硬车技术
硬车削技术及其在柴油机气阀加工中的应用

性 。普通高速钢和硬质合金不能进行 硬车削 ,必须用新
型硬质合金、涂层硬质合金以及陶瓷和聚晶立方氮化硼
(C N P B )等刀具材料 。
当工件硬度 为 4 5 H C时 ,可 采用新 型硬 质合 0 0R
陶瓷刀具硬度高,耐磨性好,但脆性大,强度较
低 。硬车 削淬硬钢时 ,进给量对 刀具破损影 响最 大 ,所
( )硬车削的定 义 通常 所说 的硬车 削是指用 车刀 1 对淬硬钢 (4~6 H C 5 3 R )进行 的切 削加 工 ,这种加工 通
法 ,可配备多种刀具 转盘 、刀库等 以实 现加工转换 。现
代 C C车床 尤其 适 合 硬 车 削,对多 品 种 、计 划 多变 、 N 交货期短 、生产批量 小的柔性 化生产更显其优越性。 ④ 硬车削可使零件 获得 良好 的整体加工精度。一般
维普资讯
c ‰
圈
硬车削技术及其在 柴油机气阀加工中的应用
河南 工业大学化学工业职业学院 ( 郑州 4 04 ) 李凤银 5 0 2
1 引言 .
切 削加工是制造业 的主要加工 方法 ,也是 当前 环境 污染的主要源头之一 。干切削加工技术 是实现绿 色制造 的关键技术 ,是一种先进的制造技 术。2 世纪 ,制造业 1
缸槭 冷工 l 加
z 囫 笪
ww ma hns . 0n c w c i t c r . n i
维普资讯
C t n o l ut g T o i s
()硬车 削的刀具 材料 1
实 现干式切 削的最大 技术
产率 、加工成本 、加工质量和 刀具寿命 。一般来 说 , 硬 态车削时 ,通常采用 P B C N或 陶瓷 刀具材料 ,由于其 耐
热后硬车技术在发动机齿轮加工中的应用
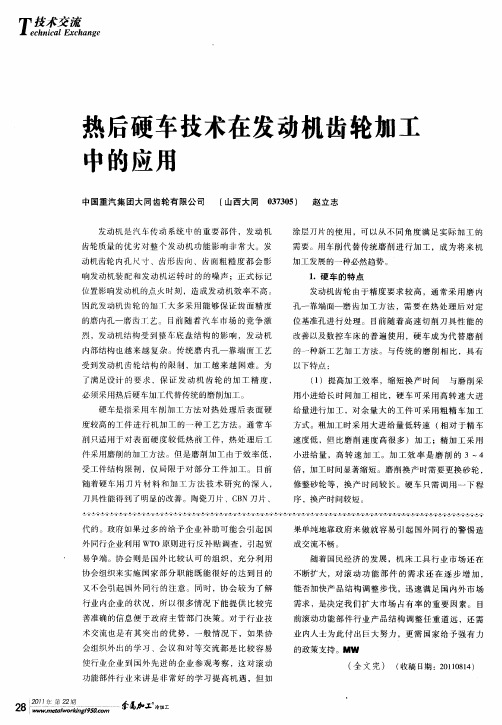
协会组 织来 实施 国家 部 分 职 能 既能 很 好 的 达 到 目的 又不会 引 起 围外 同行 的 注 意 。同 时 ,协 会较 为 了解
不 断扩大 ,对 滚 动 功 能 部 件 的需 求 还 在 逐 步 增 加 . 能 否加快 产 品 结构 调 整 步 伐 ,迅 速满 足 国 内外 市 场
代 的。政府 如果 过 多 的给予 企 业 补 助 可 能 会 引起 围
外 同行 企业利 用 WT O原 则进 行 反补 贴调 查 ,引 起 贸 易争端 。协 会 则是 国外 比较认 可 的组 织 ,充 分 利用
果单 纯地靠 政 府 来 做就 容 易 引 起 国外 同行 的警 惕 造
成交 流不 畅 。 随着 国 民经济 的发 展 ,机 床 工 具 行 业 市 场 还 在
3 .应 用 现在 我公 司 加工 的发 动 齿 轮 对 于 有 内 凹 端 面 的
可采用 多 把 刀 在 工 件 一 次 装 夹 下 完 成 端 面 、内孔 、 外 圆 、凹端 面 、圆 角 的 加 工 ,可 以获 得 较 高 的加 工 精度 。磨削 由于 加工 时 只有 一个 砂 轮 表 面进 行 磨 削 ,
前 滚动功 能 部件 行 业 产 品 结 构调 整 任 重 道 远 ,还 需 业 内人 士为 此 付 出 巨大 努 力 ,更 需 国 家 给予 强 有 力 的政策 支持 。MW
使行业企业到 国外先进的企业参观考察,这对滚动
功能部 件行 业来 讲 是 非 常好 的学 习 提 高机 遇 ,但 如
序 ,换 产 时间较 短 。
‘ ・ ‘ ‘ l/ ’ ’ i / {/ 、 、 !/
随着硬 车 用 刀 片 材 料 和 加 工方 法 技 术 研 究 的深 入 ,
YZ25G型空调硬座车

YZ25G型空调硬座车
赵大斌
【期刊名称】《铁道车辆》
【年(卷),期】1996(034)011
【摘要】简要介绍25G型空调硬座车的主要技术参数,平面布置和车体钢结构、转向架,制动,空调,采暖,设备,电气等结构特点。
【总页数】4页(P19-22)
【作者】赵大斌
【作者单位】无
【正文语种】中文
【中图分类】U271.103.8
【相关文献】
1.基于坐姿体压仿真的25G型硬座车座椅舒适性研究 [J], 肖露
2.YZ25G型客车3种电源供电方式并存的配置 [J], 唐明昌
3.浦厂25G型硬座车和硬卧车车体钢结构静强度试验结果比较与分析 [J], 徐凤妹;劳世定
4.中长途双层旅客列车(续完)——SRW25B,SYZ25B型双层空调软卧车,硬座车[J], 牛得田;梁世宽
5.YZ25A型空调硬座车,RW25A型空调软卧车概况 [J], 柯风法
因版权原因,仅展示原文概要,查看原文内容请购买。
以车代磨技术在生产中的应用

