金相侵蚀液电解抛光液
金相试样电解抛光、腐蚀规程

金相试样电解抛光、腐蚀规程本标准规定了金属试样电解抛光、腐蚀操作的试验规范。
本标准适用于金属试验中金相试样的制备。
1.主要技术参数见设备(EP—6型电解抛光腐蚀仪)的操作说明书2.操作步骤见设备的操作说明书,抛光工艺可参考附表中的电解抛光、腐蚀参考资料3.安全规程3.1 使用含高氯酸电解液时,必须通循环水冷却,配制温度低于15C,使用温度应低于200C注意安全,防止燃烧和爆炸。
3.2 使用电压超过60V时,要注意安全,应先放好试样,再调电压到所需值,后进行电解抛光,结束后将电压调到零位再取试样。
3.3 当电源接通后,直流档无论有无负载,要严防短路,尤其使用外电解浸蚀时更应注意。
3.4 接通负载后(即抛光或腐蚀进行时),严禁转换电压调整器。
每次抛光后,应关闭电源防止过热。
3.5 抛光结束后,将电解液倒入其它容器中,用水清洗电解槽及冷却循环系统。
4.下列情况不适用本方法4.1 不能用塑料镶嵌试样,因为塑料不导电容易被电解液浸蚀。
4.2 极易受电解液浸蚀的金属相和一些夹杂物不能采用电解抛光。
4.3 需要边、角的试样,不适宜进行电解抛光。
附表1 电解抛光参考资料试验材料电解液配比电压时间备注不锈钢1Cr—18Ni9Ti 酒精(95%)940ml高氯酸(65%)60ml30~40V 15~60秒不锈钢、合金钢、高速钢等酒精(95%)700ml;高氯酸(30%)200ml;甘油(丙三醇)100ml15~50V 15~60秒通用电解液之一钢、铸铁、铝、铝合金等酒精(95%)700ml;高氯酸(30%)200ml;丁氧基乙醇100ml30~65V 15~60秒最好的通用配方之一不锈钢、碳钢铁、合金钢等醋酸(冰醋酸)900ml高氯酸(60%)100ml12~70V 0.5~2分铀、锆、钛、铝合金钢、碳钢醋酸(冰醋酸)800ml高氯酸(60%)200ml40~100V 1~15分不锈钢水250ml硫酸750ml1.5~6V 1~2分不锈钢磷酸(85%)600ml硫酸400ml1.5~12V 10~60秒不锈钢水80ml硫酸720ml甘油200ml1.5~6V 0.5~5分不锈钢和合金钢水:240ml,硫酸:340ml磷酸(85%):650ml1.5~12V 2~10分0.1~0.2A/cm2不锈钢水:330ml,硫酸120ml磷酸(85%):550ml1.5~12v 1分0.05A/ cm2不锈钢和合金钢水:240ml,磷酸:(85%):650ml铬酸80% 硫酸130ml1.5~12V 5~60分0.5A/cm2100~130。
金相抛光的常用方法
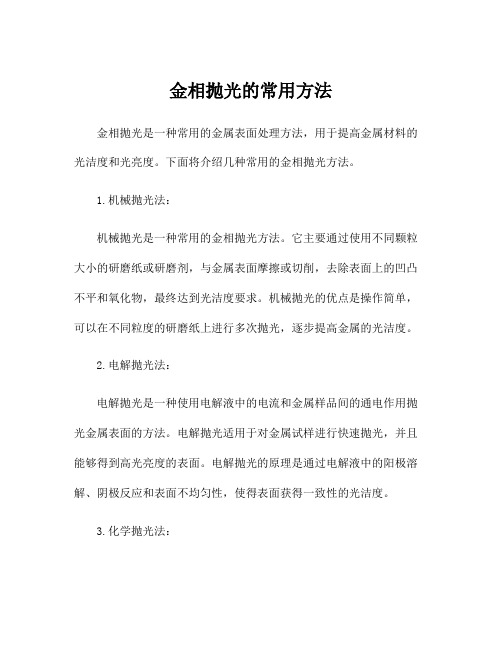
金相抛光的常用方法金相抛光是一种常用的金属表面处理方法,用于提高金属材料的光洁度和光亮度。
下面将介绍几种常用的金相抛光方法。
1.机械抛光法:机械抛光是一种常用的金相抛光方法。
它主要通过使用不同颗粒大小的研磨纸或研磨剂,与金属表面摩擦或切削,去除表面上的凹凸不平和氧化物,最终达到光洁度要求。
机械抛光的优点是操作简单,可以在不同粒度的研磨纸上进行多次抛光,逐步提高金属的光洁度。
2.电解抛光法:电解抛光是一种使用电解液中的电流和金属样品间的通电作用抛光金属表面的方法。
电解抛光适用于对金属试样进行快速抛光,并且能够得到高光亮度的表面。
电解抛光的原理是通过电解液中的阳极溶解、阴极反应和表面不均匀性,使得表面获得一致性的光洁度。
3.化学抛光法:化学抛光是利用化学试剂在金属表面发生化学反应,去除表面的氧化膜和污染物,达到光洁度要求的方法。
常用的化学抛光方法有酸洗和碱洗。
酸洗抛光可以去除金属表面的氧化膜和杂质,碱洗抛光可以去除有机物和脏污。
化学抛光的优点是能够在短时间内获得高质量的平坦和光洁表面。
4.溶剂抛光法:溶剂抛光是一种利用有机溶剂和湿抛法来提高金属表面质量的方法。
溶剂抛光适用于一些脆性和敏感的金属材料,可以避免机械抛光或化学抛光过程中可能引起的变形或污染问题。
溶剂抛光的步骤包括:清洗金属表面、去除残留的溶剂和颗粒、用纯溶剂溶解有机污染物以及润湿剂的涂覆。
5.磁力抛光法:磁力抛光是利用磁力场和磁性研磨颗粒来平整和抛光金属表面的方法。
磁力抛光适用于对大批量金属试样进行抛光,并且能够获得一致性的表面质量。
磁力抛光的原理是通过磁力场的作用,使磁性研磨颗粒在金属表面滚动或磨削,去除表面的杂质和凹凸不平,最终得到光滑的表面。
以上是金相抛光的常用方法,每种方法都有自己的特点和适用范围。
在实际应用中,可以根据具体的金属材料和表面要求选择合适的抛光方法,以达到最佳的抛光效果。
金相试样电解抛光腐蚀规程

金相试样电解抛光腐蚀
规程
Coca-cola standardization office【ZZ5AB-ZZSYT-ZZ2C-ZZ682T-ZZT18】
金相试样电解抛光、腐蚀规程
本标准规定了金属试样电解抛光、腐蚀操作的试验规范。
本标准适用于金属试验中金相试样的制备。
1.主要技术参数
见设备(EP—6型电解抛光腐蚀仪)的操作说明书
2.操作步骤
见设备的操作说明书,抛光工艺可参考附表中的电解抛光、腐蚀参考资料3.安全规程
使用含高氯酸电解液时,必须通循环水冷却,配制温度低于15C,使用温度应低于200C注意安全,防止燃烧和爆炸。
