热喷涂中电弧喷涂铝涂层性能指标
电弧喷涂涂层性能检测方法

电弧喷涂涂层性能检测方法胡为峰 葛 爽(北京赛亿表面工程技术有限公司100083)①摘要:锅炉喷涂涂层在锅炉运营中对管壁的性能起到重要的作用,为确定涂层所得喷涂性能和喷涂效果,本文主要介绍了几种在测试涂层性能过程中比较常见的几种测试方法和测试步骤。
关键词:电弧喷涂 涂层性能 测试1、引言作为电厂锅炉防护热喷涂材料中的重要体系,热喷涂涂层的性能由于影响着所防护材料的使用性能而倍受关注。
电弧喷涂层的质量是通过涂层得性能来反映的,而涂层得性能又取决于喷涂设备、材料、工艺等多种因素。
涂层性能的检测时评估涉及很多检测方法,就一般的电弧喷涂层而言,涂层性能主要包括了涂层得物理性能(如外观、密度、厚度、金相等)、力学性能(如结合强度、耐磨性、残余应力等)和化学性能(如化学成分、耐蚀性、耐热性、电化学性等)。
当然,在实际工作中并不要求电弧喷涂层一定要测试上述所有性能,而是要根据不同的目的来选择不同的测试项目。
一般来说,电弧喷涂层性能试验与测试的目的主要有三个方面:z满足工艺上的要求;z满足技术的要求;z满足使用上的要求。
2、涂层性能测试标准和测试方法2.1 涂层性能测试所涉及的国家标准为了可靠地评价电弧喷涂涂层质量的优劣,准确测定涂层性能是否达到工艺、设计或者使用上的预期要求,就需要一套比较准确的涂层质量和性能检测的方法。
当然,最有效的地方就是采用现有的国家标准。
表2-1列出了现有的一些国家标准。
表2-1 热喷涂涂层性能试验方法与标准标准号标准名称备注GB/T 11374-1989 热喷涂涂层厚度的无损检测方法idt ISO 2064GB/T 4956-2003 磁性金属基体上非磁性覆盖层厚度测量磁性方法idt ISO 2178GB/T 6462-1986 金属和氧化物覆盖层横断面厚显微镜测量方法idt ISO 1463GB/T 11378-1989 金属覆盖层厚度轮廓尺寸测量方法idt ISO 4518GB/T 4955-1997 金属覆盖层覆盖层厚度测量阳极溶解库仑法idt ISO 2177① 本文通讯联系人:胡为峰(北京赛亿表面工程技术有限公司 100083)GB/T 16921-1997 金属覆盖层厚度测量X射线光谱方法eqv ISO 3497 GB/T 4957-2003 非磁性金属基体上非导电覆盖厚度测量涡流法idt ISO 2360 GB/T 17722-1999 金属覆盖层厚度的扫描电镜测量方法eqv ISO 9220ISO 3543 金属和非金属覆盖层-覆盖层厚度测量-β射线反向散射法ISO 10111 金属和其他无机覆盖层-单位面积质量的测量-重量法和化学分析法的评述JB/T 7509-1994 热喷涂涂层空隙率实验方法——铁试剂法GB/T 8640-1988 金属热喷涂涂层表面洛式硬度试验方法GB/T 9790-1988 金属覆盖层及其他有关覆盖层维式和努式显微硬度试验方法GB/T 8642-2002 热喷涂涂层抗拉强度的测定取代GB 8642-88GB/T 13222-1991 热喷涂涂层剪切强度的测定GB/T 5210-1985 涂层附着力的测定法拉开发eqv ISO 4624-1978GB/T 6458-1986 金属覆盖层中性盐雾试验(NSS试验)GB/T 9789-1988 金属和其他非有机覆盖层通常凝露条件下的二氧化硫腐蚀试验idt ISO 6988-1985GB/T 9793-1997 金属和非金属覆盖层热喷涂锌、铝及其合金取代GB9793~9796-882.2 热喷涂涂层的测试方法2.2.1 涂层显微金相组织显微金相观察是测试材料组织结构的重要方法之一,也是测量材料性能的最基本的测试方法,对于喷涂涂层同样重要。
大功率电弧锌铝伪合金喷涂技术及其应用
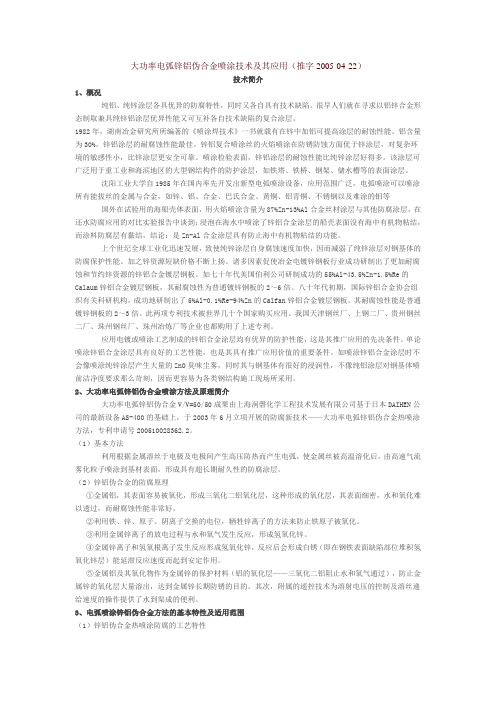
大功率电弧锌铝伪合金喷涂技术及其应用(推字2005-04-22)技术简介1、概况纯铝、纯锌涂层各具优异的防腐特性,同时又各自具有技术缺陷。
很早人们就在寻求以铝锌合金形态制取兼具纯锌铝涂层优异性能又可互补各自技术缺陷的复合涂层。
1982年,湖南冶金研究所所编著的《喷涂焊技术》一书就载有在锌中加铝可提高涂层的耐蚀性能。
铝含量为30%,锌铝涂层的耐腐蚀性能最佳。
锌铝复合喷涂丝的火焰喷涂在防锈防蚀方面优于锌涂层,对复杂环境的敏感性小,比锌涂层更安全可靠。
喷涂检验表面,锌铝涂层的耐蚀性能比纯锌涂层好得多。
该涂层可广泛用于重工业和海滨地区的大型钢结构件的防护涂层,如铁塔、铁桥、钢架、储水槽等的表面涂层。
沈阳工业大学自1985年在国内率先开发出新型电弧喷涂设备,应用范围广泛,电弧喷涂可以喷涂所有能拔丝的金属与合金,如锌、铝、合金、巴氏合金、黄铜、铝青铜、不锈钢以及难涂的钼等国外在试验用的海船壳体表面,用火焰喷涂含量为87%Zn-13%Al合金丝材涂层与其他防腐涂层,在还水防腐应用的对比实验报告中谈到;浸泡在海水中喷涂了锌铝合金涂层的船壳表面没有海中有机物粘结,而涂料防腐层有黏结,结论:是Zn-Al合金涂层具有防止海中有机物粘结的功能。
上个世纪全球工业化迅速发展,致使纯锌涂层自身腐蚀速度加快,因而减弱了纯锌涂层对钢基体的防腐保护性能。
加之锌资源短缺价格不断上扬。
诸多因素促使冶金电镀锌钢板行业成功研制出了更加耐腐蚀和节约锌资源的锌铝合金镀层钢板。
如七十年代美国伯利公司研制成功的55%Al-43.5%Zn-1.5%Re的Calaum 锌铝合金镀层钢板,其耐腐蚀性为普通镀锌钢板的2~6倍。
八十年代初期,国际锌铝合金协会组织有关科研机构,成功地研制出了5%Al-0.1%Re-94%Zn的Calfan锌铝合金镀层钢板。
其耐腐蚀性能是普通镀锌钢板的2~3倍。
此两项专利技术被世界几十个国家购买应用。
我国天津钢丝厂、上钢二厂、贵州钢丝二厂、珠州钢丝厂、珠州冶炼厂等企业也都购用了上述专利。
GB9793热喷涂锌铝涂层word精品文档7页
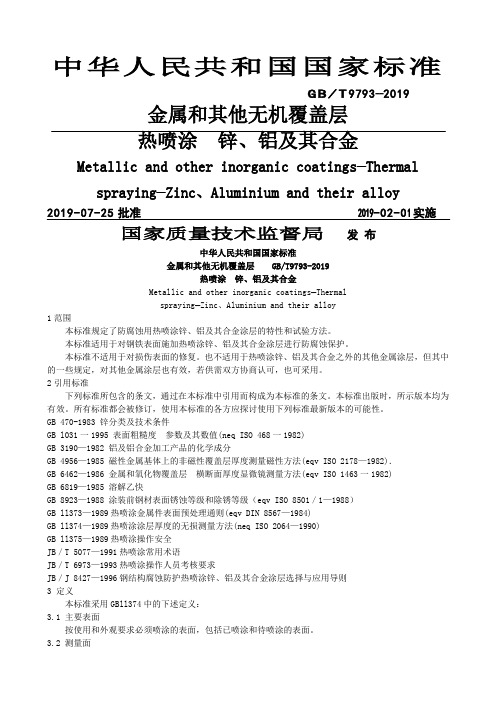
