镀金工艺发展分解
谈一谈电镀工艺发展历程与前景
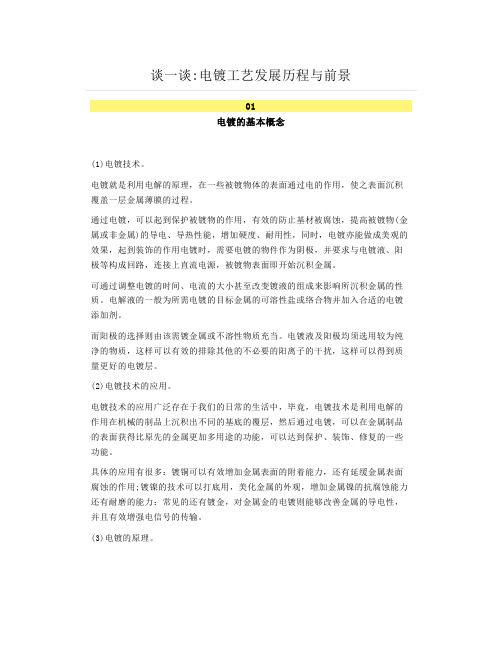
谈一谈:电镀工艺发展历程与前景01电镀的基本概念(1)电镀技术。
电镀就是利用电解的原理,在一些被镀物体的表面通过电的作用,使之表面沉积覆盖一层金属薄膜的过程。
通过电镀,可以起到保护被镀物的作用,有效的防止基材被腐蚀,提高被镀物(金属或非金属)的导电、导热性能,增加硬度、耐用性,同时,电镀亦能做成美观的效果,起到装饰的作用电镀时,需要电镀的物件作为阴极,并要求与电镀液、阳极等构成回路,连接上直流电源,被镀物表面即开始沉积金属。
可通过调整电镀的时间、电流的大小甚至改变镀液的组成来影响所沉积金属的性质。
电解液的一般为所需电镀的目标金属的可溶性盐或络合物并加入合适的电镀添加剂。
而阳极的选择则由该需镀金属或不溶性物质充当。
电镀液及阳极均须选用较为纯净的物质,这样可以有效的排除其他的不必要的阳离子的干扰,这样可以得到质量更好的电镀层。
(2)电镀技术的应用。
电镀技术的应用广泛存在于我们的日常的生活中,毕竟,电镀技术是利用电解的作用在机械的制品上沉积出不同的基底的覆层,然后通过电镀,可以在金属制品的表面获得比原先的金属更加多用途的功能,可以达到保护、装饰、修复的一些功能。
具体的应用有很多:镀铜可以有效增加金属表面的附着能力,还有延缓金属表面腐蚀的作用;镀镍的技术可以打底用,美化金属的外观,增加金属镍的抗腐蚀能力还有耐磨的能力:常见的还有镀金,对金属金的电镀则能够改善金属的导电性,并且有效增强电信号的传输。
(3)电镀的原理。
电镀的原理是在一种特殊的存有电镀液的容器中,经过溶液的特殊处理,使金属的表面得到一层镀层,在电流的阴阳两极的电位差的作用下,镀层的材料会比被电镀的金属材料更加质量好,更加的适用于社会生活。
电镀中,影响电镀的材料有电镀阳极的材质、电镀溶液的成分、温度、电流密度、通电时间、搅拌时间以及电流的波形等因素,每个因素都需要仔细的操作,避免出现差错。
(4)电镀的要素。
首先,电镀需要电镀的容器,即电镀槽,用来存放电镀的溶液,一般说来,电镀槽的材质都是高强度的、耐腐蚀的、并且耐高温的,适合储存化学溶液。
化学镀工艺简介

化学镀工艺简介化学镀是指在没有外电流通过的情况下,利用化学方法使溶液中的金属离子还原为金属并沉积在基体表面,形成镀层的一种表面加工技术。
被镀工件浸入镀液中,化学还原剂在溶液中提供电子使金属离子还原沉积在镀件表面,其反应式为M n++ne→M。
该过程是一个催化的还原过程,还原作用仅仅发生在催化表面上。
如果被镀金属本身是反应的催化剂,则化学镀的过程就具有自催化作用。
反应生成物本身对反应的催化作用,使反应不断继续下去,因此化学镀又称自催化镀(Auto catalytic plating)、无电解镀(Electroless plating)。
应当注意的是不能把化学镀与置换沉积相混淆,因为后者存在着基体金属的溶解。
此外,也不能把化学镀与均相的化学还原过程(如浸银)相混淆,因为此时沉积过程会发生在与溶液接触的所有物体上。
化学镀是在催化剂作用下,溶液中的金属离子被生长着的镀层表面所催化,不断地被还原,沉积在基体表面。
在这个过程基体表面的催化作用相当重要,元素周期表中的Ⅷ族金属元素都具有化学镀过程中所需的催化效应。
金属离子与还原剂在镀液中同时存在,是处于热力学的不稳定状态。
选择使金属离子趋于稳定的强络合剂对提高镀液稳定性有利,但使沉积速度降低。
选择适当的络合剂可控制稳定性和沉积速度,改善镀层光亮度和耐蚀性,同时还能改变还原反应的活化能,实现低温施镀。
酸性镀液常用的络合剂有乳酸、氨基乙酸、羟基乙酸、柠檬酸、苹果酸、酒石酸、硼酸、水杨酸等。
碱性镀液常用的络合剂有氯化铵、醋酸铵、柠檬酸铵和焦磷酸铵等。
化学镀的络合剂正向复合应用方向发展。
若被镀材料不具备自动催化作用,如塑料、陶瓷等非金属材料,还需经过前处理,使镀面活化后再进行化学镀。
在施镀过程中,因种种原因不可避免地在镀液中产生活性的结晶核心,致使镀液自行分解而失效,稳定剂可对活性结晶核心进行掩蔽,达到防止镀液分解的目的。
常用的稳定剂有铅离子、硫脲、锡的硫化物、硫代硫酸盐、铝酸盐和碘酸盐等。
线路板镀金工艺流程

线路板镀金工艺流程
线路板镀金工艺流程一般包括以下几个步骤:
1. 表面处理:首先需要对线路板的表面进行处理,以便提供一个良好的基底。
常用的表面处理方法有机械化处理、化学处理和电化学处理。
2. 防腐蚀处理:将线路板浸泡在硫酸铜溶液中,以防止线路板表面产生氧化层。
3. 清洗:使用溶剂或水洗去线路板上的污垢和残留物,以保证金属表面的洁净度。
4. 化学镀铜:将线路板浸泡在化学镀铜液中,通过化学反应使线路板表面镀上一层铜。
5. 光刻:将线路板上的光刻胶涂敷在金属表面上,然后使用光源照射,通过光刻胶的固化和显影步骤,保留下所需的线路图案。
6. 金属化处理:将线路板浸泡在金属化液中,使显影后的线路部分表面镀上一层金属,一般使用电镀法进行。
7. 镀金:将线路板浸泡在金电镀液中,通过电化学反应使线路板表面镀上一层金。
8. 清洗:清洗镀金后的线路板,以去除任何残留物和碱性物质,
准备下一个步骤。
9. 检查:对镀金后的线路板进行检查,以确保无任何缺陷或损伤。
10. 包装:将镀金后的线路板进行包装,以保护其表面免受污染和机械损伤。
需要注意的是,上述工艺流程仅为一般性流程,具体的工艺步骤和参数可能会因不同的行业或产品要求而有所不同。
此外,镀金工艺一般需要在专门的工厂或生产线上进行,需要具备相应的设备和技术。
铜镀金电镀工艺与制作技术分享

