H08焊条钢连铸坯质量的研究
日钢H08A焊条钢炼钢工艺实践
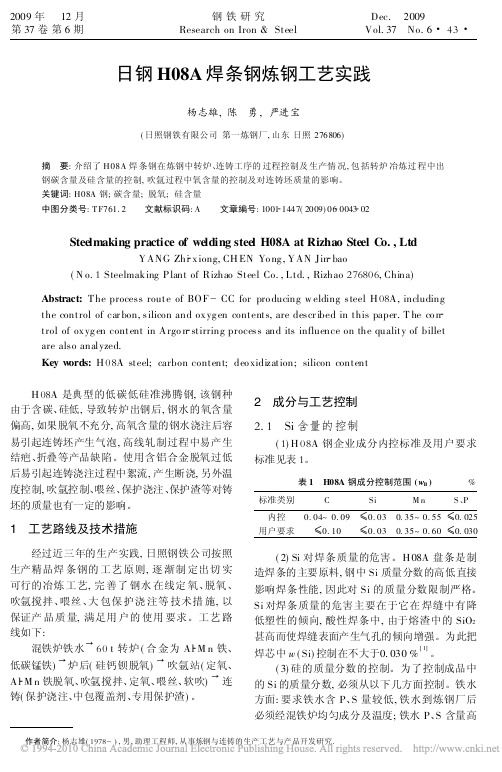
系统压力也不断波动, 供油管路无休止地振荡, 轧
机压下系统很难正常工作。应当指出, 伺服阀前
的蓄能器可以减少这种压力波动的幅值, 但不能
消除压力波动。并联运行的几台泵, 其相互影响
也不能忽略。
( 3) 如无节流阀或节流阀被堵塞, 则 PD = P,
当活塞调节右移时( QO 增大, P 增大) , Q T 压向泵
从表 2 看出, H 08A 中包钢水合理的氧含量 应控制 50 ∀ 10- 6 ~ 65 ∀ 10- 6 之间, 此时既能保证 铸坯质量, 又能保证正常生产, 连铸坯低倍样如图 2, 氧含量较高时, 易使连铸坯产生气泡, 连铸坯低 倍样如图 3。氧含量过低, 加入 Al Mn 铁量较多, 钢水中的 Al 含量较大, 在连铸浇注 过程中导致 中包水口絮流, 当钢水中氧含量达到要求后, 软吹
( 3) 硅的质量分数的控制。为了控制成品中 的 Si 的质量分数, 必须从以下几方面控制。铁水 方面: 要求铁水含 P、S 量较低, 铁水到炼钢厂后 必须经混铁炉均匀成分及温度; 铁水 P、S 含量高
作者简介: 杨志雄( 1978- ) , 男, 助理工程师, 从事炼钢与连铸的生产工艺与产品开发研究.
Abstract: T he process rout e of BOF - CC for pro ducing w elding steel H 08A, including t he cont rol of car bon, silicon and ox yg en cont ent s, are descr ibed in t his paper. T he co n t rol of ox yg en cont ent in Argo n st irring process and its influence on the qualit y of billet are also anal yzed. Key words: H 08A st eel; carbon cont ent; deo xidizat ion; silicon cont ent
影响焊条钢产品H08A质量的主要因素浅析

影响焊条钢产品H08A质量的主要因素浅析作者:陆阳赵越来源:《科学与财富》2017年第16期摘要:焊条(丝)钢是用于制造各种焊条焊芯的主要原材料,它广泛地应用于人民生产生活的各个方面。
宣钢二钢轧厂通过近十余年的生产实践,目前已经具备了批量生产优质焊条及焊丝钢的能力。
技术人员通过分析影响H08A产品质量的主要因素,总结提升产品质量的措施。
关键词:焊条钢、冶金、质量1前言焊接材料在我国经济建设中占据着重要的位置,在人民生产生活中发挥着不可或缺的作用。
在品种方面,焊接材料主要是焊条钢(H08A)与气保及埋弧焊丝。
焊接用钢线材消费的主要市场在天津、东北、江浙、保定及西南地区,需求量较大。
为应对角钢广阔市场和满足用户需求,宣钢二钢轧厂积极采取有效措施,改进焊条钢H08A产品质量。
2焊条钢概述焊接用钢包括焊接用碳素钢、焊接用合金钢和焊接用不锈钢等,其牌号表示方法是在各类焊接用钢牌号头部加符号“H”。
例如:“H08”、“H08Mn2Si”、“H1Cr18Ni9”。
高级优质焊接用钢,在牌号尾部加符号“A”。
例如:“H08A”、“08Mn2SiA”。
3影响焊条钢产品H08A质量的主要因素3.1化学成分研究表明,影响焊条钢产品质量的主要因素包括化学成分、线材表面质量与钢中非金属夹杂物、线材的显微组织和控冷与轧制工艺参数。
(1)化学成分一般说来,市场对H08A的要求,其化学成分的控制是关键,脱氧度、钢水浇注性和铸坯表面气孔的控制是核心。
目前国内市场要求H08A的碳含量0.05%-0.08%,硅含量0.01%-0.03%,硫、磷含量≤0.015%,铝含量≤0.01%。
氧(O):含氧量减少,氧化物夹杂的含量必然随之降低,能大大改善钢的冷拔性能及焊条的质量和性能,另外钢水在氧含量高时铸坯会产生皮下气泡等缺陷,严重影响轧制及钢丝的冷拔性能。
一般情况下,H08A冶炼钢水上连铸浇注的氧活度要求30-50ppm。
碳(C):碳是钢中的主要合金元素,当含碳量增加时,钢的强度、硬度明显提高,而塑性降低。
连铸圆坯质量控制

连铸圆坯质量控制连铸坯质量检验及控制一、连铸坯的内部结构(凝固组织)的一般特征及检验。
连铸坯的检验方法连铸坯的内部结构:经过酸浸(酸洗)或硫印的方法在连铸坯横断面或纵断面上用肉眼或低倍放大镜看到内部组织结果。
硫印硫印是用感光相纸显示试样上硫偏析(合金中各组成元素在结晶时分布不均匀的现象称为偏析)的方法,主要用于钢铁行业铸坯质量的检验。
从铸坯上取纵向或横向试样,试验面加工的光洁度不应低于6。
使用反差大的溴化银表面相纸,把与试样大小相同的相纸放入稀硫酸中浸泡1-2分钟后取出,将相纸对准检查面轻轻覆盖好,将试样与相纸间气泡赶净,待接触2-5分钟后取下,将相纸在流水中冲洗,然后定影烘干,即完成一张硫印。
印基本原理:硫酸与试样上的硫化物(FeS、MnS)发生反应,生成硫化氢气体,硫化氢气体再与感光相纸上的溴化银作用,生成硫化银沉淀在相纸相应的位置上,形成黑色或褐色斑点。
用硫印试验,可显示钢锭、连铸坯中心裂纹、偏析线、低倍结构和夹杂分布等。
酸洗用酸液洗去基体表面锈蚀物和轧皮的过程。
用酸浸或硫印法所显示的组织结构属于宏观结构,是连铸坯和金属材料检验中最为常见的检验技术。
连铸坯的内部结构连铸坯自表面至中心都是由边缘等轴晶区(激冷区)、柱状晶区和中心等轴晶,区三部分组成。
温度梯度较大时,固液两相区(图1)小,有利于柱状晶的生长,而凝固速度较快,则易于生成枝晶间距小的铸造组织,所以连铸坯具有较发达的柱状晶组织,并具有较小的枝晶间距。
(图1)枝晶间距是指相邻同次枝晶间的垂直距离,它是树枝晶组织细化程度的表征。
枝晶间距越小,组织就越细密,分布于其间的元素偏析范围也就越小,故越容易通过热处理而均匀化。
通常采用的有一次枝晶(柱状晶主干)间距d1,和二次分枝间距d2两种。
连铸坯宏观组织的好坏可以用等轴晶所占的比例多少来衡量,轴晶结构致密,加工性能能好。
柱状晶具有明显的方向性,加工性能差,容易导致中心偏析,中心疏松和中心裂纹等缺陷。
连铸板坯质量

连铸板坯质量概述纵裂纹时发生在板坯宽面与浇注方向平行的表面裂纹。
该类缺陷造成板坯表面清理量增大,收得率低,严重时大量报废,甚至漏钢,给生产带来不稳定因素,影响铸机生产和铸坯质量。
铸坯纵裂纹影响因素✧钢水过热度与拉速过热度高,拉速波动大,对板坯表面质量有显著影响。
过热度和拉速决定结晶器内坯壳的厚度。
在结晶器水量设定不变,二冷水自动控制的条件下,拉速与过热度的匹配,对纵裂纹的发生率有着重要影响。
过热度过高时,拉速降低,虽然能在结晶器上部形成一定厚度的坯壳,但在结晶器中下部过早形成气隙,使传热不均匀,坯壳不能均匀生长,造成热应力,摩擦力加大,极易导致纵裂纹,另外,钢水过热度高,导致钢水凝固推迟,坯壳厚度薄且平均温度高,坯壳温度向钢的第Ⅰ脆性区移动,使纵裂倾向加重。
✧钢种成份1、碳的影响C在0.10%—0.16%范围内的碳钢凝固过程会发生包晶反应,在凝固点附近体积收缩率增大,属于裂纹敏感区,极易因收缩不均匀产生纵裂。
而又因Mn等合金的加入,碳的范围还要向下移,宝钢生产的中碳钢相当一部分在这个范围内。
例如,表3-1中Ⅳ钢,其碳含量在0.08%—0.11%之间,属亚包晶钢,占每个月纵裂报废的大头。
2、钢种各元素对纵裂纹的影响程度用纵裂纹敏感因子表示如下:CSF=36%C+12%Mn+8%Si+540%S+812%P+5%Ni+3.5%Co-20%V从上式中可以看到,P和S对纵裂的影响极大,主要是因为P、S在δ-Fe中的溶解度和扩散系数要比在γ-Fe中大得多,在相变时有可能产生晶界富集,导致裂纹的发生。
因此降低钢中P、S含量,对提高坯壳的强度,减少裂纹的初生与扩展都是有益的,有经验表明提高Mn/S可以有效降低S对裂纹的影响,减少纵裂的发生,当Mn/S<40时,会发生严重的晶界脆化现象,Mn/S>100时,使FeS充分转化为MnS,减少了低熔点硫化物的析出,可使裂纹发生率降低。
