数控电火花线切割培训资料
数控 电火花 线切割

放电峰值电流对工艺指标的影响
放电峰值电流增大,单个脉冲能量增多,工件放电痕 迹增大,故切割速度迅速提高,表面粗糙度数值增 大,电极丝损耗增大,加工精度有所下降。因此第 一次切割加工及加工较厚工件时取较大的放电峰值 电流。
工件接在脉冲电源的正极,电极丝接负极 。
种类
快走丝:走丝速度 8~10m/s,往复运动(我国独创) 慢走丝:走丝速度< 0.2 m/s,单向运动
2电火花线切割加工特点
• (1)加工对象不受硬度的限制,可用于一般切削方法 难以加工或者无法加工的金属材料和半导体材料,特别 适合淬火工具钢、硬质合金等高硬度材料的加工;但无 法加工非金属导电材料。
为了实现锥度加工,最常见的方法是在上 丝架的上导轮上加两个小步进电动机,使上丝 架上的导轮作微量坐标移动(又称U、V轴移动), 其运动轨迹由计算机控制。
②线切割机床控制系统(7.1)
• 控制系统在电火花线切割加工中起着重要作用,具体体 现在两方面:
• (1) 轨迹控制作用。它精确地控制电极丝相对于工件
• 一、线切割加工的主要工艺指标 • 二、电参数对工艺指标的影响 • 三、非电参数对工艺指标的影响 • 四、合理选择电参数
一、主要工艺指标
– 线切割速度(mm2/min):在保证一定的表面粗糙度的切割过程 中,单位时间内电极丝中心线在工件上切过的面积的总和。 最高切割速度是指在不计切割方向和表面粗糙度等条件下,所能 达到的最大切割速度。 高速走丝:切割速度 20~180mm2/min,切割效率20mm2/(min.A) 低速走丝:切割速度 20~240mm2/min 切割效率:每安培电流的切割速度( mm2/min A)
数控电火花线切割加工资料

第六章数控电火花线切割加工电火花加工属于特种加工的一种方法,它是在加工过程中,使工具和工件之间不断产生脉冲性的火花放电,靠放电时局部、瞬时产生的高温去除工件多余材料,以及使材料改变性能或被镀覆等的放电加工,因放电过程可见到火花,故称之为电火花加工。
6.1数控电火花线切割加工原理与特点6.1.1 数控电火花线切割加工原理数控电火花线切割是利用移动的细金属导线作为工具电极,在金属丝与工件间施加脉冲电流,产生放电腐蚀,对工件进行切割加工。
工件的形状是由数控系统控制工作台相对于电极丝的运行轨迹决定的,因此不需制造专用的电极,就可以就可以加工形状复杂的模具零件。
其加工原理如图6-1所示,工件连接脉冲电源的正极,电极丝接负极,加上高频脉冲电源后,在工件与电极丝之间产生很强的脉冲电场,使其间的介质被电离击穿,产生脉冲放电。
电极丝在贮丝筒的作用下作正反向交替运动,在电极丝和工件之间浇注工作介质,在机床数控系统的控制下,工作台相对电极丝按预定的程序运动,从而切割出需要的工件形状。
图6-1 电火花切割原理6.1.2 数控电火花线切割加工特点1.直接利用线状的电极丝作为电极,可节约电极设计、制造费用、缩短了生产准备周期。
2.可以加工用传统切削加工方法难以加工或无法加工的微细异形孔、窄缝和形状复杂的工件。
3.采用线切割加工冲模时,可实现凸、凹模一次加工成形。
6.2 数控电火花线切割机床6.2.1 电火花线切割机床分类(1)按控制方式可分为靠模仿型控制、光电跟踪控制、数字程序控制及微机控制等;(2)按电源形式可分为RC电源、晶体管电源、分组脉冲电源及自适应控制电源等;(3)按加工特点可分为大、中、小型以及普通直壁切割型与锥度切割型等;(4)按走丝速度可分为慢走丝方式和快走丝方式两种。
6.3 数控电火花线切割工艺基础数控电火花线切割加工,一般是作为工件尤其是模具加工中的最后工序。
要达到加工零件的精度及表面粗糙度要求,应合理控制线切割加工时的各种工艺参数(电参数、切割速度、工件装夹等),同时应安排好零件的工艺路线及线切割加工前的准备加工。
数控电火花线切割加工技术培训教程
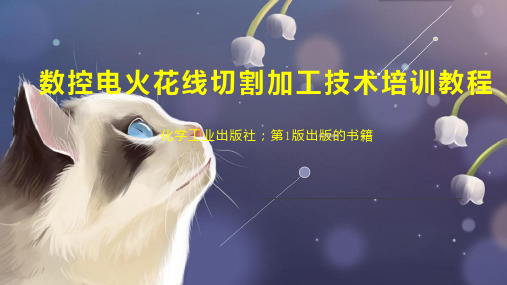
谢谢观看
数控电火花线切割加工是实践性与理论性都很强的一门技术,技术工人既要掌握电火花线切割工艺方面的知 识,又要充分熟悉数控电火花线切割机床的功能,还要熟练运用自动编程CAD/CAM软件。为适应数控技术现代化 的要求,作为一名合格的数控电火花线切割机床技术工人,要全面掌握所需的专业知识。数控电火花线切割领域 的技术工人、编程员急切希望提高自己的技术水平,企业也急需培养一批能够熟练掌握数控编程、操作和维护的 应用型技术人才。针对以上现状,编写了这本《数控电火花线切割加工技术培训教程》。
数控电火花线切割加工技术培训教程
化学工业出版社;第1版出版的书籍
01 内 序言
《数控电火花线切割加工技术培训教程》是2008年化学工业出版社;第1版出版的一本图书。
内容简介
《数控电火花线切割加工技术培训教程》与数控电火花线切割加工的实际操作相结合,详细介绍了数控电火 花线切割加工技术基础、数控高速走丝电火花线切割加工技术、数控低速走丝电火花线切割加工技术等相关内容。 《数控电火花线切割加工技术培训教程》采用流程化的讲解方式,以典型的数控电火花线切割机床为例进行剖析, 精选了典型的数控电火花线切割加工实例,重点介绍数控电火花线切割工艺、编程及操作,使读者能够系统掌握 数控线切割加工技术。《数控电火花线切割加工技术培训教程》取材新颖,对实际操作技能做了详尽的讲解,并 融入了大量的企业生产实际经验,具有较强的指导性和实用性。
数控电火花线切割机床操作方法资料
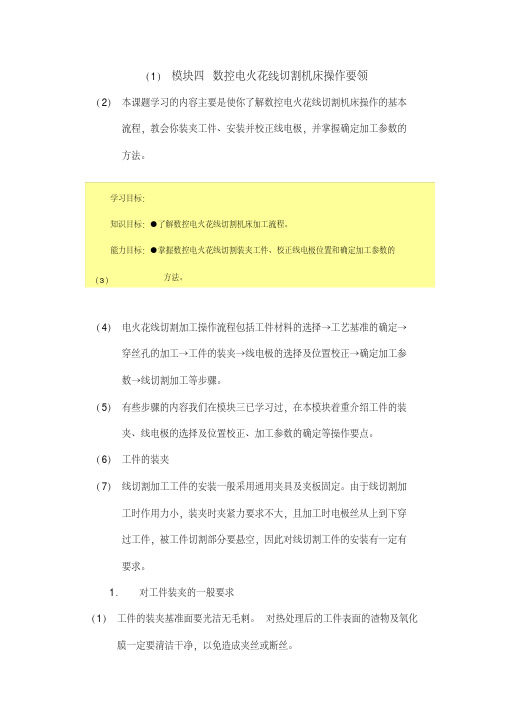
(1)模块四数控电火花线切割机床操作要领(2)本课题学习的内容主要是使你了解数控电火花线切割机床操作的基本流程,教会你装夹工件、安装并校正线电极,并掌握确定加工参数的方法。
(3)(4)电火花线切割加工操作流程包括工件材料的选择→工艺基准的确定→穿丝孔的加工→工件的装夹→线电极的选择及位置校正→确定加工参数→线切割加工等步骤。
(5)有些步骤的内容我们在模块三已学习过,在本模块着重介绍工件的装夹、线电极的选择及位置校正、加工参数的确定等操作要点。
(6)工件的装夹(7)线切割加工工件的安装一般采用通用夹具及夹板固定。
由于线切割加工时作用力小,装夹时夹紧力要求不大,且加工时电极丝从上到下穿过工件,被工件切割部分要悬空,因此对线切割工件的安装有一定有要求。
1.对工件装夹的一般要求(1)工件的装夹基准面要光洁无毛刺。
对热处理后的工件表面的渣物及氧化膜一定要清洁干净,以免造成夹丝或断丝。
学习目标:知识目标:●了解数控电火花线切割机床加工流程。
能力目标:●掌握数控电火花线切割装夹工件、校正线电极位置和确定加工参数的方法。
