自动钻铆技术的应用和无头铆钉安装
先进的装配连接技术在航空制造领域的应用分析
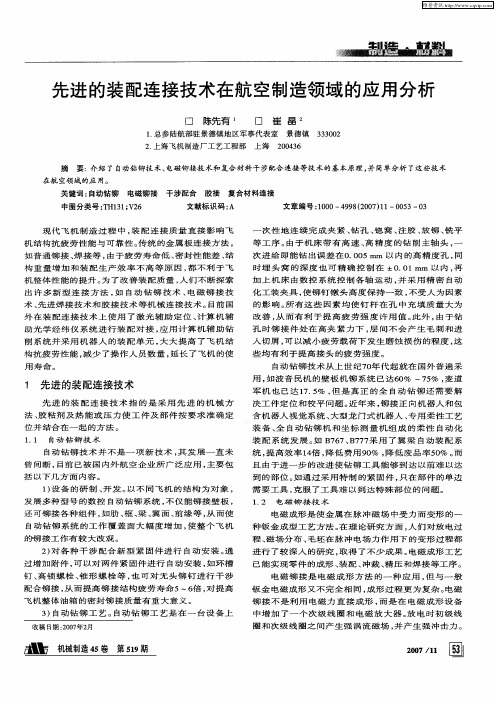
先进 的装 配连接技术在 航空制造领域 的应 用分析
口 陈先 有 口
上海
崔 晶
景德镇 3 30 302
20 3 04 6
1总参陆航部驻景德镇地 区军事代表室 .
2 上 海 飞 机 制 造 厂 工艺 工 程 部 . 摘
要 : 绍 了 自动 钻 铆 技 术 、 介 电磁 铆接 技 术 和 复 合 材 料 干 涉配 合 连 接 等 技 术 的基 本原 理 , 简 单 分 析 了这 些 技 术 并
时 埋 头 窝 的 深 度 也 可 精 确 控 制 在 士0 0 . 1mm 以 内 , 再 加 上 机 床 由数 控 系 统 控 制 各 轴 运 动 , 采 用 精 密 自动 并
化 工 装 夹 具 , 铆 钉 镦 头 高 度 保 持 一 致 , 受 人 为 因素 使 不 的 影 响 。 有 这 些 因 素 均 使 钉 杆 在 孔 中 充 填 质 量 大 为 所 改 善 , 而有 利 于提 高疲 劳强 度许 用 值 。 外 , 于钻 从 此 由 孔 时铆 接 件处 在 高夹 紧 力 下 , 间不 会 产 生 毛刺 和进 层 入 切 屑 , 以减 小 疲 劳 载 荷 下 发 生 磨 蚀 损 伤 的程 度 , 可 这 些 均 有 利 于 提 高 接 头 的疲 劳 强 度 。 自动 钻 铆 技 术 从 上 世 纪 7 年 代 起 就 在 国 外 普 遍 采 O 用 , 波 音 民机 的壁 板 机 铆 系 统 已 达 6 % ~7 % , 道 如 O 5 麦 军 机 也 已 达 1 . % , 是 真 正 的 全 自动 钻 铆 还 需 要 解 75 但 决 工 件 定 位 和 校 平 问 题 。 年 来 , 接 正 向机 器 人 和 包 近 铆 含 机 器 人 视 觉 系 统 、 型 龙 门式 机 器 人 、 用 柔 性 工 艺 大 专 装 备 、 自动 钻 铆 机 和 坐 标 测 量 机 组 成 的柔 性 自动 化 全 装 配 系 统 发 展 。 B 6 B 7  ̄ 用 了 翼 梁 自动 装 配 系 如 7 7、 7 7 统 , 高 效 率 1 倍 , 低 费 用 9 % , 低 废 品率 5 % 。 提 4 降 0 降 O 而 且 由 于 进 一 步 的 改 进 使 钻 铆 工 具 能 够 到 达 以 前 难 以达 到 的部 位 。 通 过 采 用 特 制 的 紧 固 件 , 在 部的研 制 、 发 。 不 同 飞 机 的 结 构 为 对 象 , ) 开 以 发 展 多 种 型 号 的数 控 自动 钻 铆 系 统 , 仅 能 铆 接 壁 板 , 不 还可铆 接各种 组件 , 肋 、 、 、 面 、 缘 等 , 而使 如 框 梁 翼 前 从
无头铆钉自动钻铆工艺试验研究
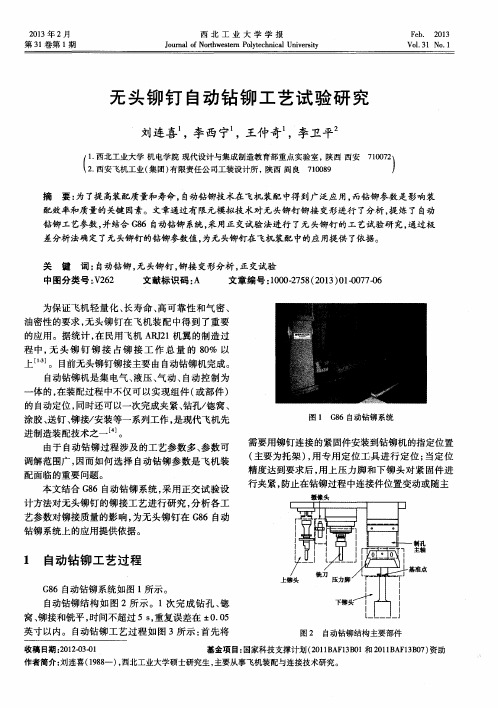
体的, 在装配过程 中不仅可 以实现组件 ( 或部件 )
图1 G 8 6自动钻铆 系统
的 自动 定位 , 同时还 可 以一次 完成 夹 பைடு நூலகம் 、 钻孔 / 锪窝 、
涂胶、 送钉 、 铆接/ 安装等一系列工作 , 是现代 飞机先 进 制造 装 配技术 之一 - 4 J 。 由于 自动钻铆过程涉及 的工艺参数多 、 参数可 调解范 围广 , 因而如何选择 自动钻铆参数是 飞机装
置, 并 在达 到该 位置 时铣 刀 自动终 止 。 3 . 2 铆钉 和试 片
表中: A ——压 铆力 、 B ——压 力 脚 回缩 压 力 、 c ——夹紧解除力 、 D ——双 向挤压夹紧力、 E ——镦
铆 过程 时 间 、 F —— 镦 铆 停 留 时 间 、 G — —上 铆 头 空
配 面临 的重 要 问题 。
需要用铆钉连接的紧固件安装到钻铆机的指定位置 ( 主要为托架) , 用专用定位工具进行 定位 ; 当定位 精度达到要求后 , 用上压力脚 和下铆头对紧固件进 行夹紧 , 防止在钻铆过程中连接件位置变动或随主
本文结合 G 8 6自动钻铆系统 , 采用正交试验设 计方法对无头铆钉 的铆接工艺进行研究 , 分析各工
摘
要: 为了提高装配质量和寿命 , 自 动钻铆技 术在飞机装配 中得到广泛应用, 而钻铆参数是影响装