中华人民共和国国家标准GB/T9793--2019金属和其他无机覆盖层热喷涂锌、铝及其合金Metallic and other inorganic coatings—Thermal spraying—Zinc、Aluminium and their alloy2019-07-25批准2019-02-01实施国家质量技术监督局发布中华人民共和国国家标准金属和其他无机覆盖层 GB/T9793-2019热喷涂锌、铝及其合金Metallic and other inorganic coatings—Thermalspraying—Zinc、Aluminium and their alloy1范围本标准规定了防腐蚀用热喷涂锌、铝及其合金涂层的特性和试验方法。
本标准适用于对钢铁表面施加热喷涂锌、铝及其合金涂层进行防腐蚀保护。
本标准不适用于对损伤表面的修复。
也不适用于热喷涂锌、铝及其合金之外的其他金属涂层,但其中的一些规定,对其他金属涂层也有效,若供需双方协商认可,也可采用。
2引用标准下列标准所包含的条文,通过在本标准中引用而构成为本标准的条文。
本标准出版时,所示版本均为有效。
所有标准都会被修订,使用本标准的各方应探讨使用下列标准最新版本的可能性。
GB 470-1983 锌分类及技术条件GB l031一1995 表面粗糙度参数及其数值(neq ISO 468一1982)GB 3190—1982 铝及铝合金加工产品的化学成分GB 4956—1985 磁性金属基体上的非磁性覆盖层厚度测量磁性方法(eqv ISO 2178—1982).GB 6462—1986 金属和氧化物覆盖层横断面厚度显微镜测量方法(eqv IS0 1463一1982)GB 6819—1985 溶解乙快GB 8923—1988 涂装前钢材表面锈蚀等级和除锈等级(eqv ISO 8501/1—1988)GB ll373—1989热喷涂金属件表面预处理通则(eqv DIN 8567—1984)GB ll374—1989热喷涂涂层厚度的无损测量方法(neq ISO 2064—1990)GB ll375—1989热喷涂操作安全JB/T 5077—1991热喷涂常用术语JB/T 6973—1993热喷涂操作人员考核要求JB/J 8427—1996钢结构腐蚀防护热喷涂锌、铝及其合金涂层选择与应用导则3 定义本标准采用GBll374中的下述定义:3.1 主要表面按使用和外观要求必须喷涂的表面,包括已喷涂和待喷涂的表面。
电弧喷涂工艺参数对涂层组织和性能的影响

相同工艺条件下获得的不同材料涂层 ,它们中的氧化物含 量也有很大差别的 。这是因为不同的材料 ,喷涂过程中所发生 的化学反应和氧化程度是不同的 。比较本次试验的两种喷涂材 料 ,发现 1Cr13 涂 层 中 的 氧 化 物 含 量 要 比 3Cr13 高 。1Cr13 和 3Cr13 材料属于 Cr13 型不锈钢 ,其中的 Cr 元素加入的作用是极 易在材料表面形成 Cr2O3 的致密的钝化膜 。喷涂这两种材料 时 ,熔滴雾化过后 ,熔融金属粒子在飞行中与空气高温接触会形 成该钝化膜 ,起到隔绝熔滴与空气的屏障作用 ,将显著降低它们 的氧化程度 。
a 01 号 ; b 02 号 ; c 03 号 ; d 04 号 ; e 05 号 ; f 06 号 图 1 不同工艺参数下涂层的金相组织
比较相同工艺条件下制备的不同材料的涂层结构 ,如比较 02 、05 号试样上所得的涂层 ,可发现涂层的致密度由高到低依 次为 05 、02 。这表明涂层组织结构致密度以 3Cr13 涂层最好 、 1Cr13 涂层次之 。
热镀锌、热喷锌、电弧喷铝的比较

热镀锌、热喷锌、电弧喷铝的比较一、热镀锌、热喷锌、电弧热喷铝的介绍热镀锌热镀锌又称为热浸镀锌,他是在高温下把锌锭融化,在放入一些辅助材料,然后把金属结构件浸入镀锌槽中,使金属构件上附着一层锌层。
热镀锌的优点在于他的防腐能力强,镀锌层的附着力和硬度较好。
缺点在于价格较高,需要大量的设备和场地,钢结构件过大不易放入镀锌槽中,钢结构件过于单薄,热镀又容易变形。
工艺过程工件→脱脂→水洗→酸洗→水洗→浸助镀溶剂→烘干预热→热镀锌→整理→冷却→钝化→漂洗→干燥→检验热喷铝目前热喷铝应用较多的是线材火焰喷涂和电弧喷涂两种方法,该项目采用线材火焰喷涂。
线材火焰喷涂是研制早、应用早、技术成熟的热喷涂方法,其特点是轻便、灵活、机动性好,因此在该项目中应用尤为合适。
该方法采用氧-乙炔焰作为热源,喷涂材料为铝线材。
工艺过程除油脱脂→喷砂除锈(Sa2.5 Rz 40-60μm)→热喷铝→表面清理→喷铝检测→喷涂或刷涂密封涂层电弧喷铝电弧喷涂技术就是通过专用电源,使带电的耐腐蚀金属丝材产生电弧熔化,在1/1000—1/10000秒内,熔融金属的高温液滴被压缩空气喷吹、雾化、喷涂至预先喷砂除锈的钢铁构件表面,形成纯度高、结合力强的机械—冶金结合喷涂层,它对活泼的钢铁基体具有阴极保护作用。
然后在该喷涂层上均匀涂敷具有抑制腐蚀作用的专用封闭剂,它不仅能进一步隔绝腐蚀介质侵蚀基体钢铁,同时使电弧喷涂金属层与封闭涂层界面阻抗增大,耐腐蚀性能大为增强。
工艺过程:除油脱脂→喷砂除锈(Sa2.5 Rz 40~100μm)→电弧喷铝→封闭→喷涂面漆二、热喷锌与热镀锌工艺性能和价格分析比较1、热喷锌涂层和热镀锌镀层与钢铁基体结合力大小的比较热喷锌工艺钢铁基体采用喷砂除锈,基体表面具有一定的粗糙度(达40~60um),使得基体表面电化活化能力增加,大部分锌涂层以金属键的形式与钢铁基体表面结合。
浸镀锌工艺钢铁基体采用酸洗除锈,基体表面较光滑,而钢铁基体表面还将残留有害离子,影响镀层与基体结合力。
金属的热喷锌(铝)防腐、有机涂料防腐、热浸镀锌防腐的工艺性能及经济效益比较
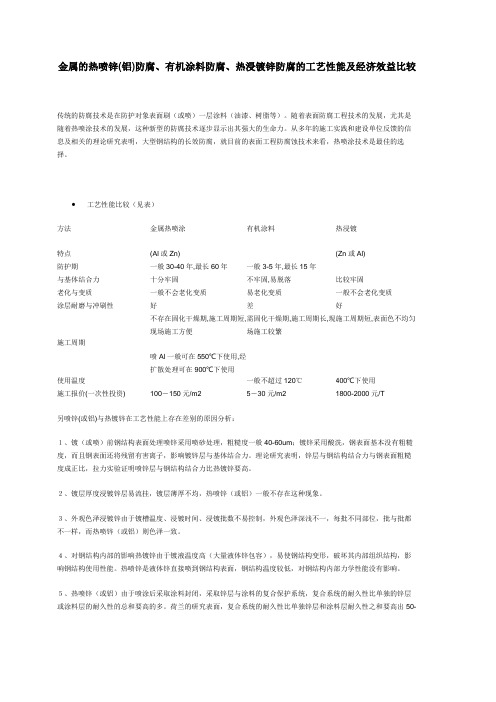
金属的热喷锌(铝)防腐、有机涂料防腐、热浸镀锌防腐的工艺性能及经济效益比较传统的防腐技术是在防护对象表面刷(或喷)一层涂料(油漆、树脂等)。
随着表面防腐工程技术的发展,尤其是随着热喷涂技术的发展,这种新型的防腐技术逐步显示出其强大的生命力。
从多年的施工实践和建设单位反馈的信息及相关的理论研究表明,大型钢结构的长效防腐,就目前的表面工程防腐蚀技术来看,热喷涂技术是最佳的选择。
