氯化物镀锌低铬彩钝变色与脱膜原因浅析
解析镀锌层低铬彩色钝化脱膜的原因
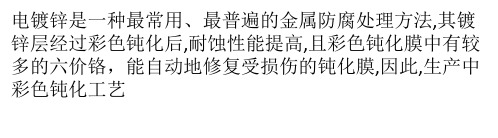
调整pH值最好用硝酸,不要用硫酸或盐酸。但硝酸含量也 不能太高,因为硝酸含量增大,膜溶解加快,使膜变薄,结合 不牢固,易脱落。硝酸含量低,膜的光泽差,不光亮。在平时 操作中
,不能直接加入硫酸,而加入硫酸盐。硫酸过多,加入少量的 碳酸锁或熟石灰,再用硝酸调pH值至1.5左右。同时,钝化 液中锌过多,溶液会老化,钝化膜易脱落或发雾。应再生或 更新
对镀锌层起到化学抛光作用,获得光泽均一的镀层,保证了 钝化膜的结合力和外观质量。5、钝化后处理(1)清洗钝化 后应认真清洗,否则,零件表面残留的酸易造成钝化膜脱落。 所以要
用几道水彻底清洗,且最后要用流动水清洗。(2)烘干(老化) 烘干温度应不大于65°C为宜,以提高钝化膜的硬度及 结合力。否则,钝化膜失水过多,偏红,甚至偏黄,膜易
脱落,易开裂,抗蚀能力下降,且烘干温度应基本保持一致。
பைடு நூலகம்
dejhtsh (小型实验室)电解设备
难控制。时间短,色彩差;时间稍长,膜厚,易脱落。所以在 低铬钝化中,硫酸根的影响最严重。其含量不宜超过0.8g/L, 在通常情况下,活化剂与铬酸酐比值大致为SO2-4/C
r03=1.0-4.0,Cl-/Cr03=1.5-1.0,活化剂不足,成膜速率慢,膜不 清亮,易发白雾;活化剂过多,成膜速率快,膜色泽减退,甚 至得不到彩色钝化膜。因此,
膜的结合力。(3)由于钝化前清洗不认真,会带入大量的氯 离子,虽然氯离子会加速成膜,但会使膜太厚而易脱落。同 时造成钝化时间不易控制。(4)由于操作者的衣物、手套 及与镀件
接触的物品上粘有酸,没有及时清洗掉,在操作过程中无意 和镀件接触,就有可能使钝化膜脱落。3、镀前处理由于镀 前处理时油污及氧化皮等脏污没有彻底清除干净,造成局 部镀层结合力
氯化钾镀锌钝化膜变色原因探讨及控制措施
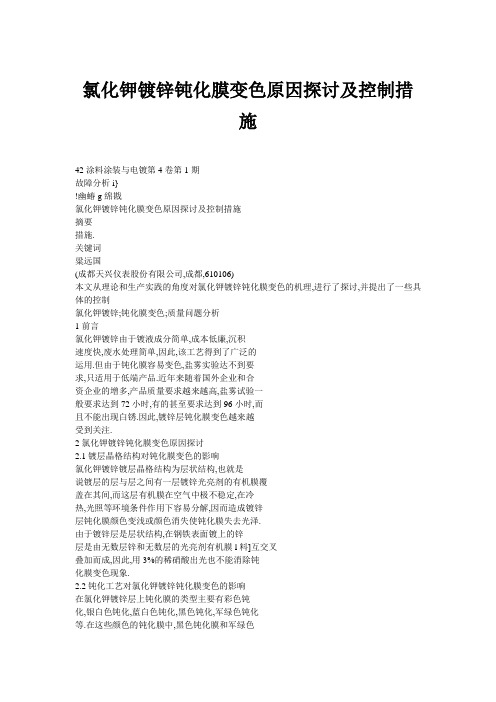
氯化钾镀锌由于镀液成分简单,成本低廉,沉积
速度快,废水处理简单,因此,该工艺得到了广泛的
运用.但由于钝化膜容易变色,盐雾实验达不到要
求,只适用于低端产品.近年来随着国外企业和合
资企业的增多,产品质量要求越来越高,盐雾试验一
般要求达到72小时,有的甚至要求达到96小时,而
且不能出现白锈.因此,镀锌层钝化膜变色越来越
氯化钾镀锌一水洗一碱性溶液除膜一水洗—钝
化一水洗一甩干一老化.
碱性溶液的配方为:
NaOH,g/L80—120
ZnO.g/L8一l2
温度室温
时间,min3—5
经过该方法处理过的镀锌件,其钝化膜的结合
能力得到显着改善.中性盐雾试验能够增长3—8
小时(与同批同槽同一产品比较).
3.2科学合理地添加光亮剂.定期用活性炭处理镀
Yuanguo
(ChengdutianxinginstrmnentandmeterCo.,Ltd,Chengdu,610106)
AilsUm~ThemechanismofchromatingfilmchangecoloronKC1zincplatingarediscussedfromthetheoryandprac-
理技术工作,发表论文十余篇.
3
温
53c:;室
2OO6年2月粱远国:氯化钾镀锌钝化膜变色原因探讨及控制措施43
温度室温
时间,S10—20s
先在低铬彩色钝化液中钝化,不经过老化处理,
直接浸入碳酸钡漂白溶液中除去彩色膜,从而可以
形成银白色钝化膜,然后在含O.3%铬酐的热水
(80Y:一9oc【=)中封闭处理.最后放入温度为6oc【=一
于8oc【=时会造成钝化膜开裂.
镀锌层彩色钝化常见问题及对策-推荐下载
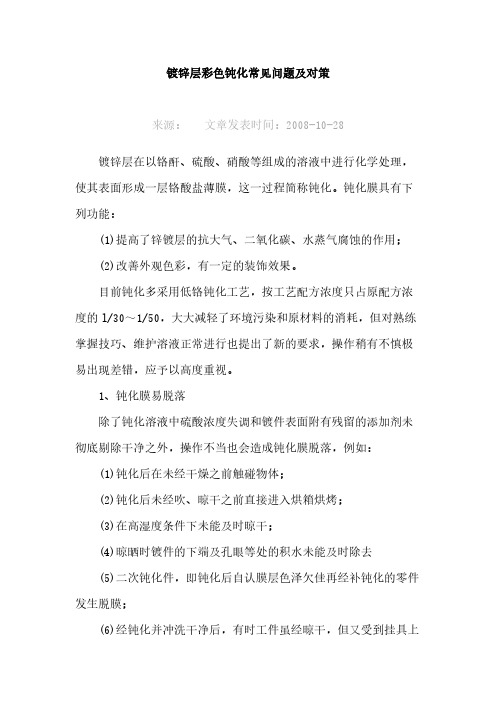
镀锌层彩色钝化常见问题及对策来源:文章发表时间:2008-10-28镀锌层在以铬酐、硫酸、硝酸等组成的溶液中进行化学处理,使其表面形成一层铬酸盐薄膜,这一过程简称钝化。
钝化膜具有下列功能:(1)提高了锌镀层的抗大气、二氧化碳、水蒸气腐蚀的作用;(2)改善外观色彩,有一定的装饰效果。
目前钝化多采用低铬钝化工艺,按工艺配方浓度只占原配方浓度的l/30~1/50,大大减轻了环境污染和原材料的消耗,但对熟练掌握技巧、维护溶液正常进行也提出了新的要求,操作稍有不慎极易出现差错,应予以高度重视。
1、钝化膜易脱落除了钝化溶液中硫酸浓度失调和镀件表面附有残留的添加剂未彻底剔除干净之外,操作不当也会造成钝化膜脱落,例如:(1)钝化后在未经干燥之前触碰物体;(2)钝化后未经吹、晾干之前直接进入烘箱烘烤;(3)在高湿度条件下未能及时晾干;(4)晾晒时镀件的下端及孔眼等处的积水未能及时除去(5)二次钝化件,即钝化后自认膜层色泽欠佳再经补钝化的零件发生脱膜;(6)经钝化并冲洗干净后,有时工件虽经晾干,但又受到挂具上流下的水所润湿而发生部分膜层脱落;(7)钝化溶液温度过高,钝化时间过长而引起的膜层过厚,影响到膜层的结合力。
对于氯化钾光亮镀锌件,若钝化之前未经预处理而脱膜,则必须先经预处理,这是因为氯化钾光亮镀锌件表面附有添加剂,若添加剂未能彻底清洗干净,钝化后必然会引起脱膜,为此,钝化前尚需在沸水中煮3~4min,经冷却后再钝化,这一脱膜问题就能得到解决。
为减少因脱膜而造成返修,在镀件钝化后尚未烘烤之前应做一次检查,当发现有脱膜的应当立即在稀盐酸中退除,用流动水冲洗后重新钝化,这样可以大大简化返修工序。
2、根据钝化溶液温度调节钝化时间溶液温度偏低时成膜速度缓慢,所获的膜层薄,光泽性差,有雾状,需要延长钝化时间,尤其是延长空气中的停留时间才能有所改善,但仍难免“地图”形的花纹出现。
溶液温度偏高时所获钝化膜虽较光亮,色彩自然,但钝化膜结合力差,要防止因钝化时间过长而引起膜层脱落。
电镀锌低铬钝化故障处理

∙电镀行业解析:镀锌低铬钝化故障处理∙前言镀锌低铬钝化从上世纪70年代中期起,由1809/L、40glL高铬二次钝化基础上降到2一59/L低铬钝化新工艺,并且钝化膜的耐蚀性基本上可达到高铬钝化的耐蚀性,初步解决了环境污染问题。
本文将低铬彩钝化和白钝化常见的膜层缺陷、产生原因及处理方法,汇总如下。