使用电压超过60V时,要注意安全,应先放好试样,再调电压到所需值,后进行电解抛光,结束后将电压调到零位再取试样。
当电源接通后,直流档无论有无负载,要严防短路,尤其使用外电解浸蚀时更应注意。
接通负载后(即抛光或腐蚀进行时),严禁转换电压调整器。
每次抛光后,应关闭电源防止过热。
抛光结束后,将电解液倒入其它容器中,用水清洗电解槽及冷却循环系统。
4.下列情况不适用本方法
不能用塑料镶嵌试样,因为塑料不导电容易被电解液浸蚀。
极易受电解液浸蚀的金属相和一些夹杂物不能采用电解抛光。
需要边、角的试样,不适宜进行电解抛光。
附表1 电解抛光参考资料
附表2 电解浸蚀参考资料
附表3 显示钢的显微组织的电解浸蚀剂及电解抛光液表
附表4 贵金属及其合金电解浸蚀剂和电解抛光液表。
电解抛光溶液

电解抛光溶液电解抛光溶液是一种常用的表面处理方法,其通过电解作用将金属表面上的杂质和氧化物去除,从而实现表面光洁度的提高。
本文将从电解抛光溶液的成分、工作原理、应用领域等方面进行介绍。
电解抛光溶液通常由电解液和添加剂组成。
电解液是溶解金属离子的介质,常用的电解液有硫酸、硝酸、磷酸等。
添加剂则可以调节电解液的性质,如提高电导率、调节pH值、改善溶液中的气泡等。
不同金属材料需要使用不同的电解抛光溶液。
电解抛光溶液的工作原理是利用电解作用将金属表面上的氧化物还原成金属离子,并利用电流将金属离子转移至阴极,从而实现对金属表面的抛光。
在电解抛光过程中,阴极通常采用不锈钢材料,而阳极则是要进行抛光的金属材料。
通过调节电解液的成分和工艺参数,可以控制电解抛光的速度和效果。
电解抛光溶液在许多领域都有广泛的应用。
首先,电解抛光可以提高金属表面的光洁度和平整度,使其更具观赏性。
这在珠宝、钟表、汽车等行业中非常重要。
其次,电解抛光还可以去除金属表面的氧化物和腐蚀物,提高材料的耐腐蚀性能。
这在航空航天、化工设备等领域中具有重要意义。
此外,电解抛光还可以改善金属材料的导电性能和润滑性能,提高其使用寿命。
然而,电解抛光溶液也存在一些问题。
首先,电解抛光过程中会产生大量的废液和废气,对环境造成一定的污染。
其次,电解抛光的工艺参数需要精确控制,否则容易导致金属表面的不均匀抛光。
此外,一些金属材料可能会在电解抛光过程中发生腐蚀或变色等问题。
为了解决这些问题,研究人员不断改进和优化电解抛光溶液的配方和工艺。
例如,可以采用新型的电解液和添加剂,提高抛光效果和工艺稳定性。
此外,还可以引入先进的电解抛光设备和自动控制系统,提高生产效率和产品质量。
电解抛光溶液是一种重要的金属表面处理方法,广泛应用于各个领域。
通过合理选择电解液、优化工艺参数和引入先进设备,可以实现对金属材料表面的高效抛光,提高产品质量和附加值。
然而,电解抛光过程中也存在一些问题,需要进一步研究和改进。
在不锈钢金相检验过程中电解制样的应用及分析

在不锈钢金相检验过程中电解制样的应用及分析在目前的金相检验工作中,我们常会使用两种方法,分别是电解法以及機械制样。
对于前者来讲,它是把电流通到电解质里面,经由反应进而对金属本身的构造有详细的了解。
这个措施和机械措施比对来讲,能够防止抛光过程中形成杂质,而且它的速率非常快,所需的时间较少,节省资源,能够明显的提升效率,在实际的工作中其获取的成就非常显著,因此得到非常广泛的应用。
文章具体的分析了这种措施的特征等内容。
标签:不锈钢金相检验;电解制样;应用分析引言所谓的金相,指的是金属自身的物化模式,能够体现其实际形态的我们称之为金相组织。
目前常用的措施有两类,分别是电解法以及机械制样。
对于前者来讲,它是把电流通道电解质里面,经由反应进而对金属本身的构造有详细的了解。
这个措施和机械措施比对来讲,能够防止在抛光过程中形成杂质,而且它的速率非常快,所需的时间较少,节省资源,能够明显的提升效率,在实际的工作中获取的成就非常显著,因此得到非常广泛的应用。
1 金相技术及制备要想得知金属的性能,首先就要分析它的构造和成分。
我们通常将其内部的构造称之为金相。
进项测试工作主要是通过分析金属的特性,完善部件的制作工艺,进而得知部件存在问题的缘由。
该项检测活动不论是对金属领域来讲,亦或是其制品行业来讲都有着非常明显的意义。
在具体检验的时候,必须要认真按照相关的标准来开展,假如试样出现问题的话,就会导致结论不正确,所以必须高度关注试样制备工作。
接下来作者以电解方法为例具体的阐述试样工作。
2 电解制样试验试验材料主要有A(马氏体不锈钢)、B(铁素体不锈钢)、C(奥氏体不锈钢)三种不锈钢材料。
分别切割上述材料,得到很多的小块样本,使用专门的砂纸处理表面。
该测试活动使用的电解措施,使用的机械是具有抛光以及腐蚀等多项功效的抛光仪,而电解液的驱动用到的是电磁泵。
对于电解数值来讲,要确保其合乎如下的规定:工作电压在150V以内,输入电压为220V;正常使用的电流在0-6A,输出的直流电流在0-10A之间;电磁泵的转速保持在0-750r/min,可以进行适当的调整,磁泵的两极磁感应的强度在0.08T以上;电磁泵的驱动电机功率通常为30W,电压为12V;实际抛光的时候,要控制好面积,通常控制在5cm2之内,时间在1-999s内,具体工作时要结合具体情况来分析。
金相试样的制备.