3、另外Cu、Sn等元素在钢种能显著降低钢的热塑性,在晶界富集降低晶界表面能,增大晶界处孔洞形核与长大速度,增加裂纹的敏感度。
连铸坯产生质量问题的原因
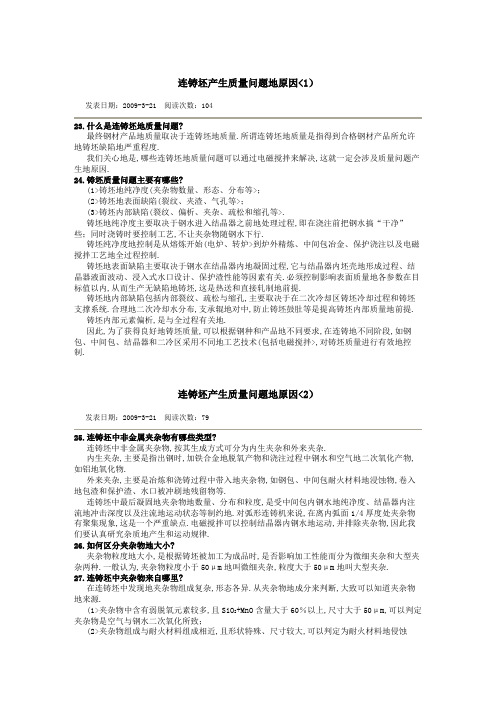
连铸坯产生质量问题地原因<1)发表日期:2009-3-21 阅读次数:10423.什么是连铸坯地质量问题?最终钢材产品地质量取决于连铸坯地质量.所谓连铸坯地质量是指得到合格钢材产品所允许地铸坯缺陷地严重程度.我们关心地是,哪些连铸坯地质量问题可以通过电磁搅拌来解决,这就一定会涉及质量问题产生地原因.24.铸坯质量问题主要有哪些?(1>铸坯地纯净度(夹杂物数量、形态、分布等>;(2>铸坯地表面缺陷(裂纹、夹渣、气孔等>;(3>铸坯内部缺陷(裂纹、偏析、夹杂、疏松和缩孔等>.铸坯地纯净度主要取决于钢水进入结晶器之前地处理过程,即在浇注前把钢水搞“干净”些;同时浇铸时要控制工艺,不让夹杂物随钢水下行.铸坯纯净度地控制是从熔炼开始(电炉、转炉>到炉外精炼、中间包冶金、保护浇注以及电磁搅拌工艺地全过程控制.铸坯地表面缺陷主要取决于钢水在结晶器内地凝固过程,它与结晶器内坯壳地形成过程、结晶器液面波动、浸入式水口设计、保护渣性能等因素有关.必须控制影响表面质量地各参数在目标值以内,从而生产无缺陷地铸坯,这是热送和直接轧制地前提.铸坯地内部缺陷包括内部裂纹、疏松与缩孔,主要取决于在二次冷却区铸坯冷却过程和铸坯支撑系统.合理地二次冷却水分布,支承辊地对中,防止铸坯鼓肚等是提高铸坯内部质量地前提.铸坯内部元素偏析,是与全过程有关地.因此,为了获得良好地铸坯质量,可以根据钢种和产品地不同要求,在连铸地不同阶段,如钢包、中间包、结晶器和二冷区采用不同地工艺技术(包括电磁搅拌>,对铸坯质量进行有效地控制.连铸坯产生质量问题地原因<2)发表日期:2009-3-21 阅读次数:7925.连铸坯中非金属夹杂物有哪些类型?连铸坯中非金属夹杂物,按其生成方式可分为内生夹杂和外来夹杂.内生夹杂,主要是指出钢时,加铁合金地脱氧产物和浇注过程中钢水和空气地二次氧化产物,如铝地氧化物.外来夹杂,主要是冶炼和浇铸过程中带入地夹杂物,如钢包、中间包耐火材料地浸蚀物,卷入地包渣和保护渣、水口被冲刷地残留物等.连铸坯中最后凝固地夹杂物地数量、分布和粒度,是受中间包内钢水地纯净度、结晶器内注流地冲击深度以及注流地运动状态等制约地.对弧形连铸机来说,在离内弧面1/4厚度处夹杂物有聚集现象,这是一个严重缺点.电磁搅拌可以控制结晶器内钢水地运动,并排除夹杂物,因此我们要认真研究杂质地产生和运动规律.26.如何区分夹杂物地大小?夹杂物粒度地大小,是根据铸坯被加工为成品时,是否影响加工性能而分为微细夹杂和大型夹杂两种.一般认为,夹杂物粒度小于50μm地叫微细夹杂,粒度大于50μm地叫大型夹杂.27.连铸坯中夹杂物来自哪里?在连铸坯中发现地夹杂物组成复杂,形态各异.从夹杂物地成分来判断,大致可以知道夹杂物地来源.(1>夹杂物中含有弱脱氧元素较多,且SiO2+MnO含量大于60%以上,尺寸大于50μm,可以判定夹杂物是空气与钢水二次氧化所致;(2>夹杂物组成与耐火材料组成相近,且形状特殊、尺寸较大,可以判定为耐火材料地侵蚀物;(3>夹杂物中含有钾、钠等元素,说明是由于结晶器保护渣卷入钢水中所致.28.弧形连铸机铸坯内夹杂物聚集有何特点?截至2000年,我国已建成大小方坯弧形铸机1039流,圆坯专用弧形铸机23流,总计1062流,其中不少方坯铸机可同时兼拉圆坯.夹杂物在内弧聚集对圆坯穿管极为有害.弧形铸机由于结构上地原因,铸坯中大颗粒夹杂物是比较严重地,而且聚集在内弧面1/4处,其成因如图2—1所示.夹杂物随钢流冲向结晶器下部,拉速越快,冲击越深.由于比重地原因,夹杂物有一个上浮地趋势.钢流运动是一个圆弧轨迹,与上浮力(垂直方向>合成,杂质便向铸坯内弧侧运动,至凝固前沿,被黏稠区所俘获.这种质量问题,无论是方坯、圆坯、板坯地弧形铸机,都是存在地,不得不采取多种方法,如在弧形机上加电磁搅拌,在板坯机上加电磁制动来解决.日本川崎水岛钢厂和日本钢管福山厂甚至将弧形板坯铸机改为立弯式铸机,使上段有3m以上地垂直段,以利于夹杂物上浮,对于大多数弧型圆坯铸机来说,一个性能良好地结晶器电磁搅拌是必须地.电磁搅拌所产生地旋转力,使钢液在下行过程中,作强烈地圆周运动,这种运动会使钢液(比重大>产生离心力,向坯壳压缩,而夹杂(比重轻>则向心运动,聚集起来,高温地夹杂集合会使颗粒增大而更趋于上浮,避免了向内弧移动.而电磁旋转力地作用,减轻了钢液注流冲击深度,也有利于夹杂物上浮.29.按影响成品加工性能分,夹杂物有哪些类型?按夹杂物变形能力可分为脆性夹杂、塑性夹杂和半塑性夹杂.脆性夹杂物一般指那些不具备塑性变形能力地简单氧化物、复杂和复合氧化物,氮化物和不变形地球状、点状夹杂物.由于钢丝是经钢坯热轧成盘条后再经拉拔而形成地,要求变形量很大,所以A1203、尖晶石等不变形脆性夹杂对线材地危害是很大地.塑性夹杂物在钢经受加工变形时具有良好地塑性,沿着钢地流变方向延伸成长条状,属于这类地有SiO2含量较低地铁硅酸盐、硫化铁、锰(Fe、Mn>S等.半塑性地夹杂物一般指各种复合地铝硅酸盐类夹杂物.钢中非金属夹杂物地变形行为比较复杂,不仅取决于夹杂物地类型,而且与夹杂物地成分及变形温度密切相关.连铸坯产生质量问题地原因<3)发表日期:2009-3-21 阅读次数:7230.裂纹地种类有哪些?连铸坯表面缺陷是影响连铸机产量和质量地重要缺陷.据统计,各类缺陷中裂纹占50%.铸坯出现裂纹,重者会导致拉漏或形成废品,轻者要进行精整,这样既影响连铸机生产率,又影响产品质量,增加了成本.连铸坯裂纹地种类见表2—1.对各种裂纹产生地原因进行分析,目地是研究电磁搅拌工艺对裂纹地影响.虽然到目前为止,学术界尚未认可电磁搅拌器对裂纹肯定有什么影响,但是,一些连铸专家曾认为,结晶器搅拌器对铸坯角部裂纹有抑制作用,而我们通过F—EMS地研究,发现搅拌器对铸坯局部裂纹有明显地控制作用.31.表面纵裂纹有什么危害?连铸坯表面纵裂纹会影响轧制产品质量.如长300mm、深2.5mm地纵裂纹在轧制板材上会留下1125mm分层缺陷.研究表明,纵裂纹发源于结晶器弯月面初生坯壳地不均匀性,作用于坯壳地热应力超过钢地允许强度,在坯壳薄弱处产生应力集中导致断裂,出结晶器后在二次冷却区扩展.32.表面纵裂纹产生地原因有哪些?水口与结晶器不对中、保护渣溶化性能不良、液渣层过厚或过薄导致渣膜不均等、结晶器液面波动、钢中S+P含量超过允许值等.以上原因会造成凝壳厚薄不匀或使局部凝固壳过薄容易发生裂纹;液渣层过薄、液面波动过大,纵裂纹明显增加;S+P含量超标,钢地高温性能和塑性明显降低,易发生纵向裂纹.33.电磁搅拌对表面纵裂纹有什么影响?连铸工艺上防止纵裂纹地措施有:水口和结晶器对中;结晶器液面波动稳定在±10mm;合适地浸入式水口插入深度;合适地结晶器锥度;结晶器与二冷区上部对弧要准;合适地保护渣性能等.M—EMS产生地旋转磁场,使钢液沿凝固前沿不停地冲刷,因而有理由认为,它能使初生坯壳均匀化,从而减轻纵裂.在使用结晶器电磁搅拌时要注意强度,过强地搅拌,会使液面波动过大,反而引发裂纹.34.表面横裂纹产生地原因及防止方法有哪些?横裂纹位于铸坯内弧表面振痕地波谷处,通常是隐藏不见地,裂纹深度可达7mm,宽度0.2mm.裂纹位于铁索体网状区.产生地原因一般是连铸工艺控制失常所引起.比如:振痕太深、钢中Al、N含量增加,促使质点(A1N>在晶界沉淀,诱发横裂纹;钢坯在脆性温度700~900℃区间矫直;二冷太强等.连铸工艺方面防止横裂地措施一般有:结晶器采用高频小振幅;二次冷却采用平稳地弱冷却,并使矫正时铸坯表面温度大于900℃;结晶器液面稳定,并采用有良好润滑性能、黏度较低地保护渣.一般来说,M—EMS对横裂影响甚微,但末端电磁搅拌(F—EMS>可以使铸坯表面温度回升,可使因振痕引起地横裂(细小>在下行时,特别是空冷区内,不致受力而继续扩大,特别是对矫直温度可能低于900℃地铸机工艺来说,更有降级地效果.35.表面网状裂纹和铸坯角部裂纹产生地原因有哪些?