摆线双曲面齿轮减速器设计及性能优化
摆线针轮减速器设计与性能分析

摆线针轮减速器设计与性能分析摆线针轮减速器是一种广泛应用于各种机械设备中的传动装置,它以其紧凑结构、高效率和良好的运转平稳性在工业领域得到了广泛的应用。
本文将探讨摆线针轮减速器的设计与性能分析,希望为读者对该领域的了解提供一些帮助。
1.摆线针轮减速器的工作原理摆线针轮减速器由摆线齿轮和针轮组成,其工作原理类似于一种啮合的相位器。
当输入轴旋转时,摆线齿轮上的齿槽将针轮带动旋转,从而实现转速的减小。
该减速器适用于响应速度要求高的场景,如机床、机械手等。
2.摆线针轮减速器的设计要点在摆线针轮减速器的设计过程中,有几个要点需要注意。
首先是减速比的确定,减速比是指输出轴转速与输入轴转速之间的比值。
减速比的选择需要根据具体应用来确定,一般来说,较大的减速比可以提供更大的输出扭矩,但会降低输出转速。
其次是齿轮的材料选择,传动齿轮需要具备足够的强度和耐磨性,常见的材料有合金钢和硬质合金等。
此外,减速器的结构布局和每个零件的尺寸也需要进行合理的设计。
3.摆线针轮减速器的性能评估摆线针轮减速器的性能评估是设计过程中的重要一环。
在实际应用中,通过对减速器的转矩、转速和效率等指标进行测试和分析,可以评估其运行状态和性能。
转矩是减速器输出的主要性能指标,其大小决定了减速器的承载能力;转速是指输出轴的旋转速度,需要根据具体应用来选择;效率是指减速器输出功率与输入功率之间的比值,常见的摆线针轮减速器效率在80%以上。
4.摆线针轮减速器的应用案例摆线针轮减速器在机械设备中有着广泛的应用。
以机床为例,摆线针轮减速器可以将高速且低扭矩的电机输出转换为低速且高扭矩的运动,从而满足机床对转矩和速度的要求。
另外,摆线针轮减速器还常用于自动化设备、包装机械、输送设备等领域。
总结起来,摆线针轮减速器是一种常用于机械设备中的传动装置,通过齿轮的啮合实现转速的减小。
在设计过程中,需要注意减速比的选择、齿轮材料的确定等要点,并通过性能评估方法对减速器进行验证。
双曲柄四环板摆线针轮减速器中环板的形状优化_金映丽

!"#$%&’$( .67 89:;<7 =>?@A B9:> >C@D 3 E<?F7 3 FGE7 =G=<9C8?< EC@H677< >78:=7> CI ? @7H FGE7 >78:=7> ;?I78 9@ ? @7H 8>CJ7 E>C@=CE<71 .9 >78:=7 F67 H7CD6F 9B F67 H69<7 >78:=7>K F67 LM* I9BFH?>7 *+,-, CI ?89EF78 B9> F67 I6?E7 9EFCNCO?FC9@ 87ICD@ 9B F67 >C@D 3 E<?F7 C@ F67 89:;<7 =>?@A B9:> >C@D 3 E<?F7 =G=<9C8?< EC@H677< >78:=7> ?@8 ? D998 >7I:<F CI ?=6C7J781 .6CI N7F698 CI ?<I9 ?EE<CP =?;<7 B9> F67 I6?E7 9EFCNCO?FC9@ 9B 9F67> N7=6?@C=?< =9NE9@7@FI ?@8 6?I ? 6CD6 ?EE<C=?FC9@ J?<:71 )*+ ,-%.#( /-0"1* 2%&34 5-0% 6738 9 :1&$* 9 $+:* 2+’1-7.&1 ;73<=**1 5737$* B1*@*3$ (如图 & 双电机驱动双曲柄四环板摆线针轮减速器 所示 ) , 省去了传统摆线行星传动中制造精度要求很高 的复杂输出机构, 简化了传动结构; 将摆线轮装在两边 对称支承的定轴线输出轴上, 改变了输出轴处于悬臂
减速器性能优化设计及动力学仿真分析

减速器性能优化设计及动力学仿真分析在工程设计中,减速器扮演着至关重要的角色。
减速器能够将高速旋转的输入轴转换成低速大扭矩输出轴,广泛应用于各个领域,例如机械制造、航空航天、汽车工业等。
为了提高减速器的性能和可靠性,优化设计和动力学仿真分析成为必不可少的工作。
一、减速器性能优化设计1.设计目标的设定在进行减速器性能优化设计之前,我们首先需要明确设计目标。
设计目标可以包括传动效率的提高、承载能力的增加、噪音和振动的降低等。
2.材料选择和结构设计减速器的性能受到材料选择和结构设计的影响。
合理选择材料可以提高减速器的强度和耐久性,同时减小重量和成本。
结构设计需要考虑传动性能、紧凑性和装配性等因素。
3.齿轮副的优化设计齿轮副是减速器的核心部件,其设计对减速器性能起着决定性的影响。
通过选择合适的齿轮模数、齿数、齿形和齿向等参数,可以实现传动效率的最大化和噪音的最小化。
4.润滑和密封设计减速器在运行过程中需要进行润滑和密封。
恰当的润滑和密封设计可以减小齿轮与轴承之间的摩擦和磨损,延长减速器的使用寿命。
二、动力学仿真分析1.建立减速器的动力学模型动力学仿真分析是通过建立减速器的数学模型,模拟减速器在不同工况下的运动和力学特性。
根据设计和实际参数,可以建立各个部件的质量、惯性矩和刚度等参数,以及齿轮副的传动比、啮合刚度等参数,进而建立整个减速器的动力学模型。
2.动力学仿真参数的选择在进行动力学仿真分析之前,需要选择合适的仿真参数。
例如,输入轴的转速和扭矩、载荷的大小和方向、润滑条件等。
选择合适的仿真参数可以更好地反映实际工况下的减速器性能。
3.分析减速器的动态特性通过动力学仿真分析,可以得到减速器的动态特性。
包括扭矩传递特性、振动和噪音特性、轴承的受力和寿命等。
通过对动态特性的分析,可以评估减速器在不同工况下的性能表现,并针对性地进行优化设计。
4.动力学仿真结果的分析和优化分析动力学仿真结果,可以发现减速器存在的问题和不足之处,并针对性地进行优化设计。
rv减速器中摆线轮齿形优化修形与参数化设计

