自动钻铆
《2024年度一种3自由度自动钻铆机构的运动学分析与优化设计》范文

《一种3自由度自动钻铆机构的运动学分析与优化设计》篇一一、引言随着制造业的飞速发展,对于机械装置的性能与精度的要求不断提高。
3自由度自动钻铆机构作为一种广泛应用于航空航天等高精度加工领域的关键设备,其性能与稳定性的重要性不言而喻。
本文将对一种3自由度自动钻铆机构的运动学进行分析,并对其设计进行优化,以提高其工作效率和精度。
二、3自由度自动钻铆机构概述3自由度自动钻铆机构主要由驱动系统、执行机构、传感器等部分组成。
该机构具有沿X轴、Y轴和Z轴的移动能力,能够实现对工件的精确定位和钻铆操作。
该机构广泛应用于航空航天、汽车制造等领域,具有较高的加工精度和效率。
三、运动学分析1. 坐标系建立为了便于分析和计算,首先建立笛卡尔坐标系。
原点O设定为机构初始位置,X轴、Y轴和Z轴分别代表机构的三个移动方向。
2. 运动学模型建立根据机构的运动特点,建立相应的运动学模型。
该模型应包括机构的各个部件的尺寸、位置、速度和加速度等参数。
通过该模型,可以分析机构的运动轨迹、速度和加速度等运动特性。
3. 运动学仿真与分析利用运动学仿真软件对机构进行仿真分析。
通过输入机构的各项参数,可以得到机构在各个方向上的运动轨迹、速度和加速度等数据。
通过对这些数据的分析,可以评估机构的性能和稳定性。
四、优化设计1. 设计目标与约束条件根据实际需求,确定优化设计的目标。
例如,提高机构的加工精度、降低能耗、提高工作效率等。
同时,需要考虑机构的尺寸、重量、成本等约束条件。
2. 优化算法选择根据设计目标和约束条件,选择合适的优化算法。
例如,遗传算法、粒子群算法、模拟退火算法等。
这些算法可以通过搜索空间中的最优解来提高机构的性能。
3. 优化设计实施利用优化算法对机构进行优化设计。
通过调整机构的尺寸、形状、材料等参数,使机构达到最优的性能。
在优化过程中,需要不断进行仿真分析和实验验证,以确保设计的可行性和有效性。
五、实验验证与结果分析1. 实验装置与方案为了验证优化设计的有效性,搭建实验装置并进行实验。
飞机装配自动钻铆技术研究与分析
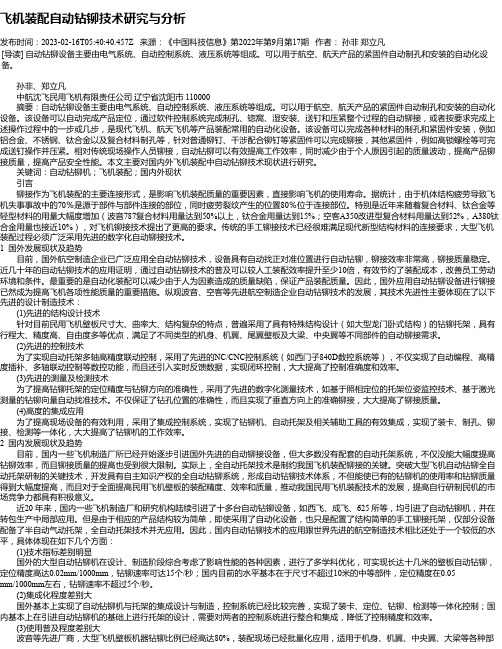
飞机装配自动钻铆技术研究与分析发布时间:2023-02-16T05:40:40.457Z 来源:《中国科技信息》第2022年第9月第17期作者:孙非郑立凡[导读] 自动钻铆设备主要由电气系统、自动控制系统、液压系统等组成。
可以用于航空、航天产品的紧固件自动制孔和安装的自动化设备。
孙非、郑立凡中航沈飞民用飞机有限责任公司辽宁省沈阳市 110000摘要:自动钻铆设备主要由电气系统、自动控制系统、液压系统等组成。
可以用于航空、航天产品的紧固件自动制孔和安装的自动化设备。
该设备可以自动完成产品定位,通过软件控制系统完成制孔、锪窩、湿安装、送钉和压紧整个过程的自动铆接,或者按要求完成上述操作过程中的一步或几步,是现代飞机、航天飞机等产品装配常用的自动化设备。
该设备可以完成各种材料的制孔和紧固件安装,例如铝合金、不锈钢、钛合金以及复合材料制孔等,针对普通铆钉、干涉配合铆钉等紧固件可以完成铆接,其他紧固件,例如高锁螺栓等可完成送钉操作并压紧。
相对传统现场操作人员铆接,自动钻铆可以有效提高工作效率,同时减少由于个人原因引起的质量波动,提高产品铆接质量,提高产品安全性能。
本文主要对国内外飞机装配中自动钻铆技术现状进行研究。
关键词:自动钻铆机;飞机装配;国内外现状引言铆接作为飞机装配的主要连接形式,是影响飞机装配质量的重要因素,直接影响飞机的使用寿命。
据统计,由于机体结构疲劳导致飞机失事事故中的70%是源于部件与部件连接的部位,同时疲劳裂纹产生的位置80%位于连接部位。
特别是近年来随着复合材料、钛合金等轻型材料的用量大幅度增加(波音787复合材料用量达到50%以上,钛合金用量达到15%;空客A350改进型复合材料用量达到52%,A380钛合金用量也接近10%),对飞机铆接技术提出了更高的要求。
传统的手工铆接技术已经很难满足现代新型结构材料的连接要求,大型飞机装配过程必须广泛采用先进的数字化自动铆接技术。
1 国外发展现状及趋势目前,国外航空制造企业已广泛应用全自动钻铆技术,设备具有自动找正对准位置进行自动钻铆,铆接效率非常高,铆接质量稳定。
《2024年一种3自由度自动钻铆机构的运动学分析与优化设计》范文
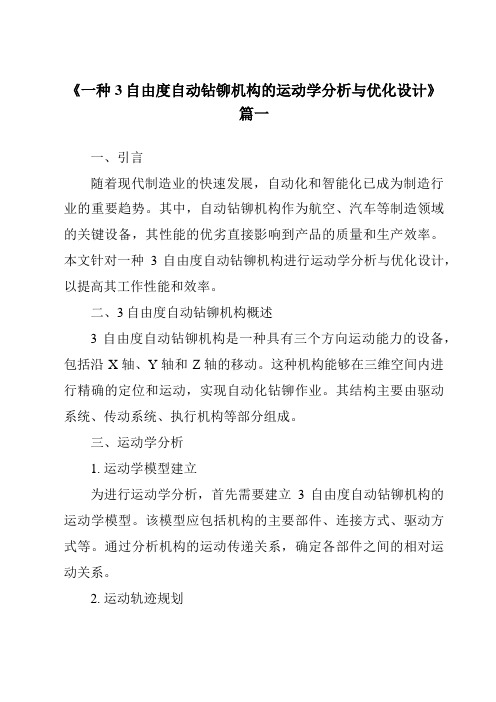
《一种3自由度自动钻铆机构的运动学分析与优化设计》篇一一、引言随着现代制造业的快速发展,自动化和智能化已成为制造行业的重要趋势。
其中,自动钻铆机构作为航空、汽车等制造领域的关键设备,其性能的优劣直接影响到产品的质量和生产效率。
本文针对一种3自由度自动钻铆机构进行运动学分析与优化设计,以提高其工作性能和效率。
二、3自由度自动钻铆机构概述3自由度自动钻铆机构是一种具有三个方向运动能力的设备,包括沿X轴、Y轴和Z轴的移动。
这种机构能够在三维空间内进行精确的定位和运动,实现自动化钻铆作业。
其结构主要由驱动系统、传动系统、执行机构等部分组成。
三、运动学分析1. 运动学模型建立为进行运动学分析,首先需要建立3自由度自动钻铆机构的运动学模型。
