适的措施。
板料成形回弹问题研究新进展_朱东波

第7卷第1期2000年3月塑性工程学报JOU RN AL O F PLASTICITY EN GIN EERIN GV ol.7 No.1Ma r . 2000板料成形回弹问题研究新进展*(西安交通大学先进制造技术研究所 710049)朱东波 孙 琨李涤尘 卢秉恒摘 要:本文从回弹理论、回弹数值模拟分析、回弹控制三方面对弯曲成形、3-D 复杂浅拉深成形中回弹研究的历史和最新发展状况作了较全面的介绍。
文章所引用的大量文献基本概括了前人在这些方面的主要研究方法和重要研究成果。
关键词:回弹;板料成形;模具*国家“九·五”重点攻关资助项目(项目号:85-951-19)。
收稿日期:1999-4-281 引 言板料成形过程中普遍存在有回弹问题,特别在弯曲和浅拉深过程中回弹现象更为严重,对零件的尺寸精度和生产效率造成极大的影响,有必要对其进行深入的研究和有效的控制。
零件的最后回弹形状是其整个成形历史的累积效应,而板料成形过程与模具几何形状、材料特性、摩擦接触等众多因素密切相关,所以板料成形的回弹问题非常复杂。
半个多世纪来国内外许多学者对回弹问题进行了深入的研究和探讨,这些研究涵盖了从弯曲成形到复杂拉深成形、从理论分析到数值模拟、从回弹预测到回弹控制等诸多方面。
本文从三个方面对前人的工作进行了概括性回顾,重点介绍了90年代回弹研究的一些新进展。
2 弯曲理论研究和回弹的解析分析方法 弯曲成形一般只涉及较为简单的几何形状和边界条件,所以有条件用解析方法对其进行深入的研究。
50年代,R .H ill 、F .Proska 、F .J .Gardiner 等人的工作奠定了板料弯曲及回弹分析的理论基础[1],后来不断有学者对这些理论进行深化和发展。
Huang ,etc [2]在其文章中对50年代到80年代间诸多学者的回弹研究工作做了较详细的回顾和评述。
回弹是弯曲卸载过程产生的反向弹性变形,板料回弹的经典计算公式为:Δk =1R -1R S =12M (1-ν2)Et3(1)式中 Δk ——曲率变化量R ——回弹前中面半径R S ——回弹后中面半径E ——弹性模量ν——泊松比t ——回弹前板料厚度M ——回弹前板内弯矩弯矩M 由截面纵向应力分布唯一确定。
铝板冲压工艺——外板回弹原因分析及控制措施

铝板冲压工艺——外板回弹原因分析及控制措施铝板零件的回弹补偿相对于钢板而言更加复杂,且更加具有不稳定性。
为此针对铝板回弹较大的问题,我们提出了综合化的前期补偿策略,即在铝板模具开发前期,综合考虑零件工艺的稳健性(材料,设备,润滑条件),GD&T的合理性,回弹量,补偿策略等重要因素进行回弹补偿。
经过综合化补偿策略完成高品质的前期要求后,在后期的制造中,零件经过较少的整改即能够达到90%以上的合格率。
下面以铝板前罩外板与车门外板为例,进行分析介绍。
前罩外板材料回弹控制1 前罩外板材料特性简介本次分析的是江淮汽车正在生产的某个前罩外板,采用的外板料来自Novelis e170,厚度为0.9mm,由于板料的加工和材料特点,铝板是具有时效性的,从板料冲压成形角度考虑,3个月时的性能为最佳,并且需进行6个月的验证,用以指导板料的生产,如表1所示。
表1 e170的板料性能失效数据对比2 前罩外板的成形模拟前罩外板的工艺流程为拉延→修边、侧修边→翻边、侧翻边、修边→翻边、侧翻边→空工位。
根据前罩外板产品的形状和材料的特点进行拉延面设计,用CATIA设计如图1所示。