1 彩钝化常见故障及处理1.1 膜层不亮、有雾状1.1.1 产生原因(1) 硝酸出光失效;(2) 钝化液中硝酸和铬酸太少;(3) 三价铬和锌离子积累过多,即钝化液已老化;(4) 钝化后清洗水中含有大量氯离子,或使用了曾进行白钝化件的漂洗水槽。
1.1.2 处理方法(1) 更换出光溶液;(2) 添加适量硝酸和铬酸,予以调整;(3) 重新配制钝化液,旧液可用袋装732 阳离子交换树脂浸渍处理,除去溶液中C扩‘和ZnZ干后再用。
平时也最好用此法定期浸渍处理,延长钝化液使用期;(4) 更换清洗水,不能用白钝化件漂洗水槽来清洗彩钝化件。
1.2 膜层不牢、易擦1.2.1 产生原因(1) 钝化液pH值偏低;(2) 钝化操作时间长;(3) 锌镀层表面吸附一层有机物;(4) 钝化件出槽在空气中停留时间长。
1.2.2 处理方法(1) 调整钝化液pH值,一般刚配好的钝化液pH值往往偏低,可加人少量氢氧化钠,使溶液pH值升高至工艺范围的下限,当pH值过高时加硫酸调整;(2) 适当缩短钝化时间,掌握好工件在液下成膜的时间,一般pH值在下限时,操作时间短一些,反之时间长一些,成膜时间随pH值而变,不能固定不变;(3) 可用质量分数为5%的氢氧化钠溶液脱膜,清洗后再进行钝化;(4) 适当缩短钝化件在空气中停留时间。
1.3 彩色浅、烘干后呈黄红色1.3.1 产生原因(1) 钝化液中硫酸含量高;(2) 钝化后在空气中停留时间短。
1.3.2 处理方法(1) 在钝化液中加铬酸和硝酸以平衡浓度;(2) 适当增加钝化件在空气中暴露时间。
1.4 膜层发黑或棕揭色1.4.1 产生原因(1) 镀锌液中金属杂质含量太高;(2) 钝化液中铬酸太少;(3) 硫酸含量过高。
氯化物镀锌常见故障处理
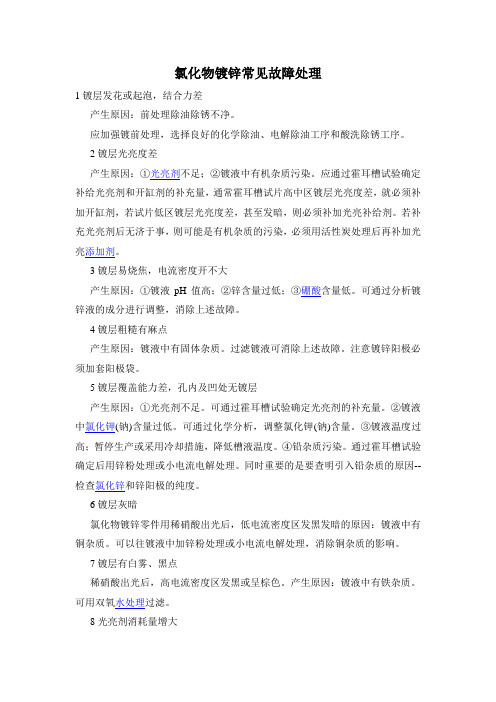
氯化物镀锌常见故障处理1镀层发花或起泡,结合力差产生原因:前处理除油除锈不净。
应加强镀前处理,选择良好的化学除油、电解除油工序和酸洗除锈工序。
2镀层光亮度差产生原因:①光亮剂不足;②镀液中有机杂质污染。
应通过霍耳槽试验确定补给光亮剂和开缸剂的补充量,通常霍耳槽试片高中区镀层光亮度差,就必须补加开缸剂,若试片低区镀层光亮度差,甚至发暗,则必须补加光亮补给剂。
若补充光亮剂后无济于事,则可能是有机杂质的污染,必须用活性炭处理后再补加光亮添加剂。
3镀层易烧焦,电流密度开不大产生原因:①镀液pH值高;②锌含量过低;③硼酸含量低。
可通过分析镀锌液的成分进行调整,消除上述故障。
4镀层粗糙有麻点产生原因:镀液中有固体杂质。
过滤镀液可消除上述故障。
注意镀锌阳极必须加套阳极袋。
5镀层覆盖能力差,孔内及凹处无镀层产生原因:①光亮剂不足。
可通过霍耳槽试验确定光亮剂的补充量。
②镀液中氯化钾(钠)含量过低。
可通过化学分析,调整氯化钾(钠)含量。
③镀液温度过高;暂停生产或采用冷却措施,降低槽液温度。
④铅杂质污染。
通过霍耳槽试验确定后用锌粉处理或小电流电解处理。
同时重要的是要查明引入铅杂质的原因--检查氯化锌和锌阳极的纯度。
6镀层灰暗氯化物镀锌零件用稀硝酸出光后,低电流密度区发黑发暗的原因:镀液中有铜杂质。
可以往镀液中加锌粉处理或小电流电解处理,消除铜杂质的影响。
7镀层有白雾、黑点稀硝酸出光后,高电流密度区发黑或呈棕色。
产生原因:镀液中有铁杂质。
可用双氧水处理过滤。
8光亮剂消耗量增大产生原因:①镀液温度高。
最好采用冷却措施将降低槽液温度或采用间歇生产;②镀液中氯化钾、氯化锌含量过高,使镀液浊点降低,光亮剂析出。
通过分析镀液成分,稀释镀液;③工件除油不净,将大量油污带入镀液中,消耗光亮添加剂中的载体光亮剂。
保证镀锌零件电镀前除油要彻底。
9镀层有条纹产生原因:①光亮剂失调,配槽时添加剂严重不足。
可通过霍耳槽试验,补充添加剂的用量。
镀锌层彩色钝化常见问题及对策

镀锌层彩色钝化常见问题及对策来源:文章发表时间:2008-10-28镀锌层在以铬酐、硫酸、硝酸等组成的溶液中进行化学处理,使其表面形成一层铬酸盐薄膜,这一过程简称钝化。
钝化膜具有下列功能:(1)提高了锌镀层的抗大气、二氧化碳、水蒸气腐蚀的作用;(2)改善外观色彩,有一定的装饰效果。
目前钝化多采用低铬钝化工艺,按工艺配方浓度只占原配方浓度的l/30~1/50,大大减轻了环境污染和原材料的消耗,但对熟练掌握技巧、维护溶液正常进行也提出了新的要求,操作稍有不慎极易出现差错,应予以高度重视。
1、钝化膜易脱落除了钝化溶液中硫酸浓度失调和镀件表面附有残留的添加剂未彻底剔除干净之外,操作不当也会造成钝化膜脱落,例如:(1)钝化后在未经干燥之前触碰物体;(2)钝化后未经吹、晾干之前直接进入烘箱烘烤;(3)在高湿度条件下未能及时晾干;(4)晾晒时镀件的下端及孔眼等处的积水未能及时除去(5)二次钝化件,即钝化后自认膜层色泽欠佳再经补钝化的零件发生脱膜;(6)经钝化并冲洗干净后,有时工件虽经晾干,但又受到挂具上流下的水所润湿而发生部分膜层脱落;(7)钝化溶液温度过高,钝化时间过长而引起的膜层过厚,影响到膜层的结合力。
对于氯化钾光亮镀锌件,若钝化之前未经预处理而脱膜,则必须先经预处理,这是因为氯化钾光亮镀锌件表面附有添加剂,若添加剂未能彻底清洗干净,钝化后必然会引起脱膜,为此,钝化前尚需在沸水中煮3~4min,经冷却后再钝化,这一脱膜问题就能得到解决。
为减少因脱膜而造成返修,在镀件钝化后尚未烘烤之前应做一次检查,当发现有脱膜的应当立即在稀盐酸中退除,用流动水冲洗后重新钝化,这样可以大大简化返修工序。
2、根据钝化溶液温度调节钝化时间溶液温度偏低时成膜速度缓慢,所获的膜层薄,光泽性差,有雾状,需要延长钝化时间,尤其是延长空气中的停留时间才能有所改善,但仍难免“地图”形的花纹出现。
溶液温度偏高时所获钝化膜虽较光亮,色彩自然,但钝化膜结合力差,要防止因钝化时间过长而引起膜层脱落。
镀锌低铬彩色钝化工艺研究

---------------------------------------------------------------范文最新推荐------------------------------------------------------ 镀锌低铬彩色钝化工艺研究摘要:课题阐述了镀锌低铬彩色钝化工艺,高铬钝化对人体和环境的危害严重,本课题寻求在低铬条件下进行镀锌后的钝化,并得到优良性能的钝化膜。