摆线轮齿形优化修形与参数化设计随着机械制造技术的不断进步和现代工业的快速发展,各种各样的机械设备在日常生活和生产中得到了广泛的应用。
而作为机械传动系统中关键的一环,减速器在提高传动效率、减小体积和减轻重量方面发挥着至关重要的作用。
而减速器中的摆线轮齿形优化修形与参数化设计,则是保证减速器正常运转和提高性能的关键之一。
1. 摆线轮齿形优化修形的意义摆线轮作为减速器中的主要传动元件,其齿形的优化修形对于减小摩擦、提高传动效率和延长零件使用寿命至关重要。
以往传统的摆线轮齿形设计往往存在着一些缺陷,比如齿根强度不足、传动效率低、噪声大等问题。
而通过对摆线轮齿形进行优化修形,可以有效地解决这些问题,提高减速器的整体性能。
2. 摆线轮齿形优化修形的方法与技术在摆线轮齿形的优化修形过程中,可以采用一系列现代化的方法与技术。
利用计算机仿真技术对摆线轮齿形进行力学分析,找出齿形设计中存在的问题并进行改进。
还可以借助CAD/CAM软件进行参数化设计,快速、精准地生成优化后的摆线轮齿形。
这些方法与技术的应用,可以大大提高摆线轮齿形优化修形的效率和精度。
3. 摆线轮齿形优化修形的关键技术与要点在进行摆线轮齿形优化修形时,需要重点关注一些关键技术与要点。
首先是确定优化修形的目标,例如提高传动效率、减小噪声等,并进行相应的设计方案选择。
其次是进行齿形参数化设计,确定摆线轮齿形的各项参数,并结合计算机仿真技术进行力学分析,找出存在的问题并进行优化。
最后是进行实际加工验证,验证优化后的摆线轮齿形设计是否可以满足要求,并在实际生产中取得良好的效果。
4. 摆线轮齿形优化修形的应用与展望摆线轮齿形优化修形是一个重要的工程技术领域,其应用范围非常广泛。
除了在减速器中的应用外,还可以应用于其他机械传动系统中,如齿轮箱、电机等,以提高传动效率和性能。
未来随着工业制造技术的不断发展,摆线轮齿形优化修形还有很大的发展空间,可以结合新型材料、加工工艺等,进一步提高传动系统的整体性能。
摆线齿准双曲面齿轮齿面主动设计

摆线齿准双曲面齿轮齿面主动设计杜进辅;方宗德;张永振;李建华【摘要】In order to pre-control the meshing performance of cycloid hypoid gears,a conjugate pinion tooth surface was generated by gear theoretical tooth surface.The pinion target tooth surface that meets the preconditions was obtained by modifying the conjugate tooth surface along the contact path and the contact line.The sum of tooth surface normal square errors between pinion theoretical and target tooth surface was calculated. The optimal model was built,setting the modifications of pinion machining parameters as variables and the least sum of square errors between pinion tooth surface and pinion target tooth surface on both sides as object.This optimization model was solved via sequence quadratic program.The validity of this modification method was demonstrated by using a numerical example of a high speed axle gear pair.The results show that the max normal errors on both sides are -4.7μm and -4.67μm,the transmission error deviations are 6.67% and 4%,the max contact path deviations are 0.275 mm and 0.177 mm,the results are found in line with the preconditions.%为预控双面法加工的摆线齿准双曲面齿轮的啮合性能,用大轮理论齿面展成与之共轭的小轮共轭齿面,将小轮共轭齿面沿啮合线方向和接触迹线方向分别进行修形,得到满足预置传动误差曲线以及接触印痕的目标齿面,计算出目标齿面与小轮理论齿面的法向偏差。
RV减速器摆线轮拓扑修形及啮合性能研究

RV减速器摆线轮拓扑修形及啮合性能探究摆线轮是RV减速器中用于传递动力的关键部件之一。
一般来说,摆线轮是由内凸轮和外摆线轮构成的。
内凸轮是一个曲线轮廓,与外摆线轮的啮合面相对应。
摆线轮的外形决定了其与外摆线轮的接触区域,从而影响摆线轮的传动效率和稳定性。
因此,探究摆线轮的拓扑修形对于提高RV减速器的性能至关重要。
摆线轮的拓扑修形主要包括轮齿修形和轮体修形两个方面。
轮齿修形是指对摆线轮的齿形进行调整,以提高其与外摆线轮的啮合性能。
轮体修形是指对摆线轮的整体外形进行调整,以改善其在传动过程中的运动特性和承载能力。
在轮齿修形方面,一般接受的方法是通过改变轮齿的曲线外形来调整摆线轮的啮合性能。
常用的曲线外形有圆弧、抛物线和渐开线等。
不同的曲线外形对摆线轮的啮合性能有不同的影响。
一般来说,圆弧外形的轮齿啮合效果较差,而抛物线和渐开线外形的轮齿啮合效果较好。
因此,在详尽设计中应选择合适的曲线外形,以提高摆线轮的啮合性能。
在轮体修形方面,主要是对摆线轮的外貌进行调整,以改善其运动特性和承载能力。
常用的调整方法有减小轮齿尖端的厚度、改变轮齿的压力角和增加齿面接触宽度等。
这些调整方法可以有效减小摆线轮在运动过程中的摩擦和磨损,提高其传动效率和寿命。
除了摆线轮的拓扑修形,摆线轮的材料选择和加工工艺也对其性能有影响。
一般来说,摆线轮的材料应具有较高的硬度、强度和耐磨性,以保证其在传动过程中的稳定性和耐久性。
常用的材料有合金钢、硬质合金和陶瓷等。
加工工艺方面,摆线轮的加工精度和表面质量对其啮合性能有直接影响。
因此,在摆线轮的加工过程中应注意加工工艺的控制和自动化水平的提高。
综上所述,RV减速器摆线轮的拓扑修形和啮合性能探究对于提高减速器的性能具有重要意义。
通过调整摆线轮的拓扑结构和优化轮齿外形,可以提高摆线轮的啮合性能和运行稳定性。
同时,在材料选择和加工工艺方面的优化也能进一步提高摆线轮的性能。
因此,对于RV减速器摆线轮的拓扑修形和啮合性能探究具有重要的理论和实际意义综合以上所述,摆线轮的拓扑修形和啮合性能的探究对于RV减速器的性能提升具有重要的意义。
双曲面齿轮减速电机

双曲面齿轮减速电机
双曲面齿轮减速电机是一种近年来出现的新型减速电机,它结合了普通齿轮减速电机及双曲面齿轮减速器,用较少的零部件和体积,又能够较高效地达到较大的传动比和较小的功率损耗。
双曲面齿轮减速电机不仅有较大的齿距,而且具有良好的精度特性,可以获得较好的低速和高功率传动效率。
此外,由于其减速齿轮的较大齿距,对于质量较轻的装置也有良好的传动效率。
在高传动比及低噪声应用中,双曲面齿轮减速电机的优势更加突出。
此外,该减速电机广泛适用于居家、商业及工业场所,可用于变频调速,及安装于电扶梯、自动扶梯、货梯等特种设备上,具备许多优点,如高可靠性、低噪声、高效率、可调节等优点,及可根据特定项目设计形状、技术参数等。
双曲面齿轮减速电机在高端应用领域具有三大优势:一是使用精度高、噪声低、效率高;二是结构紧凑、外形美观;三是维护消耗低、寿命长。
因此,双曲面齿轮减速电机不仅可用于高精度驱动设备,如机械手、电机调速器、齿轮箱、轴承半径抛光机等,也可用于高速高精度的智能装置,如机器人、印刷机、夹具机械臂等。
双曲面齿轮减速电机技术可以大大减少传动部件的数量和体积,大大降低传动机构的摩擦损耗和噪音,同时也减少了系统的刚性,可使传动系统一定程度上抗震,从而可以有效提高双曲面齿轮减速电机的可靠性和精度。
总而言之,双曲面齿轮减速电机具有较高减速比、较小功率损耗、高效率、结构紧凑、低噪声等优点,是当今高端减速机械的典范,具备良好的可靠性和精度特性,广泛应用于居家、商业及工业等多种场所。
减速器齿轮设计优化及其应用