该模型应包括机构的主要部件、连接方式、驱动方式等。
通过分析机构的运动传递关系,确定各部件之间的相对运动关系。
2. 运动轨迹规划运动轨迹规划是自动钻铆机构运动学分析的关键步骤。
根据实际需求,规划出机构在钻铆过程中的运动轨迹。
通过优化轨迹规划,可以提高机构的运动效率和精度。
3. 运动学仿真与分析利用计算机仿真软件对3自由度自动钻铆机构进行运动学仿真。
通过仿真分析,可以验证机构运动的可行性和稳定性,以及评估机构的性能指标。
四、优化设计1. 结构优化针对3自由度自动钻铆机构的结构进行优化设计。
通过改进机构的传动系统、驱动系统等部分,提高机构的刚度和精度。
同时,优化机构的布局和尺寸,以减小机构的体积和重量。
2. 控制策略优化为提高3自由度自动钻铆机构的控制性能,需要对其控制策略进行优化。
通过引入先进的控制算法和传感器技术,实现机构的高精度、高速度控制。
同时,优化控制系统的响应速度和稳定性,以提高机构的整体性能。
3. 工艺参数优化针对3自由度自动钻铆机构的工艺参数进行优化。
通过分析钻铆过程中的力、速度、加速度等参数,确定最优的工艺参数组合。
这有助于提高机构的钻铆效率和产品质量。
五、实验验证与结果分析为验证3自由度自动钻铆机构的运动学分析与优化设计效果,进行实际实验验证。
《一种3自由度自动钻铆机构的运动学分析与优化设计》范文

《一种3自由度自动钻铆机构的运动学分析与优化设计》篇一一、引言在当今制造业的发展趋势下,3自由度自动钻铆机构已经成为一种关键的技术装备,被广泛应用于航空航天、汽车制造和精密仪器等领域。
该机构能高效地完成精确的钻孔、攻牙以及铆接等工艺,其性能的优劣直接影响到产品的制造质量和生产效率。
因此,对3自由度自动钻铆机构的运动学分析与优化设计,显得尤为重要。
本文将通过对其运动学分析、设计方法和优化过程的研究,以实现该机构性能的优化和提升。
二、3自由度自动钻铆机构概述3自由度自动钻铆机构主要由驱动系统、导向系统、钻铆头等部分组成。
该机构具有三个方向的自由运动能力,包括X轴的平移运动、Y轴的平移运动和绕Z轴的旋转运动。
这些自由度的运动能够实现对工作区域内任意位置的精确定位和操作。
三、运动学分析3.1 运动学模型建立首先,我们根据3自由度自动钻铆机构的构造和工作原理,建立其运动学模型。
通过将机构的主要部分(如驱动系统、导向系统等)抽象为节点和连杆,我们建立了能够描述机构运动的物理模型。
在此基础上,我们可以分析机构在不同输入下的输出响应。
3.2 运动学分析方法对于3自由度自动钻铆机构的运动学分析,我们主要采用了D-H参数法。
D-H参数法是一种常用的机器人运动学分析方法,它通过定义连杆之间的相对位置和姿态,来描述机构的运动。
我们通过对机构进行分段,并定义每段的D-H参数,从而得到机构的运动方程。
四、设计方法4.1 设计原则在设计3自由度自动钻铆机构时,我们遵循了以下几点原则:一是保证机构的运动精度和稳定性;二是考虑机构的制造和装配的便捷性;三是追求机构的轻量化和高效率。
4.2 设计流程设计流程主要包括需求分析、方案制定、结构设计、运动学分析和优化等步骤。
在需求分析阶段,我们明确了机构的工作环境、任务要求和性能指标。
在方案制定阶段,我们根据需求分析的结果,提出了多种可能的机构设计方案。
在结构设计和运动学分析阶段,我们选择了最合适的方案,并对其进行了详细的设计和分析。
《一种3自由度自动钻铆机构的运动学分析与优化设计》范文

《一种3自由度自动钻铆机构的运动学分析与优化设计》篇一一、引言在现代化工业生产中,自动化和智能化的机械装备对于提高生产效率和产品质量起着至关重要的作用。
自动钻铆机构作为其中的重要组成部分,其性能和效率直接影响着整个生产线的运作。
本文旨在研究一种具有3自由度的自动钻铆机构的运动学分析与优化设计,以实现更高的工作效率和更佳的铆接质量。
二、运动学分析2.1 机构结构与工作原理该3自由度自动钻铆机构主要由驱动系统、执行机构和夹具等部分组成。
其中,执行机构是核心部分,具有三个方向的自由度,可实现空间内的任意位置和姿态调整。
该机构通过精确控制驱动系统,使执行机构按照预设的轨迹和速度进行运动,完成钻铆作业。
2.2 运动学建模为了分析该机构的运动特性,我们建立了三维运动学模型。
通过分析机构的关节运动、连杆长度等参数,确定了机构的空间位置和姿态。
同时,我们还建立了机构的动力学模型,为后续的优化设计提供了理论依据。
2.3 运动学仿真利用计算机仿真技术,我们对机构的运动过程进行了模拟。
通过分析仿真结果,我们发现机构在运动过程中存在一些不必要的振动和误差,这可能会影响钻铆的精度和效率。
因此,我们需要对机构进行优化设计。
三、优化设计3.1 设计目标为了提高机构的运动精度、工作效率和铆接质量,我们设定了以下优化目标:降低振动和误差、提高运动速度和加速度、优化机构结构以减轻重量。
3.2 优化方法为了实现上述目标,我们采用了多种优化方法。
首先,我们对机构的关节进行了优化设计,使其在运动过程中更加平稳。
其次,我们通过改进驱动系统和控制算法,提高了机构的运动速度和加速度。
此外,我们还采用了轻量化设计,减轻了机构重量,提高了其运动灵活性。
3.3 优化结果经过优化设计后,该3自由度自动钻铆机构的运动精度得到了显著提高,振动和误差明显降低。
同时,机构的工作效率也得到了提高,铆接质量得到了进一步保障。
