标准工时与生产效率
生产效率的计算
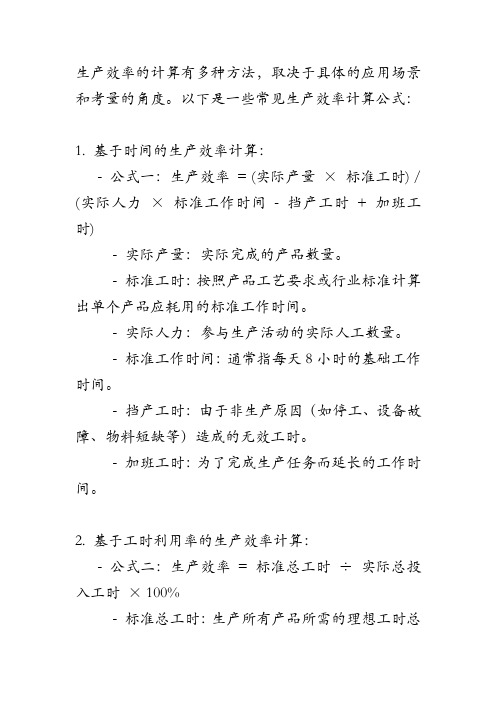
生产效率的计算有多种方法,取决于具体的应用场景和考量的角度。
以下是一些常见生产效率计算公式:
1. 基于时间的生产效率计算:
- 公式一:生产效率= (实际产量× 标准工时) / (实际人力× 标准工作时间- 挡产工时+ 加班工时)
- 实际产量:实际完成的产品数量。
- 标准工时:按照产品工艺要求或行业标准计算出单个产品应耗用的标准工作时间。
- 实际人力:参与生产活动的实际人工数量。
- 标准工作时间:通常指每天8小时的基础工作时间。
- 挡产工时:由于非生产原因(如停工、设备故障、物料短缺等)造成的无效工时。
- 加班工时:为了完成生产任务而延长的工作时间。
2. 基于工时利用率的生产效率计算:
- 公式二:生产效率= 标准总工时÷ 实际总投入工时× 100%
- 标准总工时:生产所有产品所需的理想工时总
量。
- 实际总投入工时:实际用于生产的员工总工作时间,包括有效工作时间和可能出现的损失工时。
3. 全员劳动生产率计算:
- 公式三:全员劳动生产率= 工业增加值/ 全部从业人员平均人数
- 工业增加值:一定时间内工业生产创造的新价值,体现了生产效率的经济效益层面。
4. 实物量或产值计算:
- 公式四:生产效率= 实际产出量/ 投入综合因素
- 投入综合因素可以包括物资、劳动力、资本等多种资源的投入。
在计算生产效率时,可根据具体情况选取适当的计算模型,同时也要考虑到生产环境的变化、设备状态、管理水平、生产流程等因素对效率的影响。
此外,生产效率的提升不仅关注产量,也包括质量、能耗、成本等方面的综合考量。
生产效率计算方法
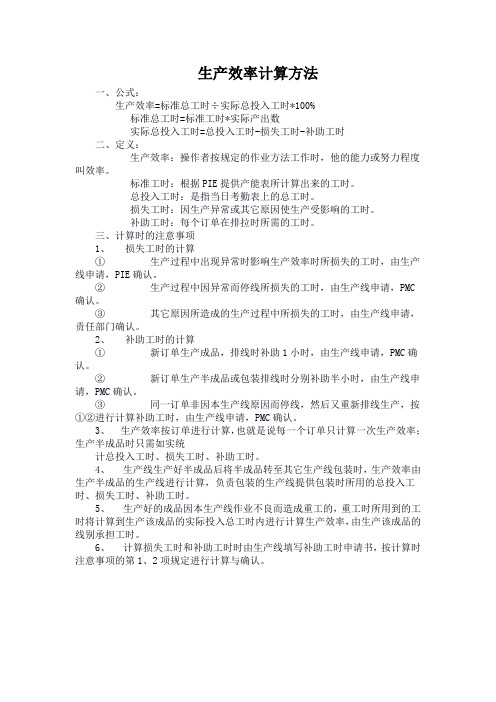
生产效率计算方法一、公式:生产效率=标准总工时÷实际总投入工时*100%标准总工时=标准工时*实际产出数实际总投入工时=总投入工时-损失工时-补助工时二、定义:生产效率:操作者按规定的作业方法工作时,他的能力或努力程度叫效率。
标准工时:根据PIE提供产能表所计算出来的工时。
总投入工时:是指当日考勤表上的总工时。
损失工时:因生产异常或其它原因使生产受影响的工时。
补助工时:每个订单在排拉时所需的工时。
三、计算时的注意事项1、损失工时的计算①生产过程中出现异常时影响生产效率时所损失的工时,由生产线申请,PIE确认。
②生产过程中因异常而停线所损失的工时,由生产线申请,PMC确认。
③其它原因所造成的生产过程中所损失的工时,由生产线申请,责任部门确认。
2、补助工时的计算①新订单生产成品,排线时补助1小时,由生产线申请,PMC确认。
②新订单生产半成品或包装排线时分别补助半小时,由生产线申请,PMC确认。
③同一订单非因本生产线原因而停线,然后又重新排线生产,按①②进行计算补助工时,由生产线申请,PMC确认。
3、生产效率按订单进行计算,也就是说每一个订单只计算一次生产效率;生产半成品时只需如实统计总投入工时、损失工时、补助工时。
4、生产线生产好半成品后将半成品转至其它生产线包装时,生产效率由生产半成品的生产线进行计算,负责包装的生产线提供包装时所用的总投入工时、损失工时、补助工时。
5、生产好的成品因本生产线作业不良而造成重工的,重工时所用到的工时将计算到生产该成品的实际投入总工时内进行计算生产效率,由生产该成品的线别承担工时。
6、计算损失工时和补助工时时由生产线填写补助工时申请书,按计算时注意事项的第1、2项规定进行计算与确认。
生产效率ope的计算公式

生产效率ope的计算公式生产效率(OPE,Overall Production Efficiency)是指企业或组织在一定时间内所实现的生产产值或服务价值与相关资源投入的比率。
计算生产效率有多种方法,以下是两种常见的计算公式:1.生产效率=有效产出/总输入其中,有效产出是指在一定时间内真正对外提供的产品或服务的价值,包括销售额、产量等;总输入是指为了产出这些产品或服务所耗费的全部资源,包括人力、物力、财力等。
例如,企业在一周内的生产效率计算如下:有效产出=销售额=100,000元总输入=员工工资+原材料费用+设备折旧=50,000元生产效率=100,000元/50,000元=2这意味着该企业每投入1元的资源,可以创造2元的销售额。