一
到 尺 寸 ,真 空 气 淬 ,硬 度 达6 ~6 H C,数 控 硬车 0 4R 削 内外 圆到 尺 寸 ,保 证 形 位 公差 要 求 。硬 质车 削 时 定 要 注 意 夹 紧 力的 大 小 ,夹 紧 力 太 大 易 引起 内孔 变 形 ,太 小 夹 不 紧 工 件 ,夹 紧 时 液 压 压 力 设 定 06 .
图 1
两 道 环 槽 ( . )mm × 2 H 1 、 根部 4 23 4 1 个
R .mm粗 车 到 尺 寸 ,右 端 台 阶 1 mm长 3 05 2 mm, 根 部R1 mm: 尺 寸 , 钻 攻M 6 尺 寸 ,其 余 端 面 . 5  ̄ l J 到 及 外 圆全 部 单 面 留01 .mm粗 车 成 形 ;采 用 真 .~02 空 气 淬 ,硬 度 达 N 5 ~6 HR 5 1 C;内 圆磨 2 H8 0 0  ̄ 尺 寸 ,同 时 并 靠 磨 端 面 ,保 证 尺 寸 及 表 面 粗 糙 度 要 求 ; 内孔 2 H 穿 心 棒 磨 外 圆 2 h  ̄ 尺 寸 , 0 8 6 8l J 保 证 外 圆尺 寸 及 表 面 粗 糙 度 要 求 ,同 时 保 证 内 外
~
吃 刀量 为00 mm。此 工 艺 在 车 间 一 线 实 行 后 ,取 . 6 得 了 很 好 的 效 果 。加 工 出 的 产 品 完 全 满 足 图 样 要 求 ,且 质 量控 制 稳 定 ,加 工 速 度大 大 提 升 。 以一 台
08 a 宜 。机 床主 轴 转 速 设 为 1 0 r n . MP 为 0/ ,转 6 mi
我们经过认真评审 ,认为采用数控硬车 削以车 代磨能保 证要求 ,改进后 的工 艺为下料 2 mm长 8
探析高速切削中硬态切削技术的应用
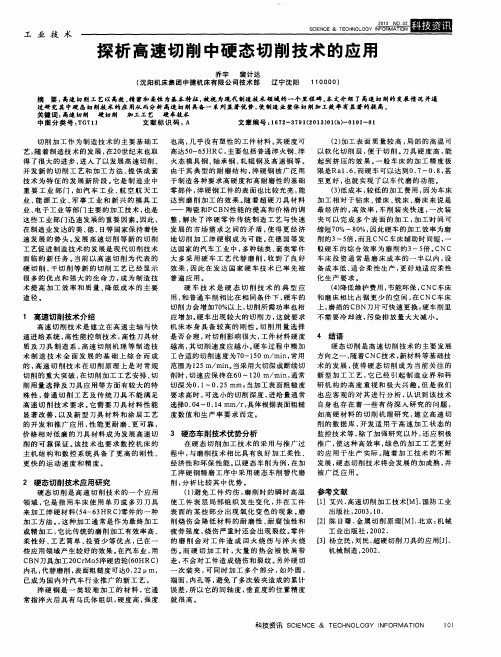
发 展 的 市场 需 求 之 间的 矛 盾 , 使 得 更 经 济 缩 短7 0 %~8 0 %, 因 此 硬 车 的加 工效 率 为磨 地切削加 工淬硬 钢成为 可能 。 在 德 国 等 发 削 的3 ~5 倍, 而且 C NC车床 辅 助 时 间短 , 一
速发展 的势头 。 发 展 高 速 切 削 等 新 的 切 削
高 速 切 削 技 术 是 建 立 在 高 速 主 轴 与 快 机 床 本 身具 备 较 高 的 刚 性 。 切 削 用 量 选 择 速进给系统 , 高性能控制技术 , 高 性 刀 具 材 是 否 合 理 , 对切 削影 响 很 大 , 工 件材 料 硬 度 4 结语 其切削速度应越小 。 硬 车 过 程 中精 加 硬 态 切 削 是 高 速 切 削 技 术 的 主 要 发 展 质 及 刀具 制 造 系 , 高 速 切 削 机 理 等 制 造 技 越 高 ,
限 是Ra 1 . 6 , 而硬车可以达到0 . 7 ~0 . 8 , 甚 也 就 实现 了 以 车 代 磨 的功 能 。 于 制造 各 种 要 求 高 硬 度 和 高 耐 磨 性 的基 础 至 更 好 , 零部件 , 淬 硬 钢 工 件 的表 面 也 比较 光 亮 , 能 ( 3 ) 低成本 , 较低的加工费用 , 因 为 车床
切 削 加 工 作 为 制 造 技 术 的 主 要 基 础 工
也高, 几乎 没 有 塑 性 的工 件 材 料 。 其 硬 度 可
( 2 ) 加 工表面 质量较高 , 局 部 的 高 温 可
艺, 随着制造技术的发展 , 在2 0 世 纪 末 也 取 得 了很 大 的 进 步 , 进 入 了以 发 展 高 速 切 削 开发新 的切 削工艺和 加工方法 、 提 供 成 套 技术 为特征 的发展新 阶段 。 它 是 制 造 业 中 重要 工业 部 门 , 如汽 车 工业 、 航 空 航 天 工
SPK硬车

修光刃技术
i
修光刃技术的优势
ZZ型修光刃 标准刀片
千里之行,始于足下。使用ZZ修光 刃刀片进行精加工,这应该是描述 高效加工的最好方式。一般来讲,ZZ 型刀片也可以直接理解成修光刃刀 片。比较标准刀片,ZZ型修光刃刀 片更容易得到高精度的表面质量。 另外在不影响表面质量的前提下, 大大减少加工时间。因此,ZZ型刀 片代表提高生产效率的最有效方法 之一,特别是精加工。
TIP
切深 ap:
传统硬车: 软硬过渡车削:
ap = 0.1 - 0.5 mm ap max: = 4.0 mm
反向车削
f
传统车削
f
反向切削:
• 整体刀片的大概 2/3的刃长可用 • 选择一个小的实际主偏角 • 在高进给的情况下依然具有良好的表面质量
ap
接触面 Eingriffslänge
IKS-PROMini
最新开发的IKS-PROMINI夹紧系统是基 于 IKS-PRO开发的.事实证明应用凹槽 夹紧 IKS-PRO系统 得到进一步发展, 结合整体刀片可以满足硬钢高效加 工。形状和压力配合确保刀片精确定 位在刀座中,同时保证在硬钢加工中 优秀的稳定性和安全性。在硬车中作 用于刀片和夹紧系统的切削力被最佳 分布在整个刀垫和刀座上。这使的 IKS- PROMINI夹紧系统在连续切削、轻 微断续切削到重型断续可以实现最苛 刻的公差要求和绝对的工艺可靠性。 此外,它实用、简单且易于操 作,IKS-PROMINI使客户能快速、安全 的实现严格的质量要求。因此,IKSPROMINI通过其严格的夹紧系统,优 化切削力分布和简单操作,可以大大 提高生产力,同时进一步降低硬车成 本。
SPK PCBN刀片命名规则
带有ZZ型修光刃的焊尖HD-Line刀片命名举例
硬车削大功率静压轴承电主轴设计分析

2 几个关键结构设计 .
( )轴 承 浮 动 支 承 结 构 电主 轴 的 定 子 和 转 1
子被设置在静压轴承的尾部 ,由于主轴尾部悬伸比
图2 轴承外圈采用浮动支承
( 2) 装 卸 夹 紧 工
结构形式
件 的 自 动 卡 盘 动 力 装 裱动 轴承 2 ・ 密封圈 3 由 座 .承 车 置 普 通 车床 自动 卡 盘 ,当油缸 中通 入 压 力油 时 ,
本 项 目 电 主 轴 要 求 切 削 工 件 的表 面 粗 糙 度 值 尺 ≤0 . 4“m,采 用P B C N刀具 ,设 计 最 高转 速 达 到 40 0/ n 0 r mi ,内 装伺 服 主 轴 电 动机 额 定 功 率 8 W , k
二 静压轴承的设计计算
1 液体静压径 向轴 承的设计计算 .
液体 静 压 轴 承可 以分 为 液体 静 压 径 向轴 承 和 液 体 静 压止 推 轴 承 ,根 据 车床 电主 轴 的用 途 ,采 用小
孔节流隧道式静压轴承 ,其结构如图5 所示。
弹 力能够使卡盘顶杆产生拉 紧力,作用到车床卡盘
构 的原 因,密封端盖 装配调试 到位后注意 定位锁 死 ,只要能保持密封 间隙的可靠性 ,运行 中一般不
需 要额 外 加 以维 护 。
簧为动力。如图3 所示 ,D为进 ( 出)油 口, 为 出 E
( )油 口,F 压 缩 空 气 入 口。在 夹 紧 工 件 的 时 进 为 候 ,活 塞 5 与卡 盘 顶 杆 8 开 接 触 , 同时 定 心 套 2 脱 在 空 气 弹 簧的 作 用下 ,带 动活 塞 缸4 配油 盘 1 、 和卡 爪 6 一起 滑移 ,致 使 卡 爪 滑 移 后 实 际 上 是 空 套 在 反 扣 环 7 ,也 就 是 主轴 9 油缸 脱 离 。而 蝶 形 弹 簧 1的 上 与 0
以车代磨在淬硬齿轮内孔加工中的应用

