夹紧力计算
夹紧力计算缸径公式

夹紧力计算缸径公式夹紧力是指夹紧物体所需的力量,它在工业生产中具有重要的应用价值。
夹紧力计算缸径是一种常见的求解夹紧力的方法,它可以帮助工程师们在设计夹紧装置时确定合适的缸径。
下面就来详细介绍一下夹紧力计算缸径的公式以及其应用。
夹紧力计算缸径的公式如下:F=P×A其中,F表示夹紧力,P表示压力,A表示缸面积。
根据这个公式,我们可以通过已知的压力和缸面积来计算夹紧力。
在实际应用中,夹紧力的大小直接影响到夹紧效果。
如果夹紧力过大,可能会损坏被夹物体,而夹紧力过小则可能导致夹紧不牢固。
因此,正确计算缸径以确定合适的夹紧力非常重要。
在进行夹紧力计算缸径时,首先需要明确夹紧物体的特性和要求。
根据夹紧物体的尺寸、形状、材料等属性,可以确定所需的夹紧力范围。
然后,根据夹紧力范围来选择合适的压力值。
一般情况下,夹紧力可以通过测量或计算得到,可以根据具体情况来确定。
在确定了夹紧力和压力后,接下来就是计算缸面积。
缸面积即为缸体内表面的面积,可以通过测量或计算得到。
需要注意的是,缸面积的计算应该考虑到夹紧物体与缸体之间的摩擦力,以确保夹紧力的准确性。
当夹紧力和缸面积确定后,就可以利用上述公式来计算缸径。
根据夹紧力和压力的关系,可以通过改变缸径来调节夹紧力的大小。
一般来说,较大的缸径会产生较大的夹紧力,而较小的缸径则会产生较小的夹紧力。
因此,在设计夹紧装置时,需要根据具体的夹紧力要求来选择合适的缸径。
夹紧力计算缸径的公式可以提供对夹紧力进行准确计算的方法,为工程师们设计夹紧装置提供了参考。
同时,它也提醒我们在进行夹紧力计算时需要充分考虑夹紧物体的特性和要求,以确保夹紧力的准确性。
只有在正确计算缸径的基础上,夹紧装置才能正常工作,从而保证生产的质量和效率。
总之,夹紧力计算缸径是一项重要的工程计算,它可以帮助工程师们确定合适的夹紧力范围,并选择合适的缸径来实现所需的夹紧力。
合理使用这一计算方法,可以保证夹紧装置的稳定性和可靠性,提高工业生产的效率和质量。
夹紧力计算
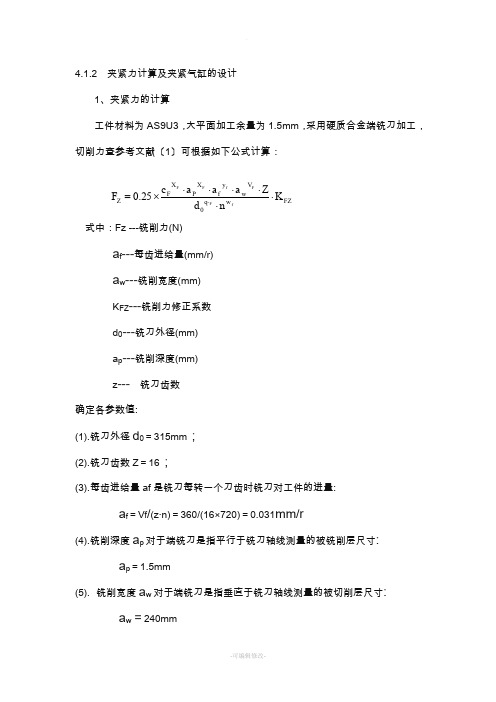
4.1.2 夹紧力计算及夹紧气缸的设计1、夹紧力的计算工件材料为AS9U3,大平面加工余量为1.5mm ,采用硬质合金端铣刀加工,切削力查参考文献〔1〕可根据如下公式计算:•式中:Fz ---铣削力(N)a f ---每齿进给量(mm/r)a w ---铣削宽度(mm)K FZ ---铣削力修正系数d 0---铣刀外径(mm)a p ---铣削深度(mm)z ---•铣刀齿数确定各参数值:(1).铣刀外径d 0=315mm ;(2).铣刀齿数Z =16;(3).每齿进给量af 是铣刀每转一个刀齿时铣刀对工件的进量:a f =V f /(z ·n)=360/(16×720)=0.031mm/r(4).铣削深度a p 对于端铣刀是指平行于铣刀轴线测量的被铣削层尺寸:a p =1.5mm(5). 铣削宽度a w 对于端铣刀是指垂直于铣刀轴线测量的被切削层尺寸:a w =240mmFZw q 0V w y f X P X F Z K n d Za a a c 25.0F f F F f F F ⋅⋅⋅⋅⋅⋅⨯=⋅(6). 修正系数K FZ 取1.6;由表查得: c F =7750 x F =1.0 y F =0.75u F =1.1 w F =0.2 q F =1.3 1.00.75 1.11.30.277501.50.031240160.25 1.6315720Z F ⨯⨯⨯⨯=⨯⨯⨯Fz=276.5N=28Kg(7). 理论所需夹紧力计算确定安全系数:总的安全系数k =k1·k2·k3·k4k 1---- 一般安全系数; k 1取1.7;k 2----加工状态系数; 由于是精加工,所以k 2取1;k 3----刀具钝化系数; k 3取1.4;k 4----断续切削系数; k 4取1.2;∴ k =1.7×1×1.4×1.2≈3W =k ·p =3×28kg =84kg2. 气缸的选择Q=W/(i ·η1·n )=84/(0.8×0.8×3)=44kg由气缸传动的计算公式:Q=P·(πD2/4)·η式中: P--压缩空气压力=6atm =6kg/cm2η--气缸摩擦系数,取0.8i —压板与工件的摩擦系数,取0.8n —夹紧气缸个数,本夹具为3D--气缸直径(cm)D ==D=34.2cm通过以上理论计算,可以选择直径为50mm 的气缸。
m5螺栓夹紧力

m5螺栓夹紧力M5螺栓夹紧力是指在螺栓被拧紧后,螺栓对连接件施加的压力。
螺栓夹紧力的大小直接影响着连接件的稳定性和安全性。
本文将从螺栓夹紧力的定义、计算方法以及影响因素等方面进行详细介绍。
一、螺栓夹紧力的定义螺栓夹紧力是指在螺栓被拧紧后,由于螺栓和连接件之间的摩擦力和弹性变形而产生的压力。
螺栓夹紧力的大小决定了连接件是否能够在工作条件下保持稳定,避免松动和脱落。
二、螺栓夹紧力的计算方法螺栓夹紧力的计算方法有多种,常见的有两种:摩擦力法和应变法。
1. 摩擦力法摩擦力法是通过计算螺栓和连接件之间的摩擦力来确定螺栓夹紧力的大小。
摩擦力法的计算公式如下:F = μ * P其中,F为螺栓夹紧力,μ为摩擦系数,P为预紧力。
2. 应变法应变法是通过测量螺栓伸长量来确定螺栓夹紧力的大小。
应变法的计算公式如下:F = k * ΔL其中,F为螺栓夹紧力,k为螺栓的弹性系数,ΔL为螺栓的伸长量。
三、螺栓夹紧力的影响因素螺栓夹紧力的大小受到多个因素的影响,主要包括以下几个方面:1. 螺纹摩擦系数螺栓和连接件之间的摩擦系数是影响螺栓夹紧力的重要因素。
摩擦系数越大,螺栓夹紧力就越大。
2. 预紧力预紧力是指在螺栓被拧紧之前施加在螺栓上的力。
预紧力越大,螺栓夹紧力就越大。
3. 螺栓的弹性系数螺栓的弹性系数是指螺栓在受力时的变形量与受力的比值。
弹性系数越大,螺栓夹紧力就越大。
4. 连接件的材料和硬度连接件的材料和硬度也会影响螺栓夹紧力的大小。
材料越硬,螺栓夹紧力就越大。
5. 工作温度工作温度的变化会导致螺栓和连接件的热胀冷缩,从而影响螺栓夹紧力的大小。
四、螺栓夹紧力的重要性螺栓夹紧力对于连接件的稳定性和安全性至关重要。
夹紧力过小会导致连接件松动和脱落,从而影响设备的正常运行;夹紧力过大则可能导致连接件的损坏和变形。
因此,在实际应用中,需要根据实际情况合理确定螺栓夹紧力的大小。
螺栓夹紧力是连接件中不可忽视的重要参数。
通过合理计算和控制螺栓夹紧力的大小,可以确保连接件的稳定性和安全性,从而保证设备的正常运行。
夹紧力计算

