轧制工艺参数
dp780热轧带钢生产工艺参数

DP780热轧带钢是一种高强度、高延展性的汽车板材,具有良好的成形性能和焊接性能,在汽车制造领域得到广泛应用。
为了生产出符合要求的DP780热轧带钢,生产工艺参数的选择至关重要。
本文将从热轧带钢的工艺参数选择、控制和调整等方面进行讨论。
一、热轧带钢的工艺参数选择1、轧制温度的选择热轧带钢的轧制温度对其组织和性能有着至关重要的影响。
一般而言,DP780热轧带钢的轧制温度一般在800~1100摄氏度之间。
过低的轧制温度会使钢材的塑性降低,难以形成均匀的组织;而过高的轧制温度会导致晶粒长大,影响其强度和塑性。
在选择热轧带钢的轧制温度时,需要考虑其成分、厚度、宽度等因素,综合考虑找到最适宜的温度范围。
2、轧制力的控制在热轧带钢的生产过程中,轧制力的控制对最终产品的性能有着重要的影响。
适当的轧制力可以有效地改变钢材的组织结构,提高其强度和延展性。
但是,过大的轧制力可能会导致过度的塑性变形,影响产品的表面质量,甚至导致裂纹的产生。
在热轧带钢的生产中,需要根据钢材的特性和成型要求,合理控制轧制力的大小和分布。
3、冷却方式的选择热轧带钢在轧制后需要进行冷却,以使其组织结构得到稳定和均匀的改善。
冷却方式的选择对最终产品的组织和性能有着直接的影响。
常见的冷却方式包括空气冷却、水冷却、油冷却等。
不同的冷却方式会对热轧带钢的强度、塑性和表面质量产生不同的影响。
在选择冷却方式时,需要考虑产品的具体要求,合理选择适宜的冷却方式。
二、热轧带钢的工艺参数控制1、轧制温度的控制在热轧带钢的生产中,轧制温度的控制是一个复杂而关键的问题。
轧制温度受到许多因素的影响,如进料温度、轧制速度、轧辊温度等。
为了确保热轧带钢的组织和性能达到要求,需要对轧制温度进行精确而有效的控制。
采用先进的温度控制系统和实时监测手段,能够及时调整轧制温度,保证产品的质量稳定和一致性。
2、轧制力的监测与调整轧制力是影响热轧带钢成形过程的重要因素之一。
通过对轧制力的监测和分析,可以了解产品在轧制过程中的变形状态,及时发现异常情况并进行调整。
轧机工艺参数

轧机工艺参数轧机工艺参数是指在金属轧制过程中,对轧机进行调整和控制的一些关键参数。
这些参数的选择和调整直接影响到轧机的工作效果和产品质量。
本文将从轧机速度、轧制压力、轧辊直径和材料温度等方面介绍轧机工艺参数的重要性及其对轧制过程的影响。
首先是轧机速度。
轧机速度是指轧机轧制工作时金属材料的进给速度。
轧机速度的选择要根据金属材料的性质、厚度和轧制要求等因素进行调整。
过高的轧机速度会导致轧制过程中产生过大的热量,可能引起材料内部结构的改变,从而影响产品的力学性能。
而过低的轧机速度则会导致生产效率低下。
因此,合理选择适当的轧机速度是保证轧机工艺顺利进行的重要因素之一。
其次是轧制压力。
轧制压力是指轧机在轧制过程中对金属材料施加的压力。
轧制压力的大小决定了金属材料的变形程度和轧制效果。
过大的轧制压力会导致轧制过程中金属材料的塑性变形过大,可能引起内部裂纹和变形不均匀等问题。
而过小的轧制压力则会导致轧制效果不理想,产品表面质量不达标。
因此,合理选择适当的轧制压力对保证产品质量和工艺效果至关重要。
轧辊直径也是轧机工艺参数中的重要因素。
轧辊直径的选择与轧制材料的厚度和硬度密切相关。
较小直径的轧辊适用于轧制较薄的材料,能够提供更高的轧制压力,但对轧辊的耐用性要求较高。
而较大直径的轧辊适用于轧制较厚的材料,能够提供较大的轧制力,但对轧机的承载能力要求较高。
因此,在轧机工艺中,合理选择适当的轧辊直径能够提高轧制效果,保证产品质量。
最后是材料温度。
材料温度是指轧制过程中金属材料的温度。
材料温度的控制对轧制过程中的变形能力、力学性能和表面质量等方面都有重要影响。
过高的材料温度会导致材料塑性变形能力增加,但容易引起材料表面氧化和热裂纹等问题。
而过低的材料温度会导致材料的塑性变形能力降低,轧制效果不理想。
因此,在轧机工艺中,合理控制金属材料的温度对保证轧制过程的顺利进行和产品质量的提高至关重要。
轧机工艺参数是保证金属轧制过程顺利进行和产品质量的关键因素。
【文献综述】环形件轧制工艺的参数化设计
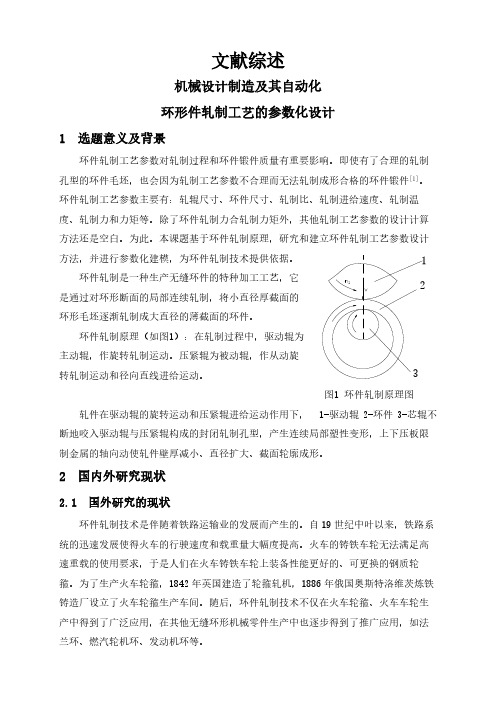
文献综述机械设计制造及其自动化环形件轧制工艺的参数化设计1 选题意义及背景环件轧制工艺参数对轧制过程和环件锻件质量有重要影响。
即使有了合理的轧制孔型的环件毛坯,也会因为轧制工艺参数不合理而无法轧制成形合格的环件锻件[1]。
环件轧制工艺参数主要有:轧辊尺寸、环件尺寸、轧制比、轧制进给速度、轧制温度、轧制力和力矩等。
除了环件轧制力合轧制力矩外,其他轧制工艺参数的设计计算方法还是空白。
为此。