减速器齿轮设计优化及其应用减速器是一种广泛应用于机械传动系统中的装置,其作用是通过减小输出转速的方式来实现力的放大和力矩传递。
作为减速器的核心组成部分,齿轮的设计和优化对于减速器的性能起着至关重要的作用。
本文将从减速器齿轮的设计优化及其应用方面展开讨论。
一、齿轮设计优化的原则和方法1.1 齿轮设计优化的原则齿轮设计的优化应基于减速器的工作条件和传动要求,以提高齿轮的传动效率、增强其承载能力和延长使用寿命为目标。
在设计过程中,应注重以下几个原则:(1) 合理选择齿轮的材料和热处理工艺,以确保齿轮具有足够的强度和硬度,同时要考虑到材料的可加工性和经济性。
(2) 通过合适的齿形设计和分布加载的方法,减小齿轮的啮合冲击和振动,降低噪声水平。
(3) 避免齿轮的过载和磨损,合理计算滚动接触疲劳寿命,确保齿轮的可靠性和稳定性。
(4) 考虑齿轮的润滑和冷却方式,以提高齿轮的工作效率和散热效果。
1.2 齿轮设计优化的方法为了实现齿轮的设计优化,通常可以采取以下几种方法:(1) 利用计算机辅助设计软件进行齿轮的建模和仿真分析,以快速评估不同设计方案的性能,并选择最佳方案。
(2) 通过理论计算和试验验证相结合的方式,确定齿轮的几何参数和材料参数,以满足设计要求。
(3) 运用优化算法和优化理论,对齿轮的设计参数进行调整和优化,以获得最佳的设计结果。
二、齿轮设计优化的应用案例2.1 汽车减速器齿轮的设计优化汽车减速器是汽车传动系统中的重要部件,其中的齿轮设计的优化对汽车的性能和经济性有着重要影响。
例如,在汽车变速器的设计中,通过优化齿轮的齿形曲线和齿数比,可以实现更加平稳的换挡和更高的传动效率,提升汽车的加速性能和燃油经济性。
2.2 工业减速器齿轮的设计优化在工业生产中,减速器扮演着至关重要的角色,广泛应用于各种机械设备中。
例如,在钢铁、矿山等重工业领域,减速器的传动功率和承载能力要求较高。
通过对齿轮的设计参数进行优化,可以提高减速器的工作效率和传动精度,延长减速器的使用寿命。
汽车双曲面锥齿轮双级主减速器设计毕业论文

汽车双曲面锥齿轮双级主减速器设计毕业论文第一章绪论1.1 引言本课题是设计汽车驱动桥双级主减速器,故本说明书将以“驱动桥双级主减速器设计”内容对驱动桥以及双级主减速器的结构型式与设计计算作一一介绍。
汽车驱动桥是汽车的重大总成,承载着汽车的满载簧荷重及地面经车轮、车架及承载式车身经悬架给予的铅垂力、纵向力、横向力及其力矩,以及冲击载荷;驱动桥还传递着传动系中的最大转矩,桥壳还承受着反作用力矩。
汽车驱动桥结构型式和设计参数除对汽车的可靠性与耐久性有重要影响外,也对汽车的行驶性能如动力性、经济性、平顺性、通过性、机动性和操动稳定性等有直接影响。
汽车主减速器是驱动桥最重要的组成部分,故称之为主减速器是由于它的减速比是传动系统中最大的,起到主要的降速增距作用,其功用是将万向传动装置传来的发动机转矩传递给驱动车轮,是汽车传动系中减小转速、增大扭矩的主要部件。
对发动机纵置的汽车来说,主减速器还有改变动力传输方向的作用。
汽车正常行驶时,发动机的转速通常在2000~3000r/min左右,这样高的转速直接传到驱动轮上,汽车将达到几百公里的时速,如果将这么高的转速只靠变速箱来降低下来,那么变速箱内齿轮副的传动比则需要很大,齿轮的半径也相应加大,也就是说变速箱的尺寸会加大。
另外,转速下降,扭矩必然增加,也加大了变速箱与变速箱后一级传动机构的传动负荷。
所以,在动力向左右驱动轮分流的差速器之前设置一个主减速器,可以使主减速器前面的传动部件,如变速箱、分动器、万向传动装置等传递的扭矩减小,同时也减小了变速箱的尺寸和质量,而且操控灵敏省力。
根据汽车分类标准(GB/3730.1-2001),车辆分为商用车和乘用车,车辆总质量>13T的商用车为重型汽车。
对一些载质量较大的载货汽车和公共汽车来说,根据发动机特性和使用条件,要求主减速器具有较大的传动比时,需要用两组减速齿轮实现两次减速增扭的双级主减速器。
1.2 国内汽车驱动桥主减速器发展现状目前我国正在大力发展汽车产业,尤其是中国加入WTO以后,中国的汽车工业迎来了新的机遇和挑战,汽车工业将发生深刻的改变,中国汽车也将从封闭走向开放,国外一些先进的汽车理念,也将会源源不段的输入到中国汽车行业中来,中国汽车工业逐渐成为世界汽车整体市场的一个重要组成部分。
减速器的设计与优化

减速器的设计与优化第一章:减速器的概述减速器是一种常用的机械传动装置,主要用于将高速、大扭矩的动力传递器降低至低速、小扭矩的动力传递器,以适应动力源与负载之间的转速、转矩要求。
减速器通常由输入轴、输出轴、齿轮和轴承等部件组成,其中关键部件是齿轮,齿轮的设计和制造质量对减速器的性能和寿命影响较大。
随着工况和负载的变化,不同用途的减速器需要有不同的设计和优化方案,以提高其性能和可靠性。
第二章:减速器的设计要求减速器的设计要求主要包括传递动力的效率、传动的稳定性、传递的准确性和承受负载的能力。
在设计减速器时,需要考虑负载的性质,例如负载的大小、方向和转速等因素,并确定减速器的减速比。
同时,还需要考虑齿轮的外形尺寸、齿轮的材料、齿轮的强度、齿轮的合理精度、齿轮的磨损和齿轮的合理润滑等问题。
以下是具体的设计要求:1. 传递动力的效率减速器传递的动力越高,其效率就越重要。
减速器的效率应该通常为95%以上,可以通过正确的齿轮参数设计来实现。
2. 传动的稳定性在传输高扭矩和低速运行的机械系统中,传动的稳定性至关重要。
维护传动的稳定性需要对齿轮数、进给率、模数、齿轮的形状和大小等做出妥善的选择。
3. 传递的准确性传递的准确性在精密机床、自动控制和仪器仪表等应用中尤为重要。
为了确保准确性,必须控制齿轮的精度和铸造沉降的影响,以保证准确的轴向和径向距离。
4. 承受负载的能力减速器将扭矩增加到在轴承支撑下并传递负载。
在设计这种承受负载能力的要求时,应考虑齿轮大小的参数和材料强度的选择。
第三章:减速器的优化针对如何进一步提高减速器的运行效率、寿命及可靠性问题,在减速器的设计过程中往往需要进行优化。
通过优化,可以改进齿轮的材料、精度、半径、斜面和支撑结构等,以获得所需的性能和可靠性。
以下是具体优化方法:1. 优化齿轮材料在确定齿轮结构后,可以通过使用更耐磨和耐高温材料来提高齿轮的使用寿命。
航空、轮船和能源等行业通常在齿轮设计中采用优质材料。
齿轮减速器的优化设计

