模具行业十三五规划
2024年模具企业三年发展战略规划
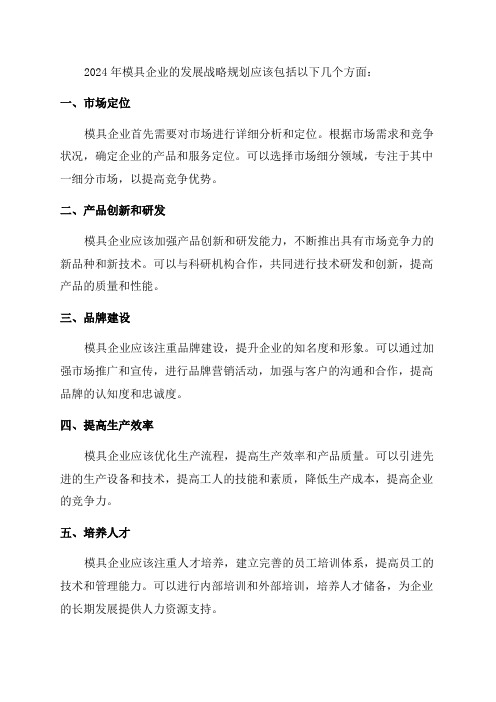
2024年模具企业的发展战略规划应该包括以下几个方面:一、市场定位模具企业首先需要对市场进行详细分析和定位。
根据市场需求和竞争状况,确定企业的产品和服务定位。
可以选择市场细分领域,专注于其中一细分市场,以提高竞争优势。
二、产品创新和研发模具企业应该加强产品创新和研发能力,不断推出具有市场竞争力的新品种和新技术。
可以与科研机构合作,共同进行技术研发和创新,提高产品的质量和性能。
三、品牌建设模具企业应该注重品牌建设,提升企业的知名度和形象。
可以通过加强市场推广和宣传,进行品牌营销活动,加强与客户的沟通和合作,提高品牌的认知度和忠诚度。
四、提高生产效率模具企业应该优化生产流程,提高生产效率和产品质量。
可以引进先进的生产设备和技术,提高工人的技能和素质,降低生产成本,提高企业的竞争力。
五、培养人才模具企业应该注重人才培养,建立完善的员工培训体系,提高员工的技术和管理能力。
可以进行内部培训和外部培训,培养人才储备,为企业的长期发展提供人力资源支持。
六、加强合作与合作模具企业应该主动寻求合作和合作机会。
可以与供应商、客户、科研机构等建立紧密的合作关系,共同开展研究和开发活动,优化资源配置,提高企业的综合竞争力。
七、加强企业文化建设模具企业应该注重企业文化建设,树立良好的企业形象和价值观念。
可以通过组织员工活动、加强内部沟通、建立健全的激励机制等方式,打造积极向上、团结互助的企业文化氛围。
八、加强质量管理模具企业应该加强质量管理,确保产品的质量和可靠性。
可以建立完善的质量管理体系,规范生产流程,加强质量检验和控制,提高产品的质量标准和用户满意度。
以上是2024年模具企业三年发展战略规划的一些建议,企业可以根据实际情况进行调整和完善,以实现可持续发展和长期竞争力。
模具行业计划书范文怎么写
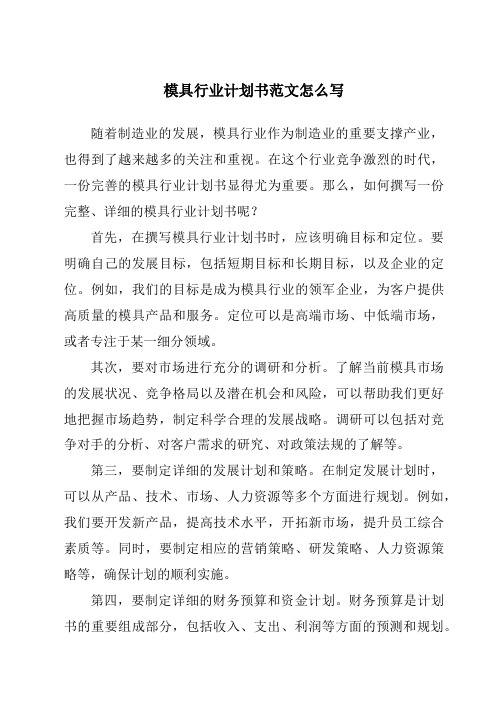
模具行业计划书范文怎么写随着制造业的发展,模具行业作为制造业的重要支撑产业,也得到了越来越多的关注和重视。
在这个行业竞争激烈的时代,一份完善的模具行业计划书显得尤为重要。
那么,如何撰写一份完整、详细的模具行业计划书呢?首先,在撰写模具行业计划书时,应该明确目标和定位。
要明确自己的发展目标,包括短期目标和长期目标,以及企业的定位。
例如,我们的目标是成为模具行业的领军企业,为客户提供高质量的模具产品和服务。
定位可以是高端市场、中低端市场,或者专注于某一细分领域。
其次,要对市场进行充分的调研和分析。
了解当前模具市场的发展状况、竞争格局以及潜在机会和风险,可以帮助我们更好地把握市场趋势,制定科学合理的发展战略。
调研可以包括对竞争对手的分析、对客户需求的研究、对政策法规的了解等。
第三,要制定详细的发展计划和策略。
在制定发展计划时,可以从产品、技术、市场、人力资源等多个方面进行规划。
例如,我们要开发新产品,提高技术水平,开拓新市场,提升员工综合素质等。
同时,要制定相应的营销策略、研发策略、人力资源策略等,确保计划的顺利实施。
第四,要制定详细的财务预算和资金计划。
财务预算是计划书的重要组成部分,包括收入、支出、利润等方面的预测和规划。
资金计划则是确保计划执行的关键,要明确资金需求、资金来源以及资金使用的安排,确保资金的合理利用和充分保障。
最后,要将计划书进行完整的整理和总结。
计划书的整体结构应该清晰、简洁,重点突出,逻辑严谨。
可以根据不同章节的内容进行分节,采用标题、段落、图表等形式进行布局。
计划书中的内容应该具有可操作性和可衡量性,能够清晰地指导实际操作和监督评估。
模具行业计划书的撰写需要全面了解行业情况和内外部环境,同时也需要结合企业自身的实际情况和目标,制定出科学合理的发展战略和计划。
只有在不断完善和执行计划的过程中,才能够实现模具行业的可持续发展和长远目标。
模具行业十三五规划
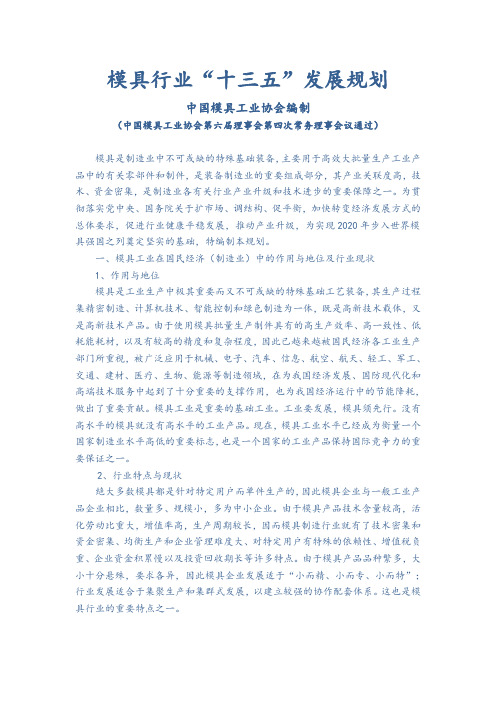
模具行业“十三五”发展规划中国模具工业协会编制(中国模具工业协会第六届理事会第四次常务理事会议通过)模具是制造业中不可或缺的特殊基础装备,主要用于高效大批量生产工业产品中的有关零部件和制件,是装备制造业的重要组成部分,其产业关联度高,技术、资金密集,是制造业各有关行业产业升级和技术进步的重要保障之一。
为贯彻落实党中央、国务院关于扩市场、调结构、促平衡,加快转变经济发展方式的总体要求,促进行业健康平稳发展,推动产业升级,为实现2020年步入世界模具强国之列奠定坚实的基础,特编制本规划。
一、模具工业在国民经济(制造业)中的作用与地位及行业现状1、作用与地位模具是工业生产中极其重要而又不可或缺的特殊基础工艺装备,其生产过程集精密制造、计算机技术、智能控制和绿色制造为一体,既是高新技术载体,又是高新技术产品。
由于使用模具批量生产制件具有的高生产效率、高一致性、低耗能耗材,以及有较高的精度和复杂程度,因此已越来越被国民经济各工业生产部门所重视,被广泛应用于机械、电子、汽车、信息、航空、航天、轻工、军工、交通、建材、医疗、生物、能源等制造领域,在为我国经济发展、国防现代化和高端技术服务中起到了十分重要的支撑作用,也为我国经济运行中的节能降耗,做出了重要贡献。