铜镀金电镀工艺与制作技术分享1. 简介铜镀金是一种常用的表面处理工艺,用于美化和保护物体的表面。
它涉及在物体表面覆盖一层薄薄的金属镀层,通常是铜与金属相结合。
铜镀金既能提供金属的高光泽度和金色外观,又能增加物体的耐腐蚀性和耐磨性。
本文将分享铜镀金的工艺流程、常见的制作技术以及其在不同领域的应用。
2. 铜镀金工艺流程铜镀金的工艺流程包括以下几个步骤:2.1 清洗和预处理在进行铜镀金之前,物体的表面必须经过彻底的清洗和预处理,以去除污垢、氧化物和其他杂质。
常用的清洗方法包括碱性清洗、酸洗和电解清洗。
清洗后,物体表面将变得清洁,有利于金属镀层的附着性和均匀性。
2.2 铜镀层的制备在制备铜镀层前,物体的表面需要涂覆一层铜基底层,通常使用静电沉积或化学沉积的方法进行。
铜基底层有助于提高铜镀层的附着力和平滑度,并提供一个良好的导电层。
2.3 电镀铜电镀铜是铜镀金的关键步骤。
在铜镀液中,通过电解的方式,在待镀物体表面上沉积一层均匀的铜层。
电镀铜可以使用钝化法、电解沉积法或包覆法等不同的方法进行。
其中,阳极氧化法是最常用的技术之一。
在电镀过程中,要控制镀液的温度、电压和电流密度等参数,以确保铜层的质量和厚度符合要求。
2.4 镀金层的制备铜层完成后,需要在其表面上镀覆一层薄薄的金属层,通常选择金或金合金。
金层的厚度可以根据需求进行调节,一般在几微米至数十微米之间。
镀金层不仅赋予物体金色的外观,还提供了更高的耐腐蚀和耐磨性。
3. 铜镀金的制作技术3.1 真空金属化技术真空金属化技术是一种常用的制作镀金层的技术。
它通过在真空环境中蒸发金属,使其在待镀物体表面沉积形成金层。
这种技术具有制备金属层均匀、致密和光滑的优点。
真空金属化技术可以实现高质量的铜镀金,适用于精密仪器、珠宝和装饰品等领域。
3.2 浸镀技术浸镀技术是一种实现金属镀层的简单方法。
它通过将含有金属离子的溶液浸泡在待镀物体中,使金属离子还原并沉积在物体表面形成金层。
金属镀金工艺

金属镀金工艺
金属镀金工艺是一种将金属表面涂覆一层金属(通常是金)的过程。
镀金工艺可以增加金属制品的美观度,提高耐腐蚀性和耐磨性,同时也可以增加金属制品的价值。
金属镀金工艺主要分为电镀和化学镀金两种。
电镀是通过直流电流将金属离子转移到工件表面上形成金属镀层的过程。
在电镀过程中,金属离子通过电解液中的阳极由阴极释放,形成金属镀层。
电镀常用的金属包括金、银、铜、镍等。
电镀工艺需要特殊的设备和溶液来完成。
化学镀金是通过化学反应将金属镀层沉积在金属表面上的过程。
与电镀相比,化学镀金不需要电流,而是通过特定的化学物质和反应条件来实现金属镀层的沉积。
化学镀金可以在大多数金属表面上实现金属镀层,包括铜、银、金、铝等。
金属镀金工艺在很多领域中得到了广泛应用,包括珠宝、饰品、钟表、器皿等。
镀金工艺可以改善产品的外观和质感,使产品更加独特和吸引人。
同时,金属镀金也有助于保护金属制品表面,延长其使用寿命。
钼铜合金镀金工艺流程

钼铜合金镀金工艺流程《钼铜合金镀金工艺流程:一场金属变身的奇妙之旅嘿,大家好呀!今天咱就来唠唠这个钼铜合金镀金的工艺流程,这可真是个超级有趣又神秘的事儿呢。
首先得把钼铜合金好好收拾一下,就像给即将参加华丽舞会的姑娘洗脸一样。
这个清洁的过程可不能马虎,得把合金表面的脏东西、油脂啥的统统赶走。
这就好比不把脸上的灰尘洗干净,再漂亮的妆容也涂不均匀不是?可以用专门的化学试剂来清洗,看着那些脏东西一点点消失,合金表面变得光亮起来,就像给它进行了一场“洁面spa”。
接下来就是准备镀金的“魔法药水”了。
这个镀金溶液啊,就像是能让金属变身的神奇魔药。
里面含着金离子啊,像一个个微小的金色精灵,正等着附着到钼铜合金上面呢。
可这金离子好不好附着还是个问题,因为钼铜合金它有自己的小脾气。
然后就到了关键的镀金环节啦。
通常会用电镀的方法,就像用魔法棒引导金离子搬家到钼铜合金上一样。
电极一接通,电流就像小邮差,载着金离子哼着小曲儿就朝着合金奔去。
看那金离子一层一层地在合金上堆积起来,就像是给钼铜合金穿上了一件金色的铠甲,超级帅!不过在这个过程中,可得控制好电流大小呢,要是电流太大,那金离子可就跟疯了一样,说不定都把铠甲涂得歪七扭八,就像新手画家乱涂鸦;要是电流太小,金离子就像懒虫,好久才能铺上一点点金,那得多耽误功夫啊。
镀完金后也不是就大功告成了。
还得像检查艺术品一样把镀金后的工件仔仔细细检查一遍。
看看有没有镀金不均匀的地方,就像检查衣服有没有掉色一样。
要是发现哪个小角落的金色不够亮或者有点薄,还得进行修补呢,就像给小女孩补补裙子上的破洞。
总的来说,钼铜合金镀金这工艺流程就像是一场紧张刺激、又充满惊喜的冒险。
就好比我们把一个普通的小石子,经过一道道神奇的工序,变成了闪闪发光的金石子一样。
它既有精准科的学性,就像一个严谨的老学究,要求每个步骤都不能出错,又像是一场充满创意和惊喜的魔法表演,只要过程中有一点小变化,就可能让最终的“金色造型”不一样。
pcb镀金工艺流程

