氯化物镀锌工艺的控制与常见问题的分析
氯化钾镀锌典型故障_周长虹 奥邦电镀

些电镀厂的镀液容易产生浮油 ( 漂在液面上的一种 油状有机物 ) 。其产生的原因主要为: ( 1) 前处理除 油不佳, 槽中有大量的有机油脂, 与表面活性剂形成 皂化等 ; ( 2) 镀液中有较多的铁杂质 , 镀液一般很混 浊; ( 3) 氯化钾的质量浓度过高; ( 4) 添加剂配比有 问题 , 添加剂中某类载体过多等 ; ( 5) 镀液的 pH 值 6。 氯化钾镀锌液面浮油的黏度大 , 易黏在槽壁、 挂 具、 滚桶、 阳极及镀件上或沉淀于镀液底部, 难以彻 底清除。氯化钾镀锌液是弱酸性的 , 本身不具有除 油能力。导电盐氯化钾对镀液的浊点有很大影响 , 在高温季节 , 当镀液中有较多铁杂质时, 添加剂的浊 点会大幅下降。随着组合型添加剂中某类载体添加 剂的不断积累, 与电镀液中的悬浮物和镀件中带入 的油污及三价铁离子共同作用 , 形成酸性且黏度大 的油渍, 严重影响镀层质量。 找到液面浮油产生的原因后, 解决起来就比较 容易了。要选择大品牌的氯化钾镀锌添加剂, 保证 前处理后镀件表面无油, 无锈, 无挂灰, 夏天镀液中 氯化钾的质量浓度不应过高 , 控制镀液的 pH 值在 5. 6~ 6. 0, 镀液温度不宜过高 , 对于已产生浮油的镀 液可按大处理方法进行认真处理 , 可除掉已产生的 浮油。
收稿日期: 2010 10 11
3
低铬彩钝较多有机添 加剂。这些有机物由于种种原因会夹杂在镀层中或 吸附在镀层表面。如果添加剂的质量不佳、 添加过 量或镀后清洗不干净 , 都会产生不良后果。 ( 1) 当镀层中夹杂过多的有机物 , 在钝化过程 中因膜首先被溶解, 结果有机物暴露出来 , 夹杂在工 件表面起隔离作用而使膜脱落或褪色。 ( 2) 清洗不彻底, 工件表面吸附的有机物会在 成膜过程中和工件存储过程中把六价铬还原成三价 铬, 过多的三价铬可能会影响彩钝膜的结合力或使 之变浅褪色。 ( 3) 由于钝化前清洗不认真或清洗不够 , 会带 入大量的氯离子 , 虽然少量的氯离子有利于成膜的 进行 , 但过量会使膜过厚而易脱落。 ( 4) 由于镀前处理时没有彻底清除油污及氧化 膜, 造成局部镀层结合力不好 , 导致钝化膜脱落。 ( 5) 镀锌液工艺控制不当, 使镀液不稳定, 局部 导电不良, 造成镀层疏 松、 脆性 大及结合力差等 缺 陷。 ( 6) 钝化剂硫 酸根和氯 离子的质 量浓度过 高 时, 成膜过快过厚, 时间上很难掌握 , 时间短色泽浅 ,
氯化物镀锌层发雾原因及解决方法

氯化物镀锌层发雾原因及解决方法氯化物镀锌层是一种常见的金属表面处理方法,它可以有效地提高金属的耐腐蚀性能和美观度。
然而,在使用氯化物镀锌层的过程中,有时会出现发雾的现象,这会影响到产品的质量和外观。
本文将探讨氯化物镀锌层发雾的原因和解决方法。
一、氯化物镀锌层发雾的原因1. 镀液中杂质含量过高在氯化物镀锌层的制备过程中,如果镀液中的杂质含量过高,就会导致镀层表面出现雾状物质。
这些杂质可能来自于原材料、设备或操作人员等方面。
2. 镀液中氯离子含量过高氯离子是氯化物镀锌层制备过程中必不可少的成分,但如果氯离子含量过高,就会导致镀层表面出现雾状物质。
这是因为氯离子会与金属离子结合形成氯化物,当氯离子过多时,就会形成过多的氯化物,从而导致镀层表面出现雾状物质。
3. 镀液中温度过高在氯化物镀锌层的制备过程中,如果镀液的温度过高,就会导致镀层表面出现雾状物质。
这是因为温度过高会使镀液中的气体溶解度降低,从而导致气泡在镀层表面聚集形成雾状物质。
二、氯化物镀锌层发雾的解决方法1. 控制镀液中杂质含量为了避免镀液中杂质含量过高导致镀层表面出现雾状物质,可以采取以下措施:(1)使用高纯度的原材料。
(2)定期清洗设备,避免设备中积累过多的杂质。
(3)加强操作人员的培训,确保操作规范。
2. 控制镀液中氯离子含量为了避免镀液中氯离子含量过高导致镀层表面出现雾状物质,可以采取以下措施:(1)控制氯化物的加入量,避免过量加入。
(2)定期检测镀液中氯离子含量,确保在合理范围内。
3. 控制镀液中温度为了避免镀液中温度过高导致镀层表面出现雾状物质,可以采取以下措施:(1)控制镀液的温度,确保在合理范围内。
(2)加强镀液的搅拌,避免气泡在液体中聚集。
综上所述,氯化物镀锌层发雾的原因主要是镀液中杂质含量过高、氯离子含量过高和温度过高等因素导致的。