模具工业是重要的基础工业。
工业要发展,模具须先行。
没有高水平的模具就没有高水平的工业产品。
现在,模具工业水平已经成为衡量一个国家制造业水平高低的重要标志,也是一个国家的工业产品保持国际竞争力的重要保证之一。
2、行业特点与现状绝大多数模具都是针对特定用户而单件生产的,因此模具企业与一般工业产品企业相比,数量多、规模小,多为中小企业。
由于模具产品技术含量较高,活化劳动比重大,增值率高,生产周期较长,因而模具制造行业就有了技术密集和资金密集、均衡生产和企业管理难度大、对特定用户有特殊的依赖性、增值税负重、企业资金积累慢以及投资回收期长等许多特点。
由于模具产品品种繁多,大小十分悬殊,要求各异,因此模具企业发展适于“小而精、小而专、小而特”;行业发展适合于集聚生产和集群式发展,以建立较强的协作配套体系。
模具2024年度工作计划

模具2024年度工作计划一、引言随着制造业的快速发展,模具行业作为先进制造业的重要支撑,发挥着越来越重要的作用。
为了适应不断变化的市场需求和提高企业的竞争力,我们制定了2024年度模具工作计划。
本计划将紧紧围绕提高质量、提升技术、优化管理、创新发展等方面,全面推动模具企业的健康发展。
二、市场分析1. 市场需求分析根据对市场的调研,预计2024年度模具市场需求将保持稳定增长,主要体现在汽车、家电、电子产品等行业对模具的需求增加。
2. 市场竞争分析模具行业竞争激烈,市场上存在众多的竞争对手,包括大型企业和小型企业。
为了提高竞争力,我们需要加强技术研发,提高产品质量,降低成本,提供更好的售后服务。
三、2024年度工作目标1. 销售目标在2024年,我们的销售目标是实现年销售额增长20%,提高市场占有率。
2. 技术创新目标加强技术研发,提升产品设计及制造工艺,提高产品质量和性能。
力争在2024年推出新产品或新工艺,提升公司的竞争力。
3. 生产目标提高生产效率,降低生产成本,保证产品质量。
力争在2024年达到产品生产周期缩短10%,每月生产能力提高20%。
4. 人才培养目标加强人才培养和引进,提升团队核心竞争力。
力争在2024年培养出一批技术精湛、专业素质过硬的高级工程师和技术管理人才。
5. 质量目标提高产品质量和生产工艺的稳定性,力争在2024年通过ISO9001质量管理体系认证,并在质量排名中进入前五名。
四、具体工作计划1. 技术创新加大技术研发投入,加强市场调研和产品研发,推动新产品开发。
优化产品设计、工艺流程和制造工艺,提高产品质量和性能。
2. 设备更新与升级对现有设备进行评估,更新老旧设备,引进新一代先进设备,提高生产效率和产品质量。
3. 供应链管理建立完善的供应链管理体系,优化供应商选择和管理,确保原材料的质量和交货准时。
4. 质量管理加强质量管理,推行全面质量管理,确保产品质量符合客户要求。
模具广泛应用于哪些行业
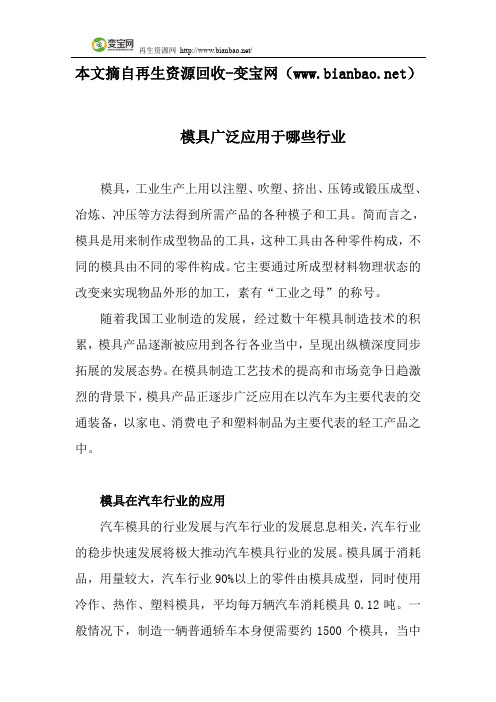
本文摘自再生资源回收-变宝网()模具广泛应用于哪些行业模具,工业生产上用以注塑、吹塑、挤出、压铸或锻压成型、冶炼、冲压等方法得到所需产品的各种模子和工具。
简而言之,模具是用来制作成型物品的工具,这种工具由各种零件构成,不同的模具由不同的零件构成。
它主要通过所成型材料物理状态的改变来实现物品外形的加工,素有“工业之母”的称号。
随着我国工业制造的发展,经过数十年模具制造技术的积累,模具产品逐渐被应用到各行各业当中,呈现出纵横深度同步拓展的发展态势。
在模具制造工艺技术的提高和市场竞争日趋激烈的背景下,模具产品正逐步广泛应用在以汽车为主要代表的交通装备,以家电、消费电子和塑料制品为主要代表的轻工产品之中。
模具在汽车行业的应用汽车模具的行业发展与汽车行业的发展息息相关,汽车行业的稳步快速发展将极大推动汽车模具行业的发展。
模具属于消耗品,用量较大,汽车行业90%以上的零件由模具成型,同时使用冷作、热作、塑料模具,平均每万辆汽车消耗模具0.12吨。
一般情况下,制造一辆普通轿车本身便需要约1500个模具,当中有接近1000个的冲压模具和超过200个的内饰件模具。
据专业机构测算,汽车模具占模具行业的市场份额约1/3,而根据国家统计局的统计数据,2017年我国汽车模具的销售收入为2663.42亿元,据此测算2017年中国汽车模具市场规模达到888亿元。
到2023年,中国汽车产量将达到近4182万辆,年均增速在6.0%左右,而对于汽车模具的需求将达到500吨左右。
模具在消费电子行业的应用随着人们消费水平的日益提升,消费电子产品的需求不断扩大,产品更新换代加速,消费电子产品市场规模持续增长,同时带动模具相关产业快速向前发展。
数据显示,仅2015年全球消费电子产品市场在智能手机、平板电脑、个人电脑等等终端设备的快速增长的拉动下,达到近7900亿欧元,较上年增长1.5%。
而我国电子信息产业规模的持续增长,形成了产品门类相对齐全的制造业体系和产业配套基础。
模具行业的年度总结(3篇)
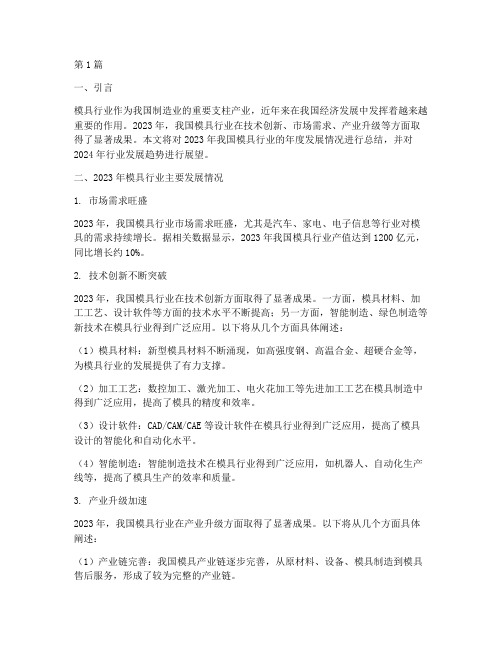