资料范本本资料为word版本,可以直接编辑和打印,感谢您的下载齿轮减速器的优化设计地点:__________________时间:__________________说明:本资料适用于约定双方经过谈判,协商而共同承认,共同遵守的责任与义务,仅供参考,文档可直接下载或修改,不需要的部分可直接删除,使用时请详细阅读内容齿轮减速器的优化设计南昌航空大学机械工程专业苑晓帅齿轮传动是现代机械中应用最广的一种传动形式。
它的主要优点是:① 瞬时传动比恒定、工作平稳、传动准确可靠可传递空间任意两轴之间的运动和动力;② 适用的功率和速度范围广;③ 传动效率高,η=0.92-0.98;④ 工作可靠、使用寿命长;⑤ 外轮廓尺寸小、结构紧凑。
由齿轮、轴、轴承及箱体组成的齿轮减速器,用于原动机和工作机或执行机构之间,起匹配转速和传递转矩的作用,在现代机械中应用极为广泛。
国内的减速器多以齿轮传动、蜗杆传动为主,但普遍存在着功率与重量比小,或者传动比大而机械效率过低的问题。
另外,材料品质和工艺水平上还有许多弱点,特别是大型的减速器问题更突出,使用寿命不长。
国外的减速器,以德国、丹麦和日本处于领先地位,特别在材料和制造工艺方面占据优势,减速器工作可靠性好,使用寿命长。
但其传动形式仍以定轴齿轮传动为主,体积和重量问题,也未解决好。
当今的减速器是向着大功率、大传动比、小体积、高机械效率以及使用寿命长的方向发展。
减速器与电动机的连体结构,也是大力开拓的形式,并已生产多种结构形式和多种功率型号的产品。
近十几年来,由于近代计算机技术与数控技术的发展,使得机械加工精度,加工效率大大提高,从而推动了机械传动产品的多样化,整机配套的模块化,标准化,以及造型设计艺术化,使产品更加精致,美观化。
针对减速器存在的问题,本课题采用优化设计的方法,力求使减速器的体积达到最小,建立数学模型,并通过matlab语言编辑后,得到一组优化数据,到达预期目标,使减速器的体积比传统的经验设计结果减小20%--30%。
摆线减速机的优化设计与制造

摆线减速机的优化设计与制造摆线减速机是一种高效、耐用、减速比大的减速装置,在工业企业及机械制造中得到广泛应用。
在其创新发展的过程中,优化设计和制造已成为了一个不可或缺的环节。
本文旨在探讨如何通过优化设计和制造来提高摆线减速机的工作效率。
一、优化设计在摆线减速机的设计流程中,优化设计是一个核心环节,它关系到摆线减速机工作效率的提高。
下面从摆线轮、摆线节数、轴承、箱体四个方面探讨优化设计。
(一)摆线轮设计优化摆线轮是摆线减速机的核心部件,其设计和制造质量的稳定性和高度是保障减速器稳定工作的基础。
目前,常用的摆线轮一般都选用20CrMnTi合金轮齿钢。
在摆线轮的设计中,齿形设计是关键。
目前市面上常见的齿形设计有三种:S 型、C型、U型。
在实际运用中,S型是最优化的设计。
因为过流区域较小,能有效减少节渐变,并且较佳的预正和后逆微调效果,使摆线减速机运营更为平稳。
(二)摆线节数设计优化在设计摆线减速机时要注意摆线节数的设定,因为节数个数直接关系到其传动比和传动效率。
在制造摆线减速机时,选取多少节数,应根据实际的工作要求和工作环境来设定。
一般而言,节数的增多会降低传动效率,但是齿床误差影响反而会更小。
因此,有时候,增加一个节数可能会提高减速器的平稳程度。
关键在于如何掌握其配置方式。
一种实际可行的做法是以65、100、120、145、175、205的数列值作为摆线节数进行摆线减速机的设计。
(三)轴承设计优化轴承设计也是优化设计的重要环节,选用质量稳定的轴承能够增加减速器的稳定性,而不同型号的轴承也会直接影响减速器的寿命和效率。
三排圆柱滚子轴承结合式和双列锥形滚子轴承都可使用在摆线减速机中。
对于近几年来双列锥形滚子轴承较为流行,选择这种轴承的原因主要是因为其传力与轴向力更稳定,是一种较为理想的结构轴承。
(四)箱体设计优化通过优化箱体的结构,可以减小减速器在工作中对油温、噪音等的影响。
合适的箱体设计是通过计算得来的,箱体内部结构的合理设计能让减速器在工作中得到更好的润滑和冷却,同时减少摆线减速机的噪音。
摆线齿轮减速器设计与强度分析方法c
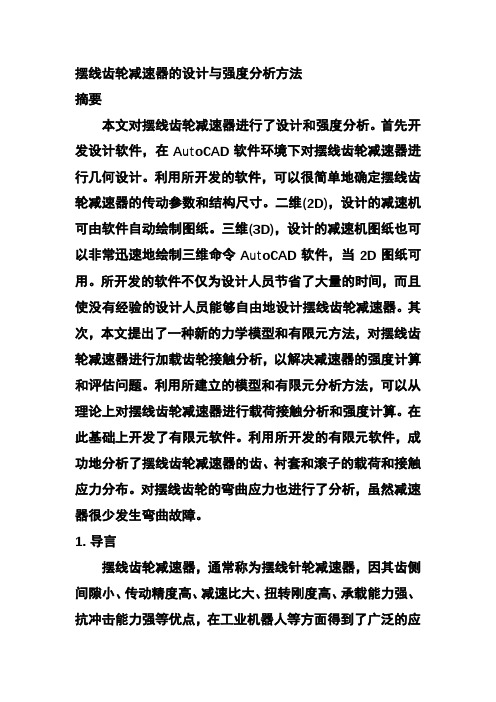
摆线齿轮减速器的设计与强度分析方法摘要本文对摆线齿轮减速器进行了设计和强度分析。
首先开发设计软件,在AutoCAD软件环境下对摆线齿轮减速器进行几何设计。
利用所开发的软件,可以很简单地确定摆线齿轮减速器的传动参数和结构尺寸。
二维(2D),设计的减速机可由软件自动绘制图纸。
三维(3D),设计的减速机图纸也可以非常迅速地绘制三维命令AutoCAD软件,当2D图纸可用。
所开发的软件不仅为设计人员节省了大量的时间,而且使没有经验的设计人员能够自由地设计摆线齿轮减速器。
其次,本文提出了一种新的力学模型和有限元方法,对摆线齿轮减速器进行加载齿轮接触分析,以解决减速器的强度计算和评估问题。
利用所建立的模型和有限元分析方法,可以从理论上对摆线齿轮减速器进行载荷接触分析和强度计算。
在此基础上开发了有限元软件。
利用所开发的有限元软件,成功地分析了摆线齿轮减速器的齿、衬套和滚子的载荷和接触应力分布。
对摆线齿轮的弯曲应力也进行了分析,虽然减速器很少发生弯曲故障。
1.导言摆线齿轮减速器,通常称为摆线针轮减速器,因其齿侧间隙小、传动精度高、减速比大、扭转刚度高、承载能力强、抗冲击能力强等优点,在工业机器人等方面得到了广泛的应用。
Lorenz Braren先生发明减速器至今已有70多年的历史,目前该减速器的许多部件已经制造和使用,但该减速器的许多设计问题至今仍未得到解决。
特别是这种减速器的强度计算方法在理论上还没有找到。
Lehman对摆线针轮减速器的齿面载荷分布进行了理论分析。
虽然Lehman得到了齿面载荷分布,但由于没有考虑摆线齿轮的结构变形,因此该方法不能用于摆线齿轮减速器的实际设计。
Lehman也无法研究摆线齿轮减速机的轴瓦和中心轴承滚子上的载荷。
Malhotra 和Parameswaran也用解析法对摆线针轮减速器的载荷分析和效率计算进行了初步的理论研究。
和Lehman的研究一样,由于在他们的分析中没有考虑摆线齿轮的结构变形的影响,因此无法得到准确的载荷在齿上的分布。
齿轮减速器体积减小优化设计项目实施效果