配效率和质量的关键 因素。文章通过有限元模拟技 术对无头铆钉铆接变形进行 了分析, 提炼 了自 动
钻铆工艺参数, 并结合 G 8 6自 动钻铆 系统, 采用正交试验法进行 了无头铆钉的工艺试验研究, 通过极 差分析法确定 了 无头铆钉的钻铆参数值 , 为无头铆钉在飞机装配中的应用提供 了 依据。
自动钻铆技术在直升机机身总装中的应用研究
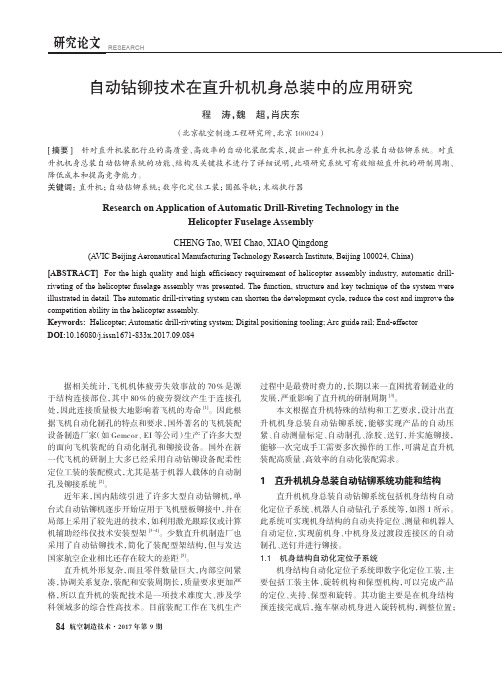
研究论文RESEARCH据相关统计,飞机机体疲劳失效事故的70%是源于结构连接部位,其中80%的疲劳裂纹产生于连接孔处,因此连接质量极大地影响着飞机的寿命[1]。
因此根据飞机自动化制孔的特点和要求,国外著名的飞机装配设备制造厂家(如Gemcor、EI 等公司)生产了许多大型的面向飞机装配的自动化制孔和铆接设备。
国外在新一代飞机的研制上大多已经采用自动钻铆设备配柔性定位工装的装配模式,尤其是基于机器人载体的自动制孔及铆接系统[2]。
近年来,国内陆续引进了许多大型自动钻铆机,单台式自动钻铆机逐步开始应用于飞机壁板铆接中,并在局部上采用了较先进的技术,如利用激光跟踪仪或计算机辅助经纬仪技术安装型架[3-4]。
少数直升机制造厂也采用了自动钻铆技术,简化了装配型架结构,但与发达国家航空企业相比还存在较大的差距[5]。
直升机外形复杂,而且零件数量巨大,内部空间紧凑,协调关系复杂,装配和安装周期长,质量要求更加严格,所以直升机的装配技术是一项技术难度大、涉及学科领域多的综合性高技术。
目前装配工作在飞机生产自动钻铆技术在直升机机身总装中的应用研究程 涛,魏 超,肖庆东(北京航空制造工程研究所,北京100024)[摘要] 针对直升机装配行业的高质量、高效率的自动化装配需求,提出一种直升机机身总装自动钻铆系统。
对直升机机身总装自动钻铆系统的功能、结构及关键技术进行了详细说明,此项研究系统可有效缩短直升机的研制周期、降低成本和提高竞争能力。
关键词: 直升机;自动钻铆系统;数字化定位工装;圆弧导轨;末端执行器Research on Application of Automatic Drill-Riveting Technology in theHelicopter Fuselage AssemblyCHENG Tao, WEI Chao, XIAO Qingdong(A VIC Beijing Aeronautical Manufacturing Technology Research Institute, Beijing 100024, China)[ABSTRACT] For the high quality and high efficiency requirement of helicopter assembly industry, automatic drill-riveting of the helicopter fuselage assembly was presented. The function, structure and key technique of the system were illustrated in detail . The automatic drill-riveting system can shorten the development cycle, reduce the cost and improve the competition ability in the helicopter assembly.Keywords: Helicopter; Automatic drill-riveting system; Digital positioning tooling; Arc guide rail; End-effector DOI:10.16080/j.issn1671-833x.2017.09.084过程中是最费时费力的,长期以来一直困扰着制造业的发展,严重影响了直升机的研制周期[3]。
自动钻铆技术的应用和无头铆钉安装
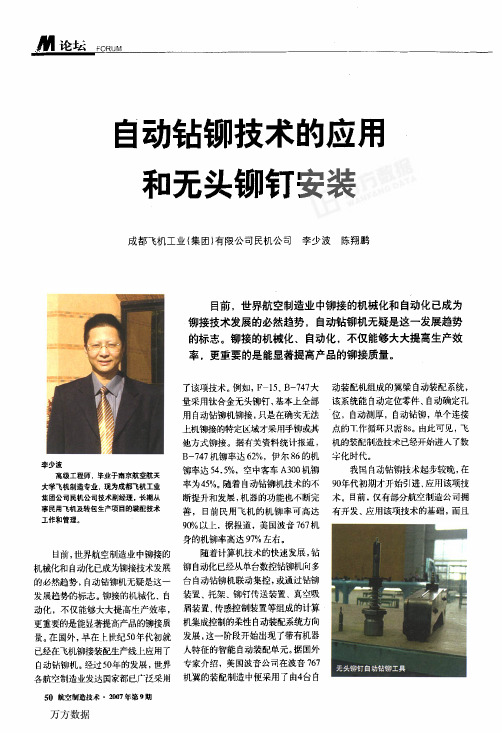
小,这样易于填满埋头窝,保证密封 性能和干涉配合均氨(2)可以减少压 铆力,如果压铆力太大,铆钉容易出 现裂纹,且易引起工件变形。
无头铆钉由于其铆接过程的特殊 性和复杂性,技术标准极其严格,用 自动钻铆机来安装无头铆钉是最佳的
821±1.