第1篇一、引言模具行业作为我国制造业的重要支柱产业,近年来在我国经济发展中发挥着越来越重要的作用。
2023年,我国模具行业在技术创新、市场需求、产业升级等方面取得了显著成果。
本文将对2023年我国模具行业的年度发展情况进行总结,并对2024年行业发展趋势进行展望。
二、2023年模具行业主要发展情况1. 市场需求旺盛2023年,我国模具行业市场需求旺盛,尤其是汽车、家电、电子信息等行业对模具的需求持续增长。
据相关数据显示,2023年我国模具行业产值达到1200亿元,同比增长约10%。
2. 技术创新不断突破2023年,我国模具行业在技术创新方面取得了显著成果。
一方面,模具材料、加工工艺、设计软件等方面的技术水平不断提高;另一方面,智能制造、绿色制造等新技术在模具行业得到广泛应用。
以下将从几个方面具体阐述:(1)模具材料:新型模具材料不断涌现,如高强度钢、高温合金、超硬合金等,为模具行业的发展提供了有力支撑。
(2)加工工艺:数控加工、激光加工、电火花加工等先进加工工艺在模具制造中得到广泛应用,提高了模具的精度和效率。
(3)设计软件:CAD/CAM/CAE等设计软件在模具行业得到广泛应用,提高了模具设计的智能化和自动化水平。
(4)智能制造:智能制造技术在模具行业得到广泛应用,如机器人、自动化生产线等,提高了模具生产的效率和质量。
3. 产业升级加速2023年,我国模具行业在产业升级方面取得了显著成果。
以下将从几个方面具体阐述:(1)产业链完善:我国模具产业链逐步完善,从原材料、设备、模具制造到模具售后服务,形成了较为完整的产业链。
(2)产业集群发展:我国模具产业集群发展迅速,如宁波、东莞、苏州等地已成为国内外知名的模具产业基地。
(3)品牌建设:我国模具企业在品牌建设方面取得了显著成果,一批具有国际竞争力的模具品牌脱颖而出。
4. 国际市场拓展2023年,我国模具企业在国际市场拓展方面取得了积极成果。
以下将从几个方面具体阐述:(1)出口增长:我国模具出口额持续增长,主要出口到欧美、东南亚、中东等地区。
中国模具行业相关政策法规及行业相关标准汇总分析
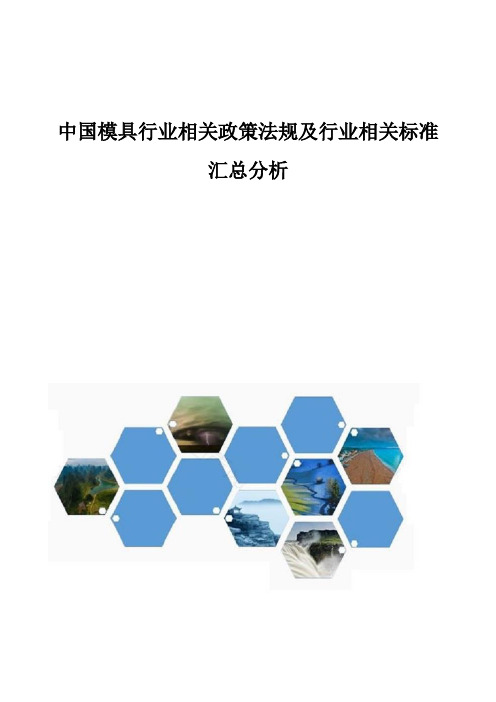
中国模具行业相关政策法规及行业相关标准汇总分析模具是指工业生产上用以注塑、吹塑、挤出、压铸或锻压成型、冶炼、冲压等方法得到所需产品的各种模子和工具。
我国模具工业在经历了半个多世纪的发展后已有了较大的提高,发展速度十分迅速。
总的来说,我国模具设计与制造技术的发展经历了手工作坊制造的萌芽阶段、工业化生产的快速发展及产品竞争阶段和现代化生产的品牌竞争阶段。
—、模具产业链分析——模具行业其上游行业主要为原材料行业,主要包括原材料模具钢、塑料橡胶等以及铸造机、机床等配套设备。
——模具行业中游为模具研发、生产及销售行业,包括金属模具与非金属模具(塑料模具及无机非金属材料)。
——模具不是最终消费品,其主要用户为下游制造业生产企业,主要包括汽车、家电、消费电子、航空航天、OA设备等行业。
模具行业产业链结构资料来源:立鼎产业研究中心整理模具行业具有覆盖面广、带动性强的特点,因此模具行业的产品需求不是由某个行业的需求单独决定的,而是取决于下游行业,乃至国民经济的整体发展。
下游行业的发展对模具行业具有较大的拉动作用。
同时,模具行业的发展也会带动了下游行业的发展。
随着模具行业技术水平的提高和加工精度的提升,会使得下游行业提升产品质量和性能,从而推动下游行业的发展。
二、模具行业管理体制——行政主管部门国家发改委是行业的行政主管部门,负责制订产业政策,提出产业发展战略与规划,指导行业技术法规和行业标准的拟订,推动高技术发展,实施技术进步和产业现代化的宏观指导等。
国家工业和信息化部负责拟订并实施工业行业规划、产业政策和标准,监测工业行业日常运行,推动重大技术装备发展和自主创新等。
——行业协会行业的自律性组织为中国模具工业协会、中国机械工业联合会。
中国模具工业协会的主要职责为掌握模具行业的现状,研究行业发展方向、战略和政策目标,提出行业发展政策建议,协助有关部门制定模具产品的技术标准,提高模具工业的标准化、专业化、信息化、商品化水平,组织技术经济信息交流网络,分析经济信息资料与提供信息服务,组织举办相关国内外展览会、交流会,交流推广模具新技术、新工艺、新材料及企业改革管理经验,培训技术和管理人才,推广新技术,开展对外经济技术交流与合作等。
2022年我国模具行业现状分析

2022年我国模具行业现状分析近几年来,因模具行业的各方面缘由,模具业进展面临很多逆境,随着技术的进步,模具行业进展迎来机遇与挑战,详细如何呢?下面请看我为你整理的2022年我国模具行业现状分析:今年,是中国装备制造行业实施“十三五”规划的重要一年,是供应侧结构性改革的深化之年。
面对国内外依旧简单的经济环境,装备制造行业各大协会及企业,励精图治、迎难而上,坚守在行业和企业的岗位上,以迎接曙光的到来。
模具工业水平已经成为衡量一个国家制造业水平凹凸的重要标志,也是一个国家的工业产品保持国际竞争力的重要保证之一。
模具关联性高、涉及面广。