实验采用单因素试验法,改变单一的工艺参数来探求一个最适宜的工艺参数,探讨如何在大量减少铬含量的情况下,通过添加添加剂,改变工艺参数使得到的工艺能满足需求。
实验中得出各工艺参数对实验过程或者实验结果的影响,测定了各个工艺参数的最佳值:铬酐3.5g/L,冰醋酸4mL/L,硝酸4mL/L,硫酸镍1.2g/L,高锰酸钾0.1g/L,锌粉0.8g,pH1.4,固化60℃,钝化液中钝化20s,空气中18s。
所得的工艺适合自动线生产,并且镀液稳定、易于调整、成本低、污染少等优点,并且保证了钝化膜的外观、耐腐蚀性能、结合力等性能达到标准。
关键词:低铬;污染;镀锌层;彩色钝化38731 / 35Study on Low-chrome colorful passivation technology for Galvanized CoatingAbstract: Topics elaborated galvanized low chromium passivation process color, high-chromium passivation for serious harm to humans and the environment, the subject sought under conditions at low chromium passivation of galvanized and get excellent performance of the passive film. Experiments using single factor test, change a single process parameters to explore an optimum process parameters, to explore ways to reduce the chromium content in a large number of cases, by adding additives, changing the process parameters so that the resulting technology to meet the demand. The process parameters obtained in the experiment or the results of the experiment the influence of various process parameters determined optimum values: Chromic anhydride 3.5g/L, acetic acid 4mL/L, nitrate 4mL/L, nickel sulfate 1.2g/L, potassium permanganate 0.1g/L, zinc powder 0.8g, pH1.4, curing 60 ℃, passivation solution passivation 20s, the air 18s. The resulting process is suitable for automatic line production - bath is stable, easy to adjust, low cost, less pollution, etc.,---------------------------------------------------------------范文最新推荐------------------------------------------------------and to ensure that the passive film appearance, corrosion resistance, adhesion strength and other properties up to standard.4.3 钝化膜的制备174.3.1 钝化液的配制174.3.2 钝化膜的制备184.4 工艺流程185实验结果及讨论195.1 钝化液工艺试验结果及各工艺的作用195.1.1 铬酐195.1.2 硝酸193 / 355.1.3 冰醋酸205.1.4 硫酸镍205.1.5 锌粉215.1.6 高锰酸钾215.2 工艺条件及其影响21 5.2.1 pH215.2.2 钝化时间225.2.3 固化温度225.2.4 钝化液温度235.2.5 工件的晃动235.3 实验结果23---------------------------------------------------------------范文最新推荐------------------------------------------------------5.4 钝化时的故障与维护245.4.1 钝化后发现的故障与处理方法245.4.2 镀液的维护256结论267谢词27参考文献28,38731绪论1.1镀锌低铬彩色钝化研究的概况和意义电镀生产中也许除了镀铬外,其他镀种电镀后都需要采取某些处理措施。
氯化钾镀锌典型故障_周长虹 奥邦电镀

些电镀厂的镀液容易产生浮油 ( 漂在液面上的一种 油状有机物 ) 。其产生的原因主要为: ( 1) 前处理除 油不佳, 槽中有大量的有机油脂, 与表面活性剂形成 皂化等 ; ( 2) 镀液中有较多的铁杂质 , 镀液一般很混 浊; ( 3) 氯化钾的质量浓度过高; ( 4) 添加剂配比有 问题 , 添加剂中某类载体过多等 ; ( 5) 镀液的 pH 值 6。 氯化钾镀锌液面浮油的黏度大 , 易黏在槽壁、 挂 具、 滚桶、 阳极及镀件上或沉淀于镀液底部, 难以彻 底清除。氯化钾镀锌液是弱酸性的 , 本身不具有除 油能力。导电盐氯化钾对镀液的浊点有很大影响 , 在高温季节 , 当镀液中有较多铁杂质时, 添加剂的浊 点会大幅下降。随着组合型添加剂中某类载体添加 剂的不断积累, 与电镀液中的悬浮物和镀件中带入 的油污及三价铁离子共同作用 , 形成酸性且黏度大 的油渍, 严重影响镀层质量。 找到液面浮油产生的原因后, 解决起来就比较 容易了。要选择大品牌的氯化钾镀锌添加剂, 保证 前处理后镀件表面无油, 无锈, 无挂灰, 夏天镀液中 氯化钾的质量浓度不应过高 , 控制镀液的 pH 值在 5. 6~ 6. 0, 镀液温度不宜过高 , 对于已产生浮油的镀 液可按大处理方法进行认真处理 , 可除掉已产生的 浮油。
