水泥烧失量试验作业指导书
水泥检验作业指导书

水泥检验作业指导书本作业指导书参照GB12573—90《水泥取样方法》、GB1345—2005《水泥细度检验方法》、GB175—1999《硅酸盐水泥、普通硅酸盐水泥》、GB/T1346—2001《水泥标准稠度、凝结时间、安定性检验方法》、GB/T17671—1999《水泥胶砂强度检验方法》、GB/T176—1996《水泥化学分析方法》等标准进行编制。
注:仅适合于本公司常用的普通硅酸盐水泥一、验收批水泥进场后按同一生产厂家、同一等级、同一品种、同一批号且连续进场的水泥,袋装不超过200吨为一批、散装不超500吨为一批。
对初次使用的水泥每批检验其细度、凝结时间、安定性、烧失量、3d和28d强度;正常每批检验其细度、凝结时间、安定性、3d和28d强度。
二、取样1、取样要求1.1、取样工具:手工取样器。
1.2、取样部位:散装水泥在水泥运输车上用取样器抽取,取样要求不同深度、不同部位。
1.3、取样数量:抽取20kg。
1.4、样品的制备:样品抽取后通过0.9mm方孔筛,进行编号,均分为试验样和封存样。
1.5、样品的包装与贮存:样品取得后应存放在密封的金属容器中,加封条。
容器应洁净、干燥、防潮、密闭、不易破损、不与水泥发生反应。
贮存于干燥、通风的环境中。
试验样应妥善保管40~60天。
1.6、样品的标识:对封存样和试验样都应标有品种、等级、编号、取样时间、地点、取样人等贴于取样筒上。
三、细度检验1. 仪器1.1 负压筛析仪:负压可调范围4000~6000Pa ;喷气嘴上口平面与筛网之间距离为2~8mm 。
1.2 天平:最大称量为100g ,分度值不大于0.01g 。
1.3 0.080mm 方孔筛2、操作程序2.1筛析试验前,应把负压筛放在筛座上,盖上筛盖,接通电源,检查控制系统,调节负压至4000~6000Pa 范围内。
2.2称取试样25g ,置于洁净的负压筛中,盖上筛盖,放在筛座上,开动筛析仪连续筛析2min ,在此期间如有试样附着在筛盖上,可轻轻地敲击,使试样落下。
水泥的化学分析--烧失量
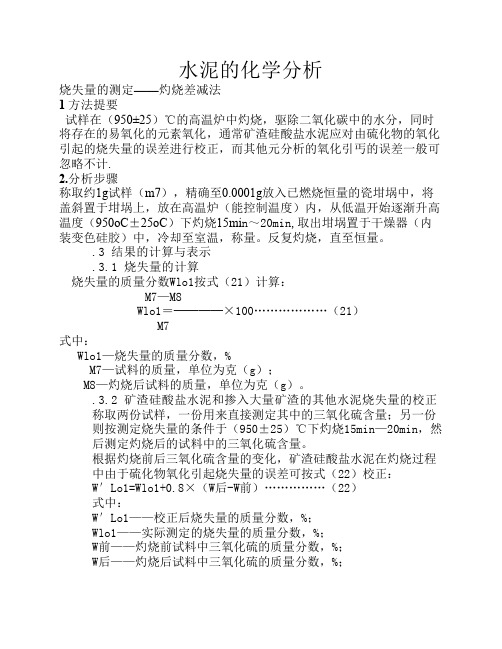
水泥的化学分析烧失量的测定——灼烧差减法1 方法提要试样在(950±25)℃的高温炉中灼烧,驱除二氧化碳中的水分,同时将存在的易氧化的元素氧化,通常矿渣硅酸盐水泥应对由硫化物的氧化引起的烧失量的误差进行校正,而其他元分析的氧化引丐的误差一般可忽略不计.2.分析步骤称取约1g试样(m7),精确至0.0001g放入已燃烧恒量的瓷坩埚中,将盖斜置于坩埚上,放在高温炉(能控制温度)内,从低温开始逐渐升高温度(950oC±25oC)下灼烧15mi n~20min,取出坩埚置于干燥器(内装变色硅胶)中,冷却至室温,称量。
反复灼烧,直至恒量。
.3 结果的计算与表示.3.1 烧失量的计算烧失量的质量分数Wlo1按式(21)计算:M7—M8Wlo1=────×100 (21)M7式中:Wlo1—烧失量的质量分数,%M7—试料的质量,单位为克(g);M8—灼烧后试料的质量,单位为克(g)。
.3.2 矿渣硅酸盐水泥和掺入大量矿渣的其他水泥烧失量的校正称取两份试样,一份用来直接测定其中的三氧化硫含量;另一份则按测定烧失量的条件于(950±25)℃下灼烧15min—20min,然后测定灼烧后的试料中的三氧化硫含量。
根据灼烧前后三氧化硫含量的变化,矿渣硅酸盐水泥在灼烧过程中由于硫化物氧化引起烧失量的误差可按式(22)校正:W′Lo1=Wlo1+0.8×(W后-W前) (22)式中:W′Lo1——校正后烧失量的质量分数,%;Wlo1——实际测定的烧失量的质量分数,%;W前——灼烧前试料中三氧化硫的质量分数,%;W后——灼烧后试料中三氧化硫的质量分数,%;0.8——S2-氧化为SO42-时增加的氧与SO3的摩尔质量比,即(4×16)/80=0.8.。
水泥试验作业指导书
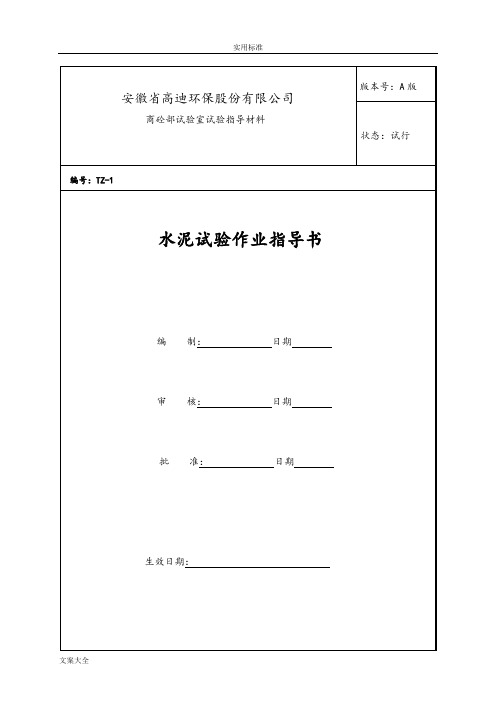
1目的为了规范商品砼试验室对水泥的细度、安定性、凝结时间、强度等检验的工作程序,实现标准化操作,特制定此作业指导书作为检测依据。