齿轮减速器体积减小优化设计项目实施效果
齿轮减速器体积减小优化设计项目的实施效果可以通过以下几个方面来评估:
1. 体积减小程度:通过比较优化设计前后齿轮减速器的体积大小来评估优化设计的效果。
如果体积减小达到预期,那么项目实施效果就可以认为是良好的。
2. 性能稳定性:优化设计后的齿轮减速器性能是否稳定,并且与原来的性能相当。
这可以通过性能测试和实际使用情况的比较来确定。
3. 使用寿命:优化设计后的齿轮减速器是否具有更长的使用寿命,如果寿命得到延长,那么项目实施效果就可以认为是良好的。
4. 成本节约:优化设计是否降低了生产成本。
如果生产成本能够得到降低,那么项目实施效果就可以认为是良好的。
5. 产品市场竞争力:优化设计后的产品是否具有更高的市场竞争力,比如更好的性能和更低的价格等。
如果齿轮减速器相对于竞争对手的产品具有更多的优势,那么项目实施效果就可以认为是良好的。
综上所述,优化设计后的齿轮减速器体积减小项目的实施效果可以通过上述几个方面来评估,只有在这些方面都取得了良好的效果时,我们才能说该项目的实施效果是成功的。
摆线磁齿轮复合电机设计与优化