度
无头铆钉制孔连接示意图 选择。
设备情况
本次试验件的紧固件安装采用自 动钻铆机,自动钻铆机由机械、液压、 电气三大部分组成。该设备具有4个 工作头:钻孔工作头、铣切工作头、 密封工作头和铆接工作头。每个工作 头都可以通过操作台单独设置程序进 行循环周期运行。其循环工作周期有 6个,即:钻孔周期、铆接周期、铣 切周期、HI—LOK周期、HUcK周 期、振动周期。每个周期之间也可通 过操作台设置复合程序进行复合周期 运行。该设备具备无头铆钉铆接功能 以及相关的工具和配件。
试验过程
(1)按技术标准zs5076260A中 的参数要求,选择与产品材料、厚度 相同的试片进行钻孔试验。无头铆钉 与钉孔的配合公差要求比普通铆接严 得多,钉杆与孔的间隙仅为O.03~ O.15mm,当间隙超过0.25mm时,就 难以形成较好的干涉配合;钉孔表面 粗糙度应比普通铆接好;孔壁容许的 划伤深度为O.04mm,在接近零件表 面处不允许有划伤,这些划伤虽然不
在产品钻孔铆接过程中,自动钻 铆机可一次完成夹紧、钻孔一锪窝、 去毛刺、密封、送钉、插入和铆接等 工序。以上各工序的加工参数都可以 通过操作面板精确设置,由于设备带 有较高精度的钻孔动力头,能钻出较 高精度的孔,锪窝的调节深度和窝深 重复精度均可控制在±0.0005英寸 (土0.0127mm)范围内。加之设备由
影响干涉量,但裂纹会降低疲劳寿命 和气密性能。
根据以上要求,通过对自动钻铆 机的钻头转速、锪窝深度、进刀速度 等参数的反复调节和钻孔试验,用 82—30一(8)一sR窝径量规测量制孔质 量,通过反复调试获得最佳的工艺参 数。
自动钻铆技术在波音737尾段项目中的应用
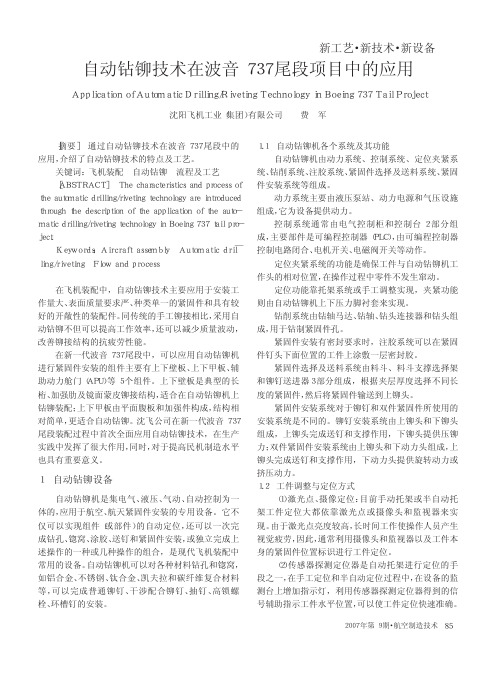
0.1 0.2 0.2 0.1 10.4 8.8 3.2 7.2 0.360 0.495 0.410 0.135
润滑系统压力 / 105Pa D
孔壁划伤长度 / mm
1 自动钻铆设备
自动钻铆机是集电气、液压、气动、自动控制为一 体的,应用于航空、航天紧固件安装的专用设备。它不 仅可以实现组件(或部件)的自动定位,还可以一次完 成钻孔、锪窝、涂胶、送钉和紧固件安装,或独立完成上 述操作的一种或几种操作的组合,是现代飞机装配中 常用的设备。自动钻铆机可以对各种材料钻孔和锪窝, 如铝合金、不锈钢、钛合金、凯夫拉和碳纤维复合材料 等,可以完成普通铆钉、干涉配合铆钉、抽钉、高锁螺 栓、环槽钉的安装。
2.2 自动钻铆机加工工艺参数设计 影响自动钻铆机加工质量的关键是各种加工工艺
参数的设定。在铆接工序,影响不同直径的铆钉镦头大 小、镦头高度等的主要因素是压铆力,压铆力与镦头成 形的关系基本呈线性关系,所以在这里主要讨论影响 制孔和锪窝的工艺参数。
影响自动钻铆机制孔质量的因素相对较多,包括 钻轴转速、钻轴进给量、夹紧力、钻头润滑压力等,同时 各个因素的变化范围又相对较大,本课题用正交试验 方法来确定工艺参数。 2.2.1 试验方法和过程
表 2 自动钻铆时孔和锪窝质量指标
要 求 孔壁划伤长度 / mm
合格要求
≤0.2
较高要求 越小越好
锪窝表面粗糙度 Ra /μm
3.2 越小越好
毛刺高度 / mm
≤0.127 越小越好
表 3 试验因素及水平
水平
因
素
转速 / 进给量 / 夹紧力 / (r·min-1) (mm·min-1) N
自动钻铆
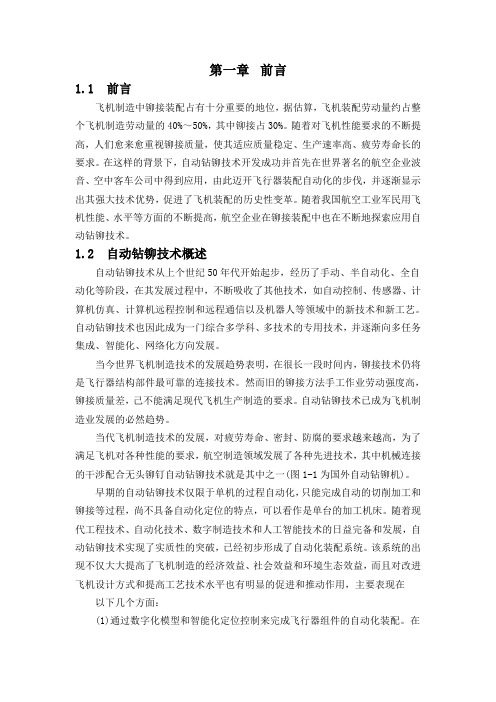
第一章前言1.1 前言飞机制造中铆接装配占有十分重要的地位,据估算,飞机装配劳动量约占整个飞机制造劳动量的40%~50%,其中铆接占30%。
随着对飞机性能要求的不断提高,人们愈来愈重视铆接质量,使其适应质量稳定、生产速率高、疲劳寿命长的要求。
在这样的背景下,自动钻铆技术开发成功并首先在世界著名的航空企业波音、空中客车公司中得到应用,由此迈开飞行器装配自动化的步伐,并逐渐显示出其强大技术优势,促进了飞机装配的历史性变革。
随着我国航空工业军民用飞机性能、水平等方面的不断提高,航空企业在铆接装配中也在不断地探索应用自动钻铆技术。
1.2 自动钻铆技术概述自动钻铆技术从上个世纪50年代开始起步,经历了手动、半自动化、全自动化等阶段,在其发展过程中,不断吸收了其他技术,如自动控制、传感器、计算机仿真、计算机远程控制和远程通信以及机器人等领域中的新技术和新工艺。