•工艺性能比较(见表)方法特点金属热喷涂(Al或Zn)有机涂料热浸镀(Zn或Al)防护期一般30-40年,最长60年一般3-5年,最长15年与基体结合力十分牢固不牢固,易脱落比较牢固老化与变质一般不会老化变质易老化变质一般不会老化变质涂层耐磨与冲刷性好差好施工周期不存在固化干燥期,施工周期短,现场施工方便需固化干燥期,施工周期长,现场施工较繁施工周期短,表面色不均匀使用温度喷Al一般可在550℃下使用,经扩散处理可在900℃下使用一般不超过120℃400℃下使用施工报价(一次性投资) 100-150元/m2 5-30元/m2 1800-2000元/T另喷锌(或铝)与热镀锌在工艺性能上存在差别的原因分析:1、镀(或喷)前钢结构表面处理喷锌采用喷砂处理,粗糙度一般40-60um;镀锌采用酸洗,钢表面基本没有粗糙度,而且钢表面还将残留有害离子,影响镀锌层与基体结合力。
理论研究表明,锌层与钢结构结合力与钢表面粗糙度成正比,拉力实验证明喷锌层与钢结构结合力比热镀锌要高。
2、镀层厚度浸镀锌层易流挂,镀层薄厚不均,热喷锌(或铝)一般不存在这种现象。
3、外观色泽浸镀锌由于镀槽温度、浸镀时间、浸镀批数不易控制,外观色泽深浅不一,每批不同部位,批与批都不一样,而热喷锌(或铝)则色泽一致。
4、对钢结构内部的影响热镀锌由于镀液温度高(大量液体锌包容),易使钢结构变形,破坏其内部组织结构,影响钢结构使用性能。
热喷锌是液体锌直接喷到钢结构表面,钢结构温度较低,对钢结构内部力学性能没有影响。
锅炉受热面防磨喷涂

喷涂技术应用
谢谢合作!
是#10钢的20倍 耐冲蚀磨损:耐冲蚀性能是#10钢的10倍 平均磨损速度:≤0.13㎜/年 孔隙率:<2% 膨胀系数:与金属相近:8.8×10-6/K
喷涂工艺要求 ①用10---12目石英砂对设备表面进行喷砂处理,其作
用:清除金属表面锈斑及油污 ;增加金属表面粗 糙度,管壁打磨减薄量不超过管壁厚度的0.08~0.1 ㎜ ;清洁金属表面;喷涂前对管排进行喷砂处理, 漏出金属光泽并保持一定粗糙度,以利于喷涂层粘 接。 。
耐高温、抗磨、耐气蚀、微创面修复。
超音速喷涂性能指标
名称
性能指标
涂层厚度
≤ 0.2 mm
结合强度
70 MPa
硬度
≥ 69 HRC
平均磨损速度
≤ 0.03 mm / 年
孔隙率 膨胀系数
<2% 与金属相近: 10.6×10 -6/ K
注:适用于阀门密封面、汽轮机转子叶片喷涂
⑶ 等离子喷涂
等离子喷涂采用氩气启弧、氮气加氢气 做为离子气,气体在喷嘴内经电弧燃烧 电离形成高能等离子弧气束,将合金粉 末注入等离子束流中,粉末熔融并以很 高的速度冲击基体表面,形成坚固的涂 层。
喷涂工艺要求
冷喷涂: ①施工工艺流程: 表面清灰→化学清洗→机
械除锈→喷涂防磨层 ②表面清灰:用扫把、压缩空气、自来水、
抹布等工具清理施工部位的浮灰及杂物。 ③用专用化学清洗剂清洗表面。
喷涂工艺要求
④机械除锈除垢(喷石英砂除锈)。 ⑤用专用喷枪进行喷涂(GN、GM系列涂料+
耐高温胶液)。 ⑥进行喷涂层质量验收。
抗冲蚀性能是#10钢的10倍 ≤ 0.13 mm/年 <2% 与金属相近: 8.8×10 -6/ K
电弧喷铝防腐要求及技术数据
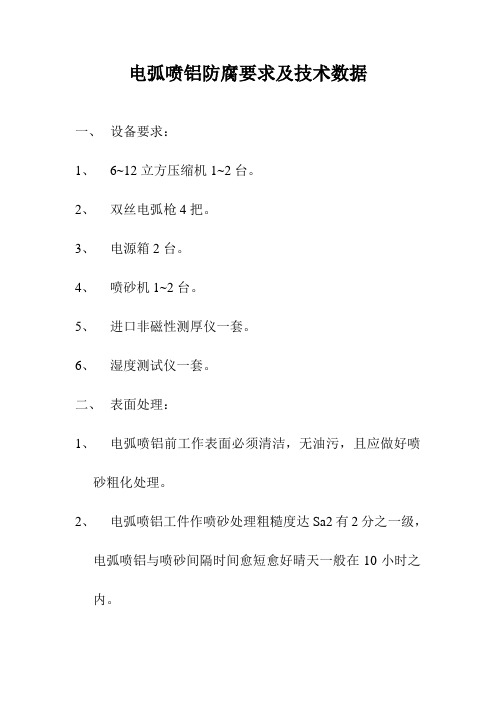
电弧喷铝防腐要求及技术数据
一、设备要求:
1、6~12立方压缩机1~2台。
2、双丝电弧枪4把。
3、电源箱2台。
4、喷砂机1~2台。
5、进口非磁性测厚仪一套。
6、湿度测试仪一套。
二、表面处理:
1、电弧喷铝前工作表面必须清洁,无油污,且应做好喷
砂粗化处理。
2、电弧喷铝工件作喷砂处理粗糙度达Sa2有2分之一级,
电弧喷铝与喷砂间隔时间愈短愈好晴天一般在10小时之内。
三、表面电弧喷铝要求:
1、对处理后对工件进行电弧喷铝加工要求涂层必须均
匀,不起绉及裂纹,掉块现象,并没有影响涂层的缺陷。
2、电弧喷铝层厚度大于150μ(用非磁性测厚仪测量)。
3、涂层结合强度可采用切格法试验,对多块铝涂层的试
验平均结合强度不得小于0.6KG/MM平方。
四、表面涂层耐腐蚀性:
电弧喷铝涂层≥150μ并加封闭常规用开林造漆厂842环氧云铁底漆,前提之下可保用20年(根据试验大气腐蚀每年平均5——10μ)。
以上是电弧喷铝的技术要求及参数。
注:如果考虑防腐及结合强度,可采用喷锌打底,电弧喷铝覆盖;842环氧云铁底漆封闭可能更好(以上供参考)。
上海南福五金喷涂塑料厂。
电弧喷涂工艺参数对3Cr13涂层性能稳定性的影响
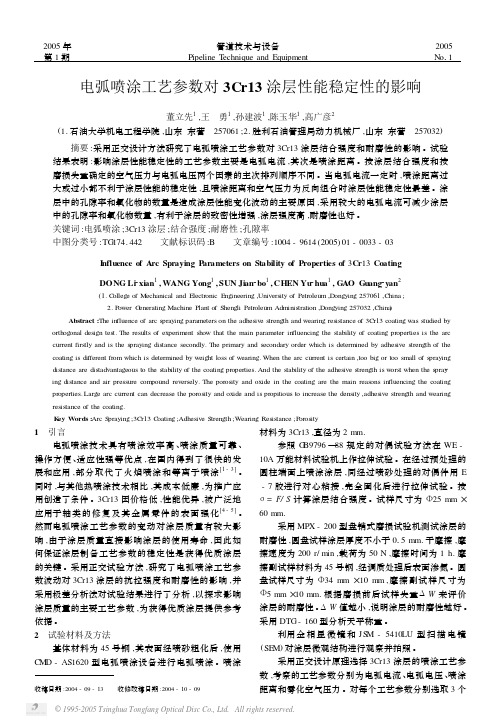
properties. Large arc current can decrease the porosity and oxide and is propitious to increase the density ,adhesive strength and wearing
resistance of the coating.
Influence of Arc Spraying Parameters on Stability of Properties of 3Cr13 Coating
DONG Li2xian1 , WANG Yong1 , SUN Jian2bo1 , CHEN Yu2hua1 , GAO Guang2yan2
表 2 涂层性能试验结果
编号
结合强度 σ/ MPa
1#
3219
3310
3218
3416
3615
2#
3611
3714
3812
3610
3612
3#
3210
3215
3612
3114
3116
4#
3012
3215
3016
2716
3411
5#
2813
2914
3110
3318
2619
6#
ቤተ መጻሕፍቲ ባይዱ
2816
3018
3219
2618
3213
7#
3214
2716
3013
3418
2917
8#
3211
2918
2519
2611
3413
9#
3115
3311
2819
锅炉受热面防磨喷涂

精选ppt
1
一、锅炉受热面防磨喷涂类型
• 1、金属热喷涂; • 2、高温耐磨防腐喷涂; • 3、电弧喷涂; • 4、特种陶瓷喷涂; • 5、钠米材料喷涂。
精选ppt
2
二、喷涂技术应用