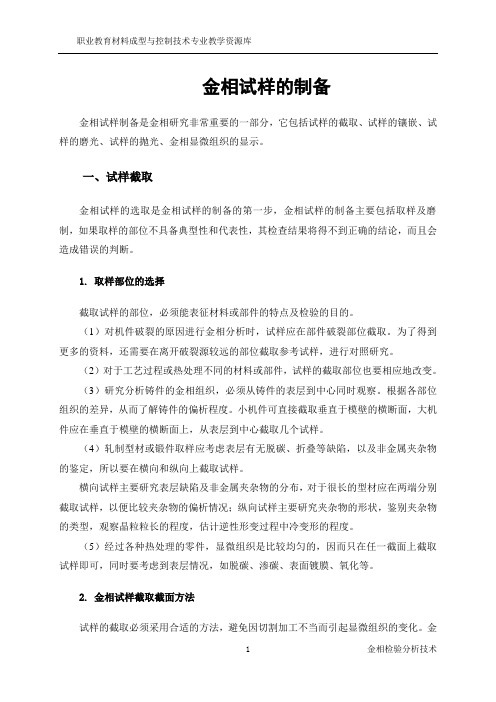
金相试样的制备金相试样制备是金相研究非常重要的一部分,它包括试样的截取、试样的镶嵌、试样的磨光、试样的抛光、金相显微组织的显示。
一、试样截取金相试样的选取是金相试样的制备的第一步,金相试样的制备主要包括取样及磨制,如果取样的部位不具备典型性和代表性,其检查结果将得不到正确的结论,而且会造成错误的判断。
1. 取样部位的选择截取试样的部位,必须能表征材料或部件的特点及检验的目的。
(1)对机件破裂的原因进行金相分析时,试样应在部件破裂部位截取。
为了得到更多的资料,还需要在离开破裂源较远的部位截取参考试样,进行对照研究。
(2)对于工艺过程或热处理不同的材料或部件,试样的截取部位也要相应地改变。
(3)研究分析铸件的金相组织,必须从铸件的表层到中心同时观察。
根据各部位组织的差异,从而了解铸件的偏析程度。
小机件可直接截取垂直于模壁的横断面,大机件应在垂直于模壁的横断面上,从表层到中心截取几个试样。
(4)轧制型材或锻件取样应考虑表层有无脱碳、折叠等缺陷,以及非金属夹杂物的鉴定,所以要在横向和纵向上截取试样。
横向试样主要研究表层缺陷及非金属夹杂物的分布,对于很长的型材应在两端分别截取试样,以便比较夹杂物的偏析情况;纵向试样主要研究夹杂物的形状,鉴别夹杂物的类型,观察晶粒粒长的程度,估计逆性形变过程中冷变形的程度。
(5)经过各种热处理的零件,显微组织是比较均匀的,因而只在任一截面上截取试样即可,同时要考虑到表层情况,如脱碳、渗碳、表面镀膜、氧化等。
2. 金相试样截取截面方法试样的截取必须采用合适的方法,避免因切割加工不当而引起显微组织的变化。
金相试样的选取分为:(1)纵向取样;纵向取样是指沿着钢材的锻轧方向进行取样。
主要检验内容为:非金属夹杂物的变形程度、晶粒畸变程度、塑性变形程度、变形后的各种组织形貌、热处理的全面情况等。
(2)横向取样;横向取样是只垂直于钢材锻扎方向取样。
主要检验内容为:金属材料从表层到中心的组织、显微组织状态、晶粒度级别、碳化物网、表层缺陷深度、氧化层深度、脱碳层深度、腐蚀层深度、表面化学热处理及镀层厚度等。
金相抛光剂
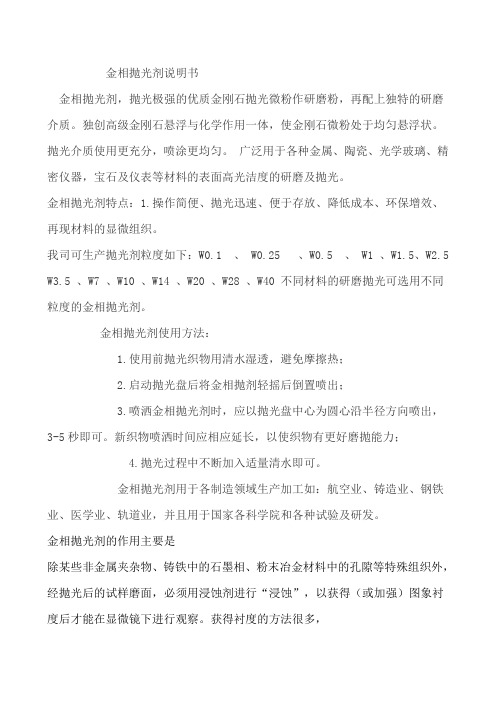
金相抛光剂说明书金相抛光剂,抛光极强的优质金刚石抛光微粉作研磨粉,再配上独特的研磨介质。
独创高级金刚石悬浮与化学作用一体,使金刚石微粉处于均匀悬浮状。
抛光介质使用更充分,喷涂更均匀。
广泛用于各种金属、陶瓷、光学玻璃、精密仪器,宝石及仪表等材料的表面高光洁度的研磨及抛光。
金相抛光剂特点:1.操作简便、抛光迅速、便于存放、降低成本、环保增效、再现材料的显微组织。
我司可生产抛光剂粒度如下:W0.1 、 W0.25 、W0.5 、 W1 、W1.5、W2.5 W3.5 、W7 、W10 、W14 、W20 、W28 、W40 不同材料的研磨抛光可选用不同粒度的金相抛光剂。
金相抛光剂使用方法:1.使用前抛光织物用清水湿透,避免摩擦热;2.启动抛光盘后将金相抛剂轻摇后倒置喷出;3.喷洒金相抛光剂时,应以抛光盘中心为圆心沿半径方向喷出,3-5秒即可。
新织物喷洒时间应相应延长,以使织物有更好磨抛能力;4.抛光过程中不断加入适量清水即可。
金相抛光剂用于各制造领域生产加工如:航空业、铸造业、钢铁业、医学业、轨道业,并且用于国家各科学院和各种试验及研发。
金相抛光剂的作用主要是除某些非金属夹杂物、铸铁中的石墨相、粉末冶金材料中的孔隙等特殊组织外,经抛光后的试样磨面,必须用浸蚀剂进行“浸蚀”,以获得(或加强)图象衬度后才能在显微镜下进行观察。