为了避免这种现象的发生,需要控制镀液中的各项参数,确保在合理范围内。
只有这样,才能制备出高质量的氯化物镀锌层。
氯化镀锌霍尔槽高区漏镀

氯化镀锌霍尔槽高区漏镀氯化镀锌是一种常见的电镀方法,可用于将金属表面涂上一层锌。
在实际应用中,氯化镀锌通常用于保护金属材料不受腐蚀。
然而,在进行氯化镀锌过程中,由于各种因素的影响,也会出现一些问题,比如高区漏镀。
本文就围绕氯化镀锌霍尔槽高区漏镀问题阐述一下解决方法。
步骤一:分析高区漏镀原因首先,需要对高区漏镀问题进行分析。
高区漏镀指的是电镀液在霍尔槽高区过度蒸发,导致涂层质量受到影响,表现为镀层薄、不均匀等问题。
这种现象通常是由于电镀液的组成及加热方式等因素引起的,因此需要进行详细的现场调查,确定高区漏镀的具体原因。
步骤二:调整电镀液组成和加热方式根据分析结果,可以逐步采取一些措施,以消除或缓解高区漏镀问题。
在实际应用中,我们可能需要调整电镀液的组成,增加某些特定添加剂的浓度,或增加一些稳定剂等。
此外,为了防止电镀液在高区过度蒸发,我们还可以调整加热方式,尽可能降低电镀槽霍尔槽高区的温度。
步骤三:优化工艺参数除了调整电镀液组成和加热方式外,我们还可以通过优化工艺参数来解决高区漏镀的问题。
优化工艺参数可以包括电流密度的调整、涂层厚度的控制、镀层停留时间的调整等。
通过合理优化工艺参数,我们可以有效缓解高区漏镀问题的出现。
步骤四:加强监控和管理最后,我们还需要加强监控和管理工作。
在实际运行中,我们需要经常对电镀槽的工作状态进行监测和调整,及时发现问题并加以解决。
此外,还需要对操作人员进行培训和管理,确保他们能够正确操作设备以及及时发现电镀槽内部的问题。
总结综上所述,高区漏镀是氯化镀锌过程中常见的问题,合理解决高区漏镀问题,不仅可以提高电镀涂层的质量和稳定性,还可以延长设备的使用寿命,提高生产效率,降低生产成本。
在实际应用中,通过分步骤分析解决问题,可以迅速有效地解决高区漏镀等氯化镀锌过程中的问题。
常见13种氯化钾镀锌 故障分析告诉你答案

常见13种氯化钾镀锌故障分析告诉你答案本篇汇总了氯化钾镀锌的常见故障,包括镀层不光亮、发雾、结合力差、烧焦、黑色条纹、厚度不均、脆性、沉积速度慢、分散能力差、镀液浑浊等。
介绍了这些疵病的产生原因及其处理方法。
提出了应加强工艺管理、认真做好镀液维护、定期进行净化等措施,以期避免或减少故障发生。
氯化钾镀锌是由最早的无氰氯化铵镀液发展而来的一种无铵弱酸性光亮镀锌工艺。
其优点是:(1)镀液导电性好,槽压低,节省电能;(2)镀层结晶细致、光亮、平整;(3)电流效率高,沉积速度快;(4)镀液分散能力好;(5)适用于铸件直接电镀;(6)废水处理简便,解决了环境污染的问题。
因此,氯化钾镀锌在工业上得到了广泛应用。
但是,在日常生产中难免会发生质量故障,主要原因在于镀液维护不力,组分失调或受到有害杂质干扰,以及工件前处理不良。
本篇拟就氯化钾镀锌中常见故障的产生原因及其处理方法进行汇总和介绍。
各种常见故障的产生原因及其处理方法1.镀层不光亮产生原因:(1) 镀液浓度过低(即氯化锌、氯化钾和硼酸的含量均低);(2) 光亮剂不足;(3) pH 过高;(4) 镀液温度过高;(5) 阴极电流密度小;(6) 金属铁杂质多;(7) 有机杂质多。
处理方法:(1) 通过分析,补加氯化锌、氯化钾和硼酸至工艺规范;(2) 适当添加光亮剂;(3) 用稀盐酸溶液调节pH 至工艺规范;(4) 降低镀液温度至工艺规范;(5) 适当提高阴极电流密度;(6) 加入~ 2 mL/L 的双氧水(w = 30%),充分搅拌后,用w = 5% 的氢氧化钠调节pH 至,沉淀、过滤后可除去氢氧化铁;(7) 在镀液温度为45 °C 时加入1 ~ 3 g/L 活性炭,搅拌约30 min 后过滤;或采用高锰酸钾法处理,即先用稀盐酸调低pH 至3 ~ 4,然后在搅拌的情况下将溶有~ 1 g/L 高锰酸钾的热水均匀加入镀液中,再继续搅拌30 min ,然后静置过滤,可除去有机物。
氯化钾镀锌的生产应用现状,及技术误区的探讨

氯化钾镀锌的生产应用现状,及技术误区的探讨氯化钾镀锌作为取代氰化镀锌的较成功工艺之一,得到广泛应用。
经30多年应用,但在生产实践中不少人仍对其缺乏深入全面的了解,对过去认知的优缺点应作重新审视;生产实践中反映出的不少问题,尚值得讨论。
在此,我结合个人实践体会,对一些问题提出看法,供同行参考。
