SMT设备故障处理分析报告
SMT不良分析及改善措施
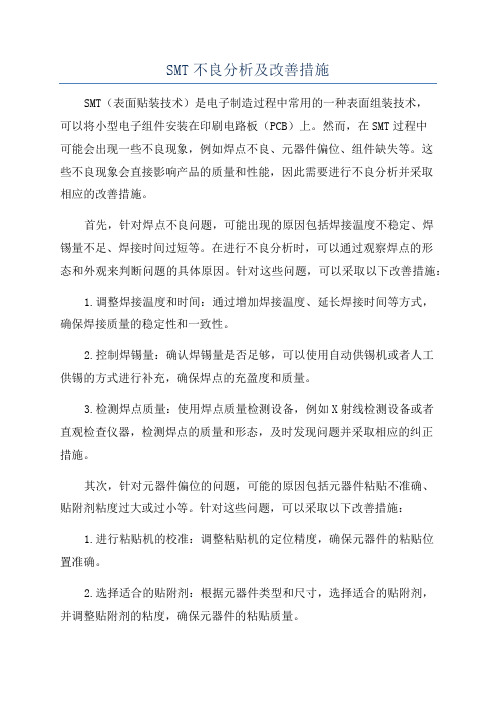
SMT不良分析及改善措施SMT(表面贴装技术)是电子制造过程中常用的一种表面组装技术,可以将小型电子组件安装在印刷电路板(PCB)上。
然而,在SMT过程中可能会出现一些不良现象,例如焊点不良、元器件偏位、组件缺失等。
这些不良现象会直接影响产品的质量和性能,因此需要进行不良分析并采取相应的改善措施。
首先,针对焊点不良问题,可能出现的原因包括焊接温度不稳定、焊锡量不足、焊接时间过短等。
在进行不良分析时,可以通过观察焊点的形态和外观来判断问题的具体原因。
针对这些问题,可以采取以下改善措施:1.调整焊接温度和时间:通过增加焊接温度、延长焊接时间等方式,确保焊接质量的稳定性和一致性。
2.控制焊锡量:确认焊锡量是否足够,可以使用自动供锡机或者人工供锡的方式进行补充,确保焊点的充盈度和质量。
3.检测焊点质量:使用焊点质量检测设备,例如X射线检测设备或者直观检查仪器,检测焊点的质量和形态,及时发现问题并采取相应的纠正措施。
其次,针对元器件偏位的问题,可能的原因包括元器件粘贴不准确、贴附剂粘度过大或过小等。
针对这些问题,可以采取以下改善措施:1.进行粘贴机的校准:调整粘贴机的定位精度,确保元器件的粘贴位置准确。
2.选择适合的贴附剂:根据元器件类型和尺寸,选择适合的贴附剂,并调整贴附剂的粘度,确保元器件的粘贴质量。
3.进行视觉系统的检测:使用视觉系统检测元器件的粘贴质量,如果发现问题,及时进行修正。
最后,针对组件缺失的问题,主要原因可能是元器件的供应链问题,例如供应商发货错误或者内部库存管理不善。
针对这些问题,可以采取以下改善措施:1.加强供应商管理:与供应商建立良好的合作关系,加强供应链的沟通和管理,确保元器件的质量和数量。
2.设立内部库存管理系统:建立完善的库存管理系统,确保元器件的采购、入库、出库等流程的可控性和准确性。
3.进行组件跟踪和检测:使用条码或者RFID等技术,对每个组件进行跟踪和检测,确保组件的精确性和完整性。
smt不良改善报告
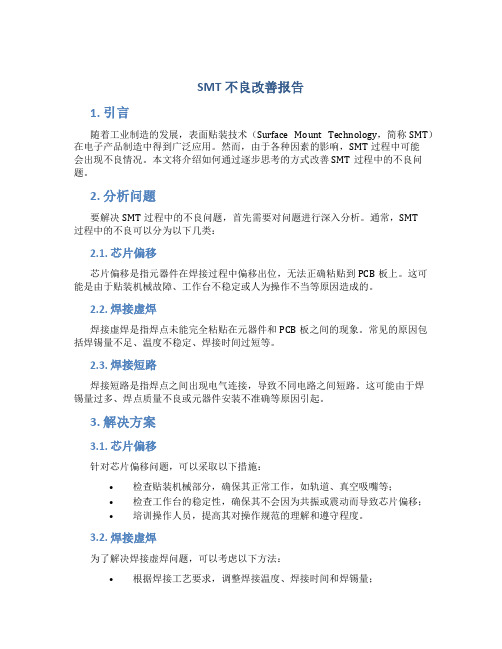
SMT不良改善报告1. 引言随着工业制造的发展,表面贴装技术(Surface Mount Technology,简称SMT)在电子产品制造中得到广泛应用。
然而,由于各种因素的影响,SMT过程中可能会出现不良情况。
本文将介绍如何通过逐步思考的方式改善SMT过程中的不良问题。
2. 分析问题要解决SMT过程中的不良问题,首先需要对问题进行深入分析。
通常,SMT过程中的不良可以分为以下几类:2.1. 芯片偏移芯片偏移是指元器件在焊接过程中偏移出位,无法正确粘贴到PCB板上。
这可能是由于贴装机械故障、工作台不稳定或人为操作不当等原因造成的。
2.2. 焊接虚焊焊接虚焊是指焊点未能完全粘贴在元器件和PCB板之间的现象。
常见的原因包括焊锡量不足、温度不稳定、焊接时间过短等。
2.3. 焊接短路焊接短路是指焊点之间出现电气连接,导致不同电路之间短路。
这可能由于焊锡量过多、焊点质量不良或元器件安装不准确等原因引起。
3. 解决方案3.1. 芯片偏移针对芯片偏移问题,可以采取以下措施:•检查贴装机械部分,确保其正常工作,如轨道、真空吸嘴等;•检查工作台的稳定性,确保其不会因为共振或震动而导致芯片偏移;•培训操作人员,提高其对操作规范的理解和遵守程度。
3.2. 焊接虚焊为了解决焊接虚焊问题,可以考虑以下方法:•根据焊接工艺要求,调整焊接温度、焊接时间和焊锡量;•定期检查焊接设备,确保其温度控制和焊锡供应正常;•对操作人员进行培训,提高其焊接技能和操作规范的遵守程度。
3.3. 焊接短路解决焊接短路问题的方法如下:•通过控制焊锡量和焊接温度,减少焊锡流动过多的可能性;•检查焊点质量,确保焊盘和元器件之间的连接质量良好;•定期检查焊接设备,确保其工作正常,如焊锡供应均匀等。
4. 结论通过逐步思考的方式,我们可以有效改善SMT过程中的不良问题。
针对芯片偏移、焊接虚焊和焊接短路等问题,分析原因并采取相应的解决方案,可以提高SMT过程的品质和效率。
SMT异常分析和改善报告
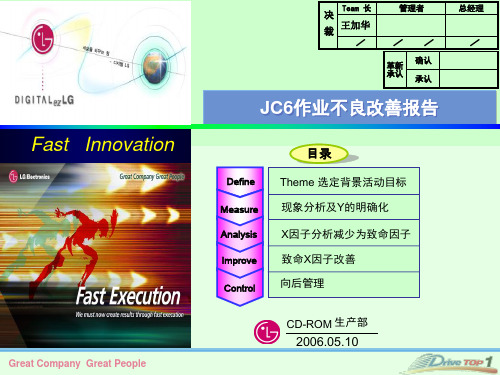
2006.05.10
Great Company Great People
Background Output
D
M
A
I
C
通过4月份工程不良数据分析发现作业不良占比率高,特选定作业不良为活动主题.
4月不良细部分析( PPM )
作业不良改善
TDR改善中
生产规模的迅速扩大,品质控制的
力度相对不足.
1236
修定 叠板 未检SET堆机现象严重
采用JIG放板
未检SET固定车放置 邀请生技,PM进行维修
PCB作业 不良
元件脱落
过桥掉机
修理叠板现象严重
修理不良追加JIG放置 作业者教育数量减少
投入位叠板
线路断
切板JIG不良 作业者修坏
设备重新更换改善 作业者教育数量减少
XS7 XS8
Two-proportions P-Value = 0.038 <0.05
改善前
1,236 1,246 1,123
改善后
作业不良率 改善目标