2适用范围本作业指导书适用于民用建筑的砼及制品中的水泥细度、安定性、凝结时间、强度的检测。
3编制依据3.1GB1345-2005 《水泥细度检验方法》3.2GB/T1346-2001 《水泥标准稠度用水量、凝结时间、安定性检验方法》3.3GB/T17671-1999 《水泥胶砂强度检验方法》3.4GB/J2419-2005 《水泥胶砂流动度测定方法》3.5GB/J 208-94 《水泥密度测定方法》3.63GB8074-87 《水泥比表面积测定方法》3.7GB/T24001-2004《环境管理体系规范及使用指南》3.8GB/T28001-2001《职业安全健康管理体系审核规范》4作业项目概述4.1细度:硅酸盐水泥比表面积大于300m2/kg,普通、矿渣水泥80μm方孔筛筛余不得超过10%。
4.2安定性:用沸煮法检验必须合格。
4.3凝结时间:•普通水泥初凝不得小于45min,终凝不得大于10h;硅酸盐水泥终凝不得迟于6.5h。
4.4强度:水泥强度等级按规定龄期的抗压强度和抗折强度来划分,各强度等级水泥的各龄期强度不得低于规定的数值。
4.5水泥试样:水泥试样应充分拌匀,通过0.9mm方孔筛并记录筛余物情况,但要防止过筛时混进其他水泥。
5作业准备5.1人员有建筑材料试验岗位证书试验员、记录员各一人;所有试验人员须经过专业技术培训,且考核合格,并取得相应的上岗证书。
5.2仪器设备试验筛(负压筛或水筛)、天平(称量100g,分度值不大于0.05g)水泥净浆搅拌机、•净浆标准稠度与凝结时间测定仪、沸煮箱、雷氏夹、量水器(最小刻度为1ml,精度1%)、天平(能准确称量至1g)、标准养护箱、雷氏夹膨胀值测量仪(标尺最小刻度为1mm)。
胶砂搅拌机、胶砂振动台、试模及下料漏斗、抗折试验机、抗压试验机和抗压夹具、金属直尺。
水泥企业化学分析作业指导书

试剂配制及标准溶液配制与标定作业指导书1.前言1.1本作业指导书规定了试剂配制及标准溶液配制与标定操作规程;1.2本作业指导书根据GB/T176—1996《水泥化学分析方法》提出。
2.适用范围本作业指导书适用于本公司化学分析中试剂配制及标准溶液配制与标定。
3.引用标准GB/T176—1996《水泥化学分析方法》4.主要内容4.1试剂的配制4.1.1盐酸(1+1)、(1+5);4.1.2氨水(1+1);4.1.3氢氧化钾溶液(200g/L);将200g氢氧化钾(KOH)溶于水中,加稀释至1L,贮存于塑料瓶中;4.1.4 硝酸银溶液(5g/L):将5g硝酸银(AgNO3)溶于水中,加10mL硝酸(HNO3),用水稀释至1L;4.1.5 氯化钡溶液(100g/L):将100g二水氯化钡(BaCI2〃2H2O)溶于水中,加水稀释至1L;4.1.6 PH4.3的缓冲溶液:将42.3g无水乙酸钠(CH3COONa)溶于水中,加80mL冰醋酸(CH3COOH),用水稀释至1L,摇匀;4.1.7 PH10的缓冲溶液:将67.5g氯化铵(NH4CI)溶于水中,加570mL氨水,加水稀释至1L;4.1.8 三乙醇胺[N(CH2CH2OH)3]:(1+2);4.1.9 酒石酸钾钠溶液(100 g/L):将100g酒石酸钾钠(C4H4KNaO6〃4H2O)溶于水中,稀释至1L;4.1.10 氟化钾溶液(150 g/L):称取150g氟化钾(KF〃2H2O)于塑料杯中,加水溶解后,用水稀释至1L,贮存于塑料瓶中;4.1.11 氟化钾溶液(20 g/L):称取20g氟化钾(KF〃2H2O)溶于水中,稀释至1L,贮存于塑料瓶中。
4.1.12 氯化钾溶液(50g/L):将50g氯化钾(KCI)溶于水中,加水稀释至1 L。
4.1.13 氯化钾—乙醇溶液(50g/L):将5g水氯化钾(KCI)溶于50mL水中,加入50mL95%(V/v)乙醇(C2H5OH),混匀。
水泥的烧失量

即水泥所排开的无水煤油的体积(mL)。
②水泥密度ρ(g/cm3)按下式计算:水泥密度ρ=水泥密度(g)/排开的体积(cm3)试试验结果取两次测定结果的算术平均值,两次测定结果之差不得超过0.02g/cm3.