图1前罩外板和内板拉延模面设计图3 零件的稳健性分析流程零件的成形使用AutoForm R7进行分析,对软件的设置和参数的评估,需要根据相应企业标准进行设置,用以判断变薄、开裂、起皱、回弹、全局的变薄率等大的问题项,然后针对各个问题项进行解决,并结合生产线的要求,调整初版的工艺,最后进行工艺审核和稳健性因素的排查,得到稳健性的工艺工法,分析流程如图2所示。
图2铝板冲压稳健性分析流程其中,稳健性分析主要有以下内容:⑴料片形状和位置波动(±5mm);⑵材料的屈服和抗拉强度波动(±10%);⑶材料的r值和n值波动(±10%);⑷摩擦系数波动(±10%);⑸压边力波动(±10%)。
代入对应的参数进行Sigma分析,分析完成后进行判断:对于最大失效可设置为0.8,减薄可设置为16%,外加起皱,自由回弹的情况进行评价。
汽车厚板料零件冲压成形分析及回弹计算

工 步 -7 4
工步
9 5
时 间 .12 0 + 0e
0 e 0 00 -0 2 2 e 0 00 一0 2 4 e 0 00 -0 2 6 0 00 0 e- 2 8 0 00 0 e- 2 0 0 00 0 e一 2
8 7 3 2 6 5 4 4 2 1 8
■
中国第 一汽车 股份 有 限公 司技术 中心
富 壮
随着 我 国 汽 车 板 料 零 件 设 计 、制 造 水 平 的 不 断
提 高 ,薄板料零件冲压成形C 技术 的应用 已 日趋 AE
成 熟 ,相 关 产 品 的设 计 和 制 造 部 门针 对 不 同软 件 及
1 厚 板料零 件 冲压成形及 其CA 技术 E 的特点
0 0 00 0 e+ 0
4 00 e 0 0 -0 2 32 0 0 2 0 e一 0 2. 0 0 2 40 e一 0 160 e- 0 . 0 02 8. 0 0 3 00 e一 0 0. 0 0 0 00 e+ 0
( ) 通 实体 单元 a 普
( )实体 厚 壳单元 b
工步 .1 时间 1 0 e 0 0 0 + 0 0
2 计算模型建立时需要注意 的问题
2 1 单元 选择 .
MS 软 件 有两种 单 元供 厚板 料零 件 冲压 成 C Mac r 形C E A 分析 时选 用 。一 种是 普通 实体 单 元 ,另 一种 是 实体 厚壳 单 元。 实体厚 壳 单元 是基于 选 择性缩减 积 分和假 定应 变 技术 的 ,由于是 八节 点拓 扑结 构 ,可 以实现 板料 内外
80 0 0 e一0 2 0 7 2 0 00 0 e~ 2
6 4 0 00 0 e- 2 5 60 e 0 0 -0 2 4. 0 0 2 80 e一 0
板的冲压塑性成型及回弹分析
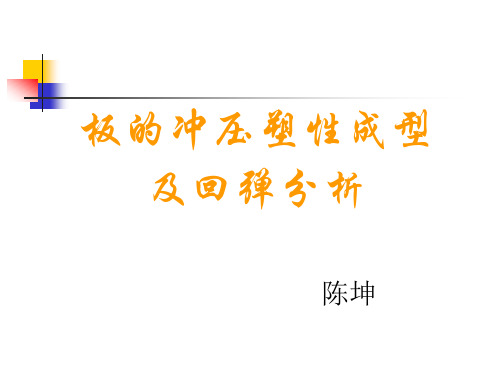
3问题描述
1、假设 a>模具是刚性的(即不考虑 任何变形),而钢板是柔性的; b>假设冲头下降了0.5m,且 整个过程完成历时1s;然后冲头 上升0.25m 。 2、过程分析 a>冲压过程中发生了塑性大 变形(该过程与加载路径相关), 是一个典型的塑性成型的问题。 b>当冲压成型完成后,当冲 头上升,钢板将有一定的回弹。
27
keyopt,5,10,2 keyopt,3,10,2
