搅齿造粒机应用在干法造粒的过程
搅齿造粒机应用在干法造粒地过程

搅齿造粒机应用在干法造粒的过程炭黑是一种堆积密度很低的粉末状物质,易飞扬而污染环境,运输性极差。
一般说来,增加其密度,在某种程度上会克服或清除这些缺点,但也降低了它在介质中的分散性。
炭黑工业常以湿法或干法造粒的方式对粉状炭黑进行加工。
湿法造粒是上个世纪4o年代开发的一项技术。
在最近5O多年中,炭黑工业也在一直不断地改进湿法造粒过程,使之日臻完善。
这些改进主要包括如下几个方面:·开发各种粘合剂,提高造粒品的强度;·探索最适宜的搅齿排列方式,以产生理想的颗粒;·寻求合适的搅齿材质,明显降低其磨损速率;·摸索搅齿轴功率与水量的关系,建立炭黑/水自调系统;·改进设备结构,如筒壁夹套加热除去附着层、粉料人口加设螺旋叶片、局部更换搅齿尖以及保持搅齿尖与筒壁的最佳距离等。
尽管湿法造粒过程是一种能耗较高的单元操作,人们一直力图对它进行改造,但是,到目前为止该方法仍在世界上橡胶用炭黑的后加工工序中占主流地位。
对橡胶用炭黑而言,由于橡胶在混炼过程中粘度较高,高硬度的湿法造粒品在胶料中受到强烈的剪切作用,完全能均匀地分散在聚合物中。
另外,随着橡胶加工业混炼工序自动化程度的不断提高,炭黑的气力输送和自动称量,也要求使用强度较高的湿法造粒品。
至今,散装炭黑的规模亦愈来愈大,由集散纸箱、槽车,到容量lt 的太空包,以至lO一20t的大型集散箱运输。
从橡胶用户的需求来看,湿法造粒产品仍是人们所优选的。
炭黑在介质中的良好分散是制品达到最佳使用性能的基础。
在非橡胶应用领域,特别是塑料和油墨等制品中,由于聚合物性质和混配设备的制约,常采用干法造粒炭黑。
但是,这种造粒方式的粒子硬度较差,在贮运过程中粒子极易破碎,细粉量相对较多而且是变化的,导致喂料机很难均匀送料,致使混配过程不稳定。
另外,从炭黑生产的角度看,在普通的干法造粒机中,炭黑的造粒速率很慢,过程效率亦太低。
毫无疑问,对非橡胶用炭黑而言,提高现有干法过程的效率或寻求其他方式增加炭黑密度,仍是当前技术开发的热点。
陶瓷干法制粉工艺及装备的研究开发

陶瓷干法制粉工艺及装备的研究开发陶瓷墙地砖新型陶瓷干法制粉工艺及关键装备的研究开发是一个整体的系统研发领域,具体研究内容可概括为以下几个方面。
1.适应于陶瓷干法制粉工艺的原料及配方的研究干法制粉工艺有别于湿法制粉工艺,需先将原料经过干法粉碎到工艺要求的细度,然后经过加水造粒形成压型需要的粉料。
适应于干法制粉工艺的原料性能的研究包括原料的物理性能及化学性能研究。
对于塑性原料,塑性指数是主要参数,它影响着最终粉料的成粒效果及粒度分布。
对于瘠性原料,原料硬度决定着干法细磨的细度和干磨效率,其性能特点也是重要的研究内容。
适应于干法制粉工艺的原料配方的研究是干法制粉工艺的关键。
由于干法粉碎及研磨设备是连续工作状态,达到工艺细度要求的细粉料被粉磨机、风选机及集料设备回收且用于造粒。
虽然细度达到工艺要求的筛分细度,但与同样筛分细度的湿法球磨机间歇式研磨的泥浆细度比较,其粉料粒度的分布和颗粒的表面能是有区别的,这些区别会影响后期的产品性能,如产品吸水率、强度。
为了保证配方原料在干磨(粉碎)后成分的均匀性和稳定性,从理论上讲,干法制粉工艺由于其自身特点,要求配方中原料的硬度应基本一致,并且原料种类不宜太多,在满足粉料性能及产品性能的前提下,配料物理性能尽可能相似,这样可保证原料细磨时原料配方成分的均匀一致性和稳定性。
然而实际情况是:我国地域辽阔,生产厂家所处的地理位置不同,可供选择的原料种类有限;不同厂家所生产的产品不同,不同种类的产品对原料的选择也有不同的要求。
因此,对于原来采用湿法工艺制备粉料的厂家,若采用干法工艺替代原来的湿法工艺,原料的配方一定要进行重新调整、试验。
鉴于干法粉磨设备的要求,一般来讲,原料的含水率不能超过10%,大于该含水率的原料,在干磨时需要进行预干燥处理。
2.原料干磨工艺及设备的研究开发与湿法球磨机间歇式研磨方式不同,干法粉碎及研磨设备是连续式工作状态。
为了保证配方料的均匀性和稳定性,除了考虑研究设计配方的同时,考虑粉碎研磨工艺流程也是干法制粉工艺需要重点研究的内容。
干法制粒的流程

干法制粒的流程一、制粒工艺概述干法制粒是指在无水或低水条件下将粉状物料通过压缩、挤压、切割等方式制成颗粒状的固体物料。
它是一种常见的制粒技术,广泛应用于化工、医药、食品等行业。
二、干法制粒的流程1. 原料处理干法制粒的原料通常为粉状或颗粒状,需要进行预处理。
首先将原料筛选去除杂质,然后根据要求进行混合,添加必要的辅料和助剂。
混合后的原料需要进行干燥处理,以保证其含水量不超过规定范围。
2. 破碎和分级对于大颗粒的原料需要进行破碎和分级处理。
这可以通过机械设备实现,例如颚式破碎机、锤式破碎机等。
分级则是根据颗粒大小将原料分类,以便后续操作。
3. 制粒在干法制粒过程中,通常采用压力或挤压方式将原料加工成颗粒。
具体操作方法包括:(1)压片法:将原料放入模具中,通过加压将原料压成固体片状,然后通过切割机将其切成颗粒;(2)挤出法:将原料放入挤出机中,通过挤压将原料推出模具,形成颗粒状;(3)滚压法:将原料放在双辊式压制机中,通过双辊的旋转将原料压制成颗粒状。
4. 干燥制粒后的颗粒需要进行干燥处理,以去除多余的水分。
通常采用流化床干燥器、旋转干燥器等设备进行干燥处理。
干燥后的颗粒含水量应符合规定要求。