5.制备试验:
按GB/T12573方法取样,送往实验室的样品赢是具有代表性的均匀性样品。
采用四分法或缩分器将试样缩分至约100g,经80μm方孔筛筛析,用磁铁吸去筛余物中金属铁,将筛余物经过研磨后使其全部通过孔径为80μm方孔筛,充分混匀,装入试样瓶中,密封保存,供测定用。
5.试验过程:
⑴称取约1g试样(m7),精确至0.0001g,置于已灼烧恒量的瓷坩埚中,将盖斜置于坩埚上,放在马弗炉内,从低温开始逐渐升高温度,在950~1000℃下灼烧15~20min,取出坩埚置于干燥器中冷却至室温,称量,反复灼烧,直至恒量。
⑵X=((m7-m8) /m7)×100
式中:m7——试料的质量,g;
m8——灼烧后试料的质量,g;。
烧失量的测定检验规程
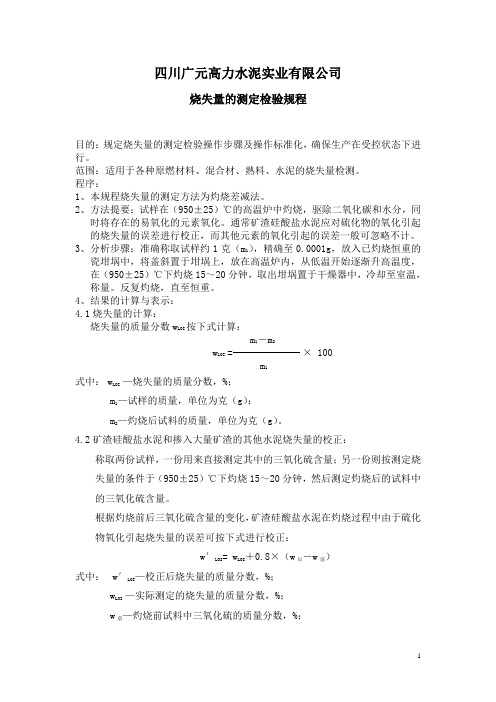
四川广元高力水泥实业有限公司烧失量的测定检验规程目的:规定烧失量的测定检验操作步骤及操作标准化,确保生产在受控状态下进行。
范围:适用于各种原燃材料、混合材、熟料、水泥的烧失量检测。
程序:1、本规程烧失量的测定方法为灼烧差减法。
2、方法提要:试样在(950±25)℃的高温炉中灼烧,驱除二氧化碳和水分,同时将存在的易氧化的元素氧化。
通常矿渣硅酸盐水泥应对硫化物的氧化引起的烧失量的误差进行校正,而其他元素的氧化引起的误差一般可忽略不计。
3、分析步骤:准确称取试样约1克(m1),精确至0.0001g,放入已灼烧恒重的瓷坩埚中,将盖斜置于坩埚上,放在高温炉内,从低温开始逐渐升高温度,在(950±25)℃下灼烧15~20分钟,取出坩埚置于干燥器中,冷却至室温,称量。
反复灼烧,直至恒重。
4、结果的计算与表示:4.1烧失量的计算:烧失量的质量分数wLOI按下式计算:m1-m2wLOI= × 100m1式中:wLOI—烧失量的质量分数,%;m1—试样的质量,单位为克(g);m2—灼烧后试料的质量,单位为克(g)。
4.2矿渣硅酸盐水泥和掺入大量矿渣的其他水泥烧失量的校正:称取两份试样,一份用来直接测定其中的三氧化硫含量;另一份则按测定烧失量的条件于(950±25)℃下灼烧15~20分钟,然后测定灼烧后的试料中的三氧化硫含量。
根据灼烧前后三氧化硫含量的变化,矿渣硅酸盐水泥在灼烧过程中由于硫化物氧化引起烧失量的误差可按下式进行校正:w′LOI = wLOI+0.8×(w后-w前)式中:w′LOI—校正后烧失量的质量分数,%;wLOI—实际测定的烧失量的质量分数,%;w前—灼烧前试料中三氧化硫的质量分数,%;w后—灼烧后试料中三氧化硫的质量分数,%;0.8—S2-氧化为SO42-时增加的氧与SO3的摩尔质量比,即(4×16)/80=0.8。
5、允许差:同一实验室的允许差为±0.15%。
水泥检测作业指导书

1 水泥检测作业指导书1.1 水泥概述:1.1.1 定义水泥是一种水硬性无机胶凝材料。
通用硅酸盐水泥包括六大品种水泥:硅酸盐水泥,普通硅酸盐水泥,矿渣硅酸盐水泥,火山灰质硅酸盐水泥,粉煤灰硅酸盐水泥和复合硅酸盐水泥。
产品标准:《通用硅酸盐水泥》GB/T175-20071.2 相关标准:产品标准:GB/T175-2007《通用硅酸盐水泥》检测方法:GB/T1345-2005《水泥细度检验方法(筛析法)》GB/T208-2014《水泥密度检验方法》GB/T8074-2008《水泥比表面积测定方法(勃氏法)》GB/T1346-2011《水泥标准稠度用水量、凝结时间、安定性检验方法》GB/T17671-1999《水泥胶砂强度检验方法(ISO法)》GB/T2419-2005《水泥胶砂流动度测定方法》GB/T176-2008《水泥化学分析方法》GB/T12573-2008《水泥取样方法》GB/T750-1992《水泥压蒸安定性试验方法》验收标准:TB10424-2010《铁路混凝土工程施工质量验收标准》注:硅酸盐水泥和普通硅酸盐水泥的性能按TB10424-2010,其他品种水泥的性能按国家现行标准《通用硅酸盐水泥》(GB175-2007)的规定。
1.3 水泥的技术指标、抽检频次及检验方法见表1-11.4 所用到的仪器设备见表1-21.5 环境要求:水泥室的环境要求:试验室温度为 20℃±2℃,相对湿度应不低于 50%;水泥试样、拌和水、仪器和用具的温度应与试验室一致;1.6水泥取样方法:1.6.1 手工取样:散装水泥,当所取水泥深度不超过2m时,每一个编号内采用散装水泥取样器随机取样。
通过转动取样器内管控制开关,在适当位置插入水泥一定深度,关闭后小心抽出取样管,将所取样品放入符合要求的容器中。