夹紧力的计算Mz=328.715Nm 转台径向转矩n=4 刹车片个数Mh=Mz/n 每个刹车片承受的摩擦力矩d=0.3 刹车位置到转台中心距离Fh=2*Mh/d 单个刹车片的摩擦力f=0.18 摩擦系数F=Fh/2/f 油压提供的法向力ds=0.030 油压作用面的直径s=pi*ds^2/4 油压作用面积P=F/s 油压求得P =2.1529e+006=2.1529MP4.1.2 百度夹紧力计算及夹紧气缸的设计1、夹紧力的计算工件材料为AS9U3,大平面加工余量为1.5mm,采用硬质合金端铣刀加工,切削力查参考文献〔1〕可根据如下公式计算:•式中:Fz ---铣削力(N)af---每齿进给量(mm/r) aw---铣削宽度(mm) KFZ---铣削力修正系数d0---铣刀外径(mm) ap---铣削深度(mm) z---•铣刀齿数确定各参数值:(1).铣刀外径d0=315mm;(2).铣刀齿数Z=16;(3).每齿进给量af是铣刀每转一个刀齿时铣刀对工件的进量:af=Vf/(z·n)=360/(16×720)=0.031mm/r(4).铣削深度ap对于端铣刀是指平行于铣刀轴线测量的被铣削层尺寸:ap=1.5mm(5). 铣削宽度aw对于端铣刀是指垂直于铣刀轴线测量的被切削层尺寸:aw=240mm(6). 修正系数KFZ取1.6;由表查得: cF=7750 xF=1.0 yF=0.75uF=1.1qF=1.3FFz=276.5N=28Kg(7). 理论所需夹紧力计算确定安全系数:总的安全系数k=k1·k2·k3·k4k1---- 一般安全系数;k1取1.7;k2----加工状态系数;由于是精加工,所以k2取1;k3----刀具钝化系数;k3取1.4;k4----断续切削系数;k4取1.2;∴k=1.7×1×1.4×1.2≈3W=k·p=3×28kg=84kg 2. 气缸的选择Q=W/(i·η1·n)=84/(0.8×0.8×3)=44kg 由气缸传动的计算公式:Q=P·(πD2/4)·η式中: P--压缩空气压力=6atm=6kg/cm2η--气缸摩擦系数,取0.8i—压板与工件的摩擦系数,取0.8n—夹紧气缸个数,本夹具为3D--气缸直径(cm)444463.140.8QDpD=34.2cm通过以上理论计算,可以选择直径为50mm的气缸。
夹紧力计算
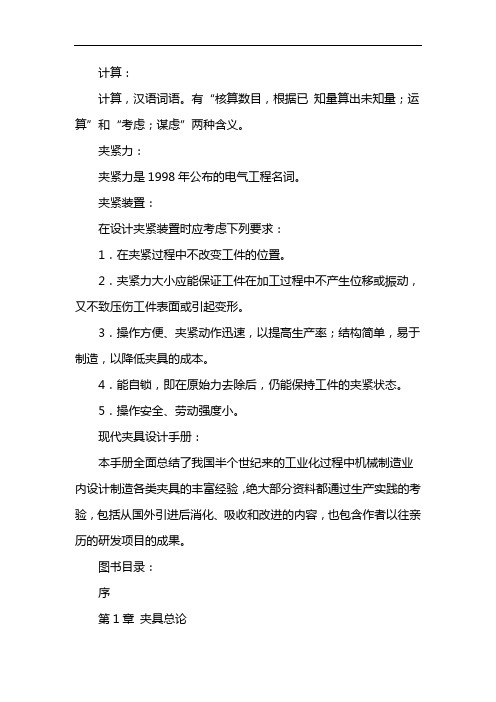
计算:计算,汉语词语。
有“核算数目,根据已知量算出未知量;运算”和“考虑;谋虑”两种含义。
夹紧力:夹紧力是1998年公布的电气工程名词。
夹紧装置:在设计夹紧装置时应考虑下列要求:1.在夹紧过程中不改变工件的位置。
2.夹紧力大小应能保证工件在加工过程中不产生位移或振动,又不致压伤工件表面或引起变形。
3.操作方便、夹紧动作迅速,以提高生产率;结构简单,易于制造,以降低夹具的成本。
4.能自锁,即在原始力去除后,仍能保持工件的夹紧状态。
5.操作安全、劳动强度小。
现代夹具设计手册:本手册全面总结了我国半个世纪来的工业化过程中机械制造业内设计制造各类夹具的丰富经验,绝大部分资料都通过生产实践的考验,包括从国外引进后消化、吸收和改进的内容,也包含作者以往亲历的研发项目的成果。
图书目录:序第1章夹具总论1.1 夹具产生和发展的背景1.1.1 夹具和机床附件1.1.2 机床专用夹具催生了现代大批大量生产1.1.3 夹具是现代制造系统的重要组成部分1.2 夹具的功能、组成和设计要求1.2.1 夹具的基本结构和组成1.2.2 夹具的各种功能1.2.3 设计夹具的基本要求1.3 夹具和机械零件的分类1.3.1 夹具的各种分类方法1.3.2 根据生产规模或品种和批量的分类最重要1.3.3 机械零件和夹具分类编码系统1.4 夹具系统的选择和技术经济指标1.4.1 选择夹具系统的基本原则1.4.2 选择夹具系统的步骤1.4.3 常用夹具系统的技术经济指标1.4.4 夹具设计制作成本的估算1.4.5 使用专用夹具的简易经济分析1.4.6 夹具系统的经济分析1.5 现代夹具发展趋势1.5.1 夹具柔性化1.5.2 夹具自动化和智能化1.5.3 计算机辅助夹具设计(CAD)1.5.4 应对“寻位-加工”的挑战1.5.5 结语第2章夹具功能部件的典型结构2.1 定位装置典型结构2.1.1 插销定位装置2.1.2 V形块定位装置2.1.3 齿轮齿形定位装置2.1.4 其他特殊定位装置2.2 定位支承装置典型结构2.2.1 可调支承典型结构2.2.2 辅助支承典型结构2.3 夹紧装置典型结构2.3.1 螺旋夹紧典型结构2.3.2 快速螺旋夹紧典型结构2.3.3 斜楔夹紧典型结构2.3.4 偏心(凸轮)夹紧典型结构2.3.5 端面凸轮夹紧典型结构2.3.6 铰链夹紧典型结构2.3.7 联动夹紧典型结构2.3.8 可移动位置的典型夹紧结构2.3.9 气(液)动自动夹紧装置典型结构2.3.10 自动定心夹紧典型结构2.3.11 肘节式快速夹紧装置2.3.12 其他特种类型夹紧装置2.4 分度装置典型结构2.4.1 分度定位销2.4.2 典型分度装置2.4.3 精密分度装置第3章夹具设计计算3.1 定位尺寸的相关计算3.1.1 V形块的计算3.1.2 夹具上两定位销的尺寸及定位误差的计算3.1.3 夹具上定位销的尺寸及定位误差的计算3.1.4 定位销高度的计算3.1.5 小锥度心轴尺寸的计算3.1.6 带圆柱部分的锥度心轴尺寸的计算3.1.7 压入配合光滑心轴尺寸的计算3.1.8 滚柱心轴的尺寸及有关计算3.1.9 齿轮按渐开线齿形定位时的计算3.1.10 三圆弧自定心夹紧机构偏心圆弧尺寸的计算3.1.11 钻斜孔钻模工艺基准孔中心至钻套孔轴线间的距离x的计算3.1.12 弹簧夹头结构尺寸的计算3.2 定位误差的计算3.2.1 常见定位形式的定位精度计算3.2.2 钻模的钻孔精度计算3.2.3 用定位销定位的分度装置的分度概率精度3.3 典型夹紧形式的夹紧力计算3.3.1 计算时的计算系数3.3.2 常见典型夹紧形式所需夹紧力的计算3.4 典型夹紧机构的作用力计算3.4.1 螺旋夹紧机构3.4.2 圆偏心夹紧机构3.4.3 复合圆偏心轮夹紧机构3.4.4 端面凸轮夹紧机构3.4.5 复合端面凸轮夹紧机构3.4.6 斜锲夹紧机构3.4.7 压板夹紧机构3.4.8 切向夹紧机构3.4.9 齿条滑柱钻模圆锥锁紧机构3.4.10 铰链杠杆增力机构3.4.11 离心式夹紧机构3.4.12 楔槽式夹紧机构3.4.13 复合气(液)动夹紧机构3.5 自定心夹紧机构的相关计算3.5.1 碗形弹簧片定心夹具的设计计算3.5.2 碟形弹簧片定心夹具的设计计算3.5.3 V形弹性夹盘定心夹具的设计计算3.5.4 弹性薄壁膜片卡盘的设计计算3.5.5 薄壁波纹套定心夹具的设计与计算3.5.6 自定心夹紧装置的定心精度3.5.7 液性塑料薄壁套筒夹具的设计与计算3.6 端齿分度盘的相关计算3.6.1 直齿端齿分度盘的结构及其参数的确定3.6.2 端齿分度盘的锁紧力计算3.6.3 YX-DZ系列直齿端齿盘的规格、主要尺寸及精度3.6.4 差动端齿分度装置的设计与计算3.7 夹具夹紧误差的估算3.8 多轴传动头的齿轮系几何尺寸计算3.8.1 外啮合标准直齿圆柱齿轮的几何尺寸计算3.8.2 外啮合高变位直齿圆柱齿轮的几何尺寸计算3.8.3 外啮合标准斜齿圆柱齿轮的几何尺寸计算3.8.4 