我国目前通过模具成形制造也称等材制造的金属制品约为8000万吨,与切削加工减材制造的数量相当;而7500万吨左右的塑料制品和600万吨的橡胶制品,几乎全部由模具成形制造;模具被称为产品制造业的效益放大器仅2022年统计,2100亿的模具支撑了23万亿元的产品制造业。
模具行业已完成了技能型向技术复合型的转变,由模具制造向模具+技术服务过渡,模具企业不仅仅是模具供应商还成为集成技术服务商。
“项目式”、“工程式”管理代替“订单式”管理,模具产品在整个制造生命周期中是个共同探讨修改的过程;模具企业在交付模具产品的同时要交付设计、工艺、分析的数字化过程,模具企业供应的产品是模具与模具成形工艺的一体化方案,是完成产品从设计到制造的产业化关键结点,模具企业不仅仅是模具供应商还成为了集成技术服务商。
我国模具出口从2022年的10亿美元扩大到2022年超过50亿美元,出口模具达140个国家地区,国际产能合作已显现出我们的竞争力,已成为国际模具舞台的重要力气。
模具行业的技术创新走在了制造业的前列。
“十二五”期间模具行业授权专利达到105789项,其中创造专利9393项;“十三五”模具行业连续实施项目带动战略,提高企业作为技术创新主体的力量和企业自主创新力量;重点进展高技术含量、高附加值的高品质模具产品。
发展模具行业政策
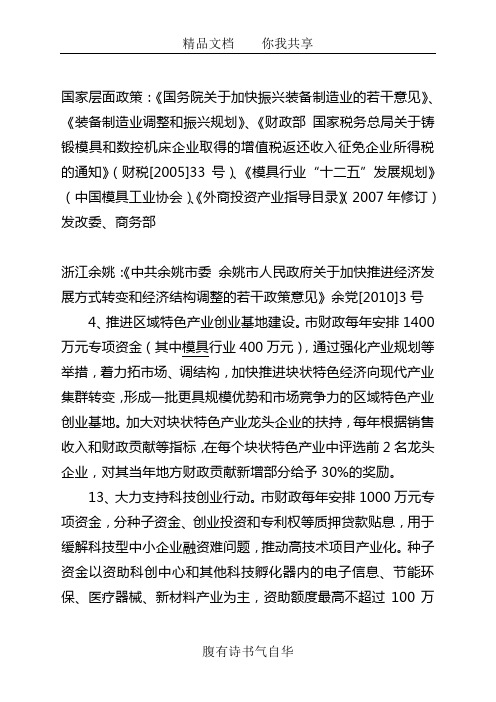
国家层面政策:《国务院关于加快振兴装备制造业的若干意见》、《装备制造业调整和振兴规划》、《财政部国家税务总局关于铸锻模具和数控机床企业取得的增值税返还收入征免企业所得税的通知》(财税[2005]33号)、《模具行业“十二五”发展规划》(中国模具工业协会)、《外商投资产业指导目录》(2007年修订)发改委、商务部浙江余姚:《中共余姚市委余姚市人民政府关于加快推进经济发展方式转变和经济结构调整的若干政策意见》余党[2010]3号4、推进区域特色产业创业基地建设。
市财政每年安排1400万元专项资金(其中模具行业400万元),通过强化产业规划等举措,着力拓市场、调结构,加快推进块状特色经济向现代产业集群转变,形成一批更具规模优势和市场竞争力的区域特色产业创业基地。
加大对块状特色产业龙头企业的扶持,每年根据销售收入和财政贡献等指标,在每个块状特色产业中评选前2名龙头企业,对其当年地方财政贡献新增部分给予30%的奖励。
13、大力支持科技创业行动。
市财政每年安排1000万元专项资金,分种子资金、创业投资和专利权等质押贷款贴息,用于缓解科技型中小企业融资难问题,推动高技术项目产业化。
种子资金以资助科创中心和其他科技孵化器内的电子信息、节能环保、医疗器械、新材料产业为主,资助额度最高不超过100万元;创业投资主要用于对科技型中小企业的跟进投资和对装备制造、先进模具制造、节能环保、医疗器械、电子信息、新材料等高技术产业化项目的直接投资;专利权、商标权质押贷款贴息用于推进金融机构开展专利权、商标权质押贷款业务。
2005年《关于进一步鼓励发展模具行业的若干意见》佛山市:《佛山市顺德区人民政府关于促进机械装备及模具制造业发展的若干意见》佛府发(2005)3号台州市人民政府:《关于加快我市五大主导行业发展的若干政策意见》塑料模具行业:1.支持模具行业企业不断提高模具质量,经中国模具协会评审达到国内先进水平的模具,每项奖励2万元。
模具行业十四五发展纲要

模具行业十四五发展纲要主要包括以下几个方面的内容:
一、行业概述与目标定位
模具是成形技术产业链中的关键制造要素,几乎面向所有的工业制造产业。
模具行业十四五发展纲要的首要任务是明确行业的发展方向和目标定位,推动模具产业向高精度、高复杂度、高一致性的技术特点发展,提高加工效率,满足全球零件成形制造业的需求。
二、技术创新与研发
推动模具行业的技术创新和研发是十四五期间的重要任务。
通过加大科研投入,提升自主创新能力,推动模具行业向数字化、智能化、绿色化方向发展。
加强与国际先进水平的交流与合作,引进消化吸收再创新,提升我国模具行业的整体技术水平。
三、产业结构优化与转型升级
优化模具产业结构,推动产业转型升级是十四五期间的另一重要任务。
通过政策引导和市场机制,推动模具企业向专业化、规模化、集群化发展,提高产业集中度。
同时,鼓励企业加强内部管理,提升产品质量和服务水平,增强市场竞争力。
四、市场拓展与品牌建设
拓展模具市场,提升品牌影响力是十四五期间的重要目标。
通过加强市场调研,了解客户需求,制定针对性的市场营销策略。
加强品牌建设,提升品牌知名度和美誉度,树立行业良好形象。
拓展国际市场,推动模具产品走向世界。
五、人才培养与队伍建设
重视人才培养和队伍建设是十四五期间的重要保障措施。
通过加强人才培养体系建设,培养一批高素质、高技能的模具人才。
加强企业文化建设,营造良好的人才成长环境。
建立激励机制,吸引和留住优秀人才为模具行业的发展贡献力量。
模具设计与中国制造2025
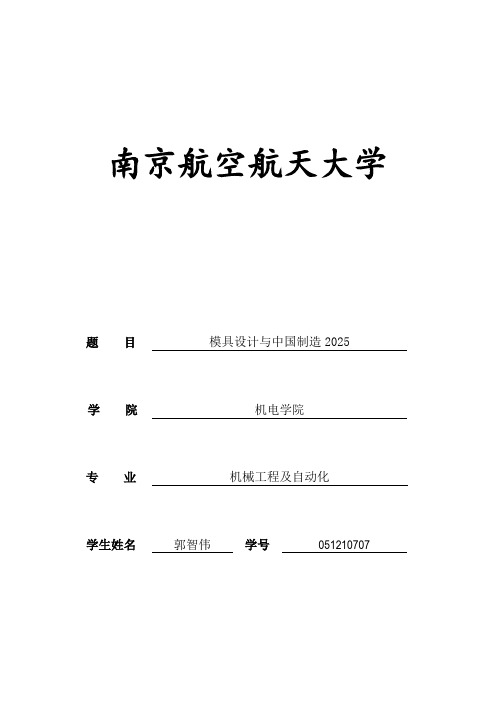
南京航空航天大学题目模具设计与中国制造2025 学院机电学院专业机械工程及自动化学生姓名郭智伟学号*********摘要模具作为重要的工艺装备,在消费品、电器电子、汽车、飞机制造等工业部门有举足轻重的地位。
工业产品零件粗加工的75%、精加工的50%及塑料零件的90%将由模具完成。