本课题基于环件轧制原理,研究和建立环件轧制工艺参数设计方法,并进行参数化建模,为环件轧制技术提供依据。
是通过对环形断面的局部连续轧制,将小直径厚截面的环形毛坯逐渐轧制成大直径的薄截面的环件。
环件轧制原理(如图1):在轧制过程中,驱动辊为主动辊,作旋转轧制运动。
压紧辊为被动辊,作从动旋转轧制运动和径向直线进给运动。
图1 环件轧制原理图轧件在驱动辊的旋转运动和压紧辊进给运动作用下, 1-驱动辊 2-环件 3-芯辊不断地咬入驱动辊与压紧辊构成的封闭轧制孔型,产生连续局部塑性变形,上下压板限制金属的轴向动使轧件壁厚减小、直径扩大、截面轮廓成形。
2 国内外研究现状2.1 国外研究的现状环件轧制技术是伴随着铁路运输业的发展而产生的。
自19世纪中叶以来,铁路系统的迅速发展使得火车的行驶速度和载重量大幅度提高。
火车的铸铁车轮无法满足高速重载的使用要求,于是人们在火车铸铁车轮上装备性能更好的、可更换的钢质轮箍。
为了生产火车轮箍,1842年英国建造了轮箍轧机,1886年俄国奥斯特洛维茨炼铁铸造厂设立了火车轮箍生产车间。
随后,环件轧制技术不仅在火车轮箍、火车车轮生产中得到了广泛应用,在其他无缝环形机械零件生产中也逐步得到了推广应用,如法兰环、燃汽轮机环、发动机环等。
英国学者W.Johnson[2-4]等首先开展了环件轧制试验研究。
他们先在立式二辊轧环机上进行了基本参数的试验研究,发现环件轧制时径向变形区的径向对称点存在塑性铰。
同年,Johnson等在实验室建造了小型卧式环件轧机,其结构形式与工业生产轧机相同,在该轧机上,他们进行了轧制力、力矩及压下量的连续测量,得到了一些基本结论。
BJ001-铸轧工艺参数计算

读书笔记
铸轧工艺参数计算
铸轧的主要工艺参数
铸轧区长度 铸轧速度 浇注温度 冷却强度 凝固瞬间铝熔体供给所需的静压力
在轧辊直径、铸轧板厚度一定的正常铸轧情况下,上述工艺参数之一有变化,其它工艺参数将随之变 化才可能保持铸轧工艺的稳定性。生产实践表明,在调整各工艺参数之间的关系时,应使凝固区与变形区 的高与长有一定的比例关系,以保证绝对压下量△h 恒定,才能确保铸轧过程的连续性和稳定性,使铸轧 带坯具有优良的组织。
1 铸轧区长度
双辊式铸轧机的铸轧区的建立与铸轧辊的冷却强度、铸轧速度、带坯厚度有直接关系。图 1 为双辊式 连续铸轧机铸轧区示意图,由图可知,铸轧区由铝熔体冷却到结晶温度的冷却区(Z1),铸轧区(Z2)和轧 制变形区(Z3)组成。根据铸轧工艺的不同,各区长度存在一定比例关系。铸轧区长度可按下式计算,其 计算结果与实际情况比较接近。
Z
∆ 2
√∆
式中: Z——铸轧区长度,cm; H——前箱熔体水平面与氧化膜之间的高度差,cm; ρ——熔体密度,kg/—铸轧速度,m/min; v2——平均凝固速度,cm/min; h——带坯厚度,cm; σ——表面张力系数,N·cm-1; Δh——绝对压下量,cm; R——铸轧辊半径,cm。
对于双辊倾斜式连续铸轧机,生产实践表明,铸轧角在 8°~9°范围内变化,铸轧区长度可用式 2 计 算。生产实践证明,双辊倾斜式φ650mm 铸轧机和φ980mm 铸轧机铸轧区最大长度分别为 50mm 和 70mm 左右。
Z Rsinθ
式中: Z——铸轧区长度,mm;
读书笔记
θ——铸轧角,°(度); R——轧辊半径,mm。 2 铸轧力计算公式 p K应宽外 p——铸轧坯对铸轧辊的平均单位压力,MPa; 应——应力状态系数,用来考虑外摩擦和张力对单位压力的影响; 外——外端影响系数,由于轧制外区对轧制区有影响而引入的系数; 宽——宽展系数,轧制时带坯宽展时而引入的对平均单位压力的影响系数; K——铝带坯在铸轧温度时的真实变形抗力,MPa;
薄带铸轧工艺技术规范
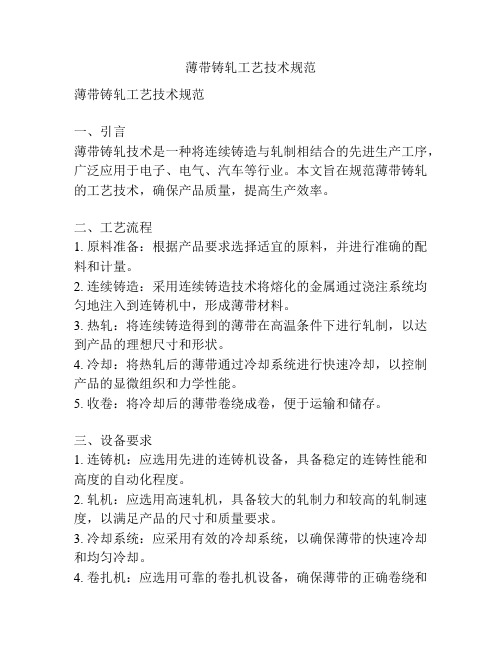
薄带铸轧工艺技术规范薄带铸轧工艺技术规范一、引言薄带铸轧技术是一种将连续铸造与轧制相结合的先进生产工序,广泛应用于电子、电气、汽车等行业。
本文旨在规范薄带铸轧的工艺技术,确保产品质量,提高生产效率。
二、工艺流程1. 原料准备:根据产品要求选择适宜的原料,并进行准确的配料和计量。
2. 连续铸造:采用连续铸造技术将熔化的金属通过浇注系统均匀地注入到连铸机中,形成薄带材料。
3. 热轧:将连续铸造得到的薄带在高温条件下进行轧制,以达到产品的理想尺寸和形状。
4. 冷却:将热轧后的薄带通过冷却系统进行快速冷却,以控制产品的显微组织和力学性能。
5. 收卷:将冷却后的薄带卷绕成卷,便于运输和储存。
三、设备要求1. 连铸机:应选用先进的连铸机设备,具备稳定的连铸性能和高度的自动化程度。
2. 轧机:应选用高速轧机,具备较大的轧制力和较高的轧制速度,以满足产品的尺寸和质量要求。