1对工艺优缺点的重新审视当初推广氯化钾镀锌时对其优缺点有所评述,现经实践检验未必完全正确。
我人人这样认为,其主要优点有:(1)镀液呈微酸性,阴极电流效率可高达90%~95%,镀速较快,特别对铸件电镀有利;(2)镀液组分简单,易于调整;(3)相对于锌酸盐镀锌,对杂质敏感性低,允许容存量较大且易于处理;(4)比其他镀锌工艺易获得高亮度镀层,利于蓝白钝化与银白钝化;(5)镀前除油处理比锌酸盐镀锌要求低。
其原本存在及新暴露出来的主要缺点有:(1)镀层及钝化层防蚀性能在各种镀锌工艺中处于最差地位。
主要原因是为保证阴极极化,镀液中表面活性物质加入量很大,在镀层中的夹附量也很大,镀锌层纯度很差。
在发生电化学腐蚀时,因微电池作用,锌的腐蚀加快;钝化层中的有机夹杂也降低了其抗蚀力。
故该工艺不适合于防蚀性要求较高的汽车及电器产品镀锌。
(2)钝化层中因有机物夹附过多,蓝白钝化易泛彩、发花、发黄;白钝层易变灰暗,甚至长白灰、白毛;彩钝层色泽很易变淡,彩钝膜附着力远不如锌酸盐镀锌。
(3)过去认为废水处理简单而现在看来因无强配位剂,锌易处理,但废水中大量的表面活性剂成了废水处理的一大负担:即便采用成本高的活性炭处理也几乎无效,排放废水产生让人生厌的大量泡沫、必测指标化学耗氧量COD很易超标,阴离子表面活性剂ALS 也易超标。
(4)对设备腐蚀性较强,铜极杆等很易生成碱式碳酸铜。
2主要成分的控制2.1主盐氯化锌过去追求允许电流密度越大越好,实际不对。
由于镀液中无强配位剂(Cl-对Zn2+有微弱配位能力),必须保持适度的浓差极化,因而主盐浓度不能过高。
氯化钾镀锌主要成分及工艺条件的控制

氯化钾镀锌主要成分及工艺条件的控制前言氯化钾镀锌是上世纪80年代发展起来的一种光亮镀锌工艺。
近年来,我国在电镀添加剂研究开发上取得了显著进展,使得氯化钾镀锌工艺水准达到一个全新的高度,例如:LAN-930氯化钾镀锌工艺较为成功地解决了传统氯化钾镀锌工艺的3大难题:(1)镀层的耐盐雾试验性能比碱性镀锌差;(2)添加剂的分解产物多;(3)铁杂质易超标。
新型氯化钾镀锌添加剂的使用,降低了电镀生产厂商的生产成本,促进了国内电镀锌工艺朝更利于节约成本且环境友好的方向发展。
1·氯化钾镀锌成分及工艺条件的控制氯化钾镀锌工艺的常用配方的工艺条件范围是比较宽广的,其主要成分及工艺条件为:氯化锌30~80g/L,氯化钾180~280g/L,硼酸20~30g/L,添加剂适量,pH值4.5~6.0,10~50℃。
1.1 氯化钾镀锌液主要成分的控制1.1.1 氯化锌氯化锌系主盐,溶于水中会大量放热。
当溶液的pH值≥6.2时,有沉淀产生。
锌离子的质量浓度≥90g/L 时,光亮电流密度范围扩大,但镀液的分散能力和深镀能力会有所下降。
锌离子的质量浓度较低时,光亮电流密度的上限下降,高电流密度区易烧焦,此时的深镀能力较好,但镀层沉积速率较慢。
可增加阳极面积,同时保持镀液较低的pH值,从而使锌离子的质量浓度逐渐上升。
对挂镀而言,当氯化锌的质量浓度为60~70g/L 时,镀液的分散能力最好。
氯化钾镀锌液中无强配位剂,其分散能力和深镀能力不如氰化物镀锌,更加不如无氰碱性锌酸盐镀锌。
有人喜欢在氯化钾镀锌液中加入少量氯化铵,但镀液中加入氯化铵后其分散能力和深镀能力均无改善;又会增加电镀废水的达标难度,所以当使用优良氯化钾镀锌光亮剂时,一般不建议加入氯化铵。
1.1.2 氯化钾氯化钾是弱的配位剂和导电盐,其质量浓度应适当。
当其质量浓度恰当时,镀液的导电性最好,过多或过少都会降低镀液的电导率,从而影响镀液的分散能力和深镀能力。
大量氯离子的存在能增加阴极极化,提高镀液的分散能力和深镀能力,促进阳极的正常溶解。
氯化物镀锌常见故障处理
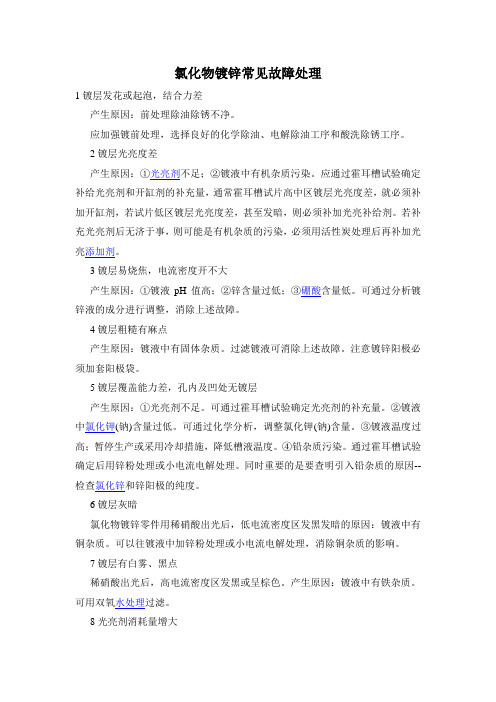
氯化物镀锌常见故障处理1镀层发花或起泡,结合力差产生原因:前处理除油除锈不净。
应加强镀前处理,选择良好的化学除油、电解除油工序和酸洗除锈工序。
2镀层光亮度差产生原因:①光亮剂不足;②镀液中有机杂质污染。
应通过霍耳槽试验确定补给光亮剂和开缸剂的补充量,通常霍耳槽试片高中区镀层光亮度差,就必须补加开缸剂,若试片低区镀层光亮度差,甚至发暗,则必须补加光亮补给剂。
若补充光亮剂后无济于事,则可能是有机杂质的污染,必须用活性炭处理后再补加光亮添加剂。
3镀层易烧焦,电流密度开不大产生原因:①镀液pH值高;②锌含量过低;③硼酸含量低。