我国模具行业近年来均增长速度为21%。
今后一段时期,对模具的需求主要集中在四个行业:汽车行业、家用电器行业、电子及通讯行业和建材行业。
模具是“效益放大器”,用模具生产的最终产品的价值要比模具自身的价值高几十倍。
如汽车行业,目前我国汽车产量超过400万辆,基本车型达到170种,新车型和改装车型将达430种,汽车换型是约有80%的模具需要更换。
1999年7月,国家计委和科学技术部发布了《当前国家优先发展的高新技术产业化重点领域指南(目录)》,《指南》中列入了电子专用模具、塑料成形新技术与新设备、快速原型制造工艺及成套设备、激光加工技术及成套设备、汽车关键零部件等。
例如,采用快速原型制造技术和设备,用分层实体堆积等方法,可以将复杂的CAD模型转化为实物,使模具和产品的设计、评价与制造周期大大缩短,企业就能快速抢占市场,取得竞争优势。
相对应的,不难看出,模具作为制造技术与信息技术相结合的产物和最佳表现平台,在《中国制造2025》智能制造的目标下,将成为“工业 4.0”的主流方向之一。
关键词;【注塑机】【模具加工】【pro/e建构】【中国制造2025】一、工业背景分析新中国改革开放以来,伴随着经济的腾飞,我国的制造业也引来了一个发展的良机,但虽经过几十年的发展,仍然摆脱不了大而不强的尴尬局面,但就模具设计领域就可见一斑,低端模具方面每年国内大批量的生产,甚至模具厂林立产能过剩造成恶性竞争,而中高端模具方面则完全由国外掌控,国内外模具几十倍的价差令人目瞪口呆。
与此同时,近年来,发达国家们在迎来新一轮技术革新中,仍然将制造业作为重中之重,例如,美国在2012年提出“美国先进制造业国家战略计划”,2013年又推出“美国制造业创新网络计划”;德国提出的举世瞩目的“德国工业4.0”;日本提出了“日本制造业白皮书”等等,针对这一大背景,“中国制造2025”在2015年由我国国务院提出,不久之前国务院又公布了《关于积极推进“互联网+”行动的指导意见》,加上近十年来推出了包括01、02、03、04专项在内的十余项“国家重大科技专项”规划,构成了我国振兴制造业的战略与战术部署【1】。
2024年注塑模具企业三年发展战略规划
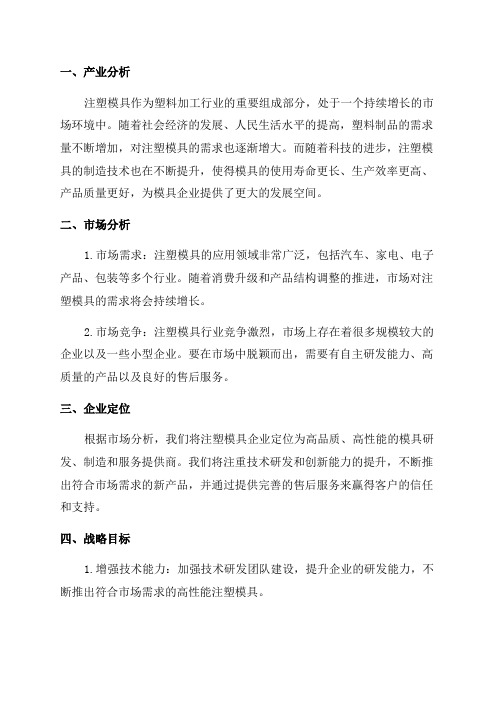
一、产业分析注塑模具作为塑料加工行业的重要组成部分,处于一个持续增长的市场环境中。
随着社会经济的发展、人民生活水平的提高,塑料制品的需求量不断增加,对注塑模具的需求也逐渐增大。
而随着科技的进步,注塑模具的制造技术也在不断提升,使得模具的使用寿命更长、生产效率更高、产品质量更好,为模具企业提供了更大的发展空间。
二、市场分析1.市场需求:注塑模具的应用领域非常广泛,包括汽车、家电、电子产品、包装等多个行业。
随着消费升级和产品结构调整的推进,市场对注塑模具的需求将会持续增长。
2.市场竞争:注塑模具行业竞争激烈,市场上存在着很多规模较大的企业以及一些小型企业。
要在市场中脱颖而出,需要有自主研发能力、高质量的产品以及良好的售后服务。
三、企业定位根据市场分析,我们将注塑模具企业定位为高品质、高性能的模具研发、制造和服务提供商。
我们将注重技术研发和创新能力的提升,不断推出符合市场需求的新产品,并通过提供完善的售后服务来赢得客户的信任和支持。
四、战略目标1.增强技术能力:加强技术研发团队建设,提升企业的研发能力,不断推出符合市场需求的高性能注塑模具。
2.提升产品质量:加强质量管理,优化生产工艺,提高产品的质量稳定性和一次合格率,确保客户满意度。
3.拓展市场份额:通过与现有客户的长期合作关系和积极开拓新客户,扩大企业在市场中的占有率。
4.提升服务水平:建立完善的售前、售中、售后服务体系,提供快速响应和高效率的服务,为客户提供最优质的解决方案。
五、战略措施1.加强人才队伍建设:增加研发人员数量,培养和引进高端技术人才,提升企业的研发能力。
2.不断技术创新:加大研发投入,提高研发效率和创新能力,推出适应市场需求的新产品。
3.加强生产管理:优化生产流程,提高生产效率和工艺标准化水平,降低生产成本。
4.加强营销渠道建设:与现有客户建立长期合作关系,拓展新客户,扩大市场份额。
5.提升售后服务水平:建立售后服务团队,快速解决客户问题,提供优质的售后服务。
2023年模具刀具行业市场前景分析

2023年模具刀具行业市场前景分析一、行业概述模具和刀具是制造业中不可或缺的一环,被广泛应用于各种工业制造领域。
模具是制造工业和产品的工具,包括压铸模、注塑模、冲压模、挤压模、弯曲模等。
刀具是机械加工的重要工具,包括钻头、铣刀、车刀、切削刀具等。
这两者的产业链互相联系,形成了一个庞大的模具刀具行业。
中国模具刀具行业已经成为全球最大的生产、使用和出口国家之一。
根据统计数据,中国模具行业市场规模已达到2300亿元,超过欧美发达国家。
二、市场前景分析十三五规划中提到了国家工业转型升级的战略目标,其中包括大力发展装备制造业,实现由数量型向质量型转变。
模具刀具作为装备制造业中的“利器”,其需求量必将逐步增大。
近年来,我国民用航空、军用航空、新材料、节能环保、高端轨道交通、新能源汽车等行业的快速发展,都对模具刀具行业提出了更高的要求,也为该行业带来了更广阔的发展前景。