1,400 1,200 1,000 800 600 400 200 0
1,146
1,023
986 798
1,240
320
4月实绩 5月1日 5月2日 5月3日 5月4日 5月5日 5月6日 5月7日 5月8日
246
5月9日
235
155
13270 1930 2271 4月实际 部品
2435
1498
作业不良给品质,市场不良埋下了
很大的隐患.急需改善.
作业
MD
拆装
其他
不良细部分析( PPM )
Pareto Chart of 作业不良 _1
SMT设备故障处理报告

Create by: Ji yingyue
2
Copyright Diehl Controls(Nanjing) Co.,Ltd
目录
2.2 D4 2.2.1 Gantry异响 2.2.2 segment松动 2.2.3 取料马达无法初始化 2.2.4 贴装马达无法初始化 2.2.5 segment松动 2.2.6 吸嘴高度测试报错 2.2.7 S-axis counting error 2.2.8 Bottom Z light barrier did not respond at pick-up 2.2.9 Station computer自动重启 2.2.10 Gantry3 生产过程中发现异响 2.2.11 Gantry1 segment1撞断 2.2.12 按Start键时报错:Main contactor can not be pickup
目录
3. Rehm 3.1 主机自动重启 3.2 风扇不转动及加热区无法工作 3.3 Peak bottom无法加热 3.4 传输轨无法转动 3.5 传输轨无法转动 3.6 主机电脑自动关闭 3.7 按加热键炉子无法升温 3.8 所有温区加热风扇不转,变频器报0C1 3.9 传输轨2轨定轨链条无法传动 4.0 链条驱动约3秒后停止,报警:Drive fault
Create by: Ji yingyue
1
Copyright Diehl Controls(Nanjing) Co.,Ltd
目录
2.1.22 Gantry distance insufficient , Protective circuit reacted。 2.1.23 RV/D :Counting error 1,5,7,9,10,12 并报错RV/D does not reach required position seg12。 2.1.24 芯片贴装偏移 2.1.25 传板时报“The stopper in processing area 2 not reacting”, “Error on conveyor control”。 2.1.26 Time out during head Z axis function。 2.1.27 Difference between open and closed vacuum values too low。 2.1.28 S axis: jamming during reference run。 2.1.29 Star can’t reach the position 和Star jamming。 2.1.30 No Dain flag before new command。
SMT常见不良现象原因分析报告

缺锡 摇动 手印锡膏
零件沾锡性差
库存条件不佳
使用 过久
含助 量焊
过 大
粒 子
周 期
过 使
剂 径用
膏
黏 性亲 度 低金 高属
通风设备不好
心情不佳 手拨零件
力度 不饱 不够 满
零件掉落地上
零件尺寸不符 无尘布起毛
手印台钢板偏移
锡膏搅拌 不均
炉温曲线的测量 钢板开口方式
手印台不洁
停电
其他
PCB 上有 染物
轨道残留锡膏 机器置件不稳
机器
Nozzle Size Error
part data
置件速 度过快
真空 不畅
置件偏移
吃锡
不良
環境
人
材料
溼度影響錫膏特性
拿零件未戴手套 未做好來料檢驗
工作態度 錫 膏被抹掉
熟練程度
工作壓力
鋼板
零 件 拆 真 空 包 裝 后氧 化
手放散 料
鋼 板 未抆 拭 干 淨
錫 膏 添 加 不及 時
錫尖
無塵布使用 次數過多
人為點 錫/點漆 零件 管制
軌道 內有 異物
參數 設定 不當
水平
排風 不通
角度
鋼板 張力
鋼板 材質
開口 規格
鋼板 厚度
鋼板
錫膏 選
回焊爐
擇不 當
錫膏的管制
機 器的保養 未依 SOP
溫度 設定 預熱
抽
鋼 板底 貼 紙多
開口 不良
表面 粗糙
鋼板不 平
損壞
不當
不足
風
置件
T able
两边 不一致
有小孔 表面 内距 不洁 损伤
SMT设备常见故障机器解决方法

2.2.2.4)反光板的影响,反光板只是对背光才起作用,当反光板上有灰尘时,反 射时摄像机的光源强度减小,灰度值也小,这样易出现识别不良,导致元件 损耗,反光板是需要定期擦试的部件。 2.2.2.5)镜头上异物的影响,在光圈上面有个玻璃镜片,其作用是防止灰尘进入 光圈内,影响光源强度,但如果在玻璃镜片上有灰尘、元件等异物,同样也 影响光源强度,光源强度低,灰度值低。这样也容易导致识别不良发生,贴 片机要注意镜头和各种镜片的清洁。 2.3 飞件 飞件指元件在贴片位置丢失,其产生的主要原因有以下几方面: (2.3.1)元件厚度设置错误,若元件厚度较薄,但数据库中设置较厚,那么吸 嘴在贴片时就会在元件还没达到焊盘位置时就将其放下,而固定PCB的x-y工 作台又在高速运动,从而由于惯性作用导致飞件。所以要正确设置元件厚度 。