获得衬度的方法很多,据获得衬度过程是否改变试样表面,可分为不改变表面方法,如光学法,和改变试样表面方法,如电化学浸蚀法、物理浸蚀法两大类。
最常用的浸蚀方法是化学浸蚀法。
纯金属或单相金属的浸蚀是一个化学溶解过程。
晶界处由于原子排列混乱,能量较高,所以易受浸蚀而呈现凹沟。
各个晶粒由于原子排列位向不同,受浸蚀程度也不同。
因此,在垂直光线照射下,各部位反射进入物镜的光线不同,从而显示出晶界及明暗不同的晶粒。
两相或两相以上合金的浸蚀则是一个电化学腐蚀过程。
由于各相的组织成分不同,其电极电位亦不同,当表面覆盖一层具有电解质作用的浸蚀剂时,两相之间就形成许多“微电池”。
金相检测常用腐蚀液
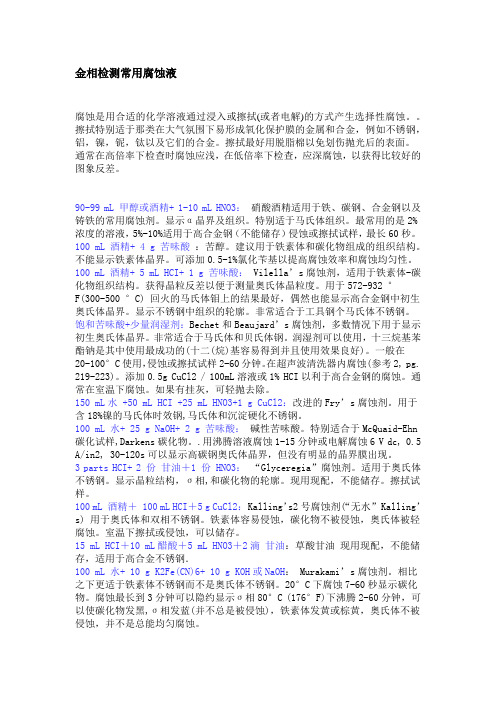
金相检测常用腐蚀液腐蚀是用合适的化学溶液通过浸入或擦拭(或者电解)的方式产生选择性腐蚀。
擦拭特别适于那类在大气氛围下易形成氧化保护膜的金属和合金,例如不锈钢,铝,镍,铌,钛以及它们的合金。
擦拭最好用脱脂棉以免划伤抛光后的表面。
通常在高倍率下检查时腐蚀应浅,在低倍率下检查,应深腐蚀,以获得比较好的图象反差。
90-99 mL 甲醇或酒精+ 1-10 mL HNO3:硝酸酒精适用于铁、碳钢、合金钢以及铸铁的常用腐蚀剂。
显示α晶界及组织。
特别适于马氏体组织。
最常用的是2%浓度的溶液,5%-10%适用于高合金钢(不能储存)侵蚀或擦拭试样,最长60秒。
100 mL 酒精+ 4 g 苦味酸:苦醇。
建议用于铁素体和碳化物组成的组织结构。
不能显示铁素体晶界。
可添加0.5-1%氯化苄基以提高腐蚀效率和腐蚀均匀性。
100 mL 酒精+ 5 mL HCI+ 1 g 苦味酸:Vilella’s腐蚀剂,适用于铁素体-碳化物组织结构。
获得晶粒反差以便于测量奥氏体晶粒度。
用于572-932 °F(300-500 °C) 回火的马氏体钼上的结果最好,偶然也能显示高合金钢中初生奥氏体晶界。
显示不锈钢中组织的轮廓。
非常适合于工具钢个马氏体不锈钢。
饱和苦味酸+少量润湿剂:Bechet和Beaujard’s腐蚀剂,多数情况下用于显示初生奥氏体晶界。
非常适合于马氏体和贝氏体钢。
润湿剂可以使用,十三烷基苯酯钠是其中使用最成功的(十二(烷)基容易得到并且使用效果良好)。
一般在20-100°C使用,侵蚀或擦拭试样2-60分钟。
在超声波清洗器内腐蚀(参考2, pg. 219-223)。
添加0.5g CuCl2 / 100mL溶液或1% HCI以利于高合金钢的腐蚀。
通常在室温下腐蚀。
如果有挂灰,可轻抛去除。
150 mL水 +50 mL HCI +25 mL HNO3+1 g CuCl2:改进的Fry’s腐蚀剂。
用于含18%镍的马氏体时效钢,马氏体和沉淀硬化不锈钢。
金相分析之六——试样的电解抛光及电解浸蚀
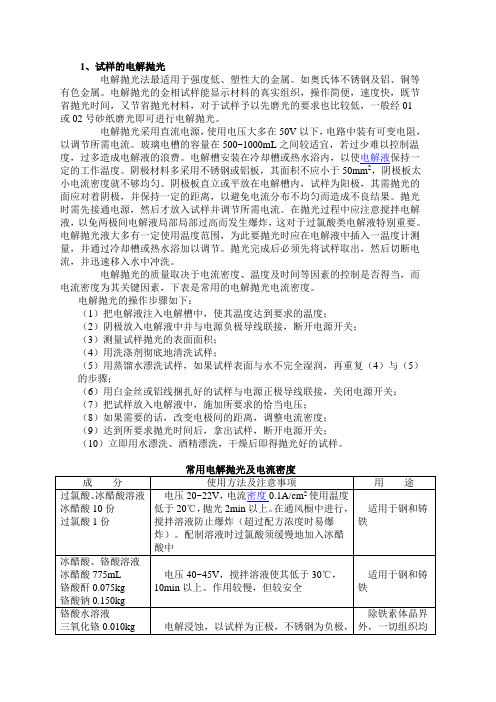
1、试样的电解抛光电解抛光法最适用于强度低、塑性大的金属。
如奥氏体不锈钢及铝、铜等有色金属。
电解抛光的金相试样能显示材料的真实组织,操作简便,速度快,既节省抛光时间,又节省抛光材料,对于试样予以先磨光的要求也比较低,一般经01或02号砂纸磨光即可进行电解抛光。
电解抛光采用直流电源,使用电压大多在50V以下,电路中装有可变电阻,以调节所需电流。
玻璃电槽的容量在500~1000mL之间较适宜,若过少难以控制温度,过多造成电解液的浪费。
电解槽安装在冷却槽或热水浴内,以使电解液保持一定的工作温度。
阴极材料多采用不锈钢或铝板,其面积不应小于50mm2,阴极板太小电流密度就不够均匀。