• 火力发电厂中,高速烟气携带的飞灰颗粒
对金属基体表面的撞击、滑动形成冲蚀磨 损和磨粒磨损,承压部件的磨损主要是由 这两种磨损形成的,有时还存在高温硫腐 蚀等,严重危及电厂安全运行。
精选ppt
16
四、喷涂工艺要求
• 电弧喷涂:
• 技术标准
• 涂层厚度:0.3~1.0㎜(可根据实际情况选
择)
• 结合强度:>41.3Mpa
• 硬度:≥60HRC
• 抗氧化性能:在800℃时抗冲击、抗氧化性
是#10钢的20倍
• 耐冲蚀磨损:耐冲蚀性能是#10钢的10倍
• 平均磨损速度:≤0.13㎜/年
抗冲蚀性能是#10钢的10倍
平均磨损速度
≤ 0.13 mm/年
孔隙率 膨胀系数
<2% 与金属相近: 8.8×10 -6/ K
精选ppt
6
⑵超音速喷涂Leabharlann • 超音速喷涂技术是一项先进的防磨技术。
用氧气和液态燃料通过预混合系统在高压 下输入燃烧室爆燃,形成高压气流。气流 通过拉阀尔喷嘴膨胀,加速到1500m/s,该 气流将合金粒子加热并加速到二次喷嘴, 高能粒子束冲击到基材表面,形成致密、 高强附着性涂层。
• 主要应用于锅炉尾部受热面(省煤器)的
管壁防磨等。
精选ppt
13
冷喷涂性能指标
名称
性能指标
外观
灰白色
比重
电弧喷涂防磨损涂层性能评价

电弧喷涂防磨损涂层性能评价电弧喷涂涂层作为一种新型涂层,具有良好的抗磨损性能,因此成为重要的表面处理技术。
但随着电弧喷涂参数不断优化,其防磨损涂层性能也不断优化,电弧喷涂抗磨损涂层性能的评价成为重要的研究课题。
本文以电弧喷涂抗磨损涂层性能的评价为主题,介绍了其评价指标和评价方法,并对电弧喷涂抗磨损涂层性能的优化研究进行了简要介绍。
一、电弧喷涂抗磨损涂层性能评价指标电弧喷涂抗磨损涂层性能的评价指标主要包括耐磨性,耐腐蚀性,疲劳性能,热稳定性,微观结构,表面精度等。
1.耐磨性:耐磨性表示涂层在磨耗下能维持其机械性能和结构不变,可用钢丝研磨试验来测定电弧喷涂抗磨损涂层耐磨性。
2.耐腐蚀性:耐腐蚀性表示涂层在酸碱腐蚀及水和气体腐蚀下的耐受性。
可用盐雾试验、浸渍试验及电化学阻抗谱等方法来测定电弧喷涂抗磨损涂层的耐腐蚀性。
3.疲劳性能:疲劳性能表示涂层在大幅度变形后、超过疲劳极限后,能够维持其机械性能和形状不变,疲劳性能可用循环载荷实验来测定。
4.热稳定性:热稳定性表示涂层在高温下的稳定性,及防止涂层失效的能力,可用耐热稳定性试验来测定电弧喷涂抗磨损涂层的热稳定性。
5.微观结构:微观结构测试表明涂层的结构形状、孔隙大小、晶粒尺寸等,可以用扫描电子显微镜等方法来测量电弧喷涂抗磨损涂层的微观结构。
6.表面精度:表面精度是指涂层表面的平整度和光洁度,可用测量仪器测量表面粗糙度及表面光洁度等指标,从而计算出抗磨损涂层的表面精度。
二、电弧喷涂防磨损涂层性能评价方法1.实验室试验:主要包括磨损试验、表面检测、电化学检测等,可以进行定量的获取电弧喷涂抗磨损涂层的性能参数。
2.数值模拟:数值模拟可以通过多场耦合技术,将多个影响因素耦合起来,定量的对电弧喷涂抗磨损涂层的耐磨性性能进行模拟仿真。
三、电弧喷涂防磨损涂层性能优化研究为了提高电弧喷涂抗磨损涂层的性能,在不同参数优化方面均作出了努力。
根据晶粒结构优化已取得了良好的效果,其中涂层晶粒大小的优化已取得了良好的效果,晶粒的形状则影响抗磨损涂层的耐磨性,因此在参数优化方面应重视晶粒形状的优化。
热喷涂国际标准
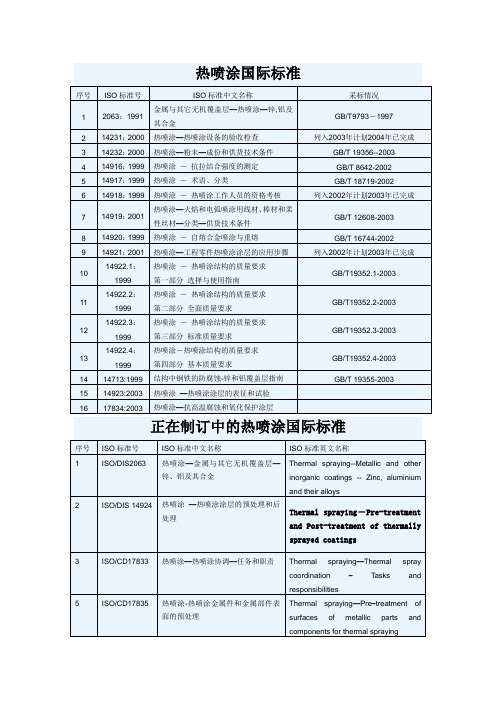
8
14920:1999
热喷涂-自熔合金喷涂与重熔
GB/T 16744-2002
9
14921:2001
热喷涂—工程零件热喷涂涂层的应用步骤
列入2002年计划2003年已完成
10
14922.1:1999
热喷涂-热喷涂结构的质量要求
第一部分选择与使用指南
GB/T19352.1-2003
14
14713:1999
结构中钢铁的防腐蚀-锌和铝覆盖层指南
GB/T 19355-2003
15
14923:2003
热喷涂—热喷涂涂层的表征和试验
16
17834:2003
热喷涂—抗高温腐蚀和氧化保护涂层
正在制订中的热喷涂国际标准
序号
ISO标准号
ISO标准中文名称
ISO标准英文名称
1
ISO/DIS2063
11
14922.2:1999
热喷涂-热喷涂结构的质量要求
第二部分全面质量要求
GB/T19352.2-2003
12
14922.3:1999
热喷涂-热喷涂结构的质量要求
第三部分标准质量要求
GB/T19352.3-2003
13
14922.4:1999
热喷涂-热喷涂结构的质量要求
第四部分基本质量要求
GB/T19352.4-2003
10
JB/T9191-1999
等离子喷焊技术条件
11
JB/T9192-1999
等离子喷焊电源
线材喷涂碳钢及不锈钢
5
JB/T6975-1993
自熔合金喷焊技术条件
6
JB/T7509-1994
6061铝合金表面电弧喷涂纯铝涂层的研究
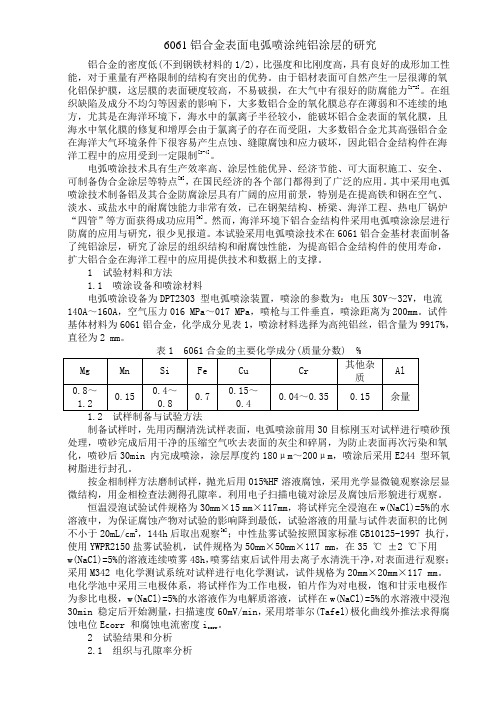
6061铝合金表面电弧喷涂纯铝涂层的研究铝合金的密度低(不到钢铁材料的1/2),比强度和比刚度高,具有良好的成形加工性能,对于重量有严格限制的结构有突出的优势。
由于铝材表面可自然产生一层很薄的氧化铝保护膜,这层膜的表面硬度较高,不易破损,在大气中有很好的防腐能力[1-2]。
在组织缺陷及成分不均匀等因素的影响下,大多数铝合金的氧化膜总存在薄弱和不连续的地方,尤其是在海洋环境下,海水中的氯离子半径较小,能破坏铝合金表面的氧化膜,且海水中氧化膜的修复和增厚会由于氯离子的存在而受阻,大多数铝合金尤其高强铝合金在海洋大气环境条件下很容易产生点蚀、缝隙腐蚀和应力破坏,因此铝合金结构件在海洋工程中的应用受到一定限制[3-4]。
电弧喷涂技术具有生产效率高、涂层性能优异、经济节能、可大面积施工、安全、可制备伪合金涂层等特点[5],在国民经济的各个部门都得到了广泛的应用。
其中采用电弧喷涂技术制备铝及其合金防腐涂层具有广阔的应用前景,特别是在提高铁和钢在空气、淡水、或盐水中的耐腐蚀能力非常有效,已在钢架结构、桥梁、海洋工程、热电厂锅炉“四管”等方面获得成功应用[6]。