mp,ex,1,7e10 mp,prxy,1,0.325 tb,miso,1,1,4 tbtemp,0 tbpt,,0.0007857,55e6 tbpt,,0.00575,112e6 tbpt,,0.02925,172e6 tbpt,,0.1,241e6 mp,ex,2,2e13 mp,prxy,2,0.3 mshkey,0 asel,s,loc,y,0,1 type,6 mat,2 mshape,0,2d amesh,all mshkey,2 lsel,s,loc,y,1.2 lsel,r,loc,x,1 lesize,all,,,80 lsel,s,loc,x,-0.1,-2 lesize,all,,,10 asel,s,loc,y,1,1.2 type,1 mat,1 amesh,all
面面接触:目标面和接触面组成一个接触对,ANSYS 用相同的实常数编号识别接触对。 目标单元:二维tartet169和三维tartet170号单元 接触单元:二维contact171和contact172 contact171 contact172 三维contact173和contact174
接触向导
塑性——材料非线性
路径相关性:必须按真实的加载过程加载。 应力应变数据:对大应变的塑性分析一般采 用真实的应力、应变数据,而小应变分析一 般采用工程的应力、应变数据。 经典双线性随动强化(BKIN),适用于遵守 Von Mises屈服准则,初始为各向同性材料 的小应变问题,这包括大多数的金属。需要 输入的常数是屈服应力和切向斜率。
板料成形回弹特征及其控制技术
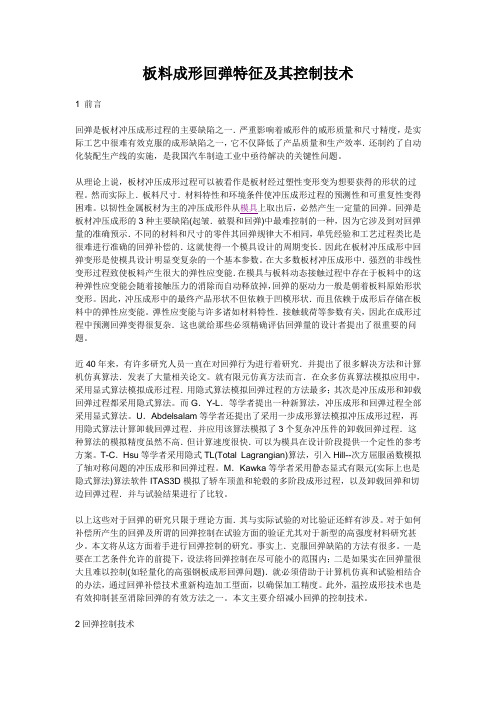
板料成形回弹特征及其控制技术1 前言回弹是板材冲压成形过程的主要缺陷之一.严重影响着威形件的威形质量和尺寸精度,是实际工艺中很难有效克服的成形缺陷之一,它不仅降低了产品质量和生产效率.还制约了自动化装配生产线的实施,是我国汽车制造工业中亟待解决的关键性问题。
从理论上说,板材冲压成形过程可以被看作是板材经过塑性变形变为想要获得的形状的过程。
然而实际上.板料尺寸.材料特性和环境条件使冲压成形过程的预测性和可重复性变得困难。
以韧性金属板材为主的冲压成形件从模具上取出后,必然产生一定量的回弹。
回弹是板材冲压成形的3种主要缺陷(起皱.破裂和回弹)中最难控制的一种,因为它涉及到对回弹量的准确预示.不同的材料和尺寸的零件其回弹规律大不相同,单凭经验和工艺过程类比是很难进行准确的回弹补偿的.这就使得一个模具设计的周期变长.因此在板材冲压成形中回弹变形是使模具设计明显变复杂的一个基本参数。
在大多数板材冲压成形中.强烈的非线性变形过程致使板料产生很大的弹性应变能.在模具与板料动态接触过程中存在于板料中的这种弹性应变能会随着接触压力的消除而自动释放掉,回弹的驱动力一般是朝着板料原始形状变形。
因此,冲压成形中的最终产品形状不但依赖于凹模形状.而且依赖于成形后存储在板料中的弹性应变能。
弹性应变能与许多诸如材料特性.接触载荷等参数有关,因此在成形过程中预测回弹变得很复杂.这也就给那些必须精确评估回弹量的设计者提出了很重要的问题。
近40年来,有许多研究人员一直在对回弹行为进行着研究.并提出了很多解决方法和计算机仿真算法.发表了大量相关论文。
就有限元仿真方法而言.在众多仿真算法模拟应用中,采用显式算法模拟成形过程.用隐式算法模拟回弹过程的方法最多;其次是冲压成形和卸载回弹过程都采用隐式算法。
而G.Y-L.等学者提出一种新算法,冲压成形和回弹过程全部采用显式算法。
U.Abdelsalam等学者还提出了采用一步成形算法模拟冲压成形过程,再用隐式算法计算卸载回弹过程.并应用该算法模拟了3个复杂冲压件的卸载回弹过程.这种算法的模拟精度虽然不高.但计算速度很快.可以为模具在设计阶段提供一个定性的参考方案。