收稿日期: 2010 10 11
3
低铬彩钝较多有机添 加剂。这些有机物由于种种原因会夹杂在镀层中或 吸附在镀层表面。如果添加剂的质量不佳、 添加过 量或镀后清洗不干净 , 都会产生不良后果。 ( 1) 当镀层中夹杂过多的有机物 , 在钝化过程 中因膜首先被溶解, 结果有机物暴露出来 , 夹杂在工 件表面起隔离作用而使膜脱落或褪色。 ( 2) 清洗不彻底, 工件表面吸附的有机物会在 成膜过程中和工件存储过程中把六价铬还原成三价 铬, 过多的三价铬可能会影响彩钝膜的结合力或使 之变浅褪色。 ( 3) 由于钝化前清洗不认真或清洗不够 , 会带 入大量的氯离子 , 虽然少量的氯离子有利于成膜的 进行 , 但过量会使膜过厚而易脱落。 ( 4) 由于镀前处理时没有彻底清除油污及氧化 膜, 造成局部镀层结合力不好 , 导致钝化膜脱落。 ( 5) 镀锌液工艺控制不当, 使镀液不稳定, 局部 导电不良, 造成镀层疏 松、 脆性 大及结合力差等 缺 陷。 ( 6) 钝化剂硫 酸根和氯 离子的质 量浓度过 高 时, 成膜过快过厚, 时间上很难掌握 , 时间短色泽浅 ,
浅谈镀锌层低铬钝化脱膜的原因
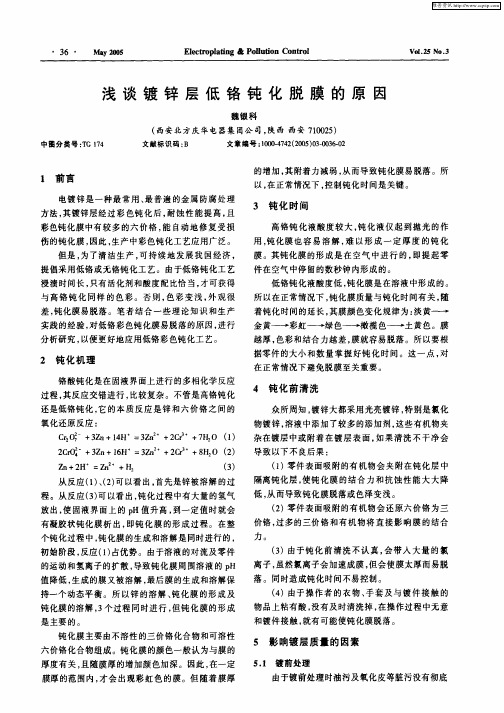
差; 时间稍长 , 膜厚 , 易脱落。所 以在低铬钝化 中, 硫 酸根的影响最严重 。其含量不宜超过 0 . 8 g / L , 在通
7 钝化后 处理
7 . 1 清 洗
常情况下, 活化剂与铬酸酐比值大致为 s O j 一 / C r O 3 =
1 . 0—4 . 0 , C 1 一 / C r O 1 . 5 ~1 . 0 , 活化 剂不 足 , 成 膜 速
6 钝 化工艺 的控制
6 . 1 活化 剂 与铬 酸 酐 比值 的控 制 钝 化液老化或组成不 当, 即硫 酸 根 或 氯 离 子 过 多, 成 膜 过快 , 膜厚 , 时间 上很 难 控 制 。时 间短 , 色 彩
用。因此 , 钝化前一定要进行抛光 , 既可避免钝化液 p H值升 高 , 更 主要 的是对 镀锌层 起 到化学 抛光 作 用, 获得光泽均一 的镀层 , 保证 了钝化膜 的结合力和
分析 研究 , 以便更 好地应 用低铬 彩 色钝 化工 艺 。
3 钝 化 时 间
高铬钝化液酸度较大, 钝化液仅起到抛光 的作
用, 钝 化膜 也 容 易 溶 解 , 难 以形 成 一 定 厚 度 的钝 化
膜。其钝化膜的形成是在空气 中进行 的, 即提起零 件在空气中停留的数秒钟内形成的。
钝 化膜 的溶解 , 3 个 过程 同时 进行 , 但 钝 化 膜 的形 成
是 主要 的 。
( 3 )由于钝化前清洗不认 真, 会带人大量的氯 离子 , 虽然氯离子会加速成膜 , 但会使膜太厚而易脱 落。同时造成钝化时间不易控制。 ( 4 )由于操作者的衣物、 手套及与镀件接触的 物品上粘有酸 , 没有及时清洗掉, 在操作过程中无意 和镀件接触 , 就有可能使钝化膜脱落。
镀锌层彩色钝化常见问题及对策-10页word资料

镀锌层彩色钝化常见问题及对策来源:文章发表时间:2008-10-28镀锌层在以铬酐、硫酸、硝酸等组成的溶液中进行化学处理,使其表面形成一层铬酸盐薄膜,这一过程简称钝化。
钝化膜具有下列功能:(1)提高了锌镀层的抗大气、二氧化碳、水蒸气腐蚀的作用;(2)改善外观色彩,有一定的装饰效果。
目前钝化多采用低铬钝化工艺,按工艺配方浓度只占原配方浓度的l/30~1/50,大大减轻了环境污染和原材料的消耗,但对熟练掌握技巧、维护溶液正常进行也提出了新的要求,操作稍有不慎极易出现差错,应予以高度重视。
1、钝化膜易脱落除了钝化溶液中硫酸浓度失调和镀件表面附有残留的添加剂未彻底剔除干净之外,操作不当也会造成钝化膜脱落,例如:(1)钝化后在未经干燥之前触碰物体;(2)钝化后未经吹、晾干之前直接进入烘箱烘烤;(3)在高湿度条件下未能及时晾干;(4)晾晒时镀件的下端及孔眼等处的积水未能及时除去(5)二次钝化件,即钝化后自认膜层色泽欠佳再经补钝化的零件发生脱膜;(6)经钝化并冲洗干净后,有时工件虽经晾干,但又受到挂具上流下的水所润湿而发生部分膜层脱落;(7)钝化溶液温度过高,钝化时间过长而引起的膜层过厚,影响到膜层的结合力。
对于氯化钾光亮镀锌件,若钝化之前未经预处理而脱膜,则必须先经预处理,这是因为氯化钾光亮镀锌件表面附有添加剂,若添加剂未能彻底清洗干净,钝化后必然会引起脱膜,为此,钝化前尚需在沸水中煮3~4min,经冷却后再钝化,这一脱膜问题就能得到解决。
为减少因脱膜而造成返修,在镀件钝化后尚未烘烤之前应做一次检查,当发现有脱膜的应当立即在稀盐酸中退除,用流动水冲洗后重新钝化,这样可以大大简化返修工序。
2、根据钝化溶液温度调节钝化时间溶液温度偏低时成膜速度缓慢,所获的膜层薄,光泽性差,有雾状,需要延长钝化时间,尤其是延长空气中的停留时间才能有所改善,但仍难免“地图”形的花纹出现。
溶液温度偏高时所获钝化膜虽较光亮,色彩自然,但钝化膜结合力差,要防止因钝化时间过长而引起膜层脱落。
浅谈氯化锌的返点及变色

浅谈氯化物镀锌层返点及变色一、前言由于我国改革开放日益深入,各行各业蓬勃发展,同时带来了环境问题的严重挑战,尤其我们电镀行业更加面临着生产工艺日益月新的改革,才能紧跟时代发展的步伐,以前我们的工艺落后,污染严重,比如我们以前使用的氰化物镀锌,由高氰镀锌发展到中氰镀锌,后来由于光亮剂的研发成功的改进为低氰,微氰镀锌,对环境保护起到积极作用,但还不能满足当前适应我们环境保护的要求,但是我们的工艺中还存在着含氰物质,所以氯化物镀锌工艺越来越受到广大电镀界,环保界人士所重视,我国从70年代初发展到至今的氯化物镀锌已得到长足的发展,说明该工艺确有其优点,氯化物镀锌的电流效率高达(95%以上),槽压低,所以比氰化镀锌节约50%以上的电,同时适用各种高碳黑色金属基体的表面镀锌层。
生产效益也比氰化物镀锌高出30%-50%左右,但是由于氯化物镀锌的光亮剂的主要成分是载体表面活性剂去乳化光亮剂醛类,因表面活性剂对镀件有一定的附着力,水洗效果不十分好,同时氯化物镀锌对铁,铜,铅等杂质很敏感,所以镀锌件返点变色,也不足为奇了,那么我们怎样才能改变这个缺点呢?靠我们去改变操作工艺或使用原料上去想办法。