pcb镀金工艺流程PCB镀金工艺流程PCB(Printed Circuit Board)是电子产品中不可或缺的一部分,而PCB镀金工艺则是为了提高PCB的导电性和耐腐蚀性,同时也起到美观的作用。
下面将介绍PCB镀金的整个工艺流程。
1. PCB表面处理PCB在进行镀金之前,需要进行表面处理,以保证金属层与基板之间的黏附性。
常用的表面处理方法包括化学镀铜、化学镀镍、电镀铜等。
这些处理方法能够清除表面的氧化物、污染物和其他不良物质,提高金属层的附着力。
2. 清洗清洗是PCB镀金过程中非常重要的一步,其目的是去除表面的污染物和残留物,保证金属层的质量。
常见的清洗方法有化学清洗、超声波清洗等。
清洗剂的选择应根据具体的PCB材料和表面处理方法进行,以避免对基板造成损害。
3. 化学镀镍化学镀镍是PCB镀金工艺中的一种重要步骤,其主要作用是在PCB 表面形成一层镍层,以提高PCB的耐腐蚀性和导电性。
化学镀镍的工艺流程包括预处理、酸洗、活化、镀镍等步骤。
在镀镍过程中,需要控制好镀液的温度、PH值和镀液中镍盐的浓度,以保证镀层的质量和均匀度。
4. 化学镀金在完成化学镀镍后,需要进行化学镀金,以在镀镍层上形成一层金属层,提高PCB的导电性和美观性。
化学镀金的工艺流程包括预处理、酸洗、活化、镀金等步骤。
在镀金过程中,需要控制好镀液的温度、PH值和镀液中金盐的浓度,以保证镀层的质量和均匀度。
5. 电镀保护层为了保护镀金层,防止氧化和腐蚀,需要在镀金层上进行电镀保护层的处理。
常见的保护层材料有有机保护漆和无机保护层。
有机保护漆是一种涂覆在镀金层表面的保护层,能够有效防止氧化和腐蚀。
无机保护层则是通过热处理在镀金层表面形成一层氧化层,起到保护作用。
6. 检测和质量控制在完成PCB镀金工艺后,需要进行质量检测,以确保镀金层的质量和均匀度。
常见的检测方法包括显微镜检测、X射线检测和化学分析等。
同时,还需要进行质量控制,对每一批次的PCB进行严格的检查和测试,以确保其符合相关标准和要求。
镀金工艺发展分解

镀金工艺发展分解镀金1.概述金是一种黄色的贵金属,有极好的延展性及可塑性,易抛光。
金的化学稳定性高,不溶于一般酸,只溶于王水、氰化钾和氰化钠溶液。
镀金层耐腐蚀性强、导电良好、能耐高温和容易焊接。
在普通镀金溶液中,加人少量锑、钴等金属离子,可以获得硬度大于130HV 的硬金镀层。
如含金(质量分数)为5%的合金镀层,硬度可以达到200HV以上,金铜合金镀层的硬度可达300HV以上,具有一定的耐磨性。
金镀层抗变色性能好,还可作为银的防变色镀层。
由于金合金镀层色调丰富,光泽持久,所以常用于首饰、艺术品的电镀。
另外,镀金层还被广泛用于通信设备、宇航工业、工业设备和精密仪器仪表等设备制造中[1]。
常用的镀金溶液主要有三种类型,即氰化物镀金溶液、柠檬酸盐酸性镀金溶液和亚硫酸盐碱性镀金溶液。
在某些普通镀金溶液中,添加少量锑、镍、钴等金属离子,可以得到硬金镀层,使其硬度提高1—2倍。
为了节约金的用量和增加色调,提高光泽、硬度和耐磨性能等,满足工业生产中的某些特殊要求,还可以在镀金溶液中添加一定量的银、铜、镍、钴等金属化合物,得到金合金镀层。
2.镀金的发展史电镀黄金的历史非常悠久,早在17世纪就有了雷酸液镀金的方法,真正的电镀黄金是1800年Brugnatalli 的工作。
1838年,英国伯明翰的G.Elkington和H.Elkington兄弟发明了高温碱性氰化物镀金,并取得了专利。
它后来被广泛用于装饰品、餐具和钟表的装饰性镀薄金,成了以后一个世纪中电镀黄金的主要技术。
其作用的基本原理到了1913年才为Fray所阐明,到1966年Raub才把亚金氰络盐的行为解释清楚。
在电镀金历史上第一次革命性的变革是酸性镀金液被开发出来。
早在1847年时,Derulz曾冒险在酸性氯化金溶液中添加氢氰酸,发现可以在短时间内获得良好的镀层。
后来Erhardt发现在弱有机酸(如柠檬酸)存在时,氰化亚金钾在pH= 3时仍十分稳定,于是酸性镀金工艺就诞生了。
滚镀金线工艺流程ppt课件

连续过滤/每天 碳处理
1-3/120g/l
连续过滤/每星 期碳处理
回收水
无
无
水
无
无
纯水
无
无
纯水
无
无
无
精选课无件
无
更换周期 700-900KG 700-900KG 700-900KG 1400-1800 1400-1800
两天 1400-1800
无
无 700-900KG
无
无
无 1400-1800 1400-1800 1400-1800
无
备注
50-70℃ 50-70℃
50-70℃
电压:9.15v, 时间:30min
补镍缸水位用 22-28℃ 电压:12 时间:10S
电压:6.55v; 时间:15s 温度
22-28℃ 收集统一处理
5
超声波
超声波原理:
超声波由发生器和振子组成。发生器是产生电磁 振荡信号和提供能量的电源,振子是把发生器产生 的电磁振荡电流转换成超声震动的换能器。零件浸 泡在除油液中,超声波产生机械荡力,形成数以万 计的微小气泡。这些小气泡在生成,生长和破裂时 产生强大的机械力,使黏附在金属表面的油污被剥 离下来,油污在浮力作用下浮出水面。超声波槽体 用于接收超声震动,采用不锈钢材质,并有一定厚 度。
精选课件
6
化学除油
化学除油分为皂化和乳化反应达到除油效果: 1、皂化作用:金属表面油脂中的动植物油(主要成分是硬脂酸)
与碱性除油剂中的碱生成硬脂酸钠(即肥皂)和甘油溶解进入 碱性溶液,俗称“皂化反应”。从而达到除去金属表面的油脂。 2、乳化作用:矿物油或其它不可皂化油是不能用碱皂化的,此时 采用表面活性剂进行乳化除油,乳化是使两种互不相溶液体中 的一种呈极细小的液滴分散在另一种液体中形成乳浊液的过程, 具有乳化作用的表面活性物质为乳化剂,在化学除油的过程中 采用阳离子型或非离子型表面活性剂,如硅酸钠、硬脂酸钠、 OP乳化剂等,在除油的过程中,首先乳化剂吸附在油溶液的分 界面上,其中亲油基与零件表面的油发生亲种作用,而亲水基 则与除油水溶液亲和,在乳化剂的作用下,油污对零件表面的 附着力逐渐减弱,在流体的动力因素共同的作用下,油污破裂 变成细小的珠状逐渐从金属零件表面脱离,而呈细小的液滴分 散在除油液中,变成乳蚀液,从而达到除去零件表面油污的效 果。皂化和乳化作用是相互相成的。
接插件端子连续选择性镀金工艺的发展趋势