以车代磨在淬硬齿轮内孔加工中的应用新乡航空工业(集团)有限公司 453000摘要针对淬硬齿轮内孔磨削效率的不足,结合硬车削的特点,分析淬硬齿轮内孔采用以车代磨工艺的可行性。
通过制订切合实际的以车代磨加工方案,并给出了相应数据,在生产中获得成功,极大地提高了生产效率。
关键词以车代磨内孔加工粗糙度刀片一、引言二十一世纪初期,随着高硬度刀具材料、涂层技术机床结构刚性不断改进,如采用CBN 刀具、陶瓷刀具新型精密车床及车削加工中心上对淬硬钢进行车削等,结果都取得了非常好加工效果,其加工质量和精度可以达到精磨水平,车削硬度极限也已达到HRC68。
越来越多的工业强国已将硬车削作为替代磨削一种经济实用方法普及。
二、车削粗糙度的理论计算车床加工回转体工件时,刀刃在工件上运动轨迹是螺旋线,所以,让工件通过放大观测可以看到工件表面不是光滑的圆柱表面,而是等于螺距很小(等于进给量)的螺纹表面。
这是形成表面粗糙度的原因之一。
在加工过程中由于加工表面的塑性变形、刀具在工作表面的摩擦以及在切削过程中产生的其它现象,往往使已加工表面的实际粗糙度H实大于理论高度H。
表面粗糙度的理论高度H的计算可以按刀尖圆弧半径re=0与re≠0情形分别加以讨论。
2.1当re≠0时,根据几何学知识,有AB2=O1A2- O1B2即((re-H) 2=re2–(f 2)2∴ H= re(1- )一般来说,在加工粗糙度较高的工件表面时,刀尖圆弧半径re取得较大,而进给量f远比re小,这时≈1- 1 2( f 2re)2注:根据微分学中的近似计算公式f(x)= f(x0)+ f'(x0)(x-x0),对于f(x)= ,取x0=0,有≈ 1- 1 2x,(|X|充分小)故H= re{1-(1- 1 2( f 2re)2}得到H≈ f2 8re …………………………… 公式 12.2当re=0时∵ cotΨ1= f1H , cotΨ= f2H因(其中f1 + f2=f)∴cotΨ1+ cotΨ= f1H+ f2H= fH故H=f/( cotΨ1+ cotΨ)……………………… 公式 22.3提高表面粗糙度的研究由公式1、2可以看出:主偏角Ψ及副偏角Ψ1越小,刀尖圆弧re越大,f 越小时,表面粗糙度的理论高度H就越小。
浅谈车削加工的新工艺——硬车技术

浅谈车削加工的新工艺——硬车技术文/李秀艳在车削加工领域,对于复杂零件和难加工材料的车削,一直是车削加工中的难题。
随着高硬度切削材料和相关机床的发展,立方氮化硼刀具、陶瓷刀具及新型硬质合金刀具在新型车床或车削加工中心上的应用,使得对淬硬钢、高温合金的车削不再是难题,其加工质量可以达到精磨的水平。
在发达国家,硬车技术已被普遍应用于各种零件加工,大多数硬车技术的应用已成功替代了磨削。
一、硬车技术的概述一般情况下,车削只是淬火前进行的粗加工。
直到20世纪90年代前,淬火后的精加工还只能采用磨削工艺,而车削也只能加工硬度值低于55HRC的工件。
硬车技术,简称硬车削(即以车代磨)。
通常所说的硬车削是指把淬硬钢的车削作为最终加工或精加工的工艺方法,以替代目前普遍采用的磨削技术。
淬硬钢通常指淬火后具有马氏体组织,硬度高,强度也高,几乎没有塑性的工件材料。
当淬硬钢的硬度>55HRC时,其强度sb约为2100~2600N/mm2。
利用多晶立方氮化硼(PCBN)刀具、陶瓷刀具或涂层硬质合金刀具等在车床或车削加工中心上采用硬车削对淬硬钢(55~65HRC)进行加工,其加工精度可达IT5,表面粗糙度Ra≤0.4μm。
二、硬车技术的特点1.硬车削加工效率高硬车削具有比磨削更高的加工效率,且其所消耗的能量是普通磨削加工的1/5。
硬车削往往采用大切削深度和较高的工件转速,其金属切除率通常是磨削加工的3~4倍。
硬车削加工时一次装夹即可完成多种表面加工(如车外圆、车内孔、车槽等),而磨削则需要多次装夹。
因此,硬车削的辅助时间短,加工表面之间位置精度高。
2.硬车削是洁净加工工艺大多数情况下,硬车削无须冷却液。
事实上,使用冷却液会给刀具寿命和表面质量带来不利影响。
因为,硬车削是通过使剪切部分的材料退火变软而实现切削的。
而在使用冷却液的加工工艺过程中,若冷却率过高,就会减小由切削力而产生的这种效果,导致机械磨损加快,刀具寿命缩短。
同时硬车削可省去相关的冷却液配套装置,降低了生产成本,简化了生产系统,且形成的切屑干净清洁,易于回收处理。
“硬车”技术泛谈

“ 硬车 ’ ’ 技术泛谈
郑 维 宁
Ta l k i ng a bo u t H a r d Tu r n i ng Te c h no l o g y
Z HENG We i - n i n g
( 哈挺 机 床 ( 上海) 有 限公 司 , 上海
引起 的谐 振 现象 ( 5 ) 阀输 出忽 正 忽负 , 不能连续控制 , 成“ 开关 ” 控
1 9 9 8 .
参
考 文
献
[ 1 ] 雷天觉. 新编液压工程 手册【 M】 . 北京 : 北京理 工大学 出版社 , 【 2 】 刘宝桁- 车 L 钢 机 械设 备 【 M 】 . 北京 : 冶 金 工 业 出版 社 , 1 9 8 4 .
制 。原馈机 构断 开 ; 出现 某种 正反 馈 现象
[ 3 】 刘军 营. 液压伺 服控 制系统 的设计【 M】 . 北京 : 机械 工业 出版
社. 2 0 1 0 .
[ 4 ] 张利平. 液压 阀原 理使用与维护【 M 】 . 北京 : 化学工业 出版社 ,
7 6
Hy d r a u l i c s P n e u ma t i c s& S e a l s / N O . 0 2 . 2 0 1 4
更加 容 易 处 理 。 并 且 相 对 各 种 材质 的 砂轮 库 存 。 车床 刀
( 8 ) .
[ 6 ] 周 士 昌. 液 压 系统 设 计 图集 [ M】 . 北京 : 机械 工业 出 版社 , 2 0 8 3 . [ 7 ] 况群意. 夹送矫直机下矫直辊升降液压系统的故障诊断[ J ] . 液
以车代磨