表面网状裂纹:高温铸坯表面吸收了结晶器地铜,以及表面铁地选择性氧化.解决地办法是结晶器铜板加镀层.电磁搅拌不能改善网状裂纹.连铸坯角部裂纹:角部纵向或横向裂纹主要原因是结晶器结构和安装不对称所造成.经验证明,过强地M—EMS搅拌,会使角部裂纹加重.36.连铸坯地内部裂纹有哪些?根据《连续铸钢500问》地定义,内部裂纹是从结晶器拉出来地带液芯地铸坯,在弯曲、矫直或辊子压力地作用下,在正在凝固地、非常脆弱地固液交界面产生地裂纹,叫内部裂纹,它地种类大致分为8种:(1>矫直裂纹:是带液芯地铸坯在进行矫正时受到超过允许地变形率造成地.(2>压下裂纹:由于拉辊压力太大,于正在凝固地铸坯固液两相区中产生地.(3>中间裂纹:主要是由于铸坯通过二次冷却区时冷却不均匀,温度回升大而产生地热应力造成地.另外铸坯鼓肚或不对中造成外力,也可产生这种裂纹.(4>角部裂纹:由于结晶器冷却不均所造成地.(5>皮下裂纹:离表面3~10㎜范围内,细小裂纹地产生主要是铸坯表层温度反复多次变化而发生相变,裂纹沿两种组织交界面扩展而形成.因为3~10mm纯粹是在结晶器内生成,因此M—EMS 可以有效地控制其生成.(6>中心线裂纹:在板坯横断面中心可见地裂隙,并伴随有S、P地正偏析,它是凝固末期铸坯鼓肚造成地.(7>星状裂纹:方坯横断面中心裂纹呈放射状.二冷区冷却太强,随后温度回升而引起凝固层鼓肚,使铸坯中心黏稠区受到拉应力破坏所致.(8>对角形裂纹:二次冷却不均,使铸坯产生菱形变形所致.裂纹发生地力学原理是,凝固界面地晶体强度非常小(仅1—3N/mm2>、由变形到断裂地应变为0.2%~0.4%.因此铸坯受到外力(如鼓肚力、矫直力、热应力等>超过上述临界值,就在固液界面产生裂纹,并沿柱状晶扩展,直到凝固壳能抵抗外力为止.从上述各处裂纹来看,多数在结晶器内发生地表面裂纹、气泡、针孔等,可以通过M—EMS来抑制.中间裂纹也可以通过电磁感应地办法来控制,只是目前尚未为此而专门设置这种装置.至少,在板坯地四角因冷却过速,在矫直时会发生裂纹,因而已有专门地电磁感应加热装置使其均温而改善裂纹地例子.事实上,电磁感应加热与电磁搅拌器是同一种结构,只不过一种是利用电磁推力,而另一种是利用电磁感应涡流发热和磁滞发热而已.电磁感应能改善铸坯局部裂纹,已经有了一定数量地实验数据,至于工业推广,还需要机会.连铸坯产生质量问题地原因<4)发表日期:2009-3-21 阅读次数:5337.连铸坯皮下气泡是如何产生和受控地?在位于铸坯表皮以下,有直径和长度各在1mm和10mm以上地向柱状晶方向生长地大气泡,这些气泡如裸露在外地叫表面气泡,没有裸露地叫皮下气泡,比气泡小地呈密集状地小孔叫针孔.电磁搅拌可以冲刷初生壳凝固前沿,旋转地钢液有强地离心力,压迫坯壳,使气泡分离上浮.因此是一种有效地工艺手段.38.连铸坯地内部质量主要指哪些?连铸坯地内部质量主要指中心元素偏析、中心疏松和缩孔.连铸坯地中间裂纹、中心裂纹也应当是考察质量内容之列;与影响内部质量相关联地指标还有等轴晶率、V状偏析等.39.影响连铸坯内部质量地主要原因有哪些?影响连铸坯内部质量地主要原因是钢液冷却、铸坯凝固过程.研究电磁搅拌技术,目地是为控制连铸坯地凝固过程,因而,我们首先要关注铸坯地凝固过程.40.钢液冷却过程释放地热量包括哪些?钢水凝固过程中释放地热量包括:(1>钢水过热.由浇注温度T C来决定:T1=T C一T L(2>凝固潜热.不同地钢种凝固潜热是不同地:T2=T L一T S低碳钢地潜热为310KJ/kg,潜热放出地速率,直接关系到连铸生产率;(3>物理显热.钢从固相线温度冷却到室温所放出地热量.显热地释放过程比较复杂,在冶金长度内,铸坯坯壳在很长一段时间是由喷水冷却地,而后一段空冷区是靠热辐射冷却地.外壳边冷却边接受坯芯传出地热量.铸坯完全凝固后,铸坯继续向空气中辐射热量,使铸坯表面温度上升并且均匀化.41.钢液冷却地动力是什么?首先,钢液在结晶器内通过传热消除过热,紧贴结晶器壁地那部分钢液由液相转变到固相,发生相变结晶,形成初生坯壳.铸坯凝固过程地冷却动力就是温度梯度.液芯温度为T C,凝固前沿为T L,初生壳为T S,结晶器铜板外壳是冷却水温,外壳表面水温在沸点以下,因此绝不会接近或超过100℃,即在核态沸腾区以下.在很短地距离内,温度差值约1400℃,温度梯度很大.巨大地温度梯度,产生强烈地对流和传导.连铸坯产生质量问题地原因<5)发表日期:2009-3-21 阅读次数:6042.在结晶器区段内,传热有几个渠道?(1>浇铸和搅拌会引起钢液地运动,因而引起热地对流;(2>钢液与结晶器壁接触受冷凝固,形成初生坯壳;(3>弯月面以下坯壳与器壁之间有传导传热;(4>坯壳内部因温度梯度而从内向外地热传导;(5>钢液与凝固壳在两相区地传热;(6>冷却水与结晶器外壁之间地传导和结晶器铜板很短距离内地强烈地传热.43.结晶器壁传热过程是怎样地?(1>在结晶器口下100~140mm处,称为弯月面,钢液与结晶器铜板有压力接触.此处是靠结晶器壁传热地,此处传热效率最高.不过在钢水和器壁之间,还有很薄地一层熔渣和润滑剂,对传热有些影响,初生坯壳就从弯月面开始生长.结晶器壁具有良好地导热性,只需要结晶器壁很薄,热阻很小,相当于传热系数为2W/cm2·℃,这是一种传导传热.(2>凝固壳与结晶器壁之间地传热,钢水在弯月面处冷却速度高达100℃/s,据测定钢液弯月面处地结晶器热流密度高达1.5~2.0MW/m2·℃.(3>冷却水与结晶器壁地对流传热.冷却水通过强制对流,把结晶器壁地热量迅速带走,当水流达到6m/s时,传热系数Hw=4W/cm2·℃,结晶器内冷却水不会产生沸腾现象.44.凝固壳地传导传热是怎样进行地?凝固壳地传导传热是在坯壳内进行地,是单方向地,坯壳内温度梯度可达550℃/m.45.钢液与铸坯凝固壳界面地对流传热是怎样进行地?钢液与铸坯凝固壳界面地对流传热.钢液由中间包水口向结晶器内不断注入,引起结晶器内钢液地对流运输,对流会把钢液地过热传给凝固地坯壳,对已凝固地坯壳产生冲刷作用,使其减薄,达到热交换行为.实践表明,当钢水过热度每增高10℃,凝壳就减薄2mm,可见过热度高地钢水既影响铸坯质量(中心偏析等>,又影响铸机效率(控制拉速,以防拉漏>.46.二冷区传热有什么特点?铸坯在二冷区有约60%地热量放出,二冷区铸坯表面热量传递方式有:(1>冷却水地蒸发和冷却水加热带走热量占58%;(2>铸坯表面辐射占25%,辊子与铸机地接触传热占17%.可用对流传热方程来描述这一过程:φ=h(T S—T W>式中φ——热流,W/cm2;h——二冷区综合传热系数,W/cm2·℃;T S——铸坯表面温度,℃;T W——冷却水温度,℃.47.什么是二冷区传热效率?二冷区喷水冷却是一个复杂地传热过程,一般采用铸坯表面与冷却水之间地传热系数h来表示二冷区冷却能力,h大则传热效率高.传热系数与单位时间、单位面积地冷却水量W(水流密度>地关系,以经验公式表示:h=AW n式中A、n——常数,n=0.5~0.7;W一水流密度,t/(m2·min>.48.空冷区传热如何计算?铸坯在空冷区传热主要是向空中辐射传热.故空冷区导出地热流由下式计算:φ=δ·ε·[(T S+273>4一(T0+273>4]式中φ——空冷区平均热流,W/m2;T S——铸坯表面温度,℃;T0——空气地温度,℃;δ——表面辐射系数;ε——斯蒂芬-波耳兹曼常数,5.76×10-8,W/m2·K4.连铸坯产生质量问题地原因<6)发表日期:2009-3-21 阅读次数:5749.连铸二次冷却工艺控制与电磁搅拌有什么关系?二冷区电磁搅拌和末端电磁搅拌效果与铸坯液芯直径有很大关系,而在线测量液芯直径是很困难地,一般通过了解二冷制度,并通过数学模型计算液芯,然后通过实验来检验.一方面,搅拌器安装位置要与冷却相匹配;另一方面,搅拌器安装以后,可以适当调节二冷水量,来与搅拌器匹配,以求得最好地搅拌效果.50.铸坯初生结晶形成有什么特性?一般认为,钢液温度降低到1535℃时就有晶体析出.在冷却铜管,这种晶体会落脚于不平地管壁表面,形成基底;还有一部分自由悬浮,因重力作用下落或被钢液地流场卷起.铜管受到冷却水地强烈冲刷,形成很大地温度梯度场,即产生冷却动力,结晶核心具有冷却优势,于是以晶核为基底就产生初生坯壳.