可通过分析镀锌液的成分进行调整,消除上述故障。
4镀层粗糙有麻点产生原因:镀液中有固体杂质。
过滤镀液可消除上述故障。
注意镀锌阳极必须加套阳极袋。
5镀层覆盖能力差,孔内及凹处无镀层产生原因:①光亮剂不足。
可通过霍耳槽试验确定光亮剂的补充量。
②镀液中氯化钾(钠)含量过低。
可通过化学分析,调整氯化钾(钠)含量。
③镀液温度过高;暂停生产或采用冷却措施,降低槽液温度。
④铅杂质污染。
通过霍耳槽试验确定后用锌粉处理或小电流电解处理。
同时重要的是要查明引入铅杂质的原因--检查氯化锌和锌阳极的纯度。
6镀层灰暗氯化物镀锌零件用稀硝酸出光后,低电流密度区发黑发暗的原因:镀液中有铜杂质。
可以往镀液中加锌粉处理或小电流电解处理,消除铜杂质的影响。
7镀层有白雾、黑点稀硝酸出光后,高电流密度区发黑或呈棕色。
产生原因:镀液中有铁杂质。
可用双氧水处理过滤。
8光亮剂消耗量增大产生原因:①镀液温度高。
最好采用冷却措施将降低槽液温度或采用间歇生产;②镀液中氯化钾、氯化锌含量过高,使镀液浊点降低,光亮剂析出。
通过分析镀液成分,稀释镀液;③工件除油不净,将大量油污带入镀液中,消耗光亮添加剂中的载体光亮剂。
保证镀锌零件电镀前除油要彻底。
9镀层有条纹产生原因:①光亮剂失调,配槽时添加剂严重不足。
可通过霍耳槽试验,补充添加剂的用量。
氯化钾镀锌常见故障分析

已经应用 于怀集 登 云 汽配 股 份 有 限公 司 的生产 中。 实践 证 明效果 良好 。
参 考文 献
[ ] Q / 6 - 0 , 1 C T4 92 2 汽车发动机气 门技术条件[ ] 0 S. [ ] 文斯雄。钢铁 零件化 学抛 光 [ ] 电镀 与环 保 ,0 5 2 J. 20 ,
a .加强 除油 、 洗 ; 酸 b .调 整光亮 剂含 量 ; C .调整 p 至工艺 范 围 ; H d .补充 硼酸 ; e .降低 阴极 电流密度 。
6 掉入槽 内的镀件 必须及 时捞取 , ) 防止腐蚀
溶解 。
田 永 良
( 中航成 飞热表 处理 厂 )
1 产生原 因 )
对 镀液成 份 、H进行分 析 , 液 温度 、 p 对镀 电流密
度 和 电镀 时 间进 行排 查均未 发现 问题 。怀疑是 光亮
a .镀锌槽 温度 过高 ; b .光亮 剂不 足 ;
C H过高 ; .p
剂 少 了 , 量 添加光 亮 剂 也无 效 。只好 做 赫 尔槽 试 适
2 漏
镀
1 产 生原 因 ) a .镀锌槽 中光亮 剂 比例失调 ; b .镀 锌槽 中有杂 质离子 ; C .镀锌槽 中 C 一 1 含量 低 ; d .局部 前处理 不净 , 有绝缘 物 附着 。 2 处 理方法 ) a .调 整镀锌槽 中光亮剂 比例 ; b .去除镀 锌槽 中杂质 离子 ; c .调 整镀锌槽 中 c 一 量至工 艺 范围 ; 1含 d .加 强除 油 、 酸洗 。
验, 试验也 正 常。在 现场发 现一零件 上有 指纹 , 这下
d .锌离 子含 量过 高 , 钾盐 含量 少 ;
e .硼 酸含 量少 ; f .有重金 属杂 质 。 2 处理 方法 )
氯化物镀锌层表面粗糙度的影响因素及其控制

采用 双 电极体 系 , 阳极 为 电解 锌 板 , 阴极 为紫 铜
圆片 ( 径 4 直 O mm, 度 0 5 mm) S e :S 极一 厚 . ,m 2:1 阴阳 极 间 距 为 2 , 0 mm。 阴 极 前 处 理 工 艺 流
性变大, 出现少 量氢 气被 晶粒 包裹 的情 况【 , 4 导致 镀 ]
2 0 3 ( ):5 — 4 0 4, 3 5 25 .
电流密度 的增加 而增 大 , 随镀 液温 度 的升 高而 降低 ,
随 镀液 p 值 的增 大 先降 低后 升高 。 H
参考文献 :
[ ] 朱 晓 东 , 宁 ,黎 德 育 ,等 .镀 液 流速 对 高 速 镀 锌 层 粗 糙 度 及 1 李
dn i e st y,b t e e a u e a d b t H a u n is s ra e r u h e s we e i v s ia e . An h p i a p o e s p r me e s a h t mp r t r n a h p v l e o t u f c o g n s r n e tg t d d t eo t m l r c s a a t r
1 2 实 验 方 法 .