3. 冷却系统:应采用有效的冷却系统,以确保薄带的快速冷却和均匀冷却。
4. 卷扎机:应选用可靠的卷扎机设备,确保薄带的正确卷绕和稳定性。
四、工艺参数1. 连铸工艺参数:包括浇注温度、冷却方式、浇注速度等,应根据具体材料和产品要求进行合理的设定。
2. 轧制工艺参数:包括轧制温度、轧制力、轧制速度等,应根据材料的热变形特性和产品的尺寸要求进行合理的设定。
3. 冷却工艺参数:包括冷却速度、冷却介质等,应根据材料的热处理要求和产品的显微组织控制要求进行合理的设定。
五、质量控制1. 原料检验:对原材料进行化学成分、物理性能等方面的检验,确保原材料符合产品要求。
2. 在线检测:对连续铸造、热轧、冷却等过程进行在线检测,及时发现并纠正问题,确保产品质量。
3. 产品检验:对成品薄带进行外观质量、尺寸精度、机械性能、化学成分等方面的检验,确保产品达到标准要求。
六、安全环保1. 设备安全:保证设备的安全运行,提供必要的防护设施和安全培训。
2. 废水处理:配备有效的废水处理设施,确保废水符合环保要求。
(整理)几个重要工艺参数的计算.
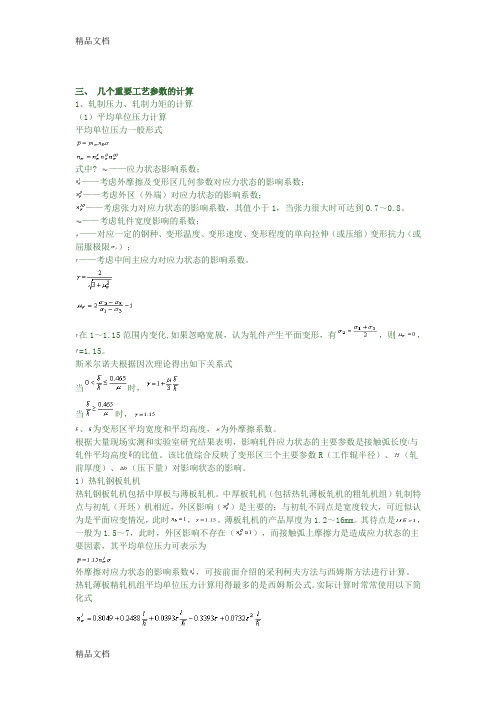
三、几个重要工艺参数的计算1、轧制压力、轧制力矩的计算(1)平均单位压力计算平均单位压力一般形式式中? ——应力状态影响系数;——考虑外摩擦及变形区几何参数对应力状态的影响系数;——考虑外区(外端)对应力状态的影响系数;——考虑张力对应力状态的影响系数,其值小于1,当张力很大时可达到0.7~0.8。
——考虑轧件宽度影响的系数;——对应一定的钢种、变形温度、变形速度、变形程度的单向拉伸(或压缩)变形抗力(或屈服极限);——考虑中间主应力对应力状态的影响系数。
在1~1.15范围内变化,如果忽略宽展,认为轧件产生平面变形,有,则,=1.15。
斯米尔诺夫根据因次理论得出如下关系式当时,当时,、为变形区平均宽度和平均高度,为外摩擦系数。
根据大量现场实测和实验室研究结果表明,影响轧件应力状态的主要参数是接触弧长度与轧件平均高度的比值。
该比值综合反映了变形区三个主要参数R(工作辊半径)、(轧前厚度)、(压下量)对影响状态的影响。
1)热轧钢板轧机热轧钢板轧机包括中厚板与薄板轧机。
中厚板轧机(包括热轧薄板轧机的粗轧机组)轧制特点与初轧(开坯)机相近,外区影响()是主要的;与初轧不同点是宽度较大,可近似认为是平面应变情况,此时,。
薄板轧机的产品厚度为1.2~16mm。
其待点是,一般为1.5~7,此时,外区影响不存在(),而接触弧上摩擦力是造成应力状态的主要因素,其平均单位压力可表示为外摩擦对应力状态的影响系数,可按前面介绍的采利柯夫方法与西姆斯方法进行计算。
热轧薄板精轧机组平均单位压力计算用得最多的是西姆斯公式。
实际计算时常常使用以下简化式或美板佳助简化式。
2)冷轧带钢轧机冷轧带钢轧机的轧件尺寸更接近于推导理论公式时所做的假设,即宽度比厚度大得多,宽展很小,可认为是平面变形问题。
轧件厚度小,轧件内部不均匀变形可忽略,因而平面断面假设和滑动摩擦理论与冷轧带钢(薄板)的情况较符合。
此外,冷轧时均采用张力轧制,因而计算冷轧平均单位压力时,必须考虑张力影响。
几个主要工艺参数的计算

三、几个重要工艺参数的计算1、轧制压力、轧制力矩的计算(1)平均单位压力计算平均单位压力一般形式式中? ——应力状态影响系数;——考虑外摩擦及变形区几何参数对应力状态的影响系数;——考虑外区(外端)对应力状态的影响系数;——考虑张力对应力状态的影响系数,其值小于1,当张力很大时可达到0.7~0.8。
——考虑轧件宽度影响的系数;——对应一定的钢种、变形温度、变形速度、变形程度的单向拉伸(或压缩)变形抗力(或屈服极限);——考虑中间主应力对应力状态的影响系数。
在1~1.15范围内变化,如果忽略宽展,认为轧件产生平面变形,有,则,=1.15。
斯米尔诺夫根据因次理论得出如下关系式当时,当时,、为变形区平均宽度和平均高度,为外摩擦系数。
根据大量现场实测和实验室研究结果表明,影响轧件应力状态的主要参数是接触弧长度与轧件平均高度的比值。
该比值综合反映了变形区三个主要参数R(工作辊半径)、(轧前厚度)、(压下量)对影响状态的影响。
1)热轧钢板轧机热轧钢板轧机包括中厚板与薄板轧机。
中厚板轧机(包括热轧薄板轧机的粗轧机组)轧制特点与初轧(开坯)机相近,外区影响()是主要的;与初轧不同点是宽度较大,可近似认为是平面应变情况,此时,。
薄板轧机的产品厚度为1.2~16mm。
其待点是,一般为1.5~7,此时,外区影响不存在(),而接触弧上摩擦力是造成应力状态的主要因素,其平均单位压力可表示为外摩擦对应力状态的影响系数,可按前面介绍的采利柯夫方法与西姆斯方法进行计算。