外啮合高变位斜齿圆柱齿轮的几何尺寸计算3.8.5 内啮合高变位直齿圆柱齿轮的几何尺寸计算3.8.6 内齿直齿圆柱齿轮测量尺寸的计算3.9 典型加工方法切削力的计算3.9.1 车削力的计算3.9.2 钻削力的计算3.9.3 铣削力的计算第4章专用夹具常用零部件及其标准或规范4.1 概述4.2 夹具常用紧固件与连接件国家标准索引4.2.1 螺栓4.2.2 螺柱4.2.3 螺钉4.2.4 螺母4.2.5 垫圈4.2.6 销4.2.7 挡圈4.2.8 键4.3 定位件4.3.1 定位销及定位插销4.3.2 定位轴4.3.3 键4.3.4 V形块及挡块4.3.5 定位器4.4 支承件4.4.1 标准支承件4.4.2 非标准支承件4.4.3 辅助支承4.5 夹紧件4.5.1 压块、压板4.5.2 偏心轮4.5.3 支座、支柱4.5.4 夹具专用螺钉和螺栓4.5.5 夹具专用螺母4.5.6 夹具专用垫圈4.6 导向件4.6.1 钻套4.6.2 其他导向件4.7 对刀块及塞尺4.7.1 对刀块4.7.2 塞尺4.8 操作件4.8.1 夹具常用操作件4.8.2 其他操作件4.9 与夹具相关的机床附件4.9.1 顶尖4.9.2 卡夹件4.9.3 拨盘、花盘及过渡盘4.9.4 活铁爪4.9.5 角铁4.10 其他件4.10.1 圆柱螺旋压缩弹簧4.10.2 圆柱螺旋拉伸弹簧4.10.3 弹簧用螺钉4.10.4 弹簧用吊环螺钉4.10.5 切向夹紧套4.10.6 焊接环首螺钉4.10.7 带锁紧槽圆螺母4.10.8 带扳手孔圆螺母4.10.9 堵片4.10.10 螺塞4.10.11 锁口4.11 夹具体4.11.1 夹具体的毛坯种类及基本要求4.11.2 夹具体座耳尺寸4.11.3 夹具体的排屑结构4.11.4 夹具体的标准毛坯和零件4.11.5 标准毛坯件和零件组合的夹具体图例4.11.6 夹具体结构的正误分析4.12 机床夹具零部件标准件应用图例4.12.1 定位件及辅助支承应用图例4.12.2 夹紧件应用图例4.12.3 导向件应用图例4.12.4 其他零部件应用图例4.13 夹具元件公差配合的选择及机床夹具零部件通用技术条件4.13.1 夹具中常用元件间的配合及公差4.13.2 常用夹具元件的配合图例4.13.3 机床夹具零件及部件通用技术条件第5章气动、液压、电力、电磁、真空夹具传动系统及其元件和夹具图例5.1 夹具夹紧动力源概述5.1.1 手动夹紧和动力夹紧5.1.2 动力夹紧的各种动力源5.2 气动夹具5.2.1 气动夹具优缺点和应用场合5.2.2 气源和气压系统5.2.3 气压传动夹紧系统的设计计算及其元件5.2.4 气动夹具应用图例5.3 液压夹具和液压夹紧的动力源5.3.1 夹具用液压系统的特点5.3.2 基本液压夹紧系统、结构及其元件5.3.3 液压夹具常用典型液压回路5.3.4 夹具液压夹紧系统的相关计算5.3.5 液压夹具用液压缸结构和尺寸5.3.6 液压夹紧的各种动力源5.3.7 液压夹紧机构和液压夹具应用示例5.4 电力传动夹具5.4.1 电力传动夹紧装置5.4.2 偏心式电动卡盘5.4.3 电磁铁夹紧装置5.5 电磁夹具及其应用5.5.1 电磁夹具工作原理5.5.2 各种电磁吸盘结构形式和设计要点5.5.3 强力电磁夹具5.5.4 电磁无心夹具5.6 真空夹具及其应用5.6.1 真空系统工作原理及夹紧力计算5.6.2 真空发生装置5.6.3 真空夹具及典型结构5.6.4 真空夹具的设计要点第6章机床专用夹具设计方法6.1 机床专用夹具设计步骤6.2 设计前期准备6.2.1 信息资料收集与研究6.2.2 加工精度和工艺性分析6.2.3 切削力、夹紧力综合平衡计算6.3 夹具结构方案选择6.3.1 定位原则及方案选择6.3.2 辅助支承方式选择6.3.3 对刀与引导方式选择6.3.4 夹紧原则及方案选择6.3.5 其他组成部分结构形式选择6.4 夹具总装配图绘制6.4.1 总体结构确定6.4.2 定位元件结构绘制6.4.3 辅助支承结构绘制6.4.4 对刀与引导装置结构绘制6.4.5 夹紧元件结构绘制6.4.6 夹具体结构绘制6.4.7 其他部分结构绘制6.4.8 夹具总图标注和技术条件给定6.4.9 夹具设计普遍应注意的问题6.4.10 夹具总装配图绘制示例6.5 夹具零件图绘制6.5.1 零件结构确定6.5.2 材料选择与工艺性分析6.5.3 技术要求确定6.5.4 工艺孔在夹具设计中的应用6.6 夹具设计与制造中的信息处理第7章机床专用夹具设计及典型图例7.1 车床专用夹具7.1.1 车床专用夹具的主要类型7.1.2 车床夹具设计要则7.1.3 车床(圆磨床)夹具的技术要求7.1.4 车床(圆磨床)夹具的磨损极限7.1.5 车床专用夹具典型图例7.1.6 车床通用可调夹具典型图例7.2 钻床、镗床专用夹具7.2.1 钻床、镗床专用夹具的主要类型7.2.2 钻床夹具(钻模)设计要则7.2.3 镗床夹具设计要则7.2.4 钻床(镗床)夹具的技术要求7.2.5 钻床(镗床)夹具的磨损极限7.2.6 钻模通用部件7.2.7 钻床专用夹具(钻模)典型图例7.2.8 钻床通用可调夹具典型图例7.2.9 钻床多轴头7.2.10 镗床专用夹具典型图例7.3 铣床专用夹具7.3.1 铣床专用夹具的主要类型7.3.2 铣床专用夹具设计要则7.3.3 铣床夹具的技术要求7.3.4 铣床夹具的磨损极限7.3.5 铣床专用夹具典型图例7.3.6 铣床通用可调夹具典型图例7.4 拉床专用夹具7.4.1 拉床专用夹具主要类型7.4.2 拉床专用夹具设计要则7.4.3 拉床专用夹具典型图例7.5 齿轮机床专用夹具7.5.1 齿轮机床专用夹具主要类型7.5.2 齿轮机床专用夹具设计要则7.5.3 齿轮机床专用夹具技术要求7.5.4 齿轮机床专用夹具典型图例7.6 磨床专用夹具7.6.1 圆磨床专用夹具7.6.2 平面磨床专用夹具7.7 组合机床及其自动线专用夹具7.7.1 概述7.7.2 组合机床及其自动线夹具设计要则7.7.3 定位、夹紧及刀具导向的结构7.7.4 组合机床及其自动线专用夹具典型图例7.8 数控机床和加工中心夹具7.8.1 数控机床和加工中心夹具设计要则7.8.2 数控机床与加工中心夹具典型图例第8章可调夹具和成组夹具8.1 概述8.1.1 可调夹具和成组夹具的定义和分类8.1.2 可调夹具和成组夹具的结构特点及适用场合8.1.3 可调夹具和成组夹具的标识方法8.1.4 可调夹具和成组夹具的应用效果8.2 成组夹具的设计与应用8.2.1 成组夹具的设计依据、原则、程序和附加说明8.2.2 成组夹具的应用与管理8.3 可调夹具示例8.3.1 回转体类零件用可调夹具示例8.3.2 非回转体类零件用可调夹具示例8.4 成组夹具示例8.4.1 回转体零件用成组夹具示例8.4.2 非回转体零件用成组夹具……第9章组合夹具,数控机床、加工中心、柔性制造系统用夹具第10章检验夹具第11章焊接夹具第12章计算机辅助夹具设计(CAFD)。