2.生产效率=标准工时/实际工时其中,标准工时是指完成一项特定任务或工作所需的合理时间,通常通过工作量和生产能力来确定;实际工时是指实际完成这项工作所花费的时间。
例如,工人在完成一件任务时,标准工时为10小时,实际工时为8小时。
生产效率=10小时/8小时=1.25这意味着该工人在同样的时间内,能够完成1.25倍标准工时的工作量。
为了提高生产效率,企业可以采取以下措施:1.优化流程:通过开展流程改进,消除不必要的环节和浪费,提高生产效率。
2.提升技术水平:引进先进的生产设备和技术,提高生产效率和品质。
3.培训员工:提升员工的技能和知识水平,提高工作效率和质量。
4.优化物料管理:合理安排物料的进货、存储和使用,减少浪费和损耗。
5.激励机制:建立激励机制,通过奖励和激励员工,促使其积极主动地提高生产效率。
总之,生产效率是企业实现高效生产和创造价值的关键指标,通过合理的绩效评估和持续的改进措施可以不断提高生产效率,实现可持续发展。
标准工时和生产效率

D
E1 可
E2
F1 欠 佳 F2
+0.15 +0.13 +0.11 +0.08 +0.06
+0.03
0.00 -0.05 -0.10 -0.16
(1)超佳
有高度的技术; 动作极为迅速,衔接圆滑;
动作犹如机器作业; 熟练程度最高;
(2)优
对所担任的工作有高度的适应性; 十分有效的使用机器设
能够正确的工作而不需检查,核对;工 备;动作很快且正确;
宽放率 %
3.5 6.0 7.0 0 1.0 1.5 1.75 0 0.3 1.0 1.5 0 0.2 0.6 0.75 0 0.3 0.4 0.7 0 0.3 0.4 0.7
工厂取值%
标准工时宽放项目与宽放率
项次 宽放项目
2
疲劳宽放
评价项目 单调性
创造性注意力
对责任与危 险注意度
环
境
评 价内 容
所谓特定熟练程度的作业者是指经过训练,肉体和精 神上可以适应并能充分完成工作的作业员。
标准工时的作用
需配置多少机器 需雇佣多少員工 计算产品成本 排定生产计划 以现有之设备及人工, 可处理多少工作 如何规划机器,工作站,各部门和员工的排程 如何平衡生产线,使每一工作站的负荷均等 如何衡量生产力 如何奖励杰出员工 如何选择较佳的方法或评估降低成本的方法 如何评估采购新设备及其费用的依据 如何编制人力预算
平均时间
评比系数 宽放系数
作业时间
标准时间
标准工时的计算
标准工时 = [平均实操工时×(1+评比系数)] + (正常时间×宽放
系数) = 正常时间×(1+宽放系数)
标准工时与生产效率
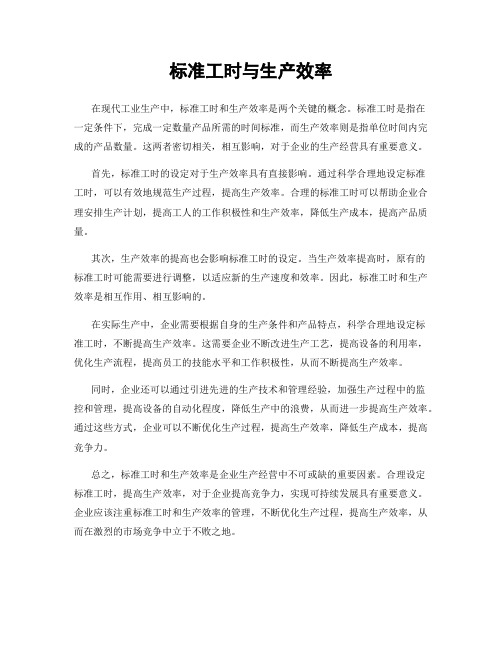
标准工时与生产效率
在现代工业生产中,标准工时和生产效率是两个关键的概念。
标准工时是指在
一定条件下,完成一定数量产品所需的时间标准,而生产效率则是指单位时间内完成的产品数量。
这两者密切相关,相互影响,对于企业的生产经营具有重要意义。
首先,标准工时的设定对于生产效率具有直接影响。
通过科学合理地设定标准
工时,可以有效地规范生产过程,提高生产效率。
合理的标准工时可以帮助企业合理安排生产计划,提高工人的工作积极性和生产效率,降低生产成本,提高产品质量。
其次,生产效率的提高也会影响标准工时的设定。
当生产效率提高时,原有的
标准工时可能需要进行调整,以适应新的生产速度和效率。
因此,标准工时和生产效率是相互作用、相互影响的。
在实际生产中,企业需要根据自身的生产条件和产品特点,科学合理地设定标
准工时,不断提高生产效率。
这需要企业不断改进生产工艺,提高设备的利用率,优化生产流程,提高员工的技能水平和工作积极性,从而不断提高生产效率。
同时,企业还可以通过引进先进的生产技术和管理经验,加强生产过程中的监
控和管理,提高设备的自动化程度,降低生产中的浪费,从而进一步提高生产效率。
通过这些方式,企业可以不断优化生产过程,提高生产效率,降低生产成本,提高竞争力。
总之,标准工时和生产效率是企业生产经营中不可或缺的重要因素。
合理设定
标准工时,提高生产效率,对于企业提高竞争力,实现可持续发展具有重要意义。
企业应该注重标准工时和生产效率的管理,不断优化生产过程,提高生产效率,从而在激烈的市场竞争中立于不败之地。
工时与效率

工时管理与生产效率一、工时概念1.标准工时1.1定义:标准工时是一名操作熟练程度中等偏上的作业人员,在机器设备、物料等生产条件正常的情况下,以标准作业方法,顺利流畅地完成符合质量要求的一道工序或一个组件或一个产品所需的作业时间。