摘 要 : 插件 端 子连 续选择 性镀 金 工 艺技 术 的发展 趋 势 , 接 主要 是 围绕提 高镀 金 层技 术质 量 , 降低 镀
金 成本 。介 绍 了在 端子镀 金 前 处理 工序 中, 增加 化 学抛光 或 电化 学抛 光 以及 预镀 工 艺等 , 高端子 提 基材 表 面光 亮度 , 改善镀 金层 的外观 质 量。 开发新 的镀金 中间阻挡 层 和 应 用 中间 阻挡 层 组 合 工 来
艺技 术 , 少镀金 中间 阻挡 层 孔 隙 , 高 阻挡 层致 密性. 减 提 防止 铜 合金 基 材 金 属扩 散 迁移 到镀 金 层表
面。介 绍 了镀 金新 添加 剂 应 用 , 防沉 积 ( 换 ) 如 置 的微 酸性镀 金 、 自封 孔 的微 酸性 镀 金 、 钴合 金 镀金
工 艺等 。应 用 防变 色保 护 剂 降低 镀金 层 厚度 。介 绍 了应 用环保 新材料 丙 尔金 替代 有毒 氰化 亚金钾
镀金 工 艺 。
关
键
词: 镀金 前 处理 ;阻挡层 ;镀金 新 添加 剂 ; 插件 端 子 ;选择 性镀金 接
文献标 识码 :A
中 图分类 号 : Q 5 .8 T 1 3 1
v l p e tTr n s o n i u u e e tv l a i g e o m n e d f Co t o s S lc i e Go d Pl tn n Te h i u s f r Co n c o s c n q e o n e t r
ZHANG n - u n Ro g g a g,HUANG o Ha
( h n d o g n h ag i T c .C . t. C e g u6 0 9 , hn ) C e g uH nmigS u n x eh o ,Ld , h n d 10 1 C ia n
半导体集成电路行业电镀工艺解析

半导体集成电路行业电镀工艺解析金镀层具有接触电阻低、导电性能好、可焊性好、耐腐蚀性强,因而电镀金在集成电路制造中有着广泛的应用,例如:在驱动IC封装中普遍使用电镀金凸块;在CMOS/MEMS中应用电镀金来制作开关触点和各种结构等;在雷达上金镀层作为气桥被应用;电镀还被用于UBM阻挡层的保护层,以及用于各种引线键合的键合面等等。
1电镀金工艺1.1电镀金工艺流程集成电路中的金电镀工艺流程:①在硅片上溅射钛、钛钨等金属作为黏附层,再溅射很薄的一层金作为电镀的导电层;②涂布光刻胶,光刻显影出电镀所需的图形;③清洗后进行电镀金;④褪除光刻胶;⑤蚀刻图形以外的导电层;,⑥退火。
1.2电镀金原理镀金阳极一般采用铂金钛网材料。
当电源加在铂金钛网(阳极)和硅片(阴极)之间时,溶液会产生电流,并形成电场。
阳极发生氧化反应释放出电子,同时阴极得到电子发生还原反应。
阴极附近的络合态金离子与电子结合,以金原子的形式沉积在硅片表面。
镀液中的络合态金离子在外加电场的作用,向阴极定向移动并补充阴极附近的浓度消耗,如图1为水平杯镀示意图,图2为垂直挂镀示意图。
电镀的主要目的是在硅片上沉积一层致密、均匀、无孔洞、无缝隙、无其它缺陷的金。
1.3电镀药水集成电路电镀金工艺通常有两种体系的电镀液:氰化物体系及非氰化物体系。
氰化物体系稳定性高,寿命长,因而成本较低,但氰化物有毒性,需有严格的使用规范加以管理。
目前集成电路制造中常见的氰化物电镀金药水是微氰体系,呈弱酸性,镀液中金以Au(CN)-2的络合物形式存在。
主要成分为:金盐、导电盐、缓冲剂和添加剂。
这种镀液体系稳定,毒性较小,镀层光亮平滑,硬度适中,耐磨性好,孔隙率低,可焊性好。
非氰化物体系的以亚硫酸金钠为常见的金盐,亚硫酸根比较容易被氧化,因而较之氰化物体系,其工艺稳定要差一些。
本文主要针对氰化物体系的电镀金工艺。
1.4电镀金设备选择合适的电镀设备,将会获得较为满意的镀层。
电镀设备可分为二类:水平喷流式杯镀和垂直挂镀两种方式。
铝镀金工艺流程
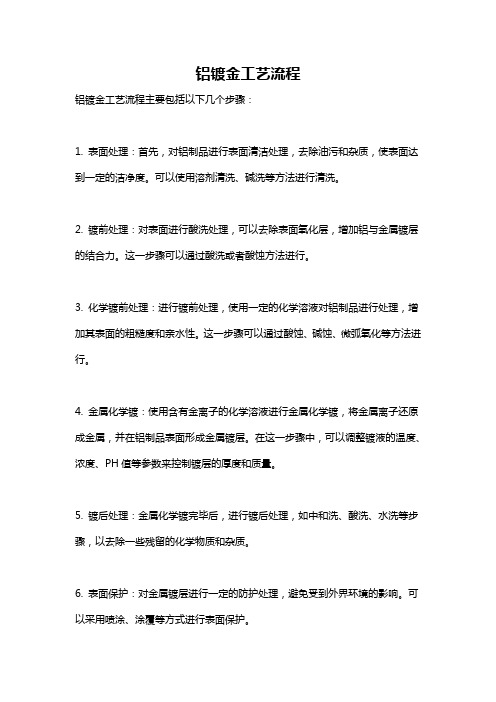
铝镀金工艺流程
铝镀金工艺流程主要包括以下几个步骤:
1. 表面处理:首先,对铝制品进行表面清洁处理,去除油污和杂质,使表面达到一定的洁净度。
可以使用溶剂清洗、碱洗等方法进行清洗。
2. 镀前处理:对表面进行酸洗处理,可以去除表面氧化层,增加铝与金属镀层的结合力。
这一步骤可以通过酸洗或者酸蚀方法进行。
3. 化学镀前处理:进行镀前处理,使用一定的化学溶液对铝制品进行处理,增加其表面的粗糙度和亲水性。
这一步骤可以通过酸蚀、碱蚀、微弧氧化等方法进行。
4. 金属化学镀:使用含有金离子的化学溶液进行金属化学镀,将金属离子还原成金属,并在铝制品表面形成金属镀层。
在这一步骤中,可以调整镀液的温度、浓度、PH值等参数来控制镀层的厚度和质量。
5. 镀后处理:金属化学镀完毕后,进行镀后处理,如中和洗、酸洗、水洗等步骤,以去除一些残留的化学物质和杂质。
6. 表面保护:对金属镀层进行一定的防护处理,避免受到外界环境的影响。
可以采用喷涂、涂覆等方式进行表面保护。
以上就是铝镀金工艺流程的基本步骤,每个工艺流程的具体操作细节会有所不同,可以根据具体需要进行调整和改进。
电镀发展趋势
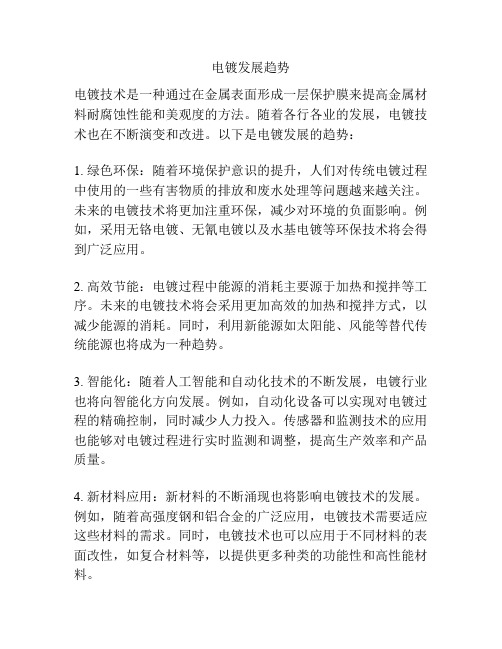
电镀发展趋势电镀技术是一种通过在金属表面形成一层保护膜来提高金属材料耐腐蚀性能和美观度的方法。
随着各行各业的发展,电镀技术也在不断演变和改进。
以下是电镀发展的趋势:1. 绿色环保:随着环境保护意识的提升,人们对传统电镀过程中使用的一些有害物质的排放和废水处理等问题越来越关注。
未来的电镀技术将更加注重环保,减少对环境的负面影响。
例如,采用无铬电镀、无氰电镀以及水基电镀等环保技术将会得到广泛应用。
2. 高效节能:电镀过程中能源的消耗主要源于加热和搅拌等工序。
未来的电镀技术将会采用更加高效的加热和搅拌方式,以减少能源的消耗。
同时,利用新能源如太阳能、风能等替代传统能源也将成为一种趋势。
3. 智能化:随着人工智能和自动化技术的不断发展,电镀行业也将向智能化方向发展。
例如,自动化设备可以实现对电镀过程的精确控制,同时减少人力投入。
传感器和监测技术的应用也能够对电镀过程进行实时监测和调整,提高生产效率和产品质量。
4. 新材料应用:新材料的不断涌现也将影响电镀技术的发展。
例如,随着高强度钢和铝合金的广泛应用,电镀技术需要适应这些材料的需求。
同时,电镀技术也可以应用于不同材料的表面改性,如复合材料等,以提供更多种类的功能性和高性能材料。
5. 细化和微观化:随着微电子技术和纳米技术的发展,电子设备和零部件的尺寸越来越小,对电镀技术的要求也更加严格。
未来的电镀技术需要不断提高对微小尺寸和复杂形状的表面进行镀层的能力,以满足不同领域对精密度和性能要求的不断提高。
总之,未来的电镀技术将更加注重环保、高效节能、智能化以及新材料和微观领域的应用。
这些趋势将推动电镀技术不断向前发展,提供更多样化和高品质的电镀产品。
同时,也需要在技术研发和产业转型方面加大投入力度,以满足市场需求和推动电镀行业的可持续发展。
电镀合金工艺的历史与发展进程概述