以车代磨的切削技术一、什么是以车代磨?硬车(以车代磨)是指用车削的工艺方法作为淬硬钢的最终加工或精加工二、以车代磨的关键技术第一:刀具材料⑴:磨性好的TiN、TiCN、TiAlN和Al2O3等,涂层的厚度为2~18mm。
涂层的作用能够降低摩擦,减少切削热的生成;⑵:陶瓷刀具具有高硬度、高强度、耐磨性好、化学稳定性好、摩擦系数低且价格低廉等特点,可加工硬度HRC60以下的各类淬硬钢和硬化铸铁。
⑶:立方氮化硼(CBN)的硬度和耐磨性仅次于金刚石,具有极好的高温硬度。
⑷:通常,CBN适合加工硬度大于HRC55的淬硬钢工件,PCBN刀具适合工件硬度高于HRC60的加工,对于硬度小于HRC50的淬硬钢工件选用陶瓷刀具更为合适。
第二:切削用量与切削条件切削用量选择是否合理,对硬车削影响很大,工件材料硬度越高,其切削速度应越小。
第三:硬车削机床:车削淬硬钢与车削非淬硬钢相比,切削力将增加50%以上,切削所需功率增加2倍左右,所以硬车削对机床提出了更高要求,如系统刚性、功率等。
三、硬车削的经济性1:加工效率高硬车削所用刀具(PCBN)的成本比传统车刀一般高10~20倍,但与磨削相比,硬车削比磨削具有更高的加工效率。
2:设备投资少,维护费用低,适合柔性生产要求在生产率相同时,车床的投资只是磨床的1/3~1/10,其辅助系统费用也较低。
3:硬车削可使零件获得良好的表面加工质量硬车削中生产的大部分热量被切屑带走,不会产生像磨削加工的表面烧伤和裂纹,具有优良的加工表面质量,有精确的加工圆度,能保证加工表面精度。
4:硬车削是洁净加工工艺硬车削是通过从工件上“剥”软化的切屑来有效地去除金属。
在大多数情况下,硬车削无须冷却液,而使用冷却液会给刀具寿命和表面质量带来不利影响。
硬车削加工技术对产品质量成本的影响和作用
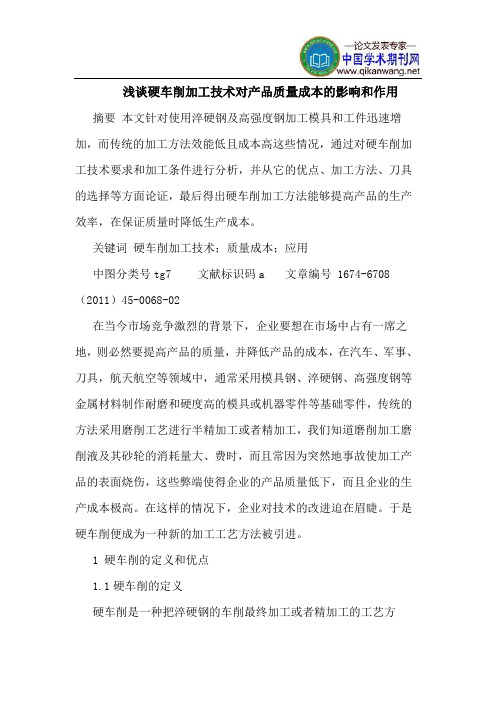
浅谈硬车削加工技术对产品质量成本的影响和作用摘要本文针对使用淬硬钢及高强度钢加工模具和工件迅速增加,而传统的加工方法效能低且成本高这些情况,通过对硬车削加工技术要求和加工条件进行分析,并从它的优点、加工方法、刀具的选择等方面论证,最后得出硬车削加工方法能够提高产品的生产效率,在保证质量时降低生产成本。
关键词硬车削加工技术;质量成本;应用中图分类号tg7 文献标识码a 文章编号 1674-6708(2011)45-0068-02在当今市场竞争激烈的背景下,企业要想在市场中占有一席之地,则必然要提高产品的质量,并降低产品的成本,在汽车、军事、刀具,航天航空等领域中,通常采用模具钢、淬硬钢、高强度钢等金属材料制作耐磨和硬度高的模具或机器零件等基础零件,传统的方法采用磨削工艺进行半精加工或者精加工,我们知道磨削加工磨削液及其砂轮的消耗量大、费时,而且常因为突然地事故使加工产品的表面烧伤,这些弊端使得企业的产品质量低下,而且企业的生产成本极高。
在这样的情况下,企业对技术的改进迫在眉睫。
于是硬车削便成为一种新的加工工艺方法被引进。
1 硬车削的定义和优点1.1硬车削的定义硬车削是一种把淬硬钢的车削最终加工或者精加工的工艺方法,而淬硬钢是淬火后硬度高、有马氏组织、几乎无塑性、强度高的工件材料,它的强度为2 100mpa~2 600mpa,硬度hrc>55。
硬车削的表面粗糙度是0.2um~0.3um,加工精度则可达5um~10um。
1.2硬车削的优点通过硬车削技术在风顺车桥公司的具体使用情况和传统的磨削技术相比,它有以下几个优点:1)加工的效能高,提高了产品的质量在风顺车桥公司引进硬车削工艺艺术代替原来的传统的技术后,发生了这样的变化:该公司加工的轴承产品,原来加工时采用磨削加工,磨削加工余量很难控制,且加工效率极低,直接影响产品的质量。
而使用硬车削工艺方法后,车削加工消耗的能量只约为原来的1/5,而它的金属切除率为原来方法下的3~4倍,并可以在一次装夹时完成多个表面加工,使得同轴度的质量都达到了技术上的规格,而在此同时,车削加工的工效高、辅助时间短,由此可见,采用硬车削方法后,生产效率大大地提高了,所以它提高产品质量的同时降低了生产成本。
硬车技术在汽车领域的应用分析
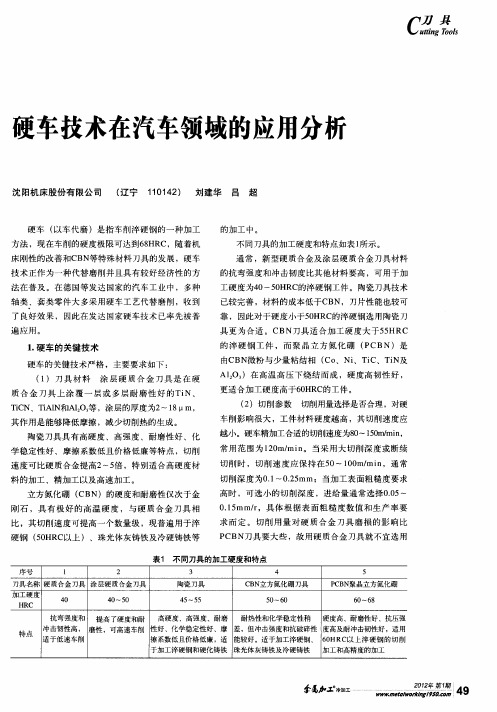
对 基 准A、B都 有跳 动要 求 ,因此 采 用专 业 夹 以齿 形 定心 ,专 用 浮动 卡 爪压 紧4 。斜 面 。 5 ( ) 刀具 及 参 数 3 刀 具 采 用 CBN立 方 ;
硼 刀 片 ,能 保 证 加 工 这 样 的 硬 度 。加 工 时 线 : 10 / n ( 2 m mi 主轴 无 极 变 速 保 证 了恒 线 速 加 工 )
已较完善 ,材料的成本低于C N,刀片性能也较可 B 靠 ,因此对于硬度小于5 H C 0 R 的淬硬钢选用陶瓷刀
具 更 为 合 适 。C BN刀具 适 合加 工 硬 度大 于5 HR 5 C
了良好效果 ,因此在发达 国家硬车技术已率先被普
遍应用。
1 硬车 的关键技术 .
硬 车 的 关 键技 术 严 格 ,主要 要 求如 下 :
硬车技术在汽车领域的应用分析
沈 阳机床股 份有 限公 司 ( 辽宁 1 O 4 ) 刘 建华 吕 超 1 1 2
硬车 ( 以车 代磨 )是指车削淬 硬钢的一种加工 方法 ,现在车削的硬度极限可达 ̄ 6 H C,随着机 ] I8 R 床刚性 的改善 ̄ C N N B 等特殊材料 刀具的发展,硬车 技术正作为一种代替磨削并且具有较好经济性的方 法在普及。在德 国等发达国家的汽车工业 中,多种
MW ( 稿 日期 :2 10 t 收 0 19
5 0
, 一
参磊 籼工
( )刀具 材料 1
涂 层硬 质合金 刀具是 在 硬
质 合 金 刀具 上 涂 覆 一 层 或 多 层 耐 磨 性 好 的Ti N、
TC iN、TA1 ̄ A 23 ,涂 层的厚度为2 8. iNI1 等 ] O ~1 m, I t 其作用是能够降低摩擦 ,减 少切削热的生成。 陶瓷 刀具具有高硬度、高强度 、耐磨性好、化
绿色制造中硬车削技术的研究及应用