二、镀锌层返点变色产生的原因1.镀前处理不良,工件表面的油污清洗不干净,经酸洗后,水洗的难度加大基体表面形成花斑或条纹状,该表面镀层难以沉积或沉积镀层很薄,若工件表面的铁锈处理不完全,镀层只能在锈迹周围沉积,出现黑色斑点,或者如滚镀经过物理作用锈迹渐渐被摩擦被溶解,后期方有镀层沉积,该部位镀层沉积时间短,镀层很薄,光亮度差而出现白色斑点2.阴极电流密度大,阴极区PH值升高过快,镀层中有金属氢氧化物或碱式盐类附于镀层中,而出现斑点。
3.镀液中有机杂质的来源主要是添加剂分解产物和未清洗干净的油污长时间在镀液中积累会使镀层发雾。
4.光亮剂添加太多,会造成阴极无法消耗,形成光亮剂过剩夹入镀锌层,或附着在工件表面,清洗不干净,经钝化后产生酸性胶体状的表面活性剂。
氯化物镀锌故障分析与处理措施及工序控制

氯化物镀锌故障分析与处理措施及工序控制氯化物镀锌中由于镀液成分维护不当,可能会导致镀锌层质量的下降。
因此,要做到以下几点:1.把好电镀原料关要得到厚度均匀、结晶细致的氯化物镀锌层,选用具有良好分散能力和深镀能力的镀锌工艺配方是重要的,但选择质量优良的原材料和添加剂更重要。
若使用的氯化钾、氯化锌、硼酸、添加剂等成分的质量不能得到保证,也同样无法获得高质量的镀锌层。
对于有些原料必须进行双氧水一活性炭处理。
如对氯化钾可用80℃以上的热水搅拌溶解,加30%H2O2lmL/L,搅拌lOmin左右,静置2h;再用5%NaOH溶液调pH值到7.0~7.5;然后,加活性炭2g/L并加温到70℃,搅拌lh,静置沉淀2h,过滤即可。
2.氯化物镀锌液主盐含量的控制氯化锌是镀液的主盐。
一般随氯化锌含量的增加,允许电流密度上限提高,可以提高沉积速度和生产效率,还可减少金属杂质的影响,但分散能力和覆盖能力会随氯化锌含量增大而降低。
氯化锌含量低,有利于提高镀液的分散能力和覆盖能力,所以滚镀锌或形状较为复杂的零件挂镀锌宜采用锌浓度稍低的镀液。
在氯化物电镀生产过程中,镀液中锌离子浓度呈上升趋势,这与镀槽中锌阳极板的多少以及镀液的pH值有关。
3.镀液中氯化钾(钠)含量的控制氯化钾、氯化钠既是导电盐又是镀液的络合剂。
在含大量氯化钾或氯化钠的镀溶液中,锌离子不是以简单阳离子形式存在,而是以各种络合阴离子形式如[ZnCh(H20)2]2一存在。
严格讲,氯化钾(钠)镀锌液是络合物镀液,但由于络合离子在阴极过程中起电子桥作用,催化了电极过程,因而无显著的极化作用。
氯化钾(钠)含量的增加可提高镀液的导电性和分散能力。
氯化钾含量高,镀液分散能力好,光亮电流密度范围宽,同时镀层光亮度提高。
氯化钾含量从210~240g/L无明显影响,若低于180g/L,上述性能下降。
但含量过高将明显降低镀液的浊点,配槽时溶解也困难。
因此氯化钾的含量宜取180~230g/L,配槽时最好采用上限含量。
镀锌层彩色钝化常见问题及对策

镀锌层彩色钝化常见问题及对策来源:文章发表时间:2008-10-28镀锌层在以铬酐、硫酸、硝酸等组成的溶液中进行化学处理,使其表面形成一层铬酸盐薄膜,这一过程简称钝化。
钝化膜具有下列功能:(1)提高了锌镀层的抗大气、二氧化碳、水蒸气腐蚀的作用;(2)改善外观色彩,有一定的装饰效果。
目前钝化多采用低铬钝化工艺,按工艺配方浓度只占原配方浓度的l/30~1/50,大大减轻了环境污染和原材料的消耗,但对熟练掌握技巧、维护溶液正常进行也提出了新的要求,操作稍有不慎极易出现差错,应予以高度重视。
1、钝化膜易脱落除了钝化溶液中硫酸浓度失调和镀件表面附有残留的添加剂未彻底剔除干净之外,操作不当也会造成钝化膜脱落,例如:(1)钝化后在未经干燥之前触碰物体;(2)钝化后未经吹、晾干之前直接进入烘箱烘烤;(3)在高湿度条件下未能及时晾干;(4)晾晒时镀件的下端及孔眼等处的积水未能及时除去(5)二次钝化件,即钝化后自认膜层色泽欠佳再经补钝化的零件发生脱膜;(6)经钝化并冲洗干净后,有时工件虽经晾干,但又受到挂具上流下的水所润湿而发生部分膜层脱落;(7)钝化溶液温度过高,钝化时间过长而引起的膜层过厚,影响到膜层的结合力。
对于氯化钾光亮镀锌件,若钝化之前未经预处理而脱膜,则必须先经预处理,这是因为氯化钾光亮镀锌件表面附有添加剂,若添加剂未能彻底清洗干净,钝化后必然会引起脱膜,为此,钝化前尚需在沸水中煮3~4min,经冷却后再钝化,这一脱膜问题就能得到解决。
为减少因脱膜而造成返修,在镀件钝化后尚未烘烤之前应做一次检查,当发现有脱膜的应当立即在稀盐酸中退除,用流动水冲洗后重新钝化,这样可以大大简化返修工序。
2、根据钝化溶液温度调节钝化时间溶液温度偏低时成膜速度缓慢,所获的膜层薄,光泽性差,有雾状,需要延长钝化时间,尤其是延长空气中的停留时间才能有所改善,但仍难免“地图”形的花纹出现。
溶液温度偏高时所获钝化膜虽较光亮,色彩自然,但钝化膜结合力差,要防止因钝化时间过长而引起膜层脱落。
氯化钾镀锌钝化膜变色原因探讨及控制措施
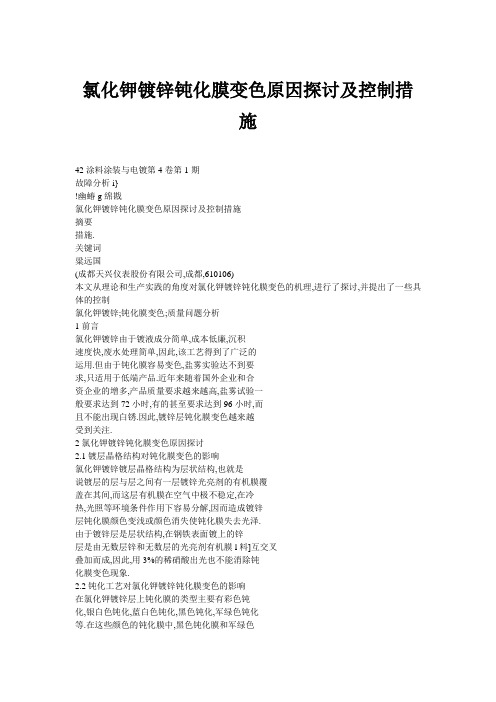
3氯化钾镀锌钝化膜变色的控制措施
笔者经过多年的研究和实践,认为以下一些方
法和措施,对降低氯化钾镀锌钝化膜变色,提高氯化
钾镀锌钝化膜耐腐蚀性能有帮助.
3.1用碱性溶液去除零件表面的光亮剂薄膜
零件从氯化钾镀锌槽中取出后,先经过一道水
洗后浸入碱性溶液中去除表面多余的光亮剂薄膜,
然后再进行其它工序.其工艺流程为:
锌溶液
从氯化钾镀锌溶液的性质和镀层结构分析可
知:要完全去除镀锌层中夹杂的光亮剂薄膜几乎是
不可能的,但是将镀层中的有机物控制在有限的范
围内是完全能够办到的.我们可以通过以下一些措
施来解决问题:
(1)添加剂应采用”少加勤加”的办法.同时,避
免在镀槽工作期间加入.加光亮剂最好是在每班下
班后添加.添加时,应将光亮剂用镀液稀释后加入,
氯化钾镀锌钝化膜变色原因探讨及控制措施
42涂料涂装与电镀第4卷第1期
故障分析i}
!幽蝽g绵戡
氯化钾镀锌钝化膜变色原因成都天兴仪表股份有限公司,成都,610106)
本文从理论和生产实践的角度对氯化钾镀锌钝化膜变色的机理,进行了探讨,并提出了一些具体的控制
氯化钾镀锌;钝化膜变色;质量问题分析
理技术工作,发表论文十余篇.