然而,海洋环境下铝合金结构件采用电弧喷涂涂层进行防腐的应用与研究,很少见报道。
本试验采用电弧喷涂技术在6061铝合金基材表面制备了纯铝涂层,研究了涂层的组织结构和耐腐蚀性能,为提高铝合金结构件的使用寿命,扩大铝合金在海洋工程中的应用提供技术和数据上的支撑。
1 试验材料和方法1.1 喷涂设备和喷涂材料电弧喷涂设备为DPT2303 型电弧喷涂装置,喷涂的参数为:电压30V~32V,电流140A~160A,空气压力016 MPa~017 MPa,喷枪与工件垂直,喷涂距离为200mm。
试件基体材料为6061铝合金,化学成分见表1,喷涂材料选择为高纯铝丝,铝含量为9917%,直径为2 mm。
表1 6061合金的主要化学成分(质量分数) %制备试样时,先用丙酮清洗试样表面,电弧喷涂前用30目棕刚玉对试样进行喷砂预处理,喷砂完成后用干净的压缩空气吹去表面的灰尘和碎屑,为防止表面再次污染和氧化,喷砂后30min 内完成喷涂,涂层厚度约180μm~200μm,喷涂后采用E244 型环氧树脂进行封孔。
热喷涂高铝含量Zn-Al合金涂层热带岛礁大气环境腐蚀行为研究

第21卷第3期装备环境工程2024年3月EQUIPMENT ENVIRONMENTAL ENGINEERING·129·热喷涂高铝含量Zn-Al合金涂层热带岛礁大气环境腐蚀行为研究郭强1,赵巍2,张冲1(1.北京机械设备研究所,北京 100854;2.空军装备部驻北京地区第一军事代表室,北京 100854)摘要:目的研究Zn-Al合金涂层在热带海洋大气环境中的腐蚀行为,为低合金钢长效防护涂层的选用提供依据。
方法采用电弧热喷涂和高铝合金丝制备高铝含量Zn-Al合金涂层,通过户外暴露试验,采用目视、扫描电镜及能谱仪、金相显微镜、XRD、电化学交流阻抗谱和动电位极化曲线等方法,对不同暴露周期的涂层宏观、微观表面形貌、成分组成、截面形貌、腐蚀产物组成、电化学性能和腐蚀速率等进行观察、测试。
结果 Zn-Al合金涂层是以质量比为50%:50%的Zn/Al合金组成。
在0~540 d周期内,涂层腐蚀产物主要由碱式锌铝碳酸盐化合物Zn6Al2(OH)16CO3·H2O和羟基锌铝碳酸盐化合物Zn0.70Al0.30(OH)2(CO3)0.15·x H2O、Zn0.71Al0.29(OH)2(CO3)0.145·x H2O等组成,其对涂层孔隙进行填充。
相对于初始涂层,180、360、540 d腐蚀后,涂层的极化电阻增加1个数量级,自腐蚀电位增加了约200 mV,自腐蚀电流密度降低至30%左右。
结论该Zn-Al合金涂层在腐蚀后保持较低且稳定的腐蚀速率,具有较好的耐腐蚀性能,致密且黏性的腐蚀产物对涂层孔隙起到了自封闭作用,显著提高了涂层的耐蚀性。
关键词:电弧热喷涂;高铝锌基合金;涂层;热带岛礁;大气腐蚀;腐蚀规律中图分类号:TG172 文献标志码:A 文章编号:1672-9242(2024)03-0129-09DOI:10.7643/ issn.1672-9242.2024.03.017Corrosion Behavior of Thermal Sprayed Zinc-Aluminum Alloy Coating withHigh Aluminum Content in Tropical Island-reef Atmospheric EnvironmentGUO Qiang1, ZHAO Wei2, ZHANG Chong1(1. Beijing Institute of Machinery and Equipment, Beijing 100854, China; 2. First Military RepresentativeOffice of Air Force Equipment Department in Beijing, Beijing 100854, China)ABSTRACT: The work aims to investigate the corrosion behavior of thermal sprayed Zn-Al alloy coatings with high aluminum content in the tropical marine atmospheric environment, so as to provide selection evidence of long-term protective metal coat-ings on low alloy steel. An outdoor exposure test in a tropical island-reef atmospheric environment was conducted to research the corrosion behavior of Zn-Al alloy coatings with high content of Al on low alloy steel. By the means of visual observation, scanning electron microscope (SEM), energy diffraction spectrum (EDS), optical microscope, X-ray diffraction, electrochemical impedance spectroscopy (EIS) and potential-dynamic polarization curve, et al, the macroscopic and microscopical surface mor-phology, chemical composition, section morphology, corrosion product composition, electrochemical properties and corrosion收稿日期:2023-10-31;修订日期:2024-02-18Received:2023-10-31;Revised:2024-02-18引文格式:郭强, 赵巍, 张冲. 热喷涂高铝含量Zn-Al合金涂层热带岛礁大气环境腐蚀行为研究[J]. 