(2)夹紧力要均匀,不得使工件变形或翘起。
(3)装夹位置要有利于工件的找正,且要保证在机床加工行程范围内。
(4)所用的夹具精度要高,以确保加工精度。
(5)细小、精密及薄壁工件应先固定在辅助夹具上再装夹到工作台。
(6)批量加工零件时,最好设计专用夹具以提高生产率。
2.常用的工件装夹方式(1)悬臂支撑,如图3-22(a)所示。
此方式装夹方便,通用性强,适用于对加工要求不高或悬臂部分较少的工件的装夹。
(2)两端支撑,如图3-22(b)所示。
此方式工件两端固定在夹具上,支撑稳定,定位精度高,适用于较大零件的装夹。
(3)桥式支撑,如图3-22(c)所示。
此方式是把两支撑垫铁放到两端支撑夹具上,桥的侧面也可作定位面使用,使装夹更方便,通用性广,适用于大、中、小工件的装夹。
(4)板式支撑,如图3-22(d)所示。
数控线切割操作工培训第6章电火花切割机床的基本操作

第6章 电火花线切割机床的基本操作
6.1电火花线切割机床的安全操作规程 (1)进入实训区必须穿合身的工作服、戴工作帽,衬衫要系入裤内,
敞开式衣袖要扎紧,女同学必须把长发纳入帽内;禁止穿高跟鞋、拖鞋、 凉鞋、裙子、短裤及戴围巾。
(2)开机前按机床说明书要求对各润滑点加油。 (3)开动机床前,要检查机床电气控制系统是否正常,工作台和传 动丝杆润滑是否充分。检查工作液是否充足,然后开慢车空转3~5min, 检查各传动部件是否正常,确认无故障后,才可正常使用。 (4)按照线切割加工工艺正确选用加工参数,按规定的操作顺序操 作。 (5)用手摇柄转动储丝筒后,应及时取下手摇柄,防止储丝筒转动 时将手摇柄摔出伤人。 (6)装卸电极丝时,注意防止电极丝扎手,卸下的废丝应放在规定 的容器内,防止造成电器 短路等故障。
数控线切割操作工培训教程
2
2020年1月16日
6.2电火花线切割机床的维护与保养 线切割机床维护和保养的目的是为了保持机床能正常可靠地工作,延长其使
用寿命。 6.2.1机床的维护
(1)整机应经常保持清洁,停机8小时以上应擦抹并涂油防锈。 (2)丝架上的导电块、排丝轮、导轮周围以及储丝筒两端应经常用煤油清 洗干净,清洗后的脏油不应流回工作台的回液槽内。 (3)钼丝电极与工件间的绝缘是由工件夹具保证的,应经常将导电块、工 件夹具的绝缘物擦抹干净,保证绝缘要求。
数控线切割操作工培训教程
8
2020年1月16日
6.4工件的装夹与校正 6.4.1工件的装夹
线切割加工,特别是慢走丝线切割加工属于较精密加工,工作的装夹对 加工零件的定位精度有直接影响,特别在模具制造等加工中,需要认真仔细 地装夹工件。
线切割加工的工件在装夹中需要注意如下几点。 (1)工件的定位面要有良好的精度,一般以磨削加工过的面作为定位基 准为好,棱边倒钝,孔口倒角。 (2)切入点要导电,热处理件切入处要去除残物及氧化皮。 (3)热处理件要充分回火去应力,平磨件要充分退磁。 (4)工件装夹的位置应利于工件找正,并应与机床的行程相适应,夹紧 螺钉高度要合适,避免干涉到加工过程,上导丝轮要压得较低。 (5)对工件的夹紧力要均匀,不得使工件变形和翘起。 (6)批量生产时,最好采用专用夹具,以利于提高生产率。 (7)对细小、精密、薄壁等工件要固定在不易变形的辅助夹具上。
数控电火花线切割培训资料
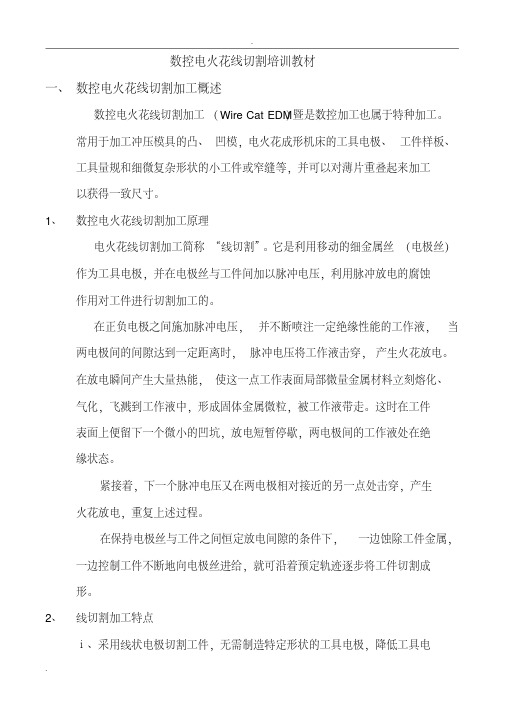
数控电火花线切割培训教材一、数控电火花线切割加工概述数控电火花线切割加工(Wire Cat EDM)暨是数控加工也属于特种加工。
常用于加工冲压模具的凸、凹模,电火花成形机床的工具电极、工件样板、工具量规和细微复杂形状的小工件或窄缝等,并可以对薄片重叠起来加工以获得一致尺寸。
1、数控电火花线切割加工原理电火花线切割加工简称“线切割”。
它是利用移动的细金属丝(电极丝)作为工具电极,并在电极丝与工件间加以脉冲电压,利用脉冲放电的腐蚀作用对工件进行切割加工的。
在正负电极之间施加脉冲电压,并不断喷注一定绝缘性能的工作液,当两电极间的间隙达到一定距离时,脉冲电压将工作液击穿,产生火花放电。
在放电瞬间产生大量热能,使这一点工作表面局部微量金属材料立刻熔化、气化,飞溅到工作液中,形成固体金属微粒,被工作液带走。
这时在工件表面上便留下一个微小的凹坑,放电短暂停歇,两电极间的工作液处在绝缘状态。
紧接着,下一个脉冲电压又在两电极相对接近的另一点处击穿,产生火花放电,重复上述过程。
在保持电极丝与工件之间恒定放电间隙的条件下,一边蚀除工件金属,一边控制工件不断地向电极丝进给,就可沿着预定轨迹逐步将工件切割成形。
2、线切割加工特点ⅰ、采用线状电极切割工件,无需制造特定形状的工具电极,降低工具电极的设计和制造费用,缩短加工周期。
ⅱ、直接利用电能进行脉冲放电加工,便于实现自动化控制。
ⅲ、加工时电极丝与工件不接触,两者之间宏观作用力极小,不产生毛刺和明显刀痕等缺陷。
ⅳ、加工中电极丝的损耗极小,加工精度高,无须刃磨刀具,缩短辅助时间。
3、线切割机床的分类通常按电极丝的运行速度快慢,线切割机床可分为快走丝线切割机和慢走丝线切割机。
快走丝线切割机床应用比较广泛,具有结构简单、操作方便、可维护性好,加工费用低、占地面积小及性价比高等特点。
慢走丝线切割机床采用一次性电极丝,可多次切割,有利于提高加工精度和降低表面粗糙度,属于精密加工设备。
电火花线切割加工培训共17页
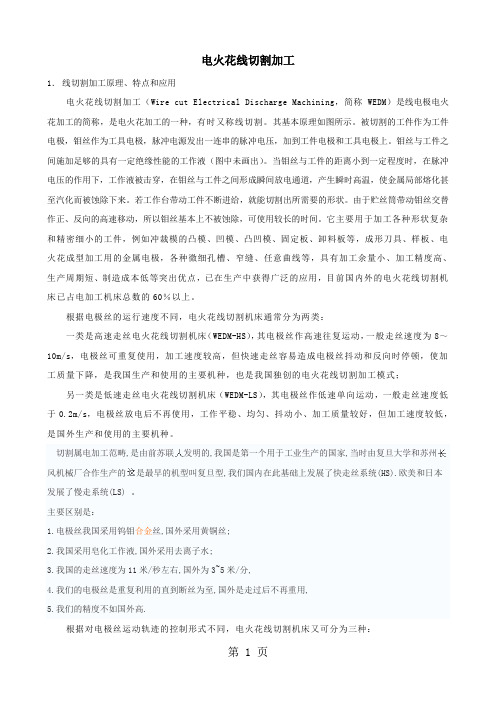
电火花线切割加工1.线切割加工原理、特点和应用电火花线切割加工(Wire cut Electrical Discharge Machining,简称WEDM)是线电极电火花加工的简称,是电火花加工的一种,有时又称线切割。
其基本原理如图所示。
被切割的工件作为工件电极,钼丝作为工具电极,脉冲电源发出一连串的脉冲电压,加到工件电极和工具电极上。
钼丝与工件之间施加足够的具有一定绝缘性能的工作液(图中未画出)。
当钼丝与工件的距离小到一定程度时,在脉冲电压的作用下,工作液被击穿,在钼丝与工件之间形成瞬间放电通道,产生瞬时高温,使金属局部熔化甚至汽化而被蚀除下来。
若工作台带动工件不断进给,就能切割出所需要的形状。
由于贮丝筒带动钼丝交替作正、反向的高速移动,所以钼丝基本上不被蚀除,可使用较长的时间。
它主要用于加工各种形状复杂和精密细小的工件,例如冲裁模的凸模、凹模、凸凹模、固定板、卸料板等,成形刀具、样板、电火花成型加工用的金属电极,各种微细孔槽、窄缝、任意曲线等,具有加工余量小、加工精度高、生产周期短、制造成本低等突出优点,已在生产中获得广泛的应用,目前国内外的电火花线切割机床已占电加工机床总数的60%以上。