每次抽取的单样量应尽量一致。
袋装水泥,每一个编号内随机抽取不少于20袋水泥,采用袋装水泥取样器取样,将取样器沿对角线方向插入水泥包装袋中,用大拇指按住气孔,小心抽出取样管,将所取样品放入符合要求的容器中,每次抽取的单样量应尽量一致。
3116 水泥检测作业指导书

水泥检测作业指导书哈尔滨市盛兴达商品混凝土制造有限公司实验室持有人:水泥检测作业指导书一、执行标准GB 50204-2002 混凝土结构工程施工及验收规范GB 175-2007 硅酸盐水泥、普通硅酸盐水泥GB/T 1345-2005 水泥细度检验方法(筛析法)GB/T 17671—1999 水泥胶砂强度检验方法(ISO法)GB/T 1346-2001 水泥标准稠度用水量、凝结时间、安定性检验方法二、代表批量及取样方法检查数量,按同一生产厂家、同一等级、同一品种、同一批号且连续进场的水泥,袋装不超过200t为一批,散装不超过500t为一批,每一批抽样不少于一次。
从分布均匀的不同部位,至少从20袋中抽取(散装至少从三个罐中抽取)大致相同数量,混合后取12kg样品送试。
三、送试样品处理试验前:接到水泥试样后,应立即将水泥(约12 kg)装入内部套有塑料袋的留样桶里,然后封紧袋口、盖严桶盖,贴上编号标签后送至水泥试验室,待24h后进行试验。
试验后:试验完毕,剩余水泥应妥善处理,同样封紧袋口、盖严桶盖,放置于水泥样品留样架上,留置三个月,再报质量负责人按要求处理。
四、水泥试验室要求温度应保持在20℃±2℃,相对湿度应不低于50%;试体带模养护的养护箱或雾室、养护池水温度应保持在20℃±1℃,相对湿度不低于90%。
试验室空气温度和相对湿度及养护池水温在工作期间每天至少记录一次;养护箱或雾室的温度与相对湿度至少每4h记录一次,在自动控制的情况下记录次数可以酌减至一天记录二次。
五、化学指标(见下表:)1、化学指标应符合下表规定。
2、碱含量(选择性指标)水泥中碱含量按Na2O+0.658K2O计算值表示。
若使用活性骨料,用户要求提供低碱水泥时,水泥中碱含量应不大于0.60%或由双方协商确定。
3、物理指标A、凝结时间硅酸盐水泥初凝不小于45min,终凝不大于390min;普通硅酸盐水泥、矿渣硅酸盐水泥、火山灰硅酸盐水泥、粉煤灰硅酸盐水泥和复合硅酸盐水泥初凝小于45min,终凝不大于600min。
水泥烧失量试验
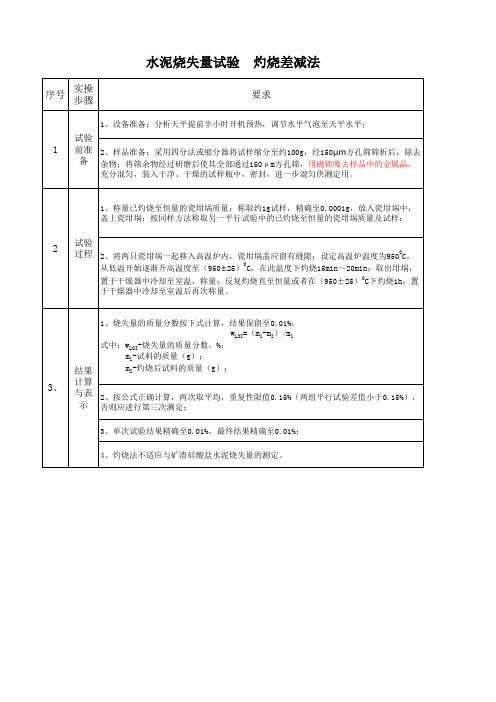
计算 与表 2、按公式正确计算,两次取平均,重复性限值0.15%(两组平行试验差值小于0.15%),
示 否则应进行第三次测定;
3、单次试验结果精确至0.01%,最终结果精确至0.01%;
4、灼烧法不适应与矿渣硅酸盐水泥烧失量的测定。
水泥烧失量试验 灼烧差减法
ห้องสมุดไป่ตู้
序号
实操 步骤
要求
1、设备准备:分析天平提前半小时开机预热,调节水平气泡至天平水平;
试验 1 前准 2、样品准备:采用四分法或缩分器将试样缩分至约100g,经150μm方孔筛筛析后,除去
备 杂物;将筛余物经过研磨后使其全部通过150μm方孔筛,用磁铁吸去样品中的金属品,
充分混匀,装入干净、干燥的试样瓶中,密封,进一步混匀供测定用。
置于干燥器中冷却至室温,称量;反复灼烧直至恒量或者在(950±25)0C下灼烧1h,置
于干燥器中冷却至室温后再次称量。
1、烧失量的质量分数按下式计算,结果保留至0.01%;
wLOI=(m1-m2)/m1
式中:wLOI-烧失量的质量分数,%;
m1-试料的质量(g);
结果
m2-灼烧后试料的质量(g);
3、
1、称量已灼烧至恒量的瓷坩埚质量;称取约1g试样,精确至0.0001g,放入瓷坩埚中, 盖上瓷坩埚;按同样方法称取另一平行试验中的已灼烧至恒量的瓷坩埚质量及试样;
2
试验 过程 2、将两只瓷坩埚一起移入高温炉内,瓷坩埚盖应留有缝隙;设定高温炉温度为9500C,
从低温开始逐渐升高温度至(950±25)0C,在此温度下灼烧15min~20min;取出坩埚,
检测作业指导书

文件编号:XXXXX-ZY-2018作业指导书控制状态:控制号:持有者:发布日期:XXXXXXXX实施日期:XXXXXXXXXXXXXXXXXX作业指导书批准:XXXXXX审核:XXXXXX主编:编写人员:编制依据:相关试验规程前言为使公司新增各项试验工作有章可循,使工作(作业)安全风险评估和过程控制规范化,保证试验全过程的安全和质量,公司质量办公室特制订了本作业指导书,作为持续改进试验工作质量、保证管理体系正常运作的基础和依据,同时用作学习与培训教材,以提高试验人员的素质和技术水平。