氢 过 电位低 且沉 积 速 率 慢 , 电极 反 应所 消耗 掉 的金
属 离子 能及 时得 到 补给 , 因而 氢气 的产 生量 小 , 镀层 表 面 的针孔 、 瘤 等 缺 陷少 , 面相 对 较 平 整 ; 电 积 表 当 流 密度 为 9A/ m 时 , 管 阴极 过 电 位 增 大 , 助 d 尽 有 于细化 晶粒 , 此 时 电极 过 程 液 相 传 质受 限 的 可能 但
镀锌工艺技术难点

镀锌工艺技术难点镀锌是一种常见的表面处理方法,能够为金属制品提供良好的耐腐蚀性能。
镀锌工艺技术在实践中存在着一些技术难点,下面将对其中的几个难点进行详细介绍。
首先,镀锌工艺技术难点之一是处理前的表面处理。
在进行镀锌之前,金属制品的表面需要进行一系列的前处理,以确保镀层的质量和附着力。
其中最关键的步骤是除去金属表面上的油污和氧化物,这种污染物会影响锌层的附着力和涂层的质量。
但是,由于金属表面的特殊性和种类的多样性,选择合适的前处理方法成为了一个难点。
对于铁和钢制品,常见的方法是酸洗和磷化,而对于铝制品,一般使用酸洗和化学稳定剂。
因此,在实践中,需要根据不同金属材料的特点,选择合适的表面处理方法。
其次,镀锌工艺技术的另一个难点是锌电解液的控制。
镀锌的关键步骤是将金属制品浸入锌电解液中,在电流的作用下,将锌金属沉积在金属表面上。
而锌电解液的成分、温度和搅拌速度等参数都会影响锌层的质量和均匀性。
其中最重要的参数是锌电解液的成分,它会影响锌层的亮度、硬度和附着力。
常见的锌电解液成分包括硫酸锌、氯化锌和氯化铵等。
在实际操作中,需要根据镀锌的要求和金属材料的特点,进行合理的电解液配方和控制。
最后,镀锌工艺技术的另一个难点是镀层的控制。
镀锌后的金属制品需要具有一定的锌层厚度和均匀性,以保证其良好的耐腐蚀性能。
然而,镀锌的过程中,锌层的厚度和均匀性会受到很多因素的影响,如电流密度、浸泡时间和金属制品的形状等。
特别是对于复杂形状的金属制品,如管道、角钢等,由于其表面积分布不均,容易出现锌层不均匀的情况。
因此,在实践中,需要通过优化工艺参数和调整操作方法,实现镀层的均匀性控制。
综上所述,镀锌工艺技术中存在着一些技术难点,包括处理前的表面处理、锌电解液的控制和镀层的控制等。
解决这些难点需要对金属材料和工艺参数有深入的了解和掌握。
通过不断的研究和实践,相信这些难点能够得到有效的解决,为镀锌工艺技术的发展提供更好的支持。
氯化镀锌霍尔槽高区漏镀

氯化镀锌霍尔槽高区漏镀随着工业化进程的不断发展,金属材料的需求量也越来越大,而镀锌技术在金属材料的生产中起着至关重要的作用。
氯化镀锌技术作为一种高效、环保的表面处理技术,被广泛应用于各种金属材料的表面处理中。
但是,氯化镀锌技术在应用过程中也会遇到一些问题,其中之一就是氯化镀锌霍尔槽高区漏镀问题。
本文将从氯化镀锌技术的原理和氯化镀锌霍尔槽高区漏镀问题的原因入手,探讨这一问题的解决方法。
一、氯化镀锌技术原理氯化镀锌技术是利用电化学原理,在金属表面形成一层锌层,使金属表面具有耐腐蚀性、耐磨性和美观性的表面处理技术。
氯化镀锌技术的主要原理是:将含有锌离子的氯化锌溶液作为电解液,将金属材料作为阴极,通过外加电压,使锌离子在金属表面还原成锌层。
氯化镀锌技术的优点是镀层均匀、致密,与基材结合牢固,耐腐蚀性好,而且生产效率高、环保。
因此,氯化镀锌技术被广泛应用于各种金属材料的表面处理中。
二、氯化镀锌霍尔槽高区漏镀问题的原因氯化镀锌霍尔槽高区漏镀问题是指在镀锌过程中,霍尔槽高区的部分区域出现镀锌不良的现象。
这一问题的原因主要有以下几个方面: 1、氯化镀锌液中的镁离子含量过高。
氯化镀锌液中如果含有过多的镁离子,会导致氢气析出不完全,从而影响镀层的质量。
而镁离子在霍尔槽高区的沉积速度较快,因此在高区容易出现漏镀的问题。
2、氯化锌溶液的温度过低。
氯化镀锌液的温度过低会影响锌离子的扩散速度,从而影响镀层的质量。
而霍尔槽高区的温度往往比其他区域低,因此在高区容易出现漏镀的问题。
3、氯化镀锌液中的氢离子浓度过高。
氢离子是氯化镀锌液中的一种离子,如果氢离子浓度过高,会导致氢气析出不完全,从而影响镀层的质量。
而霍尔槽高区的氢离子浓度往往比其他区域高,因此在高区容易出现漏镀的问题。
三、氯化镀锌霍尔槽高区漏镀问题的解决方法针对氯化镀锌霍尔槽高区漏镀问题,可以采取以下措施:1、控制氯化镀锌液中的镁离子含量。