热轧薄板精轧机组平均单位压力计算用得最多的是西姆斯公式。
实际计算时常常使用以下简化式或美板佳助简化式。
2)冷轧带钢轧机冷轧带钢轧机的轧件尺寸更接近于推导理论公式时所做的假设,即宽度比厚度大得多,宽展很小,可认为是平面变形问题。
轧件厚度小,轧件内部不均匀变形可忽略,因而平面断面假设和滑动摩擦理论与冷轧带钢(薄板)的情况较符合。
此外,冷轧时均采用张力轧制,因而计算冷轧平均单位压力时,必须考虑张力影响。
轧制参数计算模型及其应用(一)

轧制参数计算模型及其应用(一)轧制参数计算模型及其应用概述轧制参数计算模型是一种用于计算轧机工艺参数的数学模型,通过模拟折弯、伸拉和扭转等过程,计算出轧制板材的几何形状和力学性能。
该模型在轧机设计、质量控制和工艺优化等方面具有广泛应用。
模型构建材料模型轧制板材的力学性能由材料性能决定,因此必须首先确定材料模型。
常用的材料模型有等效应力模型和本构模型。
轧制力学模型轧制力学模型可分为几何模型和力学模型。
几何模型是指轧制板材的形状和尺寸模型,力学模型是指轧制板材的应力、应变和塑性变形模型。
数值模拟方法常用的数值模拟方法有有限元法、边界元法和有限差分法。
其中,有限元法是最常用的方法,具有高精度、高效率和高稳定性等优点。
应用轧机设计轧机设计中需要确定轧制力学参数,以控制轧制板材的形状和力学性能。
轧制参数计算模型可以提供合理的轧制参数,以满足不同尺寸、材质和工艺需求。
质量控制轧制板材的质量受多种因素影响,如轧制力、轧制速度和冷却方式等。
轧制参数计算模型可以提供轧制板材的几何形状和力学性能参数,以确定轧制质量是否符合要求。
工艺优化轧制工艺中的轧制参数可以影响轧制板材的形状、尺寸和力学性能。
轧制参数计算模型可以提供不同轧制参数对轧制板材性能的影响程度,以优化轧制工艺,提高生产效率和产品质量。
结论轧制参数计算模型是一种重要的数学模型,可以为轧机设计、质量控制和工艺优化等方面提供重要参考,促进轧制生产技术的发展和进步。
发展方向随着轧制技术的不断发展和进步,轧制参数计算模型也在不断完善和提高。
未来,轧制参数计算模型的发展方向主要包括以下几个方面:•更精确的材料模型,使得轧制参数计算模型能够更好地预测轧制板材的性能特征;•更高效的数值计算方法,以提高计算效率并降低计算成本;•精细化的轧制力学模型,以更真实地模拟轧制板材的变形和应力分布;•基于机器学习和人工智能的轧制参数计算模型,使得模型能够“自学习”,更好地适应复杂的轧制工艺。
1450轧机轧制工艺规程
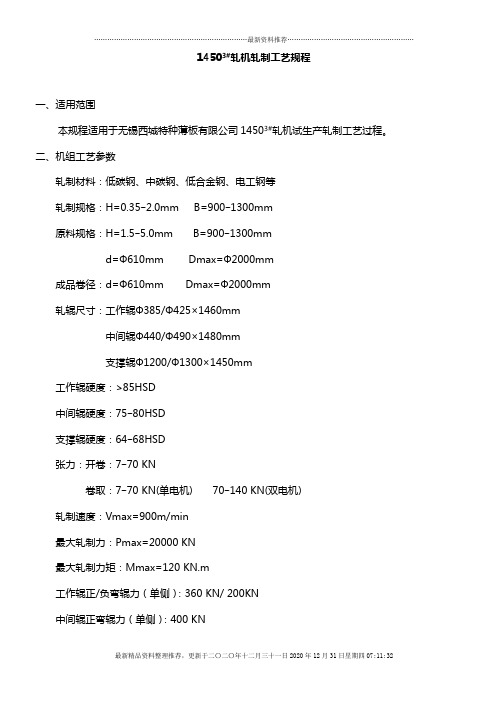
14503#轧机轧制工艺规程一、适用范围本规程适用于无锡西城特种薄板有限公司14503#轧机试生产轧制工艺过程。
二、机组工艺参数轧制材料:低碳钢、中碳钢、低合金钢、电工钢等轧制规格:H=0.35~2.0mm B=900~1300mm原料规格:H=1.5~5.0mm B=900~1300mmd=Ф610mm Dmax=Ф2000mm成品卷径:d=Ф610mm Dmax=Ф2000mm轧辊尺寸:工作辊Ф385/Ф425×1460mm中间辊Ф440/Ф490×1480mm支撑辊Ф1200/Ф1300×1450mm工作辊硬度:>85HSD中间辊硬度:75~80HSD支撑辊硬度:64~68HSD张力:开卷:7~70 KN卷取:7~70 KN(单电机) 70~140 KN(双电机)轧制速度:Vmax=900m/min最大轧制力:Pmax=20000 KN最大轧制力矩:Mmax=120 KN.m工作辊正/负弯辊力(单侧):360 KN/ 200KN中间辊正弯辊力(单侧):400 KN中间辊横移量:Max365 mm主电机功率:Nmax=1197*4 KW= 4788 KW主电机转速:350/800 r/min 减速比:1.0588传动方式:双电机上、下工作辊单独传动三、轧制工艺规程3.1原料制度3.1.1化学成分低碳钢化学成分应符合下表规定其余化学元素:N2≤0.005%,Cu≤0.15%,Cr≤0.08%,Ni≤0.10%,也可供应符合上表规定的其他牌号钢种。
3.1.2尺寸精确性和均匀性3.1.3坯料表面质量钢带表面不得有气泡、结疤、裂纹、夹杂和其他对使用有害的缺陷,钢带卷不得有分层。
3.1.4工艺性能冷轧用坯料力学性能应符合下表规定3.2压下制度3.2.1压下制度主要是依据设备能力﹑轧制要求,充分利用带钢塑性,并考虑加工硬化程度,用最少的道次,最大的压下量,分配道次加工量,以尽可能减少中间退火次数,轧出质量合格的产品,达到优质﹑高产﹑低成本,操作方便﹑可靠。
轧钢工艺标准

编号:C(C)-04-501 A/2
轧钢工艺标准
编制:张进京
审核:
批准:
发布日期:2016年4月29 日生效日期:2016年5月5 日.