6 马骋, 冯之敬, 赵广木, 活塞立体靠模的数控车削加工 【 . 等. J 】
清华大学学报, 99 3 ( ) 19 ,9 4 .
7 朱心雄 , 自由曲线曲面造 型技术 f . 等. M】北京: 科学出版社,
2 0. 00
2 刘金凌 , 王先逵, 冯之敬, 中凸变椭圆活塞数控 车削技术 等. 【】组合机床与 自动化加工技术, 9 4 ( ) J_ 19 , 4 .
具 、 用合 理 的进给 量 和切 削速 度实 现干 切削加 工 , 选 因
而 干 车 削 是 目前 应 用 最 广 泛 的 干 切 削 加 工 工 艺 方 法 。 根 据 加 工 对 象 的 特 点 、 加 工 过 程 中 采 用 的 不 同 在
收稿 日期 :0 6 1月 20年 1
硬 车 削 与 传 统 的 磨 削 相 比 , 有 以下 特 点 。 具
辅 助 措 施 等 可 以将 干 车 削 分 为 硬 车 削 、 温 冷 却 干 车 低 削 加 工 和 激 光 辅 助 干 车 削 加 工 等 。 中 尤 其 以 硬 车 削 其
应 用最 为普遍 。
1 1 硬 车 削 的 定 义 .
造 业 必 将持 续 发 展 , 求 产 品 的制 造 过程 应 当在保 证 要 高 生产 效率 和 优 良质量 的 同时 , 能 维 护生 态 良性循 又
标 值 的划 分精 度有 关 。 时 , 超磁致 伸 缩材 料在 机械 同 为
加 工 领 域 的 应 用 奠 定 了 理 论 基 础 , 为 活 塞 裙 面 制 造 将 业 提供 一种 新 的加工 方法 。
4 王 晓江, 蔡永林 。 陈耿. 曲面造 型及数加工工具 轨迹生成方
法 的研究 【】模具技术,0 3 () J. 20,4.
硬车削加工技术分析

硬车削加工技术分析王丽红(漯河高级技工学校,河南漯河462000)臻自要]硬车削技*-4-着传统加工无可比拟的优势,是高硬材料精加工的发展方向,本文从工艺系统中的刀具、机床、夹具以及硬车削加工中应注意问题入手,阐述了硬车N加-r-的技术特点。
联键词]硬车削;工艺系统;刀具材料;白化层随着现代科学技术的不断发展,具有高硬度、高耐磨性、高耐热性、离化学稳定性的难加工材料的应用日益增多,僵同时也带来了一个难题,传统的车削技术难以胜任或根本无法实现对这些高硬度材料的精j]0-r-,而一直采用磨削加工,由于超硬材料刀具的出现及数控机床等加工设备精度的提高,以硬切削来完成零件的最终加工成为一种新的精加工途径。
1硬车削及其特点通常所说的硬车削是指对高硬度工件进行单点车削并作为最终精/J t]T-r序的工艺方法。
通常该工艺的硬度范围是H R C45一H R C68。
它主要是精力rl T I艺,要求在尺寸外形和表面粗糙度上达到很高的精度。
以前是对这些表面进行磨削加工。
与磨削相比硬态车削有如下特点:1.1加工效率高、经济效益好去除相同体积的金属时,硬车削往往可以采用较大的切削深度和较高的转速,而磨削则只能采用小切深,否则容易产生磨削烧伤,径向分力大引起变形,硬车削的金属去除率可为磨削的3~4倍,能耗仅为磨削的1/5:车削一次装夹可完成多表面的加工,磨削贝0不能。
12是一种洁净的加工工艺硬车削所用的刀具,基本可不使用切削液,这样就节省了相关的切削液传输装置和处理装置,大大节省了投资费用;切削液中一般都含有毒有害物质,会对环境造成污染,也损害了操作者的健康。
13可获缮良好的整体加工质量工件安装次数的减少,可使工件得到较高的位置精度和圆度,车削不会引起表面烧伤和微裂纹。
目前硬车削的加工精度可达IT5级,表面粗糙度R a可达O B~02um。
2硬车削加工对工艺系统的要求21刀具,i'4-44-常用于硬车削加工的刀具材料主要有以下几种:涂层硬质合金:涂层通常起到以下两方面的作用:一方面,它具有比刀具基体和工件材料低得多的热传导系数,减弱了刀具基体的热作用;另一方面,它能够有效地改善切削过程的摩擦和粘附作用,降低切削热的生成。
硬车削加工技术的应用研究