1.2说明:a)操作熟练程度中等偏上:能够担任高精度的工作,可以指导他人提高操作熟练程度,对作业流程\器具使用非常熟悉,操作有效,动作迅速且正确。
b)生产条件正常:机器设备运行良好,工模具齐备,物料供应顺畅,人员配合到位,环境符合要求。
c)标准作业方法:作业标准(如《作业指导书》)规定的操作方法。
d)顺利流畅地完成:对外届影响的要求。
e)符合质量要求:只有符合质量要求,完成的作业才有效。
1.3标准工时的制定1.3.1制定方法目前,制定标准工时经常采用的方法有如下四种﹕秒表法、经验判断法、历史记录法、预定时间标准法。
我公司目前的采用的方法是历史记录法加经验判断法,逐步应该推行秒表法。
由于公司产品的特殊性,用户个性化比较强,标准化工作还需要改进,所以更准确的定义应该是产品的定额工时。
只有对产品进行彻底的标准化、系列化、模块化改善,细化作业单元,才有可能利用秒表法对标准工时进行彻底的优化。
1.3.2秒表法制定标准工时秒表法制定标准工时是指在一段有限的时间内﹐连续地直接观测作业者的作业﹐除了记录工作次数与工作时间之外﹐还要与标准作业的观念比较﹐赋予一个估计值﹐然后再考虑工作之外的放宽时间,即得标准工时。
标准工时=标准主体作业时间(净作业时间+宽放时间)+准备作业时间(净准备时间+宽放时间);标准作业时间由工艺过程决定,主要为直接增加产品价值的人工/机器时间消耗。
对标准工时的降低只能通过工艺改善和辅助时间降低。
宽放时间﹕正常时间仅指一位合格胜任的工人﹐以正常速度运行该工作所需的时间﹔经验告诉我们﹐一个人不可能没有任何中断的整天以相同的速度操作﹐在操作中﹐因私事原因、疲劳、不可避免之延迟等因素的影响﹐使工作中断﹐操作时间增加﹔设定宽放值,加入足够的时值在正常生产时间内﹐使以正常速度操作的员工能合理地达到标准。
生产效率计算说明new

生产效率计算方法
一、公式:
生产效率=标准总工时÷实际总投入工时*100%
标准总工时=标准工时*实际产出数
实际总投入工时=总投入工时-损失工时-补助工时
二、定义:
生产效率:操作者按规定的作业方法工作时,他的能力或努力程度叫效率。
标准工时:根据PIE或工程提供产能表或C/T周期时间所计算出来的工时。
总投入工时:是指当日考勤表上的总工时。
损失工时:因生产异常或其它原因使生产受影响的工时。
如,修模等
补助工时:每个订单在排拉或换线时所需的工时。
三、计算时的注意事项
1、损失工时的计算
①生产过程中出现异常时影响生产效率时所损失的工时,由生产线申请,
PIE或工程确认。
②生产过程中因异常而停线所损失的工时,由生产线申请,PMC确认。
③其它原因所造成的损失工时,由生产线申请,责任部门确认。
2、生产效率按订单进行计算,也就是说每一个订单只计算一次生产效率;生
产半成品时只需如实统计总投入工时、损失工时、补助工时。
3、生产好的成品因本生产线作业不良而造成重工的,重工时所用到的工时将
计算到生产该成品的实际投入总工时内进行计算生产效率,由生产该成品
的线别或班组承担工时。
标准工时与效率分析

SDM Division
标工的用途:
1、公司可以以之来计生产力,制定各项标准,如:标准成本、标准要员、机械负荷等,从而使各 项有一个明确的基准,只有在有明确的情况下,公司的管理才会相应地走向正规化。
2、标工的使用和维护过程,便是督导现场改善的过程。标工以及在标工基础上的各种标准制定以 后,各职场在既定目标的基准上,才能得以检验自已职场的得失,去找问题点,并针对问题进行改 善。
1、基本创作:
不含困难性的动作【即不含操作因素(W、S、P、U、D)】基本动作的时间只与移动的距离 有关,但并不成正比。
2、基本动作随身体使用部位之不同而不同。
3、有困难性的动作,所需时间较基本动作为长,长的程度与动作困难性的数目有关,与种类无关。
4、动作困难性的种类:
W——Weight
工作物或阻力
2、握取
Gr——Grasp
3、放开
RL——Release
4、前置
PP——Preposition
5、组立
Asy——Assembly
6、使用
Use
7、分解
Dsy——Disassembly
8、精神作用 Mp——Mental Process
真正有附加价值的动作只有组立、使用、分解,故在简化动作时要减少其它动 作的产生。
型號:PT-195
工序号
工序名称
1 揀火牛/穿PCA引線