此外,轻量化设计还降低了机构的制造成本,提高了其市场竞争力。
数字化自动钻铆系统在飞机制造中的应用
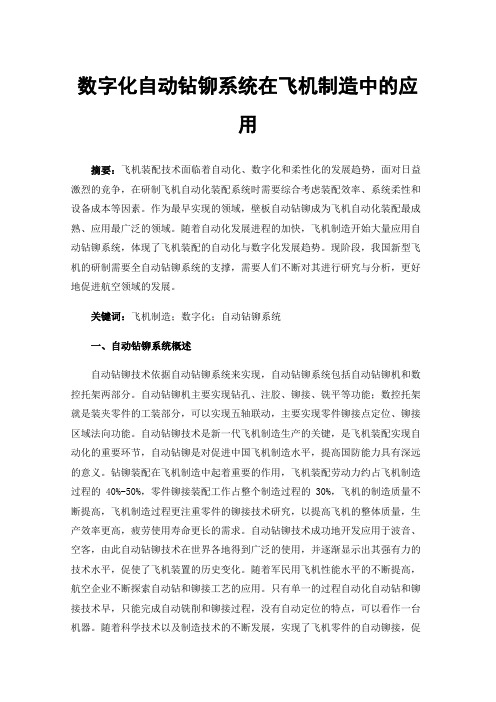
数字化自动钻铆系统在飞机制造中的应用摘要:飞机装配技术面临着自动化、数字化和柔性化的发展趋势,面对日益激烈的竞争,在研制飞机自动化装配系统时需要综合考虑装配效率、系统柔性和设备成本等因素。
作为最早实现的领域,壁板自动钻铆成为飞机自动化装配最成熟、应用最广泛的领域。
随着自动化发展进程的加快,飞机制造开始大量应用自动钻铆系统,体现了飞机装配的自动化与数字化发展趋势。
现阶段,我国新型飞机的研制需要全自动钻铆系统的支撑,需要人们不断对其进行研究与分析,更好地促进航空领域的发展。
关键词:飞机制造;数字化;自动钻铆系统一、自动钻铆系统概述自动钻铆技术依据自动钻铆系统来实现,自动钻铆系统包括自动钻铆机和数控托架两部分。
自动钻铆机主要实现钻孔、注胶、铆接、铣平等功能;数控托架就是装夹零件的工装部分,可以实现五轴联动,主要实现零件铆接点定位、铆接区域法向功能。
自动钻铆技术是新一代飞机制造生产的关键,是飞机装配实现自动化的重要环节,自动钻铆是对促进中国飞机制造水平,提高国防能力具有深远的意义。
钻铆装配在飞机制造中起着重要的作用,飞机装配劳动力约占飞机制造过程的 40%-50%,零件铆接装配工作占整个制造过程的 30%,飞机的制造质量不断提高,飞机制造过程更注重零件的铆接技术研究,以提高飞机的整体质量,生产效率更高,疲劳使用寿命更长的需求。
自动钻铆技术成功地开发应用于波音、空客,由此自动钻铆技术在世界各地得到广泛的使用,并逐渐显示出其强有力的技术水平,促使了飞机装置的历史变化。
随着军民用飞机性能水平的不断提高,航空企业不断探索自动钻和铆接工艺的应用。
只有单一的过程自动化自动钻和铆接技术早,只能完成自动铣削和铆接过程,没有自动定位的特点,可以看作一台机器。
随着科学技术以及制造技术的不断发展,实现了飞机零件的自动铆接,促使了飞机自动装配技术的实现。
飞机自动装配的实现,不单极大提高了飞机产业的三大效益,对提高飞机制造设计和改进工艺技术程度也有重要推动作用。
飞机自动钻铆技术研究现状及其关键技术

飞机自动钻铆技术研究现状及其关键技术发布时间:2022-11-07T05:47:54.026Z 来源:《中国科技信息》2022年第13期7月作者:周华[导读] 随着计算机、信息和自动化技术的发展,数字飞机的组装技术迅速发展。
数字装配技术被周华中航飞机股份有限公司陕西西安 710089摘要:随着计算机、信息和自动化技术的发展,数字飞机的组装技术迅速发展。
数字装配技术被空客、波音等大型飞机制造商平等使用。
我国大型飞机研究项目的实施将加快数字飞机的装配。
自动钻铆技术是数字装配技术不可或缺的组成部分,可以大大提高飞机装配效率,有效保证装配质量,提高疲劳强度。
关键词:航空壁板;自动钻铆;高精度定位随着现代飞机制造技术的发展,对飞机性能、密封性和耐腐蚀性的要求越来越高。
为了满足飞机的性能要求,航天工业开发了一系列先进技术,如机械连接与自动钻铆的应用。
几十年来国外铆接装配技术的应用表明,自动自动钻铆机的效率至少是手工铆接的十倍,节省了安装成本,改善了工作条件。
最重要的是保证安装质量,大大减少人为缺陷。
自动钻铆机的使用是目前提高飞行效率的主要技术措施之一。
一、自动钻铆技术的发展现状1.设备开发。
针对不同类型的飞机设计,开发了各种数控自动钻铆系统,不仅壁板铆接,而且肋、框、梁、翼面、前缘铆接。
因此,自动钻铆系统的作用范围明显扩大,铆接整体性能得到显着提高。
2.自动安装紧固件。
添加附件后,可自动安装两件型紧固件(槽、高锁、锥形螺栓),从而使无头铆钉铆接干涉配合。
因此,铆接结构的疲劳可以增加5至6倍,改进油箱的密封铆接至关重要。
3.自动钻铆。
整个过程是通过数字程序编程的,自动钻铆程序是一个连续的过程,用于夹紧、钻孔、锪窝、注胶、铣平。
机床配有高速旋转轴,可同时钻至0.005mm钻孔精度高,埋头窝深度精确控制在±0.0lmm范围内。
此外,机床还通过数字控制系统和自动化化工装夹具。
无论人为影响因素如何,铆钉镦头的高度都是恒定的。
《2024年度一种3自由度自动钻铆机构的运动学分析与优化设计》范文
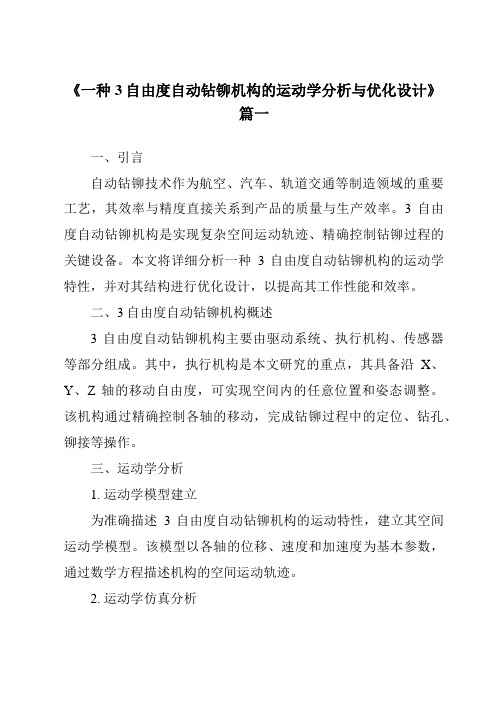
《一种3自由度自动钻铆机构的运动学分析与优化设计》篇一一、引言自动钻铆技术作为航空、汽车、轨道交通等制造领域的重要工艺,其效率与精度直接关系到产品的质量与生产效率。
3自由度自动钻铆机构是实现复杂空间运动轨迹、精确控制钻铆过程的关键设备。
本文将详细分析一种3自由度自动钻铆机构的运动学特性,并对其结构进行优化设计,以提高其工作性能和效率。
二、3自由度自动钻铆机构概述3自由度自动钻铆机构主要由驱动系统、执行机构、传感器等部分组成。
其中,执行机构是本文研究的重点,其具备沿X、Y、Z轴的移动自由度,可实现空间内的任意位置和姿态调整。
该机构通过精确控制各轴的移动,完成钻铆过程中的定位、钻孔、铆接等操作。
三、运动学分析1. 运动学模型建立为准确描述3自由度自动钻铆机构的运动特性,建立其空间运动学模型。
该模型以各轴的位移、速度和加速度为基本参数,通过数学方程描述机构的空间运动轨迹。