自动钻铆技术也因此成为一门综合多学科、多技术的专用技术,并逐渐向多任务集成、智能化、网络化方向发展。
当今世界飞机制造技术的发展趋势表明,在很长一段时间内,铆接技术仍将是飞行器结构部件最可靠的连接技术。
然而旧的铆接方法手工作业劳动强度高,铆接质量差,己不能满足现代飞机生产制造的要求。
自动钻铆技术已成为飞机制造业发展的必然趋势。
当代飞机制造技术的发展,对疲劳寿命、密封、防腐的要求越来越高,为了满足飞机对各种性能的要求,航空制造领域发展了各种先进技术,其中机械连接的干涉配合无头铆钉自动钻铆技术就是其中之一(图1-1为国外自动钻铆机)。
早期的自动钻铆技术仅限于单机的过程自动化,只能完成自动的切削加工和铆接等过程,尚不具备自动化定位的特点,可以看作是单台的加工机床。
随着现代工程技术、自动化技术、数字制造技术和人工智能技术的日益完备和发展,自动钻铆技术实现了实质性的突破,已经初步形成了自动化装配系统。
该系统的出现不仅大大提高了飞机制造的经济效益、社会效益和环境生态效益,而且对改进飞机设计方式和提高工艺技术水平也有明显的促进和推动作用,主要表现在以下几个方面:(1)通过数字化模型和智能化定位控制来完成飞行器组件的自动化装配。
数字化自动钻铆系统在飞机制造中的应用
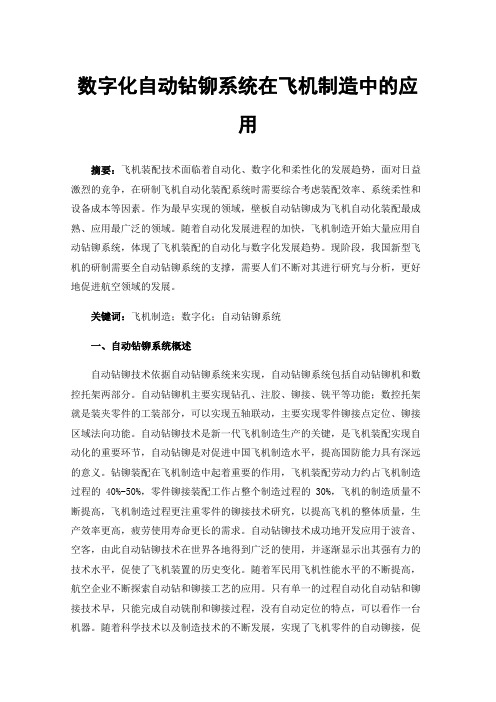
数字化自动钻铆系统在飞机制造中的应用摘要:飞机装配技术面临着自动化、数字化和柔性化的发展趋势,面对日益激烈的竞争,在研制飞机自动化装配系统时需要综合考虑装配效率、系统柔性和设备成本等因素。
作为最早实现的领域,壁板自动钻铆成为飞机自动化装配最成熟、应用最广泛的领域。
随着自动化发展进程的加快,飞机制造开始大量应用自动钻铆系统,体现了飞机装配的自动化与数字化发展趋势。
现阶段,我国新型飞机的研制需要全自动钻铆系统的支撑,需要人们不断对其进行研究与分析,更好地促进航空领域的发展。
关键词:飞机制造;数字化;自动钻铆系统一、自动钻铆系统概述自动钻铆技术依据自动钻铆系统来实现,自动钻铆系统包括自动钻铆机和数控托架两部分。
自动钻铆机主要实现钻孔、注胶、铆接、铣平等功能;数控托架就是装夹零件的工装部分,可以实现五轴联动,主要实现零件铆接点定位、铆接区域法向功能。
自动钻铆技术是新一代飞机制造生产的关键,是飞机装配实现自动化的重要环节,自动钻铆是对促进中国飞机制造水平,提高国防能力具有深远的意义。
钻铆装配在飞机制造中起着重要的作用,飞机装配劳动力约占飞机制造过程的 40%-50%,零件铆接装配工作占整个制造过程的 30%,飞机的制造质量不断提高,飞机制造过程更注重零件的铆接技术研究,以提高飞机的整体质量,生产效率更高,疲劳使用寿命更长的需求。
自动钻铆技术成功地开发应用于波音、空客,由此自动钻铆技术在世界各地得到广泛的使用,并逐渐显示出其强有力的技术水平,促使了飞机装置的历史变化。
随着军民用飞机性能水平的不断提高,航空企业不断探索自动钻和铆接工艺的应用。
只有单一的过程自动化自动钻和铆接技术早,只能完成自动铣削和铆接过程,没有自动定位的特点,可以看作一台机器。
随着科学技术以及制造技术的不断发展,实现了飞机零件的自动铆接,促使了飞机自动装配技术的实现。
飞机自动装配的实现,不单极大提高了飞机产业的三大效益,对提高飞机制造设计和改进工艺技术程度也有重要推动作用。
飞机自动钻铆技术研究现状及其关键技术

飞机自动钻铆技术研究现状及其关键技术发布时间:2022-11-07T05:47:54.026Z 来源:《中国科技信息》2022年第13期7月作者:周华[导读] 随着计算机、信息和自动化技术的发展,数字飞机的组装技术迅速发展。
数字装配技术被周华中航飞机股份有限公司陕西西安 710089摘要:随着计算机、信息和自动化技术的发展,数字飞机的组装技术迅速发展。
数字装配技术被空客、波音等大型飞机制造商平等使用。
我国大型飞机研究项目的实施将加快数字飞机的装配。
自动钻铆技术是数字装配技术不可或缺的组成部分,可以大大提高飞机装配效率,有效保证装配质量,提高疲劳强度。
关键词:航空壁板;自动钻铆;高精度定位随着现代飞机制造技术的发展,对飞机性能、密封性和耐腐蚀性的要求越来越高。
为了满足飞机的性能要求,航天工业开发了一系列先进技术,如机械连接与自动钻铆的应用。
几十年来国外铆接装配技术的应用表明,自动自动钻铆机的效率至少是手工铆接的十倍,节省了安装成本,改善了工作条件。
最重要的是保证安装质量,大大减少人为缺陷。
自动钻铆机的使用是目前提高飞行效率的主要技术措施之一。