阴极板直立或平放在电解槽内,试样为阳极,其需抛光的面应对着阴极,并保持一定的距离,以避免电流分布不均匀而造成不良结果。
抛光时需先接通电源,然后才放入试样并调节所需电流。
在抛光过程中应注意搅拌电解液,以免两极间电解液局部局部过高而发生爆炸,这对于过氯酸类电解液特别重要。
电解抛光液大多有一定使用温度范围,为此要抛光时应在电解液中插入一温度计测量,并通过冷却槽或热水浴加以调节。
抛光完成后必须先将试样取出,然后切断电流,并迅速移入水中冲洗。
电解抛光的质量取决于电流密度、温度及时间等因素的控制是否得当,而电流密度为其关键因素,下表是常用的电解抛光电流密度。
电解抛光的操作步骤如下:(1)把电解液注入电解槽中,使其温度达到要求的温度;(2)阴极放入电解液中并与电源负极导线联接,断开电源开关;(3)测量试样抛光的表面面积;(4)用洗涤剂彻底地清洗试样;(5)用蒸馏水漂洗试样,如果试样表面与水不完全湿润,再重复(4)与(5)的步骤;(6)用白金丝或铝线捆扎好的试样与电源正极导线联接,关闭电源开关;(7)把试样放入电解液中,施加所要求的恰当电压;(8)如果需要的话,改变电极间的距离,调整电流密度;(9)达到所要求抛光时间后,拿出试样,断开电源开关;(10)立即用水漂洗、酒精漂洗,干燥后即得抛光好的试样。
金相化学浸蚀与电解浸蚀原理

金相化学浸蚀与电解浸蚀原理金相试样经过抛光后,具有光亮无痕的磨面。
在显微镜下观察,看到的也仅是光亮的一片,个别视场中也可能存在一些磨痕、凹坑、水渍等,这些缺陷越少,说明制样的质量越高。
经抛光后的试样,可以进行钢中非金属夹杂物的检查,各种夹杂物有它的特定形状及颜色,如塑性夹杂物在显微镜下为浅绿色条带状;铸铁中灰色的片状或球状石墨,也都能在抛光后的磨面上显示出来。
在某些合金中,由于各相组成物的硬度差别较大,或由于各相本身色泽显著不同,在上海光密仪器厂6XCP倒置金相显微镜下能分辨出它的组织。
如铅青铜组织中,暗黑色的铅点与亮黄色的铜在色泽上有很大差别,未经浸蚀就能清楚的看出来。
但除了上述情况以外,大部分的显微组织均需经过不同方法的浸蚀,才能显示出各种组织来,常用的金属组织浸蚀法有化学浸蚀及电解浸蚀法等。
一、化学浸蚀法1.化学浸蚀的原理此法是利用化学试剂的溶液,借助于化学或电化学作用显示金属的组织。
纯金属及单相合金的浸蚀纯粹是一个化学溶解过程,磨面表层的原子被溶入浸蚀剂中,在溶解过程中由于晶粒与晶粒之间溶解度的不同,组织就被显示出来。
浸蚀剂首先把磨面表层的非晶形层溶去,接着就对晶界起化学溶解的作用,因为晶界上原子排列的规律性较差,并具有较高的自由能,所以晶界处较易浸蚀而呈凹沟状,在上海光密仪器厂产的6X CP倒置金相显微镜下显示纯金属或固溶体的多面体晶粒。
化学浸蚀用的浸蚀剂,随合金性能而不同,有的合金易被浸蚀,只需用稀酸作为浸蚀剂即可,如碳素钢只需用4%硝酸酒精浸蚀;而某些合金却极难浸蚀,需要用极强的酸和碱才能浸蚀。
二相合金的浸蚀与单相合金的浸蚀原理不同,它主要是电化腐蚀过程。
合金中的两个组成相具有不同的电位,当磨面浸入浸蚀剂中便形成许多对微小的局部电池,具有较高负电位的一相成为局部电池的阳极,被很快地溶入浸蚀剂中,因而该相逐渐呈现凹沟。
常用的金相腐蚀剂

50
奥氏体不锈钢
硝酸5
氢氟酸1
水44
在通风条件下浸蚀5分钟
51
奥氏体不锈钢
盐酸25
10%铬酸水溶液50
室温浸蚀速度快.均匀.效果好.
52
马氏体不锈钢
三氯化铁5g
盐酸25
乙醇25
室温浸蚀
53
马氏体不锈钢
氯化铜1.5g
盐酸33
乙醇33
水33
室温浸蚀
试剂马氏体变暗铁素体着色奥氏体不受浸蚀