可以通过增加氯化锌的浓度或者添加其他镀锌助剂来降低氯化镀锌液中的镁离子含量。
氯化物镀锌工艺的控制与常见问题的分析

氯化物镀锌工艺的控制与问题分析何氏槽的试验2A,5分钟(挂镀)和1A,5分钟(滚镀)的试片的状况,与镀液的下述情况对应:最佳组成:试片全光亮,仅高电流密度端0.6cm宽的部分有烧焦。
锌含量过低:试片的高电流密度端烧焦,在此区域内非常粗糙。
锌含量过高:试片的低电流密度端均镀能力差。
氯化物含量过低:低电流密度下的效率低,氯化物含量高时不可察觉。
光亮剂含量过低:测量该镀液镀得的试片上,高电流密度端的粗糙面或烧焦面的宽度。
如果加入光亮剂后,此粗糙面或烧焦面的宽度出现可以测得的缩小,则表示此镀液中光亮剂的含量低于最佳值。
光亮剂含量过高:中、高电流密度区极其光亮,光亮剂含量极高时,低电流密度区出现漏镀,高电流区起泡。
故障处理:当镀锌出现问题时,首先应检查一些明显的参数:温度、金属浓度、pH和氯化物的含量。
如果这些参数都正确,则最多的问题是清洗不充分而引起的,无论是零件,还是镀槽、清洗不好,均会遇到问题。
检查来自吸风罩的灰尘,天花板上的锈等。
检查过滤机,看有哪些污染物存在。
记住:大多数的电镀问题都是前处理(脱脂、酸浸渍和清洗)或物理因素(差的电接触与整流,杂散电流等)引起的,而不是化学原因。
污染:金属杂质有铁、镉、铅、镍、铜和铬,如果金属杂质引起共沉积和污点,用下述方法处理。
铁:定期地、频繁地取出落入槽底的零件,以防止铁杂质的积累。
铁含量达有害限度时,将与锌共沉积,在零件镀后用硝酸浸光或进行钝化时,在高电流密度区会产生兰色到黑色的斑点,对于各个镀液来说,铁含量的有害限度不同,它还取决于电镀的电流密度和所用的铬酸盐钝化的类型等。
如果铁杂质的量超出了容忍度,可以用高锰酸钾或双氧水处理镀液,以除去铁。
约180 g/1000L的高锰酸钾可将铁氧化为可过滤的沉淀,从而避免了斑点的生成。
如果没有高锰酸钾,则可用250ml/1000L 的35% 的双氧水处理镀液,然而高锰酸钾是更可取的氧化剂。
铜、镉和铅:铜杂质使镀层在光亮浸渍或铬酸盐钝化时,在低电流密度区产生棕色到黑色的斑点;镉杂质使镀层变得不亮,且在光亮浸渍或铬酸盐钝化时,在低电流密度区产生黑色斑点;铅杂质引起低电流密度区漏镀。
氯化物全光亮锌铁合金电镀工艺的应用
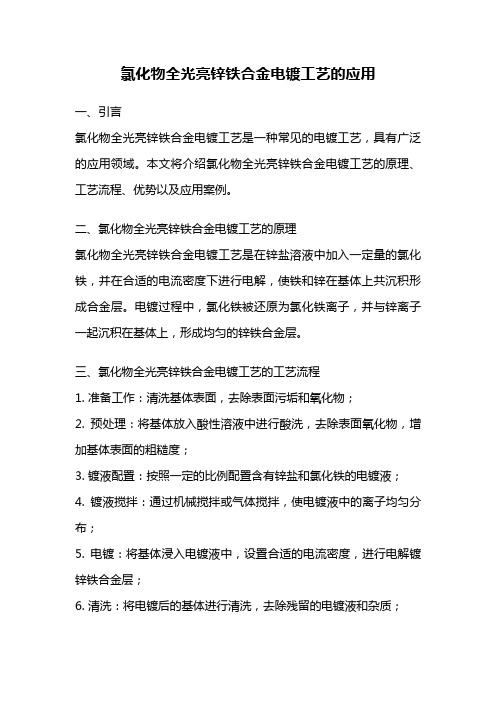
氯化物全光亮锌铁合金电镀工艺的应用一、引言氯化物全光亮锌铁合金电镀工艺是一种常见的电镀工艺,具有广泛的应用领域。
本文将介绍氯化物全光亮锌铁合金电镀工艺的原理、工艺流程、优势以及应用案例。
二、氯化物全光亮锌铁合金电镀工艺的原理氯化物全光亮锌铁合金电镀工艺是在锌盐溶液中加入一定量的氯化铁,并在合适的电流密度下进行电解,使铁和锌在基体上共沉积形成合金层。
电镀过程中,氯化铁被还原为氯化铁离子,并与锌离子一起沉积在基体上,形成均匀的锌铁合金层。
三、氯化物全光亮锌铁合金电镀工艺的工艺流程1. 准备工作:清洗基体表面,去除表面污垢和氧化物;2. 预处理:将基体放入酸性溶液中进行酸洗,去除表面氧化物,增加基体表面的粗糙度;3. 镀液配置:按照一定的比例配置含有锌盐和氯化铁的电镀液;4. 镀液搅拌:通过机械搅拌或气体搅拌,使电镀液中的离子均匀分布;5. 电镀:将基体浸入电镀液中,设置合适的电流密度,进行电解镀锌铁合金层;6. 清洗:将电镀后的基体进行清洗,去除残留的电镀液和杂质;7. 表面处理:对电镀后的基体进行必要的表面处理,如喷砂、抛光等;8. 检验:对镀层进行检验,检查其厚度、硬度和耐腐蚀性能;9. 包装:将符合要求的镀件进行包装。
四、氯化物全光亮锌铁合金电镀工艺的优势1. 均匀性:氯化物全光亮锌铁合金电镀工艺能够使锌和铁均匀共沉积,形成均匀的合金层,提高镀层的质量;2. 耐腐蚀性:锌铁合金层具有良好的耐腐蚀性能,能够有效地保护基体不受外界环境的侵蚀;3. 耐磨性:锌铁合金层具有较高的硬度和耐磨性,能够增加基体的使用寿命;4. 美观性:氯化物全光亮锌铁合金电镀工艺能够使镀层表面光亮、平整,提高镀件的美观度;5. 环保性:氯化物全光亮锌铁合金电镀工艺使用的电镀液中无铅,对环境无污染。
五、氯化物全光亮锌铁合金电镀工艺的应用案例氯化物全光亮锌铁合金电镀工艺广泛应用于汽车零部件、机械设备、电子产品等领域。