电镀合金工艺的历史与发展进程概述大约在1853--1845年期间,研究电镀合金的文献开始陆续发表,最早得到的是电镀贵金属合金(如金,银的合金,主要以装饰为目的)和电镀铜锌合金(即黄铜)。
劳尔兹(Ruolz)用电沉积的方法得到黄铜和青铜。
1942年他发表了与现代电镀青铜相似的电镀溶液,主要成份包括氰化亚铜和锡酸盐。
在1850-1883年间,美国和英国大约发表了380篇关于电镀的专利,其中近30篇是电镀合金方面的,包括电镀黄铜,青铜以及金基和银基合金等,电镀青铜的专著是1870年前发表的。
大量应用于工业化生产,而主要使用的是电镀黄铜。
1925年施尔策(Spitzer)在电化学杂志上发表了电镀黄铜及其电沉积理论的文章。
1910年法尔德(Fild)发表了两篇电镀合金的专论:一篇是电镀黄铜,另一篇是电镀铜银合金。
1916年有人研究了电镀的沉积电位及工艺条件对沉积合金组成的影响,并用量显微镜观察了电沉积层的组织结构。
霍因(Hoing)在1910-1920年间系统地研究了电镀黄铜及其镀液性能,同时,布卢姆(Blum)等研究了电沉积铅锡合金及其镀液性能。
1925-1929年间金属学家用X射线研究了电沉积合金的结构,他们发现用电沉积得到的合金镀层结构与热熔法得到的合金结构相类似。
自1930年以后,加快了电沉积合金的发展速度,1936年一个重要的进展即电镀光亮镍钴合金被开发,并在工业生产上得到了应用,电镀铅锡合金进一步推广且应用于轴承。
福斯特(Faust)等人得到了含铜,镍,锑和铬的电沉积合金。
1950年后,美国布伦纳(Brenner)等人系统地研究了铁族金属(铁,钴和镍)与钨,磷生成的合金。
在英国研究了以锡为基与镍铜锑的合金。
在苏联主要研究了含锰,钨,钼,铬与其它金属组成的合金我,还有轴承合金以及电沉积合金的添加剂。
劳布(Raub)教授的研究所用了15年产时间,发表了20篇有关电镀合金的文章,研究的范围包括电镀合金工艺,电镀条件对合金组成的影响,测定合金镀层的性质,并用金相法和X射线研究了合金镀层的结构。
铜表面镀金的工艺手段

铜表面镀金的工艺手段铜表面镀金的工艺手段铜是一种常见且广泛应用的金属材料,具有良好的电导率和导热性能。
然而,铜的外观容易被氧化和腐蚀,影响其美观以及性能稳定性。
为了保护铜表面并赋予其更加高贵的外观,人们发展了多种镀金工艺手段。
本文将深入探讨铜表面镀金的工艺手段以及其应用。
一、电镀1. 鍍金金是一种常用的镀金材料,具有高度的电导率和耐腐蚀性。
通过电镀工艺,可以在铜表面形成均匀的金层。
该工艺需要使用金盐溶液和电镀设备。
将铜部件作为阴极浸泡在金盐溶液中,同时将金作为阳极。
通过电流的作用,金离子会在铜表面沉积形成金层。
此方法可以提供持久的镀层,并赋予铜部件更高的价值和美观度。
2. 镍镀金镍镀金是另一种常见的电镀方法。
与直接电镀金相比,镍镀金可提供更好的耐磨性和耐腐蚀性。
该工艺需要先在铜表面镀一层镍,然后再进行金层的电镀。
这样可以在保护铜表面的同时赋予其金色的外观。
镍镀金广泛应用于装饰品、首饰以及电子元件等领域。
3. 银镀金银是另一种常用的镀金材料,具有良好的导电性和导热性。
银镀金可以在铜表面形成一层均匀的银层,赋予铜部件高端大气的外观。
银镀金常用于制造高品质的音频设备、电子元件以及精密仪器。
二、化学方法1. 化学氧化法化学氧化法是一种常见的对铜表面进行金属镀膜的方法。
该方法利用还原剂和金属盐溶液,使金属得以还原并在铜表面形成薄膜。
这种膜可以提供镀金的效果,并具有保护铜表面的作用。
2. 化学还原法化学还原法是一种通过化学反应在铜表面生成金属层的方法。
通常使用含有金属离子的溶液,如氰化金溶液。
在溶液中,金属离子会还原并在铜表面生成金属镀层。
三、机械方法1. 真空镀膜真空镀膜是一种在无氧环境下进行的镀膜工艺。
铜部件首先被放置在真空室中,然后蒸发或溅射金属,使金属蒸汽在铜表面沉积。
这种方法可以形成均匀且致密的金属镀层,并具有较高的附着力。
2. 热压镀金热压镀金利用高温和压力使金箔与铜表面结合。
在工艺中,金箔被放置在铜表面上,然后通过加热和压力使其与铜表面结合。
镀金工艺流程