54
沉淀硬化不锈钢
盐酸3
硝酸1.5
苦味酸3g
乙醇95
室温浸蚀
40
显示高强度钢中的马氏体和铁素体
1%焦亚硫酸钠水溶液1份4%苦味酸乙醇1份
室温浸蚀
马氏体-白色贝氏体-黑色铁素体-黄褐色
41
显示低合金钢中板条马氏体与贝氏体的区别
1# 2#
a: 1份1.2份
b: 1.5份1份
1# 4%苦味酸乙醇
2# 1%焦亚硫酸钠水溶液
先浸入(a)中20s,
三氯化铁1g
盐酸2
乙醇100
室温浸蚀浸蚀1-5秒
27
双相不锈钢
30g
K3()6 30g
H2O 100
82~89℃时间2~6
28
碳钢合金钢
硝酸1-10
乙醇90-99
硝酸加入量按材料选择,常用34%溶液,1%溶液适用于碳钢中温回火组织及共渗黑色组织
最常用浸蚀剂。但热处理组织不如苦味酸溶液的分辩能力强
29
19
显示极细珠光体
戊醇100
苦味酸5g
通风柜内操作不能存放
20
显示淬火马氏体与铁素体的反差
一种镍基合金金相组织的电解抛光腐蚀剂及其使用方法[发明专利]
![一种镍基合金金相组织的电解抛光腐蚀剂及其使用方法[发明专利]](https://img.taocdn.com/s3/m/5ffa55050a4c2e3f5727a5e9856a561253d32148.png)
(19)中华人民共和国国家知识产权局(12)发明专利申请(10)申请公布号 (43)申请公布日 (21)申请号 201611160397.6(22)申请日 2016.12.15(71)申请人 上海电气核电设备有限公司地址 201306 上海市浦东新区临港重型产业装备区层林路77号(72)发明人 顾佳磊 纵海 陆连萍 宣文 (74)专利代理机构 上海信好专利代理事务所(普通合伙) 31249代理人 朱成之(51)Int.Cl.C25F 3/22(2006.01)G01N 1/32(2006.01)(54)发明名称一种镍基合金金相组织的电解抛光腐蚀剂及其使用方法(57)摘要本发明公开了一种镍基合金金相组织的电解抛光腐蚀剂及其使用方法,该抛光腐蚀剂包含以下以体积份数计的原料:硫酸30~40份,磷酸120~150份,去离子水30~40份,硝酸 5~10份,甘油50~80份。
该电解腐蚀剂的使用方法为:以所述的电解抛光腐蚀剂作为电解液,以经由粗到细的不同规格的水磨砂纸依次打磨后的待腐蚀镍基耐蚀合金样品作为阳极,不锈钢材料为阴极,再经两次不同电流密度电解抛光,使得镍基耐蚀合金样品的金相组织清晰显示出来。
本发明的电解腐蚀剂配方简单,大大降低了对实验人员的健康损害;不易挥发,可长期保存并能重复使用;使用不同的电流强度可以达到抛光和显现组织的效果,省去了机械抛光的过程,实现抛光腐蚀一体化。
权利要求书1页 说明书4页 附图1页CN 106757299 A 2017.05.31C N 106757299A1.一种镍基合金金相组织的电解抛光腐蚀剂,其特征在于,该抛光腐蚀剂包含以下以体积份数计的原料:硫酸30~40份、磷酸120~150份、去离子水30~40份、硝酸 5~10份及甘油50~80份。
2.如权利要求1所述的镍基合金金相组织的电解抛光腐蚀剂,其特征在于,所述的硫酸的质量分数浓度为95%~98%。
3.如权利要求1所述的镍基合金金相组织的电解抛光腐蚀剂,其特征在于,所述的磷酸的质量分数浓度为85%以上。
一种制备钼铼合金金相试样的电解抛光液及其方法
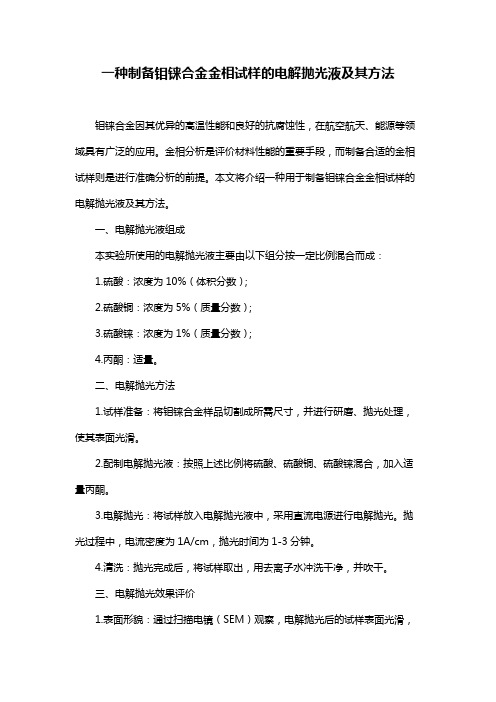
一种制备钼铼合金金相试样的电解抛光液及其方法
钼铼合金因其优异的高温性能和良好的抗腐蚀性,在航空航天、能源等领域具有广泛的应用。