5. 筛分和包装最后对制得的颗粒进行筛分和包装。
筛分是为了去除不合格品,保证产品质量。
包装则是为了方便储存和运输。
三、注意事项1. 原料处理过程中需要严格控制含水量,过高或过低都会影响产品质量。
2. 制粒时需要选择适当的工艺方法和设备,并根据实际情况进行调整。
3. 干法制粒过程中产生的尘埃对工作环境和操作人员健康有影响,需要采取相应的防护措施。
4. 制得的颗粒应符合相关标准要求,否则会影响产品质量和使用效果。
制粒工艺流程

总的工序流程:领料→拆料→处理→投料→制软材(叫粘合剂)→制湿颗粒→干燥→整粒→称重混合(加草莓粉末香精)→储存一原辅料粉碎过筛1.相关流程:预算领取物料>上报统计员拿取领料单>仓库领料至物净间点数(检查外包装袋有无破损,如有破损应及时与仓库人员说明情况)> 拆外包装消毒放置原辅料存放间>过筛置备料间。
(做好标识,并填写生产记录与管理记录)2.头孢克肟颗粒使用原辅料过筛目数:头孢克肟过100目,甘露醇过60目,交联聚维酮过60目。
3.如何提前预算领取的物料数量。
确保足够的备料量,需根据周生产计划量和岗位原辅料使用记录来确定,提前领取的物料数量。
4.在仓库领料需做的工作?核对物料的批号、品名、数量、进库批号,并且拿相应的物料检验报告单。
5.拆除处包装,需检查物料处包装是否破损,物料颜色是否异常有变化的情况并及时反馈给质检员或工艺员。
6.拆除外包装的物料需用3%的过氧化氢消毒物料外表面,并贴上物料卡,拉置原辅料存放间。
7.原辅料粉碎过筛,应核对对处理物料所需筛网目数,物料品名,批号,数量更换品种必须换筛网清洗摇摆机。
8.物料过筛后收率应不低于99.5%。
9.处理后的物料应将原始批号,进库批号,物料总重量报至工艺员处。
10.对于不合格的物料应放回到原包装或原物料桶内并做好密封与标识。
二.投料称量11.(一)生产前的准备。
12.1.检查工作区已没有存在任何与本次生产无关的残留物或生产记录等,并已清洁消毒且在有效期内。
13.2.检查生产区内的压差,温度,温度是否在规定范围内。
14.3.在工艺员领取本次需生产的指令单和所需记录。
(记得复核指令单)15.4.根据指令单,在生产门口挂上生产状态牌,并填写相应的产品名称,批号,规格,生产日期。
16.5.生产前,用标准砝码校准秘需的衡器。
17.6.在需用生产的设备,衡器上换挂上生产状态牌(正在运行)18.7.领取所需的生产用具,工具,容器等,并确认清洁消毒在有效期内。
干法制粒设备原理

干法制粒设备原理干法制粒设备是一种常用的固体颗粒物处理装置,其原理为通过将粉状物料经过干燥、研磨和分类处理后,再通过压制或喷雾等方式将其转化为固体颗粒物。
下面将详细介绍干法制粒设备的原理。
首先,干法制粒设备主要包括干燥机、研磨机和分类器。
其中,干燥机主要用于去除物料中的水分,使其达到所需的湿度。
研磨机负责将固体物料进行研磨处理,使其达到所需的细度和均匀度。
分类器则是将物料按照粒径分级,以保证粒径在一定范围内的固体颗粒物。
除此之外,还有再结晶设备、喷雾制粒设备等用于特殊需求的制粒设备。
干法制粒设备的主要工作过程如下:首先,经过预处理的物料首先进入干燥机,在其中被热空气吹干,去除水分。
干燥后的物料进入研磨机,通过切割、碾磨和撞击等力量,将其研磨成细小的颗粒。
然后,经过研磨的物料再进入分类器,通过离心力将粒径较大的物料分离出来,而较小的物料则通过筛孔进行分级,以获得所需的颗粒物。
最后,固体颗粒物可通过收集器进行收集和包装。
干法制粒设备的原理主要包括以下几个方面:1. 研磨原理:物料在研磨机中经过旋转的刀片、球体或者滚轮等破碎装置的作用下,产生剪切、挤压、撞击等力量,使物料被破碎成细小的颗粒。
研磨机的选择和操作方式能够控制物料的细度和均匀度。
2. 干燥原理:干燥机通过热风产生的高温和流体化的气流,将物料中的水分蒸发出去。
干燥机常用的加热方式有燃烧炉加热、蒸汽加热等。
物料在干燥过程中需要注意温度和时间的控制,以避免过热或过烘干物料。
3. 分级原理:分类器通过离心力和筛孔的作用将不同粒径的物料进行筛分和分离。
离心力使大颗粒物沉降分离,而较小的颗粒则能够通过较细的筛孔顺利流出。
分类器的选择和参数的调整能够控制颗粒物的粒径分布。
总之,干法制粒设备通过干燥、研磨和分类等工序,将粉状物料转化为固体颗粒物。
研磨原理通过力学作用将原料研磨成所需粒度和均匀度的颗粒;干燥原理通过热风蒸发物料中的水分;分级原理通过筛孔和离心力将颗粒物按粒径分离。
颗粒饲料加工工艺流程
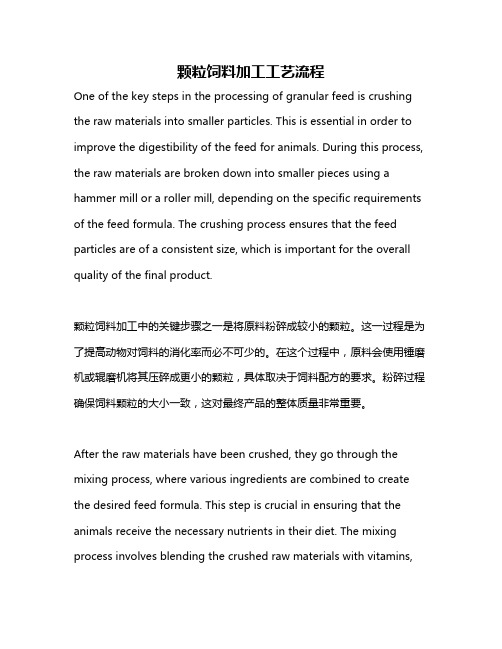
颗粒饲料加工工艺流程One of the key steps in the processing of granular feed is crushing the raw materials into smaller particles. This is essential in order to improve the digestibility of the feed for animals. During this process, the raw materials are broken down into smaller pieces using a hammer mill or a roller mill, depending on the specific requirements of the feed formula. The crushing process ensures that the feed particles are of a consistent size, which is important for the overall quality of the final product.颗粒饲料加工中的关键步骤之一是将原料粉碎成较小的颗粒。