由于冷却地不均匀性,坯壳中地一部分柱状晶得到快速发展,并生成侧晶、一次侧晶、二次侧晶等,我们叫树枝状晶.而越是发达地柱状晶,越是具有冷却优势,生长会更快.而自由晶地一部分可能被凝固前沿粥状区所俘获,另一部分自由悬浮或下落到熔池底部.坯壳在出结晶器口后,被二冷区喷淋水直接冷却,柱状晶地发展,可能会产生“搭桥”效果,形成所谓穿晶结构,这种现象对连铸坯是十分有害地.它地存在,会使铸坯产生一种“小钢锭”结构,会加重中心偏析和缩孔,见图2—2、图2—3.51.结晶还可能出现哪些缺陷?(1>结晶器不同位置在正常凝固时,首先会在弯月面处形成初生壳,壳体紧贴结晶器铜管地四壁(图2—4a>,到结晶器中部时,因凝固壳收缩,坯壳与铜板平面之间会形成一个很小地空隙(图2—4b>.空隙地产生,会大大降低传热效果,缝隙可能会被熔融地保护渣或润滑剂所填充,以改善传热.在结晶器出口处,因凝固收缩空隙应当增大(图2—4c>,但由于结晶器地倒锥角关系,坯壳与铜板不能完全脱离.在结晶器地中部,坯壳一方面受收缩力地作用,离开铜板;另一方面受到钢水静压力而向外扩张(靠近铜管壁>,这个过程是一种不稳定过程.如果有电磁搅拌力让钢水旋转起来,则离心力会给铸坯初生壳更大压力,使其紧贴铜管管壁.电磁旋转力会使液芯内部过热钢水作强烈地热对流运动,会使初生壳重熔,一方面影响了坯壳地成长,这对柱晶生长是不利地;另一方面却使弯月面附近热传递加快4~6倍,因而最终会改善凝固结构.(2>实际上没有电磁搅拌时,结晶器内初生壳生成是不理想地,一方面冷却存在不均匀问题;另一方面,注流从水口进入结晶器在结晶器这个方柱体内(等似>是不均匀地,即流场不对称,紊流地冲刷,使得坯壳生长不均匀,会出现如图2—5地情况,产生如下后果.①初生壳不均匀,是表面和次表面裂纹地根源;②初生壳不均匀,有拉漏地危险;③冷却不均匀,使某些部位柱状晶得以快速发展,以致在二冷区“搭桥”.为改善注流钢水地不良影响,要妥善地使用M—EMS,使旋转钢流成为主流场,控制由于注流紊流形成地冲刷.结晶器段M—EMS地作用是:加快热交换,抑制初生柱状晶,增加等轴晶面积.可以改善铸坯中心地质量,也为F—EMS功能地发挥提供了很好地条件.综上所述,铸坯表面质量和次表面质量取决于结晶器内凝固地环境和条件.一般从弯月面开始形成初生壳,到出结晶器口,铸坯厚度为:小方坯h=8~12mm,板坯h=12~15mm.表面地机械损伤(振痕>、气泡、夹杂、皮下夹杂,裂纹等都与结晶器地条件有关.振痕是由机械来调整地,而夹渣与中间包衬、水口材料、保护渣有关;夹渣地严重程度,与水口浸入深度和液面稳定性有很大关系,如钢种对铸坯要求高,则必须加液面控制和恒拉速控制系统.为了减轻夹杂并改善裂纹,控制铸坯表面质量,应当使用电磁搅拌器.连铸坯产生质量问题地原因<7)发表日期:2009-3-21 阅读次数:6352.什么是连铸坯中心偏析?连铸坯和模铸坯地区别就在于钢坯是直接轧制成材而不经开坯工序,因而产生了中心偏析,这在成品加工中是无法消除和补救地.在某种连铸条件下,不同钢种出现客观偏析是由于溶质元素被连续地挤入液体内而导致连铸坯中心地凝固组织出现正偏析,这种中心线偏析或称轴向偏析,主要是在拉速高和中间罐内钢液过热度高且浇注高碳钢小方坯时比较严重.它地产生不难理解,溶质元素凝固温度低,因此它总是被先冷凝地坯壳往中心挤,以致富集起来.溶质元素特别是碳,沿铸坯中心线地宏观偏析,在热加工或热处理后保留下来,并导致钢材最终产品机械性能不均匀.53.如何分析偏析?偏析地程度通常是在要求地区域内钻样分析后确定.取样方法有纵剖面中心取样和横剖面中心取样.钻头直径和钻孔深度对分析数据有重要影响,横剖面中心点偏析数据会偏大.中心点是指几何对角线地中心点,有时取样在这点会碰到缩孔,而不得不偏移,这也对取样数据有影响.计算偏析率C/C0时,C0可以是断面对角线或十字线上平均距离取点测试值相加地平均值,例如每条直线等距取10~14个点,也可以是中间包钢水中元素成分值.用中间包取样,整个分析数据会减少工作量.不同地取值方法会得出不同地结果.20世纪80年代,Moil等人就做过分析,钻头为Φ3、孔深3mm、拉速1.5m/min、过热度为50℃、含碳量0.85%、断面为160mm×160mm方坯.分析结果是在纵向最大碳偏析率为1.8.而Haminton和Moore对含碳0.79%、过热度为63℃、拉速为2.9m/min地90mm×90mm方坯用直径(Φ8mm钻头,取样深度4mm,得到最大偏析率为1.2,这种较低地数值,无疑是由于钻头直径较大取样而引起地平均效果.前面提到过地一个重要问题是,中心线偏析值在轴线上是不连续地,因此横断面上中心点取样可能离散值很大,结果令人迷惑不解.具体地取样分析方法将在以后有关章节中介绍.54.为什么偏析与连铸坯组织特点有关?一般认为,合金元素地偏析是由于溶质元素在凝固前沿析出,并由随后地物质流动和扩散引起地再分配而生成.宏观偏析是由溶质富集地钢液离开凝固前沿地物质运动所产生.这种运动地引起是由于:(1>液体内部地温度差和浓度差而引起地对流运动;(2>钢液注入结晶器产生地运动;(3>重力对液体中生长晶体地作用.一个基本地现象是:在有利于柱晶成长和被溶质元素富集地液体流动地条件下,连铸坯地轴向偏析将加剧.在有利于形成大面积等轴晶,而且微观偏析分布均匀地条件下,则可以看到轴向偏析减轻.。
连铸坯质量解析(共20张PPT)
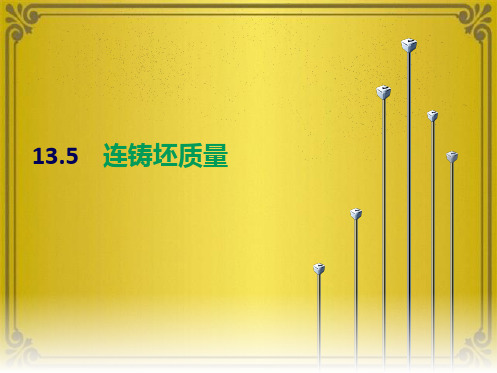
(2)二,冷区如采果用平夹稳杂的热物冷细却,小矫,直呈时铸球坯形的表,面弥温度散要分高于布质,点沉对淀钢温度质或量高的于γ影--α。响比集中存在要小些;当夹杂物大,
Your company slogan
13.5.2 连铸坯表面质量
13.5.2.1 表面裂纹
表面裂纹就其出现的方向和部位,可以分为面部纵裂纹.角部纵裂纹与横裂纹,星状 裂纹等。
纵向裂纹在板坯多出现宽面的中间部位.方坯多出现在棱角处。表面纵裂纹直接影响钢材质量。
若铸坯表面存在深度为,长度为300mm的裂纹,轧成板材后就会形成1125mm的分 层缺陷。严重的裂纹深度达10mm以上,将造成漏钢事故或废品。
(从4)表选1。用3—性大5能所于良列好5数的0据保μ可m 护以渣看的;出大,富型集夹溶杂质元物素往的母往液伴流动有是裂加剧纹中出心偏现析.的造重要成原连因。铸坯低倍结构不合格,板材分层,并
2 连铸坯表面质量 (4)选用性能良好的保护渣;
中2 间连包损铸使坏坯用表冷双面层轧质渣量钢覆盖板剂的,隔表绝面空气等,,避免对钢钢液的危二害次很氧化大。。夹杂物的大小形态和分布对钢质量的影响也不同
来看,锰-硅盐系夹杂物的外观颗粒大而浅,Al2O3系夹杂物细小而深。若不清除,会造成成品表面缺陷
,增加制品的废品率。夹渣的导热性低于钢,致使夹渣处坯壳生长缓慢,凝固壳薄弱,往往是拉漏的起因, 一般渣子的熔点高易形成表面夹渣。
敞开浇铸时,由于二次氧化.结晶器表面有浮渣。浮渣的熔点和流动性以及钢液的浸润性均与浮渣的组成
首钢第二炼钢厂连铸H08A的研制与开发
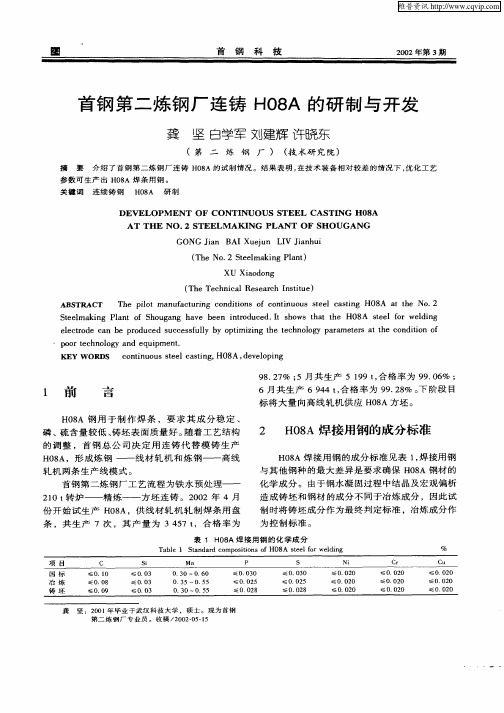
G NG Ja B IX eu L V Ja h i O in A u jn I in u
( h . tem kn ln ) T eNo 2Sel a igPa t
X U a d ng Xi o o
( h e h ia R sac nt u ) T eT c ncl e erh[si e t
参数 可 生产 出 H0 A 焊条 用钢 。 8
关键 词 连续 铸 钢 H0 A 研 制 8
D EV ELo PM EN T F o C0 N Tl U o US STE EL A ST G O8 C H A
AT THE NO . 2 STEELn AKI NG PLANT oF SHo UGANG
ABS TRACT The iot a f c u i g o dii ns f c ntn u se l a tng H 08 p l m nu a t rn c n to o o i uo s t e c si A a t e t h N o 2 .