近年来,随着工业的改进和改革开放的深入,我国模具刀具行业也得到了快速发展。
根据中国机械工业联合会报道,目前我国每年模具刀具应用市场的需求量约为3亿元人民币,且需求不断增加。
与此同时,国际模具刀具市场也在不断扩大,范围也在不断提高。
中国模具刀具企业要想在国际市场上立足,必须提高产品质量和技术水平,增强核心竞争力。
在自主创新方面,我国模具刀具行业还有很大提升空间,尤其是高端产品仍然依赖进口。
总体来看,我国目前的模具刀具行业市场前景十分广阔。
但是,仍有一些问题亟待解决,例如行业内市场竞争激烈、行业发展水平差异较大等。
我国模具刀具行业需要不断发展和改进,提高产品质量、技术水平和市场竞争力,才能实现更为可持续的发展。
中国模具行业的发展现状及前景分析
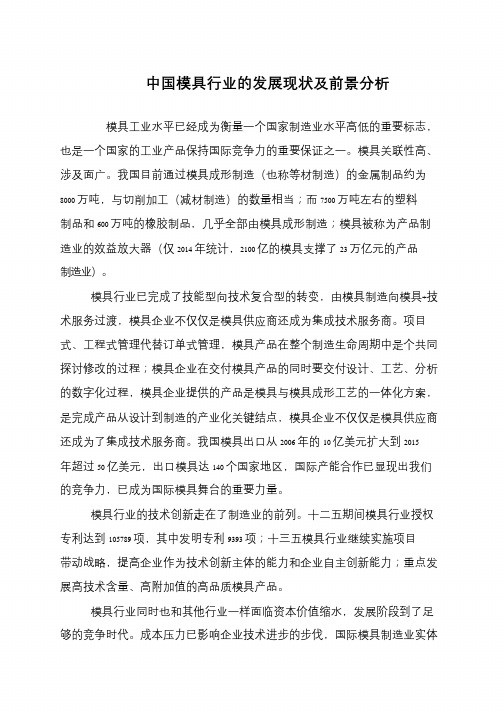
中国模具行业的发展现状及前景分析
模具工业水平已经成为衡量一个国家制造业水平高低的重要标志,也是一个国家的工业产品保持国际竞争力的重要保证之一。
模具关联性高、涉及面广。
我国目前通过模具成形制造(也称等材制造)的金属制品约为8000 万吨,与切削加工(减材制造)的数量相当;而7500 万吨左右的塑料
制品和600 万吨的橡胶制品,几乎全部由模具成形制造;模具被称为产品制造业的效益放大器(仅2014 年统计,2100 亿的模具支撑了23 万亿元的产品
制造业)。
模具行业已完成了技能型向技术复合型的转变,由模具制造向模具+技术服务过渡,模具企业不仅仅是模具供应商还成为集成技术服务商。
项目式、工程式管理代替订单式管理,模具产品在整个制造生命周期中是个共同探讨修改的过程;模具企业在交付模具产品的同时要交付设计、工艺、分析的数字化过程,模具企业提供的产品是模具与模具成形工艺的一体化方案,是完成产品从设计到制造的产业化关键结点,模具企业不仅仅是模具供应商还成为了集成技术服务商。
我国模具出口从2006 年的10 亿美元扩大到2015
年超过50 亿美元,出口模具达140 个国家地区,国际产能合作已显现出我们的竞争力,已成为国际模具舞台的重要力量。
模具行业的技术创新走在了制造业的前列。
十二五期间模具行业授权专利达到105789 项,其中发明专利9393 项;十三五模具行业继续实施项目
带动战略,提高企业作为技术创新主体的能力和企业自主创新能力;重点发展高技术含量、高附加值的高品质模具产品。
模具行业同时也和其他行业一样面临资本价值缩水,发展阶段到了足够的竞争时代。
成本压力已影响企业技术进步的步伐,国际模具制造业实体。
模具建议书【范本模板】

篇一:“十三五”规划重点—模具设备项目建议书(立项报告)“十三五”规划重点—模具设备项目建议书(立项报告)编制单位:北京智博睿投资咨询有限公司定义及作用定义:项目建议书又称立项报告,是由项目投资方向其主管部门上报的文件,从宏观上论述项目设立的必要性和可能性,建议书内容包括项目的战略、市场和销售、规模、选址、物料供应、工艺、组织和定员、投资、效益、风险等,把项目投资的设想变为概略的投资建议.目前广泛应用于项目的国家立项审批工作中.项目建议书通常是在项目早期使用,由于项目条件还不够成熟,仅有规划意见书,对项目的具体建设方案还不明晰,市政、环保、交通等专业咨询意见尚未办理.项目建议书主要论证项目建设的必要性,建设方案和投资估算也比较粗,投资误差为±30%左右.对于大中型项目,有的工艺技术复杂,涉及面广,协调量大的项目,还要编制预可行性研究报告,作为项目建议书的主要附件之一。
作用:项目建议书是项目发展周期的初始阶段,是国家选择项目的依据,也是可行性研究的依据.项目建议书是项目发展周期的初始阶段基本情况的汇总,可以减少项目选择的盲目性,是国家选择和审批项目的依据,也是制作可行性研究报告的依据。
涉及利用外资的项目,只有在项目建议书批准后,才可以开展对外工作。
项目建议书批准后,可以着手成立相关项目法人。
民营企业(私人投资)项目一般不再需要编写项目建议书,只有在土地一级开发等少数领域,由于行政审批机关习惯沿袭老的审批模式,有时还要求项目方编写项目建议书.外资项目目前主要采用核准方式,项目方委托智博睿等有资格的机构编写项目建议书即可。
项目建议书和可行性研究报告的区别项目建议书和可行性研究是项目前期两个不同的阶段,其内容、深度、作用都是不一样的.项目建议书往往是在项目早期,由于项目条件还不够成熟,仅有规划意见书,对项目的具体建设方案还不明晰,市政、环保、交通等专业咨询意见尚未办理。
项目建议书主要论证项目建设的必要性,建设方案和投资估算也比较粗,投资误差为±30%左右。
- 1、下载文档前请自行甄别文档内容的完整性,平台不提供额外的编辑、内容补充、找答案等附加服务。
- 2、"仅部分预览"的文档,不可在线预览部分如存在完整性等问题,可反馈申请退款(可完整预览的文档不适用该条件!)。
- 3、如文档侵犯您的权益,请联系客服反馈,我们会尽快为您处理(人工客服工作时间:9:00-18:30)。