希望各有关人员在工作中严格遵照此作业指导书的工作流程进行日常工作、试验,以保证工作质量,为客户提供更好的服务。
XXXXXXXXXXXXXXX质量办公室XXXXXXXXX水泥作业指导书一、烧失量1 方法提要试样在(950±25)℃的高温炉中灼烧,驱除水分和二氧化碳,同时将存在的易氧化元素氧化。
通常矿渣硅酸盐水泥应对由硫化物的氧化引起的烧失量误差必须进行校正,而其他元素存在引起的误差一般可忽略不计。
2 引用标准《水泥化学分析方法》 GB/T176-20083 分析步骤称取约 1g 试样( m ),精确至 0.0001g ,置于已灼烧恒量的瓷坩埚上,将盖斜置于坩埚上,放在高温炉内从低温开始逐渐升高温度,在(950 ± 25 )℃的高温炉中灼烧 15~20 min ,取出坩埚置于干燥器中冷却至室温,称量。
反复灼烧,直至连续两次称量之差小于 0.0005g 时,即达到恒量。
4 结果计算烧失量的质量百分数ω LOI 按下式计算:ω LOI = ×100式中:ω LOI ——烧失量的质量百分数, % ;m ——试料的质量,单位为克( g );m 1 ——灼烧后试料的质量,单位为克( g )。
5 结果整理试验结果精确至 0.01% 、平行试验两次,允许重复性误差为0.15% 。
二、.碱含量水泥氧化钾和氧化钠试验检测细则(火焰光度计基准法)1 方法提要试样经氢氟酸 - 硫酸蒸发处理除去硅,用热水浸取残渣,以氨水和碳酸铵分离铁、铝、钙、镁。
水泥试验作业指导书
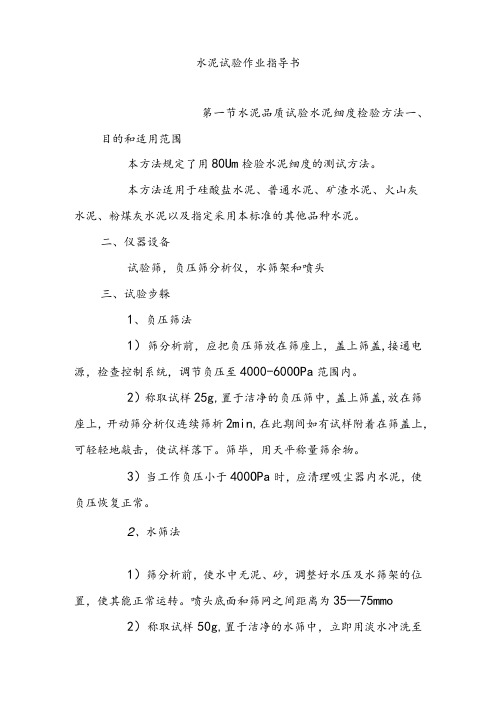
水泥试验作业指导书第一节水泥品质试验水泥细度检验方法一、目的和适用范围本方法规定了用80Um检验水泥细度的测试方法。
本方法适用于硅酸盐水泥、普通水泥、矿渣水泥、火山灰水泥、粉煤灰水泥以及指定采用本标准的其他品种水泥。
二、仪器设备试验筛,负压筛分析仪,水筛架和喷头三、试验步躲1、负压筛法1)筛分析前,应把负压筛放在筛座上,盖上筛盖,接通电源,检查控制系统,调节负压至4000-600OPa范围内。
2)称取试样25g,置于洁净的负压筛中,盖上筛盖,放在筛座上,开动筛分析仪连续筛析2min,在此期间如有试样附着在筛盖上,可轻轻地敲击,使试样落下。
筛毕,用天平称量筛余物。
3)当工作负压小于400OPa时,应清理吸尘器内水泥,使负压恢复正常。
2、水筛法1)筛分析前,使水中无泥、砂,调整好水压及水筛架的位置,使其能正常运转。
喷头底面和筛网之间距离为35—75mmo2)称取试样50g,置于洁净的水筛中,立即用淡水冲洗至大部分细粉通过后,放在水筛架上,用水压为0.05士0.02MPa的喷头连续冲洗3min。
筛毕,用少量水把筛余物冲至蒸发皿中,等水泥颗粒全部沉淀后,小心倒出清水,烘干并用天平称量筛余物。
3、手工干筛法在没有负压筛析仪和水筛的情况下,允许用手工干筛法测定。
4、试验筛的清洗试验前必须保持洁净,筛孔通畅。
四、试验结果计算F-ms*100/mF一水泥试样的筛余百分数(%)ms—水泥筛余物的质量(g)m—水泥试样的质量(g)计算结果精确到0.1%负压筛法与水筛法或手工筛法测定的结果发生争议时,以负压筛法为准。
水泥的烧失量试验一、仪器设备高温炉,分析天平,瓷卅锅、干燥器、培蜗钳等二、试验步骤称取通过筛孔的烘干水泥时称准到O.0001g;重复灼烧称量,至少两次质量相差小于0.5mg,即为恒量。
至少做一次平行试验。
三、结果整理烧失量(%)—[m-(m2-m1)]*100/m m一烘干水泥试样质量,gml一空用蜗质量,gm2一灼烧后水泥+培病质量,g烧失量测定结果允许偏差测定值绝对偏差相对偏差>50<0.91.0~1.550~30<0.71.5~2.030-10<0.52.0~3.010-5<0.33.0~4.05~1<0.24.0~5.01~0.K0.055.0~6.00.1-0.05<0.0066.0~8.00.05~0.0K0.0048.0—10.0O.01~0.005<0.OO11O.0-12O.005-0.OOKO.000612—15.O<0.OOKO.0001515.0~20.O水泥标准稠度用水量、凝结时间、安定性检验方法一、目的和适用范围本方法规定了水泥标准稠度用水量、凝结时间和体积安定性的测试方法。
水泥化学分析方法作业指导书

水泥化学分析方法作业指导书F1水泥试样的制备按GB12573方法进行取样,送往实验室样品应是具有代表性的均匀样品。
采用四分法缩分至约100g,经0.080mm方孔筛筛析,用磁铁吸去筛余物中金属铁,将筛余物经过研磨后使其全部通过0.080mm方孔筛。