2019年第47卷第4期D设计分析esign and analysis 葛研军等 摆线磁齿轮复合电机设计与优化13 收稿日期:2019-01-15基金项目:国家自然科学基金项目(51375063);大连市创新基金项目(2018J12SN071)摆线磁齿轮复合电机设计与优化葛研军,张 剑,李佩聪,杨小聪(大连交通大学,大连116028)摘 要:将摆线磁齿轮与永磁电机相结合,研究了一种可双端输出的摆线磁齿轮复合电机(CMGCM),给出了CMGCM 的运行机理及结构参数的设计方法;建立了摆线磁齿轮的有限元仿真模型,通过双控制变量法对各关键参数进行了仿真优化㊂结果表明,在总体积不变的条件下,优化后摆线磁齿轮的最大输出转矩较优化前提高了4.6%,可实现低速大扭矩直接式驱动㊂关键词:摆线磁齿轮复合电机;双变量控制法;参数优化中图分类号:TM359.9 文献标志码:A 文章编号:1004-7018(2019)04-0013-03Design and Optimization of Cycloidal Magnetic Gear Composite MotorGE Yan -jun ,ZHANG Jian ,LI Pei -cong ,YANG Xiao -cong(Dalian Jiaotong University,Dalian 116028,China)Abstract :Combining cycloidal magnetic gears with permanent magnet motors,a cycloidal magnetic gear composite mo⁃tor (CMGCM)with two-terminal output was proposed,and the operation mechanism and design method of structural pa⁃rameters of CMGCM were given.The finite element simulation model of the cycloidal magnetic gear was established,and the key parameters were simulated and optimized by the dual control variable method.The results show that the maximum output torque of the cycloidal magnetic gear was 4.6%higher than that before optimization under the condition of constant total volume,which can realize low speed and high torque direct drive.Key words :cycloidal magnetic gear composite motor (CMGCM),two-variable control method,parameter optimiza⁃tion0 引 言现有传动装置多以机械齿轮直接接触传动为主,在运行过程中会产生振动和噪声,严重时还会出现点蚀和胶合,且无过载保护作用㊂随着科学技术的发展,以磁场理论为基础并借助磁场相互耦合来实现的无接触传动得到了广泛关注[1]㊂与机械齿轮传动相比,磁齿轮传动具有降低传动系统噪声及减小摩擦损耗并提高整个系统工作效率等优势[2-4]㊂2001年,英国人Atallah K 和Howe D 提出了一种磁场调制式永磁齿轮[5],其传动比为5.57∶1,转矩密度可达100kN㊃m /m 3以上㊂磁场调制式永磁齿轮结构主要由高速内永磁圈㊁低速外永磁圈及调磁环组成,通过调磁环可实现内㊁外永磁圈的磁极对数匹配而进行变速传动㊂由于磁场调制式永磁齿轮机械结构复杂,运行过程中发热量大,且传动比较小等缺陷[6-7],导致其应用范围严重受限㊂2008年,丹麦学者Joergense F T 等提出了一种传动比为21∶1,转矩密度高达183kN㊃m /m 3的摆线永磁齿轮(以下简称CMG)[8],由于其机械结构与现有的少齿差摆线齿轮相同,因此可较好地弥补磁场调制式永磁齿轮的上述缺陷,具有较好的应用前景㊂本文将摆线磁齿轮与永磁电机相结合,设计出一种基于摆线磁齿轮的永磁复合电机(以下简称CMGCM),该电机利用摆线磁齿轮的高转矩密度与高传动比特性,可实现低速大扭矩直驱式驱动,若将其替代传统异步电动机+机械齿轮箱的传动系统,既可取消机械齿轮箱所必须的润滑油,又可消除机械齿轮箱所造成的振动和噪声,且能提高传动系统的运行效率并降低相关维护费用㊂1 CMGCM 运行机理所设计的CMGCM 为一种如图1所示的双端输出结构㊂图1中,永磁转子㊁偏心轴压装在空心轴上,内永磁圈压装在偏心轴上;当定子绕组通电时,永磁转子带动空心轴及偏心轴产生旋转运动,进而使内永磁圈产生摆线运动,并通过销轴及其所连接的动力输出圆盘将动力传递给双端输出轴输出㊂由摆线齿轮传动原理可知,销轴及动力输出盘产生的D设计分析esign and analysis 2019年第47卷第4期 葛研军等 摆线磁齿轮复合电机设计与优化14 旋转运动与双端输出轴同心㊂图1 CMGCM 轴向剖面结构示意图图1中,CMG 由两个几何形状完全相同且与空心轴中心线对称安装的内永磁圈和一个共用的外永磁圈构成;其中,偏心轴同时与两个内永磁圈刚性连接;两个内永磁圈在偏心方向互成180°,以平衡空心轴上由内永磁圈引起的不对称受力,以提高CMG 的承载能力[9]㊂图1中,外永磁圈固定,动力从空心轴输入,经内㊁外永磁圈磁场作用,由动力输出圆盘输出㊂若设CMG 的传动比为G ,内㊁外永磁圈的磁极对数分别为p i 和p o ,则有p o =p i +1,且传动比G =p i p i -p o =-pi1[10]㊂2 CMGCM 结构参数选取若设永磁电机磁极对数p =10,额定功率P =23kW ,额定电压U =380V ,额定频率f =50Hz ,CMGCM 的额定输出转速n =6r /min ,则CMG 所需的传动比G :G =60fpn所需的输出转矩T :T =9.55P n 代入上述数据㊂G =50,T ≈37kN㊃m㊂取p i =50,则p o =p i +1=51㊂图2为CMG 机械结构示意图㊂图2中,R 1为内永磁圈轭铁内径,R 2为内永磁圈轭铁外径,R 3为内永磁圈永磁体内径,R 4为内永磁圈永磁体外径,R 5为外永磁圈永磁体内径,R 6为外永磁圈永磁体外径,R 7为外永磁圈轭铁内径,R 8为外永磁圈轭铁外径,h 为永磁体厚度,τ为永磁体宽度,δ为最小气图2 CMG 机械结构示意图隙,d 为偏心距㊂设CMG 体积及轴向长度分别为V 及L ,并取CMG 转矩密度T d =225kN㊃m /m 3,则有:V =πR 24㊃L =TT d(1)若取L =250mm ,则由式(1)可得R 4=460mm ㊂由电磁场理论知,两个磁场之间应有足够的有效作用面积,才能实现转矩的稳定传递㊂由于CMG中内永磁圈与外永磁圈的轴向长度相同,因此当内㊁外永磁圈永磁体的几何尺寸及磁极极距相同时,所传递的转矩达到最大㊂综上,可得表1所示的CMG 结构参数初选值㊂表1 CMG 模型参数初选值参数物理意义数值p o 外永磁圈永磁体极对数51p i内永磁圈永磁体极对数50R 1/mm 内永磁圈轭铁内径434R 2/mm 内永磁圈轭铁外径456R 3/mm 内永磁圈永磁体内径449R 4/mm 内永磁圈永磁体外径460R 5/mm 外永磁圈永磁体内径469R 6/mm 外永磁圈永磁体外径480R 7/mm 外永磁圈轭铁内径473R 8/mm 外永磁圈轭铁外径495δ/mm 最小气隙1τ/mm 永磁体宽度26h /mm 永磁体厚度11M /(A㊃m -1)永磁体磁化强度-890000μ0/(H㊃m -1)真空磁导率4π×10-7μr相对磁导率 1.0997B r /T 永磁体剩磁 1.233 CMG 静态模型基于表1的CMG 结构参数,采用Ansys 有限元分析软件建立二维静态仿真模型,可得如图3所示的输出转矩T 与转角θ的关系曲线㊂图3 输出转矩T 与相对转角θ关系由图3可知,随着内永磁圈的旋转,输出转矩T 呈正弦波形变化,当内永磁圈转过1/2个及3/2个磁极角度时,即θ为1.8°及5.4°时,输出转矩达到峰值,即T max =36.9kN㊃m ㊂T max 与永磁材料性能及CMG 各结构参数直接相关㊂将T max 代入式(1)可得T d =222kN㊃m /m 3,与设计时初选的T d =225kN㊃m /m 3基本一致,说明模型初选参数基本正确㊂ 2019年第47卷第4期D设计分析esign and analysis 葛研军等 摆线磁齿轮复合电机设计与优化15 4 CMG 参数优化由于输出转矩是评价CMG 最重要的性能指标之一,为此本文将其作为参数优化目标,并以此分析各结构参数对CMG 输出转矩的影响㊂在R 4和R 5不变的条件下,采用双变量控制法分析并优化各结构参数对T max 的影响㊂4.1 h 与T max 关系由图2可知:R 3=R 4-h i R 6=R 5+h o h =h i =h üþýïïïïo (2)式中:h i ,h o 分别为内,外永磁圈永磁体厚度㊂固定外永磁圈不动,使内永磁圈旋转,并控制h 的变化范围为8~15mm㊂由静态仿真可得h 与T max 关系,如图4所示㊂由图4可知,当h 增加时,内㊁外永磁圈的磁场强度不断增强,T max 也随之增加;当h ≥12mm 时,T max 即满足设计要求㊂综合考虑CMG 过载能力及永磁体用量,取h =12mm ,则由式(2)可得:R 3=448mm ,R 6=481mm㊂图4 内外永磁圈永磁体厚度h 与T max 关系4.2 R 1和R 8与T max 关系R 1和R 8决定了内㊁外永磁圈轭铁厚度㊂若轭部太厚,将造成材料成本增加,并使转动惯量增大;反之,会使磁路饱和,影响CMG 输出转矩㊂由静态仿真可得如图5所示的R 1和R 8与T max关系㊂图5 R 1,R 8与T max 关系由图5可知,当R 1在438~449mm,R 8在481~492mm 范围内,T max 随着R 1减小和R 8增大而逐渐增大;当R 1≤438mm,R 8≥492mm 时,T max 基本不变,此时轭部厚度为11mm,即轭部厚度约为永磁体宽度的1/2时,轭部厚度足以满足永磁体磁路要求㊂综合考虑磁路及机械结构,选取R 1=434mm ,R 8=495mm ㊂4.3 R 2和R 7与T max 的关系R 2和R 7决定内㊁外永磁圈的齿槽转矩㊂由静态仿真可得如图6所示的R 2和R 7与T max 关系㊂由图6可知,T max 随R 2的增大和R 7的减小而减小,此时齿槽转矩增大而输出转矩降低㊂当R 2在454~460mm,R 7在469~475mm 范围内时,T max 随着R 2减小和R 7增大而逐渐减小;当R 2≤454mm ,R 7≥475mm 时,T max 不再有明显变化,即齿槽转矩对CMG 输出转矩的影响可以忽略㊂因此,取R 2=454mm,R 7=475mm㊂图6 R 2,R 7与T max 关系综上,可得如表2所示优化后的CMG 结构参数,未变参数参见表1㊂表2 CMG 模型参数优化值参数物理意义数值R 1/mm内永磁圈轭铁内径434R 2/mm 内永磁圈轭铁外径454R 3/mm 内永磁圈永磁体内径448R 6/mm 外永磁圈永磁体外径481R 7/mm 外永磁圈轭铁内径475R 8/mm 外永磁圈轭铁外径495h /mm永磁体厚度12 重新建立优化1后的有限元仿真模型,可得如图7所示优化后的输出转矩T 与转角θ的关系曲线㊂图7 模型优化前后输出转矩对比图由图7可知,在CMG 体积不变的条件下,优化后的最大输出转矩T max =38.6kN㊃m,较优化前的T max (与图3相同)提高了4.6%;说明通过对主要结构参数的合理优化,可较大幅度地提高CMG 最大输出转矩及其转矩密度㊂(下转第20页) D设计分析esign and analysis 2019年第47卷第4期 汪思敏等 磁极偏移对无齿槽无刷电动机振动与噪声影响研究 20 对应的电机声压级仿真值为62Hz,实验值67Hz;而高频段电机发生二阶共振,声压级较大,仿真值为63dB(12427Hz),实验值为60dB(11139Hz),与振动加速度对应㊂4 结 语无齿槽无刷电动机转子磁极偏移后,电机径向力波的非极数倍数次谐波大幅度增加,特别是极对数次谐波,该阶次下电磁力谐波幅值随偏移角度增加而大幅度增大,对电机的低频段振动噪声影响较大,而高频段与电机二阶固有模态接近,电机发生二阶共振;电机的最大振动加速度幅值随磁极偏移角度增加而增大㊂从限制振动加速度角度看,磁极偏移角应控制在5°以内㊂参考文献[1] YOON T,LIEU D K.Magnetization patterns of permanent ringmagnets in brushless DC motors[J].Electric Machines&PowerSystems,2005,33(2):127-144.[2] YOON T,LIEU D K.A method to verify accuracy of predictedmagnetic orientation of a permanent ring magnet in a brushless DCmotor[J].IEEE Transactions on Magnetics,2007,43(9):3638-3644.[3] WON S H,KIM W H,JU L.Effect of the incomplete magnetizationof permanent magnet in the characteristics of BLDC motor[J].IEEE Transactions on Magnetics,2009,45(6):2847-2850. [4] PARK S C,YOON T H,KWON B I,et al.Influence on brushlessDC motor performance due to unsymmetric magnetization distribu⁃tion in permanent magnet[J].IEEE Transactions on Magnetics, 2000,36(4):1898-1901.[5] 李艳明,郭宏,谢清明,等.充磁导致的超高速永磁同步电机不平衡磁拉力[J].北京航空航天大学学报,2013,39(6):771-775.[6] 张家思.山地车永磁无刷电机振动与噪声研究[D].武汉:湖北工业大学,2017:30-31.[7] ZHU Z Q,HOWE D.Instantaneous magnetic field distribution inbrushless permanent magnet DC motors,Part I:Open-circuit Field [J].IEEE Transactions on Magnetics,1993,29(1):143-151.[8] ZHU Z Q,HOWE D.Electromagnetic noise radiated by brushlesspermanent magnet DC drives[C]//International Conference on E⁃lectrical Machines and Drives.IET,2012:606-611. [9] SUN T,KIM J M,LEE G H,et al.Effect of pole and slot combina⁃tion on noise and vibration in permanent magnet synchronous motor [J].IEEE Transactions on Magnetics,2011,47(5):1038-1041.[10] ISLAM M S,ISLAM R,SEBASTIAN T.Noise and vibration char⁃acteristics of permanent-magnet synchronous motors using elec⁃tromagnetic and structural analyses[J].IEEE Transactions on In⁃dustry Applications,2011,50(5):3214-3222. [11] KO H S,KIM K J.Characterization of noise and vibration sourcesin interior permanent-magnet brushless DC motors[J].IEEETransactions on Magnetics,2004,40(6):3482-3489. [12] 陈阳生,林友仰.永磁电机气隙磁密的分析计算[J].中国电机工程学报,1994(5):17-26.[13] HUANG S,AYDIN M,LIPO T A.Electromagnetic vibration andnoise assessment for surface mounted PM machines[C]//IEEE.Power Engineering Society Summer Meeting.2001(3):1417-1426.[14] YANG H,CHEN Y.Influence of radial force harmonics with lowmode number on electromagnetic vibrationof PMSM[J].IEEETransactions on Energy Conversion,2014,29(1):38-45. [15] 代颖,崔淑梅,宋立伟.车用电机的有限元模态分析[J].中国电机工程学报,2011,31(9):100-104.(上接第15页)5 结 语当内永磁圈与外永磁圈上永磁体轴向长度㊁几何尺寸及磁极极距相同时,CMG所传递的转矩及转矩密度最大㊂CMG内㊁外永磁圈轭铁厚度约为永磁体宽度的1/2时,即可满足永磁体磁极的磁路要求㊂基于CMG运行原理的永磁复合电机,具有大传动比特性,可替代现有机械齿轮箱并较好实现低速大转矩的直接驱动㊂参考文献[1] 宁文飞,包广清,王金荣.磁齿轮拓扑分析及其应用综述[J].机械传动,2012,36(2):91-96.[2] 杨岸涛,井立兵,李浩.一种混合充磁同心磁齿轮及其复合电机分析[J].微特电机,2017,45(4):31-33,38.[3] MCGILTON B,CROZIER R,MCDONALD A,et al.Review ofmagnetic gear technologies and their applications in marine energy[J].IET Renewable Power Generation,2018,12(2):174-181.[4] 周晓刚,辛灿祥.基于响应面法的磁力齿轮参数优化设计[J].微特电机,2016,44(10):41-43.[5] ATALLAH K,HOWE D.A novel high-performance magnetic gear[J].IEEE Transactions on Magnetics,2001,37(4):2844-2846.[6] 葛研军,王彪,牛志,等.同心式永磁齿轮损耗分析及结构优化[J].大连交通大学学报,2016,37(4):61-66.[7] EVANS D J,ZHU Z Q.Influence of design parameters on magneticgear's torque capability[C]//Electric Machines&Drives Confer⁃ence(IEMDC),IEEE.2011:1403-1408.[8] JORGENSEN F T,ANDERSEN T O,RASMUSSEN P O.The cy⁃cloid permanent magnetic gear[J].IEEE Transactions on Industry Applications,2008,44(6):1659-1665.[9] 郑文纬,吴克坚.机械原理[M].北京:高等教育出版社,1997:262-266.[10]葛研军,胡浩,王玥,等.摆线式永磁齿轮结构参数与转矩关系[J].机械设计,2016(6):91-95.作者简介:葛研军(1964 ),男,教授,主要研究方向为机电传动与控制㊂。
毕业设计方案说明书一摆线锥齿轮减速器设计方案说明书