SMT设备常见机器故障解决方法
——技术员培训教材
1.引言:
随着SMT(表面贴装技术)在电子产品中的广泛应用, SMT生产中的关键设备-贴片机也得到了相应的发展,但在 贴片机的使用过程中,会不可避免地发生一些故障。如何 排除这些故障,确保机器处于最佳运行状态,是贴片机日 常使用管理过程中的一个主要任务,本文将以SMT设备为 例,介绍贴片机日常使用过程中的一些常见故障与排除方 法。
(2.2.2)元件视觉检测错误,光学识别系统是固定安装在一个仰视CCD摄像系 统,它是在贴装头的旋转过程中经摄像头识别元件外形轮廓而光学成像,同 时把相对于摄像机的器件中心位置和旋转角度测量并记录下来,传递给传动 控制系统,从而进行x、y坐标位置偏差与θ角度偏差的补偿,其优点在于精确 性与可适用于各种规格形状器件的灵活性。它有背光识别方式和前光识别方 式两种,前光识别以元件引线为识别依据,识别精度不受吸嘴大小的影响, 可清晰地检测出器件的电极位置,即使引脚隐藏于元件外形内的器件PLCC、 SOJ等也可准确贴装,而背光识别是以元件外形为识别依据,主要用来识别 片式阻容元件和三极管等,识别精度会受吸嘴尺寸的影响。
SMT设备故障处理报告_Date_Version

整 理 人 :纪应跃yingyue
Copyright Diehl Controls(Nanjing) Co.,Ltd
目录
1.DEK
1.1 Y轴印刷偏移 1.2 System power down 1.3 生产时报No paper 1.4 生产时跳电 1.5 Rail lifted error 1.6 System power down 1.7 Camera卡住 1.8 System power down 1.9 System power down,Rising table position error 2.0 生产时机器报:Lifting table position error,关机重启后相机闪烁,无法 初始化 2.1 擦拭丝网时,机器掉电 2.2 生产时PCB卡板
2.4 F4 2.4.1 X does not reach the position 2.4.2 Start键无作用 2.4.3 轨道不进板 2.4.4 料带切不断 2.4.5 料带不切料带
Create by: Ji yingyue
4
Copyright Diehl Controls(Nanjing) Co.,Ltd
4. ASYS 4.1 Monitor 无画面 4.2 无法传板 4.3 Drive fault
Create by: Ji yingyue
5
Copyright Diehl Controls(Nanjing) Co.,Ltd
目录
5. VCD 5.1 6241D 5.1.1 Waiting left anvil down 5.1.2 Table 一直连转 5.1.3 转台连转 5.1.4 无元件插入时不报错 5.1.5 上刀头卡死 5.2 6241F 5.2.1 刀头卡住 5.2.2 刀头卡住 5.2.3 head chain错位 5.2.4 X-axis坐标漂移 5.2.5 料站无法下料 5.2.6 玻璃二极管不居中 5.2.7 转台不转
SMT不良分析报告

空焊现象的产生可能是由于焊盘与焊料之间的润湿性差、焊点尺寸过小、焊接 温度过低等原因所致。空焊可能导致电气连接不良、机械连接不稳定等问题, 影响电子产品的性能和可靠性。
短路现象
总结词
短路是指SMT加工过程中,两个原本 不应该连接的焊点意外地形成了连接 的现象。
详细描述
短路现象的产生可能是由于焊料飞溅 、元器件贴装位置偏差、焊盘重叠等 原因所致。短路可能导致电路功能异 常、安全风险等问题,影响电子产品 的性能和可靠性。
提高焊接温度和时间
适当提高焊接温度和时间,确 保焊点充分熔融、浸润,减少 空焊现象的产生。
控制焊膏量
根据焊接需求,合理调整焊膏 量,确保焊点表面光滑、饱满 。
加强工艺控制
定期对设备和工艺进行检查和 校准,确保工艺稳定、可靠。
短路现象的预防措施
短路现象
在SMT工艺中,由于焊点之间存在杂质 或气泡等原因,可能导致焊接后出现短
锡珠
在焊接过程中,锡 膏熔化后形成的小 珠状突起。
冷焊
焊接点表面不光滑 ,呈现凹凸不平的 状态。
元件移位
元件在焊接过程中 位置发生偏移。
CHAPTER 02
SMT不良现象分析
锡珠现象
总结词
锡珠是指在SMT加工过程中,焊料在经过回流焊后形成的球状物,通常出现在焊 点周围。
详细描述
锡珠现象的产生通常是由于焊料在熔融状态下受到重力、表面张力以及温度梯度 的影响,导致焊料在冷却过程中无法完全回流,从而形成球状物。锡珠可能导致 电气连接不良、机械卡滞等问题,影响电子产品的性能和可靠性。
选用低残留焊膏
选择低残留、低松香含量的焊 膏,减少锡珠形成。
锡珠现象
在SMT工艺中,由于焊膏过多 或温度过高,导致焊膏在回流 过程中形成锡珠状残留物。
SMT不良分析及改善措施

板 模 2、开口不当
3、开口偏移
重新制作模板
4、模板太厚
5、
.