根据电极丝的运行速度不同,电火花线切割机床通常分为两类:一类是高速走丝电火花线切割机床(WEDM-HS),其电极丝作高速往复运动,一般走丝速度为8~10m/s,电极丝可重复使用,加工速度较高,但快速走丝容易造成电极丝抖动和反向时停顿,使加工质量下降,是我国生产和使用的主要机种,也是我国独创的电火花线切割加工模式;另一类是低速走丝电火花线切割机床(WEDM-LS),其电极丝作低速单向运动,一般走丝速度低于0.2m/s,电极丝放电后不再使用,工作平稳、均匀、抖动小、加工质量较好,但加工速度较低,是国外生产和使用的主要机种。
切割属电加工范畴,是由前苏联发明的,我国是第一个用于工业生产的国家,当时由复旦大学和苏州风机械厂合作生产的是最早的机型叫复旦型,我们国内在此基础上发展了快走丝系统(HS).欧美和日本发展了慢走系统(LS)。
线切割培训课件

优化切割路径
采用最短的路径,减少切割时间和损耗。
使用切割液
调整切割参数
根据材料和厚度调整电流、电压、速度等参 数,以获得最佳的切割效果。
选择合适的切割液,提高切割表面的质量和 精度。
02
维护设备
定期检查和保养设备,确保设备的稳定性和 精度。
04
03
01
线切割加工的质量控制
保证电极丝的质量
使用高质量的电极丝, 确保切割的稳定性和精 度。
使用CAD软件绘制零件 的几何图形,并确定加 工参数。
编写程序
根据加工方案和几何图 形,编写线切割程序。
校验程序
在加工前对编写的程序 进行校验,以确保程序 正确性。
线切割编程的实例
简单零件加工
以一个简单的方形零件为例,演示如 何进行线切割编程。
复杂零件加工
以一个具有复杂形状的零件为例,演 示如何进行线切割编程。
案例二:大批量零件的线切割加工
介绍大批量零件的线切割加工 的基本原理和难点。
分析大批量零件的线切割加工 的生产效率和质量控制方法。
展示大批量零件的线切割加工 的实例和效果。
案例三:高精度零件的线切割加工
介绍高精度零件的线切割加工的基本原理和难点。 分析高精度零件的线切割加工的工艺流程和注意事项。
展示高精度零件的线切割加工的实例和效果。
1.谢谢聆 听
03
应用领域
广泛应用于机械制造、模具制造、航空航天等领域。
线切割的原理
工作原理
利用电火花放电的原理,将金属 材料按预定轨迹进行切割。
加工过程
首先在工件上放置铜丝或钢丝,然 后通过电火花放电产生高温将金属 材料熔化,最后将熔化的金属冲刷 出去完成切割。
数控高速走丝电火花线切割加工实训教程

典型零件加工工艺实例
01
02
03
钢板零件加工
针对钢板零件,选择合适 的电极丝和放电参数,进 行高效、精确的切割加工 。
铝合金零件加工
针对铝合金材料,调整放 电参数和电极丝张力,实 现高质量的切割效果。
复杂形状零件加工
对于具有复杂形状的零件 ,采用多次切割、变换切 割角度等方法,确保加工 精度和表面质量。
实训要求
学生应熟悉数控高速走丝电火花线切割机床的基本操作,掌 握编程方法、电极丝安装与调整、工件装夹与定位、加工工 艺参数设置等技能,能够独立完成简单工件的加工。
安全操作规程
安全防护
在操作前,必须穿戴好防护用品,如工作服、安全帽、防 护眼镜等。禁止穿戴宽松衣物、长发未束等不安全装束进 行操作。
规范操作
05
实训项目设计与实施
实训项目设计思路及要求
01
设计思路
02
基于工作过程系统化的课程设计理念
以典型工作任务为载体Biblioteka 03实训项目设计思路及要求
明确实训目标,突出能力 培养
设计要求
理论与实践相结合
01
03 02
实训项目设计思路及要求
注重知识、技能和态度的整合
强化安全意识,规范操作行为
实训项目实施步骤与方法
工作原理及工作流程
工作原理
利用脉冲放电对工件进行电蚀加 工,通过钼丝与工件间的放电产 生高温,使工件局部熔化或气化 ,从而达到切割目的。
工作流程
编程→输入程序→机床准备→工 件装夹→对刀→启动加工→监控 加工过程→结束加工→卸下工件 。
关键部件及功能介绍
数控装置
接收并处理加工指令,控制各轴运动 ,实现加工过程的自动化。
数控电火花线切割技术
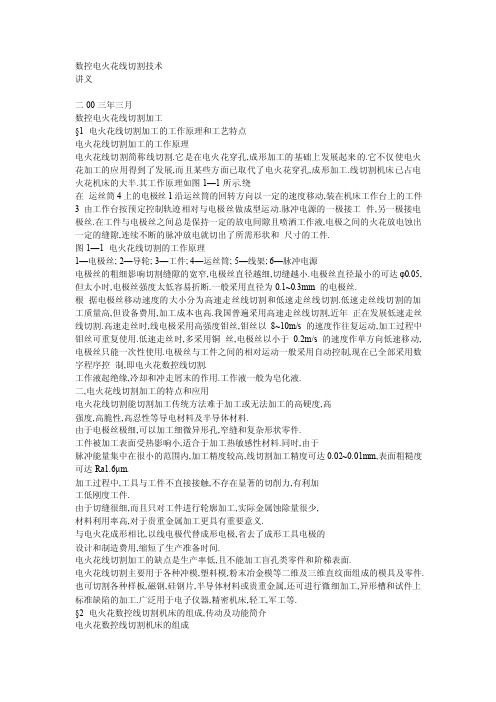
数控电火花线切割技术讲义二00三年三月数控电火花线切割加工§1 电火花线切割加工的工作原理和工艺特点电火花线切割加工的工作原理电火花线切割简称线切割.它是在电火花穿孔,成形加工的基础上发展起来的.它不仅使电火花加工的应用得到了发展,而且某些方面已取代了电火花穿孔,成形加工.线切割机床已占电火花机床的大半.其工作原理如图1—1所示.绕在运丝筒4上的电极丝1沿运丝筒的回转方向以一定的速度移动,装在机床工作台上的工件3由工作台按预定控制轨迹相对与电极丝做成型运动.脉冲电源的一极接工件,另一极接电极丝.在工件与电极丝之间总是保持一定的放电间隙且喷洒工作液,电极之间的火花放电蚀出一定的缝隙,连续不断的脉冲放电就切出了所需形状和尺寸的工件.图1—1 电火花线切割的工作原理1—电极丝; 2—导轮; 3—工件; 4—运丝筒; 5—线架; 6—脉冲电源电极丝的粗细影响切割缝隙的宽窄,电极丝直径越细,切缝越小.电极丝直径最小的可达φ0.05,但太小时,电极丝强度太低容易折断.一般采用直径为0.1~0.3mm 的电极丝.根据电极丝移动速度的大小分为高速走丝线切割和低速走丝线切割.低速走丝线切割的加工质量高,但设备费用,加工成本也高.我国普遍采用高速走丝线切割,近年正在发展低速走丝线切割.高速走丝时,线电极采用高强度钼丝,钼丝以8~10m/s的速度作往复运动,加工过程中钼丝可重复使用.低速走丝时,多采用铜丝,电极丝以小于0.2m/s的速度作单方向低速移动,电极丝只能一次性使用.电极丝与工件之间的相对运动一般采用自动控制,现在已全部采用数字程序控制,即电火花数控线切割.工作液起绝缘,冷却和冲走屑末的作用.工作液一般为皂化液.二,电火花线切割加工的特点和应用电火花线切割能切割加工传统方法难于加工或无法加工的高硬度,高强度,高脆性,高忍性等导电材料及半导体材料.由于电极丝极细,可以加工细微异形孔,窄缝和复杂形状零件.工件被加工表面受热影响小,适合于加工热敏感性材料.同时,由于脉冲能量集中在很小的范围内,加工精度较高,线切割加工精度可达0.02~0.01mm,表面粗糙度可达Ra1.6μm.加工过程中,工具与工件不直接接触,不存在显著的切削力,有利加工低刚度工件.由于切缝很细,而且只对工件进行轮廓加工,实际金属蚀除量很少,材料利用率高,对于贵重金属加工更具有重要意义.与电火花成形相比,以线电极代替成形电极,省去了成形工具电极的设计和制造费用,缩短了生产准备时间.电火花线切割加工的缺点是生产率低,且不能加工盲孔类零件和阶梯表面.