装备环境工程, 2024, 21(3): 129-137. GUO Qiang, ZHAO Wei, ZHANG Chong.Corrosion Behavior of Thermal Sprayed Zinc-Aluminum Alloy Coating with High Aluminum Content in Tropical Island-reef Atmospheric Environment[J]. Equipment Environmental Engineering, 2024, 21(3): 129-137.·130·装备环境工程 2024年3月rate were observed and tested. The weight ratio of Zn and Al in Zn-Al alloy coatings was 50%: 50wt%. The corrosion product layer on the Zn-Al alloy coating mainly consisted of basic zinc aluminum carbonate compound Zn6Al2(OH)16CO3.H2O, and hy-droxy zinc aluminum carbonate compounds such as Zn0.70Al0.30(OH)2(CO3)0.15·x H2O and Zn0.71Al0.29(OH)2(CO3)0.145·x H2O, which sealed the pores in the Zn-Al alloy coating. Compared with the uncorroded coating, the coating after 180 d, 360 d and 540d exposure increased by an order of magnitude, and the free corrosion potential increased about 200 mV, and the self-corrosioncurrent density decreased to about one-third of the uncorroded coating. After corrosion, the Zn-Al alloy coating shows low and stable corrosion rate, which shows excellent anti-corrosion properties. Dense and viscous corrosion products seal the pores of the coating, improving the corrosion resistance of the Zn-Al alloy coating.KEY WORDS: arc thermal spraying; high Al-Zn based alloy; coating; tropical island-reef; atmospheric corrosion; corrosion rule由于纬度较低、远离大陆等地理原因,我国某热带海域腐蚀等级较高,按照ISO 9223—2012《金属和合金的腐蚀大气的腐蚀性分类》的规定,其腐蚀等级达到了C5或CX级,该海域是我国乃至世界腐蚀等级极高的海域之一[1-3]。
电弧喷涂铝涂层工艺参数优化和涂层结构分析

表 1 电弧喷涂铝涂层工艺参数因素水平表
因素 水平
1 2 3
喷涂电 流 I/ A
100 120 150
喷涂电 压 U/ V
28 32 35
雾化空气 压力 P/ MPa
0. 4 0. 5 0. 6
喷涂距离 L/ mm 150 200 250
表 2 正交试验设计方案及实验结果
试验 喷涂电 喷涂电 雾化空气 喷涂距 结合强度
同的 。极差越大 ,说明这个因素的水平改变时对试
验指标的影响越大 。极差最大的那个因素就是需
要考虑的主要因素 。按极差大小排列出各因素对
结合 强 度 指 标 影 响 的 主 次 顺 序 为 : PL I U ( 主 →
次) ;各 因素对 孔隙率 指 标 影 响 的 主 次 顺 序 为 :
PL I U (主 →次) 。
提高了 2. 30 %。从孔隙率来看 ,a 组涂层的孔隙率比
优化前降低了大约 6. 64 % ,b 组涂层孔隙率最低 ,比
优化前降低了 9. 88 %。综合考虑结合强度和孔隙率
2 个因素 ,确定优化后 b 组参数 I3 U2 P3 L 1 为最优工 艺参数 。
图 1 结合强度效应与因素水平关系图 图 2 孔隙率效应与因素水平关系图
p rocessing parameters were optimized by ort hogo nal experimental design. The optimized p rocessing parameters were : sp ray current 150A , sp ray voltage 32V , atomizing air p ressure 0. 6M Pa , and sp ray distance 150mm. The result s showed t hat t here were 9. 88 % decrease in coating poro sity and 2. 30 % increase in bond st rengt h after optimization. The p rime reason was t hat large elect ric arc power was favorable to t he interf usion of aluminum particles. Sp ray current and sp ray voltage had different effect s on t he increase of arc power. Increase of sp ray current imp roved t he quality of coatings more effectively t han sp ray voltage.