m6螺栓夹紧力
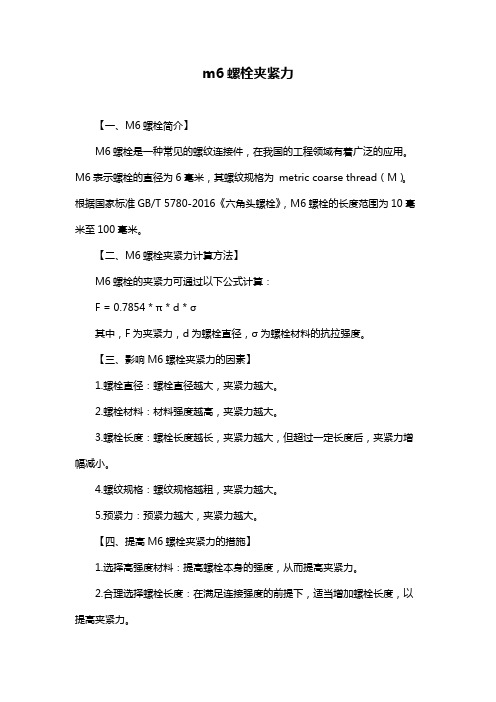
m6螺栓夹紧力
【一、M6螺栓简介】
M6螺栓是一种常见的螺纹连接件,在我国的工程领域有着广泛的应用。
M6表示螺栓的直径为6毫米,其螺纹规格为metric coarse thread(M)。
根据国家标准GB/T 5780-2016《六角头螺栓》,M6螺栓的长度范围为10毫米至100毫米。
【二、M6螺栓夹紧力计算方法】
M6螺栓的夹紧力可通过以下公式计算:
F = 0.7854 * π * d * σ
其中,F为夹紧力,d为螺栓直径,σ为螺栓材料的抗拉强度。
【三、影响M6螺栓夹紧力的因素】
1.螺栓直径:螺栓直径越大,夹紧力越大。
2.螺栓材料:材料强度越高,夹紧力越大。
3.螺栓长度:螺栓长度越长,夹紧力越大,但超过一定长度后,夹紧力增幅减小。
4.螺纹规格:螺纹规格越粗,夹紧力越大。
5.预紧力:预紧力越大,夹紧力越大。
【四、提高M6螺栓夹紧力的措施】
1.选择高强度材料:提高螺栓本身的强度,从而提高夹紧力。
2.合理选择螺栓长度:在满足连接强度的前提下,适当增加螺栓长度,以提高夹紧力。
3.增加预紧力:适当加大预紧力,使螺栓夹紧力得到提高。
4.优化螺栓结构:如采用螺纹加密、加大螺栓头部等措施,以提高夹紧力。
【五、总结】
M6螺栓作为一种常见的螺纹连接件,在工程领域具有重要应用价值。
了解M6螺栓的夹紧力计算方法及影响因素,有助于我们更好地选择和使用M6螺栓,提高连接件的稳定性和安全性。
夹紧力计算

上海德珂斯机械自动化技术有限公司Tuenkers Machinery & Automation Technology Co., Ltd, Shanghai夹紧器夹紧力计算上海德珂斯机械自动化技术有限公司Tuenkers Machinery & Automation Technology Co., Ltd, Shanghai1.压块垂直夹紧时,此时夹紧力处于垂直方向, 其受力分析如下:夹紧力Fs 压块M缸径 5bar气压夹紧力矩L40夹紧力Fs50120Nm 160Nm63380Nm80600NmFs =有效夹紧力 L=夹紧点与转动轴中心距离当压块垂直夹紧时,夹紧力方向与力矩切线方向相同,此时产生的夹紧力最大,计算公式如下: Fs= M ÷ L举例: 当L=200mm时,缸径63mm. 夹紧力Fs=380Nm ÷0.2m=1900N上海德珂斯机械自动化技术有限公司Tuenkers Machinery & Automation Technology Co., Ltd, Shanghai2.压块水平夹紧时,此时夹紧力处于水平状方 向,其受力分析如下:夹紧力Fs压块M L2L1 Fs α FFs =有效夹紧力 L1=夹紧点与转动轴中心距离 F=切向力缸径 5bar气压夹紧力矩M40120Nm50160Nm63380Nm80600Nm当压块水平夹紧时,其有效夹紧力会相对减小,计算公式如下: Cos α =L2 ÷ L1 F= M ÷ L1 Fs= F × Cos α举例: 当L1=200mm,L2=100mm时,缸径63mm。
F=380Nm÷0.2=1900N Fs=F × Cos α=1900N×(100÷200)=950N上海德珂斯机械自动化技术有限公司Tuenkers Machinery & Automation Technology Co., Ltd, Shanghai谢谢!上海德珂斯机械自动化技术有限公司Tuenkers Machinery & Automation Technology Co., Ltd, Shanghai。
电动卡盘夹紧力计算

电动卡盘夹紧力计算摘要:一、电动卡盘的工作原理与分类1.电动卡盘的工作原理2.电动卡盘的分类二、电动卡盘夹紧力的计算方法1.静态夹紧力计算2.动态夹紧力计算3.计算实例三、电动卡盘夹紧力的影响因素1.电动卡盘的结构参数2.工件的材质与加工参数3.工作环境与使用条件四、提高电动卡盘夹紧力的方法1.优化电动卡盘的结构设计2.选用适当的材料与加工参数3.加强日常维护与保养正文:电动卡盘是一种常用于机械加工中的夹紧设备,具有结构紧凑、操作简便、夹紧力可调等优点。
在实际应用中,电动卡盘的夹紧力对于工件的加工精度与安全性具有重要影响。
本文将针对电动卡盘夹紧力的计算方法及其影响因素进行探讨,并提出提高电动卡盘夹紧力的方法。
一、电动卡盘的工作原理与分类电动卡盘的工作原理主要是通过电动机驱动卡盘的夹紧装置,实现对工件的夹紧与放松。
根据电动卡盘的结构特点与工作原理,可将其分为内涨式、外夹式和复合式等几种类型。
二、电动卡盘夹紧力的计算方法电动卡盘夹紧力的计算方法主要包括静态夹紧力计算与动态夹紧力计算。
其中,静态夹紧力计算主要考虑电动卡盘的静态结构参数,如卡爪的夹紧面积、材料性能等;动态夹紧力计算则需要考虑工件的材质、加工参数以及工作环境等因素。
具体计算公式如下:静态夹紧力F1 = π*D*Fmax / 2动态夹紧力F2 = F1 + 4*Fn其中,D 为卡爪直径,Fmax 为电动卡盘的最大夹紧力,Fn 为工件所受切削力。
三、电动卡盘夹紧力的影响因素电动卡盘夹紧力的影响因素主要包括电动卡盘的结构参数、工件的材质与加工参数以及工作环境与使用条件等。
例如,卡盘的结构参数会影响其夹紧力的大小与分布;工件的材质与加工参数会导致切削力的变化,从而影响夹紧力的需求;工作环境与使用条件的差异也会对夹紧力产生影响。
四、提高电动卡盘夹紧力的方法针对电动卡盘夹紧力的问题,可以从以下几个方面进行改进:1.优化电动卡盘的结构设计,提高其最大夹紧力与夹紧稳定性;2.根据工件的材质与加工参数,选用适当的电动卡盘,以满足夹紧需求;3.加强日常维护与保养,确保电动卡盘的正常工作状态。
夹紧力计算
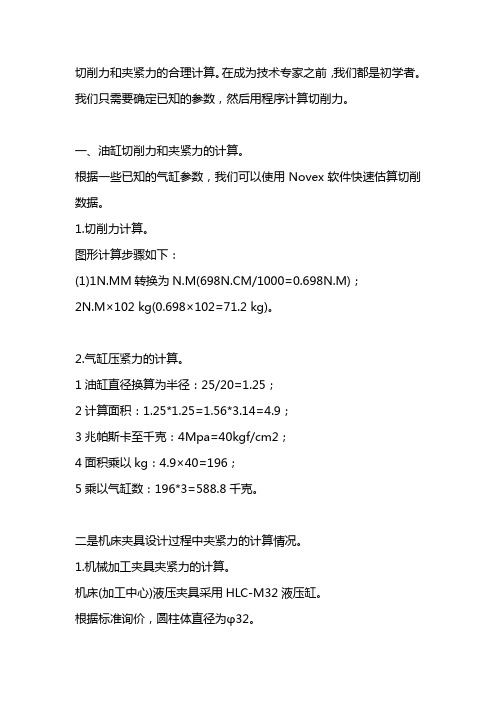
切削力和夹紧力的合理计算。
在成为技术专家之前,我们都是初学者。
我们只需要确定已知的参数,然后用程序计算切削力。
一、油缸切削力和夹紧力的计算。
根据一些已知的气缸参数,我们可以使用Novex软件快速估算切削数据。
1.切削力计算。
图形计算步骤如下:(1)1N.MM转换为N.M(698N.CM/1000=0.698N.M);2N.M×102 kg(0.698×102=71.2 kg)。
2.气缸压紧力的计算。
1油缸直径换算为半径:25/20=1.25;2计算面积:1.25*1.25=1.56*3.14=4.9;3兆帕斯卡至千克:4Mpa=40kgf/cm2;4面积乘以kg:4.9×40=196;5乘以气缸数:196*3=588.8千克。
二是机床夹具设计过程中夹紧力的计算情况。
1.机械加工夹具夹紧力的计算。
机床(加工中心)液压夹具采用HLC-M32液压缸。
根据标准询价,圆柱体直径为φ32。
该夹具共使用6个液压缸。
夹紧力的计算方法如图6所示。