Байду номын сангаас
St e ma i Pl nt f Sh u a ha e e l k ng a o o g ng v be i to u e I s o t t he en n r d c d. t h ws ha t H08 A s e l o wedi g t e f r l n
轧 机 两 条 生产 线模 式 。 首 钢 第 二 炼 钢 厂 工 艺 流 程 为 铁 水 预 处 理— — 2 0t 炉 — — 精 炼 — — 方 坯 连铸 。2 0 1 转 0 2年 4月
与 其 他 钢 种 的最 大 差 异 是 要 求 确 保 H 8 钢材 的 0A 化 学 成 分 。 由 于 钢 水 凝 固过 程 中结 晶 及 宏 观偏 析
H08A钢水质量控制
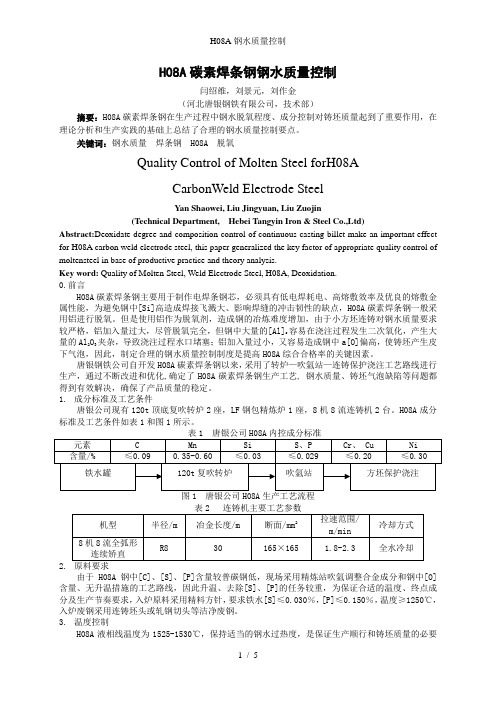
H08A碳素焊条钢钢水质量控制闫绍维,刘景元,刘作金(河北唐银钢铁有限公司,技术部)摘要:H08A碳素焊条钢在生产过程中钢水脱氧程度、成分控制对铸坯质量起到了重要作用,在理论分析和生产实践的基础上总结了合理的钢水质量控制要点。
关键词:钢水质量焊条钢 H08A 脱氧Quality Control of Molten Steel forH08ACarbonWeld Electrode SteelYan Shaowei, Liu Jingyuan, Liu Zuojin(Technical Department, Hebei Tangyin Iron & Steel Co.,Ltd)Abstract:Deoxidate degree and composition control of continuous casting billet make an important effect for H08A carbon weld electrode steel, this paper generalized the key factor of appropriate quality control of moltensteel in base of productive practice and theory analysis.Key word: Quality of Molten Steel, Weld Electrode Steel, H08A, Deoxidation.0.前言H08A碳素焊条钢主要用于制作电焊条钢芯,必须具有低电焊耗电、高熔敷效率及优良的熔敷金属性能,为避免钢中[Si]高造成焊接飞溅大、影响焊缝的冲击韧性的缺点,H08A碳素焊条钢一般采用铝进行脱氧。
但是使用铝作为脱氧剂,造成钢的冶炼难度增加,由于小方坯连铸对钢水质量要求较严格,铝加入量过大,尽管脱氧完全,但钢中大量的[Al]s容易在浇注过程发生二次氧化,产生大量的Al2O3夹杂,导致浇注过程水口堵塞;铝加入量过小,又容易造成钢中a[O]偏高,使铸坯产生皮下气泡,因此,制定合理的钢水质量控制制度是提高H08A综合合格率的关键因素。
《连铸H型异型坯二冷配水及凝固规律的研究》范文
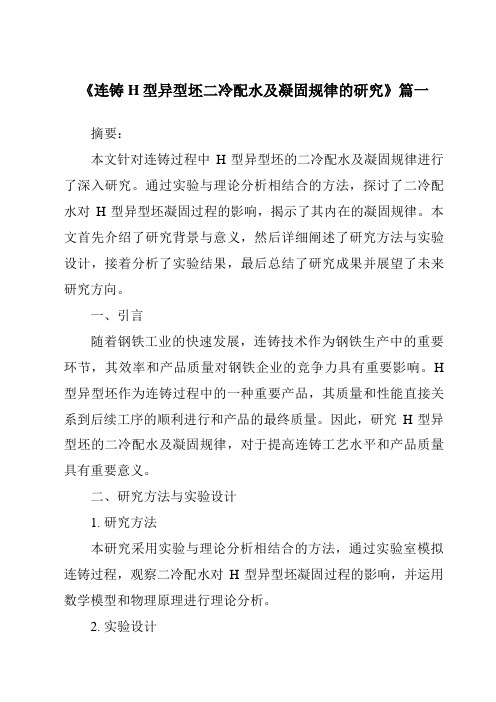
《连铸H型异型坯二冷配水及凝固规律的研究》篇一摘要:本文针对连铸过程中H型异型坯的二冷配水及凝固规律进行了深入研究。
通过实验与理论分析相结合的方法,探讨了二冷配水对H型异型坯凝固过程的影响,揭示了其内在的凝固规律。
本文首先介绍了研究背景与意义,然后详细阐述了研究方法与实验设计,接着分析了实验结果,最后总结了研究成果并展望了未来研究方向。
一、引言随着钢铁工业的快速发展,连铸技术作为钢铁生产中的重要环节,其效率和产品质量对钢铁企业的竞争力具有重要影响。
H 型异型坯作为连铸过程中的一种重要产品,其质量和性能直接关系到后续工序的顺利进行和产品的最终质量。
因此,研究H型异型坯的二冷配水及凝固规律,对于提高连铸工艺水平和产品质量具有重要意义。
二、研究方法与实验设计1. 研究方法本研究采用实验与理论分析相结合的方法,通过实验室模拟连铸过程,观察二冷配水对H型异型坯凝固过程的影响,并运用数学模型和物理原理进行理论分析。
2. 实验设计实验设计了不同二冷配水方案,包括配水量的变化、配水方式的调整等,观察了这些变化对H型异型坯凝固过程的影响。
同时,通过采集数据,分析了凝固过程中的温度变化、组织结构变化等。
三、实验结果与分析1. 二冷配水对凝固过程的影响实验结果表明,合理的二冷配水可以有效控制H型异型坯的凝固过程,使得凝固组织更加均匀,减少热裂等缺陷的产生。
而配水不当则会导致凝固组织不均,甚至产生热裂等质量问题。
2. 凝固规律分析通过对实验数据的分析,我们发现H型异型坯的凝固过程具有一定的规律性。
在二冷区,坯料的温度逐渐降低,凝固过程从表面向内部进行。
合理的配水可以使得这个过程中温度梯度适中,有利于形成良好的凝固组织。
3. 数学模型与物理原理的应用我们建立了数学模型,描述了二冷配水与H型异型坯凝固过程的关系。
同时,结合物理原理,如热传导、相变等理论,对实验结果进行了理论解释。
四、研究成果总结本研究通过实验与理论分析,深入探讨了连铸H型异型坯的二冷配水及凝固规律。
连铸坯表面质量缺陷及处理措施

连铸坯表面质量缺陷及处理措施【摘要】对于连铸板坯而言,振痕和裂纹是其主要的质量缺陷问题。
虽然这个缺陷在大多数情况下对连铸坯的质量影响不大,但是如果不及时有效的处理调还会带来很多附加的质量问题。
尤其是在生产不锈钢和高强度钢品种时,这种质量缺陷所带来的弊端更加明显。
【关键词】连铸坯;振痕;质量影响1振痕形成机理在连铸坯生产中,振痕和裂纹是两种最为常见的质量缺陷问题,主要是由于弯月面顶端溢流造成的,该缺陷形成以后会附带其他质量缺陷一并产生。
2振痕对铸坯质量的影响振痕对连铸坯的质量影响会导致后期出现列裂纹,包括横裂纹、角部横裂纹及矫直裂纹。
如果连铸坯内掺杂的杂质较多,会导致大规模网状裂纹的出现,甚至出现穿钢现象。
如果在连铸坯出现振痕的地方晶粒很大,就会产生晶间裂纹现象,在这样的情况下需要对连铸坯修磨,从而提高成材率。
3影响振痕深度的因素振动参数对振痕形状和深度有重要影响。
其中振幅、频率、负滑脱时间及振动方式最为重要;结晶器保护渣的耗量、粘度、保温性能及表面性能等有着重要影响;.钢的凝固特性对振痕有着重要影响,特别是当钢中碳含量和钢中Ni/Cr 比影响最突出。
当钢中碳含量为0.1%左右,Ni/Cr≈0.55左右,铸坯表面振痕最深。
4减少振痕深度的措施采用小振幅(s)、高频率(f)及减少负滑脱时间(tN),可以有效的减少振痕的深度;采用非正弦振动方式可以减少振痕的深度,这是因为非正弦振动其负滑脱时间tN比正弦振动短;采用渣耗量低,粘度高的保护渣,可以使振痕深度变浅。
采用保温性能好和能增加弯月面半径的保护渣可以减少振痕深度;提高不锈钢、钢液的过热度,尤其是含钛和含铝的不锈钢对减少该钢表面振痕深度是有效的。
提高结晶器进出冷却水的温差,对减少振痕深度是有利的。
5铸坯表面裂纹5.1表面纵裂纹铸坯表面纵裂纹是铸坯最主要表面缺陷,对铸坯质量影响极大,特别是板坯和圆坯最为突出,报废量和整修量很大。
5.1.1纵裂纹类型铸坯表面沟槽纵裂纹。
高延率易拉拔H08A轧制工艺优化
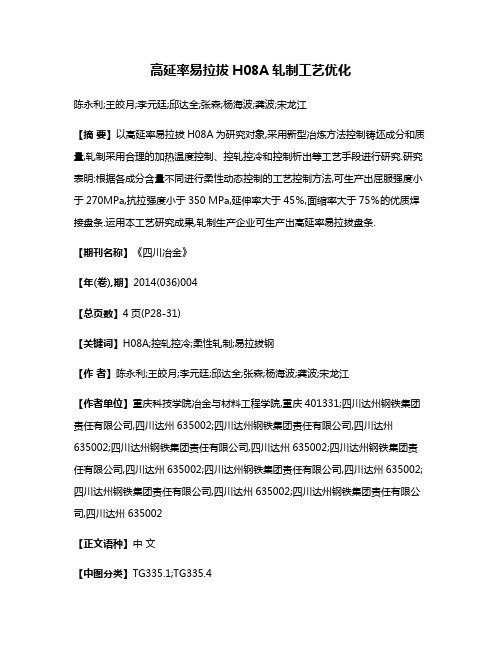