本科毕业设计说明书EBJ-160掘进机装载部件设计及关键件加工工艺EBJ-160 BORING MACHINE LOADED WITH THE KEY COMPONENTS OF THE DESIGN AND PROCESSING TECHNOLOGY学院<部):机械学院专业班级:机械设计05-2班学生姓名:戴兵指导教师:周哲波2009年 6 月 8 日安徽理工大学毕业设计任务书专业班级机械05级2班姓名戴兵日期 2009-6-81.设计题目EBJ-160掘进机装载部件设计及关键件加工工艺<专题)一级摆线锥齿轮减速器设计2.设计原始资料:3.设计文件:说明书:1-1.5万字图纸:减速器装配图,锥齿轮轴零件图,大锥齿轮零件图,偏心盘零件图,轴承座零件图模型<工业设计专业)4. 设计任务下达日期:2009.3.175. 设计完成日期:2009.6.86. 设计各章节答疑人:部分部分部分部分部分部分7. 指导教师8. 系<室)负责人9. 院负责人中文摘要摘要:本次设计的题目是EBJ-160掘进机装载部件设计及关键件加工工艺设计,我的专题是对该掘进机的一级摆线锥齿轮减速器设计。
首先,对有关掘进机的书籍进行初步阅读,了解掘进机的发展现状及其的技术上发展情况和瓶颈。
核心是研究掘进机的装载部分的作用及其设计方案,为后期的设计打好基础。
其次,对这次设计主题即掘进机一级摆线锥齿轮减速器设计进行研究,从现有的减速器装配图上的研究开始,分析装配图上的各个零部件的作用及其位置关系,弄清部件彼此之间的装配关系。
最后重新设计这个减速器,设计思想是在不改变原有结构的基础上,对不足的地方进行优化改进。
这次设计的重点是摆线锥齿轮轴的设计和校核,以及该轴上的轴承的设计和校核。
关键词:掘进机;摆线锥齿轮;减速器;English AbstractAbstract:The design is the subject of EBJ-160 boring machine loaded with the key components of the design and processing technology design, my topic is the level of the boring machine cycloid bevelgear reducerdesign.First of all, boring machine for the preliminary reading of the bookto understand the development of boring machine and its technical developments and bottlenecks. The core is to study the loading part of boring machine and its design, for the latter designed to lay a solid foundation. Secondly, the design theme of the boring machine that is a cycloid bevel gear reducer design study, the reducer from the existing assembly drawing on the beginning of the study, analysis of the assembly drawing on the role of the various components and its location, clarify the components of the assembly relations between. Finally, re-design of the reducer, the design idea is not to change the original structure on the basis of lack of improvement of the local optimization. Is designed to focus on the cycloid bevel gear shaft design and verification, as well as the axis of the bearing design and verification. Key words: boring machine。
汽车主要减速器双曲面齿轮的稳健优化设计