2. 运动学仿真分析利用专业仿真软件对3自由度自动钻铆机构的运动过程进行仿真分析。
通过模拟实际工作过程中的各种工况,分析机构的运动轨迹、速度、加速度等参数,评估机构的运动性能。
四、结构优化设计1. 设计目标与约束条件针对3自由度自动钻铆机构的实际工作需求,设定优化目标为提高工作效率、降低能耗、提高钻铆精度。
同时,考虑机构的制造、安装、维护等因素,设定一系列约束条件。
2. 结构优化方法(1)材料选择:选用高强度、轻质材料,降低机构重量,提高运动速度。
(2)驱动系统优化:采用高性能电机和控制器,提高驱动系统的响应速度和精度。
(3)执行机构优化:通过优化各轴的布局和传动方式,减小运动过程中的摩擦阻力,提高运动平稳性。
(4)传感器优化:采用高精度传感器,实时监测机构的位置、速度和加速度等参数,为精确控制提供依据。
五、实验验证与结果分析1. 实验验证为验证优化后的3自由度自动钻铆机构的性能,进行实际工况下的实验验证。
通过对比优化前后机构的工作效率、能耗、钻铆精度等参数,评估优化效果。
自动钻铆技术在大直径运载火箭筒段装配中的应用
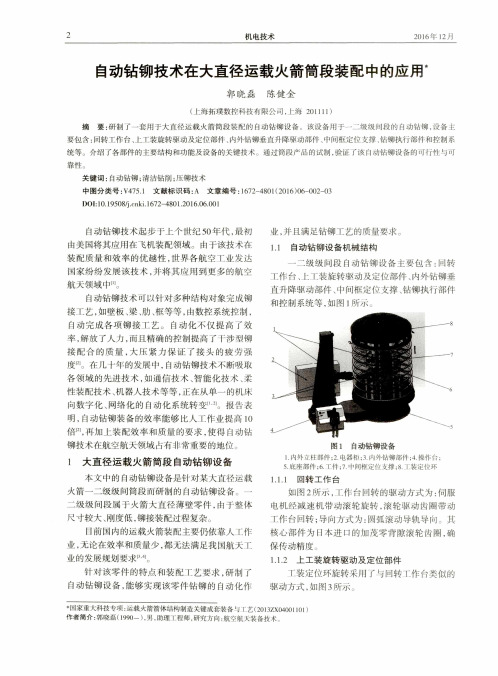
I . 内外 立柱部件; 2 . 电器 ! ; 3 . 内外钻铆部件 ; 4 . 操作台 ; 5 . 底座 部件 ; 6 . 工件 ; 7 . 中间框定化支撑 ; 8 . ‘ I . 装定化环
l 大直径运载火箭简段 自动钻铆设备
本 文 中的 自动钻 铆设 备 是针 对某 大 直径 运 载
要包含 : 回转 工作 台 、 上工装旋转驱 动及定 位部件 、 内外钻铆垂直升降驱动部件 、 中间框定位支撑 、 钻铆执 行部件干 ¨ 控制 系
统等 。介绍 了各部件 的主要结构 和功 能及设备的关键技术 。通过筒段产 品的试 制 , 验证 r该 自动钻 铆没备的 r 叮 行性 与I ] 靠性 。
3
板, 用于 同定支撑 杆和 方便 T件 『 J 、 】 部人 1 操作 ~ 1 . 1 . 5 钻铆 执行 部件
没备钻孑 L 豸 毛 统包 含高速电主轴( 钻速 3 0 0 0 0 r / ai r n ) 、 风 冷喷 头 和 紧装 置 ; 铆接 方式 为静 伺 服 铆 ,
最 大 铆 力 5 5 k N. .
1 . 2 自动 钻铆 设 备关键 技 术
1 . 2 . 1 清 洁钻 削技 术
‘
对 火箭 舱 段 装 配 T 艺 对 多 余 物 的控 制 要
求, 研 究 丁火箭舱 段 铝 合金 的 自动钻 孑 L T芝, 可 有
效 减 少加 T 毛刺 、 控 制 铆 接 过 程舱 段 的夹 层 问 多
保传动精度 。
1 . 1 . 2 上 工装 旋转 驱动 及定 位部 件
针 对 该 零 件 的 特 点 和装 配T 艺 要 求 , 研 制 了 自动 钻 铆 设 备 , 能 够 实 现该 零 件 钻 铆 的 自动化 作
《2024年度一种3自由度自动钻铆机构的运动学分析与优化设计》范文
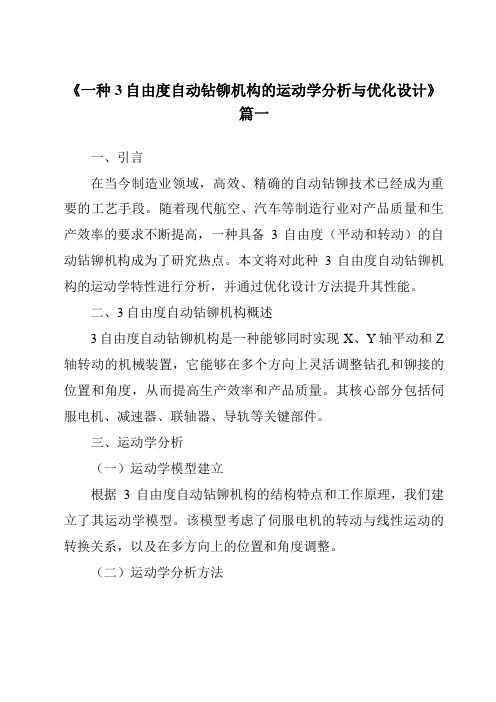
《一种3自由度自动钻铆机构的运动学分析与优化设计》篇一一、引言在当今制造业领域,高效、精确的自动钻铆技术已经成为重要的工艺手段。
随着现代航空、汽车等制造行业对产品质量和生产效率的要求不断提高,一种具备3自由度(平动和转动)的自动钻铆机构成为了研究热点。
本文将对此种3自由度自动钻铆机构的运动学特性进行分析,并通过优化设计方法提升其性能。
二、3自由度自动钻铆机构概述3自由度自动钻铆机构是一种能够同时实现X、Y轴平动和Z 轴转动的机械装置,它能够在多个方向上灵活调整钻孔和铆接的位置和角度,从而提高生产效率和产品质量。
其核心部分包括伺服电机、减速器、联轴器、导轨等关键部件。
三、运动学分析(一)运动学模型建立根据3自由度自动钻铆机构的结构特点和工作原理,我们建立了其运动学模型。
该模型考虑了伺服电机的转动与线性运动的转换关系,以及在多方向上的位置和角度调整。
(二)运动学分析方法我们采用了矢量法、解析法等运动学分析方法,对机构的运动过程进行数学描述和仿真分析。
通过分析机构的运动轨迹、速度和加速度等参数,为后续的优化设计提供了依据。
四、优化设计(一)设计目标与约束条件优化设计的目标是在满足机构工作要求的前提下,提高其运动性能和结构稳定性。
约束条件包括机构的工作空间、运动速度、加速度等参数的限制。
(二)优化设计方法我们采用了多目标优化算法、有限元分析等方法,对机构的关键部件进行优化设计。
通过对机构的结构参数、材料选择等进行综合分析,以提高机构的刚度、强度和稳定性。
同时,我们还考虑了机构的轻量化设计,以降低能耗和提高工作效率。
五、实验验证与结果分析(一)实验验证为了验证优化设计的有效性,我们进行了实验验证。
通过对比优化前后机构的运动性能、工作精度等参数,评估优化设计的成果。
(二)结果分析实验结果表明,经过优化设计的3自由度自动钻铆机构在运动性能、工作精度等方面得到了显著提升。
同时,机构的刚度、强度和稳定性也得到了提高,满足了实际生产需求。
《2024年一种3自由度自动钻铆机构的运动学分析与优化设计》范文
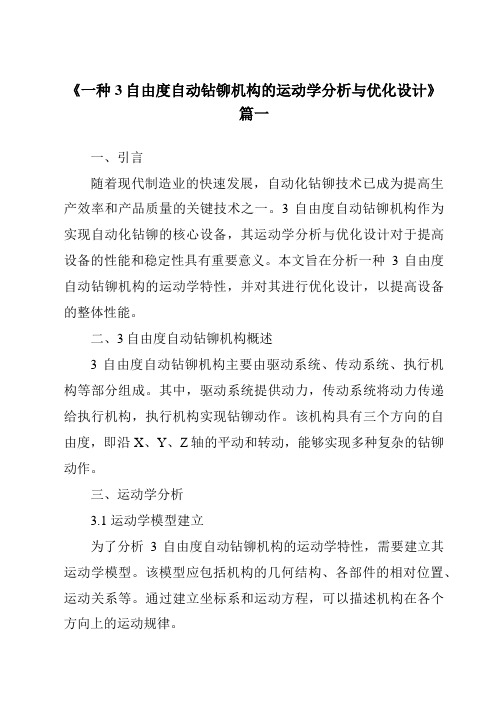