高延率易拉拔H08A轧制工艺优化陈永利;王皎月;李元廷;邱达全;张森;杨海波;龚波;宋龙江【摘要】以高延率易拉拔H08A为研究对象,采用新型冶炼方法控制铸坯成分和质量,轧制采用合理的加热温度控制、控轧控冷和控制析出等工艺手段进行研究.研究表明:根据各成分含量不同进行柔性动态控制的工艺控制方法,可生产出屈服强度小于270MPa,抗拉强度小于350 MPa,延伸率大于45%,面缩率大于75%的优质焊接盘条.运用本工艺研究成果,轧制生产企业可生产出高延率易拉拔盘条.【期刊名称】《四川冶金》【年(卷),期】2014(036)004【总页数】4页(P28-31)【关键词】H08A;控轧控冷;柔性轧制;易拉拔钢【作者】陈永利;王皎月;李元廷;邱达全;张森;杨海波;龚波;宋龙江【作者单位】重庆科技学院冶金与材料工程学院,重庆401331;四川达州钢铁集团责任有限公司,四川达州635002;四川达州钢铁集团责任有限公司,四川达州635002;四川达州钢铁集团责任有限公司,四川达州635002;四川达州钢铁集团责任有限公司,四川达州635002;四川达州钢铁集团责任有限公司,四川达州635002;四川达州钢铁集团责任有限公司,四川达州635002;四川达州钢铁集团责任有限公司,四川达州635002【正文语种】中文【中图分类】TG335.1;TG335.41 引言随着我国自动焊接设备应用范围的不断扩大与焊接自动化水平的不断提高,大型构件利用埋弧焊的比例不断提高,埋弧焊丝需求量在不断上升。
H08A作为一种专用的焊丝拉拔盘条钢种,具有“低碳、低硅、低锰”的成分特点[1],由于C、Si和 Mn含量较低,容易导致钢水的氧含量偏高引起连铸坯产生气泡,轧制过程中易产生结疤[2-3]、折叠等产品缺陷[4-5]。
使用含铝合金脱氧过低后易引起连铸浇注过程中絮流等生产事故,同时,LF温度控制,吹氩强度和时间、喂丝类型和长度、浇注环境、保护渣等对都会对铸坯的质量产生较大的影响[6-7];同时焊丝拉拔企业要求在执行GB/T3429-2002的同时要求该钢种具备“高延伸、易拉拔”的拉拔加工性能,这就对组织均匀性和组织相成分控制提出更加严格的要求[8],其控冷工艺参数对该钢种力学性能起决定性影响作用[9]。
高碳钢连铸坯偏析问题的分析与探讨

2007年炉外精炼年会论文集211高碳钢连铸坯偏析问题的分析与探讨曾四宝1,2)李洪波1,2)包燕平1)刘建华1)韩丽娜1)1)北京科技大学冶金与生态工程学院; 2)济南钢铁集团石横特殊钢厂摘要本文针对石横特殊钢厂R9m连铸机生产SWRH82B、GCr15等高碳钢连铸坯的偏析问题,分析讨论了钢水过热度、拉速、二次冷却强度和组合式电磁搅拌对连铸坯碳偏析影响,并对中心碳偏析问题提出了改善措施。
关键词偏析;钢水过热度;二次冷却强度;拉速;电磁搅拌1 前言对高碳钢来说,由于碳含量较高造成导热性差、凝固区间大,连铸坯本身容易产生偏析、疏松和缩孔等缺陷。
当前轴承钢连铸坯的控制水平普遍要求碳中心偏析指数≤1.15;钢帘线钢对碳偏析有更严格的要求,一般碳中心偏析指数≤1.05,否则在拉丝和扭转过程中容易引起断裂。
最近十几年来,随着钢水二次精炼、保护浇注、二次冷却、电磁搅拌和轻压下等技术的发展,高碳钢连铸技术也相应得到发展。
实际上,影响高碳钢连铸坯偏析的因素很多,如钢液过热度、二冷参数、拉速及电磁搅拌方式等。
关于钢液过热度对偏析的影响,国内外冶金工作者进行过大量的研究,得出了明确的结论,即随着过热度的降低,连铸坯的偏析逐渐减轻。
但是关于电磁搅拌和二冷水量等对偏析的影响目前还有争议。
通过统计分析石横特殊钢厂2006年3~9月份的生产情况和工艺变化情况,探讨了高碳钢(如SWRH82B、GCr15)连铸坯碳偏析的产生原因以及公司进一步改善碳偏析的途径,为工艺和装备优化、改进提供依据。
2 连铸机基本参数流数:4流;铸机半径:R9000/17500mm;流间距:1250mm;结晶器长度:850mm;浇铸断面:150mm×150mm;最大拉速:2.8m/min;电磁搅拌方式:M + F—EMS;二次冷却方式:足辊水冷0段+气雾冷却1、2、3段;浇铸钢种:碳结钢20#、45#、40Cr、ML10~35,20CrMo、高碳钢70#、80#、72A、82B、GCr15焊条钢H08A、H08Mn2SiA等。
H08A焊条钢的开发
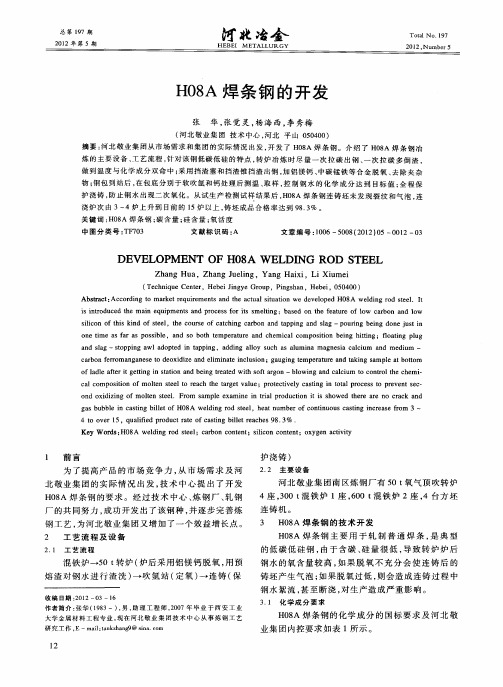
关键 词 : 0 A 焊 条 钢 ; 含 量 ; 含 量 ; 活 度 H 8 碳 硅 氧 中 图 分 类 号 :F 0 T 73 文献 标 识 码 : A 文 章 编 号 :0 6— 0 8 2 1 ) 5— 0 2— 3 10 5 0 (0 2 0 0 1 0
DEVELOP ENT 8 W ELDI M OF HO A NG ROD TEEL S
H08A品质提升技术研究
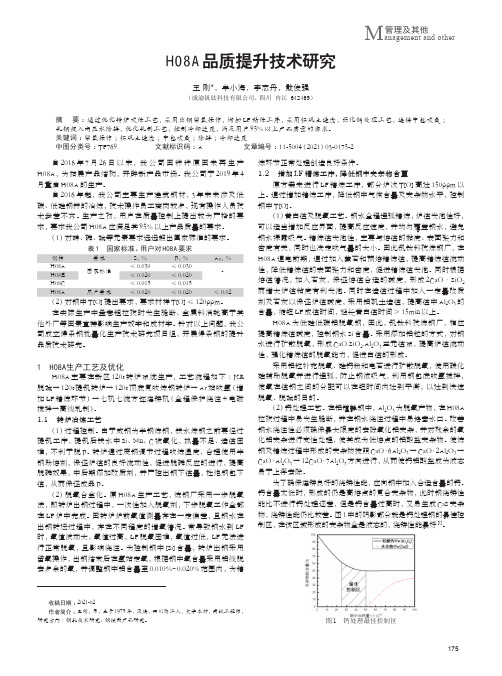
175管理及其他M anagement and otherH08A 品质提升技术研究王 刚*,牟小海,李志丹,戢俊强(成渝钒钛科技有限公司,四川 内江 642469)摘 要:通过优化转炉吹炼工艺,采用出钢留氧操作,增加LF 精炼工序,采用铝矾土造渣,强化钙处理工艺,连铸中包吹氩;轧钢投入高压水除鳞,优化轧制工艺,控制冷却速度,满足用户95%以上产品质量的需求。
关键词:留氧操作;铝矾土造渣;中包吹氩;除鳞;冷却速度中图分类号:TF769 文献标识码:A 文章编号:11-5004(2021)03-0175-2 收稿日期:2021-02作者简介:王刚,男,生于1975年,汉族,四川内江人,大学本科,高级工程师,研究方向:钢轧技术研究、钢铁新产品研究。
自2016年7月26日以来,我公司因种种原因未再生产H08A,为拓展产品结构,开辟新产品市场。
我公司于2019年4月重启H08A 的生产。
自2016年起,我公司主要生产建筑钢材,3年来未涉及低碳、低硅钢钟的冶炼,技术操作员工离岗较多,现有操作人员技术参差不齐。
生产之初,用户在质量控制上提出较为严格的要求,要求我公司H08A 应满足其95%以上产品质量的要求。
(1)对砷、磷、硫等元素要求远远超出国家标准的要求。
表1 国家标准、用户对H08A 要求钢种要求S,%P,%As,%H08A 国家标准≤0.030≤0.030-H08E ≤0.020≤0.020H08C ≤0.015≤0.015H08A用户要求≤0.020≤0.020≤0.02(2)对钢中T[O]提出要求,要求材样T[O]≤120ppm。
在实际生产中盘卷粗拉拔时发生脆断、金属料消耗高于其他外厂等因素直接影响生产效率和成材率。
针对以上问题,我公司成立焊条钢批量化生产技术研究项目组,开展焊条钢的提升品质技术研究。
1 H08A生产工艺及优化H08A 主要在新区120t 转炉系统生产,工艺流程如下:KR 脱硫→120t 提钒转炉→120t 顶底复吹炼钢转炉→Ar 站吹氩(增加LF 精炼环节)→七机七流方坯连铸机(全程保护浇注+电磁搅拌→高线轧制)。
连铸坯的质量缺陷

摘要为了解决连铸坯的内部质量问题,我写此论文主要是关于连铸坯的质量缺陷主要表现为,形状缺陷,内部缺陷等.中心裂纹,皮下裂纹,横裂,纵裂较为明显,,该论文关于铸坯裂纹的形成的原因、形成过程、裂纹的类型及区别、内部缺陷、形状缺陷。
通过对设备的点检完善及工艺操作的巩固,从而找出了形成质量缺陷和裂纹的成因,并做出了相应的控制措施,从而达到了减少铸坯质量问题.关键词:形成原因;形成过程;类型及区别;内部缺陷;形状缺陷。
1 文献综述1.1 国内外研究现状及分析连铸取代模铸是炼钢生产流程中一次巨大技术变革。
在1965年前绝大部分连铸机是比较简单的立式连铸机,在1975年80%板坯、70%大方坯和小方坯采用弧型连铸机生产,1984年已有30%板坯、20%大方坯采用连续弯曲矫直的立弯式连铸机生产。