2 焊火牛次級引線
3 穿火牛輸入線
4 焊火牛輸入線
5 剪線頭/掃錫珠
6 装火牛
7 装PCA
16/07/2024
生產線平衡分析表(生产使用中)
设备/工装
控制重点
生产效率与标准工时管理办法

生产效率与标准工时管理办法-CAL-FENGHAI-(2020YEAR-YICAI)_JINGBIAN富士康科技集团生产效率与标准工时管理办法一,目的.规范各(M)BU对”综合效率” 、“投入工时有效率”、“有效工时产出率”三项KPI指标的统计办法﹐明确各相关数据的计算标准。
.统一各(M)BU对标准工时的制定标准﹐提高标准工时的时效性和准确度。
.通过此管理办法﹐全面了解产生无效工时的原因﹐找出非生产因素并加以改善﹐提高生产效率。
二,三项KPI指标的公式及其意义2.1.三项KPI指标的公式2.1.1.投入工时有效率(E1)=有效工时/投入工时投入工时有效率的意义在于找出生产过程中因管理原因而产生的无效时间。
2.1.2.有效工时产出率(E2)=产出工时/有效工时有效工时产出率的意义在于找出生产过程中因操作方法不当而产生的无效时间﹐并加以改善。
2.1.3.综合效率(E)=总产出工时/总投入工时=投入工时有效率*产出工时有效率综合效率的意义在于找出生产过程中所有的非生产因素﹐并加以改善。
※由上可以看出﹐一般情况下﹐此三项KPI 指标的计算值都<100%﹔反之﹐则可能是参与计算的各项数据资料统计有误﹐需要重新修订。
.相关参数的定义2.2.1.投入工时投入工时﹕投入工时指的是员工的支薪工时﹐包括正常上班时间和加班时间两部分﹐也就是从人资系统导出的员工实际刷卡工时。
投入工时=正常班工时+加班工时2.2.2.有效工时有效工时=投入工时-损失工时2.2.3. 损失工时损失工时﹕损失工时包括换线、待料﹑来料不良﹑机故﹑试样、重工、等损失的时间。
※在标准工时的制定中﹐计入到宽放时间的不计入在损失时间里面。
2.2.4.产出工时产出工时=产出数量*标准工时2.2.5.产出数量产出数量﹕产出数量指的是在生产过程中产出的合格产品的数量,可以是从SAP 或SFC 系统中下载的数据﹐也可以是在仓库的入库记录表中查得的数据。
成本实操-生产效率计算公式
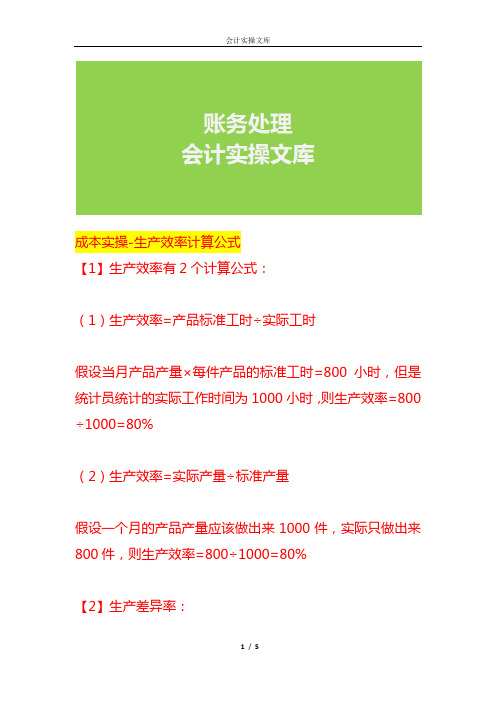
成本实操-生产效率计算公式【1】生产效率有2个计算公式:(1)生产效率=产品标准工时÷实际工时假设当月产品产量×每件产品的标准工时=800小时,但是统计员统计的实际工作时间为1000小时,则生产效率=800÷1000=80%(2)生产效率=实际产量÷标准产量假设一个月的产品产量应该做出来1000件,实际只做出来800件,则生产效率=800÷1000=80%【2】生产差异率:(1)生产差异率=(实际工时÷标准工时)-1(2)假设前例生产效率=80%,并不是说生产差异率=(1-80%)=20%。
生产效率为80%的意思是说,用100个工时制作出来了相当于80个标准工时制作出来的产品,真正的生产差异率=(1000÷800)-1=1.25-1=25%(3)假设生产效率=50%,并不是说我们的工作做了一半,离百分百的完美结果只差一半,生产差异率=(1-50%)=50%。
不是这样的,生产效率为50%的意思是说,用100个工时制作出来了相当于50个标准工时制作出来的产品,真正的生产差异率=(1000÷500)-1=2-1=100%。
【3】生产不良率,也叫不合格品率:生产不良率=不良品数量÷生产数量=不合格品数量÷生产数量【4】生产返修率:生产返修率=返修品数量÷生产数量【5】生产报废率:有2个公式:(1)生产报废率=报废品数量÷(完工入库的产成品数量+报废品数量)(2)生产报废率=报废品成本÷(完工入库的产成品成本+报废品成本)【6】质检退货率:质检退货率=退货产品数量÷送检产品数量【7】客户退货率:有2个公式:(1)客户退货率=退货产品数量÷产品销售数量;(2)客户退货率=退货产品金额÷产品销售收入【8】材料超额领用率:有2个公式:(1)材料超额领用率=材料超额领用数量÷材料定额领用数量;(2)材料超额领用率=材料超额领用成本÷材料定额领用成本;【9】生产排程达成率:生产排程达成率=实际生产数量÷计划安排生产的数量【10】生产目标达成率:有2个公式:(1)如果这个目标是一种越高越好的目标,则①生产目标达成率=实际数量÷目标数量②生产目标达成率=实际金额÷目标金额(2)如果这个目标是一种越低越好的目标,则①生产目标达成率=1-[(实际数量-目标数量)÷目标数量]②生产目标达成率=1-[(实际金额-目标金额)÷目标金额]【11】劳动力指标:(1)每直接人工生产力=生产一线人均产量=产品折算标准工时÷生产一线员工合计数;(2)每员工生产力=全公司人均产量=产品折算标准工时÷全公司所有的员工;(3)人均销售额=销售额÷全公司所有的员工(4)人均利润=利润额÷全公司所有的员工。