《一种3自由度自动钻铆机构的运动学分析与优化设计》篇一一、引言随着现代制造业的快速发展,自动化钻铆技术已成为提高生产效率和产品质量的关键技术之一。
3自由度自动钻铆机构作为实现自动化钻铆的核心设备,其运动学分析与优化设计对于提高设备的性能和稳定性具有重要意义。
本文旨在分析一种3自由度自动钻铆机构的运动学特性,并对其进行优化设计,以提高设备的整体性能。
二、3自由度自动钻铆机构概述3自由度自动钻铆机构主要由驱动系统、传动系统、执行机构等部分组成。
其中,驱动系统提供动力,传动系统将动力传递给执行机构,执行机构实现钻铆动作。
该机构具有三个方向的自由度,即沿X、Y、Z轴的平动和转动,能够实现多种复杂的钻铆动作。
三、运动学分析3.1 运动学模型建立为了分析3自由度自动钻铆机构的运动学特性,需要建立其运动学模型。
该模型应包括机构的几何结构、各部件的相对位置、运动关系等。
通过建立坐标系和运动方程,可以描述机构在各个方向上的运动规律。
3.2 运动学分析方法运动学分析主要采用解析法和仿真法。
解析法通过建立机构的数学模型,分析机构的运动规律和性能指标。
仿真法则利用计算机仿真软件,对机构的运动过程进行模拟,以验证解析法的正确性。
通过两种方法的结合,可以更全面地了解机构的运动学特性。
四、优化设计4.1 设计目标优化设计的目标是在满足机构运动学特性的前提下,提高设备的整体性能和稳定性。
具体包括提高钻铆精度、降低能耗、提高工作效率等。
4.2 优化设计方法优化设计主要采用数学规划和计算机辅助设计技术。
首先,通过数学规划方法,建立设备的性能指标和约束条件,确定优化目标。
然后,利用计算机辅助设计技术,对机构的结构和参数进行优化设计,以实现优化目标。
此外,还可以采用实验设计和仿真分析等方法,对优化设计结果进行验证和改进。
五、实例分析以一种具体的3自由度自动钻铆机构为例,进行运动学分析与优化设计。
首先,建立该机构的运动学模型,分析其在各个方向上的运动规律和性能指标。
飞机自动钻铆仿真技术
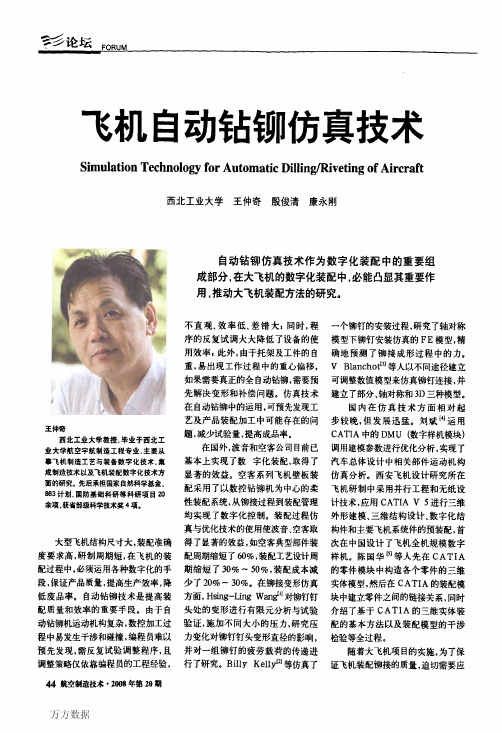
业大学航空宇航制造工程专业,主要从 事飞机制造工艺与装备数字化技术.集 成制造技术以及飞机装配数字化技术方 面的研究。先后承担国家自然科学基金. 863计划、国防基础科研等科研项目扣 余项.获省部级科学技术奖4项。
大型飞机结构尺寸大,装配准确 度要求高,研制周期短,在飞机的装 配过程中,必须运用各种数字化的手 段,保证产品质量,提高生产效率,降 低废品率。自动钻铆技术是提高装 配质量和效率的重要手段。由于自 动钻铆机运动机构复杂,数控加工过 程中易发生干涉和碰撞,编程员难以 预先发现,需反复试验调整程序,且 调整策略仅依靠编程员的工程经验,
数字化装配是未来飞机制造业 的发展趋势,在这样的背景下,仿真 软件及其相关技术的不断发展,无疑 将会对飞机制造业产生重大的推动 作用.并缩短研制周期。自动钻铆仿
自动钻铆仿真应用
(1)移动工作台建模与分析。 采用CATIA设计满足支撑自 动钻铆机X、y两自由度运动的移 动工作台结构。为确保运动定位精 度,移动工作台设计采用滚珠丝杠轨 道式,y坐标运动平台在X向运动 框架上,初步设计运动框架长、宽及 其承重,采用钢板焊接成大型框架, 使其具有很高的刚性和强度;l,坐 标运动平台在X向运动框架上可以 前后移动;面向材料特性及力学性
与自动钻铆机的安装与调试。移动 工作台的设计制造方案如图6所示。 图7为经由ABAQ U S有限元分析
本文有参考文献6篇,因篇幅所 限未能一一列出,读者如有需要,请 向本刊编辑部索取。 (责编 晓霏)
2008年第20期·航宅制造技术47
万方数据
飞机自动钻铆仿真技术
第一步,工件铆接变形数值建 模。根据铆接工件的材料、外形等特 征进行有限元前置处理,建立工件铆 接的有限元模型。
第二步,不同施铆顺序的铆接变 形分析。对不同施铆顺序下工件的 变形进行比较,探寻前一个工件铆接 对后续工件铆接的影响。
飞机装配自动钻铆技术研究

飞机装配自动钻铆技术研究摘要:本文关于自动钻铆技术展开深入研究,简要介绍了自动钻铆技术的基本概述。
然后着重探讨了飞机装配自动钻铆技术的主要内容,其中包括自动钻铆工艺、柔性装备技术、托架系统技术、自动仿真技术、末端执行器技术,从而有效延长飞机寿命,增强飞机装配效率,为相关人员提供充分参考。
关键词:飞机装配;自动钻铆技术;钻铆工艺引言:随着我国经济水平的快速提升,人们的生活质量也随之提高,在出行过程中,经常选择飞机飞行的方式。
由此对飞机的要求不断增多,为了提高飞机装配,不断加强对自动钻铆技术的全面探索,并将该技术逐渐应用到飞机装配中,促使该技术得到广泛应用,有助于提高飞机装配质量,确保飞机的安全飞行。
1自动钻铆技术的基本概述当前,飞机应用较为广泛,大型飞机的总重量大约在100t以上,大型客机约在150座以上,飞机在使用过程中,其寿命通常在90000h以上,飞行较为可靠,由此对飞机装配技术也提出较高要求。
其中,自动钻铆技术应用相对较多,在我国技术的研究发展下,该项技术也逐渐成熟,能够有效进行自动定位,并对电、汽等进行自动控制。
同时,该技术的发展时间相对久远,在航空工业发展中具有良好的应用效果。