.
说明
一、生产工艺路线:原料检查-加热-除鳞-轧制-冷床-剪切-收集-包装-堆垛冷却
二、轧钢工艺主要由加热制度、轧制制度、冷却制度三大部分组成。
三、钢种生产工艺依照轧钢工艺标准执行;客户有特别需求的出具该客户控制要点。
四、每年度对轧钢工艺标准进行修订。
五、轧钢工艺标准,作为轧钢工艺技术规程的补充,标准中未作规定的常规要求,以轧钢工艺技术规程为准。
.
一、轧钢各工序控制规范
.
二、轧钢加热制度
.
钢种加热分类预览表
.
三、轧制制度
1、根据各规格对应的孔型,使用符合要求的轧机和导卫进行轧制。
2、生产各规格时,按对应的《轧钢生产工艺卡》设定各道次料型尺寸和参数。
轧制过程中,检查轧槽和导卫,磨损严重要及时更换;轧机替换辊道和输送辊道表面要保持光滑,磨损严重的及时进行3、
修磨或更换。
4、成品外形和表面质量要符合对应产品的技术标准的相关要求;中间道次轧件不得有耳子、折叠等缺陷。
5、对需要进行精整处理的产品,尺寸需要按尽量符合正偏差要求进行控制,留出精整余量。
6、锚链钢轧制精度按照Q/CJS298-2015A/0内控标准执行
7、终轧温度控制在900-1050℃。
8、轧制降速原则
.
.
.
五、附表:钢种工艺制度明细预览表。
冷轧工艺参数对铝合金板材性能的影响及优化
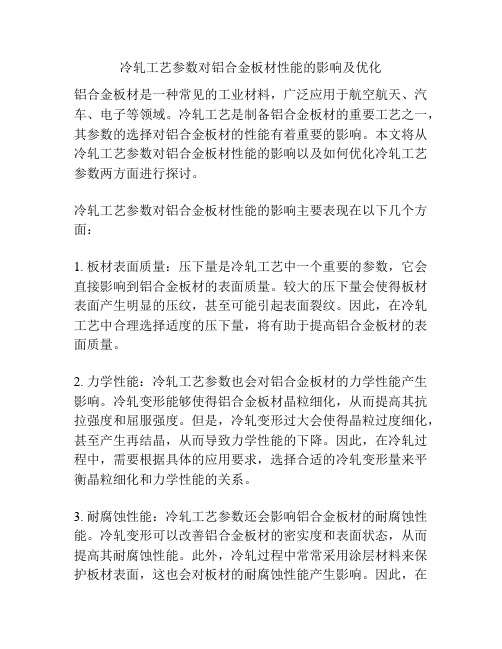
冷轧工艺参数对铝合金板材性能的影响及优化铝合金板材是一种常见的工业材料,广泛应用于航空航天、汽车、电子等领域。
冷轧工艺是制备铝合金板材的重要工艺之一,其参数的选择对铝合金板材的性能有着重要的影响。
本文将从冷轧工艺参数对铝合金板材性能的影响以及如何优化冷轧工艺参数两方面进行探讨。
冷轧工艺参数对铝合金板材性能的影响主要表现在以下几个方面:1. 板材表面质量:压下量是冷轧工艺中一个重要的参数,它会直接影响到铝合金板材的表面质量。
较大的压下量会使得板材表面产生明显的压纹,甚至可能引起表面裂纹。
因此,在冷轧工艺中合理选择适度的压下量,将有助于提高铝合金板材的表面质量。
2. 力学性能:冷轧工艺参数也会对铝合金板材的力学性能产生影响。
冷轧变形能够使得铝合金板材晶粒细化,从而提高其抗拉强度和屈服强度。
但是,冷轧变形过大会使得晶粒过度细化,甚至产生再结晶,从而导致力学性能的下降。
因此,在冷轧过程中,需要根据具体的应用要求,选择合适的冷轧变形量来平衡晶粒细化和力学性能的关系。
3. 耐腐蚀性能:冷轧工艺参数还会影响铝合金板材的耐腐蚀性能。
冷轧变形可以改善铝合金板材的密实度和表面状态,从而提高其耐腐蚀性能。
此外,冷轧过程中常常采用涂层材料来保护板材表面,这也会对板材的耐腐蚀性能产生影响。
因此,在冷轧工艺中选择适当的涂层材料和工艺参数,将有助于提高铝合金板材的耐腐蚀性能。
为了优化铝合金板材的性能,需要针对具体的应用需求,合理选择冷轧工艺参数。
以下是一些建议:1. 了解材料性能:在选择冷轧工艺参数之前,需要充分了解所使用铝合金板材的材料性能。
这包括其强度、塑性、耐腐蚀性等。
只有了解了材料的性能,才能更好地选择适合的冷轧工艺参数。
2. 设计适当的压下量:压下量是冷轧工艺中一个重要的参数。
在选择压下量时,需要充分考虑铝合金板材的表面质量和力学性能。
通常情况下,较小的压下量有助于提高板材的表面质量,而较大的压下量有助于提高板材的力学性能。
轧制工艺技术

轧制工艺技术轧制工艺技术,是指通过机械力将金属坯料进行连续轧制、变形和压制,使其从粗糙的坯料变成平整、有形状的金属条、板、管等材料的过程。
轧制工艺技术是金属加工中常用的一种工艺方法,广泛应用于冶金、机械制造、船舶、汽车等领域。
轧制工艺技术主要包括轧制方法、轧制设备和工艺参数三个方面。
轧制方法主要有热轧和冷轧两种。
热轧是将金属加热到一定温度后进行轧制,适用于低碳钢、合金钢等材料的加工。
热轧工艺具有高产量、易控制等优点,但也会引起材料强度下降、变形度不定等缺点。
冷轧是将金属在室温下进行轧制,适用于不锈钢、铝合金等材料的加工。
冷轧工艺具有制品质量好、表面光洁等优点,但也会引起轧制力大、设备损坏等缺点。
轧制设备主要包括轧机和辅助设备。
轧机是轧制过程中最重要的设备之一,它主要由辊子、辊架、传动装置等组成。
根据轧机的结构和原理的不同,可以分为压下式轧机、抓下式轧机和压痕式轧机三种。