3
温
53c:;室
2OO6年2月粱远国:氯化钾镀锌钝化膜变色原因探讨及控制措施43
温度室温
时间,S10—20s
先在低铬彩色钝化液中钝化,不经过老化处理,
直接浸入碳酸钡漂白溶液中除去彩色膜,从而可以
形成银白色钝化膜,然后在含O.3%铬酐的热水
(80Y:一9oc【=)中封闭处理.最后放入温度为6oc【=一
氯化钾镀锌一水洗一碱性溶液除膜一水洗—钝
氯化物镀锌工艺的控制与常见问题的分析包含哈氏片
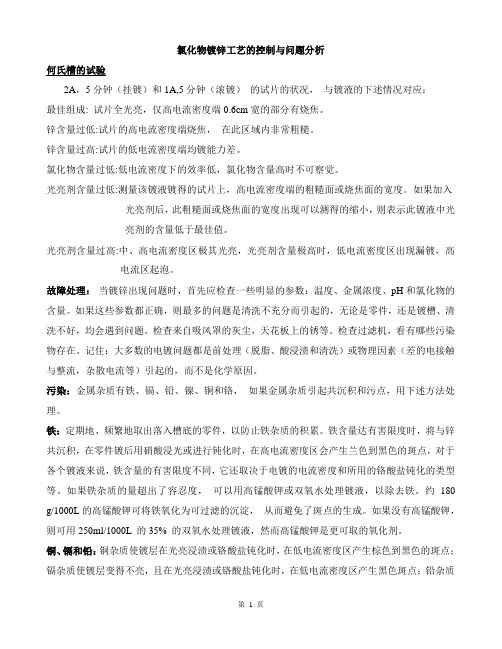
氯化物镀锌工艺的控制与问题分析何氏槽的试验2A,5分钟(挂镀)和1A,5分钟(滚镀)的试片的状况,与镀液的下述情况对应:最佳组成: 试片全光亮,仅高电流密度端0.6cm宽的部分有烧焦。
锌含量过低:试片的高电流密度端烧焦,在此区域内非常粗糙。
锌含量过高:试片的低电流密度端均镀能力差。
氯化物含量过低:低电流密度下的效率低,氯化物含量高时不可察觉。
光亮剂含量过低:测量该镀液镀得的试片上,高电流密度端的粗糙面或烧焦面的宽度。
如果加入光亮剂后,此粗糙面或烧焦面的宽度出现可以测得的缩小,则表示此镀液中光亮剂的含量低于最佳值。
光亮剂含量过高:中、高电流密度区极其光亮,光亮剂含量极高时,低电流密度区出现漏镀,高电流区起泡。
故障处理:当镀锌出现问题时,首先应检查一些明显的参数:温度、金属浓度、pH和氯化物的含量。
如果这些参数都正确,则最多的问题是清洗不充分而引起的,无论是零件,还是镀槽、清洗不好,均会遇到问题。
检查来自吸风罩的灰尘,天花板上的锈等。
检查过滤机,看有哪些污染物存在。
记住:大多数的电镀问题都是前处理(脱脂、酸浸渍和清洗)或物理因素(差的电接触与整流,杂散电流等)引起的,而不是化学原因。
污染:金属杂质有铁、镉、铅、镍、铜和铬,如果金属杂质引起共沉积和污点,用下述方法处理。
铁:定期地、频繁地取出落入槽底的零件,以防止铁杂质的积累。
铁含量达有害限度时,将与锌共沉积,在零件镀后用硝酸浸光或进行钝化时,在高电流密度区会产生兰色到黑色的斑点,对于各个镀液来说,铁含量的有害限度不同,它还取决于电镀的电流密度和所用的铬酸盐钝化的类型等。
如果铁杂质的量超出了容忍度,可以用高锰酸钾或双氧水处理镀液,以除去铁。
约180 g/1000L的高锰酸钾可将铁氧化为可过滤的沉淀,从而避免了斑点的生成。
如果没有高锰酸钾,则可用250ml/1000L 的35% 的双氧水处理镀液,然而高锰酸钾是更可取的氧化剂。
铜、镉和铅:铜杂质使镀层在光亮浸渍或铬酸盐钝化时,在低电流密度区产生棕色到黑色的斑点;镉杂质使镀层变得不亮,且在光亮浸渍或铬酸盐钝化时,在低电流密度区产生黑色斑点;铅杂质引起低电流密度区漏镀。
氯化钾镀锌故障 奥邦电镀

氯化钾镀锌典型故障奥邦公司周长虹1.1 氯化钾镀锌液面浮油在采用氯化钾镀锌工艺进行生产过程中,有一些电镀厂的电镀液容易产生浮油,即漂在液面以上的一种油状有机物,其产生的原因主要为:①前处理除油不够,槽中有大量的有机油脂,与表面活性剂形成皂化等;②镀液中有较多的铁杂质,镀液一般很混浊;③氯化钾含量过高;④添加剂配比有问题,添加剂中某类载体过多等;⑤镀液的PH≥6后更易出现。
氯化钾镀锌液面的浮油粘度大,易粘在槽壁、挂具、滚桶、阳极及镀件上或沉淀于镀液底部,难以彻底清除,氯化钾镀锌液是弱酸性的,本身不具有除油能力,导电盐氯化钾对镀液的浊点有很大影响,在夏天的高温季节,当镀液中有较多铁杂质时,添加剂的浊点会大幅下降,组合型添加剂中某类载体添加剂含量的不断积累,与电镀液中的悬浮物和镀件中带入的油污及三价铁离子的共同作用下,形成酸性且粘度大的油渍,严重影响镀层质量。
LAN-930、LAN-918氯化钾镀锌工艺,具有良好的耐温性、耐铁性。
找到镀槽浮油产生的原因后,解决起来就比较容易了,首先要选择大品牌的氯化钾添加剂,保证前处理后镀件“四无”,即无油、无锈、无挂灰、无吸附;夏天镀液中氯化钾含量不应过高,控制镀液的PH值在5.6-6之间为好,控制镀液温度不要过高,对于已产生浮油的镀液可按大处理方法进行认真处理,可除掉已产生的浮油。
1.2 氯化钾镀锌的白钝易泛彩泛黄氯化钾镀锌蓝白钝化的色调,比无氰碱性镀锌的色调更艳丽受到人们广泛欢迎,无论是六价铬蓝白钝还是三价铬蓝白钝,氯化钾镀锌的蓝白钝化比无氰碱性镀锌更易控制(无氰碱性镀锌更易泛黄泛彩),但仍是常见故障之一。
1.2.1 镀锌层的问题首先与镀层的厚度有关系,一般要求镀层厚度≥4微米,特别是三价铬蓝白钝化而言,蓝白钝化时镀层过薄会出现以下问题:一是蓝白的色调不佳,易泛彩泛黄;二是钝化膜放置后易发白(黑)点(当钝化后清洗不良及烘干不彻底时更易出现)。
其次是镀层的纯度,镀液中的重金属杂质如铜、铅等较多时,低电流密度区的镀层钝化色泽不良,整体易泛彩泛黄;特别铁杂质过量时,大面积易泛彩泛黄;镀液中的有机杂质是造成蓝白钝化时泛彩泛黄的主要原因之一,它一般有如下规律:①镀液越老化(有机和重金属杂质多),越易出现;②镀层越光亮越易出现;③生产电流密度≥1.5A/dm2更易出现,电流密度越大的部位,越易出现;④当镀液中残留有微量氧化物时,易出现。
镀锌钝化工艺

镀锌层白色钝化和蓝白色钝化白色钝化膜可用彩虹色钝化膜经“漂白”取得,也可直接获得。
白色钝化膜的色泽可分为银白色和蓝白色两种,可根据产品要;求选用。
通称为“白钝化”和“蓝钝化”,区别在于自钝化为无色透明,膜中几乎不含铬,耐蚀性很差,后者含有少量三价铬,耐蚀性比“白钝化”稍好些。
这两种钝化膜一般都用在低档产品的防护一装饰。
直接低铬白色钝化易出现彩色的原因低铬白色钝化易出现彩色的原因较多,常见的与操作工艺中四个方面的因素有关。
(1)与钝化溶液中工艺配方比例失调有关。
白色钝化溶液的配方浓度较低,当其中某一项组分消耗稍快时,各组分之间的比例将会失调,此时即会影响到膜层质量。
(2)与镀层本身的结晶及基材质量有关。
镀层本身结晶粗糙、基,材表面光洁度差的与镀层结晶细微,基材表面光洁度较好的工件所获}的钝化膜的质量大不一样,实践经验告诉我们,镀层结晶致密,基材表面光洁度较好的工件,钝化后一般都较好,不易出现明显的色彩,而结晶较粗糙且基材表面的光洁度又较差的钝化膜层易出现彩虹色,《且镀层结晶越粗糙,基材表面光洁度越差的镀层彩虹色越严重(相对阻较)。
(3)与钝化后空气中停留时间有关。
钝化后在清洗之前的空气嘲停留时间越长越容易出现彩色膜。
(4)与清洗不彻底有关。
工件表面残留钝化溶液会继续与锌层起I化学反应,这时所获的钝化膜通常较易带色彩。
为获得质量优异的纯白色钝化膜层,除操作中需要注意上述几酒方面因素之外,镀锌工艺中尽可能选用镀层结晶致密的工艺配方锺制作工件的材料也尽可能选用表面光洁度较好、无锈蚀斑点的材料。