当前,我国不断对该技术进行全面研究,充分顺应现代化的发展要求,促使自动钻铆技术也逐渐向数字化以及智能化方向发展,采用全数控系统,对其进行合理设计,完善飞机装配各项连接工序,促使铆接数量在15个/min左右,利用全自动铆接工具,可有效增强铆接效率。
但是,在该技术在应用过程中,仍然存在着相应的问题,型号需求较为缺乏,整体控制技术的不完善,造成相关工作出现中断情况,影响飞机的正常飞行。
同时,在我国飞机项目的实施过程中,装配体系尚未完善,系统集成性相对较低。
由此我国技术人员逐渐加大对自动钻铆技术的研究力度,从多角度出发对各项技术进行深入探索,提高该技术的使用效率,促使飞机得到安全运行。
2飞机装配自动钻铆技术的主要内容2.1自动钻铆工艺现阶段,自动钻铆技术在飞机装配中得到良好运用。
国内外自动钻铆技术的发展现状及应用

国内外自动钻铆技术的发展现状及应用西飞国际设备维修中心 楼阿莉当代飞机制造技术的发展,对疲劳寿命、密封、防腐的要求越来越高,为了满足飞机对各种性能的要求,航空制造领域发展了各种先进技术,其中机械连接技术的干涉配合无头铆钉自动钻铆技术就是其中之一。
国外铆接装配技术几十年的应用证明,采用自动钻铆机后装配效率至少比手工铆接装配提高10倍,并能节约安装成本,改善劳动条件,更主要的是能够确保安装质量,大大减少人为因素造成的缺陷。
现在采用自动钻铆机已成为改善飞机性能的主要工艺措施之一。
美国是最早发展自动钻铆技术的国家,早在 50 年代初就已在飞机铆接装配生产线上应用了自动钻铆机,经过 50 多年的发展,现在世界各航空工业发达国家都已广泛采用这项技术。
自动钻铆技术主要包含以下内容:(1) 设备的研制、开发。
以不同飞机的结构为对象,发展多种型号的数控自动钻铆系统,不仅能铆接壁板,而且还可铆接各种组件,如肋、框、梁、翼面、前缘等,从而使自动钻铆系统的工作覆盖面大幅度增加,使整个飞机的铆接工作有较大的改观。
(2) 对各种干涉配合新型紧固件进行自动安装。
通过增加附件,可以对两件型紧固件进行自动安装,如环槽钉、高锁螺栓、锥形螺栓等,也可对无头铆钉进行干涉配合铆接,从而提高铆接结构疲劳寿命5~6倍,对提高飞机整体油箱的密封铆接质量有重大意义。
(3) 自动钻铆工艺。
结构铆接的整个过程通过预先编程全部由CNC程序控制,自动钻铆工艺是在一台设备上一次性地连续完成夹紧、钻孔、锪窝、注胶、放铆、铣平等工序。
由于机床带有高速、高精度的转削主轴头,一次进给即能钻出0.005mm以内高精度的孔,同时埋头窝的深度也可精确控制在±0.01mm以内,再加上机床由数控系统控制各轴运动,并采用精密自动化工装夹具,使得铆钉镦头高度保持一致,不受人为因素的影响。
所有这些因素均使钉杆在孔中充填质量大为改善,从而有利于提高细节疲劳强度许用值。
此外,由于钻孔时铆接件处在高的夹紧力下,层间不会产生毛刺和进入切削,可以减小疲劳载荷下发生磨蚀损伤的程度,这些均有利于提高接头的疲劳强度。
钻铆工艺分析
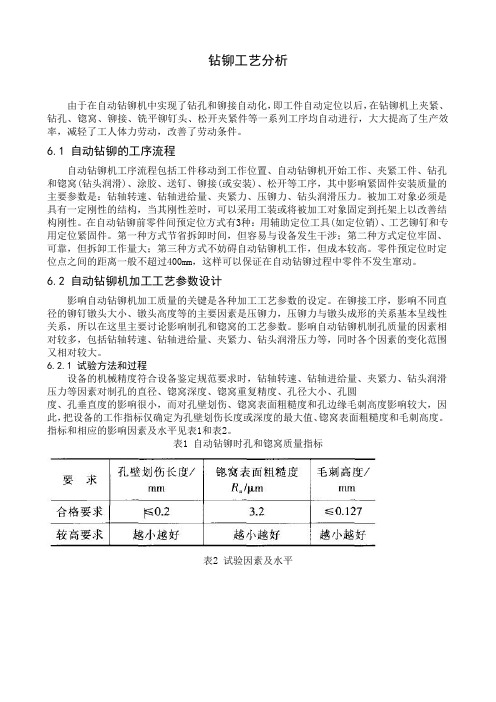
钻铆工艺分析由于在自动钻铆机中实现了钻孔和铆接自动化,即工件自动定位以后,在钻铆机上夹紧、钻孔、锪窝、铆接、铣平铆钉头、松开夹紧件等一系列工序均自动进行,大大提高了生产效率,减轻了工人体力劳动,改善了劳动条件。
6.1 自动钻铆的工序流程自动钻铆机工序流程包括工件移动到工作位置、自动钻铆机开始工作、夹紧工件、钻孔和锪窝(钻头润滑)、涂胶、送钉、铆接(或安装)、松开等工序,其中影响紧固件安装质量的主要参数是:钻轴转速、钻轴进给量、夹紧力、压铆力、钻头润滑压力。
被加工对象必须是具有一定刚性的结构,当其刚性差时,可以采用工装或将被加工对象固定到托架上以改善结构刚性。
在自动钻铆前零件间预定位方式有3种:用辅助定位工具(如定位销)、工艺铆钉和专用定位紧固件。
第一种方式节省拆卸时间,但容易与设备发生干涉;第二种方式定位牢固、可靠,但拆卸工作量大;第三种方式不妨碍自动钻铆机工作,但成本较高。
零件预定位时定位点之间的距离一般不超过400mm,这样可以保证在自动钻铆过程中零件不发生窜动。
6.2 自动钻铆机加工工艺参数设计影响自动钻铆机加工质量的关键是各种加工工艺参数的设定。
在铆接工序,影响不同直径的铆钉镦头大小、镦头高度等的主要因素是压铆力,压铆力与镦头成形的关系基本呈线性关系,所以在这里主要讨论影响制孔和锪窝的工艺参数。
影响自动钻铆机制孔质量的因素相对较多,包括钻轴转速、钻轴进给量、夹紧力、钻头润滑压力等,同时各个因素的变化范围又相对较大。
6.2.1 试验方法和过程设备的机械精度符合设备鉴定规范要求时,钻轴转速、钻轴进给量、夹紧力、钻头润滑压力等因素对制孔的直径、锪窝深度、锪窝重复精度、孔径大小、孔圆度、孔垂直度的影响很小,而对孔壁划伤、锪窝表面粗糙度和孔边缘毛刺高度影响较大,因此,把设备的工作指标仅确定为孔壁划伤长度或深度的最大值、锪窝表面粗糙度和毛刺高度。
指标和相应的影响因素及水平见表1和表2。
表1 自动钻铆时孔和锪窝质量指标表2 试验因素及水平根据上述表格,我们需要解决的问题是多个指标的,既要保证孔壁和锪窝表面粗糙度符合要求,又要保证孔边毛刺达到标准。
- 1、下载文档前请自行甄别文档内容的完整性,平台不提供额外的编辑、内容补充、找答案等附加服务。
- 2、"仅部分预览"的文档,不可在线预览部分如存在完整性等问题,可反馈申请退款(可完整预览的文档不适用该条件!)。