模具行业“十三五”发展规划中国模具工业协会编制(中国模具工业协会第六届理事会第四次常务理事会议通过)模具是制造业中不可或缺的特殊基础装备,主要用于高效大批量生产工业产品中的有关零部件和制件,是装备制造业的重要组成部分,其产业关联度高,技术、资金密集,是制造业各有关行业产业升级和技术进步的重要保障之一。
为贯彻落实党中央、国务院关于扩市场、调结构、促平衡,加快转变经济发展方式的总体要求,促进行业健康平稳发展,推动产业升级,为实现2020年步入世界模具强国之列奠定坚实的基础,特编制本规划。
一、模具工业在国民经济(制造业)中的作用与地位及行业现状1、作用与地位模具是工业生产中极其重要而又不可或缺的特殊基础工艺装备,其生产过程集精密制造、计算机技术、智能控制和绿色制造为一体,既是高新技术载体,又是高新技术产品。
由于使用模具批量生产制件具有的高生产效率、高一致性、低耗能耗材,以及有较高的精度和复杂程度,因此已越来越被国民经济各工业生产部门所重视,被广泛应用于机械、电子、汽车、信息、航空、航天、轻工、军工、交通、建材、医疗、生物、能源等制造领域,在为我国经济发展、国防现代化和高端技术服务中起到了十分重要的支撑作用,也为我国经济运行中的节能降耗,做出了重要贡献。
模具工业是重要的基础工业。
工业要发展,模具须先行。
没有高水平的模具就没有高水平的工业产品。
现在,模具工业水平已经成为衡量一个国家制造业水平高低的重要标志,也是一个国家的工业产品保持国际竞争力的重要保证之一。
2、行业特点与现状绝大多数模具都是针对特定用户而单件生产的,因此模具企业与一般工业产品企业相比,数量多、规模小,多为中小企业。
由于模具产品技术含量较高,活化劳动比重大,增值率高,生产周期较长,因而模具制造行业就有了技术密集和资金密集、均衡生产和企业管理难度大、对特定用户有特殊的依赖性、增值税负重、企业资金积累慢以及投资回收期长等许多特点。
由于模具产品品种繁多,大小十分悬殊,要求各异,因此模具企业发展适于“小而精、小而专、小而特”;行业发展适合于集聚生产和集群式发展,以建立较强的协作配套体系。
这也是模具行业的重要特点之一。
随着时代的进步和科技的发展,过去长期依赖钳工、以钳工为核心的粗放型作坊式的生产管理模式,正逐渐被以技术为依托、以设计为中心的集约型现代化生产管理模式所替代;模具产品的传统概念也正被模具是高新技术产品的概念所替代。
目前全国共有模具生产企业(厂、点)约3万个,从业人员近100万人,2009年模具销售额约980亿元。
根据2008年我国工业普查资料,模具制造行业主营收入500万元以上企业全国共有2813个,从业人员41.22万人,工业总产值1178.35亿元(含模具及非模具产品),资产总计1206.34亿元,利税总额133.90亿元。
根据海关统计,2009年我国共进口模具19.64亿美元,出口18.43亿美元。
出口模具约占模具总销售额的12.8%。
从模具产需情况看,中低档模具已供过于求,而以大型、精密、复杂、长寿命模具为主要代表的高技术含量模具自给率还较低,只有60%左右,有很大一部分依靠进口。
目前模具总销售额中塑料模具占比最大,约占45%;冲压模具约占37%;铸造模具约占9%;其他各类模具共计约9%。
从产业布局来看,珠江三角洲和长江三角洲是我国模具工业最为集中的地区,近来环渤海地区也在快速发展。
按省、市来说,广东是模具第一大省,浙江次之,上海和江苏的模具工业也相当发达,安徽发展也很快。
模具生产集聚地主要有深圳、宁波、台州、苏锡常地区、青岛和胶东地区、珠江下游地区、成渝地区、京津冀(泊头、黄骅)地区、合肥和芜湖地区以及大连、十堰等。
各地相继涌现出来的模具城、模具园区等,则是模具集聚生产最为突出的地方,具有一定规模的模具园区(模具城)全国已有20个左右。
从产业技术进步看,“十五”以来,在政府政策扶持和引导下,模具行业投入较大,企业装备水平和实力有了很大提高,生产技术长足进步, CAD/CAM技术已普及;热流道技术和多工位级进冲压技术已得到较好推广;CAE、CAPP、PLM、ERP等数字化技术已有一部分企业开始采用,并收到了较好的效果;高速加工、并行工程、逆向工程、虚拟制造、无图生产和标准化生产已在一些重点骨干企业实施。
技术的进步,促使模具产品水平近年来也有了很大提高,向高端发展趋向较为明显。
一些模具产品已达到或接近世界先进水平,其中具有代表性的如单套模具重量达到120吨的巨型模具、加工精度达到0.3~0.5μm的超精模具、使用寿命达到3亿~4亿次的长寿命模具、能与2500次/分钟高速冲床配套的高速精密冲压模具、实现多料和多工序成形的多功能复合模具、能实现智能控制的复杂模具,等等。
当然,能生产高水平模具的企业在行业中还只占少数,综合来看,我国模具行业总体水平还比较低。
模具产业的快速发展,促进了行业重点骨干企业的形成,现在被中国模协认定和授牌的重点骨干模具企业已达110个。
行业骨干队伍的形成起到了引领行业发展的作用。
二、我国模具工业与国际先进水平的主要差距及存在的主要问题1、主要差距我国模具工业与国际先进水平相比,由于在理念、设计、工艺、技术、经验等方面存在差距,因此在企业的综合水平上特别是产品水平方面就必然会有差距。
差距虽然正在不断缩小,但从总体来看,目前我们还处于以向先进国家跟踪学习为主的阶段,创新不够,尚未到达信息化生产管理和创新发展阶段,只处于世界中等水平,仍有大约10年以上的差距,其中模具加工在线测量和计算机辅助测量及企业管理的差距在15年以上。