金相分析是评价材料性能的重要手段,而制备合适的金相试样则是进行准确分析的前提。
本文将介绍一种用于制备钼铼合金金相试样的电解抛光液及其方法。
一、电解抛光液组成
本实验所使用的电解抛光液主要由以下组分按一定比例混合而成:
1.硫酸:浓度为10%(体积分数);
2.硫酸铜:浓度为5%(质量分数);
3.硫酸铼:浓度为1%(质量分数);
4.丙酮:适量。
二、电解抛光方法
1.试样准备:将钼铼合金样品切割成所需尺寸,并进行研磨、抛光处理,使其表面光滑。
2.配制电解抛光液:按照上述比例将硫酸、硫酸铜、硫酸铼混合,加入适量丙酮。
3.电解抛光:将试样放入电解抛光液中,采用直流电源进行电解抛光。
抛光过程中,电流密度为1A/cm,抛光时间为1-3分钟。
4.清洗:抛光完成后,将试样取出,用去离子水冲洗干净,并吹干。
三、电解抛光效果评价
1.表面形貌:通过扫描电镜(SEM)观察,电解抛光后的试样表面光滑,
无明显划痕和凹坑。
2.相结构:通过X射线衍射(XRD)分析,电解抛光后的试样相结构未发生明显变化。
3.硬度:电解抛光对试样的硬度影响较小,可满足后续金相分析的要求。
四、结论
本实验介绍了一种制备钼铼合金金相试样的电解抛光液及其方法。
该方法操作简便,抛光效果良好,可广泛应用于钼铼合金的金相分析。
金相试样电解抛光腐蚀规程

金相试样电解抛光、腐蚀规程本标准规定了金属试样电解抛光、腐蚀操作的试验规范。
本标准适用于金属试验中金相试样的制备。
1.主要技术参数见设备(EP—6型电解抛光腐蚀仪)的操作说明书2.操作步骤见设备的操作说明书,抛光工艺可参考附表中的电解抛光、腐蚀参考资料3.安全规程3.1 使用含高氯酸电解液时,必须通循环水冷却,配制温度低于15C,使用温度应低于200C注意安全,防止燃烧和爆炸。
3.2 使用电压超过60V时,要注意安全,应先放好试样,再调电压到所需值,后进行电解抛光,结束后将电压调到零位再取试样。
3.3 当电源接通后,直流档无论有无负载,要严防短路,尤其使用外电解浸蚀时更应注意。
3.4 接通负载后(即抛光或腐蚀进行时),严禁转换电压调整器。
每次抛光后,应关闭电源防止过热。
3.5 抛光结束后,将电解液倒入其它容器中,用水清洗电解槽及冷却循环系统。
4.下列情况不适用本方法4.1 不能用塑料镶嵌试样,因为塑料不导电容易被电解液浸蚀。
4.2 极易受电解液浸蚀的金属相和一些夹杂物不能采用电解抛光。
4.3 需要边、角的试样,不适宜进行电解抛光。
附表1 电解抛光参考资料试验材料电解液配比电压时间备注不锈钢1Cr—18Ni9Ti 酒精(95%)940ml高氯酸(65%)60ml30~40V 15~60秒不锈钢、合金钢、高速钢等酒精(95%)700ml;高氯酸(30%)200ml;甘油(丙三醇)100ml15~50V 15~60秒通用电解液之一钢、铸铁、铝、铝合金等酒精(95%)700ml;高氯酸(30%)200ml;丁氧基乙醇100ml30~65V 15~60秒最好的通用配方之一不锈钢、碳钢铁、合金钢等醋酸(冰醋酸)900ml高氯酸(60%)100ml12~70V 0.5~2分铀、锆、钛、铝合金钢、碳钢醋酸(冰醋酸)800ml高氯酸(60%)200ml40~100V 1~15分不锈钢水250ml硫酸750ml1.5~6V 1~2分不锈钢磷酸(85%)600ml硫酸400ml1.5~12V 10~60秒不锈钢水80ml硫酸720ml甘油200ml1.5~6V 0.5~5分不锈钢和合金钢水:240ml,硫酸:340ml磷酸(85%):650ml1.5~12V 2~10分0.1~0.2A/cm2不锈钢水:330ml,硫酸120ml磷酸(85%):550ml1.5~12v 1分0.05A/ cm2不锈钢和合金钢水:240ml,磷酸:(85%):650ml铬酸80% 硫酸130ml1.5~12V 5~60分0.5A/cm2100~130。