- 3、如文档侵犯您的权益,请联系客服反馈,我们会尽快为您处理(人工客服工作时间:9:00-18:30)。
第一章前言1.1 前言飞机制造中铆接装配占有十分重要的地位,据估算,飞机装配劳动量约占整个飞机制造劳动量的40%~50%,其中铆接占30%。
随着对飞机性能要求的不断提高,人们愈来愈重视铆接质量,使其适应质量稳定、生产速率高、疲劳寿命长的要求。
在这样的背景下,自动钻铆技术开发成功并首先在世界著名的航空企业波音、空中客车公司中得到应用,由此迈开飞行器装配自动化的步伐,并逐渐显示出其强大技术优势,促进了飞机装配的历史性变革。
随着我国航空工业军民用飞机性能、水平等方面的不断提高,航空企业在铆接装配中也在不断地探索应用自动钻铆技术。
1.2 自动钻铆技术概述自动钻铆技术从上个世纪50年代开始起步,经历了手动、半自动化、全自动化等阶段,在其发展过程中,不断吸收了其他技术,如自动控制、传感器、计算机仿真、计算机远程控制和远程通信以及机器人等领域中的新技术和新工艺。
自动钻铆技术也因此成为一门综合多学科、多技术的专用技术,并逐渐向多任务集成、智能化、网络化方向发展。
当今世界飞机制造技术的发展趋势表明,在很长一段时间内,铆接技术仍将是飞行器结构部件最可靠的连接技术。
然而旧的铆接方法手工作业劳动强度高,铆接质量差,己不能满足现代飞机生产制造的要求。
自动钻铆技术已成为飞机制造业发展的必然趋势。
当代飞机制造技术的发展,对疲劳寿命、密封、防腐的要求越来越高,为了满足飞机对各种性能的要求,航空制造领域发展了各种先进技术,其中机械连接的干涉配合无头铆钉自动钻铆技术就是其中之一(图1-1为国外自动钻铆机)。
早期的自动钻铆技术仅限于单机的过程自动化,只能完成自动的切削加工和铆接等过程,尚不具备自动化定位的特点,可以看作是单台的加工机床。
随着现代工程技术、自动化技术、数字制造技术和人工智能技术的日益完备和发展,自动钻铆技术实现了实质性的突破,已经初步形成了自动化装配系统。
该系统的出现不仅大大提高了飞机制造的经济效益、社会效益和环境生态效益,而且对改进飞机设计方式和提高工艺技术水平也有明显的促进和推动作用,主要表现在以下几个方面:(1)通过数字化模型和智能化定位控制来完成飞行器组件的自动化装配。
在解决自动定位方式的过程中,逐渐克服了飞行器结构尺寸带来的影响,目前已经能实现超过180°机身超大型壁板的自动化铆接装配和15m以上整机机翼的自动化定位铆接装配。
图 1-1 国内自动钻铆机(2)国外已经出现的自动精确引导对合定位装置,在自动化装配系统中起到了很好的协调作用。
飞机的各个部分都有相应的专用自动装配设备与之对应,共用工艺数据库并传递飞机的数字化数据,完成部件制造,最终对分离的部件实现精确定位对合,完成总装。
(3)智能化机器人的发展也促进了自动钻铆技术向自动化装配系统的演变。
目前,经过特殊设计的带颚式工作头的智能机器人可以进行如长桁、长桁夹和隔框之间等狭窄区域的连接以及剪切带的安装工作,可以达到很高的效率和自动识别精度。
这为解决飞行器设计中的结构设计限制提供了新的解决方案。
(4)自动化控制技术的实现和突破大大提高了自动化装配系统的可靠性和实用性。
飞机工艺技术也因此得到新的补充和发展。
例如,由GEMCOR公司开发成功的无头铆钉挤压安装技术可以得到目前为止经实验证实的最好的干涉量,提高了铆接后的材料疲劳属性和密封性,可广泛应用于机翼部件和整体油箱部件。
(5)BR歍JE公司开发出的柔性托架系统可以自动适应任何形式的壁板形状且具有记忆功能,在铆接过程中,真空吸附头可在程序的控制下自动躲避下铆头的铆接和移动动作,极具智能性。
(6)自动钻铆技术今后的发展方向以及自动化装配需求将会使飞机设计技术与自动钻铆技术有机结合,在满足飞机自身功能和结构要求的前提下尽可能采用易于实现自动钻铆的设计结构,使其更加紧密地结合起来,发挥自动钻铆系统的制造优势和技术特点。
未来的自动钻铆技术将向大系统方向发展,信息的网络化将使单一的设备有机地联系起来,进而形成自动化装配系统。
在这个系统中,所有的数据资源被集中共享和处理,并能实现自动化调度,让所有具有不同结构和不同装配特点的自动化加工设备和自动化工装集中形成一体,自动完成从机翼、机身、发动机舱等部件到部件之间自动对合的工作,从而为最终实现数字化装配工厂打下基础。
通过这种方式,可以达到远程设计、远程制造,从而为提高制造效率和充分应用制造资源提供基础平台。
但也要看到,要实现这种庞大的自动化装配系统,其投入费用是惊人的。
目前只有少数发达国家的航空制造业与自动化科技公司在联合研制局部的自动化装配系统,以完成某一特定机型的自动化装配工作。
但是可以相信,自动化装配系统技术应用方面的逐渐成熟,将会带动其他相关的智能化工装乃至智能化工厂方面的研究,最终实现真正意义上的飞机装配自动化。
1.3 国内外研究概况及发展趋势1.3.1 国内自动钻铆技术发展简况随着我国航空工业研制的新机52航空制造技术-2∞5年第6期种的性能、水平不断提高,在铆接装配中发展自动钻铆技术已经势在必行。
我国自动钻铆机的研制起步较早,70年代初,原航空部曾组织有关单位研制过各种型号的自动钻柳机,但因种种原因没能坚持下去。
分析其原因主要还是当时研制或生产的飞机机种对图 1-2 G900自动钻铆机图 1-3 G4026SXX-120型自动钻铆机使用自动钻铆机没有迫切要求,由于没有型号需求的牵引,使得继续开展这项工作缺乏动力,加之当时研制的设备中所采用的元件、控制系统等均存在各种质量问题,致使工作被迫中断。