浅谈解决回弹现象的措施

目录摘要 (Ⅱ)关键词 (Ⅱ)正文 (Ⅱ)1 板料回弹的产生 (2)2 回弹现象的分析 (2)3 影响回弹的主要因素 (2)参考文献 (Ⅴ)结束语 (Ⅵ)摘要弯曲件在机械零件中占有相当大的比例,它的质量将直接影响整机质量,而回弹是影响弯曲件质量的重要因素,因此探讨弯曲件回弹的原因和防止措施是非常必要的。
寻求防止回弹的有效途径和方法,对保证产品质量和提高弯曲件生产的经济性是有积极现实意义的。
关键词:弯曲;回弹;措施正文:一、板料回弹的产生在板料弯曲成形过程中,板料内外缘表层纤维进入塑性状态,而板料中心仍处于弹性状态,这时当凸模上升去除外载后,板料就会产生弹性回复。
金属塑性成形总是伴有弹性变形,所以板料弯曲时,即使内外层纤维全部进入塑性状态,在去除外力时,弹性变形消失,也会出现回弹。
弯曲时,弯曲变形只发生在弯曲件的圆角附近,直线部分不产生塑性变形。
影响板料弯曲回弹的因素很多,大体可分为以下几种:(1)材料的力学性能。
(2)相对弯曲半径 R/t的影响。
(3)弯曲角的影响。
(4)弯曲零件形状的影响。
(5)模具几何参数影响。
(6)张力的影响。
(7)工况参数。
(8)模具间隙的影响。
(9)弯曲校正力的影响。
(10)弯曲方式的影响。
二、回弹现象的分析由于金属板料在塑性弯曲时总伴随着弹性变形产生,当弯曲件从模具中取出之后,弯曲件不受外力的作用,弹性变形消失,使工件的弯曲角度和弯曲半径发生变化,皆与模具的设计尺寸存在一个差值,这种现象称为弯曲件的回弹。
三、影响回弹的主要因素3. 1 材料的机械性能回弹的大小与材料的屈服极限成正比,与弹性模数成反比,即 Qs/E值愈小,回弹也愈小。
Qs——材料的屈服极限E——材料的弹性模数3. 2 相对弯曲半径 r/t相对弯曲半径即弯曲半径与板料厚度之比 r/t,在相同条件下, r/t愈小,说明弯曲变形程度愈大,在总变形中弹性变形所占比例相应减小,则回弹就愈小。
3. 3 弯曲中心角弯曲中心角愈大,变形区域愈大,回弹积累值也愈大,则回弹角也愈大。
浅谈弯曲回弹及防止措施

浅谈弯曲回弹及防止措施作者:李洪林来源:《城市建设理论研究》2013年第24期摘要:本文结合作者多年的工作经验,阐述了影响回弹的主要因素及防止回弹的措施,提供给大家参考。
关键词:弯曲;回弹;措施中图分类号:TG386文献标识码: A 文章编号:弯曲件在机械零件中占有相当大的比例,它的质量将直接影响整机质量,而回弹是影响弯曲件质量的重要因素,因此探讨弯曲件回弹的原因和防止措施是非常必要的。
寻求防止回弹的有效途径和方法,对保证产品质量和提高弯曲件生产的经济性是有积极现实意义的。
如果弯曲件质量要求高时,采用特殊工艺也是必要的。
1、板料回弹的产生;在板料弯曲成形过程中,板料内外缘表层纤维进入塑性状态,而板料中心仍处于弹性状态,这时当凸模上升去除外载后,板料就会产生弹性回复。
;金属塑性成形总是伴有弹性变形,所以板料弯曲时,即使内外层纤维全部进入塑性状态,在去除外力时,弹性变形消失,也会出现回弹。
弯曲时,弯曲变形只发生在弯曲件的圆角附近,直线部分不产生塑性变形。
;影响板料弯曲回弹的因素很多,现就其定性影响综述如下:;(1)材料的力学性能。
弯曲件的材料特性对回弹有直接影响,一般来说,回弹量大小与材料的屈服强度σs成正比,与材料的弹性模量E成反比,如图1所示。