生 产要求 。
收 稿 日期 :2 1- 41 0 O0 —9
陶瓷 刀具 具有 高硬 度 ( 硬度HRA9  ̄HR 5 、 1 A9 ) 高 强 度 ( 弯 强 度 为 7 0MP 10 0MP ) 抗 5 a 0 a ,且 耐 磨 性 好 、化学稳 定性好 、抗 粘结性能 好 、摩擦 系数低 。正常 使 用 时 ,耐用 度极 高 ,车速 可 比硬 质合 金提 高2倍 ~5 倍, 特别适 合 高硬度材 料加工 、 精加 工 以及高 速加工 , 可 加工 硬度 高于 HRC6 2的各类淬硬 钢和硬 化铸铁 。 2 1 3 立 方 氮化 硼 C N 刀具 . . B 立 方 氮化 硼 的硬 度 和耐磨 性仅 次 于金 刚石 ,有 极 好 的高 温硬 度 ,与陶 瓷刀 具相 比 ,其 耐热 性 和化学 稳 定 性稍 差 ,但 冲击 强 度和 抗破 坏性 能较 好 。它 广泛 适 用 于淬 硬钢 ( HRC O以上 ) 珠 光体 灰铸 铁 、冷 硬铸 铁 5 、 和 高温合 金 等 的切 削 加工 。 2 2 刀 片结 构及 几何 参数 确 定 .
通 常所 说 的硬 车削 是指 把淬 硬 钢 的车削 作为 最终
加 工或 精加 工 的工 艺方 法 。淬硬 钢通 常是 指 淬火后 具
高 的尺 寸形 状精 度 和 良好 的表面 加工 质量 ,又能很 好 地保 证加 工 表 面之 间 的位置 精度 。
2 硬 车 削 加 工 的 条 件
有 马 氏体组 织 ,硬度 高 ,强 度也 高 ,几乎 没 有塑性 的 工 件 材料 ,其 硬 度HRC 5 ,其 强度 为 21 0MP > 5 0 a 26 0MP 。 车 削的加 工精 度 可达 5弘 0 a 硬 m~1 m, 0 表 面 粗糙 度 Ra可 达 0 2 . m ~0 3 m。 .
硬车削加工技术在实际工作中的应用研究

14 对 工 艺 系统 的要 求 .
若车床或车削 中心刚度足够, 、 刀具 工件 、 紧装置结构紧 夹 凑且具有 同等的刚性, 且加工一般工件 时能得到所要求的精度
和表面粗糙度, 即可用于淬硬钢的加工。
2 硬 车 削 加 工技 术 的 应 用
23 汽 车 加 工 行 业 .
f) 3 立方氮化硼C N J 。 B f 具 立方氮化硼 的硬度和耐磨性仅次
于金 刚石, 有极好 的高温硬 度, 与陶瓷刀具相 比, 其耐热性 和化 学稳定性稍差, 冲击强度 和抗破坏性 能较好 。它广泛适用于 但
淬硬钢( C 0:A)珠光体灰铸铁 、 HR 5 1 :、 / 冷硬铸铁和高温合金等 的
技术与市场
第1卷第9 0 0 7 期2 1年
墩 桊 珊
硬车削加 工技术在 实 际工作 中的应用研究
黄洪根
f 苏州_ 业 职业技 术 学 院 机 电机 系 , 苏 苏州 2 5 0 ) T - 江 1 14
摘 要 : 车 削的 加 工 效 率 是 普 通 磨 削 加 工 的4 6 , 消耗 的 能 量 是 普 通 磨 削 加 工 的 1 。硬 车 削 往 往 采 用 大 的 背吃 刀 硬 ~倍 所 / 5
工 。轴承内圈( 材料G r5的硬度H C 0内圈直径为 C l) R 6, 削加工后 , 4 mi就加工完成 了。 { 5 n  ̄
3 硬 车 削 加 工 中 必 须考 虑 的 几 个 问题
工时 建议 用 圆形 及 大半 径刀 片 ,精加 工 时选 择 刀尖半 径 为
08 m 1 m。淬 硬钢切 削力 比较大 , . . 2 特别是径 向切 削力 比 主切削力还要大, 以刀具宜采 用负前角( 5 和较大 的后 所 ≥一 。)
软技术与硬技术的关系

软技术与硬技术的关系软技术和硬技术是两个不同的概念,但它们在现代技术领域中却是密不可分的。
软技术指的是人类在工作中所使用的技能和技术,如沟通、领导力、协作能力等;硬技术则指的是机器、设备和程序等方面的技术,如计算机编程、机械工程等。
本文将探讨软技术和硬技术之间的关系,以及它们在现代社会中的重要性。
软技术和硬技术的关系软技术和硬技术之间的关系可以用一个简单的比喻来解释:硬技术是汽车的引擎和车架,软技术则是驾驶员的驾驶技能和行车规范。
硬技术是创造和实现的过程,而软技术则是使用和应用的过程。
软技术和硬技术之间的关系是相互依存的,它们互相补充,共同构成了现代技术领域的基础。
硬技术的发展离不开软技术的支持。
虽然硬技术是由科学家和工程师们设计、制造和实现的,但它们需要被人类使用和应用。
如果没有人类的软技术支持,硬技术的发展将无法实现最终的目标。
例如,在计算机编程领域,程序员需要具备良好的沟通、协作和领导能力,才能够与团队成员合作完成任务。
软技术的提升使得硬技术的实现更加高效和精准。
相反,软技术的发展也离不开硬技术的支持。
在现代社会中,软技术的应用范围越来越广泛,如社交媒体、在线交易平台、远程医疗等。
这些应用需要依靠硬技术的支持,如网络技术、数据库技术、安全技术等。
硬技术的发展为软技术的应用提供了更好的技术支持,使得软技术的应用范围不断拓展。
软技术和硬技术的重要性软技术和硬技术在现代社会中的重要性不言而喻。
软技术是人类应对各种挑战和机遇的能力,如沟通、协作、领导力等。
软技术的提升可以帮助人类更好地应对各种社会和工作环境的变化,提高个人和团队的工作效率和质量。
例如,在商业领域中,一个拥有良好的沟通和领导力的管理团队可以更好地协调各部门之间的工作,提高企业的竞争力。
硬技术则是现代社会中各种产业的基础。
从工业到农业,从医疗到教育,硬技术的应用范围越来越广泛。
硬技术的发展可以帮助人类更好地应对各种挑战和机遇,提高生产效率和产品质量。
硬管加油技术难在哪,为什么全世界只有美国使用这类技术?