生产效率计算方法

生产效率计算方法一、公式:生产效率=标准总工时÷实际总投入工时*100%标准总工时=标准工时*实际产出数实际总投入工时=总投入工时-损失工时-补助工时二、定义:生产效率:操作者按规定的作业方法工作时,他的能力或努力程度叫效率。
标准工时:根据PIE提供产能表所计算出来的工时。
总投入工时:是指当日考勤表上的总工时。
损失工时:因生产异常或其它原因使生产受影响的工时。
补助工时:每个订单在排拉时所需的工时。
三、计算时的注意事项1、损失工时的计算①生产过程中出现异常时影响生产效率时所损失的工时,由生产线申请,PIE确认。
②生产过程中因异常而停线所损失的工时,由生产线申请,PMC确认。
③其它原因所造成的生产过程中所损失的工时,由生产线申请,责任部门确认。
2、补助工时的计算①新订单生产成品,排线时补助1小时,由生产线申请,PMC确认。
②新订单生产半成品或包装排线时分别补助半小时,由生产线申请,PMC确认。
③同一订单非因本生产线原因而停线,然后又重新排线生产,按①②进行计算补助工时,由生产线申请,PMC确认。
3、生产效率按订单进行计算,也就是说每一个订单只计算一次生产效率;生产半成品时只需如实统计总投入工时、损失工时、补助工时。
4、生产线生产好半成品后将半成品转至其它生产线包装时,生产效率由生产半成品的生产线进行计算,负责包装的生产线提供包装时所用的总投入工时、损失工时、补助工时。
5、生产好的成品因本生产线作业不良而造成重工的,重工时所用到的工时将计算到生产该成品的实际投入总工时内进行计算生产效率,由生产该成品的线别承担工时。
6、计算损失工时和补助工时时由生产线填写<组装课损失/补助工时申请书>,按计算时注意事项的第1、2项规定进行计算与确认。
生产效率计算方法
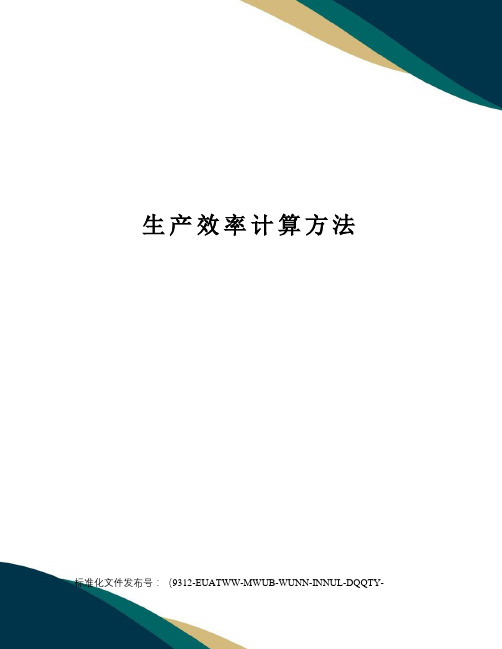
生产效率计算方法标准化文件发布号:(9312-EUATWW-MWUB-WUNN-INNUL-DQQTY-生产效率计算方法一、公式:生产效率=标准总工时÷实际总投入工时*100%标准总工时=标准工时*实际产出数实际总投入工时=总投入工时-损失工时-补助工时二、定义:生产效率:操作者按规定的作业方法工作时,他的能力或努力程度叫效率。
标准工时:根据PIE提供产能表所计算出来的工时。
总投入工时:是指当日考勤表上的总工时。
损失工时:因生产异常或其它原因使生产受影响的工时。
补助工时:每个订单在排拉时所需的工时。
三、计算时的注意事项1、损失工时的计算①生产过程中出现异常时影响生产效率时所损失的工时,由生产线申请,PIE确认。
②生产过程中因异常而停线所损失的工时,由生产线申请,PMC确认。
③其它原因所造成的生产过程中所损失的工时,由生产线申请,责任部门确认。
2、补助工时的计算①新订单生产成品,排线时补助1小时,由生产线申请,PMC确认。
②新订单生产半成品或包装排线时分别补助半小时,由生产线申请,PMC确认。
③同一订单非因本生产线原因而停线,然后又重新排线生产,按①②进行计算补助工时,由生产线申请,PMC确认。
3、生产效率按订单进行计算,也就是说每一个订单只计算一次生产效率;生产半成品时只需如实统计总投入工时、损失工时、补助工时。
4、生产线生产好半成品后将半成品转至其它生产线包装时,生产效率由生产半成品的生产线进行计算,负责包装的生产线提供包装时所用的总投入工时、损失工时、补助工时。
5、生产好的成品因本生产线作业不良而造成重工的,重工时所用到的工时将计算到生产该成品的实际投入总工时内进行计算生产效率,由生产该成品的线别承担工时。
6、计算损失工时和补助工时时由生产线填写<组装课损失/补助工时申请书>,按计算时注意事项的第1、2项规定进行计算与确认。
生产效率计算方法
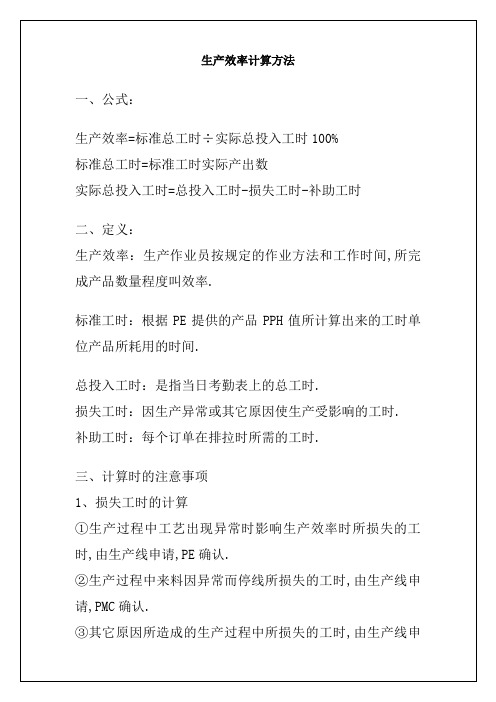
损失工时:因生产异常或其它原因使生产受影响的工时.