7
锡珠的产生原因与解决办法(二)
接焊
产生原因 1、预热区升温太急 2、保温区时间太短
3、焊接区温度太高
装 贴 1、贴片压力太大
2、 1、压力太小,使锡膏偏厚
刷 印 2、未对好位就开始印刷
3、未及时清洁模板
产生原因 1、板面氧化 2、有水份或污物
3、 1、焊端氧化 2、焊端有水份或污物 1、开口偏小
解决办法 PCB来料控制 清除PCB上的水份或污物
元件来料控制
板 模 2、毛刺过多
3、厚度太薄
重新制作模板 使用电抛光工艺
4、未及时清洗
及时清洗模板
5、
.
10
空焊的产生原因与解决办法(二)
刷印
产生原因 1、印刷压力太大 2、印刷速度太快
2、焊端有水份
3、焊端有污物
膏 锡 1、品质不好或变质
2、粘度太高 1、焊盘氧化
板 基 2、焊盘有水份或污物
3、焊盘上有过孔
4、焊盘大小不一
解决办法 元件来料控制 更换锡膏
清除PCB上的水份或污物 修改PCB Layout
5、小元件设计太靠近大颗黑色元件
.
12
墓碑的产生原因与解决办法(二)
产生原因 1、开口过大
焊
接 装贴
产生原因 1、焊接区升温太剧烈 2、回流炉内温度不均
3、履带运行时振动 1、贴件偏位
2、 1、印刷偏移
刷 印 2、印刷压力偏小
3、刮刀有磨损(缺口)
4、印刷机工作台不水平
解决办法 调整Reflow炉温 降低Reflow履带速度 检修Reflow
SMT不良维修日报表模板及综合分类分析
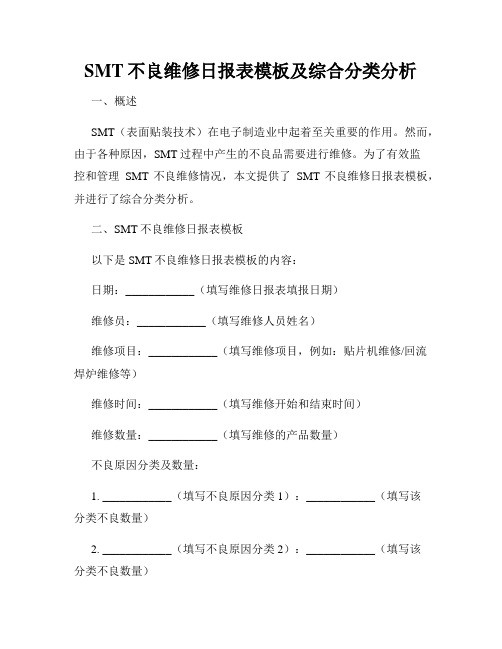
SMT不良维修日报表模板及综合分类分析一、概述SMT(表面贴装技术)在电子制造业中起着至关重要的作用。
然而,由于各种原因,SMT过程中产生的不良品需要进行维修。
为了有效监控和管理SMT不良维修情况,本文提供了SMT不良维修日报表模板,并进行了综合分类分析。
二、SMT不良维修日报表模板以下是SMT不良维修日报表模板的内容:日期:____________(填写维修日报表填报日期)维修员:____________(填写维修人员姓名)维修项目:____________(填写维修项目,例如:贴片机维修/回流焊炉维修等)维修时间:____________(填写维修开始和结束时间)维修数量:____________(填写维修的产品数量)不良原因分类及数量:1. ____________(填写不良原因分类1):____________(填写该分类不良数量)2. ____________(填写不良原因分类2):____________(填写该分类不良数量)3. ____________(填写不良原因分类3):____________(填写该分类不良数量)……三、综合分类分析根据日报表收集的数据,进行综合分类分析可以帮助我们更好地了解SMT不良维修情况,并采取相应的改进措施。
1. 不良原因分类通过对不良原因的分类,我们可以清晰地了解哪些方面的问题导致了不良品的产生。
一般而言,SMT不良原因可以分为以下几类:- 设备故障:包括贴片机故障、回流焊炉故障等设备问题导致的不良品产生。
- 操作失误:包括操作人员疏忽、不熟悉操作要求等因素导致的不良品产生。
- 材料问题:包括贴片元件质量不良、焊接材料质量不良等原因导致的不良品产生。
- 工艺参数:包括焊接温度、焊接时间等工艺参数设置不当导致的不良品产生。
2. 不良数量统计通过统计每个不良原因分类的数量,我们可以发现不同类别的不良品产生情况。
这可以帮助我们确定哪些不良原因更为突出,需要重点解决。
SMT不良分析报告

SMT不良分析报告一、概述本报告旨在分析SMT(Surface Mount Technology,表面贴装技术)生产过程中的不良现象,并提供相应的解决方案。
SMT是一种将电子元件贴装到PCB板表面的技术,具有高效、高精度、高可靠性等优点。
然而,在实际生产过程中,由于各种原因会导致SMT不良现象的发生。
二、SMT不良现象分类1、元件贴装不良:元件贴装位置偏离、倾斜、立碑等现象。
2、焊接不良:焊接点缺陷、虚焊、冷焊等现象。
3、元件质量问题:元件本身存在缺陷,如破损、功能不良等。
4、PCB板质量问题:PCB板存在缺陷,如划伤、变形、污染等。
5、操作不当:操作人员技能不足、操作不规范等导致的不良。
三、SMT不良原因分析1、元件贴装不良原因:a)贴装设备精度不高;b)操作人员技能不足;c)定位基准不准确;d)元件本身质量问题。
2、焊接不良原因:a)温度和时间控制不当;b)焊点表面污染;c)元件和PCB板质量问题;d)焊接设备故障或参数设置不当。
3、元件质量问题原因:a)供应商质量控制不严格;b)运输和存储过程中损坏;c)生产过程中质量控制不严格。