将样品充分混匀后,装入带有磨品塞的瓶中并密封。
F2烧失量的测定(基准法)F⒉1方法提要试样在950~±25℃的马弗炉中灼烧,驱除水分和二氧化碳,同时将存在的易氧化元素氧化。
由硫化物的氧化引起的烧失量误差必须进行校正,而其他元素存在引起的误差一般可忽略不计。
F⒉2分析步骤称取约1g试样(m1 ), 精确0.0001g,置于已灼烧恒量的瓷坩埚中,将盖斜置于坩埚上,放在马弗炉内从低温开始逐渐升高温度,在950~1000℃下灼烧15~20min,取出坩埚置于干燥器中冷却至室温,称量。
反复灼烧,直至恒量。
F⒉3结果表示F⒉⒊1烧失量的质量百分数LOI按式(F1)计算:m1 -m2LOI =————×100 ................(F1)m1式中: LOI—烧失量的质量百分数,%;m1—试料的质量,g;m2 —灼烧后试料的质量,g。
F⒉⒊2矿渣水泥在灼烧过程中由于硫化物的氧化引起烧失量测定的误差,可通过式(F2)、(F3) 进行校正:0.8×(水泥灼烧后测得的SO3百分数-水泥未经灼烧时的SO3百分数)=0.8×(由于硫化物的氧化产生的SO3百分数)=吸收空气中氧的百分数 .....(F2)校正后的烧失量(%)=测得的烧失量(%)+吸收空气中氧的百分数...........(F3)F⒉4允许差同一试验室的允许差为0.15%。
F3不溶物的测定(基准法)F⒊1方法提要试样先以盐酸溶液处理,滤出的不溶残渣再以氢氧化钠溶液处理,经盐酸中和、过滤后,残渣在高温下灼烧,称量。
F⒊2分析步骤称取约1g试样(m3 ),精确至0.0001g,置于150L烧杯中,加25mL 水,搅拌使其分散。
水泥生产化学分析操作规程
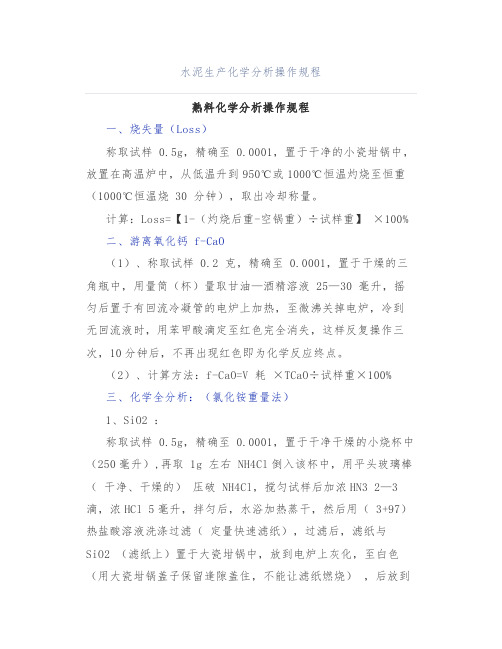
水泥生产化学分析操作规程熟料化学分析操作规程一、烧失量(Loss)称取试样 0.5g,精确至 0.0001,置于干净的小瓷坩锅中,放置在高温炉中,从低温升到950℃或1000℃恒温灼烧至恒重(1000℃恒温烧 30 分钟),取出冷却称量。
计算:Loss=【1-(灼烧后重-空锅重)÷试样重】×100%二、游离氧化钙 f-CaO(1)、称取试样 0.2 克,精确至 0.0001,置于干燥的三角瓶中,用量筒(杯)量取甘油—酒精溶液 25—30 毫升,摇匀后置于有回流冷凝管的电炉上加热,至微沸关掉电炉,冷到无回流液时,用苯甲酸滴定至红色完全消失,这样反复操作三次,10分钟后,不再出现红色即为化学反应终点。
(2)、计算方法:f-CaO=V 耗×TCaO÷试样重×100%三、化学全分析:(氯化铵重量法)1、SiO2 :称取试样 0.5g,精确至 0.0001,置于干净干燥的小烧杯中(250毫升),再取 1g 左右 NH4Cl倒入该杯中,用平头玻璃棒(干净、干燥的)压破 NH4Cl,搅匀试样后加浓HN3 2—3 滴,浓HCl 5毫升,拌匀后,水浴加热蒸干,然后用( 3+97)热盐酸溶液洗涤过滤(定量快速滤纸),过滤后,滤纸与SiO2 (滤纸上)置于大瓷坩锅中,放到电炉上灰化,至白色(用大瓷坩锅盖子保留逢隙盖住,不能让滤纸燃烧),后放到高温炉中 950℃或 1000℃灼烧至恒重,(灼烧半小时)取出冷却称重。
计算:SiO2 =(烧后重-空锅重)÷试样重×100%2、全分析:CaO、MgO、Fe2O3、Al2O3将过滤后的母液冷却后,用蒸馏水稀释至刻度线摇匀,移液管先用自来水洗涤2—3次,再用蒸馏水洗涤2—3次,然后用分析液洗涤2—3次。
(1)、CaO:吸取分析液 25 毫升,置于干净的大烧杯中,后用蒸馏水稀释至 200 毫升左右,拌匀后,先加(1+2)三乙醇胺 5 毫升,加钙指示剂少许,搅拌再加 20%KOH溶液,调至出现荧光黄后过量 7—9 毫升,拌匀后,用 EDTA 标液滴定,终点为亮红色。
水泥试验作业指导书

1目的规范和指导水泥的试验操作。
2适用范围本作业指导书适用于水泥的试验。
3工作内容3.1取样及试样处理3.1.1试样取样部位及方法应符合以下规定a)袋装水泥在袋装水泥堆场取样。
采用取样管,随机选择 20 个以上不同的部位,将取样管插入水泥适当深度,用大拇指按住气孔,小心抽出取样管。
将所取样品放入洁净、干燥、不易受污染的容器中。
b)散装水泥在散装水泥卸料处或输送水泥运输机具上取样。
当所取水泥深度不超过 2m 时,采用取样管,通过取样管内管控制开关,在适当位置插入水泥一定深度,关闭后小心抽出。
将所取样品放入洁净、干燥、不易受污染的容器中。
3.1.2试样数量:水泥按编号取样,每一编号为一取样单位。