一、自动钻铆技术的发展现状1.设备开发。
针对不同类型的飞机设计,开发了各种数控自动钻铆系统,不仅壁板铆接,而且肋、框、梁、翼面、前缘铆接。
因此,自动钻铆系统的作用范围明显扩大,铆接整体性能得到显着提高。
2.自动安装紧固件。
添加附件后,可自动安装两件型紧固件(槽、高锁、锥形螺栓),从而使无头铆钉铆接干涉配合。
因此,铆接结构的疲劳可以增加5至6倍,改进油箱的密封铆接至关重要。
3.自动钻铆。
整个过程是通过数字程序编程的,自动钻铆程序是一个连续的过程,用于夹紧、钻孔、锪窝、注胶、铣平。
机床配有高速旋转轴,可同时钻至0.005mm钻孔精度高,埋头窝深度精确控制在±0.0lmm范围内。
此外,机床还通过数字控制系统和自动化化工装夹具。
无论人为影响因素如何,铆钉镦头的高度都是恒定的。
铆钉的作用及使用方法【详细】
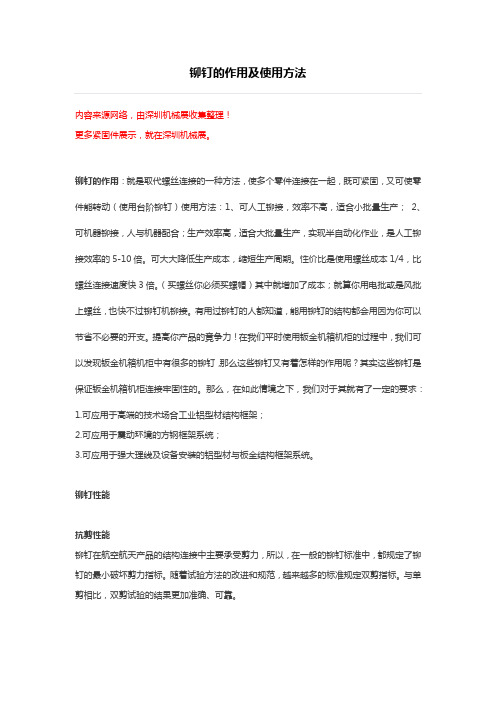
内容来源网络,由深圳机械展收集整理!更多紧固件展示,就在深圳机械展。
铆钉的作用:就是取代螺丝连接的一种方法,使多个零件连接在一起,既可紧固,又可使零件能转动(使用台阶铆钉)使用方法:1、可人工铆接,效率不高,适合小批量生产;2、可机器铆接,人与机器配合;生产效率高,适合大批量生产,实现半自动化作业,是人工铆接效率的5-10倍。
可大大降低生产成本,缩短生产周期。
性价比是使用螺丝成本1/4,比螺丝连接速度快3倍。
(买螺丝你必须买螺帽)其中就增加了成本;就算你用电批或是风批上螺丝,也快不过铆钉机铆接。
有用过铆钉的人都知道,能用铆钉的结构都会用因为你可以节省不必要的开支。
提高你产品的竟争力!在我们平时使用钣金机箱机柜的过程中,我们可以发现钣金机箱机柜中有很多的铆钉,那么这些铆钉又有着怎样的作用呢?其实这些铆钉是保证钣金机箱机柜连接牢固性的。
那么,在如此情境之下,我们对于其就有了一定的要求:1.可应用于高端的技术场合工业铝型材结构框架;2.可应用于震动环境的方钢框架系统;3.可应用于强大理线及设备安装的铝型材与板金结构框架系统。
铆钉性能抗剪性能铆钉在航空航天产品的结构连接中主要承受剪力,所以,在一般的铆钉标准中,都规定了铆钉的最小破坏剪力指标。
随着试验方法的改进和规范,越来越多的标准规定双剪指标。
与单剪相比,双剪试验的结果更加准确、可靠。
铆接性能铆接性是指铆接完成后铆成头的成型要求。
铆成头成型的好坏,直接影响铆接质量。
因此,在国内航空航天的铆接标准中对铆钉的铆接性都有严格要求,而一般用途的普通铆钉尚没有规定铆接性要求。
铆接性和强度是两项互相矛盾的指标,强度越高,铆接性越差。
一般情况下,铆接后铆成头的高度为0.35d-0.4d,铆成头直径在1.4d以上。
同时,对铆成头上出现的裂纹有严格要求,裂纹只允许在铆城投柱面上出现,不能贯穿至顶面,总数不超过3条,宽度与深度不超过0.07mm。
铆钉的用途和品种简介半圆头铆钉主要用于随较大横向载荷的铆接场合,应用最广。
铆钉铆接工艺的优化
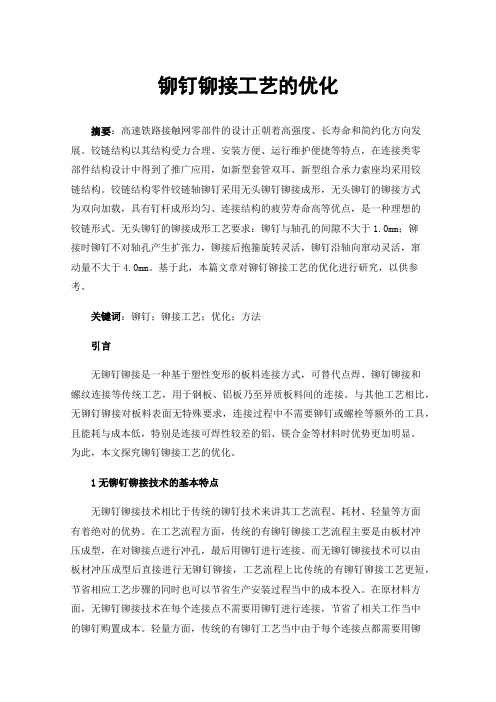
铆钉铆接工艺的优化摘要:高速铁路接触网零部件的设计正朝着高强度、长寿命和简约化方向发展。
铰链结构以其结构受力合理、安装方便、运行维护便捷等特点,在连接类零部件结构设计中得到了推广应用,如新型套管双耳、新型组合承力索座均采用铰链结构。
铰链结构零件铰链轴铆钉采用无头铆钉铆接成形,无头铆钉的铆接方式为双向加载,具有钉杆成形均匀、连接结构的疲劳寿命高等优点,是一种理想的铰链形式。
无头铆钉的铆接成形工艺要求:铆钉与轴孔的间隙不大于1.0mm;铆接时铆钉不对轴孔产生扩张力,铆接后抱箍旋转灵活,铆钉沿轴向窜动灵活,窜动量不大于4.0mm。
基于此,本篇文章对铆钉铆接工艺的优化进行研究,以供参考。
关键词:铆钉;铆接工艺;优化;方法引言无铆钉铆接是一种基于塑性变形的板料连接方式,可替代点焊、铆钉铆接和螺纹连接等传统工艺,用于钢板、铝板乃至异质板料间的连接。
与其他工艺相比,无铆钉铆接对板料表面无特殊要求,连接过程中不需要铆钉或螺栓等额外的工具,且能耗与成本低,特别是连接可焊性较差的铝、镁合金等材料时优势更加明显。
为此,本文探究铆钉铆接工艺的优化。
1无铆钉铆接技术的基本特点无铆钉铆接技术相比于传统的铆钉技术来讲其工艺流程、耗材、轻量等方面有着绝对的优势。
在工艺流程方面,传统的有铆钉铆接工艺流程主要是由板材冲压成型,在对铆接点进行冲孔,最后用铆钉进行连接。