这一过程是为了提高动物对饲料的消化率而必不可少的。
在这个过程中,原料会使用锤磨机或辊磨机将其压碎成更小的颗粒,具体取决于饲料配方的要求。
粉碎过程确保饲料颗粒的大小一致,这对最终产品的整体质量非常重要。
After the raw materials have been crushed, they go through the mixing process, where various ingredients are combined to create the desired feed formula. This step is crucial in ensuring that the animals receive the necessary nutrients in their diet. The mixing process involves blending the crushed raw materials with vitamins,minerals, and other additives to create a balanced feed that meets the nutritional needs of the animals. The quality of the mixing process directly impacts the nutritional value of the final granular feed product.原料经过粉碎后,将进行混合过程,将各种成分组合在一起,制成所需的饲料配方。
造粒车间工艺流程图
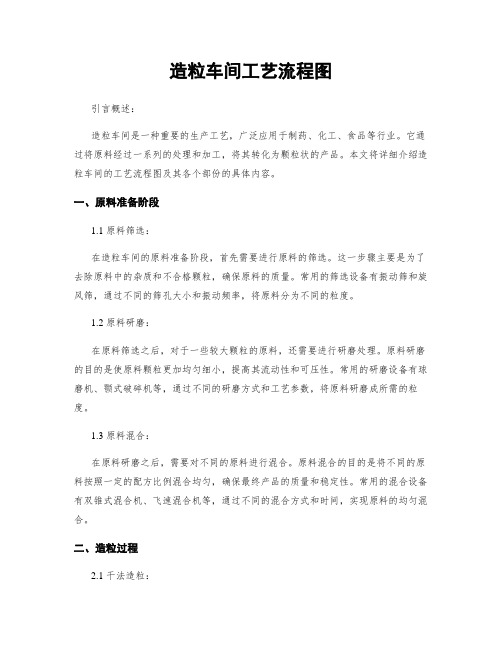
造粒车间工艺流程图引言概述:造粒车间是一种重要的生产工艺,广泛应用于制药、化工、食品等行业。
它通过将原料经过一系列的处理和加工,将其转化为颗粒状的产品。
本文将详细介绍造粒车间的工艺流程图及其各个部份的具体内容。
一、原料准备阶段1.1 原料筛选:在造粒车间的原料准备阶段,首先需要进行原料的筛选。
这一步骤主要是为了去除原料中的杂质和不合格颗粒,确保原料的质量。
常用的筛选设备有振动筛和旋风筛,通过不同的筛孔大小和振动频率,将原料分为不同的粒度。
1.2 原料研磨:在原料筛选之后,对于一些较大颗粒的原料,还需要进行研磨处理。
原料研磨的目的是使原料颗粒更加均匀细小,提高其流动性和可压性。
常用的研磨设备有球磨机、颚式破碎机等,通过不同的研磨方式和工艺参数,将原料研磨成所需的粒度。
1.3 原料混合:在原料研磨之后,需要对不同的原料进行混合。
原料混合的目的是将不同的原料按照一定的配方比例混合均匀,确保最终产品的质量和稳定性。
常用的混合设备有双锥式混合机、飞速混合机等,通过不同的混合方式和时间,实现原料的均匀混合。
二、造粒过程2.1 干法造粒:干法造粒是一种常用的造粒方式,它通过将原料在干燥状态下进行造粒。
在干法造粒过程中,首先将混合好的原料送入造粒机,然后通过机械力或者压力将原料压制成颗粒状。
常用的干法造粒设备有压片机、制粒机等,通过不同的工艺参数和模具形状,制备出不同形状和大小的颗粒。
2.2 湿法造粒:湿法造粒是另一种常用的造粒方式,它通过将原料在湿润状态下进行造粒。
在湿法造粒过程中,首先将混合好的原料与适量的溶剂或者粘合剂混合,形成湿团。
然后将湿团送入造粒机,通过机械力或者压力将湿团压制成颗粒状。
常用的湿法造粒设备有制粒机、喷雾干燥机等,通过不同的工艺参数和喷嘴形状,制备出不同形状和大小的颗粒。
2.3 热熔造粒:热熔造粒是一种特殊的造粒方式,适合于一些高熔点或者易熔化的原料。
在热熔造粒过程中,首先将原料加热至熔点或者软化点,形成熔液。
干法制粒工艺及设备若干问题的探讨_孙爱国

干法制粒是将粉体原料直接制成满足用户要求的颗粒状产品,造粒后堆积密度显著增加,可达到既控制污染,又减少粉料浪费,改善物料外观和流动性,便于贮存和运输,可控制溶解度、孔隙率和比表面积等目的。
干法制粒尤其适用于对水敏感的成分和对热敏感的成分。
本文拟从工艺和设备两方面对干法制粒常见问题做一探讨。
1工艺问题1.1辅料的选择干法制粒辅料应有良好的流动性和压缩成型性,即干燥黏合作用。
1.1.1微晶纤维素也用于湿法制粒的辅料。
其喷雾干燥法制成的产品流动性较好,药品的容纳量较大(即加入较多药品不致对其流动性及压缩成型性产生严重不良影响)。
1.1.2预胶化淀粉部分预胶化的淀粉称为可压性淀粉。
其流动性好,休止角<40°,压缩成型性好,兼有崩解作用,压成之药片崩解快,药物的释放性能好;单用预胶化淀粉为稀释剂压成的药片的硬度虽较好,但片剂的脆碎度不太好,如与微晶纤维素配合应用,则效果更好。
预胶化淀粉又具有自身润滑性,流动性比淀粉、微晶纤维素、糊精都好。
1.1.3硬脂酸镁建议干法制粒前加入1.0%~1.5%的硬脂酸镁来解决黏压辊问题。