目前世界上不少国家连铸比较接近饱和。
连铸机型已基本定型化。
目前改进的方向是使连铸机的结构和辅助设备具有更高的综合性能,操作过程自动化、可控性和安全性达到更高水平。
其目的在于进一步发挥连铸机的生产潜力和进一步提高铸坯质量。
提高连铸坯质量,主要是解决以下问题:1)改善工艺控制生产无缺陷的连铸坯,为实现直接热送和直接轧制创造条件。
2)获得内部极为均质的连铸坯,已保证产品的性能的均匀性。
对特殊用途钢种的铸坯,关键是改善铸坯内部结构和减少宏观偏析。
近几年开发的技术解决铸坯内部质量取得了明显效果。
3)浇注过程的自动监控和计算机跟踪以及与铸坯质量在线统计分析相结合,是保证连铸坯质量的主要手段。
采用这些技术可以实现对连铸坯质量在线表面缺陷进行检测,连铸设备的检控技术(如结晶器形状、振动等),铸坯质量在线识别模型。
1.2 课题的研究意义通过对连铸坯质量缺陷的研究,使我对连铸坯有进一步的认识。
使以后在生产过程中了解缺陷的形成,改善连铸坯质量有一定意义。
2内容2.1连铸坯的裂纹产生原因连铸坯裂纹的形成是一个非常复杂的过程,是传热,传质和应力相互作用的结果。
连铸车间铸坯质量问题分析解决报告

连铸车间铸坯质量问题分析解决报告
本月19日轧钢厂反应铸坯存在质量问题,随即进行取样、切割、分析、调整(详见附表)。
一、具体采取措施如下:1、根据实际情况调整配水系数(由1.2L/kg调至
1.18L/kg)、配水比例(0段35%、1段50%、2段15%调至0段35%、1段45%、2段20%)。
2、控制钢水过热度。
3、调整结晶器铜管冷却水(由150m3/h调至130m3/h)。
4、整理喷淋架。
5、调整V流1段喷嘴。
6、堵0段4角2个下喷嘴。
二、具体效果:裂纹有所减轻,但不可完全消除。
V流效果明显。
三、存在问题:
1、因铸坯切后切割面发现不了裂纹,使在生产中调整滞后。
2、二冷水喷淋架、支撑架、分水环变形,铸坯跑偏导致配水不均匀,。
虽经整理,但偏差仍然存在。
影响调水结果与分析判断。
四、下步措施:
1、按流标准调整配水,进一步跟踪、分析。
2、尽快完善喷淋冷却系统,解决铸坯跑偏。
3、继续控制中包钢水过热度及生产节奏稳定拉速。
连铸坯质量及控制方法

连铸坯质量及控制方法1、连铸坯质量的含义是什么?最终产品质量决定于所供给的铸坯质量。
从广义来说,所谓连铸坯质量是指得到合格产品所允许的铸坯缺陷的严重程度。
它的含义是:——铸坯纯净度(夹杂物数量、形态、分布、气体等)。
——铸坯表面缺陷(裂纹、夹渣、气孔等)。
——铸坯内部缺陷(裂纹、偏析、夹杂等)。
铸坯纯净度主要决定于钢水进入结晶器之前处理过程。
也就是说要把钢水搞“干净”些,必须在钢水进入结晶器之前各工序下功夫,如冶炼及合金化过程控制、选择合适的炉外精炼、中间包冶金、保护浇注等。
铸坯的表面缺陷主要决定于钢水在结晶器的凝固过程。
它是与结晶器坯壳形成、结晶器液面波动、浸入式水口设计、保护渣性能有关的。
必须控制影响表面质量各参数在目标值以内,以生产无缺陷铸坯,这是热送和直接扎制的前提。
铸坯的内部缺陷主要决定于在二次冷却区铸坯冷却过程和铸坯支撑系统。
合理的二次冷却水分布、支承辊的对中、防止铸坯鼓肚等是提高铸坯内部质量的前担。
因此,为了获得良好的铸坯质量,可以根据钢种和产品的不同要求,在连铸的不同阶段如钢包、中间包、结晶器和二次冷却区采用不同的工艺技术,对铸坯质量进行有效控制。
2、提高连铸钢种的纯净度有哪些措施?纯净度是指钢中非金属夹杂物的数量、形态和分布。
要根据钢种和产品质量,把钢中夹杂物降到所要求的水平,应从以下五方面着手:——尽可能降低钢中[O]含量;——防止钢水与空气作用;——减少钢水与耐火材料的相互作用;——减少渣子卷入钢水内;——改善钢水流动性促进钢水中夹杂物上浮。
从工艺操作上,应采取以下措施:(1)无渣出钢:转炉采用挡渣球(或挡渣锥),防止钢渣大量下到钢包。
(2)钢包精炼:根据钢种选择合适的精炼方法,以均匀温度、微调成分、降低氧含量、去除气体夹杂物等。
(3)无氧化浇注:钢水经钢包精炼处理后,钢中总氧含量可由130ppm下降到20ppm以下。
如钢包→中间包注流不保护或保护不良,则中间包钢水中总氧量又上升到60~100ppm范围,恢复到接近炉外精炼前的水平,使炉外精炼的效果前功尽弃。
- 1、下载文档前请自行甄别文档内容的完整性,平台不提供额外的编辑、内容补充、找答案等附加服务。
- 2、"仅部分预览"的文档,不可在线预览部分如存在完整性等问题,可反馈申请退款(可完整预览的文档不适用该条件!)。
- 3、如文档侵犯您的权益,请联系客服反馈,我们会尽快为您处理(人工客服工作时间:9:00-18:30)。
H08焊条钢连铸坯质量的研究摘要:转炉用准沸腾钢生产工艺冶炼H08焊条钢,生产过程中钢水的脱氧程度决定了钢中非金属夹杂物的形态和行为,会直接影响到钢的质量。
为改善H08焊条钢的质量,特别对连铸坯进行了必要的检测分析,并对H08焊条钢连铸坯中非金属夹杂物的形态与行为作了深入的研究。
碳素焊条钢必须具备低电焊耗电、高熔敷效率以及焊缝金属材料性能优良的工艺性能,因此钢中碳、硅含量要求都很低,在焊条钢的标准中对它的化学成分有严格的要求。
日本、美国、德国等发达国家的钢铁公司准沸腾钢的冶炼和连铸技术已达到很高的水平,多功能RH真空精炼处理是实现用连铸机浇铸准沸腾钢的关键技术手段。
但是,这一技术所需设备投资大,工艺复杂,处理成本高,在我国它很难为一般厂家所采纳。
在国内唐山钢铁集团公司(以下简称唐钢)首先开发出以转炉冶炼→钢包吹Ar、喂线、成分微调→方坯连铸的工艺流程生产准沸腾钢的技术,目前许多厂家也采用这种工艺生产碳素焊条钢、低碳拉丝钢等。
在无真空处理的条件下铝是最好的脱氧元素。
但过高的[A1]将会恶化钢的焊接性能,因此采用钢水脱氧程度介于镇静钢和沸腾钢之间的弱脱氧工艺来生产准沸腾钢,这样即可在保证残铝量w(A1)≤0.008%前提下,连铸能够顺利浇钢,又使钢坯的凝固过程不发生皮下气泡缺陷。
1 生产工艺及实验方案唐钢H08焊条钢的生产工艺流程为:150t转炉冶炼→钢包吹Ar并用MnAl、FeMn、SiCaBa合金和喂CaFe 线、CaAl线进行脱氧和合金化→135mm×135mm小方坯连铸→高速线材轧制→成品盘条。
H08焊条钢成分见表1。
实验共选取8炉次有代表性的连铸坯试样。
对铸坯的凝固组织结构、铸坯的气孔和非金属夹杂物进行检验分析。
取样炉次的工艺参数见表2。
表1 H08A普通碳素焊条钢的化学成分表2 取样炉次工艺数据2 铸坯的凝固组织由铸坯横断面的浸蚀试样观测到,铸坯急冷层一般为1.5~3.5mm,接着柱状晶一直生长到接近铸坯中心,中心等轴晶区宽约8~15 mm,上述情况分别见照片1、2、3。
并且随铸坯气孔量增多冷却强度降低,柱状晶粗化。
除3、4个炉次外,铸坯中心都存在着内裂,部分有微缩孔。
与一般铸坯的凝固组织相比较,本钢种铸坯凝固组织的柱状晶相当发达,几乎达到穿晶状态。
形成原因主要是由于钢的成分中合金元素含量低,并且铸坯断面小,冷却速度快,使凝固过程中溶质元素偏析低,有利于柱状晶生长。
有资料认为,含C量对准沸腾钢凝固组织有很大影响。
w(C)=0.1%左右为一次树枝状晶组织,w(C)>0.15%为二次树枝状晶组织,而w(C)<0.08%时为网络状凝固组织。
本次送检的8炉H08焊条钢均w(C)<0.08%,但浸蚀试样上未见网络状凝固组织,主要是一次柱状晶组织,没有二次枝晶生长。
由照片1可见,在距铸坯表面约2mm处一次柱状晶开始生长,并与传热方向有一定的倾斜,倾斜角度在10~15°的范围。