例如,在汽车零部件领域,氯化物全光亮锌铁合金电镀工艺可以提供耐腐蚀、耐磨、美观的镀层,保护零部件不受湿润、腐蚀性气体等环境的侵蚀,延长其使用寿命。
浅谈氯化锌的返点及变色

浅谈氯化物镀锌层返点及变色一、前言由于我国改革开放日益深入,各行各业蓬勃发展,同时带来了环境问题的严重挑战,尤其我们电镀行业更加面临着生产工艺日益月新的改革,才能紧跟时代发展的步伐,以前我们的工艺落后,污染严重,比如我们以前使用的氰化物镀锌,由高氰镀锌发展到中氰镀锌,后来由于光亮剂的研发成功的改进为低氰,微氰镀锌,对环境保护起到积极作用,但还不能满足当前适应我们环境保护的要求,但是我们的工艺中还存在着含氰物质,所以氯化物镀锌工艺越来越受到广大电镀界,环保界人士所重视,我国从70年代初发展到至今的氯化物镀锌已得到长足的发展,说明该工艺确有其优点,氯化物镀锌的电流效率高达(95%以上),槽压低,所以比氰化镀锌节约50%以上的电,同时适用各种高碳黑色金属基体的表面镀锌层。
生产效益也比氰化物镀锌高出30%-50%左右,但是由于氯化物镀锌的光亮剂的主要成分是载体表面活性剂去乳化光亮剂醛类,因表面活性剂对镀件有一定的附着力,水洗效果不十分好,同时氯化物镀锌对铁,铜,铅等杂质很敏感,所以镀锌件返点变色,也不足为奇了,那么我们怎样才能改变这个缺点呢?靠我们去改变操作工艺或使用原料上去想办法。
二、镀锌层返点变色产生的原因1.镀前处理不良,工件表面的油污清洗不干净,经酸洗后,水洗的难度加大基体表面形成花斑或条纹状,该表面镀层难以沉积或沉积镀层很薄,若工件表面的铁锈处理不完全,镀层只能在锈迹周围沉积,出现黑色斑点,或者如滚镀经过物理作用锈迹渐渐被摩擦被溶解,后期方有镀层沉积,该部位镀层沉积时间短,镀层很薄,光亮度差而出现白色斑点2.阴极电流密度大,阴极区PH值升高过快,镀层中有金属氢氧化物或碱式盐类附于镀层中,而出现斑点。
3.镀液中有机杂质的来源主要是添加剂分解产物和未清洗干净的油污长时间在镀液中积累会使镀层发雾。
4.光亮剂添加太多,会造成阴极无法消耗,形成光亮剂过剩夹入镀锌层,或附着在工件表面,清洗不干净,经钝化后产生酸性胶体状的表面活性剂。
氯化物镀锌故障分析与处理措施及工序控制

氯化物镀锌故障分析与处理措施及工序控制氯化物镀锌中由于镀液成分维护不当,可能会导致镀锌层质量的下降。
因此,要做到以下几点:1.把好电镀原料关要得到厚度均匀、结晶细致的氯化物镀锌层,选用具有良好分散能力和深镀能力的镀锌工艺配方是重要的,但选择质量优良的原材料和添加剂更重要。
若使用的氯化钾、氯化锌、硼酸、添加剂等成分的质量不能得到保证,也同样无法获得高质量的镀锌层。
对于有些原料必须进行双氧水一活性炭处理。
如对氯化钾可用80℃以上的热水搅拌溶解,加30%H2O2lmL/L,搅拌lOmin左右,静置2h;再用5%NaOH溶液调pH值到7.0~7.5;然后,加活性炭2g/L并加温到70℃,搅拌lh,静置沉淀2h,过滤即可。
2.氯化物镀锌液主盐含量的控制氯化锌是镀液的主盐。
一般随氯化锌含量的增加,允许电流密度上限提高,可以提高沉积速度和生产效率,还可减少金属杂质的影响,但分散能力和覆盖能力会随氯化锌含量增大而降低。
氯化锌含量低,有利于提高镀液的分散能力和覆盖能力,所以滚镀锌或形状较为复杂的零件挂镀锌宜采用锌浓度稍低的镀液。
在氯化物电镀生产过程中,镀液中锌离子浓度呈上升趋势,这与镀槽中锌阳极板的多少以及镀液的pH值有关。
3.镀液中氯化钾(钠)含量的控制氯化钾、氯化钠既是导电盐又是镀液的络合剂。
在含大量氯化钾或氯化钠的镀溶液中,锌离子不是以简单阳离子形式存在,而是以各种络合阴离子形式如[ZnCh(H20)2]2一存在。
严格讲,氯化钾(钠)镀锌液是络合物镀液,但由于络合离子在阴极过程中起电子桥作用,催化了电极过程,因而无显著的极化作用。
氯化钾(钠)含量的增加可提高镀液的导电性和分散能力。
氯化钾含量高,镀液分散能力好,光亮电流密度范围宽,同时镀层光亮度提高。
氯化钾含量从210~240g/L无明显影响,若低于180g/L,上述性能下降。
但含量过高将明显降低镀液的浊点,配槽时溶解也困难。
因此氯化钾的含量宜取180~230g/L,配槽时最好采用上限含量。
镀锌常见质量问题及其解决方法共46页文档
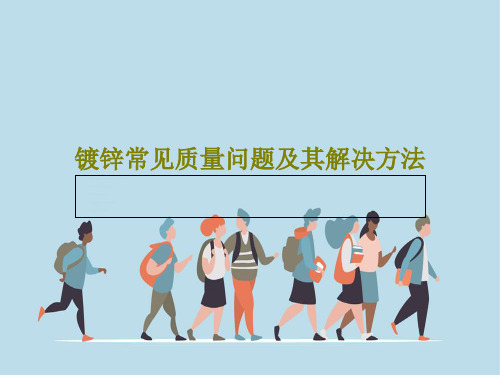
•
29、在一切能够接受法律支配的人类 的状态 中,哪 里没有 法律, 那里就 没有自 由。— —洛克
•