做颗粒剂,内加硬镁可以稍多些;如果片剂或胶囊剂干法制粒,内加硬镁只要在能改善或解决物料黏压辊的前提下,能少加则少加,因为片剂或胶囊剂还要压片或填充,为抗黏冲还要外加硬镁,这样就提高了硬镁在处方中的总量。
1.1.4直压辅料想方便的话直接采用直压辅料,JRS的直压乳糖,卡乐康的直压淀粉,FMC的直压微晶纤维素,罗盖特的直压甘露醇、木糖醇、山梨醇等多元醇类效果很不错,品种有抗吸潮需要的加微粉硅胶。
1.1.5复合辅料国外有多种直接压片用的辅料,主要由糖类组成,例如“Ludipress”即由乳糖、PVP、交联PVP组成,并成细颗粒状;再如“Di-Pac”主要由蔗糖制成;“Soludexl5”由麦芽糖糊精等组成;“Emdex”中含有90%~92%的葡萄糖及2.25%的麦芽糖。
上等复合辅料的休止角均在30°左右或<30°,流动性很好,压缩成型性好,片剂的外观、崩解及药物溶出均较好,可以大幅度地简化片剂生产过程。
制粒的方法有湿法制粒和干法制粒

制粒的方法有湿法制粒和干法制粒制粒是一种将散粉或颗粒状的原料通过力的作用,形成固体颗粒的过程。
制粒可以改善原料的流动性、减少粉尘生成、方便储存和运输,并且提高产品的溶解性和可吸收性。
常见的制粒方法有湿法制粒和干法制粒。
下面我就来详细介绍一下这两种制粒方法。
湿法制粒是利用水或其他溶液将原料湿化,并通过一定的工艺操作使其成团。
湿法制粒的主要步骤包括配料、湿化、混合、造粒、干燥和筛分等。
首先是配料:根据产品的配方,将不同种类的原料按照一定比例混合。
然后是湿化:将混合好的原料加入到湿化设备中,通过加水或其他溶液搅拌混合,使原料湿润。
接下来是混合:将湿润的原料与其他辅助物料进行混合,使各种成分充分均匀地分布在原料中。
然后是造粒:将混合好的原料送入造粒机进行制粒。
造粒机通过一定的机械力作用,使原料形成固体颗粒。
常用的造粒方法包括挤压造型、滚压制粒和喷雾干燥等。
接着是干燥:将制成的湿粒经过干燥设备进行干燥,除去水分,使颗粒达到一定的干燥度。
最后是筛分:将干燥后的颗粒进行筛分,去除过大或过小的颗粒,使颗粒的大小达到要求。
相比于湿法制粒,干法制粒更加简单、高效。
它的主要步骤包括原料准备、混合、干燥、压片和筛分等。
首先是原料准备:根据产品的配方,将各种原料按照一定比例混合。
然后是混合:将混合好的原料进行均匀混合,使各种成分充分分布在原料中。
接着是干燥:将混合好的原料送入干燥设备进行干燥,去除水分,使原料变得干燥。
然后是压片:将干燥后的原料通过压片机进行压片。
压片机通过一定的机械力作用,将原料压制成固体片状。
最后是筛分:将压制成片状的产品进行筛分,去除过大或过小的颗粒,使颗粒的大小达到要求。
总的来说,湿法制粒适用于原料比较粘稠、易溶解、需要干燥的产品。
湿法制粒可以增加颗粒的密度,改善颗粒的流动性和溶解性。
而干法制粒适用于原料比较干燥、不易溶解、需要压片的产品。
干法制粒可以提高颗粒的强度和稳定性。
不管是湿法制粒还是干法制粒,都需要根据产品的特性和使用要求选择适合的制粒方法。
干法制粒的工艺流程
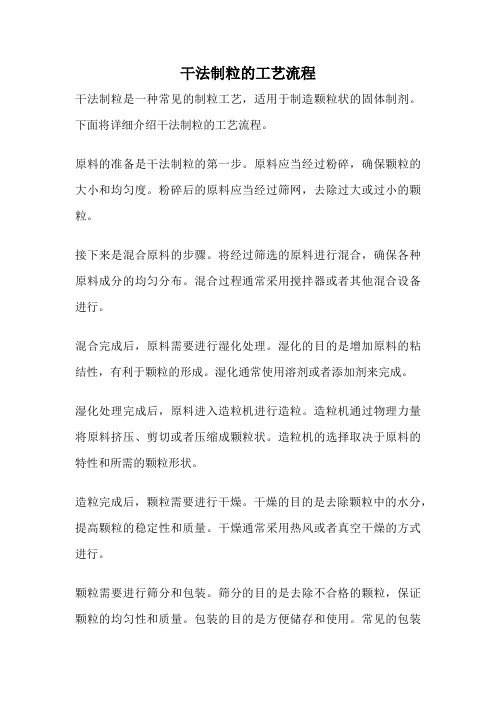
干法制粒的工艺流程
干法制粒是一种常见的制粒工艺,适用于制造颗粒状的固体制剂。
下面将详细介绍干法制粒的工艺流程。
原料的准备是干法制粒的第一步。
原料应当经过粉碎,确保颗粒的大小和均匀度。
粉碎后的原料应当经过筛网,去除过大或过小的颗粒。
接下来是混合原料的步骤。
将经过筛选的原料进行混合,确保各种原料成分的均匀分布。
混合过程通常采用搅拌器或者其他混合设备进行。
混合完成后,原料需要进行湿化处理。
湿化的目的是增加原料的粘结性,有利于颗粒的形成。
湿化通常使用溶剂或者添加剂来完成。
湿化处理完成后,原料进入造粒机进行造粒。
造粒机通过物理力量将原料挤压、剪切或者压缩成颗粒状。
造粒机的选择取决于原料的特性和所需的颗粒形状。
造粒完成后,颗粒需要进行干燥。
干燥的目的是去除颗粒中的水分,提高颗粒的稳定性和质量。
干燥通常采用热风或者真空干燥的方式进行。
颗粒需要进行筛分和包装。
筛分的目的是去除不合格的颗粒,保证颗粒的均匀性和质量。
包装的目的是方便储存和使用。
常见的包装
方式有袋装、瓶装等。
通过以上的工艺流程,干法制粒可以将原料制成颗粒状的固体制剂。
这种制粒方法具有工艺简单、成本低廉、生产效率高等优点,被广泛应用于制药、化工、冶金等领域。
希望以上的介绍能够帮助您对干法制粒的工艺流程有更加深入的了解。
制粒生产流程解读
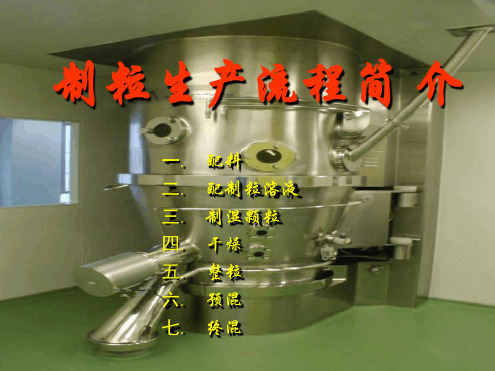
二 配制粒溶液
将粘合剂融入溶剂中制成 制粒时所需的润湿粘合剂。
设备: 配液搅拌器
配制制粒溶液
酒精分配系统
三制湿颗粒
设备:强力混合机
1.干混 2.加制粒溶液 3.湿混 4.出料
搅拌棒,制粒 刀旋转将软材切割 成颗粒。
制粒刀旋转方向
搅拌棒旋转方向
四 干燥
刀式磨粉机整粒刀磨机内部刀片组合高速旋转将颗粒打碎并通过统一孔径的筛网使颗粒成为较为匀称的颗粒摇摆式整粒机整粒通过辊筒与筛网的摩擦将颗粒挤压通过统一孔径的筛网得到较为匀称的颗粒
制粒生产流程简 介
一. 配料 二. 配制粒溶液 三. 制湿颗粒 四. 干燥 五. 整粒 六. 预混 七. 终混
一配 料
?按照处方要求将产品所需的原 辅料分量,并正确标识。
3.干燥
4.冷却
5.出料至储料罐
干燥由程序控制进行
FBD内防止粉尘外泄 的不锈钢过滤器.