管理水平、设计理念、模具结构需要不断创新,设计制造方法、工艺方案、协作条件等需要不断更新、提高和努力创造,经验需要不断积累和沉淀,现代制造服务业需要不断发展,模具制造产业链上各个环节需要环环相扣并互相匹配。
面对差距,我们既要努力追赶,更要开创自己的发展道路。
综合水平的差距最终都会反映到模具产品中可以量化和感知的具体指标上。
综合我国各类模具情况,与国外先进水平的差距主要表现为:模具使用寿命低30%~50%(精冲模寿命一般只有国外先进水平的1/3左右),生产周期长30%~50%,质量可靠性与稳定性较差,制造精度和标准化程度较低,等等。
与此同时,我国在研发能力、人员素质、对模具设计制造的基础理论与技术的研究等方面也存在较大差距,因此造成在模具新领域的开拓和新产品的开发上较慢,高技术含量模具的比例比国外也要低得多(国外约为60%左右,国内不足40%),劳动生产率也要低许多。
2、主要问题存在的主要问题大致有如下方面:⑴研发及自主创新能力薄弱。
基础差、能力不足、投入少、不够重视、缺乏长期可持续发展观念等都是造成模具产品及其生产工艺、工具(包括软件)、装备的设计、研发(包括二次开发)及自主创新能力薄弱的重要原因。
⑵企业管理落后于技术的进步。
管理落后主要体现在生产组织方式及信息化采用方面。
国内虽然已经有不少企业完成了从作坊式和承包方式生产向零件化现代生产方式的过渡,但沿用作坊式生产的小企业还不少;已实行零件化生产的企业中只有少数企业采用了信息化管理,且层次也还不高。
行业和企业的专业化水平都比较低,企业技术特长少。
⑶数字化信息化水平还较低。
国内多数企业数字化信息化大都停留在CAD/CAM的应用上,CAE、CAPP尚未普及,许多企业数据库尚未建立或正在建立;企业标准化生产水平和软件应用水平都低,软件应用开发跟不上生产需要。
⑷标准和标准件生产供应滞后于模具生产的发展。
模具行业现有的国家标准和行业标准中有不少已经落后于生产(有些模具种类至今无国标,不少标准多年未修订);生产过程的标准化还刚起步不久;大多数企业缺少企标;标准件品种规格少,应用水平低,高品质标准件还主要依靠进口;为高端汽车冲压模具配套的铸件质量问题也不少,这些都影响和制约着模具生产的发展和质量的提高。
⑸人才与发展不相适应。
人才发展的速度跟不上行业发展速度,目前全行业人才缺乏,尤其是高级人才更加匮乏,数量是一个方面,人才素质与水平更加重要。
学校与培训机构不足、培养目标不高是问题的一个方面,企业缺乏培养人才积极性也不可忽视。
⑹以模具为核心的产业链各个环节协同发展不够,尤以模具材料发展滞后最为明显。
模具材料对模具质量影响极大,国产模具材料长期以来,不论从品种、质量还是数量上都不能满足模具生产的需要,高档模具和出口模具的材料几乎全部依靠进口。
模具上游的各种装备(机床、工夹量刃具、检测、热处理和处理设备等)和生产手段(软件、辅料、损耗件等)以及下游的成形材料(各种塑料、橡胶、板材、金属与非金属及复合材料等)和成形装备(橡塑成形设备、冲压设备、铸锻设备等),甚至包括影响模具发展的物流及金融等产业链的各个环节大都分属于各有关行业,大都联系不够密切,配合不够默契,协同程度较差,这就造成了对模具工业发展的制约。
三、“十三五”发展目标及战略1、发展环境与市场“十三五”时期是我国妥善应对国内外发展环境重大变化、加快实现全面建设小康社会目标的关键时期,也是我国模具制造行业健康发展的关键时期,国内外环境不确定因素虽然很多,但我国经济发展仍在高速增长期内,我国模具在国际模具市场上的比较优势仍旧存在,国内模具市场预期也继续看好。
2015年我国人均塑料消费量约为64公斤,仅为发达国家的1/3,这预示着“十三五”期间我国塑料制品行业仍将会保持高速发展;在“以塑代钢”、“以塑代木”的必然趋势下,工程塑料制品业在“十三五”期间预计也会维持年均15%的市场增长率。
由此可以想见,在模具总量中占比最高、支撑塑料制品业的塑料模具市场,“十三五”也将会以较高的增长速度发展。
作为模具使用量最大的汽车行业,预计“十三五”期间将会以年均10%左右的增长速度发展,加上我国庞大的机动车保有量(2009年底为1.86亿辆,其中汽车7619.3万辆,摩托车9453万辆)所带动的维修配件市场和出口市场,我国汽车零部件也将在1.5万亿元的厐大市场基础上保持较高的增长速度,由此预计“十三五”期间汽车模具的年均增速不会低于10%,包括汽车轮胎模具在内的橡胶模具年均增速将达到10%以上。
电子及信息产业也是模具的大用户,“十三五”预计将有20%左右的年均增速。
轨道交通、航空航天、新能源、医疗器械、建材等行业也将为模具带来庞大的市场。
例如医疗器械,目前我国只占全球2%的份额,药品与医疗器械消费比只有2.5:1,而发达国家是1:1;美国在医用塑料方面的人均年消耗费用为300美元,而中国只有30元人民币,可见发展潜力之大。
在国际市场方面,由于工业发达国家人工成本的持续提高,迫使他们为了降低生产成本而不断把模具向发展中国家尤其是像我国这样有较好技术基础的发展中国家转移。
跨国公司到我国来采购模具的趋势尚在发展之中,国际新兴市场的开拓也大有可为。