2,f=ps=pπ(d/2)2=4823.04n.。
根据力矩平衡(杠杆)原理,该夹具的动力臂为L1,阻力臂为L2。
公式为:功率臂长度×功率=电阻臂长度×电阻。
计算三个电阻f1、f2和f3以及夹具的夹紧力(图7)。
铣削切削力的计算。
使用下面的软件,这个过程的基本参数,如转速和进给速率。
经计算,进给力FF约为12052N,径向力FP约为12873N,主切削力Fe约为36522N。
以上计算的机床夹紧力f为53053N。
夹紧力×摩擦系数(支撑块和铝合金为0.45)=23874n>ff>fp。
当摩擦力大于进给切削力和径向切削力时,确保定位销不受力。
工件重力质量=9.8×质量=196N,小重力不影响结果,合理选择液压缸压力。
结论。
过去,油缸和钢瓶的尺寸大多由设计者的经验决定。
利用软件计算结果进行合理选型,减少了因选错造成的浪费。
油缸夹具夹紧力计算

油缸夹具夹紧力计算
油缸夹具夹紧力计算
一、基本原理:
在油缸夹具进行夹紧操作时,其夹紧力是由夹具杆螺母所造成的拉拔力来完成的。
拉拔力F的大小等于夹具杆螺母的螺纹螺距与螺纹螺缝锥度之比乘以螺母的最大扭矩M max 乘以螺纹螺距P。
F = M max × P / t
其中,t 为螺纹螺缝锥度,可以通过查询标准查得。
二、夹紧力计算公式:
夹紧力F的计算公式为:
F=K × P × M / t
其中,K 为压紧系数;P 为夹具杆螺母的螺纹螺距;M 为夹具杆螺母的实际扭矩;t 为螺纹螺缝锥度。
三、夹紧力计算的实际操作:
(1)设置夹具杆螺母要求的螺纹螺距,要求螺距不能大于规定的最大螺距。
(2)使用扭矩扳手按照规定的标准及设定的最大扭矩值来扭紧夹具杆螺母,确保扭紧夹具杆螺母到规定的最大扭矩。
(3)查询准确的螺纹螺缝锥度并计算设定最大扭矩和螺纹螺距的拉拔力(夹紧力)。
四、夹紧力的控制方法:
(1)选择合适的螺母,夹具杆螺母的螺纹螺距要符合标准要求,螺母的螺纹公差级别也要符合标准要求。
(2)正确的设定夹具杆螺母的最大扭矩,并严格按照最大扭矩来进行夹紧,确保螺母可以达到最佳的夹紧力。
(3)检查夹紧力是否达到规定的要求,可以使用专用的力计或扭矩扳手等工具来进行检查。
如果夹紧力未达到规定要求,可以考虑重新调整螺母的最大扭矩或者更换螺母。
(4)经常性的进行夹紧力检测,及时发现夹紧力不足的情况,及时进行调整,确保油缸夹具的稳定和安全使用。
夹紧力计算

4、1、2 夹紧力计算及夹紧气缸的设计1、夹紧力的计算工件材料为AS9U3,大平面加工余量为1、5mm,采用硬质合金端铣刀加工,切削力查参考文献〔1〕可根据如下公式计算: •式中:Fz ---铣削力(N)a f ---每齿进给量(mm/r) a w ---铣削宽度(mm) K FZ ---铣削力修正系数 d 0---铣刀外径(mm) a p ---铣削深度(mm) z ---•铣刀齿数 确定各参数值:(1)、铣刀外径d 0=315mm ; (2)、铣刀齿数Z =16;(3)、每齿进给量af 就是铣刀每转一个刀齿时铣刀对工件的进量:a f =V f /(z ·n)=360/(16×720)=0、031mm/r(4)、铣削深度a p 对于端铣刀就是指平行于铣刀轴线测量的被铣削层尺寸:a p =1、5mm(5)、 铣削宽度a w 对于端铣刀就是指垂直于铣刀轴线测量的被切削层尺寸:a w =240mm(6)、 修正系数K FZ 取1、6;由表查得: c F =7750 x F =1、0 y F =0、75u F =1、1 w F =0、2 q F =1、3FZw q 0V wy fX PX FZ K nd Za a a c 25.0F fFFfFF⋅⋅⋅⋅⋅⋅⨯=⋅1.00.75 1.11.30.277501.50.031240160.25 1.6315720ZF ⨯⨯⨯⨯=⨯⨯⨯Fz=276、5N=28Kg(7)、 理论所需夹紧力计算 确定安全系数:总的安全系数k =k1·k2·k3·k4k 1---- 一般安全系数; k 1取1、7;k 2----加工状态系数; 由于就是精加工,所以k 2取1; k 3----刀具钝化系数; k 3取1、4; k 4----断续切削系数; k 4取1、2; ∴ k =1、7×1×1、4×1、2≈3 W =k ·p =3×28kg =84kg 2、 气缸的选择Q=W/(i ·η1·n )=84/(0、8×0、8×3)=44kg 由气缸传动的计算公式: Q=P·(πD2/4)·η式中: P--压缩空气压力=6atm =6kg/cm2η--气缸摩擦系数,取0、8i —压板与工件的摩擦系数,取0、8n —夹紧气缸个数,本夹具为3 D--气缸直径(cm)D ==D=34、2cm通过以上理论计算,可以选择直径为50mm 的气缸。
电动卡盘夹紧力计算

电动卡盘夹紧力计算
(原创实用版)
目录
1.电动卡盘夹紧力的重要性
2.计算夹紧力的方法
3.影响夹紧力的因素
4.结论
正文
电动卡盘夹紧力计算在机械加工领域中具有重要意义。
夹紧力的大小直接影响到工件在加工过程中的稳定性和加工精度。
计算夹紧力有助于选择合适的夹具和确定夹紧力的大小,从而保证加工质量。
一、计算夹紧力的方法
1.经验法:根据实际加工经验,结合工件材料、形状、加工工艺等因素,估算夹紧力。
2.理论计算法:根据材料力学性能、切削用量、刀具锋利程度等因素,利用公式计算夹紧力。
但由于影响因素较多,计算结果可能与实际夹紧力有一定差距。
3.试验法:通过实际加工试验,测量夹紧力,并根据加工结果调整夹紧力。
二、影响夹紧力的因素
1.工件材料:不同材料的硬度和韧性影响夹紧力的大小。
2.切削用量:切削速度、进给速度和刀具的切削深度等参数影响夹紧力。
3.刀具锋利程度:刀具的锋利程度和磨损状况影响夹紧力。
4.夹具结构:夹具的设计和制造质量影响夹紧力。
5.操作者技术水平:操作者在操作过程中的规范程度和技术水平影响夹紧力。
三、结论
电动卡盘夹紧力的计算是一个复杂的过程,需要综合考虑多种因素。
夹紧力计算

单螺旋所产生的夹紧力计算在图1中,螺纹可认为绕圆柱体上的一个斜面,螺母看成是斜面上的一个滑块A,因此其夹紧力可根据楔的工作原理来计算。
在手柄的作用下,滑块A沿螺旋斜面移动。
已知螺纹为方牙螺纹,手柄上的外加力为P, 手柄长度为L,螺纹中经为r,则可求出作用在滑块A上的水平力Q1,即:P LP L Q1 r ,Q1。
—(a)r挡滑块A沿着斜面作匀速运动时,从图2中可求出水平力Q i和夹紧力W之间的关系。
若不考虑摩擦力时,则作用在滑块A上的力有三个,即夹紧力W、斜面反作用力N和水平力Q i。
由于这三个力处于平衡状态,所以可得:Q1 W tg 。
线N偏斜一个摩擦角i。
(参看图3)根据平衡条件,由三角形ARW可得:Q1W tg 1。
(b)将式(a)代入式(b),可以求出夹紧力W,r tg螺纹中经Na若滑块A与斜面有摩擦力,则反作用力R与法间的摩擦力炬损失,此时夹紧力计算的一 般公式为:tg 1=0.15;r ----摩擦力炬的半径,与接触处的形状有关(参见图4)。