进风冲压室
气流导向板
一楼 整粒
将干燥后的颗粒整成较为匀称的颗粒
整粒机内部
刀片组合高速旋转将 颗粒打碎并通过统一 孔径的筛网 ,使之成为 较为匀称的颗粒 .
预混 终混
制粒结束, 等待压片.
终
Thanks
七 终混
流化床制粒
一种快速的制粒方法
三楼
PMA800混合机制湿颗粒
1.干混 2.喷制粒溶液 3.湿混 4.下料至FBG
三楼
PMA生产由PLC程序控制
喷液罐
混合机内部结构与强 力混合机相同.
二楼 FBD干燥
依靠单向流动的热气流将
湿颗粒在FBD内沸腾,带走 1.预热
水分,使颗粒干燥.
造粒车间工艺流程图
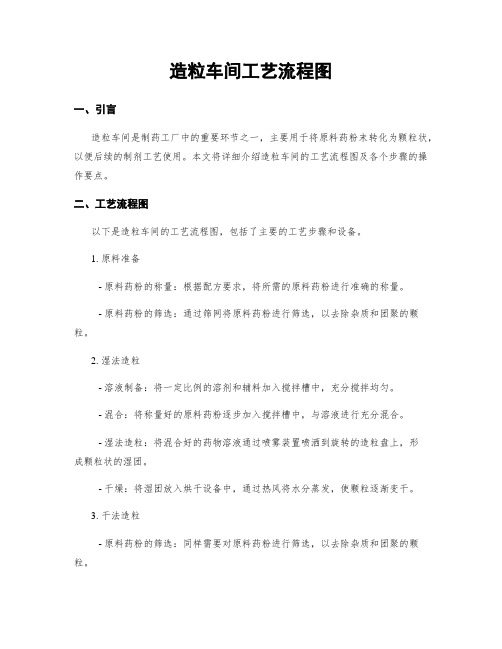
造粒车间工艺流程图一、引言造粒车间是制药工厂中的重要环节之一,主要用于将原料药粉末转化为颗粒状,以便后续的制剂工艺使用。
本文将详细介绍造粒车间的工艺流程图及各个步骤的操作要点。
二、工艺流程图以下是造粒车间的工艺流程图,包括了主要的工艺步骤和设备。
1. 原料准备- 原料药粉的称量:根据配方要求,将所需的原料药粉进行准确的称量。
- 原料药粉的筛选:通过筛网将原料药粉进行筛选,以去除杂质和团聚的颗粒。
2. 湿法造粒- 溶液制备:将一定比例的溶剂和辅料加入搅拌槽中,充分搅拌均匀。
- 混合:将称量好的原料药粉逐步加入搅拌槽中,与溶液进行充分混合。
- 湿法造粒:将混合好的药物溶液通过喷雾装置喷洒到旋转的造粒盘上,形成颗粒状的湿团。
- 干燥:将湿团放入烘干设备中,通过热风将水分蒸发,使颗粒逐渐变干。
3. 干法造粒- 原料药粉的筛选:同样需要对原料药粉进行筛选,以去除杂质和团聚的颗粒。
- 干法造粒:将筛选好的原料药粉通过造粒机进行干法造粒,通过机械力的作用使粉末会萃成颗粒。
- 筛分:将干法造粒得到的颗粒进行筛分,以控制颗粒的大小范围。
4. 成品处理- 冷却:将造粒后的颗粒通过冷却设备进行降温,以防止颗粒在后续的包装过程中变软或者粘连。
- 包装:将冷却好的颗粒通过自动包装机进行包装,通常使用密封袋或者瓶装。
5. 清洁和消毒- 设备清洁:定期对造粒车间的设备进行清洁,以确保生产环境的卫生和产品质量的稳定。
- 环境消毒:定期对车间进行消毒处理,以杀灭细菌和微生物,防止交叉污染。
三、操作要点1. 原料准备阶段:- 确保原料药粉的准确称量,避免误差对产品质量造成影响。
- 注意原料药粉的筛选工作,确保颗粒的均匀性和纯净度。
2. 湿法造粒阶段:- 溶液制备时要充分搅拌均匀,确保药物和溶剂的充分混合。
- 控制喷雾装置的喷雾量和角度,以获得均匀的湿团。
- 干燥过程中要控制热风的温度和流量,避免颗粒过度干燥或者过度结块。
3. 干法造粒阶段:- 控制干法造粒机的转速和压力,以获得理想的颗粒形态和大小。
探析干法辊压造粒技术

探析干法辊压造粒技术前言干法辊压造粒技术主要是将干粉装的化工原料采用相应的工艺技术进行加工,制成满足用户需求和符合标准大小的粒状产品。
在实际生产中,需要进行脱气、轧片、碎片、整粒、筛分等操作,具有配置合理、能耗较低、操作方便、流程简单等优势。
该方法主要是通过外部加压的方式,在两个相对旋转的辊轮间隙中强行通过,使之压缩成片。
在辊压的过程中,物料的实际密度将会增大,并且达到相应的强度要求。
一、干法辊压造粒技术的概述(一)工作原理在干法辊压造粒机顶部加入干粉物料,经过罗选定压缩和脱气之后,向轧辊弧形槽口输送。
轧辊通过反向、等速额旋转,咬入物料并进行强制压缩。
经过压缩去之后,物料的压力降低,在重力和表面张力的作用下,自然脱出,进入破碎机破碎和整粒机整粒。
最后通过振动筛进行筛分,并将合格的产品进行包装或输入成品仓[1]。
对于粉状筛下的物料,回聊装置会将其送回原料仓重新进行辊压。
根据颗粒强度的要求,液压系统能够对挤压力的大小进行调节。
对于不同形状的物料,可以相应的调整辊面开槽形式。
(二)工艺流程真空上料机将干粉原料粉末送入搅式时过渡料仓,然后物料会被上料装置均匀的送入变频式立式螺旋喂料机,在此进行物料的脱气和预压缩。
物料在预压缩之后,会在相对转动的压辊中被压实,然后进入破碎机被破碎,形成粒径不同的颗粒。
这些颗粒通过整粒机的修整,然后通过带网孔的筛板挤出,进入筛分机。
完成筛分之后,对于合格的成品,可直接收集,对于筛分下来的粉状物料,将会重新返回重新操作[2]。