补助工时:每个订单在排拉时所需的工时.
三、计算时的注意事项
1、损失工时的计算
①生产过程中工艺出现异常时影响生产效率时所损失的工时,由生产线申请,PE确认.
②生产过程中来料因异常而停线所损失的工时,由生产线申请,PMC确认.
生产效率计算方法
一、公式:
生产效率=标准总工时÷实际总投入工投入工时-损失工时-补助工时
二、定义:
生产效率:生产作业员按规定的作业方法和工作时间,所完成产品数量程度叫效率.
标准工时:根据PE提供的产品PPH值所计算出来的工时单位产品所耗用的时间.
③其它原因所造成的生产过程中所损失的工时,由生产线申请,责任部门确认.
2、补助工时的计算
①新订单生产成品,排线时补助小时,由生产线申请,PMC确认.
②新订单生产半成品或包装排线时分别补助半小时,由生产线申请,PMC确认.
生产效率计算方法

生产效率计算方法一、公式:生产效率=标准总工时÷实际总投入工时某100%标准总工时=标准工时某实际产出数实际总投入工时=总投入工时-损失工时-补助工时二、定义:标准工时:根据PIE提供产能表所计算出来的工时。
总投入工时:是指当日考勤表上的总工时。
损失工时:因生产异常或其它原因使生产受影响的工时。
补助工时:每个订单在排拉时所需的工时。
三、计算时的注意事项1、损失工时的计算①生产过程中出现异常时影响生产效率时所损失的工时,由生产线申请,PIE确认。
②生产过程中因异常而停线所损失的工时,由生产线申请,PMC确认。
③其它原因所造成的生产过程中所损失的工时,由生产线申请,责任部门确认。
2、补助工时的计算①新订单生产成品,排线时补助1小时,由生产线申请,PMC确认。
②新订单生产半成品或包装排线时分别补助半小时,由生产线申请,PMC 确认。
③同一订单非因本生产线原因而停线,然后又重新排线生产,按①②进行计算补助工时,由生产线申请,PMC确认。
3、生产效率按订单进行计算,也就是说每一个订单只计算一次生产效率;生产半成品时只需如实统计总投入工时、损失工时、补助工时。
4、生产线生产好半成品后将半成品转至其它生产线包装时,生产效率由生产半成品的生产线进行计算,负责包装的生产线提供包装时所用的总投入工时、损失工时、补助工时。
5、生产好的成品因本生产线作业不良而造成重工的,重工时所用到的工时将计算到生产该成品的实际投入总工时内进行计算生产效率,由生产该成品的线别承担工时。
6、计算损失工时和补助工时时由生产线填写补助工时申请书,按计算时注意事项的第1、2项规定进行计算与确认。
如何计算标准工时和产能?
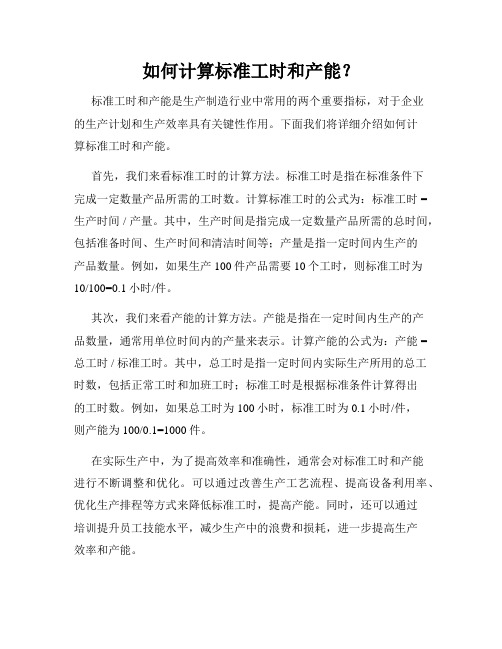
如何计算标准工时和产能?标准工时和产能是生产制造行业中常用的两个重要指标,对于企业的生产计划和生产效率具有关键性作用。
下面我们将详细介绍如何计算标准工时和产能。
首先,我们来看标准工时的计算方法。
标准工时是指在标准条件下完成一定数量产品所需的工时数。
计算标准工时的公式为:标准工时 = 生产时间 / 产量。
其中,生产时间是指完成一定数量产品所需的总时间,包括准备时间、生产时间和清洁时间等;产量是指一定时间内生产的产品数量。
例如,如果生产100件产品需要10个工时,则标准工时为10/100=0.1小时/件。
其次,我们来看产能的计算方法。
产能是指在一定时间内生产的产品数量,通常用单位时间内的产量来表示。
计算产能的公式为:产能 = 总工时 / 标准工时。
其中,总工时是指一定时间内实际生产所用的总工时数,包括正常工时和加班工时;标准工时是根据标准条件计算得出的工时数。
例如,如果总工时为100小时,标准工时为0.1小时/件,则产能为100/0.1=1000件。
在实际生产中,为了提高效率和准确性,通常会对标准工时和产能进行不断调整和优化。
可以通过改善生产工艺流程、提高设备利用率、优化生产排程等方式来降低标准工时,提高产能。
同时,还可以通过培训提升员工技能水平,减少生产中的浪费和损耗,进一步提高生产效率和产能。
总之,计算标准工时和产能是企业管理中至关重要的一环,它直接影响到生产效率和盈利能力。
只有通过科学合理地计算和分析标准工时和产能,企业才能更好地制定生产计划、合理安排生产资源,提高生产效率,降低成本,实现经济效益最大化。
希望以上内容对您有所帮助。
标准工时与效率分析