镀金工艺流程
1.基材表面处理:基材表面必须干净、平整,无任何杂质和油污,否则将影响镀层的质量和附着力。
常用的基材有铜、银、钢、铝等。
2. 镀前清洗:将基材放入镀前清洗槽中,用酸性清洗剂进行清洗,去除表面氧化物和杂质,使基材表面光洁。
3. 镀层预处理:预处理是镀金工艺中非常重要的一步,直接影响到金属电镀层的质量和附着力。
常用的预处理方法有酸洗、酸性铜化、镀铜等。
4. 金属电镀:将经过预处理的基材放入电镀槽中,进行电镀加工。
金属电镀主要使用的金属有镍、铬、金等。
在电镀过程中,需要控制电流密度、电解液浓度、电解液温度等参数,以保证电镀层质量。
5. 镀后处理:镀后处理包括清洗、烘干、抛光等步骤。
这些步骤能够提高金属电镀层的表面光洁度和抗腐蚀性能。
- 1 -。
铝合金镀镍金工艺流程

铝合金镀镍金工艺流程一、铝合金的前期处理。
铝合金在镀镍金之前呀,得好好洗个澡,把表面的脏东西都去掉。
这就像是我们出门要洗脸一样,铝合金的表面可能会有油污啦、灰尘啦,还有可能有一些氧化层。
那怎么去除这些呢?通常会用到化学试剂,就像用特别的洗面奶一样。
比如说用碱液来去除油污,这碱液就像一个强力清洁小助手,把油污一点点分解掉。
然后呢,对于氧化层,可能会用到酸液来处理,不过这个过程可得小心哦,就像我们给皮肤去角质不能太用力一样。
把铝合金表面处理得干干净净的,这样后续的镀层才能更好地附着在上面呢。
二、镀镍的步骤。
接下来就到镀镍这个环节啦。
镀镍就像是给铝合金先穿上一层银色的打底衫。
这时候要把铝合金放到专门的镀镍溶液里,这个溶液里有镍离子呢。
然后通过电的魔法,让镍离子跑到铝合金的表面,一层一层地堆积起来。
这个过程就像是小蚂蚁搬家一样,镍离子一个一个地在铝合金表面安家落户,慢慢地就形成了一层镍的镀层。
在这个过程中呀,镀镍溶液的成分和温度可是很关键的哦。
溶液的成分要调配得刚刚好,就像我们做菜放盐要适量一样。
温度呢,也得控制在合适的范围,不然镍离子就会像调皮的小孩子,不好好听话,可能就不能均匀地在铝合金表面沉积了。
三、镀金的步骤。
等镍层镀好之后,就到了更闪亮的镀金环节啦。
镀金就像是给已经穿上银色打底衫的铝合金再披上一件金色的外套。
这个镀金的溶液里当然就含有金离子啦。
同样也是利用电的力量,让金离子跑到镍层的表面。
金离子可比镍离子要金贵多啦,就像金子本身就很贵重一样。
镀金的时候要特别注意镀金层的厚度,太薄了不美观也不耐用,太厚了又浪费。
而且镀金的过程中也要关注溶液的状态,确保金离子能够均匀地覆盖在镍层上,这样镀出来的铝合金就会金光闪闪的,超级好看呢。
四、镀后处理。
最后呀,镀完镍金之后,铝合金还不能马上就去“见人”哦。
还得进行一些后处理。
比如说清洗,把在镀镍金过程中残留在铝合金表面的溶液清洗掉,不然这些溶液就像小尾巴一样,留在上面可不好看也不卫生。
镀金工艺的发展简介

镀金工艺的发展简介
2016-04-14 12:31来源:内江洛伯尔材料科技有限公司作者:研发部
早期镀金电镀金工艺最早可以追溯到1805年意大利科学家Brougnatell教授的研究。
此后的100多年间,欧洲盛行电镀镍、铜、黄铜,仅少数电镀厂为了满足富人的需要而进行钟表、随身装饰品、金属餐具等的镀金。
与此同时,美国进行的主要是与珠宝精细加工有关的镀金。
1913年,Frary建立了比较全面的电镀金体系,开创了现代电镀的先河。
1950年,Rinker最早开发了镀金电镀液中添加微量银的光亮电镀金技术。
20世纪40年代电子工业发展,金价暴涨,大都采用镀薄金。
为了进一步节约金,20世纪60年代出现了刷镀金(即选择性镀金),20世纪80年代出现了脉冲镀金和镭射镀金。
1952年,Parker开创了氰化亚金钾的应用,报道了氰化亚金钾在添加弱有机酸(如柠檬酸、酒石酸)中的稳定性,进而出现了中性和弱酸性镀金液;20世纪60年代后期无氰镀金也得到了应用,尤其是以亚硫酸盐镀金应用最广。
目前,常用的镀金溶液可分为碱性氰化物、酸性微氰、中性微氰和非氰化物4类。
镀金液多为专利配方,添加剂由专业公司供应。
铜表面镀金工艺