镀锌层白钝化出现“白霜”的原因镀锌白色或蓝白色钝化后出现白霜的原因主要与以下几种因素有关:(1)基材材质太差,严重锈蚀过;(2)工件酸洗时造成过腐蚀;(3)工件的除油、除锈工艺不到位;(4)酸洗后工件表面遗留的腐蚀产物、炭灰未曾洗刷干净;(5)钝化前、后清洗不彻底;(6)镀层过薄;(7)钝化后没有充分干燥处理。
因为提出咨询的这家电镀厂地处远郊,笔者就将上述可能引起白霜的原因函告该厂。
氯化物镀锌液中的金属杂质及其处理

氯化物镀锌液中的金属杂质及其处理袁诗璞【摘要】介绍了氯化物镀锌液中铁、铜、铅等金属杂质的产生原因以及对镀层的影响.其去除方法是:先以工业级高锰酸钾氧化,然后加入高纯细锌粉还原,最后沉淀过滤.处理后应采用双氧水将过量的高锰酸钾去除,调整pH,以及补加光亮剂.【期刊名称】《电镀与涂饰》【年(卷),期】2010(029)007【总页数】4页(P16-19)【关键词】氯化物镀锌;金属杂质;去除【作者】袁诗璞【作者单位】成都市机投镇会所花园A3-02-202,四川,成都,610045【正文语种】中文【中图分类】TQ153.15钢铁件上的锌镀层作为牺牲性阳极保护镀层,应用面极广,其加工量达电镀总量约60%以上。
尽管我国在氯化物与锌酸盐镀锌的无氰镀锌上已基本取代了剧毒氰化镀锌(一些军工产品及个别用户还在采用),且已应用多年,在生产实践中,仍不断反映出一些问题。
笔者接到过不少同行的咨询电话,除添加剂问题外,杂质问题居第二位。
添加剂受售品单位利益问题,不好公开多讲,但认真讨论一下杂质问题,对用户与助剂供应商都有益。
氯化物镀锌尽管防蚀力不高,但相对于锌酸盐镀锌,阴极电流效率高(对铸件等氢超电势低的基体易于施镀)、镀层光亮性好、对杂质敏感性较低。
由于汽摩、电器零件等现多要求采用锌酸盐镀锌,且出口件要求采用三价铬钝化,因此锌酸盐镀锌复苏很快。
但该工艺对杂质异常敏感,更有必要认真讨论杂质问题。
杂质问题涉及许多理论与实践问题,报道比较分散,且有的报道并不合实际。
笔者拟撰文分别对上述两种镀锌工艺的杂质问题进行讨论,以供参考。
本文先讨论氯化物镀锌液中的金属杂质问题。
氯化物镀锌液中最易引入的是铁杂质,其去除方法颇有考究,是重点讨论对象。
2. 1 引入途径及工艺条件的影响一是镀前酸洗后未作认真的清洗,造成大量引入(尤其是滚镀)。
沈品华[1]曾报道过一例类似的故障处理实例,寻找原因及解决办法都颇费周折。
二是钢铁件在弱酸性镀液中的化学浸蚀。
- 1、下载文档前请自行甄别文档内容的完整性,平台不提供额外的编辑、内容补充、找答案等附加服务。
- 2、"仅部分预览"的文档,不可在线预览部分如存在完整性等问题,可反馈申请退款(可完整预览的文档不适用该条件!)。
- 3、如文档侵犯您的权益,请联系客服反馈,我们会尽快为您处理(人工客服工作时间:9:00-18:30)。
氯化物镀锌低铬彩钝变色与脱膜原因浅析(时间:2004-4-29 17:46:00 共有386人次浏览)4.5.1 引言笔者在国内是较早接触氯化物镀锌工艺的人员之一。
国内最早推出的氯化物镀锌添加剂为四川拖拉机厂的CT-1。
研制时的生产性试验即在笔者当时所在的国营南光机器厂进行。
由当时机械工业部组织的鉴定会上,笔者为资料审查组组长并负责起草了鉴定意见书。
一般认为其优点为阴极电流效率高(适于铸件电镀)、镀层光亮因而能直接进行低铬钝化、无强络合剂及铵,因而废水处理简单、镀液成分不复杂,易于控制及过滤。
其不足之处为镀液分散能力与深镀能力较差、镀层纯度不够,因而抗蚀力不理想。
由于其利多,因而在国内作为无氰镀锌工艺得到了大面积应用。
多年来的生产实践,感到该工艺的一些缺点已成为不可忽视的重要问题。
其中,低铬彩钝膜的结合力差及钝化膜色泽在存放及使用期间易变淡(包括蓝白钝化层易泛彩),为许多人所头痛。
有的地方环保部门已对废水中的阴离子表面活性剂(ALS)进行监测。
若严格控制表面活性剂排放指标,则对氯化物镀锌将是致命打击。
本文拟就该工艺低铬彩钝脱膜及变色原因作一浅析,并提出一些个人建议。
4.5.2 电镀工艺的问题氯化物镀锌液中无强络合剂,主要靠有机添加剂在阴极界面的吸附来产生阴极极化,从而获得细致光亮的镀层。
添加剂中的表面活性剂含量非常高,这就为彩钝膜易产生色变淡及附着力不良,埋下了祸根。
4.5.2.1 工艺的先天不足众所周知,氯化物镀锌添加剂由主光亮剂、载体光亮剂、辅助光亮剂三大部分组成。
广泛采用的主光亮剂为苄叉丙酮,后来部分采用邻氯苯甲醛。
主光亮剂为阴极消耗型,它们会在阴极还原消耗掉,也有部分直接夹附在镀锌层中。
由于苄叉丙酮不溶于水,必须靠载体光亮剂的增溶作用即表面活性剂生成胶团或胶束,其细微颗粒分散藏隐其中而间接溶于镀液。
早期的载体光亮剂直接采用OP乳化剂、平平加之类的非离子表面活性剂,后来为了提高浊点,专门对HLB 值合适的非离子表面活性剂进行磺化,制成了多种载体光亮剂。
实际使用时还要另加上述非离子表面活性剂,否则镀层易拉丝及产生气流条痕。
在开缸剂(A剂)中表面活性剂含量相对比补给剂(B剂)为高。
在平时补加B剂时,还配合加入一定量的A剂。
这一组成体系注定了:(1)氯化物镀锌层纯度很差,远不及氰化镀锌层,也不及锌酸盐镀锌层。
在镀层中夹附有大量吸附后难以脱附的表面活性剂与主光亮剂,辅助光亮剂及其分散产物。
即使新配镀液镀出的工件,在用盐酸返修工件,退除镀层时,也有不少泡沫产生。
(2) 镀液老化较快。
由于主光亮剂属还原消耗型而载体及OP等几乎不参与电极反应,仅为带出损耗及镀层夹附损耗,而在生产中又不断加入光亮剂以维持镀层光亮性及光亮范围,这就必然造成恶性循环:镀液中的表面活性剂含量越来越高,相应镀层中的夹附量也越来越大。
一个最直接的证据是:从老化镀液中镀取的锌层,用盐酸退除时,其产生的泡沫比新配镀液的多许多倍。
这尚且是正常控制下的必然结果。
对于工艺维护差的电镀厂点,镀层亮度或深镀能力差时,不调整硼酸与氯化钾的含量,只靠加以为是万能的光亮剂过日子,或者不能坚持勤加少加光亮剂而“暴饮暴食”则其情况更糟糕。
镀层纯度差是其抗蚀力较差的主要原因:在产生电化学腐蚀时,锌作为原电池的阳极,有机杂质作为阴极而加速了对锌层的微电池腐蚀。
镀液及镀层中大量的有机物也是造成镀层钝化性能差的根本原因。
4.5.2.2 添加剂的问题如上所述,主光亮剂苄叉丙酮不溶于水是先天致命弱点。
要根本解决问题,还得重新寻找易溶于水的主光亮剂来替代苄叉丙酮,但这非一朝一夕之事。
邻氯苯甲醛相对易溶于水,且用量少,起光速度快,但镀层脆性更大,在镀液中的稳定性也差。
笔者近来在生产中发现一件憾事:含邻氯苯甲醛的镀液镀出的锌层,钝化膜结合力特别差。
一用户用进口弹簧钢丝成型的非螺旋型小弹簧,相互要交缠在一起,无法滚镀,用普通方法也无法挂镀。
找了许多本地的军工及民营电镀厂均无法镀,少量地用挂篮能镀上锌,因表面异常光洁,彩钝后均很易脱膜。