辅助设备主要包括卷板机、脱碳炉、退火炉等,它们的作用是为轧机提供原料和对轧制过程进行辅助处理。
工艺参数是指在轧制过程中需要控制的各项参数。
工艺参数的选择直接影响到轧制产品的质量和性能。
常见的工艺参数有轧制温度、轧制力、轧制速度等。
轧制温度是指轧制过程中金属的温度,不同的材料对轧制温度有不同的要求,过高或过低的温度都会影响到轧制产品的质量。
轧制力是指轧制时作用在轧辊上的力,它的大小直接影响到轧制产品的变形度和机械性能。
轧制速度是指轧制辊的线速度,不同的产品对轧制速度有不同的要求,过快或过慢的速度都会影响到轧制产品的表面质量。
轧制工艺技术的应用可以使金属材料获得更好的性能和表面质量,有助于提高产品的竞争力和降低成本。
同时,轧制工艺技术也对轧制设备和工艺参数的要求提出了挑战。
为了更好地应对这些挑战,需要不断改进和创新轧制工艺技术,提高轧制产品的质量和生产效率。
镁合金轧制板材工艺的主要热轧工艺参数是什么(精)

镁合金轧制板材工艺的主要热轧工艺参数是什么
镁合金热轧制变形时, 都会具有较好的轧制性能。
热轧制变形时多采用二辊轧机, 大批量生产时常采用三辊或者四辊轧机。
轧制时道次压下量通常控制在 10%-25%, 加热一次后可进行多道次轧制。
为了降低轧制力并改善板材性能,轧制时通常使用润滑剂,可将含 2%的调水油均匀地喷涂于加热的轧辊表面。
在粗轧时为了防止粘辊,可用猪油、石蜡、硼氮化合物等作为润滑剂。
镁合金的冷轧变形不易进行, 不能像铝合金那样可以达到 98%以上的总加工率与 60%左右的道次加工率。
镁合金的冷轧能力取决于合金成分以及热轧工艺和组织。
通常 AZ31的冷轧总变形量可达 16%,大部分镁合金对冷加工硬化很敏感,对冷轧镁合金板材进行不同程度的中间退火或成品退火, 可改善其冷变形能力, 并获得不同状态和性能的制品。
重庆大学的陈绪宏对 AZ31镁合金连续铸轧工艺过程进行了实验研究,并成功生产出了厚度为 1~3mm ,边部齐整,表面质量良好的镁合金薄带。
实验研究表明,要得到较好表面质量和力学性能的薄带需要合理的控制各个工艺参数, 当辊速为
10~15r/min, 浇铸温度为 655~ 665℃,辊缝为 0.9mm 时,获得了质量良好的镁合金薄带。
轧制工艺参数测试技
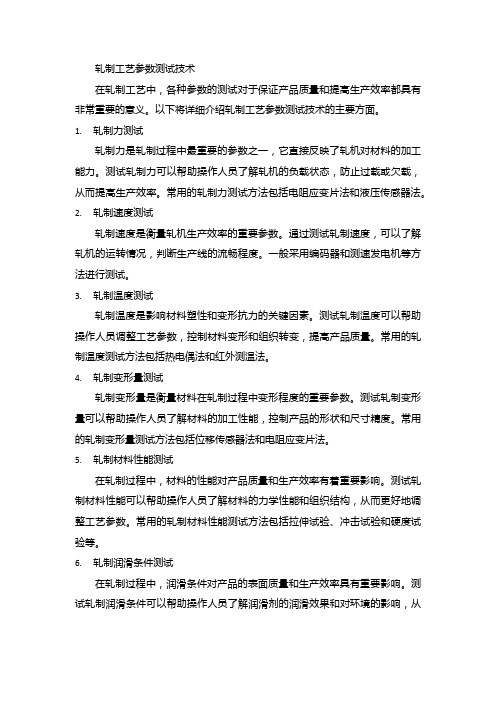
轧制工艺参数测试技术在轧制工艺中,各种参数的测试对于保证产品质量和提高生产效率都具有非常重要的意义。
以下将详细介绍轧制工艺参数测试技术的主要方面。
1.轧制力测试轧制力是轧制过程中最重要的参数之一,它直接反映了轧机对材料的加工能力。
测试轧制力可以帮助操作人员了解轧机的负载状态,防止过载或欠载,从而提高生产效率。
常用的轧制力测试方法包括电阻应变片法和液压传感器法。
2.轧制速度测试轧制速度是衡量轧机生产效率的重要参数。
通过测试轧制速度,可以了解轧机的运转情况,判断生产线的流畅程度。
一般采用编码器和测速发电机等方法进行测试。
3.轧制温度测试轧制温度是影响材料塑性和变形抗力的关键因素。
测试轧制温度可以帮助操作人员调整工艺参数,控制材料变形和组织转变,提高产品质量。
常用的轧制温度测试方法包括热电偶法和红外测温法。
4.轧制变形量测试轧制变形量是衡量材料在轧制过程中变形程度的重要参数。
测试轧制变形量可以帮助操作人员了解材料的加工性能,控制产品的形状和尺寸精度。
常用的轧制变形量测试方法包括位移传感器法和电阻应变片法。
5.轧制材料性能测试在轧制过程中,材料的性能对产品质量和生产效率有着重要影响。
测试轧制材料性能可以帮助操作人员了解材料的力学性能和组织结构,从而更好地调整工艺参数。
常用的轧制材料性能测试方法包括拉伸试验、冲击试验和硬度试验等。
6.轧制润滑条件测试在轧制过程中,润滑条件对产品的表面质量和生产效率具有重要影响。
测试轧制润滑条件可以帮助操作人员了解润滑剂的润滑效果和对环境的影响,从而更好地选择和使用润滑剂。
常用的轧制润滑条件测试方法包括摩擦系数测试和润滑剂性能测试等。
7.轧制坯料尺寸测试在轧制过程中,坯料的尺寸对产品的形状和尺寸精度有着重要影响。
测试坯料尺寸可以帮助操作人员了解坯料的形状和尺寸精度,从而更好地控制产品的加工过程。
常用的坯料尺寸测试方法包括卡尺测量法和磨床测量法等。
总之,对轧制工艺参数进行测试是保证产品质量和提高生产效率的关键手段。