4、PCB板质量问题原因:a)供应商质量控制不严格;b) PCB板制作过程中出现缺陷;c) PCB板运输和存储过程中损坏。
5、操作不当原因:a)操作人员技能培训不足;b)操作流程不完善;c)质量控制意识不强。
四、SMT不良解决方案1、提高设备精度:对贴装设备和焊接设备进行定期维护和校准,确保设备精度在规定范围内。
2、加强操作人员技能培训:定期组织技能培训,提高操作人员的技能水平。
3、完善操作流程:制定严格的SMT操作流程,确保操作人员严格按照规定进行操作。
4、加强来料质量控制:对供应商进行严格筛选,并对来料进行严格的质量控制。
同时,加强存储和运输过程中的保护措施,防止元件和PCB板损坏。
5、加强生产过程中的质量控制:建立完善的质量控制体系,对每个生产环节进行严格的质量监控。
smt不良分析及改善措施
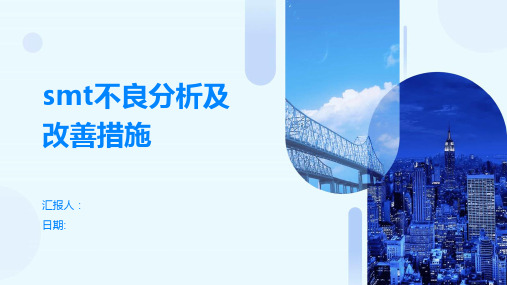
清洁保养
02
定期对设备表面进行清洁保养,保持设备整洁,防止灰尘、异
物等对设备造成损害。
润滑保养
03
按照设备制造商的推荐,定期对设备的运动部件进行润滑保养
,以减少磨损工艺文件,确保每个生产步骤都符合规范和标 准。
人员培训
对操作人员进行专业培训,确保他们熟悉设备的操作和维护,能 够及时发现并解决潜在问题。
总结词
PCB板的设计不合理可能会导致元件脱落、短路等问题。
详细描述
如果PCB板的线路设计不合理,可能会导致元件无法准确吸附在指定位置;如果 PCB板的焊盘设计不合理,则可能会导致短路或虚焊。因此,需要对PCB板的设 计进行严格审核和测试。
案例四:温度和湿度控制不当
总结词
温度和湿度控制不当可能会导致元件引脚氧化、焊接不良等问题。
工艺不良
温度异常
SMT生产线温度异常波动 ,导致零件贴装偏差、焊 接不良等
湿度异常
SMT生产线湿度异常波动 ,导致零件受潮、焊接不 良等
大气污染
SMT生产线大气污染严重 ,导致零件表面污染、焊 接不良等
管理不良
计划管理不良
生产计划不合理、生产安排不科 学等导致生产效率低下、产品质
量不稳定等不良现象
零件材质不良
零件材质不达标,如PCB 板材质不均、零件镀层不 均匀等
零件质量不良
零件本身存在质量问题, 如气泡、划痕等
设备不良
贴片机不良
贴片机精度下降、机械故障等导 致贴装位置偏差、零件损坏等不
良现象
印刷机不良
印刷机精度下降、机械故障等导致 印刷不均匀、印刷错误等不良现象
检测设备不良
检测设备精度下降、机械故障等导 致检测不准确、误判等不良现象
smt不良分析及改善措施

如零件本身的质量问 题或由于放置不当造 成的损坏。
04
焊接不良
如焊接点不足、过多 或虚焊等。
不良品产生原因
如部件质量问题、焊料质量问题 等。
如车间温度、湿度、清洁度等环 境条件不良。
设备故障 材料问题 操作失误 环境因素
如贴片机、印刷机等设备故障或 参数设置不正确。
如操作人员技能不足、工作疏忽 等。
原因和分布情况。
效果评估方法
过程能力指数评估
利用过程能力指数评估生产过程的稳定性、 一致性和可预测性。
不良率统计
统计不良品的数量与总生产量的比例,计算 出不良率。
质量成本评估
评估因质量问题导致的损失,包括返工、报 废、保修等成本。
持续改进计划
01
针对主要不良原因 进行改善
针对主要的不良原因,制定相应 的改善措施,如优化工艺流程、 更换原材料供应商等。
smt不良分析及改善措施
汇报人: 日期:
目录
• SMT不良分析 • SMT不良改善措施 • SMT不良品追踪及效果评估 • SMT不良预防措施
01
SMT不良分析
Chapter
常见不良现象
01
部件丢失
如电阻、电容等部件 在组装过程中丢失或 未正确放置。
02
部件错位
如IC芯片位置偏离或 翻转。
03
注意事项
培训应结合实际生产情况,注重理论和实践的结 合,同时要定期评估培训效果。
实施质量管理体系,加强质量控制
总ቤተ መጻሕፍቲ ባይዱ词
实施质量管理体系,加强质量控制是减少SMT不良的有效方法 。
详细描述
建立完善的质量管理体系,包括来料检验、过程控制、成品检验 等环节,确保产品质量符合预期要求。
SMT机器故障原因及对策
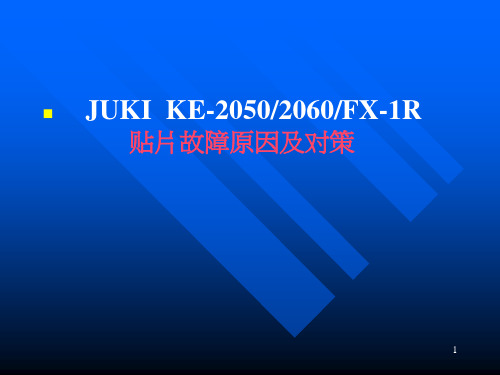
② 使用CAD 数据时,CAD 的贴片坐标或BOC 标记的
一部分出现错误。若某一处的BOC 标记的坐标移动, 其周边的贴片偏移便会增大。
③ BOC 标记脏污。
④ “基板数据”的“基板厚度”输入错误。在这种情 况下,由于基板的上下方向上出现松动,有时会在某个 区域发生贴片偏移。贴片偏移量通常参差不一。 ⑤ 支撑销设置不良。在薄基板或大型基板时易发 生贴片偏移。 ⑥ 由于支撑台下降速度快,基板夹紧解除时已完 成贴片的元件的一部分产生移动。