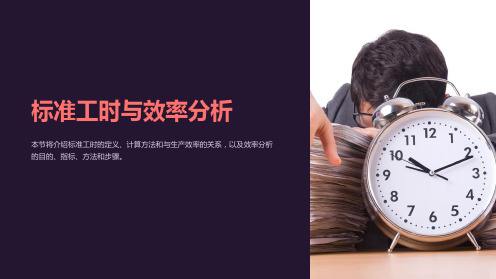
效率分析的指标
效率分析的常用指标包括生产效率、工作效率、能源利用效率、资源利用率 和资产利用率等,每个指标都能反映企业在不同方面的运营情况。
效率分析的方法和步骤
效率分析的常用方法包括比较法、趋势分析和标杆分析。效率分析的步骤包括数据收集、指标计算、问题识别、 改进措施制定和效果评估等。
标准工时与生产效率的关系
标准工时的合理设定和实施能够提高生产效率,降低成本,提升产品质量,并为企业的长期发展奠定基础。
标准工时对企业管理的意义
标准工时可以帮助企业管理团
效率分析的目的
效率分析的目的是评估生产过程中的资源利用和生产效率,发现并改进存在的问题,提高生产效率和企业竞争 力。
标准工时与效率分析
本节将介绍标准工时的定义、计算方法和与生产效率的关系,以及效率分析 的目的、指标、方法和步骤。
标准工时的定义
标准工时是一个基准,用于衡量完成特定任务所需的理论时间,它考虑到工人的技能水平、设备效率和工作条 件等因素。
标准工时的计算方法
标准工时的计算方法可以根据任务的性质和要求进行不同的选择,常见的方 法包括工作抽样法、时间测量和工序分析。
- 1、下载文档前请自行甄别文档内容的完整性,平台不提供额外的编辑、内容补充、找答案等附加服务。
- 2、"仅部分预览"的文档,不可在线预览部分如存在完整性等问题,可反馈申请退款(可完整预览的文档不适用该条件!)。
- 3、如文档侵犯您的权益,请联系客服反馈,我们会尽快为您处理(人工客服工作时间:9:00-18:30)。
标准工时与生产效率
1.1什么是标准工时?
在规定的作业条件下,用标准作业方法进行作业时所需要的时间:
(1)采用规定的方法和设备;
(2)在规定的作业条件下;
(3)完全具有某一工作所要求的特定熟练程度的作业者;
(4)在不受不利因素的影响下,以每天能够维持的完成工作的最佳节奏进行作业;
所谓特定熟练程度的作业者是指经过训练,肉体和精神上可以适应并能充分完成工作的作业员.
1.1.1需要防止的三种现象:
1.生产效率高达95%-100%,甚至超过100%;
2.设备稼动率超过80%,甚至超过90%;
3.大家都在将标准工时和效率指标当作笑谈.
标准不仅要考虑合理性,更要考虑它的导向性.
1.1.2标准工时的两个组成部分:
1.标准工时=正常时间+宽放时间
2.正常时间=平均时间x(1+评比系数)
3.宽放时间=私事宽放+疲劳宽放+程序宽放+
特别宽放+政策宽放
结构合理,系统才能科学;方法合理,管理才能科学!
1.1.3标准工时的结构图:
平均时间评比系数私事宽放疲勞宽放程序宽放特別宽放政策宽放
正常时间
标准时间
如果评比系数之和为负数,则正常时间小于平均时
间
1.1.4标准工时的计算公式:
标准工时=
【平均实操工时x(1+评比系数)】+(正常时间x宽放系数)
评比系数需要根据测量对象每次确认;
宽放系数在劳动条件和劳动环境不变的情况下只需确认一次.
评比系数:宽放系数是标准工时系统中最具专业物色的词汇.
1.1.5为什么要进行评比?
所谓评比:就是时间研究人员将所观测到的操作者的操作速度与自己所认为的理想速度(正常速度)作比较;
熟练系数:对作业者操作技能掌握即熟练程度方面进行评价;
努力系数:对作业者工作投入的程度进行评价;
工作环境系数:指因工作环境对作业者产生的影响;
一致性系数:指作业者在同种操作周期上时值的差异;
评比系数的四个关键要素(西屋评估法).
评估系数法(美国西屋电气公司首创)
1.1.6评比系数的运用案例
实测工时:10.5 10.0 9.5 9.8 11.0 11.5 9.0
熟练系数:超佳;A1 努力系数:可;E2
工作环境系数:欠佳;F 一致性系数:良;C
问答:根据实测工时和评比系数算出正常时间?
答案:正常时间=
【(11+9.8+9.5+10+10.5) ÷5】×【1+(0.15-0.08+0.07+0.01)】=11.68
1.1.7为什么要进行宽放?
1.人为宽放—人不是机器(私事宽放/疲劳宽放)
2.非人为宽放—生产需要准备(作业宽放/管理宽放)
3.工艺特点与计划周期需要调整—(特殊宽放)
同一劳动场所的同一工序其宽放系数是一致的,除非劳动条件发生变化,否则为
一个常数.
1.1.8宽放系数的含盖范围 工作环境和管理方法改善后,宽放系数需要重新评估.