当用上述条件同样简化,则得:(1) 螺栓头部是平的则W=90P;(2) 螺母夹紧形式,则 W 〜70R 。
式中:W-----工作夹紧力(公斤力);a ——螺纹升角,tg —2 rB 1----螺纹配合面的摩擦角(实际计算B i 可取8.5°);t------螺纹螺距。
对于标准三角螺纹,升角不大于 3.5°,自索性良好,当使用力臂 L=14d 平均的标准扳手时,上式可简化为 W 〜130P 。
当螺钉头部为平端面或用螺母夹紧形式时, 我们还必须考虑其旋转面 P Lr tg i r tg i式中:i ----旋转接触面的摩擦系数,可取r =3r r'=1.25-图4。
夹紧力计算

夹紧力计算公式T=KFd,K为拧紧力矩系数,F为预紧力,d为螺纹的公称直径螺栓厂家会给出一定的参数,多大的扭矩对应多大的螺栓轴拉力,也可以通过试验确定,需要用到扭矩计和螺栓轴力计等实验设备。
对于你说的这种情况在实际操作中一般采用经过准确标定过的扭矩扳手进行拧紧。
例如手动型的扭矩扳手在拧紧螺栓的过程中,如果达到预定的扭矩值就会发出声音,提醒工人停止动作。
你提到的误差范围,我查了资料,施工用的扭矩扳手进行标定时,允许误差是不得大于使用扭矩值的±5%。
校正用的扭矩扳手,其误差应控制在±3%以内。
实际的力矩公差不就是由工具精度控制的吗?如果你按照44Nm标定好扭矩扳手,那么最终施加的实际扭矩就一定会是在44Nm附近,误差不会超过±5%。
既然规范规定允许工具的公差在±5%范围,那么就是考虑了在这个范围能不会出现过松,或者扭断的危险。
夹紧力大小要适当,过大了会使工件变形,过小了则在加工时工件会松动,造成报废甚至发生事故。
采用手动夹紧时,可凭人力来控制夹紧力的大小,一般不需要算出所需夹紧力的确切数值,只是必要时进行概略的估算。
当设计机动(如气动、液压、电动等)夹紧装置时,则需要计算夹紧力的大小。
以便决定动力部件(如气缸、液压缸直径等)的尺寸。
进行夹紧力计算时,通常将夹具和工件看作一刚性系统,以简化计算。
根据工件在切削力、夹紧力(重型工件要考虑重力,高速时要考虑惯性力)作用下处于静力平衡,列出静力平衡方程式,即可算出理论夹紧力,再乘以安全系数,作为所需的实际夹紧力。
实际夹紧力一般比理论计算值大2~3倍。
夹紧力三要素的确定,是一个综合性问题。
必须全面考虑工件的结构特点、工艺方法、定位元件的结构和布置等多种因素,才能最后确定并具体设计出较为理想的夹紧机构。
夹紧力计算

4.1.2 夹紧力计算及夹紧气缸的设计1、夹紧力的计算工件材料为AS9U3,大平面加工余量为1.5mm ,采用硬质合金端铣刀加工,切削力查参考文献〔1〕可根据如下公式计算: •式中:Fz ---铣削力(N)a f ---每齿进给量(mm/r) a w ---铣削宽度(mm) K FZ ---铣削力修正系数 d 0---铣刀外径(mm) a p ---铣削深度(mm) z ---•铣刀齿数 确定各参数值:(1).铣刀外径d 0=315mm ; (2).铣刀齿数Z =16;(3).每齿进给量af 是铣刀每转一个刀齿时铣刀对工件的进量:a f =V f /(z ·n)=360/(16×720)=0.031mm/r(4).铣削深度a p 对于端铣刀是指平行于铣刀轴线测量的被铣削层尺寸:a p =1.5mm(5). 铣削宽度a w 对于端铣刀是指垂直于铣刀轴线测量的被切削层尺寸:a w =240mm(6). 修正系数K FZ 取1.6;由表查得: c F =7750 x F =1.0 y F =0.75u F =1.1 w F =0.2 q F =1.3FZw q 0V wy fX PX FZ K nd Za a a c 25.0F fFFfFF⋅⋅⋅⋅⋅⋅⨯=⋅1.00.75 1.11.30.277501.50.031240160.25 1.6315720ZF ⨯⨯⨯⨯=⨯⨯⨯Fz=276.5N=28Kg(7). 理论所需夹紧力计算 确定安全系数:总的安全系数k =k1·k2·k3·k4k 1---- 一般安全系数; k 1取1.7;k 2----加工状态系数; 由于是精加工,所以k 2取1; k 3----刀具钝化系数; k 3取1.4; k 4----断续切削系数; k 4取1.2; ∴ k =1.7×1×1.4×1.2≈3 W =k ·p =3×28kg =84kg 2. 气缸的选择Q=W/(i ·η1·n )=84/(0.8×0.8×3)=44kg 由气缸传动的计算公式: Q=P·(πD2/4)·η式中: P--压缩空气压力=6atm =6kg/cm2η--气缸摩擦系数,取0.8i —压板与工件的摩擦系数,取0.8n —夹紧气缸个数,本夹具为3D--气缸直径(cm)D ==D=34.2cm通过以上理论计算,可以选择直径为50mm 的气缸。
花键套的夹紧力计算
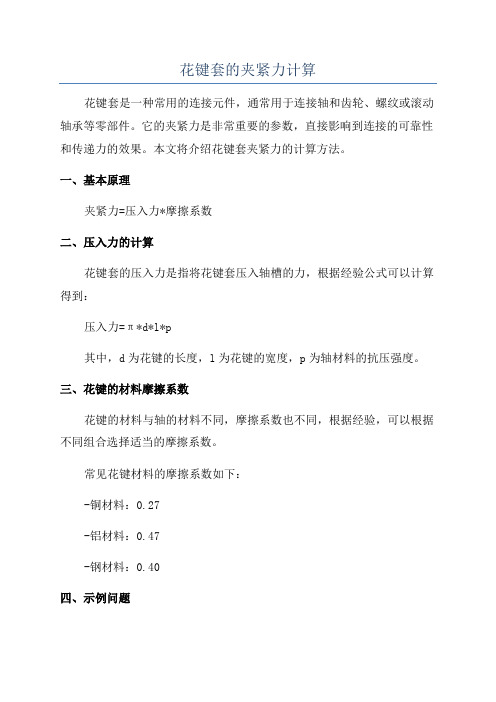
花键套的夹紧力计算花键套是一种常用的连接元件,通常用于连接轴和齿轮、螺纹或滚动轴承等零部件。
它的夹紧力是非常重要的参数,直接影响到连接的可靠性和传递力的效果。
本文将介绍花键套夹紧力的计算方法。
一、基本原理夹紧力=压入力*摩擦系数二、压入力的计算花键套的压入力是指将花键套压入轴槽的力,根据经验公式可以计算得到:压入力=π*d*l*p其中,d为花键的长度,l为花键的宽度,p为轴材料的抗压强度。
三、花键的材料摩擦系数花键的材料与轴的材料不同,摩擦系数也不同,根据经验,可以根据不同组合选择适当的摩擦系数。
常见花键材料的摩擦系数如下:-铜材料:0.27-铝材料:0.47-钢材料:0.40四、示例问题假设我们需要计算一个花键套的夹紧力,该花键套的长度为10mm,宽度为5mm,压入力为1500N,轴材料为45钢材料。
1.计算花键的夹紧力首先,根据经验,45钢材料的抗压强度为420MPa,花键的压入力可以通过公式计算:压入力= π * d * l * p = 3.14 * 10mm * 5mm * 420MP a = 6590N2.计算花键材料的摩擦系数根据常见花键材料的摩擦系数,45钢材料的摩擦系数为0.40。
3.计算花键套的夹紧力夹紧力=压入力*摩擦系数=6590N*0.40=2636N根据以上计算,该花键套的夹紧力为2636N。
五、注意事项在实际应用中,还需要注意以下几点:1.压入力的计算应该考虑到花键槽的设计参数,如尺寸和材料缺陷等。
2.材料摩擦系数可以根据实际情况进行选择,不同工况需要不同的摩擦系数。
3.在计算夹紧力时,还需要考虑到实际使用中的运动状态和环境条件,如振动、温度等因素。
4.夹紧力计算的结果只是一种理论参考值,在实际应用中还需要进行试验和验证。
总结起来,花键套的夹紧力计算包括压入力的计算和花键材料摩擦系数的选择,通过这两个参数可以得到夹紧力的估计值。
根据实际情况调整这两个参数可以得到更准确的结果。
夹紧力计算