② 清洁BOC 标记。 另外,采取适当措施以免弄脏BOC 标记
③ 确认并修正“基板数据”的“基板高度”与“基 板厚度”。 ④ 重新设置支撑销。尤其要着重设置贴片精度要 求高的元件的支撑销。
④ 支撑销设置不良。在薄基板或大型基板时易 发生贴片偏移。 ⑤ 基准销与基板定位孔之间的间隙大,基板因 生产过程中的振动而产生移动。 ⑥ 由于支撑台下降速度快,基板夹紧解除时已 完成贴片的元件产生移动。 ⑦ 基板表面平度差。
④重新设定IC 标记坐标(在已示教的情况下须确
认坐标)。 另外,采取适当措施以免弄脏IC 标记。 ⑤ 重新设置支撑销。尤其是发生贴片偏移的元件 之下要重点设置。 ⑥ 在“机器设置”的“设定组”/“基板传送”
完成贴片的元件的一部分产生移动。 尤其是焊膏的黏着力较低时,与电解电容等 元件重量相比,接地面积小的元件容易发 生。
⑦ “元件数据”的“传送间距”设定错误。
六.元件吸取错误 8)
不能吸取MTC/MTS 供给的元件。
① “元件数据”的“元件高 度”设定错误。
① 在元件高度中输入从吸嘴下底 面到元件下底面(含引脚)的尺 寸。 ② 重新设定“机器设置”的“设 定组”/“MTC 梭子吸取位置”
smt不良分析及改善措施

材料问题
原材料缺陷:如PCB板、电子元器件等原材料存 在缺陷,将直接影响SMT产品的品质。
使用过期材料:使用过期的原材料进行生产,可 能导致产品性能不稳定,产生不良品。
储存不当:原材料在储存过程中未按照要求进行 保管,可能导致性能受损,进而影响SMT产品质 量。
针对以上原因,可以采取相应的改善措施,如加 强员工培训、规范操作流程、定期维护设备、严 格把控原材料质量等,以降低SMT不良品率,提 高产品质量和生产效率。
03
SMT不良改善措施
人员培训和管理
提高技能水平
定期举办技术培训课程,提升员工在SMT操作、维护、质检等方面 的技能水平,确保员工熟悉并掌握设备操作规程和质量标准。
严格考核与奖惩制度
建立员工绩效考核体系,对操作规范、良品率等方面进行考核,奖 励优秀员工,对操作不规范、产品质量差的员工进行惩罚和再培训 。
强化质量意识
通过定期的质量教育活动,增强员工的质量意识,使其充分认识到产 品质量对企业和个人的重要性。
设备维护和管理
制定维护计划
根据设备使用情况和维护要求,制定合理的设备维护计划,确保 设备按时进行保养、检修,减少设备故障。
监控设备运行状况
通过设备自带的监测系统或额外安装传感器等方式,实时监测设备 运行状况,及时发现异常,避免故障扩大。
• 焊接不良:包括冷焊、虚焊、 焊盘脱落等问题,主要由于焊 接温度、时间等参数设置不当 或焊接材料质量差引起。
• 基板不良:包括基板变形、裂 纹、污染等,可能由基板材料 、设计或生产工艺导致。
SMT不良现象对生产的影响
01
02
03
生产效率下降
SMT不良现象会增加检修 、返工等工作量,降低生 产效率。
SMT机器常见故障分析

机台常见故障分析故障原因分析原因漏打及打飞 NOZZLE堵塞 NOZZLE没完全堵塞,但真空会变小,如果此零件从吸取到过了照相仍没有经过转动,当到了最终旋转时将零件转掉,置件时此位即漏打零件吸偏吸偏有X方向及Y方向,当X方向吸偏时D轴会自动给下颗零件offset,但当此颗零件吸偏时可能会随着重心的不同在旋转时将零件转掉.Y方向结构是固定的无法自动校正,如果料枪Y方向偏或错格式,吸取后的料Y方向偏差一方面会由于真空变小产生与上述一样的现象,另一方面会在置件时形成不是压的动作,而是搓的动作,导致将零件搓飞.Z轴深度高/低(即可为顶针顶板的高度) 桌面的水平是一致的,在标准的ZO基础上NOZZLE下压到板面30条.此目的是为了生产点胶板时零件不会浮高,生产锡膏板时不会造成不吃锡.如果板顶的太上置件形成搓的动作,太低形成扔的动作.板太大顶顶针时易造成错误的判断认为顶针顶到板就可以.实际板中间的部位由于下陷距板边的高度相差很多.这时就必须利用从侧面广告牌Y方向是否平行.技朮人员可利用ZO的深度来判断板的水平.置件时的真空破坏机器在置件时有一个真空破坏的动作(吹气)如果气太小零件易带走无法置件,气太大易将置件旁边的零件吹走.最好的方法是将气调节阀调到底反转三圈.另一种原因为SPOOL没完全破坏将零件带走.点胶机种胶小或胶距太宽电容的面实际不是一个很的面,当电容置放在较小的胶点上时,随着桌面的移动,电容从胶点中脱离.若点胶头的胶距太宽,零件置放后所接触到的胶点很少随着桌面的移动,零件从胶点中脱离.胶小或胶距宽还会造成零件倾斜.印锡膏机种锡膏太干或铜箔间隙太大锡膏印刷后在标准的室温下最好不要放超过4个小时,放的时间太长易干,零件置放后粘不住,只是浮在锡膏的表面.