铜表面镀金工艺一、前处理1. 去油:将铜表面的油污、灰尘等杂质清洗干净,以防止影响镀层的附着力。
2. 酸洗:使用酸性溶液将铜表面氧化物去除,使得表面更加光滑。
3. 洗涤:将酸洗后的铜表面用水冲洗干净,以去除酸性残留物。
二、镀金工艺1. 镀底层:首先,在铜表面涂上一层镍或铬底层,以增强镀金层与基材之间的附着力。
2. 镀金层:采用电解法进行镀金。
将含有金离子的电解液放入电解槽中,然后在阳极上放置纯金片。
通过施加电流,在铜基材上沉积出一层薄薄的金属镀层。
可调节电流密度、温度和时间等参数来控制镀层厚度和光泽度。
3. 后处理:经过镀金后,需要进行后处理以增强耐腐蚀性能和美观度。
其中包括:(1)洗涤:将镀金后的铜表面用水冲洗干净,以去除电解液残留物。
(2)抛光:使用抛光机器或手工对镀金层进行抛光,使其表面更加光滑。
(3)清漆:在镀金层上喷涂一层透明清漆,以保护镀层不受氧化或刮擦影响。
三、质量检测1. 外观检查:对铜表面的镀金层进行外观检查,包括颜色、厚度、均匀性等方面。
2. 腐蚀测试:将镀金后的铜样品浸泡在盐酸溶液中,观察其腐蚀情况。
如果出现氧化或者剥落等情况,则说明镀金质量不合格。
3. 附着力测试:采用划格法或者剥离法来测试镀金层与基材之间的附着力。
如果出现剥离现象,则说明附着力不够强。
四、注意事项1. 操作人员必须穿戴防护服和手套等防护用品,以保证安全。
2. 在操作过程中必须注意电流密度、温度和时间等参数的控制,以保证镀层的厚度和光泽度。
3. 酸洗过程中要注意安全,避免酸性溶液溅到皮肤或眼睛等部位。
4. 在操作过程中要注意环保问题,如电解液的回收和处理等。
- 1、下载文档前请自行甄别文档内容的完整性,平台不提供额外的编辑、内容补充、找答案等附加服务。
- 2、"仅部分预览"的文档,不可在线预览部分如存在完整性等问题,可反馈申请退款(可完整预览的文档不适用该条件!)。
- 3、如文档侵犯您的权益,请联系客服反馈,我们会尽快为您处理(人工客服工作时间:9:00-18:30)。
镀金1.概述金是一种黄色的贵金属,有极好的延展性及可塑性,易抛光。
金的化学稳定性高,不溶于一般酸,只溶于王水、氰化钾和氰化钠溶液。
镀金层耐腐蚀性强、导电良好、能耐高温和容易焊接。
在普通镀金溶液中,加人少量锑、钴等金属离子,可以获得硬度大于130HV 的硬金镀层。
如含金(质量分数)为5%的合金镀层,硬度可以达到200HV以上,金铜合金镀层的硬度可达300HV以上,具有一定的耐磨性。
金镀层抗变色性能好,还可作为银的防变色镀层。
由于金合金镀层色调丰富,光泽持久,所以常用于首饰、艺术品的电镀。
另外,镀金层还被广泛用于通信设备、宇航工业、工业设备和精密仪器仪表等设备制造中[1]。
常用的镀金溶液主要有三种类型,即氰化物镀金溶液、柠檬酸盐酸性镀金溶液和亚硫酸盐碱性镀金溶液。
在某些普通镀金溶液中,添加少量锑、镍、钴等金属离子,可以得到硬金镀层,使其硬度提高1—2倍。
为了节约金的用量和增加色调,提高光泽、硬度和耐磨性能等,满足工业生产中的某些特殊要求,还可以在镀金溶液中添加一定量的银、铜、镍、钴等金属化合物,得到金合金镀层。
2.镀金的发展史电镀黄金的历史非常悠久,早在17世纪就有了雷酸液镀金的方法,真正的电镀黄金是1800年Brugnatalli 的工作。
1838年,英国伯明翰的G.Elkington和H.Elkington兄弟发明了高温碱性氰化物镀金,并取得了专利。
它后来被广泛用于装饰品、餐具和钟表的装饰性镀薄金,成了以后一个世纪中电镀黄金的主要技术。
其作用的基本原理到了1913年才为Fray所阐明,到1966年Raub才把亚金氰络盐的行为解释清楚。
在电镀金历史上第一次革命性的变革是酸性镀金液被开发出来。
早在1847年时,Derulz曾冒险在酸性氯化金溶液中添加氢氰酸,发现可以在短时间内获得良好的镀层。
后来Erhardt发现在弱有机酸(如柠檬酸)存在时,氰化亚金钾在pH= 3时仍十分稳定,于是酸性镀金工艺就诞生了。
现在人们已经知道,氰化亚金钾在pH=3时是有可能形成氢氰酸的,但氢氰酸在酸性时会同弱有机酸形成较强的氢键而被束缚在溶液内。
而不会以剧毒气体的形式逸出来,这就是为何酸性镀金可以安全进行的原因。
到了20世纪40年代,电子工业的快速发展鼓舞了人们对电镀金在科学上和技术上探索的兴趣。
当时要求的是如何获得不需经过抛光的光亮镀层,而且可以精确控制镀层的厚度。
这就提出了寻找合适光亮剂的问题。
1957年,F.Volk等人开发了中性(pH 6.5~7.5)氰化物镀金液。
还发现若加入Ag、Cu、Fe、Ni和Co等元素后不仅可以提高镀层的光亮度,也可获得各种金的合金,所用温度为65~75℃,槽电压为2~3V,缓冲盐用磷酸盐。
到了60年代,各种酸性的和合金系统的镀液被开发出来,而且发现了它们的一些特殊的物理力学性能。
例如良好的延展性、耐磨性、耐蚀性和纯度等。
在1968年至1969年间,国际黄金价格急剧上涨波动,为了降低成本,减少在不必要的地方也镀上金,因而发展出了局部选择性镀金的新技术。
到了20世纪60年代后半期和70年代,无氰镀金取得了重大进展,这是电镀金历史上的第二次革命。
最早提出用金的亚硫酸盐配合物来镀金的专利是1962年Smith提出的美国专利U$3057789,但该配合物要在pH 9~11的条件下才稳定。
他建议使用加乙二胺四乙酸二钠盐的电解液。
1969年,Meyer等在瑞士专利506828中介绍了有机多胺,特别是乙二胺作为第二配位体的亚硫酸盐电镀金一铜合金时,pH值在6.5时亚硫酸金络盐仍然稳定。
1972年,Smith在U$3666640中发现由亚硫酸金盐、有机酸螯合剂和Cd、Cu、Ni、As的可溶性盐组成的电解液在pH 8.5~13是稳定的。
1977年,Stevens在U$4048023中发明了一种微碱性的亚硫酸金盐、磷酸盐和[Pd(NH3)4]C12络盐组成的镀金液[2]。
1980年,Laude在US4192723中发明了一种由一价金和亚硫酸铵组成的镀金液。
1982年,Wilkinson在US4366035中提出用亚硫酸金盐、水溶性铜盐或铜的配合物、水溶性钯盐或它的配合物、碱金属亚硫酸盐和亚硫酸铵组成的无氰镀金合金电解液。
1984年,Baker等在US4435253中发现用碱金属亚硫酸盐、亚硫酸铵、水溶性铊盐和无羟基、无氨基的羧酸组成的镀金液。