硬管加油技术难在哪,为什么全世界只有美国使⽤这类技术?硬管可允许发⽣的位移⾮常⼩,⼀旦超出其允许范围,就有可能发⽣破裂漏油。
下⾯我就从⼒学的⾓度,稍微详细解析下硬管加油技术难点。
1、空中加油的运动状态战⽃机不像客机,对机动性要求很⾼,这就决定了其油箱容量较⼩,从⽽减轻整机的重量,获得更⾼的机动性,这就造成了续航能⼒的下降。
于是,空中加油应运⽽⽣,既保证了战⽃机的机动性,⼜提⾼了其续航能⼒。
在讨论加油之前,⾸先的弄清楚飞机在空中的状态。
如上图,分别为偏航、横滚和俯仰,即可以饶三个坐标轴进⾏旋转。
此外,飞机还可以沿着三个坐标轴进⾏平⾏移动。
从⼒学上来说,我们称飞机具有6个⾃由度(三个位移和三个旋转)。
在空中,飞机完全是⾃由的状态,⽓流的影响对飞机的状态就⾮常⼤,飞机的6个⾃由度时时刻刻都在发⽣改变。
在加油的过程中,飞机的受⼒如上图,有向上的升⼒、向下的⾃重、前进的推⼒和空⽓的阻⼒。
此外,油管结构对飞机的⼒不可忽视。
在加油的过程中,这个⼒才是最重要的⼒,如图斜箭头所⽰。
2、硬管、软管加油的优缺点油⽓管道的建设中,除了末端的加油加⽓部分,传输部分全部都是硬管道。
我们在汽车加油站加油,连接加油枪的就是软管。
实际上,硬管、软管的优缺点⾮常明显。
对于软管来讲,可活动的范围更⼤,在空中加油的时候对两者的同步性要求可以降低。
但是,软管⽆法做的太粗(太粗的软管结构承载能⼒不⾏),影响了加油效率。
所以,在⽣活中,软管仅⽤来末端输⼊,⽽不是⽤来传输。
硬管可以提供更⼤的流量,提⾼加油的效率。
但是很显然,硬管太硬,⽆法⾃由移动,⽓流容易使之产⽣较⼤的应⼒,从⽽发⽣破坏。
此外,软管容易受⽓流影响,被吹的飘来飘去。
3、硬管加油技术难点通过上⾯的分析,硬管加油的技术难点已经跃然纸上。
由于飞机具有六个⾃由度,⽓流很容易影响飞机的位置。
在加油的过程中,加油机和战⽃机始终不可避免地发⽣相对位移。
这个相对位移,对硬管来⽔是致命的。
因为,硬管要求的允许相对位移⽐起软管要⼩的多。
- 1、下载文档前请自行甄别文档内容的完整性,平台不提供额外的编辑、内容补充、找答案等附加服务。
- 2、"仅部分预览"的文档,不可在线预览部分如存在完整性等问题,可反馈申请退款(可完整预览的文档不适用该条件!)。
- 3、如文档侵犯您的权益,请联系客服反馈,我们会尽快为您处理(人工客服工作时间:9:00-18:30)。
浅谈车削加工的新工艺——硬车技术目录一.什么是硬车技术‥‥‥‥‥‥‥‥‥‥‥‥‥‥‥‥‥‥‥2二、硬车技术的特点‥‥‥‥‥‥‥‥‥‥‥‥‥‥‥‥‥‥‥31、硬车削加工效率高‥‥‥‥‥‥‥‥‥‥‥‥‥‥‥‥‥‥‥ 32、硬车削是洁净加工工艺‥‥‥‥‥‥‥‥‥‥‥‥‥‥‥‥‥‥ 33、设备投资少,适合柔性生产要求‥‥‥‥‥‥‥‥‥‥‥‥‥‥‥34、硬车削可使零件获得良好的整体加工精度‥‥‥‥‥‥‥‥‥‥‥3三、硬车削的技术要求‥‥‥‥‥‥‥‥‥‥‥‥‥‥‥‥‥‥41、工件和刀具‥‥‥‥‥‥‥‥‥‥‥‥‥‥‥‥‥‥‥‥‥‥ 42、机床和工艺系统‥‥‥‥‥‥‥‥‥‥‥‥‥‥‥‥‥‥‥‥ 43、刀片‥‥‥‥‥‥‥‥‥‥‥‥‥‥‥‥‥‥‥‥‥‥‥‥‥ 54、冷却液‥‥‥‥‥‥‥‥‥‥‥‥‥‥‥‥‥‥‥‥‥‥‥‥ 55、加工工艺‥‥‥‥‥‥‥‥‥‥‥‥‥‥‥‥‥‥‥‥‥‥‥ 66、白化层‥‥‥‥‥‥‥‥‥‥‥‥‥‥‥‥‥‥‥‥‥‥‥‥ 67、镗孔‥‥‥‥‥‥‥‥‥‥‥‥‥‥‥‥‥‥‥‥‥‥‥‥‥ 68、车螺纹‥‥‥‥‥‥‥‥‥‥‥‥‥‥‥‥‥‥‥‥‥‥‥‥7四、硬车削的应用‥‥‥‥‥‥‥‥‥‥‥‥‥‥‥‥‥‥‥‥71、切削用量与切削条件‥‥‥‥‥‥‥‥‥‥‥‥‥‥‥‥‥‥‥72、加工零件及工艺参数‥‥‥‥‥‥‥‥‥‥‥‥‥‥‥‥‥‥‥7五、硬车削的发展‥‥‥‥‥‥‥‥‥‥‥‥‥‥‥‥‥‥‥‥8参考文献‥‥‥‥‥‥‥‥‥‥‥‥‥‥‥‥‥‥‥‥9【摘要】车削加工是机械制造业中最基本、最广泛、最重要的一种工艺方法,它直接影响生产的质量、效率、成本、能源消耗和环境保护。
由于现代科学技术的发展,各种高强度、高硬度的工程材料越来越多地被采用,传统的车削技术难以胜任或根本无法实现对某些高强度、高硬度材料的加工,而现代的硬车削技术使之成为可能,并在生产中取得明显效益。
硬车削是指把淬硬钢的车削作为最终加工或精加工的工艺方法,从而更容易控制切削用量,增加切屑去除量,可同时进行内孔和外圆切削,完成复杂外形工件的加工。
纵观工件加工过程,硬车技术削减了部分磨削工艺,而且在工件和刀具的安装上可节省340%时间,加工周期时间节省达575%。
【关键词】:硬车削新工艺高效在车削加工领域,对于复杂零件的和难加工材料的车削,一直是车削加工中困扰的难题。
随着高硬度切削材料和相关机床的发展,立方氮化硼刀具、陶瓷刀具及新型硬质合金刀具在新型车床或车削加工中心上的应用,对淬硬钢、高温合金的车削不再是难题,其加工质量可以达到精磨的水平。
在发达国家硬车技术已被普遍应用于各种零件加工,大多数硬车技术的应用已成功替代了磨削。
一、什么是硬车技术一般情况下,车削只是淬火前进行的粗加工。
直到20世纪90年代前,淬火后的精加工还只能采用磨削工艺,而车削也只能加工硬度值低于55HRC的工件。
硬车技术,简称硬车削(即以车代磨)。
通常所说的硬车削是指把悴硬钢的车削作为最终加工或精加工的工艺方法,以替代目前普遍采用的磨削技术。
淬硬钢通常指淬火后具有马氏体组织,硬度高,强度也高,几乎没有塑性的工件材料。
当淬硬钢的硬度 >55HRC时,其强度sb约为2100~2600N/mm2。
利用多晶立方氮化硼(PCBN)刀具、陶瓷刀具或涂层硬质合金刀具等在车床或车削加工中心上采用硬车削对淬硬钢(55~65HRC)进行加工,其加工精度可达IT5,表面粗糙度Ra≤0.4μm。
二、硬车技术的特点1、硬车削加工效率高硬车削具有比磨削更高的加工效率,且其所消耗的能量是普通磨削加工的1/5 。
硬车削往往采用大切削深度和较高的工件转速,其金属切除率通常是磨削加工的3~4倍。
硬车削加工时一次装夹即可完成多种表面加工(如车外圆、车内孔、车槽等),而磨削则需要多次装夹。
因此,硬车削的辅助时间短,加工表面之间位置精度高。
2、硬车削是洁净加工工艺大多数情况下,硬车削无须冷却液。
事实上,使用冷却液会给刀具寿命和表面质量带来不利影响。
因为,硬车削是通过使剪切部分的材料退火变软而实现切削的。
而在使用冷却液的加工工艺过程中,若冷却率过高,就会减小由切削力而产生的这种效果,从而加快机械磨损,缩短刀具寿命。