这里仅在较清晰的各炉1号试样上测定一次枝晶间距,情况见表3。
表3 一次枝晶间距测量值试样号一次枝晶间距/㎜距铸坯表面9㎜处距铸坯表面18㎜处1 0.200 0.2002 0.165 0.1663 0.163 0.1974 0.157 0.1935 0.1936 0.162 0.2227 0.205 0.1838 0.238 0.22533 铸坯中的气孔准沸腾钢连铸凝固时,易形成铸坯表层皮下气孔,铸坯气孔会影响钢的轧制和深加工,因此应尽量避免形成气孔。
准沸腾钢的脱氧程度要求控制在一个很狭窄的范围内。
连铸时由于钢水含氧量控制不当,其含量偏高时,在凝固过程中温度降低,钢水中的溶质元素平衡受到破坏,连续地冷却使碳与氧不能达到新的平衡状态,于是CO气体不停地析出。
最后析出的气体不可能浮出钢液面,滞留在钢中形成与柱状晶共同生长的表层气孔。
由于准沸腾钢仅析出少量CO气体,且连铸坯内部凝固时钢水的压力增大,所以就阻碍气泡在铸坯内部生成,而仅在铸坯表层形成气孔。
根据IRSID模型,气泡生成和发育的条件为:P g-2σl/g/r≥P1式中,P g为钢液中溶解气体的压力,MPa;P1为钢水局部液体压力,MPa;2σl/g/r为表面压力为σl/g时,液面气泡半径为r的压力,MPa。
凝固钢液出现气泡时,P1=0.1MPa,若r>200μm,则2σl/g/r可忽略不计,此时,P g≥0.1MPa时出现气泡。
所以保证铸坯质量的关键是控制临界气泡的形成,也就是P g=P CO+P N2+P H2<P1,其中最主要的是C0气泡的生成,即CO临界尺寸气泡的生成。
研究的5号样炉次脱氧不充分,造成铸坯表层向里约20mm的范围形成大量气孔,气孔的分布情况见横断面低倍酸浸试样的照片4。
典型的气孔端头形貌见照片5。
对取样各炉铸坯横断面低倍酸浸试样的气孔距表面最深距离观测情况列在表4中。
根据观测,在距铸坯表面4mm处,平行于坯表面的纵剖试样(即观察面垂直于柱状晶和气孔生长方向),它能更好地反应出气孔的数量分布密度,在铸坯上述剖面的中间20mm×18mm的试样上,气孔的数量分布及气孔直径大小情况也在表4中。
表4 H08焊条钢剖样气孔状况参数试样号气孔个数气孔直径/㎜气孔距表面最深距离/㎜1 1 0.20 32 3 0.23 123 1 0.2645 50 0.60-0.91 236 12 0.20-0.51 67 15 0.28-0.44 68 12 0.29-0.53 8通过表2相关的大包内钢液的氧活度αo参数与表4气孔状况参数相比较,可看到气孔的数量分布密度、孔径大小和气孔深度基本与钢中[0]含量相对应,所以避免铸坯出现气孔的关键是控制钢中氧含量。
由横断面试样可观察到气孔量增大,铸坯中心内裂及微缩孔情况加剧,很可能是显微气孔产生造成的结果。
4 铸坯中的非金属夹杂物焊条钢是用于制造各种焊条、焊丝的主要原材料,其盘条须经用户多次拉拔深加工,这就要求生产的钢材具有良好的拉拔性能,即均匀的材料性能,良好的塑性和冷加工性能。
为了保证这些性能,要求钢具有较高的纯净度,尤其是钢中大于50μm的大型夹杂含量要低。
因此有必要对该钢种中的夹杂物进行较深入的研究,以便于生产过程中控制它的产生。
大型夹杂物是影响焊条钢拉拔深加工的主要危害之一,用大样电解法制取钢中非金属夹杂物,将取得的较大夹杂物用电镜进行能谱分析。
分别电解8炉钢的连铸坯试样,制取的夹杂物基本相同。
其钢中大型夹杂物的平均值为0.1235×10-6。
由于5号试样含氧量高,其夹杂物类型更复杂,故以5号试样为例,电解的夹杂物见体视显微镜拍摄的照片9,由照片9可见到3种主要夹杂物,并分别作能谱分析。
①透明球状夹杂物,颜色逐渐由无色透明到淡黄色或淡紫色。
成分见能谱图1、2。
无色透明者为较纯的Si02,颜色较淡者为铁锰硅酸盐。
图1 球状复杂成分硅酸盐夹杂能谱图图2 球状含Zr高的复杂成分硅铝酸盐夹杂能谱图②灰白色不透明无光泽球状夹杂物,成分见能谱图1,为复杂硅酸盐。
③不透明深灰色到黑色有光泽球状夹杂物,成分见能谱图2,是复杂玻璃相,其中Zr含量较高,是受到耐火材料污染所致。
4.1 夹杂物的金相研究及能谱分析用金相法观测连铸坯的非金属夹杂物,选择典型夹杂物用电镜进行能谱分析。
金相观察的主要夹杂物类型:第1种为二氧化硅和铁锰硅酸盐球状夹杂物,见金相照片6为简单硅酸盐类夹杂物,其能谱图基本相似于能谱图1、2;第2种为深灰色复杂硅酸盐夹杂物,见金相照片7;第3种为硅酸盐与硫化物复相或双相夹杂物,有以硅酸盐为基体附着硫化物的复相夹杂物,见电镜照片10,也有以硫化物为基体附着硅酸盐的双相夹杂物,见电镜照片11。
第4种为铁锰氧化物固溶体夹杂,见金相照片8,大多小于3μm,主要存在于5号试样中,其它炉号未见。
电解的夹杂物中未见此种夹杂物,主要是由于它颗粒小制取过程中被水冲走。
为了避开内弧侧夹杂物聚集的影响,在横断面上垂直内外弧方向上的铸坯中心取样。
抛光试样在500倍显微镜下每处观测100个视场,用网格记点法测定夹杂物所占体积率。
根据观测将夹杂物分为上述4种类型和3种粒径范围(Φ10μm以下、Φ10μm~Φ20μm和Φ20μm以上),观测到Φ30 μm以上的大型夹杂物很少,所见最大夹杂物约Φ100μm。
4.2 夹杂物观测结果及分析(1)H08焊条钢连铸坯中主要夹杂物有3种,第1种为二氧化硅和铁锰硅酸盐球状夹杂物;第2种为复杂硅酸盐夹杂物;第3种为硅酸盐与硫化物复相或双相夹杂物。
第1种夹杂物主要是钢水氧化产物;第2种夹杂物主要是钢水氧化产物和脱氧产物的融合物;第3种夹杂物的形成是由于准沸腾钢氧含量较高,使S在铁中的溶解度降低,因此在凝固过程的较高温度下就开始沉淀。
硫化物的析出与钢的脱氧产物液态铁锰硅酸盐的析出同时进行,就形成硅酸盐与硫化物相复合的夹杂物。
而由于偏晶反应的结果形成一种球形的硫化物中含有氧化物的溶液,当温度下降时夹杂物中先是硫化物从硅酸盐中析出,而后是氧化物沉淀,固态下是一种双相夹杂物。
当钢水含氧量高,含硅量很低时(如5号样炉次w(Si)=0.006%),将出现大量的铁锰氧化物固溶体夹杂。
钢水含氧高还可造成对耐火材料的浸蚀,产生含Zr的复杂硅铝酸盐夹杂。
(2)从7个炉次3种夹杂物3个粒径范围和总量的平均体积分数上看(见表5),第1和第2两种夹杂在3个粒径范围都有分布;第3种夹杂主要为Φ10μm以下的夹杂物,且大多小于3 μm,其总量体积分数最高,即夹杂中其含量最高。
但大型夹杂以第1种最多,第2种次之。
表5 3种夹杂物各粒度范围的平均体积分数%种类<10μm10-20μm>20μm总量1 0.029 0.018 0.006 0.0532 0.016 0.012 0.001 0.0293 0.093 0.006 0 0.099(3)在铸坯横断面内外弧方向上,从表层至铸坯中心各炉次夹杂物总量的体积分数是随机分布的。
但随钢水含氧量的增高,其各部位夹杂总量有升高的趋势。
(4)在铸坯横断面中心内外弧方向上,从第7炉次的夹杂物总量体积分数的分布来看,其夹杂物在内弧侧距坯表面约30mm处含量最高,其体积分数达0.55%,见图3。
与镇静钢相比,准沸腾钢连铸坯内弧侧的夹杂物聚集尚不十分显著,这主要是由于凝固过程CO析出促进了夹杂物上浮,明显减轻了大型夹杂在内弧侧的聚集。
图3 夹杂物由内弧至外弧方向上的分布图5 结论(1)H08焊条钢铸坯凝固组织的柱状晶相当发达,几乎达到穿晶状态,无二次枝晶出现。
(2)准沸腾钢连铸凝固时易形成铸坯表层皮下气孔,气孔的数量分布密度、孔径大小和气孔深度基本与钢中[O]含量相对应,所以避免铸坯出现气孔的关键是控制钢中氧含量。