(检验样和封存样)总量至少 12kg。
3.1.3样品制备样品缩分可采用二分器,一次或多次将样品缩分到标准要求的规定量。
水泥样要通过 0.9mm 方孔筛,均分为试验样和封存样。
样品应存放在密封的金属容器中,加封条。
容器应洁净、干燥、防潮、密闭、不易破损、不与水泥发生反应。
存放于干燥、通风的环境中。
3.2水泥细度检验操作方法3.2.1仪器设备3.2.1.1试验筛a)试验筛由圆形筛框和筛网组成,筛网符合 SSW0.080/0.056GB 6004 要求,负压筛应附有透明筛盖,筛盖与筛上口应有良好的密封性;b)筛网应紧绷在筛框上,筛网和筛框接触处,应用防水胶密封,防止水泥嵌入。
3.2.1.2负压筛析仪a)负压筛析仪由筛座、负压筛、负压源及收尘器组成,其中筛座由转速为30±2r/min 的喷气嘴、气压表、控制板、微电机及壳体等构成。
b)筛析仪负压可调范围为 4000~6000Pa。
c)负压源和收尘器,由功率 600W 的工业吸尘器和小型旋风收尘筒组成或用其他具有相当功能的设备。
3.2.1.3天平:最大称量为 100g,分度值不大于 0.05g。
3.2.2试验步骤a)试验前水泥样品应充分拌匀,通过 0.9mm 方孔筛,记录筛余物情况,要防止过筛时混进其他水泥;b)筛析试验前,应把负压筛放在筛座上,盖上筛盖,接通电源,检查控制系统,调节负压至 4000~6000Pa范围内;c)称取试样 25g 置于洁净的负压筛中,盖上筛盖,放在筛座上,开动筛析仪连续筛析 2min,在此期间如有试样附着在筛盖上,可轻轻地敲击,使试样落下。
水泥试验作业指导书

水泥试验作业指导书4.1水泥进场必须附有出厂证明书、并由物资部通知试验室取样复验。
4.2 当对水泥质量有怀疑或水泥出厂日期逾3个月时应取样试验,满足GB175有关规定方可使用。
4.3 水泥其他技术要求采用品质稳定、强度等级不低于42.5级的低碱硅酸盐水泥或低碱普通硅酸盐水泥,禁止使用其它品种水泥。
水泥其技术要求符合铁道部铁建设【2009】152号文发布的《铁路混凝土工程施工质量验收补充标准》、GB/T18046-2008及GB175—2007标准之规定,水泥中的碱含量按Na20+0.65K20计算值来表示且不得大于0.6%。
4.4 水泥分批与检验试样的采取:4.4.1 水泥进场时,必须附有水泥生产厂家的质量证明书。
由物资部对进场水泥核查生产厂名、品种、强度等级、包装、重量、出厂日期、出厂编号及是否受潮等,并作好记录。
4.4.2 同一水泥厂生产的同期出厂的同品种、同强度等级、同一出厂编号的水泥为一批。
按进场批号、车号对进场的每批水泥均须进行取样检验。
散装水泥每批总量不得超过500t,袋装水泥每批总量不超过200t。
4.4.3 水泥的取样由物设部负责,检验由试验室负责。
4.4.4 对每批散装水泥,随机地从20个以上不同部位取等量水泥,经混拌均匀后,再从中称取不少于12Kg水泥作为试验样品。
4.4.5 对已进场的每批水泥,视在场存放,一般对每一品种、标号、编号的水泥罐存放超过三个月,须取样进行复验,复验合格后方可使用。
4.5 水泥的每批常规检验项目为:胶砂强度、凝结时间、安定性、细度。
对于任何新选货源,或使用同厂家、同批号、同品种的产品达3个月的产品还必须检验以下6个项目:比表面积、烧失量、游离CaO 含量、安定性、含水量。
试验方法按GB175之规定执行。
4.6 进场入库记录、试验记录与检验报告进场入库记录、试验记录与检验报告应包括下列内容:A、被检水泥的品种、标号、包装及生产厂家;B、被检水泥的编号、进场日期及储放情况;C、水泥检验试验的采取日期、采样地点及采取方法;D、水泥的检验项目;E、试验记录应记下全部原始试验数据、试验条件的控制及检验中的异常情况,必要时应在检验报告中注明;F、试验的结果;G、试验日期、试验人员。
水泥烧失量的测定作业指导书
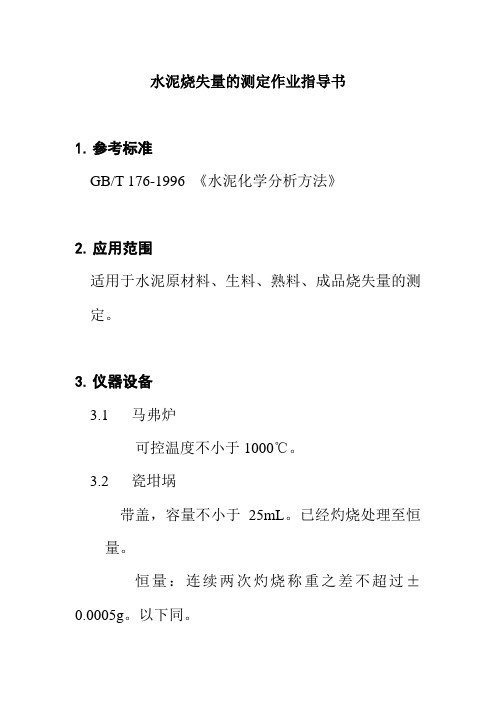
水泥烧失量的测定作业指导书1.参考标准GB/T 176-1996 《水泥化学分析方法》2.应用范围适用于水泥原材料、生料、熟料、成品烧失量的测定。
3.仪器设备3.1 马弗炉可控温度不小于1000℃。
3.2 瓷坩埚带盖,容量不小于25mL。
已经灼烧处理至恒量。
恒量:连续两次灼烧称重之差不超过±0.0005g。
以下同。
3.3 干燥器硫酸干燥器或真空干燥器。
3.4 分析天平分度值0.0001g ,量程不小于100g 。
3.5 药匙4. 烧失量的测定4.1 准确称取约1g 试样,放入已灼烧恒重的瓷坩埚中,将坩埚盖上并留有一缝隙。