而无铆钉铆接技术可以由板材冲压成型后直接进行无铆钉铆接,工艺流程上比传统的有铆钉铆接工艺更短,节省相应工艺步骤的同时也可以节省生产安装过程当中的成本投入。
在原材料方面,无铆钉铆接技术在每个连接点不需要用铆钉进行连接,节省了相关工作当中的铆钉购置成本。
轻量方面,传统的有铆钉工艺当中由于每个连接点都需要用铆钉进行连接,相应的工作当中车身整体质量较大,而无铆钉铆接技术则很大程度上减少了车身的重量,其本身不需要铆钉进行连接,车身的整体质量得到有效的控制。
疲劳强度方面,这种无铆钉铆接技术主要是通过对材料进行挤压,让金属流动形成需要的形体。
大飞机何以能安全翱翔?壁板无头铆钉干涉连接技术探析

大飞机何以能安全翱翔?壁板无头铆钉干涉连接技术探析大型飞机通常是指起飞总质量超过100t的军民用大型运输机和150座级以上的大型客机,具有尺寸大、高可靠性及长寿命(大型客机飞行寿命为90000h)等特点。
随着我国大型飞机设计与制造技术的发展,飞机的装配质量也有了新的提高。
为保证飞机轻量化、长寿命、高可靠性和气密、油密性的要求,无头铆钉、高锁螺栓和冠头铆钉等新型连接方式在大型飞机装配中得到了广泛的应用。
由于干涉配合铆接的铆钉能紧密地充满钉窝及钉孔,并使钉孔均匀而适量地胀大,形成钉杆对钉孔的“支撑效应”,所以干涉配合铆接在疲劳寿命和密封性方面优于普通铆接,大型客机C919和支线客机ARJ21在机翼壁板铆接装配中大量使用无头铆钉干涉连接,以满足连接质量要求。
随着对飞机制造效率及精度需求的不断提高,以自动钻铆系统为代表的自动化连接设备在壁板装配中得到了大量应用,尤其在无头铆钉干涉连接过程中必须尽可能使用自动化设备。
本文主要从无头铆钉干涉连接技术和设备应用两方面展开讨论。
无头铆钉连接工艺流程无头铆钉是一种没有铆钉头的实心圆杆干涉铆钉,具有以下优点:(1)铆接后沿铆钉杆全长可形成较均匀的干涉配合,成倍地提高连接结构的疲劳寿命。
(2)采用无头铆钉干涉配合的铆接,能够可靠地保证铆钉自身的密封性。
无头铆钉安装过程必须依靠自动化安装设备,才能符合设计技术要求,实现壁板稳定的、高质量的连接。
对单个铆钉连接过程而言,其主要工艺流程包括定位、夹紧、制孔、锪窝、放钉、铆接和铣平,如图1所示。
图1 无头铆钉自动钻铆安装工艺流程无头铆钉干涉连接技术无头铆钉连接过程中不仅铆钉镦粗变形,被连接件也因钉杆膨胀和镦头挤压产生不同程度的变形,同时,被连接件多为薄壁件,刚度小、易变形,大量的铆钉连接使薄壁件产生更加复杂的装配变形和残余应力,增加了连接结构的脆性,降低了飞机的疲劳寿命。
因此,开展无头铆钉干涉连接方面的技术研究,对大型飞机壁板的精准装配和使用寿命的提高有重要作用,其中应力应变分析是研究的基础。
数字化自动钻铆技术在飞机制造中的应用
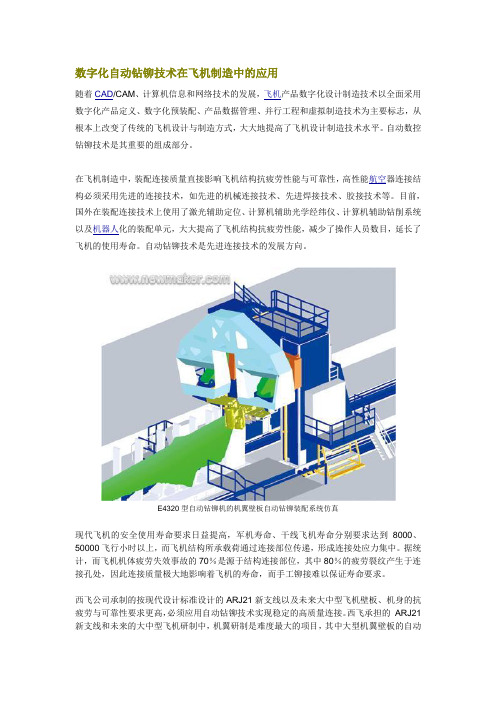
数字化自动钻铆技术在飞机制造中的应用随着CAD/CAM、计算机信息和网络技术的发展,飞机产品数字化设计制造技术以全面采用数字化产品定义、数字化预装配、产品数据管理、并行工程和虚拟制造技术为主要标志,从根本上改变了传统的飞机设计与制造方式,大大地提高了飞机设计制造技术水平。
自动数控钻铆技术是其重要的组成部分。
在飞机制造中,装配连接质量直接影响飞机结构抗疲劳性能与可靠性,高性能航空器连接结构必须采用先进的连接技术,如先进的机械连接技术、先进焊接技术、胶接技术等。
目前,国外在装配连接技术上使用了激光辅助定位、计算机辅助光学经纬仪、计算机辅助钻削系统以及机器人化的装配单元,大大提高了飞机结构抗疲劳性能,减少了操作人员数目,延长了飞机的使用寿命。
自动钻铆技术是先进连接技术的发展方向。
E4320型自动钻铆机的机翼壁板自动钻铆装配系统仿真现代飞机的安全使用寿命要求日益提高,军机寿命、干线飞机寿命分别要求达到8000、50000飞行小时以上,而飞机结构所承载荷通过连接部位传递,形成连接处应力集中。
据统计,而飞机机体疲劳失效事故的70%是源于结构连接部位,其中80%的疲劳裂纹产生于连接孔处,因此连接质量极大地影响着飞机的寿命,而手工铆接难以保证寿命要求。
西飞公司承制的按现代设计标准设计的ARJ21新支线以及未来大中型飞机壁板、机身的抗疲劳与可靠性要求更高,必须应用自动钻铆技术实现稳定的高质量连接。
西飞承担的ARJ21新支线和未来的大中型飞机研制中,机翼研制是难度最大的项目,其中大型机翼壁板的自动钻铆是决定机翼研制成败的关键。