二、干法辊压造粒机结构干法辊压造粒机是该技术应用的主要设备,其中主要包含了脱气槽、搅拌器、螺旋推进器、轧片机、碎片机、整粒机、旋振筛等部分。
脱气槽的作用是将粉状原料暂时存放,并将其中的气体排除。
搅拌器用于进一步搅拌和脱气物料,并将其输送到螺旋推进器[3]。
螺旋推进器会对物料进行预压缩,使物料的密度增大,从而符合轧片的实际要求,并且将预压缩的物料送入轧片机。
干法制粒工艺流程

干法制粒工艺流程
《干法制粒工艺流程》
干法制粒是一种常用的固体制剂制备工艺,适用于制备颗粒状或粉末状的药物、化学品等产品。
干法制粒工艺流程主要包括原料处理、混合、颗粒形成、干燥和包装等步骤。
首先,原料处理是干法制粒的第一步,对原料进行筛分、粉碎、混合等处理,以确保原料的均匀性和质量。
其次,混合是为了将不同成分的原料均匀混合在一起,以确保颗粒形成时成分均匀。
对原料进行粘结剂的添加,通过混合使每个颗粒都含有足够的粘结剂,从而保证颗粒的结实性和一致性。
接着,颗粒形成是通过压制或滚动等方法将混合好的原料制成颗粒状。
在这一步骤中,需要控制压力、温度和速度等参数,以确保颗粒的大小和形状符合要求。
随后,干燥是将颗粒中的水分蒸发掉,使颗粒达到所需的含水率。
常见的干燥方法包括气流干燥、真空干燥等,通过不同的干燥方法可以实现对颗粒的不同要求。
最后,包装是将干燥好的颗粒进行包装,以确保产品的质量和保存期限。
包装材料通常采用塑料袋、铝箔袋等,同时需要控制包装环境的湿度和温度,以保证产品的质量和稳定性。
总的来说,干法制粒工艺流程包括原料处理、混合、颗粒形成、干燥和包装等步骤,每一步都需要精确控制工艺参数,以确保最终产品的质量和稳定性。
通过不断改进和优化工艺流程,可以提高产品的生产效率和质量,满足市场的需求和要求。
造粒车间工艺流程图

造粒车间工艺流程图一、引言造粒车间是制药工厂中的重要环节,主要用于将原料粉末转化为颗粒状的制剂。
本文将详细介绍造粒车间的工艺流程图,并对每一个步骤进行详细解释。
二、工艺流程图以下是造粒车间的工艺流程图:1. 原料准备- 原料称量:根据配方要求,将所需原料按照一定比例进行称量。
- 原料筛选:将称量好的原料进行筛选,去除杂质和颗粒不均匀的原料。
2. 混合- 原料混合:将筛选好的原料放入混合机中,进行均匀混合,确保每一个颗粒中含有相同的成份。
3. 湿法造粒- 混合物溶解:将混合好的原料溶解在适量的溶剂中,形成浆状物。
- 搅拌:通过搅拌机对浆状物进行搅拌,使其均匀混合。
- 喷雾造粒:将搅拌好的浆状物通过喷雾器喷雾到烘干室中,形成颗粒状的制剂。
- 干燥:将喷雾后的颗粒状制剂在烘干室中进行干燥,除去溶剂,使其固化。
4. 干法造粒- 混合物压缩:将混合好的原料放入造粒机中,通过压力将其压缩成颗粒状的制剂。
- 筛分:将压缩后的颗粒进行筛分,去除不符合要求的颗粒。
- 干燥:将筛分后的颗粒状制剂在烘干室中进行干燥,除去水分,使其固化。
5. 筛分和包装- 筛分:将干燥后的颗粒进行筛分,去除不符合要求的颗粒。
- 包装:将筛分好的颗粒状制剂进行包装,通常使用密封包装袋或者瓶子。
6. 清洁和消毒- 清洁:定期对造粒车间的设备进行清洁,确保无尘和杂质。
- 消毒:定期对造粒车间进行消毒,以确保制剂的质量和卫生安全。
三、工艺流程解释1. 原料准备:原料的准备是创造高质量制剂的关键步骤。
通过精确的称量和筛选,可以确保原料的质量和成份的准确性。
2. 混合:混合过程中,原料的均匀性对最终产品的质量起着重要作用。
混合机的选择和操作技术对混合效果有直接影响。
3. 湿法造粒:湿法造粒适合于一些难以通过干法造粒实现的制剂。
溶解和搅拌过程确保原料均匀分散,喷雾造粒和干燥过程将浆状物转化为颗粒状制剂。
4. 干法造粒:干法造粒适合于一些不适合湿法造粒的制剂。
造粒炭黑的制法及其填充胶料

存储性会变差。颗粒硬度太低时,流动过程
或运输过程中会 因摩擦和破裂等作用造成许 多细 粉 ,结果产 生 运输上 的问题 ,并且 不利
于造粒 炭 黑混入 所使用 的介 质 中。 本 发 明 的 目的在于提 供 具有 良好 的流动 性和 存储 性 ,质地 十分柔 软 ,能 良好地 混合
的物理现象和所形成颗粒的特性密切相关。 湿 法 造粒 时 ,使用带 旋 转搅齿 轴 的 圆筒
3 ~ 10 ,以 4 " 7 ℃为宜 。 0 0℃ 0- 0 -
.