电火花线切割主要用于各种冲模,塑料模,粉末冶金模等二维及三维直纹面组成的模具及零件.也可切割各种样板,磁钢,硅钢片,半导体材料或贵重金属,还可进行微细加工,异形槽和试件上标准缺陷的加工.广泛用于电子仪器,精密机床,轻工,军工等.§2 电火花数控线切割机床的组成,传动及功能简介电火花数控线切割机床的组成电火花数控线切割机床由主机,数控装置,脉冲电源装置等三部分组成.(1)主机部分由工作台,运丝装置,丝架,锥度装置,夹具,操纵盒,工作液箱,床身,防水罩等组成.工作台和锥度装置均可在水平面内移动,工作台的移动轴称为X轴,Y轴,锥度装置的移动轴称为U轴,V轴.切割带锥度工件时,工作台和锥度装置必须同时移动,从而使电极丝相对于工件有一定的倾斜.把X,Y,U,V四轴同时移动称作四轴联动.操纵盒上设有机床的常用开关. (2)数控装置作为机床的编程,控制系统,其内配备有486以上的微机,装有线切割专用软件,通过操作线切割加工软件,能够实现绘制线切割加工轨迹图,进行自动编程并对线切割加工的全过程进行自动控制.也可以利用"Auto CAD"或"电子图板"等常用绘图软件绘制线切割加工轨迹图.(3)脉冲电源装置为线切割机床提供符合要求的脉冲电源.脉冲电源装置可单独设置,也可与数控装置合并在一个控制柜内.脉冲电源装置上设有各项脉冲参数选择按钮(旋钮).图1-2是FW-1型电火花数控线切割机床外形图.其主要技术参数如下表:主机外形尺寸mm1615×1222×1630工作台尺寸(长×宽)mm650×420X行程mmY行程mmZ行程mmU行程mmV行程mm35032015018(±9)18(±9)工作台最大承重Kg200最大切割厚度mm200最大切割锥度±3.(50mm厚)脉冲当量mm0.001最佳表面粗糙度Ra2.5μm电极丝(钼丝)直径mmφ0.12~0.20图1-2 线切割机床外观图1—动丝筒; 2—线架; 3—锥度装置; 4—电极丝; 5—工作台;6—工作液箱; 7—床身;8—操纵盒; 9—控制柜二,数控线切割机床的传动系统采用步进电机带动滚珠丝杠传动,如图1—3.工作台的传动路线为:X向控制系统发出进给脉冲——步进电机A——齿轮/齿轮——丝杠1—螺母1.Y向控制系统发出进给脉冲——步进电机B——齿轮/齿轮——丝杠2—螺母2.图1-3 线切割机床的传动控制系统每发出一个脉冲,工作台就移动0.001㎜.通过X,Y向两个摇手柄也可以使工作台实现X,Y向移动.运丝装置的传动路线为:运丝电机C——联轴节——运丝筒高速旋转——齿轮/齿轮——丝杠3——螺母3带动拖板——行程开关.运丝装置带动电极丝按一定的速度运行,并将电极丝整齐地饶在运丝筒上,行程开关控制运丝筒的正反转.线架运丝筒旋转带动电极丝往返运动,排丝轮,导轮保持电极丝轨迹,导电块通电.通过手柄转动丝杠,带动上悬臂上下移动.锥度装置位于线架上悬臂的头部,两个步进电机分别控制锥度装置作U,V两个方向运动,实现锥度切割.三,数控线切割机床控制系统功能特点:FW—1型数控线切割机床是数控高速走丝线切割机,采用计算机控制,可X,Y,U,V四轴联动,能与其它计算机和控制系统方便地交换数据,放电参数可自动选取与控制,采用国际通用的ISO代码编程,亦可使用3B/4B格式,配有CAD/CAM系统.主要系统功能如下:·镜像加工·常规锥度切割·比例缩放·上下异形切割·单段运行·四轴联动切割·程序编辑·自动电极丝半径补偿·模拟运行·加工条件自动转换· 1/2 移动·丝杠螺距补偿·接触感知·丝找正·公英制转换·图形实时跟踪·自动找孔中心·中,英,印尼,日,葡,法,西班牙文界面·图形描画·各模块的直接进入,操作快捷· X-Y轴交换·在线操作提示,使用方便·子程序调用§3 数控线切割加工的操作方法与其他机床相比,数控线切割机床的操作部位较多.按其操作部位不同可分为主机操作,计算机程控操作,脉冲电源参数的选择等.以FW—1型数控线切割机床为例分别介绍.主机操作主机的操作包括绕装电极丝,装夹工件和各种开关的操作.1,绕装电极丝绕装电极丝是指将一定长度的电极丝通过线架上各导轮后整齐排列在运丝筒上,以保证电极丝能在线架上作往复运动.上丝前应根据工件高度调整好线架高度,电极丝的松紧应当合适,且要保证电极丝与工作台垂直.2,装夹工件数控高速走丝线切割的装夹特点:(1) 由于快走丝切割的加工作用力小,不象金属切削机床要承受很大的切削力,因而其装夹夹紧力要求不大,有的地方还可用磁力夹具定位.(2) 快走丝切割的工作液是靠高速运行的丝带入切缝的,不象慢走丝那样要进行高压冲水,因此对切缝周围的材料余量没有要求,便于装夹.(3) 线切割是一种贯通加工方法,因而工件装夹后被切割区域要悬空于工作台的有效切割区域,因此一般采用悬臂支撑或桥式支撑方式装夹.工件装夹的一般要求工件的定位面要有良好的精度,一般以磨削加工过的面定位为好.切入点要导电.热处理件要充分回火去应力,平磨件要充分退磁.工件装夹的位置应利于工件找正,并应与机床的行程相适,夹紧螺钉高度要合适,避免干涉到加工过程.对工件的夹紧力要均匀,不得使工件变形和翘起.加工精度要求较高时,工件装夹后,必须用百分表找正.工件装夹完毕,要清除干净工作台面上的一切杂物.3,开关主机除设有电源总开关,急停开关,强电开关外,还设有手控盒,其上有操作停止开关OFF,工作液泵开关PUMP,运丝筒开关WR,暂停开关HALT等,根据需要操作即可.二,加工条件的选择加工条件的选用包括脉冲电源参数的选择,工作液的选择,电极丝的选择.1,脉冲电源参数的选择波形(GP)的选择数控线切割有两种波形可供选择:"0"为矩形波脉冲;"1"为分组脉冲.A:矩形波:波形如图1-3,矩形波加工效率高,加工范围广,加工稳定性好,是快走丝线切割常用的加工波形.B:分组脉冲:波形如图1-4,分组波适于薄工件的加工,精加工较稳定.脉宽(ON)的选择图1 - 3本机脉宽的值为(ON+1)μS,最大为32μS.在特定的工艺条件下,脉宽增加,切割速度提高,表面粗糙度增大,这个趋势在脉宽增加的初期,加工速度增加较快,但随着脉宽的进一步增大,加工速度的增大相对平缓,粗糙度变化趋势也一样.这是因为单脉冲脉宽过大,也就是单脉冲放电时间过长,会使局部温度升高,形成对侧边的加工量增大,热量散发快,因此减缓了加工速度.通常情况下,脉图1 - 4宽的取值要考虑工艺指标及工件的材质,厚度.如果对表面粗糙度要求较高,工件材质易加工,厚度适中,脉宽取值较小,一般在3—10μS.中,粗加工,工件材质切割性能差,较厚时,脉宽取值一般为10—25μS.脉间(OFF)的选择本机脉间的值为(OFF+1)×5Μs,最大值160μS.在特定的工艺条件下,脉间减小,切割速度增大,表面粗糙度增大不多.