电弧喷涂铝基涂层耐腐蚀性能
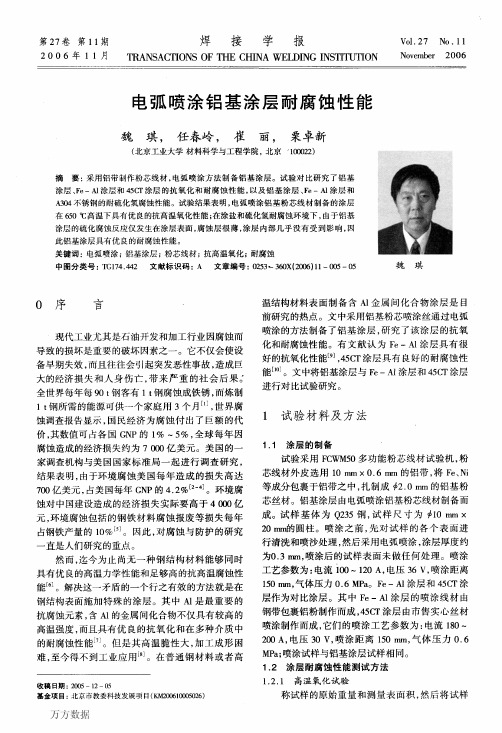
150 I姗,气体压力0.6 MPa。Fe—Al涂层和45cT涂
层作为对比涂层。其中Fe—Al涂层的喷涂线材由 钢带包裹铝粉制作而成,45CT涂层由市售实心丝材 喷涂制作而成,它们的喷涂工艺参数为:电流180~ 200 A,电压30 V,喷涂距离150 mm,气体压力0.6 MPa;喷涂试样与铝基涂层试样相同。 1.2涂层耐腐蚀性能测试方法 1.2.1高温氧化试验
1试验材料及方法
1.1涂层的制备 试验采用FCWM50多功能粉芯线材试验机,粉
芯线材外皮选用10ⅡⅡn×0.6 n硼的铝带,将Fe、Ni
等成分包裹于铝带之中,扎制成乒2.o rm的铝基粉
芯丝材。铝基涂层由电弧喷涂铝基粉芯线材制备而 成。试样基体为Q235钢,试样尺寸为≠10 n瑚×
20一的圆柱。喷涂之前,先对试样的各个表面进
基涂层氧化后生成了Al,Fe,Ni之间的化合物,A12 03 以及少量的Fe20,和Fe。
图3为Fe一灿涂层和铝基涂层氧化后表面 SEM形貌。由图3a来看图中主要为疏松的针状组 织,经分析为Fe20,。由图3b来看主要由片状的A 区域和脊状的B区域组成,经分析片状结构为亚稳 态0一A12 03,脊状结构为稳态a.A12 03,这两种结构的
600℃时的硫化氢腐蚀动力学曲线。由图7可知, A304不锈钢的硫化氢腐蚀动力学瞳线呈二次函数 增长,在600℃,经12 h硫化氢腐蚀后,腐蚀产物从 基体上剥落下来,说明其耐硫化氢腐蚀性能很差。 Fe一灿涂层和铝基涂层的硫化氢腐蚀动力学曲线 均为对数函数,曲线变化较缓,涂层均对基材具有一 定的保护作用。从图7可以看出,铝基涂层腐蚀增 重最低,抗硫化氢腐蚀性能最好。
电弧喷涂锌铝涂层耐腐蚀实验报告

电弧喷涂锌铝涂层耐腐蚀实验报告一、实验背景水工钢闸门是水电站、水库、水闸、船闸等水工建筑物中控制水位的重要水工钢构件,其制造量约为500万吨,保有量十分巨大。
水工钢闸门由于长期浸水,在阴暗潮湿、干湿交替、高速水流、风浪、水生物腐蚀等恶劣环境下工作,经多年运行后很容易被腐蚀,出现绣皮泛起、局部绣坑密布,导致整个结构强度削弱,降低了钢闸门的承载能力,还要消耗大量的人力、物力、财力。
Zn-13A1涂层具有良好的耐腐蚀性能,以高速电弧喷涂方式将之喷到水工钢闸门表面可以有效防止表面腐蚀。
二、实验目的本实验针对内陆水库及水电站工程,模拟其水工钢闸门的运行环境,研究Zn-13A1涂层对水工钢闸门的保护程度及对比分析不同保护涂层(Zn跟Zn-13A1)对防腐蚀能力的优劣程度。
三、实验器材NaCl溶液,Q235钢板,棕刚玉砂,喷砂机,高性能电弧喷涂设备,超声清洗机,电子天平,防腐涂料,交流阻抗测试仪,M273 型电位仪,5208 型锁相放大器焊机,铜导线等。
四、实验过程1、制备浸泡液:质量分数为5%的NaCl溶液。
2、加工试样,将Q235钢板加工成72片尺寸为12 mm*12mm*3mm的试样,将之分为九组,每组8片。
3、采用颗粒度为14~18#的棕刚玉砂对前六组试样表面进行喷砂处理。
喷砂操作时,压缩空气的工作压力为0.6 MPa,喷砂距离为150~200 mm,喷砂角度为70°~80°。
4、使用TLAS-III 型高性能电弧喷涂设备制备Zn-13A1涂层,电压45V,电流120A;制备Zn涂层,电压40V,电流120A。
5、丙酮超声清洗3min后烘干,将54片试样沉重,并记录,剩余的18个试样用于随时观察腐蚀情况。
6、将清洗过的试样画出工作界面:10mm*10mm;试样多余的部分用防腐涂料密封,露出10mm*10mm的工作界面。
同时将做电化学测试的试样焊接铜导线,以便测试其极化曲线和阻抗。
7、将全部处理好的试样放入浸泡液中,按照GBT19746-2005《金属和合金的腐蚀盐溶液周浸试验》标准进行全浸泡试验。
电弧喷铝工艺

施工工艺瀬(表二)三、Fl前大桥钢主梁钢结构采用的防锈、防腐工艺日前,我们在钢主梁防镌、防腐施丄中采用了“常温电弧喷涂锌铝合金”的施工工艺技术.一)电弧喷涂的特点电弧喷涂防腐原理是利川电豪喷涂设备'对两根带电的金屈丝(如锌.铝鸽)貯丁丿J出、嫌L雾化、區涂形成阪郞紘”卜加有机H 肝;紘的长效防腐复合涂层,该涂层的显著特点是:(1)具有较长久的耐腐蚀寿命. 其防腐寿命可达到50年以上,同时该防If涂层在30年便用期内无须其它任何防腐维护;(2)电孤喷涂层与金居基体具有优肚的涂层结合力,金属喷涂层以机械锻恢和倣冶金与基体金屈相结介。
-)喷涂锌铝合金的特点1、抗腐蚀性能好盐第试验表明,锌铝合金涂层的耐腐蚀性使纯锌涂层的6〜7借,是纯铝涂层的3倍,2、涂层结合力好在钳/锌复仟镀层表曲涂状涂料,因贞镀层表IIri具有复朵的表面形状特征,使期織的密着力是一傲钢材4倍•而耐食性能是常規涂装的2倍以匕3、共有良好的工芝:性验喷涂纯梓徐层时会产生大虽的enon臭味尘芜因而容易使嫌卄诸得观业病,故提高了劳动保护描施的炙忆喷涂纯铝则耍求被喷基体(如钢材)表面结晶度要求较髙,_股施工现场难以达刮。
而采用皀n/al合金喷淪由丁•其对钢棊材有很好的侵润性,不像喘余純钳对棊材纯孙度要求那么苛纵同时也不会像喷涂纯铅那样产生过黄的e∩on-4、有较髙的性能价格比为达到设计上的防腐年限,对喷涂层有厚度的耍求。
若以纯脱川瑕为设计厚丿鬼如便用en/al 金,则其总闸度仅为设计厚度纯锌涂层的1/2便可满足要求。