板厚各向异性r值和材料强化系数K值越小,材料的应变强化指数n值就越大,回弹量也就越小。
(2)相对弯曲半径R/t的影响。
相对弯曲半径表示弯曲成形的变形程度,回弹值与相对弯曲半径成正比,相对弯曲半径越小,断面中塑性变形区越大,切向总应变中弹性应变分量所占的比例越小,因此卸载时弹性回弹随相对弯曲半径的减小而减小;而相对弯曲半径较大时,虽然变形程度很小,但材料断面中心部分会出现很大的弹性区,所以回弹量较大。
;(3)弯曲角的影响。
在一定的相对弯曲半径情况下,弯曲角越大,则对应的参加变形的区域越大,弹性变形量的累积量也越大,因此工件的回弹值也越大。
;(4)弯曲零件形状的影响。
板料回弹机理及控制

板料回弹机理及控制摘要:回弹是板料冲压成形中普遍存在的现象,回弹的存在直接影响到冲压件的形状尺寸精度,产生后续的质量、装配问题。
因此,回弹问题不但是工业生产中需解决的一个实际问题,也是学术界长期关注的热点。
关键词:板料回弹;机理;控制回弹是板料加工中最常见的废次品形式之一,也是弯曲工艺中的技术难点之一。
同时,它也是板料冲压成形过程中的主要缺陷之一,严重影响了质件的尺寸精度和外观的质量,是实际工艺中很难掌握的一个缺陷。
一、板料回弹现象回弹是卸载过程产生的反向弹性变形,是板料冲压成形过程中存在的一种普遍现象。
在弯曲和托深过程中,回弹现象尤为严重,对零件的尺寸精度、生产效率和经济效益产生极大的影响。
二、板料回弹机理板料在外加弯曲力矩的作用下,首先发生弹性弯曲变形,在弹性弯曲阶段,对弯曲半径很大,板料内弯曲半径与凸模圆角半径不相重合,板料变形很小。
在弯曲变形区内,板料弯曲内侧(靠近凸模一边)的材料受到压缩而缩短,应力状态是单向受压。
板料弯曲外侧(靠近凹模的一边)受拉而伸长,应力状态是单向受拉。
弯曲内、外表面到中心,其缩短与伸长的程度逐渐变小,在缩短与伸长的两个变形区之间,有一纤维层长度始终不变即应变为零,称为应变中性层。
同样,在拉应力向压应力过渡之间,存在一个切向应力为零的应力层,称为应力中性层。
在一般情况下可认为两个不同性质的中性层重合在一起,简称为中性层。
随着弯矩的增加,板料弯曲变形增大,板料内外表层金属先达到屈服极限,板料开始由弹性变形阶段转入弹塑性变形阶段,其应力分布随着弯矩的不断增加,塑性变形区由表层向内扩展,板料中间的弹性变形区逐渐变小,最后整个断面进入塑性状态。
图1中第二副图显示了反向加了弯矩所产生的应力变化图。
第三副图显示的是残余应力图,即是能产生回弹的应力。
弯曲回弹的主要原因由于材料弹性变形引起。
板料弯曲时,内层受压应力,外层受拉应力。
弹塑性弯曲时,这两种应力尽管超过屈服应力。
但实际上从拉应力过渡到压应力时,中间总会有一段应力小于屈服应力的弹性变形区,由于弹性区的存在,弯曲卸载后工件必然产生回弹。
基于回弹控制的板料成形工艺优化方案分析
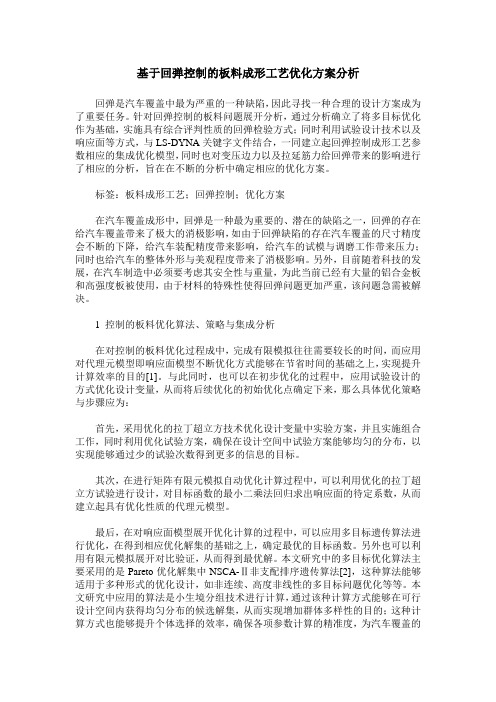
基于回弹控制的板料成形工艺优化方案分析回弹是汽车覆盖中最为严重的一种缺陷,因此寻找一种合理的设计方案成为了重要任务。
针对回弹控制的板料问题展开分析,通过分析确立了将多目标优化作为基础,实施具有综合评判性质的回弹检验方式;同时利用试验设计技术以及响应面等方式,与LS-DYNA关键字文件结合,一同建立起回弹控制成形工艺参数相应的集成优化模型,同时也对变压边力以及拉延筋力给回弹带来的影响进行了相应的分析,旨在在不断的分析中确定相应的优化方案。