这表明脉间对加工速度影响较大,而对表面粗糙度影响较小.但脉间不能太小,否则消电离不充分,电蚀产物来不及排除将使加工变得不稳定,易烧伤工件并断丝.脉间太大也会导致不能连续进给,使加工变的不稳定.通常难加工,厚度大,排屑不利的工件,脉间应选长一些,为脉宽的5—8倍较合适.对于加工性能好,厚度不大的工件,脉间可选脉宽的3—5倍.脉间取值主要考虑加工稳定,防短路及排屑,在满足要求的前提下,通常减小脉间以取得较高的加工速度.功率管数(IP)的选择选择投入放电加工回路的功率管数,以0.5为基本选择单位,取值范围为0.5—9.5.管数的增,减决定脉冲峰值电流的大小,每只管子投入的峰值电流为5A,电流越大切割速度越高,表面粗糙度增大,放电间隙变大.一般情况下,中厚度精加工为3—4只管子,中厚度中加工,大厚度精加工为5—6只管子,大厚度中粗加工为6—9只管子. 间隙电压(SV)的选择用来控制伺服的参数,最大值为7.加工状态的好坏,与间隙电压取值密切相关.间隙电压取值过小,会造成放电间隙小,排屑不畅,易短路.反之,加工速度下降,对薄工件一般取01—02,对大厚度工件一般取03—04.电压V电压V,即加工电压值.有两种选择,"0"常压,一般加工时选用."1"低压,一般找正时选用.2,工作液的选择快走丝线切割选用的工作液是乳化液,乳化液具有一定的绝缘性能,良好的洗涤性能,良好的冷却性能和良好的防锈能力.3,电极丝的选择快走丝线切割的电极丝要反复使用,因此要有一定的韧性,抗拉强度和抗腐蚀能力.可用做快走丝电极丝的材料有:钨(W)丝,钼(Mo)丝,钨钼(W50Mo)丝等,常用的丝径有φ0.12,φ0.14,φ0.18,φ0.2几种,根据需要选用.三,计算机编程,控制部分的操作计算机编程,控制部分的操作方法取决于机床控制系统所使用的软件,机床生产厂家不同,所开发的软件各具特点,具体操作方法将有所不同.这里以北京阿奇FW- 1数控线切割的控制系统为例.系统在启动成功后,即出现如图1-5所示的手动模式主画面,系统所有的操作按钮,状态,图形显示全部在屏幕上实现.手动模式主画面与自动模式主画面可分为8大区域.[1]坐标显示区:分别用数字显示X,Y,Z,U,V轴的坐标.(注:Z轴为非数控,因此其坐标显示一直为0)[2]参数显示区:显示当前NC程序执行时一些参数的状态.[3]加工条件区:显示当前加工条件.[4]输入格式说明区:在手动方式下说明主要手动程序的输入格式;在自动方式执行时,显示加工轨迹.[5]点动速度显示区:显示当前点动速度.[6]功能键区:显示各F功能键所对应的模式.[7]模式显示区:显示当前模式.[8]执行区:在手动模式执行输入的程序.在自动模式为执行已在缓冲区的NC程序.各种操作命令均可用鼠标轨迹球或相应的按键完成.[1] [2]X 0.000Y 0.000Z 0.000U 0000.000 文件名: ACT ★V 0000.000 手动公英制:公制命令:绝对座标系:G54 嵌套:0X 镜像:OFF 重复:000Y镜像:OFF 补偿:G40轴交换:OFF 旋转:OFF丝半径:000 异形:OFF喷夜:OFF 运丝:OFF锥度:G50 断丝:NO锥度角: 000.000缩放比例: 001.000旋转角度: 000.000COND = ON OFF IP SV GP V C001 = 02 03 2.0 01 00 00┃输入格式:感知:G80 X–极限:G81 X–半程:G82 X [3]移动:G00X–10.G00X–10.Y–10.加工:C004G01X10.C104G01X10.Y10.点动速度:中速FW3.05置零起点中心找正条件参数CAM自动编程F1F2F3F4F5F6F7F8F9F10[8] [7] [6] [5] [4]图1-5 FW-1系统手动模式主画面四,具体操作步骤操作准备启动电源开关,让机床空载运行,观察其工作状态是否正常.按机床加工要求注油;添加或更换工作液,一般每隔10~15天更换一次为宜;决定是否调换电极丝.调整线架,根据工件的厚度选择相应的切割跨距.校正电极丝与夹具垂直.操作步骤开机.工件装夹.定位.此步只用于工件有定位要求的情况下.编程及加工程序送控制台.确定脉冲电源参数(当需要调整参数时,必须先关断高频脉冲输出).启动运丝电机,启动工作液泵.将控制柜高频脉冲置于"ON"状态.手摇工作台手柄,使电极丝与工件接近直到出现火花(已进行定位操作时此步必须省略).按"Enter"(回车)键,开始执行程序,进行加工.加工结束后应先关闭工作液泵电机,然后关闭运丝电机,检查X,Y坐标是否到终点.到终点时拆下工件清洗并检查质量;未到终点时应检查程序是否有错或控制台有否故障.注:机床操纵盒和控制柜控制面板上都有红色急停开关,工作中如有意外情况,按下此开关即可断电停机.§4 线切割加工的绘图编程方法目前,先进的数控线切割机床都有计算机绘图及自动编程功能.其具体操作方法由计算机控制系统内应用软件来确定.一,自动编程操作方法1.绘制图形在手动模式主画面下按F8,即进入线切割自动编程系统(SCAM),显示如图1-6.线切割自动编程系统CADCAM中文返回F1F2F3F4F5F6F7F8F9F10图1-6 SCAM主菜单画面主菜单画面功能键作用:F1 —进入CAD绘图; F2 —进入CAM主画面;F10 —返回到控制系统.在SCAM主菜单画面下按F1功能键进入CAD绘图软件.进入绘图软件后即可绘制零件图,并且可把该零件转换成加工路径状态.图1-7为CAD绘图环境的主画面.辅助绘图画图编辑一编辑二显示设定档案线切割CAM北京AGIE〈〈〈〉〉〉〈辅助〉〈画图〉〈编辑一〉〈编辑二〉〈显示〉〈设定〉〈挡案〉纸张设定齿轮阿螺线补偿路径C A M端点交点中点切点圆心四分垂直引入最近方向长度半径X Y C U无法载入基本范例图设定WRK挡:SCAM.WRK外载指令:'shell'已载入.@输入指令:图1-7 CAD绘图软件主画面屏幕共分八个区:1).状态区位于屏幕最上方的一行,用来显示目前所在之图层名称,各种操作模式的ON/OFF(记录,整点,轴向),目前光标所在位置坐标…等状态.2).绘图区位于屏幕中央,为屏幕中最大的区域,用来绘制图形.3).命令区位于屏幕下方,占有三行位置,用来下达命令,显示命令提示及显示执行结果.4).屏幕功能区位于屏幕的最右边,您可选取某项目来执行TurboCAD的命令,此菜单的项目及内容是由菜单文件所定义.5).下拉式菜单区位于屏幕的最上方,当您将光标移至屏幕的最上方时,此下拉式菜单的项目会立即出现,您可选取某菜单项,然后在下拉出的菜单中选取欲执行的命令,此下拉式菜单的项目及内容由菜单文件所定义.6).