放入马弗炉内,由低温升起至所需温度,并保持15~20分钟,取出坩埚,置于干燥器中冷却至室温称量,如此反复灼烧,直至恒重。
100121⨯-=m m m 烧失量% 式中:m 1——试样的质量,g ;m 2——灼烧后剩余物的质量,g 。
5. 注意事项5.1灼烧温度,除特殊规定外(石膏800~850℃),一般均为950~1000℃。
5.2灼烧后一些试样吸水性增强,如粘土,石灰石等,所以称量时必须尽可能迅速。
5.3为了正确反应灼烧基化学组分,烧失量试样和进行全分析试样应同时称取。
5.4矿渣(矿渣水泥)试样,硫化物含量高时会被空气氧化生成硫酸盐而导致质量增加,烧失量测定结果会出现负值,须校正烧失量。
计算公式如下:校正后的烧失量(%)=测得的烧失量(%)+吸收空气中氧的百分数吸收空气中氧的百分数为(%)=0.8×(试料灼烧后测得的SO3质量百分数-试料未经灼烧时的SO3质量百分数)。
烧失量的测定检验规程
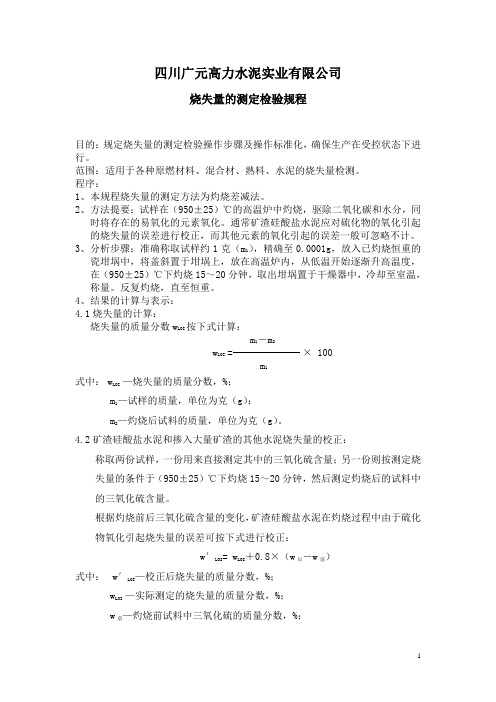
四川广元高力水泥实业有限公司烧失量的测定检验规程目的:规定烧失量的测定检验操作步骤及操作标准化,确保生产在受控状态下进行。
范围:适用于各种原燃材料、混合材、熟料、水泥的烧失量检测。
程序:1、本规程烧失量的测定方法为灼烧差减法。
2、方法提要:试样在(950±25)℃的高温炉中灼烧,驱除二氧化碳和水分,同时将存在的易氧化的元素氧化。
通常矿渣硅酸盐水泥应对硫化物的氧化引起的烧失量的误差进行校正,而其他元素的氧化引起的误差一般可忽略不计。
3、分析步骤:准确称取试样约1克(m1),精确至0.0001g,放入已灼烧恒重的瓷坩埚中,将盖斜置于坩埚上,放在高温炉内,从低温开始逐渐升高温度,在(950±25)℃下灼烧15~20分钟,取出坩埚置于干燥器中,冷却至室温,称量。
反复灼烧,直至恒重。
4、结果的计算与表示:4.1烧失量的计算:烧失量的质量分数wLOI按下式计算:m1-m2wLOI= × 100m1式中:wLOI—烧失量的质量分数,%;m1—试样的质量,单位为克(g);m2—灼烧后试料的质量,单位为克(g)。
4.2矿渣硅酸盐水泥和掺入大量矿渣的其他水泥烧失量的校正:称取两份试样,一份用来直接测定其中的三氧化硫含量;另一份则按测定烧失量的条件于(950±25)℃下灼烧15~20分钟,然后测定灼烧后的试料中的三氧化硫含量。
根据灼烧前后三氧化硫含量的变化,矿渣硅酸盐水泥在灼烧过程中由于硫化物氧化引起烧失量的误差可按下式进行校正:w′LOI = wLOI+0.8×(w后-w前)式中:w′LOI—校正后烧失量的质量分数,%;wLOI—实际测定的烧失量的质量分数,%;w前—灼烧前试料中三氧化硫的质量分数,%;w后—灼烧后试料中三氧化硫的质量分数,%;0.8—S2-氧化为SO42-时增加的氧与SO3的摩尔质量比,即(4×16)/80=0.8。
5、允许差:同一实验室的允许差为±0.15%。
- 1、下载文档前请自行甄别文档内容的完整性,平台不提供额外的编辑、内容补充、找答案等附加服务。
- 2、"仅部分预览"的文档,不可在线预览部分如存在完整性等问题,可反馈申请退款(可完整预览的文档不适用该条件!)。
- 3、如文档侵犯您的权益,请联系客服反馈,我们会尽快为您处理(人工客服工作时间:9:00-18:30)。
水泥烧失量试验作业指导书
1.依据标准:<<水泥化学分析方法>> GB/T176-1996;
2.试验目的及适用范围:
2.1目的:规定烧失量的测定检查操作步骤及操作标准化,确保生产在授椌状态下进行。
2.2 适用范围:于水泥原材料,生料,孰料,成品烧失量的测定。
3.试验环境︰高温炉周围不得堆放易燃易爆的物品。
4.试验准备:
4.1仪器设备︰○1瓷坩埚带盖,容量不小于25ml○2高温炉○3干燥器○4分析天平,分度值0.0001g。
4.2试样制备:称取满足试验要求的水泥试样,烘干至恒重。
5.试验步骤:具体试验依据GB/T176-1996《水泥化学分析方法》进行试验。
6.试验结果整理:
6.1烧失量的质量百分数W LO1按下式计算︰
W LO1=(m1-m2)/m1×100
式中:W LO1—烧失量的质量百分数,%
m1—试料的质量(g)
m2—灼烧后试料的质量(g)
7.试验注意事项:
7.1灼烧温度,除特殊规定外,一般均为9500~C~10000C。
7.2矿渣硅酸盐水泥和掺入大量矿渣的其他水泥烧失量要进行校正。
7.3灼烧后一些试样吸水性增强,如粘土,石灰等所以称量时尽可能迅速。
7.4为了正确反应灼烧的化学组分,烧失量试样和进行全分析试样应同时称取。