标签:板料成形工艺;回弹控制;优化方案在汽车覆盖成形中,回弹是一种最为重要的、潜在的缺陷之一,回弹的存在给汽车覆盖带来了极大的消极影响,如由于回弹缺陷的存在汽车覆盖的尺寸精度会不断的下降,给汽车装配精度带来影响,给汽车的试模与调磨工作带来压力;同时也给汽车的整体外形与美观程度带来了消极影响。
另外,目前随着科技的发展,在汽车制造中必须要考虑其安全性与重量,为此当前已经有大量的铝合金板和高强度板被使用,由于材料的特殊性使得回弹问题更加严重,该问题急需被解决。
1 控制的板料优化算法、策略与集成分析在对控制的板料优化过程成中,完成有限模拟往往需要较长的时间,而应用对代理元模型即响应面模型不断优化方式能够在节省时间的基础之上,实现提升计算效率的目的[1]。
与此同时,也可以在初步优化的过程中,应用试验设计的方式优化设计变量,从而将后续优化的初始优化点确定下来,那么具体优化策略与步骤应为:首先,采用优化的拉丁超立方技术优化设计变量中实验方案,并且实施组合工作,同时利用优化试验方案,确保在设计空间中试验方案能够均匀的分布,以实现能够通过少的试验次数得到更多的信息的目标。
其次,在进行矩阵有限元模拟自动优化计算过程中,可以利用优化的拉丁超立方试验进行设计,对目标函数的最小二乘法回归求出响应面的待定系数,从而建立起具有优化性质的代理元模型。
最后,在对响应面模型展开优化计算的过程中,可以应用多目标遗传算法进行优化,在得到相应优化解集的基础之上,确定最优的目标函数。
- 1、下载文档前请自行甄别文档内容的完整性,平台不提供额外的编辑、内容补充、找答案等附加服务。
- 2、"仅部分预览"的文档,不可在线预览部分如存在完整性等问题,可反馈申请退款(可完整预览的文档不适用该条件!)。
- 3、如文档侵犯您的权益,请联系客服反馈,我们会尽快为您处理(人工客服工作时间:9:00-18:30)。
板料成形回弹特征及其控制技术
1 前言
回弹是板材冲压成形过程的主要缺陷之一.严重影响着威形件的威形质量和尺寸精度,是实际工艺中很难有效克服的成形缺陷之一,它不仅降低了产品质量和生产效率.还制约了自动化装配生产线的实施,是我
国汽车制造工业中亟待解决的关键性问题。
从理论上说,板材冲压成形过程可以被看作是板材经过塑性变形变为想要获得的形状的过程。
然而实际上.板料尺寸.材料特性和环境条件使冲压成形过程的预测性和可重复性变得困难。
以韧性金属板材为主的冲压成形件从模具上取出后,必然产生一定量的回弹。
回弹是板材冲压成形的3种主要缺陷(起皱.破裂和回弹)中最难控制的一种,因为它涉及到对回弹量的准确预示.不同的材料和尺寸的零件其回弹规律大不相同,单凭经验和工艺过程类比是很难进行准确的回弹补偿的.这就使得一个模具设计的周期变长.因此在板材冲压成形中回弹变形是使模具设计明显变复杂的一个基本参数。
在大多数板材冲压成形中.强烈的非线性变形过程致使板料产生很大的弹性应变能.在模具与板料动态接触过程中存在于板料中的这种弹性应变能会随着接触压力的消除而自动释放掉,回弹的驱动力一般是朝着板料原始形状变形。
因此,冲压成形中的最终产品形状不但依赖于凹模形状.而且依赖于成形后存储在板料中的弹性应变能。
弹性应变能与许多诸如材料特性.接触载荷等参数有关,因此在成形过程中预测回弹变得很复杂.这也就给那些必须精
确评估回弹量的设计者提出了很重要的问题。
近40年来,有许多研究人员一直在对回弹行为进行着研究.并提出了很多解决方法和计算机仿真算法.发表了大量相关论文。