同时硬车削可省去相关的冷却液配套装置,从而降低生产成本,简化生产系统,形成的切屑干净清洁,易于回收处理容易。
3、设备投资少,适合柔性生产要求在生产率相同时,车床投资是磨床的1/3~1/2,其辅助系统费用也低。
对于小批量生产而言,硬车削不需特殊设备,而大批量加工高精度零件则需耍使用刚性好、定位精度和重复定位精度高的数控机床。
车床本身就是一种加工范围广的柔性加工方法,车削装夹快速,采用配有多种刀具转盘或刀库的现代CNC车床很容易实现两种不同工件之间的加工转换,硬车削尤其适合此类加工。
因此,与磨削相比,硬车削能更好地适应柔性化生产要求。
4、硬车削可使零件获得良好的整体加工精度硬车削过程中产生的大部分热量能被切屑带走,不会产生象磨削加工过程中出现的表面烧伤和裂纹,具有优良的表面加工质量,有精确的加工圆度,确保加工表面之间较高的位置精度。
三、硬车削的技术要求硬车削的目标是随切屑带走至少80%的热量,以保持零件的热稳定性。
合理的硬车削系统可以减少甚至省去磨削以及与之相关的高昂的刀具成本和较长的加工时间。
采用合理的硬车削工艺可获得0.0028μm的表面光洁度、0.0002μm的圆度和±0.005μm的直径公差。
要想这样的精度在对淬硬前工件进行“软车削”的相同机床上达到这样的精车,从而最大限度地提高设备利用率不是不可以实现的。
但由于某些工厂错误地选用了刀片(确切地说是选用了廉价刀片),或不清楚所用机床是否具有足够的刚性以承受二倍于普通车削的压力,从而使得硬车削工艺没有充分地、完全地发挥出其高率。
因此,硬车削时须注重以下8个方面:1、工件和刀具尽管45HRC硬度是硬车削的起始点,但硬车削经常在硬度高于60HRC以上硬度的工件上进行。
硬车削材料通常包括工具钢、轴承钢、渗碳钢以及铬镍铁合金、耐蚀耐热镍基合金、钨铬钴合金等特殊材料。
根据冶金学,在切深范围内硬度偏差小(小于2个HRC)的材料可显示出最好的过程可预测性。
最适合于硬车削的零件具有较小的长径比(L/D),一般来说,无支撑工件的L/D之比不大于4:1,有支撑工件的L/D之比不大于8:1。
尽管细长零件有尾架支撑,但是由于切削压力过大仍有可能引起刀振。
在传统刀具制造中,刀柄材料通常是45钢调质到HB210-240,而在硬车削工艺中采用的刀柄硬度应提高1.5倍。
为了最大限度地增加硬车削的系统刚性,刀具伸出长度不得大于刀杆高度的1.5倍,工件在装夹时也应尽量减小悬伸长度。
2、机床和工艺系统除选择合理的刀具外,机床刚度决定了硬车削的加工精度。
近15~20年内制造的机床几乎都有很好的刚性,足以承受硬车削。
若车床或车削中心刚度足够,且加工软的工件时能得到所要求的精度和表面粗糙度,即可用于淬硬钢的加工,精心维护的普通车床都可以用于硬车削。
为了保证车削操作的平稳和连续,常用的方法是采用刚性夹紧装置和中等前角刀具。
并保证工件在切削力作用下其定位、支承和旋转可以保持相当平稳。
系统刚性最大化意味着尽量减少悬空、刀具延伸和零件伸出,并取消调隙片和垫圈,其目标是保持所有零部件尽可能地接近转塔刀架。
3、刀片尽管立方氮化硼(CBN)刀片的价格昂贵,但CBN刀片最适合于硬车削。
CBN刀片能够在断续切削过程中保持定位不变,在连续切削过程中提供安全的刀具磨损率。
当采用合理的硬车削工艺时,CBN刀片除了在控制直径公差方面比不上磨削以外,其它性能都是首屈一指的。
陶瓷不如CBN耐磨,因此一般不用于公差要求小于±0.025mm的加工。
陶瓷不适合于断续切削,而且不能加冷却液,因为冷热冲击可能造成刀片破裂。
刀片的钝缘几何形状是陶瓷材料的固有特点,这一特点使切削力增大而工件表面光洁度下降。
另外,陶瓷刀片刃口断裂可能是灾难性的,它可能导致所有切削刃均不能使用。
金属陶瓷(立方碳化钛)对连续切削渗碳硬化材料很有效,尽管它不具备CBN那样的耐磨性,但这类刀片在大多数情况下会成比例地磨损而不断裂。
正前角刀片由于其切削力较小,通常用在刚性不高的机床上进行硬车削。
关于刀片的最合理应用,建议与刀具供应商密切合作,特别是在最初阶段,以迅速达到最佳切削速度。
4、冷却液其最大问题是用还是不用冷却液。
对于齿轮之类的断续切削零件来说,最好采用“干车削”,否则进刀和退刀时的热冲击很可能引起刀片破裂。
至于连续切削,刀头在干车削过程中产生的高温足以韧化(软化)预切削区域,从而降低材料硬度使之易于剪切。
这个现象说明了干切削时增大速度是有益的。
同时,无冷却液切削方式具有明显的成本优势。
在连续切削中,冷却液可能有助于延长刀具寿命和提高表面光洁度。
问题的关键是要使冷却液能够到达刀头,高压喷吸冷却法是解决这个问题的最好办法,因为它不容易在高温下蒸发。
此外,高压可以减少切屑堆积,从而减少因为切屑阻塞对冷却液流至刀头的影响。
另一个办法是将冷却液同时喷压到刀片的顶部和底部,以确保冷却液连续到达刀头。
如果使用冷却液,其成份必须是水基的。
在完全匹配的硬车削过程中形成的切屑可以带走80%~90%的热量(切削区域最高温度可达1700°F)。
如此炽热的切屑一旦接触低燃点冷却油,整个工序将有可能遭到彻底破坏。
如果在敞开式机床上进行硬车削,必须增加适当的保护装置,避免操作人员被切屑烫伤。
5、加工工艺因为硬车削产生的热量大部分由切屑带走,加工前后对切屑进行检查可以发现整个过程是否协调。
连续切削时,切屑应该呈炽燃的橙黄色,并象一根缎带似地飘逸而出。
如果切屑冷却后用手一压基本断裂,表明切屑带走的热量是正常的。
6、白化层令人讨厌的“白化层(热影响区)”可能出现在硬车削和磨削操作中,即在材料表面形成一层肉眼看不见的非常薄(通常1μm)的硬壳。
在硬车削过程中形成白化层,一般是因为刀片钝化导致过多的热量传递到零件内部。
白化层经常在轴承钢上形成,而且对于轴承圈之类需要承受高接触压力的零件是非常有害的,随着时间的推移,白化层可能剥离并导致轴承失效。
对于刚开始从事硬车削的工厂,建议在生产的头几周内进行随机抽查,以确定每个刀片能够车削多少零件而不形成白化层。
另外,一个刀片即使可加工400个零件,也有可能在加工300件后就变钝并且开始使零件表面产生白化层。
7、镗孔镗削淬硬材料需要很大的切削压力,因此往往需成倍增加镗杆承受的扭力和切向力。
采用正前角(35°或55°)、小刀尖半径刀片可以减小切削压力。
在增加切削速度的同时减小切深和进刀速度,也是减小切削压力的办法。
镗孔时,刀具必须与零件同心或略高于零件中心,因为切削引起的挠曲变形会降低实际中心线的位置降低了。