大型机翼壁板全自动钻铆系统的研制是中国新型飞机研制的急需,也是中国一航重点突破的关键技术之一,同时也是赶超国际先进航空制造技术的一次挑战。
国内外研究应用现状自动钻铆技术从70年代起就在国外普遍采用,其发展一直未曾间断。
国外目前生产中的军、民用飞机的自动钻铆率分别达到了17%和75%以上,大量采用无头铆钉干涉配合技术,新型紧固件包括无头和冠头铆钉、钛环槽钉、高锁螺栓、锥形螺栓以及各种单面抽钉等,80%的铆接和100%的不可卸传剪螺栓连接均采用干涉配合,而且孔壁还要进行强化。
国内外自动钻铆技术的发展现状及应用

国内外自动钻铆技术的发展现状及应用西飞国际设备维修中心 楼阿莉当代飞机制造技术的发展,对疲劳寿命、密封、防腐的要求越来越高,为了满足飞机对各种性能的要求,航空制造领域发展了各种先进技术,其中机械连接技术的干涉配合无头铆钉自动钻铆技术就是其中之一。
国外铆接装配技术几十年的应用证明,采用自动钻铆机后装配效率至少比手工铆接装配提高10倍,并能节约安装成本,改善劳动条件,更主要的是能够确保安装质量,大大减少人为因素造成的缺陷。
现在采用自动钻铆机已成为改善飞机性能的主要工艺措施之一。
美国是最早发展自动钻铆技术的国家,早在 50 年代初就已在飞机铆接装配生产线上应用了自动钻铆机,经过 50 多年的发展,现在世界各航空工业发达国家都已广泛采用这项技术。
自动钻铆技术主要包含以下内容:(1) 设备的研制、开发。
以不同飞机的结构为对象,发展多种型号的数控自动钻铆系统,不仅能铆接壁板,而且还可铆接各种组件,如肋、框、梁、翼面、前缘等,从而使自动钻铆系统的工作覆盖面大幅度增加,使整个飞机的铆接工作有较大的改观。
(2) 对各种干涉配合新型紧固件进行自动安装。
通过增加附件,可以对两件型紧固件进行自动安装,如环槽钉、高锁螺栓、锥形螺栓等,也可对无头铆钉进行干涉配合铆接,从而提高铆接结构疲劳寿命5~6倍,对提高飞机整体油箱的密封铆接质量有重大意义。
(3) 自动钻铆工艺。
结构铆接的整个过程通过预先编程全部由CNC程序控制,自动钻铆工艺是在一台设备上一次性地连续完成夹紧、钻孔、锪窝、注胶、放铆、铣平等工序。
由于机床带有高速、高精度的转削主轴头,一次进给即能钻出0.005mm以内高精度的孔,同时埋头窝的深度也可精确控制在±0.01mm以内,再加上机床由数控系统控制各轴运动,并采用精密自动化工装夹具,使得铆钉镦头高度保持一致,不受人为因素的影响。
所有这些因素均使钉杆在孔中充填质量大为改善,从而有利于提高细节疲劳强度许用值。
此外,由于钻孔时铆接件处在高的夹紧力下,层间不会产生毛刺和进入切削,可以减小疲劳载荷下发生磨蚀损伤的程度,这些均有利于提高接头的疲劳强度。
飞机自动钻铆技术研究现状及其关键技术
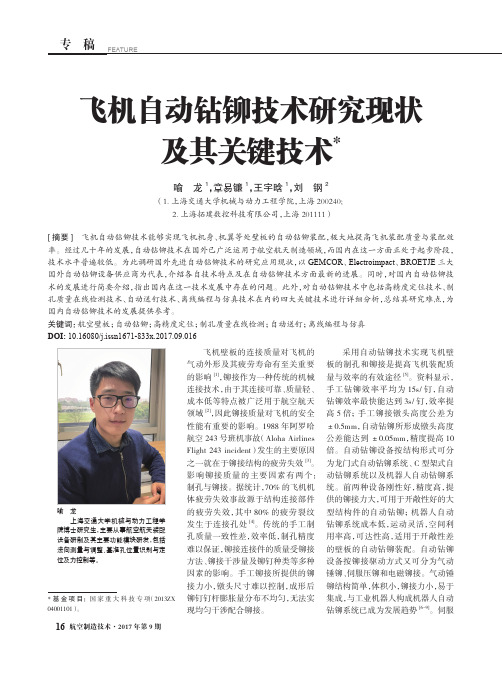
连接技术,由于其连接可靠、质量轻、 手工钻铆效率平均为 15s/ 钉,自动
成本低等特点被广泛用于航空航天 钻铆效率最快能达到 3s/ 钉,效率提 领域 [2],因此铆接质量对飞机的安全 高 5 倍;手工铆接镦头高度公差为
性能有重要的影响。1988 年阿罗哈 ±0.5mm,自动钻铆所形成镦头高度
航空 243 号班机事故(Aloha Airlines 公差能达到 ±0.05mm,精度提高 10
专稿 FEATURE
飞机自动钻铆技术研究现状 及其关键技术*
喻 龙 1,章易镰 1,王宇晗 1,刘 钢 2
(1. 上海交通大学机械与动力工程学院,上海 200240; 2. 上海拓璞数控科技有限公司,上海 201111)
[ 摘要 ] 飞机自动钻铆技术能够实现飞机机身、机翼等处壁板的自动钻铆装配,极大地提高飞机装配质量与装配效 率。经过几十年的发展,自动钻铆技术在国外已广泛运用于航空航天制造领域,而国内在这一方面正处于起步阶段, 技术水平普遍较低。为此调研国外先进自动钻铆技术的研究应用现状,以 GEMCOR、Electroimpact、BROETJE 三大 国外自动钻铆设备供应商为代表,介绍各自技术特点及在自动钻铆技术方面最新的进展。同时,对国内自动钻铆技 术的发展进行简要介绍,指出国内在这一技术发展中存在的问题。此外,对自动钻铆技术中包括高精度定位技术、制 孔质量在线检测技术、自动送钉技术、离线编程与仿真技术在内的四大关键技术进行详细分析,总结其研究难点,为 国内自动钻铆技术的发展提供参考。 关键词:航空壁板;自动钻铆;高精度定位;制孔质量在线检测;自动送钉;离线编程与仿真 DOI: 10.16080/j.issn1671-833x.2017.09.016