30、风俗可以造就法律,也可以废除 法律。 ——塞·约翰逊
56、书不仅是生活,而且是现在、过 去和未 来文化 生活的 源泉。 ——库 法耶夫 57、生命不可能有两次,但许多人连一 次也不 善于度 过。— —吕凯 特 58、问渠哪得清如许,为有源头活水来 。—— 朱熹 59、我的努力求学没有得到别的好处, 只不过 是愈来 愈发觉 自己的 无知。 ——笛 卡儿
镀锌常见质量问题及其解决方法
•
26、我们像鹰一样,生来就是自由的 ,但是 为了生 存,我 们不得 不为自 己编织 一个笼 子,然 后把自 己关在 里面。 ——博 莱索
•
27、法律如果不讲道理,即使延续时 间再长 ,也还 是没有 制约力 的。— —爱·科 克
•
பைடு நூலகம்
28、好法律是由坏风俗创造出来的。 ——马 克罗维 乌斯
拉
60、生活的道路一旦选定,就要勇敢地 走到底 ,决不 回头。 ——左
- 1、下载文档前请自行甄别文档内容的完整性,平台不提供额外的编辑、内容补充、找答案等附加服务。
- 2、"仅部分预览"的文档,不可在线预览部分如存在完整性等问题,可反馈申请退款(可完整预览的文档不适用该条件!)。
- 3、如文档侵犯您的权益,请联系客服反馈,我们会尽快为您处理(人工客服工作时间:9:00-18:30)。
氯化物镀锌工艺的控制与问题分析
何氏槽的试验
2A,5分钟(挂镀)和1A,5分钟(滚镀)的试片的状况,与镀液的下述情况对应:
最佳组成:试片全光亮,仅高电流密度端0.6cm宽的部分有烧焦。
锌含量过低:试片的高电流密度端烧焦,在此区域内非常粗糙。
锌含量过高:试片的低电流密度端均镀能力差。
氯化物含量过低:低电流密度下的效率低,氯化物含量高时不可察觉。
光亮剂含量过低:测量该镀液镀得的试片上,高电流密度端的粗糙面或烧焦面的宽度。
如果加入光亮剂后,此粗糙面或烧焦面的宽度出现可以测得的缩小,则表示此镀液中光亮剂的含量低于最佳值。
光亮剂含量过高:中、高电流密度区极其光亮,光亮剂含量极高时,低电流密度区出现漏镀,高电流区起泡。
故障处理:当镀锌出现问题时,首先应检查一些明显的参数:温度、金属浓度、pH和氯化物的含量。
如果这些参数都正确,则最多的问题是清洗不充分而引起的,无论是零件,还是镀槽、清洗不好,均会遇到问题。
检查来自吸风罩的灰尘,天花板上的锈等。
检查过滤机,看有哪些污染物存在。
记住:大多数的电镀问题都是前处理(脱脂、酸浸渍和清洗)或物理因素(差的电接触与整流,杂散电流等)引起的,而不是化学原因。
污染:金属杂质有铁、镉、铅、镍、铜和铬,如果金属杂质引起共沉积和污点,用下述方法处理。
铁:定期地、频繁地取出落入槽底的零件,以防止铁杂质的积累。
铁含量达有害限度时,将与锌共沉积,在零件镀后用硝酸浸光或进行钝化时,在高电流密度区会产生兰色到黑色的斑点,对于各个镀液来说,铁含量的有害限度不同,它还取决于电镀的电流密度和所用的铬酸盐钝化的类型等。
如果铁杂质的量超出了容忍度,可以用高锰酸钾或双氧水处理镀液,以除去铁。
约180 g/1000L的高锰酸钾可将铁氧化为可过滤的沉淀,从而避免了斑点的生成。
如果没有高锰酸钾,则可用250ml/1000L 的35% 的双氧水处理镀液,然而高锰酸钾是更可取的氧化剂。
铜、镉和铅:铜杂质使镀层在光亮浸渍或铬酸盐钝化时,在低电流密度区产生棕色到黑色的斑点;镉杂质使镀层变得不亮,且在光亮浸渍或铬酸盐钝化时,在低电流密度区产生黑色斑点;铅杂质引起低电流密度区漏镀。
铜、铅和镉等杂质可用锌粉处理来除去。
为了快速净化,将锌粉调成糊状,散布在镀液表面,每3800升镀液约需0.45 Kg锌粉。
处理后数小时内必须过滤或倾析被处理的镀液,以除去锌粉和被吸附的杂质,在过滤机中装入锌粉是一个可选择的净化方法,无论哪个净化方法,锌粉均应从被处理的镀液中除去,否则,置换了污染物的锌粉将会再溶解,并重新污染镀液。
注意:过滤出的锌粉必须小心地处理,合适地处置,湿的锌粉可能引起自燃和火灾。
铬:铬杂质会使整个镀件不亮,首先出现在低电流密度区,并发展为低电流密度区漏镀,高电流密度区起泡,每400升镀液中加入7.5克亚硫酸氢钠,可暂时减轻铬污染的问题,若能除去污染源,则连续电解和带出可消除铬的污染。
镍:镍杂质会使中至低电流密度区的镀层发糊,可用低电流密度电解除去。
故障处理表
采用下述处理方法之前,应先检测: 温度, 金属浓度, PH, 氯化物的含量. 分析镀液,并进行何氏槽试验。