2 % 宜 ,直径 0 7 ~ 1O 的颗粒 的单 个 5为 . 1 .m 颗 粒硬度 为 70 5 O ,以 8 0 0O . "2 .g . "2 .g为
宜。
造 粒炭 黑的 比表 面积 为小 于 7 m/ ,以 02g 小于 5m/ 为 宜 。未 干燥 的造 粒炭 黑 的水 0 g 分为 3 ~6% ( 5 0 以质量 计 ) 。 本 发 明的造粒 炭 黑适用 于 高分子 复合材
粒形状 和/ 或颗粒 构造 不能令 人满意 的缺 点 ,使得 可加 工性 ( 可分 散性 和混 炼速度 ) 和/ 或流动性及存储性变差。 为 了使炭 黑颗 粒迅速 碎裂 ,实现快 速而
良好 的分 散 ,应 当尽 可 能减 小造粒 炭黑 的颗 粒硬 度 。不过 ,颗 粒硬度 减 小后 ,流动 性和
未粒化 的炭 黑用 输送 螺旋 送入 搅齿 式混
的 炭 黑 颗 粒 在 其 他 工 艺 中 被 干 燥
( D 16 4 2 号 、 U P 6 7 8 号 、 E 2 4 1 S30 06
合造粒机的进料段。炭黑 的流通量与输送螺
旋 的输送 速度 相 当, 因而 能在 很 宽范 围 内加
- 1、下载文档前请自行甄别文档内容的完整性,平台不提供额外的编辑、内容补充、找答案等附加服务。
- 2、"仅部分预览"的文档,不可在线预览部分如存在完整性等问题,可反馈申请退款(可完整预览的文档不适用该条件!)。
- 3、如文档侵犯您的权益,请联系客服反馈,我们会尽快为您处理(人工客服工作时间:9:00-18:30)。
搅齿造粒机应用在干法造粒的过程炭黑是一种堆积密度很低的粉末状物质,易飞扬而污染环境,运输性极差。
一般说来,增加其密度,在某种程度上会克服或清除这些缺点,但也降低了它在介质中的分散性。
炭黑工业常以湿法或干法造粒的方式对粉状炭黑进行加工。
湿法造粒是上个世纪4o年代开发的一项技术。
在最近5O多年中,炭黑工业也在一直不断地改进湿法造粒过程,使之日臻完善。
这些改进主要包括如下几个方面:·开发各种粘合剂,提高造粒品的强度;·探索最适宜的搅齿排列方式,以产生理想的颗粒;·寻求合适的搅齿材质,明显降低其磨损速率;·摸索搅齿轴功率与水量的关系,建立炭黑/水自调系统;·改进设备结构,如筒壁夹套加热除去附着层、粉料人口加设螺旋叶片、局部更换搅齿尖以及保持搅齿尖与筒壁的最佳距离等。
尽管湿法造粒过程是一种能耗较高的单元操作,人们一直力图对它进行改造,但是,到目前为止该方法仍在世界上橡胶用炭黑的后加工工序中占主流地位。
对橡胶用炭黑而言,由于橡胶在混炼过程中粘度较高,高硬度的湿法造粒品在胶料中受到强烈的剪切作用,完全能均匀地分散在聚合物中。
另外,随着橡胶加工业混炼工序自动化程度的不断提高,炭黑的气力输送和自动称量,也要求使用强度较高的湿法造粒品。
至今,散装炭黑的规模亦愈来愈大,由集散纸箱、槽车,到容量lt 的太空包,以至lO一20t的大型集散箱运输。
从橡胶用户的需求来看,湿法造粒产品仍是人们所优选的。
炭黑在介质中的良好分散是制品达到最佳使用性能的基础。
在非橡胶应用领域,特别是塑料和油墨等制品中,由于聚合物性质和混配设备的制约,常采用干法造粒炭黑。
但是,这种造粒方式的粒子硬度较差,在贮运过程中粒子极易破碎,细粉量相对较多而且是变化的,导致喂料机很难均匀送料,致使混配过程不稳定。
另外,从炭黑生产的角度看,在普通的干法造粒机中,炭黑的造粒速率很慢,过程效率亦太低。
毫无疑问,对非橡胶用炭黑而言,提高现有干法过程的效率或寻求其他方式增加炭黑密度,仍是当前技术开发的热点。
有关造粒过程的简单描述等人在研究炭黑的内聚性(Cohesiveness)时发现,加压成型的炭黑块,随着密度的微小增加,其抗张强度迅速增大。
Rwei等人则进一步发现,炭黑块的抗张强度与其密度的4次方成正比。
他们在测定粒子在剪切流中的破碎与磨损性时也证实,炭黑的分散性与粒子密度呈类似的函数关系。
显然,造粒炭黑的粒子强度和分散性,受其密度的影响十分强烈。
在干法造粒过程中,粉状炭黑沿转鼓的筒壁滚动,聚集体靠范德华力与静电力附聚在一起。
造粒转鼓的圆周速度只有1—2m/s。
因而,这种造粒过程进行得相当柔和与缓慢。
若转鼓的圆周速度太高,在离心力的作用下,粒子则不沿筒壁发生滚动,而且作用于粒子球上的作用力太大,反而会使粒子破碎。
在湿法造粒时,粉状炭黑必须被水润湿到一定程度,以取代聚集体表面上吸附的气体。
润湿后的粉末,通过液桥和毛细力附着在一起。
在机械力作用下,粒子附聚与长大。
湿法造粒的优点在于,以水作为介质,不仅造粒速度快,过程效率高,而造粒品的强度亦较高。
造粒质量,一般以影响炭黑贮运性能有关的参数来衡量。
最常用的指标是,细粉量、粒子磨损量、堆积强度、单个粒子强度、平均颗粒尺寸以及颗粒尺寸分布等。
搅齿造粒机用于干法造粒搅齿造粒机,历来是湿法造粒的关键设备。
它与干燥机串联一起,完成炭黑的湿法造粒过程。
现在,搅齿造粒机用于干法造粒,其目的主要有两个。
一是改进现有干法造粒的过程效率;再则是提供分散性好、细粉量低而粒子尺寸分布更均匀的造粒品。
众所周知,搅齿造粒机在用于湿法过程时,搅齿端的圆周线速度一般应在1O~20m/s范围;炭黑在造粒机中的停留时间也很短,只有几秒钟。
当这种搅齿造粒机用于干法过程时,业已证实,其搅齿端的圆周线速度应降至1~6m/s,而炭黑在造粒机中的停留时间应延长到20~180s。
在这样的工艺条件下,即使不向搅齿造粒机中加水,也能获得质量稳定的造粒炭黑。
以搅齿造粒机进行干法造粒的流程示于图1。
从图中可见,该流程的特点是,造粒机轴线不是水平放置,而是粉状炭黑入口稍低,粒状炭黑出口稍高。
造粒机轴线与水平线呈0~15。
的倾角。
与传统的千法造粒一样,粉状炭黑要与一定量的母粒一起送入造粒机。
如图所示,母粒乃是由贮缶14经螺旋输送器送人搅齿造粒机10的进料口15的。
造粒机的外壁,用夹套加热,由恒温器16调节到所需温度。
该方法的优点在于,通过调整搅齿的圆周线速度和平均停留时间,即可满足任一特定炭黑品种的造粒质量要求。
另外,与传统的转鼓式造粒机相比,过程效率显著提高。