到了80年代中期,各厂外协加工项目增加,开始承担一些民机小部件(如垂尾、平尾)的铆接装配,因国外要求进行这些部件的铆接装配时必须使用自动钻铆机,以保证达到所要求的质量,于是自动钻铆机又再度得到应用。
此外,我国的干线飞机研制也正在逐步开展,为了确保干线飞机的疲劳图 1-4 加工A380的动钻铆机图 1-5 加工波音737APU门的动钻铆机寿命和安装质量要求,也迫切要求尽快发展我国的自动钻铆技术。
此后,我国一些航空工厂先后引进了自动钻铆机。
1985年,西飞公司引进一台从波音公司退役图 1-6 西飞引进的GMECOR G400自动钻铆机图 1-7 西飞与西工大联合制造的机翼托架的二手设备G400,1992年引进G900。
这两台机床均配以手动托架,分别加工美国波音和前麦道公司的垂尾平尾及法航、意航、加航的零件。
随着国际间技术交流的不断深化,我国又同美国麦道公司合作生产干线机MD一90—30。
西飞公司的两台自动钻铆机已满足不了生产的需求。
1 9 9 3年又引进了GEMCOR公司的G4026SXX 一120型自动钻铆机,用于麦道公司MD一90~30等飞机的机翼壁板的铆接装配生产。
该机床引进时,未引进托架装置,1995年西飞公司同西工大联合研究、设计、制造了该机翼托架,采用了Z坐标两立柱支撑的结构形式。
由于受当时工艺制造水平的限制,围框刚性不足,存在一定问题,而麦道干线机生产的下马使该项科研最终未进行下去。
1998年西飞又引进APS公司的RMS335钻铆机,取代G400机床。
与此同时,成飞公司先后引进了G4026、RMs335钻铆机,沈飞公司也引进法国的P R E C A 3 0 0和BR6TJE的BA96,2000年陕飞公司引进GEMCOR GRS6R30一120,配有自动送钉装置和法线传感器,但均未配置全自动定位系统。
飞机机械连接自动钻铆技术在国外发展极为迅速,而我国与国际先进水平差距越来越大。
我们应从整个航空工业全局的生存和发展出发,从技术经济综合效益考虑,努力逐步缩小与国外先进水平的差距。
我们认为应首先大幅度提高飞机装配时的机铆系数,否则就不可能实现自动钻铆,也不可能使铆接结构达到飞机对疲劳寿命、防腐、密封性和减轻结构重量的要求。
在转包生产中,通过引进国外先进的数控钻铆系统及铆接生产线,学习积累国外先进技术和工艺方法,再结合型号研制,对引进的自动钻铆机开发配套数控托架,从而降低制造成本,探索出一条与我国国情相适应飞机装配工艺技术改造的新路。
1.3.2 国外自动钻铆技术发展简况美国自动钻铆机的最早制造厂商是GEMCOR(通用电气机械公司),它是向世界各国飞机制造行业提供自动钻铆机的主要厂商之一。
该公司生产的系列化产品质量可靠,并配套有各种型号的数控托架。
到现在为止,销售的自动钻铆机数量已达2000台以上,其中190台具有定位系统。
公司生产的自动钻铆机主要型号有G200、G300、G400、G900、G666、G39A、G4013、G4026、G5013。
其中G200、G400型是较早的型号,G300为比较通用的型号,而G900型的功能比较齐全。
具有无头铆钉钻铆功能的型号有G900、G666、G39A、G4013、G4026、G5013。
近几年无头铆钉的工作原理有所发展,机床采用GEMCOR专利的SQUEEZE/SQUEEZE双挤铆方式,先预挤铆,再进行挤铆,不仅能保证上下铆头同步成形上下镦头,而且铆接质量大大提高。
各种型号机床可通过改变下铆砧形状和尺寸来适应各种结构的要求。
GEMCOR公司生产的数控托架(也称自动定位系统)主要型号有G63、G79、G86、747WRS、G2000等。
(1)G63自动定位系统。
G63的工作原理是:钻铆机固定不动,托架的框架固定在两端的架车上,架车在地面导轨上纵向移动,所有X、y、Z轴方向的运动由伺服控制的液压马达通过滚珠丝杠来带动,而绕X向的旋转贝Ⅱ依靠伺服操作液压作动筒。
该系统应用于空客公司A300机翼壁板的装配中,与G666Sp—145无头铆钉钻铆机配套组成自动钻铆系统。
在美国VOUGHT公司的波音747机身壁板的装配中,它与G400B/39A一120钻铆机配套组成自动钻铆系统。
(2)G79自动定位系统。
它与G400BH/39A一120自动钻铆机配套用于MITSUBISHI公司转包生产波音767机身段的装配。
G79为CNC控制、六坐标、中型自动定位系统。
它是GEMCOR产品中最通用、最多功能的定位系统。
铆接机作X向运动,而托架作y、Z和a、b、c向的运动(a、b、c为绕X、y、z轴的转动)。
所有的动作均由自动和手动控制的电伺服马达驱动。
(3)G86自动定位系统。
它可以与G200、G300、G400、G900、G4013、G4026、G5013等配套组成自动钻铆系统。
G86的CNC定位系统有独特的低重心设计,这样可以保证即使在高速运行的状态下也具有稳定性和可重复性。
托架可以通过宽度调节容纳不同大小的夹具。
目前,该机型已发展成全电动自动铆接系统,铆接方式也从液压镦铆发展为SQ U EEZE/SQUEEZE的双挤铆方式;10/32”以下的铆钉铆接驱动采用全电动方式,用滚柱丝杠传动,并配有自动换刀装置。