夹紧力大小对于保证定位稳定、夹紧可靠、确定夹紧装置的结构尺寸等都有很大关系。
夹紧力过小,则夹紧不稳定,在加工过程中工件仍会发生位移而破坏定位,轻则影响加工质量,重则造成生产事故;夹紧力过大,将会增大夹紧装置的结构尺寸,也会使夹紧变形增大,影响加工质量。
所以,在夹紧力方向、作用点确定之后,还须确定切合实际、恰当的夹紧力大小。
在加工过程中,工件受到切削力、离心力、惯性力及重力的作用,理论上夹紧力的作用效果应与上述各力(矩)相平衡,但在不同条件下,这些作用力(矩)在平衡力系中对工件所起的作用并不相同。
如常规切削加工中、小型工件时,起决定作用的因素是切削力(矩)。
此外,切削力本身在加工过程中随切削过程的进行而变化,很难用准确的公式确定其大小;夹紧力大小还与工艺系统的刚度、夹紧机构的传动效率等有关,因此夹紧力的计算是一个很复杂的问题,一般只能作粗略的估算。
目前,大多采用切削原理实验公式粗略算出切削力(矩),再对夹紧力作简化估算。
估算夹紧力时,首先假设系统为刚性系统,切削过程处于稳定状态。
常规情况下,为简化计算,只考虑切削力(矩)对夹紧的影响,切削力(矩)用切削原理的实验公式计算,对重型工件应计及工件重力对夹紧的影响;在工件高速运动的场合,必须计入惯性力,尤其在精加工时,惯性力常是影响夹紧力的主要因素。
其次,分析并弄清对夹紧最不利的加工瞬时位置和情况,将此时所需的夹紧力定为最大值;根据此时受力情况列出其静力平衡方程式,即可解算出理论上的夹紧力Fj。
最后按下式计算出实际需要的夹紧力。
FjK =K·Fj (5-6)式中FjK-实际需要的夹紧力,单位为N;K-安全系数,一般取K=1.5~3,粗加工取大值,精加工取小值;Fj-在最不利的条件下由静力平衡计算出的夹紧力,单位为N。
上述估算方法,对夹具设计来说,其准确程度是能满足要求的。
第十三课 夹紧力的计算

在切削分力方向上 设置止推定位元件。
二、夹紧力作用点的选择
1.夹紧力应落在支承元件上或落在几个支承 所形成的支承面内
2.夹紧力应落在工件刚性较好的部位上
3.夹紧力应靠近加工表面
增加附加夹紧力与辅助支承
夹紧力W1作用在工 件主要定位基准面上, 远离加工表面。
=14mm
=tan-1(0.12)
R=D/2; r=d/2 (μ=tanⱷ) =6.84°
螺杆底部与 工件间的摩 擦角ⱷ2
tanⱷ2 =μ =0.12
=2174.3N
2X(150/2)X((150/2) = 10.863Xtan(2.65°+6.84°)+2X14X0.12
举例1、 工件的夹紧装置如图 3-2 所示。若外力 Q=150N,L=150mm, D=40mm,d=10mm, L1=L2=100mm,α=30°,各处摩擦损耗按传递 效率η=0.95 计算,试计算夹紧力 J。
第三章 工件的夹紧
第二节 夹紧力
工件在夹具中的夹紧是通过夹紧 装置对其施加一定的夹紧力来实现的。 所以在设计夹具装置时,首先要考虑 如何施加夹紧力,然后再确定机构。
夹紧力具有三个要素:
夹紧力的作用方向 夹紧力的作用点 夹紧力的大小
一、夹紧力方向的确定
1.夹紧力应垂直于主要定位基准面
夹紧力作用方向
D——钻孔直径Φ26 f每转进给量=0.1
KP——修正系数
M=0.21*D2*f 0.8*KP
=0.21X26
2
0.8
X0.1
X1.028
=23.05N.m
材料灰铸铁:HB取200
KP=(HB/190)0.55 =1.028
- 1、下载文档前请自行甄别文档内容的完整性,平台不提供额外的编辑、内容补充、找答案等附加服务。
- 2、"仅部分预览"的文档,不可在线预览部分如存在完整性等问题,可反馈申请退款(可完整预览的文档不适用该条件!)。
- 3、如文档侵犯您的权益,请联系客服反馈,我们会尽快为您处理(人工客服工作时间:9:00-18:30)。
盛年不重来,一日难再晨。
及时宜自勉,岁月不待人。
4.1.2 夹紧力计算及夹紧气缸的设计1、夹紧力的计算工件材料为AS9U3,大平面加工余量为1.5mm ,采用硬质合金端铣刀加工,切削力查参考文献〔1〕可根据如下公式计算: •式中:Fz ---铣削力(N)a f ---每齿进给量(mm/r) a w ---铣削宽度(mm) K FZ ---铣削力修正系数 d 0---铣刀外径(mm) a p ---铣削深度(mm) z ---•铣刀齿数 确定各参数值:(1).铣刀外径d 0=315mm ; (2).铣刀齿数Z =16;(3).每齿进给量af 是铣刀每转一个刀齿时铣刀对工件的进量:a f =V f /(z ·n)=360/(16×720)=0.031mm/r(4).铣削深度a p 对于端铣刀是指平行于铣刀轴线测量的被铣削层尺寸:a p =1.5mm(5). 铣削宽度a w 对于端铣刀是指垂直于铣刀轴线测量的被切削层尺寸:a w =240mm(6). 修正系数K FZ 取1.6;由表查得: c F =7750 x F =1.0 y F =0.75u F =1.1 w F =0.2 q F =1.3FZw q 0V wy fX PX FZ K nd Za a a c 25.0F fFFfFF⋅⋅⋅⋅⋅⋅⨯=⋅1.00.751.11.30.277501.50.031240160.25 1.6315720ZF ⨯⨯⨯⨯=⨯⨯⨯Fz=276.5N=28Kg(7). 理论所需夹紧力计算 确定安全系数:总的安全系数k =k1·k2·k3·k4k 1---- 一般安全系数; k 1取1.7;k 2----加工状态系数; 由于是精加工,所以k 2取1; k 3----刀具钝化系数; k 3取1.4; k 4----断续切削系数; k 4取1.2; ∴ k =1.7×1×1.4×1.2≈3 W =k ·p =3×28kg =84kg 2. 气缸的选择Q=W/(i ·η1·n )=84/(0.8×0.8×3)=44kg 由气缸传动的计算公式: Q=P·(πD2/4)·η式中: P--压缩空气压力=6atm =6kg/cm2 η--气缸摩擦系数,取0.8i —压板与工件的摩擦系数,取0.8n —夹紧气缸个数,本夹具为3 D--气缸直径(cm)D ==D=34.2cm通过以上理论计算,可以选择直径为50mm 的气缸。
但是,考虑到由于铣削过程中每个刀齿的不连续切削,作用于每个刀齿的切削力大小及方向随时都在变化,致使在铣削过程中产生较大的振动,因此,夹具需有足够的夹紧力。
此外还考虑到工厂所供压缩空气压力不稳定,零件加工余量发生变化,零件材料缺陷,以及其它不可预见性因素的影响,为安全可靠起见,选择直径为63mm 的气缸。
4.2 铣侧面工装定位精度计算定位误差是由基准位移误差和基准不重和误差组成的。
下面对工序尺寸31.85±0.075的定位误差进行分析计算。
4.2.1 基准直线位移误差△x 1定位孔尺寸为φ6.0450.0220+,园柱定位销尺寸为φ6.0450.0130.028--,因工件定位后处于垂直状态,由于自重定位孔与定位销总是单方向接触,所以基准直线位移误差为:△x 1=04.2.2 基准角位移误差△x 2由图可知2-Φ6.0450.0220+孔中心距L 414.6mm定位时因零件自身重量,使得两定位孔移动方向相同。