金相腐蚀药水
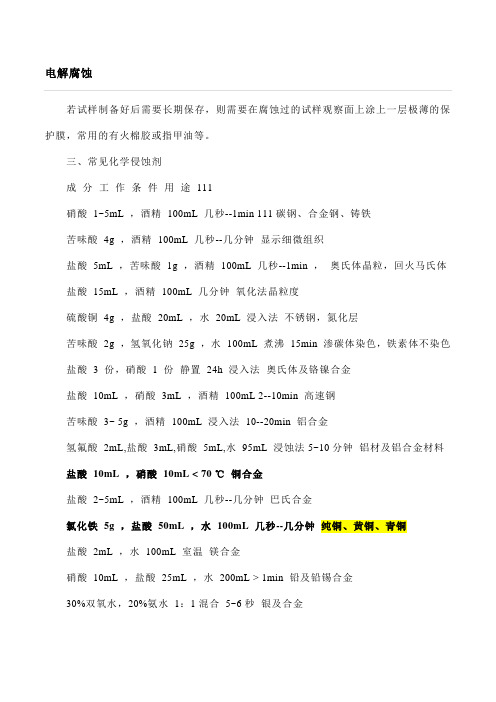
电解腐蚀若试样制备好后需要长期保存,则需要在腐蚀过的试样观察面上涂上一层极薄的保护膜,常用的有火棉胶或指甲油等。
三、常见化学侵蚀剂成分工作条件用途111硝酸1~5mL ,酒精100mL 几秒--1min 111碳钢、合金钢、铸铁苦味酸4g ,酒精100mL 几秒--几分钟显示细微组织盐酸5mL ,苦味酸1g ,酒精100mL 几秒--1min ,奥氏体晶粒,回火马氏体盐酸15mL ,酒精100mL 几分钟氧化法晶粒度硫酸铜4g ,盐酸20mL ,水20mL 浸入法不锈钢,氮化层苦味酸2g ,氢氧化钠25g ,水100mL 煮沸15min 渗碳体染色,铁素体不染色盐酸 3 份,硝酸 1 份静置24h 浸入法奥氏体及铬镍合金盐酸10mL ,硝酸3mL ,酒精100mL 2--10min 高速钢苦味酸3~ 5g ,酒精100mL 浸入法10--20min 铝合金氢氟酸2mL,盐酸3mL,硝酸5mL,水95mL 浸蚀法5~10分钟铝材及铝合金材料盐酸10mL ,硝酸10mL < 70 ℃铜合金盐酸2~5mL ,酒精100mL 几秒--几分钟巴氏合金氯化铁5g ,盐酸50mL ,水100mL 几秒--几分钟纯铜、黄铜、青铜盐酸2mL ,水100mL 室温镁合金硝酸10mL ,盐酸25mL ,水200mL > 1min 铅及铅锡合金30%双氧水,20%氨水1:1混合5~6秒银及合金浸蚀剂名称成份适用范围及使用要点硝酸酒精溶液硝酸2-4ml酒精100ml各种碳钢、铸铁等苦味酸酒精溶液苦味酸4g酒精100ml珠光体、马氏体、贝氏体、渗碳体盐酸苦味酸盐酸5ml苦味酸1g水100ml回火后马氏体或奥氏体晶粒氯化铁盐酸水溶液氯化铁5g盐酸50ml水100ml奥氏体-铁素体不锈钢奥氏体不锈钢混合酸甘油溶液硝酸10ml盐酸30ml甘油30ml奥氏体不锈钢高Cr Ni耐热钢王水酒精溶液盐酸10ml硝酸3ml酒精100ml18-8型奥氏体钢的δ相三合一浸蚀液盐酸10ml硝酸3ml甲醇100ml高速钢回火后晶粒硫酸铜盐酸溶液盐酸100ml硫酸5ml硫酸铜5g高温合金氯化铁溶液氯化铁30g氯化铜1g氯化锡0.5g盐酸50g铸铁磷的偏析与枝晶组织苦味酸钠溶液苦味酸1g水100ml区别渗碳体和磷化物氯化铁盐酸水溶液氯化铁5g盐酸15ml水100ml纯铜、黄铜及铜合金绿化铜盐酸溶液氯化铜1g氯化镁4g盐酸2ml酒精100ml灰铸铁共晶团硫酸铜-盐酸溶液硫酸铜4g 灰铸铁共晶团盐酸20ml 水20ml硫酸铜-盐酸溶液硫酸铜5g盐酸50ml水50ml高温合金盐酸-硫酸-硫酸铜溶液硫酸铜5g盐酸100ml硫酸5ml高温合金复合试剂硝酸30ml盐酸15ml重铬酸钾5g酒精30ml苦味酸1g氯化高铁3g高温合金硬质合金试剂A饱和的三氯化铁盐酸溶液B新配置的20%氢氧化钾水溶液+20%铁氰化钾水溶液硬质合金先在A试剂中浸蚀1min,然后在B试剂中浸蚀3min,WC相(灰白色),TiC-WC相(黄色)Co(黑色)氢氧化钾-铁氰化钾水新配置的10%氢氧化钾水溶液+10%铁氰化钾水溶液硬质合金的n相混合酸硝酸2.5ml氢氟酸1ml盐酸1.5ml水95ml显示硬铝组织氢氟酸水溶液氢氟酸0.5ml水99.5ml显示一半铝合金组织苛性钠水溶液苛性钠1g水100ml显示铝与铝合金组织。