1985年,Shemyakina在US4497696中提出用氯金酸、EDTA的碱金属盐、碱金属亚硫酸盐、亚硫酸铵反应后而形成的镀金液。
1988年,Nakazawa等由U$4717459中提出用可溶性金盐、导电盐、铅盐和配位体组成的镀金液。
1990年,Kikuchi等在日本公开专利JP02--232378中提出在3一硝基苯磺酸存在时,亚硫酸金盐在pH 8时仍然稳定。
1994年,Morrissey在US5277790中发现了一种pH值可低于6.5的亚硫酸盐镀金液,该溶液中必须含有乙二胺、丙二胺、丁二胺、1,2-二氨基环己烷等有机多胺作第二配位体,同时要含有芳香族硝基化合物,如2,3-或4-硝基苯甲酸、4-氯-3-硝基苯甲酸、2,3一或4一硝基苯磺酸、4一硝基邻苯二甲酸等。
2000年,Kitada在US6087516中介绍了一种新的无氰的二乙二胺合金氯化物[Au(En)z]C13的合成方法,它是由氯金酸钠(NaAuCl4)和乙二胺反应而得。
Kuhn等在US6165342中发明了一种用巯基磺酸,如2一巯基乙磺酸、双(2一磺丙基)二硫化物等作金配位体,Se、Te化合物作光亮剂,AEO、OP类表面活性剂和缓冲盐组成的无氰镀液。
2003年Kitada 等在US6565732中提出了用[Au(En)2]c13作金盐,有机羧酸作缓冲剂,噻吩羧酸、吡啶磺酸作有机光亮剂和无机钾盐作导电盐的无氰镀金液。
无氰镀金主要有亚硫酸盐(钠盐和铵盐)镀金、硫代硫酸盐镀金、卤化物镀金和二硫代丁二酸镀金等。
其中研究最多、应用最广的是亚硫酸盐镀金,它除了不含剧毒的氰化物外,还具有许多氰化物镀液没有的优点。
但是单独用亚硫酸盐作配位体时,镀液还不稳定,因此镀液中还要引入氨、乙二胺、柠檬酸盐、酒石酸盐、磷酸盐、碳酸盐、硼酸盐、EDTA、有机多膦酸等第二或第三配位体才能使镀液稳定。
这些化合物不仅有良好的pH缓冲作用,对镀液的稳定、镀层的光亮和与基材的附着力等都有相当的效果。
到了20世纪80年代,随着高级精密电子工业和航空航天工业的发展,对镀金的要求也越来越高。
人们发现脉冲镀金可以明显改善镀层的质量、厚度的均匀分布以及提高镀液的电流效率和沉积速度。
而激光镀金可以提高沉积速度和沉积的选择性,便于精准地在指定的微区沉积上金,使选择性镀金可以得到精准的控制[3]。
80年代,计算机技术已取得长足的进步,而计算机控制的全自动电镀生产线,为印制电路板的批量生产创造了良好的条件。
在电镀工艺方面,发现在加入Ni、Co在酸性镀金液中,再加入特殊的有机添加剂,可以达到以下的特殊效果:①降低镀金液中金的浓度至4g/L。
(高速电镀则为8g/L。
)。
②提高镀液的分散能力或金层的厚度分布,这是因为这类添加剂能在较高的电流密度下降低阴极效率,从而用化学方法矫正在印制电路板上的电流分布。
③扩大了工作的电流密度范围,如用3-(3一吡啶)丙烯酸作添加剂时,最高光亮的电流密度可由1.0A/dm2提高到4.3A/dmz。
④新型添加剂十分稳定,不会同阳极发生反应而形成一层阳极膜,也不会被阳极分解。
⑤新型添加剂可以被分析,这对镀液的维护控制十分有利。
这些特殊的效果,深受印制电路板从业者的欢迎,它非常适于金手指等部位的电镀,因为获得的金属具有低的接触电阻、高耐蚀、高耐磨、高硬度等特性,而工艺的操作条件宽广,分析、控制与维护都十分方便,适于大批量的连续生产[4]。
随着科学技术的发展,金镀层的高导电性、低接触电阻、良好的焊接性能、优良的延展性、耐蚀性、耐磨性、抗变色性,已成为电子元器件、印制电路板、集成电路、连接器、引线框架、继电器、波导器、警铃和高可靠开关等不可缺少的镀层。
此外,金镀层的优良反射性,特别是红外线的反射功能,已成功地用于航空航天领域,如火箭推进器、人造卫星以及火箭追踪系统等。
由于纯金可与硅形成最低共熔物,因此金镀层可广泛用于各种关键和复杂的硅芯片载体元件中。
纯金镀层具有优良的打线或键合功能,因此它成了集成电路和印制电路板首选的打线镀层,为半导体和印制板的表面组装(SMT)工艺的实施立下了汗马功劳。
含有少量其他金属,如镍或钴的酸性镀金层具有非常好的耐磨性能,是连接器和电接触器的最好镀层,它被用作低负荷电气接触器的专用精饰已有30年的历史,经久不衰。
现在,最厚的镀金层可达1mm,最薄的电镀装饰光亮金镀层只有0.025um。
3镀金发展现状到了20世纪末和21世纪初,人们发现烷基或芳基磺酸,不仅可以扩大光亮电流密度区的范围,使光亮区向高电流密度区移动,而且可以提高电流效率,加快沉积速度。
例如用吡啶基丙烯酸3g/L的酸性氰化镀硬金液,在3A/dm2时的电流效率达48%,沉积速度可达0.98ttm/min。
镀金的主要进展是无氰及无污染镀金液的开发[5]。
过去的镀金液常用三价砷(As3+)、一价铊(T1+)和二价铅(Pb2+)等半金属或金属元素作晶粒细化剂或光亮剂,这些元素都是高污染的元素,虽然它们的使用浓度都较低(<20mg/I。
),但人们还是找到了用有机光亮剂来取代这些污染的元素。
常用的有机光亮剂有以下几种:烟酸、烟酰胺、吡啶、甲基吡啶、3-氨基吡啶、2,3-二氨基吡啶、2,3-二(2-吡啶基)吡嗪、3-(3-吡啶基)-丙烯酸、3-(4-咪唑基)丙烯酸、3-吡啶基羟甲基磺酸、2-(吡啶基)-4-乙烷磺酸、1-(3-磺丙基)-吡啶甜菜碱、1-(3-磺丙基)异喹啉甜菜碱等,这些有机光亮剂都可提高镀金层的光亮度,扩大光亮区的电流密度范围且加快沉积速度或提高电流效率[6]。
4 镀金工艺特点4.1碱性氰化物镀金氰化物镀金溶液的主要组成及工艺条件氰化物镀金溶液具有较强的阴极极化作用,分散能力和覆盖能力好,电流效率高(接近于100%),金属杂质难于共沉积,镀层纯度高,但硬度稍低,孔隙多。
电镀溶液中添加镍、钴等金属离子,可使镀层耐磨性大大提高。
添加少量其他金属化合物(如添加氰化亚铜或银氰化钾),镀层可略带粉红色、浅金黄色或绿色,能满足某些特殊装饰要求。
碱性氰化物镀金溶液主要用于装饰性电镀,不适于印制线路板的电镀。
表1氰化物镀金的工艺条件5.金镀层的作用①装饰金的作用是美观。
主要用于首饰、手表、眼睛、灯饰等轻工产品。
要求镀层色泽好,耐磨损,不变色;可焊金是高纯金,纯度为99.99%,主要用于半导体、军用电子管壳及线路板的板面镀金;耐磨金是金合金,主要用于接插件、印制板插等功能方面的需求[7]。