也就是说,便用en/al合金涂层的便用寿命比純澤涂层提高1,5倍,从而可节约材料50%,其的成本可减少35%β吐电加喘余怦钳合金在久桥制主梁肪锈、防腐中的应用工艺流程O防鮒涂装工艺规程(表三)O防腐蚀涂装机械设备仪器要求I二)喷砂工艺钢材表而存在不同程度锈蚀,可以归纳为a、b、CdH个等级;根据gb∕t8923 88标准,人桥钢主梁锈蚀程度有30%达到了b级锈蚀程取■•钢材表耐京始锈蚀程度(gb∕t8923-88)※现场喷O I的难题由于黄浦江大桥周边环境有工业厂区,更有都分住宅区;对喷砂除锈的坏保要求非常高;我们的防锈防腐施工跟工区内作业要求完全不同4 喷砂除锈要达到钢主梁防锈防腐的丁艺技术耍求、施工质量要求,施工屮必定要产生一定的噪声及粉尘污染•但是周边坏境环保的要求同样要满足°1、工艺参数①气压:0.45-0.65mpa②喷射角度:60-90°③喷射距离:100-20Omm2、质量检验1)检验依据国家标^gb8923-88《涂装前钢材表面锈蚀等级和除锈等级》;U工艺参数①气压:0.45-0.6SmPa②喷射角度:60-90°③喷射距离:100-20Omm2、质扯检验1)检验依据国家标淮gb8923∙88《涂装前钢材表血勒蚀绞级和除锈等级)):喷砂后清洁达到少21/2级;喷砂粗糙度达到rz25-100μm f即崔取样长度内5个据大轮廓峰高与5个址大轮輝谷深的平沟值Z和。
热喷涂铝涂层质量要求

目录1工艺鉴定要求 (4)1.1总则 (4)1.2工艺过程要求 (4)1.3工艺鉴定程序 (4)1.4工艺鉴定试验及试样要求 (4)1.4.1试样要求 (4)1.4.2试验项目及试样数量 (5)1.5试验方法及质量指标 (5)1.5.1外观 (5)1.5.2铝涂层的表面粗糙度 (5)1.5.3铝涂层厚度 (6)1.5.4结合强度 (6)1.5.5耐蚀性 (6)1.6鉴定状态的保持 (6)2批生产中工件检验要求 (6)2.1外观 (6)2.2铝涂层的表面粗糙度 (7)2.3铝涂层厚度 (7)2.4结合强度 (7)2.5耐蚀性 (7)3参考文献 (7)表目录表1.鉴定试验项目及试样数量 (5)图目录图1 工艺鉴定用试样制作图形 (5)图2 过渡区示意图 (6)错误!未找到引用源。
范围本规范规定了热喷涂铝涂层的工艺和质量要求。
本规范适用于对钢板材料或铝材表面进行局部修复而进行的处理。
简介本规范对热喷涂铝的适用场合、基材对象、加工工艺流程及其后处理限制以及铝涂层的质量要求作出了明确规定。
其中质量要求包括外观、膜厚、表面粗糙度、耐蚀性、结合力等。
关键词热喷涂,铝,修复引用文件下列文件中的条款通过本规范的引用而成为本规范的条款。
凡是注日期的引用文件,其随后所有的修改单(不包括勘误的内容)或修订版均不适用于本规范,然而,鼓励根据本规范达成协议的各方研究是否可使用这些文件的最新版本。
凡是不术语和定义1工艺鉴定要求1.1总则热喷涂铝工艺只适用于对钢板基材或铝材所进行的局部修复处理、或者表面局部导电化处理。
生产者的工艺设备、工艺流程、质量保证措施应在其主要的工艺文件中加以说明。
生产者的工艺质量必须满足第1.2 至1.6节的要求。
1.2工艺过程要求1)热喷涂铝处理必须在工件喷涂有机涂层后进行。
2)热喷涂铝涂层进行化学转化的后处理,可以采用刷涂、喷涂或浸涂等各种方式。
1.3工艺鉴定程序被鉴定的工厂必须完成以下全部试验工作,这些试验必须在零件批生产所用的条件下完成:1)试样加工(注1)2)表面处理(注2)3)试样检查及测试(按1.4节)4)提供试验报告(注3)及试片给华为技术有限公司以便复验。
- 1、下载文档前请自行甄别文档内容的完整性,平台不提供额外的编辑、内容补充、找答案等附加服务。
- 2、"仅部分预览"的文档,不可在线预览部分如存在完整性等问题,可反馈申请退款(可完整预览的文档不适用该条件!)。
- 3、如文档侵犯您的权益,请联系客服反馈,我们会尽快为您处理(人工客服工作时间:9:00-18:30)。
铝基涂层具有优良的耐硫化氢腐蚀性能,涂层中Al可以形成金属间化合物和Al2O3 ,生成的腐蚀产物的内应力比较小,使涂层能够容纳它所产生的塑性变形,不会造成涂层的开裂或脱落;腐蚀产物中的Al2S3 能够抑制铁原子的向外扩散,并且铝原子能够优先与硫结合,阻碍了铁的硫化物的生成,保证了基体不受硫化氢的腐蚀。
循环交换腐蚀(循环): ≥40(无鼓泡,起皮,剥落现象) 2小时酸+2小时碱,40循环
耐盐雾3200hr NaCl浓度5% :无变化 GB-T1771-91
金属覆盖层全浸腐蚀试验:
H2SO4(pH=4)+H2S(20ppm)+去离子水 168小时,试样表面无明显变化。 JB/T6073-1992
附着力(划格法) :0级 GB/T9286-1998
附着力(划圈法) :1级 GB-T1720-79(89)
耐酸120hr :0.1N H2SO4 无变化(无鼓泡,起皮,剥落现象) GB-T1763-79(89)
耐碱120hr :0.1N NaOH 无变化(无鼓泡,起皮,剥落现象)
热喷涂中电弧喷涂铝涂层防腐工作机理
1、阻挡腐蚀介质的隔离作用。
搪瓷和漆类防腐都是此机理;
2、通过涂层材料自我牺牲实现的阴极保护作用。
铝及其合金涂层的电极电位较钢铁材料低,在有电解液存在的条件下,这些涂层为阳极性材料,钢铁为阴极性材料,它们间形成腐蚀原电池。在腐蚀过程中,阳极材料(涂层) 通过自身的牺牲实现对阴极材料(钢铁) 的保护。由于铝涂层的腐蚀产物能有效地减缓腐蚀速度,所以涂层的消耗也是很缓慢的,可以较长时间的保护钢铁基体。
热喷涂中的电弧喷涂,具有长效防腐性能,减少钢结构在服役期间的维护费用,减少涂料施工带来的环境污染,延长钢结构的使用寿命,是钢结构长效防腐蚀的必然趋势。研究开发新的热喷涂防腐蚀材料和相关的涂层封闭体系,深入研究涂层在相应腐蚀体系下的耐蚀机理,完善相关的技术标准,推动该项技术大面积应用,将会产生巨大的经济效益和社会效益。
热喷涂中电弧喷涂铝涂层性能指标
涂层颜色:标准色为银白色
涂层厚度μm :100-200 GB/T4956-2003
弹性mm :1 GB-T1731-93
冲击性N/cm2 :490 GB-T1732-93
光泽(60°)% :40 GB-T1743-ห้องสมุดไป่ตู้9(89)
硬度(铅笔) :3H GB/T6739-2006