据用户讲,勉强发往重庆去的产品,对方不收货,在重庆就地找电镀厂返工,也无成功者。
后经人介绍找到笔者所在的电镀厂求助。
通过采用特殊方法顺利进行挂镀,但用原生产正常、不易脱膜的钝化液进行钝化,烘干后用力擦,仍脱膜。
为此,笔者花两天时间专门又研制了一个结合力特别好的钝化液进行钝化,并在钝化前增加一道出光工序(以清洁工件表面),最终达到了要求。
其间发现:用不含邻氯苯甲醛的镀液镀该产品,尽管镀层也很亮,钝化膜结合力也很可靠;而用含邻氯苯甲醛的镀液镀该产品,用同样的钝化工艺,膜的结合力就不可靠。
新配一小槽专门镀该产品,但配制时工人不慎加入了部分含邻氯苯甲醛的老镀液,膜的结合力也不可靠。
这一事实说明,镀液中含有邻氯苯甲醛时,会降低彩钝膜的结合力,即主光亮剂的类型对钝化膜的附着力有明显影响。
近年来不少人立足于对载体和表面活性剂的浊点的提高,以适应无冷冻条件厂家在夏天挂镀,特别是滚镀温升快的现状,遗憾的是其它方面的改进并不大。
笔者认为,对于氯化物镀锌添加剂需要解决的根本问题是如何将镀层中有机杂质的夹附量减少(至少应达到锌酸盐镀锌的水平),主要应当从两方面下功夫:(1)提高载体光亮剂对苄叉丙酮的增溶性能,以期用最少的载体能增溶足够量的主光亮剂,减少载体在镀液中的积累;(2)选择表面润湿性能更好、在镀液中不易夹附的表面活性剂,以期用最小的量来消除气流条痕及拉丝现象,并提高镀件镀后的易清洗性能。
笔者作过些简单试验,发现用质量良好的十二烷基硫酸钠(K12)也能对苄叉丙酮起到增溶作用,且对镀液有较好的润湿作用。
但K12的溶解度较小,只能作稀溶液使用,其本身产生的阴极极化作用较弱,能否实用,有待进一步研究。
4.5.3 钝化层中的有机杂质与变色4.5.3.1 彩钝层变色的根本原因即使非常认真地操作,钝化前能作仔细清洗,设想钝化前工件表面已无残留有机杂质,但经钝化后,钝化层中也必然夹杂不少有机添加剂及其分解产物,因为从钝化机理讲,首先必须有锌的溶解,才伴随有界面液层pH值的上升和六价铬的还原,最终形成铬酸盐转化膜。
在锌溶解时,必然将夹杂在镀锌层中的有机物暴露出来,其一部分进入钝化液,另一部分则夹杂在钝化层中。
若钝化前清洗不良,工件表面仍残留有不少有机物,则钝化层中的夹杂量必然更大。
钝化后清洗不良时,钝化液中溶入或带入的有机物,在钝化层干燥的过程中也会再夹杂在钝化层中。
钝化层中夹杂的有机物是氯化物镀锌彩钝后色泽易变淡的根源所在:在存放或使用期间,钝化层中发生氧化还原反应,有机杂质将六价铬还原为蓝色三价铬盐,六价铬含量不断下降,钝化膜色泽即不断变淡,最后彩锌不象彩锌,白锌不象白锌,十分难看,相应钝化膜抗蚀力下降很多。
与铵盐镀锌不同,过去硫脲和聚乙二醇作添加剂的工艺,钝化层中却因夹杂这类添加剂及其还原为紫色三价铬,钝化层色泽变暗、发乌,而成为当年头痛的“钝化膜变色问题”。
因此,在克服或减轻彩钝层色泽变淡,根本办法是减少钝化层中的有机物夹杂量,其次是提高钝化层中的六价铬含量,或在钝化层中引入对六价铬还原有阻化作用的物质,即应从钝化工艺上加以改进。
4.5.3.2 减少钝化层中有机杂质的措施4.5.3.2.1 改进电镀工艺目前氯化物镀锌添加剂供应商难以计数,其产品品质相差很大,一定要认真通过试验选择用量少、性能好的品种。
若只图价格便宜,有时会得不偿失。
在市场经济条件下,“质优价廉”似乎是不合情理的。
优质产品必然用料精良、作工精细,相应成本也高些,因此优质必然优价(但优价不一定优质)。
笔者亲历过这样一件事:某个无过硬技术人员而要新上氯化物镀锌的小厂,配制一万余升镀液,因亲信朋友的可以欠货款的低价添加剂,镀出的产品一塌糊涂,找笔者协助解决,也无能为力。
后又找人,调过来调过去,都无法除去其不良效果,最终只好废弃镀液,另选优质添加剂重新配液。
不但污染环境,造成的经济损失也是惨重的。
认真对镀液进行调控,保证氯化钾、硼酸、氯化锌等在工艺范围内用pH值是合适的,是首要之事。
在此基础上再勤加少加添加剂。
对最易引入的铁杂质应勤处理,保持镀液清洁,否则毛病也多。
必须根本上克服那种“其它都不管只加光亮剂”的不入门落后的管理方式。
最简捷的办法还是勤做、做好霍尔槽试验,尽量减少镀液中有机物的积累,以延缓其老化时间。
对于因积累大量表面活性剂及添加剂分解产物老化了的镀液,笔者作过许多试验,尚未找到简单有效办法进行再生(活性炭处理的效果微乎其微)。
正如硫酸盐光亮酸性镀锡液因四价锡等杂质积累使镀层焊接性能下降,也难以根本克服一样,对于电镀工作者都是摆在面前需要解决的难题。
4.5.3.2.2 钝化前的清洗问题越是老化的镀液,环境温度越低,吸附在镀锌层表面的有机添加剂或其分解产物越难以洗净,甚至出现清洗后表面仍有似油污状不亲水的成团花斑,钝化后造成蓝白钝泛黄泛彩、彩钝后出现绿灰雾状、变色快、膜附着力差等毛病。
笔者在现场监管该工艺时,最头痛的是要不断提醒操作人员认真、再认真进行清洗,对大平面工件必须冲洗而不能只浸洗。
一些厂家可能出于无奈,只好把钝化前的处理工艺搞得很复杂:要求先用热稀碱水浸洗、流动冷水洗,再经出光、清洗后钝化。
通过脱膜处理,效果肯定是好的,但也带来几个问题:⑴工艺繁杂,对于许多电镀厂点,特别是自动线生产,存在生产线要重新改造问题,涉及场地、资金等问题;⑵因镀锌量大、价值低,热碱水洗能耗大,相应生产成本增加,甚至难以消化;⑶对定型的小件生产尚易办到,对不定型产品及大件镀锌,则设施难度很大;⑷这么复杂的钝化前处理工艺,使得氯化物镀锌已失去了“镀层光亮,可以直接低铬钝化”的优点。
因此,笔者认为,改进电镀工艺本身存在的问题,使镀层水洗性能良好,才是根本出路。
4.5.3.2.3 钝化液的老化问题过去认为低铬钝化液的老化是因为锌及三价铬的积累所造成。
对于氯化物镀锌的低铬钝化液,现在发现钝化液老化更快的重要原因是钝化液中有机添加剂的很快积累:镀前清洗不良引入及镀层夹杂物的溶解。
其现象是钝化液经搅动,表面产生大量泡沫。
在该钝化液中形成的钝化层,蓝白钝易泛彩,彩钝层更易色泽变淡、脱膜。
对于因锌及三价铬积累造成的钝化液老化,笔者在上世纪80年代作过不少试验,提出用高锰酸钾氧化三价铬、用黄血盐沉淀锌等重金属杂质的再生办法,并已发表过文章进行了较详细论述。
但对于有机添加剂积累而造成钝化液过早老化,则没有找到切实可行的再生办法。
目前唯一办法还是全部或部分更新钝化液(按要求,废弃液应处理后排放)。
因此,对低铬钝化液,应采用较低浓度的钝化工艺,以便将损失降到最低。
4.5.4 钝化工艺问题针对氯化物镀锌存在的上述诸多问题,从钝化工艺上加以改进,能减轻彩钝膜色泽变淡及附着力差的故障。
4.5.4.1 对三酸低铬钝化须加以改进镀锌低铬彩钝配方可以很简单,例如加入6-7g/L的CrO3及1g/L的ZnSO4·7H2O,新配时不加硝酸,即可形成色泽鲜艳的彩艳的彩钝层。