就有限元仿真方法而言.在众多仿真算法模拟应用中,采用显式算法模拟成形过程.用隐式算法模拟回弹过程的方法最多;其次是冲压成形和卸载回弹过程都采用隐式算法。
而G.Y-L.等学者提出一种新算法,冲压成形和回弹过程全部采用显式算法。
U.Abdelsalam等学者还提出了采用一步成形算法模拟冲压成形过程,再用隐式算法计算卸载回弹过程.并应用该算法模拟了3个复杂冲压件的卸载回弹过程.这种算法的模拟精度虽然不高.但计算速度很快.可以为模具在设计阶段提供一个定性的参考方案。
T-C.Hsu等学者采用隐式TL(Total Lagrangian)算法,引入Hill--次方屈服函数模拟了轴对称问题的冲压成形和回弹过程。
M.Kawka等学者采用静态显式有限元(实际上也是隐式算法)算法软件ITAS3D模拟了轿车顶盖和轮毂的多阶段成形过程,以及卸载回弹和切边回弹过程.并与试验结果进行了比较。
以上这些对于回弹的研究只限于理论方面.其与实际试验的对比验证还鲜有涉及。
对于如何补偿所产生的
回弹及所谓的回弹控制在试验方面的验证尤其对于新型的高强度材料研究甚少。
本文将从这方面着手进行回弹控制的研究。
事实上.克服回弹缺陷的方法有很多。
一是要在工艺条件允许的前提下,设法将回弹控制在尽可能小的范围内;二是如果实在回弹量很大且难以控制(如轻量化的高强钢板成形回弹问题).就必须借助于计算机仿真和试验相结合的办法,通过回弹补偿技术重新构造加工型面,以确保加工精度。
此外,温控成形技术也是有效抑制甚至消除回弹的有效方法之一。
本文主要介绍减小回弹的控制技术。
2回弹控制技术
为了避免回弹补偿带来的冲压模面设计的困难,对于许多成形问题,首先希望利用回弹的控制技术来尽可能地消除回弹。
在本文中,首先分门别类地介绍回弹特性和控制方法。
所有由弯曲产生变形的金属板材成形过程的表征是,由弹塑性材料特性引起的板材厚度方向不均匀的位移分布而导致回弹现象的产生。
当某一冲压件成形完毕.即在成形步骤的结尾.板材体积内存在着残余应力.这些残余应力与工具的接触力相平衡。
当工具被释放.就是把成形件从模具上卸下时.板材将寻找新的平衡位置.局部残余应力被释放,导致成形件的最终尺寸与预期值存在一定的偏差,即回弹现象的产生。
也就是说.回弹主要是由于弯曲部位外侧(拉伸)和内侧(收缩)的应力差而引起的。
因此。
为了减少弯曲变形的回弹。
可以考虑给弯曲部位施加外力以消除应力差。
但是.因产品形状和模具结构等而采取的方法有所不同。
图1a给出板材拉伸卸载的应力应变曲线.图1b给出板材弯曲后的卸载回弹特征。
为了减小弯曲变形产生的回弹,应该在工艺条件允许的前提下,尽可能选择屈服应力小的材料。
高强度钢板的屈服应力明显高于普通金属板材,这类材料的回弹量往往很大。
成形板材的厚度对弯曲回弹影响也很大,通常,板越厚,回弹量越小。
此外,工具角部的弯曲半径对回弹影响也不可忽视,弯曲半径越小,成形卸载后的回弹量越小。
因此。
,在板材可成形性允许条件下,应尽可能减小模角半径。
下面针对不同的回弹机制,介绍几种抑制回弹的具体方法和策略。
2.1局部压缩减小回弹方法
如图2,利用压缩工艺在弯曲部位压缩板料外侧(将板料在该部位压缩到大约使厚度减小5%-30%),且不让弯曲内侧变化。
这种"局部压缩"的工艺策略是利用了弯曲部位压缩板料外侧减薄导致板料局部强度降低的
有利因素。
a部分(外侧弯曲尺)不可与弯曲内侧的弯曲尺同心,由于外侧与内侧的弯曲半径不同心且有所稍稍偏移,有利于外侧部分压缩板料减薄。
如果偏移过大,会发生不该产生的变形(如图2c)。