轧制工艺参数设计

7 轧制工艺参数设计7.1 压下规程设计冷轧板带压下规程的设计一般包括原料规格的选择、轧制方案的确定、各道次压下量的分配与计算以及轧制速度的确定等。
7.1.1 坯料厚度选择在选择原料厚度时主要考虑冷轧总变形程度对性能及结构的影响。
由于对一定钢种、规格的产品,必须有一定的冷轧总变形程度,才能通过热处理获得所需要的一定的晶粒组织和性能。
坯料最大厚度受咬入能力和设备条件的限制;坯料最小厚度应考虑热轧带钢的供应情况,成品厚度和组织性能。
此外,选择原料厚度时,还要考虑生产能力的提高,故应根据具体情况做出选择。
本设计的代表产品是920×0.49 1020×0.95 1120×1.35 1220×1.75 1320×2.15 本设计选用厚度2.1 mm的带钢生产厚度为0.49mm成品板带钢,4.0 mm生产厚度为0.95mm的成品带钢,5.5mm生产厚度为1.35mm的成品带钢,4.0 mm生产厚度为1.75 mm的成品带钢,4.5mm生产厚度为2.15mm的成品带钢[4]。
7.1.2 轧制方案冷轧轧程是冷轧过程中每次中间退火所完成的冷轧工作。
冷轧轧程的确定主要取决于所轧钢种的软硬特性,坯料与成品的厚度,所采用的冷轧工艺和冷轧制度以及轧机的能力等因素,并随着工艺和设备的改进,轧制方案也在不断的变化。
例如选用润滑性能更好的工艺润滑剂或采用直径更小的高硬度工作辊都能减少所需要的轧程数。
因此,在确定冷轧轧程方案时,需要考虑已有的设备与工艺条件,还应充分研究各种提高冷轧效率的措施。
7.1.3 压下量的分配与计算在选择压下制度时,第一、二机架为利用金属的塑性,可以给予较大压下量,但往往受到咬入条件的限制,在有良好润滑研磨的轧辊允许咬入角3°到4°,而表面比较粗糙的轧辊为5°到8°,第一机架考虑到热轧来料的厚度偏差不宜采用过大压下量。
型材轧钢工艺及参数

型材轧钢工艺及参数从钢坯库100t电动平车开始至成品仓库(短尺钢轨成品库、长尺钢轨成品库、型钢成品库)为止,工程内容主要有原料准备、钢坯加热、轧制作业线、产品冷却、钢轨精整线和型钢精整线等。
产品品种以生产钢轨为主,并兼顾生产H型钢、普通型钢和异型钢。
本设计以生产100m定尺和时速350km/h高速铁路用轨的高档次产品为起点,标志着该钢轨生产工艺及装备具备世界先进水平,其生产工艺特点如下:a)采用5机架万能轧制法生产钢轨,轧制过程为对称变形,对特别重要的轨头和轨底加工良好,产品断面尺寸精度高。
b)采用长尺冷却、长尺矫直、长尺探伤和平直度检测、冷锯定尺生产工艺,从而提高产品质量、成材率和精整能力。
c)采用多级高压水除鳞,清除轧件表面的初生和次生氧化铁皮,利于提高产品表面质量,降低轧辊消耗。
d)万能轧机和轧边机采用CCS紧凑式结构全液压压下、液压位置控制HPC、自动辊缝控制AGC和下水平辊动态轴向调整,轧辊和导卫成组快速更换,轧机刚度好,调整精度高。
e)采用带钢轨预弯装置的步进梁式冷床,可适宜各种产品均匀冷却,弯曲度小,减少钢材表面划伤,降低产品残余应力。
f)钢轨在线检测中心设置钢材表面清理装置、断面尺寸检测、全长平直度检测、表面缺陷涡流探伤、内部缺陷超声波探伤以及缺陷喷标装置等,以确保产品质量等级。
g)钢轨精整采用锯钻加工100m以下各种定尺,满足不同用户需要。
1.2生产规模及产品大纲本工程拟定生产钢轨、H型钢、工字钢等产品。
生产能力为105万t/a,分品种规格的产品大纲见表1。
表1 分品种规格的产品大纲1.3生产工艺流程1.3.1生产工艺流程简述a)钢轨生产经检查合格的连铸坯由原料跨的电动平车及料耙吊车热送到装料台架上,通过装炉辊道,称重、测长后进入步进式加热炉加热。
不能热装的坯料,用吊车吊入原料跨存放。
按生产计划要求,冷坯由吊车吊到上料台架上,通过装炉辊道,经称重、测长后进入加热炉加热。
钢坯加热到1150~1200℃出炉,经高压水除鳞后在第一架开坯机(BD1)上往复轧制5~11道次,在第二架开坯机(BD2)上往复轧制5~7道次,轧出万能轧机所需要的中间坯。
轧制工艺参数设计

5 轧制工艺参数设计轧制工艺参数设计主要包括压下制度、速度制度、温度制度。
我们知道轧制工艺参数是中厚板生产的核心部分,直接关系着轧机的产量和产品的质量。
轧制工艺参数设计的主要内容就是要由所需的产品选出合适的坯料,确定由这一坯料轧制成成品总共需要多少道次、每道次的压下量等内容,具体到操作上就是要计算出每道次压下螺丝的升降位置。