锁定功能定义区位于屏幕的下方,用来定义抓点锁定功能及其它常用的功能,以便绘图时能很方便且迅速的选取使用,目前此区域的定义是由系统内定,使用者是无法更改的.7).辅助命令区与屏幕命令表区相重叠,当您执行某些具有辅助命令的命令时,屏幕命令表立即消失改而显示此命令的辅助命令,您可选取所需的辅助命令来继续此命令之操作,当命令操作完毕后会恢复原先的屏幕命令表.8).功能键定义区位于屏幕的最下方,当您将光标移至屏幕下方时,此功能键定义会立即出现,此区域之定义是对应于键盘上之功能键F1~F10,此功能键定义区的目的是希望免除去记忆那些功能键的苦恼,您直接选取所需的功能键即可执行指定的功能.2.自动编程在CAD状态下,绘制好零件图后,下拉CAD的线切割菜单,选择正确,合理的"补偿量"和"线切路径",按回车键后,屏幕显示要切割的图形及切割方向.退出CAD系统返回到SCAM主菜单.在SCAM主菜单下按F2进入CAM画面,在此画面中,进行图形文件,参数设定和放电参数的设定,完成后按F键即进入绘图和生成NC代码画面. 线切割编程起始位置与切割路线要合理选择.选择切割编程起始位置与切割路线应以工件装夹位置为依据,再考虑工件切割过程中刚性的变化以及工件内是否存在残余应力等.图1-8是线切割路线与工件刚性变化的实例.夹持部分夹持部分(a) 不合理(b) 合理图1-8加工过程中,随着切割的进行,工件上需要切离的部分和夹持部分的连接也越来越少,工件刚度也大为降低,容易产生变形,影响加工精度.这种情形是比较普遍的,应采用合理的切割路线,使其得到改善.一般应将工件与其夹持部分相分割的路线,安排在切割总程序的末端.二,编程代码含义为了能读懂程序代码以及个别场合需要对程序进行修改时能够进行手动修改.下面简要介绍编程代码含义.一般数控切割机床编程系统采用的代码是国际通用ISO代码.其格式如下:G92 X Y :以相对坐标方式设定加工坐标起点;G27:设定XY/UV平面联动方式;G01:X Y (U V ):直线插补指令;XY表示在XY平面中以直线起点为坐标原点的终点坐标;UV表示在UV平面中以直线起点为坐标原点的终点坐标;G02 X Y I J :顺圆插补指令;G02 U V I J :以圆弧起点为坐标原点,XY(UV)表示终点坐标,IJ表示圆心坐标; G03 X Y I J :逆圆插补指令;M00:暂停指令;M02:加工结束指令;例如:图1-9,可编程如下:加工起点(0,30),顺时针方向切割.G92 X0 Y30000G01 X0 Y10000G02 X10000 Y-10000 I0 J-10000G01 X0 Y-20000G01 X20000 Y0G02 X0 Y-20000 I0 J-10000G01 X-40000 Y0G01 X0 Y40000G02 X10000 Y10000 I10000 J0 图1-9G01 X0 Y-10000M00M02附表:ISO代码一览表组代码功能组代码功能AG00快速移动,定位指令JG40取消电极补偿G01直线插补,加工指令G41电极左补偿G02顺时针圆弧插补指令G42电极右补偿G03逆时针圆弧插补指令G45比例缩放G04暂停指令KG50取消锥度BG05X镜像G51左锥度G06Y镜像G52右锥度G07Z镜像LG54选择工作坐标系1G08X—Y交换G55选择工作坐标系2G09取消镜像和X—Y交换G56选择工作坐标系3CG11打开跳转(SKIP ON)G57选择工作坐标系4G12关闭跳转(SKIP OFF) G58选择工作坐标系5EG20英制G59选择工作坐标系6G21公制MG60上下异形OFFFG22软极限开关ON,未用G61上下异形ONG23软极限开关OFF,未用NG74四轴连动打开G25回最后设定的坐标系原点G75四轴连动关闭GG26图形旋转打开(ON)OG80移动轴直到接触感知G27图形旋转关闭(OFF)G81移动到机床的极限HG28尖角圆弧过渡G82移到圆点与现位置的一半G29尖角直线过渡PG90绝对坐标指令IG30取消过切G91增量坐标指令G31加入过切G92指定坐标原点I圆心X坐标SR轴转速,未用J圆心Y坐标T84启动液泵K圆心Z坐标T85关闭液泵L***子程序重复执行次数T86启动运丝机构P****指定调用子程序号T87关闭运丝机构M00暂停指令X轴指定M02程序结束Y轴指定M05忽略接触感知U轴指定M98子程序调用V轴指定M99子程序结束A指定加工锥度N****程序号C加工条件号O****程序号ON定义脉宽Q****跳转代码,未用OFF定义脉间R转角功能IP定义峰值电流RA图形或坐标旋转的角度SV定义间隙基准电压RI图形旋转的中心X坐标D***补偿码RJ图形旋转的中心Y坐标H***补偿码练习题1.线切割加工的工作原理是什么2.数控线切割机床由哪几部分组成各部分有何作用3.FW-1控制系统有哪些主要功能控制系统每发出一个进给脉冲,工作台移动多少距离4.四轴联动是指哪四轴5.解释下列代码的含义并反译成图形:G92 X-40000 Y0G02 X18292 Y33597 I40000 J0G03 X9078 Y15143 I-10854 J16799G01 X2664 Y37088G02 X19236 Y2922 I9966 J-828G01 X44581 Y-110208G01 X-43064 Y-12060G02 X-50787 Y38518 I-10787 J38518M00M026,由于线切割加工的工艺路线是一闭合回路,所以切割编程的起点和路途可以任意选择.这句话对吗为什么举例说明.。
数控电火花线切割机床的操作与加工课件
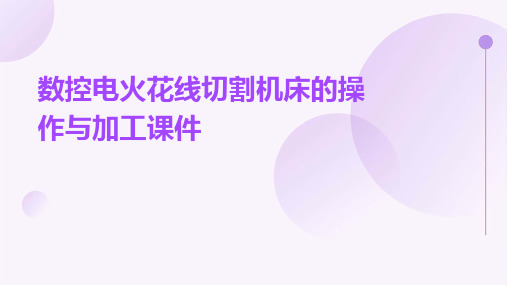
立柱
立柱是机床的重要支撑结构,用于安装上 下拖板、横向拖板及各轴。
横向拖板
横向拖板是机床的进给运动机构,可实现 工件的横向移动。
上下拖板
上下拖板是机床的主运动机构,可实现工 件的垂直升降。
工作台结构
台面
工作台面为钢制结构,可放置 工件并提供加工表面。
T型槽
工作台面设有多条T型槽,用于 安装和固定工件。
加工实例二:高精度零件的切割
总结词:通过精细化操作和误差控制,实现高 精度零件的精确切割。
01
02
详细描述
1. 准备工件与材料:选择优质材料,并确 保工件平整、无瑕疵。
03
04
2. 校准机床与工具:对机床进行精确校准 ,确保工具精度在要求范围内。
3. 精细化操作:运用微量Fra bibliotek给、补偿修正 等技巧,精确控制切割过程。
4. 执行切割程序:将程序输入数控电火花线切割机床 ,并监控切割过程,确保加工质量。
THANKS
感谢观看
加工精度异常
加工精度异常可能是由于控制系统故障、机械部件磨损等 原因造成的。排除方法包括检查控制系统、更换磨损部件 等措施。