1.1.9宽放系数的确认
1.私事(生理)宽放系数的确认;
2.疲劳宽放系数的确认;
3.程序(作业)宽放系数的确认;
4.管理宽放系数的确认;
5.特殊宽放系数的确认.
生产部门自我确认,IE 部门审核确认,上级主管核准确认,独立部门单独确认,独立产线单独确认,独立工站确认.
1.1.11建立标准工时系统的三个关键步骤
1.工序分解
工厂—部门—车间—产线—工序(设备)
2.区分影响工时的关键要素
工序(设备)—动作(行程)—动素(参数)
疲劳宽放:指作业员因作业造成的精神和肉体上的负荷导致的劳动技能減慢.
私事宽放指劳动以外的生理需要(喝水/入厕/擦汗)
作业宽放:指主要由于材料/事件/工具等相关的生产准备.
管理宽放:因管理制度,如班前会及交接班会/早操时间等.
特殊宽放:指因工艺特点或生产计划影响的长短而给予宽放.
宽放工时
3.制订现实有效的测算计划
1.1.12标准工时测算的三个关键安排
1.下个月要排产的产品优先测算(本月)
2.常做的产品紧随测算(下月)
3.剩下的产品最后测算(第三个月)
合理安排资源,缩短标准工时测试的周期.
1.1.13标准工时修订的五个时机
1.产品上线的第一个月
2.产品上线后第三个月(三个月之后)
3.产品上线后第九个月(半年之后)
4.产品上线后第二十一个月(一年之后)
5.设备/工艺/材料/治具发生变化时
标准工时不是随意乱改的,也不是固定不变的. 1.1.14标准工时审核发行的四个步骤
1.标准工时测试记录表(IE制作/班组长会签);
2.工序别标准工时总表(IE课长/制造课长会签);
3.产品别标准工时总表(工程经理/生产经理会签);
4.<<产品别标准工时总表>>经文控统一发行.
不要等到标准工时出现分歧时才来抱怨其它部门.标准只有被共同,才能被广泛的被使用.
1.2什么是生产效率?
1.2.1生产效率的计算公式:
生产效率=产出工时÷直接人员出勤工时
产出工时=产出数量×标准工时/每PCS
工作效率=产出工时÷(直接+间接)人员出勤工时
抓住投入与产出四个环节,统一分子分母的计量单位;
研究生产效率与工作效率的落差,找出改善的方向.
1.2.2生产效率的计算案例
某生产部门A款产品某日生产数量为1000PCS,该产品的标准工时为20分钟每个,直接作业人员50人,干部2名,物料员1名,当天上班10小时,请计算该日该款产品的生产效率?
生产效率=(1000×20) ÷50×10×60=66.67%
工作效率=(1000×20) ÷【(50+2+1) ×10×60】=62.89%
1.2.3生产线平衡改善的案例
平衡率=总标准工时÷排线人数×瓶颈工时
损失率=1-平衡率
每线每小时产能=3600÷瓶颈工时
每人每小时产能=3600÷瓶颈工时÷排线人数
1.2.4生产线人员需求的计算依据
计算条件:
1.产出工时=产出数量×标准工时/PCS
2.需求工时=产出工时÷生产效率
3.需求人数=需求工时÷(出货期限×工作时间)
4.出货期限:48小时之后(2天之后)
5.工作时间:10小时/每天
6.生产效率现状:60%
如何计算生产线需求人数是管理人员的基本功.
1.2.5生产线人员需求的计算案例
案例:
某生产部门A款产品计划生产数量为1000PCS,该产品的标准工时为20分钟每个,客户要求2天后交货,假设每天上班10小时,生产效率60%,该产品需要安排多少人员作业才能如期交货?
产出工时=? 产出工时=1000×20÷60=333.33H
需求工时=? 需求工时=333.33÷60%=555.55H
需求人数=? 需求人数=555.55÷(2×10)=27.83
(约等于28人)
1.3什么是设备稼动率?
1.3.1设备稼动率的计算公式
设备稼动率=时间稼动率×性能稼动率×一次良品率
时间稼动率=实际开机时间÷计划开机时间
性能稼动率=实际产量÷标准产量
一次良品率=实际良品数÷实际产量
计划开机时间一般设定为每天24小时
每小时标准产能=3600÷设备加工周期(秒)
1.3.2设备稼动率的计算案例
某大型设备计划开机时间24小时/每天,实际开机时间为21小时,设备加工周期为10秒,1模8穴,某日实际产量为60000个,其中不良品520个,试计算该设备在这一天的设备稼动率?
时间稼动率=21H÷24H=87.5%
标准产能=21×3600÷10×8=60480(PCS)
性能稼动率=60000÷60480=99.2%
一次良品率=(60000-520) ÷60000=99.1%
设备稼动率=87.5%×99.2%×99.1%=86.01%
1.3.3设备需求的计算依据
1.设备产出工时=产出数量×设备加工周期(时间/PCS)
2.需求工时=设备产出工时÷设备稼动率
3.需求设备=需求工时÷(出货期限×工作时间)
4.出货期限:24小时之后(1天之后)
5.工作时间:22小时/每天
6.设备稼动率现状:70%
1.3.4设备需求的计算案例
某生产部门A款产品计划生产数量为50000PCS,该设备的加工周期为10秒每个,客户要求1天后交货,假设设备每天开机22小时,设备稼动率70%,该产品要安排多少台设备作业才能如期交货?
产出工时=? 产出工时=50000×10÷3600=138.89H
需求工时=? 需求工时=138.89÷70%=198.4H
需求设备=? 需求设备=198.4÷(1×22)=9.01
(约等于10台) 1.3.5设备稼动率与生产效率的运用对比
有针对性的选择绩效指标,才能抓住改善的重点!。