16 航空制造技术·2017 年第 9 期
自动钻铆技术的应用和无头铆钉安装
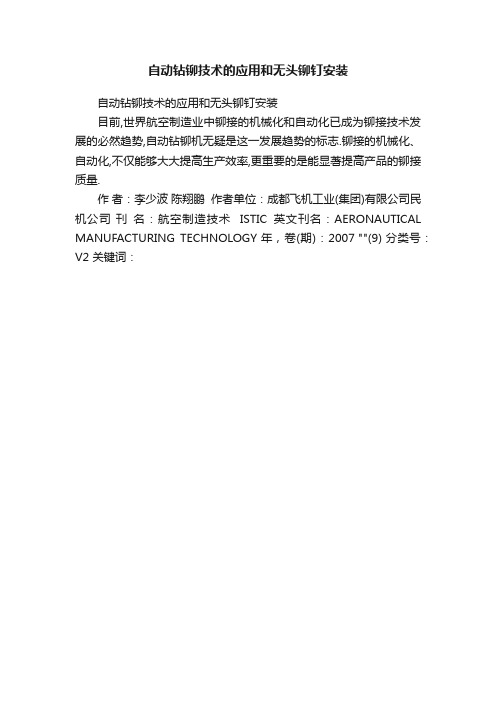
自动钻铆技术的应用和无头铆钉安装
自动钻铆术的应用和无头铆钉安装
目前,世界航空制造业中铆接的机械化和自动化已成为铆接技术发展的必然趋势,自动钻铆机无疑是这一发展趋势的标志.铆接的机械化、自动化,不仅能够大大提高生产效率,更重要的是能显著提高产品的铆接质量.
作 者:李少波 陈翔鹏 作者单位:成都飞机工业(集团)有限公司民机公司 刊 名:航空制造技术 ISTIC英文刊名:AERONAUTICAL MANUFACTURING TECHNOLOGY 年,卷(期):2007 ""(9) 分类号:V2 关键词:
- 1、下载文档前请自行甄别文档内容的完整性,平台不提供额外的编辑、内容补充、找答案等附加服务。
- 2、"仅部分预览"的文档,不可在线预览部分如存在完整性等问题,可反馈申请退款(可完整预览的文档不适用该条件!)。
- 3、如文档侵犯您的权益,请联系客服反馈,我们会尽快为您处理(人工客服工作时间:9:00-18:30)。
FORUM
航空专用设备
Special Equipment for Aviation Industry
航空制造技术2007年第9期
在装配生产中也只是部分应用,使用面还不是很广泛,铆接结构的机铆率还不到30%。
中国一航成都飞机工业(集团)有限公司,早在1993年就开始正式引进自动钻铆机,通过多年艰难摸索和不懈努力,在自动钻铆技术的开发和应用方面取得了长足的进步,也积累了不少经验。
从1999年至今,已经先后在民机转包生产线上顺利完成了B-757飞机垂平尾蒙皮壁板、大梁组件以及B-757飞机机身48段中小型双曲面蒙皮壁板的自动钻铆,工艺和质量控制均获得了美方的认证,产品的加工质量和生产能力也得到客户的好评。
随着国内大飞机项目的启动,一些装配工艺技术难题的解决已迫在眉睫,无头铆钉的自动钻铆技术就是其中之一。
凭借在自动钻铆技术方面的实践经验和相对的比较优势,一航成飞在国内众多的飞机制造工厂中被挑选出来进行ARJ21机翼无头铆钉自动钻铆试验件的加工制造。
但无头铆
钉的自动钻铆对于成飞公司来说也是
一项全新的拓展应用技术,在国内尚无先例,具有较大的难度。
1 产品结构特点
此项试验件是机翼壁板典型结
构,由蒙皮和Z字形长桁组成,结构简单,适合进行自动
钻铆,所采用的连接件为NAS1321AD8E无头铆钉,试验件要用于结构强度和疲劳试验。
由于此前国内尚无无头铆钉自动钻铆的先例,因此,这是此次试验的重点和难点。
2 连接件的特点
无头铆钉是一种没有铆钉头的实心圆杆干涉铆钉,它具有以下优点:(1)铆接后沿铆钉杆全长可形成较均匀的干涉配合,成倍地提高连接结构的疲劳寿命;(2)采用无头铆钉干涉配合的铆接,能够可靠地保证铆钉自身的密封性。
无头铆钉的埋头窝制成82°和 30°两个锥度,采用这种形状的好处是:(1)既能保证铆钉具有一定的连接强度,埋头窝的锥度又比较
小,这样易于填满埋头窝,保证密封性能和干涉配合均匀;(2)可以减少压铆力,如果压铆力太大,铆钉容易出现裂纹,且易引起工件变形。
无头铆钉由于其铆接过程的特殊性和复杂性,技术标准极其严格,用自动钻铆机来安装无头铆钉是最佳的
选择。
本次试验件的紧固件安装采用自
动钻铆机,自动钻铆机由机械、液压、电气三大部分组成。
该设备具有4个工作头:钻孔工作头、铣切工作头、密封工作头和铆接工作头。
每个工作头都可以通过操作台单独设置程序进行循环周期运行。
其循环工作周期有6个,即:钻孔周期、铆接周期、铣切周期、HI-LOK周期、HUCK周期、振动周期。
每个周期之间也可通过操作台设置复合程序进行复合周期运行。
该设备具备无头铆钉铆接功能以及相关的工具和配件。
在产品钻孔铆接过程中,自动钻
铆机可一次完成夹紧、钻孔-锪窝、去毛刺、密封、送钉、插入和铆接等工序。
以上各工序的加工参数都可以通过操作面板精确设置,由于设备带有较高精度的钻孔动力头,能钻出较高精度的孔,锪窝的调节深度和窝深重复精度均可控制在±0.0005英寸(±0.0127mm)范围内。
加之设备由
51
设备情况
工艺分析和准备
无头铆钉制孔连接示意图
82°
±1°30°±1°孔径
锪窝深度
板厚
C
机械铣平
铆成头无头铆钉
倒角.010
FORUM。