加工表面质量差
加工表面质量差可能是由于冷却液不充分、电极丝振动等 原因造成的。排除方法包括增加冷却液流量、调整电极丝 张力等措施。
设备维护保养方法
定期检查
保持清洁
应定期检查数控电火花线切割机床的各个 部件是否正常,包括电源、电极丝、冷却 系统等部件。
切割速度
切割速度过快可能会导致 加工表面粗糙,而适当的 切割速度可以获得较好的 加工效果。
参数优化方法
根据加工需求和机床性能,综 合考虑各个参数的影响,调整 参数以达到最佳效果。
电火花线切割加工技术训练(ppt 57页)

转入 AUTOP
生成 3B程序
切割
电火花线切割加工基础知识
工艺准备和工艺过程
电火花线切割加工基础知识
线切割加工基本操作
①电源接通与关闭 ②上丝操作、穿丝操作 ⑤储丝筒行程调整 ⑥建立机床坐标系 ⑦程序的编制与校验 ⑧电极丝找正 ⑨加工脉冲参数的选择
电火花线切割加工基础知识
加工操作注意事项
①工作台架内不允许放置任何杂物 ②装夹工件应保证切割路径通畅 ③电极丝不要从导轮槽中脱出,与导电块良好接触 ④摇把使用后应立即取下,避免人身事故的发生 ⑤合理配置工作液浓度 ⑥切割时,控制喷嘴流量不要过大,以防飞溅 ⑦切割时要随时观察运行情况,排除事故隐患
电火花线切割加工基础知识
储丝筒上丝步骤(可自动或手动进行)
平面作品
线切割平面作内品孔、设内计腔等技在切巧割与时 方法 必须钻穿丝孔,穿丝切割。
在平面作品的设计制作中,要注意如下技巧与 方法:
1、线切割切割路线和切割起点、终点 2、开窗、孔洞问题
0.01mm
切割起 点
切割进 出路线
线切割平面作品设计技巧与方法
两个独立的图形的衔接问题
连接处2~3mm
线切割平面作品创新训练成本概念
成本的因素
创新训练自选题
◆综合设计自选作品 涉及机械工程、电气工程训练项目
◆工业产品 结合产品实践
计算材料费 不同加工方案加工时间比较
线切割平面作品创新训练步骤
◆提出方案,讨论比较 ◆设计平面创意作品,图形矢量化转换 ◆编制程序 ◆将编制的程序用局域网将零件的加工信息
传送到机床 ◆利用线切割机床完成作品 ◆分析总结作品,讨论影响加工工艺、加工
成本的因素
创新训练自选题
- 1、下载文档前请自行甄别文档内容的完整性,平台不提供额外的编辑、内容补充、找答案等附加服务。
- 2、"仅部分预览"的文档,不可在线预览部分如存在完整性等问题,可反馈申请退款(可完整预览的文档不适用该条件!)。
- 3、如文档侵犯您的权益,请联系客服反馈,我们会尽快为您处理(人工客服工作时间:9:00-18:30)。
数控电火花线切割培训教材一、数控电火花线切割加工概述数控电火花线切割加工(Wire Cat EDM)暨是数控加工也属于特种加工。
常用于加工冲压模具的凸、凹模,电火花成形机床的工具电极、工件样板、工具量规和细微复杂形状的小工件或窄缝等,并可以对薄片重叠起来加工以获得一致尺寸。
1、数控电火花线切割加工原理电火花线切割加工简称“线切割”。
它是利用移动的细金属丝(电极丝)作为工具电极,并在电极丝与工件间加以脉冲电压,利用脉冲放电的腐蚀作用对工件进行切割加工的。
在正负电极之间施加脉冲电压,并不断喷注一定绝缘性能的工作液,当两电极间的间隙达到一定距离时,脉冲电压将工作液击穿,产生火花放电。
在放电瞬间产生大量热能,使这一点工作表面局部微量金属材料立刻熔化、气化,飞溅到工作液中,形成固体金属微粒,被工作液带走。
这时在工件表面上便留下一个微小的凹坑,放电短暂停歇,两电极间的工作液处在绝缘状态。
紧接着,下一个脉冲电压又在两电极相对接近的另一点处击穿,产生火花放电,重复上述过程。
在保持电极丝与工件之间恒定放电间隙的条件下,一边蚀除工件金属,一边控制工件不断地向电极丝进给,就可沿着预定轨迹逐步将工件切割成形。
2、线切割加工特点ⅰ、采用线状电极切割工件,无需制造特定形状的工具电极,降低工具电极的设计和制造费用,缩短加工周期。
ⅱ、直接利用电能进行脉冲放电加工,便于实现自动化控制。
ⅲ、加工时电极丝与工件不接触,两者之间宏观作用力极小,不产生毛刺和明显刀痕等缺陷。
ⅳ、加工中电极丝的损耗极小,加工精度高,无须刃磨刀具,缩短辅助时间。
3、线切割机床的分类通常按电极丝的运行速度快慢,线切割机床可分为快走丝线切割机和慢走丝线切割机。
快走丝线切割机床应用比较广泛,具有结构简单、操作方便、可维护性好,加工费用低、占地面积小及性价比高等特点。
慢走丝线切割机床采用一次性电极丝,可多次切割,有利于提高加工精度和降低表面粗糙度,属于精密加工设备。
二、本厂模具车间线切割设备DK7732P 快走丝线切割机床三光DK7732P 快走丝线切割机床普光DK7725F 快走丝线切割机床三光DK7725F 快走丝线切割机床普光DK7763J 快走丝线切割机床三光HA320 快走丝线切割机床三光HA500 快走丝线切割机床三光BKDK 快走丝线切割机床普光FA20 慢走丝线切割机床日本三菱DK7632A SKDA 慢走丝线切割机床三光G3525S 慢走丝线切割机床庆鸿GA360S 线切割机床庆鸿三、线切割加工工艺特点1、模具材料对热处理的要求模具零件一般采用锻造毛坯,其线切割加工常在淬火与回火后进行。
由于存在残余应力的影响,工件局部可能在线切割过程中产生变形,影响加工精度。
为了减少这种影响,在设计时应选用锻造性能好、淬透性好及热处理变形小的材料,还要设定合理的热处理工艺并严格执行。
2、线切割加工路线的选择ⅰ、切割工件时应尽量避免从工件端面由外向里进刀,最好从坯料预制的穿丝孔开始加工。
ⅱ、加工路线应向远离工件夹具的方向进行,即将工件与其装夹部位分离的部分安排在切割线路的末端。
ⅲ、在一块毛坯上要切出两个以上工件时,为减小变形应从不同的穿丝孔开始加工。
ⅳ、加工轨迹与毛坯边缘距离应大于5mm,以防止因工件的结构强度差而发生变形。
ⅴ、避免沿工件端面切割,这样放电时电极丝单向受电火花冲击力,使电极丝运行不稳定,难以保证尺寸和表面精度。
3、穿丝孔位置的确定ⅰ、穿丝孔应选在容易找正,并在加工过程中便于检查的位置。
ⅱ、切割凹模等零件的表面时,一般穿孔丝位置也是加工基准,通常设置在工件对称中心。
大工件加工时,为了缩短切入行程,穿丝孔应设置在靠近加工轨迹的已知坐标点上。
ⅲ、在加工大型工件时,还应沿加工轨迹设置多个穿丝孔,以便发生断丝是能就近重新穿丝,再切入断丝点。
4、切入点位置的确定ⅰ、被切割工件各表面的粗糙度要求不同时,应在粗糙度要求较低的面上选择起点。
ⅱ、工件各面的粗糙度要求相同时,则尽量在截面图形的相交点上选择起点。
ⅲ、对于工件各切割面既无技术要求的差异又没有形面交点的工件,切入点尽量选择在便于钳工修复的位置上。