2.2一道工序分2段弯曲方法
如图3,将一次拉延弯曲成形分成2段弯曲成形.以此消除回弹。
第一段弯曲采用大间隙(板厚1.15-1.3倍)加工。
由于间隙大.板料倾斜,模具的弯曲半径也大.使板料大致弯曲。
第二阶段的弯曲是将第一段弯曲的大弯曲半径尺整形到小弯曲半径厂。
第一阶段变形的间隙要从最初的小间隙开始调整,根据控制回弹
的效果而逐步放大。
预测在第二阶段弯曲变形时.由于采用小间隙容易产生。
拉毛现象"(模具磨损而导致制件拉毛).为了消除"
制件拉毛",模具的凹模有时需要采用表面硬化处理。
2.3 内侧圆角尺硬化方法
如图4,从弯曲部位的内侧进行压缩,以消除回弹。
在板材U形弯曲时,由于有两侧对称弯曲,采用这种方法效果比较好。
L形弯曲时一般面部分的材料压料力变弱.有时会产生尺寸变差。
从形状判断,弯曲部位压力弱。
对于既要保证强度又要具有弹性的成形件产品不适用。
另外,还可以变化S(圆角尺处的厚度变化量)的尺寸来调整回弹量。
往往由于压缩圆角尺使得翼面长度而稍微变化.对于翼面高度容差小的产品.有时需要展开长度的补偿。
图4 内侧圆角R硬化方法
2.4 硬化加工法
如图5.使弯曲工具的侧壁翘曲.在钢板上留下硬化筋(TYPEA-C)的痕迹。
硬化筋要用在非变薄面上,注意打痕。
由于硬化筋会划伤产品,因此要根据产品注意选择。
这种回弹抑制
方法对于越厚的板材效果越好。
2.5变整体拉延成形为部分弯曲成形的回弹控制方法
如图6.把整体拉延成形(设整体拉延深度为90 mm)的A部(设为60 mm)采用弯曲成形,消除板外侧和内侧的应力差,剩余30 mm凹模的B部.再通过拉延成形以减少回弹。
这种方法对于二维形状简单的产品有效.对于三维形状的复杂产品有时会产生不合格的效果,要注意选择产品。
2.6消除残余应力方法
如图7,拉延成形时在工具的表面增加局部的凸包形状《圆形凸包).在后道工序时再消除增加的形状,使
材料内的残留应力平衡发生变化,以消除除回弹。
2.7加强筋冻结形状方法
如图8,不改变原产品功能的前提下.改变产品形状,增加加强筋.可以控制和改善回弹。
2.8 负回弹方法
如图9.在加工工具表面时.设法使板料产生负向回弹。
上模返回后,制件回弹,通过负回弹和回弹而达
到要求的产品形状。
2.9淬火,回火抑制回弹方法
如图10.对板料的弯曲部位进行局部的淬火和回火处理,降低屈服点,进而达到消除回弹之目的。
2.10 冻结形状技术
如图11a,板料弯曲变形没有达到正确的曲率,外侧产生拉应力变平回弹.在边缘里面部位产生皱纹,这是由于弧长a和弧长6(如图11b)之la--J的长度差而造成的。
如图11b,由于弧长6比弧长a更短,进而产生堆料(边缘部)产生皱纹;弧长a产生拉应力而变平。
为了消除这种现象.可以考虑设法消除弧长a和弧长b的长度差.如图11c.追加使弧长一致的形状筋是比较有效的。
2.11焊接工序配合消除回弹技术
如图12,利用焊接工序消除回弹影响,首先要求焊接工序指定出点焊顺序,目的是保证有回弹或者回弹量大的部位先焊。
此外,在焊接工序中要追加强制夹紧及克服回弹的强制加强板。
上述回弹控制的成形加工方法基本上能够处理相对简单覆盖件回弹模面设计问题。
但是对于复杂成形覆盖件,特别是新型轻量化板材如高强钢板,屈服极限远远高于普通金属板材。
由于回弹与翘曲量很大,常规的回弹制技术往往难于消除回弹以及回弹带来的制造误差。
基于回弹仿真和试验相结合的回弹加工型面的补偿技术将是未来从根本上解决回弹控制和加工精度问题的重要途径。