∴ tg △θ=(x 2max -x 1max )/(2L)式中:△θ ----两定位孔同向移动时,定位基准的转角 x 2max ----定位孔与菱形销之间的最大配合间隙 x 1max ----定位孔与圆柱销之间的最大配合间隙 L ----两定位孔中心距菱形销尺寸为φ60.0130.028--,定位孔尺寸为φ6.0450.022+ ∴x 2max =0.022+0.028+0.045=0.95mm x 1max =0.022+0.028=0.05mmtg △θ=(x 2max -x 1max )/(2L)=(0.95-0.05)/(2X414.6) =0.54×10-4△θ=0.003°加工面(长240)两端角位移误差△x 2'为:240×sin △θ=0.013mm4.2.3 基准不重合误差△B由工序简图可知,定位基准是由底平面B 和2-φ6.0450.0220+孔组成。
而工序尺寸31.83±0.4的工序基准为φ6.0450.0220+孔。
所以基准不重合误差△B =0mm 。
定位误差△D=△x 1+△x 2+△B =0+0.013+0=0.013mm由于0.013mm<<±0.075mm ,故能很好地满足加工精度求。
4.3 铣侧面工装设计4.3.1 铣削力的计算工件材料为铸造铝合金。
侧平面加工余量为1mm 。
•采用硬质合金端铣刀加工。
切削力可根据如下公式计算:式中:Fz ---铣削力(N)a f ---每齿进给量(mm/r) a w ---铣削宽度(mm) K FZ ---铣削力修正系数 d 0---铣刀外径(mm) a p ---铣削深度(mm) z---•铣刀齿数 确定各参数值:1、铣刀外径d 0=125mm ;2、铣刀齿数Z =8;3、每齿进给量af 是铣刀每转一个刀齿时铣刀对工件的进量:a f =v f /(z ·n)=638/(8×1120)=0.071mm/r4. 铣削深度a p 对于端铣刀是指平行于铣刀轴线测量的被铣 削层尺寸:a p =1mm5. 铣削宽度a w 对于端铣刀是指垂直于铣刀轴线测量的被切削层尺寸:a w =70mm6. 修正系数K FZ 取1.6;FZw q 0V wy fX PX FZ K nd Za a a c 25.0F fFFfFF⋅⋅⋅⋅⋅⋅⨯=⋅由表查得: c F =7750 x F =1.0 y F =0.75u F =1.1 w F =0.2 q F =1.31.00.75 1.11.30.277501.0.0717080.25 1.61251120ZF ⨯⨯⨯⨯=⨯⨯⨯=168N=17Kg •4.3.2 铣削夹具底板强度校核 1、夹具底板受力分析底板材料采用45钢,其屈服极限σs =245N/mm2,安全系数ns =1.5•。
故其许用应力[σ]=σs / n s =245/1.5=163N/mm2许用剪切应力[τ]=0.6[σ]=0.6×163N/mm 2=98N/mm 2底板受力情况如下图所示:图4.3 底板受力图(1)支承反力计算如下:根据公式可知:R B=P=168N(2)弯矩计算如下:已知:P:168N L:420mmM B=-PL=-168×0.42=-70.56N.m(3)底板转角计算如下:已知:P:168N L:420mm E:200GPa I:364583mm4θA=-168×4202/(2×200×364583) =0.00108°2、由上图可知:(1)夹具底所承受的最大弯矩:Qmax=168NMmax=168×0.42=70.56N.m(2)对截面尺寸进行校核弯曲正应力:Wz=bh2/6=280×252/6=1.75×105mm3σmax=Mmax/Wz=70.56×103/(1.75×105)=40.32×10-2 N/mm2因为:σmax=40.32×10-2 N/mm2<[σ]=163N/mm2另:底板受力转角仅为0.00108°,故可忽略,不予考虑。
所以:底板所选截面280×25完全满足强度要求。
第三章夹具设计3.1选择工序工艺过程为2.3.2中的方案三,选择工序60粗铣G面的夹具设计,在此工序前顶面B,底面F,左侧面E已经加工完毕,加工要求保证距E面尺寸106.9mm.3.2确定定位方案和定位元件根据零件结构和工序安排,本工序加工时的主要定位基准(限制三个自由度)3.3.1切削力的计算本工序为用硬质合金端铣刀粗铣G面,根据手册[1],铣削切削力的计算公式为:F=490a p.1f z74.0d 0.1-b D90.0z(3.1)注:式中 F —铣削力(N );a p —铣削深度(mm ); f z —每齿进给量(mm/z ); d —铣刀直径(mm );b D —铣削宽度(mm ); z —铣刀的齿数。
其中,a p =2.3mm ,f z =0.28mm/z ,d=160mm ,b D =78mm ,z=8,所以F=490×2.30.1×0.2874.0×1600.1-×7890.0×8=1108N3.3.2夹紧力的计算根据手册[1],夹紧力的计算公式为:F k =21μμ+KF(3.2)K=K 0K 1K 2K 3K 4K 5K 6(3.3)式中 F k —实际所需的夹紧力(N ); F —切削力(N );1μ—夹紧元件与工件间的摩擦因数; 2μ—工件与夹具支承面间的摩擦因数;K —安全系数;K 0~K 6—各种因数的安全系数。
根据[1]表17-10、表17-11,K 0=1.2,K 1=1.2,K 2=1.2,K 3=1.0,K 4=1.0,K 5=1.0, K 6=1.0,则K=1.2×1.2×1.2×1.0×1.0×1.0×1.0=1.7根据[7]表18-1,1μ=0.1,2μ=0.1,则F k =1.01.011087.1+⨯=9418N每个气缸可提供的夹紧力为7000N ,则2F=14000N>9418N ,可满足要求。
3.4定位误差的分析验算夹具的主要功能是用来保证工件加工表面的位置精度,影响位置精度精度的主要因素有三个方面:(1)工件在夹具中的安装误差,它包括定位误差和夹紧误差。
(2)夹具在机床上的对定误差,指夹具相对于刀具或相对于机床成形运动的位置误差。
(3)加工过程中出现的误差,它包括机床的几何精度、运动精度,机床、刀具、工件和夹具组成的工艺系统加工时的受力变形、受热变形,磨损,调整,测量中的误差,以及加工成形原理上的误差等。
第三项一般不易估算,前两项和不大于工件允许的三分之二为合格。
常用符号w D •∆表示。
根据[1]表17-9,B w D •∆=2(H-h )tan ∆g α(3.4)共享知识 分享快乐卑微如蝼蚁、坚强似大象如图3.1:B w D •∆=2×(98-51)×tan0.1º=0.16mm根据手册[1],加工精度等级IT=8,根据《几何量公差与检测》[8]附表3-2,公差为0.54mm ,在允许的范围内。