ⅳ、工件切入处应干净,尤其对热处理工件,切入处要去除积盐及氧化皮以保证导电。
5、工件的装夹与找正ⅰ、工件的装夹:线切割是一种贯穿加工方法,装夹工件时必须保证工件的切割部位悬空于机床工作台行程的允许围之。
一般以磨削加工过的面来定位,装夹位置应便于找正。
夹紧力不需太大但要求均匀。
选用夹具优先通用件或标准件。
ⅱ、工件找正:一般使用百分表找正,使工件的定位基准面分别与机床的工作台面和工作台的进给方向X、Y保持平行。
当工件切割轨迹与定位基准之间的相互位置精度要求不高时,可采用划线法找正。
6、电极丝的选择与对刀ⅰ、电极丝的选择:快走丝线切割使用钼丝慢走丝线切割使用黄铜丝ⅱ、对刀:对于加工要求较低的工件,可以采用目测法。
第二种方法是火花法,利用电极丝与工件在一定间隙下发生火花放电来确定电极丝的坐标位置。
第三种方法是接触感知法,利用电极丝与工件基准面由绝缘到短路的瞬间,两者间电阻值突然变化的特点来确定电极丝接触到了工件,并在接触点自动停下来,显示该点的坐标,即为电极丝中心的坐标值。
利用该原理还可以实现自动找出孔的中心。
7、脉冲参数的选择ⅰ、脉冲宽度:是指脉冲电流的持续时间,与放电能量成正比,在其他加工条件相同的情况下,脉冲宽度越宽切割速度就越高,此时加工较稳定,但放电间隙大,表面粗糙度大。
相反脉冲宽度越小,加工出的工件表面质量就越好,但切割效率就会下降。
ⅱ、脉冲间隔:是指脉冲电流的停歇时间,与放电能量成反比,其它条件不变,脉冲间隔越大,切割速度下降。
但有利于排除电蚀物,提高加工的稳定性。
当脉冲间隔减小到一定程度之后,电蚀物不能及时排除,饭店间隙的绝缘强度来不及恢复,破坏了加工的稳定性,使切割效率下降。
ⅲ、峰值电流:是指放电电流的最大值。
它和脉冲宽度对切割速度和表面粗糙度的影响相似,但程度更大些,放电电流过大,电极丝的损耗也随之增大容易造成断丝。
以上只是这些参数的基本选择方法,此外它与工件材料、工件厚度、进给速度、走丝速度及加工环境等都有密切的关系,需在实际加工过程中多加探索才能达到比较满意的效果。
8、补偿量的确定由于线切割加工是一种非接触性加工,受电极丝和火花放电间隙的影响,实际切割后工件的尺寸与工件所要求的尺寸不一致。
因此在编程时就要对原工件尺寸进行偏置,使电极丝实际运行的规迹与原工件轮廓偏移一定的距离。
计算公式:F=d/2+ad---电极丝直径a---单边放电间隙,一般取0.01~0.02mmHA系列电火花线切割机床安全操作规程1、机床操作前准备①、编制程序根据加工图纸要求,用AUTOCAD绘图软件进行绘图,绘图后生成DXF 文件格式放在网络共享盘。
然后在机床电脑将DXF文件读取出来生成切割程序格式,在显示器上校对。
对形状复杂的工件,应试切割样品供校对。
②、调整线架跨距根据工件的厚度不同来调整线架跨距,一般以上悬臂到零件表面距离为10mm左右为宜。
③、装夹工件将专用夹具固定在工作台面上,再将工件放在专用夹具上。
根据加工围确定工件适当位置,用压板及螺钉固定工件。
对加工余量较小或有特别要求的工件,必须精确调整工件与工作台纵、横方向移动的平行性。
④、穿丝及丝ⅰ、将拉紧的钼丝整齐的绕在储丝筒上(一般机床有专门的上丝机构),因钼丝具有一定的力,使上下导轮间的钼丝具有良好的平直度,确保加工精度和粗糙度。
所以加工前应检查钼丝的紧程度。
ⅱ、丝轮在线架的后部左上角处,不工作时,丝轮向上旋转一角度,以M4平端紧定螺钉挂好。
当利用丝轮工作时,线架的上、下悬臂距离大于190mm,否则丝轮与运丝轴承相碰。
此时应先检查刹车和停止开关是否工作可靠,否则容易发生安全事故,应特别注意。
ⅲ、对加工封闭型孔时,如:凹模、卸料板、固定板等,选择合理的切入部位,工件上应预置穿丝孔,钼丝应通过上导轮经过穿丝孔,再经下导轮后固定在储丝筒上。
此时应记下工作台的纵、横向(X、Y的座标)起点的刻度值。
⑤、校正钼丝的垂直度ⅰ、一般校法是将校直器在X、Y方向采用光透方法。
即X、Y方向上下光透一致即为垂直。
ⅱ、放电校正法:将校直器与工作台面之间放一平整的白纸,再将工件正极接到校直器上,启动高频及开动运行钼丝,分别用手摇动X、Y方向上的拖板,使钼丝靠近校直器产生放电,如上下放电一致即为垂直。
⑥、检查主机、控制系统及高频电源是否正常。
2、加工操作顺序将加工程序输送到机台电脑上;在机台电脑屏幕,将光标移动到“编程”,打开加工程序,生成加工轨迹。
在工艺数据库设置加工参数,生成ISO代码,保存ISO加工程序。
然后将光标移动到“加工”,点击“加工”开始工作。
加工结束后拆下工件。
3、安全操作注意事项①、开机时,先开运丝系统,后开工作液泵,避免工作液浸入导轮轴承。
停机时,应先关闭工作液泵,稍停片刻再停运丝系统。
②、操作员工须穿戴好劳动保护用品。
③、操作员工须接受专业培训,考核合格后才能上岗。
④、操作吊机作业前,必须检查吊机所使用的吊装工具是否完好。
⑤、机床故障严禁自行修理,必须由专业维修人员维修。
DK系列电火花线切割机床安全操作规程1、机床操作前准备①、编制程序根据加工图纸要求,用AUTOCAD绘图软件进行绘图,绘图后生成DXF 文件格式放在网络共享盘。
然后在机床电脑将DXF文件读取出来生成切割程序格式,在显示器上校对。
对形状复杂的工件,应试切割样品供校对。
②、调整线架跨距根据工件的厚度不同来调整线架跨距,一般以上悬臂到零件表面距离为10mm左右为宜。
③、装夹工件将专用夹具固定在工作台面上,再将工件放在专用夹具上。
根据加工围确定工件适当位置,用压板及螺钉固定工件。
对加工余量较小或有特别要求的工件,必须精确调整工件与工作台纵、横方向移动的平行性,并记下纵、横坐标值。
④、穿丝及丝ⅰ、将拉紧的钼丝整齐的绕在储丝筒上(一般机床有专门的上丝机构),因钼丝具有一定的力,使上下导轮间的钼丝具有良好的平直度,确保加工精度和粗糙度。
所以加工前应检查钼丝的紧程度。
ⅱ、丝轮在线架的后部左上角处,不工作时,丝轮向上旋转一角度,以M4平端紧定螺钉挂好。
当利用丝轮工作时,线架的上、下悬臂距离大于190mm,否则丝轮与运丝轴承相碰。
此时应先检查刹车和停止开关是否工作可靠,否则不安全,应特别注意。
ⅲ、对加工封闭型孔时,如:凹模、卸料板、固定板等,选择合理的切入部位,工件上应预置穿丝孔,钼丝应通过上导轮经过穿丝孔,再经下导轮后固定在储丝筒上。
此时应记下工作台的纵、横向(X、Y的坐标)起点的刻度值。
⑤、校正钼丝的垂直度ⅰ、一般校法是将校直器在X、Y方向采用光透方法。
即X、Y方向上下光透一致即为垂直。
ⅱ、放电校正法:将校直器与工作台面之间放一平整的白纸,再将工件正极接到校直器上,启动高频及开动运行钼丝,分别用手摇动X、Y方向上的拖板,使钼丝靠近校直器产生放电,如上下放电一致即为垂直。