同时,为了轧制出合格的产品,还要确定轧制的开轧温度、终轧温度,各道次的轧制速度分配等。
另外,还应包括轧辊的辊型制度。
这样才能在生产中制定出合理的轧制制度,达到既产量和质量,又实现操作方便、设备安全等目的。
本设计的产品是ss400,42×2850×9000mm 厚板轧制工艺参数设计。
5.1 坯料的选择选择坯料是中厚钢板生产中的重要环节之一。
坯料选择是否合理,将影响轧机的生产率、成材率、钢板质量及成本,应予重视。
5.1.1 原料的种类如前所述,所以本设计选择连铸坯作为原料。
5.1.2 原料的尺寸本次设计原料的厚度选择260 mm 。
原料的宽度尺寸尽量大,考虑到展宽比1.4和实际情况,使横轧操作容易,由常用规格,原料宽度选择2030mm 。
切边100mm ,切头尾400mm 。
原料的长度尺寸应尽可能接近原料的最大允许长度。
根据生产实际情况ss400的烧损率为0.6%,并由体积不变的原则:260×2030×l =42×(2850+100)×(9000+400)×1.006mm l 22202030260006.1)4009000()1002850(42=⨯⨯+⨯+⨯=即l 取2220.00mm 。
所以坯料规格取为mm 22202030260⨯⨯。
根据钢的成分和铁碳相图以及控制控冷的要求定出开轧温度分别为1050℃。
5.2 轧制制度由轧制方式,本设计中采用横—纵轧制方式,由于横—纵轧法板坯宽度不受钢板宽度的限制,比较灵活;轧件在横向有一定的延伸,改善了钢板的横向性能。
轧机工艺参数
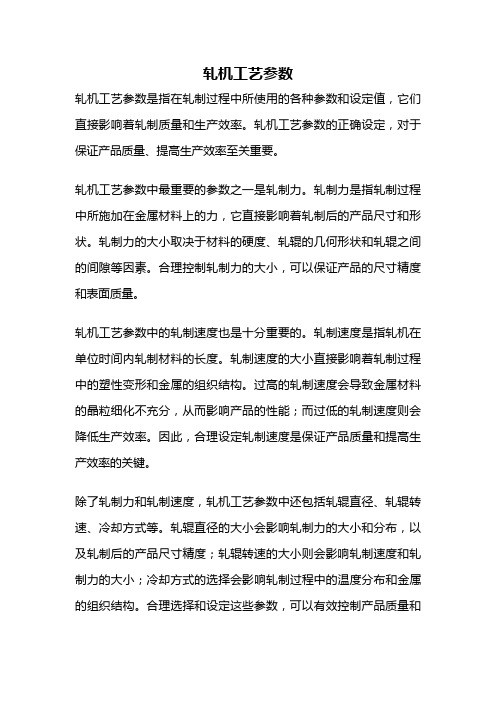
轧机工艺参数轧机工艺参数是指在轧制过程中所使用的各种参数和设定值,它们直接影响着轧制质量和生产效率。
轧机工艺参数的正确设定,对于保证产品质量、提高生产效率至关重要。
轧机工艺参数中最重要的参数之一是轧制力。
轧制力是指轧制过程中所施加在金属材料上的力,它直接影响着轧制后的产品尺寸和形状。
轧制力的大小取决于材料的硬度、轧辊的几何形状和轧辊之间的间隙等因素。
合理控制轧制力的大小,可以保证产品的尺寸精度和表面质量。
轧机工艺参数中的轧制速度也是十分重要的。
轧制速度是指轧机在单位时间内轧制材料的长度。
轧制速度的大小直接影响着轧制过程中的塑性变形和金属的组织结构。
过高的轧制速度会导致金属材料的晶粒细化不充分,从而影响产品的性能;而过低的轧制速度则会降低生产效率。
因此,合理设定轧制速度是保证产品质量和提高生产效率的关键。
除了轧制力和轧制速度,轧机工艺参数中还包括轧辊直径、轧辊转速、冷却方式等。
轧辊直径的大小会影响轧制力的大小和分布,以及轧制后的产品尺寸精度;轧辊转速的大小则会影响轧制速度和轧制力的大小;冷却方式的选择会影响轧制过程中的温度分布和金属的组织结构。
合理选择和设定这些参数,可以有效控制产品质量和生产效率。
轧机工艺参数的设定还要考虑到金属材料的性质和轧制目标。
不同的材料具有不同的塑性和硬度,因此需要根据具体材料的性质来设定轧机工艺参数。
同时,轧制目标也是设定轧机工艺参数的重要参考。
例如,如果要生产高强度的产品,就需要设定较大的轧制力和较低的轧制速度。
轧机工艺参数的正确设定对于保证产品质量和提高生产效率至关重要。
合理设定轧制力、轧制速度、轧辊直径、轧辊转速和冷却方式等参数,可以有效控制产品的尺寸精度、表面质量和金属的组织结构。
因此,在轧机生产中,必须重视轧机工艺参数的设定和调整,以提高产品质量和生产效率。
中厚板轧制规程

附录3:中板轧钢轧制工艺参数
表5
注意:(1)钢坯的降温和钢坯的表面积有关,轧薄规格降温要比轧厚规格的降温快,注意把握轧制节奏。
(2)粗轧转钢控制宽度的道次辊缝(也就是最后一道横轧道次辊缝)需要严格按照规程中规定辊缝值进行摆辊缝,否则会出现宽度超差,判为废品。
具体计算说明
(1)如果轧废,总分为系统检查分值;
(2)正钢坯常钢坯没有轧废,总分= 系统检查的分值+轧制时间得分+成本得分+粗轧规程选择得分+
粗轧异常工况正确处置得分+粗轧操作流程得分;
(3)需要跳过轧制钢坯,正确跳过,总分= 系统检查的分值+轧制时间得分+成本得分++粗轧规程选择得分+
粗轧异常工况正确处置得分+粗轧操作流程得分,这里轧制时间得分和成本得分都为单独项的满分。