适当选择搅齿造粒机尺寸,如内径700~800ram,在保持理想的造粒质量的条件下,设备生产能力可达2t/h或更高。
工艺参数对造粒质量的影响下面,以一台实验用搅齿造粒机为例,研究工艺参数对造粒质量的影响。
这台实验用造粒机,筒壁内径200mm,长度1200mm,夹套温度控制在100℃,粉状炭黑最大处理能力约60kg/h。
实验用粉状炭黑,近似于N231类产品,其BET表面积120m2/g,DBP吸油值106ml/100g,24M4DBP值81ml /100g,而堆积密度约为120g/L。
停留时间当搅齿轴的转速保持恒定的条件下,炭黑在造粒机中的停留时间,可通常以下式表达:/式中,t为平均停留时间;mf为造粒机中炭黑填充量;m为炭黑进料量。
平均停留时间,取决于造粒机中的炭黑填充量和炭黑进料量。
粉状炭黑,通常是由螺旋输送机送入搅齿造粒机的。
因此,在设备达到稳定运转的条件下,造粒炭黑产量、粉状炭黑处理和螺旋输送机的喂料量皆是相同的,并可在很宽的范围内调节。
显然,可以通过调节搅齿造粒机轴线与水平线的夹角,来改变造粒机中的炭黑填充量和延长停留时间。
当然,炭黑在造粒机中的填充量与停留时间也受搅齿轴转速的影响。
造粒炭黑产量保持恒定时,随着搅齿轴转速的加快,炭黑填充量与停留时间彼此成比例地减少。
实验表明,停留时间的调整,应在保持造粒机产量恒定的条件下,改变造粒机的倾斜度,即造粒机轴线与水平线的夹角在0—15。
之内,优选的停留时间宜在20~180s范围之内。
为此,要为每个倾斜角度计算出稳定运转条件下造粒机内的炭黑填充量。
不同倾斜度的造粒机所造出的粒状炭黑性能参见表1。
从表中数据可见,随着造粒机倾角的增大,造粒炭黑的细粉量和粒子磨损量下降,平均颗粒尺寸增大,尺寸分布明显变窄,堆积密度基本不变,而单个粒子强度有所下降。
母粒回流量原则上说来,任何类型的炭黑均可用搅齿造粒机实施干法造粒。
实验证实,比表面积和结构均较低的炭黑容易造粒。
比表面积和结构均较高的炭黑也容易造粒。
相反地,比表面积高而结构低的炭黑或比表面积低而结构高的品种,则难于造粒。
为了引发造粒过程,因此将一部分母粒送回造粒机。
母粒回流量最好是造粒炭黑产量的5%-15%。
对难于造粒的炭黑品种,母粒回流量可高达50%。
对易于造粒的品种,母粒可以不回流或在造粒设备开始运转正常之后停止回流。
表2中数据表明,对实验所用的炭黑而言,随着母粒回流量的增加,细粉量和磨损量均开始减少,在回流量达到30%时,二者呈最小值;然后,随着回流量的进一步加大,二者又回升至较大值。
当回流量比较高时,粒子尺寸分布明显变窄,堆积密度稍有增加。
然而,粒子硬度几乎不受母粒回流量的影响。
应当强调,母粒的最佳回流量,取决于炭黑类型。
它必须由各种炭黑分别通过实验确定。
表10中数据仅是该实验炭黑(近似于N231)的测定结果。
搅齿轴转速当实验用造粒机的搅齿轴转速在150~500r/min内变化,搅齿尖的圆周线速度相当于在1~6m /s范围内。
搅齿轴转速与造粒性能之间的关系参见表3。
看来,随着搅齿轴转速的增加,细粉量和磨损量开始减少,粒子尺寸分布亦更窄。
当搅齿轴转速在400r/min时(搅齿尖线速度相当于4.2m/s),这3项指标均呈现一最小值。
尔后,随着转速的增加,它们又呈上升趋势。
当转速在500r/min(相当于搅齿尖线速度5.3m/s),粒子大量破碎,细粉量急剧增加。
粉状炭黑处理量为了考察造粒机的粉状炭黑处理量对造粒过程的影响,进料量从10kg/h至60kg/h变化,造粒产品质量数据参见表4。
从表中结果可知,细粉量与粉状炭黑处理量的多少无关,细粉量在1.4%~3.2%之间变化。
磨损量则随处理量的增加而减少。
应当指出,上述4项工艺条件对造粒质量的影响均是在特定的造粒机尺寸和一种实验炭黑条件下获得的数据。
为了在搅齿造粒机中造出合乎要求的炭黑粒,必须适当地调整操作参数,以与干法造粒的质量要求相匹配。
搅齿造粒机与转鼓造粒机串联尽管搅齿造粒机完全可单独用于干法造粒,制备出质量合乎要求的粒子,但另有一项技术方案是,把搅齿造粒机串联在传统的转鼓式造粒之前,使后者的生产能力提高1.5~2.5倍,大幅提高了设备效率。
实验炭黑,选用一种普通色素品种,其BET表面积为90m/g,DBP 吸油值52ml/100g,24M4DBP 值46ml/100g,粉状产品的堆积密度为194g/L。
实验用搅齿造粒机的设备尺寸与上述的相同。
其主要工艺参数为,搅齿轴转速350r/min,粉状炭黑进料量40kg/h,母粒回流量11kg/h。
在这种条件下干法制备的产品,再作为原料送入传统的转鼓造粒机中。
实验所用的转鼓造粒机,直径600mm,长度4000mm。
当造粒机以传统操作,送入粉状炭黑,处理量从10kg/h开始,以增量20kg/h逐步递增,到处理量为30kg/h时,造粒质量尚能满足要求;当处理量增至50kg/h时,已完全不能造粒。
当以搅齿造粒机的产品为原料时,该转鼓造粒机的炭黑处理量可达70kg/h。
搅齿造粒机中加入添加剂对干法造粒而言,Jordan曾开发了一种在粉状炭黑中添加2%-15%可溶于油墨的一种油料,然后再进行干法造粒"J。
这种造粒品要比普通的干法产品的粒子更牢固,而且很容易分散在油墨中。
这是由于粒子中炭黑的密度较低,而且又含有可溶于油墨的油料,所以分散效果颇佳。
后来,人们又尝试看向粉状炭黑中添加各种蜡,以不同方式进行造粒。
然而,在这些研究工作中,蜡的添加量普遍偏高,有的竞高达40%以上,影响到造粒品的应用。
最近,Vogler和Callahan 等人分别研究,将一种在环境温度下呈固态的可熔融材料,以低于10%的添加量,用于搅齿造粒机的干法造粒过程。
添加剂的添加位置及喷入方式研究,向粉状炭黑中加入熔融的蜡或蜡的混合物,以强化搅齿造粒机的干法造粒过程。
为了防止炭黑粘在造粒机筒壁及机内部件上,加蜡之后,整个造粒机的温度要比蜡的熔点高上10%~20%。
蜡的加入位置,要尽量靠近粉状炭黑入口,必须在造粒区的前三分之一段内将蜡喷洒到炭黑上。
这样,方能保证蜡尽可能早地与炭黑均匀混合。