汽车主要减速器双曲面齿轮的稳健优化设计
廖林清;郑长松
【期刊名称】《四川兵工学报》
【年(卷),期】1998(019)002
【摘要】本文以双曲面齿轮的整体安装体积最为目标,对汽车主减速器双曲齿轮的基本参数进行稳健优化设计,较好地解决了汽车主减速器双曲面齿轮传统设计中的问题,得到了满足设计要求的最优参数组合及其容差值。
【总页数】4页(P11-14)
【作者】廖林清;郑长松
【作者单位】重庆工业管理学院;重庆工业管理学院
【正文语种】中文
【中图分类】U463.212
【相关文献】
1.降低汽车主减速器噪声的双曲面齿轮CAD优化设计 [J], 伍利群
2.基于低噪声的汽车主减速器双曲面齿轮优化设计 [J], 王猛;刘世达
3.汽车主减速器双曲面齿轮的计算机辅助设计 [J], 陈勇;王尧
4.汽车主减速器双曲面齿轮结构参数优化设计 [J], 许和变;温智灵
5.汽车主减速器双曲面齿轮结构参数优化设计 [J], 廖林清;俞宁;等
因版权原因,仅展示原文概要,查看原文内容请购买。
双曲面齿轮减速电机

双曲面齿轮减速电机双曲面齿轮减速电机是一种新型的减速电机,它以双曲面齿轮配合而成,它可以大大降低电机的驱动效率,降低振动和噪音,提高散热性能,使电机具有更高的综合性能。
曲面齿轮减速电机可以满足工业自动化,家用和家电行业的高效率和高精度驱动要求。
双曲面齿轮减速电机可以实现以下功能:一、制造可靠性双曲面齿轮减速电机可以确保整个电机的制造可靠性,并且在操作中能够保证较低的空气阻力,大大提高电机的可靠性。
二、高效减速双曲面齿轮减速电机可以实现高效减速,减少电机的体积,提高减速比,提高电机的机械效率,因此,它可以更好地节能减排。
三、低噪音双曲面齿轮减速电机能够有效减少噪音,使电机具有更高的综合性能。
同时,由于齿轮传动系统中的摩擦噪音可以被有效地减小,因此,双曲面齿轮减速电机可以实现较低的噪音水平。
四、高散热性双曲面齿轮减速电机的齿轮传动系统可以实现更好的散热能力,从而实现有效的散热补偿,使电机具有更高的可靠性。
五、高质量双曲面齿轮减速电机采用高质量的齿轮,更多的是采用优质的钢材来制造,并且可以通过多重检测保证齿轮的可靠性,这样以来,双曲面齿轮减速电机可以达到更高的故障率。
双曲面齿轮减速电机技术性能双曲面齿轮减速电机具有优异的技术性能,它的机械效率高达90%以上,电机的使用寿命可以达到30000小时以上,减速比可以达到50:1,具有较高的负载能力,最大扭矩可以达到800N m,可以满足不同环境下客户的需求。
综上所述,双曲面齿轮减速电机是一种具有高驱动效率、低噪音、良好的减振、优良的散热性能和较低的故障率的可靠的减速机。
它的出色性能可以得到许多领域的认可,在工业自动化、家用和家电行业的高效率和高精度驱动均可获得极大的收益。
双曲面齿轮减速电机的发展将有助于市场的持续繁荣发展,以满足人们不断变化的需求。
齿轮减速机的优化设计

#" 设计过程与步骤
# 6 !" 已知参数 该单级直齿圆柱齿轮减速机输入轴小齿轮的扭 矩是 -9 > !% !&? @8・AB, 原齿轮模数 B > & BB, 齿 数 C > !9 ; 两齿轮宽度 D > !< AB, 轴支承跨距 0 > #! AB, 小齿轮轴轴径 E9F > 9! AB, 大齿轮轴轴径 E!F > 9: AB, 传动比 G > ? 。按在保证承载能力条件下最大 限度地减轻重量的要求来重新确定减速机齿轮参 数。 齿轮各部分结构尺寸的符号见图 9 , 轴板孔数 为 #。
将 KF! 、 E (! 、 E$ 、 A 按上述公式代入消去后, 可 !、 B、 0、 E 9 F、 E ! F、 G 等 % 个参数, 知体积 3 决定于 D 、 C9 、 而 G 为设计常量, 故其余 : 个为设计变量。 L ! ( C9 , L# ( 0, L ? ( E 9 F, 取 L9 ( D , L< ( B , L: ( E ! F, 将设计变量代入体积和公式, 经展开整理得目 标函数为:
)按齿轮的弯曲疲劳强度条件: (<=! [ (B ] (B * ! #1! $C 1! , 小齿轮分度圆直径, 1! * $A! ; [ (B ] 式中:
( , 许用弯曲应力, 取 [ ( B ]* ( "!3 ?’ @ 0$( 小齿轮) , ( [ ( B ]* ( !%% ?’ @ 0$( 大齿轮) ; C $齿形系数。
2% 2% 实心轴取 L * -/ !1! * -/ !+% & 1! 。
得出: ’!& ( +)* &&- , !+% &
- 1、下载文档前请自行甄别文档内容的完整性,平台不提供额外的编辑、内容补充、找答案等附加服务。
- 2、"仅部分预览"的文档,不可在线预览部分如存在完整性等问题,可反馈申请退款(可完整预览的文档不适用该条件!)。
- 3、如文档侵犯您的权益,请联系客服反馈,我们会尽快为您处理(人工客服工作时间:9:00-18:30)。
摆线双曲面齿轮减速器设计及性能优化
摆线双曲面齿轮减速器是一种常用于工程机械传动系统中的重要元件,其设计和性能优化对于提高传动效率和传动精度具有重要意义。
本文将探讨摆线双曲面齿轮减速器的设计原理和性能优化方法,旨在为工程师们提供有关减速器技术的一些思路和方法。
首先,摆线双曲面齿轮减速器的设计原理是基于摆线齿轮和双曲面齿轮的组合,并通过齿数比和齿面修形来实现传递不同速比的转矩。
摆线齿轮具有较佳的传动效率和传动平稳性,而双曲面齿轮则能够实现高精度的传动和更大的传动比范围。
因此,将摆线齿轮和双曲面齿轮相结合,可以使减速器在高负荷、高转速和高精度传动等要求下得到优化。
其次,摆线双曲面齿轮减速器的性能主要有传动效率、传动精度和噪音振动三个方面。
为了提高传动效率,可以通过优化齿面修形、减少齿轮啮合损失和减小传动链条的摩擦阻力等途径来进行。
传动精度的提高可以从齿轮的制造精度、配合间隙的控制以及减少齿轮的弯曲变形等方面入手。
噪音振动的控制可以通过选择合适的齿轮材料、优化齿轮的设计参数以及采用减震结构等方法来实现。
综上所述,传动效率、传动精度和噪音振动都是设计和性能优化的重要方面。
在摆线双曲面齿轮减速器的具体设计过程中,需要考虑减速器的工作条件、功率传递要求以及材料强度等因素,并根据特定应用场景进行参数的选择和计算。
同时,为了提高减速器的性能,可以采用现代
设计软件进行模拟仿真和优化设计。
通过减速器的多种参数变量和场景模拟,可以较为准确地预测减速器的性能并进行优化。
此外,减速器的制造工艺和装配精度也对其性能表现有重要影响。
在制造过程中,需要保证齿轮的制造精度,确保啮合面的平行度和同轴度,以及齿轮与轴的配合间隙的控制等。
装配过程中,需要保证各零部件的准确定位,排除各种杂波和干扰,以保证减速器的正常工作和性能发挥。
总结起来,摆线双曲面齿轮减速器的设计和性能优化是一个综合考虑多个因素的过程。
通过理解减速器的工作原理和性能指标,重点优化传动效率、传动精度和噪音振动等方面,同时结合现代设计软件的辅助,可以实现减速器设计的理想性能。
同时,在制造和装配过程中注重精度控制和工艺流程,也是确保减速器性能的重要环节。
希望本文能够为工程机械领域的设计工程师们提供一定的参考和借鉴。