零件置放在间隙太宽的铜箔上,零件所粘住的面积很少.以上二种现象都会打飞.PCB间题: 喷锡板,纸板, 喷锡板的铜箔表面有些会不平.生产点胶板时,随着铜箔面的增高点胶头与stopper的落差所点出的胶点会很小,贴片时零件浮在铜箔的表面并没有接触到胶点,造成零件打飞.纸板的边或切割线中会有板屑,在点胶时板屑从板中弹出来粘到胶点上,贴片时零件打在板屑上打飞.旋转时下压太深零件吸取照相后进行最终角度旋转,如果机械结构下压的太深,在旋转前首先形成了一个敲的动作,这颗零件就会被敲掉.(CP4系列机型)第七站机械动作太慢机器在正常置件时SOL常开,当有一颗零件判断要吐料时,SOL要立即关闭,下一颗要立即打开,这样的动作是要在非常短的时间内完成.若打开的动作太慢这颗零件将无法置件.(CP4系列机型)东莞凯巨机电有限公司。
smt不良分析报告
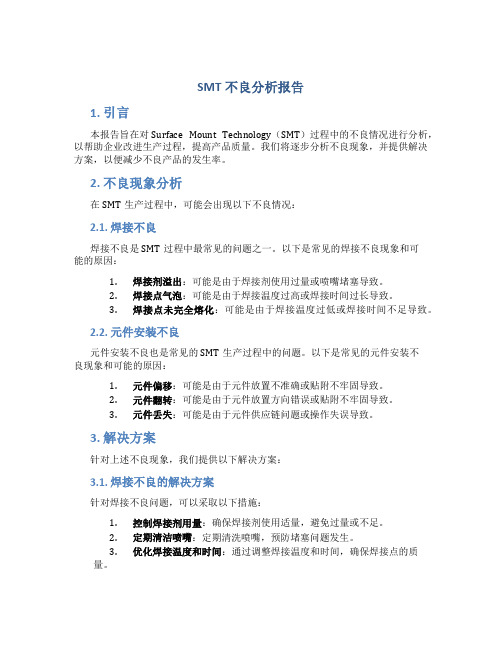
SMT不良分析报告1. 引言本报告旨在对Surface Mount Technology(SMT)过程中的不良情况进行分析,以帮助企业改进生产过程,提高产品质量。
我们将逐步分析不良现象,并提供解决方案,以便减少不良产品的发生率。
2. 不良现象分析在SMT生产过程中,可能会出现以下不良情况:2.1. 焊接不良焊接不良是SMT过程中最常见的问题之一。
以下是常见的焊接不良现象和可能的原因:1.焊接剂溢出:可能是由于焊接剂使用过量或喷嘴堵塞导致。
2.焊接点气泡:可能是由于焊接温度过高或焊接时间过长导致。
3.焊接点未完全熔化:可能是由于焊接温度过低或焊接时间不足导致。
2.2. 元件安装不良元件安装不良也是常见的SMT生产过程中的问题。
以下是常见的元件安装不良现象和可能的原因:1.元件偏移:可能是由于元件放置不准确或贴附不牢固导致。
2.元件翻转:可能是由于元件放置方向错误或贴附不牢固导致。
3.元件丢失:可能是由于元件供应链问题或操作失误导致。
3. 解决方案针对上述不良现象,我们提供以下解决方案:3.1. 焊接不良的解决方案针对焊接不良问题,可以采取以下措施:1.控制焊接剂用量:确保焊接剂使用适量,避免过量或不足。
2.定期清洁喷嘴:定期清洗喷嘴,预防堵塞问题发生。
3.优化焊接温度和时间:通过调整焊接温度和时间,确保焊接点的质量。
3.2. 元件安装不良的解决方案针对元件安装不良问题,可以采取以下措施:1.加强人员培训:对操作人员进行培训,提高其技术水平和操作准确性。
2.优化元件放置设备:确保元件放置设备准确可靠,减少元件偏移和翻转问题。
3.改进供应链管理:与元件供应商合作,确保元件质量和供应链稳定性。
4. 结论通过对SMT不良现象的分析和解决方案的提供,我们可以帮助企业改进生产过程,提高产品质量。
在实施解决方案时,建议企业根据自身情况进行调整和优化,以取得更好的效果。
最终,减少不良产品的发生率将有助于提升企业竞争力和顾客满意度。
- 1、下载文档前请自行甄别文档内容的完整性,平台不提供额外的编辑、内容补充、找答案等附加服务。
- 2、"仅部分预览"的文档,不可在线预览部分如存在完整性等问题,可反馈申请退款(可完整预览的文档不适用该条件!)。
- 3、如文档侵犯您的权益,请联系客服反馈,我们会尽快为您处理(人工客服工作时间:9:00-18:30)。
维修结果:待观察
小 结:此问题跟M24 已转移到03线。
设备故障处理报告
1.3 生产时报 设备号:01 故障现象:正常生产,在清洁丝网时报没有擦拭纸 发生时间:2011.03.31 00:00 结束时间:2011.03.31 00:45
计划措施: 1.检查清洁纸,安装正确 2.进诊断,测试卷纸马达,工作正常 3.清洁卷纸时,发现线头脱焊 4.重新焊接好线头
设备故障处理报告
1.6 设备号:03 故障现象:生产过程中掉电,报 发生时间:2011.08.30 15:30 结束时间:2011.08.30 16:00
计划措施: 1.测量24V,12V,5 2.发现5V只有4.9V,偏低。调整到5.2V
维修结果:待观察
小 结:此问题跟M24 从01线转移过来。
维修结果:
小 ቤተ መጻሕፍቲ ባይዱ:在八周维护时添加检查此项,发现异常时更换。
设备故障处理报告
1.2 设备号:01 故障现象:生产时经常掉电,报错信息有:1 ,2 发生时间:2011.03.11 10:00 结束时间:2011.03.11 14:30
,3 ,4
计划措施: 1.与03对调M24 后问题转移到三线 2.测量5V电压,发现电压4.8~4.9之间波动,电压偏低 3.按工程师吴春福建议,将电压调整到5.14V 4.观察两小时,无掉电现象
目录
2.3 S20 2.3.1 反向运行 2.3.2 飞料 2.3.3 2.3.4 无作用 2.3.5 系统无法启动 2.3.6 撞极限 2.3.7 ’t 2.3.8 启动后一直处于 状态 2.3.9 2.3.10 归零时异常 2.3.11 2.3.12 X 2.3.13 多个报 2.3.14 切刀不切料带 2.3.15 切刀不切料带
设备故障处理报告
整 理 人 :纪应跃 整理时间:2011.10月
目录
1 1.1 Y轴印刷偏移 1.2 1.3 生产时报 1.4 生产时跳电 1.5 1.6 1.7 卡住 1.8 1.9 , 2.0 生产时机器报 ,关机重启后相机闪烁,无法初始化 2.1 擦拭丝网时,机器掉电 2.2 生产时卡板
2 2.150 2.1.1 无影像 2.1.2 异响 2.1.3 ’t 2.1.4 无电源 2.1.5 ’t 2.1.6 无法识别 2.1.7 无法识别元件中心 2.1.8 无法识别元件中心 2.1.9 : 2.1.10 元件无影像 2.1.11 无法识别 2.1.12 贴装马达无法初始化 2.1.13 抛料马达无法初始化 2.1.14 料带不切断 2.1.15 无法初始化 2.1.16 : 2.1.17 无法初始化 2.1.18 脱落 2.1.19 1
目录
2.1.22 , 。 2.1.23 1,5,7,9,10,12 并报错 12。 2.1.24 芯片贴装偏移 2.1.25 传板时报“ 2 ”,“ ”。 2.1.26 Z 。 2.1.27 。 2.1.28 S : 。 2.1.29 ’t 和 。 2.1.30 。
目录
2.2 D4 2.2.1 异响 2.2.2 松动 2.2.3 取料马达无法初始化 2.2.4 贴装马达无法初始化 2.2.5 松动 2.2.6 吸嘴高度测试报错 2.2.7 2.2.8 Z 2.2.9 自动重启 2.2.10 3 生产过程中发现异响 2.2.11 1 1撞断 2.2.12 按键时报错:
4. 4.1 无画面 4.2 无法传板 4.3
目录
5. 5.1 6241D 5.1.1 5.1.2 一直连转 5.1.3 转台连转 5.1.4 无元件插入时不报错 5.1.5 上刀头卡死 5.2 6241F 5.2.1 刀头卡住 5.2.2 刀头卡住 5.2.3 错位 5.2.4 坐标漂移 5.2.5 料站无法下料 5.2.6 玻璃二极管不居中 5.2.7 转台不转
2.4 F4 2.4.1 X 2.4.2 键无作用 2.4.3 轨道不进板 2.4.4 料带切不断 2.4.5 料带不切料带
目录
3. 3.1 主机自动重启 3.2 风扇不转动及加热区无法工作 3.3 无法加热 3.4 传输轨无法转动 3.5 传输轨无法转动 3.6 主机电脑自动关闭 3.7 按加热键炉子无法升温 3.8 所有温区加热风扇不转,变频器报0C1 3.9 传输轨2轨定轨链条无法传动 4.0 链条驱动约3秒后停止,报警:
维修结果:
小 结:
设备故障处理报告
1.5 设备号:03 故障现象:生产过程中报错: 发生时间:2011.07.12 00:30 结束时间:2011.07.12 04:30
计划措施: 1.检查并清洁 感应器 2.与另台对调感应器,问题依旧 3.检查线路,发现有短路现象 4.重新焊接好线路
维修结果:
小 结:此问题属于运动部位线路磨损导致内部短路
设备故障处理报告
1 1.1 Y轴印刷偏移 设备号:04 故障现象:生产时发现Y轴印刷偏移 发生时间:2011.01.29 20:30 结束时间:2011.01.29 22:00
计划措施: 1.打开机盖,检查丝网,发现丝网在Y轴方向晃动 2.检查丝网夹紧器,发现右边已失效 3.拆下丝右边网夹紧器,发现夹紧线断 4.更换丝网夹紧线
维修结果:
小 结:此接头很脆弱,在维护清洁时都需注意。
设备故障处理报告
1.4 生产时跳电 设备号:01 故障现象:正常生产时突然掉电 发生时间:2011.05.25 09:50 结束时间:2011.05.25 13:00
计划措施: 1.重新启动机器,进诊断模式,机器正常归零 2.进入生产模式,印刷第一片,故障依旧 3.关机,打开机盖,检查发现 Y 皮带断裂 4.更换 Y 皮带,并校准原点位置 5.开机生产
设备故障处理报告
1.7 卡住 设备号:04 故障现象:生产时突然发出响声,卡死 发生时间:2011.09.09 14:30 结束时间:2011.09.09 16:30
计划措施: 1.关闭电源,打开机盖,发现有损坏 2.清理被撞坏的,用手拉动,发现卡死 3.检查皮带,皮带轮均无异物 4.松开皮带,仍拉不动 5.仔